单晶的塑性变形
5.2 晶体的塑性变形
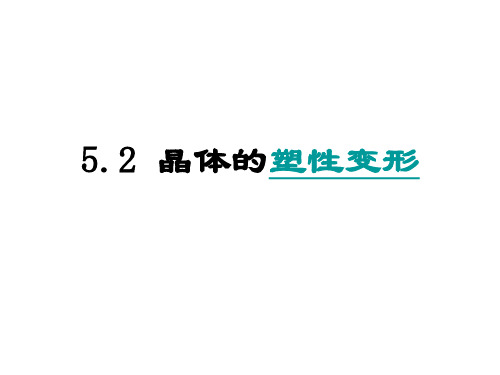
铜多晶试样拉伸后形成的滑移带, 173×
5.2.3 合金的塑性变形
• 合金分类:单相固溶体合金 多相合金 • 合金的塑性变形:单相固溶体合金塑性变形 多相合金塑性变形
一. 单相固溶体合金塑性变形
溶质原子的作用主要表现在固溶强化 (Solid—solution Strenthening)作用,提高塑性变形抗力。 1. 固溶强化 • 固溶强化:固溶体合金的σ-ε曲线:由于溶质原子加 入使σs 和整个σ-ε曲线的水平提高,同时提高了加工 硬化率n。 • 影响固溶强化的因素: ① 溶质原子类型及浓度。 ② 溶质原子与基体金属的原子尺寸差。相差大时强化 作用大。 ③ 间隙型溶质原子比置换型溶原子固溶强化效果好。 ④ 溶质原子与基体金属价电子数差。价电子数差越大, 强化作用大。 固溶强化的实质是溶质原子与位错的弹性交互作用、 化学交互作用和静电交互作用。
FCC晶体孪生变形
• FCC晶体的孪生面是(111),孪生方向是[11-2 ]。 图2是FCC晶体孪生示意图。fcc中孪生时每层晶面 的位移是借助于一个不全位错(b=a/6[11-2])的 移动造成的,各层晶面的位移量与其距孪晶面的 距离成正比。孪晶在显微镜下观察呈带状或透镜 状。每层(111)面的原子都相对于邻层(111) 晶面在[11-2 ]方向移动了此晶向原子间距的一个 分数值。 • 下图2中带浅咖啡色的部分为原子移动后形成的孪 晶。可以看出,孪晶与未变形的基体间以孪晶面 为对称面成镜面对称关系。如把孪晶以孪晶面上 的[11-2 ]为轴旋转180度,孪晶将与基体重合。 其他晶体结构也存在孪生关系,但各有其孪晶面 和孪晶方向。
(4) 孪晶的位错机制
• 孪生变形( deformation twinning )是 整个孪晶区发生均匀切变,其各层面的 相对位移是借助于一个 Shockley 不完全 位错移动而造成的。 • 形变孪晶是通过位错增值的极轴机制形 成的。(如:L型扫动位错)
单晶的塑性变形
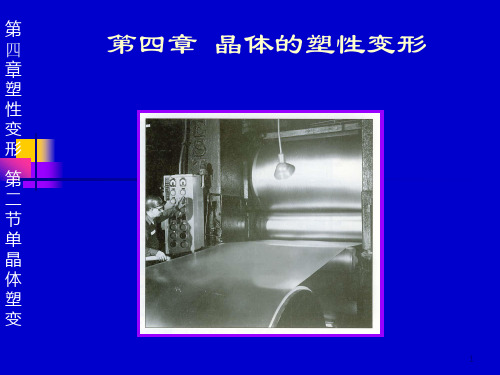
几何硬化:,远离45,滑移变得困难;
第 四 章 塑 性 变 形 第 二 节 单 晶 体 塑 变
第二节 单晶体的塑性变形
几何硬化与几何软化 · 几何硬化:如果晶体滑移面原来是处于其法线 与外力轴夹角接近45º 的位向,经滑移和转动 后,就会转到离45º 夹角越来越远的位向,从 而使滑移变得越来越困难。 几何软化:经滑移和转动后,一些原来角度远 离45º 的晶面将转到接近45º ,使滑移变得容易 进行。
第 四 章 塑 性 变 形 第 二 节 单 晶 体 塑 变
第四章 晶体的塑性变形
1
第 四 章 塑 性 变 形 第 二 节 单 晶 体 塑 变
第四章 晶体的塑性变形
纳米铜的室温超塑性
2
第 四 章 塑 性 变 形 第 二 节 单 晶 体 塑 变
第二节 单晶体的塑性变形
常温下塑性变形的主要方式:滑移、孪生、扭折。
变形机制
全位错运动的结果
分位错运动的结果
18
第 四 章 塑 性 变 形 第 二 节 单 晶 体 塑 变
第二节 单晶体的塑性变形
二 孪生 孪晶的生成方式: 变形孪晶 生长孪晶 退火孪晶
19
第 四 章 塑 性 变 形 第 二 节 单 晶 体 塑 变
第二节 单晶体的塑性变形
二 孪生 孪生的位错机制
20
不改变(对抛光面观察无 重现性)。
滑移方向上原子间距的整 数倍,较大。 很大,总变形量大。 有一定的临界分切压力 一般先发生滑移
改变,形成镜面对称关系(对抛 光面观察有重现性)
位移量 不 同 点
对塑变的贡献 变形应力 变形条件
小于孪生方向上的原子间距, 较小。 有限,总变形量小。 所需临界分切应力远高于 滑移 滑移困难时发生
金属的塑性变形与再结晶(3)
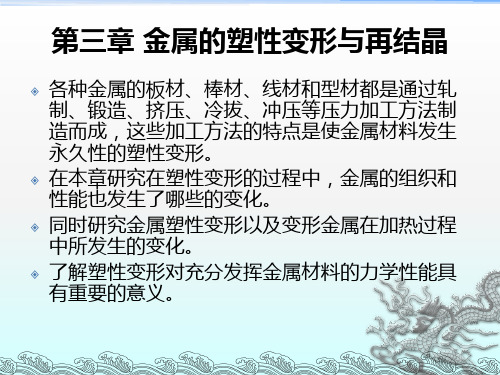
同一滑移面上若有大量的位错移出,则在晶体表 面形成一条滑移线。
位错在晶体中移动时所需切应力很小,因为当位错中心前 进一个原子间距时,一齐移动的只是位错中心少数原子, 而且其位移量都不大,形成逐步滑移,这就比一齐移动所 需的临界切应力要小得多,这称为“位错的易动性”。
研究表明,亚晶界的存在使晶体的变形抗力增加, 是引起加工硬化的重要因素之一。
3.形变织构
在塑性变形过程中,当金属按一定的方向变形量 很大时(变形量大于70%以上),多晶体中原来任 意位向的各晶粒的取向会大致趋于一致,这种有 序化结构叫作“变形织构”,又称为“择优取 向”,
金属材料的加工方式不同形成不同类型的织构: 拉拔时形成的织构称为丝织构,其特征是各个晶 粒的某一晶向平行于拉拔方向;轧制时形成的织 构称为板织构,其特征是不仅某一晶面平行于轧 制平面,而且某一晶向也平行于轧制方向。
3.变形引起的内应力
在金属塑性变形过程中,大约有10%的能量转化为内应力而残留在金属中, 使其内能增加。
