丝网印刷中常见的问题及解答
丝网印刷常见故障及对策

丝网印刷常见故障及对策一、糊版糊版(堵版),指丝印图文在印刷中不能将油墨印到材料上的现象。
丝印糊版原因是错综复杂的。
1.材料原因材料平滑度低,表面强度较差,印刷中产生掉粉、掉毛现象,会导致糊版。
2.车间温度、湿度及油墨性质原因丝印车间要保持一定的温度和相对湿度。
温度高,相对湿度低,油墨溶剂就很快挥发掉,油墨粘度变高,堵住网孔,停机时间过长,也会糊版,时间越长糊版越严重。
环境温度低,油墨流动性差也容易产生糊版。
3.丝网印版的原因网版在使用前要干净并干燥。
如果制好版放置过久不及时印刷,在保存过程中或多或少就会粘附尘土,印刷时如不清洗,就会造成糊版。
4.印刷压力的原因压力过大刮板与网版和材料不是线接触而呈面接触,这样每次刮印都不能将油墨刮干净,而留下残油,经过一定时间便会结膜造成糊版。
5.丝网印版与材料间隙不当的原因网版与材料间隙过小,间隙过小在刮印后网版不能脱离材料,网版抬起时,印版底粘附油墨,这样也容易糊版和粘版。
6.油墨的原因油墨颗粒较大时,容易出现堵住网孔的现象。
因此要过滤油墨。
油墨干燥过快,容易糊版。
特别是在使用挥发干燥型油墨时更为突出. 用氧化干燥型油墨,糊版现象出现得不是很多,如果过量使用干燥剂,也会发生糊版,油墨溶剂蒸发,使油墨粘度增高,而发生封网现象。
如果面积比较大,网版油墨消耗少,就容易造成糊版,(是经常换用新油墨)。
油墨的流动性差,会使用油墨在没有通过丝网时便产生糊版,(降低油墨粘度提高油墨的流动性来解决)。
发生糊版故障后,针对油墨的性质,用适当的溶剂擦洗。
擦洗的要领是从印刷面开始,由中间向外围轻轻擦拭。
擦拭后检查印版,如有缺损应及时修补,修补后可重新开始印刷。
应注意的是,版膜每擦一次,就变薄一些.二、油墨在材料上固着不牢1.材料印刷前应对随印材料进行印前处理的检查。
当材料表面附着油脂类、粘接剂、尘埃物等物质时,会造成油墨与材料粘接不良。
2材料在印刷时为提高与油墨的粘着性,必须进行表面处理,须除尘后才印刷.三、锯齿丝印出现锯齿(包括残缺或断线)。
丝印常见问题分析与解决
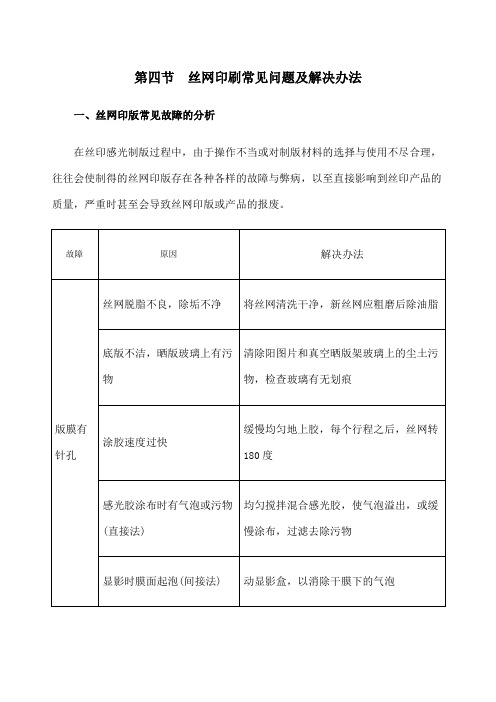
第四节丝网印刷常见问题及解决办法一、丝网印版常见故障的分析在丝印感光制版过程中,由于操作不当或对制版材料的选择与使用不尽合理,往往会使制得的丝网印版存在各种各样的故障与弊病,以至直接影响到丝印产品的质量,严重时甚至会导致丝网印版或产品的报废。
二、丝网印刷故障及对策丝印故障的产生,有单一方面原因的,但更多的则是错综复杂诸原因的交叉影响的结果。
这是操作者在判定故障原因,采取相应对策时要特别注意的。
(一)、糊版糊版亦称堵版,是指丝网印版图文通孔部分在印刷中不能将油墨转移到承印物上的现象。
这种现象的出现会影响印刷质量,严重时甚至会无法进行正常印刷。
丝网印刷过程中产生的糊版现象的原因是错综复杂的。
糊版原因从以下各方面进行分析。
1、印物的原因。
丝网印刷承印物是多种多样的,承印物的质地特性也是产生糊版现象前一个因素。
例如:纸张类、木桩类、织物类等承印物表面平滑度低,表面强度较差,在印刷过程中比较容易产生掉粉、掉毛现象,因而制成糊版。
1、车间温度、湿度油墨性质的原因。
2、丝网印刷车间要求保持一定的温度和相对湿度。
如果温度高,相对湿度低,油墨中的挥发溶剂就会很快地挥发掉,油墨的黏度变高,从而堵住网孔。
另一点应该注意的是,如果停机时间过长,也会产生糊版现象,时间越长糊版越严重。
其次是,如果环境温度低,油墨流动性差也容易产生糊版。
3、丝网印版的原因。
制好的丝网印版在使用前用水冲洗干净并干燥后方能使用。
如果制好版后放置过久不及时印刷,在保存过程中或多或少就会黏附尘土,印刷时如不清洗,就会造成糊版。
4、印刷压力的原因。
印刷过程中压印力过大,会使刮板弯曲,刮板与丝网印版和承印物不是线接触,而呈面接触,这样每次刮印都不能将油墨刮干净,而留下残余油墨,经过一定时间便会结膜造成糊版。
5、丝网印版与承印物间隙不当的原固。
丝印版与承印物之间的间隙不能过小,间隙过小在刮印后丝网印版不能脱离承印物,丝网印版抬起时,印版底部黏附一定油墨,这样也容易造成糊版。
丝网印刷中常见故障及解决方法

丝网印刷中常见故障及解决方法:一、糊版糊版(堵版),指丝印图文在印刷中不能将油墨印到材料上的现象。
丝印糊版原因就是错综复杂的。
1、材料原因材料平滑度低,表面强度较差,印刷中产生掉粉、掉毛现象,会导致糊版。
2、车间温度、湿度及油墨性质原因丝印车间要保持一定的温度与相对湿度。
温度高,相对湿度低,油墨溶剂就很快挥发掉,油墨粘度变高,堵住网孔,停机时间过长,也会糊版,时间越长糊版越严重。
环境温度低,油墨流动性差也容易产生糊版。
3、丝网印版的原因网版在使用前要干净并干燥。
如果制好版放置过久不及时印刷,在保存过程中或多或少就会粘附尘土,印刷时如不清洗,就会造成糊版。
4、印刷压力的原因压力过大刮板与网版与材料不就是线接触而呈面接触,这样每次刮印都不能将油墨刮干净,而留下残油,经过一定时间便会结膜造成糊版。
5、丝网印版与材料间隙不当的原因网版与材料间隙过小,间隙过小在刮印后网版不能脱离材料,网版抬起时,印版底粘附油墨,这样也容易糊版与粘版。
6、油墨的原因油墨颗粒较大时,容易出现堵住网孔的现象。
因此要过滤油墨。
油墨干燥过快,容易糊版。
特别就是在使用挥发干燥型油墨时更为突出、用氧化干燥型油墨,糊版现象出现得不就是很多,如果过量使用干燥剂,也会发生糊版,油墨溶剂蒸发,使油墨粘度增高,而发生封网现象。
如果面积比较大,网版油墨消耗少,就容易造成糊版,(就是经常换用新油墨)。
油墨的流动性差,会使用油墨在没有通过丝网时便产生糊版,(降低油墨粘度提高油墨的流动性来解决)。
发生糊版故障后,针对油墨的性质,用适当的溶剂擦洗。
擦洗的要领就是从印刷面开始,由中间向外围轻轻擦拭。
