二次成型熔体注射温度对模内组装成型流固耦合变形的影响
熔体注射温度对聚合物水辅共注成型过程的影响
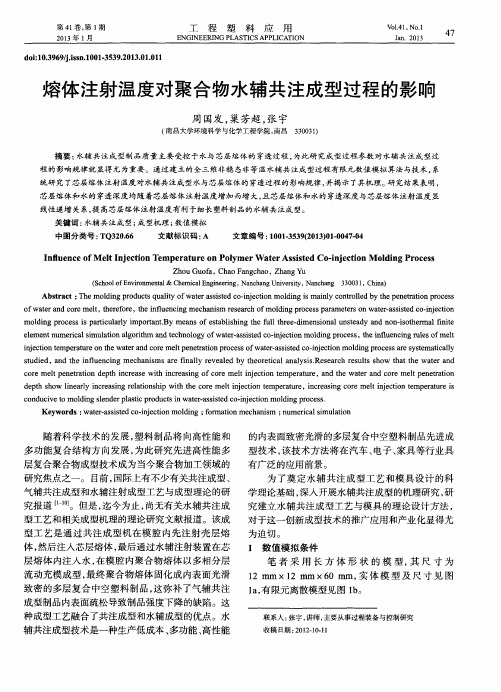
I n l f u e n c e o f Me l t I n j e c t i o n T e mp e r a t u r e o n P o l y me r Wa t e r A s s i s t e d Co — i n j e c t i o n Mo l d i n g P r o c e s s
芯层熔体和水 的穿透深度均随着芯层 熔体 注射 温度增加 而增 大, 且芯层熔体和水 的穿透深度与芯层熔体 注射 温度显
线性递增 关系, 提 高芯层熔体注射温度有利 于细长塑料 制品的水辅共注成型。
关键词 : 水辅共注成型 ; 成型机理 ; 数值模拟 中图分类号 : T Q3 2 0 . 6 6 文献 标 识 码 : A 文章 编 号 : 1 03 ) 0 1 — 0 0 4 7 . 0 4
Ab s t r a c t : T h e mo l d i n g p r o d u c t s q u a l i t y o f wa t e r a s s i s t e d C O — i n j e c t i o n mo l d i n g i s ma i n l y c o n t r o l l e d b y t h e p e n e r t a t i o n p r o c e s s o f w a t e r a n d c o r e me l t , t h e r e f o r e , t h e i n l f u e n c i n g me c h ni a s m r e s e a r c h o f mo l d i n g p r o c e s s p a r a me t e r s o n wa t e r - a s s i s t e d C O — i n j e c t i o n
熔体注射温度对聚合物气辅共注成型过程影响的试验研究

s de.Ter uto sac hwd i nr s go eietnt prtr o r m l,h oem ladgs t i h e l r er so e ,wt i e i t jco e eauefc e e tecr e n a u d s sf e h h ca n f h n i m o t t
( 南昌大学 环境科 学与工程 学院,江西 南昌 30 3 ) 30 1
摘 要: 文章对先进 的气 辅共注成型工艺进行 了实验研 究 , 系统研究 了熔体注射温度对气辅共注成型过 程的气体和芯 层
熔体穿透形貌 的影响规律。研 究结果表 明, 随着芯层熔体注射 温度升 高, 芯层熔体 和气体 的穿透 深度 减 小 , 而穿透 宽度
0 引 言
气辅共注 成形技 术 是气 辅 注 射成 型技 术 和共 注成 形技术相结 合 的一种 新型成 型技术 , 其成 型工艺是 通过 共注成型机 在模腔 内先 注射壳层 熔体 , 然后 注入 芯层 熔 体, 最后通过 气 辅 注射 装 置 在 芯 层 熔 体 内注 人 高压 氮
等气辅注射成型的优点 , 又具有能成型满足工程对制品 多功能、 高性能要求的低成本多层复合塑料制品的共注
和 穿透厚度 则增 大 , 易形成短射 。而随着壳层熔体注射 温度升 高, 气体和芯层熔体的 穿透深度增大 , 穿透厚度也 增大 , 但
穿透 宽度减 小。提 高壳层熔体注射 温度有利 于成 型 出材料 分布均 匀的 多层复合 中空塑料制品 。
关 键 词: 气辅共注成 型; 过程参数 ; 实验研 究
成型 的特点 ¨ 驯。该 成型工艺属 于三 维 、 瞬态 、 等温 多 非 相 分层流动成 型过 程 , 多相分层 流动存 在着 各分层 由于
注射工艺对不同熔体流动速率共聚聚丙烯力学性能的影响

加工设备与应用CHINA SYNTHETIC RESIN AND PLASTICS合 成 树 脂 及 塑 料 , 2019, 36(2): 67高流动共聚聚丙烯(PP)通常指熔体流动速率(MFR)大于20 g/10 min的产品,具有流动性好、橡胶相含量高、刚韧平衡性好的特点,被广泛应用于汽车、家用电器、日常用具等领域[1-3]。
由于树脂的流动性提高,可以满足高速注射的要求,有利于缩短成型周期,降低能耗,因此适于制作大型薄壁制品,可单独使用,也可作为高档改性基础树脂与其他材料配合使用。
目前,MFR在25~40 g/10 min的高流动抗冲共聚PP在国外已经十分普遍,并开始出现MFR达80g/10min以上的超高流动PP,以满足市场对这类PP的更高要求[4-7]。
高流动共聚PP是一种多组分材料,通常由基体相和分散相构成,基体相一般是等规PP的均聚物或共聚物,分散相一般是乙烯和α-烯烃中两种或者多种的共聚物[8]。
由于其结构具有特殊的多样性和复杂性,加工时,热历史和剪切历史均会影响材料内部分子链的排列和堆砌方式。
因此,在材料注塑成型过程中,每个因素都会对其成型尺寸和质量产生重要影响,最终决定高分子材料的使用性能。
