LS7说明书20160801
北方工具和设备产品说明书:通道管

Telescopic CylinderOwner’s ManualWARNING: Read carefully and understand all ASSEMBLY AND OPERATION INSTRUCTIONS before operating. Failure to follow the safety rules and other basic safety precautions may result in serious personal injury.Items #66735, #66736, #66738, #66739, #66740, #66741, #66742, #66743, #66744, #66745Thank you very much for choosing a NorTrac™ product!For future reference, please complete the owner’s record below:Serial Number/Lot Date Code: ________________________________ Purchase Date: ____________________________________________ Save the receipt, warranty, and this manual. It is important that you read the entire manual to become familiar with this product before you begin using it.This telescopic cylinder is designed for certain applications only. Northern Tool and Equipment is not responsible for issues arising from modification or improper use of this product such as an application for which it was not designed. We strongly recommend that this product not be modified and/or used for any application other than that for which it was designed.For technical questions, please call 1-800-222-5381.Intended Use (4)Packaging Contents (4)Technical Specifications (4)Important Safety Information (4)Specific Operation Warnings (6)Main Parts of Telescopic Cylinder (6)Assembly Instructions (6)Operating Instructions (14)After Each Use (17)Maintenance (17)Troubleshooting (18)Parts Diagram (18)Parts List (19)Replacement Parts (19)Limited Warranty (20)The NorTrac series telescopic cylinders are ideal for construction, mining, forestry, marine, demolition, military, material handling, agriculture, truck and trailer, loader, utility, and waste management.•Telescopic Cylinder •Owner’s ManualCylinder DisassemblyBefore Disassembling the Cylinder•Dismantle the cylinder in a clean location.•Each part should be thoroughly cleaned. If the cylinder is to be dismantled for any length of time, coat the metal parts, which are to be reused with a good rust inhibitor and store them in aprotected area.Disassembling the Cylinder1. Un-thread the top screw on the rear cap (#23).2. Remove the rear cap.3. Drain the oil inside.4. Knock the trunnion (#31) to force the inner piston rod (#32) out.5. Take out the piston rod (includes a larger and smaller one).6. Knock the inside edge of the piston rod to find the correct position of the inner support ring.7. Remove the support ring.8. Punch holes into the back of the inner groove.9. You may also drill holes with a power drill.10. Rotate the inner back-up ring hole at an angle (using the process above) to remove the innerback-up ring (#9).11. Take out the two piston rods inside.12. Repeat steps 8, 9, and 10. Remove the back-up ring (#9) from the larger piston rod.13. Take out the smaller piston rod.14. Remove the #8, the #16, and the #19 BS seals from the larger and smaller piston rod.15. The #18 back-up ring is at the other end of the piston rod. See the image below.Reassembly Procedures1. Place the 3rd stage tube (#2) back inside the outer tube assembly (#1) and install the collar (#6).2. Place the 2nd stage tube (#3) inside the 3rd stage tube (#2) and install the collar (#7).3. Re-thread the rod end (#13) onto the 1st stage tube (#4) and put the 1st stage tube (#4) into thecylinder. Be careful not to damage the seals while installing each tube.4. Thread the rear cap (#23) onto the cylinder and tighten the hex set screw (#26).Operating Conditions•The maximum operating pressure must not exceed 2500 PSI.•The contamination level of the oil must not exceed 16/13/10 from the ISO standard 4406. •The acceptable temperature range is -40° F to 200° F.Formula for Calculating the Initial Required Cylinder Force to Lift a Load:A = the distance from the center of the load to the center of the dump body hinge pin (inches)B = the length from the center of the cylinder base pin to the center of the dump body hinge pin (inches)Load (lb.) x A /B = Initial required cylinder force (lb.)Example:50,000 (lb.) x 85"/166” =25,602 lb. = Initial required force (lb.)B = The length of cylinder base pin to body hinge pin D = Dump Angle CoefficientB X D = Approximate Required StrokeExample:166(B) X 845(D)= 140 Approximate Required Stroke•When the cylinder is not in use it should be fully retracted to prevent the chromed cylinder shaft from becoming damaged.•Always store the cylinder inside to protect it against harsh weather conditions.•Fill the cylinder with oil to prevent internal corrosion caused by air condensation. Tilt the cylinder to make sure that all seals are completely in contact with the oil to avoid any prematuredeterioration of the seals.•Cover any unpainted part with a rust inhibitor to avoid corrosion.•Regularly grease the trunnion pins. The time between greasing will be dependent on the amount the cylinder is used. Improper lubrication will result in the pins wearing prematurely.•For replacement parts and technical questions, please call Customer Service at 1-800-222-5381. •Not all product components are available for replacement. The illustrations provided are a convenient reference to the location and position of parts in the assembly sequence.•When ordering parts, the following information will be required: item description, item model number, item serial number/item lot date code, and the replacement part reference number. •The distributor reserves the rights to make design changes and improvements to product lines and manuals without notice.Northern Tool and Equipment Company, Inc. ("We'' or "Us'') warrants to the original purchaser only ("You'' or "Your") that the NorTrac product purchased will be free from material defects in both materials and workmanship, normal wear and tear excepted, for a period of two years from date of purchase. The foregoing warranty is valid only if the installation and use of the product is strictly in accordance with product instructions. There are no other warranties, express or implied, including the warranty of merchantability or fitness for a particular purpose. If the product does not comply with this limited warranty, Your sole and exclusive remedy is that We will, at our sole option and within a commercially reasonable time, either replace the product or product component without charge to You or refund the purchase price (less shipping). This limited warranty is not transferable.Limitations on the WarrantyThis limited warranty does not cover: (a) normal wear and tear; (b) damage through abuse, neglect, misuse, or as a result of any accident or in any other manner; (c) damage from misapplication, overloading, or improper installation; (d) improper maintenance and repair; and (e) product alteration in any manner by anyone other than Us, with the sole exception of alterations made pursuant to product instructions and in a workmanlike manner.Obligations of PurchaserYou must retain Your product purchase receipt to verify date of purchase and that You are the original purchaser. To make a warranty claim, contact Us at 1-800-222-5381, identify the product by make and model number, and follow the claim instructions that will be provided. The product and the purchase receipt must be provided to Us in order to process Your warranty claim. Any returned product that is replaced or refunded by Us becomes our property. You will be responsible for return shipping costs or costs related to Your return visit to a retail store.Remedy LimitsProduct replacement or a refund of the purchase price is Your sole remedy under this limited warranty or any other warranty related to the product. We shall not be liable for: service or labor charges or damage to Your property incurred in removing or replacing the product; any damages, including, without limitation, damages to tangible personal property or personal injury, related to Your improper use, installation, or maintenance of the product or product component; or any indirect, incidental or consequential damages of any kind for any reason.Assumption of RiskYou acknowledge and agree that any use of the product for any purpose other than the specifieduse(s) stated in the product instructions is at Your own risk.Governing LawThis limited warranty gives You specific legal rights, and You also may have other rights which vary from state to state. Some states do not allow limitations or exclusions on implied warranties or incidental or consequential damages, so the above limitations may not apply to You. This limited warranty is governed by the laws of the State of Minnesota, without regard to rules pertaining to conflicts of law. The state courts located in Dakota County, Minnesota shall have exclusive jurisdiction for any disputes relating to this warranty.Distributed by:Northern Tool & Equipment Company, Inc.Burnsville, Minnesota 55306Made in ChinaPage 21 of 21。
LS说明书
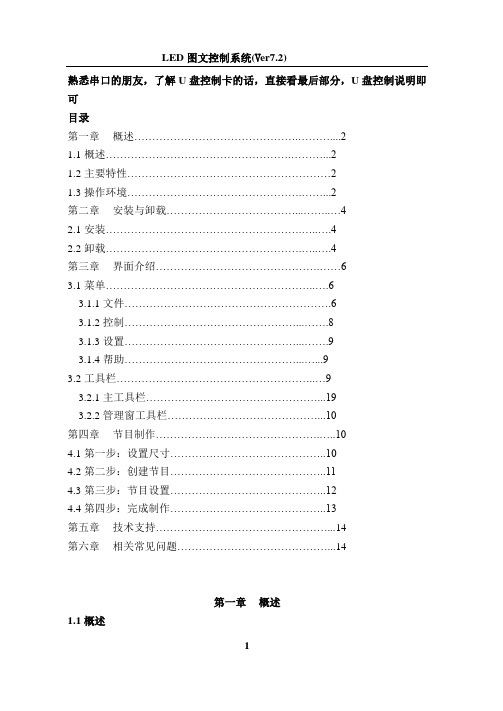
熟悉串口的朋友,了解U盘控制卡的话,直接看最后部分,U盘控制说明即可目录第一章概述 (2)1.1概述 (2)1.2主要特性 (2)1.3操作环境 (2)第二章安装与卸载 (4)2.1安装 (4)2.2卸载 (4)第三章界面介绍 (6)3.1菜单 (6)3.1.1文件 (6)3.1.2控制 (8)3.1.3设置 (9)3.1.4帮助 (9)3.2工具栏 (9)3.2.1主工具栏 (19)3.2.2管理窗工具栏 (10)第四章节目制作 (10)4.1第一步:设置尺寸 (10)4.2第二步:创建节目 (11)4.3第三步:节目设置 (12)4.4第四步:完成制作 (13)第五章技术支持 (14)第六章相关常见问题 (14)第一章概述1.1概述LED图文控制系统是由联胜电子科技公司为图文控制系统专业制作的集编辑、模拟和控制为一体的专业软件。
它不仅安全、稳定、实用而且便于各类人群的学习和使用。
由于其高可靠性和稳定性,它被广泛运用于各个领域。
本软件其根据人机交互原理设计使其结构合理、便于使用和维护,界面简洁而不单调,功能强大却不紊乱,处处显示出以人为本的特点。
最为重要的是它具有功能上的可扩展性。
1.2主要特性节目的播放是以页的方式进行的,页的数量根据LED条屏的尺寸的不同而各异。
其控制方式通常采用串口通讯,包括单机版的RS232以及服务器版的RS485网络通讯。
1.3操作环境操作系统:中/英文Windows/XP;硬件配置:CPU: 奔腾300MHz或以上内存:64M或以上第二章安装与卸载2.1 安装安装LED图文控制系统,可按照如下步骤进行:双击“setup”文件,在弹出的安装向导对话框中,系统显示界面:单击下一步,系统将自动进行安装。
)系统自动完装完毕后,会在您的电脑桌面上自动生成一个快捷方式图标双击该图标直接运行程序。
2.2卸载LED图文控制系统软件为您提供了一个自动卸载功能选择,以删除控制系统的所有文件、程序组以及快捷方式等。
杂草剃须刀产品手册说明书

Product Contents . . . . . . . . . . . . . . . .2 Assembly Instructions . . . . . . . . . . .3-4 Operating Instructions . . . . . . . . . . . .4 Blade Sharpening Instructions . . . . .5-6Safety Instructions . . . . . . . . . . . . . . .7 Replacement Parts . . . . . . . . . . . . . .8 Product Warranty . . . . . . . . . . . . . . . .8Table of Contents:Item 580110Important Information:2Please read these instructions thoroughly before use. Failure to follow instructions may result in equipment damage or failure, losses, injury or death.WARNING:To reduce the risk of injury:• T he Weed Razer is designed for cutting submerged, partially emergent, or emergent aquatic vegetation from underwater. Any other use is strictly prohibited. Before using the Weed Razer, please read this manual carefully to understand the proper use of the unit.• T he Weed Razer blade(s) are razor sharp. The blade covers should be on while assembling the tool and when tool is not in use. Failing to comply can result in severe lacerations, dismemberment, and even death. SAFETY FIRST:Instructions containing a warning within this manual are marked with a symbol.Keep out of reach of children.Do not use with children in immediate area.IMPORTANT: J enlis, Inc ® is not responsible for equipment damage or failure, losses, injury or death resulting from failure to follow safety precautions, misuse or abuse of equipment.CL D G IAB FEK HJ PRODUCT CONTENTS: 3Notes:Assembly & InstructionsTools Required: • #3 Phillips Screwdriver• 7/16” WrenchStep 1Insert 4 of the 1.2” Bolts (J) into the four outermostholes of one of the triangular Support Brackets (D)making sure to slide the bolts through the domedside, then place the bracket on a flat work surfacewith the screw heads down. Place a Nylon Spacer(G) on each of the bolts at the base of the triangularbracket.Step 2 Place each Blade (C) onto the Support Bracket (D)so that each blade edge faces outward and theholes seat over the two bolts at the narrow endof the triangular bracket. Next, seat the secondtriangular Support Bracket (D) over the assemblywith the domed side facing up and place a washerand nut on each of the four bolts—be sure tosimply hand tighten at this time.Step 3Slide the blade covers back about 2” to makeroom for the handle. Take the two halves of theWeed Deflector (F) and snap together at the pinsmolded into each piece. Slip the Weed Deflector(F) onto the Angled Handle (B) at the end withtwo holes making sure that the hole in the WeedDeflector aligns with the second hole from the end,then slide the Angle Handle (B) into the SupportBracket (D) so that the holes align. At this time, theblade covers can be slid back into place for safetyand will ride up over the Weed Deflector slightly.4Step 4 Next insert a 1.2” bolt (J) into the hole at the baseof the Support Bracket and a 1.5” bolt (I) throughthe hole with the Weed Deflector (F), then secureeach with a washer and nut. Tip the assemblyupright and tighten all fasteners securely using aPhillips screwdriver and 7/16” wrench.Step 5Handle Assembly—Press the spring-loadedbuttons on one end of the Handle Connector (E),slide into the open end of the Handle (B) and turnuntil the buttons snap into the holes in the handle.Repeat this process for the second half of thehandle.Step 1 Throw the Weed Razer out and over area to becleared. If you are on a dock, tie the rope to a postso you don’t throw too far.Step 2Let the Weed Razer sink .Step 3Pull back in using short, hard, jerking motions.Repeat as many times as needed to clear yourweeds.Assembly & Instructions (con’t)Operating Instructions 5Step 1 Always wear cut resistant gloves when handlingthe Weed Razer.Step 2 Stand the assembled Weed Razer up and grip thehandle in one hand, or rest the handle of the WeedRazer against a wall or building.Step 3Kneel or sit in front of the Weed Razer in a stableposition (Figure 1). Do not sharpen while standingor leaning over the cutting edge. Step 4Grip the handle of the Sharpener (L ) so that theguard is between your hand and the blade surface.Step 5 To remove burs from the blade surface,use the inserts on either side of the tool (1). Step 6 To sharpen BOTH SIDES of the blade at once, usethe carbide insert (3) with two pointed tips thatform a V . Run the sharpener down the cutting edgein four to six strokes using less pressure as theedge gets sharper.Notes:Blade Sharpening InstructionsFig. 113WARNING6Notes:Blade Sharpening Instructions (con’t)Step 7 To sharpen ONE SIDE of the blade only, use theinsert (2) with one pointed carbide tip and onerounded metal guide. Press the inside edge of thecarbide insert against the edge of the blade youwant to sharpen. Run the carbide over the entireedge four to six times with consistent pressure.Repeat this process for the other side of the blade.NOTE: We recommend usi ng the process i nSTEP 6 for greater consistency in sharpening.Step 8 In the end of the sharpener’s handle (4), you willfind a screw-in felt pad and oil for lubricatingthe blades. We encourage you to use the WeedRazer Sharpening Tool for all of your sharpeningneeds. When you are sharpening other tools thatmay rust or corrode, add a few drops of oil to thelubricating pad and apply to each blade after everysharpening. 7Notes:Safety Instructions1. Always wear cut resistant gloves whenhandling the Weed Razer, especially duringand after removal of the blade covers.2. The Weed Razer is to be operated by handonly. Do not pull the Weed Razer behind aboat or any other machine driven equipment.Doing so will void the warranty and damageyour Weed Razer.3. Do not use with children in immediate area.4. Do not use the Weed Razer when humansand/or animals are present within 100 feetfrom the launch point.5. Do not place or use near electrical wires orcords.6. Never touch the sharp edges of the bladeswith bare hands at any time.7. Leave blade covers on the cutting edgeswhen not in use.8. Check all bolts, connections, and rope beforeuse.9. Avoid areas with underwater structures.10. When not in use, store in a safe location out of the reach of children.NOTE: Failing to comply can result in severelacerations, dismemberment, and even death.Do not pull behind a boat Do not pull behind a vehicle or any mechanical device Do not use when humans or animals are within100 feet from the launch pointWARNINGReplacement PartsReplacement parts can be found online at ONE YEAR MANUFACTURER’S WARRANTY:1-Year Manufacturer’s Warranty – Jenlis, Inc. warrants this product to be free from defects in workmanship and materials, under normal, non-commercial use and conditions, for a period of (1) one year from the original invoice date. Warranty Limitations – Damage resulting from use in commercial environment, misuse, abuse, negligence, and/or accidents. The manufacturer agrees, at its option during the warranty period, to repair any defect in material or workmanship, or to furnish a repaired or refurbished product without charge. All warranty claims must be sent to Jenlis, at the customer’s expense. Return shipping will be pre-paid. All returns must be pre-approved. Please visit /warranty for an RMA number prior to returning product. Returns without RMA’s will be refused.8View other great products on-line at V1。