这些残留于金属内部且平衡于金属内部的应力称为残余内应力。它是由于金 属在外力作用下各部分发生不均匀的塑性变形而产生的。
内应力一般可分为三种类型:Βιβλιοθήκη (1)宏观内应力(第一类内应力)
金属材料在塑性变形时,由于各部分变形不均匀,使整个工件或在较大的 宏观范围内(如表层与心部)产生的残余应力。
3.1.2多晶体金属塑性变形的特点
大多数金属材料是由多晶体组成的。 多晶体塑性变形的实质与单晶体一样。 要考虑到晶粒彼此之间在变形过程中的约束作用,以及晶界对塑性变形的影
单晶体的塑性变形原理
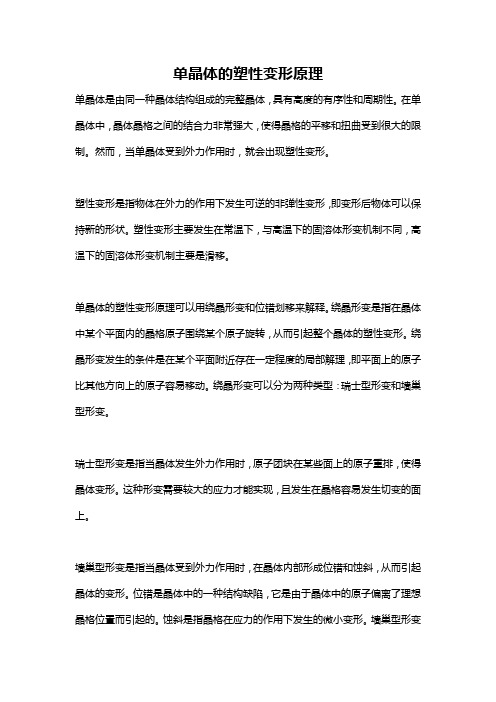
单晶体的塑性变形原理单晶体是由同一种晶体结构组成的完整晶体,具有高度的有序性和周期性。
在单晶体中,晶体晶格之间的结合力非常强大,使得晶格的平移和扭曲受到很大的限制。
然而,当单晶体受到外力作用时,就会出现塑性变形。
塑性变形是指物体在外力的作用下发生可逆的非弹性变形,即变形后物体可以保持新的形状。
塑性变形主要发生在常温下,与高温下的固溶体形变机制不同,高温下的固溶体形变机制主要是滑移。
单晶体的塑性变形原理可以用绕晶形变和位错划移来解释。
绕晶形变是指在晶体中某个平面内的晶格原子围绕某个原子旋转,从而引起整个晶体的塑性变形。
绕晶形变发生的条件是在某个平面附近存在一定程度的局部解理,即平面上的原子比其他方向上的原子容易移动。
绕晶形变可以分为两种类型:瑞士型形变和墙巢型形变。
瑞士型形变是指当晶体发生外力作用时,原子团块在某些面上的原子重排,使得晶体变形。
这种形变需要较大的应力才能实现,且发生在晶格容易发生切变的面上。
墙巢型形变是指当晶体受到外力作用时,在晶体内部形成位错和蚀斜,从而引起晶体的变形。
位错是晶体中的一种结构缺陷,它是由于晶体中的原子偏离了理想晶格位置而引起的。
蚀斜是指晶格在应力的作用下发生的微小变形。
墙巢型形变发生时,位错在晶体中移动,从而引起晶体变形。
位错划移是单晶体塑性变形的主要方式。
当晶体受到外力作用时,发生位错移动,这种移动可以看作是原子的排列发生了变化,从而引起晶格的变形。
位错划移的机制包括滑移和蠕变。
滑移是指位错在晶体中的某些面上移动,从而引起晶格的变形。
滑移的方向与晶体中原子排列的方向相吻合。
蠕变是指在晶体中,位错不仅在某些面上移动,还在垂直于该面的晶面上移动,从而引起晶体的变形。
除了绕晶形变和位错划移,单晶体的塑性变形还与材料的晶体结构和成分有关。
晶体结构的紧密性和原子间的键合方式都会影响晶体的塑性变形。
对于紧密堆积的晶体结构来说,原子之间的相互作用力较强,使得晶体更加难于发生塑性变形。
单晶体的塑性变形形变孪晶
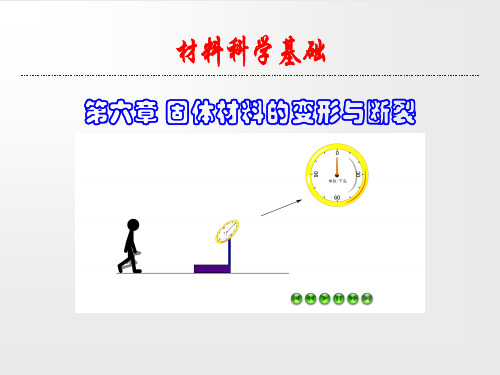
图 临界分析应力分析图
cos cos cos cos称为取向因子
s c s cos cos
τc称为临界分切应力,其数值与 晶体的类型、纯度即温度等因 素有关,还与该晶体的加工和 处理状态、变形速度以及滑移 系类型等因素有关。
2.滑移系 晶体中的滑移只能沿一定的晶面和该面上一定的晶体学方
向进行,我们将其称为滑移面和滑移方向。 滑移面和滑移方向往往是晶体中原子最密排的晶面和晶向,
这是由于最密排面的面间距最大,因而点阵阻力最小,容 易发生滑移,而沿最密排方向上的点阵间距最小,从而使 导致滑移的位错的柏氏矢量也最小。 每个滑移面以及此面上的一个滑移方向称为一个滑移系, 滑移系表明了晶体滑移时的可能空间取向。
第六章 固体材料的变形与断裂
材料在外力作用下,当外力较小时将发生弹性变形,随着 外力的逐步增大,进而会发生永久变形,直至最终断裂。 在这个过程中,不仅其形状或尺寸发生了变化,其内部组 织以及相关的性能也都会发生相应变化。
研究材料在塑性变形中的行为特点,分析其变形机理以及 影响因素具有十分重要的理论和实际意义。
图 弹性模量与原子序数的变化关系
表 几种不同材料的弹性模量
材料 钢 铜
聚乙烯 橡胶 氧化铝
E/104MPa 20.7 11 0.3
10-4~10-3 40
泊松比 0.28 0.35 0.38 0.49 0.35
§6.1.2 滞弹性
在低于弹性极限的应力范围内,实际固体的应力和应变不 是单值对应关系,往往有一个时间的滞后现象,这种特性 称为滞弹性。
工程材料 5 塑性变形
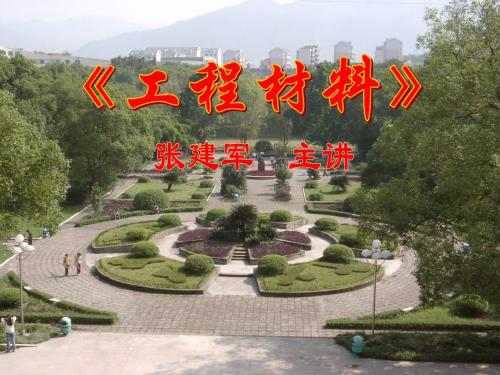
(c) 变形80%
2. 亚组织的细化 塑性变形使晶粒碎化,内部 形成更多位向略有差异的亚晶粒 (亚结构),在其边界上聚集着 大量位错。 3. 产生形变织构 由于塑性变形过程中 晶粒的转动,当变形量达 到一定程度(70%~90%) 以上时,会使绝大部分晶 粒的某一位向与外力方向 趋于一致,形成织构。
产生加工硬化
由于塑性变形的变形度增加, 使金属的强度、硬度提高,而塑 性下降的现象称为加工硬化。
二、冷塑性变形对金属组织的影响 1. 形成纤维组织 金属在外力作用下产生塑性变形时,随着外形变化,而且其 内部的晶粒形状也相应地被拉长或压偏。当变形量很大时,晶粒 将被拉长为纤维状。