如何在材料注塑成型时优化注射工艺注射工艺对不同熔体流动速率共聚聚丙烯力学性能的影响白弈青,吕 芸,侴白舸,陈若石,徐毅辉,张师军*(中国石油化工股份有限公司北京化工研究院,北京市 100013)摘要:在聚丙烯(PP)M20V中添加不同用量的过氧化物,并研究了注射工艺参数对不同熔体流动速率共聚PP力学性能的影响。
结果表明:熔体温度、注射速度和保压时间都会影响最终制品的性能。
其中,熔体温度对PP的性能影响很大,降低熔体温度,材料的冲击强度大幅提高,拉伸强度增大;提高注射速度,试样的弯曲强度和模量增大;延长保压时间会严重影响产品抗冲击性能。
关键词:共聚聚丙烯 注射工艺 力学性能 抗冲击性能中图分类号:TQ 325.1+4文献标志码:B文章编号:1002-1396(2019)02-0067-05 Effect of injection process on mechanical properties of copolymerizedpolypropylene with different melt flow ratesBai Yiqing,Lv Yun,Chou Baige,Chen Ruoshi,Xu Yihui,Zhang Shijun(Beijing Research Institute of Chemical Industry,SINOPEC,Beijing 100013,China)Abstract:Peroxide was added to polypropylene(PP) M20V in different amount to observe the effects of injection parameters on mechanical properties of copolymerized PP at different melt flow rates. The results show that the melt temperature,injection speed and holding time affect the properties of PP. The impact strength and tensile strength of the material are improved by reducing the melt temperature. The bending strength and modulus of the material are enhanced by accelerating the injection. The impact resistance of products can be affected by longer holding time.Keywords:copolymerized polypropylene; injection process; mechanical property; impact resistance收稿日期:2018-10-25;修回日期:2018-12-29。
注塑机作业中的熔体粘度对注射成型的影响

注塑机作业中的熔体粘度对注射成型的影响在注塑机作业中,熔体粘度是一个重要的参数,它直接影响到注射成型的质量和效率。
本文将讨论熔体粘度对注射成型的影响,并探讨如何在注塑机作业中合理调控熔体粘度,以获得理想的成型效果。
熔体粘度是熔融塑料流动的阻力大小的度量。
在注塑作业中,粘度过高或过低都会对成型产生不良影响。
首先,让我们先了解一下熔体粘度对注射成型的影响。
1. 熔体粘度对充填阶段的影响在注射成型中的充填阶段,熔体需要充满模具的腔体。
熔体粘度的大小会直接影响熔体的流动性能,进而影响充填的均匀性和速度。
如果熔体粘度过高,流动性能较差,可能会导致充填不完整,产生气泡、短充或缩松等缺陷;反之,如果熔体粘度过低,流动性能过强,可能会导致充填过度,产生过度充实等问题。
因此,在注塑机作业中,我们需要根据不同的塑料材料和产品要求,调节熔体粘度,以实现充填阶段的最佳效果。
2. 熔体粘度对保压阶段的影响在注射成型的保压阶段,熔体需要维持一定的压力,使其冷却固化成型。
熔体粘度的大小会直接影响保压的效果。
如果熔体粘度过高,可能会导致保压压力难以形成,产品表面质量较差;反之,如果熔体粘度过低,保压压力过大,可能会导致产品变形或破裂。
因此,在注塑机作业中,我们需要根据产品的形状和要求,以及塑料材料的特性,调节熔体粘度,以获得最佳的保压效果。
3. 如何调节熔体粘度了解了熔体粘度对注射成型的影响后,我们需要探讨如何在注塑机作业中合理调节熔体粘度。
以下是几种常见的方法:3.1 调整熔体温度熔体温度的高低直接影响到熔体粘度。
一般情况下,温度升高会使熔体粘度下降,流动性增强;反之,温度降低会使熔体粘度增加,流动性降低。
因此,在注塑机作业中,我们可以通过调节加热温度或冷却温度,控制熔体温度,以达到调节熔体粘度的目的。
3.2 改变原料配方不同的塑料材料具有不同的熔体粘度特性。
通过改变原料的配方,比如增加或减少一些添加剂的使用量,可以改变熔体粘度。
《工程塑料应用》杂志开设“技术转让与合作”、“企业风采”栏目
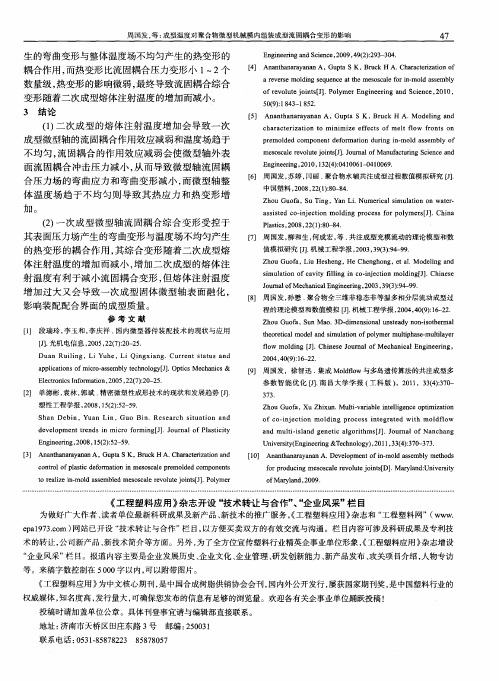
.
