FMEA横表5
质量管理五大核心工具APQP、PPAP、SPC、MSA、FMEA(精选)
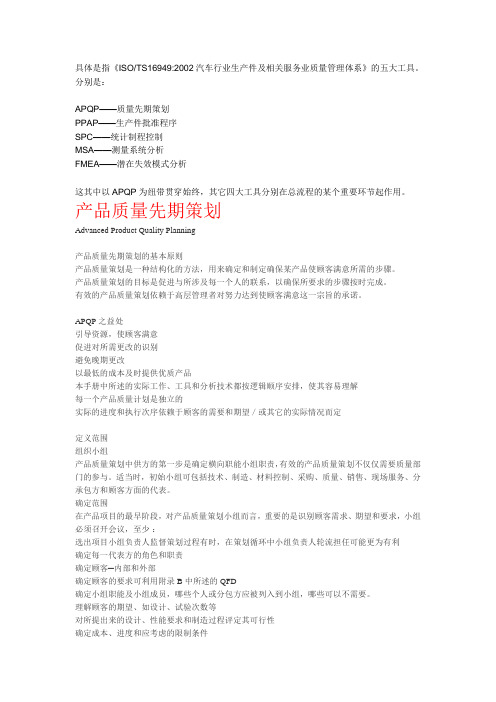
控制计划是控制零件和过程系统的书面描述,单独的控制计划包括三个独立的阶段:
样件:在样件制造过程中,对尺寸测量和材料与性能试验的描述。
试生产:在样件试制之后,全面生产之前所进行的尺寸测量和材料与性能试验的描述。
生产:在大批量生产中,将提供产品/过程特性,过程控制、试验和测量系统的综合文件。
问题的解决
第一阶段之输入
顾客的呼声
市场研究
保修记录和质量信息
小组经验
业务计划/营销策略
产品/过程基准数据
产品/过程设想
产品可靠性研究
顾客输入
第一阶段的输出作为第二阶段的输入
设计目标
可靠性和质量目标
初始材料清单
初始过程流程图
产品和过程特殊特性的初始清单
产品保证计划
管理者支持
顾客的呼声
“顾客的呼声”包括来自内部/外部顾客们的抱怨、建议、资料和信息。
确定范围
在产品项目的最早阶段,对产品质量策划小组而言,重要的是识别顾客需求、期望和要求,小组必须召开会议,至少:
选出项目小组负责人监督策划过程有时,在策划循环中小组负责人轮流担任可能更为有利
确定每一代表方的角色和职责
确定顾客─内部和外部
确定顾客的要求可利用附录B中所述的QFD
确定小组职能及小组成员,哪些个人或分包方应被列入到小组,哪些可以不需要。
APQP之益处
引导资源,使顾客满意
促进对所需更改的识别
避免晚期更改
以最低的成本及时提供优质产品
本手册中所述的实际工作、工具和分析技术都按逻辑顺序安排,使其容易理解
每一个产品质量计划是独立的
实际的进度和执行次序依赖于顾客的需要和期望/或其它的实际情况而定
FMEA5.0
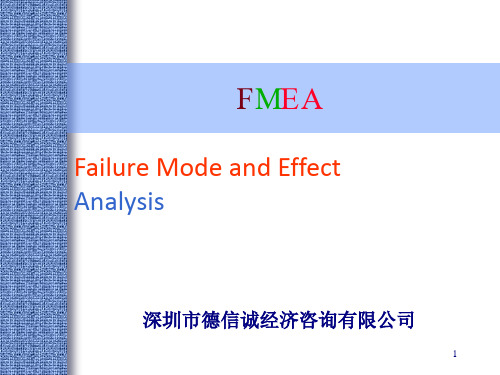
典型的开发三部曲
© Quality & Satisfy 2003-03-01
16
控制计划/过程流程结合图例
建议的产品质量计划顺序
过程流程清单 (包括所有的过程) APQP程序 将启动这个过程 过程流程清单 转化为 过程控制计划 PFMEA (所有的“”主要“过程) 利用RPN值来评定特性 值来评定特性 利用 DFMEA
机器
工具 工作站 生产线 操作者培训 过程 测量
注意:将全过程的 失效模式降为最小 目标:最大化的 全过程质量、 可靠性、成本 和可维护性
10
© Quality & Satisfy 2003-03-01
FMEAs的关联
失效模式 后 果 原 因
SFMEA DFMEA
问题的分支
问题
问题产生的原因
问题产生的原因来自 SFMEA
© Quality & Satisfy 2003-03-01 17
过程流程/ 控制计划 (所有的“”主要“过程)
FMEA 的益处
• • • • • • 预防计划 识别改变需求 降低成本 减少浪费 降低保证成本 降低无增值操作
© Quality & Satisfy 2003-03-01
18
FMEA 的前提条件
定义顾客
DFMEA的顾客 • 最终使用者:使用产品的人 PFMEA的顾客 • 后序的操作者 • 最终使用者:使用产品的人
© Quality & Satisfy 2003-03-01
31
注意
不要混淆 DFMEA与PFMEA的起因和失效 DFMEA的失效 润滑能力不足 错误的原料说明 PFMEA的失效 润滑油使用不够 错误的原料使用
FMEA管理办法

FMEA管理办法1 目的提高新产品开发质量,积累专业制造技术,全面提高生产过程质量,做好防范于未然,杜绝不良产品发生机会。
2 范围适用于本公司汽车零部件过程FMEA活动的控制。
3 职责3.1总工程师负责任命项目经理;3.2项目经理负责组织建立横向职能小组(CFT),负责PFMEA的活动管理,并组织CFT进行FMEA讨论,通过措施的实施和跟踪,总结FMEA结果,形成文件提交审批。
4 工作程序4.1对建议采取的措施必须落实责任部门和完成日期,CFT应考虑建议措施被实施的可能性,保证所有的建议己妥善地处理。
4.2措施实施顾客审查批准方能实施。
4.3重新评审采取了纠正措施之后,应重新估算缺陷的“频度数(0)”、“探测度数(D) ",并重新计算识别风险优先等级。
4.4项目组建立年度评审计划。
按评审计划组织评审,输出PFMEA评审表及PFMEA评审问题清单。
应至少每年一次必须覆盖所有工序,以确定是否有需要更新的内容并形成评审记录。
