自适应多级变速配料控制系统在饲料厂中的应用
饲料生产全线控制系统方案
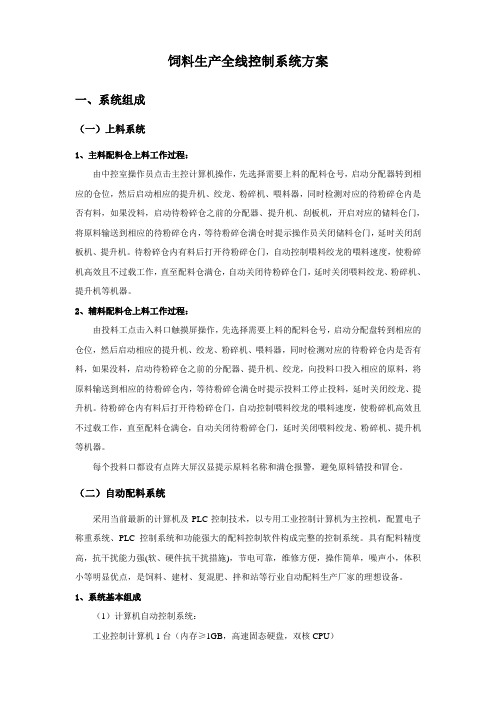
饲料生产全线控制系统方案一、系统组成(一)上料系统1、主料配料仓上料工作过程:由中控室操作员点击主控计算机操作,先选择需要上料的配料仓号,启动分配器转到相应的仓位,然后启动相应的提升机、绞龙、粉碎机、喂料器,同时检测对应的待粉碎仓内是否有料,如果没料,启动待粉碎仓之前的分配器、提升机、刮板机,开启对应的储料仓门,将原料输送到相应的待粉碎仓内,等待粉碎仓满仓时提示操作员关闭储料仓门,延时关闭刮板机、提升机。
待粉碎仓内有料后打开待粉碎仓门,自动控制喂料绞龙的喂料速度,使粉碎机高效且不过载工作,直至配料仓满仓,自动关闭待粉碎仓门,延时关闭喂料绞龙、粉碎机、提升机等机器。
2、辅料配料仓上料工作过程:由投料工点击入料口触摸屏操作,先选择需要上料的配料仓号,启动分配盘转到相应的仓位,然后启动相应的提升机、绞龙、粉碎机、喂料器,同时检测对应的待粉碎仓内是否有料,如果没料,启动待粉碎仓之前的分配器、提升机、绞龙,向投料口投入相应的原料,将原料输送到相应的待粉碎仓内,等待粉碎仓满仓时提示投料工停止投料,延时关闭绞龙、提升机。
待粉碎仓内有料后打开待粉碎仓门,自动控制喂料绞龙的喂料速度,使粉碎机高效且不过载工作,直至配料仓满仓,自动关闭待粉碎仓门,延时关闭喂料绞龙、粉碎机、提升机等机器。
每个投料口都设有点阵大屏汉显提示原料名称和满仓报警,避免原料错投和冒仓。
(二)自动配料系统采用当前最新的计算机及PLC控制技术,以专用工业控制计算机为主控机,配置电子称重系统、PLC控制系统和功能强大的配料控制软件构成完整的控制系统。
具有配料精度高,抗干扰能力强(软、硬件抗干扰措施),节电可靠,维修方便,操作简单,噪声小,体积小等明显优点,是饲料、建材、复混肥、拌和站等行业自动配料生产厂家的理想设备。
1、系统基本组成(1)计算机自动控制系统:工业控制计算机1台(内存≥1GB,高速固态硬盘,双核CPU)WINDOWS XP操作系统19"宽屏液晶显示器(2)电子秤系统:采用智能称重仪表,直接按键操作,清零、校称简单快捷。
自动配料控制系统的设计
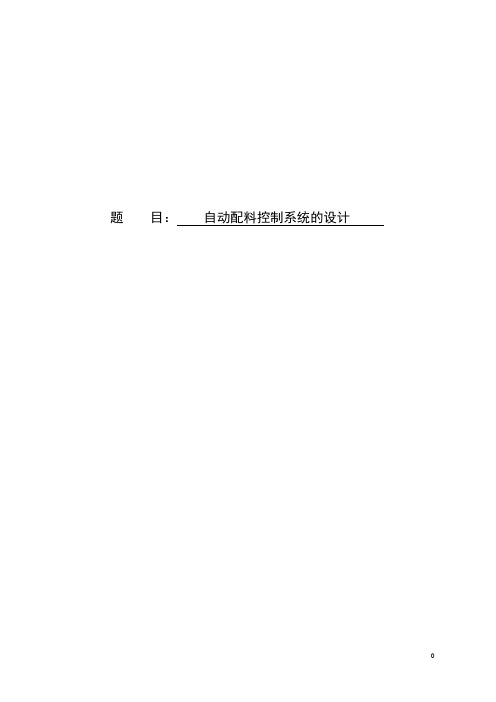
题目:自动配料控制系统的设计内容摘要自动配料系统是一种在线测量动态计量系统,集输送、计量、配料、定量等功能于一体,在冶金、建材、化工、饲料加工等行业中得到广泛应用。
设计开发自动配料优化控制系统,对于改善劳动条件、提高产品质量和生产效率具有十分重要的现实意义。
本文首先对自动配料系统的应用背景、发展趋势进行了综述,针对当前配料生产企业工艺水平相对落后、自动化水平低、生产效率低等不足,设计了一个自动配料优化控制系统,系统能够工作在全自动、远程手动以及本地手动三种模式下。
在硬件设计上,采用工控机与PLC相结合的总体控制结构,由工控制机实现系统的管理和远程监控,PLC完成设备级的动作控制及相关信号的处理,通过以太网及RS-485总线实现系统的联接与通信;改进了配料车定位系统,利用设计的定位盒实现位置编码方案,提高了定位精度。
在软件设计上,设计开发了画面实时监控和数据库管理(SCADA)等上位机应用软件,能够保存产品配方、料仓数据、实时数据等,并能够实现历史数据查询、报表打印、实时数据及状态显示、远程控制等功能,两台上位机数掘库能够有效地保持同步。
设计了下位机PLC主控程序以及通信、配料精度控制和配料车行走子程序。
针对配料系统普遍存在的配料落差控制问题,采用了一种基于模糊自适应结合PID的复合型预测控制算法,算法将模糊自适应控制宽范围快速调节和PID精确调节的特点有机结合起来,当系统的偏差大于某一设定值时,采用结合了人的经验的模糊自适应规则控制,当系统偏差小于设定值时采用PID控制,模糊控制器的两个输入分别为系统期望值和偏差,通过不同的期望值,预测不同的空中落差,并通过仿真实验证明了该方法的有效性;针对批量生产时的工作效率问题,通过对两台配料车工作时序的认真分析,建立了系统的数学模型,并利用遗传算法进行寻优,精心设计了遗传算子,求解出了最大工作效率所需的两台配料车的最佳行走路径,解决了配料车行走路径的优化问题。
饲料厂配料自动控制系统

图2配料仓配料示意 图
2 系统 的硬 件设 计
在进行具体电路设计之前 ,得根据系统及实际情况 的要求 ,进行各 个硬件器 件的选型 ,具体 包括 :传感器 、电动机 、接触 器 、电磁 阀和 Dk O I 卡等的选型 , D 使之符合生产 的要求 。 21 电源模块设计 . 本 系统 电路分为多个模块 ,而不同的模块对 电源的 电压 、电源质量 等要求都不一样 。电源对于每个 电路单元来说都 十分重要 ,尤其在系统 设计精度比较高时 ,整机的指标和 电源的质量密切相关 ,因此设计性能 优越并适合系统的电源电路是很有必要的。 对于数字电源和模拟电源 , 控制器采用从交流20 经变压为较低 电 2 V 压后 经过整 流桥为直流 ,然后经三端正 向稳压电源7 1和7 2后变成直 82 84 流l 和2 电源 。模拟 电源和数字电源分别用不 同变压绕组 , 2 V 4 V 两路 电 源互不 干扰 。由于模拟电源对 电压纹波等指标要求较为严格 , 在设计模 块地 时需加入更为严格的滤波措施 ,模拟地需通过 电感和担电容进一步
图1 系统整体结构框图
12 系统 的 工 艺 流 程 .
