高猛高的切削加工
各种机加工工时计算表

1200.00 0.833333333
0.2-0.3 0.15 26.0 1379
>>>>>>>往复式平面粗磨理论工时计算<<<<<<<
零件参数
砂轮、机床参数
工件材料
淬火钢 砂轮直径 mm
400
磨削形式
零件装置在夹具中或用千 分表校准
**当加工孔径较大 时,ap取大值;加 工孔径较小,且加 工精度要求较高 时,ap取小值
钢、铸钢 刀具材料 精镗 刀具类型 5 刀具直径 mm 20 推荐切削参数范围 0.6-1.2 1.00 8 509 请输入实际切削参数 3.00 0.60 1.00 600.00 0.3
刀具参数
硬质合金 镗刀块 5.00
4.00 20 1273
>>>>>>>高速钢铰刀铰孔理论工时计算<<<<<<<
零件参数
材料种类
材料性能
孔直径 mm
铰
刀具直径 mm 待加工孔深度 mm
切削深度 mm 铰削余量 mm 实际每转进给量 实际主轴转速 理论工时 min
推荐切削参数 中硬铸铁 铰削余量 mm
175HBS 每转进给量 f mm 6.00 切削速度 m/min 6.0 主轴转速 10.0
材料种类 孔直径 mm
深度 mm
钻
零件参数
不锈钢 刀具直径 mm
12.50 每转进给量 mm
20.00
切削速度 主轴转速
m/min
请输入实际切削参数
推荐切削参数范围 8 ~ 20
难切削材料加工参数选择

1. 前角选择的原则:刀具材料的抗弯强度和韧性较高时,可选用大前角。
高速钢刀具的前角,在同样条件下,可比硬质合金刀具的前角大5-10°,而陶瓷的前角又要比硬质合金的小一些。
加工塑性材料宜选较大的前角,以减少金属变形和摩擦。
加工脆性材料时,应选5-15读的较小前角。
工件材料硬度、强度较低时,应选用较大前角,反之,选负前角或较小的正前角,以增强刀刃的强度和散热的体积。
粗加工取较小的前角,精加工取较大的前角,精密成型刀具取零度前角。
2. 倒棱选择原则:倒棱宽度和进给量有关。
倒棱宽度一般取(0.3~0.8)f 粗加工取大值。
进给量f<=0.2mm/r 的精加工刀具,不宜磨出负倒棱。
高速钢倒棱前角取-5~0°,硬质合金倒棱角去-15~-5。
另外也可以采用刃口钝圆形式代替倒棱,可以增强刃口强度,一般用于粗加工。
3. 后角选用原则:后角主要按照切削厚度来选择。
切削厚度小时,宜选用大后角,以减少刃口圆弧半径,使刃口锋利。
当f<=0.25mm/r 时,取后角为10~12°,反之,取后角为6~8°。
后角还依据材料强度和硬度选择,材料强度和硬度高,应取小的后角,相反则取大的后角,当工艺系统刚性差时,应选用小的后角或刃带宽=0.1mm~0.2mm,角度为0的刃带。
另外后角的选择与刀具的运动轨迹有关。
副后角选择原则与主后角相似。
4. 主偏角选择原则:在工艺系统和工艺要求允许的情况下,主偏角宜选的小一些。
工艺系统刚性好、切深小和工件硬度高时,如对冷硬铸铁和淬火钢的加工,取10~30°,工艺系统差可取75~93°。
粗加工时为了增加刀尖强度,改善散热条件,应取较小主偏角。
5. 副偏角的选择原则:在工艺系统刚性较好的情况下,副偏角不宜取得太大,精加工时取5~10°,粗加工时取10~15°。
切断刀或切槽刀为了增强刀头强度,取1~2°。
锰冶炼工艺的探讨
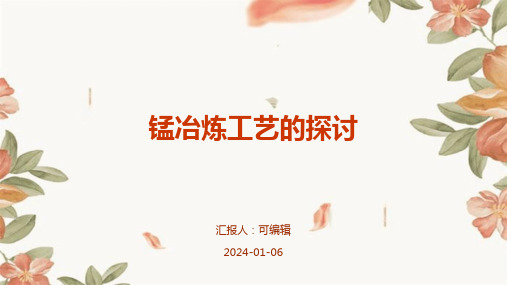
锰矿的特点包括:品位较低,通常需要经过选矿才能提高品位;成分复杂,含有多种杂质元素,需要经过冶炼 才能提取纯锰;赋存状态多样,有露天矿和地下矿之分,开采方式不同。
锰矿的开采方法
浮选设备
利用不同表面疏水性的原理,使矿石在气泡 和水的带动下按表面疏水性的差异进行分离 的设备。常用的浮选设备有浮选机、搅拌槽 、浮选柱等。
磁选设备
利用不同磁性的原理,使矿石在磁场中按磁 性强弱进行分离的设备。常用的磁选设备有 永磁滚筒、高梯度磁选机、电磁除铁器等。
03
锰矿的焙烧与还原
锰矿焙烧的目的与原理
技术
高温气体还原技术、气流控制技术、环保技术等。
04
锰合金的生产与加工
锰合金的种类与特性
锰合金种类
高锰钢、中锰钢、低碳锰钢等。
特性
高锰钢、中锰钢、低碳锰钢等。
锰合金的生产工艺
01
02
03
04
矿石准备
破碎、磨粉、磁选等。
熔炼
高温熔化矿石,加入其他合金 元素。
铸造
将熔融的金属浇注到模具中, 冷却后得到铸件。
锰合金的加工设备与技术
铣削设备
Hale Waihona Puke 铣床、加工中心等 。焊接设备
焊接机、焊枪等。
切割设备
锯床、激光切割机 等。
钻孔设备
钻床、攻丝机等。
技术参数
切削速度、进给量 、切削深度等。
05
锰冶炼的环境保护与资源利用
锰冶炼的环境影响
01
02
03
大气污染
锰冶炼过程中会产生大量 的烟尘和气体,其中含有 硫、氮等氧化物,严重污 染大气环境。
高锰钢的切削加工性讲解

返回
刃倾角
• 为了保持刀尖部分的强度,切削高锰钢时 一般应选择负刃倾角。
• 选用硬质合金刀具时,λs =-5°~0°。
• 选用陶瓷刀具时,λs =-10°~-5°。
刀尖圆弧半径
• 切削高锰钢时,不论采用何种刀具材料,刀尖 部分都应修磨出较大的圆弧半径,以加强刀 尖强度,提高刀具耐用度.一般粗车时rε=1~ 2 mm;半精车时 rε=0.5~1 mm;精车时 rε=0.2~0.5mm。工艺系统刚性好时取大 值,反之取小值 。
前后角
主副偏角
刃倾角
前角与后角
1. 切削高锰钢时,为了减轻加工硬化,要求刀具保持 锋利.但一般不可以采用大前角,因为前角大不利 于保证刃口强度和改善散热条件.常采用较小前 角或负前角及较大后角,但后角太大也会削弱刃 口强度引起崩刃。 2. 采用硬质合金刀具时,γ0=-3°~3°, α0=8°~12°;采用陶瓷刀具时,γ0=-5°~10°,α0=5°~10°。粗车时取小值,精车时取 大值。
返回
铣削ZGMn13的刀具磨损曲线
结束
水韧处理:
所谓水韧处理,就是把钢加热到1000℃~ 1100℃,保温一段时间,使钢中的碳化物全部 溶入奥氏体中,然后迅速冷却,使碳化物来不 及从奥氏体中析出,从而保持了单一的均匀 的奥氏体组织.
