生产线平衡实验报告
生产线平衡改善报告

活动期间 担当者
改善后 将控制盒悬挂于作业台下 (改善內容)
2009.01.31 郝润清,李辉
项目 改善前 改善后
效 C/T 果 PPM 內 M/H 容 UPH
不牢固,不易于设备维修
效 *投资金额:元 果 金 *有, 无形效果(人员,面积,安全,意识,劳动量…等) 额 *投资费 回收期间 ---等 用 金额 标记
2
;Slide 插
组立
ininal插入
;Slide 插 组立/Air ininal插入 机
入及检查
入及检查
blow
1
IN
4,000cm
4,000cm
6
Ⅲ. 改善事例
会社(部署)名 DS S/C
改善对象 改善项目 改善前 控制盒倒于作业台下面 (问题点) 不牢固,不易于设备维修
5
改
善
事
例
S/C MICRO LINE 控制盒摆放(3定5S)
15.47초 7.Button 入,;Grease ;Slide 插 入及检查
5.19;2.91초 11.45초
3,5 Box 及 2.M-
Plate插入, Con't/Tem
组立
ininal插入
4.17초 1.B/ P lat e Air blow
9.94초 8.特性检查
15.51초 7.Button 入,;Grease
23.3
改善前人员不固 定(8~12名变动)
22.4 22.4
2
Ⅱ. 改善活动结果及内容
2-3. S/C 科 Micro LIine改善 Cost Saving (预想削减金额)
구분
기준 단위 (09年01月
生产线平衡实验

套入右后轮
57
盖上车面
29
装右后轮钢圈套入轮胎
58
嵌入车面固定装置
2、模式一
1)模式一说明
模式一是将整辆小车的零件在同一物料箱内,随生产线流动,每个工位只完成事先安排的任务,并随其他零件流向下一工作台。
2)模式一的装配工艺作业任务及操作时间
根据整个玩具车的产品功能结构和产品零件结构表,细分安排如下装配工艺,根据模式一的方式,安排工序,如表所示:
工位
执行工艺编号
耗时(s)
1
1、2、3、4、5、6、7、8、9、10、11
21
2
12、13、14、15、16、45、46、47、48、49
24
3
24、25、26、27、28、29、39、40、41、42、43、44
22
4
17、18、19、20、21、22、23、30、31、32、33、34、35
17
3、模式二
1)模式二说明
模式二是与模式一相反,是将本工作台任务的零件事先准备好及在相同时间段内组装装配,然后依据程序装配。
2)模式二的装配工艺作业任务及操作时间
根据整个玩具车的产品功能结构和产品零件结构表,细分安排如下装配工艺,根据模式一的方式,安排工序,如表所示:
表6装配工艺作业任务表
工艺序号
工序
44
在零件F1上装4个M2螺丝
4
16
工序9
45
阶梯螺丝与垫片套入导轮
2
46
在F2上装左前导轮
3
47
阶梯螺丝与垫片套入导轮
2
48
在F2上装右前导轮
3
49
在零件F1上装4个M2螺丝
4
动态产线平衡工作总结
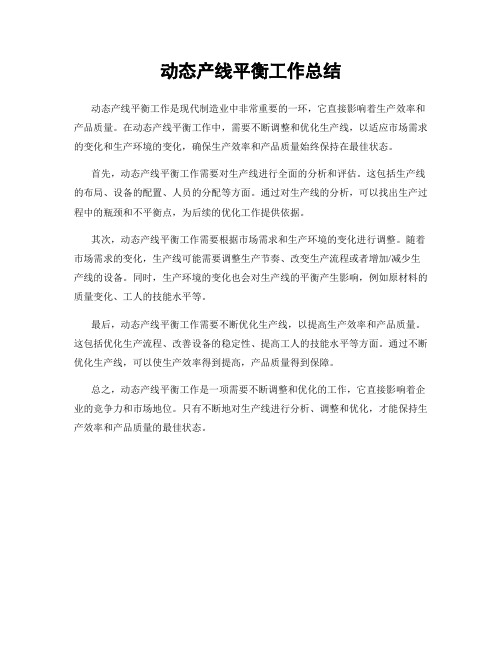
动态产线平衡工作总结
动态产线平衡工作是现代制造业中非常重要的一环,它直接影响着生产效率和产品质量。
在动态产线平衡工作中,需要不断调整和优化生产线,以适应市场需求的变化和生产环境的变化,确保生产效率和产品质量始终保持在最佳状态。
首先,动态产线平衡工作需要对生产线进行全面的分析和评估。
这包括生产线的布局、设备的配置、人员的分配等方面。
通过对生产线的分析,可以找出生产过程中的瓶颈和不平衡点,为后续的优化工作提供依据。
其次,动态产线平衡工作需要根据市场需求和生产环境的变化进行调整。
随着市场需求的变化,生产线可能需要调整生产节奏、改变生产流程或者增加/减少生产线的设备。
同时,生产环境的变化也会对生产线的平衡产生影响,例如原材料的质量变化、工人的技能水平等。
最后,动态产线平衡工作需要不断优化生产线,以提高生产效率和产品质量。
