双金属复合管塑形成型过程
双金属复合管制作工艺
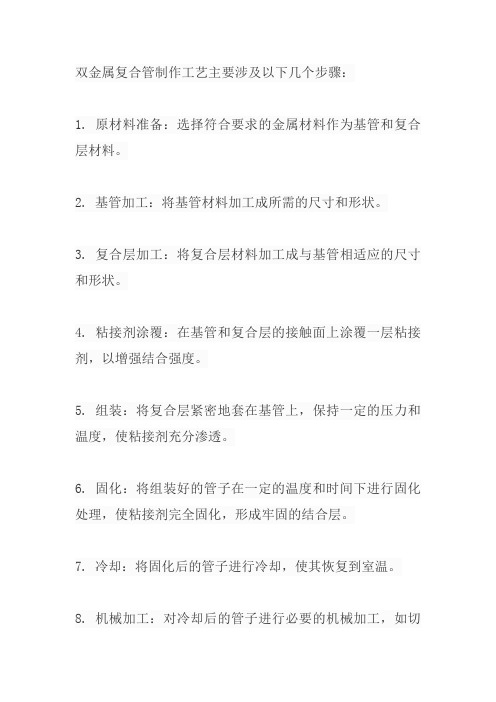
双金属复合管制作工艺主要涉及以下几个步骤:
1. 原材料准备:选择符合要求的金属材料作为基管和复合层材料。
2. 基管加工:将基管材料加工成所需的尺寸和形状。
3. 复合层加工:将复合层材料加工成与基管相适应的尺寸和形状。
4. 粘接剂涂覆:在基管和复合层的接触面上涂覆一层粘接剂,以增强结合强度。
5. 组装:将复合层紧密地套在基管上,保持一定的压力和温度,使粘接剂充分渗透。
6. 固化:将组装好的管子在一定的温度和时间下进行固化处理,使粘接剂完全固化,形成牢固的结合层。
7. 冷却:将固化后的管子进行冷却,使其恢复到室温。
8. 机械加工:对冷却后的管子进行必要的机械加工,如切
削、磨削等,以达到最终的尺寸和形状要求。
9. 检验:对成品管子进行外观、尺寸、结合强度等方面的检验,确保产品质量。
通过以上工艺流程,可以制得具有优良性能的双金属复合管,广泛应用于各种工程领域。
双金属复合管复合工艺
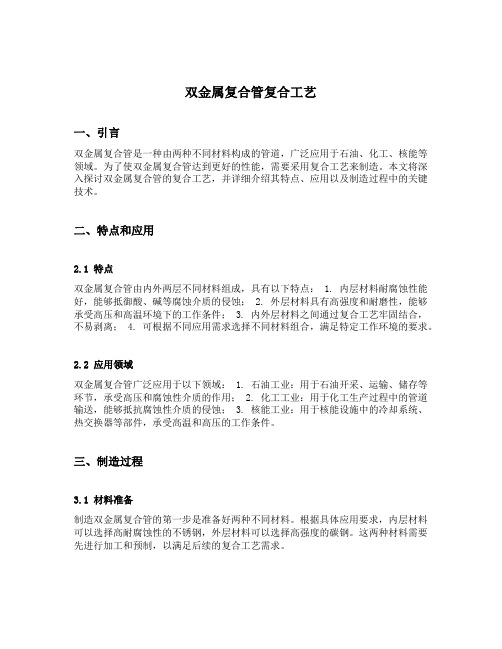
双金属复合管复合工艺一、引言双金属复合管是一种由两种不同材料构成的管道,广泛应用于石油、化工、核能等领域。
为了使双金属复合管达到更好的性能,需要采用复合工艺来制造。
本文将深入探讨双金属复合管的复合工艺,并详细介绍其特点、应用以及制造过程中的关键技术。
二、特点和应用2.1 特点双金属复合管由内外两层不同材料组成,具有以下特点: 1. 内层材料耐腐蚀性能好,能够抵御酸、碱等腐蚀介质的侵蚀; 2. 外层材料具有高强度和耐磨性,能够承受高压和高温环境下的工作条件; 3. 内外层材料之间通过复合工艺牢固结合,不易剥离; 4. 可根据不同应用需求选择不同材料组合,满足特定工作环境的要求。
2.2 应用领域双金属复合管广泛应用于以下领域: 1. 石油工业:用于石油开采、运输、储存等环节,承受高压和腐蚀性介质的作用; 2. 化工工业:用于化工生产过程中的管道输送,能够抵抗腐蚀性介质的侵蚀; 3. 核能工业:用于核能设施中的冷却系统、热交换器等部件,承受高温和高压的工作条件。
三、制造过程3.1 材料准备制造双金属复合管的第一步是准备好两种不同材料。
根据具体应用要求,内层材料可以选择高耐腐蚀性的不锈钢,外层材料可以选择高强度的碳钢。
这两种材料需要先进行加工和预制,以满足后续的复合工艺需求。
3.2 复合工艺双金属复合管的复合工艺一般包括以下几个步骤: 1. 清洁处理:将内外层材料进行表面清洁处理,以去除油污和氧化物等杂质,保证复合牢固性。
2. 巨型焊接:采用巨型焊接设备,将内层材料与外层材料进行焊接,形成初始复合管。
3. 冷拔工艺:将初始复合管进行冷拔加工,通过拉伸和压缩等力学变形,使复合管形成完整且均匀的形态。
4. 热轧工艺:对冷拔加工后的复合管进行热轧处理,以进一步提高其机械性能和表面质量。
5. 热处理:将热轧后的复合管进行热处理,消除内应力,提高材料的结构和性能。
3.3 表面处理和测试制造完成的双金属复合管需要进行表面处理,以防止腐蚀和氧化。
双金属复合管复合工艺
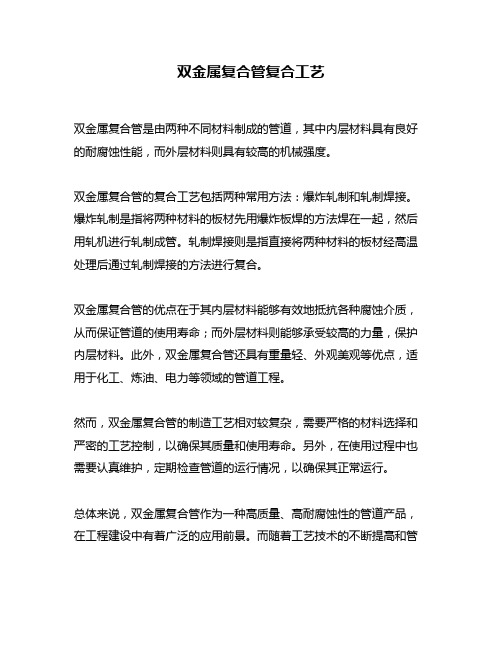
双金属复合管复合工艺
双金属复合管是由两种不同材料制成的管道,其中内层材料具有良好的耐腐蚀性能,而外层材料则具有较高的机械强度。
双金属复合管的复合工艺包括两种常用方法:爆炸轧制和轧制焊接。
爆炸轧制是指将两种材料的板材先用爆炸板焊的方法焊在一起,然后用轧机进行轧制成管。
轧制焊接则是指直接将两种材料的板材经高温处理后通过轧制焊接的方法进行复合。
