91A1DR24A15R51中文资料
KYORITSU 4105A Digital Earth Resistance Tester 说明书

INSTRUCTION MANUALMODEL 4105A KYORITSU ELECTRICAL INSTRUMENTSWORKS, LTD.CONTENTS1. Safety Precautions (1)2. Features (4)3. Specifications (5)4. Layout Diagram (8)5. Preparation for Measurement (9)5-1 Battery Voltage Check (9)5-2 Connecting Test Probes (9)6. Operating Instructions (9)6-1 Principle of Measurement (9)6-2 Precise Measurement (10)6-3 Simplified Measurement (11)7. Battery Replacement (14)8. Notes on Housing Case & Accessories (15)8-1 Case Lid (15)8-2 How to Fit Strap Belt (15)9. Before Sending for Service (16)10. Service (17)condition in accordance with the following standards.IEC 61010-1Overvoltage CAT III 300V Pollution Degree 2IEC 61010-2-31IEC 61557-1,5IEC 60529(IP54)This instruction manual contains warnings and safety rules which must be observed by the user to ensure safety operation of the instrument and to retain it in safe condition. Therefore, read through these instructions before using the instrument.on the instrument means that the user must refer to themanual for safe operation of the instrument. There are three kinds of the symbol . Read the instructions following each symbol carefully.2. FeaturesMODEL 4105A is an earth resistance tester for testing power distribution lines, in-house wiring system, electrical appliances etc. It also has an earthvoltage range for earth voltage measurement.Measurement can be made even under adverse weather conditions.and the test bar are available.permissible limit.3. Specifications5°C and RH 75% or less)RF field strength = ≤1V/m, total accuracy : specified accuracyRF field strength = 3V/m, total accuracy : specified accuracy +5% of rangeIEC 61010-1Overvoltage CAT III 300V Pollution Degree 2IEC 61010-2-31IEC 61557-1,5IEC 60529(IP54)Average sensingEarth resistance measurementConstant current inverterFrequency : Approx. 820Hz3mAAC Measuring current : 20Ωrange Approx.Operating error (B) is an error obtained within the rated operating conditions, and calculated with the intrinsic error (A), which is an error ofthe instrument used, and the error (Ei) due to variations.A:Intrinsic errorE:Variation due to changing the position1E:Variation due to changing the supply voltage2:Variation due to changing the temperatureE3E:Variation due to series interference voltage4E:Variation due to resistance of the probes and auxiliary earth 5electrode resistance:Variation due to changing the system frequencyE7E:Variation due to changing the system voltage830%)applies.20Ωrange : 5-19.99Ω200Ωrange :20-199.9Ω2000Ωrange : 200-1999Ω3300 times or more( Measure 10Ωfor 5s on 20Ωrange and take a pause for 25s)0 - 40°C, relative humidity 85% or less (no condensation)-20 - 60°C, relative humidity 75% or less (no condensation)9V DC : R6P (SUM-3) x6Earth resistance ranges : 280V AC/DC (10 seconds)Earth voltage range : 300V AC/DC (1 minute)5MΩor more at 500V between the electrical circuit and the housing case3700V AC for one minute between the electrical circuit and the housing case105(L) x 158(W) x 70(D) mmApprox. 550gM-7095Test Leads x 1 setM-8032Auxiliary Earth Spikes x 2M-7127Simplified Measurement Probe x 1 set(with safety alligator clip and flat test bar)M-9084Carrying Case x 1Strap Belt x 1Instruction Manual x 1Battery R6P (SUM-3)x 6q LCD Display w Battery Replacement MarkMeasurement(Green) r Press To Test Buttont Range Selector Switch y Measuring Terminalsu Test Leads i Auxiliary Earth Spikeso Simplified Measurement Probe!0Safety Alligator Clip!1Test BarI between the measurementobject E (earth electrode) and C(current electrode), and findingout the potential difference Vbetween E and P (potentialelectrode).Rx = V / I6-2 Precise Measurement (with Test Probe M-7095)q Test probe connectionStick the auxiliary earth spikes P and C into the ground deeply. They should be aligned at an interval of 5-10m from the earthed equipment under test. Connect the green wire to the earthed equipment under test, the yellow wire to the auxiliary earth spike P and the red wire to the auxiliary earth spike C from terminals E, P and C of the instrument in order.Note : Make sure to stick the auxiliary earth spikes in the moist part of the soil. Give enough water where the spikes have to be stuck into the dry, stony or sandy part of the earth so that it may become moist.In case of concrete, lay the auxiliary earth spike down and water it, or put a wet dustcloth etc. on the spike when making measurement.w Earth Voltage MeasurementSet the range switch to EARTH VOLTAGE position in the condition of q. Earth voltage will be indicated on the display. Make sure that the voltage is 10V or less.When the display reads more than 10V, it may result in excessive errors in earth resistance measurement. To avoid this, make measurement after reducing the voltage by turning off the power supply of the equipment under test etc.e Precise MeasurementSet the range switch to 2000Ωposition and press the test button. LED remains illuminated during testing. Turn the range switch to 200Ωand20Ωwhen the earth resistance is low. This indicated value is the earth resistance of the earthed equipment under test.Note : If the auxiliary earth resistance of auxiliary earth spike C is too high to make measurement, the display reads '...'. Recheck the connection of test leads and the earth resistance of auxiliary earth spike.6-3 Simplified Measurement (with Test Probe M-7127)Use this method when the auxiliary earth spike cannot be stuck. In this method, an existing earth electrode with a low earth resistance, such asa metal water pipe, a common earth of a commercial power supply andan earth terminal of a building, can be used with two-terminal method (E,P).Use the simplified measurement probe attached which has a convenient structure that both the safety alligator clip and the test bar are available.q WiringMake connection as shown in the figure.Note :When the simplified measurement probes are not used, short P and C terminals.w Earth Voltage MeasurementSet the range switch to EARTH VOLTAGE position in the condition of q. Earth voltage will be indicated on the display. Make sure that the voltage is 10V or less.When the display reads more than 10V, it may result in excessive errors in earth resistance measurement. To avoid this, make measurement after reducing the voltage by turning off the power supply of the equipment under test etc.e Simplified MeasurementSet the range switch to 2000Ωposition and press the test button. LEDremains illuminated during testing. Turn the range switch to 200Ωand 20Ωwhen the earth resistance is low. This indicated value is the earth resistance of the earthed equipment under test.Note :If the auxiliary earth resistance of auxiliary earth spike C is too high to make measurement, the display reads'...'. Recheck the connection of each test lead and the earth resistance of auxiliary earth spike.r Simplified Measurement ValueTwo-terminal method is used for simplified measurement. In this method, earth resistance value re of earth electrode connected to terminal P is added to true earth resistance value Rx and shown as an indicated value Re.Re = Rx + reIf the re is known beforehand, true earth resistance value Rx is calculated as follows.Rx = Re --- re7. Battery Replacementq Turn off the instrument and disconnect the test probes from the terminals.w Loosen two screws on the bottom of the instrument and remove the battery cover.e Always replace all six batteries in correct polarity.Battery : R6P (AA dry battery) x6r Put the cover back in place and tighten the two screws.8. Notes on Housing Case & Accessories8-1 Case Lid8-2 How to Fit Strap BeltThe instrument is equipped with a strap belt to suspend from the neck to allow both hands to be used freely for easy and safe operation9. Before Sending for ServiceIf this instrument should fail to operate correctly, return it to your nearest distributor stating the exact nature of the fault. Before returning the instrument follow the trouble-shooting guide shown below.If the instrument does not turn on;Check whether batteries are missing or they are installed incorrect polarity. Note that batteries were not installed in the instrument at the time of shipment.If the display reads '1...' in earth voltage measurement;A voltage exceeding 200V is being applied to the instrument.Halt the measurement immediately, otherwise the instrument may be damaged.If the display reads '...' in normal earth resistance measurement;Stick the auxiliary earth spikes deeper into the earth, or stick them at other locations; orAdd moisture to the part of the earth where C auxiliary earth spike is stuck ( connected with the red wire ); andShort the three test leads and check if the display indicates a value near ' 0.00 '. (See section 6 for details.)If the display reads '...' in simplified earth resistance measurement;Check if the connection to a metal water pipe, a common earth of commercial power supply, etc., is secure; orUse another metal water pipe, common earth of commercial power supply, etc.10. ServiceIf this instrument should fail to operate correctly, return to your nearestdistributors stating the exact nature of the fault.。
