齿轮标准中心距
齿轮齿形精度等级详解

齿轮精度等级1、齿轮精度主要是控制齿轮在运转时齿轮之间传递的精度,比如:传动的平稳性、瞬时速度的波动性、若有交变的反向运行,其齿侧隙是否达到最小,如果有冲击载荷,应该稍微提高精度,从而减少冲击载荷带给齿轮的破坏。
2、如果以上这些设计要求比较高,则齿轮精度也就要定得稍高一点,反之可以定得底一点3、但是,齿轮精度定得过高,会上升加工成本,需要综合平衡4、你上面的参数基本上属于比较常用的齿轮,其精度可以定为:7FL,或者7-6-6GM精度标注的解释:7FL:齿轮的三个公差组精度同为7级,齿厚的上偏差为F级,齿厚的下偏差为L级7-6-6GM:齿轮的第一组公差带精度为7级,齿轮的第二组公差带精度为6级,齿轮的第三组公差带精度为6级,齿厚的上偏差为G级,齿厚的下偏差为M级5、对于齿轮精度是没有什么计算公式的,因为不需要计算,是查手册得来的。
6、精度等级的确定是工程师综合分析的结果,传动要求精密、或者是高负载、交变负载……就将精度等级定高一点7、精度等级有5、6、7、8、9、10级,数值越小精度越高8、(齿厚)偏差等级也是设计者综合具体工况给出的等级,精密传动给高一点,一般机械给低一点,闭式传动给高一点,开式传动给低一点。
9、(齿厚)偏差等级有C、D、E、F、G、H、J、K、L、M、N、P、R、S 级,C级间隙最大,S级间隙最小。
10、不管是精度等级,还是偏差等级,定得越高,加工成本也越高,需要综合分析之后再具体的给出一个恰当的精度等级和偏差等级。
11、对于齿轮的常规检验项目,分为3组检验项目,分别如下:12、第一组检验项目主要是保证传递运动的准确性,其项目包括:切向综合公差Fi'、周节累积公差Fp、k个周节累积公差Fpk、径向综合公差Fi"、齿圈径向跳动公差Fr、公法线长度变动公差Fw13、第二组检验项目主要是保证传递运动的平稳性、噪声、振动,其项目包括:切向一齿综合公差fi'、基节极限偏差fpb、周节极限偏差fpt、径向一齿综合公差fi"14、第三组检验项目主要是保证载荷分布的均匀性,其项目包括:齿向公差Fβ、接触线公差Fb、轴向齿距极限偏差Fpx15、齿轮的齿坯公差的精度等级为:5、6、7、8、9、10级16、齿轮中间的孔公差、及其形位公差:IT5、IT6、IT7、IT8级17、齿轮轴的尺寸公差、及其形位公差:IT5、IT6、IT718、顶圆直径公差:IT7、IT8、IT919、基准面的径向跳动、基准面的端面跳动:根据直径的大小,按照5、6、7、8、9、10级查表20、需要说明一下:我给出的·第一组、第二组、第三组检验项目是比较全的,但是,在实际中,在实际的图纸上,我们列出的检验项目没有这么多,太多了不但给检验带来麻烦,还增加制造成本,所以,在图纸上只检验其中的几项即可,你可以参看一下专业的齿轮图纸,也可以在《机械设计手册》上看看例题,在此给你列出常规要检查的、在图纸上要列出来的项目:21、小齿轮的检验项目:21、根据你上面给出的参数,小齿轮的精度等级可以定为7FL,接下来级,就是按照精度等级差手册:22、周节积累公差Fp:0.06323、周节极限偏差fpt:0.01824、在图纸上标注的齿坯公差:内孔按照IT7级:在手册上按照孔径大小查《标准公差表》25、顶圆的径向跳动:按照外径尺寸大小查《标准公差表》26、大齿轮的检验项目:27、周节积累公差Fp:0.09028、周节极限偏差fpt:0.02029、在图纸上标注的齿坯公差:内孔按照IT7级:在手册上按照孔径大小查《标准公差表》30、顶圆的径向跳动:按照外径尺寸大小查《标准公差表》本网络手册中的圆柱齿轮精度摘自(GB10095—88),现将有关规定和定义简要说明如下:(1) 精度等级齿轮及齿轮副规定了12个精度等级,第1级的精度最高,第12级的精度最低。
齿轮各部分名称及标准齿轮的基本尺寸