双金属复合管的优点在于其内层材料能够有效地抵抗各种腐蚀介质,从而保证管道的使用寿命;而外层材料则能够承受较高的力量,保护内层材料。
此外,双金属复合管还具有重量轻、外观美观等优点,适用于化工、炼油、电力等领域的管道工程。
然而,双金属复合管的制造工艺相对较复杂,需要严格的材料选择和严密的工艺控制,以确保其质量和使用寿命。
另外,在使用过程中也需要认真维护,定期检查管道的运行情况,以确保其正常运行。
总体来说,双金属复合管作为一种高质量、高耐腐蚀性的管道产品,在工程建设中有着广泛的应用前景。
而随着工艺技术的不断提高和管
道材料的不断创新,双金属复合管的制造和应用也将得到更进一步的推广和应用。
双金属复合管技术
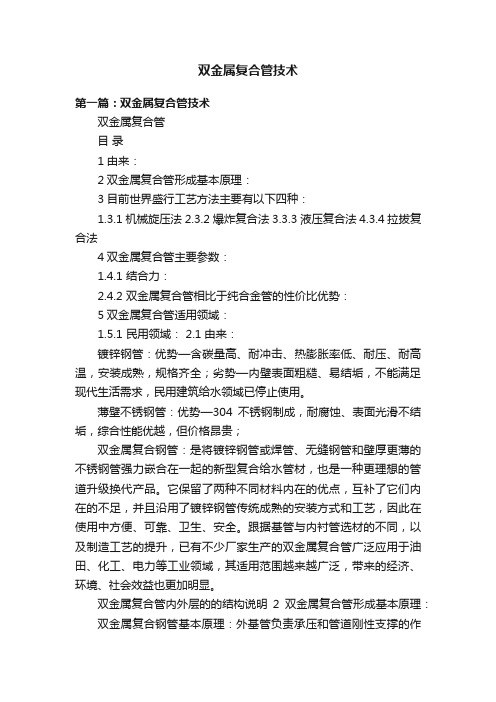
双金属复合管技术第一篇:双金属复合管技术双金属复合管目录1由来:2双金属复合管形成基本原理:3目前世界盛行工艺方法主要有以下四种:1.3.1 机械旋压法2.3.2 爆炸复合法 3.3.3 液压复合法4.3.4 拉拔复合法4双金属复合管主要参数:1.4.1 结合力:2.4.2 双金属复合管相比于纯合金管的性价比优势:5双金属复合管适用领域:1.5.1 民用领域:2.1由来:镀锌钢管:优势—含碳量高、耐冲击、热膨胀率低、耐压、耐高温,安装成熟,规格齐全;劣势—内壁表面粗糙、易结垢,不能满足现代生活需求,民用建筑给水领域已停止使用。
薄壁不锈钢管:优势—304不锈钢制成,耐腐蚀、表面光滑不结垢,综合性能优越,但价格昂贵;双金属复合钢管:是将镀锌钢管或焊管、无缝钢管和壁厚更薄的不锈钢管强力嵌合在一起的新型复合给水管材,也是一种更理想的管道升级换代产品。
它保留了两种不同材料内在的优点,互补了它们内在的不足,并且沿用了镀锌钢管传统成熟的安装方式和工艺,因此在使用中方便、可靠、卫生、安全。
跟据基管与内衬管选材的不同,以及制造工艺的提升,已有不少厂家生产的双金属复合管广泛应用于油田、化工、电力等工业领域,其适用范围越来越广泛,带来的经济、环境、社会效益也更加明显。
双金属复合管内外层的的结构说明2双金属复合管形成基本原理:双金属复合钢管基本原理:外基管负责承压和管道刚性支撑的作用,内衬管承担耐腐蚀的作用。
外基管可以根据输送介质的流量和压力要求,选用不同通径和壁厚的碳钢管材。
热镀锌钢管、直缝焊管、螺旋管、低中压流体输送用无缝钢管、高压锅炉、石油裂化用无缝管钢管、管线管等。
直径可从φ20-φ1020mm,壁厚可从2.5-50mm。
内衬管可以根据输送介质化学成分,选用不同的耐腐蚀合金。
可以是奥氏体不锈钢304、304L、316、316L、铜基合金、镍基合金、哈氏合金、钛、钛合金、双相不锈钢等新型高耐腐蚀合金材料。
内衬管壁厚可以根据使用寿命和焊接工艺的要求从0.3-4mm。
双金属复合管的弹塑性分析及有限元模拟

目前 加工 复合 管有 双 金属挤 压 、 爆炸 熔焊 、 离 心铸 造 以及 液 压 成 形 等 方 法 。液 压 成 形 法 胀 合力 均 匀且 容易 确 定 , 双 金 属 复 合 管 成 形 的 主 是 流方 法 。在 复合 管 的液 压 成 形 过 程 中 , 压力 的 胀 计算 与 控制是 关 键 。王 学生 等 在 对 液压 胀
一
O
与残余 接触 压力 P 之 间的关 系 :
一
●
2
2
p/ = 。 A+[ 1一 / i 。 B p / ( i E ]+1B × n d/ 。 i ) / I( od) 。
×
D d
+
2 )
+
2 )
继 续 加压 , 当外 管 的 内壁 开始 屈服 时 , 外管 内
内层 管 的应 变强 化应 力 ; 内层 管 的线性 强 化模 量 。
—
—
.
