材料设计
材料对设计的影响
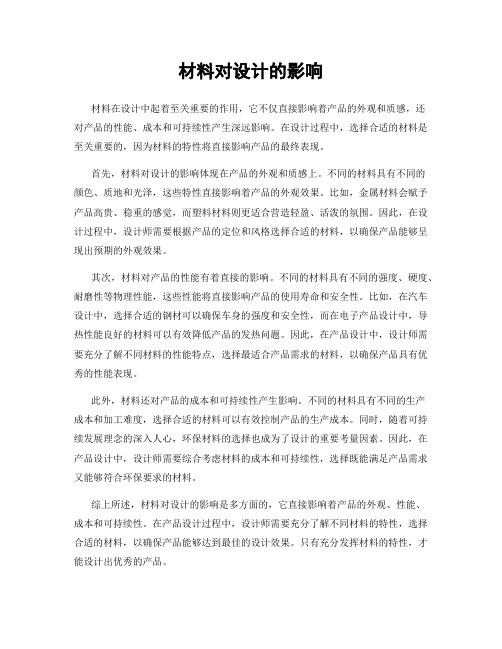
材料对设计的影响材料在设计中起着至关重要的作用,它不仅直接影响着产品的外观和质感,还对产品的性能、成本和可持续性产生深远影响。
在设计过程中,选择合适的材料是至关重要的,因为材料的特性将直接影响产品的最终表现。
首先,材料对设计的影响体现在产品的外观和质感上。
不同的材料具有不同的颜色、质地和光泽,这些特性直接影响着产品的外观效果。
比如,金属材料会赋予产品高贵、稳重的感觉,而塑料材料则更适合营造轻盈、活泼的氛围。
因此,在设计过程中,设计师需要根据产品的定位和风格选择合适的材料,以确保产品能够呈现出预期的外观效果。
其次,材料对产品的性能有着直接的影响。
不同的材料具有不同的强度、硬度、耐磨性等物理性能,这些性能将直接影响产品的使用寿命和安全性。
比如,在汽车设计中,选择合适的钢材可以确保车身的强度和安全性,而在电子产品设计中,导热性能良好的材料可以有效降低产品的发热问题。
因此,在产品设计中,设计师需要充分了解不同材料的性能特点,选择最适合产品需求的材料,以确保产品具有优秀的性能表现。
此外,材料还对产品的成本和可持续性产生影响。
不同的材料具有不同的生产成本和加工难度,选择合适的材料可以有效控制产品的生产成本。
同时,随着可持续发展理念的深入人心,环保材料的选择也成为了设计的重要考量因素。
因此,在产品设计中,设计师需要综合考虑材料的成本和可持续性,选择既能满足产品需求又能够符合环保要求的材料。
综上所述,材料对设计的影响是多方面的,它直接影响着产品的外观、性能、成本和可持续性。
在产品设计过程中,设计师需要充分了解不同材料的特性,选择合适的材料,以确保产品能够达到最佳的设计效果。
只有充分发挥材料的特性,才能设计出优秀的产品。
设计美学-材料之美

设计美学-材料之美
材料是设计中至关重要的一部分,材料的选择、质量和使用方式可以直接影响到设计的美学体验。
以下是关于材料在设计中的美学:
1. 材料的触感和质感
材料的触感和质感是设计中重要的考虑因素。
比如,皮革、毛绒等舒适的材料,可以为设计增添温暖和舒适的氛围,而金属、石头等硬朗的材料则可以创造出富有力量感的设计气息。
2. 材料的颜色和纹理
材料的颜色和纹理也是设计中重要的考虑因素。
颜色可以影响设计的整体调性,而不同的纹理可以为设计增添层次感和立体感。
例如,木材的天然纹理可以为设计增加温暖和自然感。
3. 材料的适用界限
不同的材料适用界限不同,例如有些材料只适合在室内使用,而有些材料则适合在户外使用。
如果选择了不合适的材料,会导致设计在实际使用中存在问题,影响美学体验。
4. 材料的可持续性
在现代设计中,可持续性已成为一项重要的考虑因素,材料的可持续性也需要考虑。
选择环保和可再生的材料可以为设计增
加绿色元素,展现出设计的责任感和美学价值。
综上所述,材料是设计中不可或缺的一部分,它对设计的美学体验产生着重要的影响。
因此,在设计中应该充分考虑不同材料的特点和需求,选用适合的材料才能创造出令人满意的美学体验。
ui设计的发展历程

ui设计的发展历程
1.早期UI设计:早期的UI设计主要关注用户界面的易用性和
可视化效果。
这些设计师通常会使用简单的颜色、字体和布局来创建用户界面,以尽可能地减少用户的认知负荷并帮助用户完成任务。
2.响应式设计:随着移动设备的普及,UI设计逐渐开始关注
跨平台和响应式设计。
这种设计方法旨在确保用户界面在不同的屏幕尺寸和设备上都能够自适应,并提供一致的用户体验。
3.平面设计:平面设计是一种简化的设计风格,它强调简洁、
明确和现代感。
通过使用简单的形状、明亮的颜色和大量的空白间隙,平面设计使用户界面看起来更加清晰和易于理解。
4.材料设计:材料设计是由谷歌公司推出的一种设计规范,旨
在为移动和网络应用程序创建一致和直观的用户界面。
材料设计的特点是运用现实世界的物理特性,如阴影、层次和运动,以增强用户界面的真实感和可视化效果。
5.交互设计:随着用户对数字产品的期望越来越高,交互设计
开始成为UI设计的重要组成部分。
交互设计关注用户与界面
的互动方式,并通过合适的动画、过渡和反馈来提升用户体验。
6.数据驱动设计:数据驱动设计是一种以数据为基础的UI设
计方法。
通过分析用户数据和行为,设计师可以更好地了解用户需求和偏好,并根据这些信息进行界面设计和优化。
7.全息设计:全息设计是一种使用增强现实(AR)和虚拟现实(VR)技术的设计方法。
通过将数字内容与现实世界相结合,全息设计可以提供更加身临其境的用户体验,并为用户提供与界面进行更直接、更沉浸式的互动。
材料工程作业设计方案范本
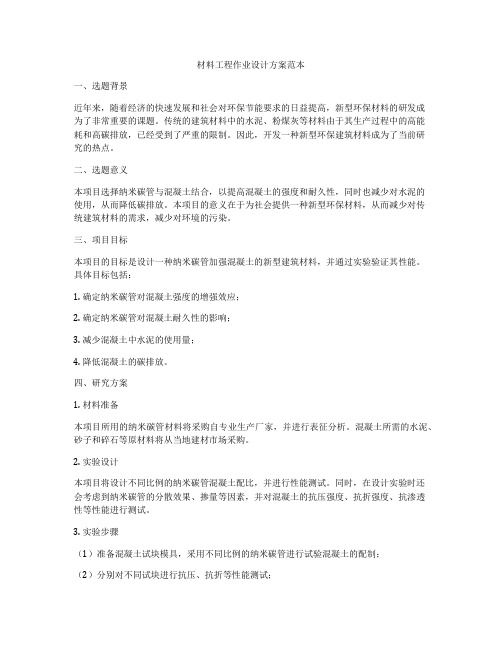
材料工程作业设计方案范本一、选题背景近年来,随着经济的快速发展和社会对环保节能要求的日益提高,新型环保材料的研发成为了非常重要的课题。
传统的建筑材料中的水泥、粉煤灰等材料由于其生产过程中的高能耗和高碳排放,已经受到了严重的限制。
因此,开发一种新型环保建筑材料成为了当前研究的热点。
二、选题意义本项目选择纳米碳管与混凝土结合,以提高混凝土的强度和耐久性,同时也减少对水泥的使用,从而降低碳排放。
本项目的意义在于为社会提供一种新型环保材料,从而减少对传统建筑材料的需求,减少对环境的污染。
三、项目目标本项目的目标是设计一种纳米碳管加强混凝土的新型建筑材料,并通过实验验证其性能。
具体目标包括:1. 确定纳米碳管对混凝土强度的增强效应;2. 确定纳米碳管对混凝土耐久性的影响;3. 减少混凝土中水泥的使用量;4. 降低混凝土的碳排放。
四、研究方案1. 材料准备本项目所用的纳米碳管材料将采购自专业生产厂家,并进行表征分析。
混凝土所需的水泥、砂子和碎石等原材料将从当地建材市场采购。
2. 实验设计本项目将设计不同比例的纳米碳管混凝土配比,并进行性能测试。
同时,在设计实验时还会考虑到纳米碳管的分散效果、掺量等因素,并对混凝土的抗压强度、抗折强度、抗渗透性等性能进行测试。
3. 实验步骤(1)准备混凝土试块模具,采用不同比例的纳米碳管进行试验混凝土的配制;(2)分别对不同试块进行抗压、抗折等性能测试;(3)在混凝土断裂后进行纳米碳管的分析,观察其在混凝土中的分布情况。
4. 实验结果分析通过对实验数据的分析和对比,得到纳米碳管对混凝土性能的影响规律,并结合纳米碳管的分散效果、掺量等因素分析其原因。
五、预期成果通过本项目的研究,预期达到以下成果:1. 确定纳米碳管对混凝土强度的增强效应;2. 确定纳米碳管对混凝土耐久性的影响;3. 减少混凝土中水泥的使用量;4. 降低混凝土的碳排放。
六、进度安排本项目的进度安排如下:1. 材料准备和实验设计阶段:2个月;2. 实验步骤和数据收集阶段:3个月;3. 实验结果分析和论文撰写阶段:2个月。
室内设计材料分析

室内设计材料分析室内设计材料是室内设计中不可或缺的一部分。
选择适合的材料能够为室内空间增添美感和舒适度。
然而,随着科技的不断发展和人们对环境友好的日益重视,现代室内设计材料种类繁多、性能多样,选择合适的材料变得更为关键。
本文将对一些常见的室内设计材料进行分析,并介绍其特点和应用场景。
1.木材:木材是一种传统而常见的室内设计材料。
它具有自然的美感和温暖的触感,可以用于地板、家具和墙面等。
一些常见的木材种类包括橡木、松木和柚木。
木材可以根据需求进行各种不同的处理,例如烘干、刮痕、染色和涂漆等,以满足不同的设计风格要求。
2.石材:石材是一种坚固耐用的室内设计材料。
大理石是最常见的石材之一,它具有高贵典雅的外观,常用于地板、墙面和台面等。
花岗岩和石英石也是常用的石材种类,它们具有坚固的性能和丰富的纹理,适用于厨房和卫生间等需要耐用材料的区域。
3.瓷砖:瓷砖是一种多功能的室内设计材料。
它可以用于地板、墙面和厨卫区域等。
瓷砖具有多样的颜色和纹理选择,易于清洁和维护。
同时,瓷砖还具有耐磨、防潮、防火和耐腐蚀等优点,可以在室内空间中创造出高品质和持久的效果。
4.玻璃:玻璃是一种透明的室内设计材料,可以用于墙面、门窗和隔断等。
玻璃具有良好的光透性和视觉效果,有助于增加空间感和明亮度。
此外,玻璃还具有隔音、防火和良好的隔热性能等。
不过,玻璃材质相对脆弱,需要注意碰撞和破损等问题。
5.金属:金属是一种现代感十足的室内设计材料。
它可以用于家具、灯具和装饰等。
不锈钢和铝合金是常见的金属材料,它们具有抗腐蚀、耐用和易于清洁的特点。
同时,金属材料还可以通过不同的工艺处理,如抛光、喷涂和喷砂等,以创造出丰富的表面效果。
6.塑料:塑料是一种轻巧和可塑性强的室内设计材料。
它可以用于家具、灯具和配件等。
塑料具有多种颜色、质地和光泽度的选择,易于成型和加工。
然而,由于塑料的环保问题,人们对于选择环保友好的塑料材料也日益关注。
综上所述,室内设计材料是室内设计中重要的一环。
无机结合料稳定材料配合比设计

无机结合料稳定材料配合比设计无机结合料在稳定材料配合比设计中发挥着重要的作用。
首先,无机结合料的选择将直接影响材料的性能和稳定性。
不同的无机结合料具有不同的化学和物理性质,因此在配合比设计中,需要根据具体的使用要求选择合适的无机结合料。
例如,在需要高强度的应用中,可以选择高强度的水泥作为无机结合料;而在需要耐久性的应用中,可以选择耐久性较好的石灰作为无机结合料。
稳定材料配合比设计需要考虑无机结合料与其他组分的相互作用。
无机结合料与其他组分(如骨料、添加剂等)之间的相互作用将直接影响材料的稳定性和性能。
在配合比设计中,需要考虑无机结合料与其他组分的相容性,以确保材料的稳定性和性能。
例如,合理选择无机结合料的粒径分布可以提高材料的密实性和抗渗性。
无机结合料的用量也是稳定材料配合比设计中需要考虑的因素之一。
过高或过低的无机结合料用量都会影响材料的性能和稳定性。
过高的用量会导致材料过于坚硬,缺乏柔韧性,容易发生开裂和变形;而过低的用量则会导致材料的强度和稳定性不足。
因此,在配合比设计中,需要根据具体的使用要求和无机结合料的特性,合理确定无机结合料的用量。
在稳定材料配合比设计中,还需要考虑无机结合料的硬化时间和早期强度发展。
无机结合料的硬化时间和早期强度发展对材料的施工和使用具有重要的影响。
过长的硬化时间会延长施工周期,而过快的早期强度发展则会影响施工的连续性和质量。
因此,在配合比设计中,需要根据具体的使用要求和施工条件,合理调整无机结合料的配合比,以控制硬化时间和早期强度发展。
无机结合料在稳定材料配合比设计中起着至关重要的作用。
合理选择无机结合料、考虑其与其他组分的相互作用、调整用量和控制硬化时间和早期强度发展,都是保证材料性能和稳定性的关键。
在实际工程中,稳定材料配合比设计需要综合考虑各种因素,并根据具体情况进行调整,以获得理想的效果。
通过科学的配合比设计,可以提高材料的性能和稳定性,满足不同的使用要求。
新型材料研发的思路与技术

