《成型技术基础》V3.1001
《成型技术基础》V3.1001解析

连接成型方法综合实验《成型技术基础》实验指导书江伟编华南理工大学机械电子工程研究所二○○八年十月十日目录注意事项2实验目的2实验内容2实验准备2试样规格3实验过程4实验一高频钎焊4点焊安全注意事项 4 实验二点固试件4点焊安全注意事项 4 焊点位置设计 4 电阻焊的原理 5 操作方法 5 实验三熔化极气体保护焊6安全注意事项 6 熔化极气体保护焊原理 6 焊缝设计7 操作方法7实验总结8实验报告8附: TPS2700焊机简介9注意事项焊接实验是强电磁场或高频设备,身体内部有金属植入物,如电子心脏起搏器等的同学,可以免做实验。
实验目的1、了解电阻焊的工作原理、特点、应用范围;2、了解熔化极气体保护焊的工作原理、特点、应用范围;熟悉其工艺规范的规律;3、了解高频钎焊焊的工作原理、特点、应用范围。
实验内容1、用高频焊机对两个金属片实施钎焊;2、用电阻点焊对工件进行点固实验;3、用气体保护焊方法焊接试件实验。
实验分班分组进行,每班几个小组,每8人或10人一组,每组选出一个组长。
每组焊若干个试样。
根据课堂理论定出几个不同的电流工艺规范进行焊接。
对比不同规范对焊接成型的影响;作好记录、分析不同的原因、写实验报告。
实验准备一、实验材料和设备1、氩气(或二氧化碳)2、氩气减压表(二氧化碳减压表)3、二氧化碳气体焊丝4、导电嘴5、喷嘴6、焊接面罩7、防护眼镜8、隔热手套9、高频焊机10、点焊机11、TPS2700焊机12、焊接电缆13、气管14、不锈钢薄片15、钢板125×40×3mm3(长宽厚)每个学生一块16、砂纸二、实验前的准备1、熟悉焊接电路回路的接法2、熟悉气路接法3、参数选择及工艺设计4、设计好记录表格5、参加实验的学生, 请准备一套阻燃性较好的衣服, 纯棉质地最合适; 避免穿丝绸或化纤的衣服。
建议穿军训时用的衣服。
试样规格1.高频钎焊使用的不锈钢薄片两片;2.试样采用普通低碳钢Q235-A(A3),板厚3mm,40X125mm2。
材料成形技术基础
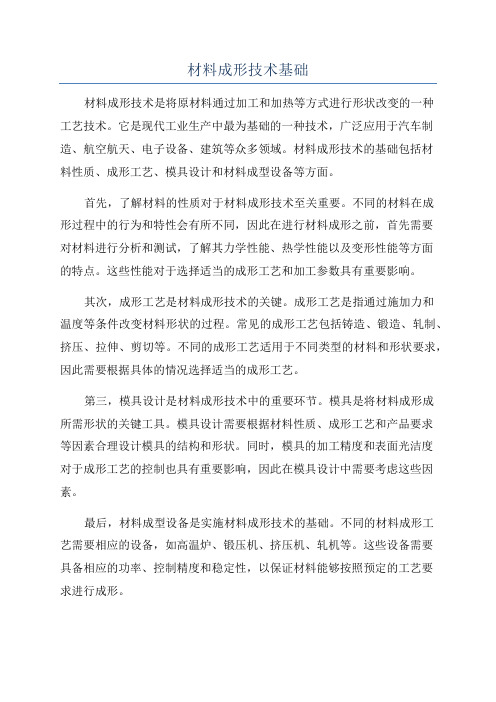
材料成形技术基础材料成形技术是将原材料通过加工和加热等方式进行形状改变的一种工艺技术。
它是现代工业生产中最为基础的一种技术,广泛应用于汽车制造、航空航天、电子设备、建筑等众多领域。
材料成形技术的基础包括材料性质、成形工艺、模具设计和材料成型设备等方面。
首先,了解材料的性质对于材料成形技术至关重要。
不同的材料在成形过程中的行为和特性会有所不同,因此在进行材料成形之前,首先需要对材料进行分析和测试,了解其力学性能、热学性能以及变形性能等方面的特点。
这些性能对于选择适当的成形工艺和加工参数具有重要影响。
其次,成形工艺是材料成形技术的关键。
成形工艺是指通过施加力和温度等条件改变材料形状的过程。
常见的成形工艺包括铸造、锻造、轧制、挤压、拉伸、剪切等。
不同的成形工艺适用于不同类型的材料和形状要求,因此需要根据具体的情况选择适当的成形工艺。
第三,模具设计是材料成形技术中的重要环节。
模具是将材料成形成所需形状的关键工具。
模具设计需要根据材料性质、成形工艺和产品要求等因素合理设计模具的结构和形状。
同时,模具的加工精度和表面光洁度对于成形工艺的控制也具有重要影响,因此在模具设计中需要考虑这些因素。
最后,材料成型设备是实施材料成形技术的基础。
不同的材料成形工艺需要相应的设备,如高温炉、锻压机、挤压机、轧机等。
这些设备需要具备相应的功率、控制精度和稳定性,以保证材料能够按照预定的工艺要求进行成形。
总结起来,材料成形技术基础包括材料性质、成形工艺、模具设计和材料成型设备等方面。
了解材料性质、选择适当的成形工艺、合理设计模具和使用符合要求的成型设备是确保材料成形质量的关键。
随着科学技术的发展,材料成形技术的研究不断推进,使得各种新材料和新工艺得以应用,推动了工业生产的进一步发展。
大学考试试卷《材料成形技术基础》及参考答案

材料成形技术基础一、判断题(本大题共100分,共 40 小题,每小题 2.5 分)1. 铸造的实质使液态金属在铸型中凝固成形。
( )。
2. 铸钢可以用来进行锻压加工。
( )3. 凝固温度范围大的合金,铸造时铸件中易产生缩松。
( )4. 随钢中含碳量增加,其可焊性变差。
( )5. 冲床的一次冲程中,在模具同一部位上同时完成数道冲压工序的模具,是连续模。
( )6. 特种铸造主要用于生产大型铸件。
( )7. 根据钎料熔点的不同,钎焊可分为硬钎焊、软钎焊两类。
( )8. 电阻焊分为点焊、缝焊、对焊三种型式。
( )9. 用离心铸造法生产空心旋转体铸件时,不需用型芯。
( )10. 提高浇注温度有利于获得形状完整、轮廓清晰的铸件,因此浇注温度越高越好。
( )11. 铸铁的焊补方法分为热焊法和冷焊法二种。