由于后续 的胀 合 过 程 中产 生 的变 形 较 小 , 因 此可 认 为 O i 以后 的复 合 过 程 中 不 发 生 变 化 , r 在
此 时 所 需 要 的 内压 力 为 :
P : 。 1( 。 8 / d + 6 ] . n d +2 ) ( i 2 ) [ () 5
管 的应 力状态 , 定 了复合 管体 的承 载能力 ; 确 上述 研 究者 均将 内管 假 设 为 理想 弹塑 性 材 料 , 实 际 但
上 内管 在成形 过 程 中已进 入 强 化 阶 段 , 此 笔者 因 在 上述 研究 的基 础上对 内管采用 线性 强化 模型进 行 了双 金属 复合 管分 析 。
当双 金属 复 合 管 内压 力 卸 载 后 , 了保 证 其 为
双金属复合管制作标准

双金属复合管制作标准
双金属复合管制作标准主要包括以下步骤:
1. 打胶:在打胶前将A、B两种胶水按1:1的比例混合搅拌均匀。
打胶时
涂抹要到位,涂抹部位要压过碳钢边缘2~3mm,涂层要均匀、饱满,涂
层厚度在1~2mm为宜。
2. 管道支架安装:内衬不锈钢复合管支架的制作安装与普通钢管支架的制作安装工艺要求相同,可参见普通钢管支架的制作安装工艺。
3. 管道试压:灌水必须在管道安装完成24小时后开始。
试压的其它工艺和要求可按照镀锌钢管或无缝钢管的相应要求。
漏点检修时拆下的管道,必须将原打胶部位的残留密封胶和水渍清理干净,重新打胶后再安装。
安装完成后必须待新胶固化后再进行二次试压。
4. 保温与防腐:内衬不锈钢复合管的保温和外部防腐无特殊要求,可按照普通钢管保温防腐的工艺施工。
请注意,双金属复合管制作标准可能因实际应用场景和具体需求而有所不同,因此建议在制作过程中遵循相关行业标准和规范,并请咨询专业人士以获取更准确的信息。
X60/2205双金属复合管短流程制备工艺研究
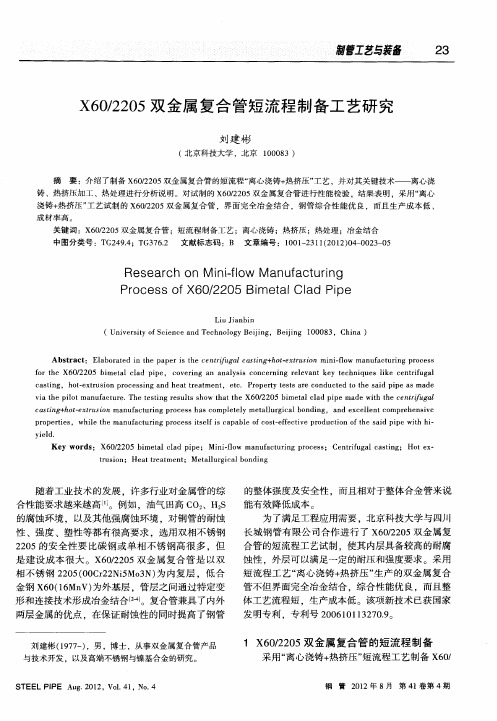
一~一 ~一 宣 _~ 一一 k. ~ 一 耐 一 ~ d 一
.