新型材料研发的思路与技术随着科技的不断发展,新型材料的研发成为了一个备受关注的领域。
新型材料追求的是更高的性能和更绿色的生产方式,同时还具备了更加广阔的应用前景。
本文将从材料设计、制备和性能等方面入手,论述新型材料研发的思路和技术。
一、从材料设计入手新型材料的研发首先需要进行材料设计。
传统的材料设计往往采用实验设计和试错法,这种方法的缺点在于需要耗费大量时间和资源来不断试验,同时也存在误差的问题。
因此,现代材料设计更加注重理论预测和模拟计算,利用计算机模拟可以预测新材料的物理和化学性质,为后续实验提供指导。
在材料设计中,需要考虑的因素有很多,如材料的组成、结构、配位方式、电子结构等,这些因素需要通过计算机模拟得出最佳的组合方式。
因此,材料设计需要具备科学严谨的理论基础和先进的计算力量。
二、从材料制备入手材料设计完成后,需要进行材料的制备。
材料制备是新型材料研发的重要环节,也是最核心的技术之一。
既要满足设计考虑,又要考虑可制备性和大规模生产性。
传统的材料制备常采用化学合成法或机械合金化法,然而这些方法由于产生的废水或危险废物等对环境的污染较大,不符合可持续发展要求。
因此,现代材料制备需要采用更为环保的方法,如绿色化学合成法、溶胶-凝胶法等。
同时,需要考虑制备工艺的可重复性、材料品质的稳定性和质量控制等问题。
新型材料的制备需要将材料设计转化为工程制造,因此制备技术的进步是新型材料产业化的重要抓手。
三、从材料性能入手新型材料的性能是其产业化应用的关键。
在材料性能研究中,需要考虑的因素包括力学性能、光学性能、热学性能、化学性能等等。
传统的性能测试方式多为单一性质的测试,无法全面评估材料的性能。
因此,现代材料性能测试常采用多维度的测试手段,如XRD分析、扫描电镜观察、热分析、红外光谱、拉伸试验等。
同时,需要通过理论模拟手段,预测材料在实际应用中的性能。
实验和理论相结合可以更为全面地评价新型材料的性能,为产业化应用提供科学依据。
无机结合料稳定材料配合比设计

无机结合料稳定材料配合比设计一、无机结合料的特点和应用无机结合料是一类由无机材料制成的胶凝材料,具有很高的强度和耐久性。
无机结合料常见的有水泥、石膏、石灰等。
这些材料在建筑、道路、桥梁等工程中广泛应用,是保障结构安全和稳定性的关键因素。
二、材料配合比的重要性材料配合比是指在一定体积或质量比例下,各种材料按照一定的配比进行混合。
合理的材料配合比能够保证结构的性能和使用寿命。
在设计中,合理的配合比可以提高材料的强度、耐久性和施工性能,并减少材料的浪费和成本。
三、无机结合料稳定材料配合比的设计原则1. 综合考虑材料性能:不同的无机结合料具有不同的物理化学性质,因此在设计配合比时需要综合考虑各种材料的性能差异,使其相互协调,达到最佳的配合效果。
2. 确定强度要求:根据工程的需求和使用环境,确定结构的强度要求,以此为基础进行配合比的设计。
同时考虑结构的安全性和经济性,避免过度配比导致材料的浪费。
3. 考虑施工性能:在设计配合比时,还需要考虑无机结合料的施工性能,包括流动性、硬化时间、抗渗性等。
合理的配合比可以提高施工的效率和质量。
4. 考虑环境因素:无机结合料在使用过程中会受到环境因素的影响,如温度、湿度、酸碱等。
在设计配合比时,需要考虑这些因素对材料性能的影响,并做出相应的调整。
5. 进行试验验证:配合比设计完成后,需要进行试验验证,以确保设计的可行性和合理性。
通过试验可以评估材料的性能和结构的稳定性,并对配合比进行进一步优化。
以水泥为无机结合料为例,设计一个适用于路面铺设的配合比。
首先根据工程要求确定强度等级和材料性能要求。
然后选择合适的骨料、矿粉和掺合料,根据其性能参数和实验数据,通过试验确定最佳的配合比。
在设计过程中,需要综合考虑水泥的含水量、初始硬化时间、强度发展规律等因素。
同时还需要考虑骨料的粒径、含水率、表面性状等因素,以及掺合料的掺量比例和掺合效果。
通过试验验证,可以评估设计的配合比的强度、耐久性和施工性能。
复合材料丢层设计-概述说明以及解释
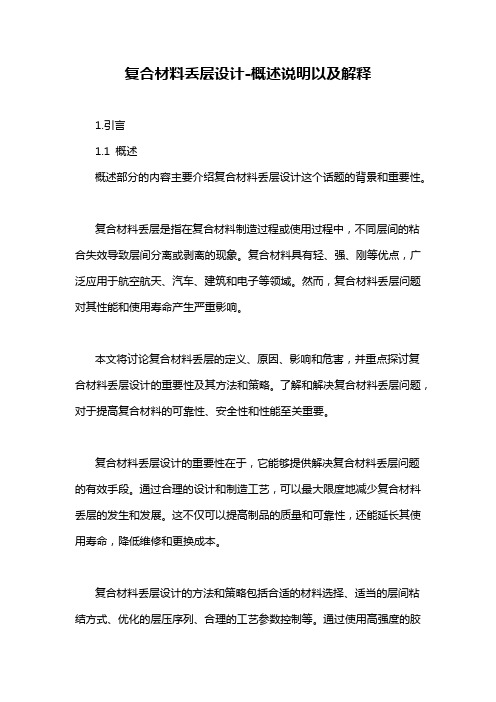
复合材料丢层设计-概述说明以及解释1.引言1.1 概述概述部分的内容主要介绍复合材料丢层设计这个话题的背景和重要性。
复合材料丢层是指在复合材料制造过程或使用过程中,不同层间的粘合失效导致层间分离或剥离的现象。
复合材料具有轻、强、刚等优点,广泛应用于航空航天、汽车、建筑和电子等领域。
然而,复合材料丢层问题对其性能和使用寿命产生严重影响。
本文将讨论复合材料丢层的定义、原因、影响和危害,并重点探讨复合材料丢层设计的重要性及其方法和策略。
了解和解决复合材料丢层问题,对于提高复合材料的可靠性、安全性和性能至关重要。
复合材料丢层设计的重要性在于,它能够提供解决复合材料丢层问题的有效手段。
通过合理的设计和制造工艺,可以最大限度地减少复合材料丢层的发生和发展。
这不仅可以提高制品的质量和可靠性,还能延长其使用寿命,降低维修和更换成本。
复合材料丢层设计的方法和策略包括合适的材料选择、适当的层间粘结方式、优化的层压序列、合理的工艺参数控制等。
通过使用高强度的胶粘剂、加强界面黏结、提高固化工艺等手段,可以有效防止复合材料的丢层问题。
另外,合理的结构设计、优化的应力分布以及可靠的品质控制也是确保复合材料丢层设计成功的关键。
通过深入研究和应用合理的复合材料丢层设计方法,可以克服复合材料丢层问题带来的困扰,提高产品的性能和可靠性,满足现代工业的要求。
本文将对这一问题进行全面的剖析和探讨,希望能为相关领域的研究者和工程师提供一些有益的参考和指导。
1.2 文章结构:本文将按照以下结构进行讨论复合材料丢层设计:1. 引言部分:首先,我们会对复合材料丢层设计的背景和意义进行概述,介绍复合材料丢层问题的重要性和影响。
同时,我们也会给出本文的目的,即通过深入分析复合材料丢层的定义、原因、影响等方面,来探讨有效的丢层设计方法和策略。
2. 正文部分:其次,我们会详细介绍复合材料丢层的定义和原因。
在这一部分,我们将解释什么是复合材料丢层,并列举可能导致丢层的一些常见原因,如接触问题、粘结问题、工艺问题等等。
包材设计基础知识点

包材设计基础知识点包材设计是指在产品包装的过程中,为了满足产品保护、运输和美观等要求所进行的材料选择和设计方案的制定。
包材设计直接关系到产品的质量和形象,是包装行业中至关重要的环节。
本文将介绍一些包材设计的基础知识点。
一、包材的选择选择适合的包材是包材设计的首要任务。
包材的选择应基于以下几个因素:1. 产品的性质:不同的产品有不同的需求,比如食品类产品对于材料的要求是无毒、无异味的,而电子产品对于防静电性能有较高的要求。
2. 运输方式:包材设计需要考虑产品的运输方式,如气运、海运还是陆运。
不同的运输方式对包材的耐力、防震性能及尺寸要求都不同。
3. 产品的保质期:产品的保质期长短也会对包材的选择产生影响,如需长期保存的产品可能需要耐候性较强的材料。
4. 目标消费人群:消费者的喜好和购买习惯也会对包材的选择产生影响,如某些高端产品需要使用高质感的包材来提升其档次感。
二、包材的外观设计包材的外观设计是包材设计中非常重要的一环,它直接关系到产品在市场上的形象和吸引力。
以下是一些常见的包材外观设计要点:1. 标志和品牌信息:在包材的设计中应突出产品的品牌信息,如标志、商标和品牌名等,使消费者能够迅速辨认出产品。
2. 色彩的运用:色彩可以传达产品的感觉和特点,如食品类产品通常运用鲜艳的颜色来增加食欲,而药品类产品通常使用清淡的颜色来表达安全感。
3. 图案和图像:图案和图像可以增加包材的吸引力和美观度,如使用产品相关的图案或独特的图像来吸引消费者的注意。
4. 字体和文字信息:在包材设计中,字体的选择和文字信息的排版需要注意简洁易读,同时符合产品的定位和风格。
三、包材的结构设计包材的结构设计是为了保护产品并方便使用。
以下是一些常见的包材结构设计要点:1. 增加结构的稳定性:在包材的设计中,应增加包材的结构稳定性,以保护产品在运输过程中不受损坏。
2. 提供易于打开和关闭的方式:包材设计应考虑到消费者的使用体验,提供易于打开和关闭的方式,使消费者能够方便地使用产品。
产品设计体现材料的美的例子

产品设计体现材料的美的例子
产品设计中,材料的选择和应用能够直接影响到产品的美感。
以下是一些体现材料美的例子:
1. 木材,木材作为一种传统的材料,具有自然的纹理和质感,
能够给人一种温暖和舒适的感觉。
在家具设计中,使用优质的木材
可以增加产品的质感和高级感。
2. 金属,金属材料如不锈钢、铝合金等常用于现代产品设计中。
金属材料的光泽和冷硬感能够赋予产品现代感和科技感。
例如,手机、笔记本电脑等电子产品常采用金属外壳,使其看起来更加精致
和高档。
3. 玻璃,玻璃材料透明、光滑的特性能够给产品带来轻盈和通
透的感觉。
在灯具、餐具等产品设计中,采用玻璃材料可以增加产
品的精致感和艺术感。
4. 塑料,塑料材料具有多样性和可塑性,能够实现各种形状和
颜色的设计。
在家居用品、玩具等产品中,采用塑料材料可以实现
丰富多彩的外观设计。
5. 纺织品,纺织品如布料、皮革等常用于家居装饰和服装设计中。
不同纹理和颜色的纺织品能够带来丰富的触感和视觉效果,增加产品的柔软度和舒适度。
6. 石材,石材材料如大理石、花岗岩等常用于建筑和家居设计中。
石材的天然纹理和质感能够赋予产品高雅和稳重的氛围。
7. 陶瓷,陶瓷材料常用于餐具、装饰品等产品设计中。
陶瓷的光泽和质感能够增加产品的艺术气息和精致感。
以上只是一些例子,产品设计中材料美的体现还有很多其他方面,如材料的质量、可持续性、环保性等也是需要考虑的因素。
通过合理选择和运用材料,产品设计能够达到更好的美感效果。
材料对设计的影响
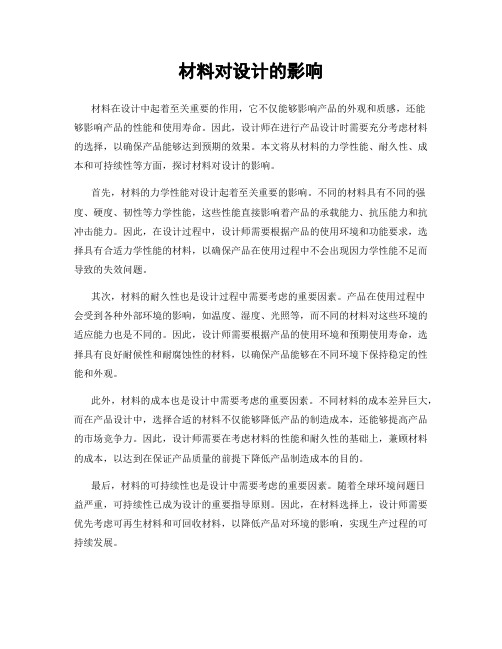
材料对设计的影响材料在设计中起着至关重要的作用,它不仅能够影响产品的外观和质感,还能够影响产品的性能和使用寿命。
因此,设计师在进行产品设计时需要充分考虑材料的选择,以确保产品能够达到预期的效果。
本文将从材料的力学性能、耐久性、成本和可持续性等方面,探讨材料对设计的影响。
首先,材料的力学性能对设计起着至关重要的影响。
不同的材料具有不同的强度、硬度、韧性等力学性能,这些性能直接影响着产品的承载能力、抗压能力和抗冲击能力。
因此,在设计过程中,设计师需要根据产品的使用环境和功能要求,选择具有合适力学性能的材料,以确保产品在使用过程中不会出现因力学性能不足而导致的失效问题。
其次,材料的耐久性也是设计过程中需要考虑的重要因素。
产品在使用过程中会受到各种外部环境的影响,如温度、湿度、光照等,而不同的材料对这些环境的适应能力也是不同的。
因此,设计师需要根据产品的使用环境和预期使用寿命,选择具有良好耐候性和耐腐蚀性的材料,以确保产品能够在不同环境下保持稳定的性能和外观。
此外,材料的成本也是设计中需要考虑的重要因素。
