注塑新模试模作业标准
注塑模具试模作业指导书

注塑模具试模作业指导书
注塑模具试模作业指导书
⒈文档目的
本文档旨在提供注塑模具试模作业的详细指导,以确保试模过程的顺利进行。
⒉准备工作
⑴检查设备和工具的完好性和可用性。
⑵准备所需材料,如模具、注塑机、原料等。
⒊试模前的准备
⑴清洁和检查注塑模具,确保其无损坏和杂质。
⑵检查注塑机的各项参数,包括温度、压力等是否符合要求。
⑶准备试模所需的样品尺寸和重量等参数。
⒋试模步骤
⑴安装模具:将模具安装到注塑机上,并确保其固定稳定。
⑵调整参数:根据样品要求,调整注塑机的温度、压力、注射速度等参数。
⑶启动注塑机:按照操作手册的指示,启动注塑机。
⑷进行试模:将原料加入注塑机,并启动注射过程。
⑸检查样品:观察注塑出的样品,检查其尺寸、外观等是否符合要求。
⑹调整参数:根据试模结果,适时调整注塑机的参数,再次进行试模。
⑺重复试模:如果样品不符合要求,重复以上步骤,直至获得满意的样品为止。
⒌试模后的处理
⑴关闭注塑机:试模完成后,关闭注塑机并进行清理。
⑵拆卸模具:拆卸模具,清洗并储存。
⒍附件
本文档所涉及的附件包括:模具清洁和维护记录表、注塑机参数调整记录表等。
⒎法律名词及注释
⑴注塑模具:用于注塑成型的模具,通常由金属材料制成。
⑵注塑机:用于将熔融的塑料原料注入注塑模具中,并形成所需产品的设备。
⑶试模:在注塑模具中注入原料,并从中获得样品的过程。
注塑厂试模流程操作规范

注塑厂试模流程操作规范1.目的为促使本公司试模流程规范化,合理化,对新开的模具(或者外厂调入的模具)在量产前进行确认模具的现状与适用机台、原料、模具缩水比例、产品的尺寸﹑外观、结构等问题并加以承认, 让新旧模具尽快地投入量产/生产,达到缩短项目运作的时间提高工作效率,明确规范试模作业程序、方法与安全注意事项﹐以保证试模品质为目的而制定本规范。
2.范围适用于注塑厂所有新模具、改模旧模具、外来试模、生产模具等量产前的试样试模作业过程。
3.职责3.1生产部:负责试模模具的上下模、试模调机,试模操作人员在试模流程中必须按照此规范操作,防止试模操作人员因操作不当造成事故。
3.2工程部权责:由工程部制定本规范并实施与管理,对本规范负责,负责提供模具图纸、产品图纸、产品检测标准、原料物性表、特殊结构等信息,试模跟进、负责提供试模原材料和特殊铺助器械的采购准备工作。
3.3修模组:负责将组装以及确认好的模具拉到生产部指定待试模区域,摆放好以及运输叉车归位,负责维修和确认试模过程中模具的异常处理。
3.4品质部:根据客户提供的产品标准确认试模产品的尺寸、外观、结构、装配、可靠性等。
4.定义试模是指在产品开发和制造流程中在产品完成模具制作后、批量生产前所进行的测试注塑步骤。
模具在完成所有配件并装配完毕后,需要通过实际的注塑并得到注塑样品,然后通过样品检测才能确定模具的制作是否完全符合设计要求。
如果注塑样品完全符合设计要求则表明模具制作没问题可以投入批量注塑生产;否则就需要根据样品反馈的问题进行模具的改模。
根据改模情况的不同,试模可能会在批量生产前多次进行直到模具完全改正所有问题。
5.内容5.1安全执行5.1.1所有人员开动桥门式天车前请佩戴安全帽、戴手套、穿劳保鞋,模具起吊后不得从人员上方经过,在模具吊起范围1.5米中心圈内不可有人员进入。
5.1.2模具吊起前请确认吊环和吊链是否有裂缝、吊环吊链不可使用变形的,变形的吊环吊链请报废到仓库,并领取新的吊环吊链。
注塑厂模具试模及验收作业指引

注塑厂模具试模及验收作业指引1、目的为了保证修改模、新模、试模效果良好,控制模具质量使生产顺利进行。
2、适用范围适用于注塑成型和工模修模组。
3、定义3.1模具试模:控制产品各类缺陷,试出各项存在影响问题,找出解决方案。
4、职责4.1注塑部:负责模具请修、试模、试样、并跟踪返修到位。
4.2班长:负责根据现场生产的要求安排修模作业。
4. 3工艺组长:负责跟踪修模、试模结果及报告填写与最终结果确认。
5、工作程序4.1 模具请修作业4.1.1 正在机台上生产的模具请修流程5. L1.1生产中出现料件不良,如镶件断、划伤、飞边、毛刺、滑块卡死、压模等不能正常工作时,班长及时上报课长处,同时课长决定是否先生产或立即修模。
若判定为立即修模模具,由班长填写模具请修单,送课长或部门经理处审核,同时在IH内下模,附上不良样板及经审核的修模单一起送到工模部。
生产中模具一般在12H间修好,并由课长或班长负责跟踪。
5.1.1.2工模部将模具修好后连同“试模通知单”一并送往注塑部,模具组长签收。
模具组长签收到机台修模、试模单时应及时安排班长或技术人员试模,班长将重新写首件,将修模后料件送于PQC处确认修模结果,OK即可正常生产,NG则通知工模返修到好为止。
5.1.2生产完模具请修5.1.2.1模具订单批量生产完,班长下模送于模房,应附有该模的“生产记录单”和尾板料件。
模具保养员接收模具后,应仔细查看“生产记录单”是否填写规范、工整,并确认是修模还是保养。
