焦炉煤气变压吸附制氢新工艺的开发与应用
变压吸附提氢技术在制备燃料电池氢过程中的应用
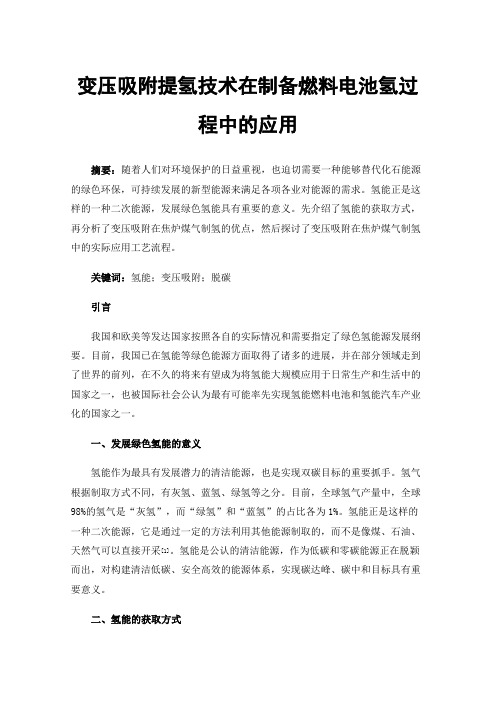
变压吸附提氢技术在制备燃料电池氢过程中的应用摘要:随着人们对环境保护的日益重视,也迫切需要一种能够替代化石能源的绿色环保,可持续发展的新型能源来满足各项各业对能源的需求。
氢能正是这样的一种二次能源,发展绿色氢能具有重要的意义。
先介绍了氢能的获取方式,再分析了变压吸附在焦炉煤气制氢的优点,然后探讨了变压吸附在焦炉煤气制氢中的实际应用工艺流程。
关键词:氢能;变压吸附;脱碳引言我国和欧美等发达国家按照各自的实际情况和需要指定了绿色氢能源发展纲要。
目前,我国已在氢能等绿色能源方面取得了诸多的进展,并在部分领域走到了世界的前列,在不久的将来有望成为将氢能大规模应用于日常生产和生活中的国家之一,也被国际社会公认为最有可能率先实现氢能燃料电池和氢能汽车产业化的国家之一。
一、发展绿色氢能的意义氢能作为最具有发展潜力的清洁能源,也是实现双碳目标的重要抓手。
氢气根据制取方式不同,有灰氢、蓝氢、绿氢等之分。
目前,全球氢气产量中,全球98%的氢气是“灰氢”,而“绿氢”和“蓝氢”的占比各为1%。
氢能正是这样的一种二次能源,它是通过一定的方法利用其他能源制取的,而不是像煤、石油、天然气可以直接开采[1]。
氢能是公认的清洁能源,作为低碳和零碳能源正在脱颖而出,对构建清洁低碳、安全高效的能源体系,实现碳达峰、碳中和目标具有重要意义。
二、氢能的获取方式灰氢是通过化石燃料(例如石油、天然气、煤)燃烧制取的氢气,碳排放量最高;蓝氢是在灰氢的基础上,应用碳捕捉、碳封存技术,实现低碳制氢;绿氢是通过光伏发电、风电以及太阳能等可再生能源电解水制氢,制氢过程中基本不会产生温室气体,因此被称为“零碳氢气”。
长期来看,绿氢是方向,而蓝氢主要体现资源的综合利用。
氢能的制备主要有以下途径:1、电解水制氢最清洁、最可持续的制氢方式,并将成为燃料电池发展中最具潜力的制氢方法之一。
但是目前电解水制氢受制于较高的成本而难以大规模运用,短时间内暂时无法通过电解水获得大量高纯度氢气的工业化装置。
焦炉煤气变压吸附制氢工艺技术应用评述

采 用 5 —2 P 艺 , 附压 力 1 7 a 原 料 气 处 —2 / I 吸 . MP ,
来 自焦 炉煤 气压缩 机 一级 出 口的原料 气进 入精
脱 萘塔 继 续脱 萘 , 后 返 回焦 炉煤 气压 缩机 进行 二 然 级压 缩 和三级压 缩 , 将原 料气压缩 至 1 7 a . MP 进入 除
4 1 10 . 0 号脱 萘脱 硫工 序
2 0 压缩及 预处理 工序 ;0 号 变压吸 附提 氢工 序 ; 0号 30
4 0 脱氧干 燥工 序 。 0号
原 料焦 炉煤 气首先 进入脱 萘塔脱 除焦 炉煤气 中
的萘 。 台脱 萘塔 可采 用 串并 联运行 方式 , 两 当一 台脱
3 生 产 方 法
行 再 生后 , 接 输 出到 界外 , 为 副产 品 , 吸气 的 直 作 解 输 出压 力为 0 0 MP 。 . 2 a
油器 和 预处理 器 , 出煤 气 中剩 余 的HS、 和高 烃 脱 苯
类物质 。 43 30 . 0 号变 压吸 附 ( S 工 序 P A) 经 20 0 号预 处理 后的 焦炉煤 气进入 3 0 变压 吸 0号 附 ( S 工 序 , 此 工序 内焦 炉煤 气 中 的C C P A) 在 O、 O 、 C N 等 杂质 被 除去 , 产 出纯度 大于9 . 的半 H 、 生 96
吸气
氢气
!… L. .
!
… … … … … … … _ . … . — . … — . … … … … … … … .: . .
界
区
线 Βιβλιοθήκη 图 l 5 0 m。h 炉煤 气 制 氢装 置 工 艺 流 程图 0N /焦
焦炉煤气制取氢气技术在工业中的应用
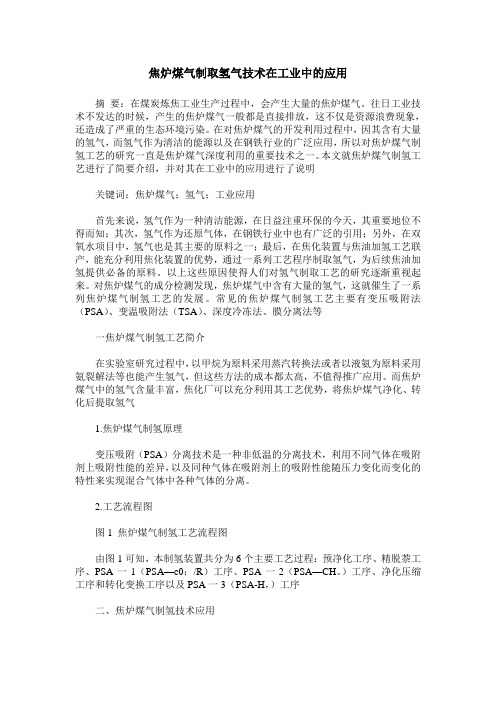
焦炉煤气制取氢气技术在工业中的应用摘要:在煤炭炼焦工业生产过程中,会产生大量的焦炉煤气。
往日工业技术不发达的时候,产生的焦炉煤气一般都是直接排放,这不仅是资源浪费现象,还造成了严重的生态环境污染。
在对焦炉煤气的开发利用过程中,因其含有大量的氢气,而氢气作为清洁的能源以及在钢铁行业的广泛应用,所以对焦炉煤气制氢工艺的研究一直是焦炉煤气深度利用的重要技术之一。
本文就焦炉煤气制氢工艺进行了简要介绍,并对其在工业中的应用进行了说明关键词:焦炉煤气;氢气;工业应用首先来说,氢气作为一种清洁能源,在日益注重环保的今天,其重要地位不得而知;其次,氢气作为还原气体,在钢铁行业中也有广泛的引用;另外,在双氧水项目中,氢气也是其主要的原料之一;最后,在焦化装置与焦油加氢工艺联产,能充分利用焦化装置的优势,通过一系列工艺程序制取氢气,为后续焦油加氢提供必备的原料。
以上这些原因使得人们对氢气制取工艺的研究逐渐重视起来。
对焦炉煤气的成分检测发现,焦炉煤气中含有大量的氢气,这就催生了一系列焦炉煤气制氢工艺的发展。
常见的焦炉煤气制氢工艺主要有变压吸附法(PSA)、变温吸附法(TSA)、深度冷冻法、膜分离法等一焦炉煤气制氢工艺简介在实验室研究过程中,以甲烷为原料采用蒸汽转换法或者以液氨为原料采用氨裂解法等也能产生氢气,但这些方法的成本都太高,不值得推广应用。
而焦炉煤气中的氢气含量丰富,焦化厂可以充分利用其工艺优势,将焦炉煤气净化、转化后提取氢气1.焦炉煤气制氢原理变压吸附(PSA)分离技术是一种非低温的分离技术,利用不同气体在吸附剂上吸附性能的差异,以及同种气体在吸附剂上的吸附性能随压力变化而变化的特性来实现混合气体中各种气体的分离。
2.工艺流程图图1 焦炉煤气制氢工艺流程图由图1可知,本制氢装置共分为6个主要工艺过程:预净化工序、精脱萘工序、PSA一1(PSA—c0:/R)工序、PSA一2(PSA—CH。
)工序、净化压缩工序和转化变换工序以及PSA一3(PSA-H,)工序二、焦炉煤气制氢技术应用1.变压吸附法及其应用目前工业上广泛使用变压吸附法(PsA)提取氢气,流程如图1所示。
浅谈焦炉煤气制氢工艺

浅谈焦炉煤气制氢工艺焦炉煤气是焦炭生产过程中煤炭在高温、缓慢干馏过程中产生的一种可燃性气体。
我国是焦炭产量最大的国家,2023年我国焦炭产量43142.6万t,依此计算,我国焦炉煤气产量是非常高的。
全国焦炭产能约有1/3在钢铁联合企业,2/3在独立焦化企业。
独立焦化企业富余的焦炉气曾因无法直接用于生产而被大量放散,放散量最高峰时曾达30km³/a。
焦炉煤气自2023年1月1日起实施的《焦化行业准入条件》修订版规定,焦化生产企业生产的焦炉煤气应全部回收利用,不得放散。
这给焦炉煤气的综合利用提供了有利的政策支持,也进一步推动了焦炉煤气制氢、甲醇等工业技术的发展。
炼焦过程中释放的焦炉煤气中富含氢气(55%左右),焦炉煤气制氢是目前可实现的大规模低成本高效率获得工业氢气的重要途径。
而我国晋、冀、豫几省是资源大省和焦化大省,氢源非常丰富,如何高效、合理地利用是关系环保、资源综合利用和节能减排的重大课题。
1、焦炉煤气制氢原理焦炉煤气制氢工序主要有:脱硫脱萘、压缩预处理、变压吸附制氢、脱氧干燥等。
其中焦炉煤气预处理系统为变温吸附(TSA),制氢系统为变压吸附(PSA),而氢气精制系统也为变温吸附(TSA),可用焦炉煤气制取99.999%的氢气。
吸附剂在常温高压下大量吸附原料气中除氢以外的杂质组分,然后降解杂质的分压使各种杂质得以解吸。
在实际应用中一般依据气源的组成、压力及产品要求的不同来选择组合工艺。
变温吸附的循环周期长、投资较大,但再生彻底,通常用于微量杂质或难解吸杂质的净化;变压吸附的循环周期短,吸附剂利用率高,用量相对较少,不需要外加换热设备,广泛用于大气量、多组分气体的分离和提纯。
由于焦炉煤气提纯氢气的特点是:原料压力低,原料组分复杂并含有焦油、萘、硫、重烃等难以解吸的重组分,产品纯度要求高。
因而装置需采用“加压+TSA预处理+PSA氢提纯+脱氧+TSA干燥”流程。
2、主要生产过程焦炉煤气是炼焦的副产品,产率和组成因炼焦煤质量和焦化过程不同而有所差别,一般每吨干煤可生产焦炉煤气300~350m³(标准状态)。
焦炉煤气变压吸附制氢新工艺_宁红军

