AT04-12PA-EC01;中文规格书,Datasheet资料
2SA2004中文资料

Collector-emitter cutoff current (Base open) Forward current transfer ratio
vi
si
VCE = −2V, IC = − 0.1 A VCE = −2 V, IC = −5 V IC = −5 A, IB = − 0.25 A IC = −5 A, IB = − 0.25 A IC = −4 A
at io n.
Max −100 −100 230 −1.2 −1.7 0.5 0.15 1.0
Unit V µA µA V V µs µs µs
Publication date: January 2003
SJD00009CED
1
This product complies with the RoHS Directive (EU 2002/95/EC).
• High forward current transfer ratio hFE • Satisfactory linearity of forward current transfer ratio hFE • Dielectric breakdown voltage of the package: > 5 kV • High−speed switching
at io n.
Request for your special attention and precautions in using the technical information and semiconductors described in this book
(1) If any of the products or technical information described in this book is to be exported or provided to non-residents, the laws and regulations of the exporting country, especially, those with regard to security export control, must be observed. (2) The technical information described in this book is intended only to show the main characteristics and application circuit examples of the products, and no license is granted under any intellectual property right or other right owned by our company or any other company. Therefore, no responsibility is assumed by our company as to the infringement upon any such right owned by any other company which may arise as a result of the use of technical information described in this book. (3) The products described in this book are intended to be used for standard applications or general electronic equipment (such as office equipment, communications equipment, measuring instruments and household appliances). Consult our sales staff in advance for information on the following applications: – Special applications (such as for airplanes, aerospace, automobiles, traffic control equipment, combustion equipment, life support systems and safety devices) in which exceptional quality and reliability are required, or if the failure or malfunction of the products may directly jeopardize life or harm the human body. – Any applications other than the standard applications intended. (4) The products and product specifications described in this book are subject to change without notice for modification and/or improvement. At the final stage of your design, purchasing, or use of the products, therefore, ask for the most up-to-date Product Standards in advance to make sure that the latest specifications satisfy your requirements. (5) When designing your equipment, comply with the range of absolute maximum rating and the guaranteed operating conditions (operating power supply voltage and operating environment etc.). Especially, please be careful not to exceed the range of absolute maximum rating on the transient state, such as power-on, power-off and mode-switching. Otherwise, we will not be liable for any defect which may arise later in your equipment. Even when the products are used within the guaranteed values, take into the consideration of incidence of break down and failure mode, possible to occur to semiconductor products. Measures on the systems such as redundant design, arresting the spread of fire or preventing glitch are recommended in order to prevent physical injury, fire, social damages, for example, by using the products. (6) Comply with the instructions for use in order to prevent breakdown and characteristics change due to external factors (ESD, EOS, thermal stress and mechanical stress) at the time of handling, mounting or at customer's process. When using products for which damp-proof packing is required, satisfy the conditions, such as shelf life and the elapsed time since first opening the packages. (7) This book may be not reprinted or reproduced whether wholly or partially, without the prior written permission of Matsushita Electric Industrial Co., Ltd.
AT4202 04 08 多路温度测试仪用户手册说明书

用户手册User’s GuideAT4202/04/08多路温度测试仪Rev.B4固件说明:适用于主程序RevA2.0及以上的版本@Instruments常州安柏精密仪器有限公司.江苏省常州市钟楼区宝龙61-3层销售服务电子邮件: *****************技术支持电子邮件: ****************©2005-2015 Applent Instruments Ltd.AT4202/4204/4208 用户手册2声明根据国际版权法,未经常州安柏精密仪器有限公司(Applent Instruments Inc.)事先允许和书面同意,不得以任何形式复制本文内容。
安全信息为避免可能的电击和人身安全,请遵循以下指南进行操作。
免责声明用户在开始使用仪器前请仔细阅读以下安全信息,对于用户由于未遵守下列条款而造成的人身安全和财产损失,安柏仪器将不承担任何责任。
仪器接地 为防止电击危险,请连接好电源地线。
不可在爆炸性气体环境使用仪器不可在易燃易爆气体、蒸汽或多灰尘的环境下使用仪器。
在此类环境使用任何电子设备,都是对人身安全的冒险。
不可打开仪器外壳非专业维护人员不可打开仪器外壳,以试图维修仪器。
仪器在关机后一段时间内仍存在未释放干净的电荷,这可能对人身造成电击危险。
不要超出本说明书指定的方式使用仪器超出范围,仪器所提供的保护措施将失效。
警告:不要加直流电压或电流到测试端,否则会损坏仪器。
安全标志:设备由双重绝缘或加强绝缘保护废弃电气和电子设备 (WEEE) 指令 2002/96/EC切勿丢弃在垃圾桶内有限担保和责任范围 3有限担保和责任范围常州安柏精密仪器有限公司(以下简称Applent)保证您购买的每一台AT4202/4204/4208在质量和计量上都是完全合格的。
此项保证不包括保险丝以及因疏忽、误用、污染、意外或非正常状况使用造成的损坏。
本项保证仅适用于原购买者,并且不可转让。
自发货之日起,Applent提供玖拾(90)天保换和贰年免费保修,此保证也包括VFD或LCD。
UFM13PL-TP;UFM12PL-TP;UFM14PL-TP;UFM11PL-TP;UFM15PL-TP;中文规格书,Datasheet资料

U FM11PL THRU U FM17PL1 Amp Ultra FastRecovery Silicon Rectifier 50 to 1000 VoltsFeaturesx Low Costx Ultra fast Recovery x High Reliabilityx O perating Temperature:-65q C to +150q C x Storage Temperature: -65q C to +150q C x Maximum Thermal Resistance;180q C/W Junction To Ambient.MCC Part Number DeviceMarking MaximumRecurrent Peak ReverseVoltageMaximum RMS Voltage Maximum DC Blocking Voltage U FM11PL U 1 50V 35V 50V U FM12PL U 2 100V 70V 100V U FM13PL U 3 200V 140V 200VU FM14PL U 4 400V 280V 400VU FM15PL U 5 600V 420V 600V Electrical Characteristics @ 25q C Unless Otherwise SpecifiedAverage Forward CurrentI F(AV) 1.0A T L = 90q C Peak Forward Surge Current I FSM 30A 8.3ms, half sine Maximum Instantaneous Forward VoltageU FM11PL -13PL U FM14P L U FM15PL-17P L V F 1.0V1.40V 1.70V I FM = 1.0A;T a = 25q C Maximum DCReverse Current At Rated DC Blocking VoltageI R 10P A 50P A Ta = 25q CTa = 125q C Maximum Reverse Recovery TimeTypical JunctionCapacitanceC J20pF Measured at 1.0MHz, V R =4.0V omp onents 20736 Marilla Street Chatsworth! "# $ % ! "#Micro Commercial ComponentsU FM11PL -13PL U FM14PL U FM15PL-16PL T rr 35ns 50ns 75ns I F = 0.5A ,I R =1.0A,T rr = 0.25ΑU FM16PL U 6 800V 560V 800V U FM17PLU 7 1000V 700V 1000VU FM17PL 100ns• Epoxy meets UL 94 V-0 flammability rating • Moisture Sensitivity Level 1x Lead Free Finish/RoHS Compliant (Note1)("P"Suffix designatesCompliant. See ordering information)Maximum RatingsNote: 1. High Temperature Solder Exemption Applied, see EU Directive Annex 7.Micro Commercial ComponentsU FM11PL THRU UFM17PLAverage Forward Rectified Current - Amperes versus Lead Temperature -°CFigure 2Forward Derating Curve1502550751000.2.4.6.81.01.21.4Single Phase, Half Wave60Hz Resistive or Inductive Load Amps°C1251.61.82.02.22.4Instantaneous Forward Current - Amperes versus Instantaneous Forward Voltage - VoltsFigure 1Typical Forward Characteristics 462010Amps.8 1.0 1.2 1.41.61.8.01.02.04.06.1.2.4.612VoltsFigure 3Junction Capacitance.1.21.4210204041002001261020100Junction Capacitance - pF versus Reverse Voltage - VoltspFVolts604044001000T J =25°C ; f=1MHZUFM11PL-UFM14PLUFM15-17PLUFM11PL-13PLT J =25°CUFM14PLUFM15-17PLMicro Commercial Componentst rr+0.5A-0.25-1.01cmSet Time Base for 20/100ns/cm25Vdc1Ω50Ω10ΩOscilloscope Note 1Pulse Generator Note 2Notes:1. Rise Time = 7ns max.Input impedance = 1 megohm, 22pF 2. Rise Time = 10ns max.Source impedance = 50 ohms 3. Resistors are non-inductiveFigure 5Reverse Recovery Time Characteristic And Test Circuit Diagram110040510158Figure 4Peak Forward Surge Current Peak Forward Surge Current - Amperes versus Number Of Cycles At 60Hz - CyclesAmpsCycles261020608040202530www.mccsemi .comRevision: B 2012/07/233 of 4Micro Commercial Componentswww.mccsemi .comDevicePackingPart Number-TP Tape&Reel: 2.5Kpcs/ReelOrdering Information :***IMPORTANT NOTICE***Micro Commercial Components Corp. reserve s the right to make changes without further notice to any product herein to make corrections, modifications , enhancements , improvements , or other changes . Micro Commercial Components Corp . does not assume any liability arising out of the application or use of any product described herein; neither does it convey any license under its patent rights ,nor the rights of others . The user of products in such applications shall assume all risks of such use and will agree to hold Micro Commercial Components Corp . and all the companies whose products are represented on our website, harmless against all damages.***LIFE SUPPORT***MCC's products are not authorized for use as critical components in life support devices or systems without the express writtenapproval of Micro Commercial Components Corporation.***CUSTOMER AWARENESS***Counterfeiting of semiconductor parts is a growing problem in the industry. Micro Commercial Components (MCC) is taking strong measures to protect ourselves and our customers from the proliferation of counterfeit parts. MCC strongly encourages customers to purchase MCC parts either directly from MCC or from Authorized MCC Distributors who are listed by country on our web page cited below . Products customers buy either from MCC directly or from Authorized MCC Distributors are genuine parts, have full traceability, meet MCC's quality standards for handling and storage. MCC will not provide any warranty coverage or other assistance for parts bought from Unauthorized Sources. MCC is committed to combat this global problem and encourage our customers to do their part in stopping this practice by buying direct or from authorized distributors./分销商库存信息:MICRO-COMMERICAL-COUFM13PL-TP UFM12PL-TP UFM14PL-TP UFM11PL-TP UFM15PL-TP。
Tektronix DMM4020数字多功能表数据手册说明书

Digital MultimetersTektronix DMM4020DataSheetDMM4020Features &Bene fitsKey Performance Speci fications 5.5Digit ResolutionBasic VDC Accuracy of up to 0.015%(1yr.)200mV to 1000V Voltage Range,with up to 10μV Resolution 200μA to 10A Current Range,with up to 1nA Resolution 200Ωto 100M ΩOhm Range,with up to 1m ΩResolution CAT I 1000V,CAT II 600VAvailable Functions and Features Volts,Ohms,and Amps Measurements Diode and Continuity Testing Frequency Measurements2×4Ohms 4-wire Measurement Technique Dedicated DC Leakage Current MeasurementsSix Dedicated Buttons for Fast Access to Instrument Setups Limit Compare Mode for Pass/Fail TestingConnectivityFront 2×4Measurement InputsRS-232on Rear Panel for Quick PC Connectivity Includes USB to RS-232Interface Adapter CableIncludes National Instrument’s LabVIEW SignalExpress™TE Limited Edition for Connecting Your Bench3-yearWarrantyData SheetMeasurements with the Push of a ButtonAs the circuits in embedded system designs become more sophisticated, you must measure a multitude of different parameters to validate your design.The Tektronix DMM40205.5digit bench multimeter offers a broad range of functions in one easy-to-use instrument.Typical multimeter measurements–volts,ohms,and amps–are made with a basic VDC accuracy of up to0.015%,ensuring you have the performance you need for your design.You can also use the DMM4020to measure frequency,and to perform continuity and diode tests.This allows youto replace your counter,continuity tester,and DMM with one versatile instrument,saving bench space and cost.Measure Nanoampere SignalsMeasuring standby current in today’s energy-efficient designs requires looking at very low currents,often in the microamp or nanoamp range. Using a traditional multimeter for this measurement can lead to inaccurate results since they typically employ the shunt resistance technique for measuring current.The DMM4020offers an improved method for measuring low currents.By using a current-to-voltage op amp technique,the DMM4020can make current measurements with1nA of resolution and with minimal loading affect on the circuit under test,giving results that reflect real-world operation of the device.Designed to Make Your Work EasierThe DMM4020multimeter is designed with the ease-of-use and familiar operation you expect from Tektronix.Intuitive OperationDedicated front-panel buttons provide fast access to frequently used functions and parameters,reducing setup time.You no longer need to search through software menus tofind the function youneed.Limit compare mode on the DMM4020.Setup Buttons for Your Common MeasurementsWith six setup buttons on the front panel,you can save the settings for your most common measurements.Simply set up the meter for a measurement, then press shift followed by a setup button to save the measurement settings.Now each time you perform that measurement,you simply press the appropriate setup key.Dual DisplayWith the unique dual display,you can measure two different parameters of the same signal from one test connection.Limit CompareThe limit compare mode provides pass/fail indicators to quickly show if a test passes or fails to help eliminate mistakes,especially for results that are close to the limit.Simple and Accurate4-wire MeasurementsPatented split terminal jacks for the2×4ohms function allow you to perform 4-wire measurements using only two leads instead of four.Special test lead accessories are available to enable you to establish the connection.You get excellent resolution and accuracy plus the convenience and ease of using a single pair of leads.Easy Connectivity to Your PCThe RS-232port on the back panel can be used to connect to your PC.A USB to RS-232interface adapter cable is included standard with the DMM4020for connecting to your PC’s USB port.Digital Multimeters—TektronixDMM4020Signal Express acquiring data from Tektronix DMM4020and DPO3052.Connect Your Bench for Intelligent Debug Easily capture,save,and analyze measurement results from your multimeter with the special Tektronix Edition of National Instrument’s LabVIEW SignalExpress™software.Every DMM4020multimeter ships with a free copy of the Limited Edition version of SignalExpress for basic instrument control,data logging,and analysis.The optional Professional Edition offers over200built-in functions that provide additional signal processing,advanced analysis,sweeping,limit testing,and user-defined step capabilities.SignalExpress supports the range of Tektronix bench instruments*1, enabling you to connect your entire test bench.You can then accessthe Signal Express used to export DMM4020data into Excel.feature-rich tools packed into each instrument from one intuitive software interface.This allows you to automate complex measurements requiring multiple instruments,log data for an extended period of time,time-correlate data from multiple instruments,and easily capture and analyze your results, all from your PC.Only Tektronix offers a connected test bench of intelligent instruments to simplify and speed debug of your complex design. Performance You Can Count OnIn addition to industry-leading service and support,every DMM4020 multimeter comes backed with a three-year standard warranty.*1NI LabVIEW Signal Express supports the following Tektronix instruments:MSO/DPO4000/3000/2000 Series oscilloscopes,TDS3000C/2000B/1000B Series oscilloscopes,AFG3000Series arbitrary/function generators,DMM4050/4040/4020Series digital multimeters.3Data SheetCharacteristics General SpecificationsVoltageCharacteristic Description100V Setting90V to110V120V Setting108V to132V220V Setting198V to242V240V Setting216V to264VFrequency47Hz to440HzPower Consumption15VA peak(10W average)DimensionsDimension mm in. Height88 3.46Width2178.56 Depth29711.7 Weight kg lb.Net 2.1 4.6DisplayVacuum Fluorescent Display,segmentEnvironmentCharacteristic DescriptionTemperatureOperating0°C to50°CStorage-40°C to70°CWarm Up½hour to full uncertainty specificationsRelative Humidity(noncondensing)Operating Uncontrolled(<10°C)<90%(10°C to28°C)<75%(28°C to40°C)<45%(40°C to50°C)Storage<95%(-40°C to70°C)AltitudeOperating2,000metersStorage12,000metersVibration Complies with MIL-PRF-28800F Class3Safety Complies with IEC61010-1:2001,ANSI/ISA61010-1(S82.02.01):2004,UL61010-1:2004,CAN/CSA C22.2No.61010.1:2004,CAT I1000V/CAT II600VEMC Designed to comply with IEC61326-1:1997+A1:1998+A2:2000TriggeringCharacteristic DescriptionTrigger Delay400msExternal Trigger Delay<2msExternal Trigger Jitter<1msTrigger Input TTL LevelsTrigger Output5V maxMath FunctionsMin/max,relative,hold,compare,and dB functionsElectricalCharacteristic DescriptionInput Protection1000V all rangesOverrange10%on the largest ranges of all functions exceptcontinuity and diode testRemote InterfacesRS-232C(RS-232to USB Adapter cable included)WarrantyThree yearsDigital Multimeters—Tektronix DMM4020Electrical SpecificationsDC Voltage SpecificationsSpecifications are valid for5½digit mode and after at least a half-hour warm-up.Characteristic DescriptionMaximum Input1000V on any rangeCommon ModeRejection120dB at50or60Hz0.1%(1kΩunbalance)Normal Mode Rejection80dB at Slow RateA/D Nonlinearity15ppm of rangeInput Bias Current<30pA at25°CSettling Considerations Measurement settling times are affected by sourceimpedance,cable dielectric characteristics,and inputsignal changesInput CharacteristicsResolutionRange Full Scale(5½Digits)Slow Medium FastInput Impedance 200mV199.999mV1V10μV10μV>10GΩ*22V 1.99999V10μV100μV100μV>10GΩ*220V19.9999V100μV1000μV1000μV10MΩ±1%200V199.999V1mV10mV10mV10MΩ±1%1000V1000.00V10mV100mV100mV10MΩ±1%*2At some dual-display measurements,the input impedance of200mV and2V ranges may be changed to10MΩ.AccuracyUncertainty*390days1year Range23°C±5°C23°C±5°C Temperature Coefficient/°C Outside18–28°C200mV0.01+0.0030.015+0.0040.0015+0.00052V0.01+0.0020.015+0.0030.001+0.000520V0.01+0.0030.015+0.0040.0020+0.0005200V0.01+0.0020.015+0.0030.0015+0.00051000V0.01+0.0020.015+0.0030.0015+0.0005*3Uncertainty given as±(%of reading+%of range).5Data SheetAC Voltage SpecificationsAC Voltage specifications are for AC sinewave signals>5%of range.For inputs from 1%to5%of range and<50kHz,add an additional error of0.1%of range,and for 50kHz to100kHz,add0.13%of range.Characteristic DescriptionMaximum Input750V RMS or1000V peak or8×107Volts-Hertz product Measurement Method AC-coupled true RMS.Measures the AC component ofinput with up to1000VDC bias on any rangeAC Filter Bandwidth20Hz–100kHzCommon ModeRejection60dB at50Hz or60Hz(1kΩunbalance)Maximum Crest Factor3:1at Full ScaleAdditional Crest Factor Errors(<100Hz)Crest Factor1-2,0.05%of full scale Crest Factor2-3,0.2%of full scale Only applies for non-sinusoid signalsInput CharacteristicsResolutionRange Full Scale(5½Digits)Slow Medium FastInput Impedance200mV199.999mV1μV10μV10μV 2V 1.99999V10μV100μV100μV 20V19.9999V100μV1000μV1000μV 200V199.999V1mV10mV10mV 750V750.00V10mV100mV100mV 1MΩ±2%shunted by<100pfAccuracyUncertainty*390days1year Range Frequency23°C±5°C23°C±5°C Temperature Coefficient/°C Outside18–28°C20Hz–45Hz0.8+0.050.9+0.050.01+0.00545Hz–20kHz0.15+0.050.2+0.050.01+0.00520kHz–50kHz0.3+0.050.35+0.050.01+0.005 200mV50kHz–100kHz0.8+0.050.9+0.050.05+0.0120Hz–45Hz0.8+0.050.9+0.050.01+0.00545Hz–20kHz0.15+0.050.2+0.050.01+0.00520kHz–50kHz0.3+0.050.35+0.050.01+0.005 2V50kHz–100kHz0.8+0.050.9+0.050.05+0.0120Hz–45Hz0.8+0.050.9+0.050.01+0.00545Hz–20kHz0.15+0.050.2+0.050.01+0.00520kHz–50kHz0.3+0.050.35+0.050.01+0.005 20V50kHz–100kHz0.8+0.050.9+0.050.05+0.0120Hz–45Hz0.8+0.050.9+0.050.01+0.00545Hz–20kHz0.15+0.050.2+0.050.01+0.00520kHz–50kHz0.3+0.050.35+0.050.01+0.005 200V50kHz–100kHz0.8+0.050.9+0.050.05+0.0120Hz–45Hz0.8+0.050.9+0.050.01+0.00545Hz–20kHz0.15+0.050.2+0.050.01+0.00520kHz–50kHz0.3+0.050.35+0.050.01+0.005 750V50kHz–100kHz0.8+0.050.9+0.050.05+0.01 *3Uncertainty given as±(%of reading+%of range).Digital Multimeters—Tektronix DMM4020 ResistanceSpecifications are for4-wire resistance function,or2-wire resistance with REL.IfREL is not used,add0.2Ωfor2-wire resistance plus lead resistance.Characteristic DescriptionMeasurement Method Current source referenced to LO inputMax Lead Resistance (4-wire ohms)10%of range per lead for200Ω,2kΩranges.1kΩper lead on all other ranges.Input Protection1000V on all rangesInput CharacteristicsResolutionRange Full Scale(5½Digits)Slow Medium FastCurrent Source200Ω199.999Ω0.001Ω0.01Ω0.01Ω0.8mA2kΩ 1.99999kΩ0.01Ω0.1Ω0.1Ω0.8mA20kΩ19.9999kΩ0.1Ω1Ω1Ω0.08mA 200kΩ199.999kΩ1Ω10Ω10Ω0.008mA2MΩ 1.99999MΩ10Ω100Ω100Ω0.9μA20MΩ19.9999MΩ100Ω1kΩ1kΩ0.16μA 100MΩ100.000MΩ1kΩ10kΩ10kΩ0.16μA||10MΩAccuracyUncertainty*390days1year Range23°C±5°C23°C±5°C Temperature Coefficient/°C Outside18–28°C200Ω0.02+0.0040.03+0.0040.003+0.00062kΩ0.015+0.0020.02+0.0030.003+0.000520kΩ0.015+0.0020.02+0.0030.003+0.0005200kΩ0.015+0.0020.02+0.0030.003+0.00052MΩ0.03+0.0030.04+0.0040.004+0.000520MΩ0.2+0.0030.25+0.0030.01+0.0005100MΩ 1.5+0.004 1.75+0.0040.2+0.0005*3Uncertainty given as±(%of reading+%of range).7Data SheetDC CurrentCharacteristic DescriptionInput Protection Tool-accessible11A/1000V and440mA/1000VfusesShunt Resistance0.01Ωfor2A and10A ranges1Ωfor20mA and200mABurden voltage<5mV for200μA and2mA rangeInput CharacteristicsResolutionRange Full Scale(5½Digits)Slow Medium FastBurden Voltage 200μA199.999μA0.001μA0.01μA0.01μA<5mV2mA1999.99μA0.01μA0.1μA0.1μA<5mV20mA19.9999mA0.1μA1μA1μA<0.05V 200mA19.9999mA1μA10μA10μA<0.5V2A 1.99999A10μA100μA100μA<0.1V10A10.0000A100μA1mA1mA<0.5V AccuracyUncertainty*390days1year Range23°C±5°C23°C±5°C Temperature Coefficient/°C Outside18–28°C200μA0.02+0.0050.03+0.0050.003+0.001 2mA0.015+0.0050.02+0.0050.002+0.001 20mA0.03+0.020.04+0.020.005+0.001 200mA0.02+0.0050.03+0.0080.005+0.001 2A0.05+0.020.08+0.020.008+0.001 10A0.18+0.010.2+0.010.008+0.001 *3Uncertainty given as±(%of reading+%of range).Digital Multimeters—Tektronix DMM4020 AC CurrentThe following AC current specifications are for sinusoidal signals with amplitudesgreater than5%of range.For inputs from1%to5%of range,add an additionalerror of0.1%of range.Characteristic DescriptionInput Protection Tool-accessible11A/1000V and440mA/1000VfusesMeasurement Method AC-coupled true RMSShunt Resistance0.01Ωfor2A and10A ranges1Ωfor20mA and200mAAC Filter Bandwidth20Hz–100kHzMaximum Crest Factor3:1at Full ScaleAdditional Crest Factor Errors(<100Hz)Crest Factor1-2,0.05%of full scale Crest Factor2-3,0.2%of full scale Only applies to non-sinusoid signalsInput CharacteristicsResolutionRange Full Scale(5½Digits)Slow Medium FastBurden Voltage 20mA19.9999mA0.1μA1μA1μA<0.05V 200mA199.999mA1μA10μA10μA<0.5V2A 1.99999A10μA100μA100μA<0.1V10A10.0000A100μA1mA1mA<0.5V AccuracyUncertainty*390days1year Range Frequency23°C±5°C23°C±5°C Temperature Coefficient/°C Outside18–28°C20Hz-45Hz1+0.05 1.25+0.060.015+0.00520mA45Hz-2kHz0.25+0.050.3+0.060.015+0.00520Hz-45Hz0.8+0.051+0.060.015+0.005200mA45Hz-2kHz0.25+0.050.3+0.060.015+0.00520Hz-45Hz1+0.05 1.25+0.060.015+0.0052A45Hz-2kHz0.25+0.050.3+0.060.015+0.00520Hz-45Hz1+0.1 1.25+0.120.015+0.00510A45Hz-2kHz1+0.10.5+0.120.015+0.005*3Uncertainty given as±(%of reading+%of range).9Data SheetFrequencyCharacteristic Description Gate Time131msMeasurement Method AC-coupled input using the AC voltage measurement functionSettling Considerations When measuring frequency after a DC offset voltage change,errors may occur.For the most accurate measurement,wait up to1second to allow input-blocking RC time constant to settleMeasurement Considerations To minimize measurement errors,shield inputs from external noise when measuring low-voltage, low-frequency signalsInput CharacteristicsUncertainty90days1year Range Frequency23°C±5°C23°C±5°C Temperature Coefficient/°C Outside18–28°C20Hz–2kHz0.01+0.0020.01+0.0030.002+0.0012kHz–20kHz0.01+0.0020.01+0.0030.002+0.00120kHz–200kHz0.01+0.0020.01+0.0030.002+0.001 100mV to750V*4,5200kHz–1MHz0.01+0.0040.01+0.0060.002+0.002 *4Input>100mV.