铁碳合金相图
返回
高锰钢在切削过程中,由于塑性变形大, 奥氏体组织转变为细晶粒的马氏体组织, 从而产生严重的硬化现象。加工前硬度一 般为HBS200~220,加工后表面硬度可达 HBW450~550,硬化层深度0.1~0.3 mm, 其硬化程度和深度要比45号钢高几倍。严 重的加工硬化使切削力增大,加剧了刀具 磨损,也容易造成刀具崩刃而损坏。
4. 高锰钢在切削过程中,由于塑性变形和切 削力的影响,切削层及表层下一定深度范围 内会产生严重的加工硬化现象。为了使刀 尖避开毛坯表层和前一次走刀造成的硬化 层,应选择较大的切削深度和进给量。 5. 一般粗车时αp =3~6 mm,f=0.3~0.8 mm/r;大件粗车时可取αp =6~10 mm; 半精车时αp =1~3 mm;f=0.2~0.4 mm/r;精车时口αp ≤1 mm;f≤0.2mm/r。
针对生产过程中各个环节分析高锰钢铸件裂纹产生的原因
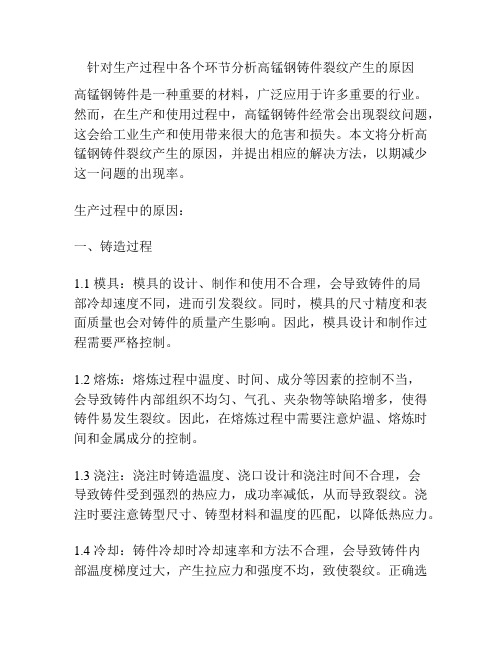
针对生产过程中各个环节分析高锰钢铸件裂纹产生的原因高锰钢铸件是一种重要的材料,广泛应用于许多重要的行业。
然而,在生产和使用过程中,高锰钢铸件经常会出现裂纹问题,这会给工业生产和使用带来很大的危害和损失。
本文将分析高锰钢铸件裂纹产生的原因,并提出相应的解决方法,以期减少这一问题的出现率。
生产过程中的原因:一、铸造过程1.1 模具:模具的设计、制作和使用不合理,会导致铸件的局部冷却速度不同,进而引发裂纹。
同时,模具的尺寸精度和表面质量也会对铸件的质量产生影响。
因此,模具设计和制作过程需要严格控制。
1.2 熔炼:熔炼过程中温度、时间、成分等因素的控制不当,会导致铸件内部组织不均匀、气孔、夹杂物等缺陷增多,使得铸件易发生裂纹。
因此,在熔炼过程中需要注意炉温、熔炼时间和金属成分的控制。
1.3 浇注:浇注时铸造温度、浇口设计和浇注时间不合理,会导致铸件受到强烈的热应力,成功率减低,从而导致裂纹。
浇注时要注意铸型尺寸、铸型材料和温度的匹配,以降低热应力。
1.4 冷却:铸件冷却时冷却速率和方法不合理,会导致铸件内部温度梯度过大,产生拉应力和强度不均,致使裂纹。
正确选择冷却方法、冷却时间和冷却速率,控制温度梯度,能够有效减少铸件的热应力。
二、热处理过程高锰钢铸件在使用前通常需要进行热处理,如退火、正火、淬火等,以获得更好的性能、组织和硬度。
但热处理过程本身也可能成为产生裂纹的原因。
2.1 温度:热处理中温度过高或温度不均匀,会导致铸件内部产生应力不均,易发生裂纹。
2.2 时长:热处理时间过长或过短,也可能导致铸件内部应力过大而产生裂纹。
2.3 冷却速度和方法:热处理后的铸件需要进行冷却,若冷却过程不恰当,也会使铸件产生裂纹。
三、机械加工过程机械加工过程中裂纹通常是由过大的切削力引起的。
多余的应力作用于铸件的表面,产生一些小裂纹,其在后续加工过程中会扩大。
这是一种慢性损伤,会减少高锰钢铸件的使用寿命。
解决方法1. 完善的工艺控制:通过合理的模具、熔炼和浇注工艺及合适的冷却方式,可以减少高锰钢铸件的热应力和应力过大的问题,从而避免裂纹的产生。
高强度钢和超高强度钢的切削加工

高强度钢和超高强度钢的切削加工什么是高强度钢和超高强度钢?所谓高强度钢,是指那些在强度和韧性方面结合很好的钢种。
低合金结构钢,经调质处理后,具有很好的综合力学性能。
其抗拉强度σb>1200MPa时,叫高强度钢;其抗拉强度σb>1500MPa时,称为超高强度钢。
超高强度钢,视其合金含量的多少,可分为低合金超高强度钢(合金含量不大于6%)、中合金超高强度钢和高合金超高强度钢。
含一种合金元素的高强度合金钢有铬钢、镍钢、锰钢等;含两种合金元素的合金钢有铬镍钢、铬锰钢、铬钼钢等;含三种以上合金元素的高强度合金钢有铬锰硅钢、铬镍钨钢、铬镍钼钢、铬锰钛钢、铬锰钼钒钢等。
高强度钢和超高强度钢的原始强度和硬度并不高,但是经过调质处理后可获得较高的强度,硬度在HRC30~50之间。
钢的抗拉强度与硬度之间存在一定的关系。
一般来说,硬度提高强度也随之增高,但不能说高强度钢就是高硬度钢。
所谓高强度钢和超高强度钢,是指综合性能而言的。
淬火钢的硬度很高,但不能称为高强度钢和超高强度钢,其原因是它的综合性能不好,几乎没有塑性,韧性也很差,只能作耐磨零件和工具。
2 高强度钢和超高强度钢有哪些切削特点?高强度钢和超高强度钢,由于加入不同量的合金元素,经热处理后,Si、Mo、Ni等元素使固溶体强化,金相组织多为马氏体,具有很高的强度(最高可达1960MPa)和较高的硬度(HRC >35),冲击韧性高于45号钢,切削时具有以下特点:1) 刀具易磨损、耐用度低:高强度钢和超高强度钢,调质后的硬度一般在HRC50以下,但抗拉强度高,韧性也好。
在切削过程中,刀具与切屑的接触长度小,切削区的应力和热量集中,易造成前刀面月牙洼磨损,增加后刀面的磨损,导致刃口崩缺或烧伤,刀具的耐用度低。
2) 切削力大:高强度钢和超高强度钢的剪切强度高,变形困难,切削力在同等的切削条件下,比切45号钢的单位切削力大1.17~1.49倍。
