确保并联机床定位精度的几项措施
数控机床工作台的定位精度检测与调整技巧

数控机床工作台的定位精度检测与调整技巧数控机床工作台是现代制造业中不可或缺的重要设备,其定位精度直接关系到加工零件的质量和精度。
本文将为大家介绍数控机床工作台的定位精度检测与调整技巧。
一、定位精度检测方法1. 平面定位精度检测:将工作台移动到机床最大行程的两端,将测量时的测头放置在工作台上,并对两个端点进行平面度测量。
根据测量结果,计算平均偏差,以评估工作台的平面定位精度。
2. 垂直定位精度检测:将工作台移动到最高点或最低点,将测量时的测头放置在工作台上,并对工作台进行垂直度测量。
根据测量结果,计算垂直度偏差,以评估工作台的垂直定位精度。
3. 水平定位精度检测:将工作台移动到机床最大行程的两端,将测量时的测头放置在工作台上,并对两个端点进行水平度测量。
根据测量结果,计算平均偏差,以评估工作台的水平定位精度。
4. 位移重复性检测:将工作台移动到同一个位置,并多次测量工作台的定位偏差。
根据测量结果,计算位移重复性误差,以评估工作台的定位精度。
二、定位精度调整技巧1. 调整导轨与滑块:导轨与滑块是数控机床工作台的关键部件,直接影响着定位精度。
通过调整导轨与滑块之间的间隙,减小摩擦力,可以提高定位精度。
调整时需仔细测量每个位置的间隙,并确保在规定范围内。
2. 调整传动系统:传动系统的精度也是影响工作台定位精度的重要因素。
可以通过调整传动装置的齿轮啮合间隙、传动带的张力以及传动链条的松紧度来提高定位精度。
3. 检查并更换磨损部件:长时间使用后,机床工作台的关键部件可能会出现磨损,导致定位精度下降。
及时检查并更换磨损的部件,可以恢复工作台的定位精度。
4. 调整液压系统:液压系统的稳定性对工作台的定位精度有重要影响。
可以通过调整液压泵的工作压力、检查液压缸的密封状况,保证液压系统的正常工作,提高工作台的定位精度。
5. 关注温度变化:温度变化也会对工作台的定位精度造成影响。
数控机床工作台应放置在稳定的温度环境中,并定期检查温度变化对定位精度的影响,必要时进行调整或采取温度补偿措施。
【VIP专享】如何提高数控机床各轴的定位精度和重复定位精度
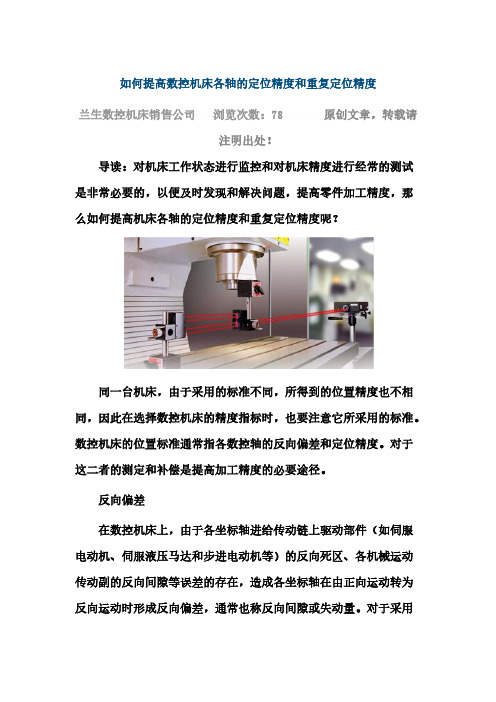
如何提高数控机床各轴的定位精度和重复定位精度兰生数控机床销售公司浏览次数:78 原创文章,转载请注明出处! 导读:对机床工作状态进行监控和对机床精度进行经常的测试是非常必要的,以便及时发现和解决问题,提高零件加工精度,那么如何提高机床各轴的定位精度和重复定位精度呢? 同一台机床,由于采用的标准不同,所得到的位置精度也不相同,因此在选择数控机床的精度指标时,也要注意它所采用的标准。
数控机床的位置标准通常指各数控轴的反向偏差和定位精度。
对于这二者的测定和补偿是提高加工精度的必要途径。
反向偏差 在数控机床上,由于各坐标轴进给传动链上驱动部件(如伺服电动机、伺服液压马达和步进电动机等)的反向死区、各机械运动传动副的反向间隙等误差的存在,造成各坐标轴在由正向运动转为反向运动时形成反向偏差,通常也称反向间隙或失动量。
对于采用半闭环伺服系统的数控机床,反向偏差的存在就会影响到机床的定位精度和重复定位精度,从而影响产品的加工精度。
在G01切削运动时,反向偏差会影响插补运动的精度,若偏差过大就会造成“圆不够圆,方不够方”的情形;而在G00快速定位运动中,反向偏差影响机床的定位精度,使得钻孔、镗孔等孔加工时各孔间的位置精度降低。
同时,随着设备投入运行时间的增长,反向偏差还会随因磨损造成运动副间隙的逐渐增大而增加,因此需要定期对机床各坐标轴的反向偏差进行测定和补偿。
【反向偏差的测定】 反向偏差的测定方法:在所测量坐标轴的行程内,预先向正向或反向移动一个距离并以此停止位置为基准,再在同一方向给予一定移动指令值,使之移动一段距离,然后再往相反方向移动相同的距离,测量停止位置与基准位置之差。
在靠近行程的中点及两端的三个位置分别进行多次测定(一般为七次),求出各个位置上的平均值,以所得平均值中的最大值为反向偏差测量值。
在测量时一定要先移动一段距离,否则不能得到正确的反向偏差值。
测量直线运动轴的反向偏差时,测量工具通常采有千分表或百分表,若条件允许,可使用双频激光干涉仪进行测量。
确保并联机床定位精度的几项措施

确保并联机床定位精度的几项措施
保证并联机床定位精度是机床制造商确保质量的重要环节。
以下是确保并联机床定位精度的几项措施:
首先,应确保机床本身的精度,例如主轴精度、滑块精度等,精度越高,定位精度越好。
此外,要定期校准机床,以确保定位精度不会随时间变化而降低。
其次,要使用高精度的零件。
零件的精度是影响机床定位精度的重要因素,因此,机床制造商应使用高精度的零件,以确保机床定位精度。
此外,应采用高精度的检测仪器,以确保机床定位精度。
机床制造商应使用高精度的检测仪器,以便更好地检测机床的定位精度,并采取相应的措施来纠正精度问题。
另外,应检查机床的接口,以确保其精度。
机床的接口精度也会影响机床定位精度,因此,机床制造商应定期检查接口,以确保其精度,以确保机床定位精度。
总之,确保并联机床定位精度是机床制造商确保质量的重要环节,要做到这一点,机床制造商应采取以上几项措施:确保机床本身的精度;使用高精度的零件;采用高精度的检测仪器;检查机床的接口。
只有采取这些措施,才能保证机床定位精度。
机床的精度和稳定性控制

机床的精度和稳定性控制机床是制造业中的关键设备,对于制造出高质量的产品至关重要。
机床的精度和稳定性作为机床本身的质量指标,在生产过程中起着重要作用。
本文将探讨机床精度和稳定性控制的相关内容。
一、机床精度控制1.1机床粗定位误差控制机床的粗定位误差主要是由伺服驱动和机械传动误差等因素造成的,因此需要通过以下措施来控制:(1)超前补偿技术超前补偿技术是通过补偿误差来预先调整控制量,使之达到更好的响应性和稳定性。
在机床的控制系统中,超前补偿器可以根据机床传动特性进行自动校正,并将得到的校正结果输入给控制器,以实现误差的补偿。
(2)全闭合环控制全闭合环控制是指机床精度控制中完全采用闭环控制,将伺服驱动系统、传动部件和测量系统全部组成机床控制系统环路,以实现更高的精度。