若保养模,则保养后上模架;若需修模,模具保养员应根据“生产记录单”上所记录的问题开出“模具请修单”和不良料件,送于模具组长或课长、经理处审核,保养员再将模具及时送于工模修模组,模具组长随后将审核好的“模具请修单”连同修模料件一并送于工模(”模具请修单”的填写:编号、时间、机型、料件名称、送修时间、完成时间、修模内容)。
模具送到工模,保养员应做好详细的送模记录,并由工模签名。
注塑模具试模作业指导书

注塑模具试模作业指导书注塑模具试模作业指导书1.介绍注塑模具试模作业指导书旨在指导操作人员正确使用注塑模具进行试模操作。
本指导书详细描述了试模前的准备工作、试模步骤、常见问题及解决方法等内容,以确保试模作业的安全、高效进行。
2.准备工作2.1 材料准备2.1.1 确保所需注塑材料已经准备好,并进行质量检测。
2.1.2 检查注塑材料的储存条件,确保其干燥、无杂质。
2.1.3 将注塑材料按照要求放置在指定区域。
2.2 模具检查2.2.1 检查注塑模具的外观,排除表面污垢,确保模具干净。
2.2.2 检查模具零部件,确保其完整、无损。
2.2.3 清洁模具的冷却系统,确保其畅通无堵塞。
2.2.4 涂抹模具专用防锈剂,保持模具的表面光洁。
2.3 设备准备2.3.1 开启注塑机设备并进行预热。
2.3.2 检查注塑机的工作性能,确保其正常运转。
2.3.3 准备好所需的模具安装工具。
3.试模步骤3.1 模具安装3.1.1 将模具安装在注塑机上,并确保模具与机器连接紧密。
3.1.2 安装模具的保护装置,确保操作人员的安全。
3.2 调整注塑参数3.2.1 根据注塑产品的要求,调整注塑机的温度、压力、速度等参数。
3.2.2 进行注塑材料的预热和预塑。
3.3 开始试模3.3.1 打开注塑机的开关,将注塑材料注入模具中。
3.3.2 关注注塑机的工作情况,确保注塑过程顺利进行。
3.3.3 观察试模产品的质量,确保其满足要求。
4.常见问题及解决方法4.1 模具堵塞问题:模具冷却系统堵塞,导致注塑过程中温度过高。
解决方法:清洁模具冷却系统,确保其畅通无堵塞。
4.2 产品质量不合格问题:产品存在短射、气孔等缺陷。
解决方法:调整注塑参数,改善注塑过程中的温度、压力控制。
5.附件本文档附带以下附件供参考:- 注塑模具试模检查表- 注塑参数调整记录表6.法律名词及注释6.1 注塑材料:用于注塑过程中的塑料原材料。
6.2 模具:用于塑料制品成型的工装,包括模具本体及相关零部件。
注塑试模作业指导书
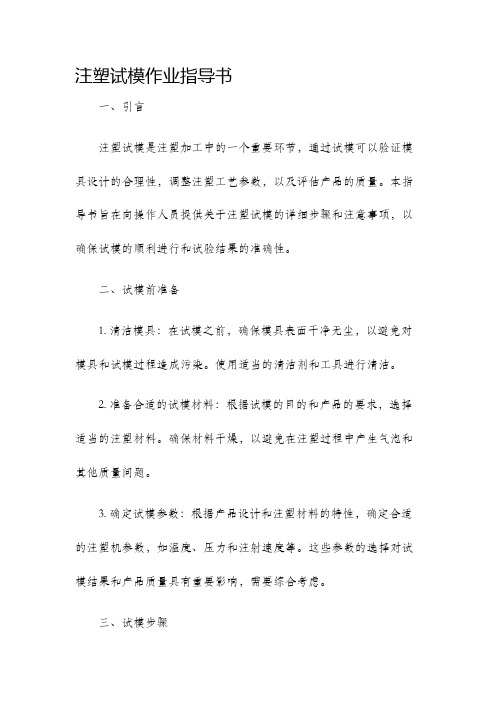
注塑试模作业指导书一、引言注塑试模是注塑加工中的一个重要环节,通过试模可以验证模具设计的合理性,调整注塑工艺参数,以及评估产品的质量。
本指导书旨在向操作人员提供关于注塑试模的详细步骤和注意事项,以确保试模的顺利进行和试验结果的准确性。
二、试模前准备1. 清洁模具:在试模之前,确保模具表面干净无尘,以避免对模具和试模过程造成污染。
使用适当的清洁剂和工具进行清洁。
2. 准备合适的试模材料:根据试模的目的和产品的要求,选择适当的注塑材料。
确保材料干燥,以避免在注塑过程中产生气泡和其他质量问题。
3. 确定试模参数:根据产品设计和注塑材料的特性,确定合适的注塑机参数,如温度、压力和注射速度等。
这些参数的选择对试模结果和产品质量具有重要影响,需要综合考虑。
三、试模步骤1. 安装模具:将试模所需模具安装到注塑机上。
确保模具位置正确,并通过紧固件固定模具,以确保稳定性。
2. 注塑机调试:启动注塑机,根据试模参数进行调试,调整温度、压力和速度等参数,并将试模材料导入注塑机料斗中。
3. 启动试模:按照注塑机操作步骤,启动注塑机进行试模。
注意观察注塑机和模具的运行状态,确保正常运转。
4. 观察注塑过程:在注塑过程中,注意观察注塑材料的熔融状态和充模情况。
根据需要进行调整,确保产品的尺寸和形状符合设计要求。
5. 停机观察:在试模过程中,及时停机观察和检查产品的质量。
尽量保留试模样品,以供后续评估和分析。
6. 试模结束:试模完成后,关闭注塑机,清理模具和注塑机设备。
将试模样品分类保存,并填写试模记录表,以备参考和进一步分析。
四、注意事项1. 安全第一:在进行注塑试模时,一定要遵守注塑机的安全操作规程,佩戴必要的防护装备,确保人身安全。
2. 精确记录:在试模过程中,准确记录注塑机参数、模具状态、试模材料和产品质量等信息。
这些记录是分析和评估试模结果的重要依据。
3. 合理调整:在试模过程中,根据观察和实际情况,及时调整注塑机参数和模具结构等,以获得更好的试模效果。
注塑模具试模和修模流程

页次注塑模试模及修模作业程序一、目的:1.1为规范塑胶注塑模的使用和保养,减少模具的损坏,确保产品质量满足客户需求.特制定以下规程二、流程说明2.1塑胶部注塑根据工程部所下发的<试模通知单>跟催模具是否到位,并安排架模员,加料员作好试模的准备,并通知试模工程师到现场试模。