(U iest o ce c n eh oo yB i n ,B in 10 8 ,C ia) nv ri f in ea dT c n lg e ig ej g 0 0 3 hn y S j i
甜 ㈨ . 善
一一 一一 ~ 一一 ~ 一 ~
随着工 业技 术 的发 展 .许 多 行业对 金 属管 的综
的整体 强度 及安 全性 ,而且 相对 于整 体合 金管 来说 能 有效 降低 成本 。
合性 能要 求越 来越 高 L。例如 ,油气 田高 C : S 1 j O 、H:
的腐蚀环境 ,以及其他强腐蚀环境 , 对钢管的耐蚀 性 、强度、塑性等都有很高要求 ,选用双相不锈钢 20 2 5的 安 全性 要 比碳 钢 或 单 相 不 锈 钢 高很 多 ,但 是 建设 成 本 很 大 。X6/2 5双金 属 复合 管 是 以双 02 0 相 不 锈 钢 2 0 (O r2 iMo N) 内复 层 .低 合 25OC2N5 3 为
Re e ch O i i l w a u a t rn s ar n M n — o M n f C u i g f
P o e s o 6 / 2 5 Bi t l a i e r c s f 0 2 0 me a d P p X Cl
L uJa i i i nb n
发出一组新 钢号 .通过采 用新 的淬火方式 ,严格控制生产过程 ,成功生产出性 能优 良的海上平台用管。 ( 阳华菱钢 管有限公司 许 莹) 衡
刘建彬 :X6 /2 5双金属复合管短流程制备工艺研究 02 0
钢 管 21 0 2年 8月 第 4 卷 第 4期 1
蚀性 ,外 层 可 以满 足一定 的耐压 和强度 要求 。采 用 短 流程 工艺 “ 离心 浇铸 + 挤压 ” 热 生产 的双金 属 复 合 管不但 界 面完 全冶 金结合 ,综 合性 能优 良 ,而且 整
双金属复合管塑性成形技术的应用及发展

第4 3卷
陈海云等 .双金属 复合 管塑性成形技术的应 用及发展
・1 7・
零, 这时 内管与外 管均处 于卸载状态 。由于第二 阶
段 中产 生 了塑性 变形 , 当加 载 压力 完 全消 除后 , 内外
结合 。
由于机 械拉 拔法 的模 具 表 面与 管材 的 表面 全接 触, 在拉 拔过 程 中摩 擦 阻力 大 , 因此 与滚 压法 相 比需
中图分类号 :Q 5 . ห้องสมุดไป่ตู้ o58
文献标识码 :A
文章 编号 : 093 8 ( 0 6 0 - 1-4 10 -2 12 0 ) 50 60 0
Ap l a i n a d De eo m e to l si o mi g p i to n v l p n fP a tc F r n c Te h i u o u l e a mb n d P p c n q e f rDo b e M t lCo ie ie
Ch n Ha y n Ca h x e iu o Z ii
( h in n uta nvrt H nzo 3 03 ) Z ea gIds il i sy a gh u 10 2 j r U e i
Absr c I h sat l,tepo esa d teme h ns o lsi omigo o bemea o ie ieweea aye .S v rlman patcfr ig t a t nti ri e h rc s n h c a im fpat fr n fd u l tlc mbn dpp r n zd e ea i lsi o n c c l m
维普资讯
第4 3卷第 5期
20 06年 1 0月
双金属复合管塑性成型有限元模拟

[ 1] 史文光. 小井眼钻采技 术整套 油井 设计方 法[ M ] . 北京: 石油工业出版社, 1992.
( 收稿日期 2008 05 23 编辑 钟水清)
[ 3] 王廷瑞. 微 台 阶 扩眼 技 术 在 玄武 岩 地 层 钻井 中 的 应 用 [ J] . 天然气工业, 2007, 27( 11) : 52 54.
[ 4] 聂荣国. 偏轴钻 具组合 防斜打 快的强 度分析 [ J] . 西南 石 油大学学报, 2007, 29( 1) : 82 84.
钻井工程
天然气工业
2008 年 9 月
双金属复合管塑性成型有限元模拟*
杜清松1 曾德智2, 3 杨 斌2 张 智2 黄黎明3
( 1. 中国石化西北油田分公司工程监督中心 2. 西南石油大学 3. 中国石油西南油气田公司天然气研究 院)
杜清松等. 双金属复合管塑性成型有限元模 拟. 天然气工业, 2008, 28( 9) : 64 66. 摘 要 随着高含二氧化碳、硫化氢及元素硫 等油气 田的相 继出现, 油管、套管 的腐蚀 问题越 来越突 出, 并 直 接影 响到油气田的经济开发和安全开采。针对机械复合管塑性成型过程中的力学 问题进行了 有限元模 拟研究, 建 立了 模拟双金属复合管塑性成型的参数化有限元力学模型。通过有限元模拟研究, 得出了 双金属复 合管所需的 最 小成型压力和成型后内外管间的结合力, 分析了 双金属复合 管在塑 性成型过 程中内 外管的 接触压 力、径 向应力 应 变等力学特性。计算实例表明, 该模型的几何尺寸、材料模型以及加载压力等参数 均可以根据 计算需要 设定, 可 用 于模拟不同材质和不同尺寸的双金属管在塑性成型过程中的力学特性研究。 主题词 完井 硫化氢 油管腐蚀 双金属复合管 模型