1.2机床加工误差控制机床加工误差主要包括切削力变化和温度变化造成的变形误差。
为了控制机床加工误差,可以采取以下措施:(1)加强机床的刚度加强机床的刚度可以提高机床的稳定性、减小振动,从而降低加工误差。
(2)加工划分技术加工划分是将一个规定的点阵划分成若干个小面,在加工小面时分别进行加工,从而降低加工误差。
二、机床稳定性控制机床的稳定性主要指机床在加工过程中的稳定性和静态稳定性。
以下措施可以提高机床稳定性:2.1结构设计机床的结构设计应保证机床加工过程中的稳定性和静态稳定性。
例如,采用支持点分离、刚度大的结构和铸铁导轨都可以提高机床的稳定性。
2.2伺服系统设计机床的伺服系统也是影响机床稳定性的重要因素。
伺服系统的速度响应速度和调节性能都需要得到优化设计。
2.3自适应控制自适应控制针对机床稳定性强相关的控制环节,通过对机床稳定性的分析和建模实现对机床稳定性的控制。
三、结论机床的精度和稳定性对于机械制造业的发展至关重要,机床的粗定位误差、加工误差和机床的稳定性都是机床精度和稳定性的关键因素。
通过机床结构、伺服系统设计和控制合理的自适应控制来优化控制系统,可以提高机床的精度和稳定性,达到更高水平的加工效果。
机床定位精度和重复定位精度标准

机床定位精度和重复定位精度标准摘要:一、机床定位精度和重复定位精度的定义二、机床定位精度和重复定位精度的标准三、影响机床定位精度和重复定位精度的因素四、机床定位精度和重复定位精度的检测方法五、总结正文:一、机床定位精度和重复定位精度的定义机床定位精度是指机床在执行加工任务时,刀具在工件上的实际加工位置与加工程序中设定的理论位置之间的误差。
而重复定位精度则是指机床在多次执行同样的加工任务时,其加工结果的重复性和一致性。
二、机床定位精度和重复定位精度的标准在我国,机床定位精度和重复定位精度的标准主要遵循《GB/T 17421.2-2000 机床检验通则第2 部分:数控轴线的定位精度和重复定位精度的确定》这一标准。
此外,还有一些其他标准,如GB/T 18400.5-2010《加工中心检验条件第5 部分:工件夹持托板的定位精度和重复定位精度》等。
三、影响机床定位精度和重复定位精度的因素机床定位精度和重复定位精度受到许多因素的影响,包括机床的设计、材料、加工工艺、操作者技术水平等。
其中,丝杆导轨等机床零部件的精度和刚度是影响机床定位精度和重复定位精度的重要因素。
四、机床定位精度和重复定位精度的检测方法为了确保机床的定位精度和重复定位精度符合标准要求,通常需要使用专业的检测设备进行检测。
其中,激光干涉仪是一种常用的检测工具。
通过多次测量,计算出定位精度和重复定位精度的平均值和标准差,从而判断机床的精度是否达标。
五、总结机床定位精度和重复定位精度是评估机床性能的重要指标,其标准主要遵循《GB/T 17421.2-2000 机床检验通则第2 部分:数控轴线的定位精度和重复定位精度的确定》等标准。
机床定位精度和重复定位精度的检测方法通常使用激光干涉仪进行。
解决机床使用中常见问题的技巧与方法

解决机床使用中常见问题的技巧与方法机床是一种用于加工各种金属材料的设备,广泛应用于制造业。
然而,在机床使用过程中,常常会遇到一些问题,如加工误差、设备故障等。
本文将介绍一些解决机床使用中常见问题的技巧与方法,帮助读者提高生产效率和加工质量。
一、调整机床的几何精度机床的几何精度是影响加工质量的重要因素。
在使用中,可能会出现一些偏差,如轴线和导轨的错位、平行度不准确等。
解决这些问题的方法包括:1. 定期检查和校准机床的几何精度,保持其稳定性。
2. 采用适当的调整工具,如数控机床能通过系统操作界面进行参数调整。
3. 使用高精度的测量仪器,定期进行测量并及时调整。
4. 遵循正确的操作规程,避免机床受到撞击或过载等情况。
二、选择合适的切削工艺参数切削工艺参数直接关系到加工质量和效率。
常见问题包括过高的切削速度、偏离理论加工参数等。
解决这些问题的方法有:1. 根据材料性质和加工件的形状、尺寸等要求,选择合适的切削工艺参数,如刀具转速、进给速度等。
2. 定期检查和维护刀具的磨损情况,及时更换磨损严重的刀具。
3. 使用先进的刀具润滑剂,减少切削摩擦和热变形,提高切削效果。
4. 根据加工件的要求,合理选择切削策略,如粗加工和精加工的切削方式不同。
三、保养并调整机床的液压系统机床的液压系统是其正常运转的重要组成部分,常见问题包括液压系统漏油、压力不稳等。
解决这些问题的方法有:1. 定期检查液压系统的油液状态和压力变化情况,确保正常运行。
2. 及时更换液压系统的密封件,防止漏油和压力损失。
3. 定期清洗液压系统中的滤芯,避免堵塞影响液压系统的工作。
4. 根据机床的使用情况,及时调整液压系统的工作参数,确保其稳定性。
四、加强设备维护和管理设备维护和管理是解决机床使用中常见问题的关键。
以下是一些建议:1. 建立完善的设备维护和管理制度,包括设备保养计划、维修记录等。
2. 对设备进行定期保养,如清洁设备、润滑设备、检查电气系统等。
机床精度的提高和调试技术

机床精度的提高和调试技术机床作为制造业的重要基础设施,对于工业生产的质量和效率有着至关重要的作用。
而机床的精度和调试技术则是保证机床功能稳定与精准的关键。
因此,如何提高机床的精度以及选择正确的调试技术,成为现代制造业的重要课题之一。
一、机床精度的分类和提高技术机床精度是指机床在加工过程中能达到的准确度,具体包括位置精度、重复定位精度、几何精度、平面度、圆度等多个方面。
1.提高位置精度机床的位置精度是机床各个可动部件和刀具锥尺之间的距离差异。
在机床使用中,常会出现因为工作台、刀具的摆动等问题导致位置精度出现偏差。
解决该问题,需要选用优质的滑轨和机床床身材质,尽量减少机床零部件的变形和磨损,同时严格控制加工过程中的温度变化,以确保机床的位置精度。
2.提高重复定位精度重复定位精度指的是机床在多次工件加工过程中,工件能在相同的位置加工。
提高重复定位精度的关键是减少机床零部件在各种因素影响下的误差,包括加工力、热变形、机床震动等。