不同材料的成本差异巨大,而在产品设计中,选择合适的材料不仅能够降低产品的制造成本,还能够提高产品的市场竞争力。
因此,设计师需要在考虑材料的性能和耐久性的基础上,兼顾材料的成本,以达到在保证产品质量的前提下降低产品制造成本的目的。
最后,材料的可持续性也是设计中需要考虑的重要因素。
随着全球环境问题日益严重,可持续性已成为设计的重要指导原则。
因此,在材料选择上,设计师需要优先考虑可再生材料和可回收材料,以降低产品对环境的影响,实现生产过程的可持续发展。
综上所述,材料对设计的影响是多方面的,它直接影响着产品的外观、性能、成本和可持续性。
因此,在产品设计过程中,设计师需要充分考虑材料的选择,以确保产品能够达到预期的效果,同时也能够在市场上获得成功。
材料设计值和标准值
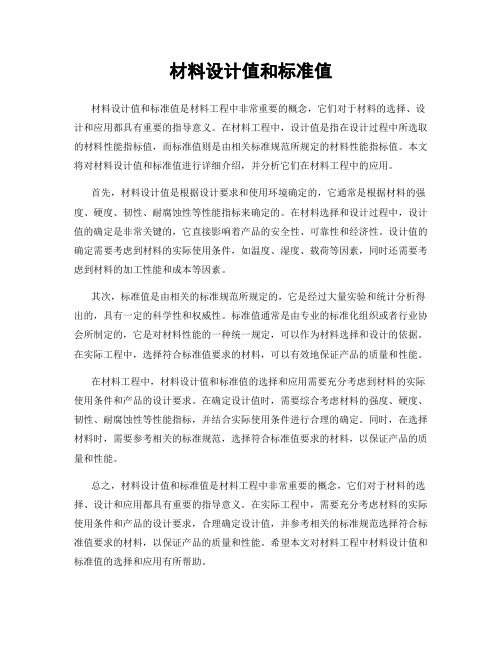
材料设计值和标准值材料设计值和标准值是材料工程中非常重要的概念,它们对于材料的选择、设计和应用都具有重要的指导意义。
在材料工程中,设计值是指在设计过程中所选取的材料性能指标值,而标准值则是由相关标准规范所规定的材料性能指标值。
本文将对材料设计值和标准值进行详细介绍,并分析它们在材料工程中的应用。
首先,材料设计值是根据设计要求和使用环境确定的,它通常是根据材料的强度、硬度、韧性、耐腐蚀性等性能指标来确定的。
在材料选择和设计过程中,设计值的确定是非常关键的,它直接影响着产品的安全性、可靠性和经济性。
设计值的确定需要考虑到材料的实际使用条件,如温度、湿度、载荷等因素,同时还需要考虑到材料的加工性能和成本等因素。
其次,标准值是由相关的标准规范所规定的,它是经过大量实验和统计分析得出的,具有一定的科学性和权威性。
标准值通常是由专业的标准化组织或者行业协会所制定的,它是对材料性能的一种统一规定,可以作为材料选择和设计的依据。
在实际工程中,选择符合标准值要求的材料,可以有效地保证产品的质量和性能。
在材料工程中,材料设计值和标准值的选择和应用需要充分考虑到材料的实际使用条件和产品的设计要求。
在确定设计值时,需要综合考虑材料的强度、硬度、韧性、耐腐蚀性等性能指标,并结合实际使用条件进行合理的确定。
同时,在选择材料时,需要参考相关的标准规范,选择符合标准值要求的材料,以保证产品的质量和性能。
总之,材料设计值和标准值是材料工程中非常重要的概念,它们对于材料的选择、设计和应用都具有重要的指导意义。
在实际工程中,需要充分考虑材料的实际使用条件和产品的设计要求,合理确定设计值,并参考相关的标准规范选择符合标准值要求的材料,以保证产品的质量和性能。
希望本文对材料工程中材料设计值和标准值的选择和应用有所帮助。
超材料的设计和制备方法及其应用
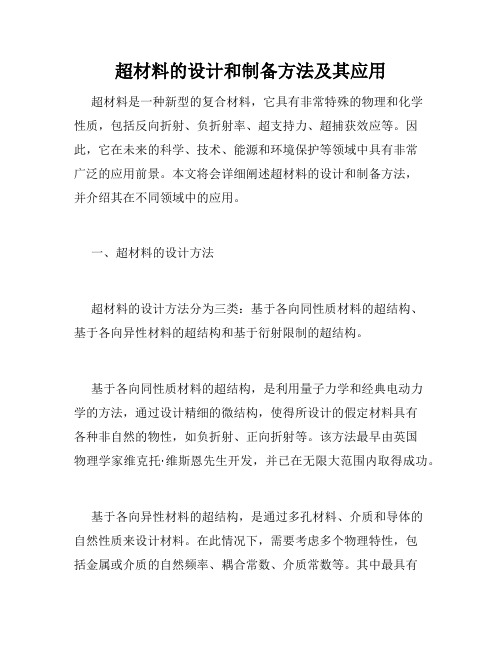
超材料的设计和制备方法及其应用超材料是一种新型的复合材料,它具有非常特殊的物理和化学性质,包括反向折射、负折射率、超支持力、超捕获效应等。
因此,它在未来的科学、技术、能源和环境保护等领域中具有非常广泛的应用前景。
本文将会详细阐述超材料的设计和制备方法,并介绍其在不同领域中的应用。
一、超材料的设计方法超材料的设计方法分为三类:基于各向同性质材料的超结构、基于各向异性材料的超结构和基于衍射限制的超结构。
基于各向同性质材料的超结构,是利用量子力学和经典电动力学的方法,通过设计精细的微结构,使得所设计的假定材料具有各种非自然的物性,如负折射、正向折射等。
该方法最早由英国物理学家维克托·维斯恩先生开发,并已在无限大范围内取得成功。
基于各向异性材料的超结构,是通过多孔材料、介质和导体的自然性质来设计材料。
在此情况下,需要考虑多个物理特性,包括金属或介质的自然频率、耦合常数、介质常数等。
其中最具有代表性的是超材料的电磁特性,这种特性被用来研究超材料及其性质与设计。
基于衍射限制的超结构,是利用超材料中的障碍物和人造结构,在电场和磁场中所产生的束缚能和相互作用力中提供微結构效应。
例如,超材料可以用如折射、透射和反射等宏观物理现象处理电磁波,从而实现信号的方向或波长的选择。
二、超材料的制备方法超材料的制备方法有很多,根据不同的应用范围和研究对象,采用的方法也不相同。
本文将介绍几种常见的方法。
1. 电化学沉积法:该方法是利用电化学沉积的原理,把金属离子沉积到悬浮液中的制成规定的杆、球、圆形等不同尺寸和形状的超材料。
该方法具有制备速度快、成本低、尺寸精度高等特点。
2. 溶胶凝胶法:该方法是将金属醇盐溶液灌入玻璃纤维等多孔介质材料中的制成超材料。
该方法具有制备晶体质量高、抗多一质量高等特点。
3. 热爆炸法:该方法是利用高能量的热冲击波来实现超材料制备的,其特点是速度快、高精度、好控制等。
4. 聚簇反应法:该方法是利用纳米材料反应的过程来制备超材料的一种方法。
聚合物材料分子设计与模拟研究
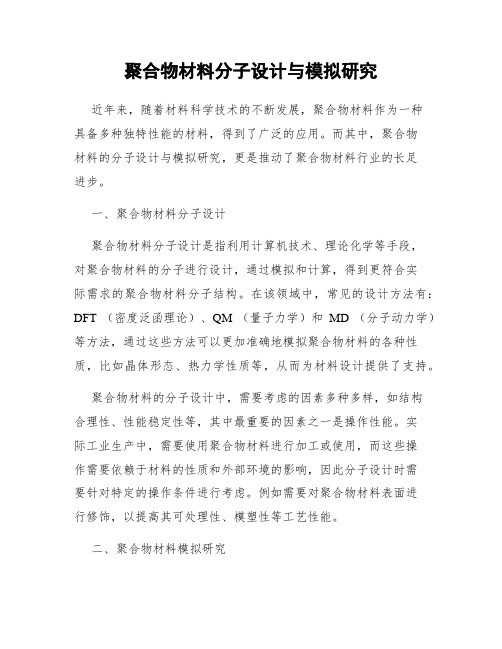
聚合物材料分子设计与模拟研究近年来,随着材料科学技术的不断发展,聚合物材料作为一种具备多种独特性能的材料,得到了广泛的应用。
而其中,聚合物材料的分子设计与模拟研究,更是推动了聚合物材料行业的长足进步。
一、聚合物材料分子设计聚合物材料分子设计是指利用计算机技术、理论化学等手段,对聚合物材料的分子进行设计,通过模拟和计算,得到更符合实际需求的聚合物材料分子结构。
在该领域中,常见的设计方法有:DFT (密度泛函理论)、QM (量子力学)和MD (分子动力学)等方法,通过这些方法可以更加准确地模拟聚合物材料的各种性质,比如晶体形态、热力学性质等,从而为材料设计提供了支持。
聚合物材料的分子设计中,需要考虑的因素多种多样,如结构合理性、性能稳定性等,其中最重要的因素之一是操作性能。
实际工业生产中,需要使用聚合物材料进行加工或使用,而这些操作需要依赖于材料的性质和外部环境的影响,因此分子设计时需要针对特定的操作条件进行考虑。
例如需要对聚合物材料表面进行修饰,以提高其可处理性、模塑性等工艺性能。
二、聚合物材料模拟研究聚合物材料模拟研究旨在利用计算机技术,模拟聚合物材料分子的行为,探究其热力学性质、力学性质、物理性质等相关问题。
这种研究方法可以为实验研究提供指导,节约研究成本,提高研究效率。
在聚合物材料模拟研究中,有两种常用的方法:一种是分子动力学模拟(Molecular Dynamics,MD);另一种是Monte Carlo (MC)模拟。
两种方法各有优缺点,选择何种模拟方法应根据模拟目的而定。
在密度泛函理论等计算机软件的赋能下,MD和MC等方法的性能得到了极大的提升,大大推进了聚合物材料的研究进程。
聚合物材料模拟研究可得到聚合物材料分子的结构、动力学及物理性质,研究聚合物材料在不同条件下的行为规律,探究聚合物材料的应用前景。
此外,还可以透过计算机模拟,了解聚合物材料在不同环境下的响应行为,并据此优化制造工艺。
新材料中的多尺度结构设计与制备

新材料中的多尺度结构设计与制备随着科学技术的不断进步和发展,新材料逐渐成为了各行各业的重要组成部分。
在新材料的设计与制备中,多尺度结构的应用日益广泛。
多尺度结构是指材料中存在着不同尺度的物理结构,从微观到宏观都有。
这些结构对材料的性能有着重要影响,因此,在新材料的研究中,多尺度结构设计与制备已经成为一项非常重要的课题。
多尺度结构的设计涉及多个层面,包括材料的微观结构、介观结构和宏观结构。
其中,微观结构是指材料的最小组成单位,包括原子、分子、晶粒等。
介观结构是指由微观结构构成的结构单元,如孪生晶、晶界等,它们直接决定了材料的力学和物理性质。
而宏观结构是指材料的整体形态,包括材料的基本形状、尺寸、厚度等。
在多尺度结构的设计中,微观结构的控制是非常关键的。
如何控制微观结构的形态和大小,决定了材料在介观和宏观尺度上的性质。
目前,有许多方法可以控制微观结构,例如物化方法、生物方法等。
物化方法是指通过物理、化学手段制备材料,其中包括溶液化学元半导体制备、金属气相沉积、球磨等。
而生物方法是指借助生物学的原理制备材料,如仿鱼鳞表面制备超疏水涂层、仿生纤维、仿生小船体系等等。
在设计多尺度结构的同时,制备方法也是非常重要的因素之一。
传统制备方法无法满足多尺度结构的制备需求,因此,新的制备方法需要被开发和探索。
目前,许多新的制备方法已经被应用于新材料的制备中。
例如,通过自组装方法制备的有序孪生晶或半导体品质的材料。
自组装技术通过控制分子间相互作用,使有机分子自组装成具有一定功能的复合材料。
这种方法制备的材料具有高度有序性和细致的结构调控能力,可广泛应用于电子、光电、生物和能源等领域。
同时,虽然自组装技术具备高度的结构控制能力,但目前还无法完全满足多尺度结构的制备需求。
因此,科学家们通过在原有制备方法的基础上做出新的改进和创新来实现多尺度结构的制备。
例如,利用微纳米加工技术制备的三维多尺度结构载体;通过生物结构与化学反应耦合制备的多尺度结构等。
综合材料设计作品及赏析
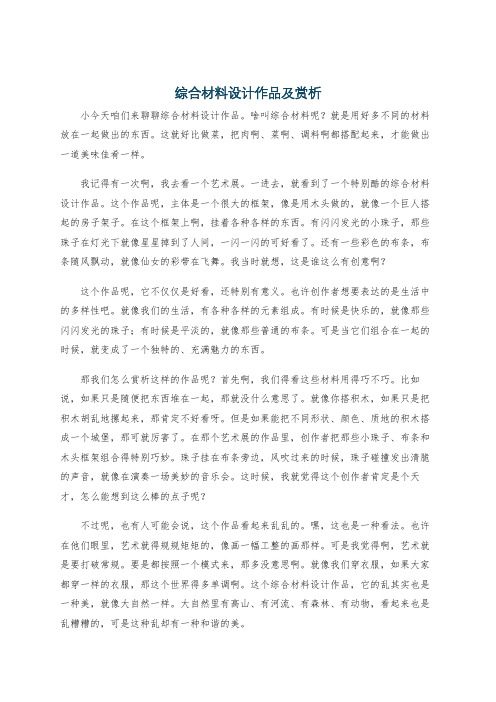
综合材料设计作品及赏析小今天咱们来聊聊综合材料设计作品。
啥叫综合材料呢?就是用好多不同的材料放在一起做出的东西。
这就好比做菜,把肉啊、菜啊、调料啊都搭配起来,才能做出一道美味佳肴一样。
我记得有一次啊,我去看一个艺术展。
一进去,就看到了一个特别酷的综合材料设计作品。
这个作品呢,主体是一个很大的框架,像是用木头做的,就像一个巨人搭起的房子架子。
在这个框架上啊,挂着各种各样的东西。
有闪闪发光的小珠子,那些珠子在灯光下就像星星掉到了人间,一闪一闪的可好看了。
还有一些彩色的布条,布条随风飘动,就像仙女的彩带在飞舞。
我当时就想,这是谁这么有创意啊?这个作品呢,它不仅仅是好看,还特别有意义。
也许创作者想要表达的是生活中的多样性吧。
就像我们的生活,有各种各样的元素组成。
有时候是快乐的,就像那些闪闪发光的珠子;有时候是平淡的,就像那些普通的布条。
可是当它们组合在一起的时候,就变成了一个独特的、充满魅力的东西。
那我们怎么赏析这样的作品呢?首先啊,我们得看这些材料用得巧不巧。
比如说,如果只是随便把东西堆在一起,那就没什么意思了。
就像你搭积木,如果只是把积木胡乱地摞起来,那肯定不好看呀。
但是如果能把不同形状、颜色、质地的积木搭成一个城堡,那可就厉害了。
在那个艺术展的作品里,创作者把那些小珠子、布条和木头框架组合得特别巧妙。
珠子挂在布条旁边,风吹过来的时候,珠子碰撞发出清脆的声音,就像在演奏一场美妙的音乐会。
这时候,我就觉得这个创作者肯定是个天才,怎么能想到这么棒的点子呢?不过呢,也有人可能会说,这个作品看起来乱乱的。
嘿,这也是一种看法。
也许在他们眼里,艺术就得规规矩矩的,像画一幅工整的画那样。
可是我觉得啊,艺术就是要打破常规。
要是都按照一个模式来,那多没意思啊。
就像我们穿衣服,如果大家都穿一样的衣服,那这个世界得多单调啊。