主要 工艺设备 :①螺旋给料机一 用于输送和分配原料 ; 电子配料 ② 秤一用 于饲料称 重 ;③电动 闸门一 用于控制进 料 ;④料位器一 用于检 测控制筒仓里原料 的料位 ;⑤混合机一 用于把各种不 同品质的饲料进行
混合。 系统工艺流程 简介 :
2 . 负载传感器的联接 .1 2 由于 电子秤采用四个传感器来进行物料 的称重 ,这就涉及 到传感器 是串联还是并联 ,现对两种联接方式介绍如下 。 1 串联组合称重方式 :每个传感器使用独立电源单独供 电,而4 ) 个 传感器 的输出端 串联连接。 对于型号规格相 同的多个传感器来说 如果 激励电源电压 u 相同 ,而 且输出电压敏度s 也~致相等 ,那么这样 ,就可以保证传 感器串联组合 后总输 出信号与秤体承载总重量w成正 比。串联组合后 ,总的输 出信号 为各传感器输 出信号之和∑u ,总的输 出阻抗为各感器输 出阻抗之和 。 2 并联组合称重方式 :各个传感器输入 端并联 , 用一个公共电 ) 使 源供 电,输出端也 以并联 的方式工作 。 多传感器输出端并联组合后 ,多个传感器并联工作 和一个传感器_ T 作时的输 出电压 是相等 的;总的输出信号为各传感 器输 出信号之 和的 I ;但并联后的输出电阻却减小 为一个传感器的1 。 / n , n 多传感器 串、并联联接方式如图4 。
自动配料系统实验报告

一、实验目的1. 了解自动配料系统的工作原理和组成。
2. 掌握自动配料系统的操作方法。
3. 通过实验验证自动配料系统的配料精度和效率。
二、实验原理自动配料系统是一种利用计算机技术、传感器技术、执行器技术等实现自动化配料过程的设备。
其工作原理如下:1. 通过传感器采集原料的重量信息。
2. 将采集到的重量信息传输至计算机控制系统。
3. 计算机控制系统根据预设的配料配方,计算出所需原料的重量。
4. 控制系统将计算结果发送至执行器,执行器驱动配料设备进行配料。
5. 通过传感器实时监测配料过程,确保配料精度。
三、实验设备与材料1. 自动配料系统一台2. 配料原料若干3. 计算机一台4. 传感器一套5. 执行器一套6. 配料设备一套四、实验步骤1. 熟悉自动配料系统的组成及各部分功能。
2. 将自动配料系统连接至计算机,并打开控制系统软件。
3. 设置配料配方,包括原料名称、配比、重量等信息。
4. 启动配料系统,观察传感器采集原料重量信息的过程。
5. 计算机控制系统根据配料配方计算所需原料的重量,并驱动执行器进行配料。
6. 观察配料过程,记录配料结果。
7. 对配料结果进行检验,分析配料精度。
五、实验结果与分析1. 实验结果:通过实验,自动配料系统能够根据预设的配料配方,实现自动化配料过程。
配料精度较高,满足实际生产需求。
2. 分析:(1)自动配料系统具有以下优点:a. 提高配料效率,降低人工成本。
b. 提高配料精度,保证产品质量。
c. 实现自动化生产,降低劳动强度。
(2)实验过程中,传感器能够实时采集原料重量信息,并传输至计算机控制系统。
控制系统根据配料配方计算出所需原料的重量,并驱动执行器进行配料。
实验结果表明,自动配料系统能够实现自动化配料过程,配料精度较高。
(3)实验过程中,配料设备运行稳定,未出现故障。
控制系统软件操作简单,易于上手。
六、实验结论1. 自动配料系统能够实现自动化配料过程,提高配料效率,降低人工成本。
自动上料配料系统方案

物料输送自动上料及配料系统方案一、项目概述锂电池负极材料生产线的前端DCS自动上料及配料系统。
该系统用于以石油炼解后的附产品石焦油为主要原料,通过物理及化学反应生产人工石墨生产线的自动上料、输送,自动配料,自动投放的系统控制,实现系统在线实时监测,信息、故障提醒、生成生产记录、统计报表等。
为业主提供准确可靠的数据报表、产出量报表等。
历史气候情况:该地区属于中亚温湿气候,年平均气温为17.3°C。
其中,一月份最冷,平均气温4.7C,历史上极端最低气温为零下15.1C,七月份最热,平均气温29C,极端最高温曾在8月初出现达40.4C。
全年平均降雨量为1612毫米,最多年份达2264毫米,最少年份只有1237毫米,降雨量集中在4—6月份,占全年的54%,7—9月雨量减少,不到全年的28%。
年相对湿度平均为79%,无霜期年平均为260天左右,年日照时数达1803小时。
石焦油参数:颗粒度(D50)8~10um,常规散装堆积密度为:0.3~0.45,最低为:0.22,挤压后最大密度为:1.1含水率:小于0.2%,物料安息角:,硬度:1-2.工艺流程要求连贯、可靠、严禁出现跑漏冒等恶性事故的发生,确保系统全年正常生产。
生产线按年度需定期检查,提起排除故障隐患。
1、用户需求分析(1)、产品规模生产要求系统具有更大的产能、更高的稳定性;(2)、降低人工上料劳动强度、改善员工工作环境、提高计量精度;(3)、粉体及液体物料均应自动上料、自动计量;(4)、每次生产的不同配方(原料配比)均可在电脑上进行操作;(5)、生产过程实现自动化控制及远程监控,同时可根据操作级别设置就地操作和急停。
(6)、对储料罐设置上限和下限报警,超限停机。
2、项目设计、制造、安装、检验标准DCS自动上料及配料系统在设计、制造和验收过程中应符合国家相关技术规范和标准,并以最新版为准。
包括但不限于下列标准:GB/T9969—2008工业产品使用说明书总则GB/T14436—1993工业产品保证文件GB/T6587—1986电子测量仪器GB/T7724—2008称重显示控制器技术条件JJG555—1996非自动秤通用检定规程QB1563—2003衡器产品型号编制方法GB/T7551—2008称重传感器GB/T14249.1—93 JJG649-90电子衡器安全要求数字称重显示器GB/T14249.2-93电子衡器通用技术要求GB/T5185-1985气焊、手工电弧焊及气体保护焊,焊缝坡口的基本形式与尺寸GB1184形状和位置公差、未注公差的规定GB1901公差与配合尺寸至500mm孔、轴工差带与配合GB/T1804一般公差线性尺寸的未注公差GB1764漆膜厚度测定法JB/TQ4000.3焊接通用技术条件IEC/GB电动机技术标准GB324-88钢焊缝符号表示法GB8923涂装钢材表面锈蚀等级和除锈等级GB9286色漆和清漆漆膜的划格试验JB8产品标牌JB/ZQ4000.3焊接通用技术要求B/ZQ4286-86包装通用技术条件GB4208外壳防护等级分类TJ231(四)GBJ17-88机械设备安装工程施工及验收规范钢结构设计规范GB191-2000包装储运图示标志GB3797-89电控设备第二部分装有电子器件的电控设备GB4064-83电气设备安全设计导则GB14285-93继电保护和安全自动装置技术规程GB/T1459898-91电气装置安装工程电气设备交接试验标准GB1497-85低压电器基本标准二、本方案自动上料及配料系统组成生产线配料主要完从与混料机下部料仓星型给料机下部开始:通过1号物料输送机f2号物料输送机f1~12号下料器—1〜12计量仓f1~12号仓下料排料阀f1~12号水平输送机f1~12号釜口气动球阀止。
