设计张紧轮支架零件的机械加工工艺规程及工艺设备
张紧轮支架加工工艺及夹具的设计

张紧轮支架加工工艺及夹具的设计
张紧轮支架加工工艺及夹具的设计
一、张紧轮支架
1.张紧轮支架的加工工艺
利用车床加工张紧轮支架,主要从它的尺寸及几何形状出发,以内圈背角、精加工外圈、内孔精加工等操作,确定加工工艺及其参数配置。
(1)内圈背角加工,是指张紧轮支架的内圈圆角,需要采用切削刀片切削内圈,确保切削刀片的定位准确,调节角度达到所要求的尺寸,切削完成后,用小磨床精加工圆角,以保证质量。
(2)外圈精加工,是指张紧轮支架的外圈精加工,使外圈圆弧达到所要求的精度和平滑度,需要使用车床进行切削,以保证圆弧的精度和平滑度。
(3)内孔精加工,是指在支架上加工的内孔,是用到张紧轮夹紧支架时的连接孔,需要使用钻床制作内孔,以确保内孔的精度和尺寸。
2.张紧轮支架夹具的设计
(1)夹具的结构及功能
张紧轮支架夹具的结构主要由底座、钻头架、固定板、调节支架等组成,底座用来固定夹具,钻头架用来定位刀具,固定板用来固定工件,调节支架用来调节刀具等。
(2)夹具的结构尺寸设计
夹具的结构设计要根据张紧轮支架的尺寸及加工工艺进行设计,如底座尺寸要比工件大,好方便安装,内孔尺寸要精确,以确保工件的准确定位和质量要求,刀具尺寸也要精确,以确保加工精度。
二、总结
张紧轮支架的加工工艺主要包括内圈背角加工、外圈精加工、内孔精加工等,而且,张紧轮支架夹具的结构及功能要根据张紧轮支架的尺寸及加工工艺进行设计,底座尺寸要比工件大,内孔尺寸要精确,以确保工件的准确定位和质量要求,刀具尺寸也要精确,以确保加工精度。
张紧轮支架加工工艺及夹具的设计
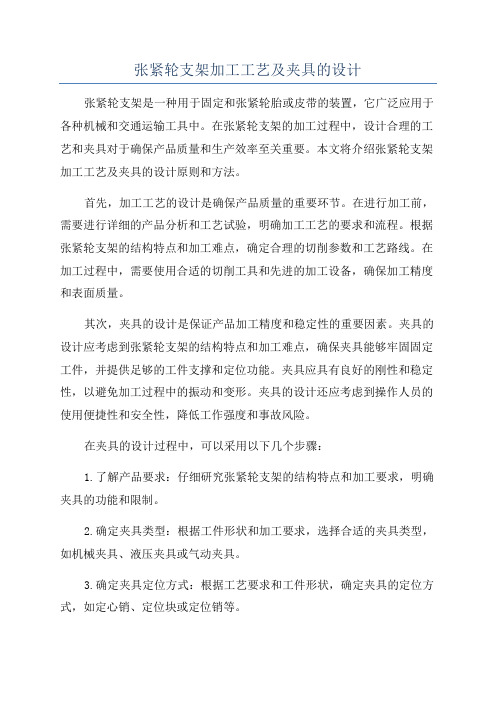
张紧轮支架加工工艺及夹具的设计张紧轮支架是一种用于固定和张紧轮胎或皮带的装置,它广泛应用于各种机械和交通运输工具中。
在张紧轮支架的加工过程中,设计合理的工艺和夹具对于确保产品质量和生产效率至关重要。
本文将介绍张紧轮支架加工工艺及夹具的设计原则和方法。
首先,加工工艺的设计是确保产品质量的重要环节。
在进行加工前,需要进行详细的产品分析和工艺试验,明确加工工艺的要求和流程。
根据张紧轮支架的结构特点和加工难点,确定合理的切削参数和工艺路线。
在加工过程中,需要使用合适的切削工具和先进的加工设备,确保加工精度和表面质量。
其次,夹具的设计是保证产品加工精度和稳定性的重要因素。
夹具的设计应考虑到张紧轮支架的结构特点和加工难点,确保夹具能够牢固固定工件,并提供足够的工件支撑和定位功能。
夹具应具有良好的刚性和稳定性,以避免加工过程中的振动和变形。
夹具的设计还应考虑到操作人员的使用便捷性和安全性,降低工作强度和事故风险。
在夹具的设计过程中,可以采用以下几个步骤:1.了解产品要求:仔细研究张紧轮支架的结构特点和加工要求,明确夹具的功能和限制。
2.确定夹具类型:根据工件形状和加工要求,选择合适的夹具类型,如机械夹具、液压夹具或气动夹具。
3.确定夹具定位方式:根据工艺要求和工件形状,确定夹具的定位方式,如定心销、定位块或定位销等。
4.设计夹具结构:根据夹具类型和定位方式,设计夹具的结构,包括夹具底座、夹具头、夹具夹持部件等。
夹具的结构应优化,以提高夹紧力和刚性。
5.验证夹具性能:设计完成后,通过模拟或实际试验,验证夹具的性能和稳定性。
如需修改,及时进行优化并重新验证。
综上所述,张紧轮支架加工工艺及夹具的设计是确保产品质量和生产效率的关键。
通过合理设计的加工工艺和夹具,能够提高产品加工精度和稳定性,降低生产成本和周期。
因此,在进行张紧轮支架加工前,应充分进行工艺分析和夹具设计,确保加工过程的顺利进行。
张紧轮支架机械加工工艺规程设计

张紧轮支架机械加工工艺规程设计1. 引言张紧轮支架是一种常用于调节带式传动装置紧张程度的重要零部件。
它通过调整张紧轮位置,控制带传动系统的紧张程度,确保带传动效果的稳定性和可靠性。
本文将详细介绍张紧轮支架的机械加工工艺规程设计。
2. 工艺流程设计2.1 产品设计图纸分析在开始机械加工工艺规程设计之前,需要对产品设计图纸进行详细的分析。
包括轮支架的尺寸、材质要求、加工精度等。
根据设计图纸,确定产品的加工工艺路线和加工工艺。
2.2 材料准备根据产品设计要求,选择合适的材料。
张紧轮支架常用的材料有铸铁、钢材等。
选择合适的材料后,进行材料清理和切割,确保材料的质量和尺寸符合要求。
2.3 加工工艺编制根据产品设计要求和材料特性,制定合适的加工工艺。
具体的加工工艺包括: -车削工艺:根据图纸尺寸,进行车削加工,包括外径、内孔等。
- 镗削工艺:根据图纸要求,进行镗削加工,包括轴孔的光滑度和尺寸精度等要求。
- 铣削工艺:根据图纸要求进行铣削加工,包括轮支架表面的平整度和形状精度等要求。
- 淬火工艺:根据材料的特性,进行适当的淬火处理,提高轮支架的硬度和耐磨性。
2.4 加工设备选择根据加工工艺要求,选择合适的加工设备。
包括车床、铣床、镗床等。
确保加工设备具备足够的精度和稳定性,能够满足产品加工要求。
2.5 制定工艺参数根据加工工艺要求和设备性能,制定合适的工艺参数。
包括车刀的进给速度、切削深度,刀具的选择和切削液的使用等。
2.6 检验和修整加工完成后,进行产品的检验和修整。
包括外观检查、尺寸测量等。
对于不合格的产品,可以进行修整,直到满足要求为止。
3. 加工工艺规程设计细节3.1 车削工艺车削工艺是对轮支架的外径和内孔进行加工。
具体工艺包括: - 选择合适的车刀,并进行预磨和调整。
- 设置车床的进给速度和材料切削速度 - 进行外径和内孔的车削加工,注意保持一定的切削量和切削速度,确保加工质量。
3.2 镗削工艺镗削工艺是对轴孔进行加工,提高其尺寸精度和光滑度。
张紧轮支架机械加工工艺规程

张紧轮支架机械加工工艺规程1. 引言张紧轮支架机械加工工艺规程是为了确保张紧轮支架在制造过程中的加工质量和工作性能符合设计要求而制定的。
本规程适用于张紧轮支架的机械加工工艺。
2. 加工设备和工具张紧轮支架的机械加工需要使用以下设备和工具: - 数控铣床 - 数控车床 - 钻床 - 磨床 - 加工夹具 - 加工刀具 - 测量工具3. 加工工艺步骤3.1 零件准备•准备轴材和板材,确保其材质和尺寸符合设计要求。
•对材料进行初步检查,去除表面的锈蚀和杂质。
3.2 零件布置•根据设计要求,确定零件的布置方式和相对位置。
•使用数字化仿真软件进行零件布置的优化和验证。
3.3 加工前准备•检查加工设备和工具的工作状态,确保其正常运转。
