丰田模式讲师用电子版TPS(TL)中文 标准手持
标准作业的三要素(含手持图)002

03
3、标准作业的条件
1、以人的动作为中心 2、重复作业
三、标准作业三要素
1、节拍时间TT 2、作业顺序 3、标准手持
三、标准作业三要素
1、生产节拍
用来衡量必须在几分几秒生 产出1台或1件部品的时间 基准
节拍时间
=
生产时间(定时) -----------------------------
生产必要数量
丰田生产方式 标准作业
旭日传播
丰田生产方式 标准作业
旭日传播
一、标准作业推行的背景条件
丰田生产方式 的两大支柱
基本原则
实施工具与方法
1、工序的流程化
物 --- 同期化
1
JUST IN TIME
2、以需要的数量决定T.T 人 ---- 多技能工
3、后工序领取
设备 ---- 按工序顺序配置
出现异常停机
CT (循环时间)指操作者一个人进行标准作业时, 毫不困难的、最快 的、一个循环内的实际作业时间(包括步行时间), 但不包括空手等待 时间。 注: ① CT是指按照操作顺序,进行一个循环作业时的最短时间。 ② 每数次操作发生一次的、测定、更换刀具等作业的时间,不纳入CT中 计算
2、作业顺序
操作者能够效率最好的生产合格品的生产操作顺序,这里需要区 别“工序顺序”和“作业顺序” ① 工序顺序是工艺文件上规定的加工先后顺序 ② 作业顺序是操作者的生产操作顺序 ③ 实际生产中作业顺序与工序顺序是往往不相同的
2、作业顺序
指技能员搬运物品、安装到 机器上,卸下部品等有效的 作业顺序
三、标准作业三要素
3、标准手持
为了确保能够按相 同的顺序进行反复 作业而需要在工程 内保持的最小数量 的未完成品。
丰田生产方式—TPS.pptx

10/22/2020
精益生产方式培训教材
不同生产方式的作用(4)
最终目标不同:Байду номын сангаас
大量生产厂家为自己建立了一个有限的目标—— “足够好”,这意味着可以容忍一定的废品率、 最大限度的库存量、系列范围很窄的标准产品 (他们争辩要做的更好就要花费更多的资金或 者是超出原有人员的能力范围)
精益生产厂家则把自己的目光确定在“尽善尽美”
1937年丰田公司成立 1961年日本汽车产量超过意大利跃居世界第五位
; 1965年超过法国居第四位; 1966年超过英国升为第三位; 1968年追上西德居世界第二位。 1980年日本汽车产量首次突破1000万辆大关,达
1104万辆,一举击败美国成为“世界第一”
10/22/2020
精益生产方式培训教材
产品,用非熟练与 通用化、系列化,实行多品
半熟练的工人采用 种、小批量生产,满足市场
昂贵的专用设备进 多品种需要。丰田生产方式
行生产。引用标准 是继承单件生产方式和福特
化、通用化,大量 生产方式的优点,克服了他
流水生产、低成本 们的缺点。适应市场多元化
。缺点是品种单一 的产物,也可以简单的说他
,不能多品种适应 是一种多品种、小批量混合
10/22/2020
精益生产方式培训教材
TPS的完整体系(3)
六、多能化,少人化(用最少的人干最多 的事情——多岗位培训、标准化作业)
七、TPM(全面生产性维护)活动的展开 八、5S现场管理的彻底化 九、全员改善活动与合理化提案制度 十、全员教育的培训制度
10/22/2020
精益生产方式培训教材
丰田汽车发展史
精益生产方式
(丰田生产方式—TPS) 李彬
TPS(ToyotaProductionSystem)丰田模式的14项原则

TPS(ToyotaProductionSystem)丰田模式的14项原则原则1:管理决策以长期理念为基础,即使因此牺牲短期财务目标也在所不惜。
1)企业的目标应该有长期目标,永续经营比短期财务目标更加重要。
不能看到短期利润率而忽视长期盈利能力和生存能力,必须牺牲短期利益而追求长远利益,这样企业才能生存长久;2)管理决策的关注点(focus)应该是顾客(包含外部和内部顾客)与社会。
企业必须使顾客满意才能生存,必须符合社会和相关方的期望,要满足法律法规要求,要不断提高社会责任形象;评估公司每个部门为顾客和社会创造价值的能力;4)要有责任感。