这个综合材料设计作品,它的乱其实也是一种美,就像大自然一样。
大自然里有高山、有河流、有森林、有动物,看起来也是乱糟糟的,可是这种乱却有一种和谐的美。
综合材料设计说明
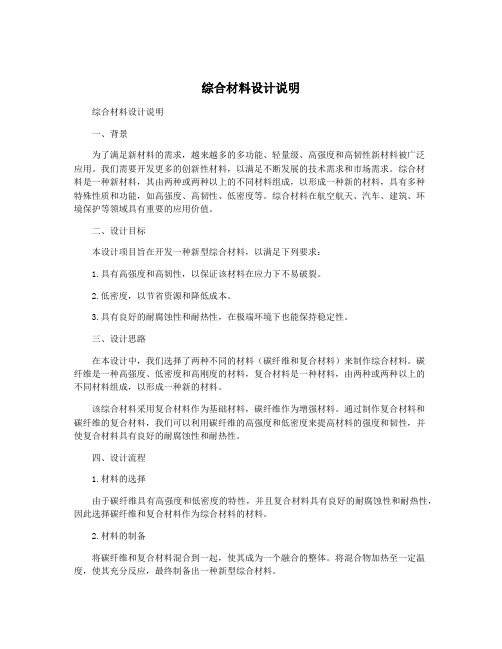
综合材料设计说明综合材料设计说明一、背景为了满足新材料的需求,越来越多的多功能、轻量级、高强度和高韧性新材料被广泛应用。
我们需要开发更多的创新性材料,以满足不断发展的技术需求和市场需求。
综合材料是一种新材料,其由两种或两种以上的不同材料组成,以形成一种新的材料,具有多种特殊性质和功能,如高强度、高韧性、低密度等。
综合材料在航空航天、汽车、建筑、环境保护等领域具有重要的应用价值。
二、设计目标本设计项目旨在开发一种新型综合材料,以满足下列要求:1.具有高强度和高韧性,以保证该材料在应力下不易破裂。
2.低密度,以节省资源和降低成本。
3.具有良好的耐腐蚀性和耐热性,在极端环境下也能保持稳定性。
三、设计思路在本设计中,我们选择了两种不同的材料(碳纤维和复合材料)来制作综合材料。
碳纤维是一种高强度、低密度和高刚度的材料,复合材料是一种材料,由两种或两种以上的不同材料组成,以形成一种新的材料。
该综合材料采用复合材料作为基础材料,碳纤维作为增强材料。
通过制作复合材料和碳纤维的复合材料,我们可以利用碳纤维的高强度和低密度来提高材料的强度和韧性,并使复合材料具有良好的耐腐蚀性和耐热性。
四、设计流程1.材料的选择由于碳纤维具有高强度和低密度的特性,并且复合材料具有良好的耐腐蚀性和耐热性,因此选择碳纤维和复合材料作为综合材料的材料。
2.材料的制备将碳纤维和复合材料混合到一起,使其成为一个融合的整体。
将混合物加热至一定温度,使其充分反应,最终制备出一种新型综合材料。
3.材料性能的测试对制备出来的综合材料进行性能测试,以评估其强度、韧性、密度、耐腐蚀性和耐热性等性能。
四、材料应用该综合材料的应用对航空航天、汽车、建筑和环境保护等领域具有重要的意义。
在航空航天领域,该材料可以用于飞机和火箭等航空器的制造。
它可以大大减轻航空器的重量,提高其速度和耐久性。
在汽车领域,该材料可以用于汽车的制造。
它可以提高汽车的速度和油耗,并使汽车更加环保。
设计方案材料选样

设计方案材料选样
在设计方案中,材料的选样是非常重要的一步。
正确选择材料可以提高设计的质量和可靠性。
以下是我对材料选样的建议:
1. 功能性:根据设计的需要选择符合功能性要求的材料。
例如,如果设计需要抗压性能较好的材料,那么可以选择强度高且耐磨的材料。
2. 可靠性:选择材料时,要考虑到其可靠性和耐久性。
材料应该能够出色地完成设计的要求,并且能够长期稳定地工作。
可以通过查阅该材料的性能指标和实际应用案例来评估其可靠性。
3. 成本效益:在选择材料时,要考虑其成本效益。
并非每个项目都需要使用最昂贵的材料,因此应根据需求和预算来选择合适的材料。
可以对不同材料进行成本效益分析,选择最具性价比的材料。
4. 可持续性:在选样过程中,要考虑材料的可持续性。
选择可以降低对环境影响的材料,例如可回收、可再生或低碳排放的材料。
这有助于减少对自然资源的消耗,并保护生态环境。
5. 美观性:材料的外观也需要考虑在内。
选择材料时,要考虑其外观和设计的整体风格是否相符。
材料的质感、颜色和纹理都会对最终效果产生影响,因此在选样时需要仔细权衡。
6. 可加工性:在选样材料时,还要考虑其可加工性。
材料应该易于加工和组装,以便能够顺利完成设计。
7. 安全性:安全性是材料选样中不可忽视的要素。
选择符合相关安全标准的材料,以确保设计的安全性和可靠性。
综上所述,材料选样是一个综合考虑多个因素的步骤。
通过根据设计的功能性、可靠性、成本效益、可持续性、美观性、可加工性和安全性等方面选择合适的材料,可以提高设计方案的质量和可用性。
- 1、下载文档前请自行甄别文档内容的完整性,平台不提供额外的编辑、内容补充、找答案等附加服务。
- 2、"仅部分预览"的文档,不可在线预览部分如存在完整性等问题,可反馈申请退款(可完整预览的文档不适用该条件!)。
- 3、如文档侵犯您的权益,请联系客服反馈,我们会尽快为您处理(人工客服工作时间:9:00-18:30)。
Effect of Al foils interlayer on microstructures and mechanical properties ofMg–Al butt joints welded by gas tungsten arc welding filling with Zn filler metalFei Liu,Daxin Ren,Liming Liu ⇑Key Laboratory of Liaoning Advanced Welding and Joining Technology,School of Materials Science and Engineering,Dalian University of Technology,Dalian 116024,Chinaa r t i c l e i n f o Article history:Received 24July 2012Accepted 6October 2012Available online 26October 2012Keywords:A.Non-ferrous metals and alloys D.Welding E.FractureF.Microstructurea b s t r a c tGas tungsten arc butt welding of Mg–Al filling with Zn filler metal without and with Al foils in different thicknesses was carried out.Additional Al element was introduced into the fusion zone to accurately modulate microstructure and composition of the welding seam.Microstructures and mechanical proper-ties of the welded joints were examined.Results show that the addition of appropriate quantity of Al ele-ment increases the content of Al-based solid solution in the fusion zone near the Mg base metal.The solid solution can eliminate the stress concentration and hinder crack propagation,so the tensile strengths of the joints are improved.However,the immoderate quantity of Al element will lead to the formation of partially Al-rich zones and deteriorate the mechanical property of the joints.Ó2012Elsevier Ltd.All rights reserved.1.IntroductionMg alloys,the lightest structural metals,are in great potential for application to manufacturing industry due to their quite lower weight ratio,electromagnetic shielding capability and some other unique properties [1].Al alloys are also widely used in many appli-cations such as automobiles,aerospace and electronic industries,because of their attractive mechanical and metallurgical proper-ties,including high specific strength and excellent corrosion resis-tance [2].Thus,welding reliability between Al alloys and Mg alloys is required in order to achieve the application of Mg–Al combina-tion [3].Besides,gas tungsten arc (GTA)welding,as a traditional welding method,is commonly used in industry due to its series of advantages,such as high energy utilization [4]and easy opera-tion [5].In addition,butt welding is widely used in manufacturing structural components,such as 304L stainless steel [6]and 16MnCr5structural steel [7],so using GTA to butt weld Mg and Al alloys shows broad application prospects.In recently years,many welding and jointing technology are proposed to joint Mg/Al dissimilar metal.The Vacuum diffusion bonding was used and the result showed that the diffusion zone of Mg/Al diffusion bonded joint consists of intermetallic com-pounds MgAl,Mg 3Al 2and Mg 2Al 3[8].Laser welding was used and the results indicated that the intermetallic layer formed near interface between two metals significantly degraded