*5Limited to8×107V Hz.ContinuityCharacteristic Description Continuity Threshold20ΩTest Current1mAResponse Time100S/s with audible tone Rate FastMaximum Reading199.99ΩResolution0.01ΩDiode TestCharacteristic Description Response Time100S/s with audible tone Rate FastMaximum Reading 1.9999VResolution0.1mVDigital Multimeters—Tektronix DMM4020Ordering InformationModelsModel DescriptionDMM4020 5.5Digit MultimeterDMM4020Includes:Meter,TL710test leads,line cord,spare line fuse,statement of cal practices,Warranty statement,Safety and Installation Guide,Connectivity Installation Manual,CD-ROM with user manual(English,French,Italian,German, Spanish,Simplified Chinese,Traditional Chinese,Korean,Russian,Japanese), RS-232to USB Adapter Cable,National Instruments LabVIEW SignalExpress™Tektronix Edition,Limited Edition Software.Please specify power plug when ordering.Instrument OptionsPower Plug OptionsOption DescriptionOpt.A0North AmericaOpt.A1Universal EuroOpt.A2United KingdomOpt.A3AustraliaOpt.A5SwitzerlandOpt.A6JapanOpt.A10ChinaOpt.A11IndiaOpt.A99No power cordOpt.E1Euro and UK power cords Service Options*6Option DescriptionOpt.CA1Provides a single calibration event or coverage for thedesignated calibration interval,whichever comesfirst Opt.C3Calibration Service3YearsOpt.C5Calibration Service5YearsOpt.D1Calibration Data ReportOpt.R5Repair Service5Years(including warranty)*6Test Leads and accessories are not covered by the DMM warranty and Service Offerings.Refer to the datasheet of each Test Lead and accessory model for its unique warranty and calibration terms.Recommended Accessories and SoftwareAccessory DescriptionCalibration Manual077-0365-xxTL710Premium Test Leads(196-3250-xx)TL7052×4Wire Ohm1000V Precision Test LeadTL7252×4Wire Ohm SMD Test TweezersAC4000Soft Transit CaseHCTEK4321Hard Carrying CaseY8846S Single Rackmount KitY8846D Dual Rackmount Kit013-0369-xx Calibration Fixture4-terminal shortSIGEXPTE NI LabVIEW SignalExpress Tektronix Edition Software–FullVersionProduct(s)are manufactured in ISO registeredfacilities.Product(s)complies with IEEE Standard488.1-1987and RS-232C.11Data Sheet Contact Tektronix:ASEAN/Australasia(65)63563900Austria+41526753777Balkans,Israel,South Africa and other ISE Countries+41526753777Belgium078160166Brazil+55(11)3759-7627Canada1(800)661-5625Central East Europe,Ukraine,and the Baltics+41526753777Central Europe&Greece+41526753777Denmark+4580881401Finland+41526753777France+33(0)169868181Germany+49(221)9477400Hong Kong(852)2585-6688India(91)80-42922600Italy+39(02)250861Japan81(3)6714-3010Luxembourg+44(0)1344392400Mexico,Central/South America&Caribbean52(55)54247900Middle East,Asia,and North Africa+41526753777The Netherlands09002021797Norway80016098People’s Republic of China86(10)62351230Poland+41526753777Portugal800812370Republic of Korea82(2)6917-5000Russia&CIS+7(495)7484900South Africa+27112068360Spain(+34)901988054Sweden020*******Switzerland+41526753777Taiwan886(2)2722-9622United Kingdom&Ireland+44(0)1344392400USA1(800)426-2200For other areas contact Tektronix,Inc at:1(503)627-7111Updated5August2009For Further Information.Tektronix maintains a comprehensive,constantly expandingcollection of application notes,technical briefs and other resources to help engineers workingon the cutting edge of technology.Please visit Copyright©Tektronix,Inc.All rights reserved.Tektronix products are covered by U.S.and foreign patents,issued and rmation in this publication supersedes that in all previously published material.Specification and price change privileges reserved.TEKTRONIX and TEK are registered trademarks ofTektronix,Inc.All other trade names referenced are the service marks,trademarks,or registered trademarksof their respective companies.08Sep20093MW-24431-0。
GCE-2001全国产化说明书

说明除列明随产品配置的配件外,本手册包含的内容并不代表本公司的承诺,本公司保留对此手册更改的权利,且不另行通知。
对于任何因安装、使用不当而导致的直接、间接、有意或无意的损坏及隐患概不负责。
订购产品前,请向经销商详细了解产品性能是否符合您的需求。
本手册所涉及到的其他商标,其所有权为相应的产品厂家所拥有。
本手册内容受版权保护,版权所有。
未经许可,不得以机械的、电子的或其它任何方式进行复制。
温馨提示1、产品使用前,务必请仔细阅读产品说明书。
2、对未准备安装的主板,应将其保存在防静电保护袋中。
3、在从包装袋中拿主板前,应将手先置于接地金属物体上一会儿,以释放身体及手中的静电4、在使用前,宜将主板置于稳固的平面上。
5、请保持主板的干燥,散热片的开口缝槽是用于通风,避免机箱内的部件过热。
请勿将此类开口掩盖或堵塞。
6、在将主板与电源连接前,请确认电源电压值。
7、请将电源线置于不会被践踏的地方,且不要在电源线上堆置任何物件。
8、当您需连接或拔除任何设备前,须确定所有的电源线事先已被拔掉。
9、为避免人体被电击或产品被损坏,在每次对整机、板卡进行拔插或重新配置时,须先关闭交流电源或将交流电源线从电源插座中拔掉。
10、请留意手册上提到的所有注意和警告事项。
11、为避免频繁开关机对产品造成不必要的损伤,关机后,应至少等待30秒后再开机。
12、设备在使用过程中出现异常情况,请找专业人员处理。
13、请不要将本设备置于或保存在环境温度高于70℃上,否则会对设备造成伤害。
目录1.产品简介 (1)1.1概述 (1)1.2产品特点 (2)1.3产品优势 (2)1.4技术指标 (3)2.细参数说明 (4)2.1产品图片 (4)2.2 测试套板接口图片 (5)2.3 COMe外形尺寸 (6)2.4 COMe连接器接口定义 (7)1.产品简介1.1概述随着具备高性能计算能力的智能装备在诸如:工业、农业、能源、国防、医疗、交通、民生等多个领域的推广和应用,越来越多的企业将大量资源,投入到高性能计算能力的智能装备的研发和生产中。
OPT101P;OPT101P-J;OPT101PG4;OPT101P-JG4;中文规格书,Datasheet资料

SPECTRAL RESPONSIVITYWavelength (nm)20030040050060070080090010001100V o l t a g e O u t p u t (V /µW )0.70.60.50.40.30.20.100.70.60.50.40.30.20.1P h o t o d i o d e R e s p o n s i v i t y (A /W )OPT101FEATURESq SINGLE SUPPLY: +2.7 to +36Vq PHOTODIODE SIZE: 0.090 x 0.090 inch q INTERNAL 1M Ω FEEDBACK RESISTOR q HIGH RESPONSIVITY: 0.45A/W (650nm)q BANDWIDTH: 14kHz at R F= 1M Ωq LOW QUIESCENT CURRENT: 120µA qAVAILABLE IN 8-PIN DIP AND 8-LEAD SURFACE-MOUNT PACKAGESMONOLITHIC PHOTODIODE ANDSINGLE-SUPPLY TRANSIMPEDANCE AMPLIFIERλDESCRIPTIONThe OPT101 is a monolithic photodiode with on-chip transimpedance amplifier. Output voltage increases linearly with light intensity. The amplifier is designed for single or dual power-supply operation, making it ideal for battery-operated equipment.The integrated combination of photodiode and transimpedance amplifier on a single chip eliminates the problems commonly encountered in discrete designs such as leakage current errors, noise pick-up, and gain peaking due to stray capacitance. The 0.09 x 0.09 inch photodiode is operated in the photoconductive mode for excellent linearity and low dark current.The OPT101 operates from +2.7V to +36V supplies and quiescent current is only 120µA. It is available in clear plastic 8-pin DIP, and J-formed DIP for surface mounting.Temperature range is 0°C to +70°C.APPLICATIONSq MEDICAL INSTRUMENTATIONq LABORATORY INSTRUMENTATION q POSITION AND PROXIMITY SENSORS q PHOTOGRAPHIC ANALYZERS q BARCODE SCANNERS q SMOKE DETECTORS q CURRENCY CHANGERSSBBS002A – JANUARY 1994 – REVISED OCTOBER 2003PRODUCTION DATA information is current as of publication date.Products conform to specifications per the terms of Texas Instruments standard warranty. Production processing does not necessarily include testing of all parameters.Copyright © 1994-2003, Texas Instruments IncorporatedPlease be aware that an important notice concerning availability, standard warranty, and use in critical applications of Texas Instruments semiconductor products and disclaimers thereto appears at the end of this data sheet.All trademarks are the property of their respective owners./OPT1012SBBS002ASPECIFICATIONSAt T A = +25°C, V S = +2.7V to +36V, λ = 650nm, internal 1M Ω feedback resistor, and R L = 10k Ω, unless otherwise noted.PHOTODIODE SPECIFICATIONST A = +25°C, V S = +2.7V to +36V unless otherwise noted.Photodiode of OPT101PPARAMETER CONDITIONS MINTYPMAXUNITS Photodiode Area (0.090 x 0.090in)0.008in 2(2.29 x 2.29mm)5.2mm 2Current Responsivity 650nm 0.45A/W 650nm865µA/W/cm 2Dark CurrentV DIODE = 7.5mV2.5pAvs Temperature Doubles every 7°CCapacitance1200pFNOTES: (1) Deviation in percent of full scale from best-fit straight line. (2) Referred to Output. Includes all error sources./OPT1013SBBS002AOP AMP SPECIFICATIONSAt T A = +25°C, V S = +2.7V to +36V, λ = 650nm, internal 1M Ω feedback resistor, and R L = 10k Ω, unless otherwise noted.OPT101 Op Amp (1)PARAMETERCONDITIONSMINTYPMAXUNITS INPUTOffset Voltage ±0.5mV vs Temperature ±2.5µV/°C vs Power Supply 10µV/V Input Bias Current (–) Input 165pAvs Temperature (–) InputDoubles every 10°C Input Impedance Differential400 || 5M Ω || pF Common-Mode250 || 35G Ω || pFCommon-Mode Input Voltage Range Linear Operation0 to [(V S ) – 1]V Common-Mode Rejection 90dB OPEN-LOOP GAIN Open-loop Voltage Gain 90dB FREQUENCY RESPONSE Gain-Bandwidth Product (2)2MHz Slew Rate1V/µs Settling Time 1%5.8µs 0.1%7.7µs 0.05%8.0µs OUTPUTVoltage Output, High (V S ) – 1.3(V S ) – 1.15V Short-Circuit Current V S = +36V15mA POWER SUPPLYOperating Voltage Range +2.7+36V Quiescent CurrentDark, V PIN3 = 0V 120240µA R L = ∞, V OUT = 10V220µANOTES: (1) Op amp specifications provided for information and comparison only. (2) Stable gains ≥ 10V/V./OPT1014SBBS002AMOISTURE SENSITIVITY AND SOLDERINGClear plastic does not contain the structural-enhancing fillers used in black plastic molding compound. As a result, clear plastic is more sensitive to environmental stress than black plastic. This can cause difficulties if devices have been stored in high humidity prior to soldering. The rapid heating during soldering can stress wire bonds and cause failures. Prior to soldering, it is recommended that plastic devices be baked-out at +85°C for 24 hours.The fire-retardant fillers used in black plastic are not compat-ible with clear molding compound. The OPT101 plastic packages cannot meet flammability test, UL-94.PIN CONFIGURATIONSTop ViewDIPV S –In –V1M Ω FeedbackCommon NC NC Output12348765(1)NOTE: (1) Photodiode location.ABSOLUTE MAXIMUM RATINGS (1)Supply Voltage (V S to “Common ” or pin 3)................................0 to +36V Output Short-Circuit (to ground)...............................................Continuous Operating Temperature ....................................................–25°C to +85°C Storage Temperature........................................................–25°C to +85°C Junction Temperature ......................................................................+85°C Lead Temperature (soldering, 10s)...............................................+300°C (Vapor-Phase Soldering Not Recommended)NOTE: (1) Stresses above these ratings may cause permanent damage.Exposure to absolute maximum conditions for extended periods may degradedevice reliability. These are stress ratings only, and functional operation of the device at these or any other conditions beyond those specified is not implied.This integrated circuit can be damaged by ESD. Texas Instruments recommends that all integrated circuits be handled with appropriate precautions. Failure to observe proper han-dling and installation procedures can cause damage.ESD damage can range from subtle performance degradation to complete device failure. Precision integrated circuits may be more susceptible to damage because very small parametric changes could cause the device not to meet its published specifications.SPECIFIED PACKAGE TEMPERATUREPACKAGE ORDERING TRANSPORT PRODUCT PACKAGE-LEADDESIGNATORRANGE MARKING NUMBER MEDIA, QUANTITYOPT101P DIP-8NTC –25°C to +85°C OPT101OPT101P Rail, 50OPT101P-JDIP-8, Surface Mount (2)DTL–25°C to +85°COPT101OPT101P-JRail, 50NOTES: (1) For the most current package and ordering information, see the Package Option Addendum at the end of this data sheet. (2) 8-pin DIP with J-formed leads for surface mounting.PACKAGE/ORDERING INFORMATION (1)/OPT1015SBBS002ATYPICAL PERFORMANCE CURVESAt T A = +25°C, V S = +2.7V to +36V, λ = 650nm, internal 1M Ω feedback resistor, and R L = 10k Ω, unless otherwise noted.VOLTAGE RESPONSIVITY vs RADIANT POWERRadiant Power (µW)O u t p u t V o l t a g e (V )0.010.1101001k11010.10.010.001RESPONSE vs INCIDENT ANGLER e l a t i v e R e s p o n s eIncident Angle (°)1.00.80.60.40.20±20±40±60±801.00.80.60.40.20DARK V OUT vs TEMPERATURETemperature (°C)1020304050607087.87.67.47.27O u t p u t V o l t a g e (m V )VOLTAGE RESPONSIVITY vs IRRADIANCEIrradiance (W/m 2)O u t p u t V o l t a g e (V )0.0010.011101000.11010.10.010.001VOLTAGE RESPONSIVITY vs FREQUENCYFrequency (Hz)1001k10k 100k1010.10.010.001R e s p o n si v i t y (V /µW )NORMALIZED SPECTRAL RESPONSIVITY Wavelength (nm)200300400500600700800900100011001.00.90.80.70.60.50.40.30.20.10N o r m a l i z e d C u r r e n t o r V o l t a g e O u t p u t/OPT1016SBBS002ATYPICAL PERFORMANCE CURVES (Cont.)At T A = +25°C, V S = +2.7V to +36V, λ = 650nm, internal 1M Ω feedback resistor, and R L = 10k Ω, unless otherwise noted.QUIESCENT CURRENT vs TEMPERATURETemperature (°C)102030406050703002752502252001751501251007550Q u i e s c e n t C u r r e n t (µA )QUIESCENT CURRENT vs (V OUT – V PIN3)V OUT – V PIN3 (V)051015202530354030025020015010050Q u i e s c e n tC u r r e n t (µA )SHORT CIRCUIT CURRENT vs V SV S (V)51015202530354020181614121086420S h o r t C i r c u i t C u r r e n t (m A )(I BIAS -I DARK ) vs TEMPERATURETemperature (°C)10203040506070180160140120100806040200–20–40I B I A S -I D A R K (p A )NOISE EFFECTIVE POWER vsMEASUREMENT BANDWIDTH, V S = +15, V OUT – V PIN3 = 0Bandwidth (Hz)101001k 10k 100k 1M10–710–810–910–1010–1110–12N o i s e E f f e c t i v e P o w e r (W )OUTPUT NOISE VOLTAGE vsMEASUREMENT BANDWIDTH, V= +15, V – V = 15VFrequency (Hz)101001k 10k 100k 1M 10001001010.1N o i s e V o l t a g e (µV r m s )/OPT1017SBBS002ATYPICAL PERFORMANCE CURVES (Cont.)At T A = +25°C, V S = +2.7V to +36V, λ = 650nm, internal 1M Ω feedback resistor, and R L = 10k Ω,unless otherwise noted.SMALL SIGNAL RESPONSELARGE SIGNAL RESPONSESMALL SIGNAL RESPONSE (C LOAD = 10,000 pF)(Pin 3 = 0V)SMALL SIGNAL RESPONSE (C LOAD = 10,000 pF)(Pin 3 = –15V)/OPT1018SBBS002Asource to sink currents up to approximately 100µA. The benefits of this current sink are shown in the typical performance curves “Small Signal Response (C LOAD =10,000pF)” which compare operation with pin 3 grounded and connected to –15V.Due to the architecture of this output stage current sink, there is a slight increase in operating current when there is a voltage between pin 3 and the output. Depending on the magnitude of this voltage, the quiescent current will increase by approximately 100µA as shown in the typical performance curve "Quiescent Current vs (V OUT – V PIN3)".APPLICATIONS INFORMATIONFigure 1 shows the basic connections required to operate the OPT101. Applications with high-impedance power supplies may require decoupling capacitors located close to the device pins as shown. Output is 7.5mV dc with no light and increases with increasing illumination.Photodiode current, I D , is proportional to the radiant power, or flux, (in watts) falling on the photodiode. At a wavelength of 650nm (visible red) the photodiode Responsivity, R I , is approximately 0.45A/W. Responsivity at other wavelengths is shown in the typical performance curve “Responsivity vs Wavelength.”FIGURE 1. Basic Circuit Connections.The typical performance curve “Output Voltage vs Radiant Power” shows the response throughout a wide range of radiant power. The response curve “Output Voltage vs Irradiance” is based on the photodiode area of 5.2mm 2.The OPT101’s voltage output is the product of the photodiode current times the feedback resistor, (I D R F ), plus a pedestal voltage, V B , of approximately 7.5mV introduced for single supply operation. The internal feedback resistor is laser trimmed to 1M Ω. Using this resistor, the output voltage responsivity, R V ,is approximately 0.45V/µW at 650nm wavelength. Figure 1shows the basic circuit connections for the OPT101 operating with a single power supply and using the internal 1M Ω feedback resistor for a response of 0.45V/µW at 650nm. Pin 3 is connected to common in this configuration.CAPACITIVE LOADINGThe OPT101 is capable of driving load capacitances of 10nF without instability. However, dynamic performance with capacitive loads can be improved by applying a negative bias voltage to Pin 3 (shown in Figure 2). This negative power supply voltage allows the output to go negative in response to the reactive effect of a capacitive load. An internal JFET connected between pin 5 (output) and pin 3allows the output to sink current. This current sink capability can also be useful when driving the capacitive inputs of some analog-to-digital converters which require the signalNOISE PERFORMANCENoise performance of the OPT101 is determined by the op amp characteristics, feedback components and photodiode capacitance. The typical performance curve “Output Noise Voltage vs Measurement Bandwidth” shows how the noise varies with R F and measured bandwidth (0.1Hz to the indicated frequency), when the output voltage minus the voltage on pin 3 is greater than approximately 50mV. Below this level, the output stage is powered down, and the effective bandwidth is decreased. This reduces the noise to approximately 1/3 the nominal noise value of 300µVrms, or 100µVrms. This enables a low level signal to be resolved.Noise can be reduced by filtering the output with a cutoff frequency equal to the signal bandwidth. This will improve signal-to-noise ratio. Also, output noise increases in proportion to the square root of the feedback resistance, while responsivity increases linearly with feedback resistance. Best signal-to-noise ratio is achieved with large feedback resistance. This comes with the trade-off of decreased bandwidth.The noise performance of the photodetector is sometimes characterized by Noise Effective Power (NEP). This is the radiant power that would produce an output signal equal to the noise level. NEP has the units of radiant power (watts), or Watts/√Hz to convey spectral information about the noise.The typical performance curve “Noise Effective Power” vs Measurement Bandwidth" illustrates the NEP for the OPT101.FIGURE 2. Bipolar Power Supply Circuit Connections./OPT1019SBBS002AThis capacitor eliminates gain peaking and prevents instability. The value of C EXT can be determined from the table in Figure 4. Values of R F , other than shown in the table,can be interpolated.FIGURE 4. Changing Responsivity with External Resistor.FIGURE 3. Dark Error (Offset) Adjustment Circuit.CHANGING RESPONSIVITYAn external resistor, R EXT , can be connected to set a different voltage responsivity. To increase the responsivity, this resistor can be placed in series with the internal 1M Ω (Figure 4a), or the external resistor can replace the internal resistor by not connecting pin 4 (Figure 4b). The second configuration also allows the circuit gain to be reduced below 106V/A by using external resistors of less than 1M Ω.Figure 4 includes tables showing the responsivity and bandwidth. For values of R F less than 1M Ω, an external capacitor, C EXT should be connected in parallel with R F .DARK ERRORSThe dark errors in the specification table include all sources.The dominant source of dark output voltage is the “pedestal”voltage applied to the non-inverting input of the op amp.This voltage