(a) 未变形
(b) 变形40%
2. 再结晶退火
把冷变形金属加热到再结晶温度以上,使其产生再结晶的热处 理称为再结晶退火。 生产中金属的再结晶退火温度比其再结晶温度高100~200℃。
三、晶粒长大
再结晶完成后,若继续升高加热温度或延长保温时间,金 属晶粒将继续长大是通过晶界的迁移进行的,是大晶粒吞食小 晶粒的过程。这是一个自发的过程。 影响晶粒大小的因素除加热温度和保温时间外,还有晶粒 原始尺寸、杂质的分布、预先变形度等。加热温度和预先变形 度影响最大。
晶粒粗大会使金属的强度,特别是塑性和冲击韧性降低。
1. 加热温度和保温时间的影响 加热温度越高,保温时间越长, 金属晶粒越粗大。
黄铜再结晶后晶粒的长大
580º C保温8秒后的组织
580º C保温15分后的组织
700º C保温10分后的组织
2. 预变形度的影响
对一般金属,当变形度为2%~10%时,由于变形很不均匀, 会造成晶粒异常长大,应予避免。变形度过大(>90%),因织 构,晶粒也会粗大。通常变形度为30%~60%。
第六章 金属材料的塑性变形

15
5. 产生变形织构 金属晶粒的取向一般是无规则的随机排列,尽管每个晶粒有各 向异性,宏观性能表现出各向同性。当金属经受大量(70%以上) 的一定方向的变形之后,由于晶粒的转动造成晶粒取向趋于一致, 形成了“择优取向”,即某一晶面在某个方向出现的几率明显 高于其他方向。金属大变形后形成的这种有序化结构叫做变形 织构,它使金属材料表现出明显的各向异性。
ys 0 kd
1/ 2
式中的d为晶粒的平均直径,k为比例常数。这是个经验公式, 但又表达了一个晶界影响的普遍规律。该公式常称为霍尔-佩 奇(Hall-Petch)关系。
8
另一方面,晶界数量的增加则材料的晶粒愈细,不仅强度愈高, 而且塑性与韧性也较高。因为晶粒愈细,单位体积中的晶粒数 便愈多,变形时同样的形变量便可分散在更多的晶粒中发生, 晶粒转动的阻力小,晶粒间易于协调,产生较均匀的变形,不 致造成局部的应力集中,而引起裂纹的过早产生和发展。因而 断裂前便可发生较大的塑性形变量,具有较高的冲击载荷抗力。 所以在工业上通过各种方法(凝固、压力加工、热处理)使材 料获得细而均匀的晶粒,使目前提高材料力学性能的有效途径
之一。
9
三、塑性变形过程
局部不均匀性: 在多晶体金属中,由于每个晶 粒的晶格位向都不同,其滑移面和滑移方向的 分布便不同,故在在同一外力作用下,每个晶 粒中不同滑移面和滑移方向上所受的分切应力 便不同。取向因子较大(接近1/2),分切应力较 大的必将首先发生滑移变形,通常称这种位向 的晶粒为处于“软位向”;而滑移面或滑移方 向处于或接近于与外力相平行或垂直,即取向 因子较小(接近0)的晶粒则处于“硬位向”,它 们所受的分切应力将较小,较难发生滑移。由 此可见,由于多晶体金属中每个晶粒所取的位 向不同,金属的塑性变形将会在不同晶粒中逐 批发生,是个不均匀的塑性变形过程。
第五章 金属的塑性变形及再结晶

孪生所需要的切应力很大。
滑移易进行。
二、多晶体金属的塑性变形
1、多晶体拉伸试验
(1)多晶体和单晶体对比试验
(2)两个晶粒试样拉伸
2、多晶体塑性变形的特点
1)每个晶粒内:滑移和孪生; 2)整个晶体:既要克服晶界的阻碍,又要同周围晶粒同时发生相 适应的变形来协调配合,以保持晶粒间的结合和晶体的连续性,否 则会导致晶体破裂。
三种典型金属晶格的滑移系
(A)体心立方晶格滑移系: 6 ×2 = 12
滑移面: {110} 6个 滑移方向:<111> 2个。
{110} <111>
(B)面心立方晶格滑移系: 4 ×3 = 12
滑移面: {111} 4个 滑移方向:<110> 3个
<110>
{111}
(C)密排六方晶ห้องสมุดไป่ตู้滑移系: 1 ×3 = 3
第五章 金属的塑性变形及再结晶
锻造 挤压
车 铣
轧制
成形加工工艺
金属获得一定的形状和尺寸
拉拔
金属塑性变形
刨
切削加工工艺
金属内部组织与结构变化
钻
改变晶粒大小、形态、分布
金属加热再结晶
改善金属材料的性能
§2-1 金属的塑性变形
P
一、单晶体金属的塑性变形
在室温下,单晶体的塑性变形主要是通过滑移和孪生进行的。
1、晶粒正常长大:
再结晶后的晶粒均匀、稳速地长大的现象。发生在再结晶 晶粒细小且均匀时。(希望的长大方式) 2、晶粒异常长大:
再结晶后的晶粒不均匀,急剧长大的现象。少数处于优越条件 的晶粒优先长大,迅速吞食周围的大量小晶粒,最后得到异常粗 大的晶粒,也称“二次再结晶”。
第5章 材料的形变和再结晶3
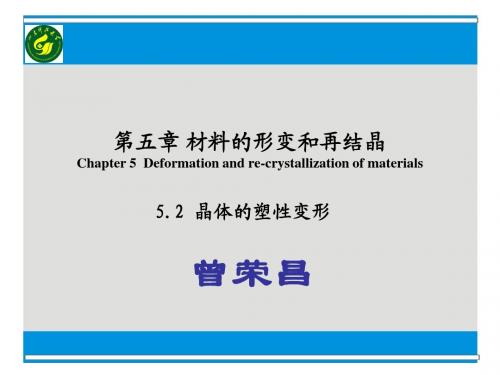
常见金属加工方法
(a) Rolling. (b) Forging (open and closed die). (c) Extrusion (direct and indirect).(d) Wire drawing. (e) Stamping.