the joining strength [9].Soldering was also proposed to joint Mg/Al dissimilar metal and the results showed that the bond strength increased obviously with the increasing of the holding pressure,and the bend strength as high as 22MPa was obtained [10].Yan YB and Zhang ZW proposed to use explosive welding and the results indicated that no intermetallics were formed on the interface,and the shear strength across the bonding interface of AZ31B/7075composite was ca.70MPa [11].Friction stir welding (FSW),as a new joining technology,could decrease the formation of Mg–Al intermetallic compounds (IMCs)and then improved the performance of the joints as reported by Chen and Nakata [12]and Kwon et al.[13].The major problem of Mg/Al welding is the formation of IMCs with a very high hardness and brittleness locating in the fusion zone as an interlayer.These IMCs preferentially act as the source of microcracks in mechanical property tests,and then deteriorate the mechanical property of the joint.Previous research indicated that the formation of Mg–Al IMCs could be avoided by filling Zn metal in the weld seam in GTA welding of Mg and Al alloys [14].By this method,Mg–Al–Zn ternary alloying weld seams were mainly composed of MgZn 2,Zn-based solid solution and Al-based solid solution.And the mixture of Zn-based solid solution and Al-based solid solution (MZAS)separated the continuous layer of MgZn 2IMCs locating in the alloying seams,so the tensile strength of the joint was improved.However,the content of MZAS in the fu-sion zone (FZ)near the Mg base metal is less than that in the center of weld seam and near the Al base metal.Hence,the FZ near the Mg base metal becomes the weakest area of the joint.In the recent work,the additional Al element was added be-tween the Zn filler metal and Mg base metal,which is expected to increase the amount of MZAS near the Mg base metal and sub-sequently improve the tensile strengths of the joints.The influ-ences of Al foils on the microstructure of fusion zone,especially0261-3069/$-see front matter Ó2012Elsevier Ltd.All rights reserved./10.1016/j.matdes.2012.10.012Corresponding author.Tel./fax:+86041184707817.E-mail address:liulm@ (L.Liu).near the Mg base metal,were investigated.In addition,the mechanical properties and the fracture mechanisms of the joints were discussed.2.Experimental procedureThe base materials employed in the experiment were AZ31B Mg alloy with composition of Mg–3Al–1Zn–0.2Mn–0.1Si(wt.%)and 6061Al alloy with composition of Al–1Mg–0.6Si–0.15Cu–0.01Mn (wt.%).The dimensions of the two sheets were50mmÂ100mmÂ2mm.Zinc wire with a purity of99.9%and a diameter of3.5mm was used as thefiller metal.In order to modulate the quantity of Al element,four kinds of Al foils with a purity of 99.9%were used.The four Al foils remain the same size which is 50mmÂ4mm,and their thicknesses are0.1,0.2,0.3and 0.4mm respectively.Prior to welding,the sheets of Mg and Al alloy were machined into120°‘V’-type groove,and the oxide layers on the surface of the Mg and Al sheets were removed.All the speci-mens were ultrasonically cleaned in acetone to remove oil and other contaminants from the specimen surface.The schematic illustration of the GTA butt welding is shown in Fig.1.Al foil was preset on the groove of Mg base metal and Znfiller metal was placed in the groove.The optimized parameters in the experiment were125A GTA welding current,440mm/min welding speed and 15L/min argon shielding gasflow rate.After GTA welding,cross-sections of the specimens were cut and mounted in epoxy resin.The samples were then mechanically polished using120,600,1000and1200grades of SiC grinding pa-pers followed by polishing using a1l m diamond polishing paste. The polished specimens were etched by3%HNO3ethanol solution tension machine(Css-2205)under a travel speed of2mm/min at room temperature,and an average of at least three specimens was taken as the tensile strength.The joint tensile strength is cal-culated according to the equation r s=F/A,where F and r s are the load(N)and the ultimate tensile strength(MPa),respectively;A, calculated by multiplying the width by the thickness of the speci-men,is the cross sectional area(mm2)of the tensile test specimen.3.Results and discussion3.1.Analysis of the surface appearance and tensile strength of the welded seamFig.3shows the surface appearance of the butt welded seam formed between the Mg and Al alloys by GTA welding process.It can be seen that the welded seam width is uniform and no welding defects,such as spatter and undercut.The tensile strengths of the Mg/Al joints are shown in Fig.4.The average tensile strength of