双金属不锈钢复合管的生产工艺汇总
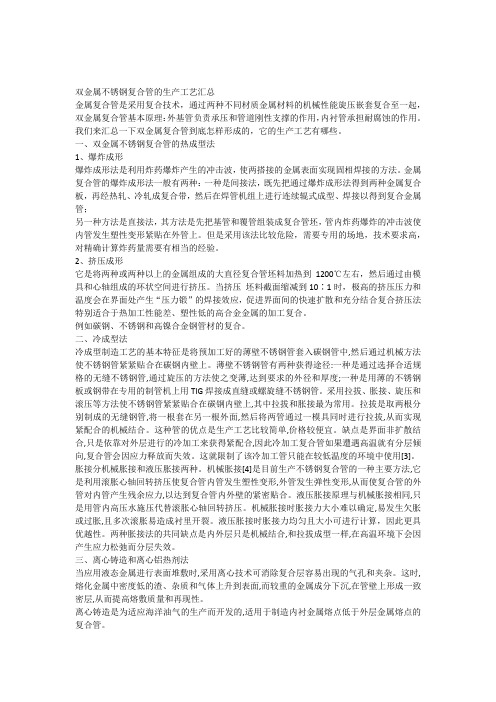
双金属不锈钢复合管的生产工艺汇总金属复合管是采用复合技术,通过两种不同材质金属材料的机械性能旋压嵌套复合至一起,双金属复合管基本原理:外基管负责承压和管道刚性支撑的作用,内衬管承担耐腐蚀的作用。
我们来汇总一下双金属复合管到底怎样形成的,它的生产工艺有哪些。
一、双金属不锈钢复合管的热成型法1、爆炸成形爆炸成形法是利用炸药爆炸产生的冲击波,使两搭接的金属表面实现固相焊接的方法。
金属复合管的爆炸成形法一般有两种:一种是间接法,既先把通过爆炸成形法得到两种金属复合板,再经热轧、冷轧成复合带,然后在焊管机组上进行连续辊式成型、焊接以得到复合金属管;另一种方法是直接法,其方法是先把基管和覆管组装成复合管坯,管内炸药爆炸的冲击波使内管发生塑性变形紧贴在外管上。
但是采用该法比较危险,需要专用的场地,技术要求高,对精确计算炸药量需要有相当的经验。
2、挤压成形它是将两种或两种以上的金属组成的大直径复合管坯料加热到1200℃左右,然后通过由模具和心轴组成的环状空间进行挤压。
当挤压坯料截面缩减到10∶1时,极高的挤压压力和温度会在界面处产生“压力锻”的焊接效应,促进界面间的快速扩散和充分结合复合挤压法特别适合于热加工性能差、塑性低的高合金金属的加工复合。
例如碳钢、不锈钢和高镍合金钢管材的复合。
二、冷成型法冷成型制造工艺的基本特征是将预加工好的薄壁不锈钢管套入碳钢管中,然后通过机械方法使不锈钢管紧紧贴合在碳钢内壁上。
薄壁不锈钢管有两种获得途径:一种是通过选择合适规格的无缝不锈钢管,通过旋压的方法使之变薄,达到要求的外径和厚度;一种是用薄的不锈钢板或钢带在专用的制管机上用TIG焊接成直缝或螺旋缝不锈钢管。
采用拉拔、胀接、旋压和滚压等方法使不锈钢管紧紧贴合在碳钢内壁上,其中拉拔和胀接最为常用。
拉拔是取两根分别制成的无缝钢管,将一根套在另一根外面,然后将两管通过一模具同时进行拉拔,从而实现紧配合的机械结合。
这种管的优点是生产工艺比较简单,价格较便宜。
双金属复合管生产工艺
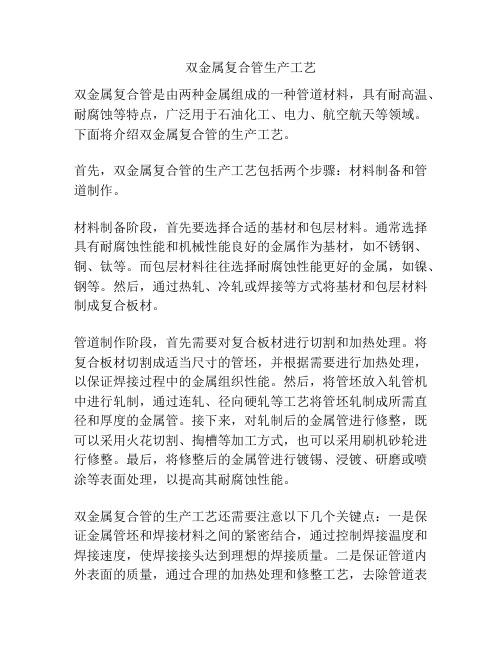
双金属复合管生产工艺双金属复合管是由两种金属组成的一种管道材料,具有耐高温、耐腐蚀等特点,广泛用于石油化工、电力、航空航天等领域。
下面将介绍双金属复合管的生产工艺。
首先,双金属复合管的生产工艺包括两个步骤:材料制备和管道制作。
材料制备阶段,首先要选择合适的基材和包层材料。
通常选择具有耐腐蚀性能和机械性能良好的金属作为基材,如不锈钢、铜、钛等。
而包层材料往往选择耐腐蚀性能更好的金属,如镍、钢等。
然后,通过热轧、冷轧或焊接等方式将基材和包层材料制成复合板材。
管道制作阶段,首先需要对复合板材进行切割和加热处理。
将复合板材切割成适当尺寸的管坯,并根据需要进行加热处理,以保证焊接过程中的金属组织性能。
然后,将管坯放入轧管机中进行轧制,通过连轧、径向硬轧等工艺将管坯轧制成所需直径和厚度的金属管。
接下来,对轧制后的金属管进行修整,既可以采用火花切割、掏槽等加工方式,也可以采用刷机砂轮进行修整。
最后,将修整后的金属管进行镀锡、浸镀、研磨或喷涂等表面处理,以提高其耐腐蚀性能。
双金属复合管的生产工艺还需要注意以下几个关键点:一是保证金属管坯和焊接材料之间的紧密结合,通过控制焊接温度和焊接速度,使焊接接头达到理想的焊接质量。
二是保证管道内外表面的质量,通过合理的加热处理和修整工艺,去除管道表面的缺陷和氧化物。
三是严格控制管道的直径和壁厚,通过精确的测量和调整,确保管道的几何尺寸满足设计要求。
总之,双金属复合管的生产工艺包括材料制备和管道制作两个步骤,需要合理选择材料、控制焊接质量和保证管道尺寸的准确性。
只有通过精细的工艺流程和严格的质量控制,才能生产出优质的双金属复合管产品。
双金属复合管塑性复合成形工艺及应用

密
成
形
工
程
J OURNAI OF NETSHAP FoRM I E NG ENGI ERI NE NG
第 3卷 第 3 期 21 0 1年 5月
双 金 属 复 合 管 塑 性 复 合 成 形 工 艺 及 应 用
谷 霞 ,张 安 义。 ,秦 建 平
(. 原 科 技 大 学 , 原 0 0 2 ; . 同 大 学 ,山西 大 同 0 8 0 ) 1太 太 304 2大 3 3 0
2 Sha xiDa o nie st . n t ng U v r iy,Da on 37 03,Chi ) t g0 0 na