艾维亚9和12kVA在线无中断电源系统产品介绍说明书
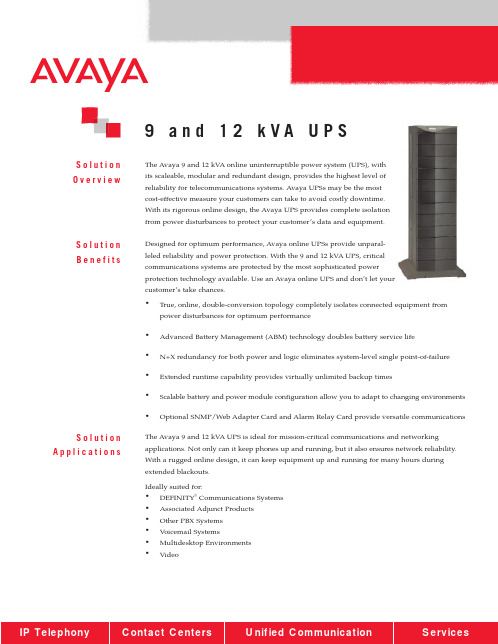
9 a n d 12 k V A U P SThe Avaya 9 and 12 kVA online uninterruptible power system (UPS), with its scaleable, modular and redundant design, provides the highest level of reliability for telecommunications systems. Avaya UPSs may be the most cost-effective measure your customers can take to avoid costly downtime.With its rigorous online design, the Avaya UPS provides complete isolation from power disturbances to protect your customer’s data and equipment.Designed for optimum performance, Avaya online UPSs provide unparal-leled reliability and power protection. With the 9 and 12 kVA UPS, critical communications systems are protected by the most sophisticated powerprotection technology available. Use an Avaya online UPS and don’t let your customer’s take chances.•True, online, double-conversion topology completely isolates connected equipment from power disturbances for optimum performance •Advanced Battery Management (ABM) technology doubles battery service life•N+X redundancy for both power and logic eliminates system-level single point-of-failure •Extended runtime capability provides virtually unlimited backup times•Scalable battery and power module configuration allow you to adapt to changing environments •Optional SNMP/Web Adapter Card and Alarm Relay Card provide versatile communicationsThe Avaya 9 and 12 kVA UPS is ideal for mission-critical communications and networking applications. Not only can it keep phones up and running, but it also ensures network reliability.With a rugged online design, it can keep equipment up and running for many hours during extended blackouts.Ideally suited for:•DEFINITY ®Communications Systems •Associated Adjunct Products •Other PBX Systems •Voicemail Systems•Multidesktop Environments •VideoS o l u t i o n O v e r v i e wS o l u t i o n B e n e f i t sS o l u t i o n A p p l i c a t i o n s。
AT89C51单片机简单介绍

简单的程序
• LOOP: SETB P10; 让P10灯灭 LCALL DELAY; //长跳转指令 (当遇到RET,则回到此下行程
序) CLR P10; //让灯P10亮 LCALL DELAY; AJMP LOOP; //绝对跳转到LOOP
AT89C51
AT89C51是美国ATMEL公司生产的低 电压,高性能CMOS8位单片机,片内含4K bytes的可反复擦写的只读程序存储器和 128bytes的随机存取数据存储器(RAM), 器件采用ATMEL公司的高密度、非易失性 存储技术生产,兼容标准MCS-51指令系统, 片内置通用8位中央处理器(CPU)和flash 存储单元。
FLASH编程和校验时,P1口作为第八位地址接收。
P2口
• P2口:P2口为一个内部上拉电阻的8位双向I/O口, P2口缓冲器可接收,输出4个TTL门电流,当P2 口被写“1”时,其管脚被内部上拉电阻拉高,且 作为输入。并因此作为输入时,P2口的管脚被外 部拉低,将输出电流。这是由于内部上拉的缘故。 P2口当用于外部程序存储器或16位地址外部数据 存储器进行存取时,P2口输出地址的高八位。在 给出地址“1”时,它利用内部上拉优势,当对外 部八位地址数据存储器进行读写时,P2口输出其 特殊功能寄存器的内容。P2口在FLASH编程和校 验时接收高八位地址信号和控制信号。
放大器的输入和输出。该反向放大
器可以配置为片内振荡器。石晶振
荡和陶瓷振荡均可采用。如采用外
部时钟源驱动器件,XTAL2应不接。
有余输入至内部时钟信号要通过一
个二分频触发器,因此对外部时钟
国产ds1991L-F5 参数说明书

SELOCKEY.SOA§ 1,152-bit secure read/write, nonvolatilememory§ Secure memory cannot be decipheredwithout matching 64-bit password§ Memory is partitioned into 3 blocks of 384bits each§ 64-bit password and ID fields for eachmemory block§ 512-bit scratchpad ensures data transferintegrity§ Operating temperature range: -40°C to+70°C§ Over 10 years of data retentionCOMMON Button FEATURES§ Unique, factory-lasered and tested 64-bitregistration number (8-bit family code + 48-bit serial number + 8-bit CRC tester) assures absolute traceability because no two parts are alike§ Multidrop controller for MicroBUS§ Digital identification and information bymomentary contact§ Chip-based data carrier compactly storesinformation§ Data can be accessed while affixed to object § Economically communicates to bus masterwith a single digital signal at 16.3k bits per second§ Standard 16 mm diameter and 1-Busprotocol ensure compatibility with Button family§ Button shape is self-aligning with cup-shaped probes§ Durable stainless steel case engraved withregistration number withstands harsh environments§ Easily affixed with self-stick adhesivebacking, latched by its flange, or locked with a ring pressed onto its rim§ Presence detector acknowledges when readerfirst applies voltageF5 MICROCAN TMAll dimensions shown in millimetersORDERING INFORMATIONTM1991L-F5F5 MicroCanTM1991MultiKey Button TMTM1991 Button DESCRIPTIONThe TM1991 MultiKey Button is a rugged read/write data carrier that acts as three separate electronic keys, offering 1,152 bits of secure, nonvolatile memory. Each key is 384 bits long with distinct 64-bit password and public ID fields (Figure 1). The password field must be matched in order to access the secure memory. Data is transferred serially via the 1-Bus protocol, which requires only a single data lead and a ground return. The 512-bit scratchpad serves to ensure integrity of data transfers to secure memory. Data should first be written to the scratchpad where it can be read back. After the data has been verified, a copy scratchpad command will transfer the data to the secure memory. This process ensures data integrity when modifying the memory. A 48-bit serial number is factory lasered into each TM1991 to provide a guaranteed unique identity which allows for absolute traceability. The family code for the TM1991 is 02h. The durable MicroCan package is highly resistant to environmental hazards such as dirt, moisture and shock. Its compact button-shaped profile is self-aligning with mating receptacles, allowing the TM1991 to be easily used by human operators. Accessories permit the TM1991 to be mounted on plastic key fobs, photo-ID badges, printed-circuit boards or any smooth surface of an object. Applications include secure access control, debit tokens, work-in-progress tracking, electronic travelers and proprietary data.OPERATIONThe TM1991 is accessed via a single data line using the 1-Bus protocol. The bus master must first provide one of the four ROM Function Commands, 1) Read ROM, 2) Match ROM, 3) Search ROM, 4) Skip ROM. These commands operate on the 64-bit lasered ROM portion of each device and can singulate a specific device if many are present on the 1-Bus line as well as indicate to the bus master how many and what types of devices are present. The protocol required for these ROM Function Commands is described in Figure 9. After a ROM Function Command is successfully executed, the memory functions that operate on the secure memory and the scratchpad become accessible and the bus master may issue any one of the six Memory Function Commands specific to the TM1991. The protocol for these Memory Function Commands is described in Figure 5. All data is read and written least significant bit first.64-BIT LASERED ROMEach TM1991 contains a unique ROM code that is 64 bits long. The first eight bits are a 1-Bus family code. The next 48 bits are a unique serial number. The last eight bits are a CRC of the first 56 bits. (Figure 2.) The 1-Bus CRC is generated using a polynomial generator consisting of a shift register and XOR gates as shown in Figure 3. The polynomial is X8 + X5 + X4 + 1. Additional information about the Dallas 1-Bus Cyclic Redundancy Check is available in the Book of TM19xx Button Standards. The shift register bits are initialized to zero. Then starting with the least significant bit of the family code, one bit at a time is shifted in. After the 8th bit of the family code has been entered, then the serial number is entered. After the 48th bit of the serial number has been entered, the shift register contains the CRC value. Shifting in the eight bits of CRC should return the shift register to all zeros.MEMORY FUNCTION COMMANDSThe TM1991 has six device-specific commands. Three scratchpad commands: Write Scratchpad, Read Scratchpad and Copy Scratchpad and three subkey commands: Write Password, Write Subkey and Read Subkey. After the device is selected, the memory function command is written to the TM1991. The command is comprised of three fields, each one byte long. The first byte is the function code field. This field defines the six commands that can be executed. The second byte is the address field. The first six bits of this field define the starting address of the command. The last two bits of this field are the subkey address code. The third byte of the command is a complement of the second byte (Figure 4).TM1991 For the first use, since the passwords actually stored in the device are unknown, the TM1991 needs to be initialized. This is done by directly writing (i. e., not through the scratchpad) the new identifier and password for the selected subkey using the Write Password command. As soon as the new identifier and password are stored in the device, further updates should be done through the scratchpad.MEMORY MAP Figure 1* Each subkey or the scratchpad has its own unique address.64-BIT LASERED ROM Figure 28-Bit CRC Code48-Bit Serial Number8-Bit Family Code (02H) MSB LSB