努力决定自己的命运,依靠自己,相信自己的能力。
对自己的行为以及保持并提高创造价值的技能等负起责任。
原则2:建立连续的作业流程以使问题浮现。
1)重新设计工作流程,使其变成创造高附加价值的连续流程(one flow一个流)。
尽力把所有计划中闲置或等候他人的工作时间减少到零(七大浪费)。
2)建立快速输送材料与信息的流程,使流程与人员紧密地联结在一起,以便立即浮现问题(SMED快速换模)。
3)使整个企业文化重视流程,这是促成真正的持续改善及员工发展的关键(改善Kaizen)。
原则3:使用拉动式生产方式以避免生产过剩(pull system)。
1)在生产流程下游的顾客需求的时候,供应给他们正确数量的正确产品。
材料的补充应该由消耗量决定,这是准时生产的基本原则(just-in-time)。
2)使在制品及仓库存货减少至最少,每项产品只维持少量存货,根据顾客实际领取的数量,经济地补充存货。
按顾客每天的需求来变化,而不是事后来分析和追踪浪费的存货。
原则4:生产均衡化(balance)。
使工作负荷平均,像龟兔赛跑中的乌龟一样均衡。
1)杜绝浪费只是实现精益所必须做的1/3,避免员工与设备的工作负荷过重,这与避免生产安排的不均匀同等重要(7种浪费)。
2)尽量使所有制造与服务流程的工作负荷平均化(生产节拍Takt Time),以取代大多数公司实行的批量生产方法中经常启动、停止的做法。
详细讲解丰田精益生产管理模式

(条件)
平准化生产
节拍时间
后工程引取
TTMC
单击此处添加大标题内容
单击此处添加正文,文字是您思想的提炼,为了演示发布的良好效果,请言简意赅地阐述您的观点。您的内容已经简明扼要,字字珠玑,但信息却千丝万缕、错综复杂,需要用更多的文字来表述;但请您尽可能提炼思想的精髓,否则容易造成观者的阅读压力,适得其反。正如我们都希望改变世界,希望给别人带去光明,但更多时候我们只需要播下一颗种子,自然有微风吹拂,雨露滋养。恰如其分地表达观点,往往事半功倍。当您的内容到达这个限度时,或许已经不纯粹作用于演示,极大可能运用于阅读领域;无论是传播观点、知识分享还是汇报工作,内容的详尽固然重要,但请一定注意信息框架的清晰,这样才能使内容层次分明,页面简洁易读。如果您的内容确实非常重要又难以精简,也请使用分段处理,对内容进行简单的梳理和提炼,这样会使逻辑框架相对清晰。为了能让您有更直观的字数感受,并进一步方便使用,我们设置了文本的最大限度,当您输入的文字到这里时,已濒临页面容纳内容的上限,若还有更多内容,请酌情缩小字号,但我们不建议您的文本字号小于14磅,请您务必注意。单击此处添加正文,文字是您思想的提炼,为了演示发布的良好效果,请言简意赅地阐述您的观点。您的内容已经简明扼要,字字珠玑,但信息却千丝万缕、错综复杂,需要用更多的文字来表述;但请您尽可能提炼思想的精髓,否则容易造成观者的阅读压力,适得其反。正如我们都希望改变世界,希望给别人带去光明,但更多时候我们只需要播下一颗种子,自然有微风吹拂,雨露滋养。恰如其分地表达观点,往往事半功倍。当您的内容到达这个限度时,或许已经不纯粹作用于演示,极大可能运用于阅读领域;无论是传播观点、知识分享还是汇报工作,内容的详尽固然重要,但请一定注意信息框架的清晰,这样才能使内容层次分明,页面简洁易读。如果您的内容确实非常重要又难以精简,也请使用分段处理,对内容进行简单的梳理和提炼,这样会使逻辑框架相对清晰。为了能让您有更直观的字数感受,并进一步方便使用,我们设置了文本的最大限度,当您输入的文字到这里时,已濒临页面容纳内容的上限,若还有更多内容,请酌情缩小字号,但我们不建议您的文本字号小于14磅,请您务必注意。单击此处添加正文,
TPS丰田生产方式中文版(完整版)_2.pptx

• JIT的基本原则
1.工序的流动化
JIT成为可能的大前提
均衡化生产
2.根据必要数量决定节拍时间 3.后工序拉动
KANBAN(看板)
JIT得以实现的
管理改善之道
6
6
我们关注企业的愿景,是帮助企业提升竞争力的发动机!