2.2试模时需要有品质工程师或专案工程师.工模人员到现场监督,试模完后,架模人员如实填写模具水路图,架模点检表;试模员填写《射出成型参数记录表》,《试模检讨报告》以便存档作为以后量产参考;工程师把试模的《射出成型参数记录表》,《试模检讨报告》经审核后再分发给模具部和工程部参考,试模要试200只左右的良品交给品质工程师确认,同时保存5模样品供工模部修模参考;自己也需保存5模左右产品供试模存档;若试模产品被判定为不合格,应通知工模部重新修模,修好后应重新试模,若在试模过程中发现模具异常则应立即通知工模人员确认并修复后才可试模,重新试模的流程同以前的流程;若试模产品被判定为OK,则工模部应重新检查模具并按要求移交模具(连同模具清单)给生产部移交时须付《模具交接单》.《模具组立检查表》,塑胶部检查OK后予以签收,并做好模具挡案。
页次2.3模具投产后,由架模员把模具从模架上领出至现场.按模具的水路图和架模点检表,技术员或领班按射出成型参数表进行生产,开机生产进行;如实填写模具保养点检表和模具的生产履历表,下模后由架摸员吹清水路喷上防锈剂保养把模具送至模具架上,如实填写模具管制表。
2.4生产中模具发生异常,如需要停机修模而下模维修时,须开立异常通知单。
停线通知单.修模通知单,通知相关人员和相关人员,经审签后需开立模具维修单连同要修模具送至工模部进行维修;修复后再进行试模,技术人员如实填写试模检讨报告,试模产品经品保工程师和研发设计工程师确认,如判定为OK则可投入生产,如判定为NG则移交模具和该模具的试模报告,通知工模检讨,给予维修,如未下机台维修,可不用开立试模检讨报告,由塑胶部依照注塑的封样进行判定OK还是NG。
注塑新模试模作业标准

28、停机前十模左右可将冷却水路关闭,并依产品用料量情况提前将料斗关闭,保证停
成 机时螺杆内是清空的;
型 29、检查模具,清洁分型面及滑块、导柱内部的残留料屑及脏污; 后 30、冷却
水31管、拆模除具
温32度、过冷高却
注 意 事
水33道、内停及机 时34模、具工不作
项 的过程中
35、机器的操作不允许两人及以上人员同时操作,必须两人操作时,每进行一个动作都
13、仔细检查所有螺丝部件是否有松动,有做拆卸动作前要观察是否有配件号码,若无 要及时打上配件号码。
14、第一模产品应以无保压、射出中压、中速、小计量、短时间为原则进行注射,不可 以一次性将产品填充完整;
15、第一模产品必须仔细检查产品结构,注意检查产品是否有拉伤、粘模、断裂,并检
初 查模具内是否有残留料屑、胶丝等物; 步 16、检查流道是否平衡,在无保压的状态下逐渐加射出压力打饱,观察一模多腔时各穴 成 号的充填过程是否均匀平衡; 型 17、产品填充完整,用低速低压、短时间进行保压,渐渐提高至外观良好状态,无吸吭
20、开模终点位置要设定在能够顺利取出产品的最小值,顶针等各行程位置调整在最小
优 值,来缩短成型周期;
化
工 艺
21、在产品外观质量允许的条件下,锁模压力、成型温度、成型压力、速度、时间等要 素均要保持在最低最小最短;
22、检查模具在生产中是否具备再改良的可能性,是否有更好的方法,来提高产品质量
和生产效率,但必须保障安全;
11、检查顶杆,手动方式推顶,从短到长,至产品及料杆拉料梢全部顶出为止,再观察 顶杆回复位状况是否顺利,要注意顶针顶出时会有与滑块撞到的隐患;
12、三板模判定是否OK须要将模具开至最大限(须小心试开,不可猛拉,否则拉杆螺栓会 断)观察四根拉杆松紧程度是否一致。若有一根或几根松则为拉杆不平衡,需做调整;
试模作业规定
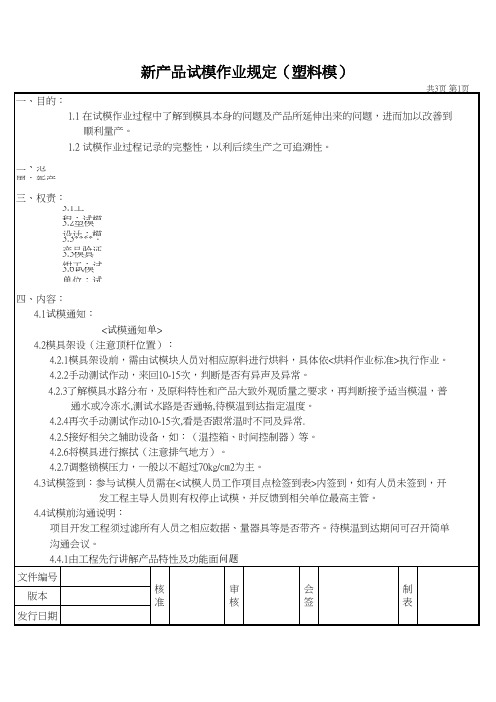
新产品试模作业规定(塑料模)
共3页 第2页
4.4.2模具设计需向试模人员解释模流走向与比例情况及产品单重等 4.4.3钳工需说明水路分布及注意事项 4.4.4品工需说明大致上质量要求状况 4.4.5制造工程需做制造工艺流程与相关位置说明 4.4.6试模人员除准备材料外还需说明调机方向 4.5模具查检:模具钳工需在试模前对模具依<塑模模具查检表>进行点检,将点检好之<塑模 模具查检表>带至现场交于试模块人员,进行试模中相应点检。 4.6开始试模时:一些压力,速度,位置之设定范围。(一般先以三段射出为主再进行保压) 第一段压力设置为:40~75 第二段压力设置为:50~90 第三段压力设置为:40~75 保压、压力:40~80 速度为:5~30 速度为:20~70 速度为:10~30 时间以不超过3秒为原则
新产品试模作业规定(塑料模)
共3页 第1页
一、目的: 1.1 在试模作业过程中了解到模具本身的问题及产品所延伸出来的问题,进而加以改善到 顺利量产。 1.2 试模作业过程记录的完整性,以利后续生产之可追溯性。 二、范围:新产品试模阶段。 三、权责: 3.1工程:试模主导,试模问题点(整机)检讨会议主导 3.2塑模设计:模流分析 3.3****:产品验证实施、质量状况记录 3.5模具钳工:试模查检、改善,试模问题点(单件)检讨会议主导 3.6试模单位:试模作业实施、并说明问题及调机方向,试模参数记录分析 四、内容: 4.1试模通知: <试模通知单> 4.2模具架设(注意顶杆位置): 4.2.1模具架设前,需由试模块人员对相应原料进行烘料,具体依<烘料作业标准>执行作业。 4.2.2手动测试作动,来回10-15次,判断是否有异声及异常。 4.2.3了解模具水路分布,及原料特性和产品大致外观质量之要求,再判断接予适当模温,普 通水或冷冻水,测试水路是否通畅,待模温到达指定温度。 4.2.4再次手动测试作动10-15次,看是否跟常温时不同及异常. 4.2.5接好相关之辅助设备,如:(温控箱、时间控制器)等。 4.2.6将模具进行擦拭(注意排气地方)。 4.2.7调整锁模压力,一般以不超过70kg/㎝2为主。 4.3试模签到:参与试模人员需在<试模人员工作项目点检签到表>内签到,如有人员未签到,开 发工程主导人员则有权停止试模,并反馈到相关单位最高主管。 4.4试模前沟通说明: 项目开发工程须过滤所有人员之相应数据、量器具等是否带齐。待模温到达期间可召开简单 沟通会议。 4.4.1由工程先行讲解产品特性及功能面问题 文件编号 版本 发行日期 核 准 审 核 会 签 制 表