the GTA butt welding Mg–Al joints without additional Al element is93MPa.The average tensile strength of the joint increasesfirstly and then decrease as Al foil thickness increases,and reach the maximum value of104MPa with the addition of Al foil which is0.2mm thick.However,the tensile strength of the joint reduces to70MPa when the thickness of Al foil increases to0.4mm.Three typical joints(without additional Al foil,with0.2mm thick Al foil and with0.4mm thick Al foil)are selected to investi-gate the fracture.The joint with0.2mm thick Al foil possesses the maximum tensile strength,while the joint with0.4mm thick AlFig.1.The schematic illustration of the GTA butt welding. Fig.2.Sketch of butt welding tensile test specimens(mm).Fig.3.Surface appearances of the weld seam.Fig.4.Tensile strength of joints with different thicknesses of Al foils.420 F.Liu et al./Materials and Design46(2013)419–425metal.However the joint with0.4mm thick Al foil fractures at the TZ.Therefore the microstructures of the weak areas of the joints are investigated emphatically.Analysis of the microstructure of weak area in the joint microstructures of the weak areas of the typical joints observed,and the distributions of major elements(Al,Mg across the fracture location in the joints were detected investigate the fracture reason.Fig.6gives the back-scattered images and corresponding EPMA line analysis results present-the distributions of major elements(Al,Mg and Zn)in the cross-sections without and with different thickness of Al metal meltsfirst but solidifies last compared with that at the bot-tom of the joint.Consequently,the Mg atoms,at the top of Mg base metal,have more time to diffuse into the FZ.This is the reason why the TZ thickness becomes narrower from the top to the bottom for each joint.The TZ thickness decreases gradually with increasing the thick-ness of Al foil comparing Fig.6a–c,which is resulted from the fact that the Al foil hinders the diffusion of Mg atom to FZ.The line scans results show that the distributions of major elements in the TZ with0.2mm thick Al foil are more uniform than those in other joints,and the uniform composition is benefit for the prop-erty of the joints.To further investigate the failure mechanism of the joints,the microstructures of the weak areas in the joints were observed as shown in Fig.7a–c are SEM images of Mg/Al GTA butt welding joints without Al foil,with0.2and0.4mm thick Al foils,respec-tively.Figs.7d–f are the magnified images of the regions I,II and III in Fig.7a–c,respectively.It can be seen from Figs.7d and e that the grains near the Mg base metal are equiaxed crystals and the grain sizes are approxi-mately3–5l m.Some white phases(pointed by arrow1)are found in Fig.7d,and the white phases are less than those(indicated by arrow3)in Fig.7e.However,as shown in Fig.7f,it is quite difficult to distinguish the sizes of grains in the FZ of the joint with0.4mm thick Al foil and the microstructures of FZ are non-uniform,and some particles and cracks can be found.The reason may be that the molten of Al react with Mg and Zn,and form hard and brittle IMCs due to the addition of too much Al element in weak area of joint.These IMCs are very easy to be the origins of cracks.Mg alloy Mg alloy Mg alloy FZ FZ FZabcFracture location of the joints with different Al foil added:(a)withoutmm Al foil and(c)0.4mm Al foil.Line analyses of TZ and FZ near the Mg base metals:(a)without Al foil,(b)0.2mm Al foil and(c)0.4mmF.Liu et al./Materials and Design46(2013)419–425421from the testing positions denoted in Fig.7are summarized in Ta-ble1.When Mg and Al alloy are weldedfilling with Zn metal without Al foil,the compositions of white phases and gray phases,indicated by arrows1and2in Fig.7d,are shown in Table1.It can be inferred that the principal reactions in the order of their occurrence during the solidification process are[16]:L!MgZn2580 Cð1ÞL!ðAlÞþMgZn2480 Cð2ÞL!ðAlÞþMgZn2þAl6Mg11Zn11þðZnÞ337 Cð3Þ(Al)and(Zn)are representatives of Al-based solid solution and Zn-based solid solution for similarly hereinafter.Therefore,it can be concluded that the white phases are mix-ture of Zn-based solid solution and Al-based solid solution(MZAS)in term of Mg–Al–Zn ternary phase diagram presented in Fig.8. The gray phases are the IMCs of MgZn2and Al6Mg11Zn11according to their element compositions and the solidification process,which are indicated by arrow2in Fig.7d.The sketch of microstructures of the joint without Al foil is shown in Fig.9a.It can be seen that the FZ of the joint is composed of white and gray phases,and the gray phases(IMCs)are separated by the white phases.These