饲料厂自动配料系统的设计

配 料 , 产 效 率 低 。2 多 采 用 传 统 控 制 算 法 更 本 无 法 满 足 高 生 )
精 度 的配 料 要 求 。3 大 部 分 配 料 现 场 工 作 环 境 恶 劣 , 度 大 , ) 强
d cd t e e e a ln f d sg o xu e o t l y tm , a i n n u t a c nr l o ue a d i ge c i e i e h g n r l p a o e i n f mit r c n r s s o e t t s h a i d s il o to c mp tr n s l- h p r n
第 2 0卷 第 l 2期
Vo.0 1 2
No 1 .2
电 子 设 计 工 程
Elc r n c De in E gn e i g e t i sg n i e r o n
21 0 2年 6月
J n 2 1 u.02
饲料 厂 自动 配料 系统 的设计
刘 艳 荣
( 疆轻工职业技 术学院 新 疆 鸟鲁木 齐 802 ) 新 3 0 1
o o to fc nrlo I ,a ts s ms d n mial e uae a d o t lp rmee f c nrlo o t f PD o n y t y a c l rg lt n c nr aa tr KP,i n d, a d f al a e y o T a d T n n l hs i y
摘 要 : 对 原 饲 料 厂 配 料 精 度 低 、 率低 的 问题 进 行 改 造 , 用 两级 分 布 式 微 机 配 料 控 制 系统 , 对 配 料 系 统 的 软 、 针 效 采 病
基于PLC控制的自动配料系统的研究与应用

基于PLC控制的自动配料系统的研究与应用1. 绪论a. 研究背景和意义b. 国内外研究现状和发展动态c. 研究目的和意义2. PLC控制系统的原理和结构a. PLC定义和功能b. PLC控制系统的结构和作用c. PLC控制系统的应用领域3. 自动配料系统的设计和实现a. 自动配料系统的概念和优势b. 自动配料系统的设计要点和目标c. 自动配料系统的实现流程和方法4. PLC控制自动配料系统的实验分析a. 实验设置和参数调整b. 实验结果分析和数据统计c. 实验总结和结论5. 自动配料系统的应用和展望a. 自动配料系统的市场前景和发展趋势b. 自动配料系统的应用领域和发展方向c. 自动配料系统的未来发展趋势和展望1. 绪论近年来,随着工业自动化程度的不断提高,自动化设备在各个行业的生产过程中的应用越来越广泛。
其中,PLC控制技术已成为工业自动化的核心技术之一,具有很高的可靠性、高效率、灵活性和易维护等优点。
在自动化生产中,自动配料系统是广泛应用的一种PLC控制系统,它主要是用于对不同物料进行配比和调整,并通过PLC程序控制实现自动化运作,从而提高生产效率、保障产品质量、降低生产成本,具有很高的技术和经济价值。
本文旨在研究PLC控制的自动配料系统的原理、性能和应用,分析探讨其在工业自动化中的优势和应用。
首先,本章将介绍研究背景和意义,包括自动化技术应用的趋势和需要,以及PLC控制技术在自动化生产中的应用优势。
其次,本章将综述国内外研究现状和发展动态,展示PLC控制的自动配料系统的研究和应用现状和未来发展方向。
最后,本章将概述本文的研究内容和意义,阐明本研究的目的和意义,为后续章节的内容铺垫。
1.1 研究背景和意义随着科技的发展和工业生产的逐步改善,自动化设备在工业生产过程中得到了广泛应用。
自动化生产的核心技术是PLC控制技术,它是一种基于数字计算机技术的控制系统,具有很高的可靠性、灵活性和稳定性,能够实现自动化生产环节的监控和控制。
自动配料系统简介及原理

自动配料系统简介及原理前言在制药、化工、食品等诸多工业领域,配料是常见的一项工作。
随着科技的发展,自动化成为了现代化生产的必备条件,自动化配料也成为了各个行业的发展趋势。
自动配料系统是一种专门用于自动化配料的设备,本文将介绍自动配料系统的基本概念、原理和应用。
自动配料系统简介自动配料系统是一种用于实现物料测量、混合、输送、卸料等全自动化的设备。
自动配料系统采用计算机和自动化控制技术,将多种不同的物料按照配方比例自动混合,然后通过输送系统将混合好的物料送到下一个工序。
自动配料系统的主要由以下几个组成部分组成:1.控制系统:控制整个自动配料系统的运行,并通过感应器等装置检测物料流动情况,实现流量控制、防止粉尘污染等功能。
2.称量系统:根据配方比例自动计量并混合相应的多种物料。
3.输送装置:输送混合好的物料到指定的储存器或下一个工序的输送装置。
4.卸料装置:控制混合好的物料在指定的地点进行卸料。
自动配料系统的应用范围非常广泛,目前已经在制药、化工、食品等领域得到了广泛的应用,并成为了自动化生产的关键环节。
自动配料系统的原理自动配料系统的原理基于两个重要的技术:计算机控制技术和传感技术。
计算机控制技术自动配料系统采用计算机控制技术,利用计算机通过程序自动化地完成配料系统的各项操作,例如控制阀门、流量传感器等设备的开关,以及根据物料比例和数量进行精确的计量和混合。
计算机控制技术不仅提高了生产效率,也比人工控制更加精确和可靠。
传感技术自动配料系统还采用了传感技术,用于监测物料的流动情况,包括流速、压力和温度等指标。
传感器能够实时监测物料的流动状态,避免了因物料故障或失控而导致的生产事故和质量问题。
自动配料系统中常见的传感器有:1.重量传感器:用于物料的重量计量。
2.压力传感器:用于检测气体、液体和蒸汽的压力。
3.温度传感器:用于检测物料的温度。
4.流量传感器:用于检测物料的流量和速度。
以上传感器用于控制自动配料系统中各种设备的操作,保证物料的精准计量和混合。
2-饲料厂中央控制室作业指导书

饲料厂中央控制室作业指导书1、目的规范控制员的正确操作,确保生产的正常运行。
2、范围饲料厂中央控制室。
3、职责3.1 组长3.1.1 负责控制一条生产线。
3.1.2 负责控制室的全面工作。
3.1.3 负责做好与各岗位人员的沟通、协调工作。
3.1.4 负责做好配方的保密工作。
3.2.控制员3.2.1 负责控制一条生产线。
3.2.2 负责电脑室的卫生,保持电脑设备的清洁、无灰尘。
3.2.3 协助组长做好相关工作。
4、工作程序4.1.生产前的准备工作4.1.1先合上电源总开关,然后将各系统(配料设备控制系统、强电控制柜和信号联络系统)逐一开启到工作状态。
