制程异常统计分析表
CAR管理List统计分析表
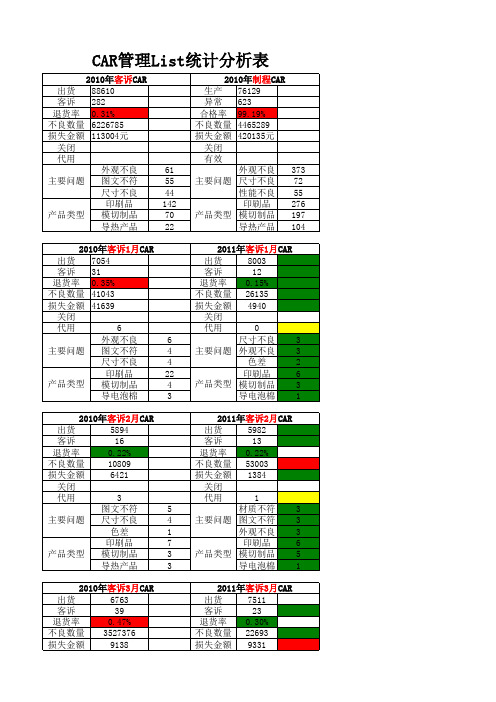
8 2 1 26 17 3
2011年客诉4月CAR 出货(批) 7144 客诉(批) 22 退货率 0.30% 不良数量 100285 损失金额 7671 关闭 代用 3 外观不良 10 主要问题 尺寸不良 3 色差 2 印刷品 8 产品类型 模切制品 8 导热产品 3 2011年客诉5月CAR 出货(批) 8418 客诉(批) 13 退货率 0.15% 不良数量 94808 损失金额 3928 关闭 代用 19 图文不符 主要问题 性能不良 色差 印刷品 产品类型 模切制品
61 55 44 142 70 22
373 72 55 276 197 104
6 4 4 22 4 3
2011年客诉1月CAR 出货(批) 8003 客诉(批) 12 退货率 0.15% 不良数量 26135 损失金额 4940 关闭 代用 0 尺寸不良 主要问题 外观不良 色差 印刷品 产品类型 模切制品 导电泡棉 2011年客诉2月CAR 出货(批) 5982 客诉(批) 13 退货率 0.22% 不良数量 53003 损失金额 1384 关闭 代用 1 材质不符 主要问题 图文不符 外观不良 印刷品 产品类型 模切制品 导电泡棉 2011年客诉3月CAR 出货(批) 7511 客诉(批) 23 退货率 0.30% 不良数量 22693 损失金额 9331 关闭
生产(批) 异常(批) 合格率 不良% 411948 83354.88 0 外观不良 图文不符 性能不良 导热产品 模切制品 印刷品
产品类型
49 5 3 23 20 14
生产(批) 4973 异常(批) 15 合格率 99.70% 不良数量 33333 损失金额 4450 关闭 让步放行 3 外观不良 主要问题 尺寸不良 色差 印刷品 产品类型 模切制品 导热产品 2011年制程3月CAR 生产(批) 6410 异常(批) 13 合格率 99.80% 不良数量 135555 损失金额 6714 关闭 让步放行 0 外观不良 主要问题 尺寸不良 性能不良 印刷品 产品类型 导电泡棉 模切制品
QP-16数据分析管理程序

制订日期2020-4-13文件名称数据分析管理程序文件类别程序文件1.目的:为适当验证物料,制程及成品之允收性,及提供各阶段之质量状况,做为相关单位参考,并及时矫正异常状况。
2.范围:物料验收、制程管制及成品检验等质量活动均适用。
3.权责:品质课:负责建立及实施数据分析管理。
4.定义:(无)5.作业内容:5.1抽样计划(标准)5.1.1本工厂抽样统计运用于物料及成品之质量检验。
5.1.2抽样统计表“MIL-STD-105E”表II级检验水准单次抽样计划执行正常检验按各产品《检验规范》执行。
5.2进料检验统计5.2.1进料检验以批数为数据,统计各个供应商进料的不良批率,以显示该月进料质量状况,并做成《供应商质量月统计表》,交采购对各供应商进行考核。
5.3制程检验统计5.3.1品质课依据《制程首件巡检日报表》对制程不良率及不良状况进行统计,做成《统计分析表》。
若不良率超过质量目标时,则用柏拉图进行分析,柏拉图的运作见《QC七大手法》。
5.3.2根据柏拉图显示状况,由品管课对前1-2项之问题发出《品质异常联络单》要求责任单位依《纠正预防措施管理程序》对潜在之问题进行分析并改善。