hard and brittle IMCs are easy to be the crack origins when the specimens bear tensile stress during the tensile strength test[17].On the contrary,the alloys whose com-positions are approximately to those of MZAS have excellent plas-ticity[18].When the sample bears the tensile stress,the MZAS can eliminate the stress concentration of the crack tip and hinder the crack propagation.For this reason,tensile strength improved sig-nificantly by ameliorating the microstructures in the joint,com-pared with the directly welding of Mg and Al alloy without Zn filler metal[14].The microstructure of the joint near the Mg base metal with 0.2mm Al foil is shown in Fig.7e.It can be seen that the content of gray phase reduces significantly with the addition of Al foil. The welding pool near the Mg base metal precipitates MgZn2pri-marily in the welding process.Due to the addition of Al metal, the several reactions as listed below:L!MgZn2480 Cð4ÞL!ðAlÞþMgZn2380 Cð5ÞL!ðAlÞþMgZn2þðZnÞ280 Cð6Þa b c d e fzone near the Mg base metal:(a)without Al foil,(b)0.2mm Al foil,(c)0.4mm Al foil;(d),(e),(f)are the magnificationTable1The composition of welded joint detected by EPMA.Serial number Percentage composition(at.%)Inference compositionMg Al Zn113.443.142.5MZAS240.27.552.3MgZn2,Al6Mg11Zn113 3.020.776.3MZAS418.4 3.778.0Mg2Zn11,(Zn)529.648.621.8(Al),Al6Mg11Zn11639.414.146.5Al6Mg11Zn11,MgZn2422 F.Liu et al./Materials and Design46(2013)419–425Finally,the FZ near the Mg base metal is comprised of MZAS compounds.The sketch of microstructures of the joint mm Al foil is shown in Fig.9b.Hence,the tensile strengths are improved,compared with those of the jointsfilling metal but without the additional Al element.However,immoderate addition of mation of partial Al-rich zones in the Fig.7f.Due to the excessive content of near the Mg base metal precipitates marily in the solicitation process,andas listed below take place:L!MgZn2560 CL!ðAlÞþMgZn2530 CLþMgZn2!ðAlÞþAl6Mg11Zn11478 Therefore,the partial Al-rich zones areZn11,MgZn2)and Al-based solid solution nary phase diagram and the solidification microstructures of the joint with0.4 Fig.9c.The IMCs are very brittle and hard,Fig.8.Mg–Al–Zn ternary phase diagram.The sketch of microstructure of the joint with different Al foil added:Al foil,(b)0.2mm Al foil and(c)0.4mm Al foil.Comparison microhardness for GTA butt welding without andthickness of Al foil along the transverse Section1mm below topbears the tension stress,these partial Al-rich zones tend to produce cracks as shown in Fig.7f.Similar results are also reported by Mofid et al.[19].Fig.10shows the microhardness distribution of the transverse section of the typical joint along the line1mm below the top sur-face.The microhardness of the joint near the Mg base metal is much higher than other locations no matter without or with addi-tional Al element.In addition,the microhardness of the joint with 0.2mm Al foil is lower than that of without Al foil in the FZ.These results verify that the joint with0.2mm Al foil has more MZAS than that in the joint without Al foil,and the MZAS have excellent plasticity.In the area near the TZ,as the weakest area of the joint, the microhardness of the joint with0.4mm Al foil is much higher than that of the other two joints.This is caused by the formation of many brittle and hard IMCs in partial Al-rich zones[20].Fig.11a–c are the fracture surfaces of the typical joints without Al foil,with0.2mm and0.4mm thick Al foils,respectively.It can be seen that there are some torn ribs and polygonal particles (shown by the black rectangular in Fig.11a)in the fracture surface of the joint with no foil added.But the particles cannot be detected in the fracture surface of the joint added with0.2mm thick Al foil. When the thickness of Al foil is increased to0.4mm,the porosity, indicated by the black arrows as shown in Fig.11c,can be found in the fracture surface of the joint.The reason is that the excessive addition of Al element prevents the full mixture of element in the molten pool in welding process.From the above analysis,it can be concluded that the content of MZAS can be increased by the appropriate addition of Al element, and the properties of the joint are improved.However,the addition of excessive Al element leads to the formation of partial Al-rich zones which are composed of IMCs,such as Al6Mg11Zn11and MgZn2,resulting in reduction in the tensile strength of the joint.4.ConclusionsGTA butt welding of Mg/Alfilling with Znfiller metal without and with different thickness of Al foils are investigated.The major conclusions can be summarized as follows:(1)Magnesium alloy AZ31B and aluminum alloy6061werewelded by GTA weldingfilling with Znfiller metal without and with Al foils in different thickness.The composition and microstructure of the welding seam are accurately mod-ulated by introducing the additional Al into FZ.The TZ and FZ near the Mg base metal are the weak parts of the joints, and these areas are mainly composed of IMCs and a small quantity of MZAS.