擦拭后检查印版,如有缺损应及时修补,修补后可重新开始印刷。
应注意的就是,版膜每擦一次,就变薄一些、二、油墨在材料上固着不牢1、材料印刷前应对随印材料进行印前处理的检查。
当材料表面附着油脂类、粘接剂、尘埃物等物质时,会造成油墨与材料粘接不良。
2材料在印刷时为提高与油墨的粘着性,必须进行表面处理,须除尘后才印刷、三、锯齿丝印出现锯齿(包括残缺或断线)。
丝网印刷常见故障报警及处理方法

丝网印刷常见故障报警及处理方法丝网印刷是一种常用的印刷方式,但在操作过程中常常会遇到一些故障和报警情况,下面将介绍一些丝网印刷常见的故障、报警以及处理方法。
1.丝网粘住物料或工件故障原因:丝网张力不够、墨版座歪斜或错位、工件表面不平整等。
处理方法:检查丝网张力是否调整合适,需要根据实际印刷要求调整;调整墨版座使其与工作台平行并调整合适的座位位置;如果是工件表面不平整导致的问题,则需要考虑更换工件或采取其他措施进行修整。
2.墨版压力不均匀故障原因:墨版座错位、墨罩与墨版不平行、墨罩压力调整不当等。
处理方法:调整墨版座使其与工作台平行并调整合适的座位位置;保证墨罩与墨版接触部分平行,可以调整墨罩的角度或采用补偿垫片等方法;检查、调整墨罩压力,确保墨版与工作台之间的距离均匀。
3.墨版的镀网不良故障原因:镀网均匀度不够、网眼堵塞等。
处理方法:加强对墨版镀网质量的检查和控制,确保镀网均匀、完整;定期检查网眼是否堵塞,及时清理。
4.墨水不均匀故障原因:墨罩调整不当、腐蚀沟纹不明显等。
处理方法:调整墨罩使其与墨版接触均匀,墨水能够均匀分布;定期清理腐蚀沟纹,以保证墨水流畅。
1.墨水不足报警报警原因:墨水不足。
处理方法:及时添加墨水,注意墨水的储存和使用量的控制。
2.丝网张力异常报警报警原因:丝网张力过大或过小。
处理方法:根据报警提示进行调整,适当调整丝网张力。
3.墨罩压力异常报警报警原因:墨罩压力过大或过小。
处理方法:根据报警提示进行调整,适当调整墨罩压力。
4.墨版座异常报警报警原因:墨版座错位或损坏。
处理方法:检查墨版座的位置和状态,如有必要,则进行更换或修复。
总之,丝网印刷过程中常见的故障和报警情况很多,但只要掌握了正确的处理方法,就能快速有效地解决问题。
及时对丝网印刷设备进行维护和保养,做好印刷过程的质量控制,可以减少故障和报警的发生,提高印刷效率和产品质量。
丝网印刷常见的问题以及解决的方法

丝网印刷常见的问题以及解决的方法:第一道:1.上料台Feed C/V2经常会有承载盒不到位引起的报警,可以分为两种:一种是Magazine 处在Down的位置,只要把盒子推到位就可以了;另一种是Magazine 处在Up 的位置,那时你推盒子是推不动的,因为被卡死了,只要让Magazine 处在Down 位置再把盒子推到位就行了。
2.Wafer transfer 经常会吸住承载盒内的拖盘而报警,原因是盒子上端开口比较大,拖盘挡住了感应器而造成,只要将拖盘放正,把Wafer Fransfer移到另一个位置就行了,把盒子整一下。
3.Wafer transfer 有吸两片的现象,方法有a .调节风刀的大小和风刀吹风的位置; b .调节四个吸嘴的高低;c .调慢气缸的上升速度;d ,风刀吹风的时间。
4.Alignment 因为硅片碎掉,摄想头定位出现报警而造成的机械手不动作,方法有a .放好片子上重新照点定位就可以;b .如果a 不行,只有甩源关掉,用手将Alignment 推离StandbyP1的位置,然后重新启动电源,让Alignment 有一个复位的过程旧可以了。
5.印刷台面有压板的现象,原因有:网板下面胶带粘的太多太厚,员工在装片时没有注意硅片与硅片之间是否有小碎片或灰尘,印刷台面没有调平或是刚带打毛,硅片本身有受过伤或裂痕。
第二道:背电场有铝包或是铝珠:1.印刷太薄2.绒面过大而且不均匀3网版折痕严重1.背电场造成弯曲的原因:铝背场印刷太厚,影响印刷厚薄有几个参数:(1)丝网间距;(2)刮刀高度;(3)印刷速度;(4)气动压力四个参数中如果有三个参数不变,那么丝网间距抬高,背电场印厚,刮刀高度越低背电场约厚,印刷速度越快,背电场越厚,但速度超过一定量时,背电场又会变薄,气动压力越小背电场变厚。
2.背电场粘板的问题原因: 1.丝网间距过底,刮刀高度过小,使网板内还留有铝浆,而将硅片粘起;2.真空吸孔堵塞或是真空发生器有问题;3.台免平整速度有问题,使硅片没有平铺在台面上而造成漏真空。
丝网印刷中常见故障的分析及处理
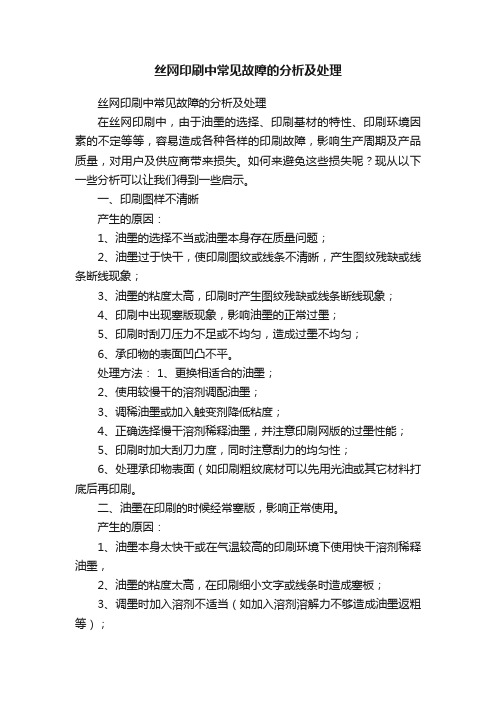
丝网印刷中常见故障的分析及处理丝网印刷中常见故障的分析及处理在丝网印刷中,由于油墨的选择、印刷基材的特性、印刷环境因素的不定等等,容易造成各种各样的印刷故障,影响生产周期及产品质量,对用户及供应商带来损失。
如何来避免这些损失呢?现从以下一些分析可以让我们得到一些启示。
一、印刷图样不清晰产生的原因:1、油墨的选择不当或油墨本身存在质量问题;2、油墨过于快干,使印刷图纹或线条不清晰,产生图纹残缺或线条断线现象;3、油墨的粘度太高,印刷时产生图纹残缺或线条断线现象;4、印刷中出现塞版现象,影响油墨的正常过墨;5、印刷时刮刀压力不足或不均匀,造成过墨不均匀;6、承印物的表面凹凸不平。
处理方法: 1、更换相适合的油墨;2、使用较慢干的溶剂调配油墨;3、调稀油墨或加入触变剂降低粘度;4、正确选择慢干溶剂稀释油墨,并注意印刷网版的过墨性能;5、印刷时加大刮刀力度,同时注意刮力的均匀性;6、处理承印物表面(如印刷粗纹底材可以先用光油或其它材料打底后再印刷。
二、油墨在印刷的时候经常塞版,影响正常使用。
产生的原因:1、油墨本身太快干或在气温较高的印刷环境下使用快干溶剂稀释油墨,2、油墨的粘度太高,在印刷细小文字或线条时造成塞板;3、调墨时加入溶剂不适当(如加入溶剂溶解力不够造成油墨返粗等);4、油墨本身的颗粒太粗,而使用印版网目过高,油墨不能正常过网。