MSB LSB MSB LSB1-BUS CRC GENERATOR Figure 3TM1991 COMMAND STRUCTURE Figure 42nd byte3rd byte Command1st byteB7 B6B5 B4 B3 B2 B1 B0writescratchpad96H readscratchpad69H 1 1any value00H to 3FHcopyscratchpad3CH0 0 0 0 0 0readSubKey66H writeSubKey99Hany value 10H to 3FHwritepassword5AH Sub-KeyNr.:00or01or100 0 0 0 0 0ones complementof 2nd byteSCRATCHPAD COMMANDSThe 64-byte read/write scratchpad of the TM1991 is not password-protected. Its normal use is to build up a data structure to be verified and then copied to a secure subkey.Write Scratchpad [96H]The Write Scratchpad command is used to enter data into the scratchpad. The starting address for the write sequence is specified in the command. Data can be continuously written until the end of the scratchpad is reached or until the TM1991 is reset. The command sequence is shown in Figure 5, first page, left column.Read Scratchpad [69H]The Read Scratchpad command is used to retrieve data from the scratchpad. The starting address is specified in the command word. Data can be continuously read until the end of the scratchpad is reached or until the TM1991 is reset. The command sequence is shown in Figure 5, first page, center column.Copy Scratchpad [3CH]The Copy Scratchpad command is used to transfer specified data blocks from the scratchpad to a selected subkey. This command should be used when data verification is required before storage in a secure subkey. Data can be transferred in single 8-byte blocks or in one large 64-byte block. There are nine valid block selector codes that are used to specify which block is to be transferred (Figure 6). As a further precaution against accidental erasure of secure data, the 8-byte password of the destination subkey must be entered. If the password does not match, the operation is terminated. After the block of data is transferred to the secure subkey, the original data in the corresponding block of the scratchpad is erased. The command sequence is shown in Figure 5, first page, right column.SUBKEY COMMANDSEach of the subkeys within the TM1991 is accessed individually. Transactions to read and write data to a secured subkey start at the address defined in the command and proceed until the device is reset or the end of the subkey is reached.Write Password [5AH]The Write Password command is used to enter the ID and password of the selected subkey. This command will erase all of the data stored in the secure area as well as overwriting the ID and password fields with the new data. The TM1991 has a built-in check to ensure that the proper subkey was selected. The sequence begins by reading the ID field of the selected subkey; the ID of the subkey to be changed is then written into the part. If the IDs do not match, the sequence is terminated. Otherwise, the subkey contents are erased and 64 bits of new ID data are written followed by a new 64-bit password. The command sequence is shown in Figure 5, 2nd page, right column.MEMORY FUNCTIONS FLOW CHART Figure 5TMTMTMTMMEMORY FUNCTIONS FLOW CHART (cont’d) Figure 5 TMTMTM TMBLOCK SELECTOR CODES OF THE TM1991 Figure 6Block Nr.Address Range LS Byte Codes MS Byte0 to 700 to 3FH56567F51575D5A7F0identifier9A9A B39D646E694C1password9A9A4C629B91694C210H to 17H9A65B3629B6E964C318H to 1FH6A6A436D6B616643420H to 27H9595BC92949E99BC528H to 2FH659A4C9D649169B3630H to 37H6565B39D646E96B3738H to 3FH65654C629B9196B3Write SubKey [99H]The Write Subkey command is used to enter data into the selected subkey. Since the subkeys are secure, the correct password is required to access them. The sequence begins by reading the ID field; the password is then written back. If the password is incorrect, the transaction is terminated. Otherwise, the data following is written into the secure area. The starting address for the write sequence is specified in the command word. Data can be continuously written until the end of the secure subkey is reached or until the TM1991 is reset. The command sequence is shown in Figure 5, 2nd page, center column. Read SubKey [66H]The Read Subkey command is used to retrieve data from the selected subkey. Since the subkeys are secure, the correct password is required to access them. The sequence begins by reading the ID field; the password is then written back. If the password is incorrect, the TM1991 will transmit random data. Otherwise the data can be read from the subkey. The starting address is specified in the command. Data can be continuously read until the end of the subkey is reached or until the TM1991 is reset. The command sequence is shown in Figure 5, 2nd page, left column.1-Bus BUS SYSTEMThe 1-Bus bus is a system which has a single bus master and one or more slaves. In all instances, the TM1991 is a slave device. The bus master is typically a micro-controller. The discussion of this bus system is broken down into three topics: hardware configuration, transaction sequence, and 1-Bus signaling (signal types and timing). A 1-Bus protocol defines bus transactions in terms of the bus state during specified time slots that are initiated on the falling edge of sync pulses from the bus master. For a more detailed protocol description, refer to Chapter 4 of the Book of TM19xx Button Standards.HARDWARE CONFIGURATIONThe 1- bus has only a single line by definition; it is important that each device on the bus be able to drive it at the appropriate time. To facilitate this, each device attached to the 1-Bus bus must have an open drain connections or 3-state outputs. The TM1991 is an open drain part with an internal circuit equivalent to that shown in Figure 7. The bus master can be the same equivalent circuit. If a bidirectional pin is not available, separate output and input pins can be tied together.The bus master requires a pullup resistor at the master end of the bus, with the bus master circuit equivalent to the one shown in Figures 8a and 8b. The value of the pullup resistor should be approximately 5 k W for short line lengths.A multidrop bus consists of a 1-Bus bus with multiple slaves attached. The 1-Bus bus has a maximum data rate of 16.3k bits per second. The idle state for the 1-Bus bus is high. If, for any reason a transactionTM1991needs to be suspended, the bus MUST be left in the idle state if the transaction is to resume. If this does not occur, and the bus is left low for more than 120 m s, one or more of the devices on the bus may be reset.EQUIVALENT CIRCUIT Figure 7BUS MASTER CIRCUIT Figure 8TMTMTMTRANSACTION SEQUENCEThe protocol for accessing the TM1991 via the 1-Bus port is as follows:§Initialization§ROM Function Command§Memory Function Command§Transaction/DataINITIALIZATIONAll transactions on the 1-Bus bus begin with an initialization sequence. The initialization sequence consists of a reset pulse transmitted by the bus master followed by presence pulse(s) transmitted by the slave(s). The presence pulse lets the bus master know that the TM1991 is on the bus and is ready to operate. For more details, see the “1-Bus Signaling” sectionROM FUNCTION COMMANDSOnce the bus master has detected a presence pulse, it can issue one of the four ROM function commands. All ROM function commands are eight bits long. A list of these commands follows (refer to flowchart in Figure 9).Read ROM [33H]This command allows the bus master to read the TM1991’s 8-bit family code, unique 48-bit serial number and 8-bit CRC. This command can be used only if there is a single TM1991 on the bus. If more than one slave is present on the bus, a data collision will occur when all slaves try to transmit at the same time (open drain will produce a wired-AND result).Match ROM [55H]The match ROM command, followed by a 64-bit ROM sequence, allows the bus master to address a specific TM1991 on a multidrop bus. Only the TM1991 that exactly matches the 64-bit ROM sequence will respond to the subsequent memory function command. All slaves that do not match the 64-bit ROM sequence will wait for a reset pulse. This command can be used with a single or multiple devices on the bus.Skip ROM [CCH]This command can save time in a single drop bus system by allowing the bus master to access the memory functions without providing the 64-bit ROM code. If more than one slave is present on the bus and a read command is issued following the Skip ROM command, data collision will occur on the bus as multiple slaves transmit simultaneously (open drain will produce a wired-AND result).Search ROM [F0H]When a system is initially brought up, the bus master might not know the number of devices on the 1-Wire bus or their 64-bit ROM codes. The Search ROM command allows the bus master to use a process of elimination to identify the 64-bit ROM codes of all slave devices on the bus. The ROM search process is the repetition of a simple 3-step routine: read a bit, read the complement of the bit, then write the desired value of that bit. The bus master performs this