粗甲醇经单塔分离作为MTO_二甲醚原料甲醇的方案探讨_张艳红
MTO

丙烯需求量年 均增长率为 7.93%同期产 能增长速度 10.76%
2004
丙烯供应 能力1.2*108t
当量需求 1.76*108t
2010
丙烯当量需求量的 年均增长率为6.93 %,同期产能增长
速度为8.75%
2015
2010~2015年丙烯市场 满足率仅为 73.15 %
我国乙烯当量消费预测( 104 t )
国内DMTO技术
2007年中科院大连化物所与神华集 团在内蒙古包头市,建立了一条年加工 甲醇180万吨、年产烯烃60万吨的大型生 产线,此前运用同样技术的陕西榆林20 万吨/年煤基烯烃工业化示范项目正式启 动。这标志着我国拥有自主知识产权的 “甲醇制取低碳烯烃(DMTO)工艺” 开始迈向工业化的道路。
MTO工艺 流化床裂解 SAPO-34
碳酸二甲醚
MTG工艺 固定床裂解
ZSM-5
醋酸
甲醇和异丁烯 酸性催化剂
MTBE
丙烯 石脑油
甲醛
MTP工艺 固定床裂解
ZSM-5
为什么要选择甲醇制低碳烯烃?
1
乙烯和丙烯是现代化学工业中的重要基础原料,其需求量 将越来越大。乙烯主要通过轻烃和石脑油等的蒸汽裂解得到, 丙烯主要来自蒸汽裂解制乙烯装置和炼油的催化裂化装置。
产物的典型组成:
丙烯
乙烯
(%)71.0
1.6
丙烷
C4~ C5
焦炭
C6
1.6
8.5
<0.01
16.1
Lurgi公司MTP工艺发展前景
❖ Lurgi公司已经与伊朗国家石油公司的Zagros子公司签署合同, 在 Bandar Assaluye 地区建设5000 t/d甲醇装置,并采用Lurgi公司 ( MTP) 技术建设520,000t/a丙烯装置 。2004年3月,Lurgi公司还 和伊朗 Fanavaran石油公司签署了MTO技术转让、初步设计和提 供专用设备的协议,并筹建100,000t/a丙烯装置,计划2009年投产。 这将是世界上第一套以甲醇为原料生产丙烯的工业装置。
甲醇制二甲醚
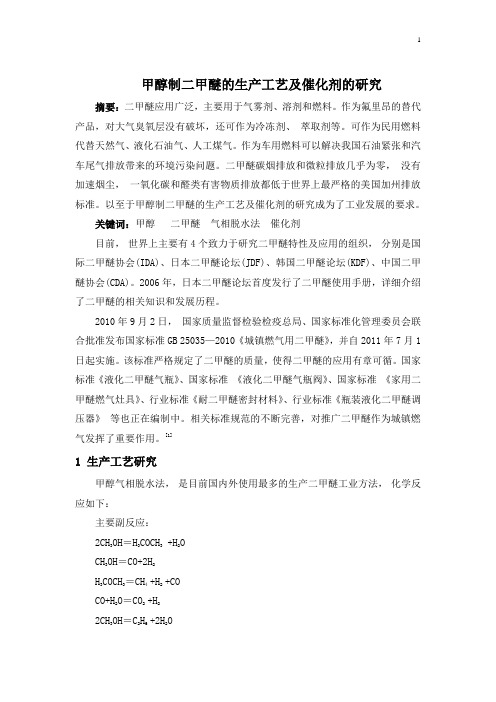
甲醇制二甲醚的生产工艺及催化剂的研究摘要:二甲醚应用广泛,主要用于气雾剂、溶剂和燃料。
作为氟里昂的替代产品,对大气臭氧层没有破坏,还可作为冷冻剂、萃取剂等。
可作为民用燃料代替天然气、液化石油气、人工煤气。
作为车用燃料可以解决我国石油紧张和汽车尾气排放带来的环境污染问题。
二甲醚碳烟排放和微粒排放几乎为零,没有加速烟尘,一氧化碳和醛类有害物质排放都低于世界上最严格的美国加州排放标准。
以至于甲醇制二甲醚的生产工艺及催化剂的研究成为了工业发展的要求。
关键词:甲醇二甲醚气相脱水法催化剂目前,世界上主要有4个致力于研究二甲醚特性及应用的组织,分别是国际二甲醚协会(IDA)、日本二甲醚论坛(JDF)、韩国二甲醚论坛(KDF)、中国二甲醚协会(CDA)。
2006年,日本二甲醚论坛首度发行了二甲醚使用手册,详细介绍了二甲醚的相关知识和发展历程。
2010年9月2日,国家质量监督检验检疫总局、国家标准化管理委员会联合批准发布国家标准GB 25035—2010《城镇燃气用二甲醚》,并自2011年7月1日起实施。
该标准严格规定了二甲醚的质量,使得二甲醚的应用有章可循。
国家标准《液化二甲醚气瓶》、国家标准《液化二甲醚气瓶阀》、国家标准《家用二甲醚燃气灶具》、行业标准《耐二甲醚密封材料》、行业标准《瓶装液化二甲醚调压器》等也正在编制中。