( )12. 液态金属在金属铸型中的流动性比在砂铸型中好。
( )13. 冲床的一次行程中,在模具不同部位上同时完成数道冲压工序的模具,是复合模( )14. 合理选择焊接顺序,可减少焊接应力的产生。
选择的主要原则是应尽量使焊缝自由收缩而不受较大的拘束。
( )15. 焊接构件中,用得最多的接头型式是对接。
( )16. 手工锻造适应于单件小批和大型锻件的生产。
( )17. 铸件的形状与结构应与零件相同。
( )18. 拉深系数越小,表明拉深件直径越小,变形程度越小。
( )19. 自由锻是巨型锻件成形的唯一方法。
( )20. 圆角是铸件结构的基本特征。
( )21. 用冲模沿封闭轮廓线冲切板料,冲下来的部分为成品,这种冲模是落料模。
( )22. 锻造加热时,时间越长越好。
( )23. 冲压零件在弯曲时,变形主要集中在圆角部分。
( )24. 金属型铸造适合于大批大量生产形状复杂的黑色金属铸件。
( )25. 某厂需生产8000件外径12mm、内径6.5mm的垫圈,采用连续冲模比简单冲模好。
( )26. 残余应力,可采用人工时效、自然时效或振动时效等方法消除。
成形基础知识(成形)课件
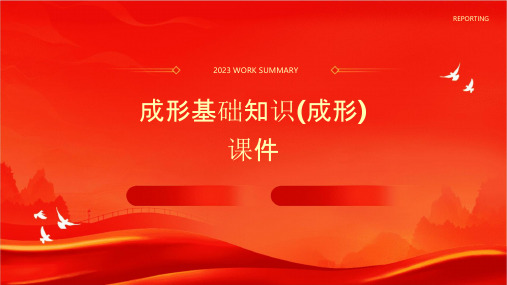
行业标准
特定行业内的质量标准, 用于规范行业内的产品质量。
2023 WORK SUMMARY
THANKS
感谢观看
REPORTING
02
固态成形原理主要包括材料的弹塑性行为、断裂准则和热变形等,这 些原理用于描述材料在固态成形过程中的行为。
03
常见的固态成形工艺包括切削加工、激光切割、3D打印等,这些工 艺广泛应用于各种材料的加工。
04
固态成形原理的应用有助于优化工艺参数、提高加工精度和降低生产 成本。
PART 03
成形工艺方法
等离子切割机
利用高温等离子气体对金属板 材进行切割的设备。
水切割机
利用高压水射流对非金属材料 进行切割的设备。
冲压机
利用模具和冲头对金属板材进 行冲压成形的设备。
PART 05
成形工艺质量控制
质量控制原理
预防原则
标准化原则
预防潜在的质量问题,而非单纯依赖 检验。
制定和执行标准操作程序,确保稳定 的生产过程。
PART 04
成形工艺设备
塑性成形设备
锻造设备
用于将金属坯料通过压 力和摩擦力进行塑性变 形,以形成所需形状的
设备。
挤压机
利用压力将金属坯料通 过模具挤压成形的设备。
轧制机
拉拔机
通过两个旋转轧辊之间 的压力将金属坯料轧制
成所需形状的设备。
通过拉伸力将金属坯料 拉制成所需形状的设备。
液态成形设备
总结词
利用固态材料的物理或化学变化,通过改变材料的内部结构 和性质,以获得所需形状和尺寸的零件的工艺方法。
详细描述
固态成形工艺方法主要包括焊接、热处理、粉末冶金等,这 些方法能够通过改变材料的内部结构和性质来控制零件的形 状和尺寸。固态成形工艺具有较低的生产成本和较高的灵活 性,适用于不同材料和形状的零件生产。
材料成形技术基础第3章

材料成形技术基础
一般地,滑 移总是沿着 原子密度最 大的晶面和 晶向发生。
(2) 孪生
在剪应力作用下,晶 体的一部分沿着一定的 晶面(称为孪生面)和一 定的晶向(称为孪生方向) 发生均匀切变。孪生变 形后,晶体的变形部分 与未变形部分构成了镜 面对称关系。
又从每个晶粒的应变分布来看,细晶粒晶界的影 响区域相对较大,使得晶粒心部的应变和晶界处 的应变差异减少,由于细晶粒金属的变形不均匀 性较小,由此引起的应力集中必然也较小,内应 力分布较均匀,因而金属断裂前可承受的塑性变 形量较大。
材料成形技术基础
三、冷塑性变形对金属组织和性能的影响 除了在晶粒内部出现滑移带和孪生带等组织特征外,
材料成形技术基础
在冷态变形条件下,多晶体的塑性变形主要是晶 内变形,晶间变形只起次要作用,而且需要有其它变 形机制相协调。
这是由于晶界强度高于晶内,各晶粒相互接触形 成犬牙交错状态,造成对晶界滑移的机械阻碍作用。 如果发生晶界变形,容易引起晶界结构的破坏和产生 裂纹,因此晶间变形量只能是很小的。
材料成形技术基础
材料成形技术基础
材料成形技术基础
2.晶间变形
晶间变形的主要方式是晶粒之间相互滑动和转动。 多晶体受力变形时,沿晶界处可能产生剪切应力,当 此剪切应力足以克服晶粒彼此间相对滑动的阻力时,便发 生相对滑动;另外,由于各晶粒所处位向不同,其变形情 况及难易程度亦不同,这样,在相邻晶粒间必然引起力的 相互作用而可能产生一对力偶,造成晶粒间的相互转动。
材料成形技术基础
塑性变形的特点
材料成形技术基础

材料成形技术基础材料成形技术是指通过对材料进行加工、变形或组装,使其得到所需形状和性能的一种技术。
在现代制造业中,材料成形技术占据着非常重要的地位,它涉及到诸多工业领域,如航空航天、汽车制造、电子设备等。
因此,对材料成形技术的基础知识有着深入的了解,对于从事相关行业的人员来说至关重要。