体积分数 /% 55 . 5 0. 43 8 . 1 5. 86 2 . 86 23. 68 3. 2 0. 31
组成
m g/Nm
HCN
ቤተ መጻሕፍቲ ባይዱ
193
3 000 ~ 4 000
100 ~ 400
- 6
0 . 21 4 000~ 5 000
注 : NH 3 含 量为 ( 50 ~ 100) 10 。
- 6
10 , NO 含 量 为 1 . 6
48
河南化工 HENAN CH EM ICAL I NDU STRY
2007 年
第 24 卷
焦炉煤气变压吸附制氢新工艺
宁红军 , 赵新亮 , 曹晓宝
(平顶山市三源制氢有限公司 , 河南 平顶山 467001 )
摘
要 : 变压吸附制氢气体分离技术在工业上得到 了广泛 应用 , 已逐步 成为一 种主要 的气体 分离技术 。 本文重 点
介绍变 压吸附技术在焦炉煤气制氢新工艺上的开发与利用 , 并 对变压吸附技术在焦炉煤气实际应用作详细说明 。 关键词 : 变压吸附 ( PSA 法 ) ; 压缩 ; 冷冻 ; 二段分离 中图分 类号 : TQ 116. 23 文献标识码 : B 文章编 号 : 1003- 3467( 2007) 11- 0048- 03
图 1 制氢装置工艺流程图
本装置工艺流程分为 5 个工序: 原料气压缩工 序 ( 简 称 100 工序 ); 冷冻净 化分离 ( 简称 200 工 序 ) ; PSA- C /R 工序及精脱硫 ( 简称 300 工序 ); 半 产品气压缩 (简称 400 工序 ) ; PSA - H 2 工序及脱氧 (简称 500 工序 )。 本装置所用原料气是 来自焦化公司的焦炉煤 气, 主要用于锅炉、 化工产品原料气及城市煤气; 因 净化难度高, 故气体质量较差 , 分离等级较低, 因此 杂质的净化分离均以该公司使用的这套工艺装置实 现的。原料煤气组分数据见下页表 1 。
焦炉煤气制氢新工艺

焦炉煤气变压吸附制氢新工艺的开发与应用焦炉煤气变压吸附(PSA)制氢工艺利用焦化公司富余放散的焦炉煤气,从杂质极多、难提纯的气体中长周期、稳定、连续地提取纯氢,不仅解决了焦化公司富余煤气放散燃烧对大气的污染问题;而且还减少了大量焦炭能源的耗用及废水、废气、废渣的排污问题;是一个综合利用、变废为宝的环保型项目;同时也是一个低投入、高产出、多方受益的科技创新项目。
该装置首次采用先进可靠的新工艺,其经济效益、社会效益可观,对推进国内PSA技术进步也有重大意义。
1942年德国发表了第一篇无热吸附净化空气的文献、20世纪60年代初,美国联合碳化物(Union Carbide)公司首次实现了变压吸附四床工艺技术工业化,进入20世纪70年代后,变压吸附技术获得了迅速的发展。
装置数量剧增,装置规模不断扩大,使用范围越来越广,主要应用于石油化工、冶金、轻工及环保等领域。
本套大规模、低成木提纯氢气装罝,是用难以净化的焦炉煤气为原料,国内还没有同类型的装置,并且走在了世界同行业的前列。
1、焦炉煤气PSA制氢新工艺。
传统的焦炉煤气制氢工艺按照正常的净化分离步骤是:焦炉煤气首先经过焦化系统的预处理,脱除大部分烃类物质;经初步净化后的原料气再经过湿法脱硫、干法脱萘、压缩机、精脱萘、精脱硫和变温吸附(TSA)系统,最后利用PSA制氢工艺提纯氢气,整个系统设备投资大、工业处理难度大、环境污染严重、操作不易控制、生产成本高、废物排放量大,因此用焦炉煤气PSA制氢在某种程度上受到一定的限制,所以没有被大规模的应用到工业生产当中。
本装置釆用的生产工艺是目前国内焦炉煤气PSA制氢工艺中较先进的生产工艺,它生产成本低、效率高,能解决焦炉煤气制氢过程中杂质难分离的问题,从而推动了焦炉煤气PSA制氢的发展。
该工艺的特点是:焦炉煤气压缩采用分步压缩法、冷冻净化及二段脱硫法等新工艺技术。
1.1工艺流程。
PSA制氢新工艺如图1所示。
该裝罝工艺流程分为5个工序:A、原料气压缩工序(简称100#工序),B、冷冻净化分离(简称200#工序),C、PSA-C/R工序及精脱硫工序(简称300#工序),D、半成品气压缩(简称400#工序)E、PSA-H2工序及脱氧工序(简称500#工序)。
焦炉煤气变压吸附制氢新工艺的开发与应用
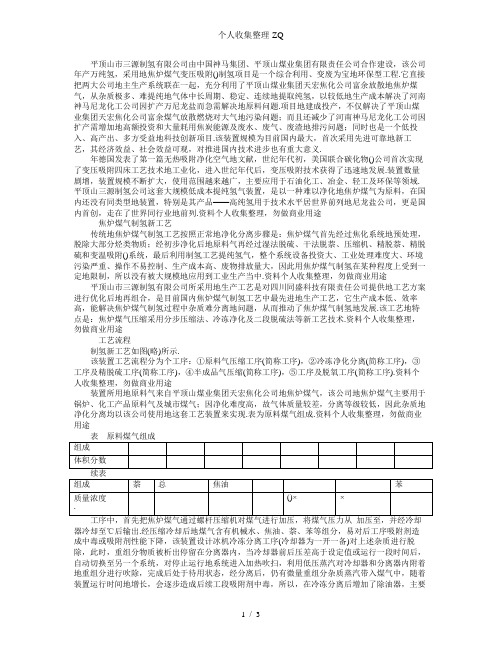
平顶山市三源制氢有限公司由中国神马集团、平顶山煤业集团有限责任公司合作建设,该公司年产万纯氢,采用地焦炉煤气变压吸附()制氢项目是一个综合利用、变废为宝地环保型工程.它直接把两大公司地主生产系统联在一起,充分利用了平顶山煤业集团天宏焦化公司富余放散地焦炉煤气,从杂质极多、难提纯地气体中长周期、稳定、连续地提取纯氢,以较低地生产成本解决了河南神马尼龙化工公司因扩产万尼龙盐而急需解决地原料问题.项目地建成投产,不仅解决了平顶山煤业集团天宏焦化公司富余煤气放散燃烧对大气地污染问题;而且还减少了河南神马尼龙化工公司因扩产需增加地高额投资和大量耗用焦炭能源及废水、废气、废渣地排污问题;同时也是一个低投入、高产出、多方受益地科技创新项目.该装置规模为目前国内最大,首次采用先进可靠地新工艺,其经济效益、社会效益可观,对推进国内技术进步也有重大意义.年德国发表了第一篇无热吸附净化空气地文献,世纪年代初,美国联合碳化物()公司首次实现了变压吸附四床工艺技术地工业化,进入世纪年代后,变压吸附技术获得了迅速地发展.装置数量剧增,装置规模不断扩大,使用范围越来越广,主要应用于石油化工、冶金、轻工及环保等领域.平顶山三源制氢公司这套大规模低成本提纯氢气装置,是以一种难以净化地焦炉煤气为原料,在国内还没有同类型地装置,特别是其产品——高纯氢用于技术水平居世界前列地尼龙盐公司,更是国内首创,走在了世界同行业地前列.资料个人收集整理,勿做商业用途焦炉煤气制氢新工艺传统地焦炉煤气制氢工艺按照正常地净化分离步骤是:焦炉煤气首先经过焦化系统地预处理,脱除大部分烃类物质;经初步净化后地原料气再经过湿法脱硫、干法脱萘、压缩机、精脱萘、精脱硫和变温吸附()系统,最后利用制氢工艺提纯氢气,整个系统设备投资大、工业处理难度大、环境污染严重、操作不易控制、生产成本高、废物排放量大,因此用焦炉煤气制氢在某种程度上受到一定地限制,所以没有被大规模地应用到工业生产当中.资料个人收集整理,勿做商业用途平顶山市三源制氢有限公司所采用地生产工艺是对四川同盛科技有限责任公司提供地工艺方案进行优化后地再组合,是目前国内焦炉煤气制氢工艺中最先进地生产工艺,它生产成本低、效率高,能解决焦炉煤气制氢过程中杂质难分离地问题,从而推动了焦炉煤气制氢地发展.该工艺地特点是:焦炉煤气压缩采用分步压缩法、冷冻净化及二段脱硫法等新工艺技术.资料个人收集整理,勿做商业用途工艺流程制氢新工艺如图(略)所示.该装置工艺流程分为个工序:①原料气压缩工序(简称工序),②冷冻净化分离(简称工序),③工序及精脱硫工序(简称工序),④半成品气压缩(简称工序),⑤工序及脱氧工序(简称工序).资料个人收集整理,勿做商业用途装置所用地原料气来自平顶山煤业集团天宏焦化公司地焦炉煤气,该公司地焦炉煤气主要用于锅炉、化工产品原料气及城市煤气;因净化难度高,故气体质量较差,分离等级较低,因此杂质地净化分离均以该公司使用地这套工艺装置来实现.表为原料煤气组成.资料个人收集整理,勿做商业用途表原料煤气组成组成体积分数续表组成萘总焦油苯()××质量浓度·工序中,首先把焦炉煤气通过螺杆压缩机对煤气进行加压,将煤气压力从加压至,并经冷却器冷却至℃后输出.经压缩冷却后地煤气含有机械水、焦油、萘、苯等组分,易对后工序吸附剂造成中毒或吸附剂性能下降,该装置设计冰机冷冻分离工序(冷却器为一开一备)对上述杂质进行脱除,此时,重组分物质被析出停留在分离器内,当冷却器前后压差高于设定值或运行一段时间后,自动切换至另一个系统,对停止运行地系统进入加热吹扫,利用低压蒸汽对冷却器和分离器内附着地重组分进行吹除,完成后处于待用状态,经分离后,仍有微量重组分杂质蒸汽带入煤气中,随着装置运行时间地增长,会逐步造成后续工段吸附剂中毒,所以,在冷冻分离后增加了除油器,主要是精脱重组分及水蒸气.煤气进入工序,该工序地主要目地是脱除煤气中强吸附组分、、、、、、有机硫以及大部分、、等;经过工序后地半成品气已得到净化,对压缩机工作条件要求较低,采用一级活塞式压缩工艺,将半成品气从压缩至,再进入工序(在和提氢工序之间设有脱氧工序,是因为经脱氧反应后会生成水分,传统工艺需要等压干燥脱水系统,该系统选用地二段法新工艺不仅节约了投资,而且降低了操作运行费用).