Prosoft MNET_MCM_Datasheet
超米特电子有限公司产品说明书

1US Headquarters TEL +(1) 781-935-4850FAX +(1) 781-933-4318 • Europe TEL +(44) 1628 404000FAX +(44) 1628 404090Asia Pacific TEL +(852) 2 428 8008FAX +(852) 2 423 8253South America TEL +(55) 11 3917 1099FAX +(55) 11 3917 0817Superior elongation and tensilestrength help to prevent tearing in use due to mishandling. Typical properties for CHO-SEAL 1310 and 1273 materi-al are shown on pages 33 and 32respectively.High Shielding PerformanceCHO-SEAL 1310 material provides more than 80 dB of shielding effectiv-ness from 100 MHz to 10 GHz, while CHO-SEAL 1273 material provides more than 100 dB.Low Volume ResistivityBoth materials have exceptionally low volume resistivity, which makes them well suited for grounding appli-cations in which a flexible electrical contact is needed.Low Compression GasketSpacer gaskets are typicallydesigned to function under low deflec-tion forces. Chomerics uses design tools such as Finite Element Analysis (FEA) to accurately predict compres-sion-deflection behavior of various cross section options. Refer to page16.LCP Plastic SpacerLiquid crystal polymer (LCP)spacers, including those made with Vectra A130 material, provide aCHO-SEAL ®1310 or 1273Conductive ElastomersWith EMI spacer gaskets, shielding and grounding are provided by Chomerics’CHO-SEAL 1310 and 1273 conductive elastomers, specifi-cally formulated for custom shape molded parts. They provide excellent shielding and isolation against electro-magnetic interference (EMI), or act as a low impedance ground path between PCB traces and shielding media. Physically tough, these elas-tomers minimize the risk of gasket damage, in contrast to thin-walled extrusions or unsupported molded gaskets.Silicone-based CHO-SEAL 1310and 1273 materials offer excellent resistance to compression set over a wide temperature range, resulting in years of continuous service. CHO-SEAL 1310 material is filled with silver-plated-glass particles, while 1273 utilizes silver-plated-copper filler to provide higher levels of EMI shielding effectiveness.EMI Spacer GasketsThe unique design of Chomerics’EMI spacer gaskets features a thin plastic retainer frame onto which a conductive elastomer is molded. The elastomer can be located inside or outside the retainer frame, as well as on its top and bottom surface. EMI spacer gaskets provide a newapproach to designing EMI gaskets into handheld electronics such as dig-ital cellular phones. Board-to-board spacing is custom designed to fit broad application needs. Customized cross sections and spacer shapes allow for very low closure forcerequirements and a perfect fit in any design or device.Robotic InstallationSpacer gaskets can be installed quickly by robotic application. Integral locater pins in the plastic spacer help ensure accuratepositioning in both manual and pick-and-place assembly. Benefits include faster assembly and lower labor costs.The integrated conductive elastomer/plastic spacer gasket is a low cost,easily installed system for providing EMI shielding and grounding in small electronic enclosures.Figure 1Single Piece EMI Gasket/Locator PinsCHO-SEAL 1310 or 1273 Conductive Elastomer (Inside)Plastic Spacer Around Outsideor InsideApplications for EMI Spacer GasketsThe spacer gasket concept is especially suited to digital and dual board telephone handsets or other handheld electronic devices. It provides a low impedance path between peripheral ground traces on printed circuit boards and components such as:•the conductive coating on a plastic housing•another printed circuit board •the keypad assemblyTypical applications for EMI spacer gaskets include:•Digital cellular, handyphone and personal communications services (PCS) handsets •PCMCIA cards•Global Positioning Systems (GPS)•Radio receivers•Other handheld electronics, e.g.,personal digital assistants (PDAs)•Replacements for metal EMI shield-ing “fences” on printedcircuit boards in wireless tele-communications devicesstable platform for direct, highprecision molding of conductive elas-tomers. The Vectra A130 material described in Table 1 has excellent heat deflection temperature character-istics (489°F, 254°C). For weight con-siderations, the LCP has aspecific gravity of only 1.61. This plas-tic is also 100% recyclable.Typical EMI Spacer Gasket Design ParametersThe EMI spacer gasket concept can be considered using the design parameters shown in Table 2. Some typical spacer gasket profiles are shown below.Figure 2Typical Spacer Gasket Profiles3US Headquarters TEL +(1) 781-935-4850FAX +(1) 781-933-4318 • Europe TEL +(44) 1628 404000FAX +(44) 1628 404090Asia Pacific TEL +(852) 2 428 8008FAX +(852) 2 423 8253South America TEL +(55) 11 3917 1099FAX +(55) 11 3917 0817Finite Element AnalysisChomerics, a division of the Parker Hannifin Corporation’s Seal Group, is the headquarters of Parker Seal’s Elastomer Simulation Group. This unit specializes in elastomer finite element analysis (FEA) using MARC K6 series software as a foundation for FEA capability.Benefits of FEA include:•Quickly optimizing elastomer gasket designs•Allowing accurate predictions of alternate elastomer design concepts •Eliminating extensive trial and error prototype evaluationTypical use of FEA in EMI spacer gasket designs is to evaluate the force vs. deflection requirements of alternate designs.For example, onespacer design features a continuous bead of con-ductive elastomer molded onto a plastic spacer. An alternative designemploys an “interrupted bead,” where the interrup-tions (gaps left on the plastic frame) are sized to maintain the requiredlevel of EMI shielding. Figure 4illustrates these alternative designs.Gasket DeflectionFigure 5 compares the effect of continuous and interrupted elastomer gasket designs in terms of the force required to deflect the conductive elastomer. This actual cellular handset application required a spacer gasket with interrupted bead to meet desired deflection forces.Chomerics Designand Application ServicesChomerics will custom design a spacer for your application. Advice,analysis and design assistance will be provided by Chomerics Applications and Design engineers at no additional fee. Contact Chomerics directlyat the locations listed at the bottom of the page.Figure 3FEA Example of an EMISpacer Gasket Cross SectionFigure 4Continuous (top) and InterruptedElastomer GasketsFigure 5Typical Spacer Gasket Deflection。
HS8916_V0.6_Datasheet Preliminary

QUAD-BAND GSM/GPRS/EDGE W Multi-Mode Transmit Module with Fourteen Linear TRx Switch Ports andDual-Band TD-SCDMA B34/39 and TDD LTE B39HS8916 Preliminary DatasheetVersion 0.62016-03-21HS8916 Front-end ModuleProduct Features ApplicationsG N DG N DG N DG N DG N DC P LG NDN CTRX10ANT TRX9TRX8GND GNDGND TRX11TRX12TRX13TRX14•LGA: 5.5 mm x 5.3 mm x 0.85 mm Max•Fully programmable MIPI RFFE control •Fourteen low -insertion-loss TRx ports (fiveultra-low loss) with enhanced linearity, for state-of-the-art 4G performance and GPS /•Cellular handsets encompassing Quad -Band GSM/EDGE, Dual-Band TD-SCDMA, and TDD LTE- Class 4 GSM850/900 - Class 1 DCS1800/PCS1900Product DescriptionThe HS8916 is a high-power, high-efficiency Front-End Module for GSM850/900, DCS1800, PCS1900 operation. The FEM supports Class.12 General Packet Radio Service (GPRS), EDGE multi-slot operation, and TD-SCDMA and TDD LTE linear transmission.The module provides 50 ohm impedance at input and output ports, consists of a CMOS Controller, a SP16T RF switch, a power amplifier supporting GSM850/900, DCS1800/PCS1900, TD-SCDMA bands 34/39, and TDD LTE band 39. The module integrated Tx low pass harmonic filtering can achieve best harmonic performance.The HS8916 provides high-power and high-efficiency Pout for GSM850/900, DCS1800, PCS1900 operation mode. In EDGE and TD-SCDMA / TDD LTE linear modes, VRAMP voltage and MIPI-based bias settings optimize PA linearity and efficiency.Absolute Maximum RatingsMIPI RFFE REGISTER MAP (1 OF 2)MIPI RFFE REGISTER MAP (2 OF 2)Electrical Specifications – TX GSM850/900 Band, GSMK ModeElectrical Specifications – TX GSM850/900 Band, EDGE ModeElectrical Specifications – TX DCS1800/1900 Band, GMSK ModeElectrical Specifications – TX DCS1800/1900 Band, EDGE ModeElectrical Specifications – TX TD-SCDMA B39 BandElectrical Specifications – TX TDD LTE B39 BandElectrical Specifications – TX TD-SCDMA B34 BandElectrical Specifications – Ports TRx1 to TRx14 ModePin-Out DiagramT R X 7T R X 6T R X 5G N DT R X 1T R X 2T R X 3T R X 4HS8916 Application CircuitT R X 7T R X 6T R X 5G N DR X 1T R X 2T R X 3T R X 4Package DrawingThe HS8916 is encapsulated in a 5.5×5.3×0.85mm Land Grid Array (LGA) package on a laminate substrate. The HS8916 is RoHS compliant.。
Modbus Master Slave通信模块MVI56E-MCM MCMXT说明书
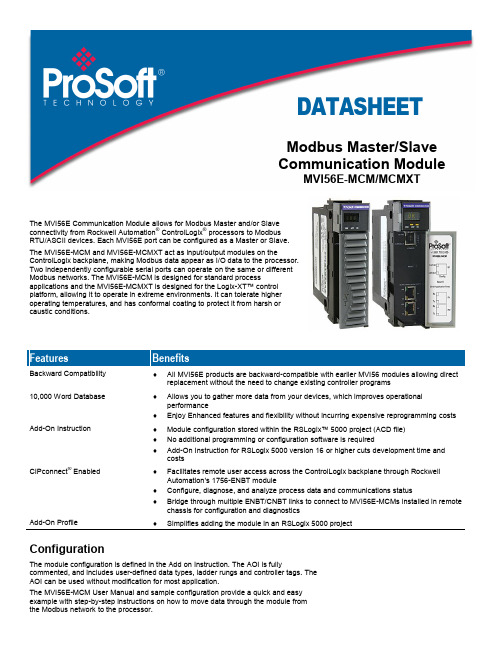
DATASHEETModbus Master/SlaveCommunication ModuleMVI56E-MCM/MCMXTThe MVI56E Communication Module allows for Modbus Master and/or Slaveconnectivity from Rockwell Automation® ControlLogix® processors to ModbusRTU/ASCII devices. Each MVI56E port can be configured as a Master or Slave.The MVI56E-MCM and MVI56E-MCMXT act as input/output modules on theControlLogix backplane, making Modbus data appear as I/O data to the processor.Two independently configurable serial ports can operate on the same or differentModbus networks. The MVI56E-MCM is designed for standard processapplications and the MVI56E-MCMXT is designed for the Logix-XT™ controlplatform, allowing it to operate in extreme environments. It can tolerate higheroperating temperatures, and has conformal coating to protect it from harsh orcaustic conditions.Features BenefitsBackward Compatibility ♦All MVI56E products are backward-compatible with earlier MVI56 modules allowing directreplacement without the need to change existing controller programs10,000 Word Database ♦Allows you to gather more data from your devices, which improves operationalperformance♦Enjoy Enhanced features and flexibility without incurring expensive reprogramming costs Add-On Instruction ♦Module configuration stored within the RSLogix™ 5000 project (ACD file)♦No additional programming or configuration software is required♦Add-On Instruction for RSLogix 5000 version 16 or higher cuts development time andcostsCIPconnect® Enabled ♦Facilitates remote user access across the ControlLogix backplane through RockwellAutomation’s 1756-ENBT module♦Configure, diagnose, and analyze process data and communications status♦Bridge through multiple ENBT/CNBT links to connect to MVI56E-MCMs installed in remotechassis for configuration and diagnosticsAdd-On Profile ♦Simplifies adding the module in an RSLogix 5000 projectConfigurationThe module configuration is defined in the Add on Instruction. The AOI is fullycommented, and includes user-defined data types, ladder rungs and controller tags. TheAOI can be used without modification for most application.The MVI56E-MCM User Manual and sample configuration provide a quick and easyexample with step-by-step instructions on how to move data through the module fromthe Modbus network to the processor.General Specifications∙Backward-compatible with previous MVI56-MCM version∙Single Slot - 1756 ControlLogix® backplane compatible∙10/100 MB Ethernet port for network configuration and diagnostics with Auto Cable Crossover Detection∙User-definable module data memory mapping of up to 10,000 16-bit registers∙4-character, scrolling, alphanumeric LED display of status and