4.1.2 查看总电压表、总电流表、液体添加控制仪、称重数显表等监控仪表工作状况是否正常。
4.1.3 查看生产工艺流程模拟屏显示各设备运转情况是否正常。
4.1.4按生产计划,把配方输入电脑,且核对配方。
4.2. 配料生产4.2.1 手动控制配料生产:是指在不使用计算机控制称重配料生产过程时,采用手动操纵控制按纽的方法进行配料生产。
4.2.1.1 根据配方配比和设备生产能力计算物料称重量。
4.2.1.2 根据生产量和配料仓内余料确定上料量和上料顺序。
4.2.1.3 通知各岗位现场作好开机准备,待各现场应答后,按下列顺序启动设备。
a) 打开所需上料原料的相应配料仓气动闸门,且同时关闭其他配料仓的气动闸门。
b) 启动配料仓顶分配螺旋。
c) 启动斗式提升机。
d) 启动其他与上料有关的设备(如:吸尘风机)。
e) 选择成品仓或待制粒仓仓位,并排除仓内的残余料及粉尘。
f) 启动入成品仓或待制粒仓设备。
g) 启动成品提升机、成品输送绞龙、混合机。
4.2.1.4 检查配料电子秤零点是否归零,然后按顺序按配比启动给料器按纽进行配料,注意控制配料误差尽可能小。
4.2.1.5 满称量后打开秤斗门向混合机放料,且同时给出添加剂信号灯通知投放预混料等添加剂,秤归零后关闭秤斗门。
待信号灯输入时,开始计算混合时间。
基于PLC的物料自动控制系统

基于PLC的物料自动控制系统一.引言连续配料输送自动控制系统在水泥、煤炭、冶金、化工、饲料、食品等行业有很广泛的应用。
具有功能全面,灵活性强,性价比高等特点,受到连续配料系统集成商和用户的欢迎。
该系统集现代物流技术、仓储技术、自动化技术于一体,是CIMS中的重要环节,在国外已经得到较广泛的应用,该技术也正在逐渐地应用于我国许多行业中。
加盟WTO后,我国商品分销、配送服务市场将逐步扩大开放的领域和范围。
而物流是企业发展的关键问题,物流会影响企业总体的生存和发展。
在2000年物流成本占国内国民经济生产总值(GDP)的16.7%,而美国仅为10%以下。
尤其是企业的物流设备水平与发达国家之间存在着巨大的差距,主要表现为,运输效率低,物流过程浪费惊人。
我们知道,差距就是潜力和发展空间,因此,提高物流设备化水平,已成为当务之急。
自动配料车是物流体系中运输分配的重要组成部分,它是能自动地存储和取出物料的系统。
二. 物料自动控制系统工艺生产控制物流自动控制系统主要是控制输送系统完成其物料的输送任务。
在物料的入口处和出口处设有升降机和输送线。
这样在库房、生产车间和包装车间范围内形成了一个既可顺畅到达各个生产位置同时又是封闭的循环输送线系统。
所有生产过程中使用的有关物料和成品等,最后都须装在贴有条形码的货箱里输送装车。
在生产管理系统发出的生产指令的作用下,物料的从指定的入口处进入输送系统。
物流自动控制系统如图1所示。
总体控制要求:如图所示,系统由料斗、传送带、检测系统组成。
配料装置能自动识别货车到位情况及对货车进行自动配料,当车装满时,配料系统自动停止配料。
料斗物料不足时停止配料并自动进料。
其工艺流程控制要求如下:(1)初始状态系统启动后,红灯L2灭,绿灯L1亮,表明允许汽车开进装料。
料斗出料口D2关闭,若料位传感器S1置为OFF(料斗中的物料不满),进料阀开启进料(D4亮)。
当S1置为ON(料斗中的物料已满),则停止进料(D4灭)。
全自动化的控制系统在搅拌站自动配料解决方案(共五则)
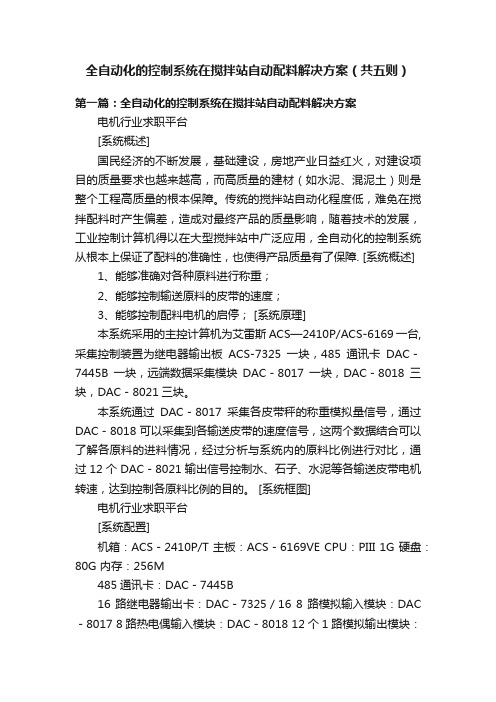
全自动化的控制系统在搅拌站自动配料解决方案(共五则)第一篇:全自动化的控制系统在搅拌站自动配料解决方案电机行业求职平台[系统概述]国民经济的不断发展,基础建设,房地产业日益红火,对建设项目的质量要求也越来越高,而高质量的建材(如水泥、混泥土)则是整个工程高质量的根本保障。
传统的搅拌站自动化程度低,难免在搅拌配料时产生偏差,造成对最终产品的质量影响,随着技术的发展,工业控制计算机得以在大型搅拌站中广泛应用,全自动化的控制系统从根本上保证了配料的准确性,也使得产品质量有了保障. [系统概述]1、能够准确对各种原料进行称重;2、能够控制输送原料的皮带的速度;3、能够控制配料电机的启停; [系统原理]本系统采用的主控计算机为艾雷斯ACS—2410P/ACS-6169一台,采集控制装置为继电器输出板ACS-7325一块,485通讯卡DAC-7445B一块,远端数据采集模块DAC-8017一块,DAC-8018三块,DAC-8021三块。
本系统通过DAC-8017采集各皮带秤的称重模拟量信号,通过DAC-8018可以采集到各输送皮带的速度信号,这两个数据结合可以了解各原料的进料情况,经过分析与系统内的原料比例进行对比,通过12个DAC-8021输出信号控制水、石子、水泥等各输送皮带电机转速,达到控制各原料比例的目的。
[系统框图]电机行业求职平台[系统配置]机箱:ACS-2410P/T 主板:ACS-6169VE CPU:PIII 1G 硬盘:80G 内存:256M485通讯卡:DAC-7445B16路继电器输出卡:DAC-7325/16 8路模拟输入模块:DAC -8017 8路热电偶输入模块:DAC-8018 12个1路模拟输出模块:DAC-8021 [推荐配置]:主板:ACS-6172VE,ACS-6188VG,ACS-6189[系统评价]该套系统长期在建筑施工中进行配料使用,工作正常可靠,确保工程的正常进度.电机行业求职平台(此文转自一览电机英才网)第二篇:混凝土搅拌站自动控制系统混凝土搅拌站自动控制系统1.项目简介混凝土搅拌站是基础设施建设中不可或缺的生产设备,同时又是一个由多环节组成的复杂控制系统。
现代饲料厂微机管理系统的开发应用
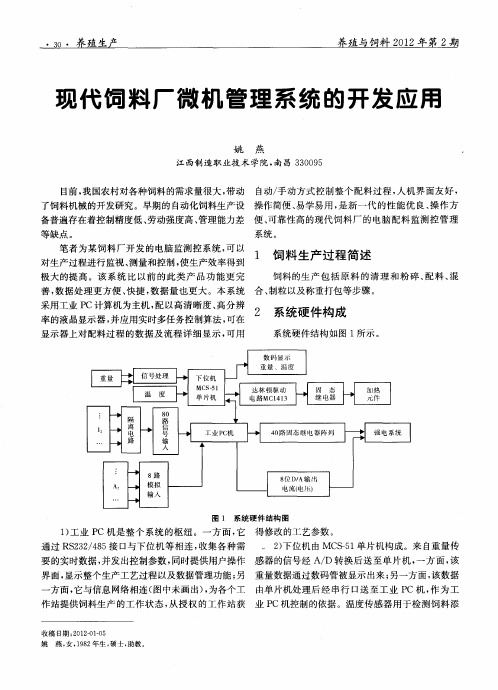
图 2 系统监控及管理软件
2 粉料 进仓 监控 程序 : 动粉 料进 仓 电路 系统 , 统通讯 , ) 启 可以对系统的配方和原料进行编辑 、 修改及 粉料 进仓 监 控 电路 同时启 动 。动态 模 拟显示 该 部分 替 换 。 工艺 流程 , 态 显示 总 电 流量 。若有 电机 跳 闸将 有 动 报警 窗 口跳 出 , 同时有 声光 报警 。 B秤 , 提示操 作 各项 功能 , 按 加料 显示 。 7 配方 优化模 块 : 物 营养 标 准 库 的全 屏 幕 编 ) 动 辑 、 改 、 盘 ; 料 原 料 成 分 库 的全 屏 幕 编 辑 、 修 存 饲 修 准 的对 照 ; 过优 化进 行配 餐 , 通 最多 1 物料 , 项 2种 该
5工业 P ) C机输 出的 4 路开关 量信号 , 0 用于控 的软 件 , 运行 于工 业 P C机 中 。该 软件 设 计 是 本 系
3 系统 软 件 构 成
及 管理 软 件 。
3 1 控 制软 件 .