这包括优化生产流程、改善设备的稳定性、提高工人的技能水平等方面。
通过不断优化生产线,可以使生产效率得到提高,产品质量得到保障。
总之,动态产线平衡工作是一项需要不断调整和优化的工作,它直接影响着企业的竞争力和市场地位。
只有不断地对生产线进行分析、调整和优化,才能保持生产效率和产品质量的最佳状态。
动态产线平衡工作总结
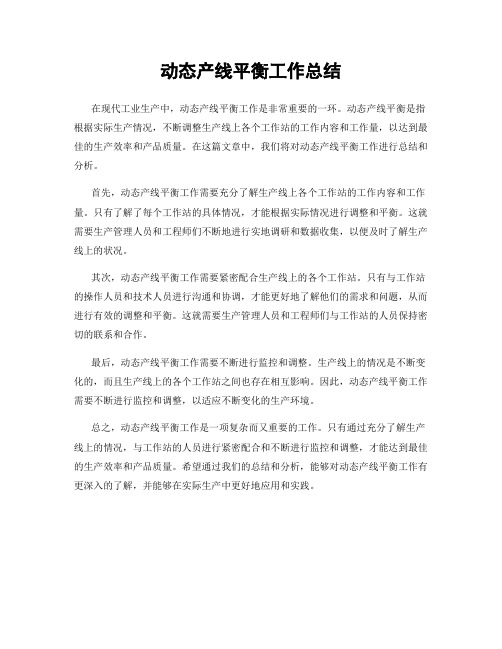
动态产线平衡工作总结
在现代工业生产中,动态产线平衡工作是非常重要的一环。
动态产线平衡是指根据实际生产情况,不断调整生产线上各个工作站的工作内容和工作量,以达到最佳的生产效率和产品质量。
在这篇文章中,我们将对动态产线平衡工作进行总结和分析。
首先,动态产线平衡工作需要充分了解生产线上各个工作站的工作内容和工作量。
只有了解了每个工作站的具体情况,才能根据实际情况进行调整和平衡。
这就需要生产管理人员和工程师们不断地进行实地调研和数据收集,以便及时了解生产线上的状况。
其次,动态产线平衡工作需要紧密配合生产线上的各个工作站。
只有与工作站的操作人员和技术人员进行沟通和协调,才能更好地了解他们的需求和问题,从而进行有效的调整和平衡。
这就需要生产管理人员和工程师们与工作站的人员保持密切的联系和合作。
最后,动态产线平衡工作需要不断进行监控和调整。
生产线上的情况是不断变化的,而且生产线上的各个工作站之间也存在相互影响。
因此,动态产线平衡工作需要不断进行监控和调整,以适应不断变化的生产环境。
总之,动态产线平衡工作是一项复杂而又重要的工作。
只有通过充分了解生产线上的情况,与工作站的人员进行紧密配合和不断进行监控和调整,才能达到最佳的生产效率和产品质量。
希望通过我们的总结和分析,能够对动态产线平衡工作有更深入的了解,并能够在实际生产中更好地应用和实践。
生产线平衡 (2)

生产线平衡
生产线平衡是指在制造过程中,通过合理地分配和安排工
作任务,使得生产线上的工位之间的负荷均衡,从而提高
生产效率和产品质量。
生产线平衡的目标是使得每个工位上的工作时间和工作量
相对均衡,并且生产线的生产节奏能够与市场需求保持一致。
平衡的生产线能够避免工位之间的等待和闲置时间,
减少生产过程中的浪费。
要实现生产线平衡,需要对生产过程进行详细的工作分析,确定每个工位上的工作内容、时间和数量,并结合工人的
技能和经验,合理地分配工作任务。
同时,还需要考虑各
种因素的影响,如不同工序之间的依赖关系、设备的容量
和效率以及工人的疲劳程度等。
生产线平衡可以通过多种方法来实现,包括重新安排工作
顺序、调整工作时间和数量、调整工位布局、提高设备效
率、培训工人等。
同时,可以利用生产线平衡的原理来优
化生产计划和调度,以便更好地满足市场需求和提高生产
效益。
生产线平衡是现代生产管理的重要内容之一,能够有效地
提高生产效率、降低生产成本,提高产品质量和交付能力,进而增强企业的竞争力。
生产线平衡案例分析过程

生产线平衡案例分析过程1. 引言生产线平衡是一种优化生产过程的方法,旨在确保生产线上的工作站之间的工作负载均衡,以提高生产效率和产品质量。
本文将以一个实际案例为例,分析生产线平衡的过程。
2. 案例背景假设某公司生产手机,并且生产线上有三个关键工作站:组装、测试和包装。
每个工作站的工人数量不同,导致工作负载不均衡,组装工作站负责最多的工作量,而测试和包装工作站的工作负载较少。
3. 数据收集为了分析生产线平衡的问题,首先需要收集一些关键数据。
包括每个工作站的工作时间、工人数量以及每个工作站的工作量。
工作站工作时间(分钟)工人数量工作量(数量)组装工作站30 3 200测试工作站25 2 150包装工作站20 2 100通过收集这些数据,可以计算出每个工作站的单位时间工作量,即每分钟能完成的工作量。