diagnostic data in plain English∙ProSoft Discovery Service (PDS) software finds the module on the network and assigns a temporary IP address to facilitate module accessFunctional SpecificationsThe MVI56E-MCM will operate on a Local or Remote rack (For remote rack applications with smaller data packet size please refer to the MVI56E-MCMR product)∙Supports Enron version of Modbus protocol for floating-point data transactions∙PCB includes powerful Modbus network analyzer∙Special functions (command control, event commands, status, and so on) are supported by message transfer (unscheduled) using the MSG instruction∙Error codes, network error counters, and port status data available in user data memorySlave SpecificationsThe MVI56E-MCM module accepts Modbus function code commands of 1, 2, 3, 4, 5, 6, 8, 15, 16, 17, 22, and 23 from an attached Modbus Master unit. A port configured as a Modbus Slave permits a remote Master to interact with all data contained in the module. This data can be derived from other Modbus Slave devices on the network, through a Master port, or from the ControlLogix processor.Master SpecificationsA port configured as a virtual Modbus Master device on the MVI56E-MCM module actively issues Modbus commands to other nodes on the Modbus network. Up to 325 commands are supported on each port. Additionally, the Master ports have an optimized polling characteristic that polls Slaves with communication problems less frequently. The ControlLogix processor ladder logic can issues commands directly from ladder logic or actively select commands from the command list to execute under ladder logic control.ControlLogix™ Modbus IntegrationGeneral Modbus SpecificationsCommunication Parameters Baud Rate: 110 baud to 115.2 kbpsStop Bits: 1 or 2Data Size: 7 or 8 bitsParity: None, Even, OddRTS Timing delays: 0 to 65535 milliseconds Modbus Modes RTU mode (binary) with CRC-16ASCII mode with LRC error checkingFloating Point Data Floating point data movement supported, includingconfigurable support for Enron and DanielimplementationsModbus Function Codes 1: Read Coils Status2: Read Input Status3: Read Holding Registers4: Read Input Registers5: Force (Write) Single Coil6: Preset (Write) Single Register8: Diagnostics15: Force (Write) Multiple Coils16: Preset (Write) Multiple Data Registers17: Report Slave ID22: Mask Write 4x Register23: Read/Write 4x RegistersModbus Master SpecificationsCommand List Up to 325 commands per Master port, each fullyconfigurable for function code, slave address, registerto/from addressing and word/bit count.Optimized Polling Configuration options allow Master ports andcommands to be optimized to poll slaves withcommunication problems less frequently.Command Status/Error Monitoring Command Status or Error codes are generated for each command as it executes, allowing careful monitoring of communication health between the Master and its Slaves.Slave Polling Control Master Port maintains a Slave Status list of all networkSlaves. Polling of each Slave may be disabled andenabled using this list.Modbus Slave SpecificationsFull Memory Access A port configured as a Modbus Slave permits a remoteMaster to read from or write to any of the 10,000registers that make up the user memory database. Multi-source Slave Data Data presented at the Slave port can be derived fromother Modbus Slave devices on a different networkthroug h the module’s Master port or from the processortag database.Node Address 1 to 247 (software selectable)Status Data Slave port error codes, counters and statuses areavailable separately for each port when configured as aSlave® products areHardware SpecificationsGeneralSpecification DescriptionBackplane Current Load 800 mA @ 5 Vdc3 mA @ 24 VdcOperating Temperature 0°C to 60°C (32°F to 140°F) - MVI56E-MCM-25°C to 70°C (-13°F to 158°F) - MVI56E-MCMXT Storage Temperature -40°C to 85°C (-40°F to 185°F)Extreme/Harsh Environment MVI56E-MCMXT comes with conformal coating Shock 30 g operational50 g non-operationalVibration: 5 g from 10 to 150 HzRelative Humidity 5% to 95% (without condensation)LED Indicators Battery Status (ERR)Application Status (APP)Module Status (OK)4-Character, Scrolling, Alpha-Numeric LED Display Shows Module, Version, IP, Port Master/Slave Setting, Port Status, and Error InformationDebug/Configuration Ethernet port (E1 - Config)Ethernet Port 10/100 Base-T, RJ45 Connector, for CAT5 cableLink and Activity LED indicatorsAuto-crossover cable detectionSerial Application ports (P1 & P2)Full hardware handshaking control, providing radio, modem, and multi-drop supportSoftware configurable communication parameters Baud rate: 110 baud to 115.2 kbpsRS-232, 485 and 422Parity: none, odd or evenData bits: 5, 6, 7, or 8Stop bits: 1 or 2RTS on/off delay: 0 to 65535 millisecondsSerial Applications Ports (P1, P2) RJ45 (DB-9M with supplied adapter cable) Configurable RS-232 hardware handshaking500V Optical isolation from backplaneRS-232, RS-422, RS-485 jumper-select, each port RX (Receive) and TX (Transmit) LEDs, each portShipped with Unit RJ45 to DB-9M cables for each serial port5 foot Ethernet Straight-Thru Cable (Gray) Agency Approvals and CertificationsAgencyRoHSATEXCSACECSA CB SafetycULusGOST-RLloyds® offers a full。
5205-MNET-PDPS配置快速向导
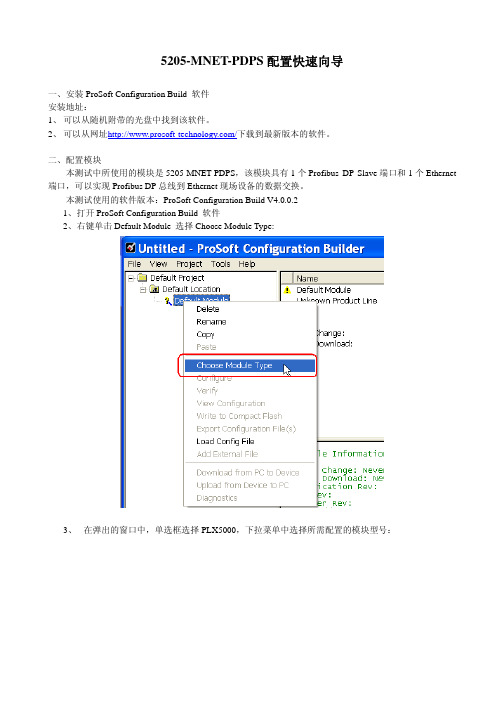
5205-MNET-PDPS配置快速向导一、安装ProSoft Configuration Build 软件安装地址:1、可以从随机附带的光盘中找到该软件。
2、可以从网址/下载到最新版本的软件。
二、配置模块本测试中所使用的模块是5205-MNET-PDPS,该模块具有1个Profibus DP Slave端口和1个Ethernet 端口,可以实现Profibus DP总线到Ethernet现场设备的数据交换。
本测试使用的软件版本:ProSoft Configuration Build V4.0.0.21、打开ProSoft Configuration Build 软件2、右键单击Default Module 选择Choose Module Type:3、在弹出的窗口中,单选框选择PLX5000,下拉菜单中选择所需配置的模块型号:三、配置Profibus DP Slave 端口参数展开5205-MNET-PDPS,然后再展开PDPS,双击Profibus Slave, 即可进入Profibus DP Slave 端口参数配置界面:双击Ethernet Configuration,打开Ethernet端口配置界面,设置该模块Ethernet端口的IP地址:展开MNET Client 0,双击MNet Client 0 Commands, 打开配置界面:点击Add Row, 添加1条命令请求(最多可以添加100条命令),再双击添加的命令行,打开配置界面:1、Enable: Yes, No or Conditional定义命令执行的条件。
2、Internal Address: 网关内部用于通信的地址。
0~4999: 字地址;0~65535: 位地址。
Modbus功能码1, 2 , 5, 15,该参数对应位地址;功能码3, 4, 6, 16,该参数对应字地址。
3、Poll Interval:请求时间间隔。
PROSOFT模块

PROSOFT模块,PROSOFT通讯模块,PROSOFT开关,PROSOFT接近传感器,PROSOFT 隔离开关,PROSOFT按钮,PROSOFT脚踏开关,PROSOFT限位开关上海秋腾贸易有限公司公司特价现货供应美国PROSOFT模块,PROSOFT通讯模块,PROSOFT开关,PROSOFT接近传感器,PROSOFT隔离开关,PROSOFT按钮,PROSOFT 脚踏开关,PROSOFT限位开关,PROSOFT安全开关,PROSOFT微动开关,PROSOFT安全开关PROSOFT微动开关,PROSOFT主控开关,PROSOFT转换开关等等。
公司从1997年在美国设立办事处,一直销售以来收到亚洲企业的一致好评,销售额从1997年的150多万到2007年总销售额达到8亿多元。
公司一直以来求质量第一,价格第一,诚信第一希望各企业单位来函来电洽谈。
以下列举部分型号:MVI94-GSC-E,MVI94-GSC-E,MVI94-GSC-E,MV146-PDPS,MV146-PDPMV1,MV146-PDPS,MV146-PDPMV1,MVI56-MCM,MVI56-DFCM,MVI56-AFC,MVI69-MCM,MVI46-PDPS,MVI46-PDPMV1,MVI56-MCM,MVI46-MCM,MVI56-MCMR,MVI56-MCM,MVI46-MCM,MVI56-MCMR,5304-MBP-PDPM,5304-MBP-PDPM,5304-MBP-PDPM,5204-MNET-PDPM,5204-MNET-PDPM,5204-MNET-PDPM5204-MNET-PDPM,5302-MBP-MCM4,5304-MBP-PDPM,5302-MBP-MCM4,5304-MBP-PDPM,5302-MBP-MCM4,5304-MBP-PDPM,5302-MBP-MCM4,5304-MBP-PDPM,5302-MBP-MCM4,5304-MBP-PDPM,PTQ-PDPMV1,5302-MBP-MCM4,5304-MBP-PDPM,3150-MCM,3150-MCM,3150-MCM,3150-MCM,5305-MBP-PDPS,5305-MBP-PDPS5305-MBP-PDPS,5305-MBP-PDPS,MV194-ADM 双口RS232/422/485,MV194-ADM 双口RS232/422/485,MV194-ADM 双口RS232/422/485,MV194-ADM 双口RS232/422/485,MV194-ADMMVI46-DFNT,MVI46-DFNT,MVI46-DFNT,5102-MBS3-MBM。
如何使用PROSOFT公司的MVI56-MNET卡件

如何使用PROSOFT 公司的MVI56_MNET 模块1 ControlLogix 架构Modbus TCP/IP 通讯模块1.1 模块简介● 单槽模块,和1756背板完全兼容 ● 在处理器和模块之间进行数据交换时,模块充当一个普通的IO 模块● 通过梯形图实现模块和处理器的数据交换(样例程序已经做好,V16版本以上可使用Add‐On 指令。
)● 可插到本地和远程IO 机架● 5000个字的寄存器区供用户使用 ● 作为主站时最多支持100条指令 ● 支持功能码1、2、3、4、5、6、15、16● 作为Client 时最大可连接100个 Server● 使用502端口1.2 工作原理MVI56‐MNET 模块通过ControlLogix 背板直接通信。
整个背板使用该模块的输入和输出数据映像的模块和ControlLogix 处理器之间的数据分页。
数据映像更新频率由预定的扫描由用户定义的模块和模块上的通讯负载率。
典型的更新时间范围从1到10毫秒。
这种数据的双向传输模块将输入数据映像中的数据发送到处理器完成。
输入数据映像中的数据被放置在处理器的控制器标签梯形逻辑。
输入数据映像设置为250字。
被转移到该模块的处理器逻辑数据插入到输出数据映像。
模块的固件程序中提取数据,并将其放置在模块的内部数据库。
输出的数据映像设置为248字。
上图显示了用于移动数据的数据传输方法,在ControlLogix 处理器,MVI56‐MNET 模块和Modbus TCP / IP 网络之间。
在背板模块和处理器之间传输的所有数据是通过输入和输出数据映像。
梯形逻辑,必须写在ControlLogix 处理器控制器标签中的数据接口的输入和输出的数据映像数据。
模块使用的所有数据都存储在其内部的数据库。
这个数据库被定义为一个虚拟的Modbus 数据地址表从0(40001 MODBUS )4999(45000 MODBUS )。
在这个数据库中的数据传输块,或网页,使用的输入和输出数据映像。
PTQ_MCM_Datasheet
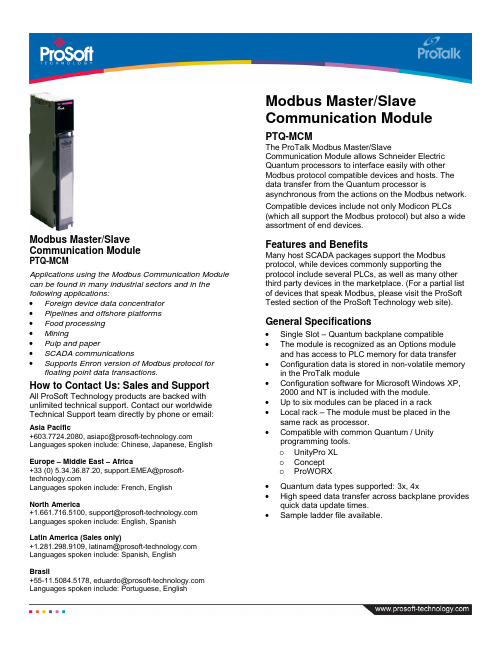
Modbus Master/Slave Communication ModulePTQ-MCMApplications using the Modbus Communication Module can be found in many industrial sectors and in the following applications:• Foreign device data concentrator • Pipelines and offshore platforms • Food processing • Mining• Pulp and paper• SCADA communications• Supports Enron version of Modbus protocol forfloating point data transactions.How to Contact Us: Sales and SupportAll ProSoft Technology products are backed with unlimited technical support. Contact our worldwide Technical Support team directly by phone or email:Asia Pacific+603.7724.2080, asiapc@Languages spoken include: Chinese, Japanese, EnglishEurope – Middle East – Africa+33 (0) 5.34.36.87.20, support.EMEA@Languages spoken include: French, EnglishNorth America+1.661.716.5100, support@ Languages spoken include: English, SpanishLatin America (Sales only)+1.281.298.9109, latinam@ Languages spoken include: Spanish, EnglishBrasil+55-11.5084.5178, eduardo@ Languages spoken include: Portuguese, EnglishModbus Master/Slave Communication ModulePTQ-MCMThe ProTalk Modbus Master/SlaveCommunication Module allows Schneider Electric Quantum processors to interface easily with other Modbus protocol compatible devices and hosts. The data transfer from the Quantum processor isasynchronous from the actions on the Modbus network. Compatible devices include not only Modicon PLCs (which all support the Modbus protocol) but also a wide assortment of end devices.Features and BenefitsMany host SCADA packages support the Modbus protocol, while devices commonly supporting the protocol include several PLCs, as well as many other third party devices in the marketplace. (For a partial list of devices that speak Modbus, please visit the ProSoft Tested section of the ProSoft Technology web site).General Specifications• Single Slot – Quantum backplane compatible • The module is recognized as an Options module and has access to PLC memory for data transfer • Configuration data is stored in non-volatile memory in the ProTalk module• Configuration software for Microsoft Windows XP, 2000 and NT is included with the module. • Up to six modules can be placed in a rack • Local rack – The module must be placed in the same rack as processor.