5.4成品检验统计5.4.1每月根据品管课《成品检验记录表》做成《统计分析表》,显示生产线的退货批数及退货制订日期2020-4-13文件名称数据分析管理程序文件类别程序文件原因。
5.4.2每月以生产部成品检验批及总批量为依据,统计该月制造部成品检验的退货率及抽样不良率。
若超出质量目标时,则品管课利用柏拉图分析,与5.3.2做法相同。
5.5客户抱怨及制程异常统计5.5.1每月由品质课统计客户抱怨及制程异常发生次数,并做成《客诉月统计表》。
5.5.2每季由品质课对制程异常利用柏拉图分析,并依《纠正预防措施管理程序》采取相应改善与预防措施。
5.6进料、制程、成品等质量月报表需于次月8日前完成,并经品质课主管审查,管理代表核准后分发相关单位作为质量改善活动的参考。
品质部月报

100.0%
100.0% 100.0%
100.0%
22
69.4%
8
77.1%
100.0% 100.0%
72.9%
4
60.0%
1
75.0%
6
81.8%
100.0%
87.8%
100.0%
1
98.4%
100.0%
98.5%
沙伯基础
7
塑胶原料
富技化工
4
100.0% 100.0%
100.0%
其它
其它
11
100.0% 100.0%
系列1, 幸福, 0.886022115
一、原材料进料检验品质(IQC)
2.3 边框材料投产不良统计
恒美, 划伤不良, 4822
供应商月不良数对比
宏茂 海达 恒美 安泰
擦伤不良 1828 904 2713 32
恒美, 碰伤不良, 3111
恒美, 擦伤不良, 2713 宏茂, 划伤不良宏, 茂23,0碰5 伤不良, 2141
合格率, 2月份, 0合格率, 3月份, 0合格率, 4月份, 0合格率, 5月份, 0合格率, 6月份, 0合格率, 7月份, 0合格率, 8月份, 0合格率, 9月份合, 0格率, 10月份, 0
一、原材料进料检验品质(IQC)
2.5 接线盒材料制程月不良统计(材料/供应商)
材料 二极管 电缆线
检验批数
批退数
厂商批合格率
材料批合 格率
恒美
70
海达
37
型材
宏茂
142
6
91.4%
100.0%
1
99.3%
96.4%
产品制程不良率统计表
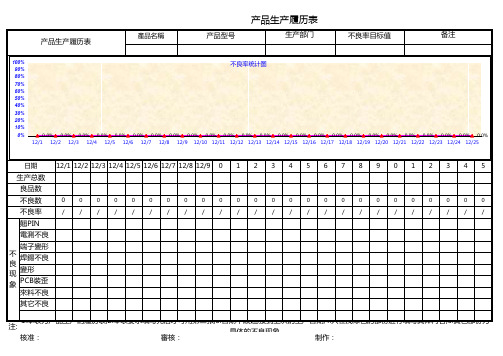
/
/
/
/
/
/
/
/
累計不良比率 不良率
1200 1000
不良項目 不良數量
翹PIN 1000 31.3% #DIV/0!
電測不良 800 56.3% #DIV/0!
端子變形 600 75.0% #DIV/0!
焊錫不良 400 87.5% #DIV/0!
端子鉚壓變形 230 94.7% #DIV/0!
日期
12-1 12-2 12-3 12-4 12-5 12-6 12-7 12-8 12-9 12-10 12-11 12-12 12-13 12-14 12-15 12-16 12-17 12-18 12-19 12-20 12-21 12-22 12-23 12-24 12-25
生产总数 良品数 不良数 不良率 翹PIN 電測不良 端子變形 不 焊錫不良 良 端子鉚壓變形 现 象 PCB裝歪 來料不良 其它不良
87.5%
94.7%
80.0% 60.0%
400 230 100 50
40.0% 20.0%
20
0.0%
翹PIN
電測不良
端子變形
焊錫不良
端子鉚壓變形
PCB裝歪
來料不良
其它不良
不良項目
不良率
原因分析
改善對策
負責人
預完日
PCB裝歪 100 97.8% #DIV/0!