(2)The content of MZAS near the Mg base metal is increased bythe addition of a critical level of Al element.The MZAS can eliminate the stress concentration and hinder crack propa-gation,and thus improves the tensile strength of the joint.However,the immoderate quantity of Al element leads to the formation of partially Al-rich zones,and subsequently the tensile strength of the joints is reduced.(3)The quantity of additional0.2mm thick Al foil is consideredas an appropriate option for the GTA butt welding of AZ31B Mg alloy to6061Al alloyfilling with Znfiller metal,and the tensile strength of the joint can reach104MPa. AcknowledgementsThe authors gratefully acknowledge the sponsorships from Pro-gram for Changjiang Scholars and Innovative Research Team in University(No.IRT1008)and National Natural Science Funds for Distinguished Young Scholar(51025520).References[1]Schubert E,Klassen M,Zerner I,Walz C,Sepold G.Light-weight structuresproduced by laser beam joining for future applications in automobile and aerospace industry.J Mater Process Technol2001;115:2–8.[2]Liu LM,Liu XJ,Liu SH.Microstructure of laser-TIG hybrid welds of dissimilarMg alloy and Al alloy with Ce as interlayer.Script Mater2006;55:383–6. [3]Somasekharan AC,Murr LE.Microstructures in friction-stir welded dissimilarmagnesium alloys and magnesium alloys to6061–T6aluminum alloy.Mater Charact2004;52:49–64.[4]Kumar Subodh,Shahi AS.Effect of heat input on the microstructure andmechanical properties of gas tungsten arc welded AISI304stainless steel joints.Mater Des 2011;32:3617–23.ab cFracture surface of the joints with different Al foil added:(a)without Al foil,(b)0.2mm Al foil and(c)0.4 424 F.Liu et al./Materials and Design46(2013)419–425[5]Kumar A,Sundarrajan S.Optimization of pulsed TIG welding processparameters on mechanical properties of AA5456aluminum alloy weldments.Mater Des2009;30:1288–97.[6]Bang Hee Seon,Bang Han Sur,Kim You Chul,Oh Ik Hyun.A study onmechanical and microstructure characteristics of the STS304L butt joints using hybrid CO2laser-gas metal arc welding.Mater Des2011;32: 2328–33.[7]Cemil C,Etinkaya,Arabaci U.Flash butt welding application on16MnCr5chainsteel and investigations of mechanical properties.Mater Des 2006;27:1187–95.[8]Liu P,Li YJ,Geng HR,Wang J.A study of phase constitution near the interface ofMg/Al vacuum diffusion bonding.Mater Lett2005;59:2001–5.[9]Borrisutthekul R,Miyashita Y,Mutoh Y.Dissimilar material laser weldingbetween magnesium alloy AZ31B and aluminum alloy A5052-O.Sci Technol Adv Mat2005;6:199–204.[10]Li XR,Liang W,Zhao XG,Zhang Y,Fu XP,Liu FC.Bonding of Mg and Al withMg–Al eutectic alloy and its application in aluminum coating on magnesium.J Alloys Compd2009;471:408–11.[11]Yana YB,Zhang ZW,Shen W,Wang JH,Zhang LK,Chin BA.Microstructure andproperties of magnesium AZ31B–aluminum7075explosively welded composite plate.Mat Sci Eng A–Struct2010;527:2241–5.[12]Chen YC,Nakata K.Friction stir lap joining aluminum and magnesium alloys.Scripta Mater2008;58:433–6.[13]Kwon YJ,Shigematsu I,Saito N.Dissimilar friction stir welding betweenmagnesium and aluminum alloys.Mater Lett2008;62:3827–9.[14]Liu F,Zhang ZD,Liu LM.Microstructure evolution of Al/Mg butt joints weldedby gas tungsten arc with Znfiller metal.Mater Charact2012;69:84–9. [15]Liu CT,Maziasz PJ.Microstructural control and mechanical properties of dual-phase TiAl alloys.Internet1998;6:653–61.[16]Villars P,Prince A,Okamoto H.Handbook of ternary alloy phase diagrams.ASMInternational;1995.[17]Zhao LM,Zhang ZD.Effect of Zn alloy interlayer on interface microstructureand strength of diffusion-bonded Mg–Al joints.Scripta Mater2008;58:283–6.[18]Straumal B,Valiev R,Kogtenkova O,Zieba P,Czeppe T,Bielanska E,et al.Thermal evolution and grain boundary phase transformations in severely deformed nanograined Al–Zn alloys.Acta Mater2008;56:6123–31.[19]Mofid MA,Abdollah-zadeh A,Malek Ghaini F.The effect of water coolingduring dissimilar friction stir welding of Al alloy to Mg alloy.Mater Des 2012;36:161–7.[20]Shang J,Wang KH,Zhou Q,Zhang DK,Huang J,Li GL.Microstructurecharacteristics and mechanical properties of cold metal transfer welding Mg/ Al dissimilar metals.Mater Des2012;34:559–66.F.Liu et al./Materials and Design46(2013)419–425425。