:JIT的实现
・
・工序的流动化
HLEAN SYSTEM 幸福·精益 高效企业管理系统!
以提高新产品完善程度的活动。
(Simultaneous Engineering)
生产准备活动 ・工序计划 ・ 设备设计
制造准备活动 ・讨论量试・制作作业标准书
现场活性化活动 ・5S+QC活动+创意提案+技能认证+可视化
生产改善活动 生产活动
・工序改善 ・物流改善
自主研究会、生产会议
原来的TPS
业务范围 的扩展
1:管理状態にない 2:不具合が見られ、維持されていない 3:ほぼ定着している 4:定着している、 5:定着(習慣)され、工夫がされている
⑰ ・5Sに関するルールは決められているか ⑱ ・4S点検は定期的に実施されているか ⑲ ・不具合の再発防止は確実か ⑳ ・働き易い 職場になっているか、
HLEAN SYSTEM 幸福·精益 高效企业管理系统!
(3)顾客满意度 CS活动:Customer Satisfaction
・
・CS提升活动:「怎样才能卖出去?」
「怎样做顾客才能满意?」
TOYOTA
(工厂)
顾客有了需求
・新产品开发 ・确保质量 ・严守交期 ・设置CS生产线
・以顾客为对象的CS提升
・在所有部门、全部业务展开 ・自主研究会・现场的活性化
丰田公司的tps管理模式

丰田公司的tps管理模式迈向Just-In-Time管理的道路--丰田公司的TPS管理模式丰田的生产和管理系统长期以来一直是丰田公司的核心竞争力和高效率的源泉,同时也成为国际上企业经营管理效仿的榜样,例如,作为丰田生产管理一大特点的看板管理已被世界各地的企业所采用。
如今,世界很多大型企业都在学习丰田管理模式的基础上,建立了各自的管理系统,以试图实现标杆超越,像通用电气公司、福特公司、克莱斯勒公司等世界著名企业都加入了这一行列。
但是,令人惊异的是,尽管丰田管理模式已为全球所认同和接受,真正成功的企业却并不多,如今位于日本的丰田公司每天都要接受数以万计的企业高级管理者参观,这些参观者将他们看到的管理方式带到本国后,并没有得到意想的效果,为此,很多人认为丰田管理模式的成功根源于其独特的文化因素。
但事实并非如此,例如同是日本公司的尼桑和本田却并没有达到丰田的标准,而丰田本身却将其独特的管理模式带到了全世界,这其中的代表就是位于美国肯塔基州的丰田乔治城汽车生产厂,该厂自1988年7月开始在1300英亩的厂址上进行批量生产,年生产能力为200000辆Camry轿车,相当于以往美国从日本进口同类型轿车的总量,1991年秋天丰田美国公司引入了全新的Camry轿车,1992年该类型车的供应量为40000辆,销售额将增加20%。
新的Camry轿车属于中等家庭车系列,占有美国所有轿车市场l/3的市场份额,价格平均为$18500,税前平均利润为17%,显然,其经营绩效是十分瞩目的。
由此看来,丰田管理模式并不是因为其独特的日本文化而难以为其他国家的企业所学习,之所以存在管理方法难以移植的情况,主要原因在于参观者所看到的丰田管理模式只是其外在的东西,诸如它的活动、连接和生产流等都是较为固定、甚至死板的东西,但是,在这些看似简单的活动和流程后面,却蕴含着丰田公司巨大的柔性和适应性,正是这些看似简单、却颇具柔性的管理特点,造就了丰田公司举世瞩目的经营业绩,也使得他的柔性化生产管理方式--TPS(Toyota Production System)成为管理中的精髓,并使大规模定制模式下的敏捷产品开发和生产成为现实。
丰田式生产模式TPS名词讲解
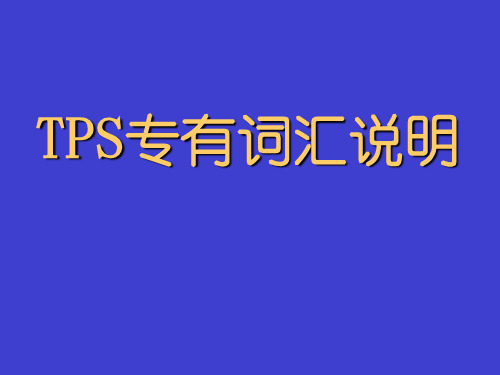
1).丰田式的制造方法:
生产现场作成物的流动
过去
1人1机
车床 车床 车床
分
铣床 铣 床 铣 床
别