正应力(Normal stress)的作用
作用在晶格上的正应力只能使晶格的距离加大,不能使原
子从一个平衡位置移动到另一平衡位置,不能产生塑性变形; 正应力达到破坏原子间的吸引力,晶格分离,材料则出现
断裂。
材料在正应力作用下,在应力方向虽然不能发生塑性变形, 但应力的分解在另一方向就有切应力,可使晶格沿另外的方向
三种典型晶格的滑移系
6 <11-20>
(0001)
48
面心立方 的滑移系
BCC: {110}6<111>2+{112}12<111>1+{123}24<111>1 =48
面心立方晶体中的滑移系
密排六方晶体中的滑移系
基面滑移面 圆锥滑移面
棱柱滑移面 按室温以上热激活能力的顺序密排六方镁的滑移面和滑移方向
Density)。
滑移系:由滑移面和此面上的一个滑移方向所组成。
FCC (111)Plane <110>direction
为什么滑移面往往是原子最密排的晶面?
这个问题将在后面回答
第四章金属材料的塑性变形与再结晶
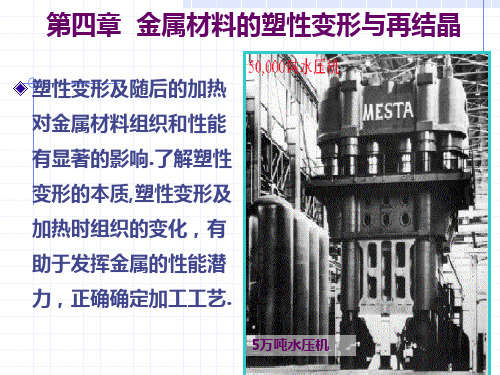
滑移方向上原子间距的 小于孪生方向上的原
整数倍,较大。
子间距,较小。
很大,总变形量大。
有限,总变形量小。
有一定的临界分切 压力 一般先发生滑移
所需临界分切应力远高于 滑移
滑移困难时发生
变形机制
全位错运动的结果 分位错运动的结果 34
(二) 多晶体金属的塑性变形
单个晶粒变形与单晶体相似,多晶体变形比单晶体复杂
① 晶界的特点:原子排列不规则;分布有大量缺陷
② 晶界对变形的影响:滑移、孪生多终止于晶界,极少穿 过。
35
当位错运动到晶界附近时,受到晶界的阻碍而堆积 起来,称位错的塞积。要使变形继续进行, 则必须增加 外力, 从而使金属的变形抗力提高。
36
晶界对塑性变形的影响
Cu-4.5Al合金晶 界的位错塞积
55
(4) 几何硬化:由晶粒转动引 起 由于加工硬化, 使已变形部 分发生硬化而停止变形, 而 未变形部分开始变形。没有 加工硬化, 金属就不会发生 均匀塑性变形。
未变形纯铁
加工硬化是强化金属的重要
手段之一,对于不能热处理
强化的金属和合金尤为重要
变形20%纯铁中的位错
56
2 对力学性能的影响
利弊
d. 孪生本身对金属塑性变形的贡献不大,但形成 的孪晶改变了晶体的位向,使新的滑移系开动, 间接对塑性变形有贡献。
33
总结
滑移
孪生
相同点
晶体位向
位移量 不 同 对塑变的贡献 点
变形应力
变形条件
1 切变;2 沿一定的晶面、晶向进行;3 不 改变结构。 不改变(对抛光面 改变,形成镜面对称关系 观察无重现性)。 (对抛光面观察有重现性)
1、晶粒取向和晶界对塑性变形的影响
第三章 金属塑性变形和加工硬化

第二阶段特征: 1)加工硬化率( Ⅱ )很高,且和应变量呈线 性关系; 2)加工硬化率对金属的种类或合金的成分(只 要为面心立方晶体)不敏感,对晶体的位向也不 敏感; 3)滑移线长度随应变量有如下规律:
2 l2
4)每根滑移线上位错数大致不变; 5)其位错结构缠结,形成胞状结构。
应力一应变曲线的另一特点是,体心立方金属的明显 屈服效应、动态形变时效现象。 原因是晶界附近最容易偏析杂质原子,由于溶质原子 特别是间隙原子与位错的相互作用强烈,柯垂尔气团 对位错的钉扎很牢,应力一应变曲线出现屈服效应现 象。当温度从室温上升时,出现动态形变时效,上下 屈服点反复出现,这种现象称为波特纹一李一沙特里 效应。
一、晶界在塑性变形中的作用
为了显示晶界对变形的影响,可将由几个晶粒 组成的大晶体承受变形并观察和测量它的变形 分布情况。如下图:
图3.6 总变形量相同时多晶铝的几个晶粒各处的实际变形量
由图可知: 1)总变形量相同时,在多晶体内,不仅各晶 粒所承受的实际变形量不同,而且每个晶粒内 部各处的实际变形程度也不一致。 2)在晶粒边界处变形程度都比晶粒内部小, 这既表明晶界处较难变形;也显示出晶界在促 进变形的不均匀分布上起很大作用。
3) 温度的影响 温度升高时,0略有降低, Ⅲ而则显著降低,
Ⅱ , Ⅲ 变短, Ⅰ 和 Ⅱ 与温度关系不大,而 Ⅲ
则随温度升高而减小。
3、FCC金属形变单晶体的表面现象
面心立方晶体研究发现,无论层错能高低,只要是 处于同一个阶段形变,都具有相同特征的表面现象。 各阶段观测研究的结果简述如下: 第1阶段;用光学显微镜一般看不到滑移线。 第Ⅱ阶段:光学显微镜在暗场下可以看到滑移线, 线长随应变的增加而递减。电镜观察到的单个滑移 线比第1阶段的粗而短。 第Ⅲ阶段:出现滑移带,带中包括靠得很近的滑移 线。应变增加时,带间不再增加新线,形变集中在 原来的带中,带端出现了碎化现象。所谓碎化现象, 系指相互连接着的滑移带的侧向移动现象。
第三章 金属材料的塑性变形
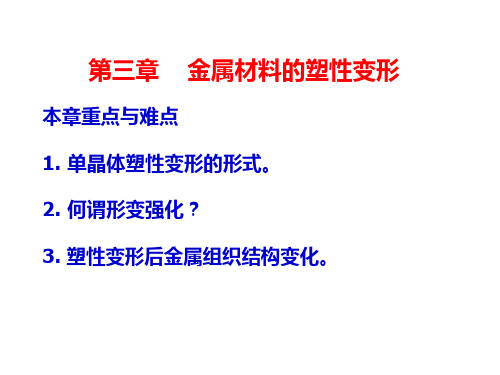