97.8%
來料不良 50 99.4% #DIV/0!
99.4%
其它不良 20 100.0% #DIV/0!
合計 3200 #DIV/0!
100.0% 100.0%
1000 800 800 600 400 200 0 31.3% 56.3% 600 75.0%
制程不良统计、分析
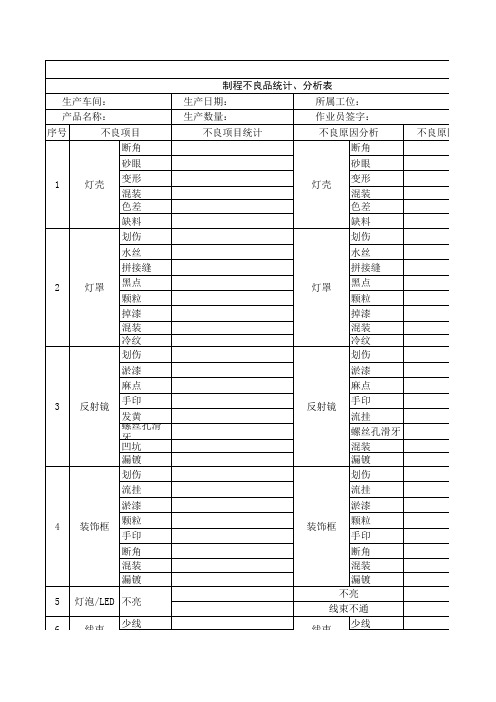
不良原因分析统计
”字标识;
改的上报品管部。
不良原因分析统计6Biblioteka 线束装反线束
装反
调节螺丝自身铆接漏气
调节螺丝与灯壳配合处漏气
后盖与灯壳配合处漏气
7
灯具气密
灯具漏气
线束与灯壳配合处漏气 线束里面线塞漏气 灯壳胶水漏气 灯壳砂眼
8
灯具调光
调光不良
银碗转不动
注:“不良项目”由生产班组所属工位人员进行统计,以“正”字标识; “不良原因”由品保部检验员和车间班组长共同分析原因,由检验员完成填写,同样以“正”字标识; 此表单由品管部检验员收集,并于每月3日前,将超过4%的不良品或者认为需要进行质量整改的上报品管部。
制程不良品统计、分析表 生产车间: 产品名称: 序号 不良项目 断角 砂眼 1 灯壳 变形 混装 色差 缺料 划伤 水丝 拼接缝 2 灯罩 黑点 颗粒 掉漆 混装 冷纹 划伤 淤漆 麻点 3 反射镜 手印 发黄 螺丝孔滑牙 凹坑 漏镀 划伤 流挂 淤漆 4 装饰框 颗粒 手印 断角 混装 漏镀 5 6 灯泡/LED 不亮 线束 少线 装饰框 反射镜 灯罩 灯壳 生产日期: 生产数量: 不良项目统计 所属工位: 作业员签字: 不良原因分析 断角 砂眼 变形 混装 色差 缺料 划伤 水丝 拼接缝 黑点 颗粒 掉漆 混装 冷纹 划伤 淤漆 麻点 手印 流挂 螺丝孔滑牙 混装 漏镀 划伤 流挂 淤漆 颗粒 手印 断角 混装 漏镀 不亮 线束不通 少线 线束
制程品质异常统计

责任单位
7月制程异 常分布
1月
2月
3月
4月
5月
6月
7月
8月
9月
10月
11月
供应商
37
41
39
41
38
41
37
37
冲压组
34424346414038
34
钣金组
37
40
42
38
42
43
37
37
全检1组
37
42
43
37
41
42
37
37
全检2组
37
43
43
39
42
42
68
供应商 14.59%
冲压组 15.19%
钣金组 14.91%
月份 责任部门 1月
2024年5 月份制程异常责任部门改善计划
原因分析
改善方案与计划
责任主管
2月
3月
4月
5月
6月
7月
8月
9月
10月
11月
12月 备注:责任单位每月10号前提交改善方案。
完成日期
备注
冲压组 14.84%
钣金组 16.15%
2024年制程异常责任部门汇总
供应商
全检4组 8.13%
冲压组 钣金组
全检3组 15.48%
全检1组
全检2组 全检3组 全检4组
全检2组 16.82%
全检1组 14.89%
12月
2024年制程 异常责任部
门汇总
273
284
279
279
315
制程品质异常处理规定