集
钻床 钻床 钻床
中
现在 车 床 铣 床 钻 床 提高生
产力
依制造过程一个流为原则的方式
2). 实行『刚好及时』生产
(1)依据上述方法,以看板为手段。
(2)看板扮演了物品之『领取情报』或 『运搬指示情报』,或作为生产工程内 之作业指示情报。
1971本社/元町工厂 冲床换模时间(3分)
1950目视管理的 灯号方式(在引 擎装配线采用)
1955本社工厂装配 线生产方式(灯号、 停止钮、混载搬运)
1962机械采用总 量限制 机械防呆装置
1961元町工厂装 配场设置灯号
1966上乡 工厂完成 自动线
1.丰田生产方式
(TOYOTA Production System)
a)生产线正常运转:绿色 b)设备异常:红色
6.看板(Kanban)
1)『看板』就是为了实现丰田生产方式第一支 柱刚好及时的管理道具
2) 多半用小纸片放入四角型的塑料袋中 3) 纸片上显示着:
a)要领取什么?多少?
b)『制造什么产品?怎样去制造?』
4)看板的类型: a)领取看板或搬运看板:后工程到前工程去 领取,其间作为『领取情报』或『搬运指 示情报』来联系的。 b)工程内看板:为使前工程只制造被取用数 量而指示生产的。
2)标准作业的三大要素: (1)表示必须以几分几秒制造一台或一个的 『节拍时间』
(2)随着时之经过而进行作业的『作业顺序』
(3)为能顺利进行作业,工程内所须的最少 制品,亦即『标准在制品』量。
丰田TPS(TL)中文--标准手持

30
某暖炉厂的事例
A
B
Manufacturing Management Course
C
L
改善前 12种炉子 (A ~L)每种1年仅生产1次
Lead time
最长1年
1 2 3 4 5 6 7 8 9 10 11 12 月
淡季
ABCDE F GHI J KL
31
4
Ⅰ.支撑丰田生产方式的经营观点·理念
1. 企业的目的
持续追求与国际社会的协调发展,
(丰田通过供应汽车)
完成社会的使命
・精神、物质文明更加丰富的生活 ・通过公司激活地区发展 ・使员工有稳定的生活基础
为此,首先要赢利,使公司长期生存下去
5
2. 不降低成本就无法提高利润
(1) 销售价 = 成本 + 利润 原价(成本)主义
間2 送 3歩
ー
ワーク取り外し取付け、送りをかける
25
ワワ粗MDーー34IRクク取 取材--12り りを74外 外62し し44取取 取ワワDTるーー付 付46RPクク5取 取け け--21り り、、送 送41外 外20り りし し41を を取 取ワか かTネー付 付Pクけ け完取け け-ジる る1り、、成送 送1径外0り り品し1をを を取をか か測付け け置け定る る、く送すりるを332かける
20 ″
作成 年月日 25 ″ 30 ″ 所属
62.11.30 35 上″ 郷 40 機″ 械部45 ″
直当り 必要数 50 ″タク全5ト5 ″ タイム
920/ 直 個 6ペ0 ″ー3ジ06中5 ″ 分秒
手作業 70 ″ペー75ジ″自動8送0 ″り
歩行
丰田讲师用电子版TPS中文
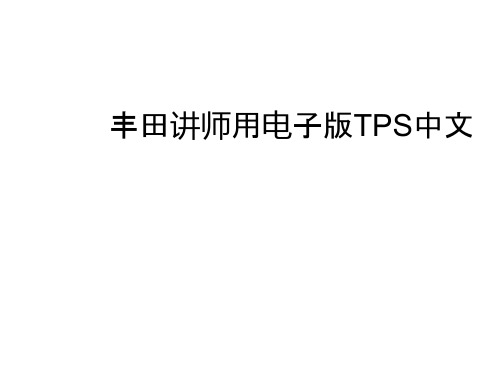
完成社会的使命
・精神、物质文明更加丰富的生活 ・通过公司激活地区发展 ・使员工有稳定的生活基础
为此,首先要赢利,使公司长期生存下去
5
2. 不降低成本就无法提高利润
(1) 销售价 = 成本 + 利润
成本主义
(2)
利润 = 销售价 - 成本
降低成本
(1) 成本主义
(2) 降低成本
利润
销售价
成本
利润 销售价
部品生产的 周期时间
〈停滞为什么会发生?〉
加工时间长
流程复杂
停滞时间长
制造方法不良
物流不良
37
4.导致周期时间变长的停滞为何会发生?