Ab ta t n t s a tc e t e pr e sofp a tcf m i ou e m e a o b n d pi s a l z d. Se r lm an p a tc sr c :I hi ril , h oc s l si or ng ofd bl t lc m i e pe wa na y e ve a i l si
管 紧 贴 在 钢 内管 内表 面 。
2 )复 合 阶 段 ( 外 管 同 步 膨 胀 ) 随 着 加 载 压 内 。 力 持续增 加 , 始对 外管加 载 。外管 出现 弹性 扩张 , 开 直 到 外 管 内表 面 满 足 屈 服 条 件 后 , 管 才 出 现 部 分 外 塑 性 扩 张 。 随 着 加 载 压 力 不 断 加 大 , 管 中 塑 性 区 外 不 断扩展 , 到达到 最大 加载 压力 。 直
3 )卸 载 阶段 。 加 载 压 力 从 最 大 值 缓 慢 减 小 至
决 于 基 管 与 覆 管 之 间 弹 性 模 量 的 差 异 、 工 性 能 的 加 不 同以及覆 材是 在 内或在外 的不 同等 。 机械 拉拔法 的 模具 表 面 与 管材 的表 面 全接 触 ,
双金属不锈钢复合管的生产工艺

双金属不锈钢复合管的生产工艺1.材料准备:首先需要准备所需的不锈钢和碳钢材料。
这两种材料通常会根据所需的规格和要求进行切割和加工。
2.清洗与处理:切割好的材料表面可能存在杂质或氧化层,需要进行清洗和处理。
可以使用酸洗、碱洗或电解处理等方法,以保证材料表面的干净和光滑。
3.冷拔工艺:经过清洗和处理的材料进一步通过冷拔工艺进行加工。
冷拔工艺是指将材料通过模具进行多次拉伸变形,以达到提高材料的强度和硬度的目的。
4.冷拔的材料经过后继的加工工艺,例如冷压和冷拉等,以进一步提高其密度和硬度。
这些工艺的目的是为了减少管道的孔隙度和气孔率,提高其机械性能和腐蚀性能。
5.高压轧制:冷拔和冷压后的材料经过高温下的高压轧制。
高压轧制是指将材料通过辊式轧机进行多道次的轧制,以进一步加工和改善材料的形态和力学性能。
6.焊接:轧制后的材料需要进行焊接。
焊接一般使用氩弧焊、电阻焊或激光焊等方法,以确保管道的连接牢固和无缺陷。
焊接时需要注意控制焊接温度和时间,避免产生过多的热应力和变形。
7.磨削和清洁:焊接完成后的管道需要进行磨削和清洁处理。
磨削是指使用砂轮或砂纸等工具将焊接点和管道表面进行打磨,以保证其光滑和平整。
清洁则是指将管道表面的残留物和污垢清除干净,以便进行下一步的处理。
8.检测和质量控制:最后,经过生产工艺加工的双金属不锈钢复合管需要进行检测和质量控制。
常用的检测方法包括压力试验、磁粉探伤、尺寸检测等,以确保产品的质量和性能达到标准要求。
以上就是双金属不锈钢复合管的生产工艺的主要步骤和流程。
通过合理的材料选择和加工工艺控制,可以生产出具有良好耐腐蚀性能和高强度的管道产品,满足不同领域的使用需求。
双金属复合管的工作原理

双金属复合管的工作原理双金属复合管是一种结构特殊的管材,由两种不同金属材料通过爆炸焊接或轧制工艺制成。
它由内外两层金属组成,内层一般采用耐腐蚀性较好的材料,如不锈钢,而外层则选择耐压强度较高的材料,如碳钢。
在实际应用中,双金属复合管常用于石油、化工、航空航天等行业,主要用于输送耐高温、耐腐蚀、耐压力的介质。
双金属复合管的工作原理可概括为以下几点:1. 优势材料的应用:双金属复合管的内外层材料选择是根据介质的特性来决定的。
内层采用耐腐蚀性较好的材料,可以保护介质不受腐蚀。
而外层则选择耐压强度较高的材料,以承受介质的压力。
通过合理的材料选择,双金属复合管能够提供更好的性能。
2. 热胀冷缩的利用:双金属复合管的内外层材料由于热胀冷缩系数不同,在不同温度下会出现不同程度的热胀冷缩变形。
当双金属复合管在高温介质中工作时,内层材料会因温度升高而膨胀,外层材料由于热胀系数小会保持相对稳定。
而在低温条件下,内层材料因温度降低而收缩,外层材料维持较低的收缩程度。
利用不同的热胀冷缩特性,双金属复合管可以实现柔性连接,缓冲介质输送过程中的热膨胀或收缩带来的应力。
3. 软硬材料的结合:双金属复合管的外层材料通常选择硬质材料,能够提供足够的强度和刚度,以承受介质的压力。
而内层材料则选择柔性材料,能够吸收介质膨胀产生的应力,并为介质提供良好的流动性。
内外层材料的不同特性结合在一起,使得双金属复合管既能够承受压力,又能够适应介质的热膨胀。
4. 弹性变形的利用:当双金属复合管在应用中受到外力作用时,内外层材料会发生相应的弹性变形。
通常情况下,外层材料受到弯曲或拉伸应力,而内层材料则受到压缩应力。
通过合理设计材料厚度和截面形状,双金属复合管可以实现弯曲或伸长的结构变形,从而增加管材运行的安全性。
双金属复合管的工作原理基于热胀冷缩和材料的特性,能够应对介质的高温、高压和腐蚀等问题。
它在工业领域的应用广泛,如化工管道系统、石油管道输送系统、航空航天结构管道等,为各行各业的发展提供了重要的技术支持。