simple 3-step routine on each bit of the ROM. After one complete pass, the bus master knows the contents of the ROM in one device. The remaining number of devices and their ROM codes may be identified by additional passes. See Chapter 5 of the Book of TM19xx Button Standards for a comprehensive discussion of a search ROM, including an actual example.1-BUS SIGNALINGThe TM1991 requires strict protocols to ensure data integrity. The protocol consists of four types of signaling on one line: Reset Sequence with Reset Pulse and Presence Pulse, Write 0, Write 1 and Read Data. All these signals except presence pulse are initiated by the bus master. The initialization sequence required to begin any communication with the TM1991 is shown in Figure 10. A reset pulse followed by a presence pulse indicates the TM1991 is ready to send or receive data given the correct ROM command and memory function command. The bus master transmits (TX) a reset pulse (t RSTL , minimum 480 m s).The bus master then releases the line and goes into receive mode (RX). The 1-Bus bus is pulled to a high state via the pullup resistor. After detecting the rising edge on the data pin, the TM1991 waits (t PDH , 15-60m s) and then transmits the presence pulse (t PDL , 60-240 m s).ROM FUNCTIONS FLOW CHART Figure 9TMTMTMTM TMTM TMTMTMTMINITIALIZATION PROCEDURE “RESET AND PRESENCE PULSES” Figure 10480 m s £ t RSTL < ¥ *480 m s £ t RSTH < ¥(includes recovery time)15 m s £ t PDH < 60 m s 60 m s £ t PDL < 240 m s* In order not to mask interrupt signaling by other devices on the 1-Bus bus, tRSTL + t R should alwaysbe less than 960 m s.READ/WRITE TIME SLOTSThe definitions of write and read time slots are illustrated in Figure 11. All time slots are initiated by the master driving the data line low. The falling edge of the data line synchronizes the TM1991 to the master by triggering a delay circuit in the TM1991. During write time slots, the delay circuit determines when the TM1991 will sample the data line. For a read data time slot, if a “0” is to be transmitted, the delay circuit determines how long the TM1991 will hold the data line low overriding the 1 generated by the master. If the data bit is a “1”, the Button will leave the read data time slot unchanged.READ/WRITE TIMING DIAGRAM Figure 11Write-One Time Slot60 m s £ t SLOT < 120 m s1 m s £ t LOW1< 15 m s 1 m s £ t REC < ¥TMREAD/WRITE TIMING DIAGRAM (cont’d) Figure 11Write-Zero Time Slot60 m s < t LOW0 < t SLOT < 120 m s 1 m s < t REC < ¥Read-Data Time Slot60 m s £ t SLOT < 120 m s 1 m s £ t LOWR < 15 m s 0 £ t RELEASE < 45 m s 1 m s £ t REC < ¥t RDV = 15 m s t SU < 1 m sTMPHYSICAL SPECIFICATIONSSize See mechanical drawingWeight 3.3 gramsHumidity 90% RH at 50°CAltitude 10,000 feetExpected Service Life 10 years at 25°C (150 million transactions, see note 4) Safety Meets UL#913 (4th Edit.); Intrinsically Safe Apparatus,Approved under Entity Concept for use in Class I, Division1, Group A, B, C and D LocationsABSOLUTE MAXIMUM RATINGS*Voltage on any Pin Relative to Ground -0.5V to +7.0VOperating Temperature -40°C to +70°CStorage Temperature -40°C to +70°C*This is a stress rating only and functional operation of the device at these or any other conditions above those indicated in the operation sections of this specification is not implied. Exposure to absolute maximum rating conditions for extended periods of time may affect reliability.DC ELECTRICAL CHARACTERISTICS (V PUP *=2.8V to 6.0V; -40°C to +70°C) PARAMETER SYMBOL MIN TYP MAX UNITS NOTES Input Logic Low V IL-0.30.8V1 Input Logic High V IH 2.2 6.0VOutput Logic Low @ 4 mA V OL0.4VOutput Logic High V OH V PUP 6.0V1,2 Input Resistance V IL500k W3* V PUP = external pullup voltageAC ELECTRICAL CHARACTERISTICS (-40°C to 70°C) PARAMETER SYMBOL MIN TYP MAX UNITS NOTES Time Slot Period t SLOT60120m sWrite 1 Low Time t LOW1115m sWrite 0 Low Time t LOW060120m sRead Data Valid t RDV exactly 15m sRelease Time t RELEASE01545m sRead Data Setup t SU1m s5 Recovery Time t REC1m sReset Low Time t RSTL480m sReset High Time t RSTH480m s4 Presence Detect High t PDH1560m sPresence Detect Low t PDL60240m sNOTES:1.All voltages are referenced to ground.2.V PUP= external pullup voltage to system supply.3.Input pulldown resistance to ground.4.An additional reset or communication sequence cannot begin until the reset high time has expired.5.Read data setup time refers to the time the host must pull the 1-Bus bus low to read a bit. Data isguaranteed to be valid within 1 m s of this falling edge and will remain valid for 14 m s minimum.。
INA219AIDCNR;INA219AIDR;INA219BIDCNT;INA219AIDCNT;INA219AIDCNRG4;中文规格书,Datasheet资料

/
Product Folder Link(s): INA219
Copyright © 2008–2011, Texas Instruments Incorporated
INA219
SBOS448F – AUGUST 2008 – REVISED SEPTEMBER 2011
Table 1. PACKAGING INFORMATION(1)
PRODUCT INA219A INA219B
PACKAGE-LEAD SO-8
SOT23-8 SO-8
SOT23-8
PACKAGE DESIGNATOR D
DCN D
DCN
PACKAGE MARKING I219A A219 I219B B219
VIN+, VIN–
Common-Mode
SDA
SCL
Input Current Into Any Pin
Open-Drain Digital Output Current
Operating Temperature
Storage Temperature
Junction Temperature
Human Body Model
0
±160
0
±160
PGA = ÷ 8
0
±320
0
±320
Bus Voltage (Input Voltage) Range(2)
BRNG = 1
0
32
0
32
BRNG = 0
0
16
0
16
Common-Mode Rejection Offset Voltage, RTI(3)
AD9914_CN

DDS内核 ..................................................................................... 19 12位DAC输出............................................................................ 20 DAC校准输出............................................................................ 20 重构滤波器 ................................................................................ 20 时钟输入(REF_CLK/REF_CLK) ............................................ 21 PLL锁定指令.............................................................................. 22 输出幅度键控(OSK)................................................................. 22 数字斜坡发生器(DRG) ........................................................... 23 省电控制..................................................................................... 27 编程和功能引脚............................................................................. 28 串行编程 .......................................................................................... 31 控制接口——串行I/O.............................................................. 31 通用串行I/O操作...................................................................... 31 指令字节..................................................................................... 31 串行I/O端口引脚功能描述 .................................................... 31 串行I/O时序图 .......................................................................... 32 MSB/LSB传输 ............................................................................ 32 并行编程(8/16位)........................................................................... 33 寄存器图和位功能描述................................................................ 34 寄存器位功能描述 ................................................................... 39 外形尺寸 .......................................................................................... 45 订购指南..................................................................................... 45
CA91中文资料
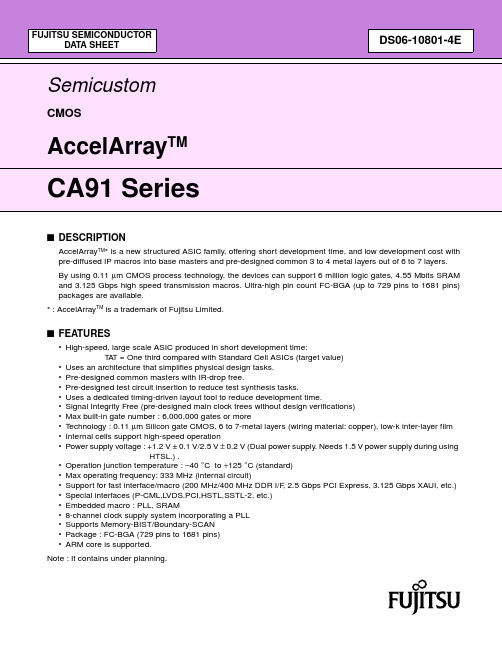
DS06-10801-4EFUJITSU SEMICONDUCTORDATA SHEETSemicustomCMOSAccelArray TMCA91 Series■DESCRIPTIONAccelArray TM * is a new structured ASIC family, offering short development time, and low development cost with pre-diffused IP macros into base masters and pre-designed common 3 to 4 metal layers out of 6 to 7 layers.By using 0.11 µm CMOS process technology, the devices can support 6 million logic gates, 4.55 Mbits SRAM and 3.125 Gbps high speed transmission macros. Ultra-high pin count FC-BGA (up to 729 pins to 1681 pins)packages are available.* : AccelArray TM is a trademark of Fujitsu Limited.■FEATURES•High-speed, large scale ASIC produced in short development time:T A T = One third compared with Standard Cell ASICs (target value)•Uses an architecture that simplifies physical design tasks.•Pre-designed common masters with IR-drop free.•Pre-designed test circuit insertion to reduce test synthesis tasks.•Uses a dedicated timing-driven layout tool to reduce development time.•Signal Integrity Free (pre-designed main clock trees without design verifications)•Max built-in gate number : 6,000,000 gates or more•T echnology : 0.11 µm Silicon gate CMOS, 6 to 7-metal layers (wiring material: copper), low-k inter-layer film •Internal cells support high-speed operation•Power supply voltage : +1.2 V ± 0.1 V/2.5 V ± 0.2 V (Dual power supply. Needs 1.5 V power supply during usingHTSL.) .•Operation junction temperature : −40 °C to +125 °C (standard) •Max operating frequency: 333 MHz (internal circuit)•Support for fast interface/macro (200 MHz/400 MHz DDR I/F , 2.5 Gbps PCI Express, 3.125 Gbps XAUI, etc.) •Special interfaces (P-CML,L VDS,PCI,HSTL,SSTL-2, etc.)