该系统软件由 2 大部分组成 , 即控制软件 、 监控 值 , 此外还要 对键盘进行 实时响应等 。如图 2所示 。
范 围 内。
理实时数据 , 然后根据工艺要求 , 采用相应的控制算
3 I,z ) I……是 8 0路 来 自工作 现 场 的开 关 量 信 法进 行计 算 , 最后 将结 果输 出到 对应接 口, 成对 温 完 号, 这些信号送人工业 P C机作为工业 P C机显示 、 度 、 重量等的控制; 通信模块 : 负责将采集 的实时数 控制 的依 据 。
界面 , 显示 整个 生产 工艺过 程 以及数 据管 理功 能 ; 另
一
. 2下位机由 MC -1 ) S5 单片机构成。来 自重量传 感器的信号经 A D转换后送至单片机, / 一方面 , 该
基于PLC的自动配料控制系统的研究

基于PLC的自动配料控制系统的研究随着工业自动化的快速发展,PLC(可编程逻辑控制器)在自动化控制领域的应用越来越广泛。
其中,基于PLC的自动配料控制系统成为了不可忽视的研究方向。
本文将从系统的基本原理、系统的优势以及未来发展方向等方面对基于PLC的自动配料控制系统进行研究。
基于PLC的自动配料控制系统的基本原理是通过PLC对物料的输送、称量、混合等过程进行控制。
系统一般包括物料输送装置、称量装置、混合装置以及PLC控制系统等组成部分。
物料输送装置负责将需要配料的物料输送到称量装置,称量装置通过传感器对物料进行精确称量,然后将称量的物料送到混合装置进行混合。
PLC控制系统根据预设的配方,通过对各个装置的控制,实现对配料过程的自动控制。
基于PLC的自动配料控制系统相较于传统的手动控制方式具有多方面的优势。
首先,系统大大提高了生产效率。
自动化控制系统可以实现物料的连续输送、精确称量和高效混合,大大减少了人力投入和生产时间。
其次,系统提高了产品质量的稳定性。
自动化控制可以减少人为因素对配料过程的影响,保证了每次配料的准确性和一致性。
此外,系统具有可编程的特点,可以实现不同配料要求下的灵活调整,提高了生产的适应性。
最后,系统的可靠性和安全性也得到了增强。
PLC控制系统具有自我诊断和故障保护功能,当发生异常情况时能及时进行报警和停机保护,保证了设备和人员的安全。
基于PLC的自动配料控制系统还有许多待发展的方向。
首先,可以进一步提高系统的可扩展性和智能化水平。
通过加入更多的传感器和设备,实现对配料过程更全面的监测和控制,使系统变得更智能化。
其次,可以进一步优化系统的人机界面。
提供更直观、友好的操作界面,使系统的使用更加方便和易于操作。
同时,可以将系统与远程监控和管理系统进行整合,实现对生产过程的远程监控和智能管理。
另外,基于PLC的自动配料控制系统还可以与其他工业自动化技术相结合,如无人机技术、物联网等,实现生产线的智能化和自动化。
粉料的自动配料设备与运输输送料仓

粉料的自动配料设备与运输输送料仓随着工业化生产的不断发展,粉料的自动配料设备与运输送料仓已经成为现代工厂生产线上不可或缺的重要设备。
它们的出现,使得生产过程更加高效、精确和安全。
本文将重点介绍粉料的自动配料设备与运输送料仓的相关信息。
一、粉料的自动配料设备粉料的自动配料设备是指能够自动完成粉料的称量、混合、包装等工作的设备。
它通常包括上料系统、称量系统、搅拌系统、包装系统等组成部分。
1. 上料系统上料系统主要负责将原料输送至配料设备的工作台。
这一过程通常需要通过输送带、螺旋输送机等设备来完成。
上料系统的设计需要考虑原料的种类、粒度、流动性等因素,以确保原料能够迅速、准确地输送到指定位置。
2. 称量系统称量系统是粉料自动配料设备中最关键的部分。
它通常采用称重传感器,能够准确地测量原料的重量,以保证配料的精确度。
称量系统的精准度对于生产工艺的稳定性和产品质量的一致性有着重要的影响。
3. 搅拌系统搅拌系统用于将不同原料混合均匀,以满足生产工艺中对原料混合比例的要求。
搅拌系统的设计需要考虑搅拌速度、搅拌时间、搅拌方式等因素,以确保混合后的产品能够达到预期的质量要求。
4. 包装系统包装系统通常将混合后的产品自动填充到包装材料中,并进行封口、打印生产日期、贴标签等工作。
包装系统的设计需要考虑包装材料的尺寸、形状、热封方式、包装速度等因素,以确保产品的包装能够满足市场需求。
粉料的自动配料设备能够帮助工厂实现原料的自动化处理,提高生产效率和产品质量,减少人力成本和生产过程中的人为因素。
二、粉料的运输送料仓除了自动配料设备外,粉料的运输送料仓也是现代工厂生产中必不可少的设备。
它可以帮助工厂实现原料的集中存储、自动运输和自动送料,大大提高生产效率和安全性。
1. 集中存储粉料的运输送料仓通常用于存放大批量的原料,以确保生产线的原料供应充足。
这些仓库通常采用自动堆垛机、输送带、搬运机器人等设备,能够实现原料的自动入库和出库,提高原料的存储密度和利用率。
PLC在饲料加工生产过程控制中的应用研究

碎、 配料 、 混合 、 制粒 、 品打 包入 库及 除尘与 消 防等 成
系统 , 一个 生产 环节 就是一 个独 立 的生产 工段 l 。 每 2 ] 淮 安某农 牧水 产有 限公 司主要 生 产 水 产 饲料 , 料 饵
要 细小 , 此 有时需 二次 粉碎 。 因 2 基 于 P C 的 总 体 控 制 方 案 设 计 L
缓 冲仓 , 落人成 品刮 板式 输送 机 , 送至 斗 式提 升 机人
口升运 至混合料仓贮存 , 至下一工 序 。
3 2 配料 混 合 系统 硬 件 设 计 .