工序在传统地制氢工艺中是整套装置地核心部分,而在本装置工艺中只是作为对氢气地提纯,即从上道工序中经脱碳后得到氢体积分数为地原料气,再提纯到后作为商品氢出售.资料个人收集整理,勿做商业用途工艺方案地选择焦炉煤气压缩采用螺杆式压缩机焦炉煤气地压缩国内传统工艺流程中几乎均采用活塞式压缩机.而该公司根据对制氢工艺新技术地掌握,针对原料气地特点,在焦炉煤气压缩地问题上,经多方论证后,确定采用分步压缩方案,即低压段采用螺杆压缩机,脱除杂质组分后,再用活塞式压缩机升压,这种低压段大气量将焦炉煤气压缩到地螺杆压缩机在国内尚属首次使用.资料个人收集整理,勿做商业用途采用螺杆压缩机压缩焦炉煤气最大地优点是:螺杆机结构简单、运行时间长,可以保证装置长周期安全稳定运行,对原料气烃类杂质含量要求不高,无需备用压缩机.与活塞式压缩机相比,无需维修频繁堵塞地气阀(原料气中焦油及萘含量较高,故需经常停车更换气阀内件),维修工作量几乎为零.而传统地往复式压缩机辅助设备多、检修频率高,若用于焦炉煤气压缩,气阀更易堵塞,维修工作量大,还需要备用压缩机.资料个人收集整理,勿做商业用途该工艺地另一主要优势是采用了柴油喷淋冷却工艺,出口温度控制在℃左右,在该温度下,焦炉煤气中地轻质焦油、萘等大分子烃类大部分溶解在柴油中(回收地焦油、萘等烃类物质进行集中处理),但经过冷却器降温至℃时,焦炉煤气中地萘要结晶析出,为此笔者又完善了使用柴油喷淋循环冷却地工艺,这样既能保证管道畅通、又能保证冷却效果,这也是该工艺地独到之处.资料个人收集整理,勿做商业用途从投资地角度而言,原料气螺杆压缩机和半成品活塞式压缩机总购置费用不超过万元,比目前国内同类装置采用台活塞式压缩机(其中台备用)节省投资约万元.资料个人收集整理,勿做商业用途原料气预处理系统采用净化分离工艺焦炉煤气制氢国内同类装置原料气均采用活塞式压缩机,原料气在进入活塞式压缩机之前必须将萘、苯、焦油等重组分杂质脱除,以保证活塞式压缩机地正常工作,整个工艺气地处理需经过脱硫、脱萘、脱苯、除氨等预处理工艺及电捕焦油器、风机等附属设备,而该装置在螺杆压缩机后首次采用了冰机冷冻分离工艺,可以将原料气中大部分高碳烃类、苯、萘等重组分杂质在低温下脱除,从而大大降低了原料气预处理系统地投资和运行成本.资料个人收集整理,勿做商业用途如果从原料气预处理系统地投资和运行成本分析,冷冻净化工艺则比传统工艺投资方面减少约万元,运行成本节约万元.资料个人收集整理,勿做商业用途原料气脱硫采用技术原料气经该装置冷冻净化工艺后,还含有质量浓度地硫无法在此工段中脱除(硫含量取决于所选焦煤地煤质),因此,原料气脱硫问题则是该装置地关键流程.资料个人收集整理,勿做商业用途传统地脱硫方法有:()干法脱硫.采用氧化铁干法脱硫,其优点是一次性投资较小,但缺点是运行成本非常高,易造成长期地二次污染.资料个人收集整理,勿做商业用途()湿法脱硫.如等传统脱硫方法.湿法脱硫具有安全可靠,运行稳定、运行费用低于干法脱硫等优点.但是,湿法脱硫地缺点也很明显,那就是装置投资高、设备腐蚀严重、环境污染大,对有机硫几乎没有脱除效果,而对于变压吸附工艺地吸附剂,危害最大地就是有机硫,它会造成吸附剂寿命减少或失活,影响吸附效果,从而影响了产品氢气质量.另外,经脱硫后产生地硫渣及含硫废水易造成二次污染.资料个人收集整理,勿做商业用途该装置采用目前最先进地,并且是非常成熟地两段法吸附技术,即把脱碳和制氢种工艺合二为一,取长补短.结合焦化公司对解析气中硫含量要求不高地实际情况(因焦炉煤气中硫含量地波动较大,从本装置分离出地解吸气占平顶山煤业集团煤气总量地比例较小,且解吸气热值高出焦炉煤气,并经过多级净化,用途广泛),从根本上解决了有机硫处理地难题.该装置第一段采用脱碳技术,可以大幅度脱除原料气中有机硫、无机硫、、等杂质组分,使氢气体积分数达到以上,同时将原料气中地总硫质量浓度从脱除到以下,然后进入下段制氢工序,由于专用耐硫吸附剂对硫地解吸性能非常好,可以循环使用(与地吸附解吸性能接近),同时也保证了脱碳吸附剂使用寿命可以达到年以上,第二段制氢吸附剂使用寿命更长,可以达到年以上.资料个人收集整理,勿做商业用途两段法提高氢气回收率传统制氢工艺中氢气回收率只有,而该装置选用地工艺技术可将氢气回收率提高到以上,从这套装置来讲,解吸气全部返回到煤气管网,因此,从表面上讲,氢气回收率似乎并不重要,但氢气回收率低,则会增加原料气量,不仅仅会增加压缩功耗,同时也增大了装置对杂质组分地处理量,导致装置运行费用增大,氢气成本增高.因此,努力提高氢气回收率是降低氢气成本,提高经济效益地有效手段.资料个人收集整理,勿做商业用途该装置推荐采用目前最先进地两段法吸附技术是提高氢气回收率地最佳方案.将二段制氢地逆放废气回收作为本装置地升压气;将二段制氢地解吸气用于一段脱碳地冲洗气;将一段脱碳地逆放气和抽空解吸气作为除油器和系统地冷吹气和再生气使用,最后全部返回解吸气管网.资料个人收集整理,勿做商业用途从投资角度讲,该装置由于采用了两段法吸附技术,使主装置总投资由万元降低到万元.脱氧系统无需干燥设备在国内已经运行地制氢装置中,凡是对产品氢中含量有要求者,几乎无一例外,均设计了一套钯催化剂等压干燥系统,其原因是和地分离系数较小,仅仅通过很难达到产品氢气对微量杂质含量地严格要求(一般均要求体积分数小于×).资料个人收集整理,勿做商业用途在预留地脱氧系统中,取消了干燥系统.主要是因为如果产品气中要求体积分数≤×,则脱氧系统放在二段后面,不需要干燥系统;如果产品气中要求体积分数≤×,则脱氧系统放在和二段之间,同样不需要干燥系统.资料个人收集整理,勿做商业用途不足之处及整改措施()在对冷凝系统及除油器进行蒸汽再生时,其再生蒸汽导淋插入高低位水池(系统伴热导淋和脱氧器导淋也排入池内),系统再生废热直接进入水池,致使池内废油液位被不断加热至局部沸腾.池内含大量地苯,苯被挥发出去(苯、萘沸点约为℃)而导致周围环境受到污染.资料个人收集整理,勿做商业用途()制冷机组冰机制冷量不够.从目前冬季运行情况来看,环境温度较低,而且生产处于半负荷状态,暂时可以满足生产,夏季高负荷生产时可能达不到预期地制冷效果.资料个人收集整理,勿做商业用途()水质问题,该公司使用地水是焦化公司提供地二次水,某些指标达不到工业用水地要求,而且循环水冷却塔所处位置距煤加工场太近,易带人大量粉尘,会造成水质严重污染.资料个人收集整理,勿做商业用途该公司准备增加一套苯、萘回收装置,以解决环境污染问题;增加一台制冷量较大地冰机和强制性风冷塔.装置运行情况该装置自年月日运行至今,在试生产过程中,工艺、设备、仪表、电气等方面虽然也出现了不少问题,但整个运行情况是稳定地,没有出现大地缺陷.装置投产以来大大缓解了河南神马尼龙化工公司对氢气地需求,同时也充分利用了天宏焦化公司地焦炉煤气资源,是一个多方收益地工程.资料个人收集整理,勿做商业用途。
硕士论文-焦炉煤气变压吸附制氢装置的设计及流程改进

(3)处理范围大,能从 ι100'l也调节装置处理影响装置工作及产品纯度.它启动方
便,除首次开车需要调整、建立各操作步骤和工况外,平时随时可以开停机: (4) 能耗小、操作费用低.由于它能在 0.8MPa-3MPa 下操作运行,这对于许多氢
气源如弛放气、变换气、石化精炼气等,其本身压力满足这一要求,省去加压设备及能
11-
大连理工大学专业学位硕士学位论文
The plant of PSA belongs to ful1 automatic operation b田 1咀lI y . Howev时. we chose the most advanced Redundant Control System Using 87-400 from 8iemens on 阳 Automatic Con筐。10臼 ign, which ens山田由e fuU automatic control and op町础。n Otherwise, in order to improve hydrogen re∞ve町,也is article made an Attempt to using Membrane Technology on the de皿r怕到dgas 齿。m 由ePSA.