处理方法:1、更换慢干形的油墨或根据印刷环境使用较慢干的溶剂调配油墨;2、调稀油墨或加入触变剂降低粘度;3、使用指定的溶剂稀释油墨,使油墨能够正常溶解或分散;4、更换细度更高的油墨。
三、印刷品出现明显网纹产生的原因:1、油墨过于快干;2、油墨的粘度太高,流动性不够;3、使用的网目太粗处理方法:1、使用较慢干的溶剂调配油墨;2、调稀油墨或加入触变剂降低粘度,提高油墨的流动性能;3、使用较高目数网纱。
四、印刷品出现明显水波纹产生的原因:油墨太稀或粘度太低,印刷时网距过低,印刷时产生油墨倒粘;排除方法:减少油墨中加入的溶剂份量,保持油墨的粘度同时适当调高网距,使印刷时能自然回弹五、油墨干燥不良产生的原因:1、选用溶剂不当,腐蚀底材(特别是印刷印刷软质PVC或覆膜尼龙布时容易产生);2、溶剂过于慢干或干燥时间不足;处理方法: 1、选择与底材相适应的溶剂;2、选用较快干溶剂或延长干燥时间六、油墨附着力不良产生的原因:1、选用油墨与底材不适应;2、底材表面不干净,有油污或表面处理剂等(如:防腐剂、脱膜剂等);另外,一些特殊材料,由于表面张力过低也会影响油墨的附着力;3、干燥时间不足,油墨没有完全固化;4、过多加入助剂或加入助剂不当。
丝印常见问题分析与解决
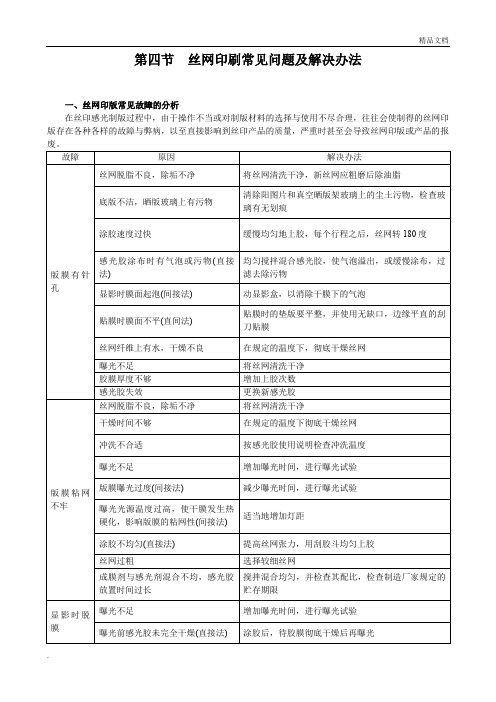
第四节丝网印刷常见问题及解决办法一、丝网印版常见故障的分析在丝印感光制版过程中,由于操作不当或对制版材料的选择与使用不尽合理,往往会使制得的丝网印版存在各种各样的故障与弊病,以至直接影响到丝印产品的质量,严重时甚至会导致丝网印版或产品的报二、丝网印刷故障及对策丝印故障的产生,有单一方面原因的,但更多的则是错综复杂诸原因的交叉影响的结果。
这是操作者在判定故障原因,采取相应对策时要特别注意的。
(一)、糊版糊版亦称堵版,是指丝网印版图文通孔部分在印刷中不能将油墨转移到承印物上的现象。
这种现象的出现会影响印刷质量,严重时甚至会无法进行正常印刷。
丝网印刷过程中产生的糊版现象的原因是错综复杂的。
糊版原因从以下各方面进行分析。
1、印物的原因。
丝网印刷承印物是多种多样的,承印物的质地特性也是产生糊版现象前一个因素。
例如:纸张类、木桩类、织物类等承印物表面平滑度低,表面强度较差,在印刷过程中比较容易产生掉粉、掉毛现象,因而制成糊版。
1、车间温度、湿度油墨性质的原因。
2、丝网印刷车间要求保持一定的温度和相对湿度。
如果温度高,相对湿度低,油墨中的挥发溶剂就会很快地挥发掉,油墨的黏度变高,从而堵住网孔。
另一点应该注意的是,如果停机时间过长,也会产生糊版现象,时间越长糊版越严重。
其次是,如果环境温度低,油墨流动性差也容易产生糊版。
3、丝网印版的原因。
制好的丝网印版在使用前用水冲洗干净并干燥后方能使用。
如果制好版后放置过久不及时印刷,在保存过程中或多或少就会黏附尘土,印刷时如不清洗,就会造成糊版。
4、印刷压力的原因。
印刷过程中压印力过大,会使刮板弯曲,刮板与丝网印版和承印物不是线接触,而呈面接触,这样每次刮印都不能将油墨刮干净,而留下残余油墨,经过一定时间便会结膜造成糊版。
5、丝网印版与承印物间隙不当的原固。
丝印版与承印物之间的间隙不能过小,间隙过小在刮印后丝网印版不能脱离承印物,丝网印版抬起时,印版底部黏附一定油墨,这样也容易造成糊版。
丝网印刷常见故障及处理方法
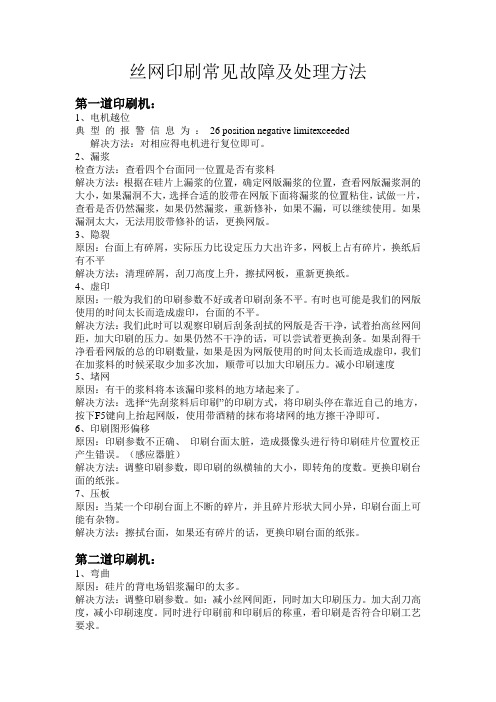
丝网印刷常见故障及处理方法第一道印刷机:1、电机越位典型的报警信息为:26 position negative limitexceeded解决方法:对相应得电机进行复位即可。
2、漏浆检查方法:查看四个台面同一位置是否有浆料解决方法:根据在硅片上漏浆的位置,确定网版漏浆的位置,查看网版漏浆洞的大小,如果漏洞不大,选择合适的胶带在网版下面将漏浆的位置粘住,试做一片,查看是否仍然漏浆,如果仍然漏浆,重新修补,如果不漏,可以继续使用。
如果漏洞太大,无法用胶带修补的话,更换网版。
3、隐裂原因:台面上有碎屑,实际压力比设定压力大出许多,网板上占有碎片,换纸后有不平解决方法:清理碎屑,刮刀高度上升,擦拭网板,重新更换纸。
4、虚印原因:一般为我们的印刷参数不好或者印刷刮条不平。
有时也可能是我们的网版使用的时间太长而造成虚印,台面的不平。
解决方法:我们此时可以观察印刷后刮条刮拭的网版是否干净,试着抬高丝网间距,加大印刷的压力。
如果仍然不干净的话,可以尝试着更换刮条。
如果刮得干净看看网版的总的印刷数量,如果是因为网版使用的时间太长而造成虚印,我们在加浆料的时候采取少加多次加,顺带可以加大印刷压力。
减小印刷速度5、堵网原因:有干的浆料将本该漏印浆料的地方堵起来了。
解决方法:选择“先刮浆料后印刷”的印刷方式,将印刷头停在靠近自己的地方,按下F5键向上抬起网版,使用带酒精的抹布将堵网的地方擦干净即可。
6、印刷图形偏移原因:印刷参数不正确、印刷台面太脏,造成摄像头进行待印刷硅片位置校正产生错误。
(感应器脏)解决方法:调整印刷参数,即印刷的纵横轴的大小,即转角的度数。
更换印刷台面的纸张。
7、压板原因:当某一个印刷台面上不断的碎片,并且碎片形状大同小异,印刷台面上可能有杂物。
解决方法:擦拭台面,如果还有碎片的话,更换印刷台面的纸张。
第二道印刷机:1、弯曲原因:硅片的背电场铝浆漏印的太多。
解决方法:调整印刷参数。
如:减小丝网间距,同时加大印刷压力。
丝网印刷问题的解决方法
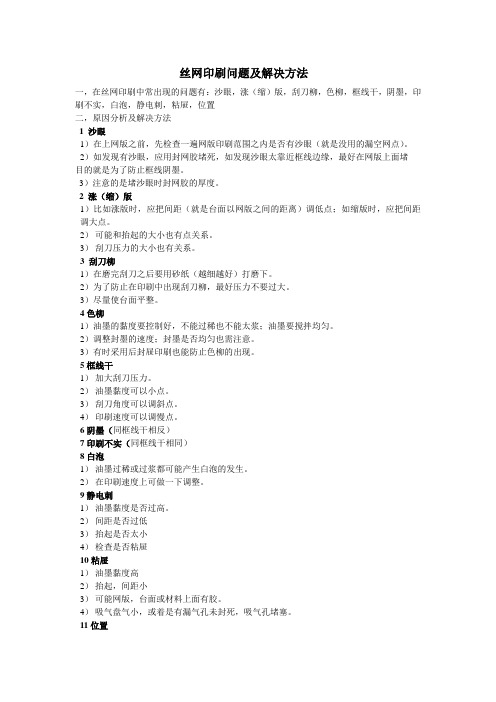
丝网印刷问题及解决方法一,在丝网印刷中常出现的问题有:沙眼,涨(缩)版,刮刀柳,色柳,框线干,阴墨,印刷不实,白泡,静电刺,粘屉,位置二,原因分析及解决方法1 沙眼1)在上网版之前,先检查一遍网版印刷范围之内是否有沙眼(就是没用的漏空网点)。