•Embedded macro : PLL, SRAM•8-channel clock supply system incorporating a PLL •Supports Memory-BIST/Boundary-SCAN •Package : FC-BGA (729 pins to 1681 pins)•ARM core is supported.Note : It contains under planning.CA91 Series2■MACRO LIBRARY1.Unit cell•Flip Flop, with clear/preset (support for Mux-D Scan, with Lock up latch)•Clock Buffer•Other combination circuits (approximately 50 different types)2.APLL•Input frequency : 25 MHz to 800 MHz•Output frequency : 400 MHz to 800 MHz•User frequency : 25 MHz to 800 MHz•Phase shift : 0/90/180/270 deg.3.SRAM•1R1W-SRAM : 32 words × 40 bits•2RW-SRAM : 512 words × 40 bitsBit Select 1 : 1, 2 : 1, 4 : 1, 8 : 11 RW operation accesses specified port bit-width4.I/O•HSTL*1(250 MHz)•2.5 V L VCMOS(200 MHz (input buffer), 75 MHz to 100 MHz (output buffer))•PCML(250 MHz)•L VDS(311 MHz)•SSTL2(250 MHz)•PCI-66 *2(66 MHz)•PCI-X*2(133 MHz)•3.3 V tolerant(200 MHz (input buffer), 75 MHz to 100 MHz (output buffer)) *1 : Needs 1.5 V power supply*2 : As the I/F is 3.3V tolerant, it does not satisfy the PCI standard in some cases. Dedicated for Giga Frame•SPI-4P2 (622 Mbps to 800 Mbps)•XAUI (3.125 Gbps)•Fibre Channel (1.0 Gbps, 2.0 Gbps)•Serial Rapid IO (1.25 Gbps, 2.5 Gbps, 3.125 Gbps)•PCI Express (2.5 Gbps)5.Memory interface•DDR-SDRAM (400 Mbps)•QDR-SDRAM (400 Mbps)•Peer to Peer SDR (200 Mbps)•Peer to Peer DDR (200 Mbps)•SDR-SDRAM (167 Mbps)CA91 Series3■ABSOLUTE MAXIMUM RATINGS(VSS = 0 V)*1 : Different limit values apply for L VDS, etc.*2 : Maximum supply current in normal operation. Supply current depends on the frame or the package.*3 : Maximum output current in normal operation *4 : Required when using HSTL I/O.WARNING:Semiconductor devices can be permanently damaged by application of stress (voltage, current,temperature, etc.) in excess of absolute maximum ratings. Do not exceed these ratings.ParameterSymbolApplicationRating Unit Min Max Power supply voltageVDDVDDI (Core)− 0.5 1.8V VDDE(for 2.5 V CMOS I/Os, 3.3 V Tolerant I/Os) − 0.5 3.6V VDDE (for 1.5 V I/Os*4) − 0.5 3.6V Input voltage *1VI2.5 V CMOS− 0.5VDDE + 0.5( ≤ 3.6) V 3.3 V Tolerant − 0.5VDDE + 3.6( ≤ 4.0) V Output voltageVO2.5 V CMOS− 0.5VDDE + 0.5( ≤ 3.6) V 3.3 V Tolerant (H/L-State) − 0.5VDDE + 0.5( ≤ 4.0)V 3.3 V Tolerant (Z-State)− 0.5 4.0V Storage temperature Tst ⎯ − 55+ 125 °C Operation junction temperature Tj⎯− 40+ 125 °C Power supply pin current *2IDEach VDDE pin⎯180mA Each VDDI pin ⎯200mA Each VSS pin⎯200mA Output current *3IO2.5 V CMOS ⎯±10mA3.3 V Tolerant⎯±7.5mACA91 Series4■RECOMMENDED OPERATING CONDITIONS• Dual power supply (VDDI =+1.2 V ± 0.1 V, VDDE =+2.5 V ± 0.2 V, (+1.5 V ± 0.1 V))(VSS = 0 V)* : Applicable to HSTL I/O.WARNING:The recommended operating conditions are required in order to ensure the normal operation of the semiconductor device. All of the device’s electrical characteristics are warranted when the device isoperated within these ranges.Always use semiconductor devices within their recommended operating condition ranges. Operationoutside these ranges may adversely affect reliability and could result in device failure.No warranty is made with respect to uses, operating conditions, or combinations not represented onthe data sheet. Users considering application outside the listed conditions are advised to contact theirFUJITSU representatives beforehand.Parameter SymbolValueUnitMin Typ MaxPower supplyvoltagePower supply voltagefor coreVDDI 1.1 1.2 1.3V Power supply voltagefor 2.5 V I/OsVDDE 2.3 2.5 2.7V Power supply voltagefor 1.5 V I/Os *VDDE 1.4 1.5 1.6V“H” level inputvoltage2.5 V CMOSVIH1.7⎯VDDE + 0.3V3.3 V Tolerant 1.7⎯ 3.6V “L” level inputvoltage2.5 V CMOSVIL− 0.3⎯0.7V3.3 V Tolerant− 0.3⎯0.7V Operation junction temperature Tj− 40⎯+ 125°CCA91 Series5■ELECTRICAL CHARACTERISTICS1.DC CHARACTERISTICS(VDDI = 1.2 V ± 0.1 V, VDDE = 2.5 V ± 0.2 V, VSS = 0 V, Tj = − 40 °C to + 125 °C)* : The input leak current may exceed the above value if an input buffer with pull-up or pull-down resistor is used.Note : Refer to the application note for details of HSTL I/O.2.AC CHARACTERISTICS*1 : Delay time = propagation delay time, enable time, and disable time.*2 : typ can be estimated from the cell specification.*3 : Measurement conditionNote : Obtains the tpd max corresponding to the maximum junction temperature Tj.■I/O PIN CAPACITANCE(Tj = +25 °C, VDDE = VI = 0 V, f = 1 MHz)Note: The capacity depends on the package, pin positions, and similar.Parameter Symbol Conditions ValueUnitMin Typ Max “H” level output voltage VOH IOH = − 100 µA VDDE − 0.2⎯VDDE V “L” level output voltage VOL IOL = 100 µA0⎯0.2V Input leak current *IL⎯− 10⎯+ 10 µA Pull-up/Pull-down resistorRP2.5 V CMOS pin,VIL = 0 V at pull-up,VIH = VDDE at pull-down 102555k Ω3.3 V Tolerant pin,VIH = 3.0 V to 3.6 V at pull-down123385k ΩParameter Symbol ValueUnit Min Typ Max Delay timetpd *1typ *2 × tmin *3typ *2 × ttyp *3typ *2 × tmax *3nsMeasurement condition tminttyp tmax VDD = 1.2 V ± 0.1 V, VSS = 0 V, Tj = − 40 °C to + 125 °C0.731.001.43ParameterSymbol Value Unit Input pin CIN Max 16pF Output pin COUT Max 16pF I/O pin CI/OMax 16pFCA91 Series6■DESIGN METHODOLOGY•T o make development faster, the number of layers customizable in AccelArray is restricted to 3 to 4. Blocks that do not need to be redesigned for each product can be designed once and then incorporated into the architecture. As only 3 to 4 customizable layers are available for development of each product, the requirements of the layout tool are low. The requirements for timing design, where excessive complexity causes convergence to be slow, are also low. As result, the time required for design work is reduced. Primarily, tools supplied by Fujitsu are used for logic design.•A special-purpose tool is used to determine the pin layout. This produces speedy and reliable results.■SUPPORT TOOL•Frame estimationFUJITSU LIMITED : FEST A•Pin assignmentFUJITSU LIMITED : P ASTEL•Logic synthesisSynopsys, Inc. : Design Compiler, Cadence Design Systems, Inc. : BuildGates•Physical synthesisSynplicity, Inc. : Amplify AccelAllay•Format verificationCadence Design Systems, Inc. : Conformal ASIC, Synopsys, Inc. : FormalityFUJITSU LIMITED : ASSURE•Delay calculationFUJITSU LIMITED : LCADFE•Timing analysisSynopsys, Inc. : PrimeTime, FUJITSU LIMITED : GIST A•SimulationCadence Design Systems, Inc. : NC-Verilog/NC-VHDL, Synopsys, Inc. : VCS,Mentor Graphics Corporation : ModelSim, FUJITSU LIMITED : LCADFE•LayoutFUJITSU LIMITED : AccelBuilder•Power calculationFUJITSU LIMITED : PScope•Power analysisCadence Design Systems, Inc. : VoltageStorm•T est synthesisFUJITSU LIMITED : DFTPlanner•A TPGFUJITSU LIMITED : FANTCAD/X-Pax/TERBAN•ValidationFUJITSU LIMITED : LCADVL•Fault simulationFUJITSU LIMITED : FANSCADNote : The company names and the product names are the trademarks or registered trademarks of their respective owners.CA91 Series■FRAME LINE UP2 groups are provided depending on the I/O transmission speed: Mega Frame (400 Mbps) and Giga Frame(622 Mbps to 3.125 Gbps).*1 : Actual available I/O count varies with the interface type.*2 : ARM9 core is supported.* : Actual available I/O count varies with the interface type.■PACKAGEHigh pin count FC-BGAs using fine solder bump pitch technology are available for high speed data networking applications.7CA91 SeriesFUJITSU LIMITEDAll Rights Reserved.The contents of this document are subject to change without notice. Customers are advised to consult with FUJITSU sales representatives before ordering.The information, such as descriptions of function and application circuit examples, in this document are presented solely for the purpose of reference to show examples of operations and uses of Fujitsu semiconductor device; Fujitsu does not warrant proper operation of the device with respect to use based on such information. When you develop equipment incorporating the device based on such information, you must assume any responsibility arising out of such use of the information. Fujitsu assumes no liability for any damages whatsoever arising out of the use of the information.Any information in this document, including descriptions of function and schematic diagrams, shall not be construed as license of the use or exercise of any intellectual property right, such as patent right or copyright, or any other right of Fujitsu or any third party or does Fujitsu warrant non-infringement of any third-party’s intellectual property right or other right by using such information. Fujitsu assumes no liability for any infringement of the intellectual property rights or other rights of third parties which would result from the use of information contained herein.The products described in this document are designed, developed and manufactured as contemplated for general use, including without limitation, ordinary industrial use, general office use, personal use, and household use, but are not designed, developed and manufactured as contemplated (1) for use accompanying fatal risks or dangers that, unless extremely high safety is secured, could have a serious effect to the public, and could lead directly to death, personal injury, severe physical damage or other loss (i.e., nuclear reaction control in nuclear facility, aircraft flight control, air traffic control, mass transport control, medical life support system, missile launch control in weapon system), or (2) for use requiring extremely high reliability (i.e., submersible repeater and artificial satellite).Please note that Fujitsu will not be liable against you and/or any third party for any claims or damages arising in connection with above-mentioned uses of the products.Any semiconductor devices have an inherent chance of failure. You must protect against injury, damage or loss from such failures by incorporating safety design measures into your facility and equipment such as redundancy, fire protection, and prevention of over-current levels and other abnormal operating conditions.If any products described in this document represent goods or technologies subject to certain restrictions on export under the Foreign Exchange and Foreign Trade Law of Japan, the prior authorization by Japanese government will be required for export of those products from Japan.F0506©2005 FUJITSU LIMITED Printed in Japan。