增 加 过 大 又 会 导 致 一 次 成 型 固 体 微 型 轴 表 面 融 化 ,
影响装配配合界面的成型质量 。
参 考 文 献
[ 1 ] 段瑞玲 , 李玉和 , 李庆祥 . 国内微型器件装配技 术的现状与应用
【 J ] ・ 光 机 电信 息 , 2 0 0 5 , 2 2 ( 7 ) : 2 0 - 2 5 ・
t h e o r e t i c a 1 m0 d e l a n d s i mu l a t i o n o f p o l y me r mu l t i p h a s e _ m u l t i l a y e r
周国发 , 等: 成型温度对聚合物微型机械模 内组装成型流 固耦合变形的影响
47
生的弯曲变形与整体温度场不均匀产生的热变形的 耦合作用, 而热变形 比流固耦合压力变形小 1 2 个 数量级 , 热变形的影响微弱 , 最终导致流固耦合综合
E n g i n e e r i n g a n d S c i e n c e , 2 0 0 9 , 4 9 ( 2 ) : 2 9 3 - 3 0 4 . [ ]A n a n t h a “ a r a y a n a n A , G u p a K , B r u c k H A ・ C h a r a c t e r i 甜 0 n 。 f 。 m o l d i n g ∞ B e 。 t h e m e s o s c a l e f o r m d a s s e m b l y
变 形 随 着 二 次 成 型 熔 体 注 射 温 度 的 增 加 而 减 小 。
3 结论
; :
P o 眦 吨 n g 盯 i n a n d 。 i e n ∞ 叭 。 ’
二次成型资料

2.注射吹塑
注射型坯包复在一根金属管上,管的一端 通入压缩空气,另一端的管壁上开有微孔。
(1)无拉伸注坯吹塑
成型过程:注射型坯→开启注射模→热型 坯移入吹塑模内→合模→吹入压缩空气→定型、 脱模 优点:壁厚均匀,不需后加工;制品无接 缝,废料少;对塑料品种的适应范围较宽。 缺点:需注塑和吹塑两套模具,故设备投 资较大;成型周期较长;型坯内应力较大,易 开裂,生产容器的形状和尺寸受限。
部分结晶聚合物的二次成型在接近熔点 Tm下进行,形变情况与无定形聚合物一样, 但冷却定型有本质的区别。分子链因结晶被 固定,不可能产生弹性回复。
三、成型条件的影响
1.成型温度
以聚合物能产生形变且伸长率最大的温度 为宜。一般无定形热塑性塑料的最宜成型温度 比其 Tg 略高。如硬聚氯乙烯 (Tg=83℃) 的最宜 成型温度为92~94℃。
第五节 冷成型
既不是一次成型也不是二次成型,是移植 金属的加工方法,使塑料在常温下固相成型。
优点:避免高温降解;取向提高性能;生 产周期短;成本低;可加工极大分子量的聚合 物;制品无熔接焊缝。
缺点:制品尺寸、形状、精密度差;引起 各向异性。
基本条件:完整坯料,形状近似成型制品; 成型温度可从室温到软化点; 在屈服点加压进行成型。 冷成型工艺:锻造、冲压成型、滚轧成型
工艺条件:
3.其它方法
二、热成型的影响因素
1.成型温度
保证较大的伸长率和足够的抗张强度,以 承受压力的作用。提高温度塑料的伸长率增大, 达某一温度时有一极大值,超过这一点伸长率 反而下降,抗张强度随温度升高而下降。 将片材加热到成型温度所需时间,约占整 个成型周朗的50%~80%。片材加热时间主要 决定于材料的品种和片材厚度,片材比热容和 导热系数。
共注塑制品芯层熔体的注射温度对制品质量的影响

共注塑制品芯层熔体的注射温度对制品质量的影响作者:卢松涛张灿辉来源:《中国科技博览》2014年第30期[摘要]在共注塑成型中,是否出现前沿突破现象和芯/壳层材料的分布情况是衡量制品质量的主要指标。
在成型过程中芯层熔体的注射速度是影响材料充填和最终分布的主要因素。
本文采用MPI软件Moldflow进行共注射模拟分析,研究不同的芯层熔体的注射温度对前沿突破现象和芯层材料的分布情况的影响。
[关键词]Moldflow 注射温度共注塑追赶距离中图分类号:F767.6 文献标识码:A 文章编号:1009-914X(2014)30-0161-02衡量共注塑制品质量的主要指标是前沿突破现象的出现与否和芯层材料厚度的分布及均匀性[1]。
所谓芯层熔体前沿冲破是指在充模过程中,芯层熔体前沿追上并超过壳层熔体前沿,致使芯层物料露出制品表面、造成废品的现象[2]。
一般认为共注射成型中前沿突破主要取决与芯层熔体前沿相对推进速度以及两前沿之间的距离[3]。
文中把芯层熔体前沿和壳层熔体前沿之间的距离定义为追赶距离,把对前沿突破的研究转换为对流动过程中的追赶距离演化趋势的研究[4]。