蜗蛇联合工程烈士警号产品说明书

©1997 Whelen Engineering Company Inc.Form No.13236F (050608)A u t o m o t i v e : S i r e n s /S w i t c h e sFor warranty information regarding this product, visit /warrantyDANGER! Sirens produce extremely loud emergency warning tones! Exposure to these tones without proper and adequate hearing protection, could cause ear damage and/or hearing loss! The Occupational Safety & Health Administration () provides information necessary to determine safe exposure times in Occupational Noise Exposure Section 1910.95. Until you have determined the safe exposure times for your specific application,operators and anyone else in the immediate vicinity should be required to wear an approved hearing protection device. Failure to follow this recommendation could cause hearing loss!•Proper installation of this product requires the installer to have a good understanding of automotive electronics, systems and procedures.•Whelen Engineering requires the use of waterproof butt splices and/or connectors if that connector could be exposed to moisture.•Any holes, either created or utilized by this product, should be made both air- and watertight using a sealant recommended by your vehicle manufacturer.•Failure to use specified installation parts and/or hardware will void the product warranty.•If mounting this product requires drilling holes, the installer MUST be sure that no vehicle components or other vital parts could be damaged by the drilling process. Check both sides of the mounting surface before drilling begins. Also de-burr the holes and remove any metal shards or remnants. Install grommets into all wire passage holes.•If this manual states that this product may be mounted with suction cups, magnets, tape or Velcro®, clean the mounting surface with a 50/50 mix of isopropyl alcohol and water and dry thoroughly.•Do not install this product or route any wires in the deployment area of your air bag. Equipment mounted or located in the air bag deployment area will damage or reduce the effectiveness of the air bag, or become a projectile that could cause serious personal injury or death. Refer to your vehicle owner’s manual for the air bag deployment area. The User/Installer assumes full responsibility to determine proper mounting location, based on providing ultimate safety to all passengers inside the vehicle.•For this product to operate at optimum efficiency, a good electrical connection to chassis ground must be made. The recommended procedure requires the product ground wire to be connected directly to the NEGATIVE (-) battery post (this does not include products that use cigar power cords).•If this product uses a remote device for activation or control, make sure that this device is located in an area that allows both the vehicle and the device to be operated safely in any driving condition.•It is recommended that these instructions be stored in a safe place and referred to when performing maintenance and/or reinstallation of this product.•FAILURE TO FOLLOW THESE SAFETY PRECAUTIONS AND INSTRUCTIONS COULD RESULT IN DAMAGE TO THE PRODUCT OR VEHICLE AND/OR SERIOUS INJURY TO YOU AND YOUR PASSENGERS!CAUTIONLoud siren noise can cause hearing damage and/or loss.Refer to OSHA Section 1910.95prior to putting ANY siren into service!Wear Protection!ACTIVATION OF THIS SIREN MAY DAMAGE UNPROTECTED EARS!Warnings to InstallersWhelen’s emergency vehicle warning devices must be properly mounted and wired in order to be effective and safe. Read and follow all of Whelen’s written instructions when installing or using this device. Emergency vehicles are often operated under high speed stressful conditions which must be accounted for when installing all emergency warning devices. Controls should be placed within convenient reach of the operator so that they can operate the system without taking their eyes off the roadway. Emergency warning devices can require high electrical voltages and/or currents. Properly protect and use caution around live electrical connections.Grounding or shorting of electrical connections can cause high current arcing, which can cause personal injury and/or vehicle damage, including fire. Many electronic devices used in emergency vehicles can create or be affected by electromagnetic interference. Therefore, after installation of any electronic device it is necessary to test all electronic equipment simultaneously to insure that they operate free of interference from other components within the vehicle. Never power emergency warning equipment from the same circuit or share the same grounding circuit with radio communication equipment. All devices should be mounted in accordance with the manufacturer’s instructions and securely fastened to vehicle elements of sufficient strength to withstand the forces applied to the device. Driver and/or passenger air bags (SRS) will affect the way equipment should be mounted. This device should be mounted by permanent installation and within the zones specified by the vehicle manufacturer, if any. Any device mounted in the deployment area of an air bag will damage or reduce the effectiveness of the air bag and may damage or dislodge the device. Installer must be sure that this device, its mounting hardware and electrical supply wiring does not interfere with the air bag or the SRS wiring or sensors. Mounting the unit inside the vehicle by a method other than permanent installation is not recommended as unit may become dislodged during swerving; sudden braking or collision. Failure to follow instructions can result in personal injury. Whelen assumes no liability for any loss resulting from the use of this warning device. PROPER INSTALLATION COMBINED WITH OPERATOR TRAINING IN THE PROPER USE OF EMERGENCY WARNING DEVICES IS ESSENTIAL TO INSURE THE SAFETY OF EMERGENCY PERSONNEL AND THE PUBLIC.Warnings to UsersWhelen’s emergency vehicle warning devices are intended to alert other operators and pedestrians to the presence and operation of emergency vehicles and personnel. However, the use of this or any other Whelen emergency warning device does not guarantee that you will have the right-of-way or that other drivers and pedestrians will properly heed an emergency warning signal. Never assume you have the right-of-way. It is your responsibility to proceed safely before entering an intersection, driving against traffic, responding at a high rate of speed, or walking on or around traffic lanes. Emergency vehicle warning devices should be tested on a daily basis to ensure that they operate properly. When in actual use, the operator must ensure that both visual and audible warnings are not blocked by vehicle components (i.e.: open trunks or compartment doors), people, vehicles, or other obstructions. It is the user’s responsibility to understand and obey all laws regarding emergency warning devices. The user should be familiar with all applicable laws and regulations prior to the use of any emergency vehicle warning device. Whelen’s audible warning devices are designed to project sound in a forward direction away from the vehicle occupants. However, because sustained periodic exposure to loud sounds can cause hearing loss, all audible warning devices should be installed and operated in accordance with the standards established by the National Fire Protection Association.Safety FirstThis document provides all the necessary information to allow your Whelen product to be properly and safely installed. Before beginning the installation and/or operation of your new product, the installation technician and operator must read this manual completely. Important information is contained herein that could prevent serious injury or damage.WARNING: This product can expose you to chemicals including Methylene Chloride which is known to the State of California to cause cancer, and Bisphenol A, which is known to the State of California to cause birth defects or other reproductive harm. For more information go to .Installation Guide:WPA™ Series Waterproof Amplifier51 Winthrop RoadChester, Connecticut 06412-0684Phone: (860) 526-9504Internet: Sales e-mail: autosale@Customer Service e-mail: custserv@®ENGINEERING COMPANY INC.INTRODUCTION...This manual outlines the procedures necessary for the installation of the WPA TM Series Waterproof Amplifier. This includes the 100 Watt models (WPA112, WPA124) and 58 Watt models (WPA512 and WPA524).Mounting the WPA Series Waterproof Siren Amplifier:Caution:If the amplifier is mounted vertically, it must be oriented so that the connector end of the amplifier is facing downward!1.Locate a suitable mounting location for the WPA. Do notmount this product in any location where it may be exposed to extreme temperatures.2.Be sure that the remote amplifier fits properly and does notinterfere with any vehicle components.3.Position the remote amplifier on the proposed mountinglocation. Using an awl or other suitable tool, scribe the mounting surface where the mounting holes are to be drilled.Caution:As mounting the WPA will require drilling, it is absolutely necessary to make sure that no other vehicle components could be damaged by the drilling process. If damage is likely, select a different mounting location.4.Carefully drill the mounting holes in the areas scribed instep 3. The diameter of these holes will be determined by the size of the mounting hardware and the thickness of the mounting surface.ing the supplied #10 x 3/4” sheet metal screws and #10external tooth lock washers, secure the remote amplifier to the mounting location.Wiring the WPA Series Waterproof Amplifier:Connecting To Power:1.Following the factory wiring harness, extend the RED andBLACK wires to the battery.WARNING! All customer supplied wires that connect to the positive terminal of the battery must be sized to supply at least 125% of the maximum operating current and FUSED at the battery to carry that load. DO NOT USE CIRCUIT BREAKERS WITH THIS PRODUCT!2.Connect the RED wire to one end of a user supplied fuseblock. Do not connect this unit to the battery yet!3.Connect the BLACK wire directly to the vehicle’s chassisground (typically adjacent to the battery).Connecting To Your Speaker:1.Route the ORANGE and BROWN wires towards yourspeaker.2.Connect the ORANGE wire to the POSITIVE (+) terminalon the speaker.3.Connect the BROWN wire to the NEGATIVE (-) terminal onthe speaker.Note:The two (2) BLUE wires are used to connect your two-way radio’s external speaker to theWPA for radio rebroadcast. This is anoptional connection and does not effect theother operations of the WPA.Wiring The WPA Siren Amplifier Radio Rebroadcast Wires (BLUE):1.Locate the two wires that connect the external speaker tothe vehicle’s two-way radio.2.Cut one of these wires and splice one of the BLUE wiresinto this circuit.3.Cut the remaining speaker wire and splice the remainingBLUE wire into this circuit.Note:Radio rebroadcast will NOT work with amplified remote speakers! If your remotespeaker is amplified (i.e.: contains a poweramp circuit in the speaker assembly), do notenable the radio rebroadcast feature.Connecting To Your Horn Relay (Optional): Note:This option can only be enabled when using customer supplied switches.1.Locate your vehicle’s horn relay. Now locate the wire thatconnects the vehicle horn to the horn relay output and cut this wire.2.Extend each end of the cut wire (using a minimum 16gauge wire) to a user supplied SPDT (single pole/double throw) horn transfer switch.3.Connect the wire coming from the horn relay output to theswitch “wiper” as shown in Figure 1.4.Connect the wire coming from the horn to one side of theswitch as shown in Figure 1.5.Connect the WHITE/GREEN wire to the other side of theswitch as shown in Figure 1.The installation of your WPA Series siren amplifier will be complete after the fuse block wire is connected to the POSITIVE (+) terminal of the battery. After this connection has been made,inspect the fuses at the amplifier and at the battery. If either of these fuses are blown,carefully inspect all of the circuit wires and make sure they are wired correctly. Replace the blown fuses with one of an identical amp rating as the original. If these fuses blow after installation or activation, contact Whelen Engineering Technical Support.Hands-Free Siren Activation...The WPA™ Series Waterproof Amplifier, when installed according to the wiring diagram above, offers the ability to activate siren tones using the vehicle’s steering wheel horn ring.After the horn transfer switch has been set to siren operation,the hands-free mode is enabled when the customer installed control switch, connected via the WHT/ORG wire, is closed.When the hands-free mode is enabled, pressing the horn ring button will start the Wail siren tone. A second press of the horn ring button will change the siren tone from Wail to Yelp. A third press will change the siren tone from Yelp to Piercer™. The siren tones will continue to cycle from Wail to Yelp to Piercer with each subsequent press of the horn ring button. Two, rapid presses on the horn ring button ends hands-free siren tone generation until the horn ring button is pressed again. At that time the cycle is repeated.To exit the hands-free mode, end current siren tone, turn off the customer installed switch for the hands-free mode and return the horn transfer switch to its normal operating position. Normal vehicle horn operation is then restored.Manual Siren Activation (Manual Mode)...The WPA Siren Amplifier, when installed according to the wiring diagram (Figure 1), offers manual siren activation using the vehicle’s steering wheel horn ring as a momentary switch. After the horn transfer switch has been set to siren operation, the horn ring button will now activate the manual siren tone. The manual siren tone “ramps up” to a predetermined level and continues at that level until the manual switch is released. When the switch is released, the tone is immediately terminated.WPA TM SIREN SPECIFICATIONS SPEC:WPA112TMWPA124TMWPA512TMWPA524TMINPUT VOLTAGE13.5 VDC ± 20%26.5 VDC ± 20%13.5 VDC ± 20%26.5 VDC ± 20%INPUT CURRENT (OFF)0 mA0 mA0 mA0 mAINPUT CURRENT (STANDBY)10 mA (TYP .) 5 mA (TYP .)10 mA (TYP .) 5 mA (TYP .)INPUT CURRENT (SIREN)8 Amps (TYP .) 4 Amps (TYP .) 5 Amps (TYP .) 3 Amps (TYP .)OUTPUT VOLTAGE 34 V RMS (MAX.)34 V RMS (MAX.)25 V RMS (MAX.)25 V RMS (MAX.)SPEAKER(1) 11 ohm(1) 11 ohm(1) 11 ohm(1) 11 ohmOUTPUT POWER @ 15 VDC 105 WATTS (MAX.)105 WATTS (MAX.)58 WATTS (MAX.)58 WATTS (MAX.)CONROL VOLTAGE INPUT VOLTAGE INPUT VOLTAGE INPUT VOLTAGE INPUT VOLTAGE CONTROL CURRENT 125 mA (TYP .)125 mA (TYP .)125 mA (TYP .)125 mA (TYP .)HORN RING VOLTAGE INPUT VOLTAGE INPUT VOLTAGE INPUT VOLTAGE INPUT VOLTAGE OR GROUND OR GROUND OR GROUND OR GROUND HORN RING CURRENT 15 mA (TYP .)15 mA (TYP .)15 mA (TYP .)15 mA (TYP .)OPERATING TEMP .-30° C TO +60° C -30° C TO +60° C-30° C TO +60° C-30° C TO +60° COPERATING HUMIDITY95% NON-CONDENSING 95% NON-CONDENSING95% NON-CONDENSING95% NON-CONDENSINGTo Adjust the Radio Repeat Levels...Before using the WPA Series Waterproof Amplifier, the Radio Repeat output volume must be adjusted to satisfactory operating levels. To adjust this level, a small, flat-blade screwdriver is needed.Radio Repeat VolumeLocate the Radio Repeat adjustment port (potentiometer) to the left of the 12-position input port on the remote amplifier. The potentiometer is hidden behind a 10-32 Phillips head machine screw. Once this screw is removed, set the volume level of the vehicle’s two-way radio to its normal operating volume. Place the amplifier in Radio Repeat mode. Insert the screwdriver in the Radio Repeat adjustment port and turn in a clockwise direction to increase the sound to its maximum desired volume.Return the Phillips head screw to its original position (see Fig. 2below).。
Eaton Foreseer 7 设备配置工具指南说明书