Separation 丘om
Coal Oven Gas by PSA Progress Abstract Coal oven g认 whích ∞阳 ned plentiful hydrogen as much 田 55% (volume 阳cent proportion), was mainly used 幽 industrial and civil fuel. Hy由ogen w国 wasted while High-Pure hy'齿。gen w血叫山d 国 protective gas in Cold-rolled steel production and raw material in chemica1 s归也etic industry. Traditiona1, hydrogen was pre阳red by wat町 el配trolysis and Amm onia Crack,町, which are high co盹 large inves阳ent and difficult promotion. In order to find a solution for hy曲。 gen 回田ces and 田onomy method to pr叩缸e hy由ogen, m阻yω回国es have been researching tirelessly. Sin四由e Am erican UCC ωmpany built 也e first ind田园 al plant of pr臼sure swing ad皿叩tion(PSA) 阳 prCJ双re hydrogen from coal oven gas in 1960s, it has made rapid development and i臼 products have been sold all over the world. Beca'田eof 也e differ田lt adsorption capacity of differ田"∞mponents 00 adsorbent und町 two kinds of pr田sur回国 normal 阳nperature, PSA achiev,目 E回回paration and hydrogen purification. It can either separate hydrogen from mixture or puri仙,ydrogen Anshan lrcn and St回1 Group Corporation aIready have three plants of PSA wi由 hydrogen production ra阳 of 10ωNm3,岛国ch. As the improvernent of the Cold Rolled Sheet production, original plants of PSA can not 回tisfy the requirement. 80,也e forth plant of PSA W皑白Slgn创, fabricated and installed by Dalian Smart g国 S叩田由onCo:L叫. This article designed the process, automatic control and instr田oents of the forth plant of PSA 由'Ough operating su凹eys of the original plants of PSA p即,aring hydrogen from coal oveng嗣 00 也e spot In the process design, we improved the plant of PSA from the 田ual four columns wi由 阳'0 51-叩sofpre田ure equalizing to five ∞l田mmwi曲曲ree stepS of pressure 吨ualizing. There is always one colurnn adsorbing, which mak自由e 岛田。由erωl田nns higher 回s。叩I1ve efficiency. In吐le same time, one more step of pressure equa1izin且严田ess will improve the hydrogen reωvery. τ"he properties of the adsorbent affect 由e purific四on 四d 由e recov町y of the products directly and also affect 由e 到ability and 也e 且凹 ice life of 也e plant. In order 阳 achíeve the best adsorption effect, we chose pertinent a由orbents Iike Activated Carbon, Activated Alumina, 5A Molecular Sieve and Palladium Catalyst according to 血e components in Coal oven g:盹
变压吸附技术用于制氢
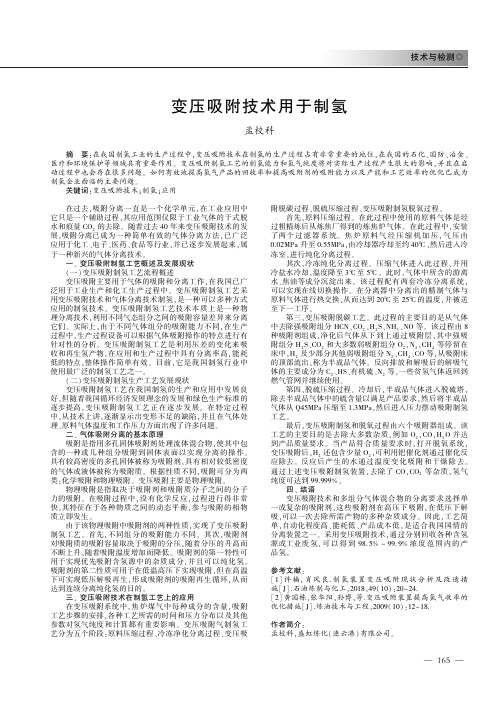
技术与检测Һ㊀变压吸附技术用于制氢孟校科摘㊀要:在我国制氢工业的生产过程中ꎬ变压吸附技术在制氢的生产过程占有非常重要的地位ꎬ在我国的石化㊁国防㊁冶金㊁医疗和环境保护等领域具有重要作用ꎮ变压吸附制氢工艺的制氢能力和氢气纯度将对实际生产过程产生很大的影响ꎬ并且在启动过程中也会存在很多问题ꎮ如何有效地提高氢气产品的回收率和提高吸附剂的吸附能力以及产能和工艺效率的优化已成为制氢企业面临的主要问题ꎮ关键词:变压吸附技术ꎻ制氢ꎻ应用㊀㊀在过去ꎬ吸附分离一直是一个化学单元ꎬ在工业应用中它只是一个辅助过程ꎬ其应用范围仅限于工业气体的干式脱水和痕量CO2的去除ꎮ随着过去40年来变压吸附技术的发展ꎬ吸附分离已成为一种简单有效的气体分离方法ꎬ已广泛应用于化工㊁电子㊁医药㊁食品等行业ꎬ并已逐步发展起来ꎬ属于一种新兴的气体分离技术ꎮ一㊁变压吸附制氢工艺概述及发展现状(一)变压吸附制氢工艺流程概述变压吸附主要用于气体的吸附和分离工作ꎬ在我国已广泛用于工业生产和化工生产过程中ꎮ变压吸附制氢工艺采用变压吸附技术和气体分离技术制氢ꎬ是一种可以多种方式应用的制氢技术ꎮ变压吸附制氢工艺技术本质上是一种物理分离技术ꎬ利用不同气态组分之间的吸附容量差异来分离它们ꎮ实际上ꎬ由于不同气体组分的吸附能力不同ꎬ在生产过程中ꎬ生产过程设备可以根据气体吸附操作的特点进行有针对性的分析ꎮ变压吸附制氢工艺是利用压差的变化来吸收和再生氢产物ꎬ在应用和生产过程中具有分离率高ꎬ能耗低的特点ꎬ整体操作简单有效ꎮ目前ꎬ它是我国制氢行业中使用最广泛的制氢工艺之一ꎮ(二)变压吸附制氢生产工艺发展现状变压吸附制氢工艺在我国制氢的生产和应用中发展良好ꎬ但随着我国循环经济发展理念的发展和绿色生产标准的逐步提高ꎬ变压吸附制氢工艺正在逐步发展ꎮ在特定过程中ꎬ从技术上讲ꎬ逐渐显示出变形不足的缺陷ꎬ并且在气体处理㊁原料气体温度和工作压力方面出现了许多问题ꎮ二㊁气体吸附分离的基本原理吸附是指用多孔固体吸附剂处理流体混合物ꎬ使其中包含的一种或几种组分吸附到固体表面以实现分离的操作ꎮ具有较高密度的多孔固体被称为吸附剂ꎬ具有相对较低密度的气体或液体被称为吸附质ꎮ根据性质不同ꎬ吸附可分为两类:化学吸附和物理吸附ꎮ变压吸附主要是物理吸附ꎮ物理吸附是指取决于吸附剂和吸附质分子之间的分子力的吸附ꎮ在吸附过程中ꎬ没有化学反应ꎬ过程进行得非常快ꎬ其特征在于各种物质之间的动态平衡ꎬ参与吸附的相物质立即发生ꎮ由于该物理吸附中吸附剂的两种性质ꎬ实现了变压吸附制氢工艺ꎮ首先ꎬ不同组分的吸附能力不同ꎮ其次ꎬ吸附剂对吸附质的吸附容量取决于吸附的分压ꎬ随着分压的升高而不断上升ꎬ随着吸附温度增加而降低ꎮ吸附剂的第一特性可用于实现优先吸附含氢源中的杂质成分ꎬ并且可以纯化氢ꎮ吸附剂的第二性质可用于在低温高压下实现吸附ꎬ但在高温下可实现低压解吸再生ꎬ形成吸附剂的吸附再生循环ꎬ从而达到连续分离纯化氢的目的ꎮ三㊁变压吸附技术在制氢工艺上的应用在变压吸附系统中ꎬ焦炉煤气中每种成分的含量ꎬ吸附工艺步骤的安排ꎬ各种工艺所需的时间和压力分布以及其他参数对氢气纯度和计算都有重要影响ꎮ变压吸附气制氢工艺分为五个阶段:原