试模打样作业标准
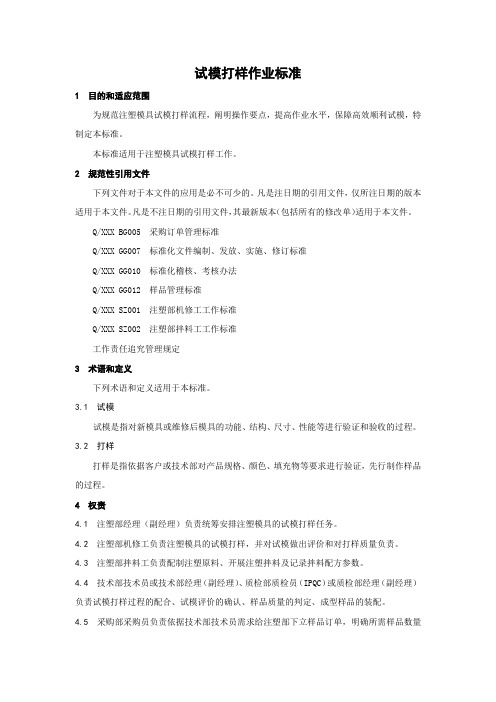
试模打样作业标准1 目的和适应范围为规范注塑模具试模打样流程,阐明操作要点,提高作业水平,保障高效顺利试模,特制定本标准。
本标准适用于注塑模具试模打样工作。
2 规范性引用文件下列文件对于本文件的应用是必不可少的。
凡是注日期的引用文件,仅所注日期的版本适用于本文件。
凡是不注日期的引用文件,其最新版本(包括所有的修改单)适用于本文件。
Q/XXX BG005 采购订单管理标准Q/XXX GG007 标准化文件编制、发放、实施、修订标准Q/XXX GG010 标准化稽核、考核办法Q/XXX GG012 样品管理标准Q/XXX SZ001 注塑部机修工工作标准Q/XXX SZ002 注塑部拌料工工作标准工作责任追究管理规定3 术语和定义下列术语和定义适用于本标准。
3.1 试模试模是指对新模具或维修后模具的功能、结构、尺寸、性能等进行验证和验收的过程。
3.2 打样打样是指依据客户或技术部对产品规格、颜色、填充物等要求进行验证,先行制作样品的过程。
4 权责4.1 注塑部经理(副经理)负责统筹安排注塑模具的试模打样任务。
4.2 注塑部机修工负责注塑模具的试模打样,并对试模做出评价和对打样质量负责。
4.3 注塑部拌料工负责配制注塑原料、开展注塑拌料及记录拌料配方参数。
4.4 技术部技术员或技术部经理(副经理)、质检部质检员(IPQC)或质检部经理(副经理)负责试模打样过程的配合、试模评价的确认、样品质量的判定、成型样品的装配。
4.5 采购部采购员负责依据技术部技术员需求给注塑部下立样品订单,明确所需样品数量和要求。
4.6 财务部会计负责依据注塑部经理(副经理)汇报的信息扣除模具厂原因导致的重复试模费用。
5 工作程序5.1 试模打样准备5.1.1 注塑模具开模后,应由模具厂模具工先行试模确认注塑模具是否符合开模要求,确认无误后由公司司机将注塑模具拉至注塑部再次试模确认。
技术部技术员或技术部经理(副经理)若有注塑模具需要试模时,应提前2天~3天以《工作联系单》(一联式表单)通知注塑部经理(副经理)。
注塑试模工作指导书

文件名称:注塑试模工作指导书
目的
本工作指导书目的是为了明确工厂注塑试模的作业流程 职责
注塑制程工程师,技术员配合执行, 注塑制程工程主管或经理监督本指导实施。
工作步骤
1.试模前准备 (详见SHDCSWE4.5-2.9F1) 1.1 材料准备 1.2 模具准备 1.3 机台准备 1.4 其它准备
2.试模步骤流程
接水管/压压块/顶杆固定
锁模力设定/模厚设定
最大开模行程/模具保护位置,压力,时间/ 高压切换位置设定
顶板回位装置/顶出次数,行程,压力设定
抽芯位置,压力设定
螺杆转速/计量行程/背压/松退行程设定
料管温度/ 模具温度/热流道温度设定
看日本注塑技术人员调机
看了一下日本的注塑技术人员验收模具时的调机,总结一下供大家参考: 1、根据模具、产品结构及原料选好合适的设备;
2、按设备的注射能力的80%设定压力50%设定速度(只用1段);
3、调整注射量。
从总重量的20%开始一直到基本成型;
4、现在开始加保压压力;
5、每次调整打3模;
6、根据注射监控的位置适当调整注射量(注射终了位置)。
这样调试后验收的模具,在任何相同的机型、条件下都可以成型。
也使工艺的调整量化、简单化。
射出压力,速度,位置设定
保压压力,时间,速度设定
在外观确认OK 后取连续300 模送QA 检验
记录工艺参数、试模报告,并让稳定工艺参数存入电脑
优化射压,射速/保压,保压切换位置/计量。
试模作业规范
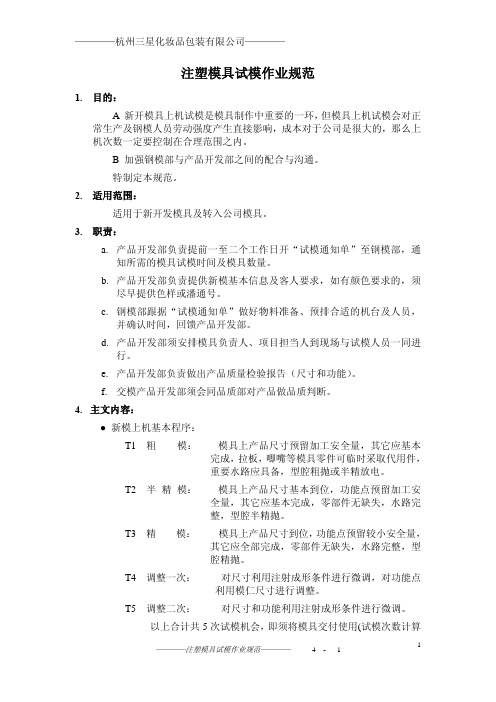
注塑模具试模作业规范1.目的:A 新开模具上机试模是模具制作中重要的一环,但模具上机试模会对正常生产及钢模人员劳动强度产生直接影响,成本对于公司是很大的,那么上机次数一定要控制在合理范围之内。
B 加强钢模部与产品开发部之间的配合与沟通。
特制定本规范。
2.适用范围:适用于新开发模具及转入公司模具。
3.职责:a.产品开发部负责提前一至二个工作日开“试模通知单”至钢模部,通知所需的模具试模时间及模具数量。
b.产品开发部负责提供新模基本信息及客人要求,如有颜色要求的,须尽早提供色样或潘通号。
c.钢模部跟据“试模通知单”做好物料准备、预排合适的机台及人员,并确认时间,回馈产品开发部。