Foreseer 7 Device ConfigurationUtility GuideForeseer 7.0 Device Configuration Utility GuidePublication date 1/2018Copyright © 2018 by Eaton Corporation. All rights reserved. Specifications contained herein are subject to change without notice.Power Xpert and Foreseer are registered trademarks of Eaton Corporation.EATON CORPORATION - CONFIDENTIAL AND PROPRIETARY NOTICE TO PERSONS RECEIVING THIS DOCUMENT AND/OR TECHNICAL INFORMATION THIS DOCUMENT, INCLUDING THE DRAWING AND INFORMATION CONTAINED THEREON, IS CONFIDENTIAL AND IS THE EXCLUSIVE PROPERTY OF EATON CORPORATION, AND IS MERELY ON LOAN AND SUBJECT TO RECALL BY EATON AT ANY TIME. BY TAKING POSSESSION OF THIS DOCUMENT, THE RE- CIPIENT ACKNOWLEDGES AND AGREES THAT THIS DOCUMENT CANNOT BE USED IN ANY MANNER ADVERSE TO THE INTERESTS OF EATON, AND THAT NO PORTION OF THIS DOCUMENT MAY BE COPIED OR OTHERWISE REPRO- DUCED WITHOUT THE PRIOR WRITTEN CONSENT OF EATON. IN THE CASE OF CONFLICTING CONTRACTUAL PROVI- SIONS, THIS NOTICE SHALL GOVERN THE STATUS OF THIS DOCUMENT.DISCLAIMER OF WARRANTIES AND LIMITATION OF LIABILITYThe information, recommendations, descriptions and safety notations in this document are based on Eaton Corporation’s (“Eaton”) experience and judgment and may not cover all contingencies. If further information is required, an Eaton sales office should be consulted. Sale of the product shown in this literature is subject to the terms and conditions outlinedin appropriate Eaton selling policies or other contractual agreement between Eaton and the purchaser. THERE ARE NO UNDERSTANDINGS, AGREEMENTS, WARRANTIES, EXPRESSED OR IMPLIED, INCLUDING WARRANTIES OF FITNESS FOR A PARTICULAR PURPOSE OR MERCHANTABILITY, OTHER THAN THOSE SPECIFICALLY SET OUT IN ANY EXIST- ING CONTRACT BETWEEN THE PARTIES. ANY SUCH CONTRACT STATES THE ENTIRE OBLIGATION OF EATON. THE CONTENTS OF THIS DOCUMENT SHALL NOT BECOME PART OF OR MODIFY ANY CONTRACT BETWEEN THE PAR- TIES.In no event will Eaton be responsible to the purchaser or user in contract, in tort (including negligence), strict liability or otherwise for any special, indirect, incidental or consequential damage or loss whatsoever, including but not limited to damage or loss of use of equipment, plant or power system, cost of capital, loss of power, additional expenses in the use of existing power facilities, or claims against the purchaser or user by its customers resulting from the use of the information, recommendations and descriptions contained herein.ContentsIntroduction (4)Interactive Device Installation (4)To install a new Device on the Foreseer Local Server: (4)Configuring a Serial Connection (5)To configure a Direct Serial Connection at the Foreseer Server: (5)To edit a device: (5)Configuring the Message Manager (6)Setup (6)SNMP Resend Parameters (9)Required Connections (10)Trusted Message Manager Connections (10)Menu Reference (11)Administration Menu (11)Configuration Menu (11)IntroductionYou can use the Device Config utility to:• Add or modify devices from the Foreseer configuration in a running ForeseerServer. You can add “driver allowed” channels as well.• Modify an existing device or to add a channel to a device, you must first load itsdriver. In this context, loading a device's driver disables that device in the Foreseerservice. When you unload the driver in the Device Config utility that driver is re-enabled in the Foreseer service. You can only load a single driver in the DeviceCon- fig utility at a time.• Add channel message settings for Message Management.Interactive Device InstallationTo install a new Device on the Foreseer Local Server:1. Select the Start Server Configuration command in the Configuration menu.The ********SERVER CONFIGURATION MODE******** message appears in thewindow’s title bar.NoteIf an administrative password is required to configure the server, adialog box will appear in which you must provide that password.2. Right-click the local server, then select the Install Device command to accessthe initial Device Installation dialog box.3. Locate the previously completed Configuration Checklist for the new equipment,then click Next.4. Choose the Select the device from a list option and click Next. The Devicemust be correctly wired and running in a normal operational mode in order tosuccessfully connect to it.5. Select the device from the list, then click Next.6. Accept the suggested name for the Device or enter another unique description,observing the character limitations, and then click Next to continue.7. Specify whether the interface between the Server and the Device is a N etworkor direct Serial connection and then select the appropriate type for that option.NoteTCP/IP Protocol must be installed on the Server PC regardless of thetype of Device connection. When utilizing a ConnectUPS NetworkAdapter (Powerware UPS products only), specify a UDP/IP connection.TCP VIM II is only used to install legacy Liebert equipment.8. In the settings dialog box that appears, enter the requested additionalinformation and then click Next. Continue to enter communications informationand click Next until requested. When the display returns to the DeviceInstallation dialog box, click OK followed by Next to continue.9. In the Identification dialog box, verify that the information displayed about the De-vice corresponds to the information recorded on the Configuration Checklist. Ifnot, Cancel the installation and recheck the Device. If the displayed Deviceinformation is correct, click Next.10. With the target Device and the interface connection defined, click Finish tocomplete the installation. The new equipment will appear in the Tree View.ImportantIf the installation is unsuccessful, or the Device information does notappear in the Identification window, click Back and check that allconfiguration entries are proper and that hardware connections with theequipment are correct. After verifying the configuration and connections,once again attempt to install the Device. Contact Eaton Corporation'sForeseer Technical Support if Device installation problems persist.11. Install any additional Devices using the same p rocedure.12. With all Devices properly installed click No in response to the Install AnotherDevice? prompt to terminate the installation process.13. Select End Server Configuration in the Configuration menu to restore normalForeseer Server operation.Configuring a Serial ConnectionThe Device's Port Settings must be specified if a Direct Serial or VIM II connection isused. Either choice requires that you specify the Serial Communications Port and itssettings.To configure a Direct Serial Connection at the Foreseer Server:1. Accept the displayed Port or select one of the Ports currently available from thelist.2. If you wish to change the port settings, click the Change Settings button to dis-play the named port's Properties dialog box containing additional serial interfaceparameters.3. Click OK to enable the displayed Port Settings and return to the DeviceInstallation Wizard.The process for entering the necessary configuration settings for a VIM II DirectSerial Connection is similar. After specifying the communications Port and DeviceSet- tings for the VIM II, you are prompted to specify the VIM II Address and Port.Click OK to enable the displayed parameters and return to the Device InstallationWizard.You can modify any existing device using the Device Config utility. The following gen-eral procedure can be used for modifying device or channel properties or adding achannel.To edit a device:1. Right-click the device in the Tree and then choose Load Driver. The device andits channel icons will turn purple.2. • To modify the device properties, right-click the device and choose Properties.• To modify a channel's properties, right-click the channel and choose Proper-ties.• To add a Channel, right-click the device and choose Add Channel.3. When you've finished, right-click the device and choose Unload Driver. You cannow load the driver for another device that you wish to configure.4. When you're finished configuring devices, select End Server Configurationfrom the Configuration menu.Configuring the Message ManagerThere are four configuration tasks for the message manager within the ForeseerServer:Setup Defines which devices or individual channels sendalerts through Message Management as well asthe configuration for various alarms and actions.You can also define the SNMP behavior.Configure Required Connections: Identifies which Foreseer systems are required to be connected to this Server in instances where the Client normally performs Message Management functions. If any one of the listed systems becomes disconnected from the Server, Foreseer Message Management begins its messaging routine to alert personnel of alarms.Setup SNMP Properties Sets global SNMP resend properties.Trusted Connections Defines a set of trusted machines that are permit-ted to connect to the Message Manager.Use this to configure Message Manager settings for the server, devices, or individual channels.1. Select the Setup command from the Administration > Message Managementsubmenu.2. Right-click any server, device, or channel in the list, and then click Edit. You canalso multi-select.3. For individual channels, you can set whether or not to use the default NotificationList (this checkbox is under the Default tab). For channels, devices, and servers you can set behavior for Critical and Cautionary alarms, as well as when an alarm is acknowledged or normal status is attained. Note that you can select theseindividually or use multi-select. You can specify:• The notification list to use.• Whether to send a message if required connections are missing.• Parameters for Alpha Messages. You can either choose to use the standard message and configure it with the checkboxes or select Use Custom Message (under Alpha Message). If you are using the standard message, you canselect to include the Server Name, Device Name, Channel Name, as well asa user defined message.If you choose Use Custom Message, you have access to all of the Message Manager variables. Click Edit the Custom Message to access the message editor dialog box.$SERVER_NAME$ - returns the server issuing the alarm$DEVICE_NAME$ - returns the name of the device issuing the alarm. $CHANNEL_NAME$ - returns by the name of the channel$ALARM_MSG$ - returns the alarm message.$DATE$ - returns the current date.$SERIAL#$ - returns the serial number of the device that issued the alarm. $ACKED_BY$ - returns the user name that acknowledged the alarm. $CHANNEL_VALUE$ - returns the current value of the channel.$CHANNEL_UNITS$ - returns the units used by the channel.$ALARM_VALUE$ - returns the channel value at the time of the alarm. $ALARM_STATE$ - returns the current state of the alarm.$ALARM_PRIORITY$ - returns the alarm priority.$ACK_NOTE$ - returns the text, if any, that was entered as a note when the alarm was acknowledged.• The command line to use for the Command Line service. This allows youto change the command line issued for each alarm state or status.Once these are configured, you can copy the settings to the other alarm orstatus tabs using the buttons at the bottom of the dialog box.Figure 1. Channel Message Settings Dialog Box4. If you are also configuring SNMP traps, click the SNMP tab:a. For both Critical Alarm and Cautionary Alarm, select one of the 25 prede-fined traps or leave the setting at Do not send a Trap.b. Set the Alarm Events parameters. You can choose to also send a trap onalarm acknowledgement or return to normal.5. Click OK.Figure 2. SNMP SettingsSNMP Resend ParametersThrough this dialog box you can globally set the trap resend behavior. These settingsapply to all channels, devices, and server for which SNMP traps are configured. Toaccess it, select the SNMP Properties command from the Administration >Message Management submenu.Required Connections1. Select the Configure Required Connection command from the Administration> Message Management submenu to display the Required Connection Set-tings dialog box.Figure 4. Required Connection Strings2. Click on the Add button to access the Enter Client IP Address dialog box.3. Furnish either the Foreseer Message Management host network address orcomputer name and click OK.4. Check the box preceding the address to enable server access by t hat client.5. Specify the Startup Delay during which the server will ignore any clients thatbe- come disconnected. This delay is in effect whenever the server is initialized,or when modifications have been made to the system.6. Repeat the process to add other Foreseer clients to the list.7. Click OK to accept the displayed settings.Trusted Message Manager ConnectionsWhen setting up the Message Manager on client machines, you must define themas having trusted IP addresses or machine names. To access the dialog box, selectthe Trusted Connections command from the Administration > MessageManagement submenu. Click the Add button to add machines to the list. Select anentry and click Remove to delete it. Use the Edit button to change an entry.11Figure 5. Trusted Message Manager ConnectionsMenu ReferenceAdministration MenuLogin/LogoffIf a password is set for administering the Foreseer serv er, you'll need to enter it configure that server. Login pro- vides a way to authenticate to the server with the pass- word while logoff removed those credentials from your De- vice Config utility session.Message ManagementYou can use this submenu to configure Message Man agement . Message Management establishes an automatic escalation procedure in response to user-specified alarms. When an alarm is detected, Foreseer calls each person in the appropriate Notification List in the order shown until the alert is acknowledged. The Status portion of the Message Management window reports the notification is being performed and its ongoing progress. If every- one on the List is called without receiving an acknowledgement, Foreseer can repeat the entire procedure until the alarm is acknowledged, thereby ensuring a response.Unload/Load DriverBy default, all devices are shown in the Device Config utili ty tree with white icons. Loading the driver for anindividual device disables that device in a running Foreseer service so that it can be modified. When you are finished configuring the device, unloading the driver re-enables it (with the changes to its configuration) in the Foreseer service. You must unload the driver to configure a device and you can only unload one driver at a time. That is, you cannot simultaneously configure more than one device.Configuration MenuStart/End Server ConfigurationCertain configuration functions are only available when in Server Configuration mode. Configuring backups is only available when not in Server Configuration mode. Functions that are only available in Server Configuration mode are:• Install Device (Device right-click menu and Configuration menu)• Add Channel (Device right-click menu and Configurationmenu).。
CL17 余氯分析仪
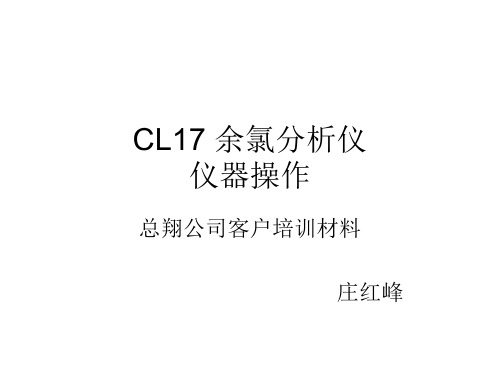
步骤如下:
a. 按ENTER,随后按上箭头键激活持续60分钟。报警LED(发 光管)将一直闪烁。
b. 为解除该标识,并返回正常运行,按MENU键,随后按下箭 头键,直至HOLD OUTPUTS(保持输出)显示出来。 c. 按ENTER。 d. 用下箭头键选择Off(关闭),并再按ENTER。
五:不定期维护
• 1:更换保险
• 仪器使用的2.5A、250V保险可用于115V和230V两种电压操作。
替换过程如下: 1. 确保仪器未供电。仪器电源开关是不能切断保险丝前的电源的。 电源必须在连接仪器之前被断开,以保证保险丝前没有电源。 2. 卸下用户检修盖。 3. 放置好保险固定器(接近用户接线箱的接线条)。 4. 卸下两个保险(F1和F2),并用同样规格的两个新保险进行替换 (2.5A、250V)。 5. 重新安装用户检修盖,并重新供电。 保险具体位置如下图所示:
2:清洗仪器外壳
关上并扣好仪器外箱盖,使用软布和温和的 清洗剂擦洗壳体外表。 勿让湿气进入壳体内。
3 清洗色度计
电源 • 2: 替换泵管道 • 在一段时间内,泵/阀模块的夹压作用将使管道变软,使管道导致破 • 裂和阻塞液流。在温度较高时,这种破裂会加速进行。基于四周环 • 境温度,推荐采用下列替换时间表: • • 低于27℃(80℉)时,间隔6个月更换一次。 • • 高于27℃,间隔3个月更换一次。
3:其他内部管线每年更换一次,具体如下图所示
一:仪器按键介绍
数字 按键 说明 1 MENU(菜单) 在测量模式中,按MENU(菜单)键可进入ALARM(报警)、 RECORDER(记录)、MAINTENANCE(维护)和SETUP(设 置)菜单。 2 右箭头 移动箭头可编辑显示器的各个部分。 当右箭头图形在显示器上出现时,为激活状态。 3 上箭头 用于滚动菜单选择或编辑显示器各个部分。 当上/下箭头图形在显示器上出现时,为激活状态。 4 左箭头 移动箭头可编辑显示器的各个部分。 当左箭头图形在显示器上出现时,为激活状态。 5 下箭头 用于滚动菜单选择或编辑显示器各个部分。 当上/下箭头图形在显示器上出现时,为激活状态。 6 EXIT (退出) 拒绝一个编辑值或从菜单结构中退出。 7 ENTER(进入) 接受一个编辑值,进入下一级菜单结构,或接受 一个菜单选择。 8 报警发光管 (LED) 指示激活的报警状态。 9 显示器屏用于测量和菜单信息的显示器区。
EPSON-LS系列手册(中文版)

EPSON-LS系列手册(中文版)这个手册旨在提供对EPSON-LS系列的总体描述和目的。
它将提供针对该系列的详细信息,包括产品规格、设置指南和操作步骤等。
无论是新手还是有经验的用户,都可以通过本手册来了解如何正确使用EPSON-LS系列产品,并充分利用其功能和特点。
本手册的目标是以简洁、清晰的语言提供信息,帮助用户快速上手并解决常见问题。
通过本手册,用户将能够全面了解EPSON-LS系列产品,并正确设置和操作其功能。
我们建议用户在使用EPSON-LS系列产品之前仔细阅读本手册,以确保能够获得最佳的使用体验。
请注意,本手册中的所有内容均基于最新可确认的信息。
在引用任何内容之前,请确保其准确性和可靠性。
本手册主要介绍EPSON-LS系列的主要特点和功能。
高精度定位:EPSON-LS系列手册采用先进的定位技术,可以实现高精度的定位和控制,确保产品的准确性和稳定性。
多功能操作:EPSON-LS系列手册提供多种操作模式,包括自动模式、手动模式和远程控制模式,能够适应不同的使用需求。
强大的数据处理能力:EPSON-LS系列手册配备了先进的数据处理功能,可以实时处理大量的数据,提供精确的结果和分析。
灵活的配置选项:EPSON-LS系列手册支持多种配置选项,可以根据用户的需求进行灵活的配置和定制。
易于使用和维护:EPSON-LS系列手册拥有直观友好的用户界面和简单易懂的操作流程,方便用户使用和维护。
以上是EPSON-LS系列手册的主要特点和功能,希望能够帮助用户更好地了解和使用该产品。
本手册将为您提供EPSON-LS系列设备的详细使用指南,包括操作步骤和注意事项。
请按照以下指南使用设备:准备工作:确保设备的电源已连接并正常工作。
将设备与计算机或其他外部设备正确连接。
操作步骤:打开EPSON-LS系列手册中提供的软件或应用程序。
在菜单中选择所需的功能或操作。
根据提示或手册中的说明执行相应的操作步骤。
注意事项:请务必仔细阅读并理解手册中的操作说明,遵循正确的操作步骤。
斯蒂尔弄泊里171偶尔使用链锯说明书