针对这些因素,可以通过优化机床床身结构、选用高品质的刀具和夹具,加强机床的稳定性,进而提高机床的重复定位精度。
3.提高几何精度几何精度主要包括平行度、垂直度、角度等方面,是衡量机床的精度的重要指标。
在加工过程中,机床的工作台、刀具、刀柄等部位的变形都会影响到几何精度。
要提高几何精度,需要由专业技术人员进行测试分析,发现并排除问题。
二、常用机床调试技术随着人们对机床精度的要求越来越高,机床调试技术也在不断提高。
下面介绍一些常用的机床调试技术:1.加工误差检查法加工误差检查法是通过加工检测以发现机床误差问题的调试方法,一般是将工序分成多道工序,将要检测的工件进行多次加工,通过检测每种工序的精度,可以得出机床加工误差的位置与情况。
2.锤击校准法锤击校准法是一种简单易行的机床调整方法,采用金属锤轻击机床或工件,通过听觉判断与震动感觉来进行校准。
这种方法不需要任何特殊的设备,操作简单,但需要专业技术人员进行操作。
并联机构精度评估

并联机构精度评估并联机构精度评估并联机构是一种由多个连杆组成的力学结构,常用于工业机械和机器人的设计中。
评估并联机构的精度对于确保其性能和功能的可靠性至关重要。
下面将按照逐步思考的方式,介绍如何进行并联机构精度评估。
第一步:确定评估指标首先,我们需要确定评估并联机构精度的指标。
常见的指标包括位置精度、角度精度、重复精度和刚度等。
位置精度是指机构输出位置与预期位置之间的偏差,角度精度是指机构输出角度与预期角度之间的偏差,重复精度是指机构在多次运动过程中输出位置或角度的重复性。
刚度则与机构的刚性有关,即在受力情况下的变形程度。
第二步:制定测试方案制定合适的测试方案是评估并联机构精度的关键。
根据评估指标,我们可以设计相应的测试方法。
例如,对于位置精度的评估,可以使用激光测距仪或编码器等设备来测量机构输出位置与预期位置之间的偏差;对于角度精度的评估,可以使用角度传感器来测量机构输出角度与预期角度之间的偏差。
第三步:进行测试在进行测试之前,需要确保测试环境的稳定性和准确性。
例如,要消除机构自身的振动和干扰,可以使用减振器和隔离器等设备。
然后,按照测试方案进行实际测试。
对于每个评估指标,可以进行多组测试,并取平均值来减少误差。
测试结果需要记录并进行分析。
第四步:分析结果对测试结果进行分析是评估并联机构精度的关键步骤。
可以使用统计方法,如计算平均值、标准差和极值等,来评估机构的精度水平。
根据分析结果,可以判断机构是否符合设计要求,并进行进一步的改进和优化。
第五步:验证和验证在分析结果之后,需要进行验证和验证,以确保评估结果的准确性和可靠性。
可以通过与其他测试方法的比较或与已知精度标准的对比来验证结果。
同时,还可以对机构进行长时间运行测试,以检查其稳定性和耐久性。
综上所述,评估并联机构的精度是确保其性能和功能可靠性的重要环节。
通过逐步思考,我们可以确定评估指标、制定测试方案、进行测试、分析结果并进行验证和验证。
并联机床工件自动定位
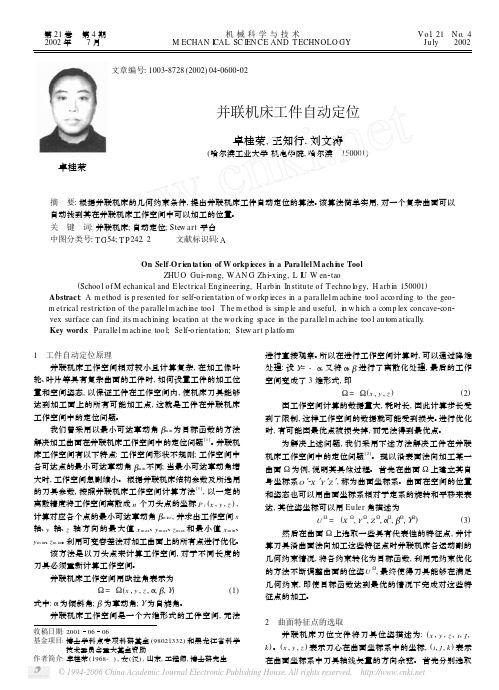
收稿日期:20010606基金项目:博士学科点专项科研基金(98021332)和黑龙江省科学技术委员会重大基金资助作者简介:卓桂荣(1968-),女(汉),山东,工程师,博士研究生卓桂荣文章编号:100328728(2002)0420600202并联机床工件自动定位卓桂荣,王知行,刘文涛(哈尔滨工业大学机电学院,哈尔滨 150001)摘 要:根据并联机床的几何约束条件,提出并联机床工件自动定位的算法。
该算法简单实用,对一个复杂曲面可以自动找到其在并联机床工作空间中可以加工的位置。
关 键 词:并联机床;自动定位;Stew art 平台中图分类号:T G 54;T P 242.2 文献标识码:AOn Self -Or ien ta tion of W orkp ieces i n a Para llelM ach i ne ToolZHUO Gu i 2rong ,W AN G Zh i 2x ing ,L I U W en 2tao(Schoo l of M echan ical and E lectrical Engineering ,H arb in In stitu te of T echno logy ,H arb in 150001)Abstract :A m ethod is p resen ted fo r self 2o rien tati on of w o rkp ieces in a parallel m ach ine too l acco rding to the geo 2m etrical restricti on of the parallel m ach ine too l .T he m ethod is si m p le and u sefu l ,in w h ich a comp lex concave 2con 2vex su rface can find its m ach in ing locati on at the w o rk ing space in the parallel m ach ine too l au tom atically .Key words :Parallel m ach ine too l ;Self 2o rien tati on ;Stew art p latfo rm 1 工件自动定位原理并联机床工作空间相对较小且计算复杂,在加工像叶轮、叶片等具有复杂曲面的工件时,如何设置工件的加工位置和空间姿态,以保证工件在工作空间内,使机床刀具能够达到加工面上的所有可能加工点,这就是工件在并联机床工作空间中的定位问题。
加强机械加工精度有效对策

加强机械加工精度有效对策随着现代制造业的快速发展,各种精密零件和装备的制造要求越来越高,这就要求机械加工的精度越来越高。
机械加工是制造过程中不可或缺的环节,如何提高机械加工的精度是一个重要的问题,本文将探讨加强机械加工精度的有效对策。
一、提高机床、工具和零部件的精度在机械加工中,机床、工具和零部件的精度对制造精度有很大的影响。
为了提高机床、工具和零部件的精度,必须采取以下措施:1、选用高精机床和工具,选择机械精度高、结构稳定、刚性好的机床,可提高加工精度。