2)如发现有沙眼,应用封网胶堵死,如发现沙眼太靠近框线边缘,最好在网版上面堵目的就是为了防止框线阴墨。
3)注意的是堵沙眼时封网胶的厚度。
2 涨(缩)版1)比如涨版时,应把间距(就是台面以网版之间的距离)调低点;如缩版时,应把间距调大点。
2)可能和抬起的大小也有点关系。
3)刮刀压力的大小也有关系。
3 刮刀柳1)在磨完刮刀之后要用砂纸(越细越好)打磨下。
2)为了防止在印刷中出现刮刀柳,最好压力不要过大。
3)尽量使台面平整。
4色柳1)油墨的黏度要控制好,不能过稀也不能太浆;油墨要搅拌均匀。
2)调整封墨的速度;封墨是否均匀也需注意。
3)有时采用后封屉印刷也能防止色柳的出现。
5框线干1)加大刮刀压力。
2)油墨黏度可以小点。
3)刮刀角度可以调斜点。
4)印刷速度可以调慢点。
6阴墨(同框线干相反)7印刷不实(同框线干相同)8白泡1)油墨过稀或过浆都可能产生白泡的发生。
2)在印刷速度上可做一下调整。
9静电刺1)油墨黏度是否过高。
2)间距是否过低3)抬起是否太小4)检查是否粘屉10粘屉1)油墨黏度高2)抬起,间距小3)可能网版,台面或材料上面有胶。
4)吸气盘气小,或着是有漏气孔未封死,吸气孔堵塞。
11位置1)首先定位块要规则(左边定位块到怀里材料的边缘和怀里左边定位块到左边材料的边缘距离是1英尺,怀里右边定位块到怀里材料边缘总长度的四分之三处),定位块要在机器台面上固定紧。
2)然后在印刷之前再检查一遍网版是否固定好。
3)在印刷当中放好(自身手感)。
丝网印刷问题及解决办法

1.印刷速度对印刷效果的影响?印刷速度提高,会使浆料对网孔的填充效果变差。
使印刷的平整性变差,容易造成葫芦状栅线。
在一定范围内,印刷速度提高,可以使栅线高度上升,宽度变小。
2.浆料黏度对印刷效果的影响?1浆料的黏度如果太小,会导致印刷的图形易扩大。
产生气泡,毛边;2浆料的黏度如果太大,会导致透墨性差,会产生橘皮,小孔。
3在许可范围内,浆料的黏度越小越好。
3.压力与间距的关系?压力越大,间距越大。
因为压力大时,刮刀与网版接触的地方凸出来的也越多。
间距小的话,硅片承受的压力会变大,容易造成碎片。
两个参数不能单独改变,否则会影响印刷质量和增大碎片率4.烧结过程中,各温区的作用?1室温~300℃:溶剂的挥发。
2.300℃~500℃,有机树脂排出,需要氧气。
3.400℃以上,玻璃软化。
4。
600℃以上,玻璃与减反层反应,实现导电。
5.出现铝珠怎么办?1如果是印刷过厚,就调整参数,降低板间距,提高印刷压力;2如果是绒面过大,提醒制绒改善工艺;3如果是浆料不匹配,就改善浆料。
6.出现铝包怎么办?1如果是印刷厚度偏薄,就调整参数,提高板间距,降低印刷压力;2如果是印刷不均匀,就查看网板和刮条是否有磨损,提醒生产更换,如果都没问题,就是绒面问题,提醒制绒工艺。
7.出现翘曲片怎么办?1如果是印刷过厚,调整参数,提高板间距,降低压力;2如果是硅片太薄,更换抗弯曲浆料;3如果是刮刀没装好,提醒生产重新安装;4如果是硅片厚度不均,就是原料问题。
8.出现节点怎么办?1如果是网板或刮刀不良,提醒生产更换;2如果是参数设置不合理,调整参数,降低压力。
9.出现虚印和断栅怎么办?1如果是参数不合理,就调整参数,提高压力,降低板间距。
2如果是网孔堵了,擦拭网板;3如果是印刷头在行进过程中抖动,与设备协商解决;4如果是网板或刮刀磨损或者是浆料不够,就提醒生产人员更换或者添加浆料。
反向电流Irev>5.6A;测试光强E范围在950~1050 测试温度T 在23~27℃串阻Rs>0 填充因子68<FF<80。
丝网印刷常见问题及解决方法

净的无尘布将网板擦拭干净 降低压力
检查机械手加紧状况 刮刀高度上升
丝网间距,适当加大压力 更换刮条 更换网板 观察刮条刮拭的网板是否干净,加浆 料时采取少加多次的方式进行加浆料
板及刮条高度或降低电机高度 检查来料
更换衬纸或调整台面 更换刮条
小down-stop;增大pressure;减小speed 改变snap-off的效果最明显,但需注 意snap-off值改变过大会出现印刷不 良 大down-stop;减小pressure;增大speed
用干净的无尘布将网板擦拭干净 降低压力 检查机械手加紧状况 刮刀高度上升 抬高丝网间距,适当加大压力 更换刮条 更换网板
降低网板及刮条高度或降低电机高 检查来料 更换衬纸或调整台面 更换刮条
减小snap-off;减小down-stop;增大pressur
增大snap-off;增大down-stop;减小pressur
刮条破损
更换刮条
解决方法 加大丝网间距 检查刮条的平整度 检查来料 更换网板
备注 调大snap-off绝对值 可放在玻璃门上检查平整度
更换网板前后测量网板张力 不建议增大印刷压力
(调大Down-stop绝对值 )和印刷压力 ( Pressure ) 更换干净的衬纸
净的酒精无尘布擦拭台面 调大真空吸力 减少搅拌时间
1号机 Ag/Al浆
漏浆
网板微破且不影响图形 印刷偏移 Working Beam 上定位卡口处有浆料 网板破坏严重无法用胶带粘住 台面上有碎屑 换纸后有不平
隐裂
网板上沾有碎屑 隐裂 压力偏大 机械手夹的太紧 实际压力比设定压力大出很多 印刷参数不适宜 虚印 刮条不平 网板使用时间太长 网板及刮条高度太高 wafer厚度不均匀 印刷模糊 面不平 刮条不平 Ag/Al偏重 Ag/Al偏轻
丝网印刷中常见问题及解答
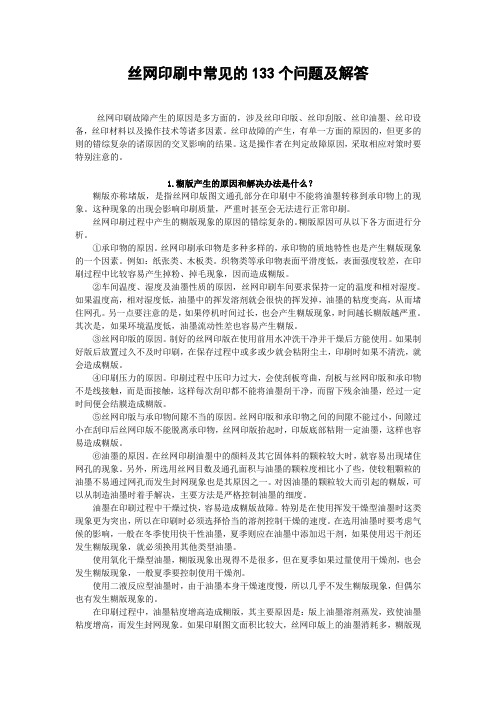
丝网印刷中常见的133个问题及解答丝网印刷故障产生的原因是多方面的,涉及丝印印版、丝印刮版、丝印油墨、丝印设备,丝印材料以及操作技术等诸多因素。
丝印故障的产生,有单一方面的原因的,但更多的则的错综复杂的诸原因的交叉影响的结果。
这是操作者在判定故障原因,采取相应对策时要特别注意的。