STIHL Introduces New Generation of OccasionalUse Chain SawsNew Technology Creates a 70% Reduction in EmissionsRelease Date: 5/27/2009Press Inquiries:Anita Gambill(757) 4869151 officeAll other inquiries:STIHL Incorporated(757) 4869100VIRGINIA BEACH, Va. Boasting a 70% reduction in emissions and a 1020% decrease in fuel consumption, this new generation of STIHL chain saws reduces both the impact to the environment and your wallet while delivering powerful cutting speed. Packed with new features, benefits and technologies all designed with the homeowner in mind, the STIHL MS 171, MS 181, and MS 211 offer a 30% reduction in vibration levels to help diminish operator fatigue.Perfect for lightduty homeowner tasks such as cutting firewood and trimming, these reliable chain saws feature a preseparation air filtration system, IntelliCarb compensating carburetor, and a toolless tank filler cap for easy maintenance. The MS 211 CBE version comes with the Quick Chain Adjuster (QCA) feature for toolless chain adjustment and the STIHL Easy2Start technology.The Easy2Start system eliminates the need for a strong fast pull of the starting cord. Using dual spring technology, it eliminates the resistance and jerks felt as compression is created in the engine's cylinder. This advanced starting system is designed to make starting STIHL products fast and easy for just about anyone.For professional arborist Mark Chisholm with Aspen Tree Expert Company in Jackson, NJ, selecting the right saw for the job is key, "With the new lowemission STIHL chain saws, homeowners have a variety of fuelefficient options to fit their needs."With low vibrations, good cutting speed and plenty of power, the durable STIHL MS 171, MS 181, and MS 211 chain saws are just what you need to get the job done.Watch a video about our new line of STIHL Chain SawsAbout STIHL Inc.STIHL Inc. manufactures the worlds largest selling brand of chain saws and produces a full line of powerful, lightweight, and versatile handheld outdoor power equipment for homeowners and professional users. STIHL products are sold through servicing power equipment retailers from coast to coast not mass merchants. STIHL products sold through U.S. STIHL dealers are for distribution in the United States only. For more information or for the name of the closest STIHL retailer call toll free 1800GO STIHL (18004678445) or visit the dealer locator on the STIHL Web site at .STIHL is pleased to support the Tree Research and Education Endowment Fund (TREE Fund), International Society of Arboriculture (ISA), the Tree Care Industry Association (TCIA), National FFA, Professional Landcare Network (PLANET), the American Tree Farm System (ATFS), and the National Association of State Park Directors (NASPD).For information on job opportunities with STIHL Inc., please go to /. STIHL is an EEO and drugfree work environment.MS 171 Specifications Occasional UseDISPLACEMENT30.1 cc (1.8 cu. in.)ENGINE POWER 1.3 kW (1.7 bhp)POWERHEAD WEIGHT 4.3 kg (9.5 lbs.)GUIDE BAR LENGTHS* (Recommended ranges)30 to 40 cm (12" to 16")FUEL CAPACITY280 cc (9.5 oz.)CHAIN OIL CAPACITY180 cc (6.1 oz.)OILOMATIC® CHAIN3/8" PMM3STIHL recommends #3610 (61 PMM3 55) OILOMATIC® saw chain and 16" 3005 000 3913 EMATIC™ guide bar combination. The actual listed guide bar length can vary from the effective cutting length depending upon which power head it is installed.。
Salt Dogg LS7 流动喷雾系统安装说明书

Installation & Operator’s Manual LS7 Liquid Spray System for SCH Style SpreadersInstallation Instructions1. Position and weld Enclosure Bracket(#3028485) and Support (#3014077) to spreader as shown on Fig.1.2. Position 30 gal. Tank (#3014062) on support as show in Fig.23. Attach Enclosure Assembly (#LS102) to Enclosure Bracket using provided hardware as show in Fig.2.4. Secure Tank on Support using 2 locators (#3014080) and provided hardware as shown in Fig.3.5. Plumb: reservoir, ball valve, filter, pump enclose and spray nozzle according to plumbing schematic using supplied fittings, hose and hose clamps. Do not use Teflon tape on threads. Use liquid thread sealant. (see fig.4, 5, 6 & 7).Fig. 1Fig. 2Fig. 3Cab Controller Installation Instructions (Fig. 4)1. Install cab controller (#WSE1) in cab for convenient driver operation. Mounting bracket and fasteners included.2. Route 8' wire harness (#WSE24) under dash from controller (#WSE1) to truck’s fuse panel.3. Ground “black” wire from controller to truck frame or truck’s battery (not dash).4. Attach “green” wire in 8' wire harness (#WSE24) to a fused and keyed 15 Amp hot wire circuit.5. Connect main power “white” wire in 8' wire har-ness (#WSE24) to fuse box that is “hot” full time or to battery “positive”.6. Route the 25' wire harness (#WSE25) from the rear of the spreader to the cab. Plug connector on controller (#WSE1) to the connector on pump harness (#WSE25).Fig. 4 WSE1 Cab Controller front viewFig. 4 WSE1 Cab Controllerback viewWSE2525' Cable ConnectorWSE248' Cable Connector25' Harness#WSE258' Harness#WSE24Fig. 5 Plumbing Dia.Fig. 7 Filter/Valve Assemblyto WSE39WSE696WSE9WSE30WSE11WSE2WSE10WSE2WSE9WSE9WSE696WSE33WSE133000269WSE7WSE15WSE14Fig. 6 Nozzle AssemblyWSE43WSE9Liquid Spray System Routine Maintenance RESERVOIR:-Inspect fittings for leaks from cracks or looseness-Inspect filler/breather for cracks. Depressbreather to check for adequate spring pressure or binding PLUMBING:-Inspect hoses/fittings/ball valve for leaks, cracks, looseness, chafing, binding etc.FILTER :-Remove and clean filter element every 8 to 10 hours or as needed depending on how clean de-icing liquid isPUMP-PRESSURE SWITCH & ENCLOSURE:-Inspect wiring for wear and loose or corroded connections-Inspect door and gasket to prevent corrosion NOZZLES:-Inspect operation for even spray pattern. Remove and clean as needed CAB CONTROLLER:-Inspect lights, switch, and flow control knob -Inspect wire harness and connections for wear and loose or corroded connections CLEANING:-Wash with hot water and soap after each use STORAGE:-Store inside to prevent freezing-Drain liquid de-icer from tank/s and hoses when not in use for more than two days or during extremely low temperatures-RV anti-freeze or windshield washer fluid should be run through the system for several minutes to flush de-icer from the system to preventcomponent freezing especially for end of season storageLiquid Spray System Operating Instructions 1. Read all instructions before operating. Always wear hand, eye, and skin protection when working with de-icing chemicals. Make sureeveryone is standing clear of liquid spray system before operating.2. Inspect all plumbing for leaks.3. Open ball valve (#WSE10) at the reservoir.4. Make sure reservoir has adequate supply of clean de-icing liquid. Do not operate pump without liquid.5. Before turning the cab controller on, turn the black speed control knob counter clockwise until it stops to set the pump at the slowest speed.6. To energize system, turn red power button to illuminate LCD screen “on” position.7. Increase pump speed to desired liquid spray application rate by turning black knob clockwise.8. If the red low pressure warning light/alarm comes on, the reservoir is empty or the pump is off. Do not operate pump without liquid. Note: Low pressure light and alarm will sound each time system is started. This is normal and occurs until sufficient pressure is achieved to open pressure switch (turning off light/buzzer).9. Close ball valve (#WSE10) at the reservoir when not in use.Liquid Spray System Trouble Shooting GuideMotor & Pump Operate Erratically: 1,2,3,4,5 (Possible Problem)Motor runs – Pump does not: 1,2,3,4,5,6,7 (Possible Problem)Motor & Pump fail to operate: 8,9,10,11,12 (Possible Problem)POSSIBLE PROBLEM: REPAIR:1. Little or no de-icer in tank/s Fill 2. Clogged filter Clean 3. Clogged Nozzles Clean 4. Damaged suction hose Replace 5. Ruptured pump diaphragm Replace 6. Ball valve is closed at tank/s Open valve 7. Frozen parts Thaw out 8. Bad electrical connection Inspect 9. Motor failure- burned/seized Replace 10. Cab controller on-off switch not turned on Turn on 11. Bad cab controller on-off switch Replace 12. Blown fuse in cab controller or fuse panelInspect/replaceCAUTIONAlways wear hand, eye, and skin protection when working withde-icing chemicals. Use extreme care!CAUTIONAlways wear hand, eye, and skin protection when working with de-icing chemicals. Use extreme care!Bill of Materials3014062 1 Tank Poly 30 Gal Wet System w/Cap 3014077 1 Support Reservoir 30 GalLS102 1 Enclosure Asm. Wetting System 3028485 2 Locator, Reservoir 3014084 1 Bracket, Enclosure– 2 Washer, Flat 3/8 USS SST– 2 Screw, HHC 3/5-16 x 1 304 SST – 2 Washer, Flat 1/2 USS, SST 3012164 1 Plug, Square Head, 3/4 NPT WSE15 1 Rubber Nozzle– 3 Screw, HHC 5/16-18 x 1.5 SST – 6 Washer, 5/16 SAE SST – 3 Nut, Nylock 5/16-18 SS WSE22 Nipple, Hex 3/4 x 1/2 Poly 149650501 1 Strap Asm. RatchetPART NO.QTY.DESCRIPTIONWSE10 1 Valve Ball, 1/2 NPT, PolypropyleneWSE11 1 Filter, 3/4 NPT, 6 GPM, 300 Micron, Poly WSE30 1 Barb, Hose 3/4 NPT x 1/2 HB WSE9 4 Clamp, HoseWSE696 2 Hose Poly 1/2 x 96 INWSE33 1 Barb, Hose 1/4 IN NPT x 1/2 IN Barb, Brass WSE13 1 Elbow, Brass 1/4 IN NPT x 1/4 NPTF WSE7 1 Nozzle Body, Brass WSE14 1 Nozzle CapWSE1 1 Controller, Wet Spray System WSE24 1 Harness, Wire w/Connector 8 Ft 3014117 1 Instruction Manual, LS7WSE43 1 Elbow Street, 3/4 NPT, Polypropylene 3009750 1 Decal, Liquid SystemPART NO.QTY. DESCRIPTIONRESERVOIR & COMPONENTS MAY CONTAIN HAZARDOUS MATERIAL.HANDLE WITH CARE.EQUIPMENT INSTALLERS & OPERATORS:TURN OFF ALL POWER BEFORE PERFOMING ANY SERVICE OPERATIONS.• Follow Recommended Operating Procedure.• Keep Equipment In Safe Operating Condition At All Times.• Recognize & Avoid Hazards While Operating,。
欧洲汽车零部件公司的链条产品说明书

Inner height (D) 37 mmDouble share Sideband & Frame construction with large anti-friction single-pin. Frames openable from inner radius. As standard the chain comes with frames every second link, on request with frames every link.Vertical and horizontal modular separator system is available.78SR660ANylon Cable Chain with openable framesL= + M or M1LS 2Length of chain (L)Half travel distance plus length of curve (M) or (M1)()LS 2Version with frames mounted on every pitch.S660AHFor sliding applications, technical data can slightly change according to frequency, added weight and environment.For further information please 0,51,521234567182,591531013Additionalload(kg)Suitable to long travel distancein frame every pitch version.To choose the guide channel For applications withand weights not included inthe area of the diagramshowing self-supportingcapacity, verify the possibleuse of support rollers (seepage 30).LS2The red marking in thediagram area considers thedifference of weight betweenvarious widths of chainsassembled with nylon framesevery second pitch.Self-SupportingCapacity DiagramThe maximum length of theself-supporting capacityin relationship to the weightof the cables and hosescontained per linear metre.()LS2The chain can be fixed frontally,inner or outer radius. (Fig A)See end brackets mountingvariations page 31.See end brackets mountingvariations page 31.End BracketsThe end brackets set allows the two ends of the chain to beattached to the equipment. Set complete with tiewrap clampsavailable on request.Nylon Type Bright Zinc Plated Steel。
esl 700 系列烟雾和温度探测器安装说明书

© 2014 UTC Fire & Security Americas Corporation, Inc. 1 / 6 P/N 13083-EN • REV J • ISS 10APR14ESL 700 Series Conventional Smoke and Heat Detector Installation SheetDescriptionThe ESL 700 Series smoke or smoke with rate-of-rise heat detectors have field-replaceable optical chambers. Thedetector uses an optical sensing chamber to detect smoke and a fixed-temperature heat sensor to detect heat from fire. For a list of model numbers, see Table 1. For a list of accessories, see Table 2.Table 1: Model numbers Number DescriptionHead (sold separately from base)711U Two-wire photoelectric smoke detector head 713-5U Two-wire rate-of-rise and 57°C (135°F) fixed temperature heat detector head721U Two-wire photoelectric smoke detector, with remote test input and remote alarm/trouble LED output721UT Two-wire photoelectric, with rate-of-rise heat detector head with remote test, alarm/trouble LED output 731U [1] Two-wire photoelectric smoke detector head with auxiliary relay (NC/NO) output741U Four-wire photoelectric smoke detector with alarm relay (NO) output and remote alarm/trouble LED output 741UTFour-wire photoelectric smoke and rate-of-rise heat detector head, alarm relay (NO) output and remote alarm/trouble LED output731L (OEM only, not for resale) see 731U description Base (sold separately from head)701UThree-terminal base for 711U and 713-5U heads, 6 in. (15 cm) base, connectorsNumber Description702E-10PKG Six-terminal base for all heads; 4 in. (10 cm) 702U Six-terminal base for all heads, 6 in. (15 cm) 702RE Six-terminal base for 731U, 4 in. (10 cm) 702RU Six-terminal base for 731U, 6 in. (15 cm)Head with base (sold together)TS7-4Four-wire photoelectric smoke detector with alarm relay (NO) output and remote alarm/trouble LED output[1] UL Listed for releasing devices such as electromagnetic door holders, fire dampers, or smoke dampers.High voltage (120 V) base and headThe 702RE and 702RU base s have a special plastic protrusion built in to prevent insertion of a low-voltage detector head into a base containing damaging high voltages (120 V). These bases can only be used with 731U heads. The 731U includes auxiliary relay contacts and is only required when connecting high voltage to the auxiliary relay.Note: The 731U heads can also be used with 702E and 702U bases for low voltage applications.Table 2: Accessories Number Description204-12/24V End-of-line, power supervision relay for four-wire applications211-10PKG Replaceable optical chamber for ESL smoke detectors (set of 10)706U1A [1] Remote indicator with red alarm LED, for use with 721U and 741UT706U2A [1][2] Remote indicator with red alarm LED and keyed remote test, for use with 721U and 721UT 706U3A [1][2]Remote indicator with red alarm LED, keyed remote test and reset, for use with 721U and 741UTSM-200 Smoke! In A Can (canned smoke) for functional testing of smoke detectorsSM-EXT1Extension tube for Smoke! In A Can[1] The remote alarm/trouble LED on the 706U1A, 706U2A, and706U3A models works with both two-wire 721U/721UT and four-wire 741U/741UT models when connected as shown in Figure 6 item 7 and Figure 7 item 11.[2] 706U2A and 706U3A only work with the 721U/721UT two-wire models, when connected as shown in Figure 6 item 6.InstallationNotes•Locate detectors in an operating environment as defined in “Specifications” on page 6.•Mount detectors on a firm, permanent surface.Placement and spacingUse the following location guidelines to optimize performance and reduce the chance of false alarms.Smoke detectors:•Locate wall-mounted smoke detectors so the top of the detector is no lower than 12 in. (30 cm) below the ceiling.See Figure 1.•As a guide, space smoke detectors on smooth ceilings30 ft. (9.1 m) apart. When determining other spacing,consider ceiling height, high air movement, and otherconditions or response requirements. Refer to NPFA 72.•Locate detectors away from air conditioners, heating registers, and any other ventilation source that mayinterfere with smoke entering the unit; also away fromkitchens, wood stoves, garages, furnaces, and bathrooms. Heat detectors:•Do not install heat detectors in areas with an ambient temperature above 100°F (38°C).•Mount heat detectors on the ceiling no closer than 4 in.from the sidewall. On the wall, mount them between 4 and12 in. from the ceiling.•When determining detector placement, consider ceiling height, construction, and ventilation as these affect adete ctor’s performance. Refer to NPFA 72.Installing the baseSelect a compatible electrical box for the base. See “Specifications” on page 6 for a list of compatible electrical boxes.The 6-inch diameter bases have three parts; the base itself that mounts on the electrical box or ceiling, a foam gasket, and the base cover that conceals the mounting screws (seeTable 1 for model numbers and descriptions). The 6-inch diameter bases are shipped loosely coupled to the base cover. Figure 1: Smoke detector placement(1) Smooth ceiling(2) Gray indicates theacceptable mounting area(3) Wall(4) Floor(5) 12 in. (300 mm) max. Figure 2: The six-inch diameter mounting base(1) Base cover(2) Screwdriver slot to unlockthe head(3) Gasket(4) Base(2)(3)(4)(1)2 / 6 P/N 13083-EN • REV J • ISS 10APR14P/N 13083-EN • REV J • ISS 10APR14 3 / 6To install the base:1. R emove the base cover by simply twisting it counter-clockwise to unsnap (see Figure 2).2. Pull the field wires through the electrical box, and thenthrough the center opening of the base. Connect the wires to the appropriate terminals according to the wiring diagrams (see Figure 6 or Figure 7). 