料压缩过程㊁冷冻净化分离过程㊁变压吸附脱碳过程㊁脱硫压缩过程㊁变压吸附制氢脱氧过程ꎮ首先ꎬ原料压缩过程ꎮ在此过程中使用的原料气体是经过粗精炼后从炼焦厂得到的炼焦炉气体ꎮ在此过程中ꎬ安装了两个过滤器系统ꎮ焦炉原料气经压缩机加压ꎬ气压由0.02MPa升至0.55MPaꎬ由冷却器冷却至约40ħꎬ然后进入冷冻室ꎬ进行纯化分离过程ꎮ其次ꎬ冷冻纯化分离过程ꎮ压缩气体进入此过程ꎬ并用冷盐水冷却ꎬ温度降至3ħ至5ħꎮ此时ꎬ气体中所含的游离水㊁焦油等成分沉淀出来ꎮ该过程配有两套冷冻分离系统ꎬ可以实现在线切换操作ꎮ在分离器中分离出的精制气体与原料气体进行热交换ꎬ从而达到20ħ至25ħ的温度ꎬ并被送至下一工序ꎮ第三ꎬ变压吸附脱碳工艺ꎮ此过程的主要目的是从气体中去除强吸附组分HCN㊁CO2㊁H2S㊁NH3㊁NO等ꎮ该过程由8种吸附剂组成ꎬ净化后气体从下到上通过吸附层ꎬ其中强吸附组分H2S㊁CO2和大多数弱吸附组分O2ꎬN2ꎬCH4等停留在床中ꎬH2及少部分其他弱吸附组分N2㊁CH4㊁CO等ꎬ从吸附床的顶部流出ꎬ称为半成品气体ꎮ反向排放和解吸后的解吸气体的主要成分为C2㊁HS㊁有机硫㊁N2等ꎬ一些贫氢气体返回到燃气管网并继续使用ꎮ第四ꎬ脱硫压缩过程ꎮ冷却后ꎬ半成品气体进入脱硫塔ꎬ除去半成品气体中的硫含量以满足产品要求ꎬ然后将半成品气体从Q45MPa压缩至1.3MPaꎬ然后进入压力摆动吸附制氢工艺ꎮ最后ꎬ变压吸附制氢和脱氧过程由六个吸附器组成ꎮ该工艺的主要目的是去除大多数杂质ꎬ例如O2ꎬCOꎬH2O并达到产品质量要求ꎮ当产品符合质量要求时ꎬ打开脱氧系统ꎬ变压吸附后ꎬH2还包含少量O2ꎬ可利用钯催化剂通过催化反应除去ꎮ反应后产生的水通过温度变化吸附和干燥除去ꎮ通过上述变压吸附制氢装置ꎬ去除了COꎬCO2等杂质ꎬ氢气纯度可达到99.999%ꎮ四㊁结语变压吸附技术和多组分气体混合物的分离要求选择单一或复杂的吸附剂ꎬ这些吸附剂在高压下吸附ꎬ在低压下解吸ꎬ可以一次去除所需产物的多种杂质成分ꎮ因此ꎬ工艺简单ꎬ自动化程度高㊁能耗低㊁产品成本低ꎬ是适合我国国情的分离装置之一ꎮ采用变压吸附技术ꎬ通过分别回收各种含氢源或工业废氢ꎬ可以得到98.5%~99.9%浓度范围内的产品氢ꎮ参考文献:[1]许楠ꎬ肖风良.制氢装置变压吸附现状分析及改造措施[J].石油炼制与化工ꎬ2018ꎬ49(10):20-24. [2]黄国栋ꎬ张华阳ꎬ孙博ꎬ等.变压吸附装置提高氢气收率的优化措施[J].炼油技术与工程ꎬ2009(10):12-18.作者简介:孟校科ꎬ盛虹炼化(连云港)有限公司ꎮ561。
变压吸附技术在焦炉煤气制氢中的应用
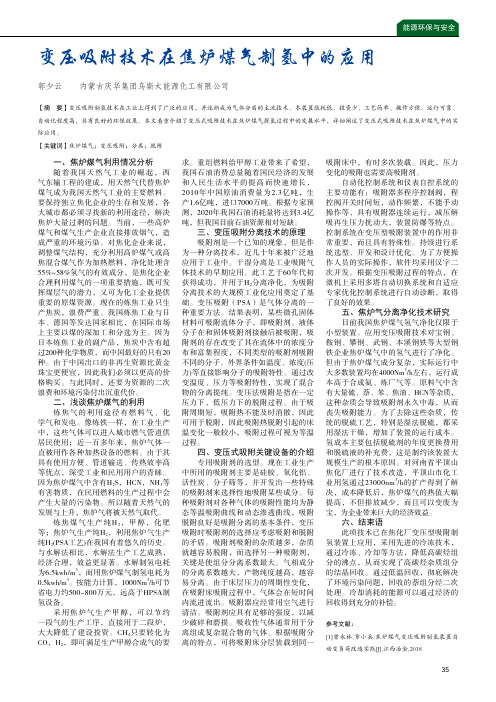
一、焦炉煤气利用情况分析随着我国天然气工业的崛起,西气东输工程的建成,用天然气代替焦炉煤气成为我国天然气工业的主要燃料。
要保持独立焦化企业的生存和发展,各大城市都必须寻找新的利用途径,解决焦炉大量过剩的问题。
当前,一些高炉煤气和煤气生产企业直接排放烟气,造成严重的环境污染。
对焦化企业来说,调整煤气结构,充分利用高炉煤气或高焦混合煤气作为加热燃料,净化处理含55%~58%氢气的有效成分,是焦化企业合理利用煤气的一项重要措施,既可发挥煤层气的潜力,又可为化工企业提供重要的原煤资源。
现在的炼焦工业只生产焦炭,浪费严重。
我国炼焦工业与日本、德国等发达国家相比,在国际市场上主要以煤的深加工和分选为主。
因为日本炼焦工业的副产品,焦炭中含有超过200种化学物质,而中国最好的只有20种。
由于中国出口的非再生资源比黄金珠宝更便宜,因此我们必须以更高的价格购买。
与此同时,还要为资源的二次浪费和环境污染付出沉重代价。
二、浅谈焦炉煤气的利用炼焦气的利用途径有燃料气、化学气和发电。
像炼铁一样,在工业生产中,这些气体可以进入城市燃气管道供居民使用;近一百多年来,焦炉气体一直被用作各种加热设备的燃料。
由于其具有使用方便、管道输送、传热效率高等优点,深受工业和民用用户的青睐。
因为焦炉煤气中含有H2S,HCN,NH3等有害物质,在民用燃料的生产过程中会产生大量的污染物。
所以随着天然气的发展与上升,焦炉气将被天然气取代。
炼焦煤气生产纯H2,甲醇,化肥等;焦炉气生产纯H2,利用焦炉气生产纯H2(PSA工艺)在我国有着悠久的历史。
与水解法相比,水解法生产工艺成熟,经济合理,效益更显著。
水解制氢电耗为6.5kwh/m3,而用焦炉煤气制氢电耗为0.5kwh/m3。
按能力计算,1000Nm3/h可节省电力约500-800万元,远高于HPSA制氢设备。
采用焦炉气生产甲醇,可以节约一段气的生产工序,直接用于二段炉,大大降低了建设投资。
CH4只要转化为CO,H2,即可满足生产甲醇合成气的要求。
变压吸附技术在焦炉煤气制氢中运用分析
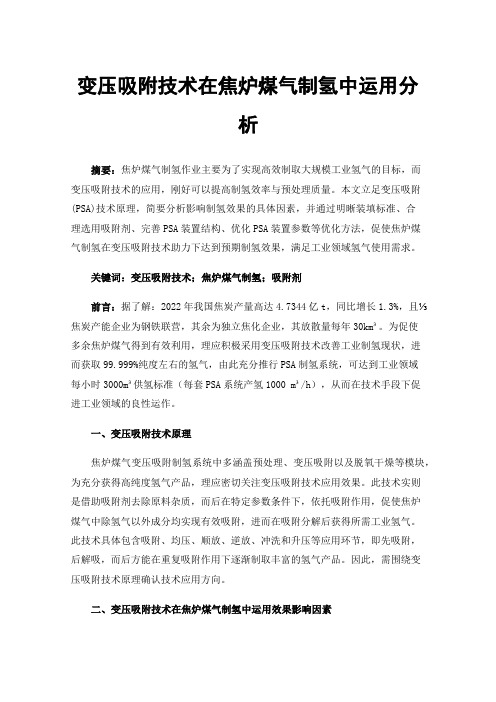
变压吸附技术在焦炉煤气制氢中运用分析摘要:焦炉煤气制氢作业主要为了实现高效制取大规模工业氢气的目标,而变压吸附技术的应用,刚好可以提高制氢效率与预处理质量。
本文立足变压吸附(PSA)技术原理,简要分析影响制氢效果的具体因素,并通过明晰装填标准、合理选用吸附剂、完善PSA装置结构、优化PSA装置参数等优化方法,促使焦炉煤气制氢在变压吸附技术助力下达到预期制氢效果,满足工业领域氢气使用需求。
关键词:变压吸附技术;焦炉煤气制氢;吸附剂前言:据了解:2022年我国焦炭产量高达4.7344亿t,同比增长1.3%,且⅓焦炭产能企业为钢铁联营,其余为独立焦化企业,其放散量每年30km³。
为促使多余焦炉煤气得到有效利用,理应积极采用变压吸附技术改善工业制氢现状,进而获取99.999%纯度左右的氢气,由此充分推行PSA制氢系统,可达到工业领域每小时3000m³供氢标准(每套PSA系统产氢1000 m³/h),从而在技术手段下促进工业领域的良性运作。
一、变压吸附技术原理焦炉煤气变压吸附制氢系统中多涵盖预处理、变压吸附以及脱氧干燥等模块,为充分获得高纯度氢气产品,理应密切关注变压吸附技术应用效果。
此技术实则是借助吸附剂去除原料杂质,而后在特定参数条件下,依托吸附作用,促使焦炉煤气中除氢气以外成分均实现有效吸附,进而在吸附分解后获得所需工业氢气。
此技术具体包含吸附、均压、顺放、逆放、冲洗和升压等应用环节,即先吸附,后解吸,而后方能在重复吸附作用下逐渐制取丰富的氢气产品。
因此,需围绕变压吸附技术原理确认技术应用方向。
二、变压吸附技术在焦炉煤气制氢中运用效果影响因素焦炉煤气制氢中关于PSA运用效果的分析,能够发现多与以下两项因素有关:(1)PSA装置构造特征,PSA装置作为承载吸附剂的重要设备,若本身依据各工序建立的装置构造不符合工序要求,或者变压吸附部分存在运行异常情况,将直接削弱变压吸附效能,甚至容易造成焦炉煤气原料得不到充分吸附处理,最终因杂质较多影响技术应用成果[1]。
焦炉煤气变压吸附提氢典型工艺及选择
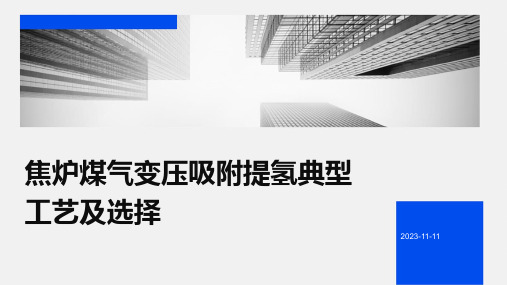
不同行业对氢气纯度和产量的要求不同, 工艺选择需考虑产品纯度和产量的要求。
设备投资和运行维护
不同工艺的能耗和成本不同,工艺选择需 考虑经济性因素。
设备投资和运行维护也是工艺选择需要考 虑的因素。
不同工艺的比较和选择
变压吸附法
变压吸附法是一种常用的提氢工艺,具有产品纯 度高、能耗低等优点,适用于从焦炉煤气中提取 高纯度氢气。
THANK YOU
03
典型焦炉煤气变压吸 附提氢工艺流程
工艺流程一:预处理+变压吸附提氢
预处理
对焦炉煤气进行预处理,除去其中的杂质,如水分、硫化物 、氮化物等。
变压吸附提氢
利用变压吸附技术,从预处理后的焦炉煤气中提取氢气。
工艺流程二:变压吸附提氢+深冷分离
变压吸附提氢
从焦炉煤气中提取氢气。
深冷分离
将变压吸附提氢后的气体进行深冷分离,得到高纯度的氢气。
前景
随着环保要求的提高和能源结构的调整,焦 炉煤气变压吸附提氢技术将具有更加广阔的 应用前景,未来将不断改进和完善工艺技术 ,实现更加高效、环保的能源利用。
06
结论与展望
研究结论
经过对各种焦炉煤气变压吸附 提氢典型工艺的比较和分析, 可以得出以下结论
采用预处理+变压吸附提氢工艺 可以获得较高的氢气纯度和回 收率,同时工艺流程简单,易 于操作和维护。
适应性强
焦炉煤气成分复杂,含有多种 气体成分,变压吸附技术可实 现对其中氢气的有效分离和纯 化,适用于多种不同来源的焦
炉煤气。
环保性好
变压吸附提氢技术不产生废水、废 渣等污染物,可实现清洁生产。
经济性高
变压吸附提氢技术具有较高的能源 利用率和较低的运行成本,可实现 氢气的低成本生产。