is introduced to provide linear operation in the absence of light falling on the photodiode. Photodiode dark current is approximately 2.5pA and contributes virtually no offset error at room temperature. The bias current of the op amp's summing junction (– input) is approximately 165pA.The dark current will be subtracted from the amplifier's bias current, and this residual current will flow through the feedback resistor creating an offset. The effects of temperature on this difference current can be seen in the typical performance curve “(I BIAS – I DARK ) vs Temperature.” The dark output voltage can be trimmed to zero with the optional circuit shown in Figure 3. A low impedance offset driver (op amp) should be used to drive pin 8 because this node has signal-dependent currents./OPT10110SBBS002AApplications using a feedback resistor significantly larger than the internal 1M Ω resistor may require special consideration.Input bias current of the op amp and dark current of the photodiode increase significantly at higher temperatures. This increase combined with the higher gain (R F > 1M Ω) can cause the op amp output to be driven to ground at high temperatures.Such applications may require a positive bias voltage applied to pin 8 to ensure that the op amp output remains in the linear operating region when the photodiode is not exposed to light.Alternatively, a dual power supply can be used. The output may be negative when sensing dark conditions.LIGHT SOURCE POSITIONINGThe OPT101 is tested with a light source that uniformly illuminates the full area of the integrated circuit, including the op amp. Although IC amplifiers are light-sensitive to some degree, the OPT101 op amp circuitry is designed to minimize this effect. Sensitive junctions are shielded with metal, and the photodiode area is very large relative to the op amp input circuitry.If your light source is focused to a small area, be sure that it is properly aimed to fall on the photodiode. A narrowly focused beam falling on only the photodiode will provide improved settling times compared to a source that uniformly illuminates the full area of the die. If a narrowly focused light source were to miss the photodiode area and fall only on the op amp circuitry, the OPT101 would not perform properly.The large 0.09" x 0.09" (2.29mm x 2.29mm) photodiode area allows easy positioning of narrowly focused light sources.The photodiode area is easily visible, as it appears very dark compared to the surrounding active circuitry.The incident angle of the light source also effects the apparent sensitivity in uniform irradiance. For small incident angles, the loss in sensitivity is simply due to the smaller effective light gathering area of the photodiode (proportional to the cosine of the angle). At a greater incident angle, light is diffracted and scattered by the package. These effects are shown in the typical performance curve “Responsivity vs Incident Angle.”DYNAMIC RESPONSEUsing the internal 1M Ω resistor, the dynamic response of the photodiode/op amp combination can be modeled as a simple R • C circuit with a –3dB cutoff frequency of approximately 14kHz. The R and C values are 1M Ω and 11pF respectively. By using external resistors, with less than 3pF parasitic capacitance, the frequency response can be improved. An external 1M Ω resistor used in the configuration shown in Figure 4b will create a 23kHz bandwidth with the same 106V/A dc transimpedance gain. This yields a rise time of approximately 15µs (10% to 90%). Dynamic response is not limited by op amp slew rate. This is demonstrated by the dynamic response oscilloscope photographs showing virtually identical large-signal and small-signal response.Dynamic response will vary with feedback resistor value as shown in the typical performance curve “Responsivity vs Frequency.” Rise time (10% to 90%) will vary according to the –3dB bandwidth produced by a given feedback resistor value:t 0.35f r C=where:t r is the rise time (10% to 90%)f C is the –3dB bandwidthLINEARITY PERFORMANCEThe photodiode is operated in the photoconductive mode so the current output of the photodiode is very linear with radiant power throughout a wide range. Nonlinearity remains below approximately 0.05% up to 100µA photodiode current.The photodiode can produce output currents of 1mA or greater with high radiant power, but nonlinearity increases to several percent in this region.This very linear performance at high radiant power assumes that the full photodiode area is uniformly illuminated. If the light source is focused to a small area of the photodiode,nonlinearity will occur at lower radiant power.FIGURE 5. Three-Wire Remote Light Measurement./分销商库存信息:TIOPT101P OPT101P-J OPT101PG4 OPT101P-JG4。
A2004中文资料

NOTE: For detailed information on purchasing options, contact your local Allegro field applications engineer or sales representative.Allegro MicroSystems, Inc. reserves the right to make, from time to time, revisions to the anticipated product life cycle plan for a product to accommodate changes in production capabilities, alternative product availabilities, or market demand. The information included herein is believed to be accurate and reliable. However, Allegro MicroSystems, Inc. assumes no responsibility for its use; nor for any infringements of patents or other rights of third parties which may result from its use.Recommended Substitutions:High Voltage High Current Darlington ArraysA2003, A2004, A2023, A2024Date of status change: May 2, 2005Deadline for receipt of LAST TIME BUY orders: October 28, 2005These parts are in production but have been determined to be LAST TIME BUY . This classification indicates that the product is obsolete and notice has been given. Sale of this device is currently restricted to existing customer applications. The device should not be purchased for new design applications because of obsolescence in the near future. Samples are no longer st Time Buy2003 THRU 2024HIGH-VOLTAGE,HIGH-CURRENT DARLINGTON ARRAYSTest ApplicableLimits Characteristic Symbol Fig.DevicesTest Conditions Min.Typ.Max.Units Output Leakage CurrentI CEX1AA llV CE = 50 V, T A = 25°C —< 150µA V CE = 50 V, T A = 70°C—< 1100µA 1BULN2004A/LV CE = 50 V, T A = 70°C, V IN = 1.0 V—< 5500µA Collector-EmitterV CE(SAT)2A llI C = 100 mA, I B = 250 µA—0.9 1.1V Saturation Voltagel C = 200 mA, I B = 350 µA— 1.1 1.3V I C = 350 mA, I B = 500 µA— 1.3 1.6V Input CurrentI IN(ON)3ULN2003A/LV IN = 3.85 V —0.93 1.35mA ULN2004A/LV IN = 5.0 V —0.350.5mA V IN = 12 V— 1.0 1.45mA I IN(OFF)4A ll l C = 500 µA, T A = 70°C5065—µA Input VoltageV IN(ON)5ULN2003A/LV CE = 2.0 V, l C = 200 mA—— 2.4V V CE = 2.0 V, I C = 250 mA—— 2.7V V CE = 2.0 V, l C = 300 mA—— 3.0V ULN2004A/LV CE = 2.0 V, l C = 125 mA—— 5.0V V CE = 2.0 V, l C = 200 mA—— 6.0V V CE = 2.0 V, I C = 275 mA——7.0V V CE = 2.0 V, l C = 350 mA——8.0V Input Capacitance C IN —A ll —1525pF Turn-On Delay t PLH 8All 0.5 E IN to 0.5 E OUT —0.25 1.0µs Turn-Off Delay t PHL 8All 0.5 E IN to 0.5 E OUT —0.25 1.0µs Clamp DiodeI R 6A ll V R = 50 V, T A = 25°C ——50µA Leakage Current V R = 50 V, T A = 70°C——100µA Clamp Diode V F7AllI F = 350 mA—1.72.0VForward VoltageComplete part number includes suffix to identify package style: A = DIP, L = SOIC.Types ULN2003A, ULN2003L, ULN2004A, and ULN2004L ELECTRICAL CHARACTERISTICS at +25°C (unless otherwise noted).2003 THRU 2024HIGH-VOLTAGE,HIGH-CURRENTDARLINGTON ARRAYS115 Northeast Cutoff, Box 15036Worcester, Massachusetts 01615-0036 (508) 853-5000Test Applicable LimitsCharacteristic Symbol Fig.DevicesTest ConditionsMin.Typ.Max.Units Output Leakage CurrentI CEX1AA ll V CE = 95 V, T A = 25°C—< 150µA V CE = 95 V, T A = 70°C—< 1100µA 1BULN2024A/LV CE = 95 V, T A = 70°C, V IN = 1.0 V—< 5500µA Collector-EmitterV CE(SAT)2A llI C = 100 mA, I B = 250 µA—0.9 1.1V Saturation Voltagel C = 200 mA, I B = 350 µA— 1.1 1.3V I C = 350 mA, I B = 500 µA— 1.3 1.6V Input CurrentI IN(ON)3ULN2023A/LV IN = 3.85 V —0.93 1.35mA ULN2024A/LV IN = 5.0 V —0.350.5mA V IN = 12 V— 1.0 1.45mA I IN(OFF)4A ll l C = 500 µA, T A = 70°C5065—µA Input VoltageV IN(ON)5ULN2023A/LV CE = 2.0 V, l C = 200 mA—— 2.4V V CE = 2.0 V, I C = 250 mA—— 2.7V V CE = 2.0 V, l C = 300 mA—— 3.0V ULN2024A/LV CE = 2.0 V, l C = 125 mA—— 5.0V V CE = 2.0 V, l C = 200 mA—— 6.0V V CE = 2.0 V, I C = 275 mA——7.0V V CE = 2.0 V, l C = 350 mA——8.0V Input Capacitance C IN —A ll —1525pF Turn-On Delay t PLH 8All 0.5 E IN to 0.5 E OUT —0.25 1.0µs Turn-Off Delay t PHL 8All 0.5 E IN to 0.5 E OUT —0.25 1.0µs Clamp DiodeI R 6A ll V R = 95 V, T A = 25°C ——50µA Leakage Current V R = 95 V, T A = 70°C——100µA Clamp Diode V F7A llI F = 350 mA—1.72.0VForward VoltageComplete part number includes suffix to identify package style: A = DIP, L = SOIC.Types ULN2023A, ULN2023L, ULN2024A, and ULN2024LELECTRICAL CHARACTERISTICS at +25°C (unless otherwise noted).115 Northeast Cutoff, Box 15036Worcester, Massachusetts 01615-0036 (508) 853-5000Dwg. GP-067COLLECTOR-EMITTER SATURATION VOLTAGE Dwg. GP-068INPUT CURRENT IN µA2003 THRU 2024HIGH-VOLTAGE,HIGH-CURRENTDARLINGTON ARRAYS115 Northeast Cutoff, Box 15036Worcester, Massachusetts 01615-0036 (508) 853-5000PACKAGE DESIGNATOR “A”Dimensions in Inches (controlling dimensions)Dimension in Millimeters (for reference only)NOTES:1.Leads 1, 8, 9, and 16 may be half leads at vendor’s option.2.Lead thickness is measured at seating plane or below.3.Lead spacing tolerance is non-cumulative.4.Exact body and lead configuration at vendor’s option within limits shown.Dwg. MA-001-16A mm18Dwg. MA-001-16A in182003 THRU 2024HIGH-VOLTAGE,HIGH-CURRENT DARLINGTON ARRAYSPACKAGE DESIGNATOR “L”Dimensions in Inches (for reference only)Dimension in Millimeters (controlling dimensions)NOTES:1.Lead spacing tolerance is non-cumulative.2.Exact body and lead configuration at vendor’s option within limits shown.Dwg. MA-007-16A mm169Dwg. MA-007-16 in1692003 THRU 2024HIGH-VOLTAGE,HIGH-CURRENTDARLINGTON ARRAYS115 Northeast Cutoff, Box 15036Worcester, Massachusetts 01615-0036 (508) 853-5000The products described here are manufactured under one or more U.S. patents or U.S. patents pending.Allegro MicroSystems, Inc. reserves the right to make, from time to time, such departures from the detail specifications as may be required to permit improvements in the performance, reliability, ormanufacturability of its products. Before placing an order, the user is cautioned to verify that the information being relied upon is current.Allegro products are not authorized for use as critical components in life-support devices or systems without express written approval.The information included herein is believed to be accurate and reliable. However, Allegro MicroSystems, Inc. assumes no responsi-bility for its use; nor for any infringement of patents or other rights of third parties which may result from its use.元器件交易网。
2004_104_EC

COMMISSION DIRECTIVE2004/104/ECof14October2004adapting to technical progress Council Directive72/245/EEC relating to the radio interference (electromagnetic compatibility)of vehicles and amending Directive70/156/EEC on the approxi-mation of the laws of the Member States relating to the type-approval of motor vehicles andtheir trailers(Text with EEA relevance)THE COMMISSION OF THE EUROPEAN COMMUNITIES,Having regard to the Treaty establishing the European Community,Having regard to Council Directive70/156/EEC of6February 1970on the approximation of the laws of the Member States relating to the type-approval of motor vehicles and their trailers(1),and in particular Article13(2)thereof,Having regard to Council Directive72/245/EEC of20June 1972relating to the radio interference(electromagnetic compat-ibility)of vehicles(2),and in particular Article4thereof,Whereas:(1)Directive72/245/EEC is one of the separate directivesunder the type-approval procedure established byDirective70/156/EEC.(2)Since1995,when Directive72/245/EEC was amended,there has been a considerable increase in the number ofelectrical and electronic components fitted to motorvehicles.Such components now control not onlycomfort,information and entertainment devices buteven certain safety-relevant functions.(3)In the light of the experience gained since theamendment to Directive72/245/EEC,it is no longernecessary for after-market equipment unrelated to safetyfunctions to be regulated by a Directive specificallyconcerning electromagnetic compatibility(EMC)in theautomobile sector.For such equipment it is sufficientto obtain a Declaration of Conformity in accordancewith the procedures laid down in Council Directive89/336/EEC of3May1989on the approximation of thelaws of the Member States relating to electromagneticcompatibility(3)and in Directive1999/5/EC of theEuropean Parliament and of the Council of9March1999on radio equipment and telecommunicationsterminal equipment and the mutual recognition of theirconformity(4).(4)The EMC requirements and test provisions for electricaland electronic equipment have constantly been updatedthrough the standardisation work of the InternationalSpecial Committee on Radio Interference(CISPR)andthe International Organisation for Standardisation(ISO).It is therefore appropriate to refer in this Directive to thetest procedures outlined in the recent editions of therelevant standards.(5)Directive72/245/EEC should therefore be amendedaccordingly.(6)The amendments to Directive72/245/EEC have animpact on Directive70/156/EEC.It is thereforenecessary to amend that directive accordingly.(7)The measures provided for in this Directive are inaccordance with the opinion of the Committee for Adap-tation to Technical Progress established by Directive70/156/EEC,HAS ADOPTED THIS DIRECTIVE:Article1The Annexes to Directive72/245/EEC are replaced by the Annexes to this Directive.(1)OJ L42,23.2.1970,p.1.Directive as last amended by CommissionDirective2004/78/EC(OJ L153,30.4.2004,p.103).(2)OJ L152,6.7.1972,p.15.Directive as last amended by Directive95/54/EC of the European Parliament and of the Council(OJ L266,8.11.1995,p.1).(3)OJ L139,23.5.1989,p.19.Directive as last amended by Directive93/68/EEC(OJ L220,30.8.1993,p.1).(4)OJ L91,7.4.1999,p.10.Article21.With effect from1January2006,for vehicles, components or separate technical units which comply with the provisions laid down in Annexes I to X to Directive 72/245/EEC as amended by this Directive,no Member State may,on grounds relating to electromagnetic compatibility:(a)refuse to grant EC type-approval,or national type-approvalor(b)prohibit registration,sale or entry into service.2.With effect from1July2006,for a type of vehicle, component or separate technical unit where the requirements laid down in Annexes I to X to Directive72/245/EEC,as amended by this Directive,are not fulfilled,Member States, on grounds related to electromagnetic compatibility:(a)shall no longer grant EC type-approval,and(b)may refuse to grant national type-approval.3.With effect from1January2009,if the provisions laid down in Annexes I to X to Directive72/245/EEC,as amended by this Directive,are not fulfilled,Member States,on grounds related to electromagnetic compatibility:(a)shall consider certificates of conformity which accompanynew vehicles in accordance with the provisions of Directive 70/156/EEC to be no longer valid for the purposes of Article7(1)of that Directive;(b)may refuse the registration,sale or entry into service of newvehicles.4.As from1January2009,the provisions laid down in Annexes I to X to Directive72/245/EEC,as amended by this Directive,relating to electromagnetic compatibility,shall apply to components or separate technical units for the purposes of Article7(2)of Directive70/156/EEC.Article3Directive70/156/EEC is amended as follows:1.Annex I is amended as follows:(a)the following line is added to point0.5:‘Name and address of authorised representative,if any:’(b)the following point is inserted:‘12.7.Table of installation and use of RF transmitters in the vehicle(s),if applicable(see Annex I,3.1.8.):frequencybands(Hz)max.outputpower(W)antenna position at vehicle,specific conditions forinstallation and/or useThe applicant for type-approval must also supply,whereappropriate:Appendix1A list(with make(s)and type(s)of all electrical and/orelectronic components concerned by this Directive(seepoints2.1.9and2.1.10)and not previously listed.Appendix2Schematics or drawing of the general arrangement ofelectrical and/or electronic components(concerned bythis Directive)and the general wiring harnessarrangement.Appendix3Description of vehicle chosen to represent the typeBody style:Left or right hand drive:Wheelbase:Appendix4Relevant test report(s)supplied by the manufacturer orapproved/recognised laboratories for the purpose ofdrawing up the type-approval certificate.’2.In Annex III,Section A,the following line is added to point0.5:‘Name and address of authorised representative,if any:’.Article4Transposition1.Member States shall adopt and publish,by31December 2005at the latest,the laws,regulations and administrative provisions necessary to comply with this Directive.They shall forthwith communicate to the Commission the text of those provisions and a correlation table between those provisions and this Directive.They shall apply those provisions from1January2006.When Member States adopt those provisions,they shall contain a reference to this Directive or be accompanied by such reference on the occasion of their official publication.Member States shall determine how such reference is to be made.2.Member States shall communicate to the Commission the texts of the main provisions of national law,which they adopt in the field governed by this Directive.Article5This Directive shall enter into force on the20th day following that of its publication in the Official Journal of the European Union.Article6This Directive is addressed to the Member States.Done at Brussels,14October2004.For the CommissionOlli REHNMember of the CommissionLIST OF ANNEXESANNEX I Requirements to be met by vehicles and electrical/electronic subassemblies fitted to a vehicle Appendix1:List of standards referred to in this DirectiveAppendix2:Vehicle broadband reference limitsAntenna-vehicle separation:10mAppendix3:Vehicle broadband reference limitsAntenna-vehicle separation:3mAppendix4:Vehicle narrowband reference limitsAntenna-vehicle separation:10mAppendix5:Vehicle narrowband reference limitsAntenna-vehicle separation:3mAppendix6:Electrical/electronic subassemblyBroadband reference limitsAppendix7:Electrical/electronic subassemblyNarrowband reference limitsAppendix8:Model for the EC type-approval markANNEX II A Information document relating to EC type-approval of a vehicleANNEX II B Information document relating to EC type-approval of an electric/electronic subassemblyANNEX III A Model of EC type-approval certificateANNEX III B Model of EC type-approval certificateANNEX III C Model of attestation with regard to Annex I,3.2.9.ANNEX IV Method of measurement of radiated broadband electromagnetic emissions from vehiclesANNEX V Method of measurement of radiated narrowband electromagnetic emissions from vehiclesANNEX VI Method of testing for immunity of vehicles to electromagnetic radiationANNEX VII Method of measurement of radiated broadband electromagnetic emissions from electrical/electronic subas-sembliesAppendix1—Figure1:Open-area test site:electrical/electronic subassembly test area boundaryLevel clear area free from electromagnetic reflecting surfacesANNEX VIII Method of measurement of radiated narrowband electromagnetic emissions from electrical/electronic subassembliesANNEX IX Method(s)of testing for immunity of electrical/electronic subassemblies to electromagnetic radiation Appendix1—Figure1:800mm stripline testingAppendix1—Figure2:800mm stripline dimensionsAppendix2:Typical TEM cell dimensionsANNEX X Method(s)of testing for immunity to and emission of transients of electrical/electronic subassembliesREQUIREMENTS TO BE MET BY VEHICLES AND ELECTRICAL/ELECTRONIC SUBASSEMBLIES FITTED TO AVEHICLE1.SCOPEThis Directive applies to the electromagnetic compatibility of vehicles covered in Article1,being vehicles or trailers(hereinafter referred to as vehicles)as supplied by the vehicle manufacturer and to components or separate technical units intended to be fitted in vehicles.It covers:—requirements regarding the immunity to radiated and conducted disturbances for functions related to direct control of the vehicle,related to driver,passenger and other road users'protection and related to distur-bances,which would cause confusion to the driver or other road users,—requirements regarding the control of unwanted radiated and conducted emissions to protect the intended use of electrical or electronic equipment at own or adjacent vehicles or nearby,and the control ofdisturbances from accessories that may be retrofitted to the vehicle.2.DEFINITIONS2.1.For the purposes of this Directive:2.1.1.