首先,材料成形技术的基础包括材料的性能和特性。
不同的材料具有不同的物理、化学性质,这决定了它们在成形过程中的行为。
例如,金属材料通常具有较好的塑性和导热性,适合进行锻造、压铸等成形工艺;而塑料材料则具有良好的可塑性和耐腐蚀性,适合注塑、挤出等成形工艺。
因此,了解材料的性能和特性对于选择合适的成形工艺至关重要。
其次,材料成形技术的基础还包括成形工艺的原理和方法。
成形工艺是指利用机械设备对材料进行加工、变形或组装的方法。
常见的成形工艺包括锻造、压铸、注塑、挤出等。
每种成形工艺都有其独特的原理和方法,需要根据不同的材料和产品要求进行选择。
同时,了解成形工艺的原理和方法,能够帮助我们更好地掌握成形过程中的关键技术和要点,提高产品质量和生产效率。
另外,材料成形技术的基础还包括成形设备和工具的选择和运用。
不同的成形工艺需要配备相应的设备和工具,如锻造需要锻压机、冲压需要冲床、注塑需要注塑机等。
选择合适的成形设备和工具,并正确地进行操作和维护,对于保证成形过程的稳定性和产品质量至关重要。
最后,材料成形技术的基础还包括对成形过程中可能出现的问题和缺陷的分析和解决方法。
在实际生产中,成形过程中可能会出现各种问题和缺陷,如气孔、裂纹、变形等。
了解这些问题和缺陷的成因,以及采取相应的解决方法,能够帮助我们及时发现和解决问题,提高产品质量和生产效率。
综上所述,材料成形技术的基础知识包括材料的性能和特性、成形工艺的原理和方法、成形设备和工具的选择和运用,以及对成形过程中可能出现的问题和缺陷的分析和解决方法。
这些基础知识对于从事相关行业的人员来说至关重要,能够帮助他们更好地掌握成形技术,提高产品质量和生产效率。
工程材料与成形技术基础习题含答案
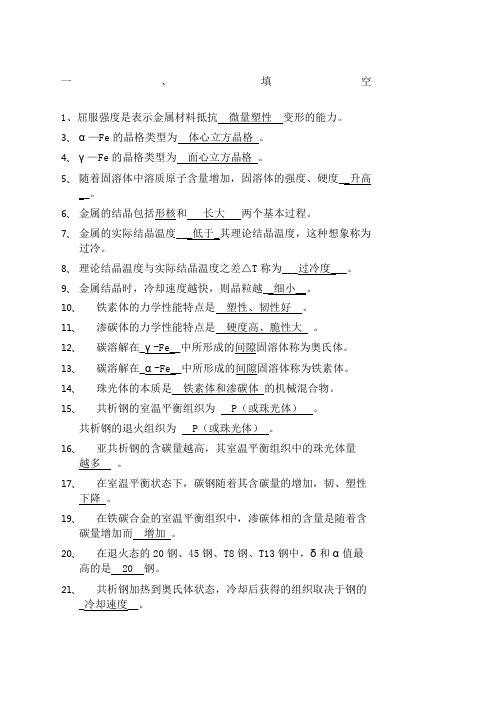
一、填空1、屈服强度是表示金属材料抵抗微量塑性变形的能力。
3、α —Fe的晶格类型为体心立方晶格。
4、γ —Fe的晶格类型为面心立方晶格。
5、随着固溶体中溶质原子含量增加,固溶体的强度、硬度__升高__。
6、金属的结晶包括形核和长大两个基本过程。
7、金属的实际结晶温度___低于_其理论结晶温度,这种想象称为过冷。
8、理论结晶温度与实际结晶温度之差△T称为___过冷度___。
9、金属结晶时,冷却速度越快,则晶粒越__细小__。
10、铁素体的力学性能特点是塑性、韧性好。
11、渗碳体的力学性能特点是硬度高、脆性大。
12、碳溶解在_γ -Fe__中所形成的间隙固溶体称为奥氏体。
13、碳溶解在_α -Fe__中所形成的间隙固溶体称为铁素体。
14、珠光体的本质是铁素体和渗碳体的机械混合物。
15、共析钢的室温平衡组织为 P(或珠光体)。
共析钢的退火组织为 P(或珠光体)。
16、亚共析钢的含碳量越高,其室温平衡组织中的珠光体量越多。
17、在室温平衡状态下,碳钢随着其含碳量的增加,韧、塑性下降。
19、在铁碳合金的室温平衡组织中,渗碳体相的含量是随着含碳量增加而增加。
20、在退火态的20钢、45钢、T8钢、T13钢中,δ 和α 值最高的是 20 钢。
21、共析钢加热到奥氏体状态,冷却后获得的组织取决于钢的_冷却速度__。
22、共析钢过冷奥氏体在(A1~680)℃温度区间等温转变的产物是珠光体(或P) 。
23、共析钢过冷奥氏体在680~600℃温度区间等温转变的产物是索氏体(细珠光体)。
24、共析钢过冷奥氏体在(600~550)℃温度区间等温转变的产物是托氏体(或极细珠光体)。
25、共析钢过冷奥氏体在550~350℃温度区间等温转变的产物是 B 上(或上贝氏体)。
26、共析钢过冷奥氏体在(350~230)℃温度区间等温转变的产物是下贝氏体(或B 下)。
27、亚共析钢的正常淬火温度范围是 Ac3 + 30~50℃ 。
28、过共析钢的正常淬火温度范围是 Ac1 + 30~50℃ 。
成型技术基础1

缺点:投资大,不适合三箱、活块造型。
1.2.2 1、金属型铸造 一 、 金属型构造
特种铸造
二 、 金属型的铸造工艺 1 2 3 喷刷涂料 金属型的型腔和金属表面必须喷 刷涂料 金属型应保持一定的工作温度 通常铸铁件 为250-350度,非铁金属件100-250度 适合的出型时间 通常小型铸铁出型时间为 10-60S, 铸件温度约为780-950C
流动性好,充型能力强,易于获得尺寸准 确、外形完整和轮廓清晰的铸件
流动性不好,充型能力差,铸件易产生浇
不到、冷隔、气孔和夹杂等缺陷
2、流动性的测定
3、影响流动性的因素 合金种类 化学成分
二、浇注条件 1.浇注温度
2.充型压力
三、铸型填充条件
1、铸型材料(铸型蓄热系数)
2、铸型温度,
3、铸型的发气和透气能力
三 、金属型铸造的特点和适用范围
金属型铸造可“一型多铸”, 便于实现机械 化和自动化生产, 提高生产率.