4.5项目组应对FMEA的CFT活动进行记录,并统一归档5.评价准则表1.严重度(S)评价准则、频度(O)评价准则表2.探测频度(D)评价准则分值探测度D 10 无探测手段9目测抽检8 100%线下检验7 100%线上检验8 定性抽检7 (止通规、检具)100%线下检验6 100%线上检验7 定量抽检6 (量具)100%线下检验5 100%线上检验,但只有报警没有办法对故障件采任何措施5设备或者定量的量具100%线上检验,但只有报警没有办法对故障件采任何措施4 100%线上检验,有报警能保证故障件不流到下一个过程3 100%线上检验,有报警,有措施保证故障件在本工序被发现2 在本工序有100%的探测手段,发现根本原因,不能产生不合格品1 失效模式不可能发生表3 PL等级评分标准。
FMEA 控制程序

1.目的:确定与产品和过程相关的潜在失效模式。
评价失效对顾客的潜在影响。
确定潜在制造或装配失效的起因并确定要采取控制来降低失效产生频度或失效条件探测度的过程变量。
确定过程变量以此聚焦于过程控制。
编制“潜在失效模式分级表”(“严重度”、“频度”、“探测度”和“风险顺序数(RPN)”),从而为制程纠正预防建立一套优先控制系统。
为客观评价设计,包括功能要求及设计方案,提供帮助。
2.范围:适用于所有新产品。
3.权责:3.1生产课负责组成跨部门功能小组统筹制订PFMEA。
3.2跨部门功能小组成员包括:生产部主管、生技、工程主管或相关工程师、品质课主管、责任品管、采购。
跨部门功能小组成员协助生产单位制订PFMEA。
4.定义:PFMEA: 制造失效模式及后果分析(PROCESS FAILURE MODE AND EFFCTS ANALYSIS)。
顾客: FMEA中“顾客”一般指“最终使用者”,但也可以是下工序。
风险顺序数(RPN): RISK PRIORITY NUMBER。
5.作业流程:5.1使用时机及范围:5.1. 1 FMEA的制定必须在小量试或生产用工装到位之前进行,并在小批量试产及量产阶段不断确认完善。
5.1. 2制程变更时,针对变更及相关影响部份。
5.1. 3考虑从备料到包装出货的所有工序。
5.1. 4 PFMEA假设所设计的产品会满足要求及提供的材料是合格的。
5.2 制订FMEA的要求:在最初的FMEA中,要求负责制造的主管能够直接地、主动地联系横向跨部门功能小组成员,以获取更多的经验和建议。
5.3 FMEA的开发:生产流程图应确定与每个制程有关的产品之特性参数,用于FMEA准备工作中的“流程/风险评定”的复制件伴随“制程FMEA”。
5.4 表格填写说明:下面介绍表格的具体应用,所述各项的序号都标在表上对应的栏中,「过程潜在失效模式及后果分析」表格见附件五:5.4.1 (1)项目/要求:5.4.1.1简单描述被分析的零部件或工序。
FMEA检查表

● 过程中可能出错的细节是否明确? ● 可能导致出错的特性是否可确定或控制? 故障原因 /机理 ● 是否考虑了过程特性? ● 是否考虑了设计缺陷? ● 是否考虑了每步工序进入的材料和零件? ● 是否考虑操作者的因素?
2
项
目
问 ● 将要采用的控制是否用于检测坏零件?
题
Yes
No
目前采用的 ● 控制可否在零件离开加工/组装厂前检测出坏零件? 过程控制 ● 控制是用于检测或是用于预防是否明确? ● 是否根据故障模式的最严重后果打分? 严重度 ● 顾客后果打分与设计 FMEA 中的打分是否一致? 频度 探测度 某一故障模式的能力确定? ● 特殊特性及其控制是否明确? ● 临界特性是否用规定的符号标明? 分类 ● 特殊特性是否作为过程(或零件)特性标明? ● 特殊特性及其控制是否已通知责任设计师? RPN ● 风险顺序数(RPN)排列是否由高到低排列? ● 过程措施是否考虑了降低临界特性的临界值? ● 特殊加工/装配控制是否明确用于特殊特性? ● 是否考虑了所有的特殊特性? ● 是否考虑了纠正措施以降低列最高位的故障模式的 RPN 值? 建议措施 ● 建议措施的责任和完成日期是否列出? ● 是否在适当的位置标出预防(而不是检测)措施? ● 是否考虑了在适宜的情况下采取了消除/减少故障模式的潜在危害发生的 措施? 跟踪 ● RPN 序号是否由高到低排列 ● 该频度数是否考虑了预防控制可减少某个故障模式发生的能力? ● 该探测度数是否根据目前采用的控制在零件离开制造或装配工位前检出
DFMEA 检查表