•Compatible with common Quantum / Unity programming tools. o UnityPro XL o Concept o ProWORX• Quantum data types supported: 3x, 4x• High speed data transfer across backplane provides quick data update times. •Sample ladder file available.Hardware SpecificationsSpecification DescriptionBackplaneCurrent Load800 mA @ 5 VOperatingTemperature0 to 60°C (32 to 140°F)StorageTemperature–40 to 85°C (–40 to 185°F)RelativeHumidity5 to 95% (non-condensing)LED Indicators Module StatusBackplane Transfer StatusSerial Port Activity LEDSerial Activity and Error LED StatusConfiguration Serial Port (PRT1) DB-9M PC Compatible RS-232 onlyNo hardware handshakingApplication Serial Ports (PRT2, PRT3)DB-9M PC CompatibleRS-232/422/485 jumper selectableRS-422/485 screw termination included RS-232 handshaking configurable500V Optical isolation from backplaneFunctional SpecificationsSome of the general specifications include:•Support for the storage and transfer of up to 5000 registers to/from the Quantum processor's data files •Module memory usage that is completely user definable•Two ports to emulate any combination of Modbus master or slave device• Configurable parameters include:Parameter DescriptionProtocol RTU or ASCIIBaud Rate 110 to 115,200Parity None, Odd and EvenData Bits 5 to 8Stop Bits 1 or 2RTS On and Off Timing 0 to 65535 milliseconds Minimum ResponseDelay0 to 65535 millisecondsUse of CTS Modem Line Yes or NoFloating-Point SupportSlave SpecificationsThe PTQ-MCM module accepts Modbus function code commands of 1, 2, 3, 4, 5, 6, 8, 15, 16, 17, 22 and 23 from an attached Modbus Master unit. A port configured as a Modbus slave permits a remote master to interact with all data contained in the module. This data can be derived from other Modbus slave devices on the network, through a master port, or from the Quantum processor.Master SpecificationsA port configured as a virtual Modbus Master device on the PTQ-MCM module actively issues Modbus commands to other nodes on the Modbus network. One hundred (100) commands are supported on each port. Additionally, the master ports have an optimized polling characteristic that polls slaves with communication problems less frequently. The Quantum processor can be programmed to control the activity on the port by actively selecting commands from the command list to execute or issuing commands directly from the ladder logic.Additional ProductsProSoft Technology offers a full complement of hardware and software solutions for a wide variety of industrial communication platforms.Visit our web site at for a complete list of products.Ordering InformationTo order this product, please use the following:PTQ-MCM Modbus Master/SlaveCommunication ModuleTo place an order, please contact your local ProSoft Technology distributor. For a list of ProSoft distributors near you, go to Distributors:Place your order by email or fax to:North American / Latin American / Asia Pacificorders@,fax to +1 661.716.5101Europeeurope@,fax to +33 (0) 5.61.78.40.52Copyright © ProSoft Technology, Inc. 2000 - 2007. All Rights Reserved.January 30, 2007。
Prosoft公司5205-DNPSNET-配置
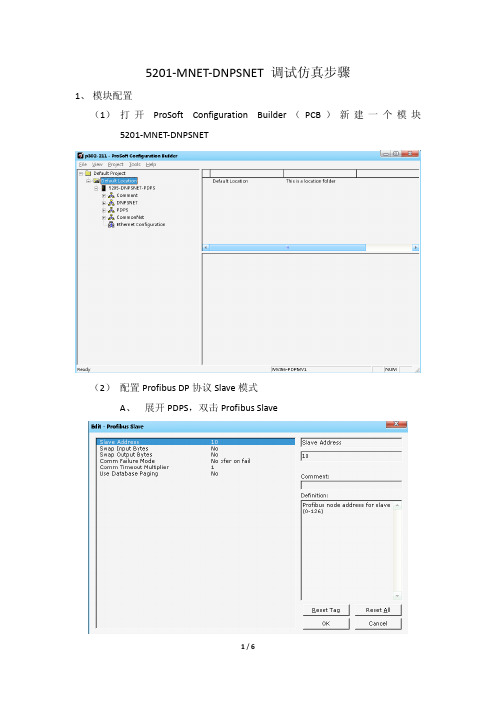
5201-MNET-DNPSNET 调试仿真步骤1、模块配置(1)打开ProSoft Configuration Builder(PCB)新建一个模块5201-MNET-DNPSNET(2)配置Profibus DP协议Slave模式A、展开PDPS,双击Profibus Slave此配置页面我们可以配置该模块在Profibus DP网络中的地址,从站地址范围为1-125;该地址为唯一地址,不可与网络中其他设备冲突。
本文档将该模块DP网络中的地址配置为“10”。
(3)配置Profibus主站,本文档以西门子PLC连接ProLinx 5205-DNPSNET-PDPS进行说明,SIEMENS CPU选用S7-315 2DP;(4)在Step 7里导入ProLinx PDPS GS*文件(5)在Profibus DP网络中挂上导入的ProLinx设备,地址配置为ProSoft Configuration Builder软件中配置的地址:“10”(6)添加IO设备,展开右侧ProSoft Profibus Slave,假如我们要从ProLinx读取24个字的数据,往ProLinx从站写36个子的数据;则我们可以配置1个16 Words input和1个8 Words input;也可配置3个8 Word input,对于数量和顺序没有要求,只要总量达到要求即可,配置方法将展开后的输入输出模块拖动到左侧的表格中;其他ProSoft DP主站配置方法也基本是同样的。
详见下图,配置完毕将该配置文件下载到处理器即可。
至此,Profibus主站配置完毕了,这里需要注意一点的是ProSoft PDPS模块的数据区输入寄存器区位寄存器0—122,输出寄存器区为200—322,即上表中西门子地址的IB256—IB303读取的是模块的0---23寄存器;西门子的QB256—QB3277的数据将会写到模块的300---335寄存器。
MCM_User_Manual_中文

请阅读以下注意事项
成功的应用这个模块需要对 Allen-Bradley PLC/SLC 硬件知识和现场 应用方式有充分的了解。因此,对于负责完成应用的工作人员,了解 应用需求并确保人员和设备不处于不安全或不适当的工作环境是非常 重要的。
© ProSoft Technology, Inc. 1995, 1996, 1997, 1998 Modbus 是 Schneider Automation 的注册商标
修订 2 中的新特性
修订 2 中的新特性
MCM 产品的修订 2 版本是对这个产品的第一次主要升级。产品集合了许多新特性,其中一些源自我们目前用户的建 议,还有一些是我们在考察了我们的用户在如何使用这个产品上总结出来的。其中一些新特性是:
1.4.3 向模块写数据................................................................................................... 10
1.4.4 主站端口驱动................................................................................................... 10
在没有得到 ProSoft Technology 许可的情况下,禁止任何对本手册内容 整体或部分性的复制。
本手册内容如有更改,恕不通知。ProSoft Technology, Inc.并不承担这 个义务。并会随时改进和/或更改此文档或产品。这些更改会阶段性的 进行,以更改技术的不准确和印刷排版错误。
1.4.1 基本概念.......................................................................................................... 9
网关配置说明
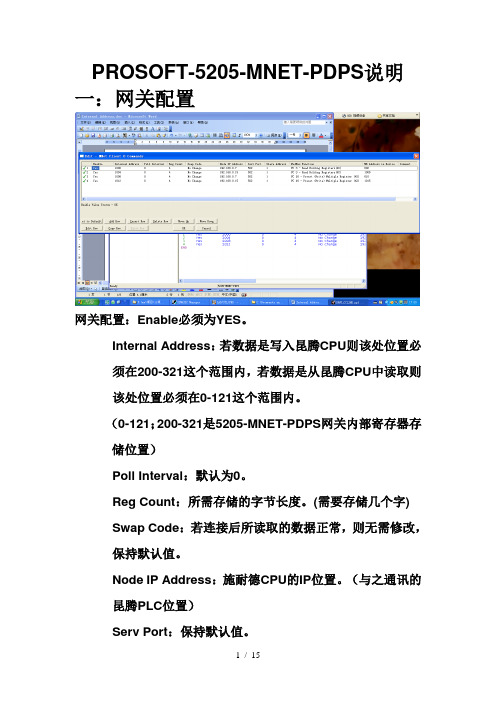
PROSOFT-5205-MNET-PDPS说明一:网关配置网关配置:Enable必须为YES。
Internal Address:若数据是写入昆腾CPU则该处位置必须在200-321这个范围内,若数据是从昆腾CPU中读取则该处位置必须在0-121这个范围内。
(0-121;200-321是5205-MNET-PDPS网关内部寄存器存储位置)Poll Interval:默认为0。
Reg Count:所需存储的字节长度。
(需要存储几个字)Swap Code:若连接后所读取的数据正常,则无需修改,保持默认值。
Node IP Address:施耐德CPU的IP位置。
(与之通讯的昆腾PLC位置)Serv Port:保持默认值。
Slave Address:保持默认值。
ModBus Function:网关对于施耐德cpu的数据处理,有读写两种方式,具体看ModBus Function的介绍。
MB Address in Device:施耐德写给网关的起始位置和网关写给施耐德的起始位置。
(此处需要注意的是,该处写的位置比施耐德中实际的使用位置低一个字)Slave Address:西门子DP从站位置,该处为5,所以在S7中配置该网关后,该网关的DP位置必须相应的也为5。
余下几项为默认值即可。
在西门子硬件配置中安装pdps-gsd文件,然后在DP上配置网关的硬件,如图所示,5号站即为网关。
二:S7的配置下图为在S7中配置该网关的截图:具体步骤为先安装该网关的GSD文件(该文件在厂家提供的光碟中有,文件夹名为PDPS_GSD)如上图所示在S7的硬件配置中选中选项菜单,在其下拉菜单中选中安装GSD文件,选中后会出现如下画面在该画面中选中浏览,在您的电脑中或厂家提供的碟片中去寻找所需要的文件,找到后的效果如下图如图中所示选中蓝色标注的文件夹,按下确定键,所需的GSD文件就会出现在安装GSD文件的窗口中了,此时按下全选按钮(对于本次的网关由于只需要pgwa05a5.gsd这个文件,所以也可以只选中该文件)选中后安装键将显示可操作了,按下安装键,所选中的GSD文件将自动安装到S7的硬件配置文件中,具体位置如下图右边配置文件栏中展开的项:此时在右侧PROFIBUS DP下additional field devices(第三方软件)gateway里找到prolinx profibus slave我们可以在S7的硬件配置中将该prolinx profibus slave拖到Profibus DP总线上。
MVI56-MCM

/downloads.cfm
产品供货
其它的 MVI56 系列的产品还有:
MVI56-MBP: Modbus Plus 通讯模块 MVI56-ADM: 应用程序开发模块 MVI56-MNET: Modbus TCP/IP 以太网通讯模块
外形
ControlLogix 外形-单槽 连接:
• 2 – RJ45 连接头支持 RS-232, RS-422, 或 RS-485 接口 • 1 – RJ45 RS-232 设置工具连接器
ControlLogix 接口
通过简单的梯形图实现模块运作 使用 RSLogix 5000 软件可以完全实现对模块的设置和监视 通过 I/O 实现 ControlLogix 背板连接 所有模块相关数据都包含在一个处理器数据对象中,这便于配置,监视和连接模块参数. 模块的配置和通讯配置数据通过一个预先在处理器定义的用户数据类型,传送到 MVI56-
设置连接器:
RJ45 RS-232 连接器 (随包装附带 RJ45 到 DB9 的电
缆)
指示灯状态 o 电池状态 o 模块状态 o 端口接收/发送活动(每个端口一个) o 背板活动状态
内置 Intel 80386 处理器 模块和放置在 ControlLogix 槽架内的任何位置
文档
MVI56-MCM ControlLogix 平台
Modbus 通讯模块
产品描述
MVI56-MCM (“Modbus 通讯模块”) 使 Allen-Bradley ControlLogix 处理器轻松的和其它 Modbus 协 议兼容设备连接起来。兼容的设备不仅仅包括 Modicon PLC's (所有型号都支持 Modbus 协议),同 时还包括很大一类的终端设备。
MVI56-MNET模块使用教程
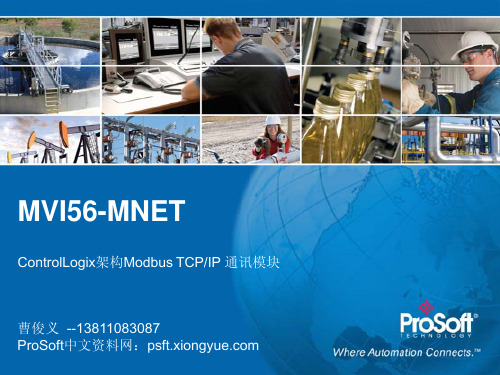
特别说明:当模块作为Server从站时,不用做任何操作,只需配置IP地址。
MVI56-MNET模块配置
第五步:下载PCB配置文件 5.1 确认模块的Ok状态灯为绿色常亮、BP橙色闪烁 5.2 将配置电缆连接到配置端口,DB9一头连接到电脑的串口 5.3 右键点击MVI56-MNET,选择Download from PC to Device下载配置 文件。
MVI56-MNET
ControlLogix架构Modbus TCP/IP 通讯模块
曹俊义 --13811083087 ProSoft中文资料网:
MVI56-MNET 技术特性
产品特性
单槽模块,和1756背板完全兼容 在处理器和模块之间进行数据交换时,模块充当一个普通的IO模块 通过梯形图实现模块和处理器的数据交换(样例程序已经做好,V16 版本以上可使用Add‐On指令。) 可插到本地和远程IO机架 5000个字的寄存器区供用户使用 作为主站时最多支持100条指令 支持功能码1、2、3、4、5、6、15、16 作为Client时最大可连接100个 Server 使用502端口
MVI56-MNET 工作原理
工作原理
MVI56-MNET 模块配置
模块配置与诊断
模块配置 1、RsLogix5000组态 第一步:新建IO模块,在IO Configuration组态1756-Module
MVI56-MNET 模块配置
第二步:导入样例程序(*.L5X),在梯形图编辑窗口找一空行,右键选择 import导入L5X文件(MVI56MNET_AOI.L5X)
MVI56-MNET模块配置
第三步:配置MNET为Client模式,一般认为若配置Client Command参数 则认为端口为Client,若不配置指令则认为是Server 3.1 配置Client端口,展开MNETபைடு நூலகம்Client0,选择里面的MNET Client0双击 进入配置界面
Prosoft MVI56-MCM ControlLogix 平台 Modbus 通讯模块 说明书

2.9.2.1 功能 5.................................................................................................... 16 2.9.2.2 功能 6 和 16.......................................................................................... 16 2.9.2.3 功能 15.................................................................................................. 17 MVI56-MCM模块和ControlLogix处理器之间的数据流.......................................... 18 2.9.3 从站驱动................................................................................................... 18 2.9.4 主站驱动模式........................................................................................... 20 2.9.4.1 主站命令列表....................................................................................... 21 3 修改模块设置........................................................................................................... 23 3.1 上电................................................................................................................... 23 3.2 运行中更改参数............................................................................................... 23 3.3 装配模块........................................................................................................... 23 3.4 模块数据对象 (MCMModuleDef)................................................................... 29 3.4.1 设置对象................................................................................................... 30 3.4.1.1 数据传输参数 (MCMModule)............................................................. 31
MGate MB3660 Series MCC Tool for Linux 发布说明书

Utility for MGate MB3660 Series (MCC Tool for Linux) ReleaseNotesSupported Operating SystemsNotesChangesApplicable ProductsBugs FixedN/AN/AEnhancementsLinux Kernel 2.6.x, Linux Kernel 3.x, Linux Kernel 4.xMGate MB3180, MGate MB3280, MGate MB3480, MGate MB3170, MGate MB3170I, MGate MB3270,MGate MB3270I, MGate MB3170-T, MGate MB3170I-T, MGate MB3270-T, MGate MB3270I-T, MGate MB3170-M-SC, MGate MB3170-M-ST, MGate MB3170-S-SC, MGate MB3170I-M-SC, MGate MB3170I-S-SC, MGate MB3170-M-SC-T, MGate MB3170-M-ST-T, MGate MB3170-S-SC-T, MGate MB3170I-M-SC-T, MGate MB3170I-S-SC-T, MGate MB3660-8-J-2AC, MGate MB3660I-16-2AC,MGate MB3660-16-J-2AC, MGate MB3660-8-2AC, MGate MB3660-8-2DC, MGate MB3660I-8-2AC,MGate MB3660-16-2AC, MGate MB3660-16-2DC, NPort 5110A, NPort 5110A-T, NPort 5130A, NPort 5130A-T, NPort 5150A, NPort 5150A-T, NPort 5210A, NPort 5210A-T, NPort 5230A, NPort 5230A-T,NPort 5250A, NPort 5250A-T, NPort 5150AI-M12, NPort 5150AI-M12-CT, NPort 5150AI-M12-T, NPort 5150AI-M12-CT-T, NPort 5250AI-M12, NPort 5250AI-M12-CT, NPort 5250AI-M12-T, NPort 5250AI-M12-CT-T, NPort 5450AI-M12, NPort 5450AI-M12-CT, NPort 5450AI-M12-T, NPort 5450AI-M12-CT-T,NPort 6150, NPort 6150-T, NPort 6250, NPort 6250-M-SC, NPort 6250-S-SC, NPort 6250-T, NPort 6250-M-SC-T, NPort 6250-S-SC-T, NPort 6450, NPort 6450-T, NPort 6610-8, NPort 6610-8-48V,NPort 6610-16, NPort 6610-16-48V, NPort 6610-32, NPort 6610-32-48V, NPort 6650-8, NPort 6650-8-T, NPort 6650-8-HV-T, NPort 6650-8-48V, NPort 6650-16, NPort 6650-16-48V, NPort 6650-16-T,NPort 6650-16-HV-T, NPort 6650-32, NPort 6650-32-48V, NPort 6650-32-HV-T, ioLogik E1210,ioLogik E1210-T, ioLogik E1211, ioLogik E1211-T, ioLogik E1212, ioLogik E1212-T, ioLogik E1213,ioLogik E1213-T, ioLogik E1214, ioLogik E1214-T, ioLogik E1240, ioLogik E1240-T, ioLogik E1241,ioLogik E1241-T, ioLogik E1242, ioLogik E1242-T, ioLogik E1260, ioLogik E1260-T, ioLogik E1262,ioLogik E1262-T, ioThinx 4510, ioThinx 4510-T• Support for plugins.• Support for ioThinx 4510.• Support for new error code -16.• Support for new commands: (1) mcc_tool -install "plugin" (2) mcc_tool -mlNew FeaturesN/AN/ASupported Operating SystemsNotesChangesApplicable ProductsBugs FixedN/AN/AEnhancementsLinux Kernel 2.6.x, Linux Kernel 3.x, Linux Kernel 4.xNPort 6250-T, NPort 6250-M-SC-T, NPort 6250-S-SC-T, NPort 6450, NPort 6450-T, NPort 6610-8,NPort 6610-8-48V, NPort 6610-16, NPort 6610-16-48V, NPort 6610-32, NPort 6610-32-48V, NPort 6650-8, NPort 6650-8-T, NPort 6650-8-HV-T, NPort 6650-8-48V, NPort 6650-16, NPort 6650-16-48V,NPort 6650-16-T, NPort 6650-16-HV-T, NPort 6650-32, NPort 6650-32-48V, NPort 6650-32-HV-T,ioLogik E1210, ioLogik E1210-T, ioLogik E1211, ioLogik E1211-T, ioLogik E1212, ioLogik E1212-T,ioLogik E1213, ioLogik E1213-T, ioLogik E1214, ioLogik E1214-T, ioLogik E1240, ioLogik E1240-T,ioLogik E1241, ioLogik E1241-T, ioLogik E1242, ioLogik E1242-T, ioLogik E1260, ioLogik E1260-T,ioLogik E1262, ioLogik E1262-T, ioThinx 4510, ioThinx 4510-T, MGate MB3180, MGate MB3280,MGate MB3480, MGate MB3170, MGate MB3170I, MGate MB3270, MGate MB3270I, MGate MB3170-T, MGate MB3170I-T, MGate MB3270-T, MGate MB3270I-T, MGate MB3170-M-SC, MGate MB3170-M-ST, MGate MB3170-S-SC, MGate MB3170I-M-SC, MGate MB3170I-S-SC, MGate MB3170-M-SC-T, MGate MB3170-M-ST-T, MGate MB3170-S-SC-T, MGate MB3170I-M-SC-T, MGate MB3170I-S-SC-T, MGate MB3660-8-J-2AC, MGate MB3660I-16-2AC, MGate MB3660-16-J-2AC,MGate MB3660-8-2AC, MGate MB3660-8-2DC, MGate MB3660I-8-2AC, MGate MB3660-16-2AC,MGate MB3660-16-2DC, NPort 5110A, NPort 5110A-T, NPort 5130A, NPort 5130A-T, NPort 5150A,NPort 5150A-T, NPort 5210A, NPort 5210A-T, NPort 5230A, NPort 5230A-T, NPort 5250A, NPort 5250A-T, NPort 5150AI-M12, NPort 5150AI-M12-CT, NPort 5150AI-M12-T, NPort 5150AI-M12-CT-T,NPort 5250AI-M12, NPort 5250AI-M12-CT, NPort 5250AI-M12-T, NPort 5250AI-M12-CT-T, NPort 5450AI-M12, NPort 5450AI-M12-CT, NPort 5450AI-M12-T, NPort 5450AI-M12-CT-T, NPort 6150,NPort 6150-T, NPort 6250, NPort 6250-M-SC, NPort 6250-S-SC• First release.New FeaturesN/AN/A。