‘Electromagnetic compatibility’means the ability of a vehicle or component(s)or separate technical unit(s)tofunction satisfactorily in its electromagnetic environment without introducing intolerable electromagnetic disturbances to anything in that environment.2.1.2.‘Electromagnetic disturbance’means any electromagnetic phenomenon which may degrade the performance ofa vehicle or component(s)or separate technical unit(s),or of any other device,unit of equipment or systemoperated in vicinity of a vehicle.An electromagnetic disturbance may be electromagnetic noise,an unwanted signal or a change in the propagation medium itself.2.1.3.‘Electromagnetic immunity’means the ability of a vehicle or component(s)or separate technical unit(s)tooperate without degradation of performance in the presence of(specified)electromagnetic disturbances which includes wanted radio frequency signals from radio transmitters or radiated in-band emissions of industrial-scientific-medical(ISM)apparatus,internal or external to the vehicle.2.1.4.‘Electromagnetic environment’means the totality of electromagnetic phenomena existing at a given location.2.1.5.‘Broadband emission’means an emission,which has a bandwidth greater than that of a particular measuringapparatus or receiver(International Special Committee on Radio Interference(CISPR)25,2nd edition).2.1.6.‘Narrowband emission’means an emission which has a bandwidth less than that of a particular measuringapparatus or receiver(CISPR25,2nd edition).2.1.7.‘Electrical/electronic system’means(an)electrical and/or electronic device(s)or set(s)of devices together withany associated electrical connections which form part of a vehicle but which are not intended to be type-approved separately from the vehicle.2.1.8.‘Electrical/electronic subassembly’(ESA)means an electrical and/or electronic device or set(s)of devices intendedto be part of a vehicle,together with any associated electrical connections and wiring,which performs one or more specialised functions.An ESA may be approved at the request of a manufacturer or his authorised representative as either a‘component’or a‘separate technical unit(STU)’(see Directive70/156/EEC,Article2).2.1.9.‘Vehicle type’in relation to electromagnetic compatibility means vehicles which do not differ essentially in suchrespects as:2.1.9.1.the overall size and shape of the engine compartment;2.1.9.2.the general arrangement of the electrical and/or electronic components and the general wiring arrangement;2.1.9.3.the primary material of which the body or shell(if applicable)of the vehicle is constructed(for example,a steel,aluminium or fibreglass body shell).The presence of panels of different material does not change the vehicle type provided the primary material of the body is unchanged.However,such variations must be notified.2.1.10.An‘ESA type’in relation to electromagnetic compatibility means ESAs which do not differ in such essentialrespects as:2.1.10.1.the function performed by the ESA;2.1.10.2.the general arrangement of the electrical and/or electronic components,if applicable.2.1.11.‘Vehicle wiring harness’means supply voltage,bus system(e.g.CAN),signal or active antenna cables,which areinstalled by the vehicle manufacturer.2.1.12.Immunity-related functions are:(a)functions related to the direct control of the vehicle:—by degradation or change in engine,gear,brake,suspension,active steering,speed limitation devices,for example,—by affecting driver’s position,e.g.seat or steering wheel positioning,—by affecting driver’s visibility:e.g.dipped beam,windscreen wiper;(b)functions related to driver,passenger and other road-user protection:—e.g.airbag and safety restraint systems;(c)functions which,when disturbed,cause confusion to the driver or other road users:—optical disturbances:incorrect operation of e.g.direction indicators,stop lamps,end outline marker lamps,rear position lamp,light bars for emergency system,wrong information from warning indicators,lamps or displays related to functions in clauses(a)or(b)which might be observed in the direct view ofthe driver,—acoustical disturbances:incorrect operation of anti-theft alarm,horn,for example;(d)functions related to vehicle data bus functionality:—by blocking data transmission on vehicle data bus-systems,which are used to transmit data,required to ensure the correct functioning of other immunity-related functions;(e)functions which,when disturbed,affect vehicle statutory data:e.g.tachograph,odometer.3.APPLICATION FOR EC TYPE-APPROVAL3.1.Approval of a vehicle type3.1.1.The application for approval of a vehicle type,with regard to its electromagnetic compatibility pursuant toArticle3(4)of Directive70/156/EEC shall be submitted by the vehicle manufacturer.3.1.2.A model for the information document is given in Annex IIA.3.1.3.The vehicle manufacturer shall draw up a schedule describing all relevant vehicle electrical/electronic systems orESAs,body styles(1),variations in body material(1),general wiring arrangements,engine variations,left-hand/right-hand drive versions and wheelbase versions.Relevant vehicle electrical/electronic systems or ESAs are those which may emit significant broadband or narrowband radiation and/or those which are involved in immunity-related functions(see paragraph2.1.12of this Annex)of the vehicle.(1)If applicable.3.1.4.A representative vehicle shall be selected from this schedule for the purpose of being tested,in mutualagreement between the manufacturer and the competent authority.This vehicle shall represent the vehicle type(see Appendix1to Annex IIA).The choice of vehicle shall be based on the electrical/electronic systems offered by the manufacturer.One or more vehicles may be selected from this schedule for the purpose of being tested if it is considered by mutual agreement between the manufacturer and the competent authority that different electrical/electronic systems are included which are likely to have a significant effect on the vehicle's electromagnetic compatibility compared with the first representative vehicle.3.1.5.The choice of the vehicle(s)in conformity with paragraph3.1.4is limited to vehicle/electrical/electronic systemcombinations intended for actual production.3.1.6.The manufacturer may supplement the application with a report from tests,which have been carried out.Anysuch data provided may be used by the approval authority for the purpose of drawing up the type-approval certificate.3.1.7.If the technical service responsible for the type-approval test carries out the test itself,then a vehicle repre-sentative of the type to be approved,according to paragraph3.1.4shall be provided.3.1.8.The vehicle manufacturer must provide a statement of frequency bands,power levels,antenna positions andinstallation provisions for the installation of RF-transmitters,even if the vehicle is not equipped with RF-transmitter at time of type-approval.This should cover all mobile radio services normally used in vehicles.This information must be made publicly available following the type-approval.Vehicle manufacturers must provide evidence that vehicle performance is not adversely affected by such transmitter installations.3.2.Approval of a type of electrical/electronic subassembly(ESA)3.2.1.Applicability of this Directive to ESA:3.2.2.The application for approval of a type of ESA with regard to its electromagnetic compatibility pursuant toArticle3(4)of Directive70/156/EEC shall be submitted by the vehicle manufacturer or by the manufacturer of the ESA or his/her authorised representative.3.2.3.A model for the information document is given in Annex II B.3.2.4.The manufacturer may supplement the application with a report from tests which have been carried out.Anysuch data provided may be used by the approval authority for the purpose of drawing up the type-approval certificate.For equipment intended for installation in a vehicle,the manufacturer may supplement the appli-cation with the manufacturer’s Declaration of Conformity in line with the provisions of Directive99/5/EC or Directive89/336/EEC,the EMC test report and the instruction for the user giving guidance for installation of such equipment in vehicles.3.2.5.If the technical service responsible for the type-approval test carries out the test itself,then a sample of the ESAsystem representative of the type to be approved shall be provided,if necessary,after discussion with the manufacturer on,for example,possible variations in the layout,number of components,number of sensors.If the technical service deems it necessary,it may select a further sample.3.2.6.The sample(s)must be clearly and indelibly marked with the manufacturer’s trade name or mark and the typedesignation.3.2.7.Where applicable,any restrictions on use should be identified.Any such restrictions must be included inAnnexes II B and/or III B.3.2.8.ESAs which are brought to the market as spare parts need no type-approval if they are obviously marked as aspare part by an identification number and if they are identical and from the same manufacturer as the corresponding original equipment manufacturer(OEM)part for an already type-approved vehicle.ponents sold as aftermarket equipment and intended for the installation in motor vehicles need no type-approval if they are not related to immunity-related functions(Annex I,2.1.12).In this case a Declaration of Conformity according to the procedures of Directive89/336/EEC or1999/5/EC must be issued.Part of this declaration must be that the ESA fulfils the limits defined in paragraphs6.5,6.6,6.8and6.9of Annex I to this Directive.During a transition period of four years after coming into force of this Directive the responsible for placing on the market of such a product has to submit all relevant information and/or a sample to a technical service which will determine if the equipment is immunity-related or not.The result of the inspection shall be available within three weeks and not require additional testing.A document according to the example given in Annex IIIC shall be issued by the technical service within the same period.Member States shall report,by a date threeyears from the entry into force of this Directive,any cases of refusals on safety grounds.Based on the practical experience with this requirement and based on the reports submitted by Member States,it will be decided, according to the procedure referred to in Article13of Directive70/156/EEC,and before the end of the transition period,if this document is still required in addition to the Declaration of Conformity.4.TYPE-APPROVAL4.1.Routes to type-approval4.1.1.Type-approval of a vehicleThe following alternative routes to type-approval of a vehicle may be used at the discretion of the vehicle manufacturer.4.1.1.1.Approval of a vehicle installationA vehicle installation may achieve type-approval directly by following the provisions laid down in the relevantparts of paragraph6of this Annex.If this route is chosen by a vehicle manufacturer,no separate testing of electrical/electronic systems or ESAs is required.4.1.1.2.Approval of vehicle type by testing of individual ESAsA vehicle manufacturer may obtain approval for the vehicle by demonstrating to the approval authority that allthe relevant(see paragraph3.1.3of this Annex)electrical/electronic systems or ESAs have individually been approved in accordance with this Directive and have been installed in accordance with any conditions attached thereto.4.1.1.3.A manufacturer,if he/she wishes,may obtain approval according to this Directive if the vehicle has noequipment of the type which is subject to immunity or emission tests.Such approvals do not require testing.4.1.2.Type-approval of an ESAType-approval may be granted to an ESA to be fitted either to any vehicle type(component approval)or to a specific vehicle type or types requested by the ESA manufacturer(separate technical unit approval).4.1.3.ESAs,which are intentional RF transmitters,which have not received type-approval in conjunction with avehicle manufacturer,must be supplied with suitable installation guidelines.4.2.Granting of type-approval4.2.1.Vehicle4.2.1.1.If the representative vehicle fulfils the requirements of this Directive,EC type-approval pursuant to Article4(3),and if applicable,Article4(4)of Directive70/156/EEC shall be granted.4.2.1.2.A model for the EC type-approval certificate is given in Annex III A.4.2.2.ESA4.2.2.1.If the representative ESA system(s)fulfil(s)the requirements of this Directive,EC type-approval pursuant toArticle4(3),and if applicable,Article4(4)of Directive70/156/EEC shall be granted.4.2.2.2.A model for the EC type-approval certificates is given in Annex III B.4.2.3.In order to draw up the certificates referred to in paragraph4.2.1.2or4.2.2.2,the competent authority of theMember State granting the approval may use a report prepared by a test laboratory accredited to ISO17025 and recognised by the Approval Authority.4.3.Amendments to approvals4.3.1.In the case of amendments to approvals granted pursuant to this Directive,the provisions of Article5ofDirective70/156/EEC shall apply.4.3.2.Amendment of a vehicle type-approval by ESA addition or substitution4.3.2.1.Where a vehicle manufacturer has obtained approval for a vehicle installation and wishes to fit an additional orsubstitutional electrical/electronic system or ESA which has already received approval pursuant to this Directive, and which will be installed in accordance with any conditions attached thereto,the vehicle approval may be amended without further testing.The additional or substitutional electrical/electronic system or ESA shall be considered as part of the vehicle for conformity of production purposes.4.3.2.2.Where the additional or substitutional part(s)has(have)not received approval pursuant to this Directive,and iftesting is considered necessary,the whole vehicle shall be deemed to comply if the new or revised part(s)can be shown to comply with the relevant requirements of paragraph6or if,in a comparative test,the new part can be shown not to be likely to adversely affect compliance of the vehicle type.4.3.3.The addition of used ESAs,which are not type-approved according to this Directive because at their first timeof installation no type-approval was required,shall not invalidate the type-approval if the installation of such used ESAs is done according to the recommendations of the ESA and vehicle manufacturer.5.MARKING5.1.Every ESA conforming to a type approved under this Directive shall bear an EC type-approval mark.5.2.The EC type-approval mark shall consist ofa rectangle surrounding the lower case letter‘e’followed by the distinguishing number of the Member Statewhich has granted the EC component type-approval:1for Germany2for France3for Italy4for the Netherlands5for Sweden6for Belgium7for Hungary8for the Czech Republic9for Spain11for the United Kingdom12for Austria13for Luxembourg17for Finland18for Denmark20for Poland21for Portugal23for Greece24for Ireland26for Slovenia27for Slovakia29for Estonia32for Latvia36for Lithuania49for Cyprus50for MaltaIn the vicinity of the rectangle the‘base approval number’contained in section4of the type-approval number referred to in Annex VII of Directive70/156/EEC preceded by the two figures indicating the sequence number assigned to the latest major technical amendment to this Directive.The amendment sequence number and the component type-approval number shown on the certificate shall be separated by a single space.In this Directive the sequence number is03.5.3.The EC type-approval mark must be affixed to the main part of the ESA(e.g.the electronic control unit)insuch a way as to be clearly legible and indelible.5.4.An example of the EC type-approval mark is shown in Appendix8.5.5.No marking is required for electrical/electronic systems included in vehicle types approved by this Directive,andfor spare parts as defined in paragraph3.2.8.5.6.Markings on ESAs in compliance with paragraph5.3need not be visible when the ESA is installed in a vehicle.6.SPECIFICATIONS6.1.General specification6.1.1.A vehicle and its electrical/electronic system(s)or ESA(s)shall be so designed,constructed and fitted as toenable the vehicle,in normal conditions of use,to comply with the requirements of this Directive.6.1.1.1.A vehicle shall be tested for radiated emissions and for immunity to radiated disturbances.No tests forconducted emissions or immunity to conducted disturbances are required for vehicle type-approval.6.1.1.2.ESA(s)shall be tested for radiated and conducted emissions,for immunity to radiated and conducted distur-bances.6.1.2.Before testing,the technical service has to prepare a test plan in conjunction with the manufacturer,whichcontains at least mode of operation,stimulated function(s),monitored function(s),pass/fail criteria(s)and intended emissions.。
CNCA-01C-008:家用及类似用途固定式电器装置电器附件装壳

CNCA-01C-008:家用及类似用途固定式电器装置电器附件装壳第一篇:CNCA-01C-008:家用及类似用途固定式电器装置电器附件装壳编号:CNCA—01C—008:2001电气电子产品类强制性认证实施规则电路开关及保护或连接用电器装置家用和类似用途固定式电器装置电器附件外壳2001-12-07发布2002-05-01实施中国国家认证认可监督管理委员会发布目录1.适用范围 .......................................................................................................................... ................................. 3 2.认证模式 .......................................................................................................................... ................................. 3 3.认证的基本环节 .......................................................................................................................... ........................ 4 3.1认证的申请 .......................................................................................................................... ......................... 4 3.2型式试验 .......................................................................................................................... ............................. 4 3.3初始工厂审查 .......................................................................................................................... ..................... 4 3.4认证结果评价与批准 .......................................................................................................................... ......... 4 3.5获证后的监督 .......................................................................................................................... ..................... 4 4. 认证实施的基本要.............. 4 4.1 认证申请 .......................................................................................................................... ............................ 4 4.2 型式试验 .......................................................................................................................... ............................ 5 4.3初始工厂审查 .......................................................................................................................... ..................... 6 4.4认证结果评价与批准 .......................................................................................................................... ......... 7 4.5获证后的监督 .......................................................................................................................... ..................... 8 5.认证证书 .......................................................................................................................... .................................. 10 5.1认证证书的保持 .......................................................................................................................... ............... 10 5.2认证证书覆盖产品的扩展 .........................................................................................................................11 6.强制性产品认证标志的使用 .......................................................................................................................... .. 11 6.1准许使用的标志样式 .......................................................................................................................... ....... 12 6.2变形认证标志的使用 .......................................................................................................................... ....... 12 6.3 加施方式 .......................................................................................................................... .......................... 12 6.4 标志位置 .......................................................................................................................... .......................... 12 7.收费 .......................................................................................................................... ....................................... 12 附件........................................ 13 附件2 ............................................................................................................................ . (14)电气电子产品类强制性认证实施规则电路开关及保护或连接用电器装置家用和类似用途固定式电器装置电器附件外壳1.适用范围本规则涉及的产品为:户内或户外使用的额定电压不超过440V的家用和类似用途固定式电气装置电器附件外壳或外壳部件,亦适用于以安装或悬吊照明设备用的安装盒。
AMP04FSZ,AMP04FPZ,AMP04EPZ,AMP04FSZ-RL,AMP04FSZ-R7,AMP04FS-REEL7,AMP04ESZ-R7, 规格书,Datasheet 资料
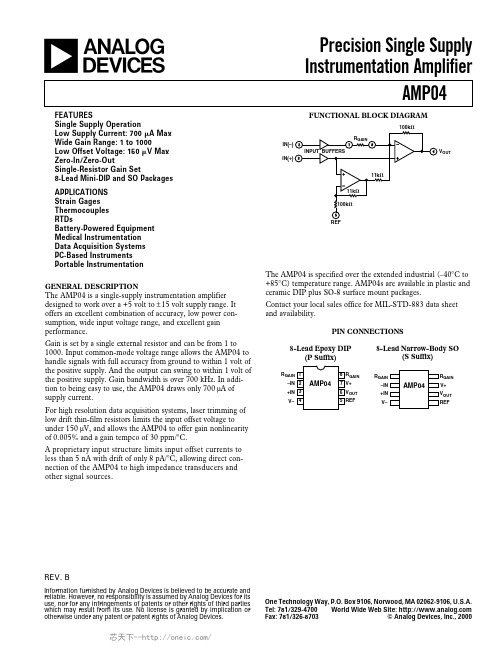
One Technology Way, P.O. Box 9106, Norwood, MA 02062-9106, U.S.A.