双金属不锈钢复合管的生产工艺汇总

双金属不锈钢复合管的生产工艺汇总金属复合管是采用复合技术,通过两种不同材质金属材料的机械性能旋压嵌套复合至一起,双金属复合管基本原理:外基管负责承压和管道刚性支撑的作用,内衬管承担耐腐蚀的作用。
我们来汇总一下双金属复合管到底怎样形成的,它的生产工艺有哪些。
一、双金属不锈钢复合管的热成型法1、爆炸成形爆炸成形法是利用炸药爆炸产生的冲击波,使两搭接的金属表面实现固相焊接的方法。
金属复合管的爆炸成形法一般有两种:一种是间接法,既先把通过爆炸成形法得到两种金属复合板,再经热轧、冷轧成复合带,然后在焊管机组上进行连续辊式成型、焊接以得到复合金属管;另一种方法是直接法,其方法是先把基管和覆管组装成复合管坯,管内炸药爆炸的冲击波使内管发生塑性变形紧贴在外管上。
但是采用该法比较危险,需要专用的场地,技术要求高,对精确计算炸药量需要有相当的经验。
2、挤压成形它是将两种或两种以上的金属组成的大直径复合管坯料加热到1200℃左右,然后通过由模具和心轴组成的环状空间进行挤压。
当挤压坯料截面缩减到10∶1时,极高的挤压压力和温度会在界面处产生“压力锻”的焊接效应,促进界面间的快速扩散和充分结合复合挤压法特别适合于热加工性能差、塑性低的高合金金属的加工复合。
例如碳钢、不锈钢和高镍合金钢管材的复合。
二、冷成型法冷成型制造工艺的基本特征是将预加工好的薄壁不锈钢管套入碳钢管中,然后通过机械方法使不锈钢管紧紧贴合在碳钢内壁上。
薄壁不锈钢管有两种获得途径:一种是通过选择合适规格的无缝不锈钢管,通过旋压的方法使之变薄,达到要求的外径和厚度;一种是用薄的不锈钢板或钢带在专用的制管机上用TIG焊接成直缝或螺旋缝不锈钢管。
采用拉拔、胀接、旋压和滚压等方法使不锈钢管紧紧贴合在碳钢内壁上,其中拉拔和胀接最为常用。
拉拔是取两根分别制成的无缝钢管,将一根套在另一根外面,然后将两管通过一模具同时进行拉拔,从而实现紧配合的机械结合。
这种管的优点是生产工艺比较简单,价格较便宜。
双金属复合管成型仿真分析

双金属复合管成型仿真分析针对石油工程中钻杆及管道材料的频繁失效问题,提出了使用双金属复合材料加工石油用管材的方法。
分析了双金属复合管的塑性成形法的几种加式方法;仿真分析了塑性成形法加式双金属复合管时材料的弹性模量及屈服强度对内外管残余应力的影响。
标签:双金属复合管;塑性成形法;弹性模量;屈服强度;残余应力1 绪论随着石油工业的飞速发展,对钻杆及管道材料性能的要求也逐渐提高,金属复合材料在这种需求下诞生。
金属复合材料是以一种性能的金属材料为基体,以另一种性能的金属材料为增强体成形而制得的复合材料所以它可以根据实际需要进行组合[1]。
在双金属复合管的成形方法及生产工艺上,分别有冶金复合、钎焊复合、爆炸复合、拉拔复合以及液压复合等多种成形方法,并且已经形成了许多专利技术[2]。
其中塑性成形法具有高产、优质、低耗等优点,己成为当今制造金属复合材料的主打技术[3],主要包括机械拉拔法、爆炸成形法、滚压法及液压胀形法等[4]。
2 塑性成形法双金属复合管塑性成形技术一般有两种,分别是机械胀接技术、柔性胀接技术。
而机械胀接技术包括了拉拔成形法、滚压成形法等;柔性胀接技术包括了爆炸成形法、液压成形法等。
2.1 滚压成形法滚压成形法典型的方法是滚压复合技术,是通过在双金属管道里面用放入滚动体,并用心轴回转带动其不断挤压内管,如图1所示。
2.2 拉拔成形法拉拔成形法是分别取两根已经制好的金属管,将内径大的套在外径小的外面,然后通过拉拔金属管或者成形模,实现二者紧密配合的机械结合,最终成形双金属复合管,如图2所示。
2.3 爆炸成形法爆炸成形法的原理是利用炸药爆炸时产生的冲击波,使制造双金属复合管的两种金属实现固相焊接。
2.4 液压成形法液压成形法的原理是先将内管和外管套装在一起将液体注入筒内,然后对内管液体进行加压,并逐渐增加压力,内层管由弹性变形逐渐进入塑性变形,并贴紧外管,贴紧后继续在直径方向向上塑性膨胀,两管紧密地贴合在一起,形成所需的双金属复合管。
316L∕X70双金属复合管液压胀接成形机理
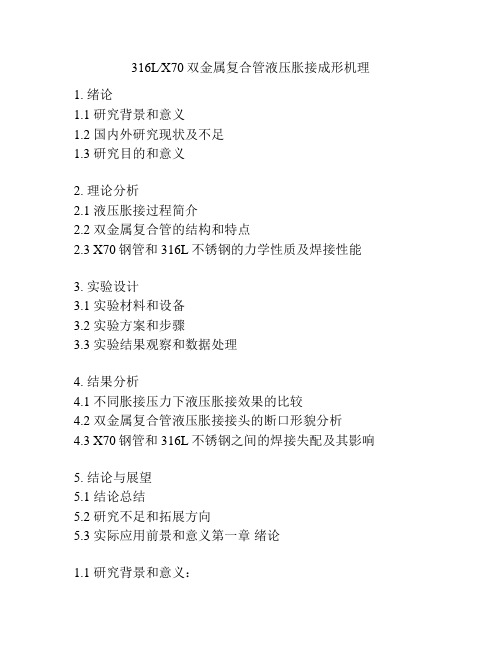
316L∕X70双金属复合管液压胀接成形机理1. 绪论1.1 研究背景和意义1.2 国内外研究现状及不足1.3 研究目的和意义2. 理论分析2.1 液压胀接过程简介2.2 双金属复合管的结构和特点2.3 X70钢管和316L不锈钢的力学性质及焊接性能3. 实验设计3.1 实验材料和设备3.2 实验方案和步骤3.3 实验结果观察和数据处理4. 结果分析4.1 不同胀接压力下液压胀接效果的比较4.2 双金属复合管液压胀接接头的断口形貌分析4.3 X70钢管和316L不锈钢之间的焊接失配及其影响5. 结论与展望5.1 结论总结5.2 研究不足和拓展方向5.3 实际应用前景和意义第一章绪论1.1 研究背景和意义:随着现代工程领域对复杂结构材料需求的增加,双金属复合管作为一种具有高强度、高韧性以及优异抗腐蚀性能的重要材料而备受关注。