3) 切削温度高:这两种钢的导热性差,切削时切屑集中于刃口附近很小的接触面内,使切削温度增高。
工件切削加工性
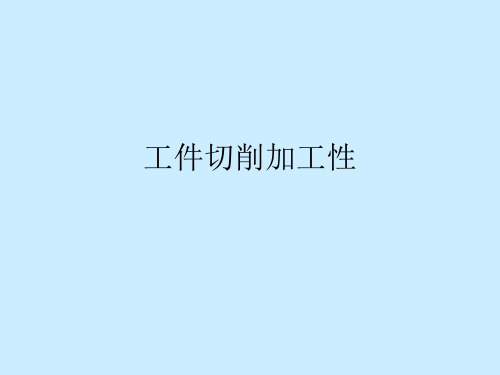
刃和刀尖的强度,一般取γ。=-4—0º,主偏角kr适当减小,刀
尖圆弧半径rε适当加大。
淬硬钢的组织为回火马氏体,硬度达HRC60以上,塑性
和导热系数都很低。其加工性及刀具材料、刀具几何参数的 选择基本上与冷硬铸铁同。对它们进行精加工,可采用CBN 刀具。
κr= 45° ~ 75°、λs= -10 °
6.钛合金切削加工性分析
1).钛合金特点和分类
a)密度小(约为 4.5g / cm3 ),比钢约小一倍。
b)强度极限高(可达σb=0.981~1.37GPa), 钛合金的比强度(单位重量强度)很高,尤其在高温下比强度仍 很高,这一点对航空、航天工业尤为重要。
工件切削加工性
表 7– 1 材料可加工性分级
分级
名称及种类
Kv
1 很容易切削材料 一般有色金属
> 3.0
2
易切削钢
容易切削材料
3
较易切削钢
2.5 ~ 3.0 1.6 ~ 2.5
4
一般钢及铸铁
1.0 ~ 1.6
普通材料
5
稍难切削材料 0.65 ~ 1.0
6
较难切削材料 0.5 ~ 0.65
7
难切削材料
理 ;对镍基高温合金可采用固溶处理(淬火)
b)、首选一足够的vc以保证加工质量,再选f 、ap
c)、选择合适的刀具材料和角度 连续切:YG6X、YW1 断续切:M42、501、B201
高速钢刀具:γo=15 ° ~20°、αo=12 ° 、κr=45 ° 硬质合金刀具:γo=5° ~ 10°、αo= 8° ~ 15° 、
在自动机床或自动生产线上,常常以切屑
工件材料的切削加工性
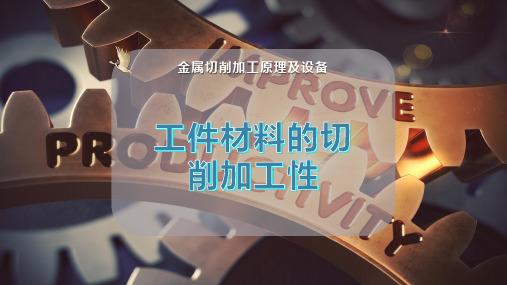
1.1切削加工性的评定指标
●考虑已加工表面质量的标志方法 在一定的切削条件下,以加工某种材料是否容易达到 所要求的加工表面质量的各项指标来衡量。 ●考虑安全生产和工作稳定性的标志方法 在相同的切削条件下,单位切削力较小的材料,其切 削加工性较好。在重型机床或刚性不足的机床上加工,考 虑到人身和设备的安全和切削力的大小。在自动化生产和 深孔加工中,往往用材料断屑的难易程度来衡量其切削加 工性的好坏。
用切削速度来衡量 的相对切削加工性
也可用加工材料的物理、化学和力学性能的高低来 衡量切削该材料的难易程度。见表4.2
1.2 影响材料切削加工性的因素
工件材料切削加工性的好坏,主要决定于工件材料的物 理、力学性能、化学成分、热处理状态和表层质量等。
1.材料的硬度和强度
工件材料在常温和高温下的硬度和强度越高,则在加 工中的切削力越大,切削温度越高,刀具耐用度越低,故 切削加工性就越差。有些材料在常温下其硬度和强度并不 高,但随着切削温度的升高,其硬度和强度也提高,切削 加工性变差。例如不锈钢。
金属切削加工原理及设备
工件材料的切削加工性
工件材料的切削加工性——是指工件材料可被切削的难 易程度。
1.1 切削加工性的评定指标
●考虑生产率和刀具耐用度的标志方法 生产率一定时,刀具耐用度越高,切削加工性越好。 刀具耐用度一定时,所允许的切削速度越高,切削加工性 越好。切削速度一定时,以达到刀具磨钝标准时所切除的 金属材料体积越大,则材料的切削加工性就越好。
2.材料的塑性和韧性
工件材料的塑性越大,其切削变形就越大;韧性越强,则切 削消耗的能量就越多,这都会使温度升高。材料的塑性和韧性越 高,刀具表面冷焊现象严重,刀具容易磨损,且不易断屑,则切 削加工性变差。若材料的塑性和韧性过低时,则使切屑与刀具前 面接触面过小,切削力和切削热就会集中在刀刃附近,将导致刀 具切削刃破损加剧和工件已加工表面质量下降。即材料的塑性和 韧性过高或过低,都会使其切削加工性能下降。例如高锰钢的硬 度和强度较低,但伸长率和冲击韧度很高。切削时塑性变形大, 加工硬化严重,断屑困难,硬化层较厚,切削时硬度提高较多, 产生的切削力较切削正火 45钢提高一倍以上。高锰钢的热导率 小,切削温度高,刀具易磨损,因此,切削加工性差。
高锰钢的切削加工探讨

高锰钢的切削加工探讨[摘要]高锰钢是含锰量在11%—18%的钢。
它是一种耐磨钢,其硬度只有hb210,屈服点较低,具有较高的塑性和韧性。
高锰钢在受到外来压力和冲击载荷时,会产生很大的塑性变形或严重的加工硬化现象。
高锰钢又分高碳高锰钢、中碳高锰钢、低碳不锈高锰钢、高锰耐热钢。
关键词高锰钢切削加工一、高锰钢切削加工特点由于高锰钢具有较高的塑性、韧性,其加工特点:一是加工硬化严重。
在切削过程中由于塑性变形大,奥氏体组织转变为晶粒的马氏体组织,从而产生硬化现象,加工后硬度达到hb450~550,硬化层深度达到0.1~0.3mm,其硬化程度比45号钢高几倍。
从而使切削力增大,加剧刀具磨损、崩刃。
二是由于其在切削时功率大,产生热量多,而其本身导热系数低,故而切削温度比45号钢高200~250°c,因此刀具磨损严重、耐用度降低。
三是其韧性是45号钢的8倍、难以断屑。