1.糊版产生的原因和解决办法是什么?糊版亦称堵版,是指丝网印版图文通孔部分在印刷中不能将油墨转移到承印物上的现象。
这种现象的出现会影响印刷质量,严重时甚至会无法进行正常印刷。
丝网印刷过程中产生的糊版现象的原因的错综复杂的。
糊版原因可从以下各方面进行分析。
①承印物的原因。
丝网印刷承印物是多种多样的,承印物的质地特性也是产生糊版现象的一个因素。
例如:纸张类、木板类。
织物类等承印物表面平滑度低,表面强度较差,在印刷过程中比较容易产生掉粉、掉毛现象,因而造成糊版。
②车间温度、湿度及油墨性质的原因,丝网印刷车间要求保持一定的温度和相对湿度。
如果温度高,相对湿度低,油墨中的挥发溶剂就会很快的挥发掉,油墨的粘度变高,从而堵住网孔。
另一点要注意的是,如果停机时间过长,也会产生糊版现象,时间越长糊版越严重。
其次是,如果环境温度低,油墨流动性差也容易产生糊版。
③丝网印版的原因。
制好的丝网印版在使用前用水冲洗干净并干燥后方能使用。
如果制好版后放置过久不及时印刷,在保存过程中或多或少就会粘附尘土,印刷时如果不清洗,就会造成糊版。
④印刷压力的原因。
印刷过程中压印力过大,会使刮板弯曲,刮板与丝网印版和承印物不是线接触,而是面接触,这样每次刮印都不能将油墨刮干净,而留下残余油墨,经过一定时间便会结膜造成糊版。
⑤丝网印版与承印物间隙不当的原因。
丝网印版和承印物之间的间隙不能过小,间隙过小在刮印后丝网印版不能脱离承印物,丝网印版抬起时,印版底部粘附一定油墨,这样也容易造成糊版。
⑥油墨的原因。
在丝网印刷油墨中的颜料及其它固体料的颗粒较大时,就容易出现堵住网孔的现象。
丝网印刷中常见的133个问题及解答

丝网印刷中常见的133个问题及解答丝网印刷故障产生的原因是多方面的,涉及丝印印版、丝印刮版、丝印油墨、丝印设备,丝印材料以及操作技术等诸多因素。
丝印故障的产生,有单一方面的原因的,但更多的则的错综复杂的诸原因的交叉影响的结果。
这是操作者在判定故障原因,采取相应对策时要特别注意的。
1.糊版产生的原因和解决办法是什么?糊版亦称堵版,是指丝网印版图文通孔部分在印刷中不能将油墨转移到承印物上的现象。
这种现象的出现会影响印刷质量,严重时甚至会无法进行正常印刷。
丝网印刷过程中产生的糊版现象的原因的错综复杂的。
糊版原因可从以下各方面进行分析。
①承印物的原因。
丝网印刷承印物是多种多样的,承印物的质地特性也是产生糊版现象的一个因素。
例如:纸张类、木板类。
织物类等承印物表面平滑度低,表面强度较差,在印刷过程中比较容易产生掉粉、掉毛现象,因而造成糊版。
②车间温度、湿度及油墨性质的原因,丝网印刷车间要求保持一定的温度和相对湿度。
如果温度高,相对湿度低,油墨中的挥发溶剂就会很快的挥发掉,油墨的粘度变高,从而堵住网孔。
另一点要注意的是,如果停机时间过长,也会产生糊版现象,时间越长糊版越严重。
其次是,如果环境温度低,油墨流动性差也容易产生糊版。
③丝网印版的原因。
制好的丝网印版在使用前用水冲洗干净并干燥后方能使用。
如果制好版后放置过久不及时印刷,在保存过程中或多或少就会粘附尘土,印刷时如果不清洗,就会造成糊版。
④印刷压力的原因。
印刷过程中压印力过大,会使刮板弯曲,刮板与丝网印版和承印物不是线接触,而是面接触,这样每次刮印都不能将油墨刮干净,而留下残余油墨,经过一定时间便会结膜造成糊版。
⑤丝网印版与承印物间隙不当的原因。
丝网印版和承印物之间的间隙不能过小,间隙过小在刮印后丝网印版不能脱离承印物,丝网印版抬起时,印版底部粘附一定油墨,这样也容易造成糊版。
⑥油墨的原因。
在丝网印刷油墨中的颜料及其它固体料的颗粒较大时,就容易出现堵住网孔的现象。
丝网印刷中常见的个问题及解答

丝网印刷中常见的个问题及解答丝网印刷中常见的133个问题及解答丝网印刷故障产生的原因是多方面的,涉及丝印印版、丝印刮版、丝印油墨、丝印设备,丝印材料以及操作技术等诸多因素。
丝印故障的产生,有单一方面的原因的,但更多的则的错综复杂的诸原因的交叉影响的结果。
这是操作者在判定故障原因,采取相应对策时要特别注意的。
1.糊版产生的原因和解决办法是什么?糊版亦称堵版,是指丝网印版图文通孔部分在印刷中不能将油墨转移到承印物上的现象。
这种现象的出现会影响印刷质量,严重时甚至会无法进行正常印刷。
丝网印刷过程中产生的糊版现象的原因的错综复杂的。
糊版原因可从以下各方面进行分析。
①承印物的原因。
丝网印刷承印物是多种多样的,承印物的质地特性也是产生糊版现象的一个因素。
例如:纸张类、木板类。
织物类等承印物表面平滑度低,表面强度较差,在印刷过程中比较容易产生掉粉、掉毛现象,因而造成糊版。
②车间温度、湿度及油墨性质的原因,丝网印刷车间要求保持一定的温度和相对湿度。
如果温度高,相对湿度低,油墨中的挥发溶剂就会很快的挥发掉,油墨的粘度变高,从而堵住网孔。
另一点要注意的是,如果停机时间过长,也会产生糊版现象,时间越长糊版越严重。
其次是,如果环境温度低,油墨流动性差也容易产生糊版。
③丝网印版的原因。
制好的丝网印版在使用前用水冲洗干净并干燥后方能使用。
如果制好版后放置过久不及时印刷,在保存过程中或多或少就会粘附尘土,印刷时如果不清洗,就会造成糊版。
④印刷压力的原因。
印刷过程中压印力过大,会使刮板弯曲,刮板与丝网印版和承印物不是线接触,而是面接触,这样每次刮印都不能将油墨刮干净,而留下残余油墨,经过一定时间便会结膜造成糊版。
⑤丝网印版与承印物间隙不当的原因。
丝网印版和承印物之间的间隙不能过小,间隙过小在刮印后丝网印版不能脱离承印物,丝网印版抬起时,印版底部粘附一定油墨,这样也容易造成糊版。
⑥油墨的原因。
在丝网印刷油墨中的颜料及其它固体料的颗粒较大时,就容易出现堵住网孔的现象。
丝印常见问题分析与解决
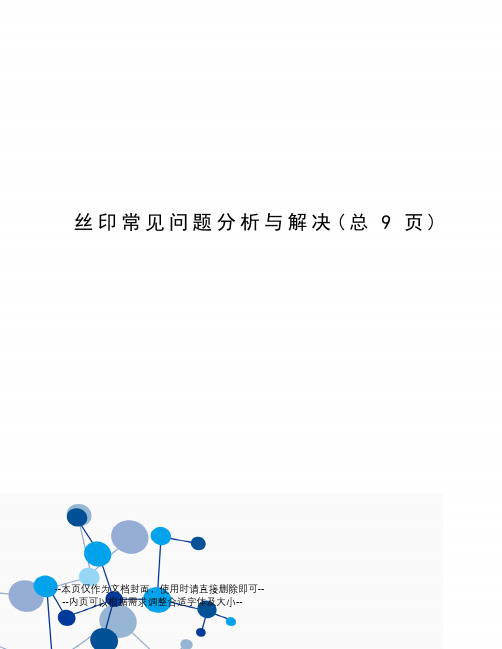