(1) 流程复杂
(2) 制造过程中的不合理 1) 批量大小过大 2) 根据客户需求生产的概念淡薄
(3) 物流不合理
38
(1) 流程复杂
a. 广义的流程
中间工序外协生产,造成影响。
観1測7イ1ン技1テ1ー能-ク2作4マ員0ニ6ホ記0ルト号業゙インフデ名ースーターク穴マ称加ニ工ホルド
時間 手 標送準作歩5 ″業組10合″ せ15票″
20 ″
作成 年月日 25 ″ 30 ″ 所属
T.T62.11.30 35 上″ 郷 40 機″ 械部45 ″
直当り 必要数
920/ 直
個
50 ″タク全5ト5 ″ ペ6ー0 ″ジ中3065 ″ ペ7ー0 ″ジ
e f g
h
i j
k l
m n o p
工序中的分歧合并点较多,产品滞留点增多。
导致半成品何时能加工成成品都不明确
40
c. 导入低成本的设备,整理流程。
迷路消除
A
B
丰田关于职场运营三本柱的管理
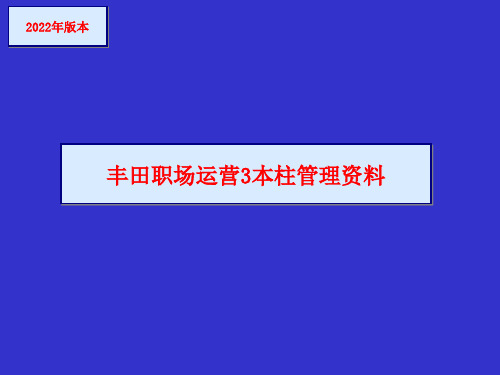
运
②
改善QA评价的弱点
加
营
工
组装不良的
点
未然防止
管
3
理
一次性调刀成功保证精度
刃具管理与加工不良的 未然防止
型整备的标准化 材料不良的未然防止
本
在清洁室中进行刀具管理
柱
③
15分钟点检
自
主
保
全
发现微小缺陷
挂飞子,摘飞子
发现问题的处置对策 修复作业顺利实施
改善
保全基准的修订・实施
设备故障的未然防止
改善事例进行横向展开
人+素养
成本
・工作图 ・要领书 ・良品条件 ・QC工程标准
・规定 ・OSHMS
・品质改善 ・不良对策 加工点管理
・设备能力 ・月度计划
・CO2低減 ・出勤率 ・受援率 •总费用 ・废弃物低減・要员管理・时间管理 •生产性
・节拍
・ISO对应 ・教育/训练・技能 •产品成本
・设备故障(TPM)
现场运营
变化点最小化
改善
通过交流沟通收集意见
④ 标准类的改订
③ 确认安全与品质
认为哪里有问题,再次进行 PDCA的循环
务必实施变化点的跟踪
「 根据标准3票把握作业方法与作业量 」
标准作业票
标准作业组合票
人的动作的标准化
山积票
把握整体负荷量
1人工的作业时间
以要素单位制作作业要领书
①把握作业时间 ②动作固定化 ③确认整体负荷量
工序的流程化
节拍 后工程取用
自働化
·如有异常 停机等待 ·人的工作 与机械工作 的分离
平
标准作业
准
作业顺序
丰田生产模式TPS学习:工业工程之防错法(Poka-Yoke)-2020.8-105页
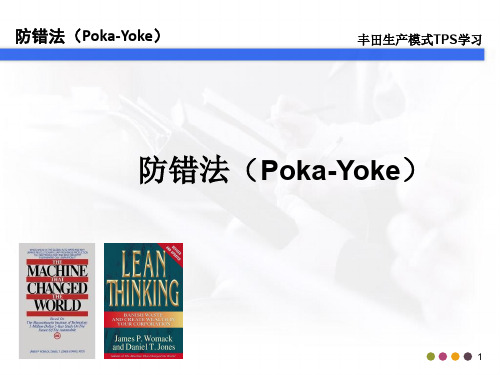
防错法(Poka-Yoke)
丰田生产模式TPS学习
防错法的作用:
在作业过程中,作业者不时会因疏漏或遗忘而发生作业 失误,由此所致的质量缺陷所占的比例很大,如果能够用防 错法防止此类失误的发生,则质量水平和作业效率必会大幅 提高。 1、防错法意味着“第一次就把事情做好”。
因为防错法采用一系列方法和或工具防止失误的发生, 某结果即为第一次即将事情做好。 2、提升产品质量,减少由于检查而导致的浪费。 3、消除返工及其引起的浪费。
33