d.产品开发部须安排模具负责人、项目担当人到现场与试模人员一同进行。
e.产品开发部负责做出产品质量检验报告(尺寸和功能)。
f.交模产品开发部须会同品质部对产品做品质判断。
4.主文内容:●新模上机基本程序:T1 粗模:模具上产品尺寸预留加工安全量,其它应基本完成,拉板,唧嘴等模具零件可临时采取代用件,重要水路应具备,型腔粗抛或半精放电。
T2 半精模:模具上产品尺寸基本到位,功能点预留加工安全量,其它应基本完成,零部件无缺失,水路完整,型腔半精抛。
T3 精模:模具上产品尺寸到位,功能点预留较小安全量,其它应全部完成,零部件无缺失,水路完整,型腔精抛。
T4 调整一次:对尺寸利用注射成形条件进行微调,对功能点利用模仁尺寸进行调整。
T5 调整二次:对尺寸和功能利用注射成形条件进行微调。
以上合计共5次试模机会,即须将模具交付使用(试模次数计算方法依“新开模奖惩制度”标准执行) 。
● 新模上机基本条件:a.. 信息:产品开发部负责提供产品材料、产品颜色及后续加工方式。
b. 产品开发部送试的模具应具备:1. 排气已经开好。
2. 滑块已经定位。
3. 水嘴已经接好并确认不漏水。
4. 各配件应齐全,模具详细资料,特别是共用模座,应确认清楚相关配件)。
注塑试模作业指导书
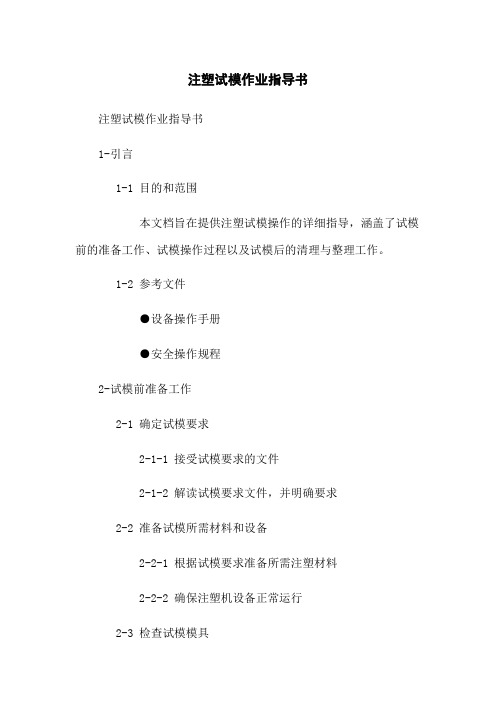
注塑试模作业指导书注塑试模作业指导书1-引言1-1 目的和范围本文档旨在提供注塑试模操作的详细指导,涵盖了试模前的准备工作、试模操作过程以及试模后的清理与整理工作。
1-2 参考文件●设备操作手册●安全操作规程2-试模前准备工作2-1 确定试模要求2-1-1 接受试模要求的文件2-1-2 解读试模要求文件,并明确要求2-2 准备试模所需材料和设备2-2-1 根据试模要求准备所需注塑材料2-2-2 确保注塑机设备正常运行2-3 检查试模模具2-3-1 检查模具的完整性和净度2-3-2 检查模具的温度控制系统2-4 安装试模模具2-4-1 确保注塑机设备停止运行2-4-2 按正确顺序安装试模模具2-5 调整注塑机参数2-5-1 根据试模要求设置注塑机的参数2-5-2 检查注塑机参数的正确性3-试模操作过程3-1 启动注塑机3-1-1 检查注塑机设备的电源和压力3-1-2 打开注塑机的电源,并调节压力3-2 加热模具3-2-1 按照模具的要求设置和调节模具温度 3-2-2 等待模具达到设定温度3-3 调试注塑机参数3-3-1 开模和闭模检查3-3-2 设置注射速度和压力3-4 进行试模操作3-4-1 进行试模前的喷嘴和溢流孔清洁3-4-2 将注塑材料放入注塑机的料斗中3-4-3 开始试模操作3-5 监控试模过程3-5-1 观察注塑机运行情况3-5-2 检查模具的冷却效果3-5-3 注意模具是否有异常情况3-6 完成试模3-6-1 停止注塑机的运行3-6-2 取出试模样品3-6-3 检查试模样品的质量和尺寸是否符合要求4-试模后清理与整理工作4-1 关闭注塑机4-1-1 关闭注塑机的电源4-1-2 清理注塑机工作区域4-2 拆卸模具4-2-1 确保注塑机设备停止运行4-2-2 按照正确顺序拆卸试模模具4-3 清洁模具4-3-1 使用适当的工具和清洁剂清洁模具4-3-2 检查模具的任何损坏或磨损4-4 整理工作区域4-4-1 清理工作区域的杂物和残留物4-4-2 检查工作台面和工具是否整齐摆放附件:1-试模要求文件2-设备操作手册法律名词及注释:1-注塑机:将熔融状态的塑料通过注射装置注入模具中的一种设备。
试模操作流程标准规范

试模操作流程试模主要分四部分:(1)试模前模具的检查(2)试模前的准备工作和调试(3)试模时的注意事项(4)试模后模具的检收一、试模前模具的检查模具做好后,需要对模具进行试模前的检查,以发现模具设计和制造中的问题,以便及时纠正,其具体步骤如下:(1)注塑模的外观检查1.成型零件、浇注系统等与熔料接触的表面应光滑、平整、无塌坑、伤痕等缺陷。
2.模具的闭合行程,安装于机器的各配合部位尺寸、脱模方式、开模距离、模具工件要求等应符合设备的相关条件。
3.模具上应有生产号和合模标志,各种接头、阀门、附件、备件应齐全。
4.各滑动零件的配合间隙应符合要求,起止位置定位正确,镶件紧固应紧固牢靠。
5.对于注塑腐蚀性较强的注塑模,其模具型腔的表面应镀铬和防腐处理。
6.模具的外观部分不应当有锐角,大、中型模具应有起吊用的吊孔、吊环。
7.互相接触的承压零件,应有合理的承压面积和承压方式,避免直接承受挤压。
8.模具的稳定性良好,有足够强度,工作时应受力匀衡,行动平稳。
(2)模具的空运转检查模具安装好后,必须经过空运转检查,经便进一步发现问题,进而解决问题。
1.将模具缓缓合拢,合模后各结合面均应接触紧密,不得出现间隙。
2.开模时顶出脱模机构应保证顺利脱模,以便取出塑件和浇注系统废料。
3.活动型芯,顶出及导向部分等运动时应滑动平稳、灵活、动作协调可靠。
4.检查各锁紧机构、应能可靠、稳妥地锁紧,各紧固件不得有任何松动现象。
5.各气动、液动控制系统动作正确,不泄漏、不产生过大振动,各阀门工作正常。
6.冷却系统的水路应畅通,不漏水,各种控制阀门控制正常。