•安装合适的加工刀具和夹具。
3.4 加工轴材•根据设计要求,在数控车床上对轴材进行车削加工。
•根据需要,进行镗削、钻孔等进一步加工。
3.5 加工板材•使用数控铣床对板材进行平面铣削,确保平整度符合要求。
•对板材进行孔加工和切割。
3.6 焊接•对加工好的轴材和板材进行对位焊接。
•根据需要,使用气体保护焊、电弧焊等方法进行焊接。
3.7 检验和调整•对焊接后的支架进行外观和尺寸检验。
•对不合格的支架进行调整或重新加工。
3.8 表面处理•对支架进行表面处理,如喷涂、镀铬等。
3.9 组装和调试•将加工好的零件进行组装,确保其结构牢固和功能正常。
•进行必要的调试和试验,验证支架的工作性能。
4. 加工质量控制•在加工过程中,严格按照工艺规程进行操作,确保加工质量。
•定期检查加工设备和工具的工作状态,做好维护保养工作。
•对加工过程中产生的废料和废品进行分类和处理。
5. 安全措施•在机械加工过程中,佩戴必要的劳动防护用品。
•使用加工设备和工具时,注意操作规程,防止事故发生。
•严禁在未经培训的情况下操作加工设备。
6. 总结本工艺规程为张紧轮支架的机械加工提供了详细的步骤和要求,符合工艺规范和质量要求。
张紧轮支架零件的加工工艺规程设计
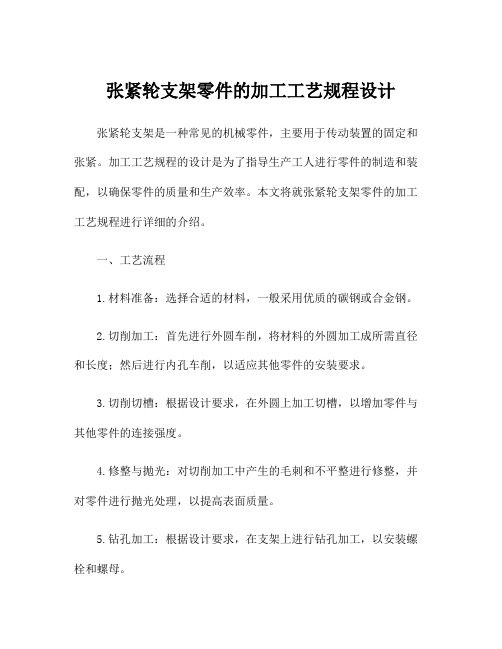
张紧轮支架零件的加工工艺规程设计张紧轮支架是一种常见的机械零件,主要用于传动装置的固定和张紧。
加工工艺规程的设计是为了指导生产工人进行零件的制造和装配,以确保零件的质量和生产效率。
本文将就张紧轮支架零件的加工工艺规程进行详细的介绍。
一、工艺流程1.材料准备:选择合适的材料,一般采用优质的碳钢或合金钢。
2.切削加工:首先进行外圆车削,将材料的外圆加工成所需直径和长度;然后进行内孔车削,以适应其他零件的安装要求。
3.切削切槽:根据设计要求,在外圆上加工切槽,以增加零件与其他零件的连接强度。
4.修整与抛光:对切削加工中产生的毛刺和不平整进行修整,并对零件进行抛光处理,以提高表面质量。
5.钻孔加工:根据设计要求,在支架上进行钻孔加工,以安装螺栓和螺母。
6.热处理:将零件进行热处理,以提高零件的硬度和强度,并消除内部应力。
二、加工工艺要点1.材料选择:根据设计要求选择合适的材料,碳钢或合金钢具有较好的机械性能和可加工性。
2.设计合理性:在零件设计中,应注重减少加工工序和次数,提高加工效率。
3.加工精度控制:切削加工时,应控制加工精度和尺寸公差,以确保零件的装配要求和功能要求。
4.螺纹加工:在支架上进行螺纹加工时,应选择合适的螺纹规格,严格控制螺纹的牙型和公差。
5.表面处理:对零件表面进行抛光处理,以提高表面质量和耐腐蚀性。
6.热处理控制:根据材料的特性和设计要求,控制热处理时间、温度和冷却速度,以获取所需的硬度和强度。
三、加工设备和工具1. CNC车床:用于外圆和内孔的车削加工,具有精度高、加工效率高的优点。
2.切削刀具:用于切削加工,根据不同的材料选取合适的刀具材料和刀具形状。
3.钻床:用于钻孔加工,需选取合适的钻头和加工速度。
4.抛光机:用于对零件表面进行抛光处理,提高表面质量。
5.热处理设备:用于对零件进行热处理,如淬火、回火等。
四、安全措施1.操作人员需穿戴好防护服、防护眼镜等个人防护用品。
2.加工设备的使用和维护需按照相关规定进行,确保设备的安全性和可靠性。
机械制造张紧轮支架机械加工工艺过程卡工序卡

机械制造张紧轮支架机械加工工艺过程卡工序卡一、设计:1.根据客户需求和产品要求,确定张紧轮支架的结构形式和尺寸。
2.设计支架的立柱、底座、焊接接头等部分的结构和尺寸,并进行强度校核。
3.绘制工程图纸,标注尺寸、标准、加工要求等信息。
二、材料准备:1.根据设计要求,选择适合的材料,一般为碳钢。
2.从供应商处采购所需的材料,并进行材料质量检测和入库登记。
3.根据工程图纸,将材料进行切割,得到所需的坯料,并对坯料进行喷砂处理。
三、车削加工:1.将坯料固定在车床工作台上,并进行粗加工,将表面整平,去除毛刺等不需要的部分。
2.根据工程图纸要求,使用车削刀具进行细加工,切割出所需的外形和孔位。
3.完成车削加工后,对轴向和直径进行测量和校正,确保加工尺寸的精度。
四、铣削加工:1.将加工好的张紧轮支架放置在铣床工作台上,并进行粗加工,将表面整平,去除毛刺等不需要的部分。
2.根据工程图纸要求,使用铣削刀具进行细加工,切割出所需的槽口和孔位。
3.完成铣削加工后,对表面质量进行检查,保证加工面光洁度和尺寸的精度。
五、钻孔加工:1.根据工程图纸要求,将支架固定在钻床工作台上,并确定孔位位置。
2.使用钻头进行孔位打孔,根据要求的孔径和深度进行逐步钻孔。
3.完成钻孔加工后,对孔径的尺寸和位置进行测量,确保符合工程图纸的要求。
六、磨削:1.将加工完的张紧轮支架放置在磨床上,并使用砂轮进行粗磨,去除残余的毛刺和瑕疵。
2.使用砂布进行细磨,对支架的外表面进行抛光,提高其光洁度和外观质量。
3.完成磨削工序后,对支架的表面进行检查和测量,确保表面质量符合要求。
以上是机械制造张紧轮支架的工序卡工序的主要内容,通过这些工序的顺序进行加工,可以制造出符合要求的张紧轮支架产品。
整个过程需要合理安排工时、严格遵循操作规范,确保产品质量和加工效率。
课程设计---KCSJ-05 支架零件的机械加工工艺规程及典型夹具

机械制造技术课程设计院系机械与材料工程学院专业机械设计制造及其自动化姓名年级指导教师二零一零年六月机械制造技术课程设计任务书机械与材料工程学院机械设计制造及其自动化专业2008年级学生姓名:题目:设计KCSJ-05 支架零件的机械加工工艺规程及典型夹具(大批量生产)主要内容:1.绘制零件图及零件的毛坯图(A3)2.设计零件的机械加工工艺规程,并填写:(1)整个零件的机械加工工艺过程卡(A4);(2)所设计夹具对应工序的机械加工工序卡(A4)。
3.设计某工序的夹具一套,绘出总装图(A2)。
4.编写设计说明书。
指导教师:班级:学生:2010年6月17 日目录第1章零件分析 (1)1.1零件的作用 (1)1.2零件的工艺性分析和零件图的审查 (1)第2章选择毛坯 (1)2.1确定毛坯的成形方法 (1)2.2铸件结构工艺性分析 (1)2.3铸造工艺方案的确定 (2)2.4铸造工艺参数的确定 (2)第3章工艺规程设计 (2)3.1定位基准的选择 (2)3.2制订工艺路线 (2)3.3选择加工设备及刀、夹、量具 (5)3.4加工工序设计 (7)3.5填写加工工艺卡片 (13)第4章夹具设计 (14)4.1确定设计方案................................. 错误!未定义书签。
4.2机械加工工序卡 (16)4.3绘出总装图参考文献 (14)序言机械制造工艺学课程设计是在学完了机械制造工艺学(含机床夹具设计)和大部分专业课,并进行了生产实习的基础上进行的一个教学环节。
这次设计使我们能够综合运用机械制造工艺学中的基本理论,并结合生产实习中学到的实践知识,独立分析和解决工艺问题,初步具备了设计一个中等复杂程度零件(转速器盘)的工艺规程的能力和运用夹具设计手册与图表等技术资料及编写技术文件等基本技能的一次时间机会,为今后的毕业设计及外来从事的工作打下良好的基础。
由于能力所限,经验不足,设计中还有许多不足之处,希望各位老师多加指导。
张紧轮支架设计说明书

机械制造工艺课程设计报告说明书课题:张紧轮支架班级:姓名:指导教师:课题:张紧轮支架的加工工艺规程设计设计内容:1、张紧轮支架的零件图 1 张2、张紧轮支架毛坯图 1 张3、机械加工工艺过程卡1份4、机械加工工序卡 1 份5、课程设计说明书 1 份年月日目录一、课题介绍31。
1任务目标31.2 设计要求3二、零件结构工艺性分析3三、毛坯的选择3四、机械加工工艺规程设计44。
1加工方法的选择44。
2 拟定工艺过程4五、机床的选择45. 1 机床的选择45。
2量具的选择5六、机械加工工序设计56。
1 确定加工余量和工序尺寸56.2 确定切削用量和时间定额6七、课程设计总结11参考文献12一、课题介绍1.1 任务目标零件材料: HT200技术要求:1、未注铸造圆角R5—R102、调质HBS1187—220零件数据:(见零件图)1。
2 设计要求要求编制一个张紧轮支架零件的机械加工工艺过程,并编写设计说明书.具体内容如下:1、分析零件加工性,选择毛胚的制造方法,指定毛胚的技术要求。
2、拟定张紧轮支架的机械加工工艺过程,填写工艺卡。
3、确定各工序所用的加工设备.4、计算加工余量,时间定额,填写工序卡。
5、提交设计说明书。
二、零件结构工艺性分析该张紧轮支架属于支撑零件,结构较简单。
其加工精度,粗糙度已给出其上下两端面精度要求较高,其他表面直接采用铸造就能满足其表面粗糙度要求。
三、毛坯的选择该撑头螺杆形状不复杂,尺寸较小,不属于精密零件或制造要求高的零件。
因此由表2—6(《机械制造技术基础课程设计》)采用HT200即可。
毛胚可直接通过铸造得出。
四、机械加工工艺规程设计4。
1加工方法的选择该零件需要加工的部分主要为:上下两端面,精度要求较高为Ra6.3.按《现代制造工艺基础》表1—4可知对应的经济加工精度部分取为IT8,查表1—4知需粗车、半精车。
1.两中间端面表面粗糙度要求为Ra12.5。
查表1—4.公差取IT10,需粗铣,半精铣.2.右端面的调紧孔已经直接在毛胚中铸造出来,表面粗糙度要求为Ra25。
张紧轮支架的机械加工工艺规程

《机械制造工艺学课程设计》课程设计说明书题目:张紧轮支架的机械加工工艺规程二级学院:机电工程学院年级专业: 15机械制造与自动化学号: **********学生姓名:**指导教师:***教师职称:讲师目录序言 (6)第一章零件的工艺分析 (7)1.1零件的作用 (7)1.2零件的工艺分析 (7)第二章零件的生产类型 (8)2.1生产纲领 (8)2.2生产类型 (8)第三章毛坯的选择与毛坯简图的绘制 (9)3.1确定毛坯类型及其制造方法 (9)3.2估算毛坯的机械加工余量 (9)第四章定位基准选择 (10)4.1选择精基准 (10)4.2选择粗基准 (10)第五章制定机械加工工艺路线 (11)5.1选择加工方法 (11)5.2加工工艺路线 (11)第六章加工余量及工序尺寸的确定 (13)6.1确定粗加工张紧轮支架上端面的加工余量及工序尺寸 (13)6.2确定支架底面的加工余量及工序尺寸 (14)6.3确定精加工支架上端面的加工余量及工序尺寸 (16)6.4确定支架右侧面的加工余量及工序尺寸 (18)6.5确定支架右侧面Φ18孔的加工余量及工序尺寸 (19)6.6确定支架下端面的加工余量及工序尺寸 (20)6.7确定支架小侧面的加工余量及工序尺寸 (23)6.8确定支架2*Φ13孔的加工余量及工序尺寸 (23)第七章切削用量和时间定额的确定 (26)第八章课程设计总结 (29)参考文献 (31)新余学院机械制造工艺学课程设计任务书指导老师黄小英学生姓名易斌专业机械制造与自动化课程设计题目张紧轮支架机械加工工艺规程制订完成日期:2017年6月15日课程设计内容如图所示张紧轮支架简图,毛坯材料HT200灰铸铁中批量生产,采用通用机床进行加工。
试完成张紧轮支架机械加工工艺规程制订。
设计要求设计要求:1、设计者必须发挥独立思考能力,禁止抄袭他人成果,不允许雷同,凡找他人代做,一经核实,取消答辩资格。
积极主动与指导教师交流,每一进展阶段至少与指导教师交流一次。
工序卡-张紧轮支架-机械加工工艺
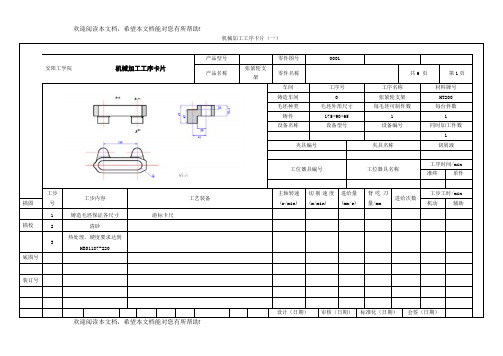
机械加工工序卡片(一)安阳工学院机械加工工序卡片产品型号零件图号0001产品名称张紧轮支架零件名称共6 页第1页车间工序号工序名称材料牌号铸造车间0 张紧轮支架HT200毛坯种类毛坯外形尺寸每毛坯可制件数每台件数铸件175*90*65 1 1设备名称设备型号设备编号同时加工件数1夹具编号夹具名称切屑液工位器具编号工位器具名称工序时间/min准终单件工步号工步内容工艺装备主轴转速(r/min)切削速度(m/min)进给量(mm/r)背吃刀量/mm进给次数工步工时/min描图机动辅助1 铸造毛坯保证各尺寸游标卡尺描校 2 清砂3热处理,硬度要求达到HBS1187-220底图号装订号设计(日期)审核(日期)标准化(日期)会签(日期)标记处数更改文件号签字日期标记处数更改文件号签字日期机械加工工序卡片(二)安阳工学院机械加工工序卡片产品型号零件图号0001产品名称张紧轮支架零件名称共6 页第2 页车间工序号工序名称材料牌号10 张紧轮支架HT200毛坯种类毛坯外形尺寸每毛坯可制件数每台件数铸件175*90*65 1 1设备名称设备型号设备编号同时加工件数铣床 1夹具编号夹具名称切屑液工位器具编号工位器具名称工序时间/min准终单件工步号工步内容工艺装备主轴转速(r/min)切削速度(m/min)进给量(mm/r)背吃刀量/mm进给次数工步工时/min描图机动辅助1 粗铣支架底面立式铣床,铣床专用夹具,高速钢套式面铣刀,游标卡尺144 37.68 0.08 0.8 5 1.6 0.236 描校2 粗洗支架上表面立式铣床,铣床专用夹具,高速钢套式面铣刀,游标卡尺144 37.68 0.08 0.8 5 1.6 0.2363 粗洗上表面台阶立式铣床,铣床专用夹具,高速钢套式面铣刀,游标卡尺144 37.68 0.08 0.85 0.62 0.092 底图号 4 半精铣支架底面5 半精铣支架上表面装订号 6 半精铣表面台阶欢迎阅读本文档,希望本文档能对您有所帮助!设计(日期)审核(日期)标准化(日期)会签(日期)标记处数更改文件号签字日期标记处数更改文件号签字日期机械加工工序卡片(三)安阳工学院机械加工工序卡片产品型号零件图号产品名称张紧轮支架零件名称共6 页第3 页、车间工序号工序名称材料牌号机加工车间15 张紧轮支架HT200毛坯种类毛坯外形尺寸每毛坯可制件数每台件数铸件175*90*65 1 1设备名称设备型号设备编号同时加工件数铣床 1夹具编号夹具名称切屑液三爪自定心卡盘工位器具编号工位器具名称工序时间/min 准终单件5.475工步号工步内容工艺装备主轴转速(r/min)切削速度(m/min)进给量(mm/r)背吃刀量/mm进给次数工步工时/min描图机动辅助1 粗铣四周表面立式铣床,铣床专用夹具,高速钢套式面铣刀,游标卡尺,分度圆卡盘144 37.68 0.08 0.8 5 4.6 0.696描校 2 半精铣四周表面3 划线,找正立式铣床,铣床专用夹具,高速钢套式面铣刀,游标卡尺,分度圆卡盘底图号 4 铣圆角144 37.68 0.08 0.8 5欢迎阅读本文档,希望本文档能对您有所帮助!装订号设计(日期)审核(日期)标准化(日期)会签(日期)标记处数更改文件号签字日期标记处数更改文件号签字日期机械加工工序卡片(四)安阳工学院机械加工工序卡片产品型号零件图号产品名称张紧轮支架零件名称共 6 页第4 页车间工序号工序名称材料牌号机加工车间20 张紧轮支架HT200毛坯种类毛坯外形尺寸每毛坯可制件数每台件数铸件175*90*65 1 1设备名称设备型号设备编号同时加工件数铣床 1夹具编号夹具名称切屑液三爪自定心卡盘工位器具编号工位器具名称工序时间/min准终单件3.82工步号工步内容工艺装备主轴转速(r/min)切削速度(m/min)进给量(mm/r)背吃刀量/mm进给次数工步工时/min描图机动辅助1 粗铣马蹄形孔立式铣床,铣床专用夹具,高速钢套式面铣刀,游标卡尺144 37.68 0.08 0.8 5 2.7 1.041 描校2 半精铣马蹄形孔立式铣床,铣床专用夹具,高速钢套式面铣刀,游标卡尺欢迎阅读本文档,希望本文档能对您有所帮助!底图号装订号设计(日期)审核(日期)标准化(日期)会签(日期)标记处数更改文件号签字日期标记处数更改文件号签字日期机械加工工序卡片(五)安阳工学院机械加工工序卡片产品型号零件图号产品名称张紧轮支架零件名称共 6 页第5 页车间工序号工序名称材料牌号机加工车间25 张紧轮支架HT200毛坯种类毛坯外形尺寸每毛坯可制件数每台件数铸件175*90*65 1 1设备名称设备型号设备编号同时加工件数钻床 1夹具编号夹具名称切屑液工位器具编号工位器具名称工序时间/min准终单件10.43工步号工步内容工艺装备主轴转速(r/min)切削速度(m/min)进给量(mm/r)背吃刀量/mm进给次数工步工时/min描图机动辅助欢迎阅读本文档,希望本文档能对您有所帮助!1 钻直径12.8的通孔直径为12.8直柄麻钻,铰刀630 15.43 0.3 45 1 0.39 描校2 扩孔直径为12.8直柄麻钻,铰刀500 14.13 0.5 14 1 0.363 去毛刺直径为12.8直柄麻钻,铰刀底图号 4 铰孔直径为12.8直柄麻钻,铰刀500 14.13 0.5 14 1 0.275 精铰孔直径为12.8直柄麻钻,铰刀500 14.13 0.5 14 1 2.00 装订号设计(日期)审核(日期)标准化(日期)会签(日期)标记处数更改文件号签字日期标记处数更改文件号签字日期机械加工工序卡片(六)安阳工学院机械加工工序卡片产品型号零件图号产品名称张紧轮支架零件名称共6页第6 页车间工序号工序名称材料牌号30 张紧轮支架HT200毛坯种类毛坯外形尺寸每毛坯可制件数每台件数铸件175*908651 1设备名称设备型号设备编号同时加工件数钻床 1夹具编号夹具名称切屑液工位器具编号工位器具名称工序时间/min准终单件欢迎阅读本文档,希望本文档能对您有所帮助!欢迎阅读本文档,希望本文档能对您有所帮助!。
张紧轮支架的机械加工工艺规程
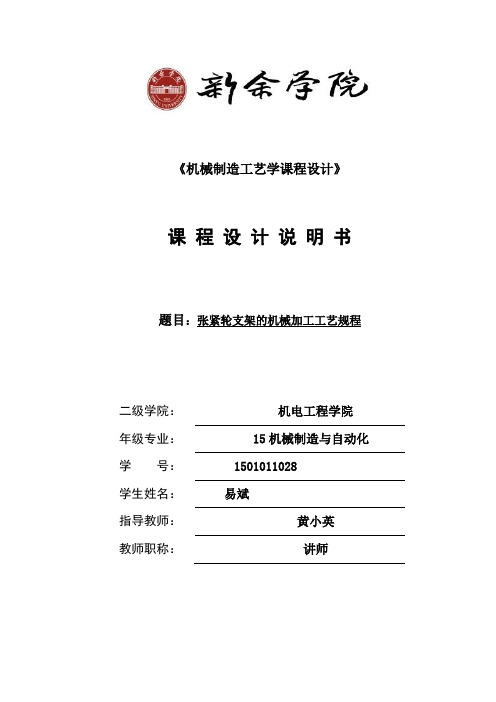
《机械制造工艺学课程设计》课程设计说明书题目:张紧轮支架的机械加工工艺规程二级学院:机电工程学院年级专业: 15机械制造与自动化学号:**********学生姓名:**指导教师:***教师职称:讲师目录序言6第一章零件的工艺分析71.1零件的作用71.2零件的工艺分析7第二章零件的生产类型72.1生产纲领72.2生产类型8第三章毛坯的选择与毛坯简图的绘制93.1确定毛坯类型及其制造方法93.2估算毛坯的机械加工余量9第四章定位基准选择94.1选择精基准94.2选择粗基准9第五章制定机械加工工艺路线105.1选择加工方法105.2加工工艺路线10第六章加工余量及工序尺寸的确定126.1确定粗加工张紧轮支架上端面的加工余量及工序尺寸126.2确定支架底面的加工余量及工序尺寸136.3确定精加工支架上端面的加工余量及工序尺寸156.4确定支架右侧面的加工余量及工序尺寸176.5确定支架右侧面Φ18孔的加工余量及工序尺寸186.6确定支架下端面的加工余量及工序尺寸196.7确定支架小侧面的加工余量及工序尺寸226.8确定支架2*Φ13孔的加工余量及工序尺寸22第七章切削用量和时间定额的确定24第八章课程设计归纳总结27参考文献28新余学院机械制造工艺学课程设计任务书指导老师黄小英学生姓名易斌专业机械制造与自动化课程设计题目张紧轮支架机械加工工艺规程制订完成日期:2017年6月15日课程设计内容如图所示张紧轮支架简图,毛坯材料HT200灰铸铁中批量生产,采用通用机床进行加工。
试完成张紧轮支架机械加工工艺规程制订。
设计要求设计要求:1、设计者必须发挥独立思考能力,禁止抄袭他人成果,不允许雷同,凡找他人代做,一经核实,取消答辩资格。
积极主动与指导教师交流,每一进展阶段至少与指导教师交流一次。
2、设计成果:(1)、设计说明书一份;(2)、机械加工工艺卡片一套;主要零件的工序卡2-3张。
设计说明书的内容应包括:(1)封面(2)目录(3)设计任务书(4)机械加工工艺规程制定的详细过程主要包括:(1)零件的工艺分析序言本次课程设计的任务是针对生产实际中的一个零件——张紧轮支架,制订其机械加工工艺规程。
张紧轮支架的机械加工工艺规程

张紧轮支架的机械加工工艺规程一、选题背景:张紧轮支架是机械加工中的一种重要零部件,是用于车辆、轮船等附着于地面上的车辆和设备中的部件,是车辆的一个重要架构部分。
张紧轮支架的机械加工过程十分重要,关系到整个车辆的稳定性和安全性。
本文将介绍张紧轮支架的机械加工工艺规程。
二、工艺流程:1、材料准备张紧轮支架的材料通常使用碳钢、合金钢、不锈钢等金属材料,实用性和耐用性较好。
为了保证零件的质量,首先要对材料进行检验并进行质检合格后的材料进行切割,加工工艺是铣削、钻孔、车削、切割等。
2、零部件加工(1) 零件的车削是主要的加工过程,它们用刀具夹紧机器,逐层移动并切削,使零件达到所需的形状和尺寸。
在车削过程中,应准确测量零件的尺寸,检查其质量,并保护车床上的零件免受损坏。
(2) 零件的铣削是将切削工具放在旋转的刀头上向工件移动,并以所需的形状和尺寸切割工件材料的一种过程。
零件铣削主要用于将工件表面切削成平面,也可用于在表面切削出特定的形状或放置并复制一个图案。
(3) 钻孔是为了在零部件上打孔,将所需的孔径和深度钻到零件上。
在钻孔的过程中,应使用正确的挖孔刀头并使用适当的冷却剂,防止零件过热并损坏刀具和工件。
3、零部件组装零件加工完毕后,需要进行组装。
组装前需检查加工零件的质量和尺寸,避免因加工误差而导致组装不良的情况出现。
在组装时,需要按照设计图纸的要求进行严格的操作,采取正确的安装方法和适当的紧固力度,以保证整个车辆的稳定性和安全性。
4、表面处理对于内部容易难以到达的凹槽和角落部位,需要使用磨光工艺将其切削到所需的形状和尺寸。
对于外壳表面,可以使用抛光、擦洗、喷砂等技术处理表面以达到预期的光滑度和外观效果。
三、工艺控制:1、加工质量控制在加工过程中,需要进行质量控制,保证零件在加工过程中的精度和尺寸的一致性。
可以使用各种测量仪器和检测设备来确保加工的准确性和零件的可靠性。
2、工具设备控制在加工过程中,需要对工具设备进行控制,保证工具设备达到最佳的使用状态。
张紧轮支架加工工艺及夹具的设计

张紧轮支架加工工艺及夹具的设计
张紧轮支架是汽车悬挂系统中的重要零部件,其主要作用是通过张紧轮胎,保证车辆行驶的稳定性和安全性。
因此,张紧轮支架的加工工艺和夹具的设计关系到整个汽车悬挂系统的质量和性能。
一般来说,张紧轮支架的加工工艺主要包括以下几个步骤:
1.工件材料的选择:一般情况下,张紧轮支架采用铝合金材料进行加工,因为铝合金具有较高的强度和韧性,同时还具有较好的耐腐蚀性和导热性能。
2.工件的切削加工:张紧轮支架需要进行精密的切削加工,以保证其尺寸和形状的精度。
一般采用数控加工中心进行加工,可以实现高精度的加工要求。
3.工件表面处理:由于张紧轮支架需要承受车辆的重量和外界的冲击力,因此需要进行表面处理,以提高其抗腐蚀性和耐磨性。
一般采用阳极氧化或电泳涂装等表面处理方法。
4.夹具的设计:夹具设计是加工工艺中的重要环节,它直接影响到工件的加工精度和效率。
夹具应该具有良好的刚性和稳定性,并能够满足不同工件的加工要求。
在以上加工工艺中,夹具的设计尤为重要。
夹具应该根据工件的形状和尺寸进行设计,并考虑到加工过程中的安全性和稳定性。
夹具的材料应该具有较高的强度和硬度,以确保加工精度和效率。
同时,夹具的结构应该简单明了,易于操作和维护。
综上所述,张紧轮支架的加工工艺和夹具的设计是汽车悬挂系统
中不可或缺的环节。
通过科学的加工工艺和夹具的设计,可以提高张紧轮支架的质量和性能,从而确保车辆行驶的安全和稳定。
专业课程设计正文张紧轮支架专业课程设计机械制造工艺学

专业课程设计正文张紧轮支架专业课程设计机械制造工艺学专业课程设计正文张紧轮支架专业课程设计机械制造工艺学机械制造工艺学课程设计设计说明书题目张紧轮支架机械加工工艺规程制订及专用夹具设计二级学院机械工程学院专业机械制造及其自动化班级 11机制本2班学号学生姓名指导教师目录第一章序言 (1)第二章零件分析 (2)1.1 任务目标 (2)1.2 设计要求 (2)1.3、零件结构工艺性分析 (2)1.4、毛坯的选择 (2)1.5、机械加工设备的选择 (3)第三章工艺规程制定 (3)3.1加工工艺过程 (3)3.2拟定工艺路线 (3)3.3加工工艺过程 (4)3.4确定各表面加工方案 (4)3.5确定定位基准 (4)3.6确定定位基准 (5)3.7张紧轮支架的偏差,加工余量,工序尺寸及毛坯尺寸的确定 (7)3.8.确定机械加工余量、毛坯尺寸和公差 (7)3.9确定毛坯尺寸 (7)3.10确定毛坯尺寸公差 (7)3.11设计毛坯图 (8)3.12 张紧轮支架的偏差计算 (8)第四章机械加工工序设计 (9)4.1确定加工余量和工序尺寸 (9)4.2确定切削用量和时间定额 (9)第五章专用夹具设计 (12)5.1机床夹具的使用 (12)5.2定位方案 (12)5.3加紧机构……………………………………………………………^125.4夹紧力分析 (13)5.5对刀装置 (13)5.6夹具体 (13)5.7误差分析 (14)5.8使用说明 (14)总结参考文献附录附录一:过程卡附录二:工序卡附录三:夹具装配图附录四:参考任务书第一章序言通过机床工艺及夹具设计,汇总所学专业知识如一体(如《公差于配合》、《机械零件设计》、《机械制造工艺》等)。
让我们对所学的专业课得以加强和巩固、复习及实用,在理论与实践上有机结合;使我们对各科的作用更加深刻的熟悉与理解,并为以后的实际工作奠定坚实的基础!就我个人而言,我希望能通过这次课程设计对自己未来将从事的工作进行一次适应性训练,从中锻炼自己分析问题、解决问题的能力,为自己以后生活打下一个良好的基础。
张紧轮支架加工工艺及夹具设计说明书

张紧轮支架加工工艺及夹具设计说明书张紧轮支架加工工艺及夹具设计说明书太原理工大学现代科技学院课程设计张紧轮支架加工工艺及夹具设计说明书II 目目录录 1 1绪绪论论∙∙∙∙∙∙∙∙∙∙∙∙∙∙∙∙∙∙∙∙∙∙∙∙∙∙∙∙∙∙∙∙∙∙∙∙∙∙∙∙∙∙∙∙∙∙∙∙∙∙∙∙∙∙∙∙∙∙∙∙∙∙∙∙∙∙∙∙∙∙∙∙∙∙∙∙∙∙∙∙∙∙∙∙∙∙∙∙∙∙∙∙∙∙∙∙∙∙∙∙∙∙∙∙∙∙∙∙∙∙∙∙∙∙∙∙∙∙∙∙∙∙∙∙∙∙∙∙∙∙∙∙∙∙∙∙∙∙∙∙∙∙∙∙∙1 2 2 张紧轮支架的分析张紧轮支架的分析∙∙∙∙∙∙∙∙∙∙∙∙∙∙∙∙∙∙∙∙∙∙∙∙∙∙∙∙∙∙∙∙∙∙∙∙∙∙∙∙∙∙∙∙∙∙∙∙∙∙∙∙∙∙∙∙∙∙∙∙∙∙∙∙∙∙∙∙∙∙∙∙∙∙∙∙∙∙∙∙∙∙∙∙∙∙∙∙∙∙∙∙∙∙∙∙∙∙∙∙∙∙∙∙∙∙∙∙∙∙∙∙∙∙∙∙∙∙∙∙∙∙∙2 2.1 张紧轮支架的工艺分析∙∙∙∙∙∙∙∙∙∙∙∙∙∙∙∙∙∙∙∙∙∙∙∙∙∙∙∙∙∙∙∙∙∙∙∙∙∙∙∙∙∙∙∙∙∙∙∙∙∙∙∙∙∙∙∙∙∙∙∙∙∙∙∙∙∙∙∙∙∙∙∙∙∙∙∙∙∙∙∙∙∙∙∙∙∙∙∙∙∙∙∙∙∙∙∙∙∙∙∙∙∙∙∙∙∙∙∙∙∙∙∙2 2.2 张紧轮支架的工艺要求∙∙∙∙∙∙∙∙∙∙∙∙∙∙∙∙∙∙∙∙∙∙∙∙∙∙∙∙∙∙∙∙∙∙∙∙∙∙∙∙∙∙∙∙∙∙∙∙∙∙∙∙∙∙∙∙∙∙∙∙∙∙∙∙∙∙∙∙∙∙∙∙∙∙∙∙∙∙∙∙∙∙∙∙∙∙∙∙∙∙∙∙∙∙∙∙∙∙∙∙∙∙∙∙∙∙∙∙∙∙∙∙2 3 3 工艺规程设计工艺规程设计∙∙∙∙∙∙∙∙∙∙∙∙∙∙∙∙∙∙∙∙∙∙∙∙∙∙∙∙∙∙∙∙∙∙∙∙∙∙∙∙∙∙∙∙∙∙∙∙∙∙∙∙∙∙∙∙∙∙∙∙∙∙∙∙∙∙∙∙∙∙∙∙∙∙∙∙∙∙∙∙∙∙∙∙∙∙∙∙∙∙∙∙∙∙∙∙∙∙∙∙∙∙∙∙∙∙∙∙∙∙∙∙∙∙∙∙∙∙∙∙∙∙∙∙∙∙∙∙∙∙∙∙∙5 3.1 加工工艺过程∙∙∙∙∙∙∙∙∙∙∙∙∙∙∙∙∙∙∙∙∙∙∙∙∙∙∙∙∙∙∙∙∙∙∙∙∙∙∙∙∙∙∙∙∙∙∙∙∙∙∙∙∙∙∙∙∙∙∙∙∙∙∙∙∙∙∙∙∙∙∙∙∙∙∙∙∙∙∙∙∙∙∙∙∙∙∙∙∙∙∙∙∙∙∙∙∙∙∙∙∙∙∙∙∙∙∙∙∙∙∙∙∙∙∙∙∙∙∙∙∙∙∙∙∙∙∙∙5 3.2 确定各表面加工方案∙∙∙∙∙∙∙∙∙∙∙∙∙∙∙∙∙∙∙∙∙∙∙∙∙∙∙∙∙∙∙∙∙∙∙∙∙∙∙∙∙∙∙∙∙∙∙∙∙∙∙∙∙∙∙∙∙∙∙∙∙∙∙∙∙∙∙∙∙∙∙∙∙∙∙∙∙∙∙∙∙∙∙∙∙∙∙∙∙∙∙∙∙∙∙∙∙∙∙∙∙∙∙∙∙∙∙∙∙∙∙∙∙∙∙∙5 3.2.1 影响加工方法的因素∙∙∙∙∙∙∙∙∙∙∙∙∙∙∙∙∙∙∙∙∙∙∙∙∙∙∙∙∙∙∙∙∙∙∙∙∙∙∙∙∙∙∙∙∙∙∙∙∙∙∙∙∙∙∙∙∙∙∙∙∙∙∙∙∙∙∙∙∙∙∙∙∙∙∙∙∙∙∙∙∙∙∙∙∙∙∙∙∙∙∙∙∙∙∙∙∙∙∙∙∙∙∙∙∙∙∙∙5 3.2.2 加工方案的选择∙∙∙∙∙∙∙∙∙∙∙∙∙∙∙∙∙∙∙∙∙∙∙∙∙∙∙∙∙∙∙∙∙∙∙∙∙∙∙∙∙∙∙∙∙∙∙∙∙∙∙∙∙∙∙∙∙∙∙∙∙∙∙∙∙∙∙∙∙∙∙∙∙∙∙∙∙∙∙∙∙∙∙∙∙∙∙∙∙∙∙∙∙∙∙∙∙∙∙∙∙∙∙∙∙∙∙∙∙∙∙∙∙∙∙∙6 3.3 确定定位基准∙∙∙∙∙∙∙∙∙∙∙∙∙∙∙∙∙∙∙∙∙∙∙∙∙∙∙∙∙∙∙∙∙∙∙∙∙∙∙∙∙∙∙∙∙∙∙∙∙∙∙∙∙∙∙∙∙∙∙∙∙∙∙∙∙∙∙∙∙∙∙∙∙∙∙∙∙∙∙∙∙∙∙∙∙∙∙∙∙∙∙∙∙∙∙∙∙∙∙∙∙∙∙∙∙∙∙∙∙∙∙∙∙∙∙∙∙∙∙∙∙∙∙∙∙∙∙∙6 3.2.1 粗基准的选择∙∙∙∙∙∙∙∙∙∙∙∙∙∙∙∙∙∙∙∙∙∙∙∙∙∙∙∙∙∙∙∙∙∙∙∙∙∙∙∙∙∙∙∙∙∙∙∙∙∙∙∙∙∙∙∙∙∙∙∙∙∙∙∙∙∙∙∙∙∙∙∙∙∙∙∙∙∙∙∙∙∙∙∙∙∙∙∙∙∙∙∙∙∙∙∙∙∙∙∙∙∙∙∙∙∙∙∙∙∙∙∙∙∙∙∙∙∙∙∙6 3.2.1 精基准选择的原则∙∙∙∙∙∙∙∙∙∙∙∙∙∙∙∙∙∙∙∙∙∙∙∙∙∙∙∙∙∙∙∙∙∙∙∙∙∙∙∙∙∙∙∙∙∙∙∙∙∙∙∙∙∙∙∙∙∙∙∙∙∙∙∙∙∙∙∙∙∙∙∙∙∙∙∙∙∙∙∙∙∙∙∙∙∙∙∙∙∙∙∙∙∙∙∙∙∙∙∙∙∙∙∙∙∙∙∙∙∙∙∙7 3.4 工艺路线的拟订∙∙∙∙∙∙∙∙∙∙∙∙∙∙∙∙∙∙∙∙∙∙∙∙∙∙∙∙∙∙∙∙∙∙∙∙∙∙∙∙∙∙∙∙∙∙∙∙∙∙∙∙∙∙∙∙∙∙∙∙∙∙∙∙∙∙∙∙∙∙∙∙∙∙∙∙∙∙∙∙∙∙∙∙∙∙∙∙∙∙∙∙∙∙∙∙∙∙∙∙∙∙∙∙∙∙∙∙∙∙∙∙∙∙∙∙∙∙∙∙∙∙∙∙8 3.4.1 工序的合理组合∙∙∙∙∙∙∙∙∙∙∙∙∙∙∙∙∙∙∙∙∙∙∙∙∙∙∙∙∙∙∙∙∙∙∙∙∙∙∙∙∙∙∙∙∙∙∙∙∙∙∙∙∙∙∙∙∙∙∙∙∙∙∙∙∙∙∙∙∙∙∙∙∙∙∙∙∙∙∙∙∙∙∙∙∙∙∙∙∙∙∙∙∙∙∙∙∙∙∙∙∙∙∙∙∙∙∙∙∙∙∙∙∙∙∙∙8 3.4.2 工序的集中与分散∙∙∙∙∙∙∙∙∙∙∙∙∙∙∙∙∙∙∙∙∙∙∙∙∙∙∙∙∙∙∙∙∙∙∙∙∙∙∙∙∙∙∙∙∙∙∙∙∙∙∙∙∙∙∙∙∙∙∙∙∙∙∙∙∙∙∙∙∙∙∙∙∙∙∙∙∙∙∙∙∙∙∙∙∙∙∙∙∙∙∙∙∙∙∙∙∙∙∙∙∙∙∙∙∙∙∙∙∙∙∙∙8 3.4.3 加工阶段的划分∙∙∙∙∙∙∙∙∙∙∙∙∙∙∙∙∙∙∙∙∙∙∙∙∙∙∙∙∙∙∙∙∙∙∙∙∙∙∙∙∙∙∙∙∙∙∙∙∙∙∙∙∙∙∙∙∙∙∙∙∙∙∙∙∙∙∙∙∙∙∙∙∙∙∙∙∙∙∙∙∙∙∙∙∙∙∙∙∙∙∙∙∙∙∙∙∙∙∙∙∙∙∙∙∙∙∙∙∙∙∙∙∙∙∙∙9 3.5 张紧轮支架的偏差,加工余量,工序尺寸及毛坯尺寸的确定∙∙∙∙∙∙∙∙∙∙∙∙∙∙∙∙∙∙∙∙∙∙∙∙∙∙∙∙∙∙∙∙∙∙∙∙∙∙∙∙∙∙∙∙∙∙10 3.5.1 毛坯的结构工艺要求∙∙∙∙∙∙∙∙∙∙∙∙∙∙∙∙∙∙∙∙∙∙∙∙∙∙∙∙∙∙∙∙∙∙∙∙∙∙∙∙∙∙∙∙∙∙∙∙∙∙∙∙∙∙∙∙∙∙∙∙∙∙∙∙∙∙∙∙∙∙∙∙∙∙∙∙∙∙∙∙∙∙∙∙∙∙∙∙∙∙∙∙∙∙∙∙∙∙∙∙∙∙∙∙∙∙10 3.5.2 张紧轮支架的偏差计算∙∙∙∙∙∙∙∙∙∙∙∙∙∙∙∙∙∙∙∙∙∙∙∙∙∙∙∙∙∙∙∙∙∙∙∙∙∙∙∙∙∙∙∙∙∙∙∙∙∙∙∙∙∙∙∙∙∙∙∙∙∙∙∙∙∙∙∙∙∙∙∙∙∙∙∙∙∙∙∙∙∙∙∙∙∙∙∙∙∙∙∙∙∙∙∙∙∙∙∙∙∙11 3.4.4 加工工艺路线方案的比较∙∙∙∙∙∙∙∙∙∙∙∙∙∙∙∙∙∙∙∙∙∙∙∙∙∙∙∙∙∙∙∙∙∙∙∙∙∙∙∙∙∙∙∙∙∙∙∙∙∙∙∙∙∙∙∙∙∙∙∙∙∙∙∙∙∙∙∙∙∙∙∙∙∙∙∙∙∙∙∙∙∙∙∙∙∙∙∙∙∙∙∙∙∙∙∙∙∙113.6 确定切削用量及基本工时(机动时间)∙∙∙∙∙∙∙∙∙∙∙∙∙∙∙∙∙∙∙∙∙∙∙∙∙∙∙∙∙∙∙∙∙∙∙∙∙∙∙∙∙∙∙∙∙∙∙∙∙∙∙∙∙∙∙∙∙∙∙∙∙∙∙∙∙∙∙∙∙∙∙∙∙∙∙∙∙∙∙∙∙∙13 4 4 铣铣35MM35MM 和和28MM28MM 平面夹具设计平面夹具设计∙∙∙∙∙∙∙∙∙∙∙∙∙∙∙∙∙∙∙∙∙∙∙∙∙∙∙∙∙∙∙∙∙∙∙∙∙∙∙∙∙∙∙∙∙∙∙∙∙∙∙∙∙∙∙∙∙∙∙∙∙∙∙∙∙∙∙∙∙∙∙∙∙∙∙∙∙∙∙∙∙∙∙∙∙∙∙∙∙∙∙∙∙∙∙∙∙∙∙∙∙∙∙23 4.1 问题的提出∙∙∙∙∙∙∙∙∙∙∙∙∙∙∙∙∙∙∙∙∙∙∙∙∙∙∙∙∙∙∙∙∙∙∙∙∙∙∙∙∙∙∙∙∙∙∙∙∙∙∙∙∙∙∙∙∙∙∙∙∙∙∙∙∙∙∙∙∙∙∙∙∙∙∙∙∙∙∙∙∙∙∙∙∙∙∙∙∙∙∙∙∙∙∙∙∙∙∙∙∙∙∙∙∙∙∙∙∙∙∙∙∙∙∙∙∙∙∙∙∙∙∙∙∙∙∙∙∙∙23 4.2 切削力和夹紧力计算∙∙∙∙∙∙∙∙∙∙∙∙∙∙∙∙∙∙∙∙∙∙∙∙∙∙∙∙∙∙∙∙∙∙∙∙∙∙∙∙∙∙∙∙∙∙∙∙∙∙∙∙∙∙∙∙∙∙∙∙∙∙∙∙∙∙∙∙∙∙∙∙∙∙∙∙∙∙∙∙∙∙∙∙∙∙∙∙∙∙∙∙∙∙∙∙∙∙∙∙∙∙∙∙∙∙∙∙∙∙∙∙∙∙23 4.3 定位误差分析∙∙∙∙∙∙∙∙∙∙∙∙∙∙∙∙∙∙∙∙∙∙∙∙∙∙∙∙∙∙∙∙∙∙∙∙∙∙∙∙∙∙∙∙∙∙∙∙∙∙∙∙∙∙∙∙∙∙∙∙∙∙∙∙∙∙∙∙∙∙∙∙∙∙∙∙∙∙∙∙∙∙∙∙∙∙∙∙∙∙∙∙∙∙∙∙∙∙∙∙∙∙∙∙∙∙∙∙∙∙∙∙∙∙∙∙∙∙∙∙∙∙∙∙∙∙25 4.4 夹具设计及操作的简要说明∙∙∙∙∙∙∙∙∙∙∙∙∙∙∙∙∙∙∙∙∙∙∙∙∙∙∙∙∙∙∙∙∙∙∙∙∙∙∙∙∙∙∙∙∙∙∙∙∙∙∙∙∙∙∙∙∙∙∙∙∙∙∙∙∙∙∙∙∙∙∙∙∙∙∙∙∙∙∙∙∙∙∙∙∙∙∙∙∙∙∙∙∙∙∙∙∙∙∙∙2 6 结结论论∙∙∙∙∙∙∙∙∙∙∙∙∙∙∙∙∙∙∙∙∙∙∙∙∙∙∙∙∙∙∙∙∙∙∙∙∙∙∙∙∙∙∙∙∙∙∙∙∙∙∙∙∙∙∙∙∙∙∙∙∙∙∙∙∙∙∙∙∙∙∙∙∙∙∙∙∙∙∙∙∙∙∙∙∙∙∙∙∙∙∙∙∙∙∙∙∙∙∙∙∙∙∙∙∙∙∙∙∙∙∙∙∙∙∙∙∙∙∙∙∙∙∙∙∙∙∙∙∙∙∙∙∙∙∙∙∙∙∙∙∙∙∙∙∙∙∙∙∙27 参考文献参考文献∙∙∙∙∙∙∙∙∙∙∙∙∙∙∙∙∙∙∙∙∙∙∙∙∙∙∙∙∙∙∙∙∙∙∙∙∙∙∙∙∙∙∙∙∙∙∙∙∙∙∙∙∙∙∙∙∙∙∙∙∙∙∙∙∙∙∙∙∙∙∙∙∙∙∙∙∙∙∙∙∙∙∙∙∙∙∙∙∙∙∙∙∙∙∙∙∙∙∙∙∙∙∙∙∙∙∙∙∙∙∙∙∙∙∙∙∙∙∙∙∙∙∙∙∙∙∙∙∙∙∙∙∙∙∙∙∙∙∙∙∙∙∙∙∙28 0 1 1 绪绪论论机械设计制造及其夹具设计是我们融会贯通所学的知识,将理论与实践相结合,对专业知识的综合运用训练,为我们即将走向自己的工作岗位打下良好的基础。
- 1、下载文档前请自行甄别文档内容的完整性,平台不提供额外的编辑、内容补充、找答案等附加服务。
- 2、"仅部分预览"的文档,不可在线预览部分如存在完整性等问题,可反馈申请退款(可完整预览的文档不适用该条件!)。
- 3、如文档侵犯您的权益,请联系客服反馈,我们会尽快为您处理(人工客服工作时间:9:00-18:30)。
东海科学技术学院课程设计成果说明书题目:设计张紧轮支架零件的机械加工工艺规程及工艺设备院系:机电工程系学生姓名:专业:机械制造及其自动化班级:指导教师:起止日期:2017.12.19-2018.1.3 东海科学技术学院教学科研部浙江海洋大学东海科学技术学院《课程设计成果说明书》规范要求课程设计说明书是课程设计主要成果之一,一般在2000~3000字。
1.说明书基本格式版面要求:打印时正文采用5号宋体,A4纸,页边距上、下、左、右均为2cm,行间距采用固定值20磅,页码底部居中。
文中标题采用4号宋体加粗。
2.说明书结构及要求(1)封面(2)课程设计成绩评定表(3)任务书(指导教师下发)(4)摘要摘要要求对内容进行简短的陈述,一般不超过300字。
关键词应为反映主题内容的学术词汇,一般为3-5个,且应在摘要中出现。
(5)目录要求层次清晰,给出标题及页次。
最后一项为参考文献。
(6)正文正文应按照目录所确定的顺序依次撰写,要求论述清楚、简练、通顺,插图清晰整洁。
文中图、表及公式应规范地绘制和书写。
(7)参考文献一、设计题目: 张紧轮支架加工工艺及2*Φ13孔钻削夹具设计二、原始资料(1) 被加工零件的零件图1张(2) 生产类型:(中批或大批大量生产)三、上交材料1.所加工的零件图1张2.毛坯图1张3.编制机械加工工艺过程卡片1套4.编制所设计夹具对应的那道工序的机械加工工序卡片1套5.绘制夹具装配图(A0或A1)1张6.绘制夹具中1个零件图(A1或A2。
装配图出来后,由指导教师为学生指定需绘制的零件图,一般为夹具体)。
1张7.课程设计说明书,包括机械加工工艺规程的编制和机床夹具设计全部内容。
(约5000-8000字)1份四、进度安排本课程设计要求在3周内完成。
1.第l~2天查资料,绘制零件图。
2.第3~7天,完成零件的工艺性分析,确定毛坯的类型、制造方法,编制机械加工工艺规程和所加工工序的机械加工工序卡片。
3.第8~10天,完成夹具总体方案设计(画出草图,与指导教师沟通,在其同意的前提下,进行课程设计的下一步)。
4.第11~13天,完成夹具装配图的绘制。
5.第14~15天,零件图的绘制。
6.第16~18天,整理并完成设计说明书的编写。
7.第19天~21天,完成图纸和说明书的输出打印。
答辩五、指导教师评语该生设计的过程中表现,设计内容反映的基本概念及计算,设计方案,图纸表达,说明书撰写,答辩表现。
摘要本次课程设计的目的是对我们以前所学知识的总结和对我们所掌握知识的一次扩展,也对我所学的各科课程进行了一次深入的综合性复习。
主要内容:设计连接座的机械加工工艺规程和加工2*φ13孔的工艺装备并绘制出支架零件图、毛坯图、夹具装配图,填写工艺卡片,编制课程设计说明书。
设计意义:本次课程设计加强了我的理论与实践相结合的能力,并在设计过程中渐渐了解本专业的专业技能知识,使我更加了解加工与设计零件的方法,同时锻炼了我分析问题的能力,让我对以后的工作方向有了较为明确的目标。
目录一、零件的工艺分析及生产类型的确定 (1)1.零件的工艺分析 (1)2.零件的生产类型 (2)二、选择毛坯,确定毛坯尺寸,设计毛坯图 (3)1.毛坯的选择 (3)2.确定机械加工余量、毛坯尺寸和公差 (3)3.确定机械加工 (3)4.确定毛坯尺寸 (3)5.确定毛坯尺寸公差 (4)6.设计毛胚图 (4)三、选择加工方法,拟定工艺路线 (6)1.基面的选择 (6)2.精基面的选择 (6)3.制定机械加工工艺线 (6)四、加工设备及刀具、夹具、量具的选择 (9)1.选择加工设备及工艺装备 (9)2.确定工序尺寸 (11)五、切削用量的选择(工序Ⅸ) (12)1.切削用量的介绍 (12)2.切削用量的计算 (13)六、基本时间的确定 (13)1.工时定额 (13)2.基本时间的计算 (14)七、夹具设计 (14)1.定位方案 (14)2.夹紧机构 (14)3.夹紧力分析 (15)4.对刀装置 (16)5.夹具体 (16)6.误差分析 (17)7.使用说明 (17)七、设计体会 (18)八、参考文献 (19)一、零件的工艺分析及生产类型的确定1.零件的工艺分析:.由零件图可知,其材料为HT200,该材料为灰铸铁,具有较高强度,耐磨性,耐热性及减振性,适用于承受较大应力和要求耐磨零件。
连接座共有两组加工表面,他们之间有一定的位置要求。
现分述如下:1.1加工表面:表面包括下端面粗糙度为Ra6.3加工方法为粗车-半精车-经车,下端面粗糙度为Ra12.5加工方法为粗车半粗车,小凸台下端面粗糙度为Ra6.3加工方法为粗钻-半精钻-精钻,右Φ30通孔粗糙度为Ra25加工方法为粗钻-半精钻-精钻,2*Φ13通孔无粗糙度要求加工方法为钻通孔,然后是右端面也无粗糙度要求加工方法为粗车-半精车-精车,最后是小凸台内侧粗糙度为Ra12.5加工方法为粗车-半精车。
其具体过程如下表:2.零件的生产类型该零件材料为HT200,考虑到零件在工作时要有高的耐磨性,所以选择铸铁铸造。
依据设计要求Q=5000 台/年,件/台;n=1 结合生产实际,备品率α和废品率β分别取10%和1%代入公式得该工件的生产纲领N=5000 5555 件/年二、选择毛坯,确定毛坯尺寸,设计毛坯图1.毛坯的选择毛坯种类的选择决定与零件的实际作用,材料、形状、生产性质以及在生产中获得可能性,毛坯的制造方法主要有以下几种:a、型材b、锻造c、铸造d、焊接e、其他毛坯。
根据零件的材料,推荐用型材或铸件,但从经济方面着想,如用型材中的棒料,加工余量太大,这样不仅浪费材料,而且还增加机床,刀具及能源等消耗,而铸件具有较高的抗拉抗弯和抗扭强度,冲击韧性常用于大载荷或冲击载荷下的工作零件。
该零件材料为HT200,考虑到零件在工作时要有高的耐磨性,所以选择铸铁铸造。
依据设计要求Q=5000 台/年,件/台;n=1 结合生产实际,备品率α和废品率β分别取10%和1%代入公式得该工件的生产纲领N=5000 5555 件/年2.确定机械加工余量、毛坯尺寸和公差(1)求最大轮廓尺寸根据零件图计算轮廓的尺寸,最大直径Ф18mm,高34mm。
(2)选择铸件公差等级查手册铸造方法按机器造型,铸件材料按灰铸铁,得铸件公差等级为8~12 级,取为11 级。
(3)求铸件尺寸公差公差带相对于基本尺寸对称分布。
(4)求机械加工余量等级查手册铸造方法按机器造型、铸件材料为HT200,得机械加工余量等级E-G 级选择 F 级。
3.确定机械加工余量根据铸件质量、零件表面粗糙度、形状复杂程度,根据查表5-4取铸件加工表面的单边余量为 1.5mm,所以最后铸件加工表面的单边余量取2mm。
4.确定毛坯尺寸上面查得的加工余量适用于机械加工表面粗糙度Ra≥1.6 。
Ra﹤1.6 的表面,余量要适当加大。
分析本零件,加工表面Ra≥1.6 ,因此这些表面的毛坯尺寸只需将零件的尺寸加上所查的余量即可。
(由于有的表面只需粗加工,这时可取所查数据的小值)生产类型为大批量,可采用两箱砂型铸造毛坯。
由于所有孔无需铸造出来,故不需要安放型心。
此外,为消除残余应力,铸造后应安排人工进行时效处理。
5.确定毛坯尺寸公差毛坯尺寸公差根据铸件质量、材质系数、形状复杂系数查手册得,本零件毛坯尺寸允许偏差见下表:毛坯尺寸允许公差/mm6.设计毛坯图(1)确定拔模斜度根据机械制造工艺设计手册查出拔模斜度为 5 度。
(2)确定分型面由于毛坯形状前后对称,且最大截面在中截面,为了起模及便于发现上下模在铸造过程中的错移所以选前后对称的中截面为分型面。
(3)毛坯的热处理方式为了去除内应力,改善切削性能,在铸件取出后要做时效处理。
下图为该零件的毛坯图:四、选择加工方法,拟定工艺路线1.基面的选择基面选择是工艺规程设计中的重要设计之一,基面的选择正确与合理,可以使加工质量得到保证,生产率得到提高。
否则,加工工艺过程会问题百出,更有甚者,还会造成零件大批报废,使生产无法进行。
2.精基面的选择精基准的选择主要考虑基准重合的问题。
选择加工表面的设计基准为定位基准,称为基准重合的原则。
采用基准重合原则可以避免由定位基准与设计基准不重合引起的基准不重合误差,零件的尺寸精度和位置精度能可靠的得以保证。
3.制定机械加工工艺路线3.1 工艺路线一:工序一: 1.粗车上端面 2.钻Φ13*2通孔 3.粗车右端面 4.粗钻Φ18孔 5.粗车下端面 6.粗车凸台端面工序二: 1. 半精车下端面2.半精车右端面3. 半精钻Φ18孔4.精车车上端面 5.半精车凸台端面工序三:1精车上端面 2.精车右端面 3.精车凸台端面工序四: 1.精钻Φ18孔工序五:休整右端面3.2 工艺路线二:工序一:1. 粗车下端面2.粗车右端面3. 粗钻Φ18孔4.粗车上端面 5.粗车凸台端面工序二:1. 半精车上端面 2.钻Φ13*2通孔 3. 半精车右端面4. 半精钻Φ18孔 5. 半精车下端面 6. 半精车凸台端面工序三:1精车上端面 2.精车右端面 3.精车凸台端面工序四:1.精钻Φ18孔工序五:休整右端面3.3 工艺路线比较:上述两个工艺路线,第一条工艺路线做得比较精细,每一道工序都安排的很到位,但是做起来很复杂;第二条工艺路线比较简洁明了,基本上可以达到精度要求,但最后的磨工感觉有点多余。
相比之下我们选择第二条工艺路线,然后对其进行修改:去掉磨式。
因为零件精度要求不高,半精车就可以达到目的。
拟定工艺过程五、加工设备及刀具、夹具、量具的选择由于生产类型为大批量,故加工设备以通用机床为主,辅以少量专用机床,其生产方式以通用机床专用夹具为主,辅以少量专用机床的流水生产线,工件在各机床上的装卸及各机床间的传送均由人工完成。
1.选择加工设备及工艺装备1.1 选择机床根据不同的工序选择机床:(1)工序1、2、3主要是粗车、半精车、精车、,由于加工零件的外廓尺寸不大,但不是是回转体,故不宜在车床上镗孔。
各工序的工步不多,成批生产不要求很高的生产率,故选用卧式车床就能满足要求,所以选用的C620-1型卧式车床即可。
(2)工序6为钻孔、扩钻和扩孔,选用立式钻床Z535即可。
1.2 选择夹具本零件除粗铣、精铣、钻孔、攻螺纹需要专用夹具外,其他各工序均可使用通用夹具。
1.3 选择刀具根据不同的工序选择刀具。
(1)在车床上加工的工序一般都选用硬质合金车刀,加工钢质零件采用YT类硬质合金,粗加工用YT5,半精加工用YT15,精加工用YT30。
为提高身产率及经济性,应选用可转位车刀。
(2)钻Φ13孔,根据表5-83选用直柄麻花钻头Φ13,l=109mm,l1=69mm,d=13mm。
(3)钻Φ18孔,根据表5-83选用直柄麻花钻头l=123mm,l1=62mm,d=18mm1.4 选择量具本零件属成批生产,一般情况下尽量采用通用量具。