二、再结晶 1. 再结晶过程及其对金属组织、性能的影 响 变形后的金属在较高温度加热时,由于原 子扩散能力增大,被拉长(或压扁)、破碎的 晶粒通过重新生核、长大变成新的均匀、细小 的等轴晶。这个过程称为再结晶。变形金属进 行再结晶后,金属的强度和硬度明显降低,而 塑性和韧性大大提高,加工硬化现象被消除, 此时内应力全部消失,物理、化学性能基本上 恢复到变形以前的水平。再结晶生成的新的晶 粒的晶格类型与变形前、变形后的晶格类型均 一样。
二、再结晶 1. 再结晶过程及其对金属组织、性能的影 响 变形后的金属在较高温度加热时,由于原 子扩散能力增大,被拉长(或压扁)、破碎的 晶粒通过重新生核、长大变成新的均匀、细小 的等轴晶。这个过程称为再结晶。变形金属进 行再结晶后,金属的强度和硬度明显降低,而 塑性和韧性大大提高,加工硬化现象被消除, 此时内应力全部消失,物理、化学性能基本上 恢复到变形以前的水平。再结晶生成的新的晶 粒的晶格类型与变形前、变形后的晶格类型均 一样。
3.3 塑性变形后的金属在加热时组织和性能的 变化 金属经塑性变形后,组织结构和性能发生 很大的变化。如果对变形后的金属进行加热, 金属的组织结构和性能又会发生变化。随着加 热温度的提高,变形金属将相继发生回复、再 结晶和晶粒长大过程。
一、回复 变形后的金属在较低温度进行加热,会发生回复 过程。 产生回复的温度T回复为: T回复=(0.25~0.3)T熔点 式中T熔点表示该金属的熔点, 单位为绝对温度 (K)。 由于加热温度不高, 原子扩散能力不很大, 只是 晶粒内部位错、空位、间隙原子等缺陷通过移动、复 合消失而大大减少,而晶粒仍保持变形后的形态, 变 形金属的显微组织不发生明显的变化。此时材料的强 度和硬度只略有降低,塑性有增高,但残余应力则大 大降低。工业上常利用回复过程对变形金属进行去应 力退火、以降低残余内应力,保留加工硬化效果。
塑性变形

一、单晶体的塑性变形1.常温或低温下单晶体塑性变形方式: 滑移 、孪生A 、滑移:在切应力作用下,晶体的一部分沿着一定的晶面(滑移面)和晶向(滑移方向)相对于另一部分产生相对位移的过程。
B 、滑移系:晶体中一个滑移面和该面上的一个滑移方向的组合。
FCC 滑移系 {111}×<110>共有4×3=12个滑移系 BCC 滑移系可能出现的滑移面有{110}、{112}、{123} 滑移方向为<111>,如果三组滑移面都能启动,则潜在的滑移系数目为:48}123{124}112{112}110{26=⨯+⨯+⨯ 滑移面滑移方向滑移系{110}><111{211}><111{321}><111HCP 滑移系滑移面滑移方向滑移系{0001}><02111×3=3C 、滑移的临界分切应力(s τ)对滑移真正有贡献的是在滑移面上沿滑移方向的分切应力τ 临界分切应力:引起晶体滑移所需要的最小分切应力s τϕλσϕλϕλτcos cos cos cos cos /cos ===AFA Fϕλστcos cos s s =取向因子或schmid 因子——ϕλcos cos()λλλϕλ2sin 2/1)90cos(cos cos cos =︒-=软取向:晶体中有些滑移系与外力的取向λ接近45º角,取向因子最大在较小的sσ作用下τ。
通常是软取向的滑移系首先滑移。
即可达到临界分切应力sσ值才能滑移,称为硬硬取向:晶体中有些滑移系与外力取向偏离45º很远,需要较大的s取向。
D、滑移时晶体的转动正应力分量会造成晶体的转动,转动的结果:拉伸时: 滑移面趋向于与力轴平行; 滑移方向趋向于与最大切应力方向一致。
压缩时: 晶面逐渐趋于垂直于压力轴线。
拉伸时:不仅滑移面在转动,而且滑移方向也改变位向。
孪生:在切应力作用下,晶体的一部分沿一定的晶面(孪生面)和晶向(孪生方向)相对于另一部分发生均匀切变的过程。
第七章 金属的塑性变形与强化
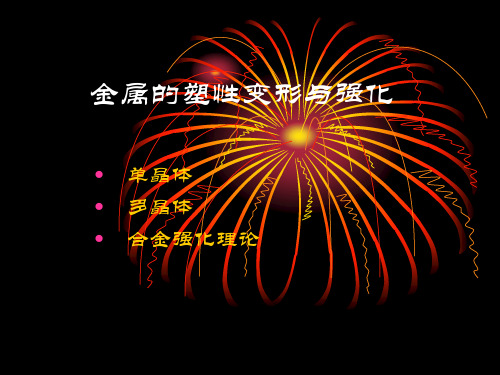
滑移系
金属中的滑移是沿着一定的晶面和晶面上一定的晶向进行的,这些晶面 称为滑移面,晶向称为滑移方向。一个滑移面和此面上的一个滑移方向结 合起来,组成一个滑移系。 滑移系表示金属晶体在发生滑移时滑移动作可能采取的空间位向。当其 它条件相同时,金属晶体中的滑移系越多,则滑移时可采取的空间位向越多, 该金属的塑性越好。
层错能较低的 FCC金属(金、银、镍 BCC 金属单晶体(铁和铌)在一定 HCP 金属(锌、镁和镉)其主要 和铜),易于出现易滑移区。随变形温度 的条件下也可以得到三阶段的应力—应 滑移系均为基面滑移,在合适的取向 的降低,第一阶段升高,硬化率有所降低, 变曲线。低于室温变形时,第一阶段开 下有利于发展易滑移变形,曲线的第 第二阶段变长而硬化率不变;随变形温度 始所需的应力随温度的降低而急剧提高; 一阶段很长,第二阶段尚未充分发展 的升高,曲线大体呈抛物线状。层错能较 在室温以上变形时,随温度的升高,第 就已经断裂。而当取向不利时,易滑 高的金属(铝),只有在低温变形,才能 二阶段应变范围减小,第三阶段应变范 移区显著缩短,而使相应的硬化率逐 得到三阶段的加工硬化曲线。 围增大。 渐提高。
应力方向。