四是其膨胀系数大,在高温切削下,局部受热影响大,尺寸难以把握控制,所以切削高锰钢时要分粗加工、半精加工、冷却后再进行精加工,以保证尺寸精度。
二、高锰钢切削性能的改变金属材料的切削性能取决于其力学性能、物理性能:强度、硬度、塑性、韧性、耐磨性、线膨胀系数。
在实际生产中,改变其物理性能及力学性能的方法主要是热处理方法,从而改变其切削性能。
我是将高锰钢加热至600°c~650°c,保温2小时后再冷却,使它的奥氏体组织转变为索氏体组织来改变加工性能。
零件加工完后,使用前再进行淬火处理,使其内部组织重新转变为单一的奥氏体组织。
三、切削高锰钢时,刀具的选用1、刀具材料的选用难以切削加工的高锰钢对刀具材料的要求更高。
刀具材料必须具有更高的高耐磨、高耐热(红硬性)、高硬度、高强度、良好的塑形与韧性及良好的工艺性。
在实际生产中,我主要选用常用的刀具材料yg类硬质合金,也可以选用陶瓷刀片、cn25涂层刀片和cbn 刀具,但较贵。
对于要求高的零件,用陶瓷刀进行精车。
工件材料的切削加工性

0
100
200 300 400 布氏硬度(HB)
500
图3-47 碳钢硬度与可切削性的关系
★ 材料的切削加工性是上述这些机械性能(硬度、强度 、塑性、韧性、弹性模量等)综合影响的结果。
6
2.7.2 材料性能对切削加工性影响
材料物理化学性能对切削加工性的影响
◆工件材料导热系数的影响 工件材料导热系数低,切削温度高,刀具易磨损,切 削加工性差。 金属材料导热系数大小顺序:纯金属、有色金属、碳 结构钢、铸铁、低合金结构钢、合金结构钢、工具钢、 耐热钢、不锈钢。 ◆ 工件材料物理化学反应的影响 如镁合金易燃烧,钛合金切屑易形成硬脆化合物等,不 利于切削进行。
v3600 Kr v3600 j
(2-10)
2
材料切削加工性概念和指标
表2-12 材料相对加工性等级
加工 性 等级
相对加
材料名称及种类 很易切削 一般有色
材料 容易切削 材料 金属
工性Kr
>3.0
代 表 性 材 料
铜铝合金,铝铜合金,铝镁合金
1
2
3 4
易切削钢 较易 切削钢 一般钢、
2.5~3 1.6~
< < < 导热系数k 418.68 293.08 83.47 167.47 ~ ~ ~ (W/m· K) 293.08 ~83.74 167.47 62.80
常用金属材料的切削加工性
常用金属材料的切削加工性
◆ 有色金属 有色金属(如铝及铝合金,铜及铜合金等)通常属于易 切削材料。 ◆ 铸铁 铸铁的加工性一般较碳钢好。比较各种铸铁加工性的好 坏,主要取决于石墨的存在形式、基体组织状态、金属 , 组织成分和热处理的影响。例如:灰铸铁,可锻铸铁和 球墨铸铁中,石墨分别呈片状、团絮状和球状,因此它 们的强度依次提高,加工性随之变差。
高锰钢的切削加工

高锰钢的切削加工1.高锰钢有哪几种?其性能如何?锰含量约为11%~18%的钢称高锰钢。
常用的铸造高锰钢ZMn13的化学成分为:Mn含量11%~14%,c含量1.0%~1.4%,Si含量0.3%~1.0%,P含量<0.03%,S含量<0.05%。
高锰钢是一种耐磨钢,经过水韧处理的高锰钢可以得到较高的塑性和冲击韧性。
所谓水韧处理,就是把钢加热到1000℃~1100℃,保温一段时间,使钢中的碳化物全部溶入奥氏体中,然后迅速冷却,使碳化物来不及从奥氏体中析出,从而保持了单一的均匀的奥氏体组织。
经过水韧处理的高锰钢称为高锰奥氏体钢。
其力学性能为:σb=980 MPa,σs=392 MPa,HB210,δ=80%,αk=2.94 MJ /m2。
高锰钢具有很高的耐磨性,虽然它的硬度只有HB210,但它的屈服点σs较低,只有σb的40%,因此具有较高的塑性和韧性。
高锰钢在受到外来压力和冲击载荷时,会产生很大的塑性变形或严重的加工硬化现象,钢被剧烈强化,硬度显著提高,可达HB450~550,因此有了较高的耐磨性。
高锰钢可分为高碳高锰耐磨钢、中碳高锰无磁钢、低碳高锰不锈钢和高锰耐热钢。
几种高锰钢的牌号和性能见表5-1。
2.高锰钢有哪些切削加工特点?高锰钢锰含量高达11%~18%,具有较高的塑性和韧性,在切削加工中有以下特点:(1)加工硬化严重:高锰钢在切削过程中,由于塑性变形大,奥氏体组织转变为细晶粒的马氏体组织,从而产生严重的硬化现象。
加工前硬度一般为HB200~220,加工后表面硬度可达HB450~550,硬化层深度0.1~0.3 mm,其硬化程度和深度要比45号钢高几倍。
严重的加工硬化使切削力增大,加剧了刀具磨损,也容易造成刀具崩刃而损坏。
(2)切削温度高:由于切削功率大,产生的热量多,而高锰钢的导热系数比不锈钢还低,只有中碳钢的1/4,所以切削区温度很高。
当切削速度Vc<50 m/min 时,高锰钢的切削温度比45号钢高200℃~250 ℃,因此,刀具磨损严重,耐用度降低。
高锰钢切削加工工艺性能的分析

高锰钢切削加工工艺性能的分析作者:孙广军来源:《工业设计》2018年第04期摘要:本文论述了高锰钢材料的特性,列举了高锰钢零件切削加工工艺性能及切削加工加工过程中经常出现的不良现象,分析了出现切削问题的原因,并以高锰钢材料的车削加工为例指出了提高切削加工工艺性能的刀具参数、切削用量和辅助切削的特殊方法,为提高高锰钢材料的切削效率提供参考。
