OEE计算及损失分析
OEE及六大损失讲解

时间利用率 停工、故障 时间利用率 换装、调整 性能利用率 空转、瞬停 性能利用率 合格率 合格率 速度降低 废品、返工 启动稳定
OEE与六大损失讲解
OEE定义
• OEE(Overall Equipment Effectiveness)是设备综合效率的缩写。 • OEE是一个独立的测量工具,它用来表现实际的生产能力 相对于理论产能的比率。 • 通过这个比率来衡量设备的运行能力。
设备能力 100% 不良 损失 速度 损失 OEE 计划 停机
0%
有效产出能力 实际总产量 设备运行时间 合格品
?
OEE公式
• • • • • • 时间利用率=设备开动时间(A)/计划工作时间(B) 这一数值,体现了在整个工作时间内,设备的实际工作比率。 性能利用率=实际总产量(C)/理想产量(设备开动时间(A)内) 这一数值体现了在设备开动时间(A)内,设备的产出比率。 合格率=实际合格品数(D)/实际总产量(C) 这一数值体现了在实际总产出中,设备的有效产出的比率。
OEE中的六大损失
工作时间 设备开动时间(负荷时间) 计 划 损 失
计划停机 教育、早会 1-停工、故障 2-换装、调整
由于政策、规划 等,这些损失为 企业允许的损失
设备正常开动时间
停 止 损 失
设备产出时间
性 能 损 失 不 良 损 失
3-空转、瞬停 4-速度降低 5-废品、返工 6-启动稳定
总称:设备六大损失
OEE及六大损失讲解

OEE中的六大损失
工作时间 设备开动时间(负荷时间) 计 划 损 失
计划停机 教育、早会 1-停工、故障 2-换装、调整
由于政策、规划 等,这些损失为 企业允许的损失
设备正常开动时间
停 止 损 失
设备产出时间
性 能 损 失 不 良 损 失
3-空转、瞬停 4-速度降低 5-废品、返工 6-启动稳定
总称:设备六大损失
谢谢! Thanks
有效产出时间
六大损失体现
序号 1 2 3 4 5 6 OEE相关 损失名称 损失体现 设备损坏、 制程异常等 待料、换规格、 人力不足、setup等 生产不畅、传感器关闭等 低于设计产能运行、 设备磨损、员工失误 生产稳定时产生的废品 启动、调试时产生的废品。
时间利用率 停工、故障 时间利用率 换装、调整 性能利用率 空转、瞬停 性能利用率 合格率 合格率 速度降低 废品、返工 启动稳定
• 结论:OEE=时间利用率X性能利用 • • • • • OEE =时间利用率x性能利用率x合格率 =(A/B)*(C/理想产量)*(D/C) 注:理想产量=理想速度(V)*设备开动时间(A) 故OEE =(A/B)*(C/(V*A))*(D/C) =D/(B*V) OEE就是在计划工作时间内,生产出合格品(有效产出) 的百分比(能力)。
0%
有效产出能力 实际总产量 设备运行时间 合格品
?
OEE公式
• • • • • • 时间利用率=设备开动时间(A)/计划工作时间(B) 这一数值,体现了在整个工作时间内,设备的实际工作比率。 性能利用率=实际总产量(C)/理想产量(设备开动时间(A)内) 这一数值体现了在设备开动时间(A)内,设备的产出比率。 合格率=实际合格品数(D)/实际总产量(C) 这一数值体现了在实际总产出中,设备的有效产出的比率。
OEE的计算公式

OEE的计算公式OEE(Overall Equipment Effectiveness)是一种衡量设备效率和生产效果的关键性指标。
它是由美国自动化协会(American Productivity & Quality Center)提出并广泛应用于各类制造企业中。
设备的有效生产时间(Net Operating Time,也称为稼动时间)指的是设备在生产过程中的全部时间减去计划维修时间、预定停机时间和计划修整时间。
公式如下:稼动时间=总时间-计划维修时间-预定停机时间-计划修整时间设备的速度损失(Speed Loss)指的是设备在生产中由于速度低于设计速度而造成的损失时间。
这可能是由于设备故障、设备调试期间的运行速度下降、设备因为操作员的技术水平不高而无法达到最大速度等原因造成的。
公式如下:速度损失=稼动时间-设备实际运行时间设备的质量损失(Quality Loss)指的是由于生产过程中产生的次品和废品所导致的损失时间。
这可能是由于操作员技术不熟练、原材料质量问题、设备故障引起的废品等原因造成的。
公式如下:质量损失=稼动时间-合格产品产生的时间根据以上三个因素,可以计算出OEE的值。
OEE的计算公式如下:OEE=稼动时间×性能指标×质量指标其中性能指标(Performance Index)表示设备在生产中实际运行时间与设备理论运行时间的比值。
性能指标的计算公式为:性能指标=设备实际运行时间÷(设备理论运行时间×合格产品产生的时间)质量指标(Quality Index)表示合格产品产生的时间与设备实际运行时间的比值。
质量指标的计算公式为:质量指标=合格产品产生的时间÷设备实际运行时间将性能指标和质量指标代入OEE计算公式中,可以得到最终的OEE值。
OEE计算与分析

OEE计算与分析OEE(Overall Equipment Efficiency)是衡量生产设备效率的一个重要指标。
它可以帮助企业评估生产过程中各种损失以及设备的利用率,为企业提供改进生产效率的参考。
OEE可以通过以下公式计算:OEE = Availability × Performance× Quality其中,Availability表示设备的可用时间与计划生产时间的比值,Performance表示实际产量与标准产量的比值,Quality表示良品产量与实际产量的比值。
首先,我们可以详细介绍一下Availability的计算和分析。
Availability的计算公式是:Availability = (计划生产时间 - 停机时间) / 计划生产时间停机时间包括计划停机时间和非计划停机时间。
计划停机时间是计划工作时间中设备停机的时间,通常用于设备维护、更换工具等。
非计划停机时间是指设备出现故障或其他原因导致的非计划停机的时间。
通过详细记录每个停机事件的开始和结束时间,可以计算出总的停机时间。
然后,将总的停机时间除以计划生产时间,即可得到Availability的值。
在分析Availability时,可以根据每个停机事件的原因进行分类,例如设备故障、物料不足、工具更换等。
通过分析停机事件的数量和持续时间,可以找出导致停机的主要原因,并采取相应的措施来减少停机时间。
其次,我们来看一下Performance的计算和分析。
Performance的计算公式是:Performance = 实际产量 / (计划生产时间 - 停机时间) Performance反映了设备在实际生产过程中运行的效率。
除了停机时间,还需要考虑设备在正常运行状态下的速度是否达到预期。
如果设备运行速度低于预期,可能是由于操作不当、工艺问题或设备老化等原因。
通过分析Performance时,可以结合操作日志以及设备监控系统的数据,找出导致设备运行效率低下的主要原因。
oee分析报告
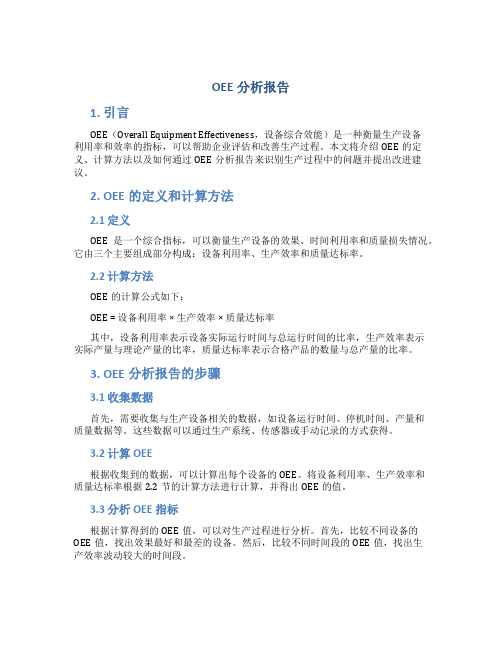
OEE分析报告1. 引言OEE(Overall Equipment Effectiveness,设备综合效能)是一种衡量生产设备利用率和效率的指标,可以帮助企业评估和改善生产过程。
本文将介绍OEE的定义、计算方法以及如何通过OEE分析报告来识别生产过程中的问题并提出改进建议。
2. OEE的定义和计算方法2.1 定义OEE是一个综合指标,可以衡量生产设备的效果、时间利用率和质量损失情况。
它由三个主要组成部分构成:设备利用率、生产效率和质量达标率。
2.2 计算方法OEE的计算公式如下:OEE = 设备利用率 × 生产效率 × 质量达标率其中,设备利用率表示设备实际运行时间与总运行时间的比率,生产效率表示实际产量与理论产量的比率,质量达标率表示合格产品的数量与总产量的比率。
3. OEE分析报告的步骤3.1 收集数据首先,需要收集与生产设备相关的数据,如设备运行时间、停机时间、产量和质量数据等。
这些数据可以通过生产系统、传感器或手动记录的方式获得。
3.2 计算OEE根据收集到的数据,可以计算出每个设备的OEE。
将设备利用率、生产效率和质量达标率根据2.2节的计算方法进行计算,并得出OEE的值。
3.3 分析OEE指标根据计算得到的OEE值,可以对生产过程进行分析。
首先,比较不同设备的OEE值,找出效果最好和最差的设备。
然后,比较不同时间段的OEE值,找出生产效率波动较大的时间段。
3.4 识别问题和改进建议通过分析OEE指标,可以识别出生产过程中存在的问题。
例如,设备利用率低可能是由于设备故障或停机时间过长导致的。
生产效率低可能是由于操作不当或工艺不合理导致的。
质量达标率低可能是由于原材料质量不良或工艺参数设置不准确导致的。
针对识别出的问题,可以提出相应的改进建议。
例如,对于设备利用率低的问题,可以进行设备维护和保养,减少故障发生的可能性;对于生产效率低的问题,可以进行员工培训和工艺优化,提高操作效率;对于质量达标率低的问题,可以加强原材料的质量控制和工艺参数的监测。
OEE计算及损失分析

Item Number CXV4250B 113802CH
Output (EA) 20,561 6,256
3. 4.
5.
6.
4. 非负荷时间
• 没生产安排的空闲时间或没生产需求的
相关活动的时间
• 包括:
法
定 工 作
非 负 荷
时 间
时 间
负 荷 时 间
用 餐
➢ 没生产需求
–产能过剩的停工时间或没生产需求的停工时间 –新设备进行IQ/OQ/PQ或设备升级改造的停工时间 –厂房建筑施工
➢ 主要的设备维护保养或清洁
OEE =
X
X
=
=
OEE的计算
1. 班次OEE计算:为该班次生产的合格品数量的价值运行时间与总的生产时间的比值。
计算TF1 9月1日第3个班次的OEE
Production Shift Line Work WO
Date
Center Number
2015.9.1 3 TF1 30611 48245
Item Number CXV4793A
➢ 首次清洁消毒 ➢ 再次清洁消毒 ➢ 产品批次转换调整
备注: 1. 产品转换是指不同产品之间的转换,清洁消毒的停机
损失,停机代码记为08 2. 同样的产品隔了一段时间重新开订单的清洁消毒的停
机损失,停机代码记为11
9. 计划停机损失
生
清
产
洁
计
时
消
划
间
毒
停
损
机
失
损
失
7.
8.
9.
非 计 划 停 机
运 行 时 间
值。
计算工作中心30666的OEE
OEE介绍和计算方法-oee介绍

OEE(Overall Equipment Effectiveness),即设备综合效率,其本质就是设备负荷时间实际产量与理论产量的比值。
企业在进行OEE计算时常常遇到很多迷惑的问题,如工厂停水、停电、停气、停汽使设备不能工作,等待定单、等待排产计划、等待检查、等待上一道工序造成的停机,不知如何计算。
本文引入非设备因素停机的概念,修改了OEE的算法,使计算得到的OEE更能够真实反映设备维护的实际状况,让设备完全利用的情况由完全有效生产率这个指标来反映。
本文同时介绍了在不同情况下如何分析设备损失的PM分析流程。
1、 OEE表述和计算实例OEE= 时间开动率×性能开动率×合格品率其中,时间开动率 = 开动时间/负荷时间而,负荷时间 = 日历工作时间-计划停机时间开动时间 = 负荷时间–故障停机时间–设备调整初始化时间性能开动率 = 净开动率×速度开动率而,净开动率 = 加工数量×实际加工周期/开动时间速度开动率 = 理论加工周期/实际加工周期合格品率 = 合格品数量/ 加工数量在OEE公式里,时间开动率反映了设备的时间利用情况;性能开动率反映了设备的性能发挥情况;而合格品率则反映了设备的有效工作情况。
反过来,时间开动率度量了设备的故障、调整等项停机损失,性能开动率度量了设备短暂停机、空转、速度降低等项性能损失;合格品率度量了设备加工废品损失。
OEE还有另一种表述方法,更适用于流动生产线的评估, 即OEE= 时间开动率×性能开动率×合格品率而,时间开动率 = 开动时间/计划利用时间而,计划利用时间 = 日历工作时间-计划停机时间开动时间 = 计划利用时间–非计划停机时间性能开动率 = 完成的节拍数/计划节拍数其中,计划节拍数 = 开动时间/标准节拍时间合格品率 = 合格品数量/加工数量这与前述的OEE公式实际上是同一的。
计算:停机时间 = 115+12 = 127 min计划开动时间 = 910 – 127 = 783 min时间开动率 = 783/910 = 86%计划节拍数 = 开动时间/标准节拍时间 = 783/3 = 261性能开动率 = 203/261 = 77.7%合格品率 = 一次合格品数/完成产品数 = 152/203 = 74.9%于是得到 OEE = 86% ×77.7%×74.9% = 50%2、 OEE的实质如果追究OEE的本质涵,其实就是计算周期用于加工的理论时间和负荷时间的百分比。
OEE计算及损失分析

OEE计算及损失分析OEE(Overall Equipment Efficiency)即设备综合效率,是一个衡量设备运营效率的指标。
它可以帮助企业了解设备的运行状况,找出可能影响生产效率的问题,从而进行改进。
OEE的计算涉及到三个主要指标:设备的可利用率(Availability)、设备的性能利用率(Performance)和生产质量利用率(Quality)。
通过计算这些指标的乘积,可以得到设备的总体效率。
设备的可利用率(Availability)指的是设备在规定工作时间内,真正开展生产的时间。
它可以通过以下公式计算:可利用率=(总运行时间-停机时间)/总运行时间其中,总运行时间指设备规定的工作时间,停机时间指设备因故障、更换备件、缺少原材料等原因停止生产的时间。
可利用率的值一般介于0和1之间,1表示设备在规定工作时间内完全可用。
设备的性能利用率(Performance)指的是设备在可利用时间内实际产出与设备理论产出之间的比例。
它可以通过以下公式计算:性能利用率=实际产出/(理论产出时间×理论产量)其中,实际产量指设备在可利用时间内真正完成的产量,理论产出时间指设备在可利用时间内能够完成的产出所需的时间,而理论产量则是指一台设备在规定工作时间内可以完成的所有产量。
生产质量利用率(Quality)指的是设备在可利用时间内实际合格品与实际产出之间的比例。
它可以通过以下公式计算:质量利用率=实际合格品/实际产出其中,实际合格品指设备在可利用时间内真正完成的合格产品数量,实际产出指设备在可利用时间内真正完成的产品数量。
计算出设备的可利用率、性能利用率和生产质量利用率之后,可以将它们相乘得到设备的OEE。
OEE=可利用率×性能利用率×质量利用率。
损失分析是对OEE计算结果进行细项分析,以找出对设备效率影响较大的损失原因,为进一步改进提供依据。
1.设备故障:设备发生故障导致停机时间增加,影响可利用率。
OEE介绍和计算方法

OEE(Overall Equipment Effectiveness),即设备综合效率,其本质就是设备负荷时间内实际产量与理论产量的比值。
企业在进行OEE计算时常常遇到很多迷惑的问题,如工厂停水、停电、停气、停汽使设备不能工作,等待定单、等待排产计划、等待检查、等待上一道工序造成的停机,不知如何计算。
本文引入非设备因素停机的概念,修改了OEE的算法,使计算得到的OEE更能够真实反映设备维护的实际状况,让设备完全利用的情况由完全有效生产率这个指标来反映。
本文同时介绍了在不同情况下如何分析设备损失的PM分析流程。
1、 OEE表述和计算实例OEE= 时间开动率×性能开动率×合格品率其中,时间开动率 = 开动时间/负荷时间而,负荷时间 = 日历工作时间-计划停机时间开动时间 = 负荷时间–故障停机时间–设备调整初始化时间性能开动率 = 净开动率×速度开动率而,净开动率 = 加工数量×实际加工周期/开动时间速度开动率 = 理论加工周期/实际加工周期合格品率 = 合格品数量/ 加工数量在OEE公式里,时间开动率反映了设备的时间利用情况;性能开动率反映了设备的性能发挥情况;而合格品率则反映了设备的有效工作情况。
反过来,时间开动率度量了设备的故障、调整等项停机损失,性能开动率度量了设备短暂停机、空转、速度降低等项性能损失;合格品率度量了设备加工废品损失。
OEE还有另一种表述方法,更适用于流动生产线的评估, 即OEE= 时间开动率×性能开动率×合格品率而,时间开动率 = 开动时间/计划利用时间而,计划利用时间 = 日历工作时间-计划停机时间开动时间 = 计划利用时间–非计划停机时间性能开动率 = 完成的节拍数/计划节拍数其中,计划节拍数 = 开动时间/标准节拍时间合格品率 = 合格品数量/加工数量这与前述的OEE公式实际上是同一的。
计算:停机时间 = 115+12 = 127 min计划开动时间 = 910 – 127 = 783 min时间开动率 = 783/910 = 86%计划节拍数 = 开动时间/标准节拍时间 = 783/3 = 261性能开动率 = 203/261 = 77.7%合格品率 = 一次合格品数/完成产品数 = 152/203 = 74.9%于是得到 OEE = 86% ×77.7%×74.9% = 50%2、 OEE的实质如果追究OEE的本质内涵,其实就是计算周期内用于加工的理论时间和负荷时间的百分比。
OEE定义和计算方式汇总

OEE定义和计算方式汇总OEE是全称为Overall Equipment Effectiveness,中文名字叫做设备综合效能,是一种用于测量和评估设备性能的指标。
OEE的计算方式将设备的可用时间、性能效率和质量损失三个方面综合考虑,通过对设备的日常运行数据进行统计和分析,可以得出设备整体效率的量化指标。
OEE的计算方式如下:1. 设备的可用时间(Available Time):表示设备在规定时间段内应该可用的时间。
可用时间可以通过设备日历时间减去计划的停机时间和非计划的停机时间来计算。
可用时间=设备日历时间-计划停机时间-非计划停机时间2. 设备的性能效率(Performance Efficiency):表示设备在实际生产过程中的效率水平。
性能效率可以通过实际生产数量除以所需生产数量来计算。
性能效率=实际生产数量/所需生产数量3. 设备的质量损失(Quality Loss):表示设备生产过程中产生的质量损失。
质量损失可以通过实际良品数量除以实际生产数量来计算。
质量损失=实际良品数量/实际生产数量4.OEE的计算公式:OEE=可用时间×性能效率×质量损失OEE的计算结果可以是一个百分比值,表示设备整体的效率水平。
一般来说,高于85%的OEE被视为优秀,70%到85%的OEE被视为良好,低于70%的OEE被视为需要改进。
OEE的计算方式能够帮助企业发现设备运行中的问题和瓶颈,从而针对性地进行改进和优化。
通过准确地测量和评估设备的性能,企业能够找出并解决影响生产效率的因素,如设备故障、停机时间、性能不良等,从而提高设备的产能和生产效率。
除了OEE的计算方式,还有一些常见的OEE的改进方法包括:1.关键性能指标(KPIs)的设定和监控:设定关键性能指标,如设备的平均停机时间、停机次数、故障频率等,并定期监控这些指标的变化,从而及时发现并解决问题。
2.停机时间分析:对设备的停机时间进行分析,找出停机原因和停机时间的分布情况,从而确定采取适当的措施来减少停机时间。
OEE的计算公式

OEE是一个独立的测量工具,它用来表现实际的生产能力相对于理论产能的比率。
国际上对OEE的定义为:OEE是Overall Equipment Effectiveness(全局设备效率)的缩写,它由可用率(Availability time),表现性(Performance)以及质量指数(Quality)三个关键要素组成。
OEE的计算公式(不考虑设备加工周期的差异)=?OEE= 时间开动率×性能开动率×合格品率[1],[4]其中,时间开动率 = 开动时间/负荷时间而,负荷时间 = 日历工作时间-计划停机时间开动时间 = 负荷时间–故障停机时间–设备调整初始化时间(包括更换产品规格、更换工装模具、更换刀具等活动所用时间)性能开动率 = 净开动率×速度开动率而,净开动率 = 加工数量×实际加工周期/开动时间速度开动率 = 理论加工周期/实际加工周期合格品率 = 合格品数量/ 加工数量在OEE公式里,时间开动率反映了设备的时间利用情况;性能开动率反映了设备的性能发挥情况;而合格品率则反映了设备的有效工作情况。
反过来,时间开动率度量了设备的故障、调整等项停机损失,性能开动率度量了设备短暂停机、空转、速度降低等项性能损失;合格品率度量了设备加工废品损失。
例1: 设某设备1天工作时间为8h, 班前计划停机20min, 故障停机20min, 更换产品型号设备调整40min, 产品的理论加工周期为0.5min/件, 实际加工周期为0.8min/件, 一天共加工产品400件, 有8件废品, 求这台设备的OEE。
计算:负荷时间 = 480-20 = 460 min开动时间 = 460 – 20 – 40 = 400 min时间开动率 = 400/460 = 87%速度开动率 = 0.5/0.8 = 62.5%净开动率 = 400×0.8/400 = 80%性能开动率 = 62.5%×80% = 50%合格品率 = (400-8)/400 = 98%于是得到 OEE = 87%×50%×98% = 42.6%。
综合设备效率OEE

为什么引进OEE
采用OEE指标的优点:
1、能使设备的技术管理与经济管理结合起来,可直
接真实地反映企业的技术经济效益。综合效率的高低能引
起领导重视,从而使各级员工建立“设备服务于生产”和“生产 靠设备”的观念;
2、影响综合效率的因素会涉及到设备的设计、制
造、检修、使用、质检、生产组织等各环节,体现了系统
从时间角度讲,OEE计算的是合格品的净生产时间(价 值开动时间)占总可用生产时间(负荷时间)的比例,其本
质就是实际合格产量与负荷时间内理论产量的比值。
为什么引进OEE
OEE由来和变迁
日本企业最早把提高设备综合效率作为TPM管理的主要目标
贯标的质量体系也把OEE作为持续改进的有效技术措施之一
在计算公式中,由时间开动率、性能开动率和合格品率来反映影响OEE
教育、训练:公司认定的企业内、外教育和训练必须参加而引 起的设备停机时间(例:外部教育、内部教育、预备役、民兵训练 等);
如何计算OEE
以下情况应归类于休止时间
停电(停水):电力供给(停水)中断引起的设备不能开 动的时间;
原材料供应:生产过程中由于原材料的品质、供应等 问题引起的生产不能持续进行导致设备停止的时间(管理 损失)。
1、设备利用率:(计算TEEP时用)
在整个日历时间中去除休止时间后的可利用时间所占的比例。
设备利用率=
日历时间-休止时间
日历时间
×100% =
负荷时间
日历时间 ×100%
总日历时间
计划停机时间(年修、定修、节假日) 非设备因素停机时间(停电、待料)
休止时间
负荷时间(总的可用生产时间)
如何计算OEE
如何计算OEE
OEE计算及损失分析

LOSS
12 . 速度损失 12.1 速度减慢 12.2 空转和短暂停机
质量合格率
定 义
良品在实际产出中的占比
公 实际产出 –不良品数量
式
实际产出
LOSS
14 . 质量损失 14.1 不良品
OEE 结构图解释
1. 日历时间
日 历 时 间
间法 定 非 工
作
时
1.
2.
日历上理论的天数时间. •每周168 小时 (24*7) •每年8,760 小时( 24*365 )
• 是指从一种产品至另一种产品 换产导致的停机损失
• 包括:
首次清洁消毒 再次清洁消毒 产品批次转换调整
备注: 1. 产品转换是指不同产品之间的转换,清洁消毒的停机
损失,停机代码记为08 2. 同样的产品隔了一段时间重新开订单的清洁消毒的停
机损失,停机代码记为11
9. 计划停机损失
生
清
(闰年为8,784 小时)
2. 法定非工作时间
日 历 时 间
间法 定 非 工
作
时
1.
2.
•因政府法规规定不允许 工作的时间
•包括:
法定假日 周未
3. 法定工作时间
法 定 工 作 时
间非 负 荷 时
负 荷 时 间
用 餐
间
•法定可用于生产的时间: • 法定工作时间 = 日历时 间 –法定非工作时间
OEE 计算及损失分析
内容
OEE 结构图 生产线利用率的定义 OEE 的定义 OEE 结构图解释 OEE 的计算 OEE 的损失 OEE 的图表 案例
OEE 结构图
生产线利用率
日 间法
OEE和TEEP损失分析

OEE和TEEP损失分析OEE(Overall Equipment Efficiency)是一个用来评估机器设备综合效能的关键指标,它考虑了设备的开动率、性能效率和质量率。
OEE的计算公式为 OEE = 开动率× 性能效率× 质量率。
OEE为企业提供了评估设备有效利用程度的直观指标。
然而,OEE只是一个评估设备效率的综合指标,它无法直接识别设备效率低下的原因。
为了进一步识别设备效率低下的原因,可以使用TEEP(Total Effective Equipment Performance)损失分析。
TEEP是一个用来评估设备综合效能损失的指标。
它考虑了设备的可用率、性能效率和质量率,类似于OEE。
但是,TEEP还额外考虑了设备的生产计划干扰因素,即设备由于计划时间外的停机导致的产能损失。
TEEP的计算公式为 TEEP = 可用率× 性能效率× 质量率× 计划率。
使用TEEP损失分析,可以更好地识别设备效率低下的根本原因,以便采取相应的措施进行改进。
通过分析TEEP的组成部分,可以识别出具体的损失类型,比如设备故障导致的停机损失、设备速度降低导致的性能损失、设备产品不合格导致的质量损失等。
这样,管理者可以有针对性地采取措施,针对不同的损失类型进行改进,以提高设备的综合效能。
TEEP还可以帮助企业评估设备修复和保养计划的优先级。
通过分析TEEP的损失类型,可以确定哪些部分的改进会对综合效能产生最大的影响。
比如,如果设备故障导致的停机损失占总损失的很大比例,那么就应优先考虑设备维护计划的改进,以减少设备故障次数和停机时间。
如果设备性能损失较大,就需要优化设备的调整和校准过程,以提高设备的性能效率。
除了以上好处,使用TEEP损失分析还可以帮助企业实施持续改进的文化。
通过识别设备效率低下的根本原因,然后采取相应的改进措施,可以不断提高设备的效率和绩效。
这种持续改进的文化能够增强企业的竞争力,提高生产效率和质量水平,最终增加了企业的盈利能力。
OEE与16大损失

OEE的定义
Overall Equipment Effectiveness —— 全局设备效率 或者叫做设备综合利用率。 OEE是衡量一个企业设备运转,操作,产品质量的一 个重要指标。 分成三个因素考核: 1. 设备的可用性(可靠性); 2. 操作设备的表现; 3. 产品的质量; OEE = 设备可用性 X 操作设备的表现 X 产品的质量
Minor Stoppages (<10´ ) Should be calculated automatically Meals break Unexpected lack of operators Lack of material at the line Lack of product from the process area Quality problem with product Quality problem with Packaging Cleaning routine Unexpected Sanitisation Machine Adjustment
OEE每一个因素影响的时间类型
Total Time
Shutdown Losses Downtime Losses
Loading Time
Operating Time Net Operating Time Value Operating Time
Defects Losses Performance Losses
OEE的定义
负载时间—停机时间 设备的可靠性 = ———————————— X100 负载时间
标准循环时间 X 产品数量(包括良品,不良品)
操作设备的表现= ———————————— X100 操作时间 产品数量—不良品数量 = ———————————— X100 产品数量
影响OEE的六大损失

•机械手问题(ROBOT ERROR)及注塑装置瞬间停止:200次 •目标节拍时间:45秒
装置产业的OEE计算
• 设备综合效率 = 时间开动率 × 装置完好率 × 良品率 • 装置产业如石油、化工等,一般配置备用设备,在实际生产中不会造成明 显的速度损失,故引用装置完好率代替性能开动率。 • 装置完好率也可采用下式计算:
装置完好率=装置密封完好率 x 装置动设备完好率 x 仪器仪表完好率
1. 停工和故障的损失 设备失效需要执行维护操作。其原因有:
–机器过载 –螺钉和螺帽松开 –过渡磨损 –缺少润滑油 –污染物
4. 降低速度的损失 设备在低于其标准设计速度运行导致的 损失。其原因有:
–机器磨损 –人为干扰 –工具磨损 –机器过载
2. 换装和调试的损失 从一种产品到另一种产品换产的时间损 失,或运行时对设置的改动。其原因有:
–移交工具 –寻找工具 –安装新工具 –调节新设置
5. 生产次品的损失 由于报废、返工或管理次品所导致的时 间损失。其原因有:
–人工错误 –劣质材料 –工具破损 –软件程序缺陷
3. 空转和瞬间停机的损失 由于小问题引起的短暂中断。其原因有:
–零件卡在滑道里 –清除碎屑 –感应器不工作 –软件程序出错
6. 启动稳定的损失 设备从启动到正常工作所需要的时间。 其原因有:
–设备要平缓加速到标准速度 –烤箱需升温到设定温度 –去除多余的材料 –处理相关原料的短缺
3.设备综合效率的计算
设 备 6大损失 0-1 计 划 停 机 计 划 损 失 时间稼动率 = 0-2 教育、 早会 ( 例) ① 停工、故障 ② 换装、调整 ③ 空转、瞬停 ④ 速 度 降低 性能稼动率 = (例) 理论节拍时间 × 生产数量 ×100 稼动时间 0.5分/个× 400个 × 100 = 50% 400分 加工数量–不良数量 ×100 加工数量 400个– 8个 ×100 = 98% 400个 设备综合效率的计算公式 负荷时间-停止时间 ×100 负荷时间 460分 – 60分× 100 =87% 460分
OEE介绍和计算方法

OEE(Overall Equipment Effectiveness),即设备综合效率,其本质就是设备负荷时间内实际产量与理论产量的比值。
企业在进行OEE计算时常常遇到很多迷惑的问题,如工厂停水、停电、停气、停汽使设备不能工作,等待定单、等待排产计划、等待检查、等待上一道工序造成的停机,不知如何计算。
本文引入非设备因素停机的概念,修改了OEE的算法,使计算得到的OEE更能够真实反映设备维护的实际状况,让设备完全利用的情况由完全有效生产率这个指标来反映。
本文同时介绍了在不同情况下如何分析设备损失的PM分析流程。
1、 OEE表述和计算实例OEE= 时间开动率×性能开动率×合格品率其中,时间开动率 = 开动时间/负荷时间而,负荷时间 = 日历工作时间-计划停机时间开动时间 = 负荷时间–故障停机时间–设备调整初始化时间性能开动率 = 净开动率×速度开动率而,净开动率 = 加工数量×实际加工周期/开动时间速度开动率 = 理论加工周期/实际加工周期合格品率 = 合格品数量/ 加工数量在OEE公式里,时间开动率反映了设备的时间利用情况;性能开动率反映了设备的性能发挥情况;而合格品率则反映了设备的有效工作情况。
反过来,时间开动率度量了设备的故障、调整等项停机损失,性能开动率度量了设备短暂停机、空转、速度降低等项性能损失;合格品率度量了设备加工废品损失。
OEE还有另一种表述方法,更适用于流动生产线的评估, 即OEE= 时间开动率×性能开动率×合格品率而,时间开动率 = 开动时间/计划利用时间而,计划利用时间 = 日历工作时间-计划停机时间开动时间 = 计划利用时间–非计划停机时间性能开动率 = 完成的节拍数/计划节拍数其中,计划节拍数 = 开动时间/标准节拍时间合格品率 = 合格品数量/加工数量这与前述的OEE公式实际上是同一的。
计算:停机时间 = 115+12 = 127 min计划开动时间 = 910 – 127 = 783 min时间开动率 = 783/910 = 86%计划节拍数 = 开动时间/标准节拍时间 = 783/3 = 261性能开动率 = 203/261 = 77.7%合格品率 = 一次合格品数/完成产品数 = 152/203 = 74.9%于是得到 OEE = 86% ×77.7%×74.9% = 50%2、 OEE的实质如果追究OEE的本质内涵,其实就是计算周期内用于加工的理论时间和负荷时间的百分比。
- 1、下载文档前请自行甄别文档内容的完整性,平台不提供额外的编辑、内容补充、找答案等附加服务。
- 2、"仅部分预览"的文档,不可在线预览部分如存在完整性等问题,可反馈申请退款(可完整预览的文档不适用该条件!)。
- 3、如文档侵犯您的权益,请联系客服反馈,我们会尽快为您处理(人工客服工作时间:9:00-18:30)。
计算工作中心30666的OEE
Production Work WO Shift Line Date Center Number 2015.9.1 2 BF1 30666 48919 2015.9.2 3 BF1 30666 49314 Item Number CXV4250B 103981CH4 Output (EA) 20,561 28,333 Defect (EA) 150 200 Good UPM Output 20,411 70 28,133 75 Total time(H) 7.2 8.0 Dining time(H) 0.7 0.7 Down time(H) 1.0 0.6 C&S time(H) 0.0 0.0 Run time (H) 5.50 6.67
10.
11.
备注:
1. 产品转换是指不同产品之间的转换,清洁消毒的停机 损失,停机代码记为08 2. 同样的产品隔了一段时间重新开订单的清洁消毒的停 机损失,停机代码记为11
9. 计划停机损失
• 包括:
生 产 时 间
清 洁 消 毒 损 失 计 划 停 机 损 失 非 计 划 停 机 损 失 运 行 时 间
非 计 划 停 机 损 失
运 行 时 间
物料原因导致停机 延迟原因导致停机
–设备仪器或水/电/气的故障导致的产线停机 –内部原因的水/电/气故障导致的产线停机 –设备调整
–缺原材料,包材或其他间接物料 –物料瑕疵造成的停线 –因前工序延迟造成的等半成品,仓库发料延迟, QA放行延迟,班车迟到 –等水 –用餐延迟
清 洁 消 毒 损 失
计 划 停 机 损 失
举例
某产线计划每班生产8小时 (480分钟)。其中计划用餐时间 为40分钟,设备故障停机为60分钟
7.
8.
9.
10.
11.
生产时间 = 480分钟 − 40分钟 = 440分钟 运行时间 = 440分钟 – 0分钟首次清洁消毒时间 – 60分钟 = 380 分钟
OEE计算及损失分析
Prepared by IE Team Nov-26-2015
内容
OEE结构图 生产线利用率的定义 OEE的定义 OEE结构图解释 OEE的计算 OEE的损失 OEE的图表 案例
OEE结构图
生产线利用率
设备综合效率=价值运行时间/生产时间
日 历 时 间 法 定 非 工 作 时 间 法 定 工 作 时 间
• • • • • • • • • •
负荷时间 = 8时 = 480分 生产时间 = 8 – 0.7 = 7.3时 = 438分 运行时间 = 6.67时 = 400.2分 时间稼动率 = 400.2/438 = 91.4% 实际产出 = 18,034 UPM = 50 性能稼动率 = 18,034/(400.2*50) = 90.1% 合格品数量 = 18,034 – 200 = 17,834 EA 质量合格率 = 17,834/18,034 = 98.9% OEE = 91.4%X90.1%X98.9% = 81.4%
14. 质量损失 14.1 不良品
OEE结构图解释
1. 日历时间
日 历 时 间
法 定 非 工 作 时 间
日历上理论的天数时间. •每周168小时 (24*7) •每年8,760小时(24*365)
(闰年为8,784小时)
1.
2.
2. 法定非工作时间
• 因政府法规规定不允许 工作的时间
• 包括:
负荷时间 = 5*8 − 1*8(停工) = 32小时
3. 4.
5. 6.
6. 用餐
• 非纽崔莱用餐时间= 40分钟
法 定 工 作 时 间 非 负 荷 时 间 负 荷 时 间
用 餐
• 纽崔莱用餐时间= 50分钟 • 用餐超过40分钟(非纽崔莱)或 50分钟(纽崔莱)的时间为非计 划停机时间
3.
4.
非 负 荷 时 间
负 荷 时 间
用 餐
生 产 时 间
清 洁 消 毒 损 失
计 划 停 机 损 失
非 计 划 停 机 损 失
运 行 时 间
速 度 损 失
有 效 运 行 时 间
质 量 损 失
价 值 运 行 时 间 15.
1.
2.
3.
4.
5.
6.
7.
8.
9.
10.
11.
12.
13.
14.
生产线利用率的定义
非 负 荷 时 间 负 荷 时 间
法 定 工 作 时 间
没生产需求
用 餐
主要的设备维护保养或清洁
–产能过剩的停工时间或没生产需求的停工时间 –新设备进行IQ/OQ/PQ或设备升级改造的停工时间 –厂房建筑施工 –每天,每周,或每月的计划维护保养或清洁卫生 –与生产计划不相关的活动
3.
4.
5.
法定假日 周未
日 历 时 间
法 定 非 工 作 时 间
1.
2.
3. 法定工作时间
法 定 工 作 时 间
非 负 荷 时 间
负 荷 时 间
用 餐
• 法定可用于生产的时间: • 法定工作时间 = 日历时 间 – 法定非工作时间
3.
4.
5.
6.
4. 非负荷时间
• 没生产安排的空闲时间或没生产需求的 相关活动的时间 • 包括:
5.
6.
7. 生产时间
• 是指计划排产后可用于生产的时间
生 产 时 间 清 洁 消 毒 损 失 计 划 停 机 损 失
• 生产时间 = 负荷时间 – 用餐时间
非 计 划 停 机 损 失 运 行 时 间
举例
某产线计划每班生产8小时 (480分钟).其中计划用餐 时间为40分钟
7.
8.
9.
10.
11.
12. 速度损失
• 是指设备以低于标准UPM运行导 致的时间损失 • 包括:
质 量 损 失 价 值 运 行 时 间 15.
速 度 损 失
有 效 运 行 时 间
空转和小停止
–速度减慢
–为1分钟以下的停机时间(ATS,WTS以及滤芯包 装线 2分钟以下)
12.
13.
14.
–设备实际运行速度低于标准速度导致的时间损失 –产前设备启动,产后设备停止
6.
非售卖产品的试产及返工(例如: R&D 试产) 管理停止
–行政管理活动(例如: 消防演习) –由管理层决定的暂停生产(例如:盘点) –外部原因造成的停水、停电
5. 负荷时间
• 负荷时间 =运行时间+停机时 间+用餐时间
负 荷 时 间 用 餐
法 定 工 作 时 间
非 负 荷 时 间
例如
某产线计划未来一周开线生产5天,由于消防演习的需求停工1 天。(每天8小时工作制)
生产准备
– 退仓,5S,会议,交接班,清场,卫生 – 工艺要求的准备工作 –换标签,换缸,更换辅助物料(油墨,色带) – 在生产时间内的计划维护保养
轮岗 培训
11.
7.
8.
9.
10.
10. 非计划停机损失
• 是指1分钟以上的停机时间:
设备原因导致停机
生 产 时 间 清 洁 消 毒 损 失 计 划 停 机 损 失
由于不良品导致的时间损失
12.
13.
14.
备注:质量损失不包括在线返工后的成品 ! (HT除外)
15. 价值运行时间
速 度 损 失
有 效 运 行 时 间
质 量 损 失
价 值 运 行 时 间
• 是指以标准UPM生产出零缺 陷产品的运行时间
12.
13.
14.
15.
OEE的计算
• 单个产品的计算公式
12. 速度损失
• 标准UPM:是指设备在理想状态下每分钟的产 出,通常选取以下3者最合理的值:
• 设备PQ的UPM • 设备达到并可维持的最好UPM • 依据类似设备经验的估计值(如业界标准)
备注:
1. UPM由IE小组进行更新及维护。
12. 速度损失
标准速度
速度减慢
启动
空转,小停止
时间 停止
生产线利用率:用于衡量一条产线的有效利用时间。
负荷时间 法定工作时间(24*249)
生产线利用率 =
• 负荷时间= 运行时间+停机时间+用餐时间 • 法定工作时间 = 24小时/天 * 249天/年 = 5,976 小时/年
OEE的定义
OEE(设备综合效率) 定义 公式 时间稼运率 定 义 公 式 运行时间在生产时间中的 占比 11. 运行时间 7. 生产时间 用来表现实际的生产能力相对于理论产能的比率 时间稼动率×性能稼动率×质量合格率 性能稼动率 质量合格率
• 工单48919:合格品数量=20561-150=20411,生产时间=7.2-0.7=6.5时=390分,UPM=70 • 工单49314:合格品数量=28333-200=28133,生产时间=8.0-0.7=7.3时=438分,UPM=75
OEE = = =
运行时间 生产时间
X
实际产出/UPM 运行时间
X
实际产出 - 不良品数量 实际产出
(实际产出 - 不良品数量)/UPM 生产时间 合格品数量/UPM 生产时间
OEE的计算
• 多个产品的计算公式
OEE =
=
X X
=
OEE的计算
1. 班次OEE计算:为该班次生产的合格品数量的价值运行时间与总的生产时间的比值。 计算TF1 9月1日第3个班次的OEE
13. 有效运行时间
速 度 损 失