对于复杂的零部件,采用多轴数控机床和自动化的加工线,将有效地提高加工精度。
2、定期维护机床及刀具,进行机床的调整,保证机床的运转平稳、准确和稳定,确保刀具的能力和寿命,以保证加工质量。
3、要求零部件的制造精度高,选材时要考虑材料的强度、波动系数和热膨胀系数等因素,以确保零件的尺寸精度可控。
二、提高加工技术水平在机械加工中,技术是关键,加工技术的高低直接影响到加工质量,提高加工技术水平是加强机械加工精度的必要步骤,主要措施如下:1、加强操作技能的培训,提高操作人员的操作水平,避免操作不当而造成的加工误差和机床损坏。
2、严格执行工艺规范和加工标准,确保产品的精度和质量。
3、要求加工人员掌握精加工等高级加工技术,如超精密加工、高速加工等技术,以确保加工出的产品精度高、成形美观。
三、加强质量管理强化质量管理是机械加工精度保证的重要途径,可以采用以下方法:1、采用先进的检测设备对零部件加工精度进行检测,及时发现缺陷和问题,进行及时调整,以防止产品质量不合格。
2、建立质量管理体系,严格控制生产过程中的质量控制点,明确质量操作规程,制定相应的质量控制计划和检测方案,及时发现和排除问题。
3、加强对供应商的管理,确保所购零部件的质量符合要求。
四、利用数控技术采用数控技术可以提高机械加工精度,采用以下方法:1、利用数控加工工艺,可以对加工精度进行更加精细的控制,保证产品的精度高,减少加工误差。
保证精度的技术措施有哪些

保证精度的技术措施有哪些在各个领域的应用中,都需要保证精度,特别是对于数据、测量、制造等领域来说,精度尤为重要。
那么,该如何保证精度呢?本文将对一些常用的技术措施进行介绍。
1. 校准校准是确保测量仪器或设备符合标准的一种方式。
对于需要高精度测量的工作,如测试、计量、仪器等,都需要进行校准以保证结果的精度。
在校准过程中,通常需要使用标准装置并将其与被测量设备进行等量比较,以检验被测物是否符合标准。
而校准的效果、周期、方法则需要根据实际情况和标准要求来决定。
2. 保护在测量或使用过程中,保护被测量设备或仪器的完整性和可靠性,可以有效提高精度。
例如,在使用测量仪器时,需要注意使用环境、避免振动、防止物体碰撞等,以保护仪器的正常工作。
在运输过程中,也需要加强包装、避免摔落等措施,以避免设备损坏。
3. 环境控制控制环境因素的影响也是保证精度的一项重要技术措施。
在测量和制造等领域,环境因素如温度、湿度、压力等都会对测量或制造过程产生影响。
因此,在实际生产和测试过程中,需要注意环境控制,合理调节温度和湿度、加强空气净化等措施,以消除或减少这些因素的影响,提高精度。
4. 运维管理对于用于数据、信息处理的设备,运维管理也是保证精度的关键因素。
良好的设备维护和管理,可以有效延长设备寿命,提升设备精度,避免设备失灵或瘫痪。
因此,在使用这类设备时,需要定期检查维护、更换易损件等,以保证其正常工作。
5. 验证验证是确保测试的数据或结果符合预期的另一种方式。
在对重要数据或结果进行处理时,需要进行数据验证,避免因数据错误或缺失等原因造成的误判和误导。
验证结果需要与相应的参考值进行比较,以确定结果是否真实合理。
总的来说,保证精度需要综合使用以上技术措施,并根据实际情况和要求制定相应的方案和措施。
而在实际操作或使用中,则需要不断总结经验,不断提升技术水平和服务质量。
提升数控机床定位精度的常用方法
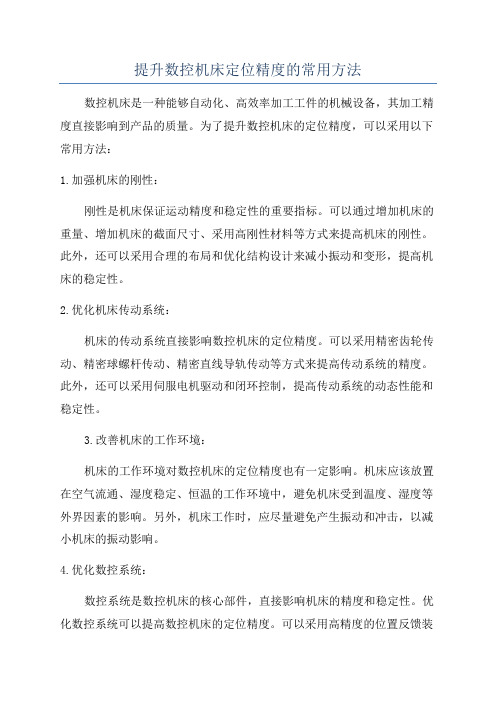
提升数控机床定位精度的常用方法数控机床是一种能够自动化、高效率加工工件的机械设备,其加工精度直接影响到产品的质量。
为了提升数控机床的定位精度,可以采用以下常用方法:1.加强机床的刚性:刚性是机床保证运动精度和稳定性的重要指标。
可以通过增加机床的重量、增加机床的截面尺寸、采用高刚性材料等方式来提高机床的刚性。
此外,还可以采用合理的布局和优化结构设计来减小振动和变形,提高机床的稳定性。
2.优化机床传动系统:机床的传动系统直接影响数控机床的定位精度。
可以采用精密齿轮传动、精密球螺杆传动、精密直线导轨传动等方式来提高传动系统的精度。
此外,还可以采用伺服电机驱动和闭环控制,提高传动系统的动态性能和稳定性。
3.改善机床的工作环境:机床的工作环境对数控机床的定位精度也有一定影响。
机床应该放置在空气流通、湿度稳定、恒温的工作环境中,避免机床受到温度、湿度等外界因素的影响。
另外,机床工作时,应尽量避免产生振动和冲击,以减小机床的振动影响。
4.优化数控系统:数控系统是数控机床的核心部件,直接影响机床的精度和稳定性。
优化数控系统可以提高数控机床的定位精度。
可以采用高精度的位置反馈装置,如光栅尺、编码器等,提供更精确的位置反馈信号。
另外,可以采用高性能的数控控制器,提供更稳定、更精确的控制信号。
5.加强机床的维护和保养:机床的定位精度会受到磨损、松动等因素的影响,因此定期的维护和保养是必不可少的。
可以定期进行机床的清洁、润滑和紧固,检查机床各部位的磨损情况,及时更换损坏的零部件。
此外,还可以定期校准机床的精度,确保机床的定位精度符合要求。
6.合理选择切削参数:切削参数的选择对机床的定位精度也有一定影响。
合理选择切削速度、进给量和切削深度,可以减小切削力和热变形,提高机床的加工精度。
7.采用补偿技术:补偿技术是提高机床定位精度的一种重要方法。
根据机床运动过程中产生的误差特点,可以通过运动轨迹的补偿来改善机床的定位精度。
补偿技术主要包括误差补偿、刀具半径补偿、刀具长度补偿、热变形补偿等。
保证和提高机床加工精度的方法有哪些
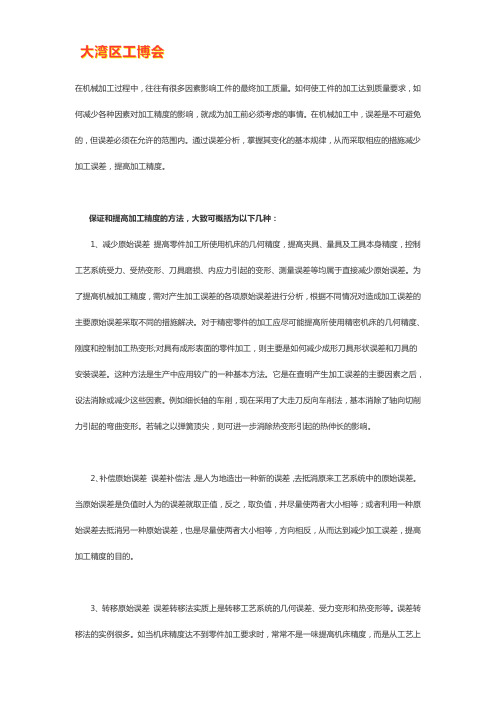
在机械加工过程中,往往有很多因素影响工件的最终加工质量。
如何使工件的加工达到质量要求,如何减少各种因素对加工精度的影响,就成为加工前必须考虑的事情。
在机械加工中,误差是不可避免的,但误差必须在允许的范围内。
通过误差分析,掌握其变化的基本规律,从而采取相应的措施减少加工误差,提高加工精度。