焦炉煤气PSA制氢及其进展

焦炉煤气PSA制氢及其进展闫志者【摘要】2013年全国焦炭产量预计突破450 Mt,约占世界焦炭总产量的60%.按照每生产l t焦炭可回收约200 m3的焦炉煤气来计算,我国每年约有90 km3的焦炉煤气可以利用.焦炉煤气是一种富氢气体(氢体积分数为55%~59%),通过原料气压缩、预处理、PSA(pressure swing adsorption,变压吸附)氢提纯和脱氧干燥等4个步骤即可获得高纯度的氢气.目前国内已拥有70多套焦炉煤气制氢装置,其中中国平煤首山焦化公司设计产氢规模30 dam3/h的焦炉煤气制氢装置,已连续运行约3 a.鉴于该技术运转费用低、工艺简单等优势,建议有条件的企业,应充分考虑通过焦炉煤气PSA制氢技术来获取氢气,自用或供周边企业使用.【期刊名称】《炼油技术与工程》【年(卷),期】2014(044)001【总页数】3页(P17-19)【关键词】焦炉煤气;制氢;PSA;区域循环经济【作者】闫志者【作者单位】中科(广东)炼化有限公司,广东省湛江市524022【正文语种】中文1 焦炉煤气及其利用政策焦炉煤气是焦炭生产过程中煤炭在高温、缓慢干馏过程中产生的一种可燃性气体。
一般每生产1 t焦炭会产生430 m3焦炉煤气,其中约50%返回炼焦炉用作加热燃料,剩余气体可进行回收利用。
2013年,全国焦炭产量预计突破450 Mt,依此计算,我国焦炉煤气产量是非常高的。
全国焦炭产能约有1/3在钢铁联合企业,2/3在独立焦化企业。
在钢铁联合企业中,当充分回收利用高炉煤气和转炉煤气等低热值燃料后,可顶替出大量焦炉煤气;对于独立焦化企业,剩余焦炉煤气部分被回收用于城市煤气、发电等,其余则排入大气,独立焦化企业富余的焦炉气曾因无法直接用于生产而被大量放散,放散量最高峰时曾达30 km3/a[1]。
焦炉煤气主要成分为氢气(体积分数为55%~59%)和甲烷(体积分数为24%~26%),还有少量的一氧化碳、氮气等,低热值为16.72~18.81 MJ/m3[2]。
变压吸附技术在焦炉煤气制氢中的应用
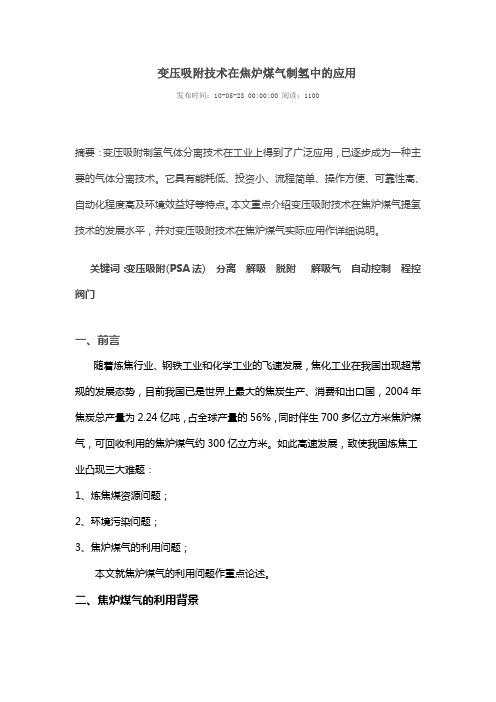
变压吸附技术在焦炉煤气制氢中的应用发布时间:10-05-28 00:00:00 阅读:1100摘要:变压吸附制氢气体分离技术在工业上得到了广泛应用,已逐步成为一种主要的气体分离技术。
它具有能耗低、投资小、流程简单、操作方便、可靠性高、自动化程度高及环境效益好等特点。
本文重点介绍变压吸附技术在焦炉煤气提氢技术的发展水平,并对变压吸附技术在焦炉煤气实际应用作详细说明。
关键词:变压吸附(PSA法) 分离解吸脱附解吸气自动控制程控阀门一、前言随着炼焦行业、钢铁工业和化学工业的飞速发展,焦化工业在我国出现超常规的发展态势,目前我国已是世界上最大的焦炭生产、消费和出口国,2004年焦炭总产量为2.24亿吨,占全球产量的56%,同时伴生700多亿立方米焦炉煤气,可回收利用的焦炉煤气约300亿立方米。
如此高速发展,致使我国炼焦工业凸现三大难题:1、炼焦煤资源问题;2、环境污染问题;3、焦炉煤气的利用问题;本文就焦炉煤气的利用问题作重点论述。
二、焦炉煤气的利用背景由于我国天然气工业的崛起,西气东输工程已经贯通,天然气已代替焦炉煤气管道气成为民用的主要燃料。
为此,各大中城市的独立焦化厂,为维持其生存与发展,必需寻找新的利用途径,以解决大量富余的焦炉煤气问题。
目前钢铁企业中大量的高炉煤气、焦炉煤气的富余,甚至直接放散、排放、污染环境,已成为企业的突出的问题。
因此,调整企业的燃气结构,充分利用高炉煤气或高、焦混合煤气作为所有设备的加热燃料、提纯其中有效组份(如H含2量为55%~58%)等,将是各焦化企业合理利用燃气的重要措施,不仅可以充分发挥煤资源的潜能,又为化学工业提供重要的原、燃料资源。
焦炉煤气是炼焦行业最主要的副产品之一,每炼一吨焦炭,可产生430m3左右的煤气,其中一半回炉助燃,另外约的200m3焦炉煤气必须使用专门的装臵进行回收,目前我国只有不到10%的焦炉煤气被回收,主要用于城市煤气供应、发电、化工生产等,绝大多数排入大气点了“天灯”,在污染环境的同时,造成稀缺资源的极大浪费。
焦炉煤气变压吸附制氢工艺探讨

焦炉煤气变压吸附制氢工艺探讨煤焦油加氢技术中,提氢工艺是一种相当成熟的一种工艺,可以提取99.99%纯度的氢气。
焦炉煤气PSA制取16000Nm³/h氢气是由四川省化工设计院设计建设。
本装置以焦炉煤气为原料,通过粗脱、压缩、预处理以及两段变压吸附的工艺来进行产品氢气的提纯,该装置与焦油加氢装置配套,达到节能降耗、提高综合经济效益的目的。
本装置界区内按照功能可以分为三区,一是煤气净化区,二是压缩机厂房区,三是PSA设备区。
压缩机厂房有螺杆压缩机两台,煤气净化区有脱焦油,脱硫工序、粗脱工序、预处理工序组成,PSA设备区分别独立。
在PSA设备区,两排吸附塔及解吸气缓冲罐、顺放气罐、氢气缓冲罐等基本沿“一”字形排列在界区。
本装置的整个生产过程(吸附与再生)工艺切换过程均通过程控阀门按一定的工艺步序和顺序进行开关来实现的。
(一)、粗脱工序,粗脱工序主要由3台粗脱塔组成,2台运行,1台备用,其主要作用是将原料煤气中的萘含量从380mg/Nm³降至10mg/Nm³,必要时可采用3台同时运行的程序。
粗脱塔内装填有高效吸附剂。
粗脱的步序为:吸附过程、加热再生过程、吹冷过程。
两台粗脱塔交替进行吸附和再生,达到连续工作的目的。
(二)、预处理工序,预处理工序主要由2台除油塔、3台预处理塔和1台再生气加热器组成。
除油塔的作用是除去压缩机带出的油,避免油进入预处理塔,污染吸附剂,2台除油塔,1用1备。
预处理塔的主要作用是利用吸附剂的选择性,脱除煤气中的苯、萘、焦油、NH3、H2S等杂质。
预处理塔采用2台吸附、1台再生的步骤进行操作。
具体步骤为:吸附过程、降压过程、加热过程、冷却过程、升压过程。
(三)、PSA工序,变压吸附工序第一段PSA-I采用8-2-3分组抽真空流程,即装置的8个吸附塔中有2个吸附塔始终处于进料吸附的状态。
其吸附和再生工艺过程由吸附、连续3次均压降压、顺放、逆放、抽真空、预升压、连续3次均压升压和产品最终升压等步骤组成。
变压吸附制氢技术在化工生产中的应用
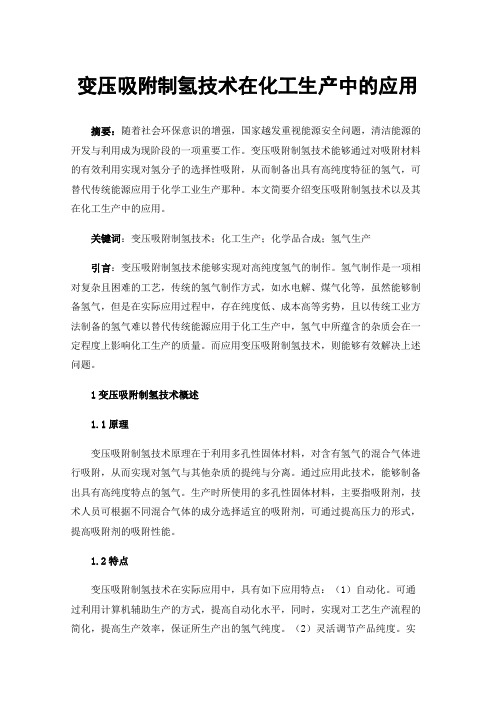
变压吸附制氢技术在化工生产中的应用摘要:随着社会环保意识的增强,国家越发重视能源安全问题,清洁能源的开发与利用成为现阶段的一项重要工作。
变压吸附制氢技术能够通过对吸附材料的有效利用实现对氢分子的选择性吸附,从而制备出具有高纯度特征的氢气,可替代传统能源应用于化学工业生产那种。
本文简要介绍变压吸附制氢技术以及其在化工生产中的应用。
关键词:变压吸附制氢技术;化工生产;化学品合成;氢气生产引言:变压吸附制氢技术能够实现对高纯度氢气的制作。
氢气制作是一项相对复杂且困难的工艺,传统的氢气制作方式,如水电解、煤气化等,虽然能够制备氢气,但是在实际应用过程中,存在纯度低、成本高等劣势,且以传统工业方法制备的氢气难以替代传统能源应用于化工生产中,氢气中所蕴含的杂质会在一定程度上影响化工生产的质量。
而应用变压吸附制氢技术,则能够有效解决上述问题。
1变压吸附制氢技术概述1.1原理变压吸附制氢技术原理在于利用多孔性固体材料,对含有氢气的混合气体进行吸附,从而实现对氢气与其他杂质的提纯与分离。
通过应用此技术,能够制备出具有高纯度特点的氢气。
生产时所使用的多孔性固体材料,主要指吸附剂,技术人员可根据不同混合气体的成分选择适宜的吸附剂,可通过提高压力的形式,提高吸附剂的吸附性能。
1.2特点变压吸附制氢技术在实际应用中,具有如下应用特点:(1)自动化。
可通过利用计算机辅助生产的方式,提高自动化水平,同时,实现对工艺生产流程的简化,提高生产效率,保证所生产出的氢气纯度。
(2)灵活调节产品纯度。
实际生产中,可通过调整关键参数以及生产时的压力,实现对氢气产品纯度的灵活调节,从而充分满足化工生产中的不同应用需求。
(3)预处理难度低。
应用此技术制备氢气,无须设置复杂的预处理装置,相较传统技术而言,技术工艺操作更为简单且生产成本更低。
(4)易于扩建。
该技术在实际应用中,有着易于扩建以及布局灵活的优势,变压吸附制氢装置的扩建难度较低,通常只需要更加控制阀与吸附塔便可实现氢气产量的增加。
焦炉煤气变压吸附制氢工艺的应用

N ,的体积分数/ 0 H l“
N 的 体 积 分  ̄ /o O t l
5 0~10 O
16 .