本文应用Moldflow plastics insight软件中的Co-injection分析模块,对的芯层熔体的注射温度进行模拟实验来研究芯层熔体的注射温度对追赶距离和芯层材料厚度的分布及均匀性的影响[5]。
一、MPI模拟1.1 几何模型本次分析中选择的模型是一个圆盘(图1),其底面直径为120mm,曲面高度为10mm,圆盘的边沿内径为130mm,外径为162mm,厚度均为2.5mm,曲面和底面所成的角度为120°,浇口设置在圆心处,为直浇口。
1.2 材料组合本次试验选用高密度聚乙烯(HDPE10062E)、低密度聚乙烯(LDPE 4012)分别作为芯层材料和壳层材料进行组合。
1.3 成型工艺参数设定壳层熔体注射温度为240℃、熔体注射速度为120cm3/s以及模具温度为50℃,壳层预填充量为60%,改变芯层熔体的注射温度(200℃,220℃,240℃),对芯壳层粘度比R不同的LDPE/LDPE, LDPE/HDPE, HDPE/LDPE三组组合进行模拟分析,研究芯层熔体注射温度的变化对追赶距离的影响。
塑料成型工艺参数对产品质量的影响实验心得

塑料成型工艺参数对产品质量的影响实验心得
1. 温度:温度是塑料成型的重要参数,对产品的物理性能、表面质量以及尺寸稳定性都有影响。
如果温度过高,可能导致材料熔化不均匀,产生气泡或烧焦的现象;如果温度过低,则可能导致成型件不完整或收缩不足。
因此,合适的温度范围对于保证产品质量非常重要。
2. 压力:压力是保证塑料充填和充实的重要参数。
适当的压力可以确保塑料在模具中充填均匀,并充实到预定的位置,避免产生缩孔和其他缺陷。
不同的成型工艺有不同的压力要求,需要进行适当的调整。
3. 时间:成型时间直接影响到产品形状的准确性和尺寸的稳定性。
过长或过短的时间都可能导致产品质量不稳定、尺寸变化或翘曲等问题。
因此,需要根据具体材料和产品要求来调整成型时间。
4. 冷却系统:冷却是保证产品质量的关键环节。
合理的冷却系统可以确保成型件在模具中完全固化和收缩,避免变形和内应力的产生。
因此,冷却时间和温度的控制非常重要。
总的来说,塑料成型工艺参数的调整对产品质量有重要影响。
合理调整温度、压力、时间和冷却系统,可以确保产品的物理性能、表面质量和尺寸稳定性。
在实际操作中,还需要结合具体的材料和产品要求,进行综合考虑和优化调整。
二次重熔工艺对触变成形Al—Pb合金力学性能的影响

[ 11 7 4 -
。
加热 时 间和加 热 温度 以获得 不 同的半 固态组 织 。之后 立 即将 其 注入 D K 5 — 4型 5 0 冷 室压 铸 机压 铸 成 A 40 5 0t 型 ( 品 如 图 1所 示 )压 射 速 度 为 5 /, 具 温 度 为 产 , m s模
706 ; 3 0 0 705 3 0 0)
摘 要 : 究 了二次 重熔 工 艺对 触 变成形 A — 0 b合 金 性 能 的影 响 , 研 12 %P 结果 表 明 : 半 固态 温度 6 5Cm热 不 同 在 1  ̄J 时间 时 , 热 10 i 加 5 m n时初 生相 球化 程 度 最 高 , 形合 金 的力 学 性能 最好 ; 不 同温度 加 热 10 i ,2  ̄ 成 在 5 r n时 6 0C时的 a
金 相 试 样 先 进 行 硬 度 测 试 后 经 粗 磨 、抛 光 、腐 蚀 在
Me3光 学 显微 镜 进 行 金 相 分 析 ,拉 伸试 验 在 WD f o W一 10 0 D万 能 材料 试 验机 上 进 行 ,拉 伸 速率 为 2 / n mm mi,
合金 的熔 炼 工 艺为 : 先 将 A 基 体 合金 ( 分 见 表 1 首 l 成 )
7
开发 研 究 D v lp n e e rh e eo me t s ac R
【) 甄子胜 , 4 毛卫民 , 陈洪涛 , . 等 电磁搅拌工艺参数对半 固态 A 9 D 镁 Z1
注射速度对塑封成型过程芯片热流固多场耦合变形的影响

中图分类号 : T Q 3 2 0 . 6 6 2 文献标 志码 : A
h I n u e n c e o f me l t i n j e c t i o n r a t e o n t h e r ma l - l f u i d — s t r u c t u r e