铸件的精度和表面质量比砂型铸造显著提 高. 金属型铸造主要用于铜,铝合金铸件的大批 生 产, 如铝活塞,气缸盖,油泵壳体,铜瓦, 衬套,轻工业品.
2、熔模铸造 一 1 熔模铸造的工艺过程 蜡模制造
1.2 金属的液态成形工艺 1.2.1 砂型铸造 砂型成型工艺:怎样用型砂制作砂型的型 腔。
分型面:砂箱间的接触表面。 每块砂型的剖分面 分模面:整体模样的剖分面。
1、手工造型 整体模造型 分模模造型
挖砂造型
活块造型
三箱造型
地坑造型
造型材料* 铸型的制造 (最重要工序)
应具备性能:
(1)强度
位于铸件表面,尺寸较大,是椭园型或梨 型。
2、析出气孔 溶解在金属液中的气体在冷凝过程中,因气体溶 解度下降而析出,铸件因此而形成的气孔。 气孔尺寸较小,分布面积较广。
材料成形技术基础
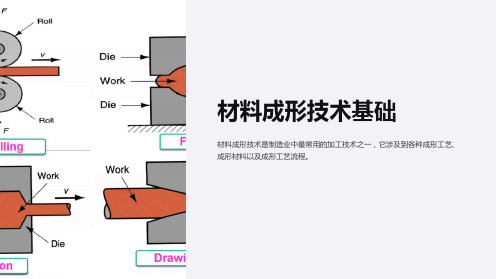
电子制造
材料成形技术在电子设备的封装和连接中起着重要 作用。
航空航天
艺术雕塑
材料成形技术用于制造航空航天部件和航天器结构。 材料成形技术被艺术家用于创作各种雕塑作品。
材料成形技术的挑战与发展趋势
1 高性能材料
随着科技的进步,材料成形技术需要适应高性能材料的特性和要求。
材料成形技术基础
材料成形技术是制造业中最常用的加工技术之一,它涉及到各种成形工艺、 成形材料以及成形工艺流程。
成形技术定义
成形技术是通过施加力或应用热量将原始材料转化为所需形状和尺寸的加工方法。
主要成形技术分类
1 压力成形技术
将材料置于模具中,并施加压力使其变形, 如冲压、铸造等。
2 热成形技术
2 节能环保
开发符合节能环保要求的成形工艺和材料,减少资源消耗和环境污染。
3 数字化制造
利用数字化技术实现材料成形过程的自动化和智能化。
3
成形操作
按照成形工艺要求进行操作,施加力或应用热量使材料变形。
常见的成形材料
金属
如铝、钢等,用于制造汽车零部件、电子设备等。
塑料
如聚乙烯、聚丙烯等,广泛用于塑料制品的生产。
陶瓷
如瓷器、陶器等,用于制作装饰品、器皿等。
复合材料
如碳纤维增强复合材料,用于制造航空航天部件。
材料成形技术的应用领域
汽车制造
通过加热材料使其变软或熔化,然后形成所 需形状,如热压、热挤压等。
3 凝固成形技术
通过材料凝固过程中的相变来实现成形,如 注射成型、凝胶成型等。
4 仿生如3D打印、 模具复制等。
成形工艺流程
1
成型技术基础

第一节 造型方法的选择
一、手工造型 整体模造型 分模模造型 挖砂造型 活块造型 三箱造型
二、机器造型
机器造型主要将繁重的紧砂和精细的起模等主要 操作实现机械化 1、机器造型基本原理 1)紧砂方法: 压实式、震实式、震压式、抛砂式、射压式 2)起模方式: 顶箱式起模 、 漏模式起模 、 ห้องสมุดไป่ตู้转式起模
第三节、工艺参数的选择
一、机械加工余量和最小铸孔 二、铸造收缩率 三、拨模斜度及铸造圆角 四、型芯头及芯座
五、浇注系统设计 引导金属液流入铸型型腔的一系列通道的 总称。 外浇口:承接金属液并将其平稳地导入直 浇道。 直浇道:产生静压力、调速。 横浇口:分配金属液,阻挡熔渣。 内浇口:控制金属液的速度与方向。 昌口:铸型中设置的一个储存金属液的空 腔
2、流动性的测定
3、影响流动性的因素
化学成分
二、浇注条件
1.浇注温度 2.充型压力 三、铸型填充条件 1、铸型材料, 2、铸型温度, 3、铸型中的气体
第二节 铸件的凝固与收缩
一、铸件凝固方式 按凝固区的宽窄来划分: 逐层凝固——凝固过程中不存在凝固区, 断面上由一条界线分开液、固体。 糊状凝固——液、固相并存的凝固区 贯穿 整个界面。 中间凝固——介于逐层凝固和糊状凝 固之 间。
受到铸型或型芯的机械阻碍而形成 的内应力。
二、铸件的变形与防止
同时凝固,反变形,自然时效
三、铸件的裂纹与防止 1、热裂:高温下形成的裂纹。裂纹短, 缝隙宽,形状曲折缝内呈 氧化色 2)冷裂:低温下形成的裂纹。裂纹细小, 呈连续直线状,缝内呈 轻微氧化色。
四、合金的吸气性*
气孔:液态合金中吸入了气体,若在其冷凝过 程中不能逸出,滞留在金属中则冷凝后在铸 件内形成的空洞 1、侵入气孔 位于铸件表面,尺寸较大,是椭园型或梨 型。
成形技术基础

赋形和固化2
• 从上图中熔体的流动充填状态看,和我们想象的相差不是 很大,可能是较正确地反映了汽车门的实际充填过程。
• 塑件的成型 取决于四大要素,即:树脂原料、模具、成型条件及注塑机.因 此,从事注塑成型技术工作的人员必须精通上述各方面的知识,这样在出 现次品时,能及时、正确地分析出原因,快速解决问题,减少损失.换句话说, 在初期阶段能正确地判断出产生次品的原因,研究上述四种因素中哪一 种因素都是十分重要的.
注塑加工前的准备工作2
部品制造课成形技术教育
---成形技术基础
注塑加工行业的概述
注塑成型加工的流程
注塑原理
• 所谓热注塑性树脂的注塑,是指将树脂加热 熔融后,在一定的压力和速度下使其注入模 具内,经冷却定形而得到具有所要求形状/尺 寸的成形品的过程.其原理和糖果的成型或 金属的铸造没什么不同,但热塑性树脂在成 型中,仅仅是把其熔融并使之自然地流入到 模具中固化,是不可能制成完好的制品的.这 是因为树脂的熔融粘度极高,靠其自然流入 到模具中赋予形状是不可能的.