一对齿轮传动时,所有啮合点都在啮合线N1N2上。
pb1 rb1 r1
B1
O1
ω1
N1
pb1
rb1 r1 B1
O1 ω1
N1
pb1
rb1
O1
ω1
r1
N1
B2
N2
N2
P r2
P
B2
N2
B2
B1 P r2
外观齿1 比齿2大
rb2
r2
rb2
rb2 ω2
从外观看齿 1比齿2小
pb1<pb2 m1<m2
ω2 O2
1.一对轮齿的啮合过程 B2 ----起始啮合点 B1----终止啮合点 B1B2 -实际啮合线 N1N2 :因基圆内无渐开线 理论上可能的最长啮合线段-理论啮合线段 N1、N 2 -啮合极限点 阴影线部分-齿廓的实际工作段。
N2
rb1
O1 ω1 B2 P B1 ra2
ra1 N1
rb2
ω2 O2
12
定义分度圆压力角为齿轮的压力角:
N rb rf r
Bi B1
Ki ri A r1 O rb
αi
K1
α1
ra
αi ω
α
O
3
α=arccos(rb/r) 或rb=rcosα,
db=dcosα
对于分度圆大小相同的齿轮,如 果 α不同,则基圆大小将不同, 因而其齿廓形状也不同。
α是决定渐开线齿廓形状的一个重要参数。 规定标准值:α=20°
α 不根切的条件: P N1≥P B2 rb3 rb 在△PN1O1 中有: PN1=rsinα =mzsinα/2 r rb1 在△PB2B’ 中有: PB2=ha*m/sinα
齿轮齿条中心距

齿轮齿条传动,齿条与齿轮的中心距怎么算?2006-03-20 19:34匿名|分类:工程技术科学|浏览44662次比如,齿轮齿条模数为4,齿轮齿数为20,齿轮中心距离尺条齿顶或齿根多远?|2006-03-22 13:35提问者采纳条件:圆柱直齿,标准齿形,标准安装[1] :计算齿轮分度圆直径4*20=80[2] : 由于标准安装,所以分度圆与节圆重合计算节圆半径= 80/2=40[3] : 计算中心距离尺条齿顶距离距离=节圆半径-模数*1.0= 40-4*1= 36[4] : 计算中心距离尺条齿根距离距离=节圆半径+模数*1.25= 40 + 4*1.25= 45============================不好意思^^,昨天马马虎虎,公式都带错了!赶快改正确,让大家笑话了。
评论(3)|711lnnao2013-1-25 19:04你这答案太有用了,大赞呐~383315742008-3-21 22:07齿轮中心距离齿条齿顶=m(z-2)÷2=4(20-2)÷2=36(毫米)齿轮中心距离齿条齿根=m(z+2.5)÷2=4(20+2.5)÷2=45(毫米)想知道这个是怎么算的huangh88522009-4-10 09:05齿轮中心距加上齿根高度或者减去齿顶高度,应该是这么算的adams怎么找到齿轮齿条的啮合点。
最好是能在图上标注出来的。
2012-10-31 20:53zlcute163|分类:工程技术科学|浏览449次|2012-11-01 13:13提问者采纳从理论上计算,如果装配正确,找到节圆位置,把MARKER点向齿条方向偏移节圆半斤距离。
追问:齿轮齿条的节圆怎么定义的呢?我这个是7齿的齿轮,变位较大回答:这要看你是怎么设计的,实际接触点所在的圆是节圆,我不知道你怎么装配的也不好。
标准齿轮计算公式