根据上表数据,可以得出以下结果:•组装工作站的单位时间工作量为6.67件/分钟(200件/30分钟)•测试工作站的单位时间工作量为6件/分钟(150件/25分钟)•包装工作站的单位时间工作量为5件/分钟(100件/20分钟)4. 分析和优化通过计算每个工作站的单位时间工作量,可以判断哪个工作站是生产线上的瓶颈工作站。
在这个案例中,组装工作站的工作量最大,成为瓶颈,会导致生产线的工作负载不平衡。
为了平衡工作负载,可以采取以下优化措施:•调整工人数量:增加组装工作站的工人数量,以减轻其工作负荷。
•优化工作时间:分析工作时间,寻找减少生产时间的方法,例如改进工艺或引入自动化设备。
•转移工作量:将部分组装工作转移到其他工作站,以平衡各工作站的负载。
5. 优化结果评估经过优化措施的实施后,重新计算每个工作站的单位时间工作量,以评估结果。
工作站工作时间(分钟)工人数量工作量(数量)单位时间工作量(件/分钟)组装工作站30 4 200 5测试工作站25 2 150 6包装工作站20 2 100 5通过调整组装工作站的工人数量,将其增加到4人,重新计算单位时间工作量之后,可以看到组装和包装工作站的工作量现在已经达到了平衡,测试工作站的工作量仍然保持不变。
生产线平衡分析
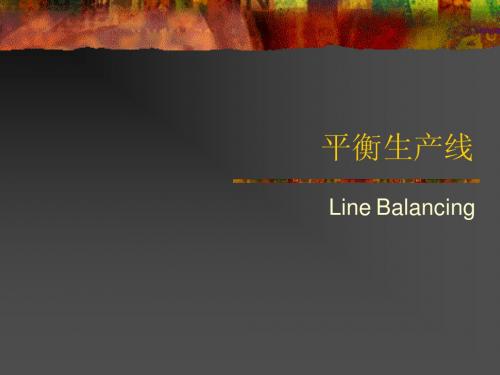
拉平
Line balancing 改善案例
现状调查
现状分析:从作业时间及平衡率看,生产 线的平衡损失比较严重,且作业分工过细, 造成作业内容调整困难。因此在作业改善 上所采取的较直接简便的方法即是合并工 序的内容,调整并取消时间过短工序,以 达到提高平衡,减少工时损失,提高人均 效率的目的。
Line balancing 与“一个流”生产
在生产现场,无论是分工的皮带生产线, 还是手工传递,当平衡率达到85%以上时, 就可以基本实现一个流的生产方式了。
•
Line balancing 的改善原则
平衡率改善的基本原则是通过调整工序的 作业内容来使各工序作业时间接近或减少 这一偏差。 方法 首先应考虑对瓶颈工序进行作业改善,作 业改善的方法,请按照程序分析的改善方 法及动作分析,工装自动化等工程方法与 手段。
将瓶颈工序的作业内容分担给其他工序。 增加各作业人员,只要平衡率提高了,人 均产量就等于提高了,单位产品成本也随 之下降。 合并相关工序,重新排布生产工序,相对 来讲,在作业内容相对较多的情况下容易 拉平衡。 分解作业时间较短的工序,把该工序安排 到其也工序中去。
平衡生产线
Line Balancing
平衡生产线的意义
• • • •
目的 提高作业员及设备工装的工作效率 减少单件产品的工时消耗,降低成本(等 同于提高人均产量); 减少工序的在制品,真正实现“一个流”; 在平衡的生产线基础上实现单元生产,提 高生产应变能力,对应市场变化实现柔性 生产系统;
通过平衡生产线可以综合应用到程序分析、 动作分析、LAYOUT分析,搬运分析、时 间分析等全部IE手法,提高全员综合素质。 Line balancing 的计算 要衡量生产线平衡状态的好坏,我们必须设 定一个定量值来表示,即生产线平衡或平 衡捐失率,以百分率表示。
生产线平衡分析

22
步驟2 每小時量產變異分析
每小時產量變異分析圖
改善前的產量變異 要因改善後的產量變異
P/T縮短後
換線換模 等
財團法人中衛發展中心中區服務處
23
[步驟 3] 生產線平衡的改善(2名作業員以上的生產線)
改善方法說明
• 以上1~2步驟的改善,可能反而使生產線平衡率降低 ,因此在第3步驟針對因省人化而生產線平衡造成的 差異,依照各工程的實際作業時間彙繪製節距圖表:
生產線編成效率
(1) 節奏時間(Tact/Time)的計算:即客戶要求的生產間隔時 間(Pitch Time) 日作業時間(秒/日) T/T= 日需求量(個/日) (2) 編成效率:表示流程作業各工程總合時間與實際需求之比值 各工程作業時間 T/T * 作業人數
財團法人中衛發展中心中區服務處
生產線編成效率=
•生產線要 如繃緊的線 •浪費集中‧ 工作集中化 •省人化