l f u i d — s t r u c t u r e c o u p l i n g w a r p a g e d e f o r ma t i o n f o r ma t t i n g p r o c e s s w a s e s t a b l i s h e d, a n d t h e f o m a r t i o n me c h a n i s m o f t h e m a r l l f u i d — s t uc r t u r e c o u p l i n g wa r p a g e d e f o m a r t i o n w a s r e v e le a d . R e s e a r c h r e s u l t s s h o w e d t h a t t h e c h i p he t m a r l l f u i d — s t uc r t u r e c o u p l i n g w a r p a g e i n c r e a s e d r a p i d l y a t i f r s t w i h t i n c r e a s i n g me l t i f l l i n g l f o w t i me , a f t e r r e a c h i n g he t
浇注温度对半固态Al2O3_2A14Al复合材料组织的影响毕业论文
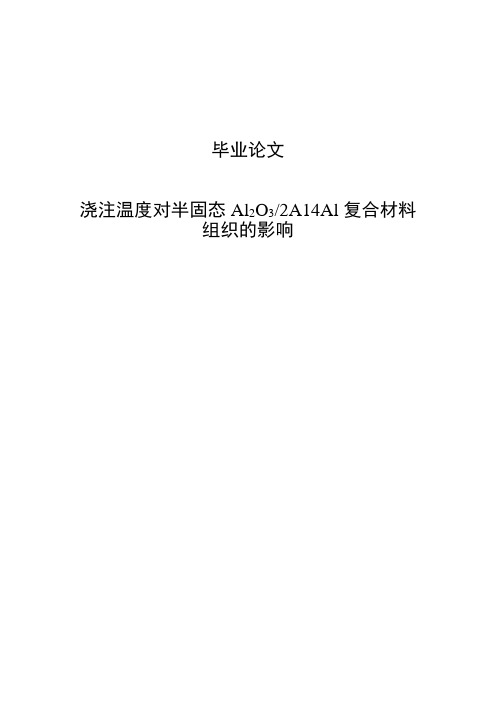
毕业论文浇注温度对半固态Al2O3/2A14Al复合材料组织的影响毕业设计(论文)原创性声明和使用授权说明原创性声明本人郑重承诺:所呈交的毕业设计(论文),是我个人在指导教师的指导下进行的研究工作及取得的成果。
尽我所知,除文中特别加以标注和致谢的地方外,不包含其他人或组织已经发表或公布过的研究成果,也不包含我为获得及其它教育机构的学位或学历而使用过的材料。
对本研究提供过帮助和做出过贡献的个人或集体,均已在文中作了明确的说明并表示了谢意。
作者签名:日期:指导教师签名:日期:使用授权说明本人完全了解XX大学关于收集、保存、使用毕业设计(论文)的规定,即:按照学校要求提交毕业设计(论文)的印刷本和电子版本;学校有权保存毕业设计(论文)的印刷本和电子版,并提供目录检索与阅览服务;学校可以采用影印、缩印、数字化或其它复制手段保存论文;在不以赢利为目的前提下,学校可以公布论文的部分或全部内容。
作者签名:日期:1文献综述1.1 引言20 世纪70 年代美国麻省理工学院的Flemings 教授等人开发出了一种崭新的金属成形方法, 称为半固态加工技术[1]。
在Flemings 的一篇论文中报道, 金属材料在凝固过程中加强烈的搅拌, 可以打碎金属凝固形成的枝晶网络结构, 形成近球状的组织, 得到一种液态金属母液中均匀悬浮着一定颗粒状固相组分的固- 液( 固相组分一般为50%) 混合浆料, 此时的半固态金属具有优良的流变性和触变性[2,3]。
因而, 易于用常规加工技术如压铸、挤压、模锻等实现成形。
采用这种既非液态又非完全固态的金属浆料加工成形的方法, 称为金属的半固态成形技术。
可见, 半固态加工是利用金属从液态向固态转变或从固态向液态转变( 即液固共存) 过程中所具有的特性进行成形的方法。
这一新的成形方法综合了凝固加工和塑性加工的长处, 即加工温度比液态低, 变形抗力比固态小, 可一次大变形量加工成形形状复杂且精度和性能质量要求较高的零件, 所以半固态加工技术被称为为21 世纪最有前途的材料成形加工方法。
注射成型中模具温度对材料流动性能的影响
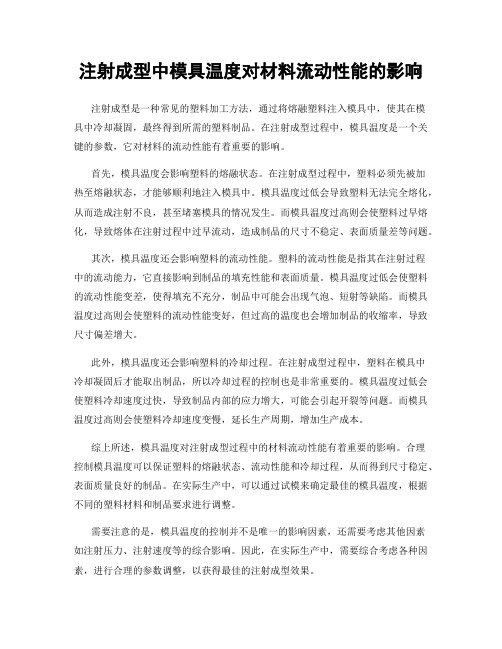
注射成型中模具温度对材料流动性能的影响注射成型是一种常见的塑料加工方法,通过将熔融塑料注入模具中,使其在模具中冷却凝固,最终得到所需的塑料制品。
在注射成型过程中,模具温度是一个关键的参数,它对材料的流动性能有着重要的影响。
首先,模具温度会影响塑料的熔融状态。
在注射成型过程中,塑料必须先被加热至熔融状态,才能够顺利地注入模具中。
模具温度过低会导致塑料无法完全熔化,从而造成注射不良,甚至堵塞模具的情况发生。
而模具温度过高则会使塑料过早熔化,导致熔体在注射过程中过早流动,造成制品的尺寸不稳定、表面质量差等问题。
其次,模具温度还会影响塑料的流动性能。
塑料的流动性能是指其在注射过程中的流动能力,它直接影响到制品的填充性能和表面质量。
模具温度过低会使塑料的流动性能变差,使得填充不充分,制品中可能会出现气泡、短射等缺陷。
而模具温度过高则会使塑料的流动性能变好,但过高的温度也会增加制品的收缩率,导致尺寸偏差增大。
此外,模具温度还会影响塑料的冷却过程。
在注射成型过程中,塑料在模具中冷却凝固后才能取出制品,所以冷却过程的控制也是非常重要的。
模具温度过低会使塑料冷却速度过快,导致制品内部的应力增大,可能会引起开裂等问题。
而模具温度过高则会使塑料冷却速度变慢,延长生产周期,增加生产成本。