项 目 ● 准备 ● 标栏 功能模型是否清楚? ● 所有标题栏是否填清? ● 设计意图与目的是否清楚? 项目/功能 ● 功能描述得清楚吗? ● 功能可度量吗? ● 失效模式是否与功能有关? 失效模式 ● 失效模式是否全想到了? ● 失效模式术语是否规范? ● 能确认是根本原因吗? 失效原因 ● 设计缺陷是否可能包括在制造/装配变差中? /机理 ● 是否将制造/装配原因排外? ● 所列出的设计控制能在投产前检测出失效模式或失效模式的原因吗? 设计控制 ● 是否将制造/装配检测方法排除在外? 严重度 频度 探测度 ● 严重度数是否基于最严重的故障模式? ● 是否以第一级原因为根据? ● 是ห้องสมุดไป่ตู้考虑在工程投放(engineering release)前被测出? ● 所有特殊特性已清楚确认? 级别 ● 特殊特性与零件特性对应? ● 特殊特性是否传递给 PFMEA 小组? RPN ● 将 RPN 从高到低进行排序了吗? ● 强调了特殊特性吗? ● 对降低高 RPN 采取措施了吗? 建议措施 ● 责任、时间列清了吗? ● 预防为主代替缺陷检测吗? ● 使设计更加有适应性吗? ● 是设计措施而不是制造装配措施吗? 其他 ● 措施执行了吗? ● 措施使 RPN 降低到期望值了吗? 问 横向职能小组(FMEA)是否建立? 题 Yes No
fmea评审表格
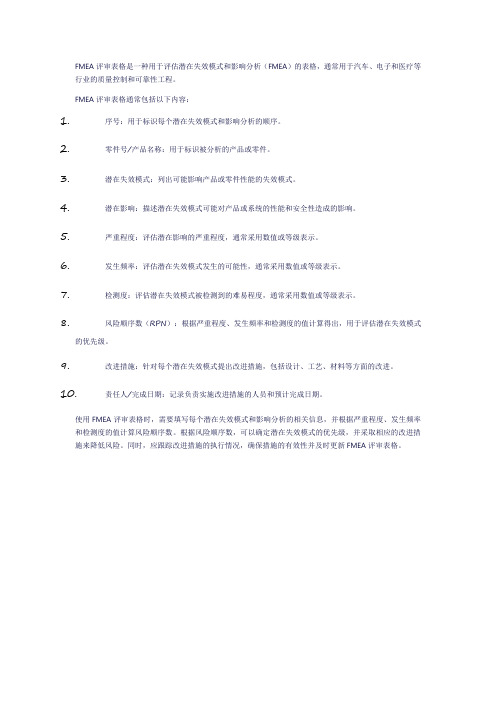
FMEA评审表格是一种用于评估潜在失效模式和影响分析(FMEA)的表格,通常用于汽车、电子和医疗等行业的质量控制和可靠性工程。
FMEA评审表格通常包括以下内容:
1.序号:用于标识每个潜在失效模式和影响分析的顺序。
2.零件号/产品名称:用于标识被分析的产品或零件。
3.潜在失效模式:列出可能影响产品或零件性能的失效模式。
4.潜在影响:描述潜在失效模式可能对产品或系统的性能和安全性造成的影响。
5.严重程度:评估潜在影响的严重程度,通常采用数值或等级表示。
6.发生频率:评估潜在失效模式发生的可能性,通常采用数值或等级表示。
7.检测度:评估潜在失效模式被检测到的难易程度,通常采用数值或等级表示。
8.风险顺序数(RPN):根据严重程度、发生频率和检测度的值计算得出,用于评估潜在失效模式
的优先级。
9.改进措施:针对每个潜在失效模式提出改进措施,包括设计、工艺、材料等方面的改进。
10.责任人/完成日期:记录负责实施改进措施的人员和预计完成日期。
使用FMEA评审表格时,需要填写每个潜在失效模式和影响分析的相关信息,并根据严重程度、发生频率和检测度的值计算风险顺序数。
根据风险顺序数,可以确定潜在失效模式的优先级,并采取相应的改进措施来降低风险。
同时,应跟踪改进措施的执行情况,确保措施的有效性并及时更新FMEA评审表格。
五大工具

五大工具:MSA、APQP、SPC、FMEA、PPAP •MSA••测量系统分析••在日常生产中,我们经常根据获得的过程加工部件的测量数据去分析过程的状态、过程的能力和监控过程的变化;那么,怎么确保分析的结果是正确的呢?我们必须从两方面来保证,一是确保测量数据的准确性/质量,使用测量系统分析(MSA)方法对获得测量数据的测量系统进行评估;二是确保使用了合适的数据分析方法,如使用SPC工具、试验设计、方差分析、回归分析等。
••测量系统的误差由稳定条件下运行的测量系统多次测量数据的统计特性:偏倚和方差来表征。
偏倚指测量数据相对于标准值的位置,包括测量系统的偏倚(Bias)、线性(Linearity)和稳定性(Stability);而方差指测量数据的分散程度,也称为测量系统的R&R,包括测量系统的重复性(Repeatability)和再现性(Reproducibility)。
••一般来说,测量系统的分辨率应为获得测量参数的过程变差的十分之一。
测量系统的偏倚和线性由量具校准来确定。
测量系统的稳定性可由重复测量相同部件的同一质量特性的均值极差控制图来监控。
测量系统的重复性和再现性由GageR&R研究来确定。
••分析用的数据必须来自具有合适分辨率和测量系统误差的测量系统,否则,不管我们采用什么样的分析方法,最终都可能导致错误的分析结果。
在ISO10012-2和QS9000中,都对测量系统的质量保证作出了相应的要求,要求企业有相关的程序来对测量系统的有效性进行验证。
••测量系统特性类别有F、S级别,另外其评价方法有小样法、双性、线性等.••分析工具••在进行MSA分析时,推荐使用Minitab软件来分析变异源并计算Gage R&R和P/T。
并且根据测量部件的特性,可以对交叉型和嵌套型部件分别做测量系统分析。
••另外,Minitab软件在分析量具的线性和偏倚研究以及量具的分辨率上也提供很完善的功能,用户可以从图形准确且直观的看出量具的信息。
最新FMEA风险评估对比SOD RLM RMP AP行动优先级

24
RMR第9-27分是红色,属于高风险区域
23
22
RMR特点:27个排列组合,同时考虑S×O、S×D、D×O,S、O、D都考虑了两次,这方法得分出的风险结果一定非常精准。
21
但操作麻烦而且RMR在排列时不优先考虑客户,上表优先等级1、2的是风险度较低的。