3. Dress the wiring neatly, and then verify that the continuityswitch (jumper wire) is touching both terminal 1 and terminal 2 (see Figure 8). Securely fasten the base with the appropriate hardware. 4. Check all wiring and mounting connections.5. Install the gasket. Align the molded line on the base withthe base cover, and then twist clockwise to snap in place. Consider the locking mechanism before installation Each detector head is equipped with a breakaway locking tab to prevent unauthorized removal of the detector head (see Figure 3). For installations where unauthorized removal of the detector head is not a concern, the head removes by simply turning counterclockwise.However, when the head must lock to the base, break away the locking tab with a pair of pliers. Then, to remove the detector head, insert a small screwdriver into the slot on the side of the base, pressing in while simultaneously turning the detector head counterclockwise (see Figure 5).Figure 3: Removing the locking tab slot(1)To lock, break out this tab with pliersInstalling the detector headTo install a detector head, insert the head and rotate it clockwise to properly align and seat it into the base (see Figure 4). Then rotate it an additional 15 degrees to lock it in place. This action automatically opens the continuity switch in the base and establishes continuity in the system.Figure 4: Installing the detector head(1) Head(2) BaseRemoving the detector headTo remove the detector head, turn it counterclockwise. If the locking tab was removed, insert a small screwdriver into the locking tab slot on the side of the base, and then press in while simultaneously turning the detector head counterclockwise (see Figure 5).Figure 5: Removing the detector head with the locking tab removedWiringCaution: Risk of system failure. The system may not operate if the detector is not connected to the control unit initiating device circuit as specified in the detector or control unit literature. For two-wire installation, see Figure 6. For four-wire installation, see Figure 7.For optional four-wire operation, verify that the voltage range of the control panel power supply is within the detector voltage range, and that sufficient current is available to ensure the operation of all detectors.End-of-line supervision for four-wire systemsNFPA 72 requires supervision of power wiring in four-wire systems. To accomplish this, install a power supervision unit for the appropriate control unit voltage at the end of the detector power circuit. See Figure 7.The model 204-12/24V power supervision relayaccommodates both 12 VDC and 24 VDC operation. See the 204-12/24 V installation sheet for more information.(2)(1)4 / 6 P/N 13083-EN • REV J • ISS 10APR14Figure 6: 700 series two-wire wiring diagramFigure 7: 700 series four-wire wiring diagram (741UT head)(1) Initiating device circuit from a compatible listed control panel (2) DC power circuit (3) Continuity switch(4) Power supervision relay (P/N 204-12/24V) (5) End-of-line device(6)Remote test switch P/N 706U2A (for 721U and 721UT detectors only in this two-wire application)(7) Remote LED P/Ns 706U1A, 706U2A ,or 706U3A (for 721U or 721UT detector only)(8) Base for 711 series and 713-5U detectors (9) Base for 721UT detector only (10) Base for 731U series detectors(11) Remote LED P/Ns 706U1A, 706U2A, or 706U3A (for 741U or741UT detectors only) Note: Alarm contacts are shown in the normal state.Testing• Prior to testing, remove the red dust cover. The units do not work with the dust cover in place.•Follow the control panel’s recommended test procedure. To limit inconvenience to building occupants during testing it may be necessary to disable or disconnect the alarm notification appliances, HVAC shutdown, elevator control, releasing service devices, and extinguishing systems prior to detector tests. If these or other functions controlled by the fire system are disconnected during testing, be sure to perform other tests to confirm that these functions will operate during an actual event.•Be sure to enable or reconnect all devices at the conclusion of testing.Testing the wiring for continuityAfter all universal mounting bases are installed, including the end-of-line device, check the system wiring for continuity. Verify that the manually operated continuity switch in each base is in the shorting position — making contact with terminals 1 and 2 (for use at initial installation only). SeeFigure 8. Use a screwdriver to reset any unshorted continuity switches (reset by prying the jumper wire out of the plastic stopper). This establishes continuity across the alarm initiating circuit at initial installation. The wiring can now be tested for continuity using an ohmmeter or “megger.”(7)(1)(6)(3)(2)(4)(1)PWR_IN PWR_INIDC_IN IDC_IN(1) Continuity switchTesting the systemAfter completing all the connections and checking the wiring per NFPA 72, apply power to the system. There should be no alarm. If there is an alarm, check each detector to see if the alarm LED is active. Reset the control panel and see if the alarm clears. If the alarm does not clear after the panel is reset, power down the system and determine if there is a problem with the wiring. If there is no alarm, go to the last unit and use a voltmeter to check the unit power for the specified voltage.Testing the smoke detectorTest the units in place annually, using Smoke! In A Can and following the directions on the can.The unit performs a smoke test every 9 seconds while flashing its LED. If smoke is detected, the rate of sampling increases to every 4.5 seconds. The smoke detector must detect excessive smoke in three consecutive tests for the alarm to sound.If the test is successful (alarm sounds), the LED stays on. This is a gross, go/no-go test and is not a reliable indication of unit sensitivity. For in-depth sensitivity testing, see “Performing a sensitivity test on a smoke detector” below.To reset the detector, follow the control panel’s reset procedure. Resetting the control panel will remove power from the detector and allow it to reset. For a complete test of each detector, verify the control unit alarm and all ancillary functions. Performing a sensitivity test on a smoke detector1. Hold a test magnet near the raised TEST letters on thedetector for more than one second (see Figure 9).The LED flashes 1 to 9 times.2. Count the number of LED flashes, and then use Table 3 todetermine the required action. Table 3: Description of LED flashes0 to 1 Indication: Unserviceable hardware fault.Action: Reset and rerun the sensitivity test. If the errorpersists, replace the unit.2 to3 Indication: Unit is becoming insensitive.Action: Clean an d reset the unit. Rerun the sensitivity test. Ifthe error persists, replace the unit.4 to 7 Indication: Unit is within normal sensitivity range.Action: None8 to 9 Indication: Unit is becoming too sensitive.Action: Verify that the optical chamber is snapped downsecurely. If the chamber is correctly installed, clean the unitand replace the optical chamber.After the sequence of flashes, if the detector finds the sensitivity to be within limits and if all other tests pass, the detector goes into alarm until reset by the panel. If the sensitivity is not within limits, or an unserviceable hardware fault is detected, the alarm LED continues to flash once per second until the detector is reset by the panel. If the sensitivity test indicates an unacceptable level, take the action recommended in Table 3. If this action does not result in acceptable sensitivity, replace the unit.Figure 9: Smoke detector sensitivity level test(1) Test magnetRemote LEDModels 721U/721UT and 741U/741UT have connections for an optional remote LED. The remote LED flashes every 9 seconds for a normal state, flashes once every second for a trouble state, and turns on steady in alarm. It does not indicate during loss of power.Testing the heat detectorThe 713-5U heat detector samples for heat continuously. The photoelectric smoke/heat detectors sample for heat every three seconds.To test the heat detector:1. Aim a hot air gun at the detector from 6 to 10 in. (15 to25 cm) away, taking care not to melt the plastic.The detector should go into alarm in less than 30 seconds.P/N 13083-EN • REV J • ISS 10APR14 5 / 6MaintenanceIf a smoke detector drifts beyond its approved sensitivity range for more than 24 hours, or fails internal diagnostic tests during power-up, the unit automatically indicates trouble by flashing its LED every second. Under normal conditions, the LED flashes every nine seconds. Therefore, a visual check of the LED status meets NFPA 72 field sensitivity testing requirements.In accordance with NFPA 72, visually check the LED flashes for unit sensitivity within one year of installation and every alternate year thereafter for commercial installations, or every three years for residential sites.Cleaning the smoke detectorThe smoke detectors have an optical chamber that unsnaps for easy field cleaning and service. Whenever the LED indicates that cleaning is necessary, follow the steps given below.To clean the smoke detector:1. Remove the detector cap (see Figure 10), and thenunsnap and throw away the optical chamber.2. Use compressed air to thoroughly clean the optical base,and then snap a new optical chamber into place.Note: Be sure the new optical chamber is seated all theway down.3. Replace the detector cap and verify sensitivity. See“Performing a sensitivity test on a smoke detector” onpage 5.Figure 10: Optical chamber(1) Detector cap (2) Field-replaceable optical chamber SpecificationsVoltage8.5 to 33 VDC, not polarity sensitive Maximum ripple 10% (Vp-p)Typical average standby current (24 V)711U, 713-5U: 70 μA721U, 721UT, 731L, 731U, 741U, 741UT:100 µATypical alarm current Two-wire: 60 mA (max.), if not limited bycontrol panelFour-wire: 50 mA (max.) but 15 mA (min.)Remote LED outputcurrent5.0 to 8.5 mARelay contacts 2 A at 30 VDC, 1 A at 120 VACRFI immunity20 V/m minimum, 0 to 1,000 MHzHeat detectorspecifications [1]Fixed temperature: 135° ±3°F (57° ±1.7°C)Rate of rise: 15°F/min and > 105°F(8.3°C/min and > 40.6°C)Heat detector spacing 721UT, 741UT: 50 ft.713-5U: 70 ft.Sensitivity 1.55 to 3.22%/ft. obscurationDrift compensationadjustment1.0%/ft. max. for photoelectric modelsRemote test input 100 Ω max.Reset voltage 2.5 V max.Reset time 1 second min.Color White head and baseDetector headdimensions4 in. (10 cm) diam., 1.75 in. (4.44 cm) heightBase dimensions 701U, 702U, 702RU: 6 in. (15.2 cm) diam.,0.6 in. (1.3 cm) height702E, 702RE: 4 in. (10 cm) diam., 0.5 in.(1.27 cm) heightCompatible electricalboxes [2]701U, 702U, 702RU: Standard single-gangelectrical boxes; 4-inch square, round, oroctagonal boxes; 3.5-inch octagonal boxes;WIREMOLD 5738A or 5739 fixture boxes702E, 702RE: 3-inch round electrical boxesTotal height, head andbase together1.98 in. (5 cm)Field wiring size 12 to 24 AWGOperating environmentTemperatureRelative humidity32 to 100°F (0 to 38°C)0 to 95% noncondensing[1] For models 713-5U, 721UT, and 741UT.[2] Bases may also be mounted without electrical boxes if the AHJapproves it or if codes allow.Regulatory informationListings UL Listed (UL 268 and UL 521)FM Approved (except for TS7-4 and TS7-4T)CSFM (California State Fire Marshal) ApprovedUL two-wirecompatibilityidentifierS10A for all models except 731U/731LS11A for 731U/731LS00 for all basesContact informationFor contact information, see .6 / 6 P/N 13083-EN • REV J • ISS 10APR14。
LT017系列S型红外加热器安装、使用和维护说明书

Series S Infrared Heater Installation, Operation and Service InstructionsInstallerRead and thoroughly understand these instructions before attempting any installation.OwnerRetain this manual for reference.Improper installation, adjustment, alteration, service or maintenance can cause injury, death or property damage. Read the installation, operation and service instructions thoroughly before installing or servicingthis equipment.Canada: 563 Barton Street, Stoney Creek, Ontario L8E 5S1USA: 315 N Madison Street, Fortville, IN 46040If you smell gas:1.Open windows2.Don’t touch electrical switches3.Extinguish any open flame4.Immediately call your gassupplierFOR YOUR SAFETYDo not store or use gasoline orother flammable vapors and liquidsin the vicinity of this or any otherappliance.FOR YOUR SAFETYSi vous sentez une odeur de gaz:1.Ouvrez les fenetres2.Ne touchez pas aux interupteurselectriques3.Eteignez tout flamme nue4.Contactez immediatment votrefournisseur de gazCONSIGNES DE SECURITEIl est interdit d’utiliser des liquidesinflammables ou degageant desvapeurs inflammables, a proximitesde tout appareil fonctionnent augaz.CONSIGNES DE SECURITEWARNINGCAUTION: FIRE OR EXPLOSION HAZARDMaintain clearance to combustible constructions as further specified in this manual. Failure to do so could result in a serious fire hazard. Heaters should not be located in hazardous atmospheres containing flammable vapors or combustible dusts. Signs should be provided in storage areas specifying maximum safe stacking height.CAUTION: MECHANICAL HAZARDThis equipment is designed and approved for indoor use only.CAUTION: FIRE OR EXPLOSION HAZARDThis heater is equipped with an automatic ignition device. Do not attempt to light the burner by hand. Failure to comply could result in a serious fire and personal injury hazard.CAUTION: MECHANICAL HAZARDDo not use high pressure (above ½ psi) to test the gas supply system with the burners connected. Failure to do so could result in damage to the burner and its control components requiring replacement.CAUTION: SERVICE LIFE RISKDo no install equipment in atmospheres containing halogenated hydrocarbons or other corrosive chemicals. High intensity heaters are not recommended for installation in enclosed swimming pool areas. Failure to do so may lead to premature equipment failure and will in-validate the warranty.TABLE OF CONTENTSINTRODUCTION ________________________________________________________________________ 4Installation Codes _____________________________________________________________________________ 5 General Installation and Gas Codes/Electrical Codes _________________________________________________________ 5 Aircraft Hangar Installation _____________________________________________________________________________ 5 Public Garages _______________________________________________________________________________________ 5 Parking Structures ____________________________________________________________________________________ 5 LAYOUT RECOMMENDATIONS ____________________________________________________________ 6Layout Considerations __________________________________________________________________________ 6Spot Heating __________________________________________________________________________________ 6Full Building Heat ______________________________________________________________________________ 7 HEATER SPECIFICATIONS _________________________________________________________________ 8 Dimensional Chart _____________________________________________________________________________ 8 Gas Supply ___________________________________________________________________________________ 9 Electrical Requirements _________________________________________________________________________ 9 CLEARANCE TO COMBUSTABLES __________________________________________________________ 10 INSTALLATION ________________________________________________________________________ 11 Gas ________________________________________________________________________________________ 11 Electric _____________________________________________________________________________________ 12 VENTILATION / CONDENSATION __________________________________________________________ 14 Ventilation __________________________________________________________________________________ 14 Condensation ________________________________________________________________________________ 14 OPERATION / MAINTENENCE ____________________________________________________________ 15 Operation ___________________________________________________________________________________ 15 Control Operating Sequence—Direct Spark Ignition_________________________________________________________ 15 Annual Maintenance __________________________________________________________________________ 15 TROUBLESHOOTING ____________________________________________________________________ 16 PARTS _______________________________________________________________________________ 17 WARRANTY __________________________________________________________________________ 18INTRODUCTIONSuperior Radiant Products is a company in the infrared heating industry founded on the principles of product quality and customer commitment.Quality commitments are evidenced by superior design, a regard for design detail and an upgrade of materials wherever justifiable.Customer commitment is apparent through our ready responses to market demands and a never-ending training and service support program for and through our distributor network.ImportantThese instructions, the layout drawing, local codes and ordinances, and applicable standards such as apply to gas piping and electrical wiring comprise the basic information needed to complete theinstallation, and must be thoroughly understood along with general building codes before proceeding.Only personnel who have been trained and understand all applicable codes should undertake theinstallation. SRP Representatives are Factory Certified in the service and application of thisequipment and can be called on for helpful suggestions about installation.INTRODUCTIONInstallation CodesInstallations must comply with all local building codes or in their absence; the latest edition of the national regulations and procedures applicable to gas fired and suspended heaters.General Installation and Gas Codes/Electrical CodesHeaters must be installed only for use with the type of gas appearing on the rating plate, and theinstallation must conform to the National Fuel Gas Code, ANSI Z.223.1 (NFPA 54) in the US andCAN/CGA B149.1 and B149.2 Installation Codes in Canada. For electrical requirements refer to the latest editions of the National Electrical Code ANSI/NFPA 70 or Canadian Electrical Code C22.1This heater maybe approved for either indoor or outdoor installation. Not for use in residential dwellings, refer to Rating plate.Aircraft Hangar InstallationInstallation in aircraft hangars must conform to the Standard for Aircraft Hangars, ANSI/NFPA 409 in the US and CAN/CGA B149.1 and B149.2 Installation Codes in CanadaPublic GaragesInstallation in public garages must conform to the Standard for Parking Structures, NFPA 88A or the Standard for Repair Garages, NFPA 88B, in the US and CAN/CGA B149.1 and B149.2 Installation Codes in Canada.Parking StructuresTechnical requirements are outlined in ANSI/NFPA 88A (USA)LAYOUT RECOMMENDATIONSLayout Considerations1.Because high intensity heaters are un-vented, verify local codes for guidance on air supply anddilution air. Also see section on Ventilation.2.Check local codes for mounting requirements and the requirement for flexible gas connectors or rigidmounting.3.Do not locate heaters near windy locations such as door openings.4.Do not locate heaters in very dusty environments5.Avoid placing heaters below sprinkler heads or provide more than adequate clearance.Spot HeatingHigh intensity heaters are ideal for spot heating applications. The following are key considerations to the success of the application:1.Minimize any wind in order to maximize the effect of the radiant heat.2.Placing two smaller heaters opposing each other will be more comfortable than placing onelarge heater.3.Hang the heaters back and at an oblique angle (rather than directly overhead) in order tomaximize the exposure of the peoples’ bodies to radiant heat.The following charts are intended for guidance only. Specific applications may require other parameters.Suggested Minimum Mounting HeightsHeater Input Rate Mounting AngleBTU/hr10°35°ft m ft m30,000-33,000 11 – 13 3.4 – 4.0 10 - 12 3.1 – 3.6 60,000-66,000 14.5 – 16.5 4.5 – 5.0 13 – 15 4.0 – 4.5 90,000-99,000 16 – 18.5 4.9 – 5.6 14.5 – 17 4.5 – 5.2 120,000-132,000 17.5– 21 5.4 – 6.4 15.5 – 18.5 4.7 – 5.6 160,000 19 – 23 5.8 – 7.0 17 - 21 5.2 – 6.4LAYOUT RECOMMENDATIONS Suggested heat loading for indoor spot heating under stated conditions:Ambient Air TemperatureBTU/hr per sq. ft ofFloor Area to be HeatedAt 50 ft/min of wind(15.2 m/min)At 100 ft/min of wind(30.5 m/min)40°F / 4°C150—165165—18055°F / 13°C 75—88 85—100Example:Work counter for light assembly, space is 15 ft x 25 ft. (4.5 m x 7.6 m), ambient airtemperature 40°F / 4 C, located near shipping doors.Approximately 170 BTUH/sq.ft x (15x25) sq.ft = 63,750 BTUHTwo heaters at opposing locations would be preferredFull Building HeatCalculate the total heat input required, ensuring the inclusion of any unheated make-up air due to exhaust fans. Use the following chart as guidance to heater placement.Model/BTUHS330-33,000S660-66,000S990-99,000S12120-132,000S16160,000Heater Mounting Height, ft (m) MountingAngle 10°11-15(3.4 – 4.6)15-20(4.6 – 6.1)20-25(6.1 – 7.6)25-30(7.6 – 9.2)30-38(9.2 – 11.6) MountingAngle 35°10-12(3.1 – 3.6)13-16(4.0 – 4.9)16-22(4.9 – 6.7)18-26(5.5 – 7.9)24-31(7.3 – 9.4)Distance of first heater row from outside wall, ft (m)6(1.9)10(3.1)12(3.7)14(4.3)16(4.9)Distance between heaters along outside wall*, ft (m)8-20(2.5 – 6.1)15-30(4.6 – 9.2)20-40(6.1 – 12.2)30-50(9.2 – 15.2)40-60(12.2 – 18.3)Distance between rows – out-side wall row to next interior row, ft (m)30-60(9.2 – 18.3)50-80(15.2 – 24.4)75-110(22.9 – 33.5)90-115(27.5 – 35.0)100-125(30.5 – 38.1)*Distance between heaters along interior rows should be up to twice the indicated numberAHEATER SPECIFICATIONSFigure 1: Overall Dimensional InformationDimensional ChartHEATER SPECIFICATIONS Gas Supply Natural Gas PropanePressure Minimum 6.5" W.C. Minimum 11.0" W.C. Maximum 14.0" W.C. Maximum 14.0" W.C.Connection½" female NPTManifold Pressure 6.0" W.C. 10" W.C.Electrical Requirements(3 options) 120 V, 20 VA wired to junction box24V, 20 VAMillivolt pilot systemCLEARANCE TO COMBUSTIBLESThe stated clearance to combustibles represents a surface temperature of 90°F (50°C) above roomtemperature. Building materials with low heat tolerance (such as plastics, vinyl siding, canvas, tri-ply,etc…) maybe subject to degradation at lower temperatures. It is the installer’s responsibility to assure that adjacent materials are protected from degradation.WARNINGClearances as marked on the heater body must be maintained from vehicles parked beneath. Signs should be posted identifying any possible violation of the clearance distances from the heater in all vehicle areas. Clearance to combustibles must be maintained according to the following chart. In storages areas, signs must be posted to specify the maximum permissible stacking height. Adequate clearance to sprinkler heads must be maintained.Model NumberTop Sides Rear Below S3 35" (89 cm) 28" (71 cm) 20" (51cm) 70" (178 cm) S6 40" (102 cm) 35" (89 cm) 20" (51 cm) 80" (203 cm) S9 50" (127 cm) 42" (107 cm) 28" (71 cm) 100" (254 cm) S12 54" (137 cm) 46" (117 cm) 28" (71 cm) 110" (280 cm) S1660" (153 cm)48" (122 cm)34" (87 cm)134" (341 cm)Figure 2:Clearance to Combustibles DiagramBELOWSIDE SIDEINSTALLATIONGas∙Figure 3 illustrate typical rigid and chain mounting configurations for the Series S heaters; verify which is permissible by local codes.∙Heaters must be hung at an angle between 10° and 35°. Typically, at the walls they are at 35° facing into the building. The gas manifold must always be at the lower side of the heater.∙Minimum 3/16" diameter S hooks and No. 1/0 chain (200 lb./ 91 kg working load) is recommended.Close S hooks after installation.∙Never use a gas line as a hanging support and never locate gas or electric lines over the heaters.∙Maintain clearance to combustibles.∙Ensure that there is a plugged tap upstream of the heater or a fitting on the valve itself to verify incoming pipeline pressure.∙Do not leave the heater connected when pressure testing the pipeline. The high pressure will damage the equipment.TYPICAL RIGID MOUNTING CONFIGURATIONTYPICAL CHAIN MOUNTING CONFIGURATIONNOTES:- OVERHEAD STRUCTURE AND FIELD CONNECTIONS MUST BE ADEQUATE TO SUPPORT WEIGHT OF THE HEATER.- MAIN GAS LINES AND ELECTRICAL LINES MUST NOT CROSS OVER TOP OF HEATER.Figure 3: Mounting ConfigurationsHEATER230/24VHEATERHEATER* In some cases the 120/24 volt transformer can be positioned prior to the thermostat. In this case, evaluate the contact load across the thermostat contacts, as the load created by the operating heaters may be too great. In that case a relay should be used.* When using a 24 volt system, be sure that the control transformer being used has enough VA (volt amp) rating for the heater control system being used. Example:Operating five 24V model "S" heaters using one transformer,each control or heater requires 20 VA. 5 units x 20VA = 100VA transformer capacity minimum.ElectricFigure 4 illustrates typical wiring arrangements for the Series S heater. Two options are available; 230V and 24V supply. Up to six heaters may be operated from one thermostat. (Verify thermostat electrical capacity if non SRP product is used.) ∙Ensure the heaters are properly grounded.∙If mechanical exhaust is used in the building, it is typical to interconnect these in the heater circuit as shown in Figure 4.∙Perform all work in accordance with local codes or the National Electric Code ANSI/NFPA 70 or Canadian Electrical Code CSA C22.1.CONTROL DESCRIPTION24 VOLTS—DIRECT SPARK IGNITION100% SHUT OFFAPPLIES TO NATURAL GAS OR PROPANE GASFigure 4: Wiring DiagramVENTILATION / CONDENSATIONVentilationBuildings using high intensity radiant heaters require ventilation. High Intensity type heaters are considered un-vented gas fired appliances, requiring ventilation to supply combustion air and dilute/remove the products of combustion.Requirements for combustion air supply and dilution air vary by jurisdiction, building type and specific installation details. See local codes for guidance . In general, where heaters are installed without direct outside combustion air, fresh air ventilation must be provided to building space (3 cfm per 1000 BTU/Hr in Canada, 4 cfm per 1000 BTU/Hr in the USA), Verify applicable local codes in the USA as requirements change by jurisdiction. ∙Mechanical exhaust should be electrically interconnected with the heaters and should always be installed in conjunction with inlet air openings. See “Block Diagram for Interconnecting Fan/Humidistat” above for details.∙Inlet air opening should be relatively small and distributed over the operating area of the heaters.They must always be located below the level of the heaters. One square inch of net free inlet area per 1000 BTUH is recommended.Figure 5: Block DiagramCondensationThe products of combustion for natural gas contain up to 1 liter of water per 100,000 BTU consumed. This may add substantial amounts of moisture to the building air environment and may become a problem of condensation on cold surfaces within the building. This is particularly true for poorly insulated metal roof decks or structural steel framing.∙To decrease condensation, increase mechanical ventilation.∙Ensure that continuous waterproof barriers are used on the inside of all insulated surfaces.∙Ensure that exhausters pull air from the entire space and across the condensing surface.∙Humidistat controls may be integrated into the electrical control circuit of the heaters.N N When using a humidistat to control exhaust fans, wire the humidistat to cause the fan to operate on humidity rise, NOT humidity fall.Depending on fan horsepower, a relay may or may not be needed.OPERATION / MAINTENENCEOperationEnsure the gas supply line has been purged.Open all gas cocks to the heaters and electrically energize the system.Follow the instructions on the heaters Lighting Instructions Label. Check to ensure that the thermostat starts and shuts down the system.Control Operating Sequence—Direct Spark Ignition1.The thermostat calls for heat.2.The combination gas valve opens and the spark igniter sparks in an attempt to light the fuel at theface of the ceramic. The spark will continue for 15 seconds3.Once flame is established (prior to complete steady-state conditions) the flame sensor signals themodule and sparking stops. If the burner does not light in 15 seconds, the system will lockout, i.e.electric energy to the gas valve and electronic module is cut. The lighting sequence may be resetby an interruption of the electric power supply.4.Once operating, the heater will continue to do so until the thermostat is satisfied; shutting the gasvalve.Annual Maintenance1.Close the fuel gas valve and de-energize electrical power to the heater.2.With an air hose regulated to no more than 15 psig blow away accumulated dust. Blow across theface of the ceramic tiles, not directly at them. Blow into each venturi for about one minute.3.Verify that there are no cracked tiles.4.Review the wiring for any loose connections.TROUBLESHOOTING Symptom PossibleCause CorrectiveActonHeaters will not turn off Defective thermostatStuck solenoid valveRepair or replaceRepair or replaceGas Odor Loose pipe connection Verify all connections are sealed by using an appropriate leak testBurning of gas/air mixture inside venturi (flashback) Cracks between or across ceramic gridsExcessive draftsReplace burner head assemblyShield or relocate heaterHeaters Cycles on/off Excessive draftsFlame sense not groundedLow gas pressureShield or relocate heaterVerify wiring and correctVerify and correctLow surface temperature on ceramic surface Dirty or plugged ceramicsLow inlet gas pressureMisaligned manifold/orificeInsufficient gas supplySee cleaning maintenanceVerify and correctReplace manifoldVerify capacity of fuel supply linesNo spark, no ignition No power to control module Control module defective No power to spark electrode No equipment groundHeater sparks but will not light No gas supplyDefective gas valve solenoidDefective electronic controlCheck shut off valve and combinationgas valveHeater lights but ‘locks out’ after about 10 seconds Poor groundReversed polarity on electric supplySense electrode not sensing flameDefective electronic controlCheck continuity of sense electrodeVerify and/or replace}V erify and correct/replace}Verify and correct/replace}Verify and correct/replacePARTSFigure 6: Replacement PartsELECTRODE ASSEMBLY(P/N SE001)(P/N CE TRANSFORMER(P/N SE004)BURNER HEAD ASSEMBLY (P/N SG009)GAS VALVEWARRANTY SERIES S INFRARED HEATERSWARRANTYThe Manufacturer warrants to the original owner that the product will be free of defects inmaterial and workmanship. For the Series S, the warranty for all components except for theceramic burner head assembly is limited to 24 months from the date of installation. The ceramic burner head assembly shall be warranted for an additional eight years for units which are provento the satisfaction of the manufacturer to be inoperative due to defects in material or workmanship.The Manufacturer’s obligation under this warranty is limited to repair or replacement, F.O.B. its facility, of the defective part. In no event shall the manufacturer be liable for incidental expense or consequential damages of any kind.This warranty does not cover any shipping, installation or other labor costs incurred in the repairor re-placement of the product. No materials will be accepted for return without authorization.This warranty will not apply if in the judgment of the Manufacturer the equipment has been improperly in-stalled, unreasonably used, damaged, or modified.This warranty will not apply to damage to the product when used in corrosive atmospheres and in particular atmospheres containing halogenated hydrocarbons. No person is authorized to assumefor the Manufacturer any other warranty, obligation or liability.THE REMEDIES PROVIDED FOR IN THE ABOVE EXPRESS WARRANTIES ARE THESOLE AND EXCLUSIVE REMEDIES. NO OTHER EXPRESS OR IMPLIED WARRANTIESARE MADE INCLUDING, BUT NOT LIMITED TO, ANY IMPLIED WARRANTY OF MERCHANTABILITY OR FITNESS FOR A PARTICULAR USE OR PURPOSE.Address questions to your local distributorHeater Series Installed rate Serial Number Installed date :_________________________ :__________________Btu/hr :_________________________ :_________________________。
HYDRA-LITE 轻型氧氛试验仪具说明书

.005 KG/CM2 .025 KG/CM2
.005 KG/CM2 .025 KG/CM2
PISTON AREA SO. IN.
.05
.05
.05
.O 1
.O 1
.O 1 .05 .O 1
.05 .01
.05 .01
WEIGHT SET NO.
1M 2M 3M 1M 2M 3M 1M
2M
3M
MODEL 1500N 3000N 4500N 7500N 15,000N 22,500N 9000N
PRESSURE - PSI
.1
.2
1
2
2
10
.5
1
5
10
10
50
WG-234 WG-230 WG-233 WG-231 WG-232 WG-23
40 200 WG-25
100
5
500
25
WG-229 w/c Assy
Piston
. Area 1/20
11100
Part No.