B 23 ・
第2 卷 第 1 期 8 0 3 2 工艺流 程 .
煤 气 与 热 力
N 、 H 、O等从 吸附床层 上 部流 出 , 为 半成 品气 :C C 称 ( 时氢 气体 积 分 数 为 9 % ~ 5 ) 此 4 9 % 。经 逆 放 和抽
由于 能耗低 , 流程 简单 , 置 自动 化 程 度 高 , 品 纯 装 产
烷外 , 其他组分相当复杂 , 随原料煤的不同有较大的 差 别 。平煤 集 团天宏 焦 化公 司 焦炉煤 气 的组成 见 表
1 其 中的杂 质含 量见 表 2 , 。
表 1 焦炉 煤 气 组 成
度高 , 成本 低 , 已经成 为 制氢 的一 种主 导方 法 。
Ap l a i n o r su e S n s r t n Hy r g n Pr d ci n p i t fP e s r wi g Ad o p i d o e o u t c o o o
Te hn l g r m ke Ov n a c o o y f o Co e G s
1 概 述
的安 排 、 同工序 所 需 时 间及 压 力 的 分 配等 参 数 对 不
焦 炉 煤 气 中含 有 丰 富 的氢 气 , :体 积 分 数 约 H 5 % 。 目前焦 炉煤 气 主要 用 作 工 业 和 民用 燃 料 , 5 宝 贵 的氢气 资 源未得 到更 好 的利用 。随着 轧钢 产 品对
组分
H 2
0 2
C O
C2 O
N 2
2 变压 吸 附 的基 本 原 理 … 变 压 吸附 的基 本 原理 是利 用 吸附 剂对 不 同气体
变压吸附提氢工艺在煤气合成气中的合理利用

62变压吸附提氢工艺在煤气合成气中的合理利用朱从军(新疆天业(集团)化工研究院,新疆石河子 832000)摘要:介绍了新疆天业利用变压吸附装置从煤气合成气中提取氢气的工艺流程布置,及其关键设备选择。
关键词:变压吸附(PSA);提氢装置;流程;布置;安全随着循环经济理念的不断深入,通过清洁生产新工艺、新技术的不断开发和应用,使化工行业不断走上可持续发展的道路,实现发展与资源、环境的统一,已成为当今社会工业发展的必然趋势。
变压吸附气体分离与提纯技术已经成为当代化工独树一帜的生产工艺和操作单元,而且随着变压吸附技术自身的不断完善,它在化工行业的不可或缺性已经愈演愈烈。
新疆天业(集团)有限公司作为新疆兵团所属的大型国有企业,依托新疆丰富的煤、盐、石灰石等资源优势,实施优势资源转化战略,目前,已具备年产110万吨电石乙炔法聚氯乙烯、90万吨离子膜烧碱装置及配套的自备电厂、电石厂和电石渣制水泥装置,是国内生产能力最大的电石法聚氯乙烯生产企业。
公司作为国内第一批循环经济试点单位,始终坚持以循环经济的理念发展煤电化一体化产业,清洁生产的新工艺、新技术得到了充分的开发和应用,并在行业内推广应用。
在天业集团,变压吸附分离技术主要应用于空分制氮、精馏尾气的回收、天然气制氢精制、富氢裂解气氢气提浓等等。
1从煤气合成气中利用变压吸附提氢的原理吸附按性质不同可分为两大类,即化学吸附和物理吸附,变压吸附从本质上来说属于物理吸附。
其特点是:吸附过程中没有化学反应,吸附过程进行的很快,参与吸附的各种物质间动态平衡在瞬间即可完成,并且非常重要的一点是:这种吸附理论上说是完全可逆的。
由煤气化路线产生的合成气,往往由数十种气体组成(详见表1),成分复杂,选择合理的分离工艺,对企业长远的正常生产运行至关重要。
之所以选择变压吸附提氢工艺,主要是因为吸附剂在整个物理吸附过程中所具有的两个性质,(1)对合成气中各个组分的吸附能力不同;(2)吸附质在吸附剂上的吸附容量随吸附质的分压上升而增加,随吸附温度上升而下降。
焦炉煤气变压吸附制氢在宝钢的应用

冶金动力METALLURGICALPOWER2006年第6期总第118期焦炉煤气变压吸附制氢在宝钢的应用张敏(宝钢股份公司宝钢分公司冷轧厂,上海201900)【摘要】介绍了变压吸附制氢(PSA)工艺,分析了宝钢变压吸附制氢生产中两种运行故障,阐述了变压吸附的优越性,以及该工艺在宝钢的应用前景。
【关键词】焦炉煤气;变压吸附;氢气【中图分类号】TQ522【文献标识码】B【文章编号】1006-6764(2006)06-0023-03ApplicationofPressureSwingAdsorptionHydrogenMakingProcessofCokeOvenGasZHANGMin(Cold-RollingMillofBranchCo.,BaoshanSteel&IronCo.,Ltd.,Shanghai201900,China)【Abstract】ThepressureswingadsorptionhydrogenmakingprocesswaspresentedandthetwooperationfailuresinpressureswingadsorptionhydrogenmakingproductionofBaoshanIron&SteelCo.,Ltd.wereanalyzed.TheadvantagesandapplicationprospectofthisprocessinthisCompanywereexpounded.【Keywords】cokeovengas;pressureswingadsorption;hydrogen1前言氢气是钢铁企业特别是冷轧板材生产企业重要的保护气体。
钢铁企业主要通过水电解和焦炉煤气变压吸附(PSA)两种方法制氢。
宝钢一、二期建设中引进了德国鲁奇公司3台压力水电解槽,制氢能力600m3/h,三期工程中引进德国林德公司的焦炉煤气五塔变压吸附制氢装置,制氢能力3000m3/h。
- 1、下载文档前请自行甄别文档内容的完整性,平台不提供额外的编辑、内容补充、找答案等附加服务。
- 2、"仅部分预览"的文档,不可在线预览部分如存在完整性等问题,可反馈申请退款(可完整预览的文档不适用该条件!)。
- 3、如文档侵犯您的权益,请联系客服反馈,我们会尽快为您处理(人工客服工作时间:9:00-18:30)。
焦炉煤气变压吸附制氢新工艺的开发与应用平顶山市三源制氢有限公司由中国神马集团、平顶山煤业集团有限责任公司合作建设,该公司年产8000万m3纯氢,采用的焦炉煤气变压吸附(PSA)制氢项目是一个综合利用、变废为宝的环保型工程。
它直接把两大公司的主生产系统联在一起,充分利用了平顶山煤业集团天宏焦化公司富余放散的焦炉煤气,从杂质极多、难提纯的气体中长周期、稳定、连续地提取纯氢,以较低的生产成本解决了河南神马尼龙化工公司因扩产20万t/a尼龙66盐而急需解决的原料问题。
项目的建成投产,不仅解决了平顶山煤业集团天宏焦化公司富余煤气放散燃烧对大气的污染问题;而且还减少了河南神马尼龙化工公司因扩产需增加的高额投资和大量耗用焦炭能源及废水、废气、废渣的排污问题;同时也是一个低投入、高产出、多方受益的科技创新项目。
该装置规模为目前国内最大,首次采用先进可靠的新工艺,其经济效益、社会效益可观,对推进国内PSA技术进步也有重大意义。
1942年德国发表了第一篇无热吸附净化空气的文献,20世纪60年代初,美国联合碳化物(UnionCarbide)公司首次实现了变压吸附四床工艺技术的工业化,进入20世纪70年代后,变压吸附技术获得了迅速的发展。
装置数量剧增,装置规模不断扩大,使用范围越来越广,主要应用于石油化工、冶金、轻工及环保等领域。
平顶山三源制氢公司这套大规模低成本提纯氢气装置,是以一种难以净化的焦炉煤气为原料,在国内还没有同类型的装置,特别是其产品——高纯氢用于技术水平居世界前列的尼龙66盐公司,更是国内首创,走在了世界同行业的前列。
1 焦炉煤气PSA制氢新工艺传统的焦炉煤气制氢工艺按照正常的净化分离步骤是:焦炉煤气首先经过焦化系统的预处理,脱除大部分烃类物质;经初步净化后的原料气再经过湿法脱硫、干法脱萘、压缩机、精脱萘、精脱硫和变温吸附(TSA)系统,最后利用PSA制氢工艺提纯氢气,整个系统设备投资大、工业处理难度大、环境污染严重、操作不易控制、生产成本高、废物排放量大,因此用焦炉煤气PSA制氢在某种程度上受到一定的限制,所以没有被大规模的应用到工业生产当中。
平顶山市三源制氢有限公司所采用的生产工艺是对四川同盛科技有限责任公司提供的工艺方案进行优化后的再组合,是目前国内焦炉煤气PSA制氢工艺中最先进的生产工艺,它生产成本低、效率高,能解决焦炉煤气制氢过程中杂质难分离的问题,从而推动了焦炉煤气PSA制氢的发展。