上位机选 择带有标 准 的 R 2 2 S 3 C通信 口、 印机 打
接 口的品牌 机 , 系 统控 制精 度要 求 高 , 本 根据 输入 输 出信号 数 量 , 位 机选 用 一个 三 菱 F z~8 MR型 下 X 0 P C和两个 F 一 6 X拓展单元 , 用 S 0 L X 1E 选 C一 9编程
区
子 系 统 继 电 器
匮
l S 3C R 2 2
原 料 接 收 与清 理
粉 碎 子 系 统 继 电 器
粉碎子 系统 传感信 号
P C的通讯 实 现 , 使 生 产过 程 整 体 优化 , 可 确保 正常
生产 和管理 水平 的提 高口 。 ] 淮 安某 农牧 水产 有 限公 司是 以生 产各 种预 混合 饲料、 浓缩 饲料 、 配合 饲 料 为 主 的 民 营科 技 企 业 , 现 有 饲料 生产 车 间两个 , 新建 成 的生 产 线采 用 了微 最 机 控制 技术 , 现代 化水 平 比较高 ; 而早 期建设 的生产 线 控制 系统 仍然 是接 触器 、 电器 控制 方式 , 管理 继 其 水 平 和生产 效率均 远低 于另 一条 生产 线 。为适应 生 产 需求 , 旧 的生产线 进行 了技术 改造 。 对
饲料混合机的自动化控制系统研究与应用
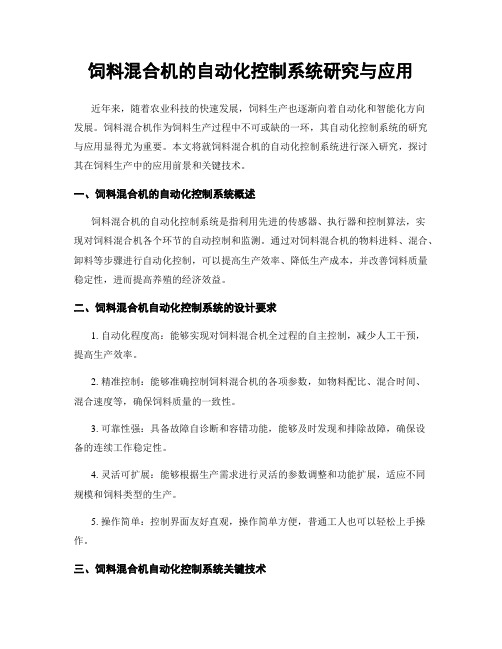
饲料混合机的自动化控制系统研究与应用近年来,随着农业科技的快速发展,饲料生产也逐渐向着自动化和智能化方向发展。
饲料混合机作为饲料生产过程中不可或缺的一环,其自动化控制系统的研究与应用显得尤为重要。
本文将就饲料混合机的自动化控制系统进行深入研究,探讨其在饲料生产中的应用前景和关键技术。
一、饲料混合机的自动化控制系统概述饲料混合机的自动化控制系统是指利用先进的传感器、执行器和控制算法,实现对饲料混合机各个环节的自动控制和监测。
通过对饲料混合机的物料进料、混合、卸料等步骤进行自动化控制,可以提高生产效率、降低生产成本,并改善饲料质量稳定性,进而提高养殖的经济效益。
二、饲料混合机自动化控制系统的设计要求1. 自动化程度高:能够实现对饲料混合机全过程的自主控制,减少人工干预,提高生产效率。
2. 精准控制:能够准确控制饲料混合机的各项参数,如物料配比、混合时间、混合速度等,确保饲料质量的一致性。
3. 可靠性强:具备故障自诊断和容错功能,能够及时发现和排除故障,确保设备的连续工作稳定性。
4. 灵活可扩展:能够根据生产需求进行灵活的参数调整和功能扩展,适应不同规模和饲料类型的生产。
5. 操作简单:控制界面友好直观,操作简单方便,普通工人也可以轻松上手操作。
三、饲料混合机自动化控制系统关键技术1. 传感器技术:通过安装适当的传感器,实时监测饲料混合机各项参数,如物料流量、温度、湿度等,提供准确的数据支持。
2. 控制算法:利用先进的控制算法,对饲料混合机进行精准控制,实现自动化生产过程中的配比、搅拌、卸料等操作。
3. 数据通信技术:通过网络通信技术,实现饲料混合机与上位机之间的数据传输和控制指令的交互,实现遥控和远程监控。
4. 故障诊断技术:通过故障诊断技术,对饲料混合机在生产过程中出现的故障进行诊断和处理,提高设备的可靠性和稳定性。
5. 人机界面技术:通过友好直观的人机界面,实现对饲料混合机的操作和监控,提高操作的简易性和工作效率。
调速定量给料拜在生料配料中的应用
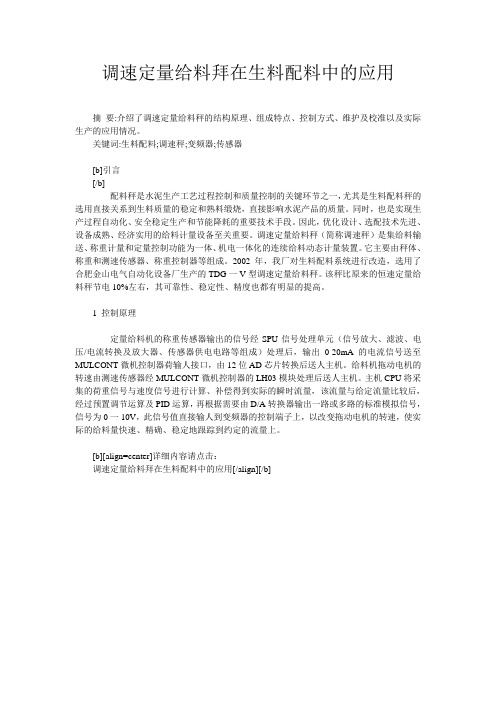
调速定量给料拜在生料配料中的应用摘要:介绍了调速定量给料秤的结构原理、组成特点、控制方式、维护及校准以及实际生产的应用情况。
关键词:生料配料;调速秤;变频器;传感器[b]引言[/b]配料秤是水泥生产工艺过程控制和质量控制的关键环节之一,尤其是生料配料秤的选用直接关系到生料质量的稳定和熟料缎烧,直接影响水泥产品的质量。
同时,也是实现生产过程自动化、安全稳定生产和节能降耗的重要技术手段。
因此,优化设计、选配技术先进、设备成熟、经济实用的给料计量设备至关重要。
调速定量给料秤(简称调速秤)是集给料输送、称重计量和定量控制功能为一体、机电一体化的连续给料动态计量装置。
它主要由秤体、称重和测速传感器、称重控制器等组成。
2002 年,我厂对生料配料系统进行改造,选用了合肥金山电气自动化设备厂生产的TDG一V型调速定量给料秤。
该秤比原来的恒速定量给料秤节电10%左右,其可靠性、稳定性、精度也都有明显的提高。
1 控制原理定量给料机的称重传感器输出的信号经SPU信号处理单元(信号放大、滤波、电压/电流转换及放大器、传感器供电电路等组成)处理后,输出0-20mA的电流信号送至MULCONT微机控制器荷输人接口,由12位AD芯片转换后送人主机。
给料机拖动电机的转速由测速传感器经MULCONT微机控制器的LH03模块处理后送人主机。
主机CPU将采集的荷重信号与速度信号进行计算、补偿得到实际的瞬时流量,该流量与给定流量比较后,经过预置调节运算及PID运算,再根据需要由D/A转换器输出一路或多路的标准模拟信号,信号为0一10V,此信号值直接输人到变频器的控制端子上,以改变拖动电机的转速,使实际的给料量快速、精确、稳定地跟踪到约定的流量上。
[b][align=center]详细内容请点击:调速定量给料拜在生料配料中的应用[/align][/b]。
饲料厂的配料系统(二)

饲料厂的配料系统(二)褚慎强(上海方露生物技术有限公司,上海 201600)1 饲料厂配料系统控制参数的解读在饲料生产过程中,自动配料秤因效率高、稳定性好、不易出错等优点,被各饲料厂广泛采用。
在实际使用过程中,不同饲料厂在所用原料的性状、配料秤的外观尺寸、喂料器的口径等方面有所不同,为了确保配料的精度,需要调整自动配料秤的一些参数。
这些参数主要分成两部分,一部分保存在配料秤的数字模拟转换器(digital to analog converter,DAC)这样的硬件中,另一部分保存在控制系统的组态软件中。
1.1 硬件参数——DAC(以常见的AC-7100DP 为例) 1.1.1 PROFIBUSPROFIBUS 是过程现场总线(process field bus)的英文缩写,是一种国际化、开放式、不依赖于设备生产商的现场总线标准。
PROFIBUS 用于总线地址设置,在自动控制系统中,所有的配料秤都连在一条总线上被送入可编程逻辑控制器(programmable logic controller,PLC),所以需要在每台秤上设置一个地址,以标明是哪台配料秤,这便于PLC 实施控制。