1. 目的为规范本公司制程品质异常的处理流程,明确质量异常及时处理、报告内容的填写与发行,提高质量异常的处理时效,确保制程中的产品品质得到有效控制.2. 适用范围适用于公司内所有质量异常问题的提出、处理、执行、验证等.3. 定义3.1 一般异常的定义:3.1.1 产品在制程生产时一小时出现功能不良、尺寸不良、装配不良,不良率超过3%;3.1.2 产品在制程生产时一小时出现外观不良,生产300pcs及以上总不良率超过5%;300pcs以下总不良率超过7%3.1.3 产品在制程中出现安全性隐患;3.1.4 制程中出现物料来料不良超过5%(特采物料除外);3.1.5 工序漏做、做错或混料.3.2 严重异常的定义:3.2.1 制程同一时间段,不良超过10%且无有效改善措施,不良有明显上升趋势;3.2.2 产品出现有安全隐患且不能有效筛选;3.2.3 物料不良且无法加工或挑选使用;3.2. 4 重大质量问题(安全测试不通过、客户端有相关投诉且该产品在线生产且无明确的纠正预防措施)不能在产线得到相关的筛选.3.2.5 批量性不良(不良超过20%).4. 职责4.1 生产部: 负责制程异常的发现、反馈,不良品的区分、处理及制程失控造成的异常原因分析、纠正预防措施的制定和执行;4.2 研发部:4.2.1负责制程异常因工艺、作业标准、包装技术问题造成的不良的产品处理、原因分析及纠正预防措施的拟订和执行以及有效措施标准化文件的建立.4.2.3对生产员工操作进行指导,对异常原因进行分析,并对工艺问题进行改善.4.3 工程部4.3.1负责品质异常中牵涉到的设备异常的设备维修、原因分析、原因改善,以及相关措施的执行.4.4 品质部:4.4.1 IPQC:对整个生产过程进行监控,将车间发生的异常向有关部门进行汇报,对不良品进行标识和隔离,对改善行动进行跟踪、监督以及改善后数据的收集、反馈4.4.2 品质工程师:参与对异常进行分析,对最终执行的纠正预防措施进行跟踪、验证,并保证本管理办法有效执行4.4.3 品质文员:负责品质单的收集、分发、归类和存档以及通报4.5 PMC: 负责异常物料的退货、补发以及产品的入库处理4.6 财务部:负责异常工时的统计,异常财产损失的计算、通报以及相关部门的责任分摊5. 作业内容5.1 发现异常5.1.1 IPQC根据作业指导书的要求进行首件、巡检以及转序产品的抽检,当发现有品质异常时,初步统计不良数量、不良项目等信息.判定异常属于一般异常还是其他异常.5.1.2 当其他人员发现异常时,应立即通知组长和IPQC.5.2 判定异常5.2.1 IPQC对异常现象进行了解并统计后,应确认是否需要发出《品质异常处理单》.如果没有达到异常标准则只需反馈给操作员或组长进行改善,并填写《制程稽查记录表》同时跟进改善结果是否有效,如果达到异常标准3.1则开出《品质异常处理单》;如达到3.2时,除开出《品质异常处理单》外还要开出《品质异常事件单》.5.2.2 IPQC确认并发出《品质异常处理单》,并将异常单中得内容填写清楚,异常单必须具备以下几点:a) 产品批次、型号;b)发生异常的时间和地点;c)已生产数量;d)已发现(抽检)的不良数量;e)不良率;f)异常现象的详细描述;填写完成后交给生产组长或生产主管确认异常.生产部门确认后,需要交给品质组长及以上进行审核.5.2.3 异常单会签完成后,IPQC组长将异常单交给文员进行编号登记.编号原则:QA+年份+月份+日+三位序列号.5.2.4 异常达到严重异常且暂时没有有效措施改善时,需要停机、停拉的,需各部门经理会签评审(夜班可根据情况电话通知,事后补签),经过副总经理批准.生产部立即将异常信息通知给PMC.5.3采取应急措施5.3.1 由生产组长主导对已生产的产品进行隔离、标识,待研发、品质现场工程师给出解决方案.5.3.2 IPQC将异常单交给研发部现场工程师,现场工程师接到异常单后,在现场对不良现象及不良率进行确认.