防错法(Poka-Yoke)
丰田生产模式TPS学习
三类检测方法和区别:
3、溯源型检测: 溯源型检测是真正意义上的预防型检测。它通过对源头
上即设计阶段进行检测从而确保产品和制造过程设计能够满 足质量要求。根据质量杠杆原理,在此阶段的检测收益比判 断式检测高一百倍,目前很多公司已认识到溯源型检测的意 义,开始探索和实施溯源型检测。
丰田生产模式TPS学习
产生失误的一般原因:
3、识别错误: 识别错误是对工作指令或程序判断或理解错误所致。如
作业指导书说明烧焊时必须预热到铜管变成鲜红色,但焊工 却误以为预热一下就可以了。 4、缺乏工作经验:
由于缺乏工作经验,很容易产生失误,如,让一个从未 在企业中做过的人去进行制造过程管理,就比较容易产生失 误。
21
防错法(Poka-Yoke) 产生失误的其他原因:
丰田生产模式TPS学习
22
防错法(Poka-Yoke) 产生失误的其他原因:
丰田生产模式TPS学习
23
防错法(Poka-Yoke) 产生失误的其他原因:
丰田生产模式TPS学习
24
防错法(Poka-Yoke) 产生失误的其他原因:
丰田TPS

一、3二、 目的:通过确保利润,保障企业续存和员工生活三、 利润出处:1.外界因素(市场定价及销售量)---由不得我们做主2.自身控制(制造的方法)---可通过不断发现、分析、改善降低成本,确保利润四、 追求目标:1.通过彻底排除浪费降低成本---降低制造成本,提升利润空间2.在必要的时间生产必要数量的产品---提升生产效率,消除浪费3.质量更高,更加便宜---满足客户需求,提高市场竞争力4.组建能够迅速应对变化的强有力的职场五、 出发点:杜绝浪费六、 杜绝浪费的方法:1.必须不断的进行改善活动2.七大浪费及措施:库存、搬运、等待---物的浪费动作、作业、过量生产---人员、设备的浪费不良品返修---质的浪费七、 改善1.指标的量化:①作业的增值活动覆盖率100%;②完成品优质率100%;③设备稼动率100%;设备稼动率=(作业时间-流失时间)/作业时间×100%2.改善定义:丰田式解决问题(TBP )① 当前水平与设定水平的差距---一般问题解决(必然问题≠改善)②设定水平与期待水平的差距---丰田式问题解决(特定问题=改善)3.遵循PDCA 循环①明确问题② 分解问题③ 设定目标④ 把握真因⑤ 制定对策⑥ 贯彻实施对策⑦ 评价结果和过程⑧巩固成果把它列到标准作业书中,防止新人操作失误或错误动作重复发生4.改善三原则:①消除的思考:不断在生产过程中发现、分析、判断继而达到消除的意识;②减少的活动:减少浪费、成本、时间、空间、人员投入、无附加值的动作等;③再一次寻找机会的活动:善于发现生产过程中每一个可改善的机会,以便实现持续的改善。
