冲裁工艺及冲裁模设计课件.pptx
合集下载
冲裁工艺及冲裁模设计课件

当制件公差为IT10以上时,取x=1;
当制件公差为IT11-IT13时,取x=0.75;
当制件公差为IT14以下时,取x=0.5;
(或按教材表2.3.1确定)
例1:如图所示零件的材料为Q235,料厚 t=0.5mm。试求凸、凹模刃口尺寸及公差。
解:该件φ36由落料得到, 2-φ6及18由冲孔得到。 查表2.2.3,得:2cmin=0.04mm,2cmax=0.06mm 则:2cmin-2cmax=0.02mm 由公差表查得:
差,另一件只标注公称尺寸并注明配做要求的间隙 值。
۞存在三种不同类型尺寸: (1)随磨损增大的尺寸,设工件尺寸为 :
(2)随磨损减小的尺寸,设工件尺寸为 :
(3)随磨损不变的尺寸,设工件尺寸为
:
例2:计算如图所示冲裁件的凸模、凹模刃口 尺寸及制造公差。料厚t=1mm,材料为10号钢 ,尺寸如下:
解:该件属于落料件, 选凹模为设计基准 件,只需计算落料 凹模刃口尺寸及制 造公差,凸模刃口 尺寸由凹模的实际 尺寸按间隙要求配 做。
返回
一、刃口尺寸计算的原则
۞1、考虑落料和冲孔的特点 落料件尺寸决定于凹模刃口尺寸;冲孔
件尺寸决定于凸模刃口尺寸。
۞2、考虑刃口的磨损规律 刃口磨损后,凹模刃
口尺寸扩大,凸模刃口尺 寸减小。
为使模具有一定的使用寿命,磨损到一定程度 仍能冲裁出合格的零件,落料时凹模刃口尺寸接近 制件尺寸的下限值,冲孔时凸模刃口尺寸接近制件 尺寸的上限值。
۞冲裁力实为剪切力:
۞其它三力的计算: ۞卸料力:
۞推料力:
۞顶件力:
二、压力机公称压力的选取
۞选择压力机的条件: • 冲裁工艺总力计算的三种情况: (1)采用弹压卸料装置和下出件的模具时:
当制件公差为IT11-IT13时,取x=0.75;
当制件公差为IT14以下时,取x=0.5;
(或按教材表2.3.1确定)
例1:如图所示零件的材料为Q235,料厚 t=0.5mm。试求凸、凹模刃口尺寸及公差。
解:该件φ36由落料得到, 2-φ6及18由冲孔得到。 查表2.2.3,得:2cmin=0.04mm,2cmax=0.06mm 则:2cmin-2cmax=0.02mm 由公差表查得:
差,另一件只标注公称尺寸并注明配做要求的间隙 值。
۞存在三种不同类型尺寸: (1)随磨损增大的尺寸,设工件尺寸为 :
(2)随磨损减小的尺寸,设工件尺寸为 :
(3)随磨损不变的尺寸,设工件尺寸为
:
例2:计算如图所示冲裁件的凸模、凹模刃口 尺寸及制造公差。料厚t=1mm,材料为10号钢 ,尺寸如下:
解:该件属于落料件, 选凹模为设计基准 件,只需计算落料 凹模刃口尺寸及制 造公差,凸模刃口 尺寸由凹模的实际 尺寸按间隙要求配 做。
返回
一、刃口尺寸计算的原则
۞1、考虑落料和冲孔的特点 落料件尺寸决定于凹模刃口尺寸;冲孔
件尺寸决定于凸模刃口尺寸。
۞2、考虑刃口的磨损规律 刃口磨损后,凹模刃
口尺寸扩大,凸模刃口尺 寸减小。
为使模具有一定的使用寿命,磨损到一定程度 仍能冲裁出合格的零件,落料时凹模刃口尺寸接近 制件尺寸的下限值,冲孔时凸模刃口尺寸接近制件 尺寸的上限值。
۞冲裁力实为剪切力:
۞其它三力的计算: ۞卸料力:
۞推料力:
۞顶件力:
二、压力机公称压力的选取
۞选择压力机的条件: • 冲裁工艺总力计算的三种情况: (1)采用弹压卸料装置和下出件的模具时:
第二章-冲裁工艺与冲裁模具设计PPT课件

沿工件全部外形冲裁,工件间、工件与板料边
都有搭边。材料利用率低,但能保证冲裁件质量,
模具寿命较高。
少废料排样
模具只沿工件部分外形轮廓冲裁,只有局部有
搭边。废料较少,工件质量不高,模具摩损快。
无废料排样
工件间、工件与条料间均没有搭边的存在。模具刃口
沿板料依次切下获取工件。材料利用率高,工件质量差,
模具易损坏。
裁板
纵裁
联合裁
横裁
21
冲压工艺力和压力中心的计算
概 念:
~是冲裁时压力机应具有的最小压力,是完成分离
所必需的力和其它附加力(卸料力、推料力、顶料力)的
总和。它是设计模具、选择压力机的重要依据。
冲裁力的计算
使板料发生分离的力称为冲裁力。一般平刃冲裁模的冲裁
力P可用下式计算:
= KLt
(K-系数,取1.3)
合理冲裁间隙值的确定:
❖ 工件断面质量无严格要求时,应取大间隙值;
❖ 工件的断面质量和制造精度较高时,应取较小间隙值;
❖ 在设计冲模刃口尺寸时,应考虑模具摩损因素,冲裁