CTA51AS4024VDC1.9S资料

GENERAL DATA
Electrical Life @ rated load Mechanical Life Insulation Resistance Dielectric Strength, Coil to Contact Contact to Contact Shock Resistance Vibration Resistance Terminal (Copper Alloy) Strength Operating Temperature Storage Temperature Solderability Weight 100K cycles, typical 10M cycles, typical 100MΩ min @ 500VDC 750V rms min. @ sea level 500V rms min. @ sea level 200m/s2 for 11ms 1.27mm double amplitude 10-40Hz 10N -40 °C to + 85 °C -40 °C to + 155 °C 230 °C ± 2 °C for 10 ± 0.5s 19g open. 21g covered
Fax: 763-535-2194
元器件交易网
CIT RELAY™
CTA5
FEATURES: • Switching capacity up to 40A @ 14VDC • Small size and light weight • PCB pin mounting available • Suitable for automobile and lamp accessories • Two footprint styles available
PMC251 中文资料

提供本文档的中文简体版是为了便于了解,请勿忽视文中英文的部份,因为其中提供有关产品性能以及产品使用的有 用信息,应广科技暨代理商对于文中可能存在的差错不承担任何责任,建议参考本文件英文版。
TLE:15626510025
©Copyright 2013, PADAUK Technology Co. Ltd
IO 类型、采用 FPPATM 技术双核心 8 位单片机
重要声明
应广科技保留权利在任何时候变更或终止产品,建议客户在使用或下单前与应广科技或代理 商联系以取得最新、最正确的产品信息。 应广科技不担保本产品适用于保障生命安全或紧急安全的应用,应广科技不为此类应用产品 承担任何责任。关键应用产品包括,但不仅限于,可能涉及的潜在风险的死亡,人身伤害,火灾 或严重财产损失。 应广科技不承担任何责任来自于因客户的产品设计所造成的任何损失。在应广科技所保障的 规格范围内,客户应设计和验证他们的产品。为了尽量减少风险,客户设计产品时,应保留适当 的产品工作范围安全保障。
Dell PowerEdge R515 系统 硬件用户手册说明书

Dell PowerEdgeR515系统硬件用户手册管制型号 E12S 系列和 E13S 系列管制类型 E12S002 和 E13S002注、小心和警告注:“注”表示可以帮助您更好地使用计算机的重要信息。
小心:“小心”表示如果不遵循说明,就有可能损坏硬件或导致数据丢失。
警告:“警告”表示可能会导致财产损失、人身伤害甚至死亡。
____________________本出版物中的信息如有更改,恕不另行通知。
© 2010 Dell Inc. 版权所有,翻印必究。
未经 Dell Inc. 书面许可,严禁以任何形式复制这些材料。
本文中使用的商标:Dell™、DELL 徽标和 PowerEdge™是 Dell Inc. 的商标。
Microsoft®、Windows®、MS-DOS®和 Windows Server®是 Microsoft Corporation 在美国和/或其它国家和地区的商标或注册商标。
本出版物中述及的其它商标和产品名称是指拥有相应商标和产品名称的公司或其制造的产品。
Dell Inc. 对其它公司的商标和产品名称不拥有任何所有权。
管制型号 E12S 系列和 E13S 系列管制类型 E12S002 和 E13S0022010 年 8 月Rev. A00目录1关于系统 (11)在启动期间访问系统功能 (11)前面板部件和指示灯 (12)LCD 面板部件(可选) (15)主屏幕 (16)Setup(设置)菜单 (17)View(视图)菜单 (17)硬盘驱动器指示灯显示方式 (18)背面板部件和指示灯 (19)连接可选外部设备的指南 (22)NIC 指示灯代码 (22)电源指示灯代码 (23)诊断指示灯(可选) (24)LCD 状态信息(可选) (26)解决 LCD 状态信息描述的问题 (36)删除 LCD 状态信息 (36)目录3系统信息 (37)警告信息 (50)诊断程序信息 (50)警报信息 (50)可能需要的其它信息 (51)2使用系统设置程序和UEFI引导管理器 (53)选择系统引导模式 (53)进入系统设置程序 (54)响应错误信息 (54)使用系统设置程序导航键 (54)系统设置程序选项 (55)主屏幕. . . . . . . . . . . . . . . . . 55Memory Settings(内存设置)屏幕 (57)Processor Settings(处理器设置)屏幕 (58)SATA Settings(SATA 设置)屏幕(可选) (59)Boot Settings(引导设置)屏幕 (60)Integrated Devices(集成设备)屏幕 (61)PCI IRQ Assignments(PCI IRQ 分配)屏幕 (62)Serial Communication(串行通信)屏幕 (63)Embedded Server Management(嵌入式服务器管理)屏幕 (64)Power Management(电源管理)屏幕 (64)System Security(系统安全保护)屏幕 (65)Exit (退出)屏幕 (67)4目录进入 UEFI 引导管理器 (68)使用 UEFI 引导管理器导航键 (68)UEFI 引导管理器屏幕 (69)UEFI Boot Settings(UEFI 引导设置)屏幕 (69)System Utilities(系统公用程序)屏幕 (70)系统密码和设置密码功能 (70)使用系统密码 (70)使用设置密码 (73)嵌入式系统管理 (74)底板管理控制器配置 (75)进入 BMC 设置模块 (75)iDRAC6 配置公用程序 (76)进入 iDRAC6 配置公用程序 (76)3安装系统组件 (77)建议使用的工具 (77)系统内部组件 (77)前挡板(可选) (80)卸下前挡板 (80)安装前挡板 (81)打开与合上系统护盖 (81)打开系统护盖 (81)合上系统护盖 (83)冷却导流罩 (84)卸下冷却导流罩 (84)安装冷却导流罩 (85)目录5硬盘驱动器 (85)卸下硬盘驱动器挡片 (85)安装硬盘驱动器挡片 (86)卸下硬盘驱动器 (86)安装硬盘驱动器 (87)从硬盘驱动器托盘中卸下硬盘驱动器 (88)将硬盘驱动器安装到硬盘驱动器托盘中 (89)内部硬盘驱动器 (89)卸下内部硬盘驱动器托架 (89)安装内部硬盘驱动器托架 (91)从内部硬盘驱动器托架上卸下内部硬盘驱动器 (91)将硬盘驱动器安装到硬盘驱动器托架中 (92)光盘驱动器(可选) (93)卸下光盘驱动器 (93)安装光盘驱动器 (94)冷却风扇 (95)卸下冷却风扇 (95)安装冷却风扇 (98)电源设备 (99)卸下电源设备 (99)安装电源设备 (100)卸下电源设备挡片 (101)安装电源设备挡片 (101)系统内存 (101)内存模块安装一般原则 (102)模式特定原则 (103)安装内存模块 (104)卸下内存模块 (106)6目录扩充卡和扩充卡提升板 (107)扩充卡安装原则 (107)安装扩充卡 (109)卸下扩充卡 (111)卸下扩充卡提升板 (111)安装扩充卡提升板 (113)集成存储控制器卡 (114)卸下存储控制器卡 (114)安装存储控制器卡 (116)iDRAC6 Express 卡(可选) (117)安装 iDRAC6 Express 卡 (117)卸下 iDRAC6 Express 卡 (118)iDRAC6 Enterprise 卡(可选) (119)安装 iDRAC6 Enterprise 卡 (119)卸下 iDRAC6 Enterprise 卡 (121)VFlash 介质(可选) (122)安装 VFlash 介质卡 (122)卸下 VFlash 介质卡 (122)内部 USB 存储钥匙 (122)处理器 (123)卸下处理器 (123)安装处理器 (126)系统电池 (127)更换系统电池 (127)RAID 电池(可选) (130)卸下 RAID 电池 (130)安装 RAID 电池 (131)目录7控制面板部件— LED (131)卸下控制面板模块 LED 指示灯 (131)安装控制面板模块 LED 指示灯 (133)控制面板部件—LCD(可选) (133)卸下控制面板显示模块 (133)安装控制面板显示模块 (134)卸下控制面板部件 (134)安装控制面板部件 (136)SAS 背板 (136)卸下 SAS 背板 (136)安装 SAS 背板 (140)配电板 (141)卸下配电板 (141)更换配电板 (144)系统板 (145)卸下系统板 (145)安装系统板 (147)8目录4系统故障排除 (149)安全第一—为您和您的系统着想 (149)系统启动失败故障排除 (149)外部连接故障排除 (149)视频子系统故障排除 (150)USB 设备故障排除 (150)串行 I/O 设备故障排除 (151)NIC 故障排除 (151)受潮系统故障排除 (152)受损系统故障排除 (153)系统电池故障排除 (154)电源设备故障排除 (154)系统冷却问题故障排除 (155)风扇故障排除 (155)系统内存故障排除 (156)内部 USB 密钥故障排除 (158)光盘驱动器故障排除 (159)硬盘驱动器故障排除 (160)内部硬盘驱动器故障排除 (161)存储控制器故障排除 (162)扩充卡故障排除 (163)处理器故障排除 (164)目录95运行系统诊断程序 (167)使用 Online Diagnostics (167)嵌入式系统诊断程序功能 (167)何时使用嵌入式系统诊断程序 (168)运行嵌入式系统诊断程序 (168)嵌入式系统诊断程序检测选项 (168)使用 Custom Test(自定义检测)选项 (169)选择要检测的设备 (169)选择诊断程序选项 (169)查看信息和结果 (169)6跳线和连接器 (171)系统板跳线 (171)系统板连接器 (172)禁用已忘记的密码 (174)7获得帮助 (177)与 Dell 联络 (177)索引 (179)10目录关于系统在启动期间访问系统功能在启动期间,可以使用下列击键访问系统功能。
艾 significance 199115 产品说明书

Eaton 199115Eaton Moeller® series Rapid Link - Reversing starter, 6.6 A,Sensor input 2, Actuator output 1, 230/277 V AC, AS-Interface®, S-7.A.E. for 62 modules, HAN Q4/2, with manual override switchGeneral specificationsEaton Moeller® series Rapid Link Reversing starter199115RAMO5-W212A32-412RS14015081971732120 mm 270 mm 220 mm 1.81 kgRoHSIEC/EN 60947-4-2 CCC UL approval CE UL 60947-4-2Assigned motor rating: for normal internally and externally ventilated 4 pole, three-phase asynchronous motors with 1500 rpm at 50 Hz or 1800 min at 60 HzProduct NameCatalog Number Model CodeEANProduct Length/Depth Product Height Product Width Product Weight Certifications Catalog NotesIs the panel builder's responsibility. The specifications for the switchgear must be observed.3 kW6.6 A (at 150 % Overload)480 V AC, 3-phase400 V AC, 3-phase10000 A0 VMeets the product standard's requirements.Is the panel builder's responsibility. The specifications for the switchgear must be observed.Does not apply, since the entire switchgear needs to be evaluated.0 kW2.238 kWMeets the product standard's requirements.0 V-40 °CKey switch position HANDManual override switch1 Actuator outputKey switch position AUTO Generation Change RASP4 to RASP5Configuration to Rockwell PLC for Rapid LinkConnecting drives to generator suppliesGeneration change from RA-SP to RASP 4.0Generation change RAMO4 to RAMO5Generation change from RA-MO to RAMO 4.0Electromagnetic compatibility (EMC)Generation Change RA-SP to RASP5Rapid Link 5 - brochureDA-SW-USB Driver PC Cable DX-CBL-PC-1M5DA-SW-drivesConnect USB Driver DX-COM-PCKITDA-SW-Driver DX-CBL-PC-3M0DA-SW-drivesConnect - InstallationshilfeDA-SW-drivesConnect - installation helpDA-SW-drivesConnectDA-SW-USB Driver DX-COM-STICK3-KITMaterial handling applications - airports, warehouses and intra-logisticsProduct Range Catalog Drives Engineering-ENProduct Range Catalog Drives EngineeringDA-DC-00004523.pdfDA-DC-00003964.pdfDA-DC-00004184.pdfDA-DC-00004525.pdfeaton-bus-adapter-rapidlink-speed-controller-dimensions-002.eps eaton-bus-adapter-rapidlink-speed-controller-dimensions-003.eps eaton-bus-adapter-rapidlink-reversing-starter-dimensions-003.eps eaton-bus-adapter-rapidlink-reversing-starter-dimensions-002.epsETN.RAMO5-W212A32-412RS1.edzIL034084ZU10.11 Short-circuit ratingRated operational power at AC-3, 380/400 V, 50 HzInput currentRated operational voltageRated conditional short-circuit current, type 1, 480 Y/277 V Rated control supply voltage (Us) at AC, 50 Hz - min10.4 Clearances and creepage distances10.12 Electromagnetic compatibility10.2.5 LiftingRated power at 575 V, 60 Hz, 3-phaseRated power at 460 V, 60 Hz, 3-phase10.2.3.1 Verification of thermal stability of enclosures Rated control supply voltage (Us) at DC - minAmbient storage temperature - minFitted with:Application notes BrochuresCatalogs Certification