20
19
18
17
16
S×O
S×D
D×O
15
14
相同
黄
2
257
6
3
RLM
SD
RLM优 先等级
SO
3
2
红
3
2
绿
2
2
红
3
3
绿
3
3
红
3
3
黄
RMR
AP
SD
DO
RMR优 RMR排 AP行动 先等级 序 优先级
AP排序
绿
黄
16
4
M
2
红
绿
10
5
M
2
绿
红
22
3
M
2
红
绿
10
5
M
2
黄
红
25
1
H
1
红
红
24
2
H
1
RPN:
1、RPN阈值 设定一个RPN值上限,如果RPN值大于阈值,则必须采取措施。 根据审核经验,由于O和D值是由主观来定义的,即可人为修改,所以一份FMEA里面超出阈值的一般只有几条甚至没有,这有悖于RPN的初衷。
频度0 探测度D
频度0
10
10
10
13
5-流程图和PFMEA

课程目标♦1-了解流程图基本知识并熟悉编写方法♦2-了解过程FMEA基本知识并熟悉编写方法流程图基本知识作业(工艺)流程图是用简明的图形\符号及文字组合形式表示的作业全过程中各过程输入\输出和过程形成要素之间的关联和顺序.可从产品的原材料\产品组成部分和作业所需的其它物料投入开始到最终产品实现的全过程中的所有备料\制作(工艺反应)\搬运\包装\防护\存储等作业的程序.检验流程图是用图形\符号,简洁明了地表示检验计划中确定的特定产品的检验流程(过程\路线)\检验工序\位置设置\和选定的检验方式\方法\和相互顺序的图样.可直接使用作业流程图,并在需要质量控制和检验的部位\处所,连接表示检验的图形和文字,必要时标明检验的具体内容\方法,同样起到检验流程图的作用和效果.②检验流程图一\流程图:①作业(工艺)流程图①作业(工艺)流程图作业(工艺)流程图是用简明的图形\符号及文字组合形式表示的作业全过程中各过程输入\输出和过程形成要素之间的关联和顺序.可从产品的原材料\产品组成部分和作业所需的其它物料投入开始到最终产品实现的全过程中的所有备料\制作(工艺反应)\搬运\包装\防护\存储等作业的程序.②检验流程图检验流程图是用图形\符号,简洁明了地表示检验计划中确定的特定产品的检验流程(过程\路线)\检验工序\位置设置\和选定的检验方式\方法\和相互顺序的图样.可直接使用作业流程图,并在需要质量控制和检验的部位\处所,连接表示检验的图形和文字,必要时标明检验的具体内容\方法,同样起到检验流程图的作用和效果.过程流程图♦过程流程图是对材料整个制造和装配过程直观地描述其连续流程的计划工具。
♦其作用是:♦制造方法改进分析,减少流程工步的数量可以用于时间和距离的研究,决定生产线的平衡及改进制造。
♦了解用于流程每一步的模具、设备或检具的细节。
♦了解每一项操作对产品和过程变化的影响因素。
这些因素可能是与材料、工具、设备、工位器具、环境条件及操作相关。
可靠性工程师模拟题及答案2
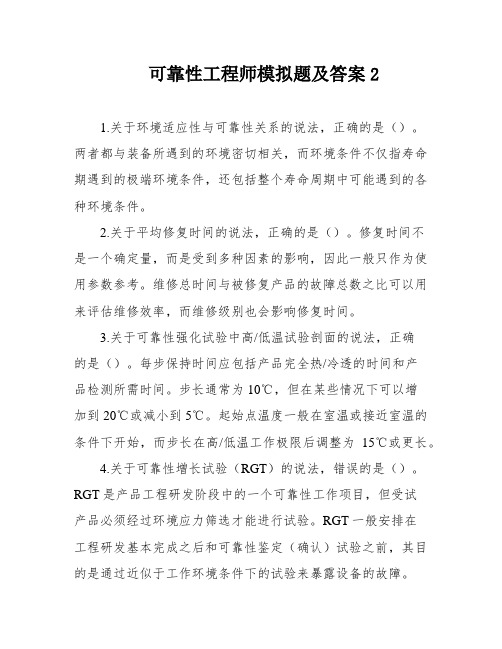
可靠性工程师模拟题及答案21.关于环境适应性与可靠性关系的说法,正确的是()。
两者都与装备所遇到的环境密切相关,而环境条件不仅指寿命期遇到的极端环境条件,还包括整个寿命周期中可能遇到的各种环境条件。
2.关于平均修复时间的说法,正确的是()。
修复时间不是一个确定量,而是受到多种因素的影响,因此一般只作为使用参数参考。
维修总时间与被修复产品的故障总数之比可以用来评估维修效率,而维修级别也会影响修复时间。
3.关于可靠性强化试验中高/低温试验剖面的说法,正确的是()。
每步保持时间应包括产品完全热/冷透的时间和产品检测所需时间。
步长通常为10℃,但在某些情况下可以增加到20℃或减小到5℃。
起始点温度一般在室温或接近室温的条件下开始,而步长在高/低温工作极限后调整为15℃或更长。
4.关于可靠性增长试验(RGT)的说法,错误的是()。
RGT是产品工程研发阶段中的一个可靠性工作项目,但受试产品必须经过环境应力筛选才能进行试验。
RGT一般安排在工程研发基本完成之后和可靠性鉴定(确认)试验之前,其目的是通过近似于工作环境条件下的试验来暴露设备的故障。
5.下列不属于“通用质量特性”的是()。
舒适性不属于通用质量特性,而可靠性、维修性和安全性都是通用质量特性。
6.可靠性鉴定试验和寿命试验是为了验证产品是否达到了规定的可靠性或寿命要求的。
而可靠性增长试验是通过暴露设备的故障来逐步提高其可靠性。
7.制定综合保障计划的是订购方,其目的是确保装备在整个使用寿命周期中得到有效的支持和维护。
8.制定综合保障工作计划的是承制方,其目的是根据综合保障计划制定具体的保障措施和工作计划。