Tel: 781/329-4700 World Wide Web Site:
Fax: 781/326-8703
© Analog Devices, Inc., 2000
For high resolution data acquisition systems, laser trimming of low drift thin-film resistors limits the input offset voltage to under 150 µV, and allows the AMP04 to offer gain nonlinearity of 0.005% and a gain tempco of 30 ppm/°C.
1000 1 0.005 0.015 0.025 30
0.75 %
1.0 %
0.75
%
1000 V/V
%
%
%
50
ppm/°C
OUTPUT Output Voltage Swing High
Output Voltage Swing Low Output Current Limit
VOH
RL = 2 kΩ
Contact your local sales office for MIL-STD-883 data sheet and availability.
PIN CONNECTIONS
8-Lead Epoxy DIP (P Suffix)
8-Lead Narrow-Body SO (S Suffix)
25
ATTINY20-SSUR;中文规格书,Datasheet资料
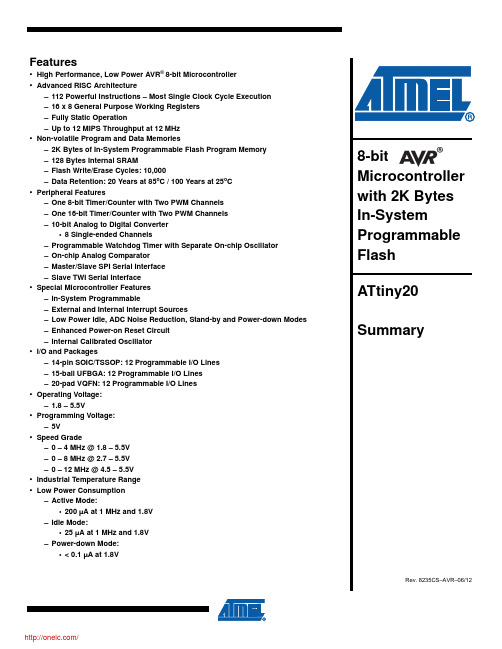
Features•High Performance, Low Power AVR® 8-bit Microcontroller •Advanced RISC Architecture–112 Powerful Instructions – Most Single Clock Cycle Execution –16 x 8 General Purpose Working Registers–Fully Static Operation–Up to 12 MIPS Throughput at 12 MHz•Non-volatile Program and Data Memories–2K Bytes of In-System Programmable Flash Program Memory–128 Bytes Internal SRAM–Flash Write/Erase Cycles: 10,000–Data Retention: 20 Years at 85o C / 100 Years at 25o C•Peripheral Features–One 8-bit Timer/Counter with Two PWM Channels–One 16-bit Timer/Counter with Two PWM Channels–10-bit Analog to Digital Converter•8 Single-ended Channels–Programmable Watchdog Timer with Separate On-chip Oscillator–On-chip Analog Comparator–Master/Slave SPI Serial Interface–Slave TWI Serial Interface•Special Microcontroller Features–In-System Programmable–External and Internal Interrupt Sources–Low Power Idle, ADC Noise Reduction, Stand-by and Power-down Modes –Enhanced Power-on Reset Circuit–Internal Calibrated Oscillator•I/O and Packages–14-pin SOIC/TSSOP: 12 Programmable I/O Lines–15-ball UFBGA: 12 Programmable I/O Lines–20-pad VQFN: 12 Programmable I/O Lines•Operating Voltage:–1.8 – 5.5V•Programming Voltage:–5V•Speed Grade–0 – 4 MHz @ 1.8 – 5.5V–0 – 8 MHz @ 2.7 – 5.5V–0 – 12 MHz @ 4.5 – 5.5V•Industrial Temperature Range•Low Power Consumption–Active Mode:•200 µA at 1 MHz and 1.8V–Idle Mode:•25 µA at 1 MHz and 1.8V–Power-down Mode:•< 0.1 µA at 1.8V 8-bit Microcontrollerwith 2K BytesIn-System ProgrammableATtiny20Summary28235CS–AVR–06/12ATtiny201.Pin ConfigurationsFigure 1-1.Pinout of ATtiny201.1Pin Description1.1.1VCCSupply voltage.1.1.2GNDGround.Table 1-1.Pinout ATtiny20 in UFBGA.1234A PA5PA6PB2B PA4PA7PB1PB3C PA3PA2PA1PB0DPA0GNDGNDVCC1234567141312111098VCC(PCINT8/TPICLK/T0/CLKI) PB0(PCINT9/TPIDATA/MOSI/SDA/OC1A) PB1(PCINT11/RESET) PB3(PCINT10/INT0/MISO/OC1B/OC0A/CKOUT) PB2(PCINT7/SCL/SCK/T1/ICP1/OC0B/ADC7) PA7(PCINT6/SS/ADC6) PA6GNDPA0 (ADC0/PCINT0)PA1 (ADC1/AIN0/PCINT1)PA2 (ADC2/AIN1/PCINT2)PA3 (ADC3/PCINT3)PA4 (ADC4/PCINT4)PA5 (ADC5/PCINT5)SOIC/TSSOP12345VQFN15141312112019181716678910NOTEBottom pad should be soldered to ground.DNC: Do Not ConnectD N C D N C G N D V C C D N C PA7 (ADC7/OC0B/ICP1/T1/SCL/SCK/PCINT7)PB2 (CKOUT/OC0A/OC1B/MISO/INT0/PCINT10)PB3 (RESET/PCINT11)PB1 (OC1A/SDA/MOSI/TPIDATA/PCINT9)PB0 (CLKI/T0/TPICLK/PCINT8)D N C D N C D N C P A 5P A 6Pin 16: PA6 (ADC6/SS/PCINT6)Pin 17: PA5 (ADC5/PCINT5)(PCINT4/ADC4) PA4(PCINT3/ADC3) PA3(PCINT2/AIN1/ADC2) PA2(PCINT1/AIN0/ADC1) PA1(PCINT0/ADC0) PA038235CS–AVR–06/12ATtiny201.1.3RESETReset input. A low level on this pin for longer than the minimum pulse length will generate a reset, even if the clock is not running and provided the reset pin has not been disabled. The min-imum pulse length is given in Table 20-4 on page 175. Shorter pulses are not guaranteed to generate a reset.The reset pin can also be used as a (weak) I/O pin.1.1.4Port A (PA7:PA0)Port A is a 8-bit bi-directional I/O port with internal pull-up resistors (selected for each bit). The Port A output buffers have symmetrical drive characteristics with both high sink and source capability. As inputs, Port A pins that are externally pulled low will source current if the pull-up resistors are activated. The Port A pins are tri-stated when a reset condition becomes active,even if the clock is not running.Port A has alternate functions as analog inputs for the ADC, analog comparator and pin change interrupt as described in “Alternate Port Functions” on page 49.1.1.5Port B (PB3:PB0)Port B is a 4-bit bi-directional I/O port with internal pull-up resistors (selected for each bit). The Port B output buffers have symmetrical drive characteristics with both high sink and source capability except PB3 which has the RESET capability. To use pin PB3 as an I/O pin, instead of RESET pin, program (‘0’) RSTDISBL fuse. As inputs, Port B pins that are externally pulled low will source current if the pull-up resistors are activated. The Port B pins are tri-stated when a reset condition becomes active, even if the clock is not running.The port also serves the functions of various special features of the ATtiny20, as listed on page 39.48235CS–AVR–06/12ATtiny202.OverviewATtiny20 is a low-power CMOS 8-bit microcontroller based on the compact AVR enhanced RISC architecture. By executing powerful instructions in a single clock cycle, the ATtiny20achieves throughputs approaching 1 MIPS per MHz allowing the system designer to optimize power consumption versus processing speed.Figure 2-1.Block DiagramThe AVR core combines a rich instruction set with 16 general purpose working registers and system registers. All registers are directly connected to the Arithmetic Logic Unit (ALU), allowing two independent registers to be accessed in one single instruction executed in one clock cycle.58235CS–AVR–06/12ATtiny20The resulting architecture is compact and code efficient while achieving throughputs up to ten times faster than conventional CISC microcontrollers.ATtiny20 provides the following features:•2K bytes of in-system programmable Flash •128 bytes of SRAM•Twelve general purpose I/O lines •16 general purpose working registers•An 8-bit Timer/Counter with two PWM channels •A 16-bit Timer/Counter with two PWM channels •Internal and external interrupts •An eight-channel, 10-bit ADC•A programmable Watchdog Timer with internal oscillator •A slave two-wire interface•A master/slave serial peripheral interface •An internal calibrated oscillator•Four software selectable power saving modesThe device includes the following modes for saving power:•Idle mode: stops the CPU while allowing the timer/counter, ADC, analog comparator, SPI, TWI, and interrupt system to continue functioning•ADC Noise Reduction mode: minimizes switching noise during ADC conversions by stopping the CPU and all I/O modules except the ADC•Power-down mode: registers keep their contents and all chip functions are disabled until the next interrupt or hardware reset•Standby mode: the oscillator is running while the rest of the device is sleeping, allowing very fast start-up combined with low power consumption.The device is manufactured using Atmel’s high density non-volatile memory technology. The on-chip, in-system programmable Flash allows program memory to be re-programmed in-system by a conventional, non-volatile memory programmer.The ATtiny20 AVR is supported by a suite of program and system development tools, including macro assemblers and evaluation kits.68235CS–AVR–06/12ATtiny203.General Information3.1ResourcesA comprehensive set of drivers, application notes, data sheets and descriptions on development tools are available for download at /avr.3.2Code ExamplesThis documentation contains simple code examples that briefly show how to use various parts of the device. These code examples assume that the part specific header file is included before compilation. Be aware that not all C compiler vendors include bit definitions in the header files and interrupt handling in C is compiler dependent. Please confirm with the C compiler documen-tation for more details.3.3Capacitive Touch SensingAtmel QTouch Library provides a simple to use solution for touch sensitive interfaces on Atmel AVR microcontrollers. The QTouch Library includes support for QTouch ® and QMatrix ® acquisi-tion methods.Touch sensing is easily added to any application by linking the QTouch Library and using the Application Programming Interface (API) of the library to define the touch channels and sensors.The application then calls the API to retrieve channel information and determine the state of the touch sensor.The QTouch Library is free and can be downloaded from the Atmel website. For more informa-tion and details of implementation, refer to the QTouch Library User Guide – also available from the Atmel website.3.4Data RetentionReliability Qualification results show that the projected data retention failure rate is much less than 1 PPM over 20 years at 85°C or 100 years at 25°C.3.5DisclaimerTypical values contained in this datasheet are based on simulations and characterization of other AVR microcontrollers manufactured on the same process technology.78235CS–AVR–06/12ATtiny204.Register SummaryAddressNameBit 7Bit 6Bit 5Bit 4Bit 3Bit 2Bit 1Bit 0Page0x3F SREG ITHSVNZCPage 140x3E SPH Stack Pointer High Byte Page 130x3D SPL Stack Pointer Low Byte Page 130x3C CCP CPU Change Protection BytePage 130x3B RSTFLR ––––WDRF BORF EXTRF PORF Page 370x3A MCUCR ICSC01ICSC00–BODS SM2SM1SM0SE Pages 28, 410x39OSCCAL Oscillator Calibration BytePage 230x38Reserved ––––––––0x37CLKMSR ––––––CLKMS1CLKMS0Page 220x36CLKPSR ––––CLKPS3CLKPS2CLKPS1CLKPS0Page 220x35PRR –––PRTWIPRSPIPRTIM1PRTIM0PRADCPage 290x34QTCSR QTouch Control and Status RegisterPage 60x33NVMCMD ––NVM Command Page 1700x32NVMCSR NVMBSY –––––––Page 1710x31WDTCSR WDIF WDIE WDP3–WDE WDP2WDP1WDP0Page 350x30SPCR SPIE SPE DORD MSTR CPOL CPHA SPR1SPR0Page 1350x2F SPSR SPIF WCOL ––––SSPS SPI2X Page 1370x2E SPDR SPI Data RegisterPage 1370x2D TWSCRA TWSHE–TWDIE TWASIETWEN TWSIE TWPME TWSME Page 1460x2C TWSCRB –––––TWAA TWCMD[1.0]Page 1470x2B TWSSRA TWDIFTWASIFTWCHTWRATWCTWBETWDIRTWASPage 1480x2A TWSA TWI Slave Address Register Page 1500x29TWSAM TWI Slave Address Mask RegisterPage 1510x28TWSD TWI Slave Data RegisterPage 1500x27GTCCR TSM ––––––PSR Page 1070x26TIMSK ICE1–OCIE1B OCIE1A TOIE1OCIE0B OCIE0A TOIE0Pages 76, 1030x25TIFR ICF1–OCF1B OCF1A TOV1OCF0B OCF0A TOV0Pages 76, 1040x24TCCR1A COM1A1COM1A0COM1B1COM1B0––WGM11WGM10Page 990x23TCCR1B ICNC1ICES1–WGM13WGM12CS12CS11CS10Page 1010x22TCCR1C FOC1AFOC1B––––––Page 1020x21TCNT1H Timer/Counter1 – Counter Register High Byte Page 1020x20TCNT1L Timer/Counter1 – Counter Register Low Byte Page 1020x1F OCR1AH Timer/Counter1 – Compare Register A High Byte Page 1030x1E OCR1AL Timer/Counter1 – Compare Register A Low Byte Page 1030x1D OCR1BH Timer/Counter1 – Compare Register B High Byte Page 1030x1C OCR1BL Timer/Counter1 – Compare Register B Low Byte Page 1030x1B ICR1H Timer/Counter1 - Input Capture Register High Byte Page 1030x1A ICR1L Timer/Counter1 - Input Capture Register Low BytePage 1030x19TCCR0A COM0A1COM0A0COM0B1COM0B0––WGM01WGM00Page 710x18TCCR0B FOC0AFOC0B––WGM02CS02CS01CS00Page 740x17TCNT0Timer/Counter0 – Counter Register Page 750x16OCR0A Timer/Counter0 – Compare Register A Page 750x15OCR0B Timer/Counter0 – Compare Register BPage 760x14ACSRA ACD ACBG ACO ACI ACIE ACIC ACIS1ACIS0Page 1090x13ACSRB HSEL HLEV ACLP –ACCE ACME ACIRS1ACIRS0Page 1100x12ADCSRA ADEN ADSC ADATE ADIF ADIE ADPS2ADPS1ADPS0Page 1260x11ADCSRB VDEN VDPD ––ADLAR ADTS2ADTS1ADTS0Page 1270x10ADMUX –REFSREFENADC0ENMUX3MUX2MUX1MUX0Page 1240x0F ADCH ADC Conversion Result – High Byte Page 1250x0E ADCL ADC Conversion Result – Low BytePage 1250x0D DIDR0ADC7D ADC6D ADC5D ADC4D ADC3D ADC2D ADC1D ADC0D Page 1280x0C GIMSK ––PCIE1PCIE0–––INT0Page 410x0B GIFR ––PCIF1PCIF0–––INTF0Page 420x0A PCMSK1––––PCINT11PCINT10PCINT9PCINT8Page 430x09PCMSK0PCINT7PCINT6PCINT5PCINT4PCINT3PCINT2PCINT1PCINT0Page 430x08PORTCR ––––––BBMB BBMA Page 580x07PUEB ––––PUEB3PUEB2PUEB1PUEB0Page 580x06PORTB ––––PORTB3PORTB2PORTB1PORTB0Page 590x05DDRB ––––DDRB3DDRB2DDRB1DDRB0Page 590x04PINB ––––PINB3PINB2PINB1PINB0Page 590x03PUEA PUEA7PUEA6PUEA5PUEA4PUEA3PUEA2PUEA1PUEA0Page 580x02PORTA PORTA7PORTA6PORTA5PORTA4PORTA3PORTA2PORTA1PORTA0Page 