关键词:高锰钢;切削加工;切削加工工艺参数高锰钢是一种耐磨钢,锰的含量通常在1O%-18%之间。
在常温下,通过对高锰钢进行水韧处理,可得到均匀启勺单相奥氏体组织,单相奥氏体组织的强度、硬度比较低,具有很好的塑性及韧性。
当材料表面遇到冲击、突然加压或摩擦后发生塑性变形,同时材料表面被剧烈强化,硬度可达HBW450-550,表面获得良好的耐磨性,同时材料内部仍保持良好的塑性及韧性。
由于高锰钢具有良好的耐磨性能及抗冲击性能,其广泛应用于采石、挖掘、采矿、铸造、煤炭工业及钢铁行业。
由于高锰钢组织具有导热系数低、线膨胀系数大、伸长率大和易加工硬化等特点,造成高锰钢材料切削加工工艺性能很差,车削加工的过程中容易出现加工硬化、切削力大、切削温度高、加工精度低及断屑困难的问题。
严重影响了高锰钢制品的成品率机加工效率,造成高锰钢制品加工成本提高。
因此需要根据高锰钢材料的特性探索合理的切削加工工艺参数,有效地解决高锰钢的切削加工难题。
1高锰钢切削加工过程中容易出现的问题1.1加工硬化由于水韧处理后的高锰钢组织为均匀的单相奥氏体组织,由于面心立方晶格的结构特点,受到外力作用晶格容易发生滑移,同时诱发硬度较低的奥氏体组织转变为高硬度的马氏体组织,使材料加工面发生加工硬化现象(硬度可达HBW 500)。
使))具磨损严重。
1.2切削力大,刀尖处应力集中严重经X射线衍射仪及比对标准卡片分析得出高锰钢工件在切削过程中,材料表面会发生氧化反应生成Mn203,经金相显微镜测定氧化层厚度约为o.1-o.3mm。
基于正交试验法的U71Mn高锰钢的表面粗糙度模型分析

基于正交试验法的U71Mn 高锰钢的表面粗糙度模型分析史柏迪,庄曙东,虞航(河海大学机电工程学院,江苏常州213022)表1因素水平表水平因素n /(r·min -1)f z /(mm ·z -1)a p /mm a e /mm 140000.04 1.03250000.06 1.56360000.08 2.09470000.10 2.512580000.123.015摘要:首先通过切削用量手册确定切削参数的区间,然后利用正交试验法设计了四因素五水平的U71Mn高锰钢铣削试验,最后通过极差分析法研究高锰钢的表面粗糙度与主轴转速n 、每齿进给量f z 、铣削深度a p 、铣削宽度a e 及除去切削参数之外其他影响因素之间的关系,以此来选择合理的切削参数来解决U71Mn高锰钢易加工硬化,以及加工过程中表面粗糙度难以控制的问题。
最后通过试验得出影响的先后次序,发现每齿进给量f z 和铣削宽度a e 对其影响较大,主轴转速n 和铣削深度a p 影响较小的结论。
关键词:U71Mn高锰钢;表面粗糙度;极差分析法;切削参数中图分类号:TG 15文献标志码:A文章编号:1002-2333(2020)05-0053-04Study on the Surface Roughness Model of U71Mn High Manganese Steel Based on Orthogonal TestSHI Baidi,ZHUANG Shudong,YU Hang(School of Mechanical and Electrical Engineering,Hohai University,Changzhou 213022,China)Abstract:This paper determines the range of cutting parameters by the manual of cutting parameters.The millingexperiment of U71Mn high manganese steel with four factors and five levels is designed using the orthogonal experiment method,and the relationship between the surface roughness of high manganese steel and the spindle speedn,the feed rate of each tooth f z ,the milling depth a p ,the milling width a e and other factors except the cutting parameters is studied by the range analysis method in this way.The reasonable chip parameters can be selected to solve the problem that U71Mn high manganese steel is easy to work hardening and the surface roughness is difficult tocontrol in the process of machining.At last,it is found that the feed per tooth f z and milling width a e have great influence on it,and the spindle speed n and milling depth a p are small.Keywords:U71Mn high manganese steel;surface roughness;range method;cutting parameters0引言我国大部分铁轨材料采用的是标准60kg/m 的U71Mn 高锰钢[1],其具有很强的抗冲击和耐磨性,但切削加工性很差。