reports DrawingseCAD model Installation instructionsThermo-clickElectronic motor protectionKey switch position OFF/RESETThermistor monitoring PTCTwo sensor inputs through M12 sockets (max. 150 mA) for quick stop and interlocked manual operationShort-circuit releaseAC-53a0 VCenter-point earthed star network (TN-S network)AC voltagePhase-earthed AC supply systems are not permitted.Is the panel builder's responsibility.Class 10 A10 kA230/277 V AC -15 % / +10 %, Actuator for external motor brake 55 °C0 kW< 95 %, no condensationIn accordance with IEC/EN 50178Parameterization: drivesConnect mobile (App) Parameterization: drivesConnectDiagnostics and reset on device and via AS-Interface Parameterization: KeypadParameterization: Fieldbus Rapid Link 5MN040003_ENramo5_v12.stp ramo5_v12.dwgOverload cycleNumber of pilot lightsRated control supply voltage (Us) at AC, 50 Hz - max System configuration type10.8 Connections for external conductorsCoordination class (IEC 60947-4-3)Rated conditional short-circuit current, type 1, 600 Y/347 V Rated conditional short-circuit current (Iq)Braking voltageAmbient operating temperature - maxRated operational power at AC-3, 220/230 V, 50 Hz Climatic proofingFeatures Installation videos Manuals and user guides mCAD modelLifespan, electrical10,000,000 Operations (at AC-3)Number of command positions2Electrical connection type of main circuitPlug-in connectionElectrical connection type for auxiliary- and control-current circuit Plug-in connectionRated control supply voltage (Us) at DC - max0 V10.9.3 Impulse withstand voltageIs the panel builder's responsibility.Braking current≤ 0.6 A (max. 6 A for 120 ms), Actuator for external motor brakeAmbient operating temperature - min-10 °C10.6 Incorporation of switching devices and componentsDoes not apply, since the entire switchgear needs to be evaluated.Current limitationAdjustable, motor, main circuit0.3 - 6.6 A, motor, main circuitCable length10 m, Radio interference level, maximum motor cable length10.5 Protection against electric shockDoes not apply, since the entire switchgear needs to be evaluated.Mounting positionVerticalMains switch-on frequencyMaximum of one time every 60 secondsClassCLASS 10 A10.13 Mechanical functionThe device meets the requirements, provided the information in the instruction leaflet (IL) is observed.10.2.6 Mechanical impactDoes not apply, since the entire switchgear needs to be evaluated.10.9.4 Testing of enclosures made of insulating materialIs the panel builder's responsibility.10.3 Degree of protection of assembliesDoes not apply, since the entire switchgear needs to be evaluated.Electromagnetic compatibilityClass AVoltage typeDCProduct categoryMotor starterOverload release current setting - min0.3 ARated control voltage (Uc)230/277 V AC (external brake 50/60 Hz)24 V DC (-15 %/+20 %, external via AS-Interface® plug)Rated operational current (Ie)6.6 AAssigned motor power at 460/480 V, 60 Hz, 3-phase3 HPRated frequency - min47 HzNumber of auxiliary contacts (normally closed contacts)Rated conditional short-circuit current (Iq), type 2, 380 V, 400 V, 415 V0 APower consumption8 W10.2.3.2 Verification of resistance of insulating materials to normal heatMeets the product standard's requirements.10.2.3.3 Resist. of insul. mat. to abnormal heat/fire by internal elect. effectsMeets the product standard's requirements.On-delay20 - 35 msLifespan, mechanical10,000,000 Operations (at AC-3)Rated operational current (Ie) at 150% overload6.6 AProtocolAS-Interface profile cable: S-7.4 for 62 modulesASIOverload release current setting - max6.6 A10.9.2 Power-frequency electric strengthIs the panel builder's responsibility.Overvoltage categoryIIIDegree of protectionIP65NEMA 12Rated frequency - max63 HzVibrationResistance: 10 - 150 Hz, Oscillation frequency Resistance: 57 Hz, Amplitude transition frequency on accelerationResistance: According to IEC/EN 60068-2-6Resistance: 6 Hz, Amplitude 0.15 mmRated operational power at 380/400 V, 50 Hz - max3 kWAmbient storage temperature - max70 °CShort-circuit protection (external output circuits)Type 1 coordination via the power bus' feeder unit, Main circuitRated control supply voltage (Us) at AC, 60 Hz - min0 V10.7 Internal electrical circuits and connectionsIs the panel builder's responsibility.Rated impulse withstand voltage (Uimp)4000 VConnectionConnections pluggable in power sectionOff-delay20 - 35 ms10.10 Temperature riseThe panel builder is responsible for the temperature rise calculation. Eaton will provide heat dissipation data for the devices.FunctionsFor actuation of motors with mechanical brakeExternal reset possibleTemperature compensated overload protectionOutput frequency50/60 HzMains voltage tolerance380 - 480 V (-15 %/+10 %, at 50/60 Hz)Rated conditional short-circuit current (Iq), type 2, 230 V0 AInterfacesMax. total power consumption from AS-Interface® power supply unit (30 V): 190 mASpecification: S-7.A.E. (AS-Interface®)Number of slave addresses: 62 (AS-Interface®)TypeReversing starter10.2.2 Corrosion resistanceMeets the product standard's requirements.Supply frequency50/60 Hz, fLN, Main circuit10.2.4 Resistance to ultra-violet (UV) radiationMeets the product standard's requirements.10.2.7 InscriptionsMeets the product standard's requirements.Rated control supply voltage (Us) at AC, 60 Hz - max0 VRated operational current (Ie) at AC-3, 380 V, 400 V, 415 V6.6 ARated operational power at 380/400 V, 50 Hz - min0.09 kWModelReversing starterEaton Corporation plc Eaton House30 Pembroke Road Dublin 4, Ireland © 2023 Eaton. All Rights Reserved. Eaton is a registered trademark.All other trademarks areproperty of their respectiveowners./socialmedia115 g, Mechanical, According to IEC/EN 60068-2-27, 11 ms, Half-sinusoidal shock 11 ms, 1000 shocks per shaft Max. 2000 m Max. 1000 mAbove 1000 m with 1 % performance reduction per 100 mNumber of auxiliary contacts (normally open contacts)Shock resistanceAltitude。
PD191 单相表用户手册说明书

南京能保电气有限公司版权所有本用户手册适用于PD191型产品V2.*版本程序。
本用户手册和产品今后可能会有小的改动,请注意核对你使用的产品与手册的版本是否相符。
1 说明书单独成册 2015-9-1823更多产品信息,请访问:目录第一章绪论 (1)第一节概述 (1)功能简述 (1)硬件配置 (1)第二节特点及参数 (2)技术特点 (2)技术参数 (2)第三节订货信息 (3)第二章安装 (4)第一节安装须知 (4)过电流保护 (4)浪涌保护 (4)第二节安装尺寸及方法 (4)端子介绍 (5)接线示意图 (6)第三章操作 (8)第一节面板图示 (8)第二节参数设定操作方法 (9)第四章通信 (12)第一节命令格式及示例 (12)第二节电量系数 (13)第三节数据地址 (14)PD191单相表用户手册第一章 绪 论第一节 概述PD191智能配电仪表是一种采集配电信息,具备数据传输的数字仪表,它集数据采集与控制功能为一身。
它可以代替多种仪表、继电器、变送器和其他元件。
PD191智能配电仪表可安装在配电系统内的不同位置。
PD191智能配电仪表,是针对电力系统、工矿企业、公用设施、智能大厦的电力监控需求而设计的配电仪表。
该系列每种产品分别对应测量常规单相电参数,如单相电流、电压、有功、无功功率,功率因数,开关状态等。
它还能接受远方的控制命令,输出相应的出口,完成远方控制功能。
它具有模拟量输出功能,自定义输出的电量。
功能简述硬件配置第二节特点及参数技术特点PD191的设计充分考虑了可靠性、简易性、性价比等方面,现具有以下特点: • 可直接从电流、电压互感器接入信号• 可任意设置PT/CT变比• 2路的开入量(隔离)输入• 2路的开出量(继电器)输出• 1路的模拟量输出4~20mA• 多块仪表可设置不同的通讯地址,多种通信速率供选择• 可通信接入SCADA、PLC系统中• 可与绝大多数PLC相连(GE、Siemens、AB等)• 可与业界多种软件通讯(inTouch、Fix、GMS800、组态王等)技术参数输入信号电压输入•额定电压:100V/380V•过载能力:1.2倍额定值(连续) 2500V/1秒(不连续)•输入负荷:小于0.2VA输入电流•额定电流:5A、1A•过载能力:1.2倍额定值(连续) 100A/1秒(不连续)•输入负荷:小于0.2VA频率输入:45~55 HZ测量精度•电压、电流精度:0.5级•其他电量精度:1级•频率精度:0.1Hz通信•通信接口:RS-485 ,异步半双工,1位起始位,8位数据位,1位停止位,无校验•协议:MODBUS-RTU•波特率:4800~9600 bps工作环境•工作温度:-20℃~60℃• 存储温度:-40℃~75℃•相对湿度:5%~90%不结露信号开入• 接入方式:干接点接入• 光电耦合器隔离:4000VAC.rms信号开出• 输出方式:脉冲输出,遥控脉冲宽度为1秒• 继电器输出容量:5A/250VAC,5A/30VDC外形尺寸和重量• 长宽深:72x72x95mm• 净重:0.25KG电源• 工作电压:AC/DC 60~265V• 最大功耗:≤3W第三节订货信息第二章安装第一节安装须知过电流保护过电流保护建议在装置电源处加入1A的保险丝或空开。
单片集成加速度计外文翻译、中英文翻译、外文文献翻译

英文资料译文:具有信号调理功能的士 1g到±5g单片集成加速度计ADXL05*特点:五千分之一 g的分辨率,噪声水平比ADXL50小12倍,用户可选择的满刻度范围是±1g到±5g,单片集成加速度测量系统,数字指令自检功能,+5V单独供电操作。
应用:用于振动测量的低成本传感器,比电解质和水银传感器更快地响应倾角变化,高灵敏的报警系统,提供速度和位置的惯性检测。
总体描述:ADXL05是一个集成在单片IC卡上的加速度测量系统。
它能够测量的加速度范围是土 5g到±1g甚至更小。
典型的噪声水平是500〃8/出(比ADX50小12倍),能够检测到低于五千分之一g的信号。
ADXL05是一种既能够测量交流加速度(振动)又能够测量直流加速度(如惯性力和重力)的电容性加速度计。
三个外部电容器和一个+5V 的可调电源就是测量+5V加速度需要的一切。
三个电阻用于设定输出缓冲放大器的输出范围从200Mv/g 到1V/g。
内部电容可以被加在电阻网络中以提供1级或2级的滤波。
不需要额外的敏感元件直接连接模数转换器件。
这个装置以可与1屋电平相容的自检功能为特色,这个功能可以通过任何时候旋转传感器的横梁来检测传感器和它的电特性是否正常作用。
ADXL05 可以封装在10管脚的金属容器内,指定的商用温度范围是0℃到+70℃,工业应用的温度范围是-40℃到+85℃。
功能简图ADXL05——规格明细表(T A=T MIN to T MAx,T A=+25℃/J,V s=+5V,a=0g)缓冲放大器 输入补偿电压标准属性1.800V ±10 ±25 mV 输出偏差520nA 开环增益 DC80dB联合增益带宽200kHz输出电压范围I O U T ±100M A0.25Vs-0.25V 电容负载 1000pF电源反馈DC, Vs=4.75V 〜5.25V110mV/V电源工作电压范围4.755.25 V 静态供应电压8.010.0mV温度范围工作范围+70 ℃ 指定范围-40 +85 ℃-40+125自动范围℃系统操作说明一一ADXL05kQ kQ kG流耦合连接(满量程范围± 1.5g )-+5V C3―O Vout标称值Rl=49. 9R3=249(如无特殊说明 0g 偏差水平=+2.5V, C1 =0.022. F, R2 = 2.57R3)参数状态ADXL05J/A单位最小值典型值最大值缓冲放大倍数G = R3/R15满量程范围-1.5 +1.5g灵敏度+25 ℃875 1000 1125mV/g温度漂移T〜T±0.5读数的百分比MIN MAX0g偏差水平+25 ℃ 2.5V温度漂移+25℃〜T或T2/5mVMIN MAX频率响应C4=3.3. F, R1=49.9k Q 1 1000Hz说明:电阻公差将影响系统的准确度。
ATAGO 数字折射率仪 DR-A 1 和 DR-A 1-Plus 的说明书
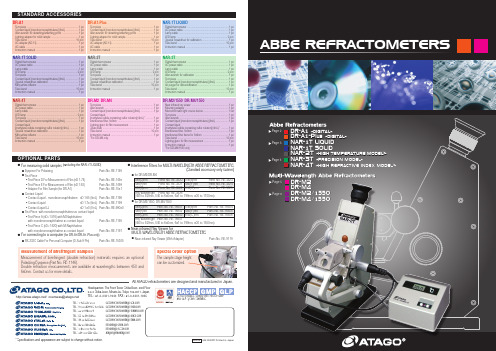