PRESSURE - KGICM~
ILLUSTRATIONS
FIGURE 1 -SIDE VIEW, HYDRA-LITETESTER
TLS电子70HDBaseT传输器与接收器说明书
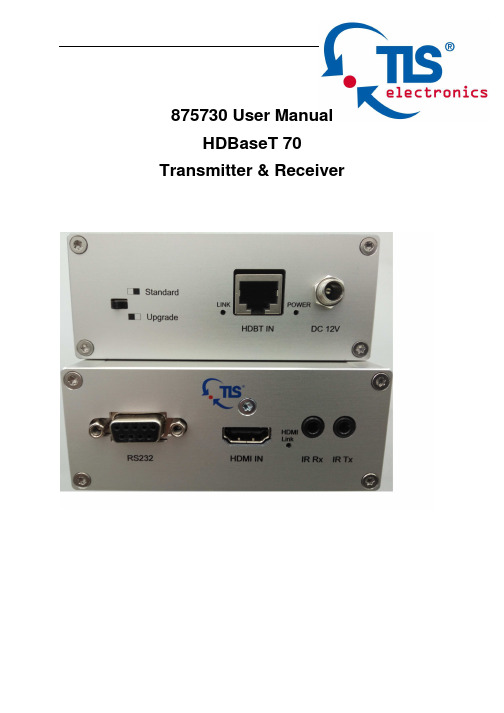
875730 User ManualHDBaseT 70 Transmitter & Receiver875730 User manualTLSelectronicsGmbHContact:************************Thank you for purchasing this product. For optimum performance and safety, please read these instructions carefully before connecting, operating or adjusting this product. Please keep this manual for future reference.SURGE PROTECTION DEVICE RECOMMENDED This product contains sensitive electrical components that may be damaged by electrical spikes, surges, electric shock, lightning strikes, etc. Use of surge protection systems is highly recommended in order to protect and extend the life of your equipment.875730 User manualTLSelectronicsGmbHContact:************************Table of Contents1. Introduction.........................................................................................4 2. Features...............................................................................................4 3. Panel Description..................................................................................5 4. Connection Diagram....................................................................9 5. Specifications.......................................................................................9 6. Package Contents................................................................................10 7. Maintenance.......................................................................................10 8. Warranty Policy.................................................................................10 9. Limitations of Warranty...............................................................................11 10. Exclusive Remedies.................................................................................12 11. RMA Policy (12)875730 User manualTLSelectronicsGmbHContact:************************IntroductionTLS HDBaseT 70 transmitter and receiver is a 70m (230ft) HDBaseT Extender. It transmits 1080P@60HZ at 48bit deep color via single Cat5e-AWG24-cable up to 70 meters (230ft). Bi-directional IR and RS232 can also be transmitted over the same cable. With support of POH (power over HDBaseT), only one power supply is needed at either transmitter or receiver.Features• HDMI v1.4 and HDCP compliant, support 1080p@60Hz, 3D, 4Kx2K@30Hz • Support 1080P@60Hz or VESA: 1920x1200@60Hz up to 70m (230ft) • Dolby TrueHD and DTS-HD master audio pass through HDMI output • Bi-Directional IR and RS232 pass through.• Power over HDBaseT supported, only one power supply needed at either transmitter or receiver side •With ESD ProtectionNote :The POH function is designed for powering compatible transmitter or receiver units of TLS only.875730 User manualTLSelectronicsGmbHContact:************************Panel Description875730 Transmitter1. RS232 connector2. HDMI link indicator3. IR TX jack4. HDMI input5.IR RX jack875730 User manualTLSelectronicsGmbHContact:************************1. Signal Link indicator2. Power status indicator3. EDID DIP switch ( UP=0, DOWN=1)[DIP]=0000: HDMI 1080p@60Hz, Audio 2CH PCM[DIP]=0001: HDMI 1080p@60Hz, Audio 5.1CH PCM/DTS/DOLBY [DIP]=0010: HDMI 1080p@60Hz, Audio 7.1CH PCM/DTS/DOLBY/HD [DIP]=0011: HDMI 1080i@60Hz, Audio 2CH PCM[DIP]=0100: HDMI 1080i@60Hz, Audio 5.1CH PCM/DTS/DOLBY [DIP]=0101: HDMI 1080i@60Hz, Audio 7.1CH PCM/DTS/DOLBY/HD [DIP]=0110: HDMI 1080p@60Hz/3D, Audio 2CH PCM[DIP]=0111: HDMI 1080p@60Hz/3D, Audio 5.1CH PCM/DTS/DOLBY [DIP]=1000: HDMI 1080p@60Hz/3D, Audio 7.1CH PCM/DTS/DOLBY/HD [DIP]=1001: HDMI 4K2K, Audio 2CH PCM[DIP]=1010: HDMI 4K2K, Audio 5.1CH PCM/DTS/DOLBY [DIP]=1011: HDMI 4K2K, Audio 7.1CH PCM/DTS/DOLBY/HD [DIP]=1100: DVI 1280x1024@60Hz, Audio None [DIP]=1101: DVI 1920x1080@60Hz, Audio None [DIP]=1110: DVI 1920x1200@60Hz, Audio None [DIP]=1111: EDID pass throughNOTE :The port will only read the DIP switch settings on power-up. The device must be powered offand then back on again for it to implement any change of the DIP switch settings.4. Upgrades DIP switch5. HDBT output6. DC 12V screw type connector875730 User manualTLSelectronicsGmbHContact:************************875730 Receiver1. Signal Link indicator2. Power status indicator3. Standard/Upgrade mode switch4. HDBT input5. DC 12V screw type connector875730 User manual TLSelectronicsGmbHContact:************************1. RS232 connector2. HDMI link indicator3. IR TX jack4. HDMI output5.IR RX jack875730 User manualTLSelectronicsGmbHContact:************************Connection DiagramSpecificationsBandwidth 2.97Gbps per Color Video input Transmitter 1XHDMI Type A, 19-pin, female Receiver 1xRJ45 Video output Transmitter 1xRJ45 Receiver 1XHDMI Type A, 19-pin, female IR input 2x3.5mm stereo jack IR output2x3.5mm stereo jack RS232 control 2x DB9Power Supply12V/2A DC, screw type connector Power Consumption 9.5WAudioPasses up to Dolby TrueHD or DTS-HD Master Audio Resolution Video: up to 4Kx2KVESA: up to 1920x1200Distance 230ft @ 1080p over CAT5e/6-AWG24 130ft @ 4Kx2K over CAT5e/6-AWG24 Dimensions 107x107x27mm Weight200gTemperature Operating 32°F to 104°F (0°C to 40°C) Storage-4°F to 140°F (20°C to 60°C) Rack-MountableRack ears includedNOTE : Specifications are subject to change without notice. Weight and dimensions are approximate .875730 User manualTLSelectronicsGmbHContact:*************************Package Contents• 1x 875730 Transmitter • 1x 875730 Receiver• 1x 12V/2A DC power supply• 1x IR Transmitter, 1x IR Receiver.MaintenanceClean this unit with a soft, dry cloth. Never use alcohol, paint thinner or benzene to clean this unit.Warranty PolicyTLS electronics products are warranted against defects in material and workmanship for two years from the date of shipment. During the warrantyperiod, TLS electronics will, at its option, repair or replace products that prove to be defective. Repairs are warranted for the remainder of the original warranty or a 90 day extended warranty, whichever is longer.For equipment under warranty, the owner is responsible for freight to TLS electronics and all related customs, taxes, tariffs, insurance, etc. TLSelectronics is responsible for the freight charges only for return of the equipment from the factory to the owner. TLS electronics will return the equipment by the same method (i.e., Air, Express, Surface) as the equipment was sent to TLS electronics.875730 User manualTLSelectronicsGmbHContact:*************************All equipment returned for warranty repair must have a valid RMA number issued prior to return and be marked clearly on the return packaging. TLS electronics strongly recommends all equipment be returned in its original packaging.TLS electronics obligations under this warranty are limited to repair orreplacement of failed parts, and the return shipment to the buyer of the repaired or replaced parts.Limitations of WarrantyThe warranty does not apply to any part of a product that has been installed, altered, repaired, or misused in any way that, in the opinion of TLS electronics, would affect the reliability or detracts from the performance of any part of the product, or is damaged as the result of use in a way or with equipment that had not been previously approved by TLS electronics.The warranty does not apply to any product or parts thereof where the serial number or the serial number of any of its parts has been altered, defaced, or removed.The warranty does not cover damage or loss incurred in transportation of the product.The warranty does not cover replacement or repair necessitated by loss or damage from any cause beyond the control of TLS electronics, such as lightning or other natural and weather related events or wartime environments. The warranty does not cover any labor involved in the removal and orreinstallation of warranted equipment or parts on site, or any labor required to diagnose the necessity for repair or replacement.The warranty excludes any responsibility by TLS electronics for incidental or consequential damages arising from the use of the equipment or products, or forany inability to use them either separate from or in combination with any other equipment or products.A fixed charge established for each product will be imposed for all equipment returned for warranty repair where TLS electronics cannot identify the cause of the reported failure.875730 User manual TLSelectronicsGmbHContact:*************************Exclusive RemediesTLS electronics ’s warranty, as stated is in lieu of all other warranties, expressed, implied, or statutory, including those of merchantability and fitness for aparticular purpose. The buyer shall pass on to any purchaser, lessee, or other user of TLS electronics ’s products, the aforementioned warranty, and shall indemnify and hold harmless TLS electronics from any claims or liability of such purchaser, lessee, or user based upon allegations that the buyer, its agents, or employees have made additional warranties or representations as to product preference or use.The remedies provided herein are the buyer ’s sole and exclusive remedies. TLS electronics shall not be liable for any direct, indirect, special, incidental, or consequential damages, whether based on contract, tort, or any other legal theory.RMA PolicyWhen returning product to TLS electronics for any reason, the customer should fill out the official RMA form to obtain a RMA number. Without the permission or approval, TLS electronics will be no responsible for any return.This can be initiated by emailing or calling your related sales.All requests are processed within 48 hours.Standard ReplacementFor customers that agree to return defective product to TLS electronics first, a Standard Replacement option is available.An RMA number must first be issued by sales. This RMA number will need to be referenced on the outside of the return shipment.Upon receipt of the defective product, TLS electronics will, at its discretion, either repair or replace the product and ship it out in the most expeditious875730 User manualTLSelectronicsGmbHContact:*************************manner possible. Subject to availability, the replacement product will be shipped on the business day following receipt of the defective product.In the event the product returned to TLS electronics has been discontinued (i.e. the product is no longer being manufactured by TLS electronics but is still under warranty), TLS electronics will, at its discretion, either repair or replace with recertified product.Once you have obtained an RMA numberAfter obtaining an RMA number from TLS electronics, you must send theproduct - freight prepaid - to TLS electronics. The TLS electronics RMA number must be prominently displayed on the outside of your package. If you send your product to TLS electronics without the RMA number prominently displayed on the outside of the package, it will be returned to you unopened.Please use a shipping company that can demonstrate proof of delivery. TLS electronics does not accept responsibility for any lost shipments unless proof of delivery to TLS electronics is provided.Please note:Product shipped to TLS electronics must be properly packaged to prevent loss or damage in transit.Shipping your RMA to TLS electronics using regular mailing envelopes is not acceptable, as they do not protect the product from damage during shipping.TLS electronics will not repair or replace a module that is shipped in such a way that the product is not properly protected.TLS electronics will not accept any product that has been damaged as a result of accident, abuse, misuse, natural or personal disaster, or any unauthorized disassemble, repair or modification .。
森林河公司的旅行车型号说明书

2715281530163212221724143310S T A N D A R D M O D E L SH M O D E L S 15’16’12’ 6”10’REFER WARDMICROOHCELECTRIC BEDS & MAX CLEARANCE DINETTESRAMP DOOR W/CABLE KIT17’70”REFERMICROSHELFWARDOHCOHCELECTRIC BEDS & MAX CLEARANCE DINETTESRAMP DOOR W/CABLE KIT14’70”CLEARANCE DINETTESDOOR QUEEN BEDCLEARANCE DOOR QUEEN BEDQUEEN BEDCLEARANCE DOOR 15’70”CLEARANCE DOOR QUEEN BEDCLEARANCE DOOR QUEEN BEDOHCMICRO2421 Century Drive / Goshen, IN 46528Phone: 574-642-0438E-mail:**************************SPECS 2217241427152815301632123310Hitch Weight 955 lb 1,050 lb 940 lb 1,230 lb TBD 1,485 lb TBD UVW 5,993 lb 6,398 lb 6,963 lb 7,718 lb TBD 8,593 lb TBD CCC3,762 lb 3,452 lb 2,777 lb 3,712 lb TBD 3,092 lb TBD Exterior Length 26' 3"28'31' 2"32' 2"TBD 36' 1"TBD Exterior Height TBD TBD TBD TBD TBD TBD TBD Exterior Width 96"96"96"102"102"102"102"Fresh Water 50 gal 50 gal 50 gal 102 gal 102 gal 102 gal 102 gal Gray Water 64 gal 64 gal 64 gal 64 gal 64 gal 64 gal 64 gal Black Water 32 gal 32 gal 32 gal 32 gal 32 gal 32 gal32 galAwning Size14'18'18'20'20'20'20'STANDARD MODELS HD MODELSEXTERIOR PACKAGEFriction Hinge Entry Door(s) w/ Window, Dual 20# LP Tanks w/ Cover, 30AMP Service w/ Transfer Switch, Black Tank Flush, UV Resistant Gel-Coated Fiberglass Exterior, Radius Fully-Walk-able Roof, Singular Roof Membrane w/ 12 Year Warranty, Insulated Storage Compartment Doors, Vacuum-Bonded Aluminum-Framed Sidewalls, Laminated & Insulated Slide Room Walls, Fully Enclosed “Body-Armor” Underbelly w/ Radiant Foil Layer, Electric Awning w/ LED Lights, Full-LED Rear Taillights, Alumi-Tread Main Entry StepsCHASSIS & SUSPENSIONPACKAGEMORRyde CRE3000 Suspension Enhancement, Aluminum Wheels, Dexter EZLube® Axles, Full-Sized Spare Tire, Nev-R-Adjust® Brakes, Radial Tires w/ Nitrofill™SAFETY PACKAGEPower Tongue Jack, 12V Battery Disconnect Switch, 80% Tint Radius Safety Glass Windows, LP/CO Detector, Fire Extinguisher, No Excuses Lionshead® Tire WarrantyINTERIOR PACKAGE17” Oven w/ Cast Iron Three Burner Cooktop, Bathroom Skylight, Lumber Core Cabinet Stiles, Adjustable Hidden Hinge Cabinet Hardware, Full Extension Four-Sided Craftsman Drawers, Radiant Foil Insulation Technology - Ceiling, Floors, Front, Stainless Steel Single Basin Sink, 15,000 BTU Ducted Air Conditioning Distribution System, Grate Style Sink Cover/Drying Rack, Hardwood Cabinet Doors, Gas/Electric Refrigerator, LED Accent Lighting, Metroplitan Grey Countertops, Master Suite w/ Queen Bed, 72” Solid Passage Doors, Master Bedroom Accent Wall, Black CabinetHardware, Underbed Storage Shelf, Black Faucets, Congoleum™ Stain-Resistant Vinyl Flooring, Roller Shades in Bedroom & Living RoomHD PACKAGE(N/A 2217, 2414, 2715)Fiberglass Front Cap w/ Automotive Window, Residential Microwave, Solid Surface Kitchen Countertop, 100 Gallons Fresh Water Tank, 16” Radial Tires, “Quick Clean” Central Vac, Electric Fireplace (N/A 2815), Rubber Garage Flooring (3212 & 3310 only)GARAGE PACKAGEGenerator Prep, 20 Gallon Fuel Station, Single Electric Queen Bed w/ Max Clearance Sofa/Dinette, 5,000# Cargo Tie Downs, Insulated Floor, Black Rear Privacy Screen,Insulated Ramp Door, Black Night Shades, Ramp Patio Cable Kit, Alumi-Tread Rear Entry StepsTECHNOLOGY PACKAGEWinegard Air 360 Antenna w/ WiFi & 4G L TE Prep, Backup Camera Prep, Dual Zone Soundbar w/ Built-in Subwoofer, TV and Cable Connections in Bedroom & Garage, Exterior Speakers, Convenient USB Charging Stations, 39” Living Room TVOPTIONAL EQUIPMENTSTANDARD EQUIPMENTMANDATORYOPTIONSActual towing capacity is dependent on your particular loading and towing circumstances, which includes GVWR, GAWR and GCWR, as well as adequate trailer brakes. Please refer to the Owners Manual of your vehicle for further information. All information contained in this brochure is believed to be accurate at the time of publication. However, during the model year, it may be necessary to make revisions and Forest River, Inc., reserves the right to make all such changes without notice, including prices, colors, materials, equipment and specifications as well as the addition of new models and the discontinuance of models shown in this brochure. Therefore, please consult with your Forest River dealer and confirm the existence of any materials, design or specifications that are material to your purchase decision. ©2019 XLR, a Division of Forest River, Inc., a Berkshire Hathaway company. All Rights Reserved. 9/19• 4.0 Onan Generator • VIP Party Deck (Railing Only) • U-shaped Booth Dinette (3212 & 3310 only)• Quick Cool Package• Solar Package • 12V Heated Holding Tanks。
LS7, 规格书,Datasheet 资料

WORLDWIDE SUBSIDIARIES AND SALES OFFICES
© 2005 PANDUIT Corp. ALL RIGHTS RESERVED.