通过这两种转动可使金属晶体轴线与外力轴线在整个滑移过程中始 终重合,但晶体的空间位向却发生了改变。 由于滑移时晶体要发生转动,所以各滑移系的取向和分切应力不断 变化。原来取向有利的滑移系可能转到不利的取向,从而使继续滑移所 需的外力增加,而原来取向不利的滑移系则可能转到有利的取向,并且 继续开始滑移。通常把这种由于晶体转动所引起的硬化或软化现象,称 为几何硬化或几何软化。
金属塑性的好坏,还与滑移面上原子的密排程度和滑移方向的数目等因 素有关。
滑移面和滑移方向与金属的晶体结构有关,滑移面通常是金属晶体中原 子排列最密的晶面,而滑移方向则是原子排列最密的晶向。这是因为在晶体 的原子密度最大的晶面上,原子间的结合力最强,而面与面之间的距离却最 大,即密排面之间的原子结合力最弱,滑移的阻力最小,因而最易于滑移。 沿原子密度最大的晶向滑动时,阻力也最小。
材料加工成型原理思考题参考答案

材料加工成型原理思考题参考答案LELE was finally revised on the morning of December 16, 20201、金属塑性变形的主要机制有哪些?单晶体的塑性变形:滑移和孪生;多晶体的塑性变形:晶内变形和晶界变形通过各种位错运动而实现的晶内一部分相对于另一部分的剪切运动,就是晶内变形。
剪切运动有不同的机理,其中最基本的是滑移、孪生和扭析。
其中滑移变形是主要的;而孪生变形是次要的,一般仅起调节作用。
在T》0.5T熔时,可能出现晶间变形。
这类变形不仅同位错运动有关,而且扩散机理起着很重要的作用。
扩散蠕变机理又包括扩散-位错机理、溶质原子定向溶解机理、定向空位流机理。
在金属和合金的塑性变形过程中,常常同时有几种机理起作用。
具体的塑性变形过程中各种机理的具体作用要受许多因素的影响。
例如晶体结构、化学成分、相状态、组织、温度、应变量和应变速率等因素的影响。
在冷态条件下,由于晶界强度高于晶内,多晶体的塑性变形主要是晶内变形,晶间变形只起次要作用,而且需要有其它变形机制相协调。
变形机理主要有:晶内滑移与孪生、晶界滑移和扩散蠕变。
热塑性变形时,通常的热塑性变形速度较快,而且高温下,由于晶界的强度低于晶内,使得晶界滑动易于进行,所以晶粒相互滑移和转动起着尤为重要的作用。
温度越高,原子动能和扩散能力就越大,扩散蠕变既直接为塑性变形作贡献,也对晶界滑移其调节作用。
热塑性变形的主要机理是晶内滑移。
2. 滑移和孪生塑性变形机制的主要区别滑移是指在力的作用下晶体的一部分沿一定的晶面和晶向相对于晶体的另一部分发生相对移动或切变,滑移总是沿着原子密度最大的晶面和晶向发生。
孪生是指晶体在切应力作用下沿着一定的晶面和一定的晶向发生均匀切变。
滑移和孪生是单晶体的主要变形机制,都是通过位错运动而实现晶内的一部分相对于另一部分的剪切运动。
但是他们也明显的区别,如下:由孪生的变形过程可知,孪生所发生的切变均匀地波及整个孪生变形区,而滑移变形只集中在滑移面上,切变是不均匀的;孪生切变时原子移动的距离不是孪生方向原子间距的整数倍(而是几分之一原子间距),而滑移时原子移动的距离是滑移方向原子间距的整数倍;孪生变形后,孪晶面两边晶体位向不同,成镜像对称;而滑移时,滑移面两边晶体位向不变;由于孪生改变了晶体的取向,因此孪晶经抛光浸蚀后仍可观察到,而滑移所造成的台阶经抛光浸蚀后不会重现;孪生的临界分切应力要比滑移的临界分切应力大得多,常萌发于滑移受阻引起的局部应力集中区;孪生变形的速度极大,常引起冲击波,发出声响;滑移时全位错运动的结果,孪生是不全位错运动。
金属材料的塑性变形

整理课件
3
2.孪生
在切应力作用下,晶体的一部分沿一定的晶面(孪晶面)和晶 向(挛晶方向)相对于另一部分所发生的切变称为孪生。
孪生与滑移的区别是: 1)孪生所需要的临界切应力比滑移大得多,变形速度极快。 2)发生切变、位向改变的这一部分晶体称为孪晶带或孪晶。 3)孪晶中每层原子沿孪生方向的相对位移距离是原子间距的分数。
⑶形变织构的产生 当变形量很大(70%以上)时,会使绝大部分 晶粒的某一位向与外力方向趋于一致,形成特殊的择优取向。择优取
向的结果形成了具有明显方向性的组织,称为织构。
整理课件
9
3.2.3 塑性变形产生的残余应力
残余应力: 金属表层与心部的变形量不同会形成表层与心部之间的
宏观内应力; 晶粒彼此之间或晶内不同区域之间的变形不均匀会形成
⑴纤维组织形成 金属在外力作用下发生塑性变形时,随着变形 量的增加晶粒形状发生变化,沿变形方向被拉长或压扁。
当拉伸变形量很大时,晶粒变成细条状,金属中的夹杂物也被 拉长,形成所谓纤维组织。
变形前后晶粒形状变化示意图
整理课件
8
⑵亚结构形成 金属经大量的塑性变形后,大量的位错聚集在 局部地区,将原晶粒分割成许多位向略有差异的小晶块,即亚晶粒。
整理课件
4
3.1.2 多晶体的塑性变形
1.晶粒取向对塑性变形的影响
在多晶体中,各个晶粒内原 子排列的位向不一致,这样 不同晶粒的滑移系的取向就 会不同。
作用在不同晶粒滑移系 上的分切应力会有差别,分 切应力最大的那些晶粒最先 开始滑移。多晶体金属的塑 性变形将会在不同晶粒中逐 批发生.