保证和提高加工精度的方法,大致可概括为以下几种:1、减少原始误差提高零件加工所使用机床的几何精度,提高夹具、量具及工具本身精度,控制工艺系统受力、受热变形、刀具磨损、内应力引起的变形、测量误差等均属于直接减少原始误差。
为了提高机械加工精度,需对产生加工误差的各项原始误差进行分析,根据不同情况对造成加工误差的主要原始误差采取不同的措施解决。
对于精密零件的加工应尽可能提高所使用精密机床的几何精度、刚度和控制加工热变形;对具有成形表面的零件加工,则主要是如何减少成形刀具形状误差和刀具的安装误差。
这种方法是生产中应用较广的一种基本方法。
它是在查明产生加工误差的主要因素之后,设法消除或减少这些因素。
例如细长轴的车削,现在采用了大走刀反向车削法,基本消除了轴向切削力引起的弯曲变形。
若辅之以弹簧顶尖,则可进一步消除热变形引起的热伸长的影响。
2、补偿原始误差误差补偿法,是人为地造出一种新的误差,去抵消原来工艺系统中的原始误差。
当原始误差是负值时人为的误差就取正值,反之,取负值,并尽量使两者大小相等;或者利用一种原始误差去抵消另一种原始误差,也是尽量使两者大小相等,方向相反,从而达到减少加工误差,提高加工精度的目的。
3、转移原始误差误差转移法实质上是转移工艺系统的几何误差、受力变形和热变形等。
误差转移法的实例很多。
如当机床精度达不到零件加工要求时,常常不是一味提高机床精度,而是从工艺上或夹具上想办法,创造条件,使机床的几何误差转移到不影响加工精度的方面去。
如磨削主轴锥孔保证其和轴颈的同轴度,不是靠机床主轴的回转精度来保证,而是靠夹具保证。
如何提高数控机床的精度_
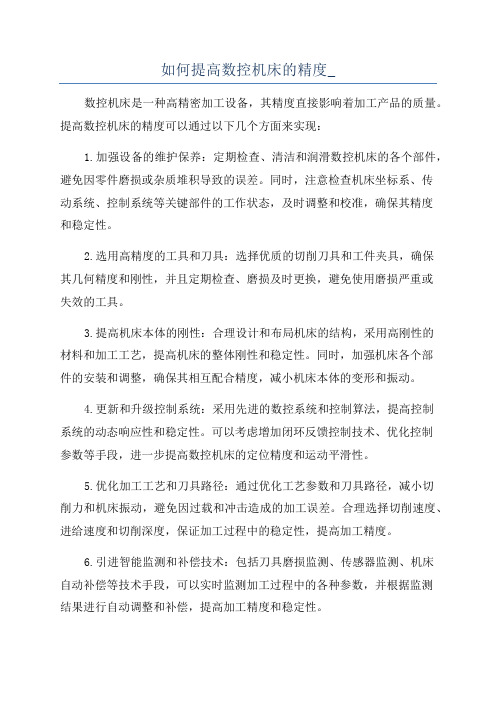
如何提高数控机床的精度_数控机床是一种高精密加工设备,其精度直接影响着加工产品的质量。
提高数控机床的精度可以通过以下几个方面来实现:1.加强设备的维护保养:定期检查、清洁和润滑数控机床的各个部件,避免因零件磨损或杂质堆积导致的误差。
同时,注意检查机床坐标系、传动系统、控制系统等关键部件的工作状态,及时调整和校准,确保其精度和稳定性。
2.选用高精度的工具和刀具:选择优质的切削刀具和工件夹具,确保其几何精度和刚性,并且定期检查、磨损及时更换,避免使用磨损严重或失效的工具。
3.提高机床本体的刚性:合理设计和布局机床的结构,采用高刚性的材料和加工工艺,提高机床的整体刚性和稳定性。
同时,加强机床各个部件的安装和调整,确保其相互配合精度,减小机床本体的变形和振动。
4.更新和升级控制系统:采用先进的数控系统和控制算法,提高控制系统的动态响应性和稳定性。
可以考虑增加闭环反馈控制技术、优化控制参数等手段,进一步提高数控机床的定位精度和运动平滑性。
5.优化加工工艺和刀具路径:通过优化工艺参数和刀具路径,减小切削力和机床振动,避免因过载和冲击造成的加工误差。
合理选择切削速度、进给速度和切削深度,保证加工过程中的稳定性,提高加工精度。
6.引进智能监测和补偿技术:包括刀具磨损监测、传感器监测、机床自动补偿等技术手段,可以实时监测加工过程中的各种参数,并根据监测结果进行自动调整和补偿,提高加工精度和稳定性。
7.培训操作人员和加工人员:提高操作人员的技术水平和操作规范,让其能够灵活运用数控机床的各项功能和操作要点。
加工人员应熟悉产品的加工要求和机床的性能特点,合理安排加工顺序和工艺参数,提高加工精度和质量。
总结起来,提高数控机床的精度需要从设备的维护保养、工具的选择和使用、机床结构和控制系统的优化、加工工艺和刀具路径的优化、智能监测和补偿技术的引进以及人员的培训等多个方面综合考虑。
只有在这些方面同时努力,才能有效提高数控机床的精度,提高产品加工的质量。
保证设备精度的措施包括

保证设备精度的措施包括高精度设备在实际应用中,其精度和稳定性对于工业制造、医疗诊断和科学研究等领域至关重要。
那么,为了保证设备的精度和稳定性,我们需要采取哪些措施呢?1. 温度控制在实际使用中,设备的精度和稳定性往往受到环境温度的影响。
因此,在使用高精度设备时,需要对环境温度进行控制。
一些高精度设备配有温度传感器,可以及时检测环境温度,并根据设定的温度范围进行自动调节。
此外,在设备周边的空气流动和空调系统的使用也可以有效控制设备的环境温度,从而达到保持设备精度的目的。
2. 电源稳定性电源稳定性对设备的精度和稳定性同样具有重要影响。
在使用高精度设备时,需要使用稳定的电源以保证设备正常工作。
如果电压不稳定,就容易影响设备的性能,进而直接影响测量或测试的结果。
因此,为了保证设备精度,需要选用稳定的电源,并对设备进行电源保护和干扰抑制。
3. 定期校准和维护为了确保设备的精度和稳定性,需要对设备进行定期校准和维护。
定期校准可以通过比对标准器和设备输出来检查设备的输出精度。
在校准过程中,可以进行设备调整,例如调整电位器、增益电路、滤波器等。
同时,需要对设备进行维护保养,包括清理机身、更换易损件、检查电路板等。
4. 降噪措施在高精度设备中,一些干扰因素会对设备的精度和稳定性产生影响。
因此,在使用设备时需要采取相应的降噪措施。
对于传输信号的电缆,可以使用屏蔽线,减少外界的干扰。
对于电路板,可以采用干扰抑制电路或地线隔离技术来降噪。
通过这些降噪措施,保证设备的信号传输稳定可靠。
5. 选择合适的环境在使用高精度设备时,需要选择一个合适的环境。
例如,需要避免使用有振动的环境,以减少设备机械振动对精度的影响。
同时,要避免涉及到强磁场等环境,以免设备受到干扰。
经过以上措施的采取,可以保证高精度设备在实际应用过程中能够准确、稳定的进行工作,达到我们对设备精度和稳定性的要求。
以上是保证设备精度的措施,希望能对读者有所帮助。
多段拼接床身的加工精度控制

1 序言床身是数控机床最基础的零件,多数床身上安装滑动导轨,工作台安装在导轨滑块上进行移动,其导轨安装面的精度对机床整机的精度及性能起着决定性的作用。
随着行业发展,对大型、长行程机床的需求越来越多,受到加工工艺性、机床行程、运输、吊运、装配的制约以及设计的模块化限制,此类长行程机床的床身均由多段床身拼接而成。
长行程机床对床身导轨安装面的精度要求更高,受制于加工机床的精度及行程,拼接床身导轨安装面的直线度精度是加工的难点。