NCP1422MNR2G,NCP1422MNR2G,NCP1422MNR2,NCP1422MNR2,NCP1422EVB,NCP1422LEDGEVB, 规格书,Datasheet 资料

NCP1422800 mA Sync−Rect PFMStep−Up DC−DC Converter with True−Cutoff andRing−KillerNCP1422 is a monolithic micropower high−frequency step−up switching converter IC specially designed for battery−operated hand−held electronic products up to 800 mA loading. It integrates Sync−Rect to improve efficiency and to eliminate the external Schottky Diode. High switching frequency (up to 1.2 MHz) allows for a low profile, small−sized inductor and output capacitor to be used. When the device is disabled, the internal conduction path from LX or BA T to OUT is fully blocked and the OUT pin is isolated from the battery. This True−Cutoff function reduces the shutdown currentto typically only 50 nA. Ring−Killer is also integrated to eliminate the high−frequency ringing in discontinuous conduction mode. In addition to the above, Low−Battery Detector, Logic−Controlled Shutdown, Cycle−by−Cycle Current Limit and Thermal Shutdown provide value−added features for various battery−operated applications. With all these functions on, the quiescent supply current is typically only 8.5 m A. This device is available in the compact and low profile DFN−10 package.Features•Pb−Free Package is Available*•High Efficiency:94% for 3.3 V Output at 200 mA from 2.5 V Input88% for 3.3 V Output at 500 mA from 2.5 V Input •High Switching Frequency, up to 1.2 MHz (not hitting current limit)•Output Current up to 800 mA at V IN = 2.5 V and V OUT = 3.3 V •True−Cutoff Function Reduces Device Shutdown Current to typically 50 nA•Anti−Ringing Ring−Killer for Discontinuous Conduction Mode •High Accuracy Reference Output, 1.20 V $1.5% @ 25°C, can Supply 2.5 mA Loading Current when V OUT > 3.3 V•Low Quiescent Current of 8.5 m A•Integrated Low−Battery Detector•Open Drain Low−Battery Detector Output•1.0 V Startup at No Load Guaranteed•Output V oltage from 1.5 V to 5.0 V Adjustable•1.5 A Cycle−by−Cycle Current Limit•Multi−Function Logic−Controlled Shutdown Pin•On Chip Thermal Shutdown with HysteresisTypical Applications•Personal Digital Assistants (PDA)•Handheld Digital Audio Products•Camcorders and Digital Still Cameras•Hand−held Instruments•Conversion from one to two Alkaline, NiMH, NiCd Battery Cells to 3.0−5.0 V or one Lithium−ion cells to 5.0 V•White LED Flash for Digital CamerasDevice Package Shipping†ORDERING INFORMATIONNCP1422MNR2DFN−103000 T ape & Reel†For information on tape and reel specifications, including part orientation and tape sizes, please refer to our T ape and Reel Packaging Specifications Brochure, BRD8011/D.*For additional information on our Pb−Free strategy and soldering details, please download theON Semiconductor Soldering and MountingT echniques Reference Manual, SOLDERRM/D. NCP1422MNR2G DFN−10(Pb−Free)3000 T ape & ReelFigure 1. Detailed Block DiagramPIN FUNCTION DESCRIPTIONSPin Symbol Description1FB Output Voltage Feedback Input.2LBI/EN Low−Battery Detector Input and IC Enable. With this pin pulled down below 0.5 V, the device is disabled and enters the shutdown mode.3LBO Open−Drain Low−Battery Detector Output. Output is LOW when V LBI is < 1.20 V. LBO is high impedance in shutdown mode.4NC No Connect Pin5REF 1.20 V Reference Voltage Output, bypass with 300 nF capacitor. If this pin is loaded, bypass with 1.0 m F capacitor; this pin can be loaded up to 2.5 mA @ V OUT = 3.3 V.6BAT Battery input connection for internal ring−killer.7GND Ground.8LX N−Channel and P−Channel Power MOSFET drain connection.9NC No Connect Pin10OUT Power Output. OUT also provides bootstrap power to the device.MAXIMUM RATINGS (T A = 25°C unless otherwise noted.)Rating Symbol Value Unit Power Supply (Pin 10)V OUT−0.3, 5.5V Input/Output Pins (Pin 1−3, Pin 5−8)V IO−0.3, 5.5V Thermal CharacteristicsDFN−10 Plastic PackageThermal Resistance Junction−to−Air (Note 5)P DR JA182468.5mW_C/WOperating Junction T emperature Range T J−40 to +150_C Operating Ambient T emperature Range T A−40 to +85_C Storage T emperature Range T stg−55 to +150_C Maximum ratings are those values beyond which device damage can occur. Maximum ratings applied to the device are individual stress limit values (not normal operating conditions) and are not valid simultaneously. If these limits are exceeded, device functional operation is not implied, damage may occur and reliability may be affected.1.This device contains ESD protection and exceeds the following tests:Human Body Model (HBM) ±2.0 kV per JEDEC standard: JESD22−A114. *Except OUT pin, which is 1k V.Machine Model (MM) ±200 V per JEDEC standard: JESD22−A115. *Except OUT pin, which is 100 V.2.The maximum package power dissipation limit must not be exceeded.P D+T J(max)*T AR q JAtchup Current Maximum Rating: ±150 mA per JEDEC standard: JESD78.4.Moisture Sensitivity Level: MSL 1 per IPC/JEDEC standard: J−STD−020A.5.Measured on approximately 1x1 inch sq. of 1 oz. Copper.ELECTRICAL CHARACTERISTICS (V OUT = 3.3 V, T A = 25°C for typical value, −40°C v T A v 85°C for min/max values unless otherwise noted.)Characteristic Symbol Min Typ Max Unit Operating Voltage V IN 1.0− 5.0V Output Voltage Range V OUT 1.5− 5.0VV REF_NL 1.183 1.200 1.217V Reference Voltage(V OUT= 3.3 V, I LOAD = 0m A, C REF= 200 nF, T A = 25°C)V REF_NL 1.174− 1.220V Reference Voltage(V OUT= 3.3 V, I LOAD = 0m A, C REF= 200 nF, T A = −40°C to 85°C)Reference Voltage T emperature Coefficient TC VREF−0.03−mV/°C Reference Voltage Load CurrentI REF− 2.5−mA(V OUT= 3.3 V, V REF = V REF_NL"1.5% C REF= 1.0 m F) (Note 6)V REF_LOAD−0.05 1.0mV Reference Voltage Load Regulation(V OUT= 3.3 V, I LOAD= 0 to 100 m A, C REF= 1.0 m F)Reference Voltage Line RegulationV REF_LINE−0.05 1.0mV/V (V OUT from 1.5 V to 5.0 V, C REF= 1.0 m F)FB Input Threshold (I LOAD= 0 mA, T A = 25°C)V FB 1.192 1.200 1.208V FB Input Threshold (I LOAD= 0 mA, T A = −40°C to 85°C)V FB 1.184− 1.210V LBI Input Threshold (I LOAD= 0 mA, T A = 25_C)V LBI 1.182 1.200 1.218V LBI Input Threshold (I LOAD= 0 mA, T A= −40_C to 85_C)V LBI 1.162 1.230V Internal N−FET ON−Resistance R DS(ON)_N−0.3−Internal P−FET ON−Resistance R DS(ON)_P−0.3−LX Switch Current Limit (N−FET) (Note 8)I LIM− 1.5−AI QBAT− 1.3 3.0m A Operating Current into BAT(V BAT= 1.8 V, V FB= 1.8 V, V LX= 1.8 V, V OUT= 3.3 V)Operating Current into OUT (V FB= 1.4 V, V OUT= 3.3 V)I Q−8.514m A LX Switch MAX. ON−Time (V FB = 1.0 V, V OUT= 3.3 V, T A = 25_C)t ON0.460.72 1.15m s LX Switch MIN. OFF−Time (V FB = 1.0 V, V OUT= 3.3 V, T A = 25_C)t OFF−0.120.22m s FB Input Current I FB− 1.050nAI BAT_SD−50−nA True−Cutof f Current into BAT(LBI/EN = GND, V OUT= 0 V, V IN= 3.3 V, LX = 3.3 V)BAT−to−LX Resistance (V FB= 1.4 V, V OUT= 3.3 V) (Note 8)R BAT_LX−100−LBI/EN Input Current I LBI− 1.550nA LBO Low Output Voltage (V LBI= 0 V, I SINK = 1.0 mA)V LBO_L−−0.2V Soft−Start Time (V IN= 2.5 V, V OUT= 5.0 V, C REF= 200 nF) (Note 7)T SS− 1.520ms EN Pin Shutdown Threshold (T A = 25°C)V SHDN0.350.50.67V Thermal Shutdown T emperature (Note 8)T SHDN−−145°C Thermal Shutdown Hysteresis (Note 8)T SDHYS−30−°C6.Loading capability increases with V OUT.7.Design guarantee, value depends on voltage at V OUT.8.Values are design guaranteed.AMBIENT TEMPERATURE, T A /°CS W I T C H O N R E S I S T A N C E , R D S (O N )/W20406080100AMBIENT TEMPERATURE, T A /°CR E F E R E N C E V O L T A G E , V R E F /V0.50.60.70.80.91.0−40−20020406080100OUTPUT LOADING CURRENT , I LOAD /mAM I N I M U M S T A R T U P B A T T E R Y V O L T A G E , V B A T T /VFigure 3. Reference Voltage vs. Voltage at OUT PinFigure 4. Reference Voltage vs. TemperatureFigure 5. Switch ON Resistance vs. TemperatureFigure 6. L X Switch Max. ON Time vs. TemperatureFigure 7. Minimum Startup Battery Voltage vs.Loading CurrentAMBIENT TEMPERATURE, T A /°C L X S W I T C H M A X I M U M , O N T I M E , t O N /m SR E F E R E N C E V O L T A G E , V R E F /V1.1801.1901.2101.220VOLTAGE AT OUT PIN, V OUT /VR E F E R E N C E V O L T A G E , V R E F /V1.20010Figure 9. Output Voltage Change vs. Load CurrenFigure 11. Low Battery DetectFigure 12. No Load Operating Current vs. InputVoltage at OUT PinO U T P U T V O L T A G E C H A N G E /%−551011001000OUTPUT LOADING CURRENT , I LOAD /mAO U T P U T V O L T A G E C H A N G E /%R I P P L E V O L T A G E , V R I P P L E /m V p −pUpper Trace: Input Voltage Waveform, 1.0 V/Division Lower Trace: Output Voltage Waveform, 2.0 V/DivisionFigure 13. Startup Transient Response1.52.02.53.03.55.0INPUT VOLTAGE AT OUT PIN, V OUT /VN O L O A D O P E R A T I N G C U R R E N T , I B A T T /m A4.04.5Upper Trace: Voltage at LBI Pin, 1.0 V/Division Lower Trace: Voltage at LBO Pin, 1.0 V/DivisionV IN = 2.5 V V OUT = 5.0 V I LOAD = 10 mA10(V IN = 2.5 V, V OUT = 3.3 V, I LOAD = 50 mA; L = 5.6 m H)Upper Trace: Output Voltage Ripple, 20 mV/Division Lower Trace: Voltage at Lx pin, 1.0 V/Division Figure 14. Discontinuous Conduction ModeSwitching Waveform (V IN = 2.5 V, V OUT = 3.3 V, I LOAD = 500 mA; L = 5.6 m H)Upper Trace: Output Voltage Ripple, 20 mV/Division Lower Trace: Voltage at LX pin, 1.0 V/DivisionFigure 15. Continuous Conduction ModeSwitching WaveformFigure 16. Line Transient Response for V OUT = 3.3 V Figure 17. Line Transient Response For V OUT = 5.0 V(V IN = 1.5 V to 2.5 V; L = 5.6 m H, C OUT = 22m F, I LOAD = 100 mA)Upper Trace: Output Voltage Ripple, 100 mV/Division Lower Trace: Battery Voltage, V IN, 1.0 V/Division (V IN = 1.5 V to 2.5 V; L = 5.6 m H, C OUT = 22m F, I LOAD = 100 mA)Upper Trace: Output Voltage Ripple, 100 mV/Division Lower Trace: Battery Voltage, V IN, 1.0 V/DivisionFigure 18. Load Transient Response For V IN = 2.5 V Figure 19. Load Transient Response For V IN = 3.0 V(V OUT = 5.0 V, I LOAD = 100 mA to 800 mA; L = 5.6 m H, C OUT = 22 m F)Upper Trace: Output Voltage Ripple, 500 mV/Division Lower Trace: Load Current, I LOAD , 500 mA/Division(V OUT = 3.3 V, I LOAD = 100 mA to 800 mA; L = 5.6 m H, C OUT = 22 m F)Upper Trace: Output Voltage Ripple, 200 mV/Division Lower Trace: Load Current, I LOAD, 500 mA/DivisionOUTPUT LOADING CURRENT , I OUT /mAE F F I C I E N C Y /%OUTPUT LOADING CURRENT , I OUT /mAE F F I C I E N C Y /%Figure 20. Efficiency vs. Load CurrentFigure 21. Efficiency vs. Load CurrentFigure 22. Efficiency vs. Load CurrentOUTPUT LOADING CURRENT , I OUT /mA E F F I C I E N C Y /%DETAILED OPERATION DESCRIPTIONNCP1422 is a monolithic micropower high−frequency step−up voltage switching converter IC specially designed for battery operated hand−held electronic products up to 800 mA loading. It integrates a Synchronous Rectifier to improve efficiency as well as to eliminate the external Schottky diode. High switching frequency (up to 1.2 MHz)allows for a low profile inductor and output capacitor to be