甲醛(POM)、防火塑料等.
• 2、熔融指数(FMI)
• 熔融指数较低的树脂-------HPVC、SPVC、聚碳酸酯、PMMA等 • 熔融指数较高的树脂-------聚苯乙烯、聚乙烯、聚丙烯、尼龙等
各种塑料在不同成型条件下的合适壁厚
三.塑料的含水量与干燥温度
• a)干燥程度很差.树脂中水分多,熔融粘度急剧下降,熔体迅速淌出,喷嘴 在劈啪响中不断喷出泡沫状、云球白烟或气体,制件的塑件无使用价值.
《成型技术基础》平时作业及答案(2021

《成型技术基础》平时作业2021年7月年级____ 专业__机械电子工程__ 姓名______一、判断题1.缩松是铸件的气孔。
(×)2.自由锻是一种不用任何辅助工具的可以锻造任何形状的零件的锻造方法。
(×)3.铸造是指将液态合金浇注到具有与零件形状、尺寸相适应的铸型型腔中,待冷却凝固后获得毛坯或零件的生产方法。
()4.铸件在冷却凝固过程中由于体积收缩得不到补充而在最后凝固部位形成的倒圆锥形孔洞称为缩孔。
(√)5.低碳钢的强度、硬度低,但具有良好的塑性、韧性及焊接性能。
(√)6.塑性是金属材料产生塑性变形而不被破坏的能力。
(√)7.可锻铸铁比灰铸铁的塑性好,因此可以进行锻压加工。
(√)8.随塑性变形程度的增大,金属强度和硬度上升而塑性和韧性下降的现象称为加工硬化。
(√)9.板料冲压是利用冲模使液态金属成型的加工方法。
(×)10.“同时凝固”这种工艺措施可以有效的防止应力、变形和缩孔缺陷。
(×)11.普通钢和优质钢是按其强度等级来区分的。
(×)12.金属的塑性变形主要通过位错的滑移进行。
(√)13.金属的晶粒越细小,其强度越高,但韧性变差。
(√)14.弹簧钢的最终热处理应是淬火+低温回火。
(×)15.奥氏体的塑性比铁素体的高。
(√)16.钢的含碳量越高,其焊接性能越好。
(×)17.锻造加热时过烧的锻件可用热处理来改正。
(×)18.给铸件设置冒口的目的是为了排出多余的铁水。
(×)19.薄板件的波浪形变形主要是焊缝局部应力较大而引起的。
(√)20.一般把金属的焊接分为熔化焊、压力焊和钎焊三大类。
(√)21.金属凝固时,过冷度越大,晶体长大速度越大,因而其晶粒粗大。
(×)22.铸型中含水分越多,越有利于改善合金的流动性。
(×)23.模锻时,为了便于从模膛内取出锻件,锻件在垂直于分模面的表面应留有一定的斜度,这称为锻模斜度。
成形技术基础知识

射出成形技術基礎知識一、成型五大要素:注塑机/模具/材料/成型條件/環境(人)二、成型條件五大要素:1.壓力:射出壓力/保壓壓力/加料壓力/開鎖模壓力/頂出壓力.2.速度:射出速度/保壓速度/加料速度/開鎖模速度/ 頂出速度.3.位置:射出位置/加料位置/鬆退位置/開鎖模位置/頂出位置4.時間:射出時間/保壓時間/加料時間/冷卻時間/ 中間時間5.溫度:料管溫度/模具溫度/干燥溫度。
三.保壓:模腔填滿塑料后,繼續施加於模腔塑料上的注射壓力,直至澆口完全冷卻封閉的一段時間要靠一個相當高的壓力來支持就是保壓.保壓作用:補充靠近澆口位置的料量,防此制件的收縮,減少真空汽泡,另一作用減少制作固受過大的注射壓力而產生粘模爆裂或彎曲.四.背壓:螺杆在加料時,在螺杆旋轉后退所施加的壓力叫背壓及塑化壓力.作用:控制料筒內塑料的壓緊程度及塑化效果,提高顏色的混和效果,排除塑料的各種氣體,減少制品的銀紋和汽泡.五:射壓切換到保壓方式一般射出壓力(射壓)切換到保持壓力(保壓)的方式有四種:1.模內壓切換2.時間切換3.射出缸壓力切換4.螺桿位置切換模內壓切換型式:在模具之模穴中,裝置一個壓力感應器。
方法:當射出成形時,感應器感應到流動塑脂傳來的壓力有在上升,一旦上升之壓力達到設定值時,射出壓力(射壓)立即切換到保持壓力(保壓)。
時間切換型式:利用射出時間( T 1 )來切換。
方法:當射出成形過程時,一旦射出時間達到設定值時,射出壓力(射壓)立即切換到保持壓力(保壓)。
射出缸壓力切換型式:利用射出缸之壓力感應裝置來切換。
方法:當射出成形過程時,射出缸之壓力感應裝置,會感應到由螺桿傳來之射出壓力,一旦射出壓力達到設定值時,射出壓力(射壓)立即切換到保持壓力(保壓)。
螺桿位置切換型式:利用螺桿位置來切換。
方法:當射出成形過程時,螺桿位置會由計量值不停的向前變化,一旦螺桿位置傳來達到設定值時, 射出壓力(射壓)立即切換到保持壓力(保壓)。
成型技术基础培训

树脂的定向
表层:低速流动 非定向层:高速流动
定向层:因速度差被剪切
模具型腔表面
树脂往同一方向配置的状态被称为分子定向.
表层: 在流动中冷却,流动速度非常慢,固化快,结晶化会根据模温的变化而变 化,收缩率小.
定向层: 流动速度较低,是处于表层与非定向层(流动层)之间,因此,产生剪 切而被拉申,且在同一方向的状态下冷却固化,固化速度较快,分子定向明确.
16
成型工艺的三大要素
浇口封合(固化)的时间
★ 浇口封合是指在成形过程中,浇口部的树脂冷却固化的状态.浇口封合时间是指 在压力(保压)不变的情况下,保压时间延长,当达到某时间后,制品的重量不再增 加,这一时间通常被称为浇口封合时间. ★ 在浇口封合完成以前,如果保压压力过小或保压时间过短的话,型腔内的压力将 从未固化的浇口中回流,将会影响制品的重量及尺寸等品质的不稳定.