间隙应取最小值。
6
方法1:理论确定法
如右图所示,可得冲裁间隙为:
= 2( − ℎ0 )tan = 2(1 − ℎ0 Τ)tan
能与其冲压时定位 基准重合 ,
并选择在冲裁过程中基本上下
不变动的面或线上。
9
凸、凹模刃口尺寸的计算
重要性:
冲模刃口处的尺寸及制造公差直接影响工件的尺寸
精度,合理的冲裁间隙也靠其保证。
前提:
尺寸
计算
的原
则:
因冲裁间隙的存在,落下的料和冲出的孔都带有锥
度,且落料件的大端尺寸与凹模刃口尺寸相近,冲出
都有搭边。材料利用率低,但能保证冲裁件质量,
模具寿命较高。
少废料排样
模具只沿工件部分外形轮廓冲裁,只有局部有
搭边。废料较少,工件质量不高,模具摩损快。
无废料排样
工件间、工件与条料间均没有搭边的存在。模具刃口
沿板料依次切下获取工件。材料利用率高,工件质量差,
模具易损坏。
裁板
纵裁
联合裁
横裁
21
冲压工艺力和压力中心的计算
概 念:
~是冲裁时压力机应具有的最小压力,是完成分离
所必需的力和其它附加力(卸料力、推料力、顶料力)的
总和。它是设计模具、选择压力机的重要依据。
冲裁力的计算
使板料发生分离的力称为冲裁力。一般平刃冲裁模的冲裁
力P可用下式计算:
= KLt
(K-系数,取1.3)
合理冲裁间隙值的确定:
❖ 工件断面质量无严格要求时,应取大间隙值;
❖ 工件的断面质量和制造精度较高时,应取较小间隙值;
❖ 在设计冲模刃口尺寸时,应考虑模具摩损因素,冲裁
间隙应取最小值。
6
方法1:理论确定法
如右图所示,可得冲裁间隙为:
= 2( − ℎ0 )tan = 2(1 − ℎ0 Τ)tan
能与其冲压时定位 基准重合 ,
并选择在冲裁过程中基本上下
不变动的面或线上。
9
凸、凹模刃口尺寸的计算
重要性:
冲模刃口处的尺寸及制造公差直接影响工件的尺寸
精度,合理的冲裁间隙也靠其保证。
前提:
尺寸
计算
的原
则:
因冲裁间隙的存在,落下的料和冲出的孔都带有锥
度,且落料件的大端尺寸与凹模刃口尺寸相近,冲出
模具设计第2章冲裁工艺与冲裁模课件

矩形孔:c、c′ ≥ 1.5t; 圆形孔:c、c′≥t。
在弯曲和拉深件上冲孔时
佛山科学技术学院
模
具
2.1.4 冲裁件的工艺性
设 计
冲孔时,孔径不能太小。 目的:防止凸模弯曲或折断
不带保护套凸模冲孔的最小孔径
佛山科学技术学院
模
具
2.1.4 冲裁件的工艺性
设 计
带保护套凸模冲孔的最小孔径
可稍小一些
佛山科学技术学院
佛山科学技术学院
模
具
2.1.4 冲裁件的工艺性
设 计
避免过长的悬臂与狭槽 目的:降低模具制造难度,增加模具强度。
允许的悬臂与狭槽尺寸:
有色金属和低碳钢板料: 宽度b≥1.5t,深度h≤5b。
中、高碳钢钢板:b≥2t
佛山科学技术学院
模
具
2.1.4 冲裁件的工艺性
设 计
孔间距、孔边距不能太小
目的:增加模具强度。 允许的孔间距、孔边距尺寸:
第2章 冲裁工艺与冲裁模
2.1 冲裁ห้องสมุดไป่ตู้艺设计基础
2.2 冲裁模典型结构 第2次课内容回顾
2.3 排样设计
第3次课内容回顾
2.4 冲裁工艺计算
第4次课内容回顾
2.5 冲裁模零部件设计
佛山科学技术学院
2.1 冲裁工艺设计基础
佛山科学技术学院
模
具
2.1.1 冲裁工艺
设 计
冲裁工艺概念
指利用装在压力机上的模具使板料沿着一定的轮廓形 状产生分离的一种冲压工艺。
佛山科学技术学院
2.2.2 冲裁模典型结构
单工序冲裁模 压力机一次行程中:只一个工位,完成一道工序
无导向式单工序冲裁模
在弯曲和拉深件上冲孔时
佛山科学技术学院
模
具
2.1.4 冲裁件的工艺性
设 计
冲孔时,孔径不能太小。 目的:防止凸模弯曲或折断
不带保护套凸模冲孔的最小孔径
佛山科学技术学院
模
具
2.1.4 冲裁件的工艺性
设 计
带保护套凸模冲孔的最小孔径
可稍小一些
佛山科学技术学院
佛山科学技术学院
模
具
2.1.4 冲裁件的工艺性
设 计
避免过长的悬臂与狭槽 目的:降低模具制造难度,增加模具强度。
允许的悬臂与狭槽尺寸:
有色金属和低碳钢板料: 宽度b≥1.5t,深度h≤5b。
中、高碳钢钢板:b≥2t
佛山科学技术学院
模
具
2.1.4 冲裁件的工艺性
设 计
孔间距、孔边距不能太小
目的:增加模具强度。 允许的孔间距、孔边距尺寸:
第2章 冲裁工艺与冲裁模
2.1 冲裁ห้องสมุดไป่ตู้艺设计基础
2.2 冲裁模典型结构 第2次课内容回顾