used. Low−Battery Detector, Logic−Controlled Shutdown,and Cycle−by−Cycle Current Limit provide value−added features for various battery−operated applications. With all these functions ON, the quiescent supply current is typically only 8.5 m A. This device is available in a compact DFN−10 package.PFM Regulation SchemeFrom the simplified functional diagram (Figure 1), the output voltage is divided down and fed back to pin 1 (FB).This voltage goes to the non−inverting input of the PFM comparator whereas the comparator’s inverting input is connected to the internal voltage reference, REF. A switching cycle is initiated by the falling edge of the comparator, at the moment the main switch (M1) is turned ON. After the maximum ON−time (typically 0.72 m S)elapses or the current limit is reached, M1 is turned OFF and the synchronous switch (M2) is turned ON. The M1OFF time is not less than the minimum OFF−time (typically 0.12 m S), which ensures complete energytransfer from the inductor to the output capacitor. If the regulator is operating in Continuous Conduction Mode (CCM), M2 is turned OFF just before M1 is supposed to be ON again. If the regulator is operating in Discontinuous Conduction Mode (DCM), which means the coil current will decrease to zero before the new cycle starts, M1 is turned OFF as the coil current is almost reaching zero. The comparator (ZLC) with fixed offset is dedicated to sense the voltage drop across M2 as it is conducting; when the voltage drop is below the offset, the ZLC comparator output goes HIGH and M2 is turned OFF. Negative feedback of closed−loop operation regulates voltage at pin1 (FB) equal to the internal reference voltage (1.20 V). Synchronous RectificationThe Synchronous Rectifier is used to replace the Schottky Diode to reduce the conduction loss contributed by the forward voltage of the Schottky Diode. The Synchronous Rectifier is normally realized by powerFET with gate control circuitry that incorporates relatively complicated timing concerns.As the main switch (M1) is being turned OFF and the synchronous switch M2 is just turned ON with M1 not being completely turned OFF, current is shunt from the output bulk capacitor through M2 and M1 to ground. This power loss lowers overall efficiency and possibly damages the switching FETs. As a general practice, a certain amount of dead time is introduced to make sure M1 is completely turned OFF before M2 is turned ON.The previously mentioned situation occurs when the regulator is operating in CCM, M2 is turned OFF, M1 is just turned ON, and M2 is not completely turned OFF. A dead time is also needed to make sure M2 is completely turned OFF before M1 is turned ON.As coil current is dropped to zero when the regulator is operating in DCM, M2 should be OFF. If this does not occur, the reverse current flows from the output bulk capacitor through M2 and the inductor to the battery input, causing damage to the battery. The ZLC comparator comes with fixed offset voltage to switch M2 OFF before any reverse current builds up. However, if M2 is switched OFF too early, large residue coil current flows through the body diode of M2 and increases conduction loss. Therefore, determination of the offset voltage is essential for optimum performance. With the implementation of the synchronous rectification scheme, efficiency can be as high as 94% with this device.Cycle−by−Cycle Current LimitIn Figure 1, a SENSEFET is used to sample the coil current as M1 is ON. With that sample current flowing through a sense resistor, a sense−voltage is developed. The threshold detector (I LIM) detects whether the sense−voltage is higher than the preset level. If the sense voltage is higher than the present level, the detector output notifies the Control Logic to switch OFF M1, and M1 can only be switched ON when the next cycle starts after the minimum OFF−time (typically 0.12 m S). With proper sizing of the SENSEFET and sense resistor, the peak coil current limit is typically set at 1.5 A.Voltage ReferenceThe voltage at REF is typically set at 1.20 V and can output up to 2.5 mA with load regulation ±2% at V OUT equal to 3.3 V. If V OUT is increased, the REF load capability can also be increased. A bypass capacitor of 200 nF is required for proper operation when REF is not loaded. If REF is loaded, a 1.0 m F capacitor at the REF pin is needed.True−CutoffThe NCP1422 has a True−Cutoff function controlled by the multi−function pin LBI/EN (pin 2). Internal circuitry can isolate the current through the body diode of switch M2 to load. Thus, it can eliminate leakage current from the battery to load in shutdown mode and significantly reduce battery current consumption during shutdown. The shutdown function is controlled by the voltage at pin 2 (LBI/EN). When pin 2 is pulled to lower than 0.3 V, the controller enters shutdown mode. In shutdown mode, when switches M1 and M2 are both switched OFF, the internal reference voltage of the controller is disabled and the controller typically consumes only 50 nA of current. If the pin 2 voltage is raised to higher than 0.5 V (for example, by a resistor connected to V IN), the IC is enabled again, and the internal circuit typically consumes 8.5 m A of current from the OUT pin during normal operation.Low−Battery DetectionA comparator with 30 mV hysteresis is applied to perform the low−battery detection function. When pin 2 (LBI/EN) is at a voltage (defined by a resistor divider from the battery voltage) lower than the internal reference voltage of 1.20 V, the comparator output turns on a 50 W low side switch. It pulls down the voltage at pin 3 (LBO) which has hundreds of k W of pull−high resistance. If the pin 2 voltage is higher than 1.20 V + 30 mV, the comparator output turns off the 50 W low side switch. When this occurs, pin 3 becomes high impedance and its voltage is pulled high again.APPLICATIONS INFORMATIONOutput Voltage SettingA typical application circuit is shown in Figure 23. The output voltage of the converter is determined by the external feedback network comprised of R1 and R2. The relationship is given by:V OUT+1.20Vǒ1)R1R2Ǔwhere R1and R2 are the upper and lower feedback resistors, respectively.Low Battery Detect Level SettingThe Low Battery Detect V oltage of the converter is determined by the external divider network that is comprised of R3 and R4. The relationship is given by:V LB+1.20Vǒ1)R3Ǔwhere R3and R4 are the upper and lower divider resistors respectively.Inductor SelectionThe NCP1422 is tested to produce optimum performance with a 5.6 m H inductor at V IN = 2.5 V and V OUT = 3.3 V, supplying an output current up to 800 mA. For other input/output requirements, inductance in the range 3 m H to 10m H can be used according to end application specifications. Selecting an inductor is a compromise between output current capability, inductor saturation limit, and tolerable output voltage ripple. Low inductance values can supply higher output current but also increase the ripple at output and reduce efficiency. On the other hand, high inductance values can improve output ripple and efficiency; however, it is also limited to the output current capability at the same time.Another parameter of the inductor is its DC resistance. This resistance can introduce unwanted power loss and reduce overall efficiency. The basic rule is to select an inductor with the lowest DC resistance within the board space limitation of the end application. In order to help with the inductor selection, reference charts are shown in Figures 24 and 25.Capacitors SelectionIn all switching mode boost converter applications, both the input and output terminals see impulsive voltage/current waveforms. The currents flowing into and out of the capacitors multiply with the Equivalent Series Resistance (ESR) of the capacitor to produce ripple voltage at the terminals. During the Syn−Rect switch−off cycle, the charges stored in the output capacitor are used to sustain the output load current. Load current at this period and the ESR combine and reflect as ripple at the output terminals. For all cases, the lower the capacitor ESR, the lower the ripple voltage at output. As a general guideline, low ESR capacitors should be used. Ceramic capacitors have the lowest ESR, but low ESR tantalum capacitors can also be used as an alternative.PCB Layout RecommendationsGood PCB layout plays an important role in switching mode power conversion. Careful PCB layout can help to minimize ground bounce, EMI noise, and unwanted feedback that can affect the performance of the converter. Hints suggested below can be used as a guideline in most situations.GroundingA star−ground connection should be used to connect the output power return ground, the input power return ground, and the device power ground together at one point. All high−current paths must be as short as possible and thick enough to allow current to flow through and produce insignificant voltage drop along the path. The feedback signal path must be separated from the main current path and sense directly at the anode of the output capacitor. Components PlacementPower components (i.e., input capacitor, inductor and output capacitor) must be placed as close together as possible. All connecting traces must be short, direct, and thick. High current flowing and switching paths must be kept away from the feedback (FB, pin 1) terminal to avoid unwanted injection of noise into the feedback path. Feedback NetworkFeedback of the output voltage must be a separate trace detached from the power path. The external feedback network must be placed very close to the feedback (FB, pin 1) pin and sense the output voltage directly at the anode of the output capacitor.TYPICAL APPLICATION CIRCUITShutdown Open DrainInput Low Battery Open DrainOutputV OUT = 3.3 V800 mA Figure 23. Typical Application Schematic for 2 Alkaline Cells Supply*OptionalGENERAL DESIGN PROCEDURESSwitching mode converter design is considered a complicated process. Selecting the right inductor and capacitor values can allow the converter to provide optimum performance. The following is a simple method based on the basic first−order equations to estimate the inductor and capacitor values for NCP1422 to operate in Continuous Conduction Mode (CCM). The set component values can be used as a starting point to fine tune the application circuit performance. Detailed bench testing is still necessary to get the best performance out of the circuit. Design Parameters:V IN = 1.8 V to 3.0 V, Typical 2.4 VV OUT = 3.3 VI OUT = 500 mAV LB = 2.0 VV OUT−RIPPLE= 40 mV p−p at I OUT = 500 mA Calculate the feedback network:Select R2 = 200 kR1+R2ǒV OUTV REF*1ǓR1+200kǒ3.3V1.20V*1Ǔ+350kCalculate the Low Battery Detect divider:V LB = 2.0 VSelect R4 = 330 kR3+R4ǒV LBV REF*1ǓR3+300kǒ2.0V1.20V *1Ǔ+220kDetermine the Steady State Duty Ratio, D, for typicalV IN. The operation is optimized around this point:V OUTV IN+11*DD+1*V INV OUT+1*2.4V3.3V+0.273Determine the average inductor current, I LA VG, atmaximum I OUT:I LAVG+I OUT1*D+500mA1*0.273+688mADetermine the peak inductor ripple current, I RIPPLE−P,and calculate the inductor value:Assume I RIPPLE−P is 20% of I LA VG. The inductance of thepower inductor can be calculated as follows:L+V IN t ON2I RIPPLE*P+2.4V0.75m S2(137.6mA)+6.5m HA standard value of 6.5 m H is selected for initial trial.Determine the output voltage ripple, V OUT−RIPPLE,andcalculate the output capacitor value:V