料温高
流动型 好
速度 压力
(设定) (设定)
慢小
周期 长
烧焦 易
缩水 分解 大易
表面 光泽
好
批锋 大
料温低
差
快 大 短 难 小 难 差小
干燥温度:
所有材料都有不同程度的吸湿性(亲水性),针对吸湿性较高的树脂必须在一定条 件下(温度及时间)进行干燥或除湿,当干燥不充分时制品会出现料花.银丝.气泡.色差 等不良现象,制品的机械强度也随之而降低.如:ABS,PC,PET,PBT,PMMA等.吸湿性 较低的树脂可不用干燥,对制品的影响也不会很大.如:PP.PE.POM.PS等.
塑料的特性
优点: ※可塑性强.很复杂的形状也很容易做出来 . ※产品重量轻并且比强度高. ※适合于大量生产,成本低. ※不生锈,不腐蚀. ※电绝缘性能好. ※断热隔热性能好. ※着色性好,可制作透明产品.
成型技术基础

成型技术基础一、成型技术概述成型技术是一种广泛应用于工程领域的加工方法,通过将原材料加热、塑料变形、冷却固化等工序,将目标形状赋予原材料,以满足工程设计的要求。
成型技术可以分为热成型和冷成型两种类型,其中在不同的应用领域有着各自的优势和适用范围。
热成型技术主要是通过将原材料加热至一定温度,使其软化、塑性增加,然后通过成型设备将其压制成目标形状,最后冷却固化得到成品。
常见的热成型技术包括注塑成型、压力成型、挤出成型等。
热成型技术通常具有生产效率高、成品精度高、成形自由度大等优点,适用于生产塑料制品、合金零件等。
冷成型技术则是通过机械冷加工方法,将原材料在常温下进行塑性变形,得到目标形状的工艺过程。
常见的冷成型技术包括冲压成型、折弯成型、剪切成型等。
冷成型技术通常具有成本低、加工效率高、成型精度高等优点,适用于生产金属零件、板材制品等。
二、热成型技术1.注塑成型技术注塑成型技术是指将加热后的塑料颗粒通过注射机射入模具中,充满模具腔形成目标形状,冷却固化后取出成品的成型方法。
注塑成型技术广泛应用于塑料制品生产领域,如家电外壳、汽车配件、玩具等。
注塑成型技术具有生产效率高、成品精度高、成形自由度大、适应性强等优点,但设备成本较高,注塑机的选型和模具设计是关键。
2.压力成型技术压力成型技术是指将加热后的原材料放置在模具中,在一定压力下进行成型的方法。
常见的压力成型技术有热压成型、冷压成型、真空吸塑等。
压力成型技术适用于生产各种塑料制品和橡胶制品,如碗盘、餐具、橡胶密封件等。
压力成型技术具有成品精度高、成型速度快、成本低等优点,但模具制作成本较高,对原材料要求严格。
3.挤出成型技术挤出成型技术是通过将加热后的原材料挤出挤出机的模头,通过挤出口的形状和尺寸,将原材料挤出成目标形状的方法。
挤出成型技术适用于生产各种管材、棒材、型材等,如PVC管、铝合金型材等。
挤出成型技术具有生产效率高、成品质量稳定、原材料利用率高等优点,但设备投资大,挤出机的选型和模具设计是关键。
材料成形技术基础

材料成形技术基础一、绪论1、机械制造一般过程示意图2、凝固成形、塑性成形、焊接成形的特点凝固成形:将金属熔炼成符合一定要求的液体并浇进铸型内,经冷却凝固、清整处理后得到有预定形状、尺寸和性能的铸件。
砂型铸造:优点:不受零件的形状、大小、复杂程度及合金的种类的限制;造型材料来源较广,生产准备周期短,成本低。
缺点:劳动条件差,铸件质量欠佳,铸型只能使用一次,生产率也较低。
塑性成形:利用金属材料的塑性性质进行加工,使之具有所需形状。
分类:板料成形,体积成形具体成形方法:锻造、轧制、挤压、拉拔、冲孔、落料、弯曲、拉伸、胀形和翻边焊接成形:通过加热或加压,或两者并用,并且用或不用填充材料,使工件达到结合方法:根据母材在焊接过程中是否融化,分为3类。
熔焊、固相焊和钎焊3、材料成形的发展概况二、材料凝固理论1、凝固过程将材料加热到液态,然后使其按规定的尺寸、形状及组织形态再次冷却至固态的过程。
凝固过程中材料的物理性质与晶体结构的变化:体积改变、外形改变、产生凝固潜热、熵值改变、结构改变、发生溶质再分配2、形核非自发形核:在不均匀液体中,依靠外来杂质界面或各种衬底形核的过程自发形核:不借助任何外来界面的均匀熔体中的形核的过程。
3、凝固方式糊状凝固:砂型铸造时,在很长一段时间内,固、液共存的两相凝固区几乎贯穿整个铸件的断面。
逐层凝固:金属型铸造时,固、液象限间距很窄,凝固自始至终仅有很薄一层的两相共存区,凝固壳由表面至中心逐渐加厚。
中间凝固:介于两者之间的凝固方式。
4、凝固控制1)充型能力控制充型能力:液态金属充满型腔,获得形状完整、轮廓清晰铸件的能力。
影响液态金属及合金充型能力的因素:金属性质、铸型性质、浇注条件、铸件结构流动性好的金属或合金填充铸型的能力就强,易于获得轮廓清晰的复杂薄壁铸件,易于补缩,可防止产生缩孔或缩松;易于使液体中的气体与夹杂物上浮和排除,可防止气孔和渣眼等缺陷的形成。
2)收缩控制收缩:铸件在凝固和冷却到室温的过程中,其体积和尺寸都会缩少的现象。
- 1、下载文档前请自行甄别文档内容的完整性,平台不提供额外的编辑、内容补充、找答案等附加服务。
- 2、"仅部分预览"的文档,不可在线预览部分如存在完整性等问题,可反馈申请退款(可完整预览的文档不适用该条件!)。
- 3、如文档侵犯您的权益,请联系客服反馈,我们会尽快为您处理(人工客服工作时间:9:00-18:30)。