相关标准规范的不断完善,对推广二甲醚作为城镇燃气发挥了重要作用。
[1]1 生产工艺研究甲醇气相脱水法,是目前国内外使用最多的生产二甲醚工业方法,化学反应如下:主要副反应:2CH3OH=H3COCH3+H2OCH3OH=CO+2H2H 3COCH3=CH4+H2+COCO+H2O=CO2+H22CH3OH=C2H6+2H2O主要生产工艺过程为:甲醇经气化与反应器出来的反应产物换热后,进入二甲醚反应器进行气相催化脱水反应,反应产物经换热后,用循环水冷却冷凝。
反应条件为 0.5~1.8MPa、230℃~400℃,催化剂为 ZSM分子筛、磷酸铝或γ-Al2O3,冷却冷凝后的物料进行气液分离,气相送洗涤塔用甲醇或甲醇-水溶液吸收回收二甲醚,液相的粗二甲醚送精馏系统分离。
气相甲醇脱水制二甲醚工艺模拟与优化

气相甲醇脱水制二甲醚工艺模拟与优化气相甲醇脱水制二甲醚(MTO)是一种重要的催化转化过程,在实际工艺中可以通过模拟和优化来提高生产效率和产品质量。
以下是常用的工艺模拟和优化方法:1.催化剂选择和优化:催化剂是气相甲醇脱水制二甲醚过程中的关键因素。
通过催化剂的选择和优化,可以提高反应速率和选择性,促进二甲醚的产生。
常用的方法包括活性组分的调整、载体的优化以及处理工艺的改进。
2.反应器模拟和优化:通过数学建模和计算方法,可以模拟和优化气相甲醇脱水制二甲醚反应器的运行。
模拟可以帮助理解反应机理和动力学,优化可以通过调整反应器的温度、压力、催化剂分布和反应物流动方式等来提高反应的效率和产量。
3.热集成和能量优化:气相甲醇脱水制二甲醚过程中的能量消耗往往较大。
通过热集成技术,优化废热的回收和利用,可以提高能量效率。
常用的方法包括热交换网络设计、废热回收系统和废热利用方案的优化等。
4.优化操作条件:通过调整反应的操作条件,如温度、压力、反应物料比和催化剂浓度等,可以找到最佳的操作窗口。
优化操作条件可以提高二甲醚的产率和选择性,减少副反应产物的生成。
5.系统整合和流程优化:气相甲醇脱水制二甲醚过程中,反应、分离、回收等单元之间相互关联。
通过系统整合和流程优化,可以在整个过程中最大程度地提高资源的利用效率、减少能耗和废物排放。
以上方法是对气相甲醇脱水制二甲醚工艺进行模拟和优化的一些常用手段。
根据具体的工艺特点和优化目标,可以结合实际情况采用适合的方法来提高工艺的效果和经济性。
在实际应用中,需要综合考虑反应动力学、传热传质、流体力学等多个因素,进行综合优化和调整。
MTO 级甲醇单塔精馏工艺能耗分析

甲醇产 品的重要 工序 , 而且精 馏的能耗也是影响甲醇 生产成
本 的关键 因素。因此 , 对 甲醇精 馏工 艺进 行系统 研究 , 可 以
指导甲醇生产企业节能减耗 , 促进 甲醇及其下游产品的更好 发展 J 。目 前广 泛使 用的 甲醇精制技术 为单塔精馏 、 双塔精
关键词 : 单塔精馏 ; 回流 比; 温度 ; 能耗 中图分类号 : T Q 2 2 3 . 1 2 1 文献标识 码: B 文章编号 : 1 0 0 8—0 2 1 X( 2 0 1 4 ) 0 9—0 1 8 4—0 4
An a l y s i s o f M TO Me t h a n o l S i n g l e T o we r Di s t i l l a t i o n Pr o c e s s En e r g y Co n s u mp t i o n