X120Mn12高锰钢加工性能特点

高镒耐磨钢X120Mnl2加工性能特点
X12OMnl3高镒钢加工特点:
(1)切割:
X120Mnl2钢板可以采用等离子或激光切割。
(2)成型:
成型可以毫无困难地进行,因为供应条件下的板材具有延展性。
为避免开裂,已通过剪切加工硬化的边缘应沿要形成的边缘进行2至3毫米的倒角研磨。
如果可能,成型应在一次操作中进行,以避免加工硬化。
(3)钻孔:
由于镒含量为11%至14%,高镒钢难以钻孔,并且很快加工硬化。
重型、非常坚固的机械需要使用8%钻高速钢的穿甲钻,或者最好使用带有可更换硬质合金刀片的特殊钻头。
避免中心冲孔或让钻头在没有钻进的情况下在表面上摩擦,这会产生加工硬化的效果。
(4)焊接:
焊接应使用E308Mo型奥氏体不锈钢耗材进行。
作为热膨胀系数高、导热系数低的高镒钢,焊接应在低热值下进行。
材料在300℃至800℃的温度范围内长时间放置会因碳化物析出而导致脆化。
上海频开实业有限公司位于国内现有规模较大的钢材市场一乐从钢铁世界,是涟钢耐磨钢战略客户,供应高镒耐磨钢X120MnI2,可供规格4-25mm,代订期货;其他产品有高强度钢板、工
程机械用钢、汽车大梁钢、冷轧高强车厢板、耐候钢、耐酸钢、中高碳钢,常备万吨库存,多种规格可选,集原材料供应、加工、物流配送于一体的现代化企业。
高锰钢的切削加工性教材
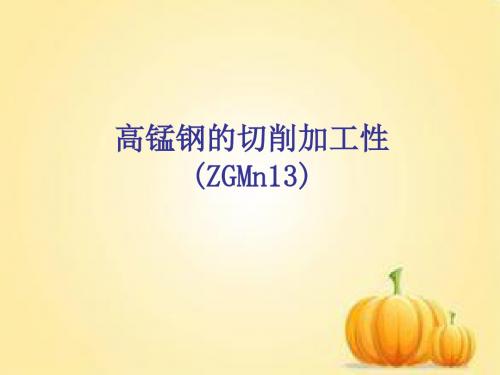
铣削ZGMn13的刀具磨损曲线
结束
水韧处理:
所谓水韧处理,就是把钢加热到1000℃~ 1100℃,保温一段时间,使钢中的碳化物全部 溶入奥氏体中,然后迅速冷却,使碳化物来不 及从奥氏体中析出,从而保持了单一的均匀 的奥氏体组织.
铁碳合金相图
返回
高锰钢在切削过程中,由于塑性变形大, 奥氏体组织转变为细晶粒的马氏体组织, 从而产生严重的硬化现象。加工前硬度一 般为HBS200~220,加工后表面硬度可达 HBW450~550,硬化层深度0.1~0.3 mm, 其硬化程度和深度要比45号钢高几倍。严 重的加工硬化使切削力增大,加剧了刀具 磨损,也容易造成刀具崩刃而损坏。
高 锰 钢 金 相 组 织
高锰钢的切削加工特点:
1. 2. 3. 4. 5. 加工硬化严重 切削力大 切削温度高 断屑困难 尺寸精度不易控制
切削高锰钢的合理方法:
一、通过热处理改善切削加工性 二、合理选择切削刀具的刀具材料 三、合理选择刀具几何参数 四、合理选择切削用量
切削前的热处理
改善高锰钢的切削性能可以通过高温回 o 火来实现。将高锰钢加热 600-650 C 保温 2h 后冷却,使高锰钢的奥氏体组织转变 为索氏体组织,其加工硬化程度显著降 低,加工性能明显改善。加工完成的零 件在使用前应进行淬火处理,使其内部 组织重新转变为单一的奥氏体组织。
刃口倒棱
• 为了保证刃口有足够的强度,减少崩刃现象, 一般应将刃口修磨出负倒棱. • 硬质合金刀具倒棱宽度 bγ1=0.2~0.8 mm, 倒棱前角 γ01=-10°~-5°;如采用陶瓷刀 具,bγ1=0.2 mm,γ01=-20°。
切削用量选择
1. 高锰钢的切削加工性很差,为了维持一定的 刀具耐用度,切削速度应低些 。 2. 采用硬合金刀具时, Vc=20~40 m/min,其 中,较低的速度用于粗车,较高的速度用于 半精车和精车。 3. 采用陶瓷刀具时, 可以选用较高的切削速 度, 一般 Vc=50~80 m/min 。
常用材料的切削加工性能

ZT:常用材料的切削加工性能parti良好的切削加工性能:1 )刀具的寿命较高,或在一定的寿命下允许的切削速度较高2)在相同的切削条件下,切削力较小3)切削温度较低,容易获得较细的表面粗糙度,容易控制切削形状或者断屑§5-1工件材料和切削的加工性本章从工工件材料方面本分析影响生产率及表面质量的因素,以及提高它们的途径:从生产实际中了解到,有些材料容易切削(生产率高,表面质量好),而另一些材料却很切削;分析工件材料的机械物理性能以及化学成分如何影响切削加性,如何提高工件材料的切削加工性。
材料的切削加工性是指导某种材料进行切削加工性的难易程度,其易程度,一般与材料的化学成份,热处理状态、金相组织、物理力学性能以及切削条件有关。
一、衡量切削加工的指标工件材料的切削加工性,通常用下面的一个或数个指标衡量:1、刀具耐用度;2、一定刀具耐用度允许的切削速度;3、切削力;4、切削温度;5、加工表面粗糙度或表面质量。