580x01DDRA DDRA7DDRA6DDRA5DDRA4DDRA3DDRA2DDRA1DDRA0Page 580x00PINAPINA7PINA6PINA5PINA4PINA3PINA2PINA1PINA0Page 5888235CS–AVR–06/12ATtiny20Note:1.For compatibility with future devices, reserved bits should be written to zero if accessed. Reserved I/O memory addressesshould never be written.2.I/O Registers within the address range 0x00 - 0x1F are directly bit-accessible using the SBI and CBI instructions. In theseregisters, the value of single bits can be checked by using the SBIS and SBIC instructions.3.Some of the Status Flags are cleared by writing a logical one to them. Note that, unlike most other AVRs, the CBI and SBIinstructions will only operation the specified bit, and can therefore be used on registers containing such Status Flags. The CBI and SBI instructions work with registers 0x00 to 0x1F only.98235CS–AVR–06/12ATtiny205.Instruction Set SummaryMnemonicsOperandsDescriptionOperation Flags#ClocksARITHMETIC AND LOGIC INSTRUCTIONSADD Rd, Rr Add without Carry Rd ← Rd + RrZ,C,N,V,S,H 1ADC Rd, Rr Add with Carry Rd ← Rd + Rr + C Z,C,N,V,S,H 1SUB Rd, Rr Subtract without Carry Rd ← Rd - Rr Z,C,N,V,S,H 1SUBI Rd, K Subtract Immediate Rd ← Rd - K Z,C,N,V,S,H 1SBC Rd, Rr Subtract with CarryRd ← Rd - Rr - C Z,C,N,V,S,H 1SBCI Rd, K Subtract Immediate with Carry Rd ← Rd - K - C Z,C,N,V,S,H 1AND Rd, Rr Logical ANDRd ← Rd • Rr Z,N,V,S 1ANDI Rd, K Logical AND with Immediate Rd ← Rd • K Z,N,V,S 1OR Rd, Rr Logical ORRd ← Rd v Rr Z,N,V,S 1ORI Rd, K Logical OR with Immediate Rd ← Rd v K Z,N,V,S 1EOR Rd, Rr Exclusive OR Rd ← Rd ⊕ Rr Z,N,V,S 1COM Rd One’s Complement Rd ← $FF − Rd Z,C,N,V,S 1NEG Rd Two’s Complement Rd ← $00 − Rd Z,C,N,V,S,H 1SBR Rd,K Set Bit(s) in Register Rd ← Rd v K Z,N,V,S 1CBR Rd,K Clear Bit(s) in Register Rd ← Rd • ($FFh - K)Z,N,V,S 1INC Rd Increment Rd ← Rd + 1Z,N,V,S 1DEC Rd DecrementRd ← Rd − 1 Z,N,V,S 1TST Rd Test for Zero or Minus Rd ← Rd • Rd Z,N,V,S 1CLR Rd Clear Register Rd ← Rd ⊕ Rd Z,N,V,S 1SER Rd Set Register Rd ← $FF None 1BRANCH INSTRUCTIONSRJMP kRelative Jump PC ← PC + k + 1None 2IJMP Indirect Jump to (Z)PC(15:0) ← Z, PC(21:16) ← 0None 2RCALL kRelative Subroutine Call PC ← PC + k + 1None 3/4ICALL Indirect Call to (Z)PC(15:0) ← Z, PC(21:16) ← 0None 3/4RET Subroutine Return PC ← STACK None 4/5RETI Interrupt Return PC ← STACKI 4/5CPSE Rd,Rr Compare, Skip if Equal if (Rd = Rr) PC ← PC + 2 or 3None 1/2/3CP Rd,Rr CompareRd − Rr Z, C,N,V,S,H 1 CPC Rd,Rr Compare with Carry Rd − Rr − C Z, C,N,V,S,H 1CPI Rd,K Compare with Immediate Rd − KZ, C,N,V,S,H 1SBRC Rr, b Skip if Bit in Register Cleared if (Rr(b)=0) PC ← PC + 2 or 3 None 1/2/3SBRS Rr, b Skip if Bit in Register is Set if (Rr(b)=1) PC ← PC + 2 or 3None 1/2/3SBIC A, b Skip if Bit in I/O Register Cleared if (I/O(A,b)=0) PC ← PC + 2 or 3 None 1/2/3SBIS A, b Skip if Bit in I/O Register is Set if (I/O(A,b)=1) PC ← PC + 2 or 3None 1/2/3BRBS s, k Branch if Status Flag Set if (SREG(s) = 1) then PC ←PC+k + 1None 1/2BRBC s, k Branch if Status Flag Cleared if (SREG(s) = 0) then PC ←PC+k + 1None 1/2BREQ k Branch if Equal if (Z = 1) then PC ← PC + k + 1None 1/2BRNE k Branch if Not Equal if (Z = 0) then PC ← PC + k + 1None 1/2BRCS k Branch if Carry Set if (C = 1) then PC ← PC + k + 1None 1/2BRCC k Branch if Carry Cleared if (C = 0) then PC ← PC + k + 1None 1/2BRSH k Branch if Same or Higher if (C = 0) then PC ← PC + k + 1None 1/2BRLO k Branch if Lower if (C = 1) then PC ← PC + k + 1None 1/2BRMI k Branch if Minus if (N = 1) then PC ← PC + k + 1None 1/2BRPL k Branch if Plusif (N = 0) then PC ← PC + k + 1None 1/2BRGE k Branch if Greater or Equal, Signed if (N ⊕ V= 0) then PC ← PC + k + 1None 1/2BRLT k Branch if Less Than Zero, Signed if (N ⊕ V= 1) then PC ← PC + k + 1None 1/2BRHS k Branch if Half Carry Flag Set if (H = 1) then PC ← PC + k + 1None 1/2BRHC k Branch if Half Carry Flag Cleared if (H = 0) then PC ← PC + k + 1None 1/2BRTS k Branch if T Flag Set if (T = 1) then PC ← PC + k + 1None 1/2BRTC k Branch if T Flag Cleared if (T = 0) then PC ← PC + k + 1None 1/2BRVS k Branch if Overflow Flag is Set if (V = 1) then PC ← PC + k + 1None 1/2BRVC k Branch if Overflow Flag is Cleared if (V = 0) then PC ← PC + k + 1None 1/2BRIE k Branch if Interrupt Enabled if ( I = 1) then PC ← PC + k + 1None 1/2BRID k Branch if Interrupt Disabled if ( I = 0) then PC ← PC + k + 1None 1/2BIT AND BIT-TEST INSTRUCTIONSLSL Rd Logical Shift Left Rd(n+1) ← Rd(n), Rd(0) ← 0Z,C,N,V,H 1LSR Rd Logical Shift Right Rd(n) ← Rd(n+1), Rd(7) ← 0Z,C,N,V 1ROL Rd Rotate Left Through Carry Rd(0)←C,Rd(n+1)← Rd(n),C ←Rd(7)Z,C,N,V,H 1ROR Rd Rotate Right Through Carry Rd(7)←C,Rd(n)← Rd(n+1),C ←Rd(0)Z,C,N,V 1ASR Rd Arithmetic Shift Right Rd(n) ← Rd(n+1), n=0..6Z,C,N,V 1SWAP Rd Swap Nibbles Rd(3..0)←Rd(7..4),Rd(7..4)←Rd(3..0)None 1BSETs Flag SetSREG(s) ← 1SREG(s)1108235CS–AVR–06/12ATtiny20BCLR sFlag ClearSREG(s) ← 0SREG(s)1SBI A, b Set Bit in I/O Register I/O(A, b) ← 1None 1CBI A, b Clear Bit in I/O RegisterI/O(A, b) ← 0None 1BST Rr, b Bit Store from Register to T T ← Rr(b)T 1BLD Rd, bBit load from T to Register Rd(b) ← TNone 1SEC Set Carry C ← 1C 1CLC Clear Carry C ← 0C 1SEN Set Negative Flag N ← 1N 1CLN Clear Negative Flag N ← 0N 1SEZ Set Zero Flag Z ← 1Z 1CLZ Clear Zero Flag Z ← 0Z 1SEI Global Interrupt Enable I ← 1I 1CLI Global Interrupt Disable I ← 0I 1SES Set Signed Test Flag S ← 1S 1CLS Clear Signed Test FlagS ← 0 S 1SEV Set Two’s Complement Overflow.V ← 1V 1CLV Clear Two’s Complement Overflow V ← 0 V 1SET Set T in SREG T ← 1T 1CLT Clear T in SREGT ← 0T 1SEH Set Half Carry Flag in SREG H ← 1H1CLHClear Half Carry Flag in SREG H ← 0H 1DATA TRANSFER INSTRUCTIONS MOV Rd, Rr Copy Register Rd ← RrNone 1LDI Rd, K Load Immediate Rd ← KNone 1LD Rd, X Load IndirectRd ← (X)None 1/2LD Rd, X+Load Indirect and Post-Increment Rd ← (X), X ← X + 1None 2LD Rd, - X Load Indirect and Pre-Decrement X ← X - 1, Rd ← (X)None 2/3LD Rd, Y Load IndirectRd ← (Y)None 1/2LD Rd, Y+Load Indirect and Post-Increment Rd ← (Y), Y ← Y + 1None 2LD Rd, - Y Load Indirect and Pre-Decrement Y ← Y - 1, Rd ← (Y)None 2/3LD Rd, Z Load IndirectRd ← (Z)None 1/2LD Rd, Z+Load Indirect and Post-Increment Rd ← (Z), Z ← Z+1None 2LD Rd, -Z Load Indirect and Pre-Decrement Z ← Z - 1, Rd ← (Z)None 2/3LDS Rd, k Store Direct from SRAM Rd ← (k)None 1ST X, Rr Store Indirect(X) ← RrNone 1ST X+, Rr Store Indirect and Post-Increment (X) ← Rr, X ← X + 1None 1ST - X, Rr Store Indirect and Pre-Decrement X ← X - 1, (X) ← Rr None 2ST Y, Rr Store Indirect(Y) ← RrNone 1ST Y+, Rr Store Indirect and Post-Increment (Y) ← Rr, Y ← Y + 1None 1ST - Y, Rr Store Indirect and Pre-Decrement Y ← Y - 1, (Y) ← Rr None 2ST Z, Rr Store Indirect(Z) ← RrNone 1ST Z+, Rr Store Indirect and Post-Increment.(Z) ← Rr, Z ← Z + 1None 1ST -Z, Rr Store Indirect and Pre-Decrement Z ← Z - 1, (Z) ← Rr None 2STS k, Rr Store Direct to SRAM (k) ← Rr None 1IN Rd, A In from I/O Location Rd ← I/O (A)None 1OUT A, Rr Out to I/O Location I/O (A) ← Rr None 1PUSH Rr Push Register on Stack STACK ← Rr None 2POPRdPop Register from Stack Rd ← STACKNone 2MCU CONTROL INSTRUCTIONSBREAK Break (see specific descr. for Break)None 1NOP No Operation None 1SLEEP Sleep(see specific descr. for Sleep)None 1WDRWatchdog Reset(see specific descr. for WDR)None1MnemonicsOperandsDescriptionOperation Flags#Clocks分销商库存信息: ATMELATTINY20-SSUR。
PA04中文资料

Rf
ULTRASONIC DRIVE
CONTROL LOGIC
Ri 1
12
2 PA04
11 10
7 R CL
TUNED TRANSFORMER
Sonar Transducer Driver
EXTERNAL CONNECTIONS
-INPUT
+INPUT
1
12
COMP
2
11
CC R C
3 4
10 TOP
PA04 • PA04A
ABSOLUTE MAXIMUM RATINGS SPECIFICATIONS
ABSOLUTE MAXIMUM RATINGS
SUPPLY VOLTAGE, +VS to –VS BOOST VOLTAGE
200V SUPPLY VOLTAGE +20V
OUTPUT CURRENT, within SOA
20A
POWER DISSIPATION, internal
200W
INPUT VOLTAGE, differential
±20V
INPUT VOLTAGE, common mode TEMPERATURE, pin solder - 10s
±VS 300°C
TEMPERATURE, junction2
APEX MICROTECHNOLOGY CORPORATION • TELEPHONE (520) 690-8600 • FAX (520) 888-3329 • ORDERS (520) 690-8601 • EMAIL prodlit@
艾睿欧 AICC-04, AIAP-01系列 铁氧体线圈 数据表说明书
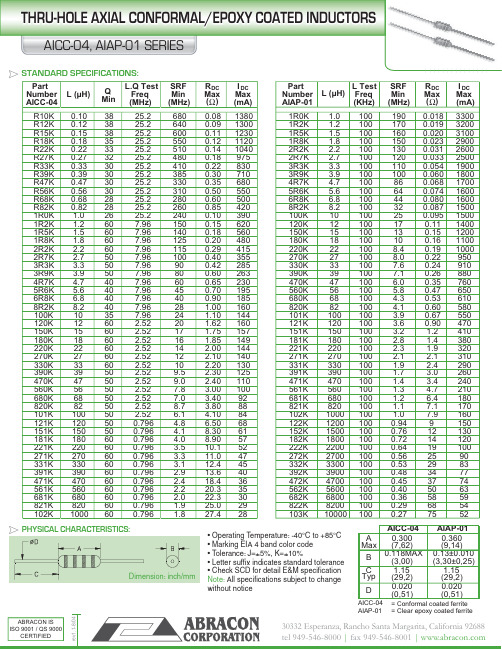
|||||||||||||||Dimension: inch/mmAIAP-01 = Clear epoxy coated ferritePart L (µH)Q L.Q Test SRF R DC I DC Part L (µH)L TestSRF R DC I DC Number Min Freq Min Max Max Number FreqMin Max Max AICC-04(MHz)(MHz) Ω (mA)( )( )AIAP-01(KHz)(MHz)Ω (mA)R10K 0.103825.26800.0813801R0K 1.01001900.0183300R12K 0.123825.26400.0913001R2K 1.21001700.0193200R15K 0.153825.26000.1112301R5K 1.51001600.0203100R18K 0.183525.25500.1211201R8K 1.81001500.0232900R22K 0.223325.25100.1410402R2K 2.21001300.0312600R27K 0.273225.24800.189752R7K 2.71001200.0332500R33K 0.333025.24100.228303R3K 3.31001100.0541900R39K 0.393025.23850.307103R9K 3.91001000.0601800R47K 0.473025.23300.356804R7K 4.7100860.0681700R56K 0.563025.23100.505505R6K 5.6100640.0741600R68K 0.682825.22800.605006R8K 6.8100440.0801600R82K 0.822825.22600.854208R2K 8.2100320.08715001R0K 1.02625.22400.10390100K 10100250.09515001R2K 1.2607.961500.15620120K 12100170.1114001R5K 1.5607.961400.18560150K 15100130.1512001R8K 1.8607.961250.20480180K 18100100.1611002R2K 2.2607.961150.29415220K 221008.40.1910002R7K 2.7507.961000.40355270K 271008.00.229503R3K 3.3507.96900.42285330K 331007.60.249103R9K 3.9507.96800.60263390K 391007.10.268804R7K 4.7407.96600.65230470K 47100 6.00.357605R6K 5.6407.96450.70195560K 56100 5.80.476506R8K 6.8407.96400.90185680K 68100 4.30.536108R2K 8.2407.9628 1.00160820K 82100 4.10.60580100K 10357.9624 1.10144101K 100100 3.90.67550120K 1260 2.5220 1.62160121K 120100 3.60.90470150K 1560 2.5217 1.75157151K 150100 3.2 1.2410180K 1860 2.5216 1.85149181K 180100 2.8 1.4380220K 2260 2.5214 2.00144221K 220100 2.3 1.9320270K 2760 2.5212 2.10140271K 270100 2.1 2.1310330K 3360 2.5210 2.20130331K 330100 1.9 2.4290390K 3950 2.529.5 2.30125391K 390100 1.7 3.0260470K 4750 2.529.0 2.40110471K 470100 1.4 3.4240560K 5650 2.527.8 3.00100561K 560100 1.3 4.7210680K 6850 2.527.0 3.4092681K 680100 1.2 6.4180820K 8250 2.528.7 3.8088821K 820100 1.17.1170101K 10050 2.52 6.1 4.1084102K 1000100 1.07.9160121K 120500.796 4.8 6.5068122K 12001000.949150151K 150500.796 4.18.3061152K 15001000.7612130181K 180600.796 4.08.9057182K 18001000.7214120221K 220600.796 3.510.152222K 22001000.6419100271K 270600.796 3.311.047272K 27001000.562590331K 330600.796 3.112.445332K 33001000.532983391K 390600.796 2.913.640392K 39001000.483477471K 470600.796 2.418.436472K 47001000.453774561K 560600.796 2.220.335562K 56001000.405063681K 680600.796 2.022.330682K 68001000.365859821K 820600.796 1.925.029822K 82001000.296854102K1000600.7961.827.428103K100001000.277552STANDARD SPECIFICATIONS:• Operating Temperature: -40°C to +85°C • Marking EIA 4 band color code • Tolerance: J=±5%, K=±10%• Letter suffix indicates standard tolerance • Check SCD for detail E&M specification Note: All specifications subject to change without noticePHYSICAL CHARACTERISTICS:|||||||||||||||• Operating Temperature: -45°C to +85°C • Wrap with UL heat shrink tube • Add -K for Lp tolerance ±10% • Lp measures at 100KHz, 0.1V RMS • Check SCD for detail E&M specification Note: All specifications subject to change without notice.PHYSICAL CHARACTERISTICS:STANDARD SPECIFICATIONS:A MaxB MaxC Typ DDIMENSION: inch/(mm)(0,81)(29,2)0.032(6,6)0.550.375(3,30±0,25)1.15(14,0)(9,53)0.260.13±0.0101.15(29,2)0.032(0,81)AIAP-02AIAP-03L (µH)R DC I DC L (µH)R DC I DC L (µH)R DC I DC ±10%Max Max ±10%Max Max ±10%Max Max Ω (A) ( ) Ω ( ) Ω ( ) Ω ( ) Ω ( ) Ω ( ) (A) (A)3.90.0197.3680.142 1.51200 2.650.354.70.022 6.3820.152 1.41500 3.450.335.60.024 5.61000.208 1.21800 4.030.296.80.026 5.31200.283 1.12200 4.480.278.20.028 4.51500.340 1.02700 5.400.24100.033 4.11800.3620.953300 6.560.22120.037 3.62200.4300.8639008.630.20150.040 3.32700.5570.7747009.660.18180.044 3.03300.6550.70560013.90.17220.050 2.73900.7720.64680016.30.15270.056 2.5470 1.150.59820020.80.14330.076 2.2560 1.270.541000026.40.14390.094 2.0680 1.610.491200029.90.11470.109 1.8820 1.960.441500042.50.10560.131 1.71000 2.300.401800048.30.096R88R2Part Number AIAP-023R96808202202701001201501804R75R6151181470560330390122152182471221271331391101121222272332392472562682822102561681821103123153183Part