丝印常见问题分析与解决(总9页)--本页仅作为文档封面,使用时请直接删除即可----内页可以根据需求调整合适字体及大小--第四节丝网印刷常见问题及解决办法一、丝网印版常见故障的分析在丝印感光制版过程中,由于操作不当或对制版材料的选择与使用不尽合理,往往会使制得的丝网印版存在各种各样的故障与弊病,以至直接影响到丝印产品的质量,严重时甚至二、丝网印刷故障及对策丝印故障的产生,有单一方面原因的,但更多的则是错综复杂诸原因的交叉影响的结果。
这是操作者在判定故障原因,采取相应对策时要特别注意的。
(一)、糊版糊版亦称堵版,是指丝网印版图文通孔部分在印刷中不能将油墨转移到承印物上的现象。
这种现象的出现会影响印刷质量,严重时甚至会无法进行正常印刷。
丝网印刷过程中产生的糊版现象的原因是错综复杂的。
糊版原因从以下各方面进行分析。
1、印物的原因。
丝网印刷承印物是多种多样的,承印物的质地特性也是产生糊版现象前一个因素。
例如:纸张类、木桩类、织物类等承印物表面平滑度低,表面强度较差,在印刷过程中比较容易产生掉粉、掉毛现象,因而制成糊版。
1、车间温度、湿度油墨性质的原因。
2、丝网印刷车间要求保持一定的温度和相对湿度。
如果温度高,相对湿度低,油墨中的挥发溶剂就会很快地挥发掉,油墨的黏度变高,从而堵住网孔。
另一点应该注意的是,如果停机时间过长,也会产生糊版现象,时间越长糊版越严重。
其次是,如果环境温度低,油墨流动性差也容易产生糊版。
3、丝网印版的原因。
制好的丝网印版在使用前用水冲洗干净并干燥后方能使用。
如果制好版后放置过久不及时印刷,在保存过程中或多或少就会黏附尘土,印刷时如不清洗,就会造成糊版。
4、印刷压力的原因。
印刷过程中压印力过大,会使刮板弯曲,刮板与丝网印版和承印物不是线接触,而呈面接触,这样每次刮印都不能将油墨刮干净,而留下残余油墨,经过一定时间便会结膜造成糊版。
5、丝网印版与承印物间隙不当的原固。
丝印版与承印物之间的间隙不能过小,间隙过小在刮印后丝网印版不能脱离承印物,丝网印版抬起时,印版底部黏附一定油墨,这样也容易造成糊版。
丝网印刷中常见故障的分析及处理.
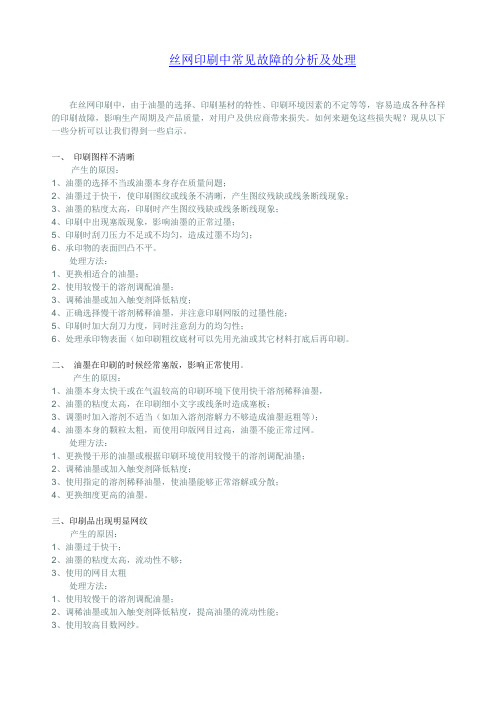
丝网印刷中常见故障的分析及处理在丝网印刷中,由于油墨的选择、印刷基材的特性、印刷环境因素的不定等等,容易造成各种各样的印刷故障,影响生产周期及产品质量,对用户及供应商带来损失。
如何来避免这些损失呢?现从以下一些分析可以让我们得到一些启示。
一、印刷图样不清晰产生的原因:1、油墨的选择不当或油墨本身存在质量问题;2、油墨过于快干,使印刷图纹或线条不清晰,产生图纹残缺或线条断线现象;3、油墨的粘度太高,印刷时产生图纹残缺或线条断线现象;4、印刷中出现塞版现象,影响油墨的正常过墨;5、印刷时刮刀压力不足或不均匀,造成过墨不均匀;6、承印物的表面凹凸不平。
处理方法:1、更换相适合的油墨;2、使用较慢干的溶剂调配油墨;3、调稀油墨或加入触变剂降低粘度;4、正确选择慢干溶剂稀释油墨,并注意印刷网版的过墨性能;5、印刷时加大刮刀力度,同时注意刮力的均匀性;6、处理承印物表面(如印刷粗纹底材可以先用光油或其它材料打底后再印刷。
二、油墨在印刷的时候经常塞版,影响正常使用。
产生的原因:1、油墨本身太快干或在气温较高的印刷环境下使用快干溶剂稀释油墨,2、油墨的粘度太高,在印刷细小文字或线条时造成塞板;3、调墨时加入溶剂不适当(如加入溶剂溶解力不够造成油墨返粗等);4、油墨本身的颗粒太粗,而使用印版网目过高,油墨不能正常过网。
处理方法:1、更换慢干形的油墨或根据印刷环境使用较慢干的溶剂调配油墨;2、调稀油墨或加入触变剂降低粘度;3、使用指定的溶剂稀释油墨,使油墨能够正常溶解或分散;4、更换细度更高的油墨。
三、印刷品出现明显网纹产生的原因:1、油墨过于快干;2、油墨的粘度太高,流动性不够;3、使用的网目太粗处理方法:1、使用较慢干的溶剂调配油墨;2、调稀油墨或加入触变剂降低粘度,提高油墨的流动性能;3、使用较高目数网纱。
四、印刷品出现明显水波纹产生的原因:油墨太稀或粘度太低,印刷时网距过低,印刷时产生油墨倒粘;排除方法:减少油墨中加入的溶剂份量,保持油墨的粘度同时适当调高网距,使印刷时能自然回弹。
丝网印刷中常见故障的分析及处理

丝网印刷中常见故障的分析及处理在丝网印刷中,由于油墨的选择、印刷基材的特性、印刷环境因素的不定等等,容易造成各种各样的印刷故障,影响生产周期及产品质量,对用户及供应商带来损失。
如何来避免这些损失呢现从以下一些分析可以让我们得到一些启示。
一、印刷图样不清晰产生的原因:1、油墨的选择不当或油墨本身存在质量问题;2、油墨过于快干,使印刷图纹或线条不清晰,产生图纹残缺或线条断线现象;3、油墨的粘度太高,印刷时产生图纹残缺或线条断线现象;4、印刷中出现塞版现象,影响油墨的正常过墨;5、印刷时刮刀压力不足或不均匀,造成过墨不均匀;6、承印物的表面凹凸不平。
处理方法:1、更换相适合的油墨;2、使用较慢干的溶剂调配油墨;3、调稀油墨或加入触变剂降低粘度;4、正确选择慢干溶剂稀释油墨,并注意印刷网版的过墨性能;5、印刷时加大刮刀力度,同时注意刮力的均匀性;6、处理承印物表面(如印刷粗纹底材可以先用光油或其它材料打底后再印刷。
二、油墨在印刷的时候经常塞版,影响正常使用。
产生的原因:1、油墨本身太快干或在气温较高的印刷环境下使用快干溶剂稀释油墨,2、油墨的粘度太高,在印刷细小文字或线条时造成塞板;3、调墨时加入溶剂不适当(如加入溶剂溶解力不够造成油墨返粗等);4、油墨本身的颗粒太粗,而使用印版网目过高,油墨不能正常过网。
处理方法:1、更换慢干形的油墨或根据印刷环境使用较慢干的溶剂调配油墨;2、调稀油墨或加入触变剂降低粘度;3、使用指定的溶剂稀释油墨,使油墨能够正常溶解或分散;4、更换细度更高的油墨。
三、印刷品出现明显网纹产生的原因:1、油墨过于快干;2、油墨的粘度太高,流动性不够;3、使用的网目太粗处理方法:1、使用较慢干的溶剂调配油墨;2、调稀油墨或加入触变剂降低粘度,提高油墨的流动性能;3、使用较高目数网纱。