传统分段加工方法采用精度传递的方式,将中间两段床身拼接成一组后磨削至精度要求,拆除一段,然后添加另一段床身拼接,再以磨好的床身为基准磨削拼接上一段床身。
以此类推,采用积木式拼接将精度一段一段传递下去。
由于床身在磨削时易变形,精度不稳定且难以控制,磨削效率低,加工时间长,所以通常在装配时要配合铲刮才能让导轨安装面达到全长直线度的要求。
公司原来将床身组件组合拼接好后用20m龙门整体加工来保证导轨安装面的直线度精度,但在机床无法保证精度或组件床身超出机床加工行程的情况下,无法采用组件组合精加工来保证精度。
本文对公司生产的PM2580、PM30100型床身组件的加工精度控制进行介绍。
2 零件介绍床身组件精度要求及其分段床身布局见表1,分析其加工难点如下。
表1床身组件精度要求及其分段床身布局1)床身为3段分件拼接,全长分别为16800mm(见图1)和21300mm。
图1床身组件PM2580HA0111-00示意2)床身为3条导轨安装面,导轨安装面正侧向直线度要求:0.06mm/全长、0.07mm/全长、0.01mm/1000mm。
3)现有机床无法直接加工至要求精度,需要分段加工保证拼接后3条导轨安装面的直线度要求。
3 精加工方案分段床身的粗加工放到精度不高的机床分段加工,导轨安装面及拼接面留余量0.5mm,其余关联尺寸在自由公差下保持一致性。
精加工时考虑机床本身的精度误差,将分段床身按照组件顺序进行摆放,使大小床身拼接面面面相对(见图2、图3),即小床身1拼接面A朝向机床X+方向,大床身拼接面B朝向机床X-方向,大床身拼接面C朝向机床X+方向,小床身2拼接面D朝向机床X-方向,以此抵消机床X、Z垂直精度误差在结合面上产生的影响[1]。
掌握这些技巧,就能保证高精度立式加工中心的正常运行

掌握这些技巧,就能保证高精度立式加工中心的正常运行高精度立式加工中心是一种用于制造高精度零件的机床,其精度和加工效率比传统机床更高。
为了确保加工中心的正常运行,需要遵循以下使用技巧。
一、安装1、安装前,应检查加工中心的配件是否齐全,各连接部位是否紧固。
2、安装时,应将加工中心放置在平稳的地面上,并确保机床水平度符合要求。
3、安装时,应根据实际需要选择进出口方向,确保进出口管道与机床的进出口相连。
4、安装完成后,应进行试运转,测试高精度立式加工中心的运行情况。
二、操作1、操作前,应检查立式加工中心的电源是否接通,各连接部位是否紧固。
2、操作时,应根据加工零件的要求选择合适的刀具和加工参数,保证加工质量和效率。
3、操作过程中,应注意观察加工零件的表面质量和尺寸精度,如有异常情况应及时处理。
4、操作完成后,应清洗立式加工中心的内部和外部,保持清洁卫生。
三、维护1、每次使用后,应清洗高精度立式加工中心的内部和外部,保持清洁卫生。
2、定期检查立式加工中心的刀具、夹具、传动系统等部件,如有磨损或损坏应及时更换。
3、定期更换立式加工中心的润滑油,保证机床的正常运行。
4、长时间停用时,应将立式加工中心的内部润滑油排干,并涂上防锈油,以避免腐蚀和损坏。
四、注意事项1、在使用时,应避免机床的过载和空载运行,以免影响加工质量和机床寿命。
2、如立式加工中心长时间运行,应注意机床的温度上升情况,及时采取降温措施。
3、在加工时,应避免机床进出刀时碰撞,以免损坏刀具和机床。
4、在使用立式加工中心时,应注意机床的维护保养,如有异常情况应及时处理。
高精度立式加工中心是一种高精度加工机床,正确的使用技巧可以确保其正常运行和延长使用寿命。
在安装、操作、维护和注意事项方面,都需要注意细节,确保立式加工中心的安全运行。
平床身线轨数控机床精度要求与优化措施

平床身线轨数控机床精度要求与优化措施随着制造业的不断进展和技术的进步,数控机床在加工领域中起到越来越紧要的作用。
其中平床身线轨数控机床作为常用的一种类型,其加工精度对于零件的质量和生产效率有着直接的影响。
下面就来说说数控机床加工的精度要求以及相应的优化措施。
一、数控机床的精度要求:1、定位精度:定位精度是指机床在进行加工时,机械移动元件停止位置与设定位置之间的偏差。
机床的定位精度要求通常在微米级别,不同的加工任务可能会有不同的精度要求。
2、重复定位精度:重复定位精度是指机床在多次定位下,机械移动元件回到相同位置的偏差。
对于机床来说,重复定位精度要求较高,以确保多次加工相同零件时的一致性。
3、直线度和平面度:直线度和平面度是指机床移动轨迹或加工表面与理想直线或平面之间的偏差。
在机床的加工过程中,直线度和平面度的要求对于工件的平整度和尺寸精度至关紧要。
二、平床身线轨数控机床精度优化措施:1、选用高精度的导轨和滚珠丝杠:导轨和滚珠丝杠是影响机床精度的关键部件。
选择高精度的导轨和滚珠丝杠可以显著提高机床的定位精度和重复定位精度。
2、提高传动系统的刚性:传动系统的刚性对于削减机械振动和提高加工精度特别紧要。
通过优化传动系统的结构设计和加强关键部件的刚性,可以有效改善机床的精度。
3、精准明确的加工调试和校正:在机床安装调试完毕后,进行精准明确的加工调试和校正是确保机床精度的关键步骤。
通过认真调整和校正机床的各项参数和位置,可以提高机床的加工精度。
4、合理选择切削条件:在进行加工时,合理选择切削条件也是优化机床精度的紧要措施。
通过选择适当的切削速度、进给量和切削深度等参数,可以降低切削过程中的振动和变形,从而提高加工精度。
平床身线轨数控机床的精度要求对于加工质量和产品性能具有紧要影响。
为了充足精细化加工的需求,需要关注选用高精度的导轨和滚珠丝杠,提高传动系统的刚性,进行精准明确的加工调试和校正,并合理选择切削条件。
组合机床设备安全技术措施
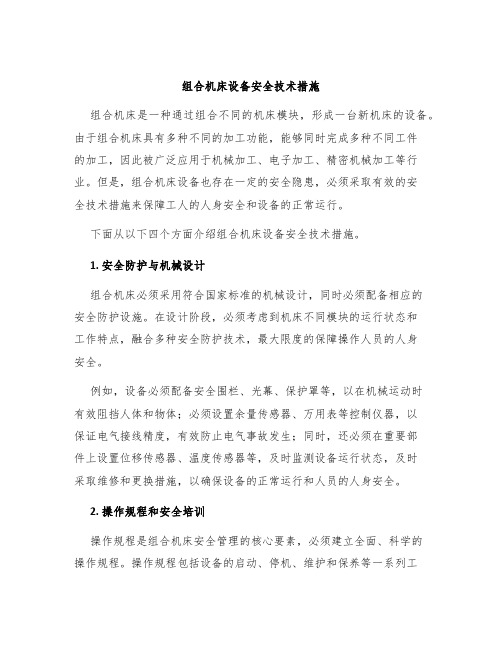
组合机床设备安全技术措施组合机床是一种通过组合不同的机床模块,形成一台新机床的设备。
由于组合机床具有多种不同的加工功能,能够同时完成多种不同工件的加工,因此被广泛应用于机械加工、电子加工、精密机械加工等行业。
但是,组合机床设备也存在一定的安全隐患,必须采取有效的安全技术措施来保障工人的人身安全和设备的正常运行。
下面从以下四个方面介绍组合机床设备安全技术措施。