Number AIAP-02Part Number AIAP-02L (µH)R DC I DC L (µH)R DC I DC L (µH)R DC I DC ±10%Max Max ±10%Max Max ±10%Max Max (A) (A) (A)3.90.00715.51200.113 2.543900 2.750.4304.70.00813.91500.129 2.224700 3.190.3905.60.01112.61800.150 1.985600 3.920.3596.80.01311.62200.162 1.896800 5.690.3228.20.0179.892700.208 1.638200 6.320.293100.0198.703300.212 1.51100007.300.266120.0008.213900.281 1.391200010.00.257150.0227.344700.380 1.241500011.20.230180.023 6.645600.420 1.171800015.20.210220.026 6.076800.548 1.052200016.80.190270.027 5.368200.6550.972700018.60.171330.032 4.8310000.8440.873300026.70.155390.033 4.361200 1.040.793900029.00.143470.035 3.981500 1.180.704700031.80.131560.037 3.661800 1.560.645600042.60.119680.047 3.312200 2.000.586800046.90.108820.060 3.102700 2.060.538200064.90.0991000.0902.7933002.630.4710000071.70.09812000037.00.070Number Number 3904701802202703308R2100271331820101560680120150272332821102122152562682182222391471561681181221822103123153683183223273333823104124Part Part Part Number 393473563AIAP-033R94R75R66R8AIAP-03AIAP-03151121392472OPTIONS:• Bulk Pack is standard • Ammo Pack availableAPPLICATIONS:• Electronic Appliance • Automotive systemFEATURES:• Ferrite core with heat shrink tube • Wire wound construction|||||||||||||||PHYSICAL CHARACTERISTICS:STANDARD SPECIFICATIONS:PHYSICAL CHARACTERISTICS:Part L R DC I DCPart L R DC I DCPartL R DC Number (µH)Max Max Number (µH)Max Max Number (µH)Max AIAP-05-±10%(A)AIAP-05-±10%(A)AIAP-05-±10%Ω3R9 3.90.019 3.60680680.1450.881221200 2.654R7 4.70.027 3.30820820.1520.801521500 3.455R6 5.60.024 3.001011000.2080.731821800 4.036R8 6.80.026 2.701211200.2830.662222200 4.488R28.20.028 2.501511500.3400.602722700 5.90100100.033 2.301811800.3620.543323300 6.56120120.037 2.102212200.4300.4939239008.63150150.040 1.902712700.5570.45472470010.5180180.044 1.703313300.6650.40562560013.9220220.050 1.503913900.7720.37682680016.3270270.058 1.40471470 1.1500.34822820020.8330330.075 1.30561560 1.2700.311031000026.4390390.094 1.20681680 1.610.2801231200029.9470470.109 1.10821820 1.960.2601531500042.5560560.1400.971021000 2.300.2301831800048.3• Lp measured @ 1KHz, 0.1VRMS • Add K for 10% tolerance• Coils finished with 135°C polyolefin sleeving • Marking: Inductance value and tolerance • Operating Temperature: -55°C to +130°C• 5% inductance drop typical from initial value @ IDC • Add -AMMO for AMMO-PACK• UL Polyolefin T ubing, 2,500 VRMS isolation • Operating T emp: -55°C to 125°C • Lp measure at 10 KHz 0.1VRMS.• T olerance: J=±5%, K=±10%, L=±15%, M=20% • Add tolerance after the part no.• Check SCD for detail E&M specification • Marking: Inductance value and tolerance Note: All specifications subject to change without noticeDimension: inch/mmDimension: inch/mm( )Ω( )Ω( )OPTIONS:• Bulk Pack is standard • Ammo Pack availableAPPLICATIONS:• Electronic Appliance • Automotive systemFEATURES:• Ferrite core with UL tube • Wire wound construction Part No.L I DC R DC AIAP-04(µH)(A Max)(Ω Max)500-2.550 2.50.120101-2.1100 2.10.160251-1.8250 1.80.280501-1.6500160.420102-1.41000 1.40.600270-3.727 3.70.060500-3.150 3.10.085101-2.7100 2.70.120251-2.4250 2.40.200501-2.3500 2.30.32050-6.85 6.80.015100-6.110 6.10.021270-4.827 4.80.040500-4.350 4.30.050880-2.588 2.50.035101-4.2100 4.20.07050-9.359.30.010100-8.3108.30.015270-6.527 6.50.030500-6.150 6.10.040101-5.91005.90.0600.700/17,78 1.050/26,670.040/1,020.700/17,781.300/33,020.040/1,020.475/12,070.475/12,070.550/13,970.500/12,700.500/12,700.550/13,970.475/12,07 1.050/26,670.040/1,020.700/17,78 1.050/26,670.040/1,020.500/12,700.475/12,070.550/13,970.550/13,970.750/19,050.600/15,24 1.175/29,850.032/0,810.475/12,07 1.050/26,670.040/1,020.550/13,970.800/20,321.050/26,670.800/20,320.920/23,370.920/23,370.800/20,321.175/29,851.050/26,670.920/23,370.920/23,370.032/0,810.032/0,810.032/0,810.032/0,810.032/0,810.032/0,810.032/0,810.032/0,810.032/0,810.032/0,810.032/0,810.920/23,370.032/0,810.550/13,970.800/20,320.032/0,810.032/0,811.050/26,670.475/12,070.800/20,320.475/12,07Max A C Typical 0.032/0,81B Max 0.800/20,32。
费加罗技研株式会社 EC01 气体传感器评价试验箱 操作使用说明书
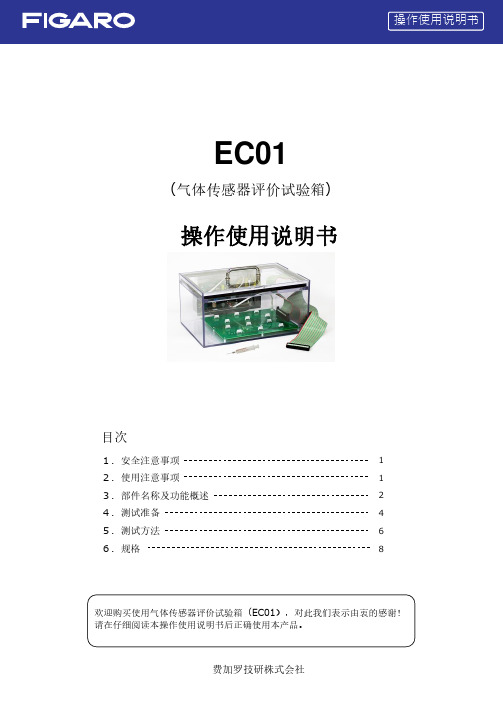
1.安全注意事项2.使用注意事项3.部件名称及功能概述4.测试准备5.测试方法6.规格目次欢迎购买使用气体传感器评价试验箱(EC01),对此我们表示由衷的感谢!请在仔细阅读本操作使用说明书后正确使用本产品。
112468费加罗技研株式会社EC01(气体传感器评价试验箱)操作使用说明书(1)(2)(3)(4)1. 安全注意事项请务必遵守2. 使用注意事项本产品是一种简易型的试验箱。
使用时请仔细盖紧盖板不能留有缝隙。
如果要进行很精确的气体测试时,请选用比本产品气密性更高的试验箱。
测试时如果将类似于气体报警器这样体积较大的设备放入试验箱的话,可能因为试验箱的有效容积减少而导致气体浓度制备出现误差。
由于氨气、VOC 、有机溶剂蒸汽等吸附性很强的气体很容易吸附在试验箱的内壁之上,因此本产品不适用于这些气体的测试用途。
吸附于箱内壁的气体液化后,有可能导致试验箱内的气体浓度下降。
有必要对吸附性很强的气体进行测试时,请选用箱内壁采用了气体不容易附着材质的试验箱,或对箱内壁进行过涂层处理的试验箱。
如果已经向本试验箱内注入了吸附性很强的气体,为了在使用后去除附着的气体,请用酒精擦拭试验箱内部,然后对内部用洁净空气进行长时间换气等的妥善处置。
如果在高温、低温或极度的低湿度与高湿度的室内环境进行测试的话,气体传感器的测定值可能会受到影响。
请在测试前对各型号传感器规格进行确认。
本试验箱没有防爆设计。
请勿在对气体爆炸下限为(LEL) 50%以上浓度的可燃性气体进行测试时使用。
本试验箱无法保证绝对完全的密闭状态。
请勿在对可能危及人身安全的高浓度毒性气体进行测试时使用。
在用于对可燃性气体进行测试时请务必注意防火措施,同时试验箱向外排气时请在可以充分换气的场所进行。
而且,为确保安全,请考虑采取设置气体报警器等措施。
尤其是在用于对毒性气体进行测试的用途时,请务必在能够保证充分换气的场所进行。
另外出于安全考虑,将试验箱中的气体排出时请注意避免人员吸入的同时,请在室外或排风罩内进行操作。
汉庭制造- Eclipse系列- NEMA 4, 12 单门壁挂式外壳说明书

Industrial Enclosures Wallmount Enclosures Application• Designed to enclose electrical and/or electronic equipment and protect against harsh, industrial environments for wallmount applications. • Impressive styling features like hidden hinges, attractive latching systems make the Eclipse a suitable addition to any high-tech equipment installation.• A wide range of sizes and practical accessories make this product line a complete package.Standards• UL 508 T ype 3R, 4, and 12• CSA T ype 3R, 4, and 12• Complies with• NEMA T ype 3R, 4, and 12• IEC 60529, IP66Construction• Formed 14 or 16 gauge steel.• Smooth, continuously weldedseams ground smooth.• Door stiffeners are provided whererequired for increased strength andrigidity - designed to also permitadditional mounting options.• Formed lip on enclosure to excludefl owing liquids and contaminants.• Door latches feature the addedsafety of quarter turn slot requiringuse of tool for opening.• Doors may be easily removedfor modifi cations and areinterchangeable.• Seamless poured-in place gasket.• Collar studs provided for mountinginner panel.• Includes hardware kit with panelmounting nuts and sealing washersfor wall mounting holes.• Bonding stud provided on doorand grounding stud installed inenclosure• Hinges are constructed from 304stainless steel.• Hinge pins are stainless steel.• Quarter turn latch and multi-pointhandle (key lockable) are zincdiecast with black epoxy fi nish.• Door alignment guide provided on36" wide enclosures.Finish• Cover and enclosure arephosphatized and fi nished with arecoatable powder inside and outwith choice of ANSI 61 smooth Gray(GY) or RAL7035 textured light gray(LG).Accessories• Air conditioners...see page349-367• Blowers...see page392• Breather kits...see page400-401• DIN rails...see page30• DIN rail mounting kit...see page30• Door stop kit...see page453• Drip shield kit...see page451• Filter fans...see page371-384• Gland Plates...see page446• Heaters...see page393-396• Handles...see page31• Inner panel...see page29• Quarter turn inserts and keys...see page31• Literature pocket...see page456• Mounting foot kit...see page31• Swing frame...see page30• Swing panel...see page29• Rear Hole Plugs...see page32• Replacement hinge pins...see page29• Replacement quarter turnassemblies...see page31• Thermostats...see page397• T ouch up paint...see page455• UL/CSA approved hardware kit...see page433• Padlock Adapter (EP A)...see page 434 Single Door withquarter turnsSingle Door with multi-pointlatching handle and quarter turnsSingle Door with latching handleIndustrial EnclosuresWallmount EnclosuresRefer to part number and dimension chart on next pageIndustrial Enclosures Wallmount EnclosuresIndustrial EnclosuresWallmount EnclosuresEN4SD241610GY EN4SD241610LG 241610161Qtr. T urn EP241622.214.221830EN4SD242010GY EN4SD242010LG 242010161Qtr. T urn EP242022.218.221836EN4SD242410GY EN4SD242410LG 242410142Qtr. Turn EP242422.222.221845EN4SD243010GY EN4SD243010LG 243010142Qtr. Turn EP243022.228.221853EN4SD302010GY EN4SD302010LG 302010142Qtr. Turn EP302028.218.231247EN4SD302410GY EN4SD302410LG 302410142Qtr. Turn EP302428.222.231253EN4SD303010GY EN4SD303010LG 303010142Qtr. Turn EP303028.228.231275EN4SD362410GY EN4SD362410LG 362410142Qtr. Turn EP362434.222.231570EN4SD363010GY EN4SD363010LG 363010142Qtr. T urn EP363034.228.231584EN4SD363610GY EN4SD363610LG 363610142Qtr. Turn EP363634.234.2315100EN4SD423010GY EN4SD423010LG 4230101413-point EP423040.228.2412107EN4SD423610GY EN4SD423610LG 4236101413-point EP423640.234.2412117EN4SD482410GY EN4SD482410LG 4824101413-point EP482446.222.241495EN4SD483010GY EN4SD483010LG 4830101413-point EP483046.228.2414120EN4SD483610GY EN4SD483610LG 4836101413-point EP483646.234.2414125EN4SD603610GY EN4SD603610LG 6036101413-point EP603658.234.2418150EN4SD201612GY EN4SD201612LG 201612161Qtr Turn EP201618.214.221432EN4SD202012GY EN4SD202012LG 202012161Qtr Turn EP202018.218.221434EN4SD242012GY EN4SD242012LG 242012161Qtr Turn EP242022.218.221838EN4SD242412GY EN4SD242412LG 242412142Qtr Turn EP242422.222.221847EN4SD302412GY EN4SD302412LG 302412142Qtr Turn EP302428.222.231257EN4SD303012GY EN4SD303012LG 303012142Qtr T urn EP303028.228.231280EN4SD362412GY EN4SD362412LG 362412142Qtr T urn EP362434.222.231562EN4SD363012GY EN4SD363012LG 363012142Qtr Turn EP363034.228.231591EN4SD363612GY EN4SD363612LG 363612142Qtr Turn EP363634.234.2315104EN4SD423012GY EN4SD423012LG 4230121413-point EP423040.228.2412111EN4SD423612GY EN4SD423612LG 4236121413-point EP423640.234.2412121EN4SD482412GY EN4SD482412LG 4824121413-point EP482446.222.241498EN4SD483612GY EN4SD483612LG 4836121413-point EP483646.234.2414148EN4SD603612GY EN4SD603612LG 6036121413-point EP603658.234.2418165EN4SD723012GY EN4SD723012LG 723012142Qtr Turn, 5-point EP723070.228.2516.5190EN4SD723612GY EN4SD723612LG 723612142Qtr T urn, 5-point EP723670.234.2516.5195EN4SD242016GY EN4SD242016LG 242016161Qtr Turn EP242022.218.221852EN4SD242416GY EN4SD242416LG 242416142Qtr Turn EP242422.222.221866EN4SD302416GY EN4SD302416LG 302416142Qtr Turn EP302428.222.231285EN4SD363016GY EN4SD363016LG 363016142Qtr T urn EP363034.228.2315102EN4SD423616GY EN4SD423616LG 4236161413-point EP423640.234.2412140EN4SD483616GY EN4SD483616LG 4836161413-point EP483646.234.2414148EN4SD603616GYEN4SD603616LG6036161413-point EP603658.234.2418200EN4SD723016GY EN4SD723016LG 723016142Qtr Turn, 5-point EP723070.228.2516.5215EN4SD723616GY EN4SD723616LG 723616142Qtr Turn, 5-point EP723670.234.2516.5217EN4SD242420GY EN4SD242420LG 242420142Qtr Turn EP242422.222.221870EN4SD302420GY EN4SD302420LG 302420142Qtr Turn EP302428.222.231282EN4SD363020GY EN4SD363020LG 363020142Qtr T urn EP363034.228.2315117EN4SD483620GY EN4SD483620LG 4836201413-point EP483646.234.2414165EN4SD603620GYEN4SD603620LG6036201413-point EP603658.234.2418210EN4SD723020GY EN4SD723020LG 723020142Qtr T urn, 5-point EP723070.228.2516.5217EN4SD302424GY EN4SD302424LG 302424142Qtr T urn EP302428.222.2312115EN4SD723024GY EN4SD723024LG723024142Qtr Turn, 5-pointEP723070.228.2516.5220。
F07A-0102,F10A-0102,F04B-0101, 规格书,Datasheet 资料

Integrated LCD
Each Fusion touch display includes an integrated LCD mechanically bonded to the touch sensor to create a single, easy-to-integrate module with high cosmetic quality. The Fusion touch firmware has been tuned to the LCD to ensure easy integration as a drop-in component.
1 mm center, 2 mm within 5 mm of edges 80–100 interrupts/sec. (single touch) Integrated on FPC (CoF) I2C (USB 2.0 Optional) Reference Driver for Linux, Android 6 pin ZIF
Benefits of Projected Capacitive Touch Technology
Touch Revolution’s Fusion displays offer a host of benefits over traditional touch sensor designs. In addition to improved optical transmittance, durable design, and integrated touch controllers; projective capacitive Fusion displays allow designers an out-of-the box experience with intuitive gesture capability, improved industrial design and a touch interface that is instantly recognizable by consumers.