de / i n p mj e c t e n t i e r p r o c e s s i n t h e d o m e s i t c p r o d u c t i o n i n 2 0 0 8 .N a me 1 y e n e r  ̄c o n s u m p i t o n f o r e f i n i n g c r u d e me t h a n o l
r e q u i ed r c o n d i t i o n s ,b y o p i t mi z i n g ef r l u x r a t i o ,r ef l u x t e mp e r a t u e ,t r he d i s t i l a t e t e mp e r a t u r e i n d i c a t o s r t o a c h i e v e t h e
甲醇催化脱水制备二甲醚的方法[发明专利]
![甲醇催化脱水制备二甲醚的方法[发明专利]](https://img.taocdn.com/s3/m/9fae15f409a1284ac850ad02de80d4d8d15a01fc.png)
[19]中华人民共和国国家知识产权局[12]发明专利申请公开说明书[11]公开号CN 1368493A [43]公开日2002年9月11日[21]申请号01103219.7[21]申请号01103219.7[22]申请日2001.02.07[71]申请人北京燕山石油化工公司研究院地址102550北京市房山区燕山凤凰亭路15号[72]发明人赵岚 雷鸣 韩春国 [74]专利代理机构中国国际贸易促进委员会专利商标事务所代理人龙传红[51]Int.CI 7C07C 43/04C07C 41/09权利要求书 2 页 说明书 13 页[54]发明名称甲醇催化脱水制备二甲醚的方法[57]摘要涉及一种甲醇催化脱水制二甲醚的方法,其中脱水是在含SO 42-的固体酸催化剂存在下进行的。
催化剂中SO 42-含量优选为2-25重量%,优选的催化剂载体选自γ-Al 2O 3,η-Al 2O 3和SiO 2。
本发明方法成本低廉,稳定性好,用于制备二甲醚时能在普通的反应条件下实现大于75%的甲醇转化率和大于99%的二甲醚选择性。
01103219.7权 利 要 求 书第1/2页 1.一种通过甲醇催化脱水制备二甲醚的方法,其中脱水是在含SO42-的固体酸催化剂存在下进行的。
2.权利要求1的方法,其中固体酸催化剂中SO42-的含量为2-25重量%。
3.权利要求1的方法,其中固体酸催化剂中SO42-的含量为5-20重量%。
4.权利要求1的方法,其中固体酸催化剂中SO42-的含量为8-15重量%。
5.权利要求1的方法,其中固体酸催化剂中SO42-是以硫酸盐的形式存在的。
6.权利要求5的方法,其中所述的硫酸盐选自硫酸铝(Al2(SO4)3),硫酸锌(ZnSO4)和硫酸亚铁(FeSO4)。
7.权利要求1或2的方法,其中固体酸催化剂包括选自γ-Al2O3,η-Al2O3和SiO2的载体。
8.权利要求7的方法,其中固体酸催化剂包括γ-Al2O3为载体。
- 1、下载文档前请自行甄别文档内容的完整性,平台不提供额外的编辑、内容补充、找答案等附加服务。
- 2、"仅部分预览"的文档,不可在线预览部分如存在完整性等问题,可反馈申请退款(可完整预览的文档不适用该条件!)。
- 3、如文档侵犯您的权益,请联系客服反馈,我们会尽快为您处理(人工客服工作时间:9:00-18:30)。