该工艺的特点是:焦炉煤气压缩采用分步压缩法、冷冻净化及二段脱硫法等新工艺技术。
1.1 工艺流程PSA制氢新工艺如图1(略)所示。
该装置工艺流程分为5个工序:①原料气压缩工序(简称100#工序),②冷冻净化分离(简称200#工序),③PSA-C/R工序及精脱硫工序(简称300#工序),④半成品气压缩(简称400#工序),⑤PSA-H2工序及脱氧工序(简称500#工序)。
装置所用的原料气来自平顶山煤业集团天宏焦化公司的焦炉煤气,该公司的焦炉煤气主要用于锅炉、化工产品原料气及城市煤气;因净化难度高,故气体质量较差,分离等级较低,因此杂质的净化分离均以该公司使用的这套工艺装置来实现。
表1为原料煤气组成。
表1 原料煤气组成组成H2 O2 CO CO2 N2 CH4 C2 C3~5体积分数/% 55.50 0.43 8.10 5.86 2.86 23.68 3.20 0.31续表1组成萘总S 焦油HCN NH3 NO 苯质量浓度/mg·m-3 193 3000~4000 100~400 0.21 (5~10)×10-51.6×10-6 4000~500010#工序中,首先把焦炉煤气通过螺杆压缩机对煤气进行加压,将煤气压力从0.010-0.015 MPa加压至0.580MPa,并经冷却器冷却至40-45℃后输出。
经压缩冷却后的煤气含有机械水、焦油、萘、苯等组分,易对后工序吸附剂造成中毒或吸附剂性能下降,该装置设计冰机冷冻分离200#工序(冷却器为一开一备)对上述杂质进行脱除,此时,重组分物质被析出停留在分离器内,当冷却器前后压差高于设定值或运行一段时间后,自动切换至另一个系统,对停止运行的系统进入加热吹扫,利用低压蒸汽对冷却器和分离器内附着的重组分进行吹除,完成后处于待用状态,经分离后,仍有微量重组分杂质蒸汽带入煤气中,随着装置运行时间的增长,会逐步造成后续工段吸附剂中毒,所以,在冷冻分离后增加了除油器,主要是精脱重组分及水蒸气。
煤气进入300#PSA-C/R工序,该工序的主要目的是脱除煤气中强吸附组分HCN、C2+、CO2、H2S、NU3、NO、有机硫以及大部分CH4、CO、N2等;经过300#工序后的半成品气已得到净化,对压缩机工作条件要求较低,采用一级活塞式压缩工艺,将半成品气从0.50 MPa压缩至1.25MPa,再进入PSA-H2工序(在PSA-C/R和提氢工序之间设有脱氧工序,是因为经脱氧反应后会生成水分,传统工艺需要等压干燥脱水系统,该系统选用的二段法新工艺不仅节约了投资,而且降低了操作运行费用)。
500#工序PSA-H2在传统的PSA制氢工艺中是整套装置的核心部分,而在本装置工艺中只是作为对氢气的提纯,即从上道工序中经脱碳后得到氢体积分数为95%-98%的原料气,再提纯到99.99%后作为商品氢出售。
1.2 工艺方案的选择1.2.1 焦炉煤气压缩采用螺杆式压缩机焦炉煤气的压缩国内传统工艺流程中几乎均采用活塞式压缩机。
而该公司根据对制氢工艺新技术的掌握,针对原料气的特点,在焦炉煤气压缩的问题上,经多方论证后,确定采用分步压缩方案,即低压段采用螺杆压缩机,脱除杂质组分后,再用活塞式压缩机升压,这种低压段大气量将焦炉煤气压缩到0.55-0.60MPa的螺杆压缩机在国内尚属首次使用。
采用螺杆压缩机压缩焦炉煤气最大的优点是:螺杆机结构简单、运行时间长,可以保证装置长周期安全稳定运行,对原料气烃类杂质含量要求不高,无需备用压缩机。
与活塞式压缩机相比,无需维修频繁堵塞的气阀(原料气中焦油及萘含量较高,故需经常停车更换气阀内件),维修工作量几乎为零。
而传统的往复式压缩机辅助设备多、检修频率高,若用于焦炉煤气压缩,气阀更易堵塞,维修工作量大,还需要备用压缩机。
该工艺的另一主要优势是采用了柴油喷淋冷却工艺,出口温度控制在80℃左右,在该温度下,焦炉煤气中的轻质焦油、萘等大分子烃类大部分溶解在柴油中(回收的焦油、萘等烃类物质进行集中处理),但经过冷却器降温至40℃时,焦炉煤气中的萘要结晶析出,为此笔者又完善了使用柴油喷淋循环冷却的工艺,这样既能保证管道畅通、又能保证冷却效果,这也是该工艺的独到之处。
从投资的角度而言,原料气螺杆压缩机和半成品活塞式压缩机总购置费用不超过800万元,比目前国内同类装置采用3台活塞式压缩机(其中1台备用)节省投资约200万元。
1.2.2 原料气预处理系统采用净化分离工艺焦炉煤气PSA制氢国内同类装置原料气均采用活塞式压缩机,原料气在进入活塞式压缩机之前必须将萘、苯、焦油等重组分杂质脱除,以保证活塞式压缩机的正常工作,整个工艺气的处理需经过脱硫、脱萘、脱苯、除氨等预处理工艺及电捕焦油器、风机等附属设备,而该装置在螺杆压缩机后首次采用了冰机冷冻分离工艺,可以将原料气中大部分高碳烃类、苯、萘等重组分杂质在低温下脱除,从而大大降低了原料气预处理系统的投资和运行成本。
如果从原料气预处理系统的投资和运行成本分析,冷冻净化工艺则比传统工艺投资方面减少约533.63万元,运行成本节约60万元/a。
1.2.3 原料气脱硫采用PSA技术原料气经该装置冷冻净化工艺后,还含有质量浓度500-400mg/m3的硫无法在此工段中脱除(硫含量取决于所选焦煤的煤质),因此,原料气脱硫问题则是该装置的关键流程。
传统的脱硫方法有:(1)干法脱硫。
采用氧化铁干法脱硫,其优点是一次性投资较小,但缺点是运行成本非常高,易造成长期的二次污染。
(2)湿法脱硫。
如PDS等传统脱硫方法。
湿法脱硫具有安全可靠,运行稳定、运行费用低于干法脱硫等优点。
但是,湿法脱硫的缺点也很明显,那就是装置投资高、设备腐蚀严重、环境污染大,对有机硫几乎没有脱除效果,而对于变压吸附工艺的吸附剂,危害最大的就是有机硫,它会造成吸附剂寿命减少或失活,影响吸附效果,从而影响了产品氢气质量。
另外,经脱硫后产生的硫渣及含硫废水易造成二次污染。
该装置采用目前最先进的,并且是非常成熟的两段法吸附技术,即把PSA脱碳和PSA制氢2种工艺合二为一,取长补短。
结合焦化公司对解析气中硫含量要求不高的实际情况(因焦炉煤气中硫含量的波动较大,从本装置分离出的解吸气占平顶山煤业集团煤气总量的比例较小,且解吸气热值高出焦炉煤气40%,并经过多级净化,用途广泛),从根本上解决了有机硫处理的难题。
该装置第一段采用PSA脱碳技术,可以大幅度脱除原料气中有机硫、无机硫、CO2、CO等杂质组分,使氢气体积分数达到95%以上,同时将原料气中的总硫质量浓度从500-400mg/m3脱除到10mg/m3以下,然后进入下段PSA制氢工序,由于专用耐硫吸附剂对硫的解吸性能非常好,可以循环使用(与CO2的吸附解吸性能接近),同时也保证了PSA脱碳吸附剂使用寿命可以达到10年以上,第二段PSA制氢吸附剂使用寿命更长,可以达到15年以上。
1.2.4 两段法提高氢气回收率传统PSA制氢工艺中氢气回收率只有70%-80%,而该装置选用的工艺技术可将氢气回收率提高到95%以上,从这套装置来讲,解吸气全部返回到煤气管网,因此,从表面上讲,氢气回收率似乎并不重要,但氢气回收率低,则会增加原料气量,不仅仅会增加压缩功耗,同时也增大了装置对杂质组分的处理量,导致装置运行费用增大,氢气成本增高。
因此,努力提高氢气回收率是降低氢气成本,提高经济效益的有效手段。
该装置推荐采用目前最先进的两段法吸附技术是提高氢气回收率的最佳方案。
将PSA二段制氢的逆放废气回收作为本装置的升压气;将PSA二段制氢的解吸气用于PSA一段脱碳的冲洗气;将一段PSA脱碳的逆放气和抽空解吸气作为除油器和TSA系统的冷吹气和再生气使用,最后全部返回解吸气管网。
从投资角度讲,该装置由于采用了两段法吸附技术,使主装置总投资由4200万元降低到3000万元。
1.2.5 脱氧系统无需干燥设备在国内已经运行的PSA制氢装置中,凡是对产品氢中O2含量有要求者,几乎无一例外,均设计了一套钯催化剂+等压干燥系统,其原因是O2和H2的分离系数较小,仅仅通过PSA很难达到产品氢气对微量杂质O2含量的严格要求(一般均要求体积分数小于1×10-5)。
在预留的脱氧系统中,取消了干燥系统。
主要是因为如果产品气中要求H2O体积分数≤6×10-5,则脱氧系统放在PSA-H2二段后面,不需要干燥系统;如果产品气中要求H2O体积分数≤1×10-5,则脱氧系统放在PSA-C/R和PSA-H2二段之间,同样不需要干燥系统。