BQ2004EPN;BQ2004HPN;BQ2004ESNTR;BQ2004HSN;BQ2004ESN;中文规格书,Datasheet资料

Features➤Fast charge and conditioning of nickel cadmium or nickel-metal hydride batteries ➤Hysteretic PWM switch-mode current regulation or gated con-trol of an external regulator ➤Easily integrated into systems or used as a stand-alone charger ➤Pre-charge qualification of tem-perature and voltage ➤Configurable,direct LED outputs display battery and charge status ➤Fast-charge termination by ∆tem-perature/∆time,peak volume de-tection,-∆V,maximum voltage,maximum temperature,and maxi-mum time ➤Optional top-off charge and pulsed current maintenance charging ➤Logic-level controlled low-power mode (<5µA standby current)General DescriptionThe bq2004E and bq2004H Fast Charge ICs provide comprehensive fast charge control functions together with high-speed switching power con-trol circuitry on a monolithic CMOS device.Integration of closed-loop current control circuitry allows the bq2004to be the basis of a cost-effective so-lution for stand-alone and system-integrated chargers for batteries of one or more cells.Switch-activated discharge-before-charge allows bq2004E/H-based charg-ers to support battery conditioning and capacity determination.High-efficiency power conversion is accomplished using the bq2004E/H as a hysteretic PWM controller for switch-mode regulation of the charg-ing current.The bq2004E/H may al-ternatively be used to gate an exter-nally regulated charging current.Fast charge may begin on application of the charging supply ,replacement of the battery ,or switch depression.For safety ,fast charge is inhibited unless/until the battery tempera-ture and voltage are within config-ured limits.Temperature,voltage,and time are monitored throughout fast charge.Fast charge is terminated by any of the following:nRate of temperature rise (∆T/∆t)n Peak voltage detection (PVD)n Negative delta voltage (-∆V)n Maximum voltage n Maximum temperature nMaximum timeAfter fast charge,optional top-off and pulsed current maintenance phases with appropriate display mode selections are available.The bq2004H differs from the bq2004E only in that fast charge,hold-off,and top-off time units have been scaled up by a factor of two,and the bq2004H provides different display selections.Timing differ-ences between the two ICs are illus-trated in Table 1.Display differ-ences are shown in Table 2.1Fast-Charge ICsbq2004E/HDCMDDischarge command DSEL Display select VSEL Voltage termination selectTM 1Timer mode select 1TM 2Timer mode select 2TCO Temperature cutoff TS Temperature sense BATBattery voltage1PN2004E01.eps16-Pin Narrow DIP or Narrow SOIC234 5678161514131211109INH DIS MOD V CC V SS LED 2LED 1SNSDCMD DSEL VSEL TM 1TM 2TCO TS BATSNS Sense resistor input LED 1Charge status output 1LED 2Charge status output 2V SS System ground V CC 5.0V ±10% power MOD Charge current control DISDischarge control outputINH Charge inhibit inputPin Connections SLUS081A - APRIL 2005Pin NamesPin DescriptionsDCMD Discharge-before-charge control inputThe DCMD input controls the conditionsthat enable discharge-before-charge.DCMDis pulled up internally.A negative-goingpulse on DCMD initiates a discharge to end-of-discharge voltage(EDV)on the BAT pin,followed by a new charge cycle start.TyingDCMD to ground enables automaticdischarge-before-charge on every new chargecycle start.DSEL Display select inputThis three-state input configures the chargestatus display mode of the LED1and LED2out-puts and can be used to disable top-off andpulsed-trickle.See Table2.VSEL Voltage termination select inputThis three-state input controls the voltage-termination technique used by thebq2004E/H.When high,PVD is active.When floating,-∆V is used.When pulled low,both PVD and-∆V are disabled.TM1–TM2Timer mode inputsTM1and TM2are three-state inputs thatconfigure the fast charge safety timer,voltagetermination hold-off time,“top-off”,andtrickle charge control.See Table1.TCO Temperature cut-off threshold inputInput to set maximum allowable batterytemperature.If the potential between TSand SNS is less than the voltage at the TCOinput,then fast charge or top-off charge is ter-minated.TS Temperature sense inputInput,referenced to SNS,for an externalthermister monitoring battery temperature. BAT Battery voltage inputBAT is the battery voltage sense input,refer-enced to SNS.This is created by a high-impedance resistor-divider network con-nected between the positive and the negativeterminals of the battery.SNS Charging current sense inputSNS controls the switching of MOD based onan external sense resistor in the currentpath of the battery.SNS is the reference po-tential for both the TS and BAT pins.IfSNS is connected to V SS,then MOD switcheshigh at the beginning of charge and low atthe end of charge.LED1–LED2Charge status outputsPush-pull outputs indicating chargingstatus.See Table2.Vss GroundV CC V CC supply input5.0V,±10%power input.MOD Charge current control outputMOD is a push-pull output that is used tocontrol the charging current to the battery.MOD switches high to enable charging cur-rent to flow and low to inhibit chargingcurrent flow.DIS Discharge control outputPush-pull output used to control an externaltransistor to discharge the battery beforecharging.INH Charge inhibit inputWhen low,the bq2004E/H suspends allcharge actions,drives all outputs to high im-pedance,and assumes a low-power opera-tional state.When transitioning from low tohigh,a new charge cycle is started.2bq2004E/HFunctional DescriptionFigure2shows a block diagram and Figure3shows a state diagram of the bq2004E/H.Battery Voltage and Temperature MeasurementsBattery voltage and temperature are monitored for maximum allowable values.The voltage presented on the battery sense input,BAT,should represent a two-cell potential for the battery under charge.A resistor-divider ratio of:RB1 RB2=N2- 1is recommended to maintain the battery voltage within the valid range,where N is the number of cells,RB1is the resistor connected to the positive battery terminal, and RB2is the resistor connected to the negative bat-tery terminal.See Figure1.Note:This resistor-divider network input impedance to end-to-end should be at least200kΩand less than1MΩ.A ground-referenced negative temperature coefficient ther-mistor placed in proximity to the battery may be used as a low-cost temperature-to-voltage transducer.The tempera-ture sense voltage input at TS is developed using a resistor-thermistor network between V CC and V SS.See Figure1.Both the BAT and TS inputs are referenced to SNS,so the signals used inside the IC are:V BAT-V SNS=V CELLandV TS-V SNS=V TEMPDischarge-Before-ChargeThe DCMD input is used to command discharge-before-charge via the DIS output.Once activated,DIS becomes active (high) until V CELL falls below V EDV,at which time DIS goes low and a new fast charge cycle begins.The DCMD input is internally pulled up to V CC(its inac-tive state).Leaving the input unconnected,therefore, results in disabling discharge-before-charge.A negative going pulse on DCMD initiates discharge-before-charge at any time regardless of the current state of the bq2004.If DCMD is tied to V SS,discharge-before-charge will be the first step in all newly started charge cycles. Starting A Charge CycleA new charge cycle is started by:1.Application of V CC power.2.V CELL falling through the maximum cell voltage,V MCV where:V MCV= 0.8∗V CC±30mV3.A transition on the INH input from low to high.If DCMD is tied low,a discharge-before-charge will be executed as the first step of the new charge cycle.Oth-erwise,pre-charge qualification testing will be the first step.The battery must be within the configured temperature and voltage limits before fast charging begins.The valid battery voltage range is V EDV<V BAT<V MCV where:V EDV= 0.4∗V CC±30mV3bq2004E/HFigure 1.Voltage and Temperature MonitoringThe valid temperature range is V HTF <V TEMP <V LTF ,where:V LTF = 0.4∗V CC ±30mVV HTF = [(1/3∗V LTF ) + (2/3∗V TCO )]±30mVV TCO is the voltage presented at the TCO input pin,and is configured by the user with a resistor divider between V CC and ground.The allowed range is 0.2to 0.4∗V CC .If the temperature of the battery is out of range,or the voltage is too low ,the chip enters the charge pending state and waits for both conditions to fall within their al-lowed limits.During the charge-pending mode,the IC first applies a top-off charge to the battery .The top-off charge,at the rateof of the fast charge,continues until the fast-charge are met or the top-off time-out period is exceeded.The IC then trickle charges until the fast-charge conditions are met.There is no time limit on the charge pending state;the charger remains in this state as long as the voltage or tempera-ture conditons are outside of the allowed limits.If the voltage is too high,the chip goes to the battery absent state and waits until a new charge cycle is started.Fast charge continues until termination by one or more of the six possible termination conditions:n Delta temperature/delta time (∆T/∆t)n Peak voltage detection (PVD)n Negative delta voltage (-∆V)n Maximum voltage n Maximum temperature nMaximum timePVD and -∆V TerminationThe bq2004E/H samples the voltage at the BAT pin once every 34s.When -∆V termination is selected,if V CELL is lower than any previously measured value by 12mV ±4mV (6mV/cell),fast charge is terminated.When PVD termination is selected,if V CELL is lower than any previ-ously measured value by 6mV ±2mV (3mV/cell),fast charge is terminated.The PVD and -∆V tests are valid in the range 0.4∗V CC <V CELL <0.8∗V CC .4bq2004E/HFigure 2.Block Diagram5VSEL InputVoltage TerminationLow DisabledFloat -∆V HighPVDVoltage SamplingEach sample is an average of voltage measurements.The IC takes 32measurements in PVD mode and 16measurements in -∆V mode.The resulting sample peri-ods (9.17ms and 18.18ms,respectively)filter out har-monics centered around 55Hz and 109Hz.This tech-nique minimizes the effect of any AC line ripple that may feed through the power supply from either 50Hz or 60Hz AC sources.Tolerance on all timing is ±16%.Temperature and Voltage Termination Hold-offA hold-off period occurs at the start of fast charging.During the hold-off period,-∆V and ∆T/∆t termination are disabled.The MOD pin is enabled at a duty cycle of 260µs active for every 1820µs inactive.This modulation results in an average rate 1/8th that of the fast charge rate.This avoids premature termination on the voltage spikes sometimes produced by older batteries when fast-charge current is first applied.Maximum voltage and maximum temperature terminations are not af-fected by the hold-off period.∆T/∆t TerminationThe bq2004E/H samples at the voltage at the TS pin every 34s,and compares it to the value measured two samples earlier.If V TEMP has fallen 16mV ±4mV or more,fast charge is terminated.The ∆T/∆t termination test is valid only when V TCO <V TEMP <V LTF .Temperature SamplingEach sample is an average of 16voltage measurements.The resulting sample period (18.18ms)filters out har-monics around 55Hz.This technique minimizes the ef-fect of any AC line ripple that may feed through the power supply from either 50Hz or 60Hz AC sources.Tol-erance on all timing is ±16%.Maximum Voltage,Temperature,and TimeAnytime V CELL rises above V MCV ,the LEDs go off and cur-rent flow into the battery ceases immediately .If V CELL then falls back below V MCV before t MCV =1.5s ±0.5s,the chip transitions to the Charge Complete state (maximum voltage termination).If V CELL remains above V MCV at the expiration of t MCV ,the bq2004E/H transitions to the Bat-tery Absent state (battery removal).See Figure 3.Maximum temperature termination occurs anytime V TEMP falls below the temperature cutoff threshold V TCO .Charge will also be terminated if V TEMP rises above the low temperature fault threshold,V LTF ,after fast charge begins.Corresponding Fast-ChargeRate TM1TM2Typical Fast-Charge Safety Time (min)Typical PVD, -∆V Hold-Off Time (s)Top-Off RatePulse-Trickle Rate Pulse-Trickle Period (Hz)2004E 2004H 2004E 2004H 2004E 2004H 2004E 2004H2004E2004HC/4C/8Low Low 325650137273Disabled Disabled Disabled C/2C/4Float Low 154325546546Disabled C/51215301C C/2High Low 77154273546Disabled C/5127.5152C 1C Low Float 3977137273Disabled C/512 3.757.54C 2C Float Float 193968137Disabled C/512 1.88 3.75C/2C/4High Float 154325546546C/16C/32C/51215301C C/2Low High 77154273546C/8C/16C/5127.5152C 1C Float High 3977137273C/4C/18C/512 3.757.54C2CHighHigh193968137C/2C/4C/5121.883.75Note:Typical conditions = 25°C,V CC = 5.0V .Table 1.Fast Charge Safety Time/Hold-Off/Top-Off Tablebq2004E/Hbq2004E/HTable 2.bq2004E/H LED Output SummaryNote:Pulse trickle is inhibited in Mode 2.6Maximum charge time is configured using the TM pin. Time settings are available for corresponding charge rates of C/4,C/2,1C,and2C.Maximum time-out termi-nation is enforced on the fast-charge phase,then reset, and enforced again on the top-off phase,if selected. There is no time limit on the trickle-charge phase.Top-off ChargeAn optional top-off charge phase may be selected to follow fast charge termination for the C/2through4C rates.This phase may be necessary on NiMH or other battery chemistries that have a tendency to terminate charge prior to reaching full capacity.With top-off en-abled,charging continues at a reduced rate after fast-charge termination for a period of time equal to 0.235∗the fast-charge safety time(See Table1.)Dur-ing top-off,the MOD pin is enabled at a duty cycle of 260µs active for every1820µs inactive.This modula-tion results in an average rate1/8th that of the fast charge rate.Maximum voltage,time,and temperature are the only termination methods enabled during top-off.Pulse-Trickle ChargePulse-trickle charging may be configured to follow the fast charge and optional top-off charge phases to com-pensate for self-discharge of the battery while it is idle in the charger.In the pulse-trickle mode,MOD is active for260µs of a period specified by the settings of TM1and TM2.See Table1.The resulting trickle-charge rate is C/512. Both pulse trickle and top-off may be disabled by tying TM1and TM2to V SS or by selecting Mode2in the dis-play.Charge Status IndicationCharge status is indicated by the LED1and LED2out-puts.The state of these outputs in the various charge cy-cle phases is given in Table2and illustrated in Figure3.In all cases,if V CELL exceeds the voltage at the MCV pin,both LED1and LED2outputs are held low regard-less of other conditions.Both can be used to directly drive an LED.Charge Current ControlThe bq2004E/H controls charge current through the MOD output pin.The current control circuitry is designed to sup-port implementation of a constant-current switching regulator or to gate an externally regulated current source.When used in switch mode configuration,the nominal regulated current is:I REG= 0.225V/R SNSCharge current is monitored at the SNS input by the voltage drop across a sense resistor,R SNS,between the low side of the battery pack and ground.R SNS is sized to provide the desired fast charge current.If the voltage at the SNS pin is less than V SNSLO,the MOD output is switched high to pass charge current to the battery.When the SNS voltage is greater than V SNSHI,the MOD output is switched low—shutting off charging current to the battery.V SNSLO= 0.04∗V CC±25mVV SNSHI= 0.05∗V CC±25mVWhen used to gate an externally regulated current source,the SNS pin is connected to V SS,and no sense re-sisitor is required.7bq2004E/Hbq2004E/HFigure 3.Charge Algorithm State Diagram8Absolute Maximum RatingsSymbol Parameter Minimum Maximum Unit NotesV CC V CC relative to V SS-0.3+7.0VV T DC voltage applied on any pin ex-cluding V CC relative to V SS-0.3+7.0VT OPR Operating ambient temperature-20+70°C CommercialT STG Storage temperature-55+125°CT SOLDER Soldering temperature-+260°C10 sec max.T BIAS Temperature under bias-40+85°CNote:Permanent device damage may occur if Absolute Maximum Ratings are exceeded.Functional opera-tion should be limited to the Recommended DC Operating Conditions detailed in this data sheet.Expo-sure to conditions beyond the operational limits for extended periods of time may affect device reliability.DC Thresholds(T A=T OPR;V CC±10%)Symbol Parameter Rating Tolerance Unit NotesV SNSHI High threshold at SNS result-ing in MOD = Low0.05*V CC±0.025VV SNSLO Low threshold at SNS result-ing in MOD = High0.04 * V CC ±0.025 VV LTF Low-temperature fault0.4*V CC±0.030V V TEMP ≥V LTF inhib-its/terminates charge V HTF High-temperature fault(1/3*V LTF) + (2/3*V TCO)±0.030V V TEMP≤V HTF inhibitschargeV EDV End-of-discharge voltage0.4*V CC±0.030V V CELL<V EDV inhibitsfast chargeV MCV Maximum cell voltage0.8*V CC±0.030V V CELL>V MCV inhibits/terminates chargeV THERM TS input change for∆T/∆tdetection-16±4mV V CC= 5V,T A= 25°C-∆V BAT input change for-∆Vdetection-12±4mV V CC= 5V,T A= 25°CPVD BAT input change for PVDdetection-6±2mV V CC= 5V,T A= 25°Cbq2004E/H9Recommended DC Operating Conditions(T A= T OPR)Symbol Condition Minimum Typical Maximum Unit NotesV CC Supply voltage 4.5 5.0 5.5VV BAT Battery input0-V CC VV CELL BAT voltage potential0-V CC V V BAT- V SNSV TS Thermistor input0-V CC VV TEMP TS voltage potential0-V CC V V TS- V SNSV TCO Temperature cutoff0.2*V CC-0.4*V CC V Valid∆T/∆t rangeV IHLogic input high 2.0--V DCMD,INHLogic input high V CC- 0.3--V TM1, TM2, DSEL, VSEL V ILLogic input low--0.8V DCMD,INHLogic input low--0.3V TM1, TM2, DSEL, VSELV OH Logic output high V CC- 0.8--V DIS, MOD, LED1, LED2,I OH≤-10mAV OL Logic output low--0.8V DIS,MOD,LED1,LED2,I OL≤10mAI CC Supply current-13mA Outputs unloadedI SB Standby current--1µA INH= V ILI OH DIS,LED1,LED2,MOD source-10--mA@V OH= V CC- 0.8VI OL DIS,LED1,LED2,MOD sink10--mA@V OL= V SS+ 0.8VI LInput leakage--±1µA INH, BAT, V = V SS to V CC Input leakage50-400µA DCMD, V = V SS to V CCI IL Logic input low source--70µA TM1, TM2, DSEL, VSEL,V = V SS to V SS+ 0.3VI IH Logic input high source-70--µA TM1, TM2, DSEL, VSEL,V = V CC- 0.3V to V CCI IZ Tri-state-2-2µA TM1,TM2,DSEL,and VSEL should be left disconnected (floating)for Z logic input stateNote:All voltages relative to V SS except as noted. bq2004E/H10分销商库存信息:TIBQ2004EPN BQ2004HPN BQ2004ESNTR BQ2004HSN BQ2004ESN BQ2004ESNTRG4 BQ2004HSNTR BQ2004HSNTRG4BQ2004EPNG4 BQ2004ESNG4。
EC12E2430401 增量类型绝对类型 194 电磁编码器说明书
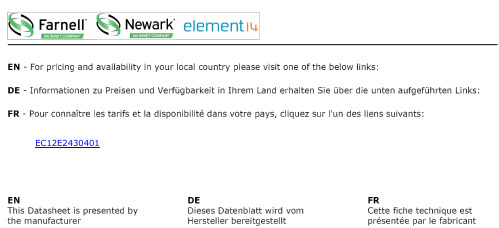
EC12E2430401Incremental Type Absolute Type194Power Push Slide Rotary Encoders Jog Shuttle Telephone-hook Detector Vibration Sensors Dual-in-line Package Type Multi Control Devices TACTInsulated shaft type with a push-on switch and other features has a wide variety of applications.A 12mm sized unit achieved high resolution,12 pulse /12detent and 24 pulse / 24 detent.Used a new structure for the shaft and bushing, and achieved a high precision, responsive system.Also available with a 0.5 mm push switch.Incremental type.0.5mA 5V DCWithout detentOther15,000 cycles 30,000 cyclesRating ItemsSpecificationsOperating lifeFeaturesTypical SpecificationsProducts LineControls for image and sound devices, including DVD players, mini component stereos, CD players, portable audio players and monitorsControls for audio mixers and electronic instrumentsApplicationsProducts No.DrawingNo.Minimum packingunit pcs.Detent torque ResolutionLength ofoperating section mm21,2001313123131VerticalNumber of detent 1224WithoutStandard 3 to 20 mN m1520251517.520258.520258.520252025Lightest jog 3 2 mN mStandard 3 to 20 mN mLightest jog 3 2 mN mLight 10mN m max.Standard 25 15 mN mEC12E1220407EC12E1220406EC12E1220405EC12E1240405EC12E1240406EC12E1220301EC12E1240301EC12E24204A7EC12E24204A2EC12E24204A8EC12E24204A9EC12E2420301EC12E24404A8EC12E24404A6EC12E2440301EC12E243040420EC12E24104A6EC12E2430401With High Collar TypeOperatingforce of switch N Travel of push-onswitchmm Operatingdirection12248.58.512mm Size Insulated Shaft Type Encoder VarietyEC12E SeriesIncremental Type Absolute Type195PowerPush Slide RotaryEncodersJog Shuttle Telephone -hookDetector Vibration Sensors Dual-in-line Package Type Multi Control Devices TACT75153.523.5surfaceMounting ø6.6(0.6)(0.8)12.4(8.2)14(10.2)13.2ø64.53.5LM1R 15(5)(0.8)23.5ø6.8ø64.5Mounting surface1412.4(8.2)(10.2)13.2Products LineWith Switch Type Products No.Drawing No.Numberof detent Resolution Length of operating section (mm)4Vertical241220252520302530Standard 3 to 20 mN mStandard 25 15 mN mHeavy 40 15 mN m2412WithoutEC12E2420802EC12E1220813EC12E2420801EC12E2430804EC12E2420803EC12E2430803EC12E2460802Operating force of switch NTravel of push-on switchmm Operating direction 5Vertical24Standard 3 to 20 mN mLightest jog 3 2 mN m 360.5242020252025EC12E2424407EC12E24244A3EC12E2424404EC12E2444400EC12E24444A33017.5EC12E24244A4EC12E24444A2Detenttorque950Minimum packingunit (pcs.)1,200Minimum packing unit (pcs.)Products No.Drawing No.Number of detent Resolution Length of operating section (mm)Operatingforce of switch N Travel of push-on switchmm Operating direction Detenttorque No nuts or washers attached. If necessary, contact us.NoteFor other products, check varieties on P.197For other detailed specifications, see P.198Dimensions7.552.12213.2BA C 3-ø1 hole13.2227.52.15A C B3-ø1 holeModelStyleShort shaftNo.12LM117.5R 152072512PC board mounting holedimensionsViewed from mounting faceUnit : mmWith Bushing Type 12mm Size Insulated Shaft Type Encoder Variety EC12E SeriesIncremental Type Absolute Type196Power Push Slide Rotary Encoders Jog Shuttle Telephone-hook DetectorVibration Sensors Dual-in-line Package Type Multi Control Devices TACTDimensionsUnit : mm3.58.55 2.651.2(0.6)2ø63.5(0.8)ø6.6Mounting surface1412.4(8.2)ø3.15(10.2)13.25.22.113.2227.52.15A C B3-ø1 holeModelStyleHollow shaftNo.3PC board mounting holedimensionsViewed from mounting face13.223-ø122.15C A B7.5holeWith bushing42.50.47XX Y Locating lug detailY With push-on switch512mm Size Insulated Shaft Type Encoder Variety EC12E SeriesL 77LM12025R 17121230123017.5LM1R 152********12.4(8.2)142Mounting surface3.5M9G 0.75L 3.55.5LM14.5ø6(10.2)13.281R 13.5LM16(5)R 10.5(0.8)23.5ø6.8Switch travelMounting surface1412.4(8.2)(10.2)13.24.5ø6D E13.222A C D EB577.52.15-ø1 holeIncremental Type Absolute Type197Power Push Slide Rotary EncodersJog ShuttleTelephone -hookDetector Vibration Sensors Dual-in-line Package Type Multi Control Devices TACTVarietyShaft DimensionsFlat TypeUnit : mmWith high collar typeLM 1R 14.50.5ø6LM 1R 117.52022.5255771212303.54.5ø613.525.5L BLM 1Mounting surfaceR 1With bushing typeLM 1R 120253035L B7712127121212Vertical typeDetail dimensionsExcept 12 detent.Detail dimensions 12mm Size Insulated Shaft EncodersIncrementalType Absolute Type198Power Push Slide RotaryEncoders Jog Shuttle Telephone-hook Detector Vibration Sensors Dual-in-line Package Type Multi Control Devices TACT50V ACVoltage proof Products Specifications5V DC RRTerminal BTerminal ATerminal CEncoder Test circuitttV V 5VON ONOFF Output waveformSliding directiont : Masking time to avoid chattering˚/s Items12mm size insulated shaft encodersStandard detentWithout detentWith switchOperating temperature range–10 to 605mA At R = 10kChattering :3ms max.Bounce :2ms max.V1 V2 1.5V max.–40 3 for 240h 300 or less, or within 3s80N50N3 2mN m, 10mN m max.3 20mN m, 40 15mN m3 to 20mN m25 15mN m260 5 , 5 1s85 3 for 240h40 2 , 90 to 95%RH for 240h30,000cycles15,000cycles30,000cycles50V DC 10M min.Maximum operating currentResistive loadElectrical performanceMechanical performanceDurabilityEnvironmental performanceRating Output signalOutput waveSliding noiseRotational torqueDetent torque Push-pull strengthRotational lifeColdDry heat Damp heatResistanceto solderingheatManual solderingDip soldering Reflow solderingInsulation resistance0.5mA 5V DCOutput of A and B signals, proportionate to phase differenceA signalB signal Detent stabillity pointWhen the switch is providedCW directionOFFONONOFFPush-on Switch SpecificationsItems12mm size insulated shaft encodersSwitch circuit the number of contactSingle pole and single throw Push-on0.5mm 0.40.33N or 61.5 1.01mA 5V DC100m for initial period; 200m after rotational life20,000 times min.Travel of switch Operating force of switchRatingContact resistance Operating life12mm Size Insulated Shaft Type EncoderEC12E2430401。