二,试模前的准备工作及调试试模是为了检查模具制作的质量好坏,能否生产出合格产品来。
1.试模前,应检查所用原料是否符合要求,不符合要求的应进行处理或更换;欲试之原料先行干燥,PE、PP、PO M不需干燥其余均要,利用新料试才标准。
2•模具挂上中心孔要对准锁模力以总顿数的1/3即可,如射出时分模面不是因射压太高之关系起毛边,可渐渐增加锁模顿数直到不起毛边为至如此做法可增长模具使用寿命。
注塑试模作业规范

注塑试模作业规范1.0目的1.1.确认模具的性能和注塑件结构状态是否满足要求。
1.2.及时发现并找出成型过程中的问题,保障生产过程顺利进行,以免造成无谓浪费。
1.3.找出最佳的成型工艺参数范围,为以后批量生产奠定成型基础。
确保产品的质量达到设计目的或客户的要求。
2.0范围适用于注塑领班、注塑技术员、注塑模具上模员的试模作业。
3.0职责按要求组织、协调相关试模事宜,上下模、工艺调试,及时发现注塑模具、产品结构、塑料原料、色母(色粉)存在的问题,并力求从工艺角度解决其问题,把存在的问题及时反馈给相关部门(开发部或采购部)。
4.0试模前的准备工作4.1.了解有关资料:最好能取得模具的设计图面,详予分析,并要求模具维修师傅和项目工程师参加试模工作。
4.2.检查机械配合动作:要注意模具外观有否刮伤,缺件及松动等现象;滑板动作是否顺畅;水道及气管接头有无泄漏;模具结构特殊的话要有顶针保护开关、或限位装置、模具的定位装置、电热插头等是否完整。
5.0选择适合的试模机器:5.1.锁模力:產品透影面的最低要求鎖模力,以機器鎖模力的70%为基准。
长×宽(cm)×0.155(平方英寸in2)×各塑料锁模力系数(ton/in2)常用:ABS、PMMA、2.5-4.0ton/in2;HIPS、PS1.0-2.0ton/in2PC、POM、3.0-5.0ton/in2;GPPS(薄壁)3.0-4.0ton/in2TPU、PP、PE、1.5-2.5ton/in2;POM2.0-5.0ton/in25.2.射胶量:产品重量的30%~75%最合适.5.3.导柱的宽度:装上模具并能安全的锁紧.5.4.最大的开模行程:能方便取出产品和水口。
6.0原料准备:6.1依不同原料特性做正确的烘烤。
6.2试模与将来量产尽可能采用同样的原料。
7.0安装模具:7.1装模时注意在锁上所有夹模板及开模前吊钩不要取下,以免夹模板松动或断裂导致模具掉落。
注塑试模作业指导书

注塑试模作业指导书注塑试模作业指导书一、目的:确认注塑模具、产品结构的状态、塑料原料、色母(色粉)是否符合开发设计的要求,保证量产的顺利进行。
二、范围:适用于注塑领班、注塑技术员、注塑架模员的试模作业。
三、职责:按要求组织、协调相关试模事宜,上下模、工艺调试,及时发现注塑模具、产品结构、塑料原料、色母(色粉)存在的问题,并力求从工艺角度解决其问题,把存在的问题及时反馈给相关部门(开发部或采购部)。
四、作业指导:(一)试模前的注意事项1、了解模具的有关资料:取得模具的设计图纸、模具使用说明书等相关资料,详细分析,并约得模具维修师参加试模工作。
2、先在工作台上检查其机械配合动作:要注意有否刮伤、缺件及松动等现象,模向滑板动作是否确实,水路及气管接头有无泄漏,模具的开程若有限制的话也应在模上标明。
以上动作若能在挂模前做到的话,就可避免在挂好模后发现了问题,再去拆卸模具所发生的工时浪费。
3、当确定模具各部动作得宜后,就要选择适合的试模射出机,在选择时应注意①射出容量②导杆的宽度③最大的开程④配件是否齐全等。
一切都确认没有问题后则下一步骤就是吊挂模具,吊挂时应注意在锁上所有夹模板及开模之前吊钓不要取下,以免夹模板松动或断裂以致模具掉落。
模具装妥后应再仔细检查模具各部份的机械动作,如滑板、顶针、退牙结构及限制开关等动作是否确实。
并注意射料嘴与进料口是否对准。
下一步则是注意合模动作,此时应将关模压力调低,在手动及低速的合模动作中注意看及听是否有任可不顺畅动作及异声等现象。
4、试模时不可忽略模具温度,而在短时试模及将来量产时模具温度最不易掌握,而不正确的模温足以影响样品的尺寸、光度、缩水、流纹及欠料等现象,若不用模温机予以控制,将来量产时就可能出现困难。
5、适当提高模具温度:依据成品所用原料的性能及模具的大小选用适当的模温机将模具的温度提高至生产时所须的温度。
待模温提高之后须再次检视各部份的动作,因为钢材因热膨胀之后可能会引起卡模现象,因此须注意各部的滑动,以免有拉伤及颤动的产生。
塑胶模具试模作业规范

塑膠模具試模作業規範1. 目的為使塑膠模具試模作業有標準之試模流程,訂立此標準,以利確認模具之良窳及量產性是否良好,並作為修模之參考,減短投產試模之日程。
2. 適用範圍公司開發之塑膠模具3. 權責3.1. 工程(開發階段)單位負責試模及提出試模後之檢討。
3.2 . 試模廠商依工程.試模之需求,排定機台及工程師依試模作業標準之流程試模3.3. 工程單位試模時,模具製造商及其設計人員,需會同試模並檢討改善對策4. 定義4.1. 工程單位:執行試模依時程提出需求及檢討,及試模後樣品及表單資料之確認。