必要时可向销售部了解交期,然后与生产主管、品质工程师共同分析确认,研发、品质现场工程师根据实际情况制定应急措施(严重异常时,可召集相关人员召开会议进行讨论).5.3.3 如应急措施需要返工,则由研发部现场工程师制定返工方案后,生产部按照公司《返工返修管理规定》进行返工.研发部现场工程师现场指导,IPQC对返工后的产品进行确认.5.3.4 研发、品质现场工程师提出临时解决方案一定对现场具有指导性、可行性等,不可用“加强”、“建议”等字眼. 提出临时处理措施时,应具备以下两点:a 对已经生产的产品给出处理措施,如:报废、返工、返修、挑选使用、区分下转等.b 对后续的生产过程给出纠正措施,提升产品合格率.5.3.5 研发部主管或经理负责对临时解决方案的可行性、合理性进行确认.5.4 临时处理措施验证5.4.1现场品质人员、以及现场负责人对于研发、品质现场工程师给出的临时处理措施的实施效果的可行性、合理性进行验证,确保临时处理措施可提升产品合格率或能准确区分、拦截不良品.5.4.2现场品质人员应对已生产产品的处理过程进行监督;对已按临时处理措施处理过的产品进行复检、标识和区分,并统计出准确数量记录在《品质异常处理单》上(含合格数量、不良数量或报废数量).5.4.3 对处理措施涉及到的报废、降级等方案,现场品质人员需复印异常单副本交于PMC和财务部,由PMC评估是否需要补料;由财务部统计异常损失(待追查到责任部门后,将异常损失转嫁到责任部门).5.5 原因分析5.5.1 研发、品质现场工程师对不良现象进行分析,并将分析结果记录在《品质异常处理单》中.必要时组织相关部门进行会议讨论或进行试验验证.5.5.2 研发、品质现场工程师找出异常造成的责任部门并记录在异常单中(异常责任部门明确到车间工序),异常单经部门负责人核准,核准后的异常单传递给责任部门.5.5.3 原因分析要合理、得体,不可用“估计”、“大概”、“可能是”等模棱两可的字眼.5.5.4 在涉及到物料问题时,要写清楚物料名称、物料编码、入库日期、入库状态;在涉及到文件问题时,要写清楚文件编码与版次,以便相关人员追溯、处理.5.5.5 品质工程师须对分析原因的符合性进行确认,并跟进确认库存物料、供应商处物料、在线产品、客户处产品的处理.5.5.6 责任部门收到异常单后,应立即对异常情况进行调查分析,并将分析结果记录在异常单中.如果对异常责任部门判定有异议时,需立即找到对应的现场工程师共同分析或进行试验验证,必要时可召集品质、研发以及总经理进行裁决,直到找到真因为止.5.5 纠正预防措施5.5.1 责任部门(工序)负责人将异常分析结果及改善对策填写在异常单后,经部门主管/经理审核.将异常单回复给品质工程师.如异常单填写的改善措施无法有效解决问题,则直接退回给责任部门的主管/经理,由主管/经理监督或协助完成此异常单的回复.填写要求如下:A.责任部门对异常问题点提出纠正预防措施,须用简洁、明确、确定性的文件进行描述,多项措施应用项目符号标注,如:①、②….B.纠正预防措施应具备可行性、可测量性、权威性、有效性等,不可用“加强”、“建议”、“看情况”、“待确认(待验证)”等字眼.C.纠正预防措施如涉及到其他部门职责范围内,应提交相关责任部门填写预防方案;5.5.2 负责执行的职责部门必须明确纠正预防方案的完成时间,以保证此方案能够得到及时、有效的落实.5.5.3 现场研发部主管级以上人员负责对工程纠正与预防方案的可行性、合理性、有效性进行确认.