OUT−RIPPLE= 40 mV P−P at I OUT = 500 mAC OUT uI OUT t ONV OUT*RIPPLE*I OUT ESR COUTwhere t ON = 0.75 m S and ESR COUT = 0.05 ,C OUT u500mA0.75m S45mV*500mA0.05W+18.75m FFrom the previous calculations, you need at least 18.75m F in order to achieve the specified ripple level at the conditions stated. Practically, a capacitor that is one level larger is used to accommodate factors not taken into account in the calculations. Therefore, a capacitor value of 22 m F is selected. The NCP1422 is internally compensated for most applications, but in case additional compensationis required, the capacitor C4 can be used as external compensation adjustment to improve system dynamics.In order to provide an easy way for customers to select external parts for NCP1422 in different input voltage and output current conditions, values of inductance and capacitance are suggested in Figures 24, 25 and 26.024681012Figure 24. Suggested Inductance of VOUT = 3.3 V Figure 25. Suggested Inductance of V OUT = 5.0 VFigure 26. Suggested Capacitance for Output CapacitorINPUT VOLTAGE (V)I N D U C T O R V A L U E (m H )INPUT VOLTAGE (V)OUTPUT CURRENT (mA)C A P A C I T O R V A L U E (m F )4035302520151050100200300400500600700800253350100CAPACITOR ESR (m W )Table 1. Suggestions for Passive ComponentsOutput CurrentInductorsCapacitors 800 mA Sumida CR43, CR54,CDRH6D28 seriesPanasonic ECJ series Kemet TL494 series 250 mASumida CR32 seriesPanasonic ECJ series Kemet TL494 seriesPACKAGE DIMENSIONSDFN10, 3 x 3mm, 0.5mm PitchCASE 485C−01ISSUE ADIMENSIONS: MILLIMETERS*For additional information on our Pb−Free strategy and soldering details, please download the ON Semiconductor Soldering and Mounting T echniques Reference Manual, SOLDERRM/D.SENSEFET is a trademark of Semiconductor Components Industries, LLC.ON Semiconductor and are registered trademarks of Semiconductor Components Industries, LLC (SCILLC). SCILLC reserves the right to make changes without further notice to any products herein. SCILLC makes no warranty, representation or guarantee regarding the suitability of its products for any particular purpose, nor does SCILLC assume any liability arising out of the application or use of any product or circuit, and specifically disclaims any and all liability, including without limitation special, consequential or incidental damages. “Typical” parameters which may be provided in SCILLC data sheets and/or specifications can and do vary in different applications and actual performance may vary over time. All operating parameters, including “Typicals” must be validated for each customer application by customer’s technical experts. SCILLC does not convey any license under its patent rights nor the rights of others. SCILLC products are not designed, intended, or authorized for use as components in systems intended for surgical implant into the body, or other applications intended to support or sustain life, or for any other application in which the failure of the SCILLC product could create a situation where personal injury or death may occur. Should Buyer purchase or use SCILLC products for any such unintended or unauthorized application, Buyer shall indemnify and hold SCILLC and its officers, employees, subsidiaries, affiliates, and distributors harmless against all claims, costs, damages, and expenses, and reasonable attorney fees arising out of, directly or indirectly, any claim of personal injury or death associated with such unintended or unauthorized use, even if such claim alleges that SCILLC was negligent regarding the design or manufacture of the part.SCILLC is an Equal Opportunity/Affirmative Action Employer. This literature is subject to all applicable copyright laws and is not for resale in any manner. PUBLICATION ORDERING INFORMATION。
ProSoft Technology MVI56(E)-MNET添加指令安装指南说明书
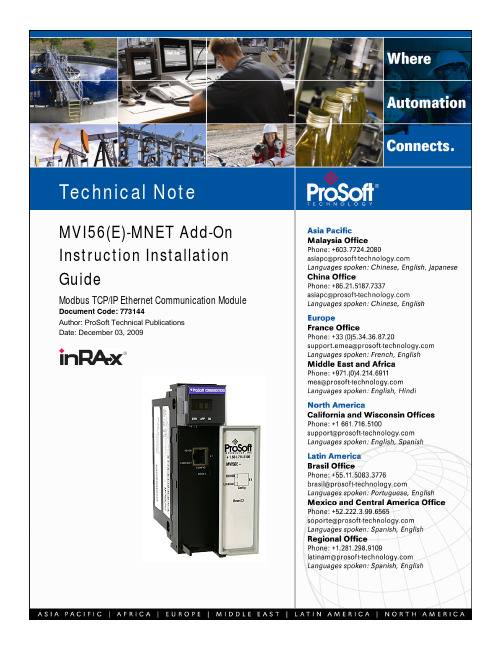
MVI56(E)-MNET Add-On Instruction Installation GuideModbus TCP/IP Ethernet Communication Module Document Code: 773144Author: ProSoft Technical PublicationsDate: December 03, 2009Document InformationAuthor ProSoft Technical PublicationsDescription Modbus TCP/IP Ethernet Communication ModuleDate December 03, 2009Revision 2.04.00Product Name MVI56(E)-MNETDocument Code773144ProSoft Technology5201 Truxtun Ave., 3rd FloorBakersfield, CA 93309+1 (661) 716-5100+1 (661) 716-5101 (Fax)Copyright © ProSoft Technology, Inc. 2009. All Rights Reserved.December 03, 2009ProSoft Technology ® ProLinx ®, inRAx ®, ProTalk®, and RadioLinx ® are Registered Trademarks of ProSoft Technology, Inc. All other brand or product names are or may be trademarks of, and are used to identify products and services of, their respective owners.How to contact us: Sales & SupportAll ProSoft Technology® products are backed with unlimited technical support. Contact our worldwide Technical Support team directly by phone or email:Asia Pacific+603.7724.2080,***********************************Languages spoken include: Chinese, Japanese, EnglishEurope – Middle East – Africa+33(0)5.34.36.87.20,***********************************Languages spoken include: French, English*****************************,fax to +33 (0) 5.61.78.40.52North America+1.661.716.5100,******************************Languages spoken include: English, Spanish*****************************,fax to +1 661.716.5101Latin America (Sales only)+1.281.298.9109,******************************Languages spoken include: Spanish, EnglishBrasil+55-11.5084.5178,******************************Languages spoken include: Portuguese, EnglishContentsDocument Information (2)ADD MODBUS TCP/IP ETHERNET COMMUNICATION TO CONTROLLOGIX WITH AN ADD-ON INSTRUCTION FOR RSLOGIX® 5000 VERSION 16 (4)Introduction (4)Instructions (5)Benefits (10)Add Modbus TCP/IP Ethernet Communication to ControlLogix with an Add-On Instruction for RSLogix® 5000 Version 16In This ChapterIntroduction (4)Instructions (5)Benefits (10)IntroductionBeginning with version 16 of RSLogix™ 5000 software, Rockwell Array Automation added an extremely helpful feature to make it easier that everto set up third party modules, custom code, or proprietary code. Theycalled this new feature an "Add-On Instruction" (AOI). This AOI featureallows third party vendors, panel builders, and system integrators to createladder logic code that can be protected for safety or security reasons andcan be locked to ensure that the code remains unchanged.ProSoft Technology®’s inRAx® Modbus TCP/IP Ethernet CommunicationModule for ControlLogix®, the MVI56(E)-MNET, is provided with an Add-On Instruction to allow easy integration of the module into new or existingRSLogix 5000 Version 16 and newer projects.ProSoft Technology® has enhanced the MVI56(E)-MNET module’s Add-On Instruction in a way that will significantly simplify installation.Now users can integrate the module into a new or existing project byimporting a single ladder logic import file, as opposed to importing multipleUser Defined Data Types and ladder logic rungs, one-by-one.The entire ladder logic required by the MVI56(E)-MNET is encapsulated inone, single Add-On Instruction. And, when the ladder logic .L5X file isimported, it automatically creates all the required User-Defined Data Types,Controller Tags, and the Add-On Instruction logic, all while adding thepreconfigured AOI instruction to the ladder rung.This new way of importing an AOI as a completed ladder rung enables quicker and easier integration of theMVI56(E)-MNET with fewer chances for human typographical errors and ladder coding or setup errors.Instructions1 Open the F ILE menu, and then choose N EW…2 Select your ControlLogix controller model.3 Select R EVISION 16.4 Enter a name for your controller, such as "My_Controller".5 Select your ControlLogix chassis type.6 Select S LOT 0for the controller.7 Add the MVI56(E)-MNET module to the project.In the C ONTROLLER O RGANIZATION window, select I/O C ONFIGURATION and click the right mouse button to open a shortcut menu. On the shortcut menu, choose N EW M ODULE...This action opens the S ELECT M ODULE dialog box.8 Select the 1756-M ODULE (G ENERIC 1756M ODULE)from the list and click OK.This action opens the N EW M ODULEdialog box.9 In the N EW M ODULE dialog box, enter the following values.Parameter ValueN AME Enter a module identification string. Example: Modbus TCP/IPEthernet.D ESCRIPTION Enter a description for the module. Example: Modbus TCP/IPEthernet Communication ModuleC OMM F ORMAT SelectD ATA-INT.S LOT Enter the slot number in the rack where the MVI56(E)-MNETmodule is located.I NPUT A SSEMBLY I NSTANCE 1I NPUT S IZE250O UTPUT A SSEMBLY I NSTANCE 2O UTPUT S IZE248C ONFIGURATION A SSEMBLY I NSTANCE 4C ONFIGURATION S IZE0Important: You must select the C OMM F ORMAT as D ATA -INT in the dialog box, otherwise the module will not communicate over the backplane of the ControlLogix rack.10 Click OK to continue.11 Edit the Module Properties. Select the R EQUESTED P ACKET I NTERVA l value for scanning the I/O on the module.This value represents the minimum frequency at which the module will handle scheduled events. This value should not be set to less than 1 millisecond. The default value is 5 milliseconds. Values between 1 and 10 milliseconds should work with most applications.12 Save the module.Click OK to close the dialog box. Notice that the module now appears in the C ONTROLLER O RGANIZATION window.13 In the C ONTROLLER O RGANIZATION window, expand the T ASKS folder and subfolder until you reach theM AIN P ROGRAM folder.14 In the M AIN P ROGRAM folder, double-click to open the M AIN R OUTINE ladder.15 Select an empty rung in the new routine, and then click the right mouse button to open a shortcut menu. On theshortcut menu, choose I MPORT R UNG…16 Navigate to the location on your PC where you saved the Add-On Instruction (for example, "My Documents" or"Desktop"). Select the MVI56(E)M ODBUS TCP/IP E THERNET_A DD O N_R UNG_<V ERSION #>.L5X fileThis action opens the I MPORT C ONFIGURATION dialog box, showing the controller tags that will be created.17 If you are using the module in a different slot (or remote rack), select the correct connection input and outputvariables that define the path to the module. If your module is located in Slot 1 of the local rack, this step is not required.18 Click OK to confirm the import. RSLogix will indicate that the import is in progress:When the import is completed, the new rung with the Add-On Instruction will be visible as shown in the following illustration.The procedure has also imported new User Defined Data Types, data objects and the Add-On instruction for your project.19 Save the application and then download the sample ladder logic into the processor.BenefitsThis process for importing the MVI56(E)-MNET Add-On Instruction into the RSLogix ladder logic file has replaced the practice of importing User Defined Data Types and multiple rungs of ladder in multiple ladder files.This enhancement allows you to easily integrate the module into a new or existing RSLogix project without manually copying over each file. Doing so practically eliminates human typographical errors. Additionally, errors that do occur are significantly easier to correct.。
MCM教程

3、PC机通过EtherNet/IP连
接到控制器
4、支持CIP连接
MVI56E-MCM模块诊断
第三步:选择连接类型,可选择EtherNet或者1756-ENBT,若选择
Ethernet则需要将以太网线连接到模块的以太网端口,若选择1756-ENBT
则需要将网线连接到1756-ENBT上,通过CIP方式连接。
* 选择Ethernet方式,点击Browse Device会连接到PDS软件。
* 从站站部分设置
SlaveID:作为从站时的Modbus地址
BitinOffset:开关量输入地址偏移(1x)