对氨要求≤1 mg/L,总金属离子≤1 mg/L、硫≤0.5 mg/L
C4 以上的烃 ≤0.01 ~0.86
从表 1 中可见,粗甲醇中微量的低碳烷烃和烯烃 与 MTO 反应的副产物一致,其含量不超过 MTO 对甲醇 原料纯度的要求,并且不会影响 MTO 催化剂的性能; 粗甲醇中微量的乙醇在 250 ℃左右就会发生分子内 脱水反应,转化为乙烯和水。丙醇、丁醇、乙酸、水等杂 质的沸点高于甲醇,难于通过加热挥发的方式从甲醇 中分离,但是一方面这几种杂质的含量与 MTO 反应产 物的含量相当,进入反应器后,不会对 MTO 反应的催 化剂产生不良的影响。另一方面,MTO 反应产物分离 的技术方案中,包含了对乙酸等各种残存氧化物的脱 除工艺,含氧有机物不会再次随循环物流进入反应 器。由此可见,粗甲醇中重馏分副产物不会影响 MTO 反应。粗甲醇中的水是甲醇制烯烃过程原料中必须添 加 的 组 分 ;粗 甲 醇 中 的 水 含 量 范 围 较 宽 ,通 过 调 整 甲
~77.3
~0.060Βιβλιοθήκη 5 ~0.012 4 ~0.681
~0.269 ~0.857 5 0.2~0.05 ~0.017 8
沸点 /℃
100
-191
-78.5
-253
64.8
-161.5 -195.8
78.4
MTO 对原料要求 ≤8.5
~91
组成 粗甲醇 MTO 出口气 沸点 /℃ MTO 对原料要求
收稿日期:2013-04-16 作者简介:张艳红(1968— ),女,黑龙江肇东,高级工程师,博士,1991 年本科毕业于齐齐哈尔大学精细化工专业,现从事 煤制化学品工业技术研究及设计管理工作,E-mail:zhangyh680529@sina.com。
-6-
煤化工
2013 年第 4 期
1.2 粗甲醇中的杂质对 MTO 反应影响的分析 甲醇合成的过程中,合成气在铜基催化剂的作用
醇合成气中 CO2 的含量,可以使粗甲醇中的水含量达 到 MTO 反应对甲醇的含水量要求。 1.3 通过控制合成气中 CO2 的含量降低粗甲醇的含
水量 在甲醇合成反应中,CO2 也是有效成分,由甲醇合 成的主反应方程式可见,CO2 在参与甲醇合成反应的 过程中生成水。水能够抑制甲醇脱水生成二甲醚,阻 止 C0 的变换反应,防止催化剂结炭,降低反应的放热 量,起到调节系统温度的作用。合成气中 CO2 的含量 越高,粗甲醇中的水含量也越高。 受限于原料煤的氢碳比低于甲醇合成反应的原 料 气 的 要 求 ,以 煤 为 原 料 制 甲 醇 的 生 产 过 程 中 ,需 要 将部分 CO 变换成 CO2 和 H2,并将过剩的 CO2 排放至环 境中,以实现甲醇合成气氢碳比在 2.05 左右的要求。
MTO 反应的速度非常快,反应接触时间至 0.04 s 时,甲醇的转化率就可以达到 100%,甲醇转化的快速 反应特征受到分子筛骨架结构的限制,带来的副作用 是催化剂上发生结焦,结焦会造成催化剂的活性和产 物的选择性降低。为了降低副产物的生成量、减少 MTO 催化剂表面的结焦现象,MTO 反应的甲醇原料中 通常需掺入 5%左右的水。
羰基化合物≤2 000 mg/L;酸度(以 HCOOH 计)≤150 mg/L;碱度(以 NH3 计)≤8 mg/L
组成 粗甲醇 MTO 出口气 沸点 /℃ MTO 对原料要求
氨 ≤0.001
-33.5
乙烷
乙烯
丙烯
丙烷
0.203 -88.6
~10.98 -103.71
~7.13 -47.7
~0.456 -42.1