标准齿轮计算公式一、标准齿轮的基本参数。
1. 模数(m)- 定义:齿距p与圆周率π的比值,即m = (p)/(π),单位为mm。
它是决定齿轮尺寸的一个基本参数,模数越大,齿轮的尺寸越大,轮齿也越粗壮。
2. 压力角(α)- 标准值:一般取α = 20^∘。
它是在节点处,齿廓曲线的公法线(压力线)与两节圆的公切线(节点速度方向)所夹的锐角。
3. 齿数(z)- 表示齿轮轮齿的个数。
4. 分度圆直径(d)- 计算公式:d = mz。
分度圆是齿轮上具有标准模数和标准压力角的圆。
5. 齿顶高(ha)- 计算公式:ha = m。
齿顶圆到分度圆的径向距离。
6. 齿根高(hf)- 计算公式:hf=(h_a^*+c^*)m,对于标准齿轮h_a^*=1,c^*=0.25(h_a^*为齿顶高系数,c^*为顶隙系数),所以hf = 1.25m。
齿根圆到分度圆的径向距离。
7. 齿全高(h)- 计算公式:h=h_a+h_f=2.25m。
齿顶圆到齿根圆的径向距离。
8. 齿顶圆直径(da)- 计算公式:da = d + 2h_a=m(z + 2)。
9. 齿根圆直径(df)- 计算公式:df=d - 2h_f=m(z- 2.5)。
10. 基圆直径(db)- 计算公式:db = dcosα=mzcosα。
基圆是形成渐开线的发生圆。
11. 中心距(a)- 对于标准安装的标准齿轮(两个齿轮的分度圆相切),计算公式:a=frac{d_1+d_2}{2}=frac{m(z_1+z_2)}{2}。
齿轮各部分名称及标准齿轮的基本尺寸

最常用
齿轮加 工方法
铣削 拉削 插齿 滚齿 范成法 (展成法共 剃齿 轭法 磨齿
包络法)
一、成形法铣削
盘铣刀
指状铣刀
14
ω
分度 进给
铣刀旋转,工件进给 分度、断续切削。
切削
适用于加工大模数 m>20 的齿轮和人字 齿轮。 切削 进给
ω
盘铣刀加工 由db=mzcosα可知,渐 开线形状随齿数变化。 要想获得精确的齿廓, 加工一种齿数的齿轮, 就需要一把刀具。这在 工程上是不现实的。
γ
进给 t
为什么滚刀要倾斜一个角度呢?
V=ωr=ωmz/2
ω
v
19
t
t
γ
t
t
范成法加工的特点: 一种模数只需要一把刀具连续切削,生产效率 高,精度高,用于批量生产。
20
c*m h*amh*am c*m
4.用标准齿条型刀具加工标准齿轮 α=20° πm/2 πm/2 4.1标准齿条型刀具 GB1356-88规定了标准齿条 型刀具的基准齿形。
ha=h*am
s
e
21
§4-7 根切现象、最少齿数及变位齿轮 一、根切现象 图示现象称为轮齿的根切。
根切的后果: ①削弱轮齿的抗弯强度; ②使重合度ε下降。
以下分析产生根切的原因: 当B2落在N1点的下方: PB2<PN1 刀具在位置1开始切削齿间; 在位置2开始切削渐开线齿廓; 在位置3切削完全部齿廓;
让刀运动
ω0
ω
ω
i=ω0 /ω=z/z0
齿轮插刀加工
17
2. 齿条插刀 切削 v
范成
让刀
齿轮各部分名称及标准齿轮的基本尺寸