SA-IDCB19 Repla源自es SA-IDCB04 04/2005 Printed in the U.S.A.
Label Wires, Terminal Blocks, Tool Bins and more
Easy
• Fast loading label cassette includes both label material and ribbon to make changing labels easy • No more spacing and guesswork — length function lines up legends with ports and terminals • Advanced alpha and numeric serialization speeds label creation
LS7-75NL-1 LS7-75NL-2 3/4" (18mm) black/white 3/4" (18mm) black/clear
For a copy of PANDUIT limited warranties, log onto /warranty
®
PANDUIT Corp. Tinley Park, IL 60477-3091
The Solution to Your Labeling Problems
PANACEA LS7
®
Part Numbers
Printer and Accessories:
七驱动器混合入耳式耳机 IT07 使用说明书

Thank you for selecting the IT07 Audiophile in-ear monitors. Plesae take a few minutes to read these instructions carefully before using the product.谢谢您选择 IT07 入耳式耳机。
请您在使用本产品前花几分钟时间仔细阅读本说明书。
SAFETY INSTRUCTIONSWhen you connect the in-ear monitors, please make sure that the volume level is set to minimum. Adjust the volume level only after inserting the eartips. To avoid possible hearing damage, do not use your in-ear monitors for extended periods of time at high volume.The ability to hear your own voice while listening and speaking normally with in-ear monitors can serve as a measure of correct volume adjustment.We would like to point out that excessively high volumes and long listening times may cause hearing damage. Hearing defects can constitute an irreversible impairment of hearing ability.1安全须知当您连接耳机时,请确保音量设置为最小。
LIS HL7(网口通讯协议)之欧阳文创编
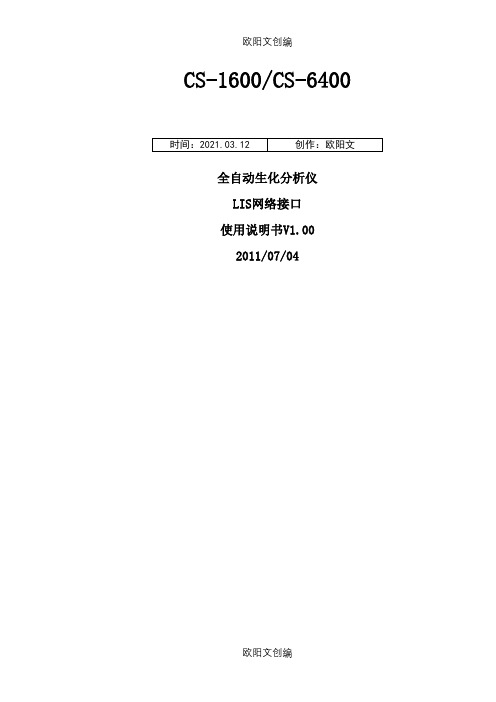
CS-1600/CS-6400全自动生化分析仪LIS网络接口使用说明书V1.002011/07/04前言使用本系统前,请仔细阅读并理解本接口手册的内容,以便正确使用该系统。
本使用说明书的读者对象为进行LIS(实验室信息系统)开发的人员以及需要了解HL7 接口的其他相关人员。
本接口手册用于指导LIS系统开发商开发LIS接口,目的是使LIS系统能够同生化分析仪系统进行通信。
开发者需要具备一定的LIS、HL7标准相关知识以及网络编程的能力。
网络层通讯协议为TCP/IP,应用层协议为HL7,版本2.3.1。
建议在Windows平台下使用Visual C++、Delphi等开发工具进行接口开发。
本使用说明书为CS-1600/CS-6400全自动生化分析仪HL7接口使用说明书。
目录1. 接口概述- 1 -1.1 HL7消息结构- 1 -1.2 HL7底层协议- 1 -2. 通讯格式- 3 -2.1 支持的HL7消息- 3 -2.2 消息段- 6 -3. 通迅示例- 22 -3.1发送检测数据过程- 22 -3.2发送查询请求过程- 25 -1. 接口概述HL7是标准化的卫生信息传输协议,是医疗领域不同应用之间电子传输的协议。
HL7汇集了不同厂商用来设计应用软件之间界面的标准格式,它将允许各个医疗机构在异构系统之间,进行数据交互。
最初它由美国定义,现在已经被很多国家采用。
本接口下数据的传输格式都是按照HL7版本2.3.1来创建的。
1.1 HL7消息结构在HL7通讯协议中,消息(Message)是数据在系统之间交换的基本单元,每条消息都有各自的消息类型,用于定义消息目的消息类型中有触发事件。
一个消息由多个段(Segment)组成,每一段都有相应的名称,用于界定其内容或功能。
而一个段又由多个数据字段(Data Field)组成。
一个消息中的第一个段总是消息头段(Message head segment),它指明了发送和接收的程序名、消息类型、以及一个唯一的消息ID号码等,接下去段的构成由消息的类型决定。
- 1、下载文档前请自行甄别文档内容的完整性,平台不提供额外的编辑、内容补充、找答案等附加服务。
- 2、"仅部分预览"的文档,不可在线预览部分如存在完整性等问题,可反馈申请退款(可完整预览的文档不适用该条件!)。
- 3、如文档侵犯您的权益,请联系客服反馈,我们会尽快为您处理(人工客服工作时间:9:00-18:30)。
LandStar7软件使用说明书LandStar7概述本章节介绍●软件简介●软件界面●软件安装软件简介软件界面LandStar7软件主界面分为4个页面:【项目】【测量】【配置】【工具】。
启动界面:在某台安卓设备上,首次安装运行本软件,会直接进入主界面。
依次滑动进入下一页。
状态栏:【】:接收机电池的电量。
【】:设备信息,点击可查看当前设备的详细信息。
【】:N/A,A表示接收卫星的总数;N表示有效解算的卫星数。
【】:单点状态,点击该标志可以查看DOP信息及位置信息。
【】:浮动状态,点击该标志可以查看DOP信息及位置信息。
【】:固定状态,点击该标志可以查看DOP信息及位置信息。
【精度】:H:平面精度;V:高程精度;RMS:相对中误差。
1、设备信息点击“状态栏”,可以查看当前设备的详细信息。
如下图所示:详细内容请参照章节2.52、星空图点击“状态栏”可以打开星空图显示界面,点击星空图界面“列表”可以查看当前卫星信息。
点击卫星信息列表界面“星空图”可以返回星空图界面。
星空图:显示当前星空图各卫星的参考位置信息。
不同颜色代表不同卫星系统,同时在星空图下方用双向柱状图显示L1、L2信噪比。
柱状图颜色代表不同信噪比范围:信噪比≤20 显示绿色;20<信噪比≤40 显示蓝色;卫星信息列表:点击“列表”进入卫星信息列表,显示当前搜到的各卫星编号、卫星系统、L1\L2\L5信噪比、高度角、方位角、锁定情况等信息。
卫星号:星座卫星号范围GPS 1-32SBAS 120-138GLONASS 38-61BDS 161-1903、精度包括位置信息,精度和DOPs值信息。
位置:解算状态(单点、浮动或固定);当前位置WGS84坐标;GPS时间;差分延迟;精度:H,V,RMS;DOPs:表示当前卫星搜索状态的空间精度因子,包含PDOP、HDOP、VDOP、TDOP和GDOP 五个值。
点击【】,当前WGS84坐标转换成WGSXYZ、本地BLH、本地XYZ,坐标值可相互转换。
标题栏可以显示当前打开项目的项目名称和打开程序所在的项目。
菜单栏显示项目包含的各个功能项目,如工程模块、测量模块、工具模块、配置模块等。
软件安装将软件LandStar7程序(*.apk)拷贝至安卓设备上,触屏点击程序开始安装,程序安装成功,在桌面上出现LandStar7程序图标。
一、项目本章节介绍:●工程管理●坐标系参数●导入●导出●其他导出●底图管理●点管理●线管理●地物管理●华测云●代码管理●工程代码1.1工程管理在主界面项目页点击【工程管理】进入工程管理界面,对工程进行管理,如图1-1所示。
图1-1无论何种作业模式下工作,都必须首先新建一个工程对数据进行管理。
点击【新建】,弹出新建工程对话框,如图1-2所示。
图1-2 图1-3在“工程名”中输入工程名称;“作者”中输入操作员的姓名;“日期”默认是当地时间;“时区”是指当地时间和GPS时间相差的时区,可以在下拉列表中选择-12时区到+14时区。
套用工程选中套用工程后,会弹出一个历史工程列表,如图1-3所示,可选中其中一个工程点击【确定】,即可完成套用工程,套用工程的目的是为了套用工程中的坐标系及转换参数,这样在多个工地来回作业时,参数选取变得更加简单直观。
操作如下:第一天有任务A,做过点校正,第二天新建任务时想继续使用这个校正参数,在工程管理输入新建工程名称,选中“套用工程”选择“A”即可完成新建任务并套用参数功能。
注:新建任务若不套用工程,默认无转换参数。
套用工程,只套用工程参数。
坐标系选中坐标系后,会弹出坐标系管理界面,如图1-4所示:点此按钮,会出现“选择椭球界面”如下①-④图所示①②图1-4【登录】:用户登录,点击输入用户名,密码,用户名为admin ,初始密码为123456;登陆之后才可以查看基准转换或平面校正下的参数。
【另存为】:点击另存为之后,会提示此坐标系参数将保存的路径。
【接收】:点击接受按钮之后,将返回新建工程界面,此时说明坐标系已选好。
【添加】如果常用列表下没有可选的椭球,点此按钮进行添加。
【删除】点此按钮,可删除常用列表下的某一坐标系。
【接受】点击接受按钮之后,将返回坐标系管理界面,此时说明椭球已选好。
代码集选中代码集之后,会弹出代码集界面,如图1-5所示:图1-5【新建】如果常用列表下没有要选择的代码,可以选择新建代码。
可选择常用列表下的某一种椭球,也可以点击【添加】按钮自定义添加椭球③④常用代码,包含CASS 代码。
如果选择CASS 格式,在地图和点测量中,将会出现CASS 中的地物【编辑】对当前新建的代码进行编辑。
【删除】删除当前代码【导入】此处可以通过导入的方式导入其他代码。
【接受】完成代码集的选择之后将返回上一界面,此时说明已完成代码集的选择和新建。
1.【新建】点击新建,会弹出创建代码集界面,如图1-6所示:图1-61)新建图层点击,进入新建图层界面。
点击新建,进行图层创建,输入图层名称,选择图层的颜色、透明度和样式,可以对图层进行描述。
点击确定,完成图层新建,如图1-7所示。
图1-62)新建代码点击,进入创建代码界面,输入代码名称,代码类型包括:点状地物、面状地物、线状地物,选择代码的颜色、样式,也可对代码进行描述,点击确定,即可完成代码的新建,如图1-7所示。
图1-7完成坐标系和代码集的选择或新建之后,点击确定,即完成了工程的新建。
LandStar7中无法删除已打开的工程,对正在操作的工程文件有保护和删除提醒机制“无法删除当前打开的工程”。
删除未打开的工程文件,会弹出一个对话框“确定删除此工程?”,选择确认,删除该确定工程文件;选择取消,不删除该工程文件。
若想继续某一项作业,则可以打开之前的工程,点击【确认】即可。
打开另一个工程时会提示“关闭当前工程并打开一个工程”? 选择确认,打开工程XXX,选择取消,不打开工程XXX。
点击【上传或下载+】,进入华测云服务,上传或下载工程文件,IP为服务器端的IP 地址,端口为服务端设置中采集端服务中设置的参数,输入用户名密码,点击登陆即可完成上传或下载。
1.2坐标系参数坐标系参数中包含:椭球、投影、基准转换、平面校正、高程拟合。
【椭球】包括椭球名称、半长轴、扁率倒数等。
半长轴和扁率倒数无需设置,为默认值即可。
坐标系名称是定义所需坐标系统名称,建议使用项目名作为坐标系统名。
【投影模型】内置了各国常用的投影方法,包括高斯投影、横轴墨卡托、UTM投影等。
并显示各投影模型的参数。
通常需要更改的只有中央子午线,它是指项目平面投影的中央子午线,若自定义坐标系,则输入该测区的平均经度,经度误差一般要求小于30分。
【基准转换】表示两个坐标系转换所采用的数学模型。
基准转换模型(包括无参数、三参数、7参数)。
用户如果有当地的七参数可直接输入则不需点校正。
七参数转换:至少需要三个已知点(已知点可以国家坐标系下的坐标,或者与WGS84坐标系之间存在较小旋转坐标系下的坐标,最好三个以上的已知点,可以检查已知点的正确性)。
此方法解算模型严谨,因此要求已知点的坐标精度高,一般在大范围作业时使用。
当已知点精度不高时,不推荐使用七参数三参数转换:至少一个已知点(已知点可以国家坐标系下的坐标,或者与WGS84坐标系之间存在较小旋转坐标系下的坐标,最好两个以上的已知点,可以检查已知点的正确性),小范围使用,精度由作业范围决定,且随作业距离增加而降低。
【加常数】为了转换过后的坐标保持为正数所加的常数,东加常数一般默认为500000米,可根据需要填写。
【投影面高】若在投影模型下拉框中选择自定义选项,则需在此顶一此项。
【平面校正】经过点校正并应用后,校正参数会在坐标系参数界面显示出来,用户登录成功后可查看。
平面校正目前支持TGO方法【高程拟合】高程拟合目前支持四种算法:固定差、平面拟合、曲面拟合和TGO方法,默认选择固定差。
●固定差:即平移,至少一个起算点;●平面拟合:指对应于多个水准点处的高程异常,生成一个最佳的拟合平面,当此平面平行于水平面时,平面拟合等同于固定差改正,该拟合方法至少要求三个起算点;●曲面拟合:指对应于多个水准点处的高程异常,生成一个最佳的拟合抛物面。
曲面拟合对起算书据的要求比较高,如果拟合程度太差,可能造成工作区域中的高程改正数发散。
该拟合至少要求五个起算点;●TGO方法:天宝TGO软件的高程转换模型,包括五个参数:北原点、东原点、北斜坡、东斜坡、高差常量。
【大地水准面模型】如勾选大地水准面模型,点击选择,选择大地水准面模型文件。
目前软件支持*.ggf格式的大地水准面模型文件。
1.3导入若输入大量已知点到手簿,浪费时间且易出错。
点击主界面【导入】可把已知数据根据导入要求编辑成指定格式,复制到手簿存储的某一路径或手簿存储卡里。
【坐标系统】可选择平面或经纬度。
【文件类型】txt,csv类型的文件格式,多种固定排列格式可选,能满足大部分客户需求,用户也可自定义文件格式。
【路径】选择到数据文件所存的路径选择导入的数据文件。
选择需要导入的文件后,点击导入。
选择路径1.4导出点击主界面【导出】,软件会把需要导出的点导出在手簿内存中的某一路径下,可通过同步软件将文件复制到电脑上。
【导出点类型】用户可选择导出点类型包括输入点,测量点,放样点,计算点四种。
【时间】可通过设定起始时间和截止时间选择要到导出的点。
【坐标系统】可选择平面或经纬度。
【文件类型】txt,csv类型的文件格式,多种固定排列格式可选,能满足大部分客户需求,用户也可自定义文件格式。
【路径】选择文件导出路径,点击导出。
选择路径1.5其他导出其他导出信息包括:KML导出,DXF导出,控制点测量报告导出,测量点详细成果导出。
点击导出,提示“导出成功”。
报告存放的路径在程序安装所在的目录下如:项目名/报告.htm文件,手簿和电脑连接后,将文件拷出到电脑,双击此文件可以查看该报告文件。
1.6底图管理底图管理主要是将需要的底图通过某一路径导入至软件中。
导入的图层将会出现在【测量】-【地图】-【设置】-【显示】下1.7点管理点管理中可查看输入点和测量点以及待放样点的坐标点击【】来创建点。
创建点时包括如下属性:名称,代码,坐标系统(包括:本地NEH,本地BLH,本地XYZ,WGS BLH,WGS XYZ坐标),角色(包括:一般点,放样点,控制点),输入要创建的点坐标,其中代码项为非必填项。
设置好以上值,点击【】,一个点坐标即可建好。
点击【】,点的条件可以通过名称,代码,解状态等字段进行时间等任意一个条件来查询。
名称:可以通过名称进行完全匹配筛选。
代码:可以通过代码准确筛选。
数据来源:通过数据来源进行精确查询,数据来源包括:测量,计算,输入、导入、图选。