四、印刷品出现明显水波纹产生的原因:油墨太稀或粘度太低,印刷时网距过低,印刷时产生油墨倒粘;排除方法:减少油墨中加入的溶剂份量,保持油墨的粘度同时适当调高网距,使印刷时能自然回弹五、油墨干燥不良产生的原因:1、选用溶剂不当,腐蚀底材(特别是印刷印刷软质PVC或覆膜尼龙布时容易产生);2、溶剂过于慢干或干燥时间不足;处理方法:1、选择与底材相适应的溶剂;2、选用较快干溶剂或延长干燥时间六、油墨附着力不良产生的原因:1、选用油墨与底材不适应;2、底材表面不干净,有油污或表面处理剂等(如:防腐剂、脱膜剂等);另外,一些特殊材料,由于表面张力过低也会影响油墨的附着力;3、干燥时间不足,油墨没有完全固化;4、过多加入助剂或加入助剂不当。
- 1、下载文档前请自行甄别文档内容的完整性,平台不提供额外的编辑、内容补充、找答案等附加服务。
- 2、"仅部分预览"的文档,不可在线预览部分如存在完整性等问题,可反馈申请退款(可完整预览的文档不适用该条件!)。
- 3、如文档侵犯您的权益,请联系客服反馈,我们会尽快为您处理(人工客服工作时间:9:00-18:30)。
丝网印刷中常见的个问题及解答诸原因的交叉影响的结果。
这是操作者在判定故障原因,采取相应对策时要特别注意的。
第一节丝网印刷对丝网的要求丝网印刷制版、印刷工艺,对丝网的性能有如下几项基本要求:1.抗张力大。
抗张力强度是指丝网受拉力时,抵抗破坏(断裂)的能力。
另外,丝网吸湿后的强度变化应小。
2.断裂伸长率小。
伸长率是指丝网在一定张力下断裂时的伸长量与原长之比,以百分比表示。
伸长率大,平面稳定性差,但丝网还要求一定张力(3%左右)下具有足够的弹性。
3.回弹性好。
回弹性是指丝网拉伸一定长度(如伸长3%后),释去外力时,其长度回复能力,称伸长回复度,其值越大越好,回弹后,印后边缘清晰。
4.耐温湿度变化的稳定性好。
5.油墨的通过性能好。
6.对化学药品的耐抗性好。
7.具体目数见工程单。
第二节网框和绷网一.网框材料的选择一般选用LY12、LF2等硬质合金铝方管型材,尺寸选用宽20mm,厚20mm,四角用氩弧焊接或铆接加工而成。
金属框架精度高,尺寸稳定。
二.丝网材料的选择目前用得最多的是尼龙丝网和涤纶丝网。
尼龙丝网耐热性较差,受热后易产生热塑性变形,使张力不均匀,影响网印质量。
粘结绷网或丝网模版制作不宜高温烘烤。
涤纶丝网耐热性较好,尺寸稳定,图形不因温度和湿度的变化产生较大的变动。
为了保证网印图形精度最好选用单丝涤纶丝网。
同时应选用丝网目数较高,丝径较细,网眼较小的丝网,丝网的颜色以黄色或棕黄色为好,以防产生晕影。
三.绷网最好采用气动绷网机,绷网的质量要求如下:1.绷网张力合适、均匀(1)使用气动绷网在达到张力要求的时候一定要静置3-6小时再上绷网胶;(2)绷好的网最少要放置24小时以上,特别是做大货或机印的网,以保证各点应力均等,防止变形。
网目越高的网版要求放置的时间越长,一般2-3天为宜。
放置后网版张力稳定,名点的应力相等,以保证网版不变形,不易损坏。
2.经纬网丝保持垂直3.防止松弛四.丝网模版制版工艺目前用得最多的是直接法制作丝网模版,在此制作工艺中注意上胶涂层的厚度合适、上浆均匀,严格控制干燥、曝光、显影等环节,方能得到高质量的丝网模板。
第三节丝网印刷对感光材料的要求1.丝网制版对感光材料的要求:制版性能好,便于涂布,有适当的感光光谱范围,一般宜在340~440μm,感光波长,制版操作和印版贮存需有严格的暗室条件;波长过短,光源的选择、人员的防护将变得较为困难;感光度高,可达到节能,快速制版的目的;显影性能好,则分辩力高,稳定性好,则便于贮存,感少浪费。
2.丝网印刷对感光材料的要求:感光材料形成的版膜应适应不同种类油墨的性能要求,具有相当的耐印力,能承受刮墨的相当次数的刮压;与丝网的结合能力好,印刷时不产生脱膜故障;易剥离,不易产生鬼影,利于丝网版材的再生使用。
对不干油墨来说,要求感光膜在承印面达到一定的厚度10~40μm,约为1~2张80克复印纸的厚度。
第四节晒版光源和设备一.晒版光源的选用。
在感光法丝网制版工艺中,晒版是极为重要的工艺过程。
如果正确地选择和使用晒版光源,对于提高丝网印版的质量,有效地节约能源,简化操作,维护操作者的身体健康,降低成本具有极为重要的意义。
由于感光性树脂感光材料的种类不同,所以要选择使用符合各种感光材料需要的光源。
目前我们所用的各种丝网感光材料其感色性大多分布在250~510μm之间。
因此,从理论上讲,凡是发光光谱能量发布曲线上的峰值波长于250~510μm的光源,均可用于丝网晒版。
另外,在晒版时,要充分研究一下版的大小,光源的输出功率,版和光源间的距离,并且要特别注意灯光反射板的作用。
二.选择光源时的注意事项1.光源的发射光谱应与感光材料的吸收特性和感色性相匹配。
光的能量因波长的频率不同而有所不同,波长越短,频率越高,光子能量越大。
当光在辐射的过程中被物质吸收后,由于光子具有一定的能量,因而会使物质发生物理和化学变化,由光能量所引起的化学反应,称之为光化学反应。
所谓光化学匹配性,是指所选用的光源的光谱输出分布应与感光材料的光谱感色性想匹配。
即感光材料吸收光发生光化学反应的波长范围,正好是光源发光光谱的输出范围,感光材料的最大吸收峰正好是在光源的输出峰值处。
这样光源的光能最大限度地被感光材料吸收而发生光化学反应。
2.发光效率高、强度大。
在其它条件不变的情况上,光源的功率和发光效率越大,其发光强度或亮度越大,曝光表面的照度也随之增大,感光材料获得同等曝光量所需的时间也就越短。
3.光源热辐射小。
在保证光源具有足够的发光强度或亮光的前提下,光源的热辐射应尽可能的小。
使用大功率强光源时,必须对灯管采取强制冷却(风冷、水冷)等措施,并采用其它措施,使感光材料的曝光而温度控制在32℃以下。
4.发光强度均匀。