9.纠正措施报告中必需包含截止日期、责任部门和故障证据,而故障费用不是必需的。
10.关于分布参数点估计解析法的说法,错误的是()。
最小二乘法和极大似然法并不适用于所有情况,而矩法只适用于完全样本情况。
最好线性无偏和最好线性不变估计法只适用于定数截尾情况,而极大似然法适用于定数截尾情况,并且求解方法相对简单。
FMEA知识
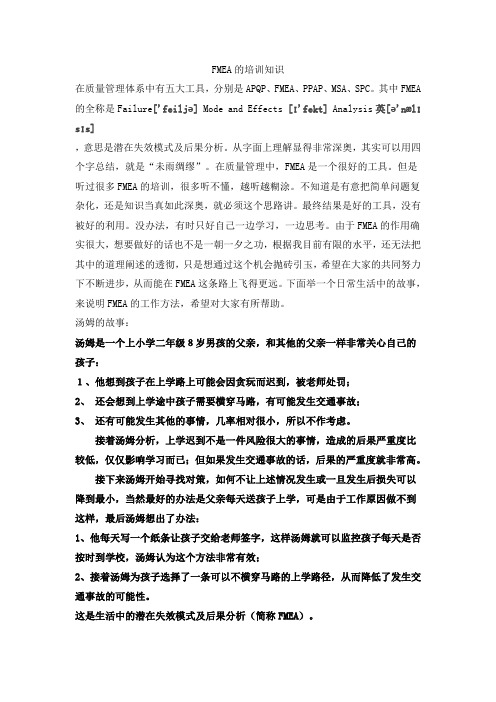
FMEA的培训知识在质量管理体系中有五大工具,分别是APQP、FMEA、PPAP、MSA、SPC。
其中FMEA 的全称是Failure['feiljə] Mode and Effects [ɪ'fekt] Analysis英[ə'nælɪsɪs],意思是潜在失效模式及后果分析。
从字面上理解显得非常深奥,其实可以用四个字总结,就是“未雨绸缪”。
在质量管理中,FMEA是一个很好的工具。
但是听过很多FMEA的培训,很多听不懂,越听越糊涂。
不知道是有意把简单问题复杂化,还是知识当真如此深奥,就必须这个思路讲。
最终结果是好的工具,没有被好的利用。
没办法,有时只好自己一边学习,一边思考。
由于FMEA的作用确实很大,想要做好的话也不是一朝一夕之功,根据我目前有限的水平,还无法把其中的道理阐述的透彻,只是想通过这个机会抛砖引玉,希望在大家的共同努力下不断进步,从而能在FMEA这条路上飞得更远。
下面举一个日常生活中的故事,来说明FMEA的工作方法,希望对大家有所帮助。
汤姆的故事:汤姆是一个上小学二年级8岁男孩的父亲,和其他的父亲一样非常关心自己的孩子:1、他想到孩子在上学路上可能会因贪玩而迟到,被老师处罚;2、还会想到上学途中孩子需要横穿马路,有可能发生交通事故;3、还有可能发生其他的事情,几率相对很小,所以不作考虑。
接着汤姆分析,上学迟到不是一件风险很大的事情,造成的后果严重度比较低,仅仅影响学习而已;但如果发生交通事故的话,后果的严重度就非常高。
接下来汤姆开始寻找对策,如何不让上述情况发生或一旦发生后损失可以降到最小,当然最好的办法是父亲每天送孩子上学,可是由于工作原因做不到这样,最后汤姆想出了办法:1、他每天写一个纸条让孩子交给老师签字,这样汤姆就可以监控孩子每天是否按时到学校,汤姆认为这个方法非常有效;2、接着汤姆为孩子选择了一条可以不横穿马路的上学路径,从而降低了发生交通事故的可能性。
FMECA介绍及使用
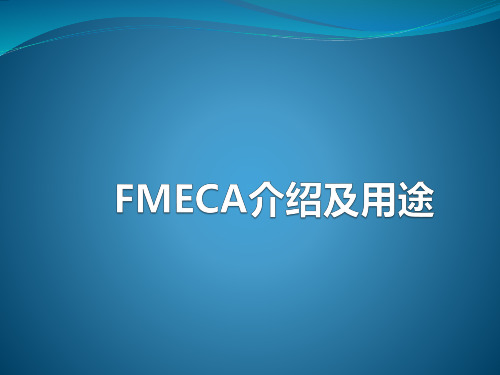
2
扰。(不利于空气净化和水处理,严重时威胁产品 质量)
4
3
12
高风险
3
总体布局:不符合《工业企业总平面设计规范》,
不符合GMP的要求。(不符合GMP的基本原则)
总体布局:没有按照行政、生产、辅助和生活等划 区布局。 (存在污染的可能)
4
3
12
高风险
4
4
3
12
高风险
FMECA介绍及用途
10/20/2017
FMECA的构成
10/20/2017
FMECA的构成
FMEA的构成
失效后的严重程度(S)
失效的可能性性(O)
FMECA介绍及用途
10/20/2017
FMECA的构成
严重程度
(定性评估)
SEV危害影响的严重程度
高
后果严重:
1. 非常重大的GMP违规
2. 可能对患者造成危害
中
后果严重程度中等:
1. 严重GMP违规 2. 可能对患者造成不良影响
4
3
2
24
高风险
4
4
3
2
24
高风险
FMECA介绍及用途
10/20/2017
FMECA的构成
FMECA
(练习)
将刚才使用FMEA列出的高中低风险,再对其的可检测性进 评估,得出FMECA评价表 时间:1min
FMECA介绍及用途
10/20/2017
FMECA的构成
FMECA
编号
1
(练习)
严重程度S 可能性O 可检测性 RPN
FMECA来源于 FMEA
设计阶段,对构成产品的子系统、 零件,对构成过程的各个工序逐一 进行分析,找出所有潜在的失
fmea大纲

FMEA大纲通常包括以下几个部分:
1. FMEA简介:介绍FMEA的概念、目的、意义和应用范围。
2. FMEA基本概念:包括失效模式、失效效应、风险优先数等基本概念,帮助理解FMEA的分析方法。
3. FMEA功能:介绍FMEA在产品设计阶段和过程设计阶段的功能,如识别潜在失效模式、分析失效影响、评估风险优先数等。
4. FMEA使用时机:说明在何时使用FMEA,例如在产品设计阶段、过程设计阶段、产品制造阶段等。
5. FMEA运用成功的关键:介绍运用FMEA成功的关键因素,如团队协同合作、有效沟通、数据分析等。
6. FMEA应用流程:详细介绍FMEA的应用流程,包括准备阶段、分析阶段、结果解释阶段等。