目前,常用一定刀具耐用度下充许的切削速度V T作为衡量指标。
V T__-指刀具耐用度为T时,切削某种材料的允许的切削速度。
V T越高,说明该材料的切削加工性能好。
任何事情都是相对而言,那么对于材料的切削加工性,也要用相对加工性Kr表示。
它的基准是以切削抗拉强度& b = 0.735Gpa的45#钢,耐用度T=60min时的切削速度Vb60为基准。
相对加工性就是以该基准与切削其它材料时V60的比值。
即Kr=V60 / Vb60①当Kr>1时,说明该材料比45#钢易切削;切削加工性好;②当Kr<1时,该材料比45#钢难切削,切削加工性能差。
常用材料切削加工性,根据相对加工性Kr的大小切分为八级,见表 5 —1。
二、改善材料可切削性的途经1、改善材料的化学成份。
1*在黄铜中加入1 %〜3%的铅,在钢中加入0 .1%〜0.2 5%的铅。
铅可以球状粒子存在于材料的金相组织中,切削时能起很好润滑作用,减少摩擦,使刀具耐用度和表面质量得提咼。
1144易切削钢化学成分

1144易切削钢化学成分
1144易切削钢是一种常用的材料,它具有优异的切削性能和较高的强度。
下面将从化学成分、特性和应用等方面进行介绍。
1144易切削钢的化学成分主要包括碳、锰、硫和磷等元素。
其中碳的含量较低,约为0.4%左右,这使得该钢具有较好的可焊性和可锻性。
同时,锰的含量约为 1.35%,能够提高钢的硬度和强度。
此外,硫和磷的含量较低,分别为0.08%和0.04%,这有助于提高钢的切削性能和加工性能。
1144易切削钢具有一系列优异的特性。
首先,它具有较高的切削性能,能够在切削过程中减少切削力和磨损,提高切削效率。
其次,该钢具有较好的可加工性,能够满足各种复杂零件的加工要求。
此外,1144易切削钢具有较高的强度,能够满足一些对强度要求较高的应用场景。
由于1144易切削钢的优良性能,它在许多领域得到广泛应用。
首先,它常用于制造机械零件,如轴承、齿轮、螺栓等。
其次,该钢还常用于制造汽车零件,如车轴、连接杆等。
此外,1144易切削钢还可以用于制造工具和模具,如刀具、冲模等。
总之,1144易切削钢在机械制造、汽车制造和工具制造等行业都具有重要的应用价值。
1144易切削钢具有优异的切削性能和较高的强度,适用于制造各种机械零件、汽车零件和工具等。
它的化学成分和特性使得它在各个
领域都有广泛应用。
希望通过本文的介绍,读者能够对1144易切削钢有更加清晰的了解。
9crsi是什么材料
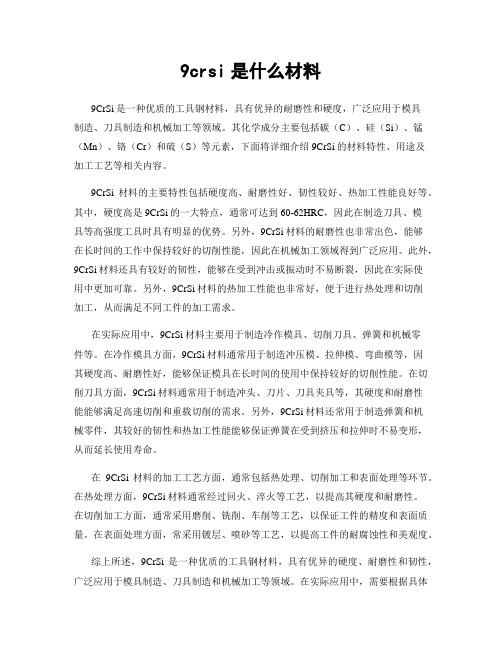
9crsi是什么材料9CrSi是一种优质的工具钢材料,具有优异的耐磨性和硬度,广泛应用于模具制造、刀具制造和机械加工等领域。
其化学成分主要包括碳(C)、硅(Si)、锰(Mn)、铬(Cr)和硫(S)等元素,下面将详细介绍9CrSi的材料特性、用途及加工工艺等相关内容。
9CrSi材料的主要特性包括硬度高、耐磨性好、韧性较好、热加工性能良好等。
其中,硬度高是9CrSi的一大特点,通常可达到60-62HRC,因此在制造刀具、模具等高强度工具时具有明显的优势。
另外,9CrSi材料的耐磨性也非常出色,能够在长时间的工作中保持较好的切削性能,因此在机械加工领域得到广泛应用。
此外,9CrSi材料还具有较好的韧性,能够在受到冲击或振动时不易断裂,因此在实际使用中更加可靠。
另外,9CrSi材料的热加工性能也非常好,便于进行热处理和切削加工,从而满足不同工件的加工需求。
在实际应用中,9CrSi材料主要用于制造冷作模具、切削刀具、弹簧和机械零件等。
在冷作模具方面,9CrSi材料通常用于制造冲压模、拉伸模、弯曲模等,因其硬度高、耐磨性好,能够保证模具在长时间的使用中保持较好的切削性能。
在切削刀具方面,9CrSi材料通常用于制造冲头、刀片、刀具夹具等,其硬度和耐磨性能能够满足高速切削和重载切削的需求。
另外,9CrSi材料还常用于制造弹簧和机械零件,其较好的韧性和热加工性能能够保证弹簧在受到挤压和拉伸时不易变形,从而延长使用寿命。
在9CrSi材料的加工工艺方面,通常包括热处理、切削加工和表面处理等环节。
在热处理方面,9CrSi材料通常经过回火、淬火等工艺,以提高其硬度和耐磨性。
在切削加工方面,通常采用磨削、铣削、车削等工艺,以保证工件的精度和表面质量。
在表面处理方面,常采用镀层、喷砂等工艺,以提高工件的耐腐蚀性和美观度。
综上所述,9CrSi是一种优质的工具钢材料,具有优异的硬度、耐磨性和韧性,广泛应用于模具制造、刀具制造和机械加工等领域。
- 1、下载文档前请自行甄别文档内容的完整性,平台不提供额外的编辑、内容补充、找答案等附加服务。
- 2、"仅部分预览"的文档,不可在线预览部分如存在完整性等问题,可反馈申请退款(可完整预览的文档不适用该条件!)。
- 3、如文档侵犯您的权益,请联系客服反馈,我们会尽快为您处理(人工客服工作时间:9:00-18:30)。
高锰钢的切削加工
1.切削高锰钢时怎样选择刀具材料?