2013 年 8 月
张艳红:粗甲醇经单塔分离作为 MTO、二甲醚原料甲醇的方案探讨
-7-
将煤制合成气中 CO2 的含量通过脱碳调整到 2.5%左 右,可以使粗甲醇中的水质量分数降低到 5%,满足 MTO 反应对甲醇原料的水含量要求。 1.4 粗甲醇单塔分离方案在煤化工中的优势及简化
流程 目前甲醇生产装置中,主要采用双塔精馏或三 塔精馏技术实现粗甲醇的精制,少部分装置采用四塔 精馏流程。3 种精馏流程均有 1 个预精馏塔,在预精 馏塔内,粗甲醇经塔底再沸器加热后,其中的二甲醚、 甲乙醚、部分甲酸甲酯、甲醛、CO、H2、N2 等低沸点杂质 从 液 相 中 挥 发 ,并 从 塔 顶 脱 除 ,塔 底 液 经 加 压 后 进 入 精馏主塔。双塔流程中精馏主塔塔顶出甲醇产品,塔 底 为 精 馏 废 水 ,侧 线 抽 出 杂 醇 油 [4]。 三 塔 流 程 分 别 从 加 压 精 馏 塔 、常 压 塔 的 塔 顶 分 离 出 精 甲 醇 产 品 ,塔 底 分出高沸点醇类、水[5]。采用三塔和四塔精馏工艺,可 得到纯度高的甲醇,但是提高了投资,流程长,提高了 操作成本。3 种甲醇精制的生产方案均已实现了大型 化,因塔内件结构、产品精度、能量综合利用等方面不 同 ,多 塔 精 馏 的 低 压 蒸 汽 消 耗 量 有 所 差 别 ,精 甲 醇 精 馏的蒸汽消耗大多数在 2 t/t 左右[6]。 由表 1 可知,甲醇合成过程副产物的种类大部分 包含在 MTO 反应副产物中,并且部分杂质的含量高于 MTO 反应产物中的杂质含量。影响 MTO 反应催化剂性 能 的 杂 质 为 :氨 氮 、金 属 、氯 等(各 项 杂 质 均 低 于 1 mg/L)及硫(低于 0.5 mg/L),除氨氮为甲醇反应系统 易 生 成 的 杂 质 外 ,其 他 几 种 为 外 源 性 杂 质 ,防 止 原 料 及生产设备带入该类杂质,或通过加净化床等措施可 以 消 除 此 类 杂 质 ;粗 甲 醇 中 甲 酸 甲 酯 、氨 类 杂 质 的 含 量超过了 MTO 反应产物及 MTP 反应对甲醇原料的要 求。因此粗甲醇中可能影响 MTO 反应性能的杂质可以 不采用粗甲醇经过多塔精馏的方式脱除。 粗甲醇中氨、含羰基杂质的含量高,为满足 MTO 反应对甲醇的质量要求,需要实施脱除措施。粗甲醇 中 轻 组 分 杂 质 的 沸 点 低 于 甲 醇 ,易 于 在 低 压 、加 热 的 条件下脱除。通过调节煤制合成气中 CO2 的体积分数 在 2.5%左右,控制粗甲醇中的水含量,同时采用与甲 醇精馏预塔结构相似的稳定塔,脱除粗甲醇中的轻组 分,基本能满足 MTO 反应对甲醇质量的要求。 煤制合成气生产甲醇的装置中,控制合成气中的 二氧化碳体积分数在 2.5%左右。设计单塔分离获取 甲醇制烯烃甲醇原料的工艺流程(见图 1)为:粗甲醇 通过泵输送进稳定塔中部的进料段,在塔底再沸器的 加 热 作 用 下 ,粗 甲 醇 中 的 氢 气 、CO、CO2、甲 烷 、氮 、氩 气 、氨 、甲 酸 甲 酯 、丙 酮 、二 甲 醚 等 溶 解 气 和 轻 组 分 杂
关键词 甲醇,单塔分离,精馏,MTO,二甲醚
文章编号:1005-9598(2013)-04-0005-05 中图分类号:TQ54 文献标识码:B