1.1.2 零点追踪范围配料秤不可能在一个绝对稳定的环境中工作,因此需要给配料秤一个范围值,在范围值内的影响将被配料秤忽略不计。
例如设定零点追踪范围是两个分度值,配料秤分度值是5 g,那么10 g(2×5=10 g)的重量影响,配料秤显示为0。
这个参数不宜设置过大,有些饲料厂环境震动较大,为了能正常配料,会将这个值设得大一些,但这只掩盖了震动造成的影响,却不利于质量的把控。
1.1.3 动态检测范围动态检测范围和零点追踪范围相反,当给配料秤一个范围值时,虽然影响在范围值内,但配料秤会停止传送当前数据,直到这个影响消失。
例如设定动态检测范围是两个分度值,配料秤分度值是5 g,那么10 g 的重量影响,配料秤显示不稳定,并停止传送数据给配料系统。
(完整版)自动配料控制系统文献综述
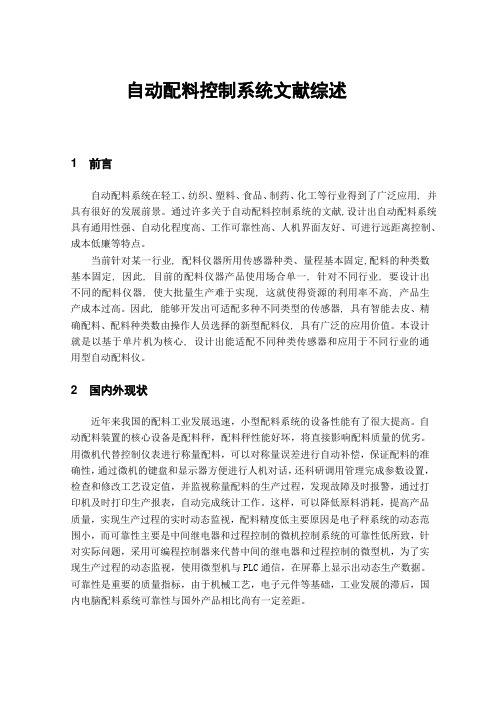
自动配料控制系统文献综述1 前言自动配料系统在轻工、纺织、塑料、食品、制药、化工等行业得到了广泛应用, 并具有很好的发展前景。
通过许多关于自动配料控制系统的文献,设计出自动配料系统具有通用性强、自动化程度高、工作可靠性高、人机界面友好、可进行远距离控制、成本低廉等特点。
当前针对某一行业, 配料仪器所用传感器种类、量程基本固定,配料的种类数基本固定, 因此, 目前的配料仪器产品使用场合单一, 针对不同行业, 要设计出不同的配料仪器, 使大批量生产难于实现, 这就使得资源的利用率不高, 产品生产成本过高。
因此, 能够开发出可适配多种不同类型的传感器, 具有智能去皮、精确配料、配料种类数由操作人员选择的新型配料仪, 具有广泛的应用价值。
本设计就是以基于单片机为核心, 设计出能适配不同种类传感器和应用于不同行业的通用型自动配料仪。
2 国内外现状近年来我国的配料工业发展迅速,小型配料系统的设备性能有了很大提高。
自动配料装置的核心设备是配料秤,配料秤性能好坏,将直接影响配料质量的优劣。
用微机代替控制仪表进行称量配料,可以对称量误差进行自动补偿,保证配料的准确性,通过微机的键盘和显示器方便进行人机对话,还科研调用管理完成参数设置,检查和修改工艺设定值,并监视称量配料的生产过程,发现故障及时报警,通过打印机及时打印生产报表,自动完成统计工作。
这样,可以降低原料消耗,提高产品质量,实现生产过程的实时动态监视,配料精度低主要原因是电子秤系统的动态范围小,而可靠性主要是中间继电器和过程控制的微机控制系统的可靠性低所致,针对实际问题,采用可编程控制器来代替中间的继电器和过程控制的微型机,为了实现生产过程的动态监视,使用微型机与PLC通信,在屏幕上显示出动态生产数据。
可靠性是重要的质量指标,由于机械工艺,电子元件等基础,工业发展的滞后,国内电脑配料系统可靠性与国外产品相比尚有一定差距。
主要面临的问题是:( 1)不同行业使用的传感器不同, 输出的电信号不同, 这就给信号的初期放大处理和程序设计带来困难。
- 1、下载文档前请自行甄别文档内容的完整性,平台不提供额外的编辑、内容补充、找答案等附加服务。
- 2、"仅部分预览"的文档,不可在线预览部分如存在完整性等问题,可反馈申请退款(可完整预览的文档不适用该条件!)。
- 3、如文档侵犯您的权益,请联系客服反馈,我们会尽快为您处理(人工客服工作时间:9:00-18:30)。
料控 制策 略 , 配 料 过程 分 成 高 速 配 料 、 速 配料 、 将 慢 脉 冲配料 3个 阶段 , 配料 控 制 曲线 如 图 2所 示 。多 级变 速配 料控 制 曲线 包含 卸料 器转 速 曲线和 配料秤 上 的物料 质 量 曲线 , 中 快 慢 切 换 点 P 、 切 点 其 预 P 、 慢速 切换 时 间 t、 料器 速度 、 和最 大配 快 卸 料脉 冲数 等参数 都 可 以通 过 上 位 机 设定 , 定界 面 设
配 料 的 精 度 和 速 度 , 而提 高 了产 品 质 量 和 生 产 效 率 。 从
关键词 : 自适 应 控 制 ; 多级 变速 连 续 配 料 ; 料 参 数 ; 配 配料 精 度
中 图 分 类 号 :8 6 9 ¥ 1 . 文献标志码 : A 文章 编 号 :0 3 6 0 ( 0 2 0 —0 4 —0 10 ~ 2 2 2 1 )7 0 9 3
图 3
卸 料 器 参 数 设 定
配 料 秤 参 数 设 置 界 面 如 图 4所 示 , 要 用 于 配 主 料 监视 参数 、 液体 添加 参数 、 配料 参数 和修 正参数 等
4部 分参 数 的设 置 。配料 监视 参 数部 分 主要 用 于 设 置 延 时监视 时 间 、 视 周 期 时 间和 稳 定 时 间等 参 数 监 的设置 , 中延 时监 视 时 间是 指 系 统 自动监 测 在 该 其 时间段 内卸 料器 卸料 质 量 是 否达 到 快/ 慢进 料 监 视 所 设 定 的最 小进 料 质量 , 果 未达 到 则 输 出报 警 提 如 示 缺料 。稳 定 时 问是 用 于延 时监 测 配 料 实 际质 量 , 提高 系统稳 定性 ; 液体 添 加 参 数部 分 用 于 设 置实 际 标定 的单 位脉 冲液 体 质 量 , 统会 根 据 采 集 到 的脉 系 冲数 量计 算 出添加 的液 体 质 量 ; 配料 参 数 设 置部 分 用于设 置 清空 监视 周期 、 监视 清空 质量 、 最大 清空 时
如图 3图 4 示 。 、 所
料 仓
各组 分料 仓 、 变频 螺旋 卸料器 与 控制 阀组 、 配料 秤 和 混合 机等 , 制器 作 为 主站 通 过 P oiu 控 rf s总线 与 上 b 位机 、 配料 秤 通讯 , 图 1 示 。 如 所
开始 配料 时卸 料 器转 速 为 高速 , 时 配料 秤 此 上物料 质量 增加 很 快 , 达快 慢 切换 点 质 量 P 到 时 , 卸料器 在 快慢切 换 时间 t 内完 成 快慢 速 度切 换 , 慢 配料 目标 时 间设 为 t( +t≤ £) 。到 达 预 切 断 点 质量 P 。时 , 卸料 器停 止 卸料 , 由于 “ 中落料 ” 空 的存 在, 在稳 定 时 问 t 。内 , 料 质 量 还 要 增加 。稳 定 时 物 间结束 , 配料 秤称 量结 果应 该有 3种情 况 : 是 正好 一 在 允许 误差 范 围 , 明本次 所设 的配 料参数 很好 , 表 保 存 当前 参数 ; 二是 偏差 过大 且超 过 目标 质量正 偏差 , 配 料 系统 已经 无法 调 整 本 次结 果 , 需要 调 整 配料 参