ATAGO products comply with HACCP,GMP, and GLP system standards.AllATAGO refractometers are designed and manufactured in Japan.TEL : 1-425-637-2107*****************************TEL : 91-22-28544915, 40713232 *******************************TEL : 86-20-38108256 ********************TEL : 66-21948727-9 **********************************TEL : 55 16 3913-8400 ********************************TEL : 39 02 36557267 ********************************TEL : 7-812-777-96-96 *********************TEL : 234-707-558-1552**********************Headquarters: The Front T ower Shiba Koen, 23rd Floor 2-6-3 Shiba-koen, Minato-ku, Tokyo 105-0011, JapanTEL : 81-3-3431-1943 FAX : 81-3-3431-1945/******************NAR-1T LIQUIDDigital thermometer ···························································1 pc AC power cable ·································································1 pc Lamp cable ·······································································1 pc LED lamp ········································································3 pcs Special screwdriver for calibration ······································1 pc Tube band ·····································································10 pcs Instruction manual ·····························································1 pcDR-A1DR-A1-PlusTest piece ··········································································1 pc Contact liquid [monobromonaphthalene] (4mL) ··················1 pc Allen wrench for detaching/attaching prism ·······················1 pc Lighting adapter for solid sample ·······································1 pc Tube band ·····································································10 pcs AC adapter (AD-13) ···························································1 pc AC cable ···········································································1 pc Instruction manual ·····························································1 pcTest piece ··········································································1 pc Contact liquid [monobromonaphthalene] (4mL) ··················1 pc Allen wrench for detaching/attaching prism ·······················1 pc Lighting adapter for solid sample ·······································1 pc Tube band ·····································································10 pcs AC adapter (AD-13) ···························································1 pc AC cable ···········································································1 pc Instruction manual ·····························································1 pcNAR-1T SOLIDDigital thermometer ···························································1 pc AC power cable ·································································1 pc Lamp cable ·······································································1 pc LED lamp ········································································3 pcs Test piece ··········································································1 pc Contact liquid [monobromonaphthalene] (4mL) ··················1 pc Special screwdriver calibration ···········································1 pc Milky white reflector ···························································1 pc Tube band ·····································································10 pcs Instruction manual ·····························································1 pcNAR-2TDigital thermometer ···························································1 pc AC power cable ·································································1 pc Lamp cable ·······································································1 pc LED lamp ········································································3 pcs Test piece ··········································································1 pc Contact liquid [monobromonaphthalene] (4mL) ··················1 pc Special screwdriver calibration ···········································1 pc Tube band ·····································································10 pcs Instruction manual ·····························································1 pcNAR-3TDigital thermometer ···························································1 pc AC power cable ·································································1 pc Lamp cable ·······································································1 pc LED lamp ········································································3 pcs Allen wrench for calibration ················································1 pc Test piece ··········································································1 pc Contact liquid [monobromonaphthalene] (4mL) ··················1 pc Air purger for dehumidfication ············································1 pc Tube band ·····································································10 pcs Instruction manual ·····························································1 pcNAR-4TDigital thermometer ···························································1 pc AC power cable ·································································1 pc Lamp cable ·······································································1 pc LED lamp ········································································3 pcs Test piece ··········································································1 pc Contact liquid [monobromonaphthalene] (4mL) ··················1 pc Contact liquid[methylene iodide containing sulfur solution] (4mL) ·············1 pc Special screwdriver calibration ···········································1 pc Milky white reflector ···························································1 pc Tube band ·····································································10 pcs Instruction manual ·····························································1 pcDR-M2 DR-M4Test piece ··········································································1 pc Allen wrench ······································································1 pc Contact liquid [monobromonaphthalene] (4mL) ··················1 pc Contact liquid[methylene iodide containing sulfur solution] (4mL) * ··········1 pc Interference filter, 589nm ···················································1 pc Lighting glass for film measurement ···································1 pc Spare bulb ·········································································1 pc Tube band ·····································································10 pcs Instruction manual ·····························································1 pc *For DR-M4 onlyDR-M2/1550 DR-M4/1550Near infrared ray viewer ·····················································1 pc Mounting adapter ······························································1 pc Monochromatic light source device ···································1 set Test piece ··········································································1 pc Allen wrench ······································································1 pc Contact liquid [monobromonaphthalene] (4mL) ··················1 pc Contact liquid[methylene iodide containing sulfur solution] (4mL) * ··········1 pc Interference filter, 589nm ···················································1 pc Interference filter frame for 589nm ·····································1 pc Tube band ·····································································10 pcs Lighting glass for film measurement ···································1 pc Instruction manual ·····························································1 pc *For DR-M4/1550 only1 <DIGITAL>DR-M2 DR-M4 DR-M2/1550 DR-M4/1550For measuring solid samples (excluding the NAR-1T LIQUID)Eyepiece For Polarizing Parts No. RE-1146Test Piece •Test Piece D For Measurement of Film (nD 1.74) Parts No. RE-1498 •Test Piece E For Measurement of Film (nD 1.92) Parts No. RE-1499 •Adapter For Film Sample (for DR-A1)Parts No. RE-1581 Contact Liquid•Contact Liquid - monobromonaphthalene nD 1.65 (4mL) Parts No. RE-1196 •Contact Liquid nD 1.78 (4mL) Parts No. RE-1199 •Contact Liquid LJnD 1.80 (7mL) Parts No. RE-99080Test Piece with monobromonaphthalene as contact liquid•Test Piece A (nD=1.516) with M-Naphthalene with monobromonaphthalene as contact liquid Parts No. RE-1195•Test Piece C (nD=1.620) with M-Naphthalenewith monobromonaphthalene as contact liquidParts No. RE-1197 For connecting to a computer (for DR-A1/DR-A1-Plus only)RS-232C Cable For Personal Computer (D-Sub 9 Pin)Parts No. RE-15305 Interference Filters for MULTI-WAVELENGTH ABBE REFRACTOMETERS (Standard accessory only 589nm)Near-infrared Ray Viewer forMULTI-WAVELENGTH ABBE REFRACTOMETERSNear-infrared Ray Viewer (With Adapter)Parts No. RE-9119Measurement of birefringent (double refraction) materials requires an optional Polarizing Eyepiece (Part No. RE-1146).Double refraction measurements are available at wavelengths between 450 and 680nm. Contact us for more details.for DR-M2/DR-M4for DR-M2/1550, DR-M4/1550Measurement of Birefringent Samples。