C1-第二节塑性变形与强化机制

3、振动和搅拌
整理课件 Ti变质处理
未变质处理13
(三)位错强化 1、概念
金属中的位错密度越高,则位错运动时越容易发 生相互交割,形成割阶,造成位错缠结等位错运 动的障碍,给继续塑性变形造成困难,从而提高 金属的强度,这种用增加位错密度提高金属强度 的方法称为位错强化。
金属材料经冷塑性变形后,其强度与硬度随变形 程度的增加而提高,而塑性、韧性则很快降低的 现象为加工硬化或形变强化。
10
细化晶粒不仅能提高材料的强度,还可以改善 材料的塑性和韧性。
因为晶粒越细,单位体积内的晶粒数就越多, 变形时同样的变形量可分散到更多的晶粒中发生, 以产生比较均匀的变形,这样,因局部应力集中而 引起材料开裂的几率较小,使材料在断裂前就有可 能承受较大的塑性变形,得到较大的伸长率、断面 收缩率和具有较高的冲击载荷抗力。
整理课件
14
例如:自行车链条板(16Mn钢板) 原始厚度3.5mm 150HB 五次冷轧后1.2mm 275HB
b=520MPa b>1000MPa
又如:冷拔高强度钢丝和冷卷弹簧是利用加工变 形来提高他们的强度和弹性极限;坦克和拖拉机 的履带、破碎机的颚板以及铁路的道叉等也都是 利用加工硬化来提高他们的硬度和耐磨性的。
第二节 塑性变形与强化机制
一、单晶体的塑性变形
1、滑移
当作用在位错上的切应力达到某一临界值时, 晶体的一部分将沿着一定的晶面(滑移面)和 一定的方向(滑移方向)发生相对的滑动,产 生了相对的位移。
整理课件
1
滑移的特征
滑移只能在切应力 的作用下发生
滑移的结果:
不同加载方式发生塑性变形的 能力不同。拉伸、扭转、压缩 塑性变形能力依次增加。
单晶体的塑性变形-1

• Structure: close-packed planes & directions are preferred.
close-packed plane (bottom)
ห้องสมุดไป่ตู้
close-packed directions close-packed plane (top)
view onto two close-packed planes.
bcc滑移系数目最多,但不能同时启动, 通常塑性不如fcc金属好。
材料的变形与再结晶
(3)hcp滑移系 滑移方向为< 1,1,-2,0>,滑移面为(0001)或 棱柱面{ 1,0,-1,0}、棱锥面{1,0,-1,1}
hcp滑移系数目较 少,故密排六方 金属的塑性通常 都不太好。
材料的变形与再结晶
• If dislocations don't move, deformation doesn't happen!
材料的变形与再结晶
晶体的滑移借助位错在滑移面上的运动逐步实现的
1. 位错的启动力
(位错中心偏离平衡位置引起晶体能量增加,构成 能垒-位错运动阻力,Peierls-Nabarro力)
2G 2πa exp[− ] τ≈ 1 −ν (1 − ν )b
σ
τR = σ cos λ cos φ
σ
σ
τR = 0 λ=90º
τR = 0 φ=90º
τR = σ/2 λ=45º φ=45º
λ=90º- φ 当 φ=45º 时,取向因子有最大值 1/2 ,此时得 到最大分切应力,滑移处于最有利的取向,也 称软取向。 当 φ=00 、 90o 时 , 取 向 因 子 为 0 , 称 为 硬 取 向。 最大分切应力正好落在与外力轴成45º角的晶 面以及与外力轴成45º角的滑移方向上。
- 1、下载文档前请自行甄别文档内容的完整性,平台不提供额外的编辑、内容补充、找答案等附加服务。
- 2、"仅部分预览"的文档,不可在线预览部分如存在完整性等问题,可反馈申请退款(可完整预览的文档不适用该条件!)。
- 3、如文档侵犯您的权益,请联系客服反馈,我们会尽快为您处理(人工客服工作时间:9:00-18:30)。
cosλ cosφ
称为取向因子,取向因子 越大,则分切应力越大。
材料的变形与再结晶
• Crystals slip due to a resolved shear stress, τ. • Applied tension can produce such a stress.