在液压胀接方面,其具有优异的连接性能,更是在航空、航天、化工、核电等领域得到了广泛应用。
然而,由于双金属复合管内、外管材相对较薄并且质量不同,液压胀接加工时容易使得使用X70钢管和316L不锈钢管胀接液压系统链路出现变形、开裂或其他缺陷,严重影响双金属复合管的使用性能,这也成为当前研究的热点问题。
1.2 国内外研究现状及不足:目前液压胀接研究较为丰富,以国外的美国和日本为代表得到广泛应用。
在国内,随着工业发展需求,液压胀接的研究不断提升,其实验方法和过程也在不断完善。
但是对于液压胀接加工双金属复合管的研究仍不足,无法满足实际应用的需求。
1.3 研究目的及意义:针对现有问题,本文旨在通过对X70钢管与316L不锈钢管液压胀接加工过程的研究,探究液压胀接加工双金属复合管的机理、影响因素及其加工精度等问题。
从而提升液压胀接技术在双金属复合管领域的应用,为相关领域的研究和实际应用提供参考和依据。
第二章理论分析2.1 液压胀接过程简介液压胀接是一种以外界力量加压胀入管端的加工方法,通过运用压入球形或锥形扩展头,将内膜度过厚的管端撑开,从而让最终的液压胀接成形。
双金属不锈钢复合管的生产工艺汇总

双金属不锈钢复合管的生产工艺汇总双金属不锈钢复合管是一种由两种不同金属制成的管材,具有不锈钢外层和内层。
它结合了不锈钢的耐腐蚀性和强度以及其他金属的导热性和导电性能,可以广泛应用于石化、化工、船舶、核电站等行业。
以下是关于双金属不锈钢复合管的生产工艺的汇总。
1.材料准备:2.钢管制备:首先需要将不锈钢以及其他金属制成管材。
制备钢管的工艺通常包括热轧、冷拉或焊接等工序,根据不同的材料和要求选择合适的加工方式。
在制备的过程中需要控制好管材的尺寸、表面质量和机械性能等指标。
3.内外钢管的清洗:由于双金属复合管的内外层由不同材料组成,为了保证内外界面的粘接质量,需要对内外钢管进行清洗。
清洗一般使用酸洗、碱洗或电解清洗等方法,以去除管材表面的氧化皮、油污和其他杂质,为后续的粘接工艺做好准备。
4.内外管的粘接:将清洗过的钢管进行内外粘接。
粘接工艺通常采用高温焊接或物理粘接的方式。
高温焊接可以将内外层金属材料熔融并形成强力的粘接。
物理粘接包括滚压法、滚焊法和镶嵌法等,将内层金属塞入外层金属管中,通过一定的力量和变形将两者粘接在一起。
5.精整加工:粘接后的双金属复合管具有一定的粘接接头,需要进行进一步的精整加工。
精整加工可以采用机械加工、切割或抛光等方法。
目的是去除管材表面的凸凹、毛刺和瑕疵等缺陷,获得光滑的表面和合适的尺寸,确保管材的质量和使用性能。
6.性能测试:制备完成的双金属不锈钢复合管需要进行性能测试。
性能测试包括力学性能、耐腐蚀性能、密封性能等方面的测试。
通过对复合管的性能测试可以验证其质量是否符合要求,并对管材进行分类和检验。
7.表面处理:最后对复合管进行表面处理,以提高其耐腐蚀性和装饰性。
表面处理可以采用喷涂、镀锌、抛光等方法。
根据具体的使用要求和环境条件选择合适的表面处理方式。
双金属不锈钢复合管的生产工艺需要进行多个环节的操作和控制,确保制备出质量优良的管材。
生产工艺的每一个环节都需要严格控制,保证各种加工参数、设备、工艺和材料的符合要求。
- 1、下载文档前请自行甄别文档内容的完整性,平台不提供额外的编辑、内容补充、找答案等附加服务。
- 2、"仅部分预览"的文档,不可在线预览部分如存在完整性等问题,可反馈申请退款(可完整预览的文档不适用该条件!)。
- 3、如文档侵犯您的权益,请联系客服反馈,我们会尽快为您处理(人工客服工作时间:9:00-18:30)。
双金属复合管塑形成形过程
塑形复合成形技术利用材料的弹塑性特性,使内外管接触并产生紧密的结合。
塑形复合成形技术种类很多,但其复合过程与机理基本上是一致的,以内覆管为例,其塑性复合过程可以分以下三个连续过程:
⑴内管变形阶段
开始时内层管与外层管之间存在间隙,当内管内壁施加加载压力后,内管关闭产生径向膨胀,知道内管外表面与外管内表面刚好接触,间隙消除,此时还未产生接触压力。
⑵复合阶段
随着加载压力的继续增加,开始了对外管的加载过程。
外管首先出现弹性扩张,知道外管内表面满足屈服条件后,外管出现部分塑性扩张,随着加载压力不断加大,外管中的塑性区不断扩展,直到达到最大加载压力为止。
⑶卸载阶段
加载压力从最大逐渐减少至零,这时内管和外管均处于卸载状态。
由于第二阶段中产生了塑性变形,当加载压力完全消除后,内外管之间仍然接触,产生残余接触压力。
在塑性复合过程中,内管发生了大塑性变形,外管则处于弹性变形状态或部分塑性变形状态,在卸载时由于外管的回弹量大于内管的回弹量,外管箍紧内管,两管之间形成胀紧力,即残余接触压力,达到紧密的机械结合;残余接触压力的大小取决于材料的回弹能力。
如果再高温条件下,则在复合阶段管层间塑性变形量越大,越易在结合界面发生扩散反应,达到界面冶金结合。