2.3 排样设计
第3次课内容回顾
2.4 冲裁工艺计算
第4次课内容回顾
2.5 冲裁模零部件设计
佛山科学技术学院
2.1 冲裁工艺设计基础
佛山科学技术学院
模
具
2.1.1 冲裁工艺
设 计
冲裁工艺概念
指利用装在压力机上的模具使板料沿着一定的轮廓形 状产生分离的一种冲压工艺。
佛山科学技术学院
2.2.2 冲裁模典型结构
单工序冲裁模 压力机一次行程中:只一个工位,完成一道工序
无导向式单工序冲裁模
冲裁工艺与冲裁模设计.ppt
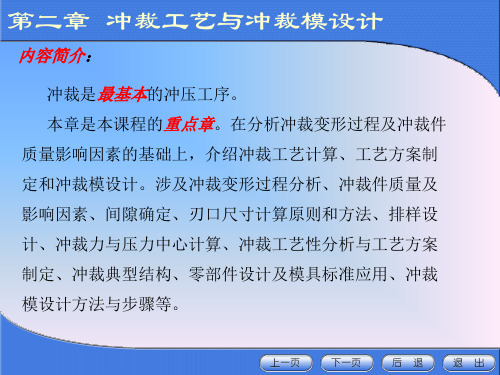
第二章 冲裁工艺与冲裁模设计
本章目录
第一节 冲裁变形机理 第二节 影响冲裁件质量的因素 第三节 凸、凹模间隙的决定 第四节 冲裁力、推件力、卸料力的计算及降低冲裁力的方法 第五节 凸、凹模刃口尺寸的计算 第六节 冲裁工作的排样 第七节 齿圈压板精密冲裁 第八节 冲裁的工艺设计 第九节 冲裁模的典型结构 第十节 冲裁模零部件设计
第十一节 冲裁模设计程序
第二章 冲裁工艺与冲裁模设计
冲裁: 利用模具使板料沿着一定的轮廓形状产生分离的一种
冲压工序。 基本工序:落料和冲孔。既可加工零件,也可加工冲 压工序件。
冲裁模: 冲裁所使用的模具叫冲裁模,它是冲裁过程必不可少
的工艺装备。凸、凹模刃口锋利,间隙小。
分类: 普通冲裁、精密冲裁
第二章 冲裁工艺与冲裁模设计
从以上各点的应力状态可以断定,凸模与凹模端面(B、 D点处)的静水压应力比侧面(A、E处)的高,且凸模刀口附 近的静水压应力又比凹模刃口附近的高,这就是裂纹首先从凹 模刃口侧面(E处)产生的原因。
第二章 冲裁工艺与冲裁模设计
3.冲裁时的F一h曲线
冲裁变形过程中冲裁力与凸 模行程关系曲线见图。图中OA段 相当于弹性变形阶段。AB段为塑 性变形阶段。切刃一旦挤入板料, 力的上升就缓慢下来。这是由于 承受力的板料面积虽然减少了, 但是材料冷作硬化的影响超过了 受剪面积减小的影响,冲载力仍 然继续上升。当硬化与受剪面积 两者影响达到相等时,冲裁力便 达到最大值。BC为裂纹扩展直至 极料断裂阶段。CD则是凸模的推 料过程。
五、剪切面周围材料性能的变化
冲裁后,剪切面周围变形区域的材料产生加工硬化,随着加工 硬化的加剧,材料的强度、硬度上升,而塑性和韧性下降。
第二章 冲裁工艺与冲裁模设计
冲裁工艺及冲裁模具的设计概述.pptx

第三节 冲压变形理论基础
四、金属塑性变形的一些基本规律
1.硬化规律 加工硬化: 塑性降低,变形抗力提高。能提高变形均匀性。
硬化曲线: 实际应力曲线或真实应力曲线。表示硬化规律。 这种变化规律可近似用指数曲线表示。 σ=Aεn
第三节 冲压变形理论基础
四、金属塑性变形的一些基本规律(续)
3.体积不变条件 金属材料在塑性变形时,体积变化很小,可以忽略不计。 一般认为金属材料在塑性变形时体积不变,可证明满足: ε1 +ε2 + ε3 = 0
第三节 冲压变形理论基础
四、金属塑性变形的一些基本规律(续)
4.最小阻力定律 在塑性变形中,破坏了金属的整体平衡而强制金属流动,当金
属质点有向几个方向移动的可能时,它向阻力最小的方向移动。
在冲压加工中,板料在变形过程中总是沿着阻力最小的方向发
展。这就是塑性变中的最小阻力定律。
弱区先变形,变形区为弱区
落料冲孔复合模
1-下模板 2-卸料螺钉 3-导柱 4-固定板 5-橡胶 6-导料销 7-落料凹模 8-推件块 9-固定板 10-导套 11-垫板 12、20-销钉 13-上模板 14-模柄 15-打杆 16、21-螺钉 17-冲孔凸模 18-凸凹模 19-卸料板 22-挡料销
圆角带(塌角)a:刃口压入时附近的材料产生弯曲和伸长变形。 光亮带b:塑性剪切变形。表面光滑,断面质量最好的区域。
决定孔或落料件的尺寸
断裂带c:裂纹形成及扩展形成的撕裂面。断面粗糙,有斜度。 毛刺区d: 由于间隙存在,裂纹产生不在刃尖,毛刺不可避
免。此外,间隙不正常、刃口不锋利,还会加大 毛刺。
垫圈的落料与冲孔 a)落料 b)冲孔
受拉,也可能受压,与间隙有关。
冲裁工艺ppt课件

2、刃口计算方法
(1)凸、凹模分开加工 即:在设计图上分别标注凸、凹模尺寸及公差
刃 口 计 算
必须同时满足下列两个条件 (1)形状简单 (2)符合δ凸+δ凹≤Zmax-Zmin 计算方法: ①落料 工件标注尺寸为(D-Δ) 先计算凹模尺寸: D凹=(D-xΔ)+δ凹 减去间隙为凸模尺寸:D凸=(D-xΔ- Zmin)-δ凸