Al易交滑 移,产生 波纹状滑 移带
材料的变形与再结晶
4. 复滑移
主滑移系 共轭滑移系 随一次滑移进行,晶体的取向相对于加载轴发 生变化,到一定程度后,另一个等同的滑移系也 能启动,称共轭滑移系。
材料的变形与再结晶
三、滑移过程的次生现象
滑移产生的不均匀塑性 变形区: 1. 扭折带 2. 形变带
材料的变形与再结晶
Mg (HCP)
Al (FCC)
tensile direction
6
材料的变形与再结晶
3.临界分切应力定律
滑移的临界分切应力:只有当外力在某 一滑移系中的分切应力达到一定临界值 时,该滑移系方可以首先发生滑移,该分 切应力称为滑移的临界分切应力。
分切应力τ作用在滑移 方向使晶体产生滑移, 其大小为:
材料的变形与再结晶
(1)fcc滑移系 滑移方向<110>,滑移面{111} 面心立方结构共有4×3=12个滑移系
材料的变形与再结晶
(2)bcc滑移系
滑移方向为<111>,可能出现的滑移面有 {110}、{112}、{123},如果三组滑移面都 能启动,则潜在的滑移系数目为:
6× 2 + 12 × 1 + 24 × 1 = 48 {110} {112} {123}
组滑移面同时转到有利位向,使滑移可能在两组或更 多的滑移面上同时或交替地进行,形成“双滑移”或 “多滑移”。
多滑移时两个滑移面上的位错产生相互作用,形成割 阶或扭折,使位错进一步运动的阻力增加,因此多 系滑移比单系滑移要困难。
两根互相垂 直的刃型位
错的交割
刃型位错中 两个螺型位 刃型位错与
的 割 阶 与 扭 错的交割
第三章第二节
单晶体的塑性变形
《材料科学基础》第九章第二节
材料的变形与再结晶
单晶体金属的塑性变形
塑性变形:当外加应力超过一定值(屈服 极限 )时,应力和应变不再呈线性关系, 卸载后变形也不能完全消失,而会留下一 定的残余变形或永久变形,这种不可恢复 的变形称塑性变形。
微观上,单晶体中的塑性变形有两个基本 方式:滑移和孪生。
• Condition for dislocation motion:
• Crystal orientation can make it easy or hard to move disl.
σ τR= σ cos λ cos φ σ
τR > τCRSS
typically 10 -4G to 10 -2G
Adapted from Fig. 7.8, Callister 6e.
二、滑移的位错机制
晶体的滑移借助位错在滑移面上的运动逐步实现的
DISLOCATION MOTION
• Produces plastic deformation, • Depends on incrementally breaking
τ ≈ 2G exp[− 2πa ]
1−ν
(1 −ν )b
a为滑移面的面间距,b为滑移方向上的原子间距
密排面(a大),密排方向(b小),故派纳力较小 →滑移系的确定
材料的变形与再结晶
2.多系滑移
单滑移:只有一个特定的滑移系处于最有利位置而优 先开动,形成单滑移。
多系滑移:由于变形时晶体转动的结果,有两组或几
材料的变形与再结晶
一、滑移
1. 滑移现象
滑移线; 滑移带; 台阶
当应力超过晶体的弹性极限 后,晶体中就会产生层片之 间的相对滑移,大量的层片 间滑动的累积就构成晶体的 宏观塑性变形。 对滑移线的观察也表明了晶 体塑性变形的不均匀性,滑 移只是集中发生在一些晶面 上,而滑移带或滑移线之间 的晶体层片则未产生变形, 只是彼此之间作相对位移而 已。
面心立方晶体的滑移系共有{111}4<110>3=12个; 体心立方晶体,可同时沿{110}{112}{123}晶面滑移,故滑移 系共有{110}6<111>2+{112}12<111>1+{123}24<111>1=48个; 密好六方晶体的滑移系仅有(0001)1 3=3个。由于滑移系数目 太少,hcp多晶体的塑性不如fcc或bcc的好。
σ
τR = 0 λ=90º
τR = 0 φ=90º
τR = σ/2
λφ==4455ºº
λ=90º- φ 当φ=45º时,取向因子有最大值1/2,此时得
到最大分切应力,滑移处于最有利的取向,也 称软取向。
当 φ=00 、 90o 时 , 取 向 因 子 为 0 , 称 为 硬 取 向。 最大分切应力正好落在与外力轴成45º角的晶 面以及与外力轴成45º角的滑移方向上。
Applied tensile stress: σ = F/A
F A
slipdirection
F
Resolved shear stress: τR=Fs /As
Relation between σ and τR
slip plane normal, ns
Fs
slipdirectioτnR
τR
τR=Fs /As
螺型位错的
折形成
交割
带割阶位错 的运动
材料的变形与再结晶
如果发生双滑移或多系滑移,会出现Βιβλιοθήκη 叉形的滑移带交叉形的滑移带
3. 交滑移
螺位错在不改变滑移方向的情况下,从一个滑 移面转到另一个滑移面的过程。
材料的变形与再结晶
扩展位错的交滑移:不全位错须先束集为全螺位错, 再进行交滑移。
Cu不易交 滑移,无 波纹状滑 移带
材料的变形与再结晶
滑移带示意图
2. 滑移系
塑性变形时位错只沿着一定的晶面和晶向运动,这些 晶面和晶向分别称为“滑移面”和“滑移方向”。晶体结 构不同,其滑移面和滑移方向也不同。
一个滑移面(通常为密排面)和此面上的一个滑移方 向(通常为密排晶向)合起来叫做一个滑移系。
在其他条件相同时,晶体中的滑移系愈多,滑移过程 可能采取的空间取向便愈多,滑移容易进行,它的塑 性便愈好。
bonds.
• If dislocations don't move, deformation doesn't happen!
材料的变形与再结晶
晶体的滑移借助位错在滑移面上的运动逐步实现的
1. 位错的启动力
(位错中心偏离平衡位置引起晶体能量增加,构成 能垒-位错运动阻力,Peierls-Nabarro力)
• Structure: close-packed planes & directions are preferred.
close-packed plane (bottom)
view onto two close-packed planes.
close-packed directions
close-packed plane (top)
As
Fcos λ A/cos φ
F
λ
slipdirection
Fs
nsφ
A As
τR= σ cos λ cos φ
推导
滑移面面积: Q = A cos φ
作用在此滑移面的滑移 方向上的分力 :
F cosλ
作用在滑移面上 的分切应力:
τ = F cosφ cos λ = σ cosφ cos λ
A
CRITICAL RESOLVED SHEAR STRESS
bcc滑移系数目最多,但不能同时启动, 通常塑性不如fcc金属好。
材料的变形与再结晶
(3)hcp滑移系 滑移方向为< 1,1,-2,0>,滑移面为(0001)或 棱柱面{ 1,0,-1,0}、棱锥面{1,0,-1,1}
hcp滑移系数目较 少,故密排六方 金属的塑性通常 都不太好。
材料的变形与再结晶
最大分切应力正好落在与外力轴成45º角的 晶面以及与外力轴成45º角的滑移方向上。
τR= σ cos λ cos φ
σ
τR = σ/2
λ=45º φ =45º
Plastically stretched zinc single crystal.
Adapted from Fig. 7.9, Callister 6e. (Fig. 7.9 is from C.F. Elam, The Distortion of Metal Crystals, Oxford University Press, London, 1935.)
• Comparison among crystal structures:
FCC: many close-packed planes/directions; HCP: only one plane, 3 directions; BCC: none
• Results of tensile testing.