并填写职责部门及具体完成日期.5.5.5 相关职责部门经理负责对本部门采取的纠正与预防方案的可行性、合理性、有效性进行确认.并确定部门纠正与预防措施的主责人.5.5.5 确认OK后的异常单,由部门文员将异常单给生产部统计异常损失的工时及物料.并将异常单复印分发给生产部、财务部、、PMC及相关责任部门.5.5.6 相关部门收到异常单后,应按照异常单的内容对改善行动进行执行,并将执行结果反馈给品质部.5.5.7 各部门在填写时须严格按以上职责与权限进行,并明确本身在此工作中的职能作用,避免越权,以避免造成异常单的层次不清与混乱及给处理者及执行者带来迷惑与误导.若有好的建议和其他意见,则以附件形式提出.5.5.8 改善措施一旦给出,相关职责部门须按照改善措施执行,如未执行改善措施,品质部有权要求停止生产,所造成异常损失由相关责任部门承担.5.6 效果确认5.6.1 IPQC在异常单原件上对改善后的效果进行跟踪,如改善OK,则可以关闭.如改善NG,则重新开出异常单.5.6.2 改善效果跟踪中,如发生的问题属于新发生的问题,则此份异常单也可关闭.如不良原因相同或由于改善措施引发的问题点,则改善措施无效.5.6.3 效果确认后,IPQC将填写完成的异常单给品质组长审核,品质工程师对已结案或完成改善的项目最终执行结果进行验证,,并对结批数据汇总进行汇报,必要时提供相应验证资料和异常单交给上级批准关闭项目.交由文员存档.5.6.4文员进行汇总各负责人跟进纠正预防措施执行情况,并抄送各部门负责人、副总;5.7 标准化如改善措施经最终判定合格有效,由研发部负责将改善措施增加(修改)到相关文件内,形成标准受控文件6. 相关文件《制程与出货检验作业规范》、《返工返修管理规定》7. 记录表单《品质异常处理单》、《制程稽查记录表》、《品质异常事件单》8. 附流程图。
制程不良率统计分析表
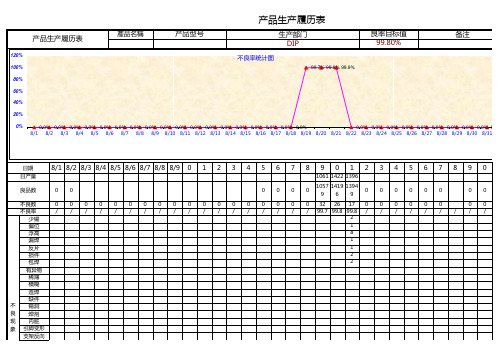
0.00% 0.00% 0.00% 0.00% 0.00% 0.00% 0.00% 0.00% 0.00% 0.08% 0.07% 0.19%
32
100.00%
26 80.00% 65.33% 57.336%0.00%
40.00%
22.67% 22.67% 22.67% 22.67% 22.67% 22.67% 22.67% 22.67% 22.67%
0
0
0
0
0
0
0
0
0
未入 多件 掉件 极性反 偏位 撞件 来料不良脚铜铂翘 溢胶 立片
20.00%
0.00% 线路断
检查人 完成日期
/
/
2
1
8
1
1
2
2
00 ///
掉件
极性反
偏位
撞件
来料不良
脚铜铂翘
溢胶
立片
线路断
注: 1:本表为产品生产的履历表;2:红色为旧件.
核准:
審核:
32 26
制作:
0.0% /31
8/31
0 0 /
制程不良統計表
不良項目
少锡 偏位 浮高 漏焊 反片 损件 包焊 有异物 稀薄 模糊 连焊 缺件 锡洞 焊剂 内脏 引脚变形 支架反向
产品生产履历表
产品生产履历表
120% 100%
產品名稱
产品型号
生产部门 DIP
不良率统计图
99.7% 99.8% 99.9%
良率目标值 99.80%
备注
80%
60%
40%
20%
0%
0.0% 0.0% 0.0% 0.0% 0.0% 0.0% 0.0% 0.0% 0.0% 0.0% 0.0% 0.0% 0.0% 0.0% 0.0% 0.0% 0.0% 0.0%