1. 安全防护与机械设计组合机床必须采用符合国家标准的机械设计,同时必须配备相应的安全防护设施。
在设计阶段,必须考虑到机床不同模块的运行状态和工作特点,融合多种安全防护技术,最大限度的保障操作人员的人身安全。
例如,设备必须配备安全围栏、光幕、保护罩等,以在机械运动时有效阻挡人体和物体;必须设置余量传感器、万用表等控制仪器,以保证电气接线精度,有效防止电气事故发生;同时,还必须在重要部件上设置位移传感器、温度传感器等,及时监测设备运行状态,及时采取维修和更换措施,以确保设备的正常运行和人员的人身安全。
2. 操作规程和安全培训操作规程是组合机床安全管理的核心要素,必须建立全面、科学的操作规程。
操作规程包括设备的启动、停机、维护和保养等一系列工作流程,必须明确每个操作步骤及其安全风险。
同时,针对不同的设备模块和工件特点,不同工岗的操作者必须配备不同的安全保护措施,且必须经过专业的安全培训后方可上岗。
安全培训的目的是让操作者了解机床设备的工作原理和操作规程,并掌握必要的安全技能。
培训包括理论培训和实践培训。
理论培训需要在上岗前完成,操作者必须掌握设备安全规程的必要知识,如何使用机床监控仪器、如何维护和保养设备等;实践培训的主要目的是让操作者进行设备操作、设备维护等真实环境下的实践操作,锻炼其操作技能和安全意识,为接下来的操作提供有力支持。
3. 设备检查和维护组合机床设备的安全检查和维护是组合机床安全管理的重要环节。
对设备的常规检查和维护可以及时归纳和分析设备的故障,及时采取维护措施,确保设备的长期稳定运行。
- 1、下载文档前请自行甄别文档内容的完整性,平台不提供额外的编辑、内容补充、找答案等附加服务。
- 2、"仅部分预览"的文档,不可在线预览部分如存在完整性等问题,可反馈申请退款(可完整预览的文档不适用该条件!)。
- 3、如文档侵犯您的权益,请联系客服反馈,我们会尽快为您处理(人工客服工作时间:9:00-18:30)。
确保并联机床定位精度的几项措施魏华亮哈尔滨量具刃具集团有限责任公司 我公司与哈尔滨工业大学联合研制了用于汽轮机叶片加工的7轴联动并联机床,6个制动器构成了标准的6自由度Stewart 并联机构,电主轴装在并联机构的动平台上实现6自由度运动;另1个轴为卧式布置的回转轴,用于实现叶片的回转运动。
该并联机床最终定位精度的保证不是单靠一两个环节实现的,而是在机床的设计、制造、检验及标定等整个过程中,建立了一个由多环节构成的整体保障体制,下面对各环节进行介绍。
图1 机床结构简图1 设计阶段的分辨率分析在机床设计阶段,分辨率分析是涉及精度问题的首项环节。
对于传统数控机床,由于各驱动轴正交布置并且独立作用,因此驱动轴所能实现的分辨率就是机床的分辨率;而并联机床各驱动轴由于是联合作用的,机床分辨率与各驱动轴分辨率之间的关系不是太直观,为此引入了输入至输出分辨率放大系数K io 的概念,K io 等于机构输入至输出雅可比矩阵所有元素平方和的平方根。
另外工作空间不同位置、不同姿态下的K io 是不同的;对并联机床工作空间不同位置和姿态下的位置分辨率放大系数K p 和姿态角分辨率放大系数K a 进行采样分析,姿态角为θX =0°,θY =0°,θZ =0°时,工作空间各点处的位置分辨率放大系K p 数范围为1.87-1.90(mm /mmm )、姿态角分辨率放大系K a 数范围为0.30-0.34(°/mm ),姿态角为θX =25°,θY =25°,θZ =0°时,K p 变为2.17-3.47(mm /m m )、K a 变为0.35-0.48(°/mm )。
从以上结果可以看出:这台并联机床各位置、各姿态下的K p 和K a 变化均不是很大,选取较大的值作为机床各位置和姿态下通用的分辨率放大系数,即K p =3.3(mm /mm ),K a =0.45(°/mm ),根据设计要求机床的位置输出分辨率为0.001mm ,角度输出分辨率为0.001°,则根据位置分辨率要求算出的驱动杆分辨率上限为t i =0.0013.3≈0.0003(mm )根据角度分辨率要求算出的驱动杆分辨率上限为t i =0.0010.45≈0.0022(mm )取其中较小者作为要求驱动杆所能提供的分辨率上限,即t i =0.0003mm 。
事实上,驱动轴丝杠导程为6mm ,伺服电机反馈码盘分辨率为1/65536,故驱动轴实际的分辨率为t i =665536≈0.00009(mm )由于驱动轴的实际分辨率小于要求提供的分辨率,因此可以满足要求。
根据这个分辨率来计算,本台机床理论上的位置分辨率可以达到:3.3×0.00009≈0.0003(mm ),理论上的姿态角分辨率可以达到:0.45×0.00009≈0.00004(°)。
2 运动部分结构尺寸确定(1)虎克铰中心位置该产品设计要求:上平台六个虎克铰旋转中心的准确坐标值及动平台虎克铰旋转中心的准确坐标值,上平台比较大,且虎克铰旋转中心在空间位置,因此,无法直接测量其尺寸。
在研制过程中,先用数控机床加工动平台和虎克铰座的定位销孔,用三坐标测量机测出虎克铰座的定位销孔到旋转中心、旋转中心到其下定位面的距离,然后用C AD 根据测得数据作图,求的各上虎克铰旋转中心的坐标点;动平台较小,故可直接在三座标测量机上测量,即可得到各下虎克铰的旋转中心的位置。
(2)虎克铰轴线与伸缩杆轴线相交精度设计要求虎克铰轴线与伸缩杆轴线必需相交,114工具技术DOI :10.16567/j .cn ki .1000-7008.2010.02.037试制时在虎克铰转轴外端加工一与轴线重合的工艺孔装配时用定位芯杆定位,经检测,其偏移量不超过0.015mm 。
(3)伸缩杆长度机床复位时,六根伸缩杆长度必须有其精确值,为保证这一尺寸,特地设计了一专用检具;先将检具在一标准样件上调零位,然后将其置于伸缩杆上,转动丝杠使其对零,在三坐标测量机上测量两虎克铰中心距离并记录下来。
联机调试时,仍用这个检具进行单杆长度调整。
从而得出机床复位时的各杆长度。
从以上过程可见,这种标准检具虽然简单却起着很大作用(见图2)。
图2 杆长的测量试制结果证明,采用以上方法确定的结构尺寸,完全可以满足标定前的要求。