O2
能正确啮合!
r2 rb2
外观齿1 比齿2大
pb1>pb2
ω2
m1<不m2能正确O啮2 合!
8
1.正确啮合条件
要使进入啮合区内的各对齿轮都能正确地进入啮合,两 齿轮的相邻两齿同侧齿廓间的法向距离应相等:
pb1= pb2
pb1
将pb=π mcosα代入得: m1cosα1=m2cosα2
rb1 r1
t
V=ωr=ωmz/2
为什么滚刀要倾斜一个角度呢?
ω0
滚刀轴剖面 相当于齿条
v
19
t
t
γ
t
t
范成法加工的特点:
一种模数只需要一把刀具连续切削,生产效率 高,精度高,用于批量生产。
20
c*m h*amh*am c*m
4.用标准齿条型刀具加工标准齿轮
α=20°
4.1标准齿条型刀具
πm/2 πm/2
GB1356-88规定了标准齿条
B1----终止啮合点
B1B2 -实际啮合线
N N : 1 2
因基圆内无渐开线
理论上可能的最长啮合线段--
理论啮合线段
B2 N1 P
N2
B1
ra2
rb2
ω2
N1、N 2 -啮合极限点
O2
阴影线部分-齿廓的实际工作段。
12
2.连续传动条件
一对轮齿啮合传动的区间是有限的。要保证 齿轮连续转动,则在前一对轮齿脱离啮合之
定义分度圆压力角为齿轮的压力角:
N
rb rf r ra
α
Ki
αi
B1 Bi αi
ri K1 A
α1
ω
r1
渐开线标准齿轮的基本尺寸

5.正常齿制:齿顶高系数ha*=1,顶隙系数C=0.25
标准齿轮标准安装
1
a
2
c*m
o1 r1= r’1
r2= r'2 o2
标准安装时, 1)两分度圆相切,中心距为标准中心距:
a= r’1+r‘2 = r1 + r2 ,其顶隙为标准值c*m。 2)压力角与啮合角相等。
必须清晰的几个概念
3. 标准中心距:一对标准齿轮标准安装 (即分度园相切)时的中心距a。
4.只有当标准齿轮标准安装时,压力角与啮合角 相等。
5.正常齿制:齿顶高系数ha*=1,顶隙系数C=0.25。
渐开线标准直齿圆柱齿轮的基本参数
五个基本参数 Z;m ;=200 ;ha*=1 ;C=0.25
标准直齿圆柱齿轮的几何尺寸计算
4-4 齿轮各部分名称及 渐开线标准齿轮的基本尺寸
渐开线齿轮的轮齿是由 两段反向的渐开线组成的。
齿宽 齿顶圆
齿根圆
分度圆齿Biblioteka 高ha 齿根高hf 齿全高 h= ha+hf
h
任意圆上的齿厚sK, 齿槽宽eK和齿距pK
pK= sK + eK
eK p
K
s
K
rK
od
K
直径为dK的任意圆上: 圆周长为:dK=ZpK dK=Z(pK/)
力角=200,模数 m
对于同一条渐开线:rK ↓ →αK ↓ αb=0 为标准值(表4-1)。
定义分度圆压力角为齿轮的压力角 :
N
K αK
rb
作者:潘存云教授
α
rf r
ra
BK
B1
圆柱齿轮精度标准

齿轮精度的标注.1
(1)精度等级标注示例如下:
7
GB/T1表示轮齿同侧齿面偏差项目应符合 GB/T10095.1的要求,精度均为7级。
齿轮精度的标注.2
标注示例如下:
7Fp 6(Fα、Fβ) GB/T10095.1—2008
齿轮各项偏差的精度等级 精度标准代号
基准面和工作安装面的形状公差见表7.23
安装基准面的跳动公差
表7.24 安装基准面的跳动公差
表面粗糙度的选择
齿轮各表面的粗糙度,将影响到齿轮的加工
方法、使用性能和经济性,见表7.25。
表7.25 齿轮各表面的表面粗糙度Ra推荐值
4、齿轮精度的标注
齿轮工作图上,应标注齿轮的精度等级、检 验组公差、齿厚偏差的数值。 视图上直接标注齿顶圆直径及公差、分度圆 直径、齿宽及公差、孔(轴)直径及公差、 定位面及其要求、表面粗糙度等。
齿轮副的精度
(2)轴线平行度偏差fΣδ 、fΣβ fΣδ是指一对齿轮的轴线在其基准平面上投影 的平行度偏差。 fΣβ 是指一对齿轮的轴线在垂直于基准平面 且平行于基准轴线的平面上投影的平行度 偏差,见图7.31。
齿轮副的精度.1
为保证载荷分布均匀性和齿面接触精度,轴 线平行度偏差应加以控制。
f
齿轮精度的标注.4
(2)齿厚偏差标注方法:
Esn s SnE ——其中Sn为法向齿厚,Esns为齿厚 sn i
的上偏差,Esni为齿厚的下偏差。
Eb n s WkE ——其中Wk为跨k个齿数的公法线长 bni
度,Ebns为公法线长度上偏差,Ebni为公法
线长度下偏差。
四、齿轮副的精度和齿侧间隙
1、齿轮副的精度 (1)齿轮副的中心距极限偏差±fa fa是指在齿轮副的齿宽中间平面内,实际中 心距与公称中心距之差。 齿轮副中心距的尺寸偏差不但会影响齿轮侧 隙,而且对齿轮的重合度产生影响 。 中心距极限偏差±fa见表7.26。
标准中心距的计算公式

标准中心距的计算公式根据不同的情况有所不同。
对于两个互相啮合的齿轮,其圆心距离称为中心距。
外啮合的计算公式为a=m(z1+z2)/2,内啮合的计算公式为a=m(z1-z2)/2。
其中,m代表模数,z1和z2分别代表两个齿轮的齿数。
此外,中心距也可以通过两节圆的半径之和或两分度圆半径与分离量之和来计算,公式为a=r1′+r2′或a=r1+r2+ym。
其中,r1′和r2′分别代表两节圆的半径,r1和r2代表两分度圆的半径,ym代表分离量。
另外,根据两个点在x轴和y轴上的差值,也可以计算两点的距离,即中心距。
公式为等于齿轮副两节圆半径之和(a=r1′+r2′),或等于两分度圆半径与分离量之和(a=r1+r2+ym)。
在具体应用中,需要根据实际情况选择合适的计算公式,以得到准确的结果。
标准齿轮主要参数及其计算-标准齿轮
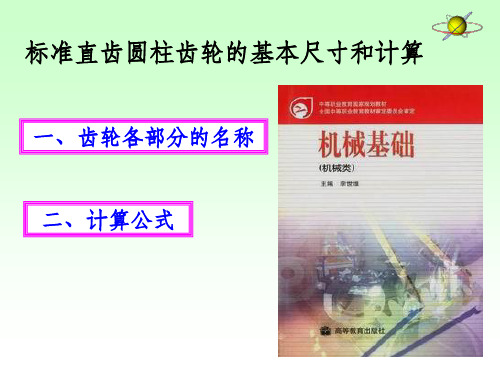
外啮合标准直齿圆柱齿轮计算公式
名称 代 号
计算公式
模数 压力角 齿数
m 通过计算定出 α α=200 z 由传动比计算求得
齿距
p p=πm
齿厚
s s=p/2=πm/2
槽宽
e e=s=p/2=πm/2
基圆齿距 pb pb=pcos α=πmcos α
名称
顶系 分度圆直径 基圆直径 齿顶圆直径 齿根圆直径
正常齿制: ha* = 1
c * = 0.25
短齿制: ha* = 0.8 标准齿轮
c * = 0.3
分度圆上齿厚与齿槽宽相等,且齿顶高和 齿根高为标准值的齿轮称为标准齿轮。
根据齿轮所承 受的载荷大小等条 件,选定了模数, 并选定了齿顶高系 数、顶隙系数、压 力角,并确定了齿 轮的齿数后,标准 齿轮各部分的尺寸 就能够利用公式进 行计算。
已知: α=200 z1=20
ha*=1 z2=32
c*=0.25 m=10mm
求: d
da df s
db a
练习
1、已知标准直齿圆柱外齿轮的全齿高 h=18mm,z=30,试计算齿轮的模数m和 分度圆直径d。
2、一对标准直齿圆柱外啮合齿轮传动,大 齿轮的齿顶圆直径da2=408mm,齿数 z=100,压力角α=200,两轴的中心距 a=310mm,试确定小齿轮的:①模数m, 齿数z②计算分度圆直径d1③齿顶圆直径 da1④齿根圆直径df1
代
计算公式
号
c c=c*m=0.25m
d d=mz
db db=dcos α=mzosα da da=d+2ha=m(z+2) df df=d-2hf=m(z-2.5)
齿顶高 齿根高 全齿高
齿轮标准安装中心距

齿轮标准安装中心距
齿轮标准安装中心距是指两个相邻齿轮啮合齿廓的中心距离。
中心距是齿轮传动的重要参数,确定了齿轮之间的位置和相对运动关系。
中心距的计算公式为:C = (D1 + D2) / 2,其中C为中心距,D1和D2分别为两个齿轮的分度圆直径。
根据国际标准(ISO 1328),齿轮的标准中心距是通过模数计算得出的,公式为:C = (m1 + m2),其中m1和m2分别为两个齿轮的模数。
在实际安装中,为了确保齿轮间的啮合和传动精度,中心距一般会有一定的误差范围。
标准安装中心距的允许误差和相关参数可根据具体的齿轮设计和制造标准进行调整。
齿轮实际中心距小于标准中心距

齿轮实际中心距小于标准中心距1. 引言在机械传动中,齿轮是一种常见的传动方式,它通过齿轮的啮合来传递动力和转速。
在设计齿轮传动系统时,通常会根据标准中心距来选择齿轮。
然而,在实际的应用中,有时会出现齿轮的实际中心距小于标准中心距的情况。
本文将从深度和广度的角度探讨这一主题,并对齿轮实际中心距小于标准中心距的影响和解决方法进行全面评估。
2. 齿轮实际中心距小于标准中心距的影响2.1 在传动精度上的影响齿轮实际中心距小于标准中心距会导致齿轮的啮合位置发生偏移,从而影响传动的精度。
这会导致传动系统的转动不稳定,增加系统的振动和噪音,降低传动效率。
由于齿轮啮合位置的偏移,还会加剧齿轮的磨损,缩短齿轮的使用寿命。
2.2 在传动效率上的影响齿轮实际中心距小于标准中心距还会影响传动系统的效率。
由于齿轮啮合位置的偏移,传动过程中会出现能量损失,从而降低传动效率。
这不仅会增加动力传递的能耗,还会影响整个机械系统的工作效率。
3. 解决方法3.1 优化齿轮设计针对齿轮实际中心距小于标准中心距的问题,可以通过优化齿轮的设计来解决。
调整齿轮的轴向位置和尺寸,使得实际中心距接近标准中心距,从而减小齿轮的偏差。
还可以采用更高精度的加工工艺和材料,提高齿轮的制造精度和耐磨性,从而改善齿轮的传动特性。
3.2 优化传动系统结构除了优化齿轮设计,还可以通过优化传动系统的结构来解决齿轮实际中心距小于标准中心距的问题。
增加齿轮的支撑和固定装置,减小齿轮的振动和偏移;采用更合理的润滑方式,减小齿轮的磨损和能量损失;调整传动系统的布局和连接方式,改善传动的稳定性和效率。
4. 个人观点和理解在实际工程应用中,齿轮实际中心距小于标准中心距的问题是一个常见的挑战。
针对这一问题,需要工程师们在齿轮设计和传动系统的优化上下足功夫,以确保传动系统能够稳定、高效地工作。
也需要注重对齿轮制造工艺和材料的选择,以提高齿轮的制造精度和耐磨性。
通过综合应用工程设计、制造技术和材料科学的知识,才能有效解决齿轮实际中心距小于标准中心距的问题,实现传动系统的稳定、高效运行。
中心距标准值