高锰钢属难加工材料,对刀具材料要求较高。
一般来说,要求刀具材料红硬性高、耐磨性好,有较高的强度、韧性和导热系数。
切削高锰钢可选用硬质
合金、陶瓷做刀具材科,也可以用cn25涂层刀片或cbn(立方氮化硼)刀具。
其
中yg类硬质合金具有较高的抗弯强度和冲击韧性(与yt类硬质合金比较),可
减少切削时的崩刃。
同时,yg类硬质合金的导热性较好,有利于切削热从刀尖
散走,降低刀尖温度,避免刀尖过热软化。
yg类硬质合金的磨加工性较好,可
以磨出锐利的刃口。
一般情况下,刀具的耐用度取决于刀具材料的红硬性、耐
磨性和冲击韧性。
yg类硬质合金中含钴量较多时,抗弯强度和冲击韧性好,特
别是提高了疲劳强度,因此适于在受冲击和震动的条件下作粗加工用;含钴量
较少时,其硬度、耐磨性和耐热性较高,适合作连续切削的精加工。
yt类硬质合金具有较高的硬度和较高的耐热性,但与yg类硬质合金相比,其强度低、脆性大,导热性差。
因此,切削高锰钢时通常选用韧性好的yg类硬质合金作刀具材料。
应当注意的是,yg类硬质合金不适于高速切削,因为在高
速切削钢料时,切削时的高温将使刀具前刀面上形成强烈的月牙洼磨损,并加
速后刀面磨损,刀具耐用度降低。
在切削速度较高且切削过程较平稳的情况下
可考虑选用yt类硬质合金作刀具材料。
yg类硬质合金中添加适量的(一般为0.5%~3%左右)tac(碳化钽)或
nbc(碳化铌),可提高其硬度和耐磨性而不降低其韧性。
切削高锰钢可选硬质合金牌号有:yg8、yg6a、yg6x、yg8n、yw1、yw2a、
yw3、yc45、767、798、813等。
采用陶瓷刀片进行高锰钢的精车、半精车,但不能加工粗车,可选用较高
的切削速度,加工表面质量好,刀具耐用度高。
例如利用al2o3基陶瓷刀具切
削50mn18cr4高锰钢比用硬质合金刀具效率提高1~4倍。
采用cbn(立方氮化硼)刀具:CBN刀具可以对高锰钢进行粗车,半精车,
精车。
在使用cbn刀具时应注意被切削材料含锰量不能高于14%,否则,cbn
可能与mn元素产生化学反应使刀具磨损严重,切削性能下降。
具体参见:高锰钢加工用刀具牌号及参数选用
2.切削加工高锰钢时怎样选择刀具几何参数?
高锰钢具有较高的塑性和韧性,加工硬化严重,切削温度高,断屑困难,
容易造成崩刃,因此合理选择刀具的几何参数尤为重要。
(1)前角与后角:切削高锰钢时,为了减轻加工硬化,要求刀具保持锋利。
但一般不可以采用大前角,因为前角大不利于保证刃口强度和改善散热条件。
常
采用较小前角或负前角及较大后角,但后角太大也会削弱刃口强度引起崩刃。
采用硬质合金刀具时,γ0=-3°~3°,α0=8°~12°;采用陶瓷刀具时,
γ0=-5°~-10°,α0=5°~10°。
粗车时取小值,精车时取大值。
(2)主偏角与副偏角:切削高锰钢时,主偏角应小些,这样可以增加刀具散热面积和刀尖强度,副偏角也不宜过大。
选用硬质合金刀具时,一般取
κr=25°~45°,κ′r=10°~20°。
工艺系统刚性好时取小值,反之可适当加大主偏角和副偏角。
选用陶瓷刀具时,主偏角还可大些,一般取κr=45°~60°,精车时可取κr=60°~90°。
(3)刃倾角:为了保持刀尖部分的强度,切削高锰钢时一般应选择负刃倾角。
选用硬质合金刀具时,λs =-5°~0°;选用陶瓷刀具时,λs =-10°~-5°。
(4)刀尖圆弧半径:切削高锰钢时,不论采用何种刀具材料,刀尖部分都应修磨出较大的圆弧半径,以加强刀尖强度,提高刀具耐用度。
一般粗车时
rε=1~2 mm;半精车时rε=0.5~1 mm;精车时rε=0.2~0.5mm。
工艺系统刚性好时取大值,反之取小值。
(5)刃口倒棱:为了保证刃口有足够的强度,减少崩刃现象,一般应将刃口修磨出负倒棱。
硬质合金刀具倒棱宽度bγ1=0.2~0.8 mm,倒棱前角γ01=-10°~-5°;如采用陶瓷刀具,bγ1=0.2 mm,γ01=-20°。
3.切削高锰钢时怎样选择切削用量?
高锰钢的切削加工性很差,为了维持一定的刀具耐用度,切削速度应低些。
采用硬合金刀具时, vc=20~40 m/min,其中,较低的速度用于粗车,较高的
速度用于半精车和精车。
采用陶瓷刀具时,可以选用较高的切削速度,一般
vc=50~80 m/min
高锰钢在切削过程中,由于塑性变形和切削力的影响,切削层及表层下一
定深度范围内会产生严重的硬化现象。
为了使刀尖避开毛坯表层和前一次走刀
造成的硬化层,应选择较大的切削深度和进给量。
一般粗车时αp =3~6 mm,
f=0.3~0.8 mm/r;大件粗车时可取αp =6~10 mm;半精车时αp =1~3 mm;
f=0.2~0.4 mm/r;精车时口。
≤1 mm;f≤0.2mm/r。
4.钻高锰钢硬质合金群钻有哪些特点?
在工程机械、矿山机械和越野车辆的制造中,常采用zgmn13类高锰钢。
zgmn13高锰钢锰含量达11%~14%,这类钢经过水韧处理后在受到剧烈冲击压力时,会产生很强的硬化现象,硬度可达hb450~550,硬化层深度达0.3 mm
左右。
高锰钢在受到冲击压力发生变形的过程中,会消耗那些对钢材表面继续
作用的冲击力,阻止作用力传到更深的内层去。
加之高锰钢的导热系数很低,
只有碳钢的1/3~1/4,给切削带来很大困难。
特别是钻削时,刀具磨损严重,
耐用度较低。
因此,常采用硬质合金群钻进行高锰钢的钻削。
钻高锰钢硬质合金群钻的本体为40cr制造,切削部分为yg8或yw硬质合金。
切削部分形状与铸铁群钻近似,只是将钻尖高h加大到0.08 d,圆弧刃的
圆弧半径加大到0.4 d,以加大b点刃尖的刀尖角,提高刀尖强度,改善散热
条件,同时也起到分屑作用。
同样,在外缘处磨出双重锋角,并磨出负前角,
把外缘处后角加大到20°,如图1所示。
钻头磨好后,要用油石仔细鐾研刃口,不得有锯齿。