综上所述,模具温度对注射成型过程中的材料流动性能有着重要的影响。
合理控制模具温度可以保证塑料的熔融状态、流动性能和冷却过程,从而得到尺寸稳定、表面质量良好的制品。
在实际生产中,可以通过试模来确定最佳的模具温度,根据不同的塑料材料和制品要求进行调整。
需要注意的是,模具温度的控制并不是唯一的影响因素,还需要考虑其他因素如注射压力、注射速度等的综合影响。
因此,在实际生产中,需要综合考虑各种因素,进行合理的参数调整,以获得最佳的注射成型效果。
总之,注射成型中模具温度对材料的流动性能有着重要的影响。
合理控制模具温度可以保证塑料的熔融状态、流动性能和冷却过程,从而得到高质量的制品。
第11节 注射成型工艺72问与答
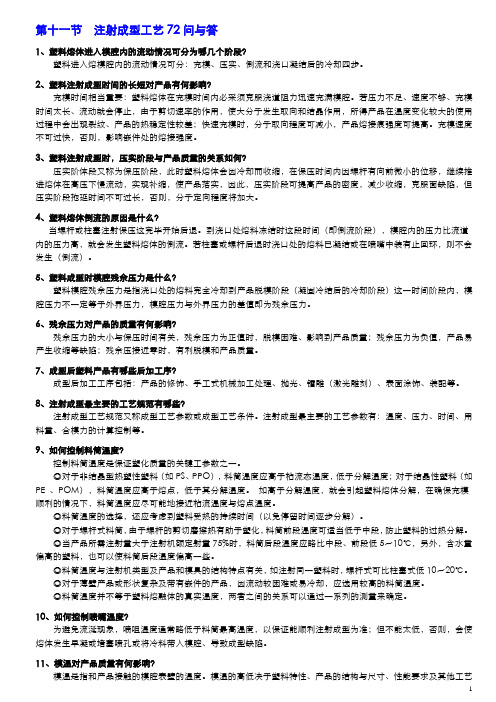
第十一节注射成型工艺72问与答1、塑料熔体进入模腔内的流动情况可分为哪几个阶段?塑料进入熔模腔内的流动情况可分:充模、压实、倒流和浇口凝结后的冷却四步。
2、塑料注射成型时间的长短对产品有何影响?充模时间相当重要:塑料熔体在充模时间内必采须克服浇道阻力迅速充满模腔。
若压力不足、速度不够、充模时间太长、流动就会停止,由于剪切速率的作用,使大分子发生取向和结晶作用,所得产品在温度变化较大的使用过程中会出现裂纹、产品的热稳定性较差;快速充模时,分子取向程度可减小,产品熔接痕强度可提高。
充模速度不可过快,否则,影响嵌件处的熔接强度。
3、塑料注射成型时,压实阶段与产品质量的关系如何?压实阶体段又称为保压阶段,此时塑料熔体会因冷却而收缩,在保压时间内因螺杆有向前微小的位移,继续推进熔体在高压下慢流动,实现补缩,使产品落实,因此,压实阶段可提高产品的密度,减少收缩,克服面缺陷,但压实阶段拖延时间不可过长,否则,分子定向程度将加大。
4、塑料熔体倒流的原因是什么?当螺杆或柱塞注射保压这完毕开始后退。
到浇口处熔料冻结时这段时间(即倒流阶段),模腔内的压力比流道内的压力高,就会发生塑料熔体的倒流。
若柱塞或螺杆后退时浇口处的熔料已凝结或在喷嘴中装有止回环,则不会发生(倒流)。
5、塑料成型时模腔残余压力是什么?塑料模腔残余压力是指浇口处的熔料完全冷却到产品脱模阶段(凝固冷结后的冷却阶段)这一时间阶段内,模腔压力不一定等于外界压力,模腔压力与外界压力的差值即为残余压力。
6、残余压力对产品的质量有何影响?残余压力的大小与保压时间有关,残余压力为正值时,脱模困难、影响到产品质量;残余压力为负值,产品易产生收缩等缺陷;残余压接近零时,有利脱模和产品质量。
7、成型后塑料产品有哪些后加工序?成型后加工工序包括:产品的修饰、手工式机械加工处理、抛光、镭雕(激光雕刻)、表面涂饰、装配等。
8、注射成型最主要的工艺规范有哪些?注射成型工艺规范又称成型工艺参数或成型工艺条件。
7塑料的二次成型

二、热成型的影响因素
(一)成型温度 1、对伸长率的影响
温度升高,延伸率有一峰值,热成型在最大延伸率温度 时加工成型
1-聚乙烯; 2-聚苯乙烯; 3-聚氯乙烯; 4-聚甲基丙烯酸甲酯; - - - -抗张强度 ——伸长率
2021/6/4
成型压力与抗张 强度要匹配
加热温度低,节省能源、缩短冷却时间 但制品外观轮廓不清晰
2、注射吹塑成型:飞边少、原材料损失少、口 部规整,尺寸精度高;但需两套模具,热量消耗大
2021/6/4
一、成型工艺
挤出-吹塑成型工艺原理示意图
2021/6/4
注射-吹塑成型工艺原理示意图
2021/6/4
注射-拉伸-吹塑成型工艺原理示意图
2021/6/4
二、工艺过程的影响因素
影响成型工艺和制品质量的因素主要有型坯的温 度、壁厚、空气压力、吹胀比、模温和冷却时间等 (一)型坯温度
一、薄膜取向的原理和方法 拉幅薄膜是大分子具有取向结构的一种材料。 单轴取向 双轴拉伸
薄膜的拉伸取向方法主要分为平膜法和管膜法两种 平膜法:单向拉伸和双向拉伸;双向拉伸又分为逐次拉伸 (先纵后横拉伸和先横后纵拉伸)和纵横同时拉伸 管膜法:双向同时拉伸(泡管法和平板式拉伸法)
2021/6/4
二、拉幅薄膜的成型工艺
2021/6/4
(三)成型压力
压力的作用是使片材产生形变,但材料有抵 抗形变的能力,其弹性模量随温度升高而降低
在成型温度下,只有当压力在材料中引起的 应力大于材料在该温度时的弹性模量时,才能使 材料产生形变
如果在某一温度下所施加的压力不足以使材 料产生足够的伸长时,只有提高压力或升高成型 温度才能顺利成型
(1)管坯经第一对夹辊折叠进入拉伸区 (2)从机头吹入压缩空气吹胀,坯体横向拉伸形成泡管 (3)泡管受到向下的牵引产生纵向拉伸达适当拉伸比 (4)拉伸后的泡管再经第二个夹辊折迭,进入热处理区 (5)继续保持压力,泡管在张紧下进行热处理定型 (6)冷却 2021/6/4 特点:设备简单,占地面积小