连接成型方法综合实验《成型技术基础》实验指导书江伟编华南理工大学机械电子工程研究所二○○八年十月十日目录注意事项2实验目的2实验内容2实验准备2试样规格3实验过程4实验一高频钎焊4点焊安全注意事项 4 实验二点固试件5点焊安全注意事项 5 焊点位置设计 5 电阻焊的原理 5 操作方法 6 实验三熔化极气体保护焊7安全注意事项7 熔化极气体保护焊原理7 焊缝设计7 操作方法8实验总结9实验报告9附: TPS2700焊机简介10注意事项焊接实验是强电磁场或高频设备,身体内部有金属植入物,如电子心脏起搏器等的同学,可以免做实验。
实验目的1、了解电阻焊的工作原理、特点、应用范围;2、了解熔化极气体保护焊的工作原理、特点、应用范围;熟悉其工艺规范的规律;3、了解高频钎焊焊的工作原理、特点、应用范围。
实验内容1、用高频焊机对两个金属片实施钎焊;2、用电阻点焊对工件进行点固实验;3、用气体保护焊方法焊接试件实验。
实验分班分组进行,每班几个小组,每8人或10人一组,每组选出一个组长。
每组焊若干个试样。
根据课堂理论定出几个不同的电流工艺规范进行焊接。
对比不同规范对焊接成型的影响;作好记录、分析不同的原因、写实验报告。
实验准备一、实验材料和设备1、氩气(或二氧化碳)2、氩气减压表(二氧化碳减压表)3、二氧化碳气体焊丝4、导电嘴5、喷嘴6、焊接面罩7、防护眼镜8、隔热手套9、高频焊机10、点焊机11、TPS2700焊机12、焊接电缆13、气管14、不锈钢薄片15、钢板125×40×3mm3(长宽厚)每个学生一块16、砂纸二、实验前的准备1、熟悉焊接电路回路的接法2、熟悉气路接法3、参数选择及工艺设计4、设计好记录表格5、参加实验的学生, 请准备一套阻燃性较好的衣服, 纯棉质地最合适; 避免穿丝绸或化纤的衣服。
建议穿军训时用的衣服。
试样规格1.高频钎焊使用的不锈钢薄片两片;2.试样采用普通低碳钢Q235-A(A3),板厚3mm,40X125mm2。
如下图所示实验过程实验一高频钎焊安全注意事项焊接前先对工件焊接部位进行清理干净,不要直接用黑色的带氧化层的表面焊接,工件不要涂太多助焊剂,焊接操作时工件距离感应圈保持在0.5CM至1CM不要太近或太远。
焊接原理通过加热的方法将焊缝加热到合金钎料熔化的温度,但是此时被焊接的金属仍然未到达熔化温度,低熔点合金通过强大的表面张力将两个金属粘连在一起,冷却后就形成固体焊缝。
操作方法1.将两块待焊工件清理干净2.在焊接部位加一点助焊剂3.放一片焊接钎料4.把工件放在高频焊机的感应圈上方0.5CM至1CM位置5.踩脚踏开关,焊机开始加热6.待钎料熔化时,松开脚踏开关焊接完成实验二 点固试件 点焊安全注意事项1. 避免手被焊钳夹伤;2. 拿工件的手要带手套,以免被高温的工件烫伤;3. 焊接过程中有可能有大量的飞溅,请勿穿丝绸或化纤的衣服,以免损坏衣服,烫伤皮。
焊点位置设计点固用电阻焊机。
由组长安排,每两个同学将相互的工件点焊连接。
如下图4:电阻焊的原理电阻焊(Resistance Welding)是工件组合后通过电极施加压力和大电流, 利用工件的接触面及邻近区域产生的电阻热量进行焊接的方法。
电阻焊过程的物理本质,是利用焊接区本身的电阻热和塑性变形,使两个分离表面熔化或金属原子之间接近到晶格距离形成金属键,在结合面上产生足够量的共同晶粒而得到的焊接接头。
因此,电阻焊接头是在热——机械(力)联合作用下形成的。
电阻点焊(Resistance spotwelding )原理和接头形成如图5所示。
可简述为:将焊件3压紧在两电极2之间,施加电极压力后, 阻焊变压器1向焊接区通过强大的焊接电流,在焊件接触面上形成物理接触点,并随着通电加热的进行而不断扩大。
塑变能与热能使触点的原子不断激活,消失了接触面,继续加热形成熔化核心4,简称熔核。
熔核中的液态金属在电磁力的作用下发生强烈的搅拌,熔核中的金属成分均匀化,结合界面迅速消失。
操作方法 一、开机1. 开冷却水;2. 开压缩空气;3. 开电源;以上有指导老师或组长负责二、操作1. 调节规范。
2. 将电极对准要点焊的位置;(注意:手绝对不允许放到两电极之间,以防夹伤)3. 踩脚踏开关;电极压下,焊接自动完成,电极抬起。
4. 取出工件。
三、关机1. 关冷却水开关;2. 关焊机电源开关;3. 关气瓶总开关;4.打扫卫生。
1实验三熔化极气体保护焊安全注意事项1.避免被弧光直接照射眼睛;观察熔滴过度时使用面罩。
眼睛被强光照射后会暂时性失明;弧光也会令眼睛得电光性眼炎。
2.因为弧光含有大量的紫外光,避免皮肤被弧光近距离长时间照射,以免被晒伤;3.拿工件的手要带手套,以免被高温的工件烫伤。
熔化极气体保护焊原理气体保护电弧焊是用外加气体作为电弧介质并保护电弧和焊接区的电弧焊,简称气体保护焊。
氩弧焊是使用氩气作为保护气体的气体保护电弧焊方法。
二氧化碳气体保护焊是利用二氧化碳作为保护气体的气体保护电弧焊,简称二氧化碳焊。
熔化极氩弧焊又称熔化极惰性气体保护焊,简称MIG焊。
它是使用熔化极的惰性气体(氩气)保护焊。
通过电弧的燃烧产生热量,热量一方面加热工件、维持熔池,另一方面熔化焊丝填充到熔池中去,补充焊缝金属。
在焊接过程中,熔滴通过电弧空间向熔池转移的过程称为熔滴过渡。
熔滴过度有射流过渡、亚射流过渡和短路过渡。
当熔化极氩弧焊在小电流下工作时,电弧在焊丝端部熔滴的底部燃烧,此时熔滴过渡形式为体积较大的粗滴过渡。