7. 失效分析技巧:介绍失效分析的技巧和方法,如因果图分析、故障树分析等。
8. 探究根因方法:介绍探究产品或过程失效根本原因的方法,如实验设计、数据分析等。
9. FMEA案例分析:通过实际案例分析,展示FMEA在产品设计和过程设计中的应用和效果。
10. 总结与展望:总结FMEA的重要性和应用前景,提出未来研究方向和应用建议。
以上是FMEA大纲的一般内容,具体内容和结构可能会因不同的培训课程或教材而有所差异。
动力定位船舶的FMEA介绍

万方数据万方数据万方数据第3期沈锦康:动力定位船舶的FMEA介绍29从图中还可以进一步分析得到:分别为1号与2号主机及其齿轮箱轴系、l号艏侧推和1号艉侧推服务的辅助泵,其动力和控制电源均接自1号柴油发电机配电系统,所以任何单点故障都不能导致2台柴油发电机同时停机或脱扣。
1号与2号主机和3号与4号主机之间达成了更高的冗余:主推和齿轮箱安装机带滑油泵,或者是有冗余供电的双电动润滑、冷却和执行机构。
我们假设这在本例中实现了1号柴油发电机母排短路不会引起1号与2号主机、左主推和齿轮箱故障等停机,那么本船在预定的DP操作状态下,最严重的单点故障就是:左齿轮箱故障。
因为能引起左主推和轴带发电机停止,进而失去1号艏侧推和l号艉侧推,使本船DP定位能力降低。
但还有2号艏艉侧推在船艏和船艉提供横向推力,右主推还可提供纵向推力,在设计海况下船舶仍能保持动力定位。
如果2台舵机参与DP控制,也要适用以上的规则。
(4)船舶管系也影响到冗余的实现下面以DNV规范为例来作简要说明。
燃油系统:提供必要冗余的系统之间必须有分开的燃油管系和Et用油舱,之间的跨接是可以接受的。
如果DP操作时油品需要加热,其加热系统也得有冗余。
冷却水系统:提供必要冗余的系统之间必须有分开的冷却管系包括膨胀水箱。
滑油系统:单个设备如柴油机、齿轮箱、推进器等滑油系统应各自成体系。
压缩空气系统:提供必要冗余的系统之间必须有分开的压缩空气系统。
对于DP3船舶,以上各项和通风系统还得要防水和防火分割。
(5)冗余对推进器的配置和布置提出了要求。
在发生严重的单点故障后,船舶除了能保持位置和艏向外,还能保持以指定点为中心的转船能力(YAW)。
此外,DNV在2008版DP规范中明确规定基于推进器停止和重新启动不能被认为是冗余,这就提高了推进器的配置要求。
2008版DNV规范对DP船舶电站保护系统、电站管理系统(PMS)和推进控制保护系统进行具体细化:即必须有冗余的PMS系统,在PMS关闭时电站系统也能正常工作;需要合闸运行的母排联络开关必须有短路保护、不平衡电流监控保护、有功电流和无功电流监控保护功能,以免单个发电机励磁或调速器故障蔓延到和其并列运行的其他发电机而引起全船失电;发电机突然停机不能引起和其并列运行的其他发电机因过载脱扣导致全船失电,DP控制系统、PMS和推进器控制保护的减持负载功能应根据其反应时间相互协调实现这一目标。
FMEA标准手册

典型的失效模式可以是但不限于下列情况:裂纹、变形、松动、泄漏、粘结、短路(电器)、氧化、断裂等。
注:应用规范化、专业性的术语来描述潜在失效模式,而不同于顾客所见的现象。
11)潜在失效后果
潜在失效的后果,就是失效模式对系统功能的影响,就如顾客感受的一样。
要根据顾客可能发现或经历的情况来描述失效的后果,要记住顾客可能是内部的顾客,也可能是外部最终的顾客。要清楚地说明该功能是否会影响到安全性或与法规不符。失效的后果必须依据所分析的具体系统、子系统或零部件来说明。还应记住不同级别系统、子系统和零件之间还存在着系统层次上的关系。比如,一个零件的断裂可能引起总成的振动,从而导致系统运行的中断。这种系统运行的中断会引起性能下降,最终导致顾客的不满。因此就需要小组的努力尽可能预见失效的后果。
推荐的评价准则
(小组对评定准则和分级规则应意见一致,即使因为个别产品分析对准则作了修改也应一致)
后果
评定准则:后果的严重度
严重度
无警告的
严重危害
这是一种非常严重的失效形式,它是在没有任何失效预兆的情况下影响到行车安全/或不符合政府的法规
10
有警告的严重危害
这是一种非常严重的失效形式,是在具有失效预兆的前提下所发生的,并影响到行车安全/或不符合政府的法规
典型的失效后果可能是但不限于:噪声、工作不正常、不良外观、不稳定、
运行中断、粗糙、不起作用、异味、工作减弱等。
12)严重度(S)
严重度是潜在失效模式发生时对下序零件、子系统、系统或顾客影响后果
严重程度(列于前一栏中)的评价指标。严重度仅适用于后果。要减少失效的严重
度级别数值,只能通过修改设计来实现,严重度的评估分为1到10级。