注射成型的工艺影响因素

注射成型的工艺影响因素
注射成型工艺的影响因素包括:
1. 注射成型材料的特性:包括熔融温度、熔融指数、流动性、收缩率、熔融粘度等。
不同材料的流动性和熔融粘度不同,会影响成型的质量和效率。
2. 注射成型机的参数:包括注射速度、注射压力、射嘴温度、模具温度等。
这些参数的设置会影响材料的流动性和充填情况,进而影响成型的缺陷和质量。
3. 模具设计和制造:模具的结构、尺寸、排气系统和冷却系统等都会影响成型的质量和效率。
优化的模具设计可以减少缺陷,提高生产效率。
4. 工艺参数:包括模具温度、预冷时间、保压时间等。
这些参数的设置会影响成型的收缩率、表面质量和尺寸精度。
5. 操作人员的技术水平:操作人员的熟练程度和经验对成型效果和生产效率有重要影响。
熟练的操作人员能更好地控制工艺参数,避免缺陷和问题的发生。
6. 环境因素:包括温度、湿度、气压等。
这些因素的变化会直接影响材料的流动性和收缩率,从而影响成型的质量。
综上所述,注射成型工艺的影响因素很多,需要综合考虑材料特性、机器参数、
模具设计、工艺参数、操作人员技术和环境因素,以获得高质量的成型产品。
第七章 塑料的二次成型1

1、什么是二次成型
塑料的二次成型
在一定条件下,将板、片、棒等塑料型材通过再次加工成型为制品的 方法。 2、二次成型与一次成型的区别 一次成型主要是通过塑料的流动或塑性形变实现造型,成型过程中总 伴随有聚合物的状态或相态转变,而二次成型过程始终是在低于聚合物 流动温度或熔融温度的固体状态下进行,一般是通过粘弹性形变来实现 塑料型材或胚件的再造型。 3、二次成型方法有哪些 主要有:中空吹塑成型、热成型、取向薄膜的拉伸等。
对于Tg比室温高得多的无定型或难于结晶的聚合物(PVC、PMMA), 二次成型通常按下述方法进行:
(1)将聚合物在Tg以上的温度加热,然后使之产生形变并成型为一定形 状; (2)形变完成后将其置于接近室温冷却,使形变冻结并固定其形状 (定型)。 对于结晶高聚物,形变过程在接近熔点的温度下进行,此时粘度大,成 型可按无定型高聚物的考虑,但其冷却定型的本质与无定型高聚物的不同。 结晶聚合物冷却定型过程中产生结晶,分子链本身因为结晶结构的一部分或 与结晶区域相联系而被固定,不能再产生卷曲恢复,而达到定型的目的。
成型温度不高采用慢速成型;
(三)成型压力 作用是使片材产生形变。压力必须大于材料在该温度下的弹性模量。 (四)材料的成型性
1、材料自身加工温度的波动范围
2、伸长率对温度的敏感情况
第四节 拉幅薄膜的成型
简介:
拉幅薄膜主要是通过提高薄膜的取向,来提高材料的强度、透明性
等性能。可以将挤出的原片(或管坯)与拉幅过程联系起来连续生产, 也可以分成两个对立的过程进行。 一、薄膜取向的原理和方法 在Tg-Tm(Tf)温度区间,聚合物长链受到外力作用拉伸时,沿力的方向 伸长取向。 拉幅薄膜的特点:(1)强度提高;(2)降低成本;(3)使用范围 扩大了。
- 1、下载文档前请自行甄别文档内容的完整性,平台不提供额外的编辑、内容补充、找答案等附加服务。
- 2、"仅部分预览"的文档,不可在线预览部分如存在完整性等问题,可反馈申请退款(可完整预览的文档不适用该条件!)。
- 3、如文档侵犯您的权益,请联系客服反馈,我们会尽快为您处理(人工客服工作时间:9:00-18:30)。
二次成型熔体注射温度对模内组装成型流固耦合变形的影响
聚合物质的模内组装成型的小规模设备的精确性关键是受到二次成型熔体充填流动与一次成型固体微型零件之间的流固耦合作用,文章具体的分析了相关的事项。
标签:模内组装成型;微型机械;流固耦合;数值模拟
1 关于模拟状态
文章将轴类小型机械为前提分析了成型气温对于流固耦合的意义。
轴类微型机械如图1所示,微型轴的半径为0.6mm,长度为8mm,而矩形块为2mm×4mm×8mm。
矩形块左右两侧中间为注射的进、出口。
设备的成型步骤如下。
先设置小型的轴,当其凝固之后,进而设置矩形块,确保两者能够在模内组装好。
确保装配的精确性优秀,是保证小规模的设备的运动性的关键点。
在熔体的前方和设备接触的时候,其流动会和设备的表层之间生成耦合效应,而且会它的表层生成流固耦合力,而且确保气温不一致,进而导致其发生变形。
先分析熔体的填充时期的流场,然后分析它的耦合意义。
进而将耦合活动的压力场以及总的气温场的信息放到相关的模型之中分析,论述它的变形现象。
为了分析变形的发生原理,就要对变形以等去耦。