WordinOffset:模拟量输入地址偏移(3x)
OutOffset:开关量输出地址偏移(0x)
HoldOffset:保持寄存器地址偏移(4x)
设置获取报文的端口以及显示格式。
----------------------- Page 18-----------------------
MVI56E-MCM模块诊断
* 选择对应序列号的MVI56E-MCM右键
* 可分配临时IP地址,查看设备信息
* 进行网页诊断
* 进入PCB诊断界面
----------------------- Page 14-----------------------
MVI56E-MCM模块诊断
*集成网页诊断,脱离了串口超级终端的配置方法
*LCD滚动显示模块状态、端口状态
----------------------- Page 3-----------------------
第二步:打开PCB软件,新建一个MVI56E-MCM模块,右键选择诊断出现
6223N-SRD Module Datasheet说明书

6223N-SRDWi-Fi Single-band 1X1 + Bluetooth 4.2 Combo Module DatasheetOffice: 6 Floor, Building U6, Junxiang U8 Park,Hangcheng Avenue, Bao'an District,Shenzhen City, CHINAFactory: No.8, Litong Road, Liuyang Economic & TechnicalDevelopment Zone, Changsha, Hunan, CHINATEL: +86-755-2955-8186Website: Customer Approval :CompanyTitleSignatureDateFn-Link6223N-SRD Revision HistoryVersion Date Revision Content Draft Approvedversion fcNew1.0 2020/11/9CONTENTS1 Overview (1)1.1 Introduction (1)1.2 Features (1)1.3 General Specification (2)1.4 Recommended Operating Rating (2)2 General Specification (3)2.1 Wi-Fi RF Specifications (3)2.2 BT RF Specifications (3)3 Pin Assignments (5)3.1 Pin Outline (5)3.2 Pin Definition (5)4 Dimensions (7)4.1 Module Picture (7)4.2 Marking Description (7)4.3 Module Physical Dimensions (8)4.4 Layout Reference (9)6 Host Interface Timing Diagram (10)6.1 SDIO Pin Description (10)6.2 SDIO Default Mode Timing Diagram (11)6.3 SDIO Power-on sequence (11)6.4 UART Interface Characteristics (12)6.5 UART Interface Power-on Sequence (12)7 Reference Design (12)8 Ordering Information (14)9 The Key Material List (14)10 Environmental Requirements (15)10.1 Recommended Reflow Profile (15)10.2 Patch Wi-Fi/BT modules installed before the notice (15)11 Package (17)11.1 Reel (17)11.2 Packaging Detail (17)1 Overview1.1 Introduction6223N-SRD is a highly integrated and excellent performance Wireless LAN (WLAN) and BT. It provides SDIO interface for Wi-Fi to connect with host processor and high speed UART interface for BT. High-speed wireless connection up to 150 Mbps and Bluetooth can support BT2.1+EDR/BT3.0 and BT4.2. It can be easily manufactured on SMT process.This WLAN Module design is based on Realtek RTL8723DS-CG QFN484.4X4.4mm(Realtek).It combines a MAC, a 1T1R capable baseband, and RF in a single chip. It is designed to provide excellent performance with low power Consumption and enhance the advantages of robust system and cost-effective.6223N-SRD integrates whole Wi-Fi/BT function blocks into a chip, such asSDIO/UART, MAC, BB, AFE, RFE, PA, EEPROM and LDO/SWR, except fewer passive components remained on PCB.This compact module is a total solution for a combination of Wi-Fi + BT technologies. The module is specifically developed for Smart phones and Portable devices.1.2 Features●Operate at ISM frequency bands (2.4GHz)●CMOS MAC, Baseband PHY, and RF in a single chip for 802.11b/g/n compatibleWLAN●Wi-Fi 1 transmitter and 1 receiver allow data rates supporting up to 150 Mbpsdownstream and 150 Mbps upstream PHY rates●SDIO for Wi-Fi and UART for Bluetooth●Fully Qualified for Bluetooth 2.1+EDR specification including both 2Mbps and 3Mbpsmodulation mode●Fully qualified for Bluetooth 3.0●Fully qualified for Bluetooth 4.2 Dual mode●Full_speed Bluetooth operation with Piconet and Scatternet supportBlock Diagram:1.3 General SpecificationModel Name 6223N-SRDProduct Description Support Wi-Fi/BT functionalitiesDimension L x W x T: 23 x 21 x 4.8 (typical) mmBT Interface Support UARTWi-Fi Interface Support SDIO 2.0Operating temperature 0°C to 70°CStorage temperature -40°~125°1.4 Recommended Operating RatingUnitMax.Typ.Min.Operating Temperature 0 25 70 deg.CV VBAT 3.03.63.3VDDIO 1.7 1.8 or 3.3 3.6 V6223N-SRD2 General Specification2.1 Wi-Fi RF SpecificationsFeature DescriptionWLAN Standard IEEE 802.11b/g/n, Wi-Fi compliantFrequency Range 2412MHz-2462MHzChannels 2.4GHz:CH1~CH11Output Power 802.11b /11Mbps:17dBm ± 1.5dB@EVM<=-10dB 802.11g /54Mbps:14dBm ± 1.5dB@EVM<=-25dB 802.11n/MCS7@HT20:13dBm ± 1.5dB@EVM<=-28dB 802.11n/MCS7@HT40:13dBm ± 1.5dB@EVM<=-28dBSpectrum Mask IEEE compliantFreq. Tolerance ±15 ppmReceive Sensitivity(11b) @8% PER802.11b/11Mbps: PER@≤-76 Receive Sensitivity(11g) @10% PER802.11g/54Mbps: PER@≤-65 Receive Sensitivity(11n,20MHz) @10% PER802.11n/MCS7@HT20: PER@≤-64 Receive Sensitivity(11n,40MHz) @10% PER802.11n/MCS7@HT40: PER@≤-612.2 Bluetooth SpecificationFeature DescriptionGeneral SpecificationBluetooth Standard Bluetooth V4.2 of 1, 2 and 3 Mbps.Host Interface UARTFrequency Band 2402 MHz ~ 2480 MHzNumber of Channels 79 channelsModulation GFSK,π/4-DQPSK and 8DPSKRF SpecificationMin. Typical. Max. Output Power (Class 1.5) 6dBmOutput Power (Class 2) 2dBmSensitivity @ BER=0.1%for GFSK (1Mbps)-86dBm Sensitivity @ BER=0.01%for π/4-DQPSK (2Mbps)-86dBm Sensitivity @ BER=0.01%for 8DPSK (3Mbps)-80dBmMaximum Input Level GFSK (1Mbps): -20dBmπ/4-DQPSK (2Mbps) : -20dBm 8DPSK (3Mbps) : -20dBmSensitive @PER=30.8% FOR BLE-90dBm3 Pin Assignments3.1 Pin Outline<TOP>3.2 Pin DefinitionNO. Name Type Description Voltage1 UART-CTS UART-CTS VDDIO2 UART-RTS UART-RTS VDDIOconnections3 GND Groundconnections4 GND Groundconnections5 GND Groundoutput VDDIO6 UART-OUT O UART7 UART-IN I UARTinput VDDIO3.3V 3.3V8 VBAT P Supply9 NC Floating (Don’t connected toground)10 VDDIO PI/O Voltage supply input 1.8V to3.3V 1.8V ~ 3.3V11 GND Ground connections12 CHIP_EN I chip enable pin, default pull high 3.3V 13 WL_WAKE_HOSTI/O WLAN device wake-up host1.8V ~ 3.3V 14 SD_D2 I/O SDIO Data line 2 1.8V ~ 3.3V 15 SD_D3 I/O SDIO Data line 3 1.8V ~ 3.3V 16 SD_CMD I/O SDIO Command Input 1.8V ~ 3.3V 17 SD_CLK I SDIO Clock Input 1.8V ~ 3.3V 18 SD_D0 I/O SDIO Data line 0 1.8V ~ 3.3V 19 SD_D1 I/O SDIO Data line 11.8V ~ 3.3V20 GNDGround connections 21 BT_HOST_WAKE BT host wake-up device VDDIO 22BT_WAKE_HOSTBT device wake-up host VDDIO23 GND Ground connections 24 GND Ground connections 25 GNDGround connections26 WIFI_DIS#Pull high: ON , Pull low: OFFExternal pull low can disable WL 27 BT_DIS#Pull high: ON , Pull low: OFFExternal pull low can disable BTP:POWER I:INPUT O:OUTPUT6223N-SRD 4 Dimensions4.1 Module PictureL x W : 23 x 21 (+0.3/-0.1) mmH: 4.8 (±0.2) mmWeight 1.65g4.2 Marking Description4.3 Module Physical Dimensions (unit: mm )(TOP)4.4 Layout Reference(unit: mm )TOP6 Host Interface Timing Diagram6.1 SDIO Pin DescriptionThe module supports SDIO version 2.0 for all 1.8V 4-bit UHSI speeds: SDR12(25 Mbps), and SDR25(50Mbps) in addition to the 3.3V default speed(25MHz) and high speed (50 MHz). It has the ability to stop the SDIO clock and map the interrupt signal into a GPIO pin. This ‘out-of-band’ interrupt signal notifies the host when the WLAN device wants to turn on the SDIO interface. The ability to force the control of the gated clocks from within the WLAN chip is also provided.SDIO Pin DescriptionSD 4-Bit ModeDATA0 Data Line 0DATA1 Data Line 1 or InterruptDATA2 Data Line 2 or Read WaitDATA3 Data Line 3CLK ClockLineCMD Command6.2 SDIO Default Mode Timing DiagramClockInputOutputSDIO Interface Timing ParametersSDIO Interface Timing6.3 SDIO Power-on sequenceSymbolMinTypicalMaxUnitT 33ramp0.2 - No Limit msT off 250 500 1000 ms T 33ramp 0.2 0.5 2.5 ms T 12ramp 0.1 0.5 1.5 ms T POR 2 2 8 ms T non_rdy 12 10 ms6.4 UART Interface CharacteristicsThe RTL8723DS UART interface is a standard 4-wire interface with RX,TX,CTS and RTS. The interface supports the Bluetooth 2.0 UART HCI H4 and H5 specifications. The default baud rate is 115.2K baud. In order to support high and low speed baud rate,the RTL8723DS provides multiple UART clocks.6.5 UART Interface Power-on Sequence7 Reference DesignNote:1. BAT_EN could not use for module power off, please switch the 3.3V power for module on/off.2.please keep the antenna on no metal area.8 Ordering Information Part No. DescriptionFG6223NSRD-00 RTL8723DS,b/g/n,wifi1T1R,21*23.21mm,SDIO+UART,with metal antenna.9 The Key Material ListMain Shieldingcover6223NSRD V1.0 Shielding cover no insulation layer14.8X11mm-full height of 1.4 copper, no positioning pin(信太)Alternative Shieldingcover6223NSRD V1.0 Shielding cover no insulation layer14.8X11mm-full height of 1.4 copper, no positioning pin (精力通)Main Crystal3225 24MHZ CL=12pF, ±10ppm (东晶) Alternative Crystal 3225 24MHZ CL=12pF, ±10ppm (泰晶) Alternative Crystal 3225 24MHZ CL=12pF, ±10ppm (晶威特) Alternative Crystal 3225 24MHz CL=12pF ±10ppm (鸿星) Alternative Crystal 3225 24MHz CL=12pF ±10ppm (TXC) Main TVS 0201 5V 0.05pF 15KV TVS (Murata) Alternative TVS 0201 5V 0.05pF 15KV TVS (Sunlord) Alternative TVS 0201 5V 0.05pF 15KV TVS (维安)MainMainChipsetRTL8723DS-CG QFN48 4.4X4.4mm (Realtek)Main antenna 6223N-SRD metal antenna.Main PCB6223N-SRD-V1.0,FR4,green,21X23X0.8mm (翔宇) Alternative PCB 6223N-SRD-V1.0,FR4,green,21X23X0.8mm(广东科翔)Alternative PCB 6223N-SRD-V1.0,FR4,green,21X23X0.8mm(顺络)Alternative PCB 6223N-SRD-V1.0,FR4,green,21X23X0.8mm(深联)10 Environmental Requirements10.1 Recommended Reflow ProfileReferred to IPC/JEDEC standard.Peak Temperature : <250°CNumber of Times : ≤2 times10.2 Patch Wi-Fi/BT modules installed before the noticeWi-Fi/BT module installed note:1.Please press 1 : 1 and then expand outward proportion to 0.7 mm, 0.12 mm thickness When open a stencil.2.Take and use the WIFI/BT module, please insure the electrostatic protective measures.3.Reflow soldering temperature should be according to the customer the main size of the products, such as the temperature set at 250 + 5 ℃for the MID motherboard. About the module packaging, storage and use of matters needing attention are as follows:1.The module of the reel and storage life of vacuum packing: 1). Shelf life: 8 months, storage environment conditions: temperature in: < 40 ℃, relative humidity: < 90% r.h.2.The module vacuum packing once opened, time limit of the assembly:6223N-SRD Card:1) check the humidity display value should be less than 30% (in blue), such as: 30% ~ 40% (pink), or greater than 40% (red) the module have been moisture absorption.2.) factory environmental temperature humidity control: ≦ -30 ℃, ≦ 60% r.h..3). Once opened, the workshop the preservation of life for 168 hours.3. Once opened, such as when not used up within 168 hours:1). The module must be again to remove the module moisture absorption.2). The baking temperature: 125 ℃, 8 hours.3). After baking, put the right amount of desiccant to seal packages.6223N-SRDFN-LINK TECHNOLOGY LIMITEDProprietary & Confidential1711 Package11.1 ReelTBD11.2 Packaging DetailTBDFCC StatementFCC standards: FCC CFR Title 47 Part 15 Subpart C Section 15.247Integral antenna with antenna gain 2dBiThis device complies with part 15 of the FCC Rules. Operation is subject to the following two conditions: (1)This device may not cause harmful interference, and (2) this device must accept any interference received, including interference that may cause undesired operation.Any Changes or modifications not expressly approved by the party responsible for compliance could void the user's authority to operate the equipment.Note: This equipment has been tested and found to comply with the limits for a Class B digital device, pursuant to part 15 of the FCC Rules. These limits are designed to provide reasonable protection against harmful interference in a residential installation. This equipment generates, uses and can radiate radio frequency energy and, if not installed and used in accordance with the instructions, may cause harmful interference to radio communications. However, there is no guarantee that interference will not occur in a particular installation. If this equipment does cause harmful interference to radio or television reception, which can be determined by turning the equipment off and on, the user is encouraged to try to correct the interference by one or more of the following measures:—Reorient or relocate the receiving antenna.