財團法人中衛發展中心中區服務處
16
生產線的生產效率化-改善5步驟
[提升生產效率化的目標]
(1)縮短生產間隔時間(P/T)以符合節奏時間(T/T)
當生產需求量增加,並且不希望利用加班、休假出勤來增加 產量,在原有的作業人員數下,必頇藉由縮短生產的P/T來提 升產量。
14
編成效率之討論
Tact Time:96〞
過 銲 錫
•生產線編成效率 < 70% •80%> 生產線編成效率 > 70% •90%> 生產線編成效率 > 80% •95%< 生產線編成效率
尚未進行改善前的狀態 編成大有問題 尚有改善空間 維持改善的成果
財團法人中衛發展中心中區服務處
15
生产线平衡问题研究

5)建立新的生产流程
6)实施后的效果确认 7)改善后的总结报告
8)标准化
1)平衡前的数据收集整理与分析 了解产品生产流程 收集生产相关指标:标准工时/产能/瓶颈/节拍/平衡 率/不平衡率/损失分析/质量状况等 生产线分析:平衡率分析/不平衡率分析/损失分析 绘制改善前山积表 2)消除生产的浪费 七大浪费消除[不良品浪费/动作浪费/过程浪费/过量 浪费/库存浪费/移动浪费/不平衡浪费] 制作浪费改善前/后比较图, 报告中经验分享
Op55 IN面导管孔加 工
Op50 火花塞孔、喷 油嘴支架孔加工
Op100 U-CAP压装 堵压砂型铸造的孔
Op110 干湿试漏 缸盖压栓
Op120 进排气导管 阀座压装
Op130-1、Op130-2 导管阀座精铰
Op140 缸盖中间清 洗
Op205 配销片
Op200 最终水套压 检
Op190 缸盖中间清 洗
3)利用方法研究进行改善 动作分析 [动素分析/动作经济原则] 程序分析 [四大原则/五大内容/六大步骤]
在进行工作程序的实际分析时,应该对操作、运输、储存、 检验、等待五个方面按照6W提问技术逐一进行分析,然后 采用ECRS四大原则进行对这五个方面分别处理,以寻求最 经济合理的工作方法 操作分析 [人机操作/联合操作/双手操作]
3、生产线平衡的意义
1、提高作业员及设备工装的工作效率; 2、单件产品的工时消耗,降低成本(等同于提高人均 产量); 3、减少工序的在制品,真正实现“一个流”; 4、在平衡的生产线基础上实现单元生产,提高生产应变能 力,对应市场变化,实现柔性生产系统; 5、通过平衡生产线可以综合应用到程序分析、动作分析、 规划(Layout)分析、搬运分析、时间分析等全部IE手法, 提高全员综合素质。
(优质文档)生产线平衡分析
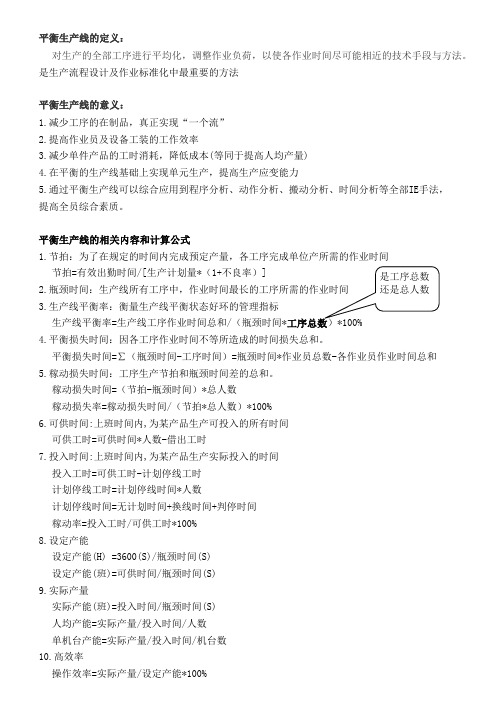
平衡生产线的定义:对生产的全部工序进行平均化,调整作业负荷,以使各作业时间尽可能相近的技术手段与方法。
是生产流程设计及作业标准化中最重要的方法平衡生产线的意义:1.减少工序的在制品,真正实现“一个流”2.提高作业员及设备工装的工作效率3.减少单件产品的工时消耗,降低成本(等同于提高人均产量)4.在平衡的生产线基础上实现单元生产,提高生产应变能力5.通过平衡生产线可以综合应用到程序分析、动作分析、搬动分析、时间分析等全部IE手法,提高全员综合素质。
平衡生产线的相关内容和计算公式1.节拍:为了在规定的时间内完成预定产量,各工序完成单位产所需的作业时间节拍=有效出勤时间/[生产计划量*(1+不良率)]3.生产线平衡率:衡量生产线平衡状态好环的管理指标生产线平衡率=生产线工序作业时间总和/(瓶颈时间*4.平衡损失时间:因各工序作业时间不等所造成的时间损失总和。
平衡损失时间=∑(瓶颈时间-工序时间)=瓶颈时间*作业员总数-各作业员作业时间总和5.稼动损失时间:工序生产节拍和瓶颈时间差的总和。