3 驱动轴复位长度的保证这台并联机床的复位方式与其他形式的数控机床一样,也是上电之后各驱动轴先找各自的零位信号,系统再将各轴在零位信号处对应的长度(复位长度)传给各驱动轴。
显然,复位长度的准确性对并联机床精度具有决定性影响。
实际工作中,最容易导致复位长度变化的因素是零位信号混淆的情况。
由于驱动轴的复位信号一般来自于伺服电机所带码盘的零位信号,当通过丝杠将旋转运动转换成直线运动时,显然沿着杆长方向每个螺距内都会有一个零位信号,为了区分出真正的复位信号,还必须安装粗定位开关,即复位时先找粗定位开关,然后将其后面的零位信号作为复位信号(见图3)。
粗定位开关与复位信号之间的距离不能太大也不能太小,最佳距离为S =(0.3-0.7)T ,这是因为粗定位开关有其触发域值范围,若S 过于接近于或T 的话,当粗定位信号的强弱突然发生变化时,很容易将前面或后面的零位误检测为复位位置。
采用“粗定位信号—复位信号—粗定位信号”的复位方式,即在完成复位之后又找了一次粗定位信号,其目的在于测出复位信号与粗定位信号之间的距离。
在机床调试完成时,系统中会将正常情况下复位信号与粗定位信号之间的距离记录下来,平时机床复位时都会将新测出的距离与系统中的记录进行比较,如果发现二者的差别较大,说明可能出现了复位信号混淆的情况,或者是驱动杆松动了等其他问题,系统就会自动报警。
图3 粗定位开关安装位置 4 标定项目的选择并联机床活动平台具有6个自由度,它的定位精度也是6维意义下的定位精度,标定项目的选择必须能体现这个特点。
选择两个标定项目:一是并联机床活动平台平动(各姿态角为0)时的空间定位精度;二是在空间任意位置让刀具做向各方向不同角度定点摆动时,刀头点保持在定点位置能力的空间聚点性精度,如图4所示,当α角和β角任意变化时,刀头点的位置应该是不动的。
如果既能保证活动平台平动时的定位精度,又能保证在定点处刀头点的位置不随姿态角变化而偏移,实际上就保证了并联机床在多自由度下的定位精度。
图4 聚点性精度的概念5 标定实例以下是将机床恢复原始参数之后重新进行的一次标定试验,标定工具是量块和接触式测头,标定的检测内容为平动时的定位精度测量和摆动时的空间聚点性精度测量,共进行了两轮标定,数据如图5所示。
图中所测量的误差项总计62项,其中1-7项为平动时的定位误差,8-62项为摆动时的空间聚1152010年第44卷№2点性误差。
从图中可见,原始数据中,平动时的定位误差最大约为0.30mm,定点摆动误差最大达0.50m m左右。
经过两轮标定之后,平动定位误差降至0.01mm以下,而定点摆动误差降为0.02mm左右。
需要说明的是,这项实验给定的定位误差是实际测得的,没有按国家标准进行数据处理,同时,由于是采用量块作为标准量,也无法将定位误差分解为单项定位误差和双向定位误差,也不宜作为验收机床的精度指标,但这种方法方便、快捷,完全可以作为机床校准过程中的工具。
通过第二轮标定后的机床,用激光干涉仪按国家标准GB/T17421.2要求的方法进行检验结果如表1所示。
表1 数控轴线的定位精度及重复定位精度检测检验项目允差(mm)结果检测工具双向定位精度A 0.022X轴0.0155Y轴0.0105Z轴0.0068单向定位精度A←和A↑0.016X轴A←0.0135A↑0.0151Y轴A←0.0068A↑0.0105Z轴A←0.0049A↑0.008E↑0.0126Y轴E←0.0026激光干涉仪执行标准GB/T17421.2机床检验通则(第二部分)数控轴线的定位精度和重复性定位精度的确定。
6 回转轴位置的确定这台并联机床除了6根并联轴外,还有一个联动的回转轴。
对回转轴的测量采用的是一根圆柱型的标准检棒(见图5),测量时用接触式测头在检棒的表面测一系列点,然后用最小二乘法算出回转轴线X*的位置。
图5 回转轴线的测量修正过程中,如果发现修正之后的坐标系X″、Y″和Z″与修正之前的坐标系X′、Y′和Z′有较大的差异,系统会认为中间产生了差错,作出自动提示报警。
西安将建全国最大摩擦焊接技术研发基地1月13日上午,总投资近亿元的摩擦焊接技术项目在西安航空基地正式开工建设。
项目建成投产后该技术将被逐步应用于飞机结构件的连接,填补该项技术在国内航空领域应用的空白。
该项目承担单位西安固本科技实业有限公司是专业从事研发、生产和营销高性能通用特种摩擦焊机、摩擦焊接制品及相关技术软件的高新技术企业。
该公司掌握国内最先进最全面的摩擦焊接技术,相关技术成果曾获国家重点新产品一项,省部级科技进步一等奖两项、二等奖一项。
搅拌摩擦焊接技术由英国焊接研究所(TWI)发明,该技术被认为是自激光焊接问世以来最引人注目的焊接方法。
由于该技术具有接头质量好且稳定、效率高、节能、节材、无污染等一系列明显的优越性,在国外已被广泛应用于航空、航天、汽车、船舶、石油设备等领域,波音、空客公司生产的飞机已经在许多部件采取了摩擦焊技术,但在我国尚未在航空领域得到广泛应用。
该项目建成后,可形成年产200台通用摩擦焊机和特种摩擦焊机、产30000吨钻杆的生产能力,建成全国最大的摩擦焊接技术研发基地。
按照计划,该项目将两年内建成投产,预计年产值将超过11亿元。
中国大飞机“中国心”发动机基地动工我国大型客机发动机项目责任主体和总承制单位中航商用飞机发动机有限责任公司(简称“中航工业商发”,AVIC/ ACAE)研发基地日前在上海市闵行区开工,预计将于2013年完成各项功能建设。
研发基地项目的总用地面积约450亩,规划总建筑面积约30万平方米,投资额约32.3亿元,预计将于2013年竣工。
该研发基地将建设成为集总部、研发中心、适航中心、国际工程中心、国际交流中心、专家公寓、客户服务中心等为一体的大型基地。
项目的总体规划既保留中国特色,又彰显国际化元素,设计方案将建筑与环境有机结合,体现节能环保和可持续发展的设计理念。
建成后的中航工业商发研发基地将成为可容纳近3000人集中办公,功能齐全、环境优美、数字化、高效率的航空发动机研发中心。
中国航空工业集团公司党组副书记、副总经理谭瑞松表示,研发基地的破土动工,是实现我国商用航空发动机产品产业发展的重要里程碑。
据介绍,该研发基地目前主要研制我国150座级的国产大型客机C919的发动机,将来还将满足我国250座级的国产大型客机的发动机研制需求。