n为凹模刃口卡住工件或废料个数
顶件力 反冲压方向从凹模中顶出工件 F顶=k顶F
(各系数K可查P57表3-8)
降低冲裁力的措施: ①.选用阶梯凸模
落料、冲孔,多孔冲制时,凸模刃口阶梯差 (0.5~1)t。
b
第 二 章 冲 裁
②.选用斜刃口模具
模具刃口做成斜面。落料时凹模为斜刃口; 冲孔时凸模为斜刃口。
③加热冲裁
冲 裁 力
2、卸料、推件力 卸料力 从凸模上卸去条料: F卸 = k 卸 F 推件力 顺冲压方向从凹模中推出工件: F推 = n k 推 F
故:先确定凹模尺寸→减去间隙为凸模尺寸。
冲孔:工件尺寸取决于凸模尺寸。
故:先确定凸模尺寸→加上间隙为凹模尺寸。
刃 口 计 算
(2)按刃口磨损规律 凹模:磨损后刃口尺寸变大。故:落料 刃口尺寸应等于或接近于工件落料最小极限 尺寸 D 。 凸模:磨损后刃口尺寸变小。故:冲孔 凸模刃口尺寸应等于或接近于工件冲孔最大 极限尺寸 d 。 无论落料或冲孔,凸、凹模磨损都使间 隙加大,故Z应取最小值Z min 。 (3)模具刃口制造公差δ 高于工件精度(Δ)2~4级; 工件一般为IT8~14,模具IT6~9; 或:取工件公差Δ的1/3~1/4 或:查表3-6,P49
(2)凸、凹模配合加工
①条件:形状复杂; 或δ凸+δ凹﹥Zmax-Zmin
冲裁及冲裁模设计(课堂PPT)

板料厚度2mm,试确定冲裁凸、 凹模的刃口尺寸及公差。
12.5 +0.24
查表(无特殊要求的一般冲孔, 落料,工件精度取IT14)
Zmax=0.24 Zmin=0.20
冲孔 p=0.02, d =0.02 ,x=0.5
落料 p=0.02, d =0.03 ,x=0.5
2021/3/29
35 -0.34
2021/3/29
1
第 2 章 冲裁
2021/3/29
2
第 2 章 冲裁
2021/3/29
3
第 2 章 冲裁工艺及冲裁模设计
▪ 冲裁:利用冲模在压力机上使板料分离的一种冲压工序。
从广义上说,是分离工序的总称,包括切断、落料、冲孔、 修边、切口等多种工序。一般来说,冲裁工艺主要是指落 料和冲孔。
a)冲孔件
b)落料件
16
第 2 章 冲裁
▪ 2 -2 冲裁模具间隙
间隙的概念 模具凸凹模刃口缝隙间的距离。 单边间隙c、双边间隙z。
间隙对冲裁件的质量、模具寿命、冲裁力都有很大 的影响,是冲裁工艺和模具设计中的最重要的工艺参数。
2.2.1 间隙对冲裁件质量的影响 2.2.2 间隙对冲裁力的影响 2.2.3 间隙对模具寿命的影响 2.2.4 间隙的确定
合理间隙 Zmin
1.理论法确定法 (P16)
Z2th0tan2t 1h t0 tan
材料厚度t越大,合理间隙值增大 材料塑性愈好,压入材料h0越大, 合理间隙值愈小。反之硬脆材料的 h0较小,合理间隙值就要大。
2021/3/29
25
第 2 章 冲裁
2.经验确定法 较小间隙值 较大间隙值
▪(a)在同样情况下,非圆形比圆形大,冲孔比落料大 ▪(b)高速冲压时,间隙应增大 ▪(c) 热冲时材料的强度低,间隙可小 ▪(d)电火花加工的模具应比机械加工方法加工的模具间隙小
冲裁工艺与冲裁模PPT课件

22
23
注意:
为保证初始间隙值小于最大合理间隙,必
须满足下列条件:
T A Zmax Zmin
T 2
或者取:
T
0.(4 Zmax
Z
)
min
A 2
A
0.(6 Zmax
Z
)
min
24
25
26
(2)凸凹模配合加工时
配合加工:先做好其中的一件为基准件,然后以此基准 件来加工另外一件,使他们之间保持一定的间隙。基准 件上标注尺寸和制造公差,另一件仅标注基本尺寸并注 明配做的间隙值。
33
⑶对基准件的尺寸进行分类(A、B、C三类)计算:
根据凸模刃口磨损情况,其尺寸变化可分为三类: ①凸模刃口磨损后,尺寸A增大,按落料凹=△/4,则:
A (60 0.5 0.74)00.74/ 4
34
②凸模刃口磨损后,尺寸B1、B2减小,按冲孔凸模类尺寸 计算。
落料件,凹模为基准件。冲孔件,凸模为基准件。
27
尺寸分类:
A类:磨损后尺寸增加 B类:磨损后尺寸减小
C类:磨损后尺寸不变
0.5
28
29
30
31
作业:
冲裁如图a所示制件,材料为A3,料厚4mm, 试用凸凹模配做法计算凸凹模的刃口尺寸及制造公差。
32
解:⑴确定基准件:此冲裁模为冲孔模,以凸模为基准件。 ⑵画出基准件的磨损图:凸模刃口磨损情况如图b所示.