稼动损失时间=(节拍-瓶颈时间)*总人数稼动损失率=稼动损失时间/(节拍*总人数)*100%6.可供时间:上班时间内,为某产品生产可投入的所有时间可供工时=可供时间*人数-借出工时7.投入时间:上班时间内,为某产品生产实际投入的时间投入工时=可供工时-计划停线工时计划停线工时=计划停线时间*人数计划停线时间=无计划时间+换线时间+判停时间稼动率=投入工时/可供工时*100%8.设定产能设定产能(H) =3600(S)/瓶颈时间(S)设定产能(班)=可供时间/瓶颈时间(S)9.实际产量实际产能(班)=投入时间/瓶颈时间(S)人均产能=实际产量/投入时间/人数单机台产能=实际产量/投入时间/机台数10.高效率操作效率=实际产量/设定产能*100%整体工厂效率(OPE)=平衡率*稼动率*操作效率11.考虑产能的损失平衡损失=(瓶颈*作業人数-单件标准时间)*设定产能操作损失 =(设定产能-实际产量)*单件标准时间-额外产出工时=不良品损失+计划外停线(机)工时 不平衡损失=(最高工序标准时间X合计人數) –合计工序时间生产线平衡分析改善方法:1.1作业改善压缩首先应考虑对瓶颈工序进行作业改善、作业改善的方法,请参照程序分析的改善方法及动作分析、工装自功化等工程方法与手段。
生产线平衡实验报告_3

实验二:用Flexible Line Balancing进行生产线平衡1. 实验目的(1)掌握对生产线平衡问题及其约束进行形式化描述以及基本思路和平衡效果的评价指标;(2)掌握用Flexible Line Balancing V.3进行生产线平衡的方法2. 实验任务(1)熟练掌握生产线问题及其约束的形式化描述(2)掌握生产线平衡的指标(3)利用软件得到生产线平衡方案3. 实验内容与步骤3.1实验内容:针对下列问题进行生产线平衡:上海大众三厂总装车间在2000年引入了国际汽车制造企业流行的模块化装配工艺,其中的底盘装配模块是四大模块中投资最大,技术含量最高的模块流水线。
该模块由动力总成预装线,底盘模块线,底盘总装,底盘螺栓拧紧及返修设备四大部分组成,采用大量自动化螺栓拧紧设备和电磁感应自动运行装配小车。
该生产线原设计为专门生产帕萨特B5轿车,但2004年公司引入全新的途安多功能乘用车,为了为尽可能利用现有资源,决定将该车与B5混线生产。
根据市场需求预测,混线后的生产节拍仍然定为3分钟,即180秒。
现使用本系统对动力总成预装模块重新进行生产线平衡。
帕沙特B5与途安的动力总成预装工艺如表5-1所示,B5工艺流程图如图5-1所示,途安工艺流程图如图5-2所示。
图5-1 帕沙特B5总成预装工艺流程图图5-2 途安动力总成预装工艺流程图原生产线上共有9个工作站,其中有两个缓冲工位。
缓冲工位主要用于解决生产线各工作站间负荷不平衡,也即在制品暂存地。
生产线效率在60%左右,且各工作站负荷相差也较大。
3.2实验步骤:(1)将两条生产线根据紧前紧后工序的关系合并成一条生产线,得到新的工艺流程图。
又考虑到由于Flexible Line Balancing V.3软件对工序有所要求,限制为15道工序,所以先人为根据工序之间的相关性和节拍时间控制的考虑,将工序合并减少到15道。
具体做法如下:1)由于工序714,720分别为制作发动机左右支架,工艺技术相差不大,且具有一定的相关性,故合为一个工序,记为714。
生产线平衡分析

3人线视频
实例计算
计算公式
电装3人柔性线(KFR-32G/DY-JN(E3))
工位 岗位
动作时间 标准工时 人员
作业内容
序号 名称
(秒) (秒) 配置
打变压器
10
打电源线
7
1 打线 贴打条室码内和外断线电 5
标贴
5
包装
5
插线
32
2 插线
外观检验
5
32 1 37 1
生产线各工位的分析如下:
电装7人柔性线岗位时间(秒)
岗位
插室温管
打线1 打线2
插线 功能检 外观检
温
工位时间 18
16
24
37
45
14
作业人数 1
1
1
1
2
1
改善前生产线平衡率=(18+16+24+37+45+16)/(37*7)*100% = 60.2%
改善前生产线各工位平衡图:
40 35 30 25 20 15 10
5
45
2
检
拆线
5
贴 断 电 标 贴4
外观检验 8
外观
6
贴条码
2
检
包装
6
16
1
生产线平衡的改善实例
电子电装7人柔性线,改善前各工位的作业时间如下所示:
50 45 40 35 30 25 20 15 10
5 0
1
2
温线检装
线线
管插能包
打打
温
功
室
插
动作6 动作5 动作4 动作3 动作2 动作1
实验二装配生产线平衡实验

实验二装配生产线平衡实验一、实验任务1.对玩具小车装配过程进行装配生产线平衡;2.在实验室生产模拟系统上模拟玩具小车装配生产线运行过程,并分析平衡效果。
二、实验目的及训练要点1.训练学生合理设计和实施一个工序平衡的生产线。
2.学会装配线平衡的基本方法和步骤。
3.在实验室生产线模拟系统上进行实际模拟,检验数据的准确性,同时掌握生产线模拟系统的操作过程。
另外,训练学生组织活动的能力。
三、实验原理1.定义工作站——操作者为了完成指定的装配作业在装配线上的工作位置。
有时候也把工作站称为“工位”或“工序”。
作业单元——作业的最小单元,一般情况下,这些操作单元不能再分。
对于很复杂的装配作业,例如汽车装配,作业单元如果划分得过细,会使整个平衡过程十分复杂,划分的过粗,又会使平衡难以很好进行,因此,必须寻找一个最佳尺度。
作业单元时间——完成某一个作业单元所用的标准时间,一般是经过工作研究和作业测定的操作时间。
节拍或周期——流水线上生产出一个产品所需要的时间,即相当于从装配线上出来成品的时间间隔。
工作站时间——完成分配给一个工作站的全部作业单元所需要的时间。
工作站空闲时间——在节拍内完成分配给一个工位的全部作业后所剩余的时间,它等于节拍减去工作站时间。
总作业时间——完成整个产品装配过程所需要时间,它等于所有作业元素时间之和。
总空闲时间——整个装配过程汇中,所有工作站空闲时间之和。
平衡效率——是衡量装配线上各工作站间均衡程度好与差的指标。
后续作业——从该作业单元出发沿着装配优先顺序图上所有路径前进直道终点所遇到的所有作业。
先行作业——从该作业开始逆路径方向而行直至起点所遇到的所有作业。
2.流水线平衡的基本步骤(1)完成初步的工艺流程的设计与优化。
制订初步的装配工艺过程,然后利用工艺程序分析方法、5W1H以及ECRS(取消、合并、重排、简化)四大准则对工艺程序进行改善,利用动作研究改善各操作单元的动作等。
改善的目的是为了消除工艺流程中存在的各种不合理的现象、减少浪费等。
生产线平衡LineBala
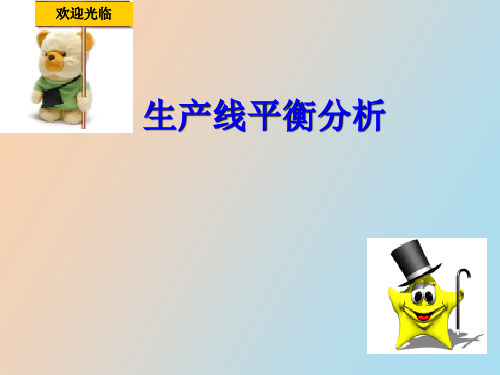
实际产能 实际产能是可供时间內所产出的良品数 1)人均产能=实际产能/投入时间/人数 2)单机台产能=实际产能/投入时间/机台数
二﹑生产线平衡的常见概念
[例]某组装线总投入人力为10人,该组装线的瓶颈 工站的工时为50秒,一天两班20小时实际产出数为 1,400Pcs,良率为95%,试计算该组装线体的标准产 量和人均产量各是多少?
欢迎光临
生产线平衡分析
课程目录
一﹑生产线平衡定义与目的 二﹑生产线平衡的常见概念 三﹑生产线平衡的分析改善
一﹑生产线平衡定义与目的
生产线平衡定义: 工程流动间或工序流动间负荷之差距最
小﹐流动顺畅﹐减少因时间差所造成的等待 或滯留現象。
21 25
每生产一个产品就有33秒损失 一个小时就会堆积几十个产品
.我们只有尽可能地使各工站处于最接近均衡的状态, 从而达到产能和生产力的最大化.
我们应该如何去克服瓶颈,达到生产线的最大平衡?
三﹑生产线平衡的分析改善
分析改善步骤﹕
1.各工站顺序(作业单位)填入生产流动平衡表內.
2.量测各工序作业时间记入表內.
3.清点各工序人数记入表內.
4.根据分配时间划出柱狀图或曲线图.
瓶颈时间
时间
T2
T1
T3 T4 T5
S1 S2 S3 S4 S5 工站
三﹑生产线平衡的分析改善
瓶颈的认识
在流线生产作业模式中,制约产能的是瓶颈工站, 一旦产生瓶颈,前工站的产品无法流下去,后工站无 产品可做,就会造成短暂的停止,从而降低产能. .一条生产线上可能存在多个瓶颈.
.瓶颈是永远存在的,克服其中一个,又出现另一个工 站成为新的瓶颈.
生产线平衡分析范文

生产线平衡分析范文在现代工业生产中,生产线平衡是一个非常重要且常见的问题。
生产线平衡是指通过合理安排工作站的工作量,达到生产线各工作站的负荷均衡,从而提高生产线整体效率的过程。
生产线平衡问题的解决对于提高生产线效率、降低生产成本具有重要意义。
本文将以汽车生产线为例,对生产线平衡进行分析。
一、问题描述汽车生产线通常由多个工作站组成,每个工作站负责不同的生产任务。
生产线平衡问题是要使得每个工作站的工作量尽量均衡,即每个工作站的工作时间相对平衡,从而避免一些工作站的负荷过大或者过小。
在汽车生产线中,工作站间的负荷不平衡会造成生产线停滞、产品积压或者产品缺货等问题,从而降低生产线效率。
二、分析方法生产线平衡问题可以通过平衡指数方法进行分析。
平衡指数是指工作站负荷与最大负荷之间的比值,用来衡量工作站的负荷程度。
当平衡指数为1时,表示工作站的负荷是最大负荷的100%,即负荷均衡;当平衡指数小于1时,表示工作站的负荷没有利用好,存在空闲时间;当平衡指数大于1时,表示工作站的负荷超过了最大负荷,存在过负荷现象。
三、实际案例以汽车生产线为例,该生产线由五个工作站组成,分别是装配车身、安装发动机、安装座椅、安装电子设备和检测工作站。
下表是各个工作站的工作时间和标准工时:工作站,工作时间(分钟),标准工时(分钟)-------------,----------------,----------------装配车身,12,15安装发动机,10,15安装座椅,8,15安装电子设备,12,15检测工作站,10,15根据上表,可以计算出各个工作站的平衡指数,如下表所示:工作站,工作时间(分钟),标准工时(分钟),平衡指数(工作时间/标准工时)-------------,----------------,----------------,-------------------------------装配车身,12,15,0.8安装发动机,10,15,0.67安装座椅,8,15,0.53安装电子设备,12,15,0.8检测工作站,10,15,0.67通过计算可以看出,装配座椅和安装电子设备的工作站负荷较轻,平衡指数较低,存在空闲时间;而装配车身、安装发动机和检测工作站的平衡指数较高,负荷较重。
实验7 生产平衡计算实训

实验十二生产平衡计算实训实训目的了解生产平衡的意义所在及几种常见的平衡算法实训流程建立BOM基础资料/生产工艺-->计算生产平衡生产线平衡概念将作业分成可控制的作业包分配给各个工作地,每一个工作地有一个或者两个工人操作,决定如何将作业分配给工作地这一过程叫生产线平衡。
生产线平衡的目标是分到各个工作地的时间大致相等。
步骤一:建立BOM基础资料/生产工艺打开【制造商】【物料管理】-【BOM资料】模块,点击整张新增按钮新建一个BOM清单,录入成品编码(父阶料号,如电脑主机),名称,再点击按钮保存表头;点击表身新增按钮,录入产品组成的零件物料(子阶料号),如下图1示:图1说明:子阶料号:就是组装电脑的物料清单。
制程代号:也就工序或工艺,就是改物料消耗的工序或者工艺。
用于工位领料的依据。
使用量:就是完成一个产品应该消耗的数量,是采购单生成的依据。
单击窗口下面的“工艺流程”标签后如下图2所示。
图2也就是完成这个产品的工艺流程(自动产生)。
CYCLE TIME:表示完成这个工序的时间(h、m、s、)用小时、分钟、秒钟表示。
紧前:就是完成这个工序前必须完成的工序,也就是做这道工序的前提,没有用“-”表示。
步骤二:计算生产平衡打开【制造商】【生产管理】模块,双击【生产平衡计算】命令。
打开图3所示对话框。
选择一种平衡算法。
图3图4所示为按照时间产量计算平衡,录入或修改产品对应的相关平衡计算必要参数,如下图4示:图4计算前:选择产品编号电脑主机模拟次数(100以上),在一定范围内,计算次数越多越平衡:瓶颈上限百分比(误差的比率),也是瓶颈时间的依据。
瓶颈时间:生产节拍的上限。
也就是说,计算的生产节拍是360秒,这个是标准的。
那么工位的生产节拍有可能会大于这个时间,但是有一个上限,这就是瓶颈上限百分比。
瓶颈时间就是生产节拍的时间+生产节拍的时间*瓶颈上限百分比。
生产平衡参数:生产情况。
输入每天的工作时间,计划产量。
生产线平衡改善报告

生产线平衡改善报告1. 前言本文档旨在分析和改善生产线的平衡性,提高生产效率和质量。
通过对生产线进行评估和改进,我们希望能够减少生产线的停机时间和浪费,提高利用率,减少生产成本,提高产品质量。
2. 背景2.1 生产线平衡的重要性生产线平衡是指在一定时间范围内,通过合理分配工序和工作量,使每个工作站的工作负荷均衡,达到最佳的生产效率。
生产线平衡的好处包括:•减少工作站之间的浮动时间,从而提高整体生产效率。
•均衡工作负荷,避免某个工作站过载或闲置。
•减少生产中的浪费,如等待时间和加工时间过长导致的缺陷品。
•提高产品质量,减少人为因素的干扰。
2.2 生产线平衡的挑战生产线平衡的调整是一个复杂而挑战性的任务。