—Increase the separation between the equipment and receiver.—Connect the equipment into an outlet on a circuit different from that to which the receiver is connected.—Consult the dealer or an experienced radio/TV technician for help.FCC Radiation Exposure StatementThe modular can be installed or integrated in mobile or fix devices only. This modular cannot be installed in any portable device if without further certify for example C2PC with SAR.This modular complies with FCC RF radiation exposure limits set forth for an uncontrolled environment. This transmitter must not be co-located or operating in conjunction with any other antenna or transmitter. This modular must be installed and operated with a minimum distance of 20 cm between the radiator and user body.If the FCC identification number is not visible when the module is installed inside another device, then the outside of the device into which the module is installed must also display a label referring to the enclosed module. This exterior label can use wording such as the following: “Contains Transmitter Module FCC ID: 2AATL-6223N-SRD Or Contains FCC ID: 2AATL-6223N-SRD”When the module is installed inside another device, the user manual of the host must contain below warning statements;1.This device complies with Part 15 of the FCC Rules. Operation is subject to the following two conditions:(1)This device may not cause harmful interference;(2)This device must accept any interference received, including interference that may cause undesired operation.Note: This equipment has been tested and found to comply with the limits for a Class B digital device, pursuant to part 15 of the FCC Rules. These limits are designed to provide reasonable protection against harmful interference in a residential installation. This equipment generates, uses and can radiate radio frequency energy and, if not installed and used in accordance with the instructions, may cause harmful interference to radio communications.However, there is no guarantee that interference will not occur in a particular installation. If this equipment does cause harmful interference to radio or television reception, which can be determined by turning the equipment off and on, the user is encouraged to try to correct the interference by one or more of the following measures:—Reorient or relocate the receiving antenna.—Increase the separation between the equipment and receiver.—Connect the equipment into an outlet on a circuit different from that to which the receiver is connected. —Consult the dealer or an experienced radio/TV technician for help.2.Changes or modifications not expressly approved by the party responsible for compliance could void the user's authority to operate the equipment.The devices must be installed and used in strict accordance with the manufacturer's instructions as described in the user documentation that comes with the product.Any company of the host device which install this modular with modular approval should perform the test of radiated & conducted emission and spurious emission, etc. according to FCC part 15C : 15.247 and 15.209 & 15.207 ,15B Class B requirement, Only if the test result comply with FCC part 15C : 15.247 and 15.209 & 15.207 ,15B Class B requirement,then the host can be sold legally.。
超快恢复电路器件说明书

Packing Tape&Reel: 5Kpcs/Reel
***IMPORTANT NOTICE***
Micro Commercial Components Corp. reserves the right to make changes without further notice to any product herein to make corrections, modifications , enhancements , improvements , or other changes . Micro Commercial Components Corp . does not assume any liability arising out of the application or use of any product described herein; neither does it convey any license under its patent rights ,nor the rights of others . The user of products in such applications shall assume all risks of such use and will agree to hold Micro Commercial Components Corp . and all the companies whose products are represented on our website, harmless against all damages.
Average Forward Current
IF(AV)
1.0A TL= 125к
Peak Forward Surge
- 1、下载文档前请自行甄别文档内容的完整性,平台不提供额外的编辑、内容补充、找答案等附加服务。
- 2、"仅部分预览"的文档,不可在线预览部分如存在完整性等问题,可反馈申请退款(可完整预览的文档不适用该条件!)。
- 3、如文档侵犯您的权益,请联系客服反馈,我们会尽快为您处理(人工客服工作时间:9:00-18:30)。
Modbus TCP/IP to Modbus Master/Slave Gateway5201/5202-MNET-MCM(4)The MNET-MCM modules are the ideal solution for the many applications where Modbus TCP/IP connectivity can be used to integrate Modbus Master/Slave serial devices into a system. The Modbus TCP/IP gateway is a powerful module designed with both Client and Server support, enabling easy connection to other ModbusTCP/IP Devices (Modicon processors and many others). In combination with the Modbus Master/Slave device support, the module provides a very powerful interface to the many Modbus Master/Slave devices which are in use in the industrial marketplace today. Applications for the module are found in most industries, especially Manufacturing, Oil and Gas, Electrical Power and Food Processing.How to Contact Us: Sales and SupportAll ProSoft Technology® products are backed with unlimited technical support. Contact our worldwide Technical Support team directly by phone or email:Asia Pacific+603.7724.2080, asiapc@ Languages spoken include: Chinese, Japanese, English Europe – Middle East – Africa+33 (0) 5.34.36.87.20, support.EMEA@prosoft-Languages spoken include: French, EnglishNorth America+1.661.716.5100, support@ Languages spoken include: English, SpanishLatin America (Sales only)+1.281.298.9109, latinam@ Languages spoken include: Spanish, EnglishBrasil+55-11.5084.5178, eduardo@ Languages spoken include: Portuguese, English Modbus TCP/IP toModbus Master/Slave Gateway5201/5202-MNET-MCM(4)The ProLinx Modbus TCP/IP to Modbus Master/Slave Gateway creates a powerful connection between devices on a Modbus TCP/IP network and Modbus serial devices. This stand-alone DIN-rail mounted protocol gateway provides one Ethernet port and up to four serial ports.The Modbus TCP/IP protocol driver can interface many different protocols into Schneider Electric Quantum processors as well other solutions supporting the protocol. The MNET driver supports Client and Server connections, and when coupled with the Web option provides a web/ftp interface as well.The Modbus protocol driver supports Master and Slave implementations of the protocol. All Modbus serial ports are individually configurable, providing a very powerful and flexible host or device interface solution.Modbus TCP/IPThe Modbus TCP/IP driver interfaces with a common internal database in the module. This permits the sharing of data between the Modbus TCP/IP and other networks and devices.Modbus TCP/IP ServerGeneral Server supports up to 5 independentconnections each to Modbus TCP/IPclients on Service Port 502 using thestandard MBAP protocol, and Service Port2000.Configurable Parameters Module IP AddressModbus address offsettingModbus TCP/IP ClientGeneral Actively reads and writes data with ModbusTCP/IP compatible devices.One client connection (up to 100servers/devices with 100 commands) Configurable parameters Number of active commands, MinCommand Delay, Response Timeout,Retry Count, Command Error Pointer Command List Up to 100 fully configurable commands onthe Client portModbus Master/SlaveThe Modbus driver provides extensive support for both the Master and the Slave implementations of the protocol. The serial port(s) on the gateway can be individually configured to support the Modbus protocol (Master or Slave, RTU or ASCII, Baud rate, etc.).General Parameters – Modbus ProtocolCommunication parameters Baud Rate: 110 to 115K baud Stop Bits: 1 or 2Data Size: 7 or 8 bitsParity: None, Even, OddRTS Timing delays: 0 to 65535 msError Checking RTU mode (binary) with CRC-16ASCII mode with LRC error checking Floating Point Floating point data movement supported,including configurable support for EnronimplementationFunction Codes 1: Read Output Status2: Read Input Status3: Read Multiple Data Registers4: Read Input Registers5: Write Single Bit6: Write Single Data Register15: Write Multiple Bits16: Write Multiple Data RegisterModbus MasterCommand List Up to 100 command per master port, eachfully configurable for function, slave address,register to/from addressing and word/bitcount.Polling of command list Configurable polling of command list,including continuous and on change of data,and dynamically user or automatic enabled. Modbus SlaveNode address 1 to 247 – software selectableGeneral SpecificationsThe ProLinx Communication Modules provide connectivity for two or more dissimilar network types. The modules, encased in sturdy extruded aluminum, are stand-alone DIN-rail mounted protocol gateways, providing communication between many of the most widely used protocols in industrial automation today. Hardware SpecificationsSpecification DescriptionPower Supply 24 VDC nominal18 to 36 VDC allowedPositive, Negative, GND Terminals2.5 mm screwdriver bladeCurrent Load 500 mA max@ 24 VDCOperating Temperature –20 to 50°C (–4 to 122°F)Storage Temperature –40 to 85°C (–40 to 185°F)Relative Humidity 5 to 95% (non-condensing)Dimensions Standard: 5.20H x 2.07W x 4.52D in.(13.2cmH x 5.25cmW x 11.48cmD)Extended: 5.20H x 2.73W x 4.52D in.(13.2cmH x 6.934cmW x 11.48cmD)LED Indicators Power and Module StatusApplication StatusSerial Port Activity LEDSerial Activity and Error LED Status Configuration Serial Port DB-9M RS-232 onlyNo hardware handshakingEthernet Port (Ethernet modules only) RJ45 ConnectorLink and Activity LED indicatorsSpecification DescriptionApplication Serial Ports RS-232/422/485RS-232 handshaking configurableRS-422/485 screw termination includedSerial Port Isolation 2500V RMS port signal isolation per UL15773000V DC min. port to ground and port tologic power isolationShipped with Each Unit Mini-DIN to DB-9M serial cables4 ft RS-232 configuration cable2.5mm screwdriverCD (docs and Configuration utility)RS-422/485 DB-9 to Screw TerminalAdaptor (1 or 4, depending on ports)ProSoft Configuration BuilderProSoft Configuration Builder (PCB) provides a quickand easy way to manage module configuration filescustomized to meet your application needs. PCB is notonly a powerful solution for new configuration files, butalso allows you to import information from previouslyinstalled (known working) configurations to new projects.Additional ProductsProSoft Technology offers a full complement ofhardware and software solutions for a wide variety ofindustrial communication platforms.Visit our web site at for a complete list of products.Ordering InformationTo order this product, please use the following:5201-MNET-MCM5202-MNET-MCM4Modbus TCP/IP to ModbusMaster/Slave GatewayTo place an order, please contact your local ProSoftTechnology distributor. For a list of ProSoft distributorsnear you, go to Distributors:Place your order by email or fax to:North American / Latin American / Asia Pacificorders@,fax to +1 661.716.5101Europeeurope@,fax to +33 (0) 5.61.78.40.52Copyright © ProSoft Technology, Inc. 2000 - 2007. All Rights Reserved.May 03, 2007。