t
式中: h ——凹模洞口的直刃壁高度; t ——板料厚度。
41
42
表3-7 卸料力、推件力、顶件力系数
注:卸料力系数Kx在冲孔、大搭边和轮廓复杂时取上限值。
23
注意:
为保证初始间隙值小于最大合理间隙,必
须满足下列条件:
T A Zmax Zmin
T 2
或者取:
T
0.(4 Zmax
Z
)
min
A 2
A
0.(6 Zmax
Z
)
min
24
25
26
(2)凸凹模配合加工时
配合加工:先做好其中的一件为基准件,然后以此基准 件来加工另外一件,使他们之间保持一定的间隙。基准 件上标注尺寸和制造公差,另一件仅标注基本尺寸并注 明配做的间隙值。
33
⑶对基准件的尺寸进行分类(A、B、C三类)计算:
根据凸模刃口磨损情况,其尺寸变化可分为三类: ①凸模刃口磨损后,尺寸A增大,按落料凹=△/4,则:
A (60 0.5 0.74)00.74/ 4
34
②凸模刃口磨损后,尺寸B1、B2减小,按冲孔凸模类尺寸 计算。
落料件,凹模为基准件。冲孔件,凸模为基准件。
27
尺寸分类:
A类:磨损后尺寸增加 B类:磨损后尺寸减小
C类:磨损后尺寸不变
0.5
28
29
30
31
作业:
冲裁如图a所示制件,材料为A3,料厚4mm, 试用凸凹模配做法计算凸凹模的刃口尺寸及制造公差。
32
解:⑴确定基准件:此冲裁模为冲孔模,以凸模为基准件。 ⑵画出基准件的磨损图:凸模刃口磨损情况如图b所示.
t
式中: h ——凹模洞口的直刃壁高度; t ——板料厚度。
41
42
表3-7 卸料力、推件力、顶件力系数
注:卸料力系数Kx在冲孔、大搭边和轮廓复杂时取上限值。
第二章冲裁工艺及模具设计课件
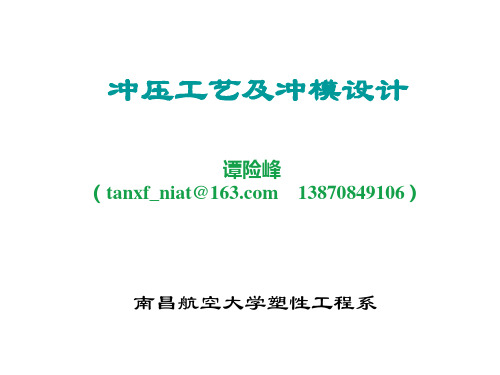
方法; ➢ 了解冲裁件的排样方法和冲裁工艺分析方法; ➢ 了解普通冲裁和精密冲裁的区别。
2021/1/10
冲裁(Blanking)工艺是利用模具使板料沿着一定的轮廓形状产生 分离的一种冲压工序。
分类:普通冲裁和精密冲裁。 通常所说的冲裁是指普通冲裁,它包括落料(Blanking)、冲孔 (Punching)、切口、剖切(Parting)、修边等(但一般所指是落料和 冲孔)。
冲压件的尺寸公差应按“入体”原则标注为单向公差,落料件上 偏
差为零,下偏差为负;冲孔件上偏差为正,下偏差为零。
2021/1/10
二、凸、凹模刃口尺寸计算方法
凸模与凹模分开加工
采用这种方法,是指凸模和凹模分别按图纸加工至尺寸; 要分别标注凸模和凹模刃口尺寸与制造公差(凸模δp、凹模δd); 它适用于圆形或简单形状的制件。 为了保证初始间隙值小于最大合理间隙Z max,必须满足下列条件:
采用大间隙值时要注意:① 为了保证制件平整,一定要有压料 与顶件装置;② 为了防止凸模将废料带出凹模表面,应在凸模上开 通气孔或装弹性顶件针。
间隙的方向:
设计落料模时,以凹模为基准,将间隙取在凸模上; 设计冲孔模时,以凸模为基准,将间隙取在凹模上。
2021/1/10
§2-3 凸模和凹模的刃口尺寸计算
35.69
0.012 0
mm
Dp
Dd Zmin
0 p
(35.69
0.04)
0 0.008
35.6500.008
mm
孔距尺寸
Ld
L
1 8
18
1 0.09 2 18 0.023 mm
8
2021/1/10
2、凸模与凹模配合加工
配合加工就是先按设计尺寸制出一个基准件(凸模或凹模),然后 根据基准件的实际尺寸再按最小合理间隙配制另一件。
2021/1/10
冲裁(Blanking)工艺是利用模具使板料沿着一定的轮廓形状产生 分离的一种冲压工序。
分类:普通冲裁和精密冲裁。 通常所说的冲裁是指普通冲裁,它包括落料(Blanking)、冲孔 (Punching)、切口、剖切(Parting)、修边等(但一般所指是落料和 冲孔)。
冲压件的尺寸公差应按“入体”原则标注为单向公差,落料件上 偏
差为零,下偏差为负;冲孔件上偏差为正,下偏差为零。
2021/1/10
二、凸、凹模刃口尺寸计算方法
凸模与凹模分开加工
采用这种方法,是指凸模和凹模分别按图纸加工至尺寸; 要分别标注凸模和凹模刃口尺寸与制造公差(凸模δp、凹模δd); 它适用于圆形或简单形状的制件。 为了保证初始间隙值小于最大合理间隙Z max,必须满足下列条件:
采用大间隙值时要注意:① 为了保证制件平整,一定要有压料 与顶件装置;② 为了防止凸模将废料带出凹模表面,应在凸模上开 通气孔或装弹性顶件针。
间隙的方向:
设计落料模时,以凹模为基准,将间隙取在凸模上; 设计冲孔模时,以凸模为基准,将间隙取在凹模上。
2021/1/10
§2-3 凸模和凹模的刃口尺寸计算
35.69
0.012 0
mm
Dp
Dd Zmin
0 p
(35.69
0.04)
0 0.008
35.6500.008
mm
孔距尺寸
Ld
L
1 8
18
1 0.09 2 18 0.023 mm
8
2021/1/10
2、凸模与凹模配合加工
配合加工就是先按设计尺寸制出一个基准件(凸模或凹模),然后 根据基准件的实际尺寸再按最小合理间隙配制另一件。
- 1、下载文档前请自行甄别文档内容的完整性,平台不提供额外的编辑、内容补充、找答案等附加服务。
- 2、"仅部分预览"的文档,不可在线预览部分如存在完整性等问题,可反馈申请退款(可完整预览的文档不适用该条件!)。
- 3、如文档侵犯您的权益,请联系客服反馈,我们会尽快为您处理(人工客服工作时间:9:00-18:30)。
为使模具有一定的使用寿命,磨损到一定程度 仍能冲裁出合格的零件,落料时凹模刃口尺寸接近 制件尺寸的下限值,冲孔时凸模刃口尺寸接近制件 尺寸的上限值。
第二章:冲裁工艺及冲裁模设计
3、考虑制件精度与模具精度之间的关系 (1)一般情况按下表执行。
(2)制件未标注公差,按以下情况处理: 非圆形件按IT14级处理,冲模按IT11级制造;圆形 件的冲模可按IT7-IT6级制造。 4、冲压件按“入体”原则进行尺寸标注 冲压件的尺寸公差应标为单向公差,落料件为轴, 上偏差为零,下偏差为负;冲孔件为孔,上偏差为 正,下偏差为零。
第二章:冲裁工艺及冲裁模设计
(2)落料 设工件的尺寸为 D0 ,则:
Dd
( Dmax
x
)
0
d
Dp
(Dd
2cmin
)
0
p
(Dmax
x 2cmin )0 p
(3)冲孔
设工件的尺寸为 d0 ,则:
d p (dmin x)0 p
dd
(d p
2cmin )0 d
(dmin
x
2cmin
)d 0
60.12 0
为IT12级,取x=0.75
3600.62 为IT14级,取x=0.5
设凸模按IT6级制造,凹模
按IT7级制造。
第二章:冲裁工艺及冲裁模设计
1、冲孔 (1)校核间隙公差条件,查公差值表得:
| p | 0.008mm,| d | 0.012mm,故有 | p | | d | 2cmax 2cmin
第二章:冲裁工艺及冲裁模设计
二、凸、凹模刃口尺寸的计算方法
(一)凸模和凹模分开加工 (1)为保证初始间隙值小于最大合理间隙, 必须满足下列条件:
| p | | d | 2cmax 2cmin
若不满足,取:
p 0.4 (2cmax 2cmin ) d 0.6 (2cmax 2cmin )
第二章:冲裁工艺及冲裁模设计
标准公差数值(摘自GB/T 1800.3—98)
第二章:冲裁工艺及冲裁模设计
第二章:冲裁工艺及冲裁模设计
第二章:冲裁工艺及冲裁模设计
一、冲裁变形时板料变形区的力学分析
模具与板料 仅在刃口附 近的狭小区 域内保持接 触。 接触宽度约 为板厚的 0.2-0.4。
第二章:冲裁工艺及冲裁模设计
二、冲裁时板料的变形过程
三个阶段: 弹性变形阶段 塑性变形阶段 断裂分离阶段
第二章:冲裁工艺及冲裁模设计
三、冲裁件的断面质量及其影响因素
1、断面特征 a:圆角带 b:光亮带 c:断裂带 d:毛刺
各部分随材料的 性能、厚度、冲 裁间隙、刃口状 态及摩擦条件不 同而不同。
第二章:冲裁工艺及冲裁模设计
第二章:冲裁工艺及冲裁模设计
(4)中心距计算 设工件的尺寸为 L ,则:
2
Ld L 0.125
X-系数,是为了使冲裁件的实际尺寸尽量 接近冲裁件公差带的中间尺寸,可按以下 选取: 当制件公差为IT10以上时,取x=1; 当制件公差为IT11-IT13时,取x=0.75; 当制件公差为IT14以下时,取x=0.5; (或按教材表2.3.1确定)
三、对冲裁工艺中力的影响
第二章:冲裁工艺及冲裁模设计
四、间隙值的确定(合理间隙值)
1、理论确定法
c
(t
h0 ) tan
t (1
h0 t
) tan
2、经验确定法
软材料:
t<1mm,c=(3%-4%)t
t<1-3mm,c=(3%-4%)t
t<3-5mm,c=(3%-4%)t
硬材料:
t<1mm,c=(4%-5%)t
0.008 0.012 0.02, 满足间隙公差条件
(2)计算冲孔凸、凹模尺寸
d p (dmin x)0 p
(6 0.75 0.12)00.008 mm 6.0900.008
dd
(d p
2cmin
)d 0
(6 0.04)00.012 mm 6.1300.012 (3)计算冲孔中心距
第二章:冲裁工艺及冲裁模设计
§2.1 §2.2 §2.3 §2.4 §2.5 §2.6 §2.7 §2.8
冲裁变形分析 冲裁模具的间隙 凸模与凹模刃口尺寸的计算 冲裁力和压力中心的计算 排样设计 冲裁模的结构设计 冲裁工艺设计 冲裁模主要零部件的结构设计与 冲模标准的选用
第二章:冲裁工艺及冲裁模设计
Ld L 0.125 (18 0.125 0.18)mm (18 0.023)mm
第二章:冲裁工艺及冲裁模设计
2、落料 (1)校核间隙公差条件,查公差值表得:
| p | 0.016mm,| d | 0.025mm,故有 | p | | d | 2cmax 2cmin
0.016 0.025 0.02,不满足间隙公差条件,故取:
| p | 0.4 (2cmax 2cmin ) 0.008 | d | 0.6 (2cmax 2cmin ) 0.012
(2)计算落料凸、凹模尺寸
Dd (dmax x)0d (36 0.5 0.62)00.012 mm 35.6900.012 Dp (Dd 2cmin )0 p
t<1-3mm,c=(6%-8%)t
t<3-5mm,c=(8%-13%)t
3、查表确定法(表2.2.3)
第二章:冲裁工艺及冲裁模设计
一、刃口尺寸计算的原则
1、考虑落料和冲孔的特点 落料件尺寸决定于凹模刃口尺寸;冲孔
件尺寸决定于凸模刃口尺寸。
2、考虑刃口的磨损规律 刃口磨损后,凹模刃
口尺寸扩大,凸模刃口尺 寸减小。
2、影响因素 (1)材料性能对断面质量的影响 (2)模具冲裁间隙对断面质量的影响 (3)模具刃口状态对断面质量的影响
第二章:冲裁工艺及冲裁模设计
一、间隙对冲裁件尺寸精度的影响
间隙过大时,冲孔件尺寸增大,落料件尺 寸减小。 间隙过小时,冲孔件 尺寸减小,落料件尺 寸增大。
二、对模具寿命的影响
间隙过小时,摩擦增大,磨损严重。 间隙过大时,摩擦减小,放宽间隙不均匀的 不利影响,从而利于提高模具寿命。
第二章:冲裁工艺及冲裁模设计
例1:如图所示零件的材料为Q235,料厚 t=0.5mm。试求凸、凹模刃口尺寸及公差。
解:该件φ36由落料得到, 2-φ6及18由冲孔得到。 查表2.2.3,得:2cmin=0.04mm,2cmax=0.06mm 则:2cmin-2cmax=0.02mm 由公差表查得:
第二章:冲裁工艺及冲裁模设计
3、考虑制件精度与模具精度之间的关系 (1)一般情况按下表执行。
(2)制件未标注公差,按以下情况处理: 非圆形件按IT14级处理,冲模按IT11级制造;圆形 件的冲模可按IT7-IT6级制造。 4、冲压件按“入体”原则进行尺寸标注 冲压件的尺寸公差应标为单向公差,落料件为轴, 上偏差为零,下偏差为负;冲孔件为孔,上偏差为 正,下偏差为零。
第二章:冲裁工艺及冲裁模设计
(2)落料 设工件的尺寸为 D0 ,则:
Dd
( Dmax
x
)
0
d
Dp
(Dd
2cmin
)
0
p
(Dmax
x 2cmin )0 p
(3)冲孔
设工件的尺寸为 d0 ,则:
d p (dmin x)0 p
dd
(d p
2cmin )0 d
(dmin
x
2cmin
)d 0
60.12 0
为IT12级,取x=0.75
3600.62 为IT14级,取x=0.5
设凸模按IT6级制造,凹模
按IT7级制造。
第二章:冲裁工艺及冲裁模设计
1、冲孔 (1)校核间隙公差条件,查公差值表得:
| p | 0.008mm,| d | 0.012mm,故有 | p | | d | 2cmax 2cmin
第二章:冲裁工艺及冲裁模设计
二、凸、凹模刃口尺寸的计算方法
(一)凸模和凹模分开加工 (1)为保证初始间隙值小于最大合理间隙, 必须满足下列条件:
| p | | d | 2cmax 2cmin
若不满足,取:
p 0.4 (2cmax 2cmin ) d 0.6 (2cmax 2cmin )
第二章:冲裁工艺及冲裁模设计
标准公差数值(摘自GB/T 1800.3—98)
第二章:冲裁工艺及冲裁模设计
第二章:冲裁工艺及冲裁模设计
第二章:冲裁工艺及冲裁模设计
一、冲裁变形时板料变形区的力学分析
模具与板料 仅在刃口附 近的狭小区 域内保持接 触。 接触宽度约 为板厚的 0.2-0.4。
第二章:冲裁工艺及冲裁模设计
二、冲裁时板料的变形过程
三个阶段: 弹性变形阶段 塑性变形阶段 断裂分离阶段
第二章:冲裁工艺及冲裁模设计
三、冲裁件的断面质量及其影响因素
1、断面特征 a:圆角带 b:光亮带 c:断裂带 d:毛刺
各部分随材料的 性能、厚度、冲 裁间隙、刃口状 态及摩擦条件不 同而不同。
第二章:冲裁工艺及冲裁模设计
第二章:冲裁工艺及冲裁模设计
(4)中心距计算 设工件的尺寸为 L ,则:
2
Ld L 0.125
X-系数,是为了使冲裁件的实际尺寸尽量 接近冲裁件公差带的中间尺寸,可按以下 选取: 当制件公差为IT10以上时,取x=1; 当制件公差为IT11-IT13时,取x=0.75; 当制件公差为IT14以下时,取x=0.5; (或按教材表2.3.1确定)
三、对冲裁工艺中力的影响
第二章:冲裁工艺及冲裁模设计
四、间隙值的确定(合理间隙值)
1、理论确定法
c
(t
h0 ) tan
t (1
h0 t
) tan
2、经验确定法
软材料:
t<1mm,c=(3%-4%)t
t<1-3mm,c=(3%-4%)t
t<3-5mm,c=(3%-4%)t
硬材料:
t<1mm,c=(4%-5%)t
0.008 0.012 0.02, 满足间隙公差条件
(2)计算冲孔凸、凹模尺寸
d p (dmin x)0 p
(6 0.75 0.12)00.008 mm 6.0900.008
dd
(d p
2cmin
)d 0
(6 0.04)00.012 mm 6.1300.012 (3)计算冲孔中心距
第二章:冲裁工艺及冲裁模设计
§2.1 §2.2 §2.3 §2.4 §2.5 §2.6 §2.7 §2.8
冲裁变形分析 冲裁模具的间隙 凸模与凹模刃口尺寸的计算 冲裁力和压力中心的计算 排样设计 冲裁模的结构设计 冲裁工艺设计 冲裁模主要零部件的结构设计与 冲模标准的选用
第二章:冲裁工艺及冲裁模设计
Ld L 0.125 (18 0.125 0.18)mm (18 0.023)mm
第二章:冲裁工艺及冲裁模设计
2、落料 (1)校核间隙公差条件,查公差值表得:
| p | 0.016mm,| d | 0.025mm,故有 | p | | d | 2cmax 2cmin
0.016 0.025 0.02,不满足间隙公差条件,故取:
| p | 0.4 (2cmax 2cmin ) 0.008 | d | 0.6 (2cmax 2cmin ) 0.012
(2)计算落料凸、凹模尺寸
Dd (dmax x)0d (36 0.5 0.62)00.012 mm 35.6900.012 Dp (Dd 2cmin )0 p
t<1-3mm,c=(6%-8%)t
t<3-5mm,c=(8%-13%)t
3、查表确定法(表2.2.3)
第二章:冲裁工艺及冲裁模设计
一、刃口尺寸计算的原则
1、考虑落料和冲孔的特点 落料件尺寸决定于凹模刃口尺寸;冲孔
件尺寸决定于凸模刃口尺寸。
2、考虑刃口的磨损规律 刃口磨损后,凹模刃
口尺寸扩大,凸模刃口尺 寸减小。
2、影响因素 (1)材料性能对断面质量的影响 (2)模具冲裁间隙对断面质量的影响 (3)模具刃口状态对断面质量的影响
第二章:冲裁工艺及冲裁模设计
一、间隙对冲裁件尺寸精度的影响
间隙过大时,冲孔件尺寸增大,落料件尺 寸减小。 间隙过小时,冲孔件 尺寸减小,落料件尺 寸增大。
二、对模具寿命的影响
间隙过小时,摩擦增大,磨损严重。 间隙过大时,摩擦减小,放宽间隙不均匀的 不利影响,从而利于提高模具寿命。
第二章:冲裁工艺及冲裁模设计
例1:如图所示零件的材料为Q235,料厚 t=0.5mm。试求凸、凹模刃口尺寸及公差。
解:该件φ36由落料得到, 2-φ6及18由冲孔得到。 查表2.2.3,得:2cmin=0.04mm,2cmax=0.06mm 则:2cmin-2cmax=0.02mm 由公差表查得: