大圆坯连铸机的设计特点及装备水平
大型连铸圆坯应用与制造环形锻件的优势
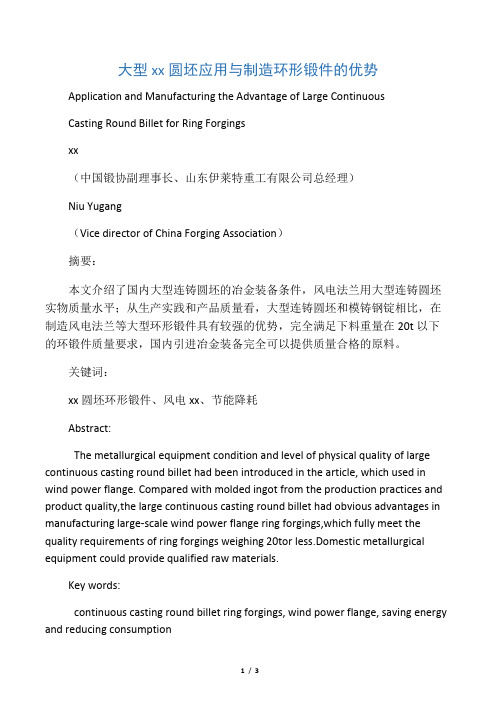
大型xx圆坯应用与制造环形锻件的优势Application and Manufacturing the Advantage of Large ContinuousCasting Round Billet for Ring Forgingsxx(中国锻协副理事长、山东伊莱特重工有限公司总经理)Niu Yugang(Vice director of China Forging Association)摘要:本文介绍了国内大型连铸圆坯的冶金装备条件,风电法兰用大型连铸圆坯实物质量水平;从生产实践和产品质量看,大型连铸圆坯和模铸钢锭相比,在制造风电法兰等大型环形锻件具有较强的优势,完全满足下料重量在20t以下的环锻件质量要求,国内引进冶金装备完全可以提供质量合格的原料。
关键词:xx圆坯环形锻件、风电xx、节能降耗Abstract:The metallurgical equipment condition and level of physical quality of large continuous casting round billet had been introduced in the article, which used in wind power flange. Compared with molded ingot from the production practices and product quality,the large continuous casting round billet had obvious advantages in manufacturing large-scale wind power flange ring forgings,which fully meet the quality requirements of ring forgings weighing 20tor less.Domestic metallurgical equipment could provide qualified raw materials.Key words:continuous casting round billet ring forgings, wind power flange, saving energy and reducing consumption前言:随着风电、石油、工程机械等行业的快速发展,环形锻件的需求越来越多,在环形锻件制造中,特别是在风电法兰锻件制造中,连铸圆坯的应用越来越广泛,比起模铸钢锭来说,无论是材料利用率,还是制造工艺,在同等质量要求下优势明显,已成为风电法兰用钢的主要原料,它必将成为我国风能产业的主要原料之一。
永钢大圆坯连铸工艺装备特点及实践
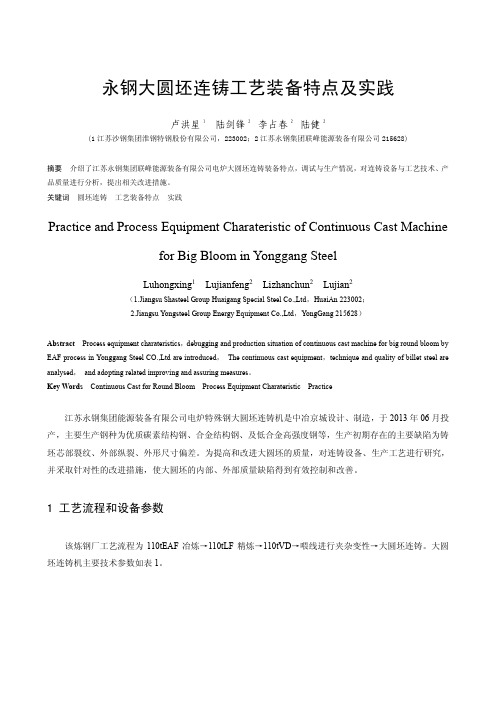
永钢大圆坯连铸工艺装备特点及实践卢洪星1陆剑锋 2 李占春 2 陆健2(1江苏沙钢集团淮钢特钢股份有限公司,223002;2江苏永钢集团联峰能源装备有限公司215628)摘要介绍了江苏永钢集团联峰能源装备有限公司电炉大圆坯连铸装备特点,调试与生产情况,对连铸设备与工艺技术、产品质量进行分析,提出相关改进措施。
关键词圆坯连铸工艺装备特点实践Practice and Process Equipment Charateristic of Continuous Cast Machinefor Big Bloom in Yonggang SteelLuhongxing1Lujianfeng2Lizhanchun2Lujian2(1.Jiangsu Shasteel Group Huaigang Special Steel Co.,Ltd,HuaiAn 223002;2.Jiangsu Yongsteel Group Energy Equipment Co.,Ltd,YongGang 215628)Abstract Process equipment charateristics,debugging and production situation of continuous cast machine for big round bloom by EAF process in Yonggang Steel CO.,Ltd are introduced,The continuous cast equipment,technique and quality of billet steel are analysed,and adopting related improving and assuring measures。
Key Words Continuous Cast for Round Bloom Process Equipment Charateristic Practice江苏永钢集团能源装备有限公司电炉特殊钢大圆坯连铸机是中冶京城设计、制造,于2013年06月投产,主要生产钢种为优质碳素结构钢、合金结构钢、及低合金高强度钢等,生产初期存在的主要缺陷为铸坯芯部裂纹、外部纵裂、外形尺寸偏差。
大方圆坯连铸机拉矫机的结构特点和设计计算
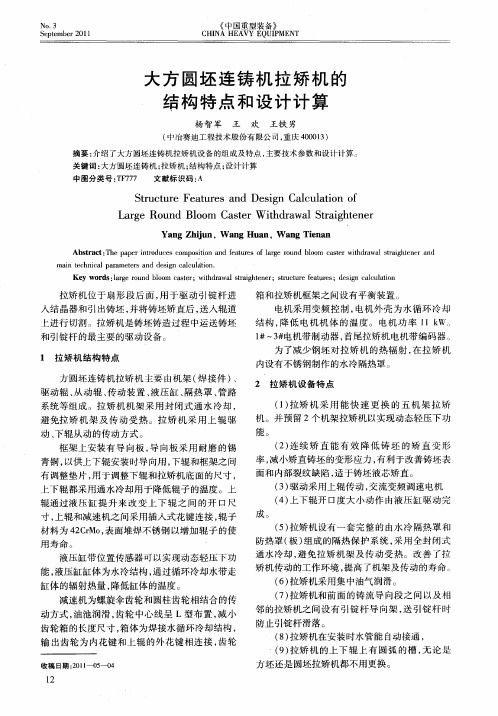
摘要 : 绍了大方圆坯连铸机拉矫机设备 的组成及特 点 , 介 主要技术参数 和设计计算 。 关键词 : 大方圆坯连铸机 ; 矫机 ; 拉 结构特点 ; 设计计算
中图 分 类 号 : F7 T77 文献标识码 : A
Sr cu e F au e n sg lu ain o tu t r e t r sa d De in Cac lto f Lag u d B o m se i d a lS r ih e e r e Ro n l o Ca trW t r w于 扇 形 段 后 面 , 于 驱 动 引锭 杆 进 用
箱 和拉矫 机框 架之 间设 有平 衡装 置 。 电机 采用 变频 控 制 , 电机 外 壳 为 水 循 环 冷 却
入结 晶器和 引 出铸坯 , 并将 铸坯 矫直 后 , 送入 辊道
上进 行切 割 。拉 矫机是 铸 坯铸造 过 程 中运送 铸坯 和 引锭杆 的最 主要 的驱动设 备 。
No. 3 Se tm b r2 pe e 01l
《 中国重型装备》
C IAH A YE UP N H N E V Q IME T
大 方 圆坯 连 铸 机 拉 矫 机 的 结构 特 点 和设 计 计 算
杨 智 军 王 欢 王铁 男
( 中冶 赛 迪 工 程 技 术 股 份 有 限公 司 , 庆 4 0 1 ) 重 0 0 3
青铜 , 以供上 下辊 安装 时导 向用 , 辊和框 架 之 间 下 有调 整垫 片 , 用于 调整 下辊 和拉 矫机 底 面 的尺寸 ,
( ) 矫 机 采 用 能 快 速 更 换 的 五 机 架 拉 矫 1拉
机 。并预 留 2个 机 架拉 矫机 以实现 动态 轻压 下 功
能。
() 2 连续 矫 直 能 有 效 降 低 铸 坯 的 矫 直 变 形 率, 减小矫 直 铸坯 的变形 应力 , 利于 改善 铸坯 表 有
连铸机的特点
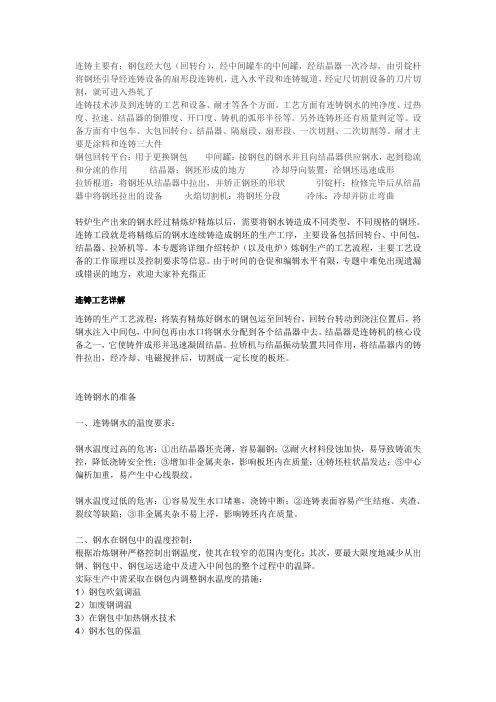
连铸主要有:钢包经大包(回转台),经中间罐车的中间罐,经结晶器一次冷却,由引锭杆将钢坯引导经连铸设备的扇形段连铸机,进入水平段和连铸辊道,经定尺切割设备的刀片切割,就可进入热轧了连铸技术涉及到连铸的工艺和设备、耐才等各个方面。
工艺方面有连铸钢水的纯净度、过热度、拉速、结晶器的倒锥度、开口度、铸机的弧形半径等。
另外连铸坯还有质量判定等。
设备方面有中包车、大包回转台、结晶器、隔扇段、扇形段、一次切割、二次切割等。
耐才主要是涂料和连铸三大件钢包回转平台:用于更换钢包中间罐:接钢包的钢水并且向结晶器供应钢水,起到稳流和分流的作用结晶器:钢坯形成的地方冷却导向装置:给钢坯迅速成形拉矫棍道:将钢坯从结晶器中拉出,并矫正钢坯的形状引锭杆:检修完毕后从结晶器中将钢坯拉出的设备火焰切割机:将钢坯分段冷床:冷却并防止弯曲转炉生产出来的钢水经过精炼炉精炼以后,需要将钢水铸造成不同类型、不同规格的钢坯。
连铸工段就是将精炼后的钢水连续铸造成钢坯的生产工序,主要设备包括回转台、中间包,结晶器、拉矫机等。
本专题将详细介绍转炉(以及电炉)炼钢生产的工艺流程,主要工艺设备的工作原理以及控制要求等信息。
由于时间的仓促和编辑水平有限,专题中难免出现遗漏或错误的地方,欢迎大家补充指正连铸工艺详解连铸的生产工艺流程:将装有精炼好钢水的钢包运至回转台,回转台转动到浇注位置后,将钢水注入中间包,中间包再由水口将钢水分配到各个结晶器中去。
结晶器是连铸机的核心设备之一,它使铸件成形并迅速凝固结晶。
拉矫机与结晶振动装置共同作用,将结晶器内的铸件拉出,经冷却、电磁搅拌后,切割成一定长度的板坯。
连铸钢水的准备一、连铸钢水的温度要求:钢水温度过高的危害:①出结晶器坯壳薄,容易漏钢;②耐火材料侵蚀加快,易导致铸流失控,降低浇铸安全性;③增加非金属夹杂,影响板坯内在质量;④铸坯柱状晶发达;⑤中心偏析加重,易产生中心线裂纹。
钢水温度过低的危害:①容易发生水口堵塞,浇铸中断;②连铸表面容易产生结疱、夹渣、裂纹等缺陷;③非金属夹杂不易上浮,影响铸坯内在质量。
高质量圆坯连铸生产的经验
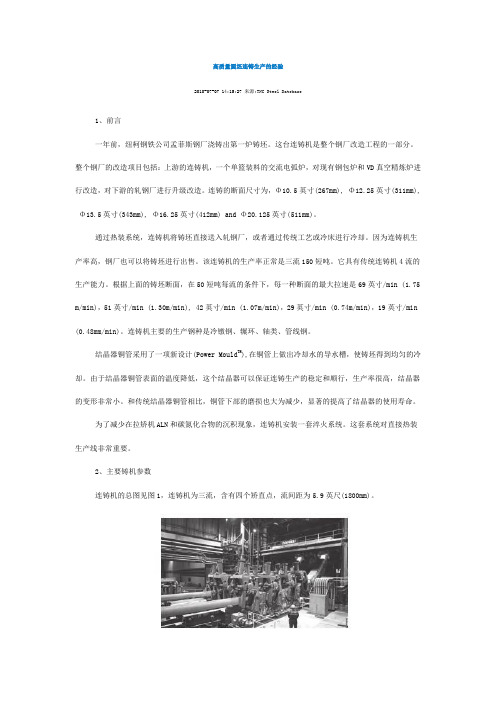
高质量圆坯连铸生产的经验2010-07-07 14:15:27 来源:TNC Steel Datebase1、前言一年前,纽柯钢铁公司孟菲斯钢厂浇铸出第一炉铸坯。
这台连铸机是整个钢厂改造工程的一部分。
整个钢厂的改造项目包括:上游的连铸机,一个单篮装料的交流电弧炉,对现有钢包炉和VD真空精炼炉进行改造,对下游的轧钢厂进行升级改造。
连铸的断面尺寸为,Φ10.5英寸(267mm), Φ12.25英寸(311mm),Φ13.5英寸(343mm), Φ16.25英寸(412mm) and Φ20.125英寸(511mm)。
通过热装系统,连铸机将铸坯直接送入轧钢厂,或者通过传统工艺或冷床进行冷却。
因为连铸机生产率高,钢厂也可以将铸坯进行出售。
该连铸机的生产率正常是三流150短吨。
它具有传统连铸机4流的生产能力。
根据上面的铸坯断面,在50短吨每流的条件下,每一种断面的最大拉速是69英寸/min (1.75 m/min),51英寸/min (1.30m/min), 42英寸/min (1.07m/min),29英寸/min (0.74m/min),19英寸/min (0.48mm/min)。
连铸机主要的生产钢种是冷镦钢、辗环、轴类、管线钢。
结晶器铜管采用了一项新设计(Power Mould TM),在铜管上做出冷却水的导水槽,使铸坯得到均匀的冷却。
由于结晶器铜管表面的温度降低,这个结晶器可以保证连铸生产的稳定和顺行,生产率很高,结晶器的变形非常小。
和传统结晶器铜管相比,铜管下部的磨损也大为减少,显著的提高了结晶器的使用寿命。
为了减少在拉矫机ALN和碳氮化合物的沉积现象,连铸机安装一套淬火系统。
这套系统对直接热装生产线非常重要。
2、主要铸机参数连铸机的总图见图1,连铸机为三流,含有四个矫直点,流间距为5.9英尺(1800mm)。
图1连铸机的总图钢包的钢水量为90短吨,目前的大包转台和中间包车保留使用。
中间包容量为24.8短吨,钢水高度31.5英寸(800mm)。
φ600mm大圆坯连铸机的设计与生产实践
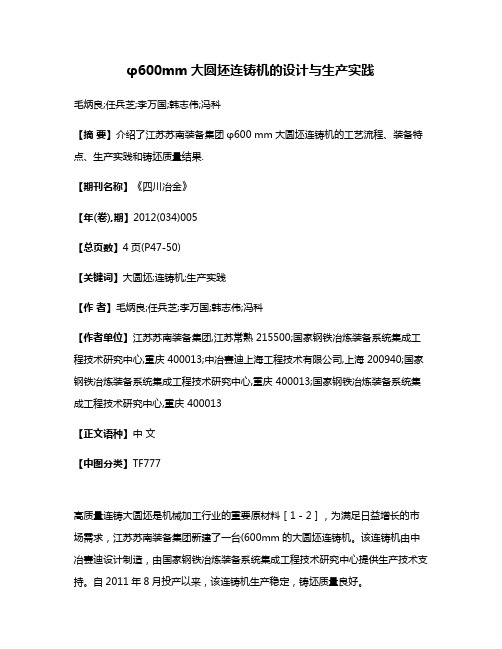
φ600mm大圆坯连铸机的设计与生产实践毛炳良;任兵芝;李万国;韩志伟;冯科【摘要】介绍了江苏苏南装备集团φ600 mm大圆坯连铸机的工艺流程、装备特点、生产实践和铸坯质量结果.【期刊名称】《四川冶金》【年(卷),期】2012(034)005【总页数】4页(P47-50)【关键词】大圆坯;连铸机;生产实践【作者】毛炳良;任兵芝;李万国;韩志伟;冯科【作者单位】江苏苏南装备集团,江苏常熟 215500;国家钢铁冶炼装备系统集成工程技术研究中心,重庆 400013;中冶赛迪上海工程技术有限公司,上海 200940;国家钢铁冶炼装备系统集成工程技术研究中心,重庆 400013;国家钢铁冶炼装备系统集成工程技术研究中心,重庆 400013【正文语种】中文【中图分类】TF777高质量连铸大圆坯是机械加工行业的重要原材料[1-2],为满足日益增长的市场需求,江苏苏南装备集团新建了一台(600mm的大圆坯连铸机。
该连铸机由中冶赛迪设计制造,由国家钢铁冶炼装备系统集成工程技术研究中心提供生产技术支持。
自2011年8月投产以来,该连铸机生产稳定,铸坯质量良好。
1 工艺流程该炼钢厂工艺流程为:120 t电炉→120 t LF炉精炼→120 tVD→大圆坯连铸机。
设计年产量为80万吨。
主要生产优质碳素结构钢、合金结构钢、管坯钢、齿轮钢等钢种。
连铸机主要工艺参数见表1。
表1 φ600 mm大圆坯连铸机的主要参数项目参数铸机流数4流间距 2 m连铸机机型全弧型基本半径 16 m钢水罐容量 120 t铸机长度 40 m工作拉速 0.20 ~0.32 m/min引锭杆型式柔性引锭杆引锭杆装入方式下装江苏苏南装备集团φ600 mm大圆坯连铸机采用全国产装备,技术装备达到国内先进水平,主要技术装备如下:(1)带升降、称量及加盖的多功能蝶式钢水罐回转台;(2)钢水罐液压操作钢水罐长水口操作器;(3)大容量带挡渣堰的中间罐;(4)带称量的液压升降中间罐车;(5)结晶器液面自动控制;(6)塞棒自动控流系统;(7)全程保护浇铸;(8)浸入式水口钢流快速切断;(9)结晶器液压振动;(10)结晶器电磁搅拌;(11)凝固末端电磁搅拌;(12)气水雾化二次冷却及自动控制;(13)仿弧运动火焰切割机;(14)拉钢式铸坯收集装置。
淮钢特殊钢大型圆坯连铸工艺装备特点及实践

淮钢特殊钢大型圆坯连铸工艺装备特点及实践淮钢特殊钢大型圆坯连铸工艺装备特点及实践淮钢特殊钢大型圆坯连铸工艺装备是一种高效、节能、环保的钢铁生产工艺,其特点在于采用了先进的连铸技术和设备,能够生产出高质量、高精度的特殊钢圆坯,满足了市场对高品质钢材的需求。
下面将从工艺装备的特点和实践两个方面进行介绍。
一、工艺装备特点1.高效节能淮钢特殊钢大型圆坯连铸工艺装备采用了先进的连铸技术,能够实现高效、连续、自动化的生产过程,大大提高了生产效率和生产能力。
同时,该工艺装备还采用了节能环保的设计理念,通过优化能源结构和节约能源消耗,实现了能源的高效利用和环保生产。
2.高精度淮钢特殊钢大型圆坯连铸工艺装备采用了先进的数控技术和自动化控制系统,能够实现高精度的生产过程。
通过对生产过程中的各个环节进行精细化控制,保证了生产出的特殊钢圆坯的尺寸精度和表面质量的稳定性。
3.高品质淮钢特殊钢大型圆坯连铸工艺装备采用了高品质的原材料和先进的生产工艺,能够生产出高品质的特殊钢圆坯。
同时,该工艺装备还采用了严格的质量控制体系和检测手段,保证了生产出的特殊钢圆坯的质量稳定性和可靠性。
二、实践淮钢特殊钢大型圆坯连铸工艺装备已经在淮钢集团的生产实践中得到了广泛应用。
通过对该工艺装备的实践应用,取得了以下成果:1.提高了生产效率和生产能力淮钢特殊钢大型圆坯连铸工艺装备的应用,使得淮钢集团的生产效率和生产能力得到了显著提高。
通过优化生产过程和提高生产效率,淮钢集团的特殊钢圆坯产量得到了大幅提升,同时还能够满足市场对高品质特殊钢圆坯的需求。
2.提高了产品质量和稳定性淮钢特殊钢大型圆坯连铸工艺装备的应用,使得淮钢集团的产品质量和稳定性得到了显著提高。
通过优化生产工艺和加强质量控制,淮钢集团的特殊钢圆坯的尺寸精度和表面质量得到了大幅提升,同时还能够保证产品质量的稳定性和可靠性。
3.提高了环保效益淮钢特殊钢大型圆坯连铸工艺装备的应用,使得淮钢集团的环保效益得到了显著提高。
大圆坯连铸机的设计特点及装备水平
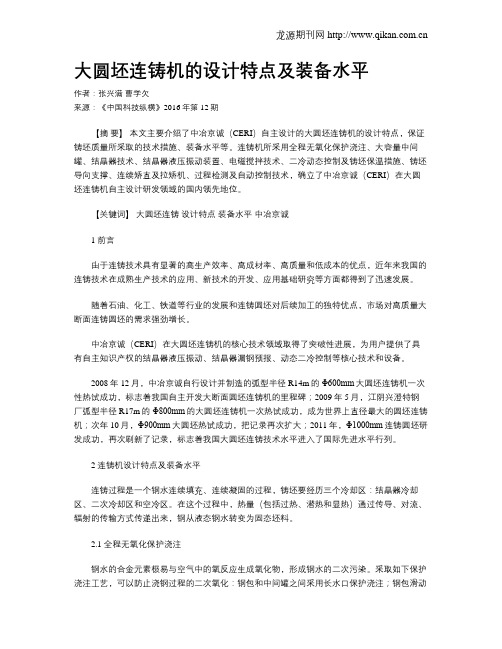
大圆坯连铸机的设计特点及装备水平作者:张兴满曹学欠来源:《中国科技纵横》2016年第12期【摘要】本文主要介绍了中冶京诚(CERI)自主设计的大圆坯连铸机的设计特点,保证铸坯质量所采取的技术措施、装备水平等。
连铸机所采用全程无氧化保护浇注、大容量中间罐、结晶器技术、结晶器液压振动装置、电磁搅拌技术、二冷动态控制及铸坯保温措施、铸坯导向支撑、连续矫直及拉矫机、过程检测及自动控制技术,确立了中冶京诚(CERI)在大圆坯连铸机自主设计研发领域的国内领先地位。
【关键词】大圆坯连铸设计特点装备水平中冶京诚1 前言由于连铸技术具有显著的高生产效率、高成材率、高质量和低成本的优点,近年来我国的连铸技术在成熟生产技术的应用、新技术的开发、应用基础研究等方面都得到了迅速发展。
随着石油、化工、铁道等行业的发展和连铸圆坯对后续加工的独特优点,市场对高质量大断面连铸圆坯的需求强劲增长。
中冶京诚(CERI)在大圆坯连铸机的核心技术领域取得了突破性进展,为用户提供了具有自主知识产权的结晶器液压振动、结晶器漏钢预报、动态二冷控制等核心技术和设备。
2008年12月,中冶京诚自行设计并制造的弧型半径R14m的Φ600mm大圆坯连铸机一次性热试成功,标志着我国自主开发大断面圆坯连铸机的里程碑;2009年5月,江阴兴澄特钢厂弧型半径 R17m的Φ800mm的大圆坯连铸机一次热试成功,成为世界上直径最大的圆坯连铸机;次年10月,Φ900mm大圆坯热试成功,把记录再次扩大;2011年,Φ1000mm连铸圆坯研发成功,再次刷新了记录,标志着我国大圆坯连铸技术水平进入了国际先进水平行列。
2 连铸机设计特点及装备水平连铸过程是一个钢水连续填充、连续凝固的过程,铸坯要经历三个冷却区:结晶器冷却区、二次冷却区和空冷区。
在这个过程中,热量(包括过热、潜热和显热)通过传导、对流、辐射的传输方式传递出来,钢从液态钢水转变为固态坯料。
2.1 全程无氧化保护浇注钢水的合金元素极易与空气中的氧反应生成氧化物,形成钢水的二次污染。
大方坯连铸机出坯系统的特点及设计要领

收稿日期:2006-04-16;修订日期:2006-05-08作者简介:刘彩玲(1963-),女,西安重型机械研究所高级工程师。
大方坯连铸机出坯系统的特点及设计要领刘彩玲,杨拉道,王 蓉,王国啸(西安重型机械研究所,陕西 西安 710032)摘 要:本文以大方坯连铸机典型的出坯线为依据,结合作者多年的设计和生产实践经验阐述了大方坯连铸机出坯系统的总体功能、设备特点、设备运转过程、设备布置及其设计原则等,供大方坯连铸设计工作者和大方坯连铸生产厂参考。
关键词:连铸;方坯;出坯;热送;中图分类号:TF77712 文献标识码:A 文章编号:1001-196X (2006)04-0038-05The run 2out system πs character isti cs and desi gn of bloom ca sterL I U Cai 2ling,Y ANG La 2dao,WANG Rong,WANG Guo 2xiao(Xi ’an Heavy Machinery Research I nstitute,Xi πan 710032,China )Abstract:Based on the run 2out line of typ ical bloom casters,the article p resents the run 2out system πs general function,equipment feature,running p r ocess,layout,design p rincip le and etc ..It p r ovides reference data t o bl oom caster designers and p lants .Key words:concaster;bloo m caster;run 2out;hot ferrying1 概述与板坯连铸机相比,大方坯连铸机具有所浇断面特殊、钢种特殊及流数多等特点,其出坯区域的设备布置和各单机设备也有其自身的特点。
合金钢大方圆坯连铸机的工艺参数及设计特点
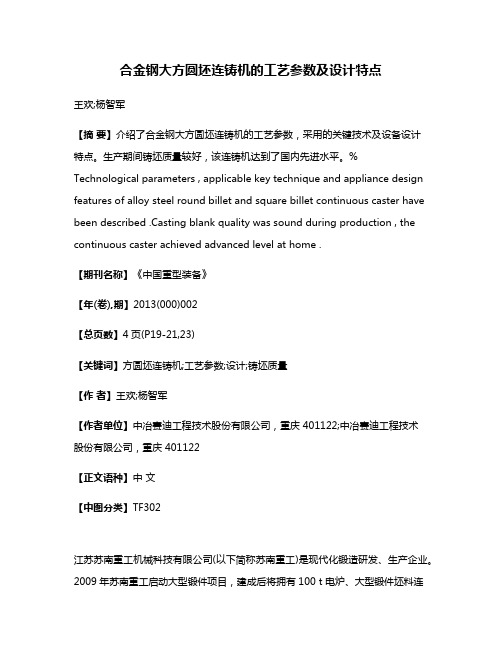
合金钢大方圆坯连铸机的工艺参数及设计特点王欢;杨智军【摘要】介绍了合金钢大方圆坯连铸机的工艺参数,采用的关键技术及设备设计特点。
生产期间铸坯质量较好,该连铸机达到了国内先进水平。
% Technological parameters , applicable key technique and appliance design features of alloy steel round billet and square billet continuous caster have been described .Casting blank quality was sound during production , the continuous caster achieved advanced level at home .【期刊名称】《中国重型装备》【年(卷),期】2013(000)002【总页数】4页(P19-21,23)【关键词】方圆坯连铸机;工艺参数;设计;铸坯质量【作者】王欢;杨智军【作者单位】中冶赛迪工程技术股份有限公司,重庆 401122;中冶赛迪工程技术股份有限公司,重庆 401122【正文语种】中文【中图分类】TF302江苏苏南重工机械科技有限公司(以下简称苏南重工)是现代化锻造研发、生产企业。
2009年苏南重工启动大型锻件项目,建成后将拥有100 t 电炉、大型锻件坯料连铸设备等,形成年产各类大型锻件25 万吨的能力。
为满足项目建设要求,需新建一台4 机4 流浇注合金钢的方圆坯兼容的连铸机,钢水由炼钢厂的一座100 t 电炉供给。
由于浇注合金钢的连铸机装备水平要求较高,所以连铸机的工艺参数及主要设备结构的选择显得尤为重要。
1 产品大纲及工艺流程新建的连铸机为方圆坯兼容,产量为52.5 万吨/年,其中圆坯29.5 万吨/年,方坯23 万吨/年,其产品及代表钢种见表1,连铸机的工艺流程见图1。
淮钢特殊钢大型圆坯连铸工艺装备特点及实践
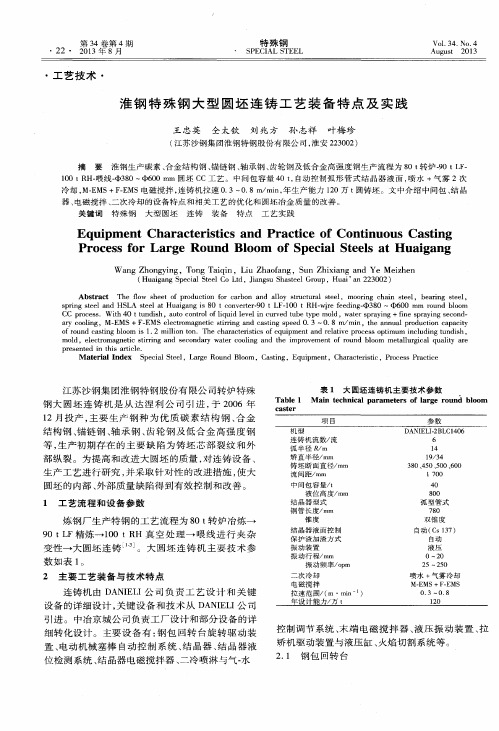
特 殊 钢
t
S PECI AL S TEEL
Vo 1 . 3 4. No. 4 Aug u s t 2 01 3
・
工艺技术 ・
淮 钢 特 殊 钢 大 型 圆 坯 连 铸 工 艺 装 备 特 点 及 实 践
王 忠 英 仝 太钦 刘兆方 孙 志祥 叶梅 珍
Eq u i p me n t Ch a r a c t e r i s t i c s a n d Pr a c t i c e o f Co n t i nu o us Ca s t i ng Pr o c e s s f o r La r g e Ro u nd Bl o o m o f S p e c i a l S t e e l s a t Hu a i g a n g
s p r i n g s t e e l a n d H S L A s t e e l a t Hu a i g a n g i s 8 0 t c o n v e r t e r 一 9 0 t L F 一 1 0 0 t R H— w i r e f e e d i n g 一  ̄ b 3 8 0~中 6 0 0 m m r o u n d b l o o m
Wa ng Zh o n g y i ng,To n g Ta i q i n, L i u Zh a o f a ng, S u n Zh i x i a ng a n d Ye Me i z h e n
( H u a i g a n g S p e c i a l S t e e l C o L t d , J i a n g s u S h a s t e e l G r o u p , Hu a i ’ a n 2 2 3 0 0 2 )
2013年国内大圆坯连铸机现状
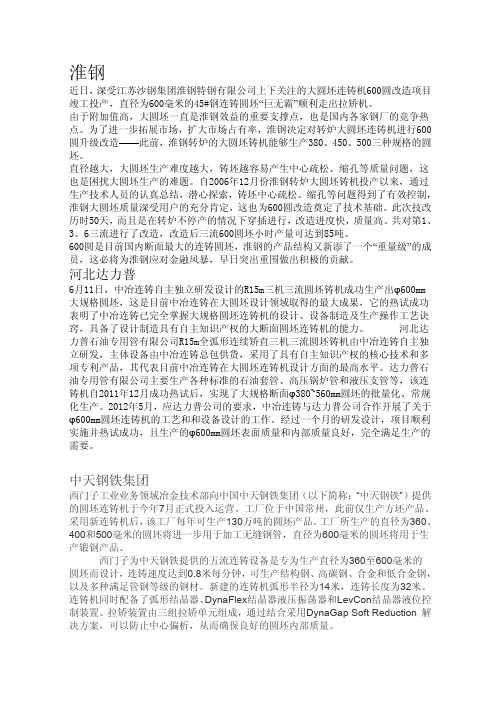
淮钢近日,深受江苏沙钢集团淮钢特钢有限公司上下关注的大圆坯连铸机600圆改造项目竣工投产,直径为600毫米的45#钢连铸圆坯“巨无霸”顺利走出拉矫机。
由于附加值高,大圆坯一直是淮钢效益的重要支撑点,也是国内各家钢厂的竞争热点。
为了进一步拓展市场,扩大市场占有率,淮钢决定对转炉大圆坯连铸机进行600圆升级改造——此前,淮钢转炉的大圆坯铸机能够生产380、450、500三种规格的圆坯。
直径越大,大圆坯生产难度越大,铸坯越容易产生中心疏松、缩孔等质量问题,这也是困扰大圆坯生产的难题。
自2006年12月份淮钢转炉大圆坯铸机投产以来,通过生产技术人员的认真总结,潜心探索,铸坯中心疏松、缩孔等问题得到了有效控制,淮钢大圆坯质量深受用户的充分肯定,这也为600圆改造奠定了技术基础。
此次技改历时50天,而且是在转炉不停产的情况下穿插进行,改造进度快,质量高。
共对第1、3、6三流进行了改造,改造后三流600圆坯小时产量可达到85吨。
600圆是目前国内断面最大的连铸圆坯,淮钢的产品结构又新添了一个“重量级”的成员,这必将为淮钢应对金融风暴,早日突出重围做出积极的贡献。
河北达力普6月11日,中冶连铸自主独立研发设计的R15m三机三流圆坯铸机成功生产出φ600mm 大规格圆坯,这是目前中冶连铸在大圆坯设计领域取得的最大成果,它的热试成功表明了中冶连铸已完全掌握大规格圆坯连铸机的设计、设备制造及生产操作工艺诀窍,具备了设计制造具有自主知识产权的大断面圆坯连铸机的能力。
河北达力普石油专用管有限公司R15m全弧形连续矫直三机三流圆坯铸机由中冶连铸自主独立研发,主体设备由中冶连铸总包供货,采用了具有自主知识产权的核心技术和多项专利产品,其代表目前中冶连铸在大圆坯连铸机设计方面的最高水平。
达力普石油专用管有限公司主要生产各种标准的石油套管、高压锅炉管和液压支管等,该连铸机自2011年12月成功热试后,实现了大规格断面φ380~560mm圆坯的批量化、常规化生产。
《大方坯连铸机总体设计及其软件系统的研究与开发》范文

《大方坯连铸机总体设计及其软件系统的研究与开发》篇一一、引言大方坯连铸机是现代钢铁工业生产中重要的设备之一,它的性能和质量直接影响钢铁企业的生产效率和产品质量。
为了适应钢铁行业的快速发展和技术的持续创新,本文将重点研究大方坯连铸机的总体设计及其软件系统的开发与实现。
本文旨在通过理论分析和实践应用,为大方坯连铸机的设计、制造和软件开发提供科学依据和技术支持。
二、大方坯连铸机总体设计1. 设计原则大方坯连铸机的设计应遵循先进性、可靠性、经济性、可维护性和可扩展性等原则。
在满足生产需求的前提下,尽可能采用先进的技术和设备,确保设备的稳定性和可靠性。
同时,要充分考虑设备的维护和升级,以便在未来的发展中能够适应新的技术需求和市场变化。
2. 总体结构大方坯连铸机的总体结构包括钢水包、中间包、结晶器、二次冷却区、拉矫机等部分。
其中,钢水包用于储存和供给钢水;中间包用于缓冲钢水流量,保证钢水的均匀供给;结晶器是连铸机的核心部分,用于结晶和初步成型;二次冷却区用于对铸坯进行冷却;拉矫机则用于拉拔和矫直铸坯。
3. 设计要点在总体设计中,要特别注意以下几个方面:一是要合理设计各部分的尺寸和结构,以保证设备的稳定性和生产效率;二是要采用先进的控制技术,实现精确的温度控制和速度控制;三是要注重设备的可维护性和可扩展性,方便设备的维护和升级。
三、软件系统开发与实现1. 软件系统架构大方坯连铸机的软件系统采用模块化设计,主要包括数据采集模块、控制模块、监控模块和故障诊断模块等部分。
数据采集模块负责采集设备运行过程中的各种数据;控制模块根据数据采集模块提供的数据进行控制决策;监控模块则实时监测设备的运行状态;故障诊断模块则用于诊断设备的故障并进行预警。
2. 软件开发环境与工具软件系统的开发采用先进的开发环境和工具,如集成开发环境(IDE)、编程语言(如C++、Java等)以及数据库管理系统等。
这些工具可以提供高效的代码编写、调试和测试功能,保证软件系统的稳定性和可靠性。
《大方坯连铸机总体设计及其软件系统的研究与开发》

《大方坯连铸机总体设计及其软件系统的研究与开发》篇一一、引言随着现代工业的快速发展,大方坯连铸机作为钢铁生产中的重要设备,其设计及软件系统的研发已成为工业领域的研究热点。
大方坯连铸机通过精确控制熔融金属的凝固过程,实现了高效、连续的钢坯生产。
本文将针对大方坯连铸机的总体设计及其软件系统进行深入研究与开发,旨在提高生产效率、优化生产流程、确保设备安全稳定运行。
二、大方坯连铸机总体设计1. 设计原则大方坯连铸机设计遵循高效、稳定、可靠的原则,注重设备的整体性能和操作便捷性。
设计过程中充分考虑了设备的可维护性、可扩展性以及环保节能等因素。
2. 设备结构大方坯连铸机主要由浇注系统、结晶器、二次冷却区、拉矫装置、切割设备等部分组成。
其中,浇注系统负责将熔融金属引入结晶器;结晶器为钢水提供冷却凝固的环境;二次冷却区通过喷水等手段进一步冷却钢坯;拉矫装置用于控制钢坯的拉速和方向;切割设备则用于将凝固的钢坯切割成一定长度的成品。
3. 设计流程在设计过程中,首先进行需求分析,明确设备的功能、性能要求以及生产环境等;其次进行方案论证,制定多种设计方案并进行比较分析;然后进行详细设计,确定设备的具体结构、参数等;最后进行优化设计,对设备进行仿真分析和实验验证,确保设计的合理性和可靠性。
三、软件系统研发1. 软件系统架构大方坯连铸机的软件系统采用模块化设计,主要包括数据采集模块、控制模块、监控模块、故障诊断模块等。
数据采集模块负责实时采集设备的运行数据;控制模块根据预设的工艺参数对设备进行控制;监控模块实时监测设备的运行状态,当出现异常时及时报警;故障诊断模块则对设备进行故障诊断和预测。
2. 软件功能实现软件系统通过与硬件设备的紧密配合,实现了对大方坯连铸机的精确控制。
具体功能包括:实时数据采集、远程监控、自动控制、故障诊断与预警等。
通过软件系统的应用,大大提高了设备的生产效率、降低了能耗、减少了故障率。
四、实验与验证为了验证大方坯连铸机总体设计及其软件系统的可行性和可靠性,我们进行了大量的实验和现场验证。
《大方坯连铸机总体设计及其软件系统的研究与开发》

《大方坯连铸机总体设计及其软件系统的研究与开发》篇一一、引言随着现代工业的快速发展,大方坯连铸机作为钢铁生产过程中的关键设备,其设计与研发对于提高生产效率、降低成本、优化产品质量具有重要意义。
本文将详细介绍大方坯连铸机的总体设计及其软件系统的研究与开发,以期为相关领域的科研与工程实践提供参考。
二、大方坯连铸机总体设计1. 设计原则大方坯连铸机设计遵循高效、稳定、可靠、节能的原则,确保生产过程中的连续性与安全性。
设计时充分考虑设备操作方便、维护简便等因素。
2. 主要结构大方坯连铸机主要由进料系统、结晶器、引锭机构、二冷段、切割段等部分组成。
进料系统负责将铁水或钢水输入到结晶器中;结晶器为铸坯提供冷却与结晶的环境;引锭机构则负责将结晶器中的铸坯引出;二冷段与切割段则分别负责铸坯的二次冷却与切割。
3. 关键技术参数在总体设计中,关键技术参数包括铸坯尺寸、铸速、结晶器振动参数等。
这些参数的合理设置对于保证产品质量、提高生产效率具有重要意义。
三、软件系统研究与开发1. 需求分析软件系统需求分析是研发过程中的重要环节。
通过对大方坯连铸机的实际需求进行调研与分析,确定软件系统的功能需求、性能需求及用户界面需求等。
2. 系统架构设计根据需求分析结果,设计合理的软件系统架构。
系统架构应具备高可靠性、高可扩展性及高可维护性等特点,以满足实际生产过程中的需求变化。
3. 功能模块设计软件系统包括多个功能模块,如数据采集模块、控制模块、监测模块、故障诊断模块等。
数据采集模块负责实时采集生产过程中的数据;控制模块负责根据实际需求调整设备运行参数;监测模块则负责实时监测设备运行状态;故障诊断模块则能够快速定位并解决设备故障。
4. 软件开发与实现在完成系统架构与功能模块设计后,进行软件开发与实现。
采用先进的编程语言与开发工具,确保软件系统的稳定性与可靠性。
同时,注重用户体验,优化用户界面,提高系统的易用性。
四、总结与展望大方坯连铸机总体设计及其软件系统的研究与开发对于提高钢铁生产效率、降低成本、优化产品质量具有重要意义。
《大方坯连铸机总体设计及其软件系统的研究与开发》

《大方坯连铸机总体设计及其软件系统的研究与开发》篇一一、引言随着现代工业的快速发展,大方坯连铸机作为钢铁生产过程中的关键设备,其设计与研发显得尤为重要。
大方坯连铸机不仅影响着钢铁生产效率,还直接关系到产品质量和企业的经济效益。
因此,本文将重点研究大方坯连铸机的总体设计及其软件系统的开发,为钢铁生产提供有力支持。
二、大方坯连铸机总体设计1. 设计原则大方坯连铸机总体设计需遵循先进性、可靠性、高效性、节能环保等原则。
设计过程中应充分考虑设备的结构、工艺流程、操作维护等因素,确保设备在满足生产需求的同时,具备较高的稳定性和可靠性。
2. 设备结构大方坯连铸机主要由浇注系统、结晶器、二次冷却区、拉矫装置、切割设备等部分组成。
其中,浇注系统负责将钢水引入结晶器;结晶器是连铸机的核心部分,用于保证铸坯的质量;二次冷却区则对铸坯进行冷却处理;拉矫装置用于控制铸坯的拉速和位置;切割设备则负责将铸坯切割成合适长度的坯料。
3. 工艺流程大方坯连铸机的工艺流程主要包括钢水浇注、结晶、二次冷却、拉矫、切割等步骤。
在浇注过程中,需严格控制钢水的温度和成分,以保证铸坯的质量。
结晶过程中,需保证结晶器的稳定性和冷却效果。
在二次冷却区,需根据铸坯的材质和规格,合理控制冷却强度和时间。
拉矫装置则需根据生产需求,调整拉速和位置。
最后,通过切割设备将铸坯切割成合适长度的坯料,为后续生产提供原材料。
三、软件系统开发1. 系统架构大方坯连铸机的软件系统采用模块化设计,主要包括数据采集模块、控制模块、监控模块、故障诊断模块等。
数据采集模块负责实时收集设备的运行数据;控制模块则根据生产需求,对设备进行控制;监控模块用于实时监测设备的运行状态;故障诊断模块则能对设备进行故障诊断和预警。
2. 功能实现数据采集模块通过传感器实时收集设备的运行数据,包括温度、压力、流量等参数。
控制模块根据生产需求和设备状态,通过PLC控制系统对设备进行控制。
监控模块通过人机界面实时显示设备的运行状态,便于操作人员实时掌握设备情况。
连铸设备主要技术参数

2010连铸设备及岗位职能love2010-1-51.设备主要技术参数1.1.设备主要技术参数:连铸机型式弧形小方坯连铸机弧形半径 R=6000mm流数三机三流流间距 1200mm铸坯断面 120×120mm 150×150mm Φ110-Φ160mm铸坯定尺长度 3.7-12米钢水罐支撑方式钢包回转台中间罐车台数 2台中间罐型式、容量电动缸自动控制塞棒开闭式,容量12t结晶器结构形式铜管水套组合式铸坯导向装置上段为活动段下段为固定段拉矫机拉速范围 0.6-6.0m/min铸坯切断方式火焰切割机出坯方式轨道,双层翻转冷床,翻缸机,移缸机和推钢机轨道速度 32m/min移钢能力 3.2t钢结构平台上层平台面标高 +6.700m(轨道面标高+0.60m)上层平台面长宽 23800×13100mm下层平台面标高 +4.05mm连铸机长度(基准线至固定挡板面) 39680mm1.2 主要设备技术性能1.2.1钢包回转台承载能力 2×80t(钢水重40t,钢包重40t)回转半径 3500mm旋转速度正常1r/min,启、制动0.1r/min旋转角度±180°;故障时±360°旋转用电机 YZR160MB-6 AC 8.5KW 930r/min 单轴伸 IM1001 380V H级绝缘 IP54事故旋转速度 0.5rpm事故旋转角度 180°事故旋转油马达斜轴式轴向柱塞马达A2F63W2P1 P=10-13MPa471r/min N=5.2-6.8KW放钢包时冲击系数 2干油润滑系统:1.2.1.1齿轮润滑系统多点干油泵 ZB-2型 N=18KW工作压力 31.5MPa贮油容积 30L给油量 3.2立方厘米/minDC24V喷射嘴 GPZ-135型(JB/ZQ4538-86)空气压力 0.45-0.6MPa喷射直径 135mm喷嘴与润滑表面距离 200mm气动三联件 398.263二位二通电磁阀 DF-10 DC24V润滑介质连铸机专用脂空气工作压力 0.45-0.6MPa1.2.1.2 轴承圈润滑系统电动干油泵 DRB4-M120Z换向阀 24EJF-M(JB/ZQ4584-86)压差开关 YCK-M5 (JB/ZQ4585-86)双线分配器 4SSP2-M1.5(JB/ZQ4583-86)2SSP2-M1.5(JB/ZQ4583-86)润滑介质连铸机专用脂1.2.2中间罐车结构型式框型结构的车架,单侧链轮驱动载重量 15.5t轨距 1700mm轮架 3800mm最大轮压 80KN减速器 BWD2.2-3-29摆线针轮行星减速器车轮直径Φ350mm走行速度 9.52m/min走行方向微调手动操作中间罐横向微调行程±30mm车体运行距离±8000mm供电方式电缆卷筒操作方式固定操作箱1.2.3中间罐烘烤站结构型式烧嘴可垂直旋转升降80°烧嘴型式鼓风助燃的天然气火焰燃烧嘴烘烤温度 -25~1100℃烘烤时间 45~60min烧嘴数量 2个/台天然气压 0.2MPa空气压力 0.4MPa风机型号(2#机配置) GY8-12-1 NO.6 右旋1.2.4 结晶器结构型式弧形铜管水套组合式外弧半径 6000mm断面尺寸 120×120mm 150×150mm Φ110-Φ160mm铜管长度方坯750mm,圆坯 800mm冷却水量 95立方米/小时水压 0.6MPa-0.8Mpa足辊水方坯角喷 120(4×4) 150(8×4);圆坯Φ110-Φ160mm(6×3),Φ160-Φ180(8×3)喷嘴型号 3/8〞PZ2265QZ11.2.5结晶器振动装置结构型式四连杆短臂振动弧形半径 R6000mm振动方式正弦曲线振幅±3~±6mm(实际±5)频率 0~300Hz(可调)1.2.6二冷装置活动段结构型式弧形导架体气缸摆动驱动用气缸 S型尾部悬挂式气缸Φ160×750mm气缸工作压力 0.4-0.6MPa1.2.7.二冷装置固定1段结构型式带导向夹辊托辊固定式水冷弧形导向架夹辊Φ160×180mm夹辊最大辊面间距 200mm1.2.8二冷装置固定Ⅱ段同固定Ⅰ段1.2.9拉矫机1.2.9.1拉矫机2#连铸机铸坯断面mm120×120mm 150×150mm Φ110-Φ160mm 拉坯速度m/min0.3-5m/min开口度mm85-237拉矫辊直径×宽Φ350×250mm 个数5驱动辊两个上辊驱动减速器型号F1212.1(上海新中专利)总速比430.25液压缸型号UY-TF/MI(JB/ZQ4181-97)规格Φ140/Φ100-320,Φ140/Φ100-520工作压力0-10MPa1.2.9.2辅助拉矫机2#连铸机铸坯断面mm120×120mm 150×150mm Φ110-Φ160mm拉坯速度m/min0.3-5m/min开口度mm85-237拉矫辊直径×宽Φ350×250mm 个数5驱动辊上辊单辊驱动减速器型号F1212.1(上海新中专利)总速比430.25液压缸型号UY-TF/MI( JB/ZQ4181-97)规格Φ140/Φ100-320工作压力0-10MPa1.2.10 蒸汽排出装置2#连铸机配风机 Y4-73N010D-4 左风量 44004立方米/min1.2.11 引锭杆承放装置结构型式气缸驱动,四连杆摆动摆动距离(升高×距离) 80×260mm托架个数/流 8每流驱动气缸数 2气缸型号 2#连铸机:SΦ200×250mm空气压力 0.4-0.6MPa1.2.12 引锭杆结构型式箱型对扣式半板簧引锭杆总长 111000mm节距 400mm插入结晶器长度 150mm引锭杆断面 145×143mm(150坯)115×113mm(120坯)Φ105(Φ110坯)Φ115(Φ120坯)Φ125(Φ130坯)Φ135(Φ140坯)Φ145(Φ150坯)Φ155(Φ160坯)1.2.13轨道1.2.13.1主要参数2#机结构型式辊子双轴承支座,分组集中链条传动(辊径×辊身长)输出辊道Φ165×180 冷床区Φ220×200辊道运行速度32m/min冷床区32.17m/min减速机行星摆线针轮减速器BWD18-23-2.2 i=23冷床区辊道:XWD4-29-2.2i=29链条16A-1(GB1243.1-83)1.2.13.2辊道分组(每流)输出辊道分组编号辊道名称每组辊子数辊子编号辊距mm备注Ⅰ切前辊道41~4820水冷Ⅱ切后辊道68~12900Ⅲ输出辊道(一)613~18900Ⅳ输出辊道(二)419~22900Ⅴ输出辊道(三)523~279002#机冷床区辊道Ⅰ328~3090030~31辊距1200Ⅱ431~341200Ⅲ335~3712001.2.14 双层翻转冷床(2#机)铸坯定尺 2600mm-12000mm铸坯截面 20×120mm 150×150mm Φ110-Φ160mm铸坯翻转角度 90°液压缸(2个) Y-HGI-E100×380LEI-HL10T2系统最大压力 14MPa1.2.15横向移钢机横移铸坯重量 3200Kg横移速度 23m/min横移行程 6200mm减速器 ZS82.5-1-Ⅲ型 i=51.22制动器 YWZ300/25型配YT1-25 ZC/4电力液压推动器额定推力 250N额定行程 40mm制动瓦退距 0.7mm制动力矩 320Nm1.2.16 推钢机和冷床冷床尺寸长12005mm 宽 11350mm存放铸坯最大重量 42t推钢机行程 1000mm液压缸(2个) SDG-160/110-e型行程650mm系统最大压力 14MPa1.2.17 中间包倾翻装置(2#机)倾翻速度 1.785rpm倾翻方向逆时针方向倾翻角度±180°行星减速器 NGW123-11 i=56输入1000r/min时允许输入功率7.5kw制动器 YT1-25电动液压推动器1.2.18 拉矫机干油润滑站(2#连铸机)干油润滑泵(江苏启东润滑设备有限公司)型号 HA-Ⅲ1X公称压力 40MPa额定给油量 430ml/min电机功率 1.5kw贮油筒容积 60升电动加油泵(江苏启东润滑设备有限公司)型号 DJB-V70/860公称压力 3.15MPa额定给油量 70L/H电机功率 0.37kw贮油筒容积 200升润滑介质连铸机专用脂1.2.19 二冷活动段,气动阀门站分水滤气器 QSL-25 1MPa空气减压阀 QTY-25 1MPa压力表 Y-60ZT 0-1.6MPa油雾器 QIU-25 1MPa电控电器滑阀 K25D2-15-L1 直流24v消音器 XS-L15-L11.2.20二冷固定段气动阀门站压力 0.2~0.6MPa流量 0.13~0.15立方米/min减压阀 QTY-25 G1〞 1Mpa节流阀 L41H-25电控电气滑阀 k25D2-15-L1 DC24及以下项目1.2.20.1快速调压阀1/2〞 AR4000-04 烟台未来气动组件设备有限公司技术参数:进口压力 0.7~1.0MPa压力调节范围 0.05~0.6MPa输入压力波动 0.2MPa时输入压力波动<0.02MPa压力变换时间 2~5秒1.2.20.2旋塞阀X13W-10 G1/2〞1.2.20.3压力表Y-100ZT 0~1.6MPa1.2.21火焰切割机型号:FGR3 方圆坯火焰切割车上海新中切割钢种:普碳钢、优质钢、低合金钢切割铸坯断面尺寸: 100×100 120×120 180×180 220×220 240×240 Φ100-Φ200mm铸坯最大拉速: 3.5m/min切割速度:300-450mm/min能源介质:乙炔、天然气、液化石油气、丙烷、丙烯、焦炉煤气等。
- 1、下载文档前请自行甄别文档内容的完整性,平台不提供额外的编辑、内容补充、找答案等附加服务。
- 2、"仅部分预览"的文档,不可在线预览部分如存在完整性等问题,可反馈申请退款(可完整预览的文档不适用该条件!)。
- 3、如文档侵犯您的权益,请联系客服反馈,我们会尽快为您处理(人工客服工作时间:9:00-18:30)。
【摘要】本文主要介绍了中冶京诚(ceri)自主设计的大圆坯连铸机的设计特点,保证铸坯质量所采取的技术措施、装备水平等。
连铸机所采用全程无氧化保护浇注、大容量中间罐、结晶器技术、结晶器液压振动装置、电磁搅拌技术、二冷动态控制及铸坯保温措施、铸坯导向支撑、连续矫直及拉矫机、过程检测及自动控制技术,确立了中冶京诚(ceri)在大圆坯连铸机自主设计研发领域的国内领先地位。
【关键词】大圆坯连铸设计特点装备水平中冶京诚
1 前言
由于连铸技术具有显著的高生产效率、高成材率、高质量和低成本的优点,近年来我国的连铸技术在成熟生产技术的应用、新技术的开发、应用基础研究等方面都得到了迅速发展。
随着石油、化工、铁道等行业的发展和连铸圆坯对后续加工的独特优点,市场对高质量大断面连铸圆坯的需求强劲增长。
中冶京诚(ceri)在大圆坯连铸机的核心技术领域取得了突破性进展,为用户提供了具有自主知识产权的结晶器液压振动、结晶器漏钢预报、动态二冷控制等核心技术和设备。
2008年12月,中冶京诚自行设计并制造的弧型半径r14m的φ600mm大圆坯连铸机一次性热试成功,标志着我国自主开发大断面圆坯连铸机的里程碑;2009年5月,江阴兴澄特钢厂弧型半径 r17m的φ800mm的大圆坯连铸机一次热试成功,成为世界上直径最大的圆坯连铸机;次年10月,φ900mm大圆坯热试成功,把记录再次扩大;2011年,φ1000mm连铸圆坯研发成功,再次刷新了记录,标志着我国大圆坯连铸技术水平进入了国际先进水平行列。
2 连铸机设计特点及装备水平
连铸过程是一个钢水连续填充、连续凝固的过程,铸坯要经历三个冷却区:结晶器冷却区、二次冷却区和空冷区。
在这个过程中,热量(包括过热、潜热和显热)通过传导、对流、辐射的传输方式传递出来,钢从液态钢水转变为固态坯料。
2.1 全程无氧化保护浇注
钢水的合金元素极易与空气中的氧反应生成氧化物,形成钢水的二次污染。
采取如下保护浇注工艺,可以防止浇钢过程的二次氧化:钢包和中间罐之间采用长水口保护浇注;钢包滑动水口与长水口连接处吹氩气密封;中间罐和结晶器之间采用整体式浸入水口;中间罐内采用保护渣或覆盖剂;结晶器内采用保护渣浇注等。
2.2 大容量中间罐
采用优化设计的t型中间罐内形有最佳的流场分布,同时也便于档渣墙、堰的砌筑;大容量中间罐内钢水有足够深度保证夹杂物有充分的上浮时间和更换钢包时钢水液面的稳定。
中间罐称重系统与钢包滑动水口连锁,保证浇注过程中中间罐钢水液面高度稳定;涡流液面检测系统和塞棒伺服系统闭环控制,实现结晶器钢水液位自动控制,改善铸坯表面质量;采用中间罐连续测温技术,确保连铸机生产稳定,提高铸坯内部质量。
2.3 结晶器技术
在结晶器设计上,采用内表面镀硬铬的管式结晶器和2排足辊支撑装置。
结晶器冷却水采用快速连接板方式自动连接。
针对大断面圆坯凝固收缩特点做了如下研发工作:(1)选择最佳的水缝结构和铜管的支撑方式,通过温度场计算和分析,选择最佳的冷却水量,使铜管上下的温度分布更加均匀,最大温差控制在2~6℃以内;
(2)采用高刚度的结晶器水箱设计,使铜管在全长范围内获得有效的固定支撑,确保浇注过程中足够的稳定性,以获得最佳的铸坯表面质量;
(3)结晶器铜管采用捏合抛物线锥度以适应铸坯的收缩,使铸坯在结晶器内达到最佳的冷却并形成最佳的坯壳厚度;
(4)结晶器铜管内表面采用镀硬铬技术,提高铜管的使用寿命。
2.4 结晶器液压振动装置
结晶器液压振动装置由内、外弧两个单独立的振动单元和一个振动底座组成,其振幅为0~±7.5mm、频率30~350cpm、非正弦系数可在0~0.4之间内调整。
通过在线调整液压振动参数可控制负滑脱时间在最佳范围之间,改善铸坯表面振痕深度,提高铸坯表面质量,改善结晶器润滑,减少漏钢。
该装置技术的先进性及特点如下:
(1)采用计算机仿真和有限元方法进行优化设计,保证系统长期稳定运行;
(2)采用无磨损设计,无易损件和润滑点,维修工作量小;
(3)采用高精度的预应力板簧导向,各向的偏差小(≤ 0.10mm);
(4)可在线根据拉速变化自动调整振幅、频率;
(5)通过设定非正弦系数,获得正弦和非正弦振动波形;
(6)工作过程中动态监视振动参数;
(7)对坯壳与铜管之间的摩擦力监测及润滑状态分析;
(8)安装方便,不需要额外的调试。
2.5 电磁搅拌技术
对大断面圆坯,为了尽可能获得稳定优良的冶金效果,改善铸坯的表面质量和内部质量(中心疏松和偏析),连铸机基本都配置了结晶器电磁搅拌系统(mems)和凝固末端电磁搅拌系统(fems),部分连铸机还配置了铸流电磁搅拌系统(sems)。
其中,铸流电磁搅拌和末端电磁搅拌位置可根据浇注断面的不同连续调整位置。
如表1所示。
2.6 二次动态控制及铸坯保温措施
连铸二冷区的冷却是决定铸坯质量的重要因素,这就要求对二次冷却参数进行控制,使铸坯表面温度在拉坯方向上均匀下降,并且要满足铸坯凝固冷却的冶金准则,完成弯曲矫直过程,生产出质量合格的连铸坯。
中冶京诚(ceri)根据凝固传热计算模型对圆坯的二冷设计做了总体研发设计,并在最后冷却区后至拉矫机前对铸坯采取保温措施:
二冷采用结晶器足辊区全水冷却,活动段区气水雾化冷却。
针对用户生产铸坯的不同断面和钢种,分别采用超强、强、中、弱、超弱五种水表进行冷却。
二冷控制系统采用按拉速参数动态控制方式进行控制,冷却水按照一定比例分配给不同的冷却区,同时,系统中还嵌入了中间罐钢水过热度参数。
冷却区域上部喷嘴采取特殊布置方式以获得最佳的冷却效果。
经过多年的生产实践,形成了很有特色的二冷水控制模式-准动态控制,加上优化的喷嘴布置与选型,能很好地保证铸坯的表面和内部质量。
凝固末期,由于圆坯宏观几何形状的原因,断面四周方向上的温度分布更加均匀,中心部位径向长度上含钢液量少,坯壳增长速度越来越快。
为了保证铸坯进入矫直区前温度要≥860℃,最后冷却区后至拉矫机前采取了均热保温措施。
2.7 铸坯导向支撑
由于圆坯自身的特点,其导向段的支撑与大方坯相比结构相对简单。
因此,大圆坯连铸机的导向段设计,采用活动段和多个固定段相结合的设计方案。
活动段随浇注断面更换,采取四周辊子夹持以保证铸坯的运行稳定及引锭杆的导向。
该段喷嘴采用环形交叉布置以达到最佳的冷却效果。
固定段的设计则适应不同的浇注断面,满足浇注各种断面前提下大大简化了设备结构。
2.8 连续矫直及拉矫机
为有效降低铸坯在矫直时表面及两相区的矫直应变和应力,中冶京诚(ceri)采用连续矫直技术,选取较长的矫直区,有效地降低在矫直区产生的矫直变形。
通过优化设计和计算,在浇注大断面圆坯时,保证铸坯表面和两相区的最大变形速率远远低于产生裂纹的临界值。
为满足不同断面大圆坯的矫直及克服矫直过程中产生的矫直反力,在矫直区和水平段上
每流配置5~9架拉矫机,并通过控制系统确保各拉矫机的负荷分布均衡。
2.9 过程检测及自动控制技术
采用三电一体化设计,按工艺过程控制要求,实现对整条生产线的自动、半自动、手动控制。
应用可靠的过程检测及自动控制技术,如钢水连续测温、钢包和中间罐称重、振动式下渣检测、结晶器液位检测与控制、结晶器液压振动、二冷动态控制、质量跟踪等,并对辅助系统工况进行实时监控和历史趋势记录。
大圆坯连铸机采用了技术先进的过程检测及自动控制技术,应用在多个钢铁企业的连铸项目上。
实践证明,上述技术设计合理、运行稳定、可控精度高、操作维护简便,为高质量大圆坯连铸机提供了可靠保障。
3 大圆坯连铸机工艺流程图(图1)
4 结语
上述连铸机,设备运行状态良好,其装备水平处于国内领先、国际先进的地位。
连铸机的控制模型,运行稳定、界面友好、操作方便。
连铸机所采用的核心工艺设备由中冶京诚(ceri)自主设计、研发、供货,确立了中冶京城工程技术有限公司在大圆坯连铸机自主设计研发领域的国内领先地位。
如表2所示。