以下是常见的挑战:•工序和工作站之间的差异:每个工作站可能具有不同的加工时间和要求,导致工作站之间的负荷不均衡。
•不确定性的存在:生产线中可能会遇到一些不可预见的情况,如设备故障或材料供应问题,这会导致生产线的不均衡。
•对于手工作业,人类的差异性:由于人的差异性,一些工作站可能比其他工作站更容易受到影响,导致生产线不平衡。
3. 生产线评估在进行生产线平衡改善之前,首先需要对当前生产线进行评估。
评估的目的是找出生产线中存在的问题和瓶颈,以便进一步改进。
3.1 收集数据要评估生产线的平衡性,首先需要收集一些关键数据,包括但不限于:•每个工作站的加工时间和要求•运输和等待时间•每个工作站的生产数量和质量指标3.2 分析数据收集完数据后,可以对数据进行分析,以了解生产线的现状和问题所在。
常见的数据分析方法包括:•Gantt图:用于可视化每个工作站的加工时间和生产数量。
•输送带平衡计算:计算每个工作站的负荷,并比较其之间的差异。
•产量和质量指标分析:分析生产线的产量和质量指标,找出存在的问题。
3.3 发现问题通过对数据的分析,可以发现生产线中存在的问题。
常见的问题包括:•某些工作站的负荷过高或过低•等待时间过长,导致生产线效率低下•缺陷品较多,质量指标不达标4. 生产线改进在发现问题后,可以采取一系列措施来改善生产线的平衡性。
生产线平衡实验报告_4

生产线平衡实验报告专业班级姓名学号日期一、概述1. 实验目的及要求熟悉了解生产线在生产运作中重要性掌握生产线设备基本操作掌握生产线平衡的测试与优化方法2.实验内容在生产系统实验室的地面生产线上进行三相异步电动机的拆装实验三相异步电动机的拆卸总共让四名同学进行电机的拆卸,在拆卸过程中注意铭牌的安装顺序以及右边风扇区有螺丝拧口,以防安装时出现错误。
三相异步电动机的装配在地面生产线工作,一名总指导员,四名搬运工,四名操作工,四名计时员,四名纠错员。
进行对生产线的模拟与平衡分析。
二、实验内容完成情况1.基于三相异步电动机拆装的生产实验(1)三相异步电动机拆装:基本结构:定子定子铁心:嵌放绕组,提供磁路。
定子绕组:产生旋转磁场。
转子转子铁心:嵌放绕组,提供磁路。
转子绕组:感应出电势、电流。
拆卸电动机1、拆除铭牌。
2、拆卸风扇或风罩,然后取下风扇上定位螺栓,用锤子轻敲扇四周,旋卸下来或从轴上顺槽拔出,卸下风扇。
3、拆卸轴承盖和端盖。
一般小型电动机都只拆风扇一侧的端盖。
5、抽出转子。
对于鼠笼式转子,可直接从定子腔中抽出即可。
注意事项1、螺丝螺母等零部件放在指定位置。
2、注意安全,操作作业在工作台中间完成,不能在边缘,以防砸伤。
3、记住铭牌安装方向。
安装电动机重新按要求将电机重装。
总共分为4个工序。
1、装前后盖端2、装风扇罩3、装接线盒4、装铭牌注意事项1、机械检查:检查机械部分的装配质量2、包括所有紧固螺钉是否拧紧3、用手转动出轴,转子转动是否灵活,无扫膛、无松动;轴承是否有杂声等。
(2)工作研究部分流程程序图装前后端盖装风扇罩装接线盒装铭牌(3)生产过程实训部分实训内容及记录数据按照车间管理模式进行试验,实训成员选择一名总指挥员负责生产线监督管理,合理安排劳动分工。
按照生产工序将实训同学分为四组,选择力气大的四名同学作为搬运工,手巧的四名同学作为操作工,另选四名眼疾手快的同学计时,还有四名同学负责查看操作过程中的瓶颈工序,不必要的动作。
- 1、下载文档前请自行甄别文档内容的完整性,平台不提供额外的编辑、内容补充、找答案等附加服务。
- 2、"仅部分预览"的文档,不可在线预览部分如存在完整性等问题,可反馈申请退款(可完整预览的文档不适用该条件!)。
- 3、如文档侵犯您的权益,请联系客服反馈,我们会尽快为您处理(人工客服工作时间:9:00-18:30)。
生产线平衡实验报告,第三道工位。
实验目的
熟悉了解生产线在生产运作中重要性
掌握生产线设备基本操作
掌握生产线平衡的测试与优化方法
实验任务
熟悉掌握生产线问题及其设备基本操作
熟悉掌握生产线平衡测试与优化方法
实验内容与步骤
一、工序名称和工位数
1. 装小外壳
2.装电容
3.检验并装电机
4.装定时器
5.检验并装换档器
6.装定时器开关
7.装换挡器开关
8.检验并固定电源线
9.接线
10.检验并整理接线
11.装扇叶
12.装后盖
13.装倒风轮
15.检验并装箱
二、试验数据
初步试验数据:
优化后的实验数据:
步骤1根据实验方案准备实验器具,确定本工序上的人员分工。
步骤2上一工序把电风扇传至本工序开始作业并计时
步骤3安装定时器和换挡器,每安装完一个记下一个数据。
四台风扇共8个数据。
步骤4完成数据记录,配合其他工序,优化生产线,准备第二次试验。
步骤5优化生产线后,开始第二次试验。
步骤6对比两次试验数据,进行分析,得出试验结果。
实验结果与分析
本次实验熟悉掌握生产线平衡测试与优化方法,通过即时计时掌握工序实际时间,然后分析数据,优化生产线,缩短了整个生产线工作时间,提高生产效率。
第一次实验结果第三道工位耗时过长,对比第四工位,所以可以优化成把第三工位中的第5工序安排到第四工位中。