摘 要 : 对 目前 国 内饲 料 厂 自动 配料 系统 普 遍 存 在 的 配料 参数 设 定 、 节难 度 大 、 针 调 配料 精 度 差 等 问题 , 出采 用 提 自适 应 多级 变速 配料 控 制 方 法 , 实现 变 工 况 下 不 同 配 方 配料 参 数 的 自整 定 , 低 了从 业 人 员 的 操 作 难 度 , 高 了 降 提
Y ()在 设 定 误 差 范 围 内 为止 。 l
《
C铷 FD 搏E&E 工 EA 饲科 NL E
! I NLUST Y R
口
自适 应 多级 变 速 配料 控 制 系统 在 饲 料 厂 中 的应 用
顾 菊 芬 曹应 明 ,
( . 锡商 业 职 业 技 术 学 院 电子 工 程 学 院 , 苏 无 锡 1无 江 2 4 5 ; . 锡高 等 交 通 职业 技 术 学 校机 电工 程 系 , 苏 无 锡 11 3 2 无 江 24 0 ) 10 0
变频 螺旋卸 料 器 与控制 阀
P D 口 } r P 茎 o —』
上 位机 控 制器
图 1 配 料 系 统 组 成 示 意 图
系统 上位界 面 由 VB编 写 , 以通 过 上 位 机 下 可 载配方 、 定配 料 参 数 等 。配 料 控 制器 根 据 配 方 要 设 求 自动 选择 仓 , 并启 动 对 应 料仓 下 的变 频 螺 旋 卸 料 器 和控 制 阀 , 同时读 取 配 料 秤 物 料质 量 进 行 检 测 判 断 , 据 自适应 多级 变速 控 制 算 法 控制 卸 料 器 转 速 根
国
顾 芬 : 应 级 速 料 制 统 饲 厂 的 用0年 7 菊 等自 多变 配 控 系在 料 中应 /2■ 期 适 2 1
正偏 差 ( 正公差 ) 质 量 负偏差 ( 负公差 )
间、 秤清 空质量 和秤 空延 时关 闭时 间等参 数 , 空监 清 视 周期 是指在 设定 时 间 内如果 秤卸 料质 量小 于设定 的监视 清空质 量 则 输 出报 警 , 示 秤 卸 料故 障 。当 提 秤 显示 质量 小于设 定 的秤清 空质 量时 系统任 务秤 已 经清 空 , 在延 时设 定 时间之后 关 闭秤卸 料 阀 。
收 稿 日期 : 0 2 0 — 3 修 回 日期 : 0 2 0 8 2 1 42 ; 2 1 - 62 作 者 简 介 : 菊 芬 (9 0) 女 , 师 , 究 方 向为 机 电 控 制 技 术 。 顾 18 , 讲 研
数; 三是 偏差过 大且 低 于 目标 质 量 负偏 差 , 料 系统 配 进入 脉冲再配料 阶段 , 制绞 龙 点动 配料 , 至 配料 控 直 质量在 配料误差允许 范 围内结束 。
目前 , 内饲料 厂普 遍 引入 自动化 生产 线 , 是 国 但 配 料 系统通 常 需要 随现 场工况 变化 ( 配方 变化 等 ) 如 由人工 重新 设定 参 数 , 即使 是 专业 调试 工 程 师 也 很 难 快速 整定 出最 优 的 参 数 , 普通 操 作 人 员 来 说 要 对 求 更 高 , 度 更大 。这 样 不 仅效 率 低 、 操 作性 差 , 难 可 而 且配 料精 度 波动 很 大 , 重 影 响 产 品 质量 。针 对 严
( 直接表 示 系统 希 望输 出即各 组分 的 目标 质 量 ; ) Y () 。 是卸 料器输 出 , 即各 组分 的实 际质量 ; 者之 间 两 产生 的误差为 e ( 。规范输 入 ( m ) 参考 输入 ) 为 配 R() 料组分 实时质量 , 多级 变速配料控制 器根据 输入 和反 馈 的偏 差 , 按照设 定 的配 料参 数 ( 料 器转 速 和相 应 卸 时问) 控制卸料器转速 和相应时 间即 () 从而 控制 , , 卸料器输 出质 量 Y () 若 参数 设 置 合适 , Y () 。 , I 。 一 Y () 在设 定误差范 围 内。一 旦配方 变 化 、 £I 卸料 器转 速变化 , 配料参数 随之需要较大 调整 。此时 由于被控 对象 的初 始参 数 不确 定 ( 或事 先未 知 ) 现 场 操 作人 , 员通常 只能 给定 大概范 围的配 料参数 , 控制器 的初始 参数不能 调节很 好 , 因此被 控对 象 的输 出 Y () 。 与参 考模 型的输出 Y () 间产 生误 差 8 () 大 。当 自 £之 较 适应误差被 引入到 自适应调节 器 中 , 经过 自适 应控 制 规律运算 , 直接改 变 多级连 续 配料 控 制参 数 , 产生 新 的控制作 用 () 制 被控 对象 。从 而使 被控 对象 的 f控 输 出渐近 地 跟 随 参 考 模 型 的 输 出 , 到 l () 直 一
时I s E/
图 2 多 级 变 速 配 料 控 制 曲线
卸料器参数设 置界面如 图 3 所示 , 主要用 于预切 断、 公差和配料 参数 3 部分参 数 的设 置 。预切 断部分 用于设置 快慢切换点质 量 、 预切点质量 和预切 断最 大 校正质 量 , 注意 是 预切 断 最大 校 正质 量 值 (。 , 需 c) 此 参数是 设置调节范 围防止优化时 调节过 量 , 后文 修正 公式 中会用到 ; 公差设 置部分用 于设 置质 量 的正 负误 差 范围( 即死 区范围)分绝 对质量误 差 和相对质 量误 , 差 两 种 , 际运 用 时取 两 者 数值 较 小 的一 组 带入 运 实 算 。另外 , 部 分 还 用 于设 置 系 统 自动 复位 误 差 范 该 围, 也分绝对误 差 和相 对误 差两 种 , 当配 料 实 际质量 与 目标质量 的差 值超 出死 区部 分在 自动复位 误 差范 围 内时系 统 自动 接 收该质 量 , 成 配 料 ; 果配 料 实 完 如 际质量与 目标质 量 的差值 超 出死 区部 分不 在 自动 复 位误差 范围 内时 系统输 出报警 , 由操 作人员 确认后 完 成配料 , 待下一批次配料 时调整参数 最终使 实 际质量 达 到设定 的死 区范围内 ; 配料参数部 分用 于设定快 配 料 速度 、 慢配料速 度 、 脉冲时间等 。
3 切 断 点 的 自适 应 调 节 。
本 文采用 的 自适应 调节 系统 是 基于模 型 参 考 的 白适应系统 。模 型参 考 自适应控 制系 统 由参考 模型 、 卸料器 ( 被控对 象) 实时质量反馈 ( 、 配料秤 反馈 信息 ) 和 自适应控制 器构成 , 其系统结 构如 图 5所示 。其 中
图 4 配 料 秤参 数 设 定
开 始上 位 机设 定 的这些 参 数 可 以只 是 经验 值 , 不 一定 是最优 的 。下位 P C接收初 次 点 质量 和切 断 点 质量 , 以获 得最 优 的 目标精 度 和速度 。