时间性是成功实施FMEA的最重要因素之一,它是一个“事前行为”,而不是“事后练习”。为达到最佳效益,FMEA必须在设计或过程失效模式被无意地纳人设计产品之前进行。事先花时间很好地进行综合的FMEA分析,能够容易、低成本地对产品或过程进行修改,从而减轻事后修改的危机。FMEA能够减少或消除因修改而带采更大损失的机会。适当地加以应用,FMEA是一个相互作用的过程,永无止境。
FMECA与FTA分析完整版本

1
FMECA: Fault Mode,Effects and Criticality Analysis 故障(失效)模式、影响(后果)及危害性(严重度)分 析
FTA: Fault Tree Analysis 故障树分析
最新课件
2
FMECA 历史
➢ 二十世纪五十年代初,美国格鲁门飞机公司在研制飞机
FMEA 分析的是潜在故障 (Potential Fault),是可能 发生但是现在还没有发生的故障; 它是 “事前预防”,而不是“事后追悔”; 事先花时间对设计进行分析,事先低成本进行改进; 减少未来更大损失的发生;
最新课件
21
2.2 基本概念
故障模式分析:找出系统中每一产品所有可能出现的 故障模式。
Effective Severity Ranking
故障模式的RPN数越高,则越重要。
最新课件
44
故障模式发生概率评分准则
等级
1
2 3 4 5 6 7 8
稀少 低 中等
高
故障发生的可能性 故障模式发生的可能性极低 故障模式发生的可能性相对较低
最新课件
25
2.2 基本概念
故障影响分析:找出系统中每一产品每一种可能出现的故障模 式所产生的影响,并按这些影响的严重程度进行分类。
检测:分析每一个故障模式的检测方法,以便为系统的维修性、 测试性设计以及系统的维修工作提供依据。
最新课件
26
2.2 基本概念
补偿措施:指在设计中能够防止故障原因发生的方法。 补偿措施分析:分析人员应提出并评价那些能够用来消除或 减轻故障影响的补偿措施。
39
分系统级
**飞机 主供压分系统
PFMEA的编制精解
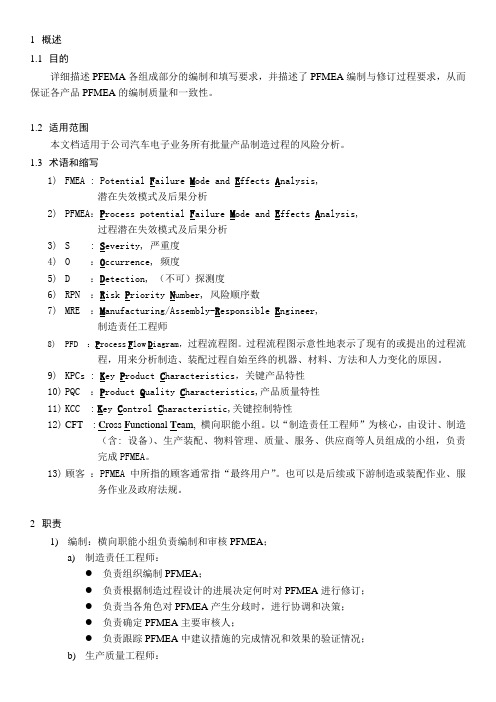
1概述1.1目的详细描述PFEMA各组成部分的编制和填写要求,并描述了PFMEA编制与修订过程要求,从而保证各产品PFMEA的编制质量和一致性。
1.2适用范围本文档适用于公司汽车电子业务所有批量产品制造过程的风险分析。
1.3术语和缩写1)FMEA : Potential F ailure M ode and E ffects A nalysis,潜在失效模式及后果分析2)PFMEA:P rocess potential F ailure M ode and E ffects A nalysis,过程潜在失效模式及后果分析3)S : S everity, 严重度4)O :O ccurrence, 频度5) D :D etection, (不可)探测度6)RPN :R isk P riority N umber, 风险顺序数7)MRE :M anufacturing/Assembly-R esponsible E ngineer,制造责任工程师8)PFD :P rocess F low D iagram,过程流程图。
过程流程图示意性地表示了现有的或提出的过程流程,用来分析制造、装配过程自始至终的机器、材料、方法和人力变化的原因。
9)KPCs : K ey P roduct C haracteristics,关键产品特性10)PQC :P roduct Q uality C haracteristics,产品质量特性11)KCC :K ey C ontrol C haracteristic,关键控制特性12)CFT : C ross F unctional T eam, 横向职能小组。
以“制造责任工程师”为核心,由设计、制造(含: 设备)、生产装配、物料管理、质量、服务、供应商等人员组成的小组,负责完成PFMEA。
13)顾客:PFMEA中所指的顾客通常指“最终用户”。
也可以是后续或下游制造或装配作业、服务作业及政府法规。
质量体系五大工具和七大手法

For personal use only in study and research; not for commercial use五大工具:APQP、SPC、FMEA、MSA、PPAP一、APQP(Advanced Product Quality Planning)即产品质量先期策划,是一种结构化的方法,用来确定和制定确保某产品使顾客满意所需的步骤。
产品质量策划的目标是促进与所涉及的每一个人的联系,以确保所要求的步骤按时完成。
有效的产品质量策划依赖于公司高层管理者对努力达到使顾客满意这一宗旨的承诺。