为了得知纯压力场之中的变形,就要事先把小规模的轴当成是非等温的变形活动,而且将其热膨胀指数设置为零,这样的话就可以降低气温场不均匀而导致的变形干扰。
不分析其表层的压力场,只是分析它的不均衡性,可以分析它的热变形意义。
这个去耦探索措施为变形的生成机理创造了优秀的条件。
2 二次成型熔体注射温度对模内组装成型流固耦合变形的影响
2.1 关于模拟活动
二次成型熔体注射温度是影响聚合物微型机械模内组装成型装配界面成型精度与质量的关键工艺参数之一,其经由流动性来干扰成型时期的流场,所以对组装成型时期的耦合活动带来很多的影响,而且其气温太高的话会使得机械的表层被熔化,进而干扰到成型的品质,最终干扰到它的精确性。
所以,经由变革其注射气温,探索它对于耦合活动的干扰。
当进行成型活动的时候,如果填充熔体和设备的表层联系比较的紧密的话,会在其表层生成耦合效应,而且在它的表层生成一种力。
当其表层的耦合活动变强的时候,它的冲击力就相应的要高很多,此时就使得其变形更为厉害,所以就越容易干扰到成型的精确性。
为了探索气温对于作用的干扰规律,先是分析二次数成型熔体注射温度对于一次生成的设备的耦合压力场的干扰。
通过实验实验验证得知,小规模的设备的表层的耦合力的最高的压力差就随着气温的变高而降低。
二次成型熔体注射温度对一次成型微型轴沿其中心轴线温度场分布规律的影
响。
通过实验验证我们可知,由于注射气温变高,设备的高温区的气温变高,导致它的温度场不均匀。
降低气温能够确保温度场均匀。
2.2 流固耦合综合变形的模拟
流固耦合综合变形的有限元力学分析模型如图1所示。
通过ANSYS软件的SOLIDE186单元将微型轴进行有限元离散,将计算流体动力学模拟分析得到的流固耦合压力场P和温度场T导入微型轴有限元模型中。
将有限元模拟视为非等温过程,以考虑温度对微型轴用ABS弹性模量的影响,微型轴用ABS的力学性能参数见表1。
二次成型熔体注射温度对微型轴流固耦合综合变形的影响。
通过实验验证可知,其耦合的变形总数会伴随气温的变高而降低,增加注射气温,对于降低变形现象,提升制作的精确性来讲有着非常积极的意义。
不过,其气温变高,又容易使得一次成型的表层融化,干扰到最终的成型品质。
所以,要积极的优化注射气温。
将表1中ABS的热膨胀系数设定为零,并将CFD模拟得到的流固耦合压力场P和温度场T导入ANSYS有限元模型中,就能得知压力场导致的变形事项。
二次成型熔体注射温度对微型轴纯压力场弯曲变形的影响经验证得知,该变形会由于注射气温的变高而降低。
二次成型熔体注射温度对微型轴流固耦合热变形的影响经验证得知,其纯热变形会伴随注射气温的变高而变高。
通过分析得知,一次成型微型轴的热变形比压力变形小1~2个数量级。
进而我们可知,其变形关键是由耦合相关的压力弯曲变形来掌控的。
2.3 模拟结果实验验证
图2为二次成型熔体充填流动对一次成型微型轴流固耦合作用综合变形的影响。
二次成型熔体充填流动与一次成型微型轴流固耦合压力场和综合变形的模拟结果如图3所示。
2.4 关于形成的机理
通过分析我们得知,在熔体的填充成型时期,其流动性和表层的耦合意义会伴随着注射气温的变高而降低。
通过分析流动变知识可知,导致这种变动性的关键缘由是在别的数值特定的背景之下,由于其注射气温的变高,导致它的流动不具有黏度,进而杀跌流动的阻力变弱了,此时就使得充填流动力变低,导致表层的压力变弱,进而使得弯曲力以及相关的变形降低。
除此之外,气温的变高会使得高温区的气温增加,导致它的温度场不均匀,进而使得热应力等增加,使得变形严重。
因为耦合变形会受到设备的表层压力场的变动而导致的变形等的干扰,
热变形比流固耦合压力变形小1~2个数量级,因为热变形导致的作用力不大,会使得耦合变形伴随气温的升高而降低。
3 结束语
3.1 通过分析我们得知,二次生成的熔体的气温的变高会导致一次设备的耦合性变低,使得气温场不均匀,耦合力的降低会导致压力变小,进而使得设备的弯曲变形力变低。
对于小轴来讲,它的气温场如果不均匀的话,就会使得热应力以及变形等变高。
3.2 一次成型微型轴流固耦合综合变形受控于其表面压力场产生的弯曲变形与温度场不均匀产生的热变形的耦合作用,它的变形会伴随注射气温的变高而降低。
提升其注射气温能够降低耦合变形力,不过气温的增加会使得一次设备表层被融化,进而干扰到最终的成型品质。
参考文献
[1]段瑞玲,李玉和,李庆祥.国内微型器件装配技术的现状与应用[J].光机电信息,2005,22(7):20-25.
[2]单德彬,袁林,郭斌.精密微塑性成形技术的现状和发展趋势[J].塑性工程学报,2008,15(2):52-59.
[3]周国发,苏婷,闫丽.聚合物水辅共注成型过程数值模拟研究[J].中国塑料,2008,22(1):80-84.。