4.2. 試模生產單位:機台.週邊之準備,模具之架設,及確認模具之作動及試模品之優劣,另成型條件及相關表單之記錄5. 流程圖附件一6. 作業程序6.1 試模先期作業6.1.1 提出試模需求(MME)確認試模材料及試模機台之規格.6.2 模具上機前作業規定6.2.1 確認模具是否保養完成,(模具油污.積碳等之清除.滑動面上油)。
6.2.2 確認機台是否適用,包括機台鎖模力.料管射出量.射出速度。
6.2.3 確認此套模具所需設備.零件是否備妥,並且可以正常運作,如模溫機.溫控箱.油管.水栓.水栓接頭……..。
6.2.4 檢查材料是否正確,烘料時間是否足夠6.2.5 機械手,治具是否備妥6.3 架模作業規定6.3.1 確認料管射嘴與模具灌嘴密合度。
6.3.2 合模前先確定頂出桿安裝是否正確6.3.3 開模前確定有將模具上公母模板固定器鬆開6.3.4 將模溫機接頭裝上並確認進出點是否正確.T1試模請將模溫機進出點記錄於試模條件表(圖示為佳)試模前作業規定6.4.1 機臺料管加熱是否正常,模具熱澆道加溫空射是否正常6.4.2 機台液壓油油溫加至設定溫度。
6.4.3 檢查模具水路是否正常,快速接頭不可有漏油現象6.4.4 檢查模具頂出裝置並頂出拉回10次確認模具頂出機構正常6.4.5 檢查模具作動是否正常(模具加熱前與加熱後),滑塊.斜銷特別注意6.4.6 請工程提供材料物性表,若有模流分析的需一併附上6.4.7 量測模具加溫後模溫是否到達所需溫度,並做記錄(試模開始時模溫)6.4.8 試模塑料必須由除濕乾燥機自動吸至料管(防止材料吸溼)6.4.9 清除模具PL面油污(避免逃氣不良)6.4.10 觀察公母模仁是否可以短射(有黏模可能,可酌量噴上離型劑,離型劑內含物需符合RoHS規定)6.4.11 機台如有空運轉(DRY RUN)功能時,可先以此功能試模具作動,特別注意模具異音6.4.12 如非第一次試模請依上次試模條件及樣品作為參考(更換機台及模具設變要如T1試模重新設定成型條件)6.5 試模中作業規定6.5.1 先短射料頭段得出進料點之料管計量位置(射出速度變更將影響進料點位置)6.5.2 必須將保壓時間加入但不給壓力,以免進料點還未封口就開始加料(未封口加料將會因加料背壓將料填充入模腔)6.5.3 在模具可以短射情況下,成品充填由30%開始,每次調整以10%漸進式增加,多模穴需觀察射料平均與否6.5.4 每次調整需射出20~30模後再取樣留底(3~5模含料頭)才可做下一個條件6.5.5 成品填充至約90%以上,再加上保壓壓力(特殊模具不在此限)6.5.6 成品未加保壓前需量成品單重與料頭重量6.5.7 冷確時間須超過加料時間1秒以上6.5.8 加保壓後需將機械手開啟,以自動方式調整成型條件6.5.9 保壓一段壓力以射壓一半為主,保壓二段以保壓一段一半為主(特殊模具不在此限)6.5.10 設定第一段保壓時,保壓時間以0.1秒開始,每次調整以0.1~0.2秒為主(但保壓總時間不變)6.5.11 試模中需觀察機台之成型條件曲線圖(成型條件需要圖識)6.5.12 加保壓後,每次更新條件都需秤重並且比較單重變化6.5.13 當成品單重不再變化需將第二段保壓加減50bar確認第二段壓力變化不會影響成品單重,單重不再變化即可將條件定下,並且開始試作6.5.14 試作取樣 .試作時間以模具結構為判定因素6.5.15 試模過程中須測試停止30秒後射嘴及熱膠道可正常射出無冷料.塞頭.冷料現象6.5.16 成品黏模時使用斜口鉗夾取時,需墊銅塊,以免碰傷模具表面,若有碰傷模面之疑慮時,務必下模分解模仁取出黏模成品6.5.17 當停機時間超過3分鐘,需退座將料管內停滯料射出,避免碳化材料射入模腔6.5.18 試模中隨時注意模具狀況,一有異常立即停止試模,並通知模具師傅到場判定6.5.19 完成條件設定停機前,先將曲線圖寫入射出機之磁碟片,以免無法填寫試模條件6.5.20 停機1小時量測模具試模後溫度,每量測1點必須再做3~5模再量測下一點每一模穴都必須記錄模溫,每套模具至少量測4點確實記錄於成型條件表,此模溫盡量以連續試跑4小時以後量測以免影響量測準確度6.6 試模完成作業規定6.6.1 T1試模後模具廠(MME)需觀察模具逃氣.料削.及模具合模狀況6.6.2 詳細填寫成型條件表,並將試模問題點明確填寫在試模記錄表(盡量以草圖標示成品問題6.6.3 記錄背壓值,若使用手動調整背壓之機台,將背壓刻度及圈數並紀錄於試模條件上6.6.5 試模條件表及試模資料表(Process Data Sheet)填寫及資料由試模單位提供,MME主擔當工程師當場確認填寫正確無誤。
试模作业指导书(注塑部)
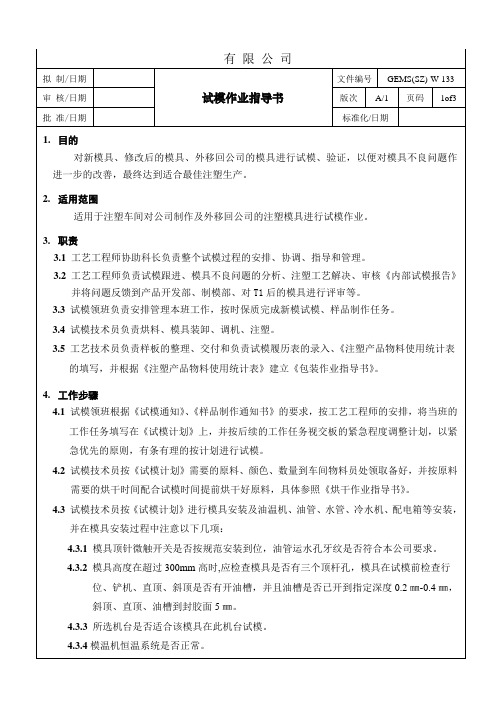
4.11试模技术员按产品不同规格填写新机型量产前《注塑产品物料使用统计表》,经工艺工程师审核后交产品开发部项目科签收,并根据《注塑产品物料使用统计表》建立《包装作业指作业导书》。
4.12试模技术员试完模后必须擦干净模腔表面、并在模腔表面上加喷防锈油后再卸模,新模具或未交付生产的模具交制模部模具管理员统一管理;特殊情况需马上修模或改模的模具,可直接交到制模车间由制模科长即时安排修模或改模。