产品质量策划有如下的益处:◆ 引导资源,使顾客满意;◆ 促进对所需更改的早期识别;◆ 避免晚期更改;◆ 以最低的成本及时提供优质产品。
二、SPC(Statistical Process Control)即统计过程控制,主要是指应用统计分析技术对生产过程进行适时监控,科学区分出生产过程中产品质量的随机波动与异常波动,从而对生产过程的异常趋势提出预警,以便生产管理人员及时采取措施,消除异常,恢复过程的稳定从而达到提高和控制质量的目的。
SPC非常适用于重复性的生产过程,它能够帮助组织对过程作出可靠的评估,确定过程的统计控制界限判断过程是否失控和过程是否有能力;为过程提供一个早期报警系统,及时监控过程的情况,以防止废品的产生,减少对常规检验的依赖性,定时以观察以及系统的测量方法替代大量检测和验证工作。
⊙SPC实施意义可以使企业:◆ 降低成本◆ 降低不良率,减少返工和浪费◆ 提高劳动生产率◆ 提供核心竞争力◆ 赢得广泛客户⊙实施SPC两个阶段分析阶段:运用控制图、直方图、过程能力分析等使过程处于统计稳态,使过程能力足够。
监控阶段:运用控制图等监控过程⊙SPC的产生:工业革命以后,随着生产力的进一步发展,大规模生产的形成,如何控制大批量产品质量成为一个突出问题,单纯依靠事后检验的质量控制方法已不能适应当时经济发展的要求,必须改进质量管理方式。
2.5故障类型、影响和危险度分析(FMEA)
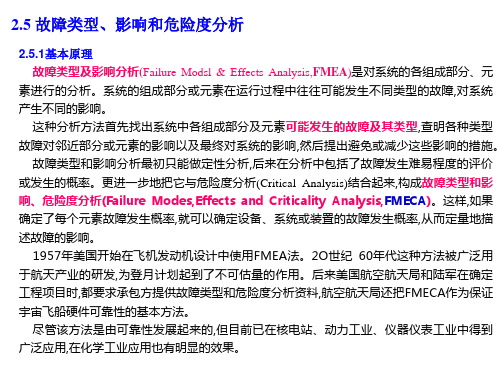
2.5.3故障类型、影响和危险度分析 (FMECA)
将故障类型及影响分析和危险度分析相结合,便可以从定性分析发展到定量分 析,称为故障类型、影响和危险度分析 (FMECA)。 危险度分析的目的在于评价系统每种故障类型的危险度,据此按轻重缓急确定 对策措施。一般地,采用风险矩阵法(概率-严重度)和致命度指数两种方法来评价故 障类型的危险度。
2.5.2故障类型和影响分析 (FMEA) 2.分析步骤
(2)确定分析的层次(2/3)
由图2-2可以看出,在各分析层次中,由于故障所在层次不同,故障类型对上一层影响 和对下一层的故障原因追究深度也不相同。
如果分析的层次太浅,就会漏掉重要的故障类型,得不到有用的资料;反之,若分析得
过深,一切都分析到元件 ,则会造成结果繁杂,费时太多,同时对制定措施也带来了困难。
2.5.3故障类型、影响和危险度分析 (FMECA)
1.风险矩阵法
故障发生的可能性和故障发生后引起的后果,综合考虑后会得出比较准确的衡量标 准,这个标准称为风险率。它代表故障概率和严重度的综合评价。 (1)故障概率 故障概率一般按统计时间内的实际故障次数除以统计时间内实际工作小时数进行计 算。若实际统计有困难,可以使用以下定性和定量分类方法确定单个故障类型的概率。 ①定性分类法: Ⅰ级:故障概率很低,元件操作期间出现的机会可以忽略; Ⅱ级:故障概率低,元件操作期间不易出现; Ⅲ级:故障概率中等,元件操作期间出现的机会为50%; Ⅳ级:故障概率高,元件操作期间易于出现。
分析对象
确定 分析层次
建立故障类型清单、分析故障 原因 及其影响
确定 故障等级
编制 分析文件
(1)了解分析对象,明确系统任务和组成 分析时首先要熟悉有关资料,从中了解系统的组成、任务、工艺流程等情况。查
- 1、下载文档前请自行甄别文档内容的完整性,平台不提供额外的编辑、内容补充、找答案等附加服务。
- 2、"仅部分预览"的文档,不可在线预览部分如存在完整性等问题,可反馈申请退款(可完整预览的文档不适用该条件!)。
- 3、如文档侵犯您的权益,请联系客服反馈,我们会尽快为您处理(人工客服工作时间:9:00-18:30)。
系统FMEA编号:1234 ①×子系统页码:共1页第1页零部件:01、03车身密封②设计责任:车身工程部③编制人:泰特—X6412—车身工程师④车型年/车辆类型:199×/狮牌 4门/旅行⑤关键日期:9× 03 01 ⑥ FMEA日期:(编制)8×03 22(修订)8×07 14 ⑦
主要参加人::T.Fender—汽车产品部、C.切利得斯—生产部、J.福特—总装部(Dalton.Fraser.Henley总装厂)⑧
项目名称:左前门/H8HX—000—A ②工艺责任部门:车身工程/装配部③FMEA编号:1450 ①
页码:共1页第1页
编制人:J.福特—X6521—装配部门④车型年/车辆类型:199×/狮牌 4门/旅行⑤关键日期:9×03 01 9×08 26 ⑥ FMEA日期(编制):9×05 17(修订)9×11 06 ⑦主要参加人:A.泰特—车身工程 J.史密斯—操作控制 R.詹姆斯—生产部 J.约翰—维修部⑧
潜在的失效模式及后果分析
(设计FMEA)
系统