随着电流的增加,由于氩气保护时弧柱的电场强度值较低,电弧容易向上扩展,斑点力阻碍熔滴过渡的作用减弱。
同时随着电流增加,熔滴温度提高,表面张力减小,使得熔滴的体积减小。
当电流进一步增加达到某一电流值时,弧根已经完全笼罩住熔滴,并且熔滴拉长形成缩颈。
这样缩颈处的电流密度大大增加,将引起液态金属的蒸发,在缩颈周围充满了金属蒸汽,具备了产生电极斑点的条件。
此时,弧根就会突然从熔滴的根部扩展到缩颈的根部,这一现象称为跳弧。
出现跳弧后,随着一个较大的熔滴过度后,焊丝端部的液态金属在较强的等离子流力的作用下被压缩成尖锥状。
端部液态金属熔滴以很小的体积、很高的加速度沿电极轴向冲向熔池。
这些细小的熔滴在宏观上看像一条细流,因此称这种过度形式为射流过度。
焊缝设计每个同学焊一道焊缝,使用的工艺规范与组长协商。
同一组别的同学不能使用相同的规范。
操作方法一、机器连接1、正确连接焊枪和工件正接焊枪;负接工件2、安装焊丝盘正确安装焊丝3、连接保护气气路;以上由指导老师或组长负责二、操作1、设定工作模式“MANUL”;MIG/MAG 非一元化直流焊接2、调节工艺规范之电流,●按参数选择键(2),令“A”上的指示灯(8)亮,●调节调节钮(1)…调节电流参数值;3、调节工艺规范之电压,●按参数选择键(3),令“V”上的指示灯(9)亮,●调节调节钮(1)…调节电压参数值;4、按焊丝材料选择键(6),选择合适的焊丝材料;5、按焊丝直径选择键(7)…选择所用焊丝直径;6、按焊枪操作模式键(5)…选择焊枪操作模式- 2 步操作模式(常规模式)7、调整焊枪的角度,并前后移动焊枪令焊丝对正焊缝;8、按下启动按钮,启动焊接开关;9、起弧成功后,马上拉起小车的离合器,小车自动行走,自动焊接;10、待焊枪接近焊缝末端时,松开启动按钮;11、按下小车离合器,停止小车;完成焊接过程。
焊接做好记录。
三、关机1.关焊机电源开关2.关气瓶总开关;3.打扫卫生。
实验总结1.对比综述三种焊接方法的特点、性能、优缺点及应用范围。
2.观察电弧焊焊缝成型,对比同组其他同学的焊接规范及焊缝成型,总结出焊接规范与成型的规律。
实验报告实验报告要求:1、综述两种焊接方法的原理、特点及应用范围。
2、画弧焊系统连接图,注意工件极性。
3、分析对比同组其他同学的熔化极气体保护焊接规范及焊缝成型,总结出焊接规范与成型的规律。
4、分析两种实验的效果。
附: TPS2700焊机简介图TPS2700焊机三示图(A)焊枪接口2)…连接焊枪(B)负极快速接口…用于MIG/MAG焊时接地线TIG焊时接焊枪电缆焊条电弧焊(MMA)时根据焊条类型接地线电缆或焊钳(C)田正极快速接口…用于TIG焊时接地线焊条电弧焊时(MMA)根据选用焊条类型接地线或焊钳(D)焊枪控制线接口…接焊枪控制线插头(E) LocalNet连接口…连接系统附加设备的标准接口(如遥控器、JobMaster焊枪等)(F)堵头(G)电源开关…用于开关焊机(H)保护气接口(D带折曲保护的电源电缆(J)堵头(可装局域网连接口)(K)带制动装置的焊丝盘安装架…用于承托标准尺寸焊丝盘,重量可达16kg, 最大直径300mm(L)四轮送丝系统4、正确连接焊枪和工件正接焊枪;负接工件5、安装焊丝盘小心!盘绕的焊丝可能造成伤害。
安装焊丝时,要紧捏住焊丝未端,防止焊丝弹开后乱窜造成伤害。
安装焊丝盘1.将开关(G)拨至“0”位置2打开焊丝盘盖3.将焊丝盘装到焊丝盘托架(K)上- 注意方向要正确4.安装时将拨杆对准插入到焊丝盘预留的孔中5.通过调谐螺丝调节制动力6.关上焊丝盘盖注意!应随时调节制动力,以使停止焊接时焊丝盘不会继续转动——但不可调得过大,免使马达过载。
小心!如果焊丝盘跌落会造成危险!确保焊丝盘牢固安装在焊丝盘托架上。
TPS2700:使用篮式焊丝盘时,配用Fronius“篮式焊丝盘盘芯”(不会有任何金属物与焊丝盘架接触)。
焊丝送进1.电源开关(G)拨至“0”位置2.打开焊丝盘盖3.向前扳下锁紧杆4.拉起压紧杆5.将焊丝穿过进丝管(e)并伸进焊枪送丝管(f)内约5cm6.扳下压紧杆7.将锁紧杆扳回垂直位置8.调节压紧力9.将焊枪尽量拉直10. 取下焊枪喷嘴及导电嘴11. 插上电源12. 将电源开关(G)拨至“I”位置13. 按下“点动送丝”钮(23)并按住不放直至焊丝穿出焊枪小心!焊丝快速穿出焊枪时是危险的!此时应握住焊枪防止朝向人的面部或身体。
14.松开“点动送丝”钮15.将电源开关(G)拨至“0”位置16.拧好导电嘴,装回喷嘴17.盖好焊丝盘盖更换送丝轮为了获得理想的送丝效果,必须根据焊丝规格及材质选用合适的送丝轮。
请参阅零备件表中送丝轮选用表——根据送丝类型(2 轮送丝/4 轮送丝系统),图20 焊丝送进焊丝规格和材质选择。
图控制面板(1) 调节钮…调节各参数值。
该调钮上指示灯亮时,可以用此钮调节对应项目的参数。
(2) 参数选择键…可选择进行操作的参数项目:- “a”焊角尺寸- 板厚- 焊接电流- 送丝速度- F1 指示- 送丝系统负载指示如果某参数项目指示灯亮并且调节钮(1)的指示灯亮则该参数项可通过调节钮进行调节。
(3) 参数选择键…可选择进行操作的参数项目:- 弧长修正- 熔滴过渡/电弧推力修正- 焊接电压- 焊接速度- 作业号n0- F3 指示如果某参数项目指示灯亮并且调节钮(1)的指示灯亮则该参数项可通过调节钮进行调节。