光源的照射面发光强度应尽可能均匀。
曝光装置的设计,应保证感光材料的曝光面各点照明度差不超过15%。
光源环境适应能力强。
光源应有较强的环境适应能力,在各种不同的温度、气流、电压变化情况下,均能正常工作。
当然,在实际生产中,要选择一种能完全满足上述要求的光源是不现实的。
上述选择原则提出的目的,仅仅是希望制版操作人员在选择使用制版光源时,应考虑到光源对感光材料曝光质量的影响,做到有的放矢。
三.晒版设备。
晒版机主要晒版设备,是感光材料的曝光器具。
它和简易的晒版装置相比,具有极大的优越性,如果没有真空晒版机,而用简易的晒版设备,那么一定程度上图案还原的精度将受到影响。
第五节感光材料的选择丝网印刷对丝网版的要求就是它对图象的再现性。
而决定再现性的一个重要因素,就是选择一种好的感光材料。
所谓丝网印版的再现性是指丝网版对原稿图像的再现能力。
它表现在丝网印版的精度、清晰度、分辩力等诸方面。
一.丝网印版的精度。
丝网印版的精度是指印版的图像、文字、符号等的位置与尺寸精度。
它当制版的材料和方法有关,如手工封涂和切刻制版的精度常低于感光制版;间接制版的精度高于直接制版。
二.丝网印版的清晰度。
在摄影中,清晰度是指软版上图像边缘密度变化的程度,在丝网印制版中则是指版膜图像边沿在水平和垂直两个方向上的整齐程度。
它包括三个要素:肩锐性、架桥性及平整性。
1.肩锐性。
是指版膜图像肩部的方正程度。
方肩(90度)其印迹的三维性好;塌肩,印迹边缘的墨厚不匀,且有印迹扩大的现象。
2.架桥性。
是指版膜图像边沿跨越丝网网也时,保持原图形状的性能。
架桥性好,图像边沿再现性好,跨越网也的图像边沿会变形,变形的程度与版膜材料、制作方法及图像边沿与网孔的位置关系有关,其印迹呈锯齿状。
3.平整性。
指版膜印刷面(与承印物接触的一面)的平整程度。
平整性决定着版膜与承印面在印刷时的密接程度。
平整性好,印刷时两面密接,墨流不会越界,印迹光洁;平整性差时,版膜表面随丝网的丝、孔而起伏,墨流会流入不密接部分,使印迹边沿出现锯齿,且每隔两个网孔出现一个锯齿,齿的开头和大小近似不密接的范围。
用粗糙度仪可测量版膜表面的起伏差。
差值大,则平整性差;差值在3~7μm间,可在各种承印面上获得清晰性好的印迹。
4.印刷面膜的厚度。
丝印版印刷面的版膜厚度影响到印迹的墨层厚度及清晰度,尤其对细小图像的影响更大,甚至会改变网点的阶调值和色彩等。
当产品要求墨层厚、线条粗时,则相应要求版膜应厚一些。
因此版膜的作用要符合厚度要求。
5.丝网印版的耐印力。
耐印力指印版能承受印刷次数的能力。
影响耐印力的因素很多,从制版角度来说,主要取决于印版本身耐机械力和化学力的强度,及其与丝网结合的牢度。
印版耐印力应与丝印任务相适应,有的只耐印几十份,有的超过10万印。
6.丝网印版的脱膜性。
脱膜性是指版膜从印版的丝网上去除的难易程度。
制版质量的标准并非愈高愈好,而是在满足任务需要的前提下,愈经济愈好。
要达到以上的要求,制出比较合格的印版,就要选择质量过关的感光材料,印制精细的照片效果,就KFG 不干油墨而言我们要求用的感光浆是油性、厚膜感光浆(最好是进口的)。
第六节感光制版方法当制版所要求的设备和其它条件都具备时,我们就要进行制版。
感光制版法分直接法、间接法、直间法三种,从本质上进上述三种制版方法的技术指标是一样的,只是涂布感光胶或贴膜的工艺方法有所不同,这里我们所说的是直接法。
一.大至程序:涂布数次底版清洁丝网干燥涂布感光胶干燥晒版曝光显影干燥修版配制感光胶加压水冲洗二.具体方法:1.网前处理。
为防止由于污物、灰尘、油脂等带来感光膜的缩孔、砂眼、图像断线等现象,在进行感光液的涂布之前有必要使用洗净剂进行充分洗网。
此时所用的洗净剂一般采用家庭用的中性或弱碱性洗衣粉即可,但市场出售的丝网洗净剂,常用的如20%的苛性钠水溶液,其脱脂效果好,能改善感光液对丝网的湿润性,可以形成十分均匀的涂布膜,因此使用这种丝网洗净剂效果很好。
洗净作业从手工操作到使用自动洗净机(最常用的是喷枪,也有超声波洗净),方式是多种多样的。
无论何种方法,无论是新网还是旧网,都要经过洗净液脱脂洗净、水洗、脱水、干燥等程序。
其它的前处理,还有用物理方法以在丝网表面磨擦进行粗化的作业,以改善丝网对感光膜的粘着性能。
另外,为防止丝网表面由于光的乱反射而引起图像伯再现性降低,有进还在丝网表面用黄、红、橙等染料进行了工业染色的丝网。
2.感光液的涂布。
往网上涂布感光液的方法很多,最常用的是刮斗法和旋转法。
(1)旋转涂布是把版固定在涂布器上使之回传,将感光液倒在版的中心,倒下的液体由于离心力的作用向四周均匀地涂布成膜的方法。
与用刮斗涂布相比可得到高度均匀的膜。
如果感光液粘度、旋转速度、网目等条件不变的话,任何人都能进行质量固定的涂布但只适用于小块版的涂布(一般不超过50×50)。
(2)刮斗涂布包括手工涂法和机涂法,胶斗长度随涂布面尺寸选择,若图幅面积=a×b(a为短边,b为长边)则刮胶面积=(a+4cm)×(b+6cm)为宜。
则刮刀的长度为a+cm。
(3)刮斗与丝网接触的刃口边,必须保证较高的平整度,不能有碰伤的痕迹。
如果平整度低或有碰伤,涂布后的膜层则会出现条痕或膜层厚度不均匀的现象,从而使印刷后的图文线条出现毛刺和墨层厚度不均匀,颜色光彩度不一等现象。
(4)刮斗涂布的顺序:A、把绷好网的网框以80~90度的倾角竖放,往斗中倒入容量为6~7成感光液,把斗前端压到网上。
B、把放好的斗的前端倾斜,使液面接触丝网。
C、保证倾角不变的同时进行涂布。
此时如果涂布的速度过快,容易产生气泡造成针孔。
D、涂布到距网框边1~2cm时,让斗的倾角恢复到接近水平,涂布至多余的液体不剩下为止。
这样全部涂布感光胶后,把框上下倒过来再重新涂布一次,然后干燥。
第一次干燥应充分,若用热风干燥,应掌握适当温度;温度过高,有产生热灰翳的可能,必须引起注意。
干燥后,再按同样的要领涂布2~3次,直到出现光泽。