七、TPS 的两大支柱:准时化(JIT)、自动化准时化生产1.目的:缩短生产周期=加工时间+停滞时间2.三原则:①后工序的引取(拉动式生产)②工序的流程(一个流制造方法)③遵守生产节拍2.前提:平准化4.收益:①消除各工序间的库存②保持均衡劳动量③提高效率④保证质量5.措施和方法:①看板/5S/3定(定点定容定量)②平准化③小批量单一流程减少准备交替时间④多功能化保留多工序⑤少人化⑥标准作业平准化生产1.三要素:①工序的流动化--- 一个流制造方法,提升生产效率,减少制造过程中的动作、搬运、等待、加工、库存、不良品的浪费②生产节拍---作业标准化,按生产必要数将生产环节的瓶颈工序细化并制定节拍,使作业者的工作量相等,消除停滞;将其他工序按瓶颈工序节拍进行,可达到少人化 ---消除工序间存量③拉动式生产---使用工具是看板,通过定时不定量(远途采购件入库)、定量不定时(对附近采购商)、定时又定量(往各工序配送的部件,目的是减小配装工具,使生产线保持整洁畅通)的配送方式,抑制制造过多产生的库存浪费2.平准化生产的缺点:①对培训的要求较高,各工序作业标准化,为保持节拍,对复杂工序进行细化,细化后的每道工序的标准书(标准动作及控制点)必须跟进②对设备和技术要求较高,增加了资金投入(对易错工序进行防呆技术保证,对小批量生产和多品种作业,要求实施柔性生产并引进成组技术)③较难适应市场需求变动大的情况。
丰田车的管理模式
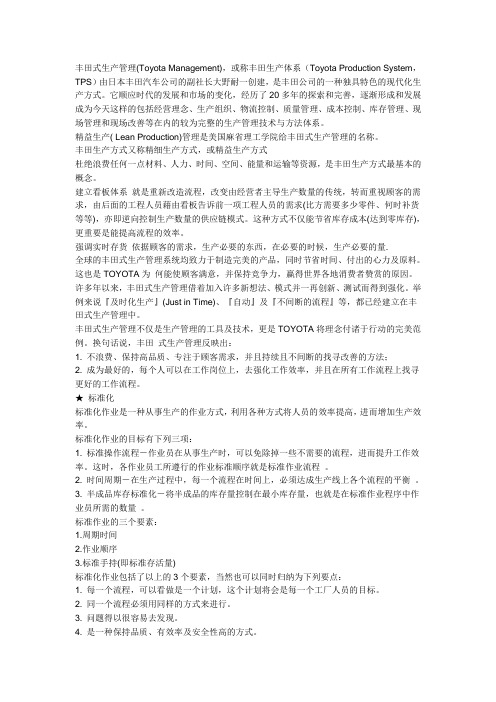
丰田式生产管理(Toyota Management),或称丰田生产体系(Toyota Production System,TPS)由日本丰田汽车公司的副社长大野耐一创建,是丰田公司的一种独具特色的现代化生产方式。
它顺应时代的发展和市场的变化,经历了20多年的探索和完善,逐渐形成和发展成为今天这样的包括经营理念、生产组织、物流控制、质量管理、成本控制、库存管理、现场管理和现场改善等在内的较为完整的生产管理技术与方法体系。
精益生产( Lean Production)管理是美国麻省理工学院给丰田式生产管理的名称。
丰田生产方式又称精细生产方式,或精益生产方式杜绝浪费任何一点材料、人力、时间、空间、能量和运输等资源,是丰田生产方式最基本的概念。
建立看板体系就是重新改造流程,改变由经营者主导生产数量的传统,转而重视顾客的需求,由后面的工程人员藉由看板告诉前一项工程人员的需求(比方需要多少零件、何时补货等等),亦即逆向控制生产数量的供应链模式。
这种方式不仅能节省库存成本(达到零库存),更重要是能提高流程的效率。
强调实时存货依据顾客的需求,生产必要的东西,在必要的时候,生产必要的量.全球的丰田式生产管理系统均致力于制造完美的产品,同时节省时间、付出的心力及原料。
这也是TOYOTA为何能使顾客满意,并保持竞争力,赢得世界各地消费者赞赏的原因。
许多年以来,丰田式生产管理借着加入许多新想法、模式并一再创新、测试而得到强化。
举例来说『及时化生产』(Just in Time)、『自动』及『不间断的流程』等,都已经建立在丰田式生产管理中。
丰田式生产管理不仅是生产管理的工具及技术,更是TOYOTA将理念付诸于行动的完美范例。
换句话说,丰田式生产管理反映出:1. 不浪费、保持高品质、专注于顾客需求,并且持续且不间断的找寻改善的方法;2. 成为最好的,每个人可以在工作岗位上,去强化工作效率,并且在所有工作流程上找寻更好的工作流程。