4.4试模领班与试模技术员按产品开发部提供的尺寸、产品外观、结构配合要求进行调校注塑参数、注塑成型,若试模过程中发现模具有异常或产品达不到品质要求时,应及时通知本部门工艺工程师或科长现场确认解决,必要时通知产品开发部项目工程师、制模部制模主管等相关人员到现场监督试模,共同分析和解决问题,并视情况决定是否作落模处理。自检确认产品已符合要求或已是最好状态时,则通知质量保证部QC员或样板工程师到机位检测,若有异常再调校注塑参数,直至达到符合产品要求。
4.3.2模具高度在超过300mm高时,应检查模具是否有三个顶杆孔,模具在试模前检查行位、铲机、直顶、斜顶是否有开油槽,并且油槽是否已开到指定深度0.2㎜-0.4㎜,斜顶、直顶、油槽到封胶面5㎜。
4.3.3所选机台是否适合该模具在此机台试模。
4.3.4模温机恒温系统是否正常。
4.3.5模具安装过程必须按《模具安装作业指导书》操作。
6.2《试模通知》(编号:GEMS(SZ)-Q-0094)
6.3《样品制作通知书》(编号:GEMS(SZ)-Q-0082)
6.4《物料试用报告》(编号:GEMS(SZ)-Q-0214)
- 1、下载文档前请自行甄别文档内容的完整性,平台不提供额外的编辑、内容补充、找答案等附加服务。
- 2、"仅部分预览"的文档,不可在线预览部分如存在完整性等问题,可反馈申请退款(可完整预览的文档不适用该条件!)。
- 3、如文档侵犯您的权益,请联系客服反馈,我们会尽快为您处理(人工客服工作时间:9:00-18:30)。
23、观察产品脱模情况,考虑是否可用于全自动生产或进行改良后能用于全自动生产。
24、注意观察模具状况,判别模具动作的声音,弹簧等部件是否正常,磨擦是否过大、 动作过程是否卡滞、顶针是否安全复位等现象;
成 25、手触 型 摸模具温 过 26、仔细 程 观察开关
27、填写成型试模报告,并将试模中的各项状况说明,填写成型工艺卡,备注栏内重点 说明需要注意的事项。
13、仔细检查所有螺丝部件是否有松动,有做拆卸动作前要观察是否有配件号码,若无 要及时打上配件号码。
14、第一模产品应以无保压、射出中压、中速、小计量、短时间为原则进行注射,不可 以一次性将产品填充完整;
15、第一模产品必须仔细检查产品结构,注意检查产品是否有拉伤、粘模、断裂,并检
初 查模具内是否有残留料屑、胶丝等物; 步 16、检查流道是否平衡,在无保压的状态下逐渐加射出压力打饱,观察一模多腔时各穴 成 号的充填过程是否均匀平衡; 型 17、产品填充完整,用低速低压、短时间进行保压,渐渐提高至外观良好状态,无吸吭
11、检查顶杆,手动方式推顶,从短到长,至产品及料杆拉料梢全部顶出为止,再观察 顶杆回复位状况是否顺利,要注意顶针顶出时会有与滑块撞到的隐患;
12、三板模判定是否OK须要将模具开至最大限(须小心试开,不可猛拉,否则拉杆螺栓会 断)观察四根拉杆松紧程度是否一致。若有一根或几根松则为拉杆不平衡,需做调整;
要告知对方将要进行的动作。
模具部
20、开模终点位置要设定在能够顺利取出产品的最小值,顶针等各行程位置调整在最小
优 值,来缩短成型周期;
化
工 艺
21、在产品外观质量允许的条件下,锁模压力、成型温度、成型压力、速度、时间等要 素均要保持在最低最小最短;
22、检查模具在生产中是否具备再改良的可能性,是否有更好的方法,来提高产品质量
和生产效率,但必须保障安全;
等不良,压力过高将出现内应力过大等问题;
18、依塑料件检验方法自检产品外观及轮廓尺寸,检查产品是否具有不良现象,并加以 微调改善,工艺稳定后连续生产10模,观测成型工艺是否稳定;
19、观察成型过程,微调整参数,选择最佳的成型工艺,在不影响质量和安全的情况下 将效率提至最高状态,包括工人取产品加工的动作,要减少浪费;
28、停机前十模左右可将冷却水路关闭,并依产品用料量情况提前将料斗关闭,保证停
成 机时螺杆内是清空的;
型 29、检查模具,清洁分型面及滑块、导柱内部的残留料屑及脏污; 后 30、冷却
水31管、拆模除具
温32度、过冷高却
注 意 事
水33道、内停及机 时34模、具工不作
项 的过程中
35、机器的操作不允许两人及以上人员同时操作,必须两人操作时,每进行一个动作都
注塑试模/开机作业标准
目的
提高生 产率,缩
范围
本标准 ห้องสมุดไป่ตู้用于新
1、机台
准2、备原:料机
试 模 准
准3、备配:件材 准4、备辅:助使
备 设备:参
5、对可能出现的事态预防,提前分析开机过程中潜在的安全、故障、损坏的可能性,错
误的发生度,哪怕出现的几率很小也要提前分析。
6、设定 开关模行
7、确认导柱与导套的配合状况,开合模的动作是否顺滑,观察机械运动部分是否有问题 存在,不可强制性动作,防止造成模具各结构部位之损伤;
8、检查抽芯油缸前退是否正常,是否有漏油现象,开关模时是否会有碰撞;
9、观察模腔表面状况,如排气槽(流道部份,型腔部份),合模时紧密程度。合模数次后 再观察分型面上是否有被压伤的痕迹;
模 10、滑块 具 弹簧、顶 检 11、滑块观察其动作状况,是否顺畅,目视是否有损伤,推动滑块时感觉其所需力道反 查 映顺畅与否,并观察其复位是否到位及滑块润滑是否良好;