中心距标准值
中心距是指机械零件上的两个相对的特征面之间的距离。
在机
械设计和制造中,中心距的标准值对于保证零件的精度和装配质量
至关重要。
本文将介绍中心距的概念、计算方法以及在实际应用中
的重要性。
首先,中心距的概念是指两个特征面之间的距离,通常用于描
述轴承、齿轮等零部件之间的相对位置关系。
在设计和制造过程中,准确计算和控制中心距是确保零件装配精度的关键因素之一。
因此,了解中心距的计算方法和标准值是非常重要的。
对于不同类型的机械零件,中心距的计算方法也有所不同。
例如,在齿轮传动中,中心距的计算需要考虑齿轮的模数、齿数、压
力角等参数;而在轴承安装中,中心距的计算则需要考虑轴承孔的
尺寸和位置等因素。
因此,在实际应用中,需要根据具体的零件类
型和要求来选择合适的计算方法,并严格按照标准值进行设计和制造。
在实际应用中,中心距的标准值对于保证零件的装配质量和工
作性能至关重要。
如果中心距偏离了标准值,就会导致零件装配后
出现偏斜、摩擦增大、噪音增加等问题,严重影响机械设备的使用
寿命和工作效率。
因此,在设计和制造过程中,必须严格按照中心
距的标准值进行计算和控制,确保零件的装配精度和工作稳定性。
总之,中心距作为机械零件装配的重要参数,其标准值的准确
计算和严格控制对于保证零件的装配质量和工作性能至关重要。
在
实际应用中,需要根据具体的零件类型和要求选择合适的计算方法,并严格按照标准值进行设计和制造,以确保机械设备的使用寿命和
工作效率。
安装中心距和标准中心距

安装中心距和标准中心距是在机械设计和工程领域中常用的两个术语。
1.安装中心距:指的是机械设备、零部件或连接件等安装时的中心距离。
安装中心距通常
用于描述两个旋转轴线或连接点之间的距离,如传动装置中的两个齿轮的中心距离、电机与传动装置之间的中心距离等。
安装中心距的选择通常需要考虑到设备的功能要求、运行平稳性、传递力矩等因素。
2.标准中心距:指的是根据相关标准所规定的特定中心距值。
各种机械设备和连接件的尺
寸和布局往往需要遵循标准,以确保互换性、配合性和兼容性。
标准中心距一般由行业和国际标准化组织制定,例如ISO(国际标准化组织)和ANSI(美国国家标准学会)等。
使用标准中心距可以方便设备设计、制造和维护,提高产品的通用性和可替代性。
在实际应用中,安装中心距可以选择与标准中心距相匹配的数值,以便满足特定的设计要求和使用环境。
然而,并非所有情况下都需要使用标准中心距,因为每个应用可能有其特定的需求和限制。
因此,在进行机械设计时,需要根据具体情况来选择适合的安装中心距,并结合实际工程需求进行合理的设计和布局。
中心距标准值

中心距标准值中心距是指两个相邻轴的轴心距离,通常用于描述机械设备中的传动结构。
在设计和制造机械设备时,中心距的选择对于传动结构的性能和稳定性至关重要。
因此,确定合适的中心距标准值对于机械设备的正常运行和使用寿命具有重要意义。
首先,中心距的选择需要考虑传动装置的工作条件和要求。
不同的传动装置在工作条件和要求上有所不同,因此中心距的标准值也会有所差异。
例如,在高速传动装置中,为了减小传动系统的惯性力和振动,中心距一般会选择较小的数值;而在大功率传动装置中,为了保证传动结构的稳定性和可靠性,中心距则会选择较大的数值。
其次,中心距的选择还需要考虑传动装置的结构特点和受力情况。
不同的传动结构在结构特点和受力情况上也存在差异,因此中心距的标准值也会有所不同。
例如,在齿轮传动结构中,中心距的选择需要考虑齿轮的模数、齿数和压力角等参数;而在链传动结构中,中心距的选择则需要考虑链条的长度、张紧装置和受力情况等因素。
此外,中心距的选择还需要考虑传动装置的安装和维护便利性。
合理选择中心距可以使传动装置的安装和维护更加方便,减小维护成本和提高工作效率。
因此,在确定中心距标准值时,需要综合考虑传动装置的安装空间、维护通道和操作便利性等因素,以便更好地满足使用要求。
总之,中心距的选择对于传动装置的性能和稳定性具有重要影响。
合理选择中心距标准值可以使传动装置在工作过程中更加稳定可靠,延长设备的使用寿命,降低维护成本,提高工作效率。
因此,在设计和制造传动装置时,需要充分考虑传动装置的工作条件和要求,结构特点和受力情况,以及安装和维护便利性等因素,以便更好地确定中心距的标准值。
传动中心距计算公式