目前,煤经甲醇制烯烃企业通常采用以精甲醇 为原料裂解制烯烃,而粗甲醇通过精馏制精甲醇的能 耗占精甲醇成本的 20%左右;部分二甲醚生产企业直 接以粗甲醇为原料,但是存在粗甲醇中的二氧化碳、 甲酸甲酯等多种轻组分杂质在二甲醚精馏塔内难以 脱除,而导致二甲醚的产品纯度低、精馏成本高、产品 中有刺激性气味等问题。研究降低脱除粗甲醇中杂质 能耗的煤制粗甲醇分离技术,在保证产品质量和生产 工艺需求的前提下,降低粗甲醇分离过程的能耗和投 资 成 本 ,对 降 低 生 产 成 本 、提 高 甲 醇 制 烯 烃 和 二 甲 醚 生产企业的竞争力有着重要意义。本文分析了通过调 节合成气中的二氧化碳含量、简化和优化粗甲醇分离 工艺,降低煤制烯烃和煤制二甲醚生产和投资成本的 技术方案。
表 1 粗甲醇、MTO 反应器出口气组成及 MTO 对原料要求
mol%
组成
H20
CO
CO2
H2
甲醇
CH4
N2
乙醇
粗甲醇
8.52~17.0 0.006 6~0.1 0.14~0.40 0.001 7~0.03 91.13~83.0 0.01~0.1 0.007 7~0.3 0.01~0.15
MTO 出口气
粗甲醇中所含杂质可分为 2 大类,第 1 类为轻馏 分(低沸点)杂质,主要包括二甲醚 、甲乙醚 、甲酸甲 酯、甲醛、丙酮、甲醛,以及不凝性气体 CO2、CO、CH4、H2、 N2 等;第 2 类为微量的高沸点组分,主要为水、高级烷 烃、除甲醇外的醇类、烯烃和有机酸等[3]。除上述杂质 外,合成气中的 CO 会与设备和管线材质反应,生成的 羰 基 铁 进 入 甲 醇 合 成 塔 后 ,在 高 温 条 件 下 ,分 解 成 活 性铁颗粒并引发合成气中氢气与杂质氮气生成氨的 反 应 ,因 而 粗 甲 醇 的 轻 组 分 杂 质 中 含 有 微 量 氨 等 。 粗 甲醇的组成、MTO 反应对甲醇原料的要求、MTO 产物的 组成见表 1。
下生成甲醇。除主反应外,还发生水煤气变换反应、甲 醇深度裂解反应、生成低碳醇的反应等。在甲醇合成 塔出口气中,有乙醇、甲烷 、长链烃类 、甲酸甲酯 、丙 酮 、甲 酸 等 几 十 种 杂 质 [1]。 杂 质 的 种 类 及 生 成 量 与 合 成甲醇的反应温度、压力、空速、反应气的组分异常变 化 等 工 艺 条 件 密 切 相 关 ,也 与 催 化 剂 的 型 号 、甲 醇 专 利商的技术方案相关,副产物占粗甲醇总量的 1%左 右[2]。除副产物外,合成气中的组分 CO2、CO、H2 溶解在 粗甲醇的总质量分数约 0.4%。
质及少量的甲醇、乙醇、水以气体状态上升至塔顶,塔 顶流出物经冷却器降温至 40 ℃左右,大部分水分和 甲 醇 经 冷 凝 后 ,经 回 流 罐 返 回 稳 定 塔 ,不 凝 的 杂 质 从 系统内脱除,送至界区管网。在稳定塔底部抽出的甲 醇 溶 液 经 冷 却 后 ,依 据 杂 质 的 情 况 ,针 对 性 地 脱 除 杂 质或直接作为产品用泵输送至 MTO 系统。粗甲醇多塔 精 馏 工 艺 中 ,甲 醇 全 部 受 热 挥 发 、大 部 分 甲 醇 蒸 汽 在 甲 醇 精 馏 塔 顶 冷 凝 之 后 ,再 回 流 至 精 馏 塔 ,精 馏 塔 顶 甲醇的回流比通常在 1.5~2.5,在气液传质的过程 中,实现粗甲醇精制。而本方案中,甲醇稳定塔与精馏 塔 在 结 构 上 有 相 近 性 ,不 需 要 甲 醇 全 部 挥 发 ,甲 醇 分 离塔顶的气相甲醇少,液相回流比可以降低至 0.15 左右,远低于甲醇精馏塔回流比为 2.0 左右的指标。 由于回流比降低,可以大幅度地降低塔底再沸器的蒸 汽消耗量,从而降低甲醇分离过程的能量消耗和产品 成本。