公式为:a=(d1+d2)/2=(Z1+Z2)*M/2=(Z1+Z2)*Mn/2*cosβ。
以上公式中a---齿轮中心距d1---齿轮1的分度圆直径d2---齿轮2的分度圆直径Z1---齿轮1的齿数Z2---齿轮2的齿数M---模数(两齿轮相等)Mt---端面模数(两齿轮相等)Mn---法向模数(两齿轮相等)β---螺旋角齿轮是能互相啮合的有齿的机械零件。
它在机械传动及整个机械领域中的应用极其广泛。
齿轮中心距,指的是两个互相啮合的齿轮的圆心距离称为中心距。
扩展资料1、标准蜗杆和标准斜齿轮啮合中心距的计算方法为了便于计算,蜗杆和斜齿轮均使用法向模数。
对于蜗杆的齿部参数,我们必须对其进行转化,引进当量齿数Zv,其计算如下:Zv = k/tgλ(1)式中:k 表示蜗杆头数,λ表示导程角。
这样,蜗杆-斜齿轮的中心距A 就按下式计算A = 0.5* mn *(Z1+Zv)/COSλ(2)式中:Z1 表示斜齿轮齿数,mn 表示蜗杆法向模数。
2、蜗杆减薄(增厚)和斜齿轮变位时啮合中心距的计算方法首先我们根据公式3,计算出蜗杆的变位系数。
然后根据斜齿轮角度变位公式4 计算蜗杆-斜齿轮的啮合中心距。
Sfn =0.5*π*mn + 2*ξw*tgαn* mn (3)A = (0.5*mn *(Z1+Zv)/COSλ)*COS(αt)/ COS(αt’) (4)αt = arctg(tgαn/cosλ) (5)invαt’= 2*tg(αt)* ξ/( Z1+Zv)+invαt (6)式中:Sfn 表示蜗杆实际法向齿厚mn 表示蜗杆法向模数ξw 表示蜗杆变位系数αn 表示蜗杆的法向压力角αt’表示端面啮合角αt 表示斜齿轮的端面压力角ξ表示总变位系数(端面)。
- 1、下载文档前请自行甄别文档内容的完整性,平台不提供额外的编辑、内容补充、找答案等附加服务。
- 2、"仅部分预览"的文档,不可在线预览部分如存在完整性等问题,可反馈申请退款(可完整预览的文档不适用该条件!)。
- 3、如文档侵犯您的权益,请联系客服反馈,我们会尽快为您处理(人工客服工作时间:9:00-18:30)。
对于标准齿轮,确定中心距a时,应满足两个要求: 1) 理论上齿侧间隙为零 s’ -e’ =0 1 2 2) 顶隙c为标准值。c=c*m 此时有:
a =ha*m +c*m + r2-(ha*m+c*m) = r1+ r2 = m(z1+z2) / 2
a =r1+ r2
标准中心距
标准安装
渐开线直齿圆柱齿轮的啮合传动
当一对标准齿轮按标准中心距(两轮分度圆相切 )安装 时,称为标准安装。
非标准安装时,两齿轮分度圆不再相切,节圆大于分度 圆;两基圆相对分离,啮合角因此不再等于分度圆压力 角而加大;同时,顶隙大于标准值,而且出现侧隙。
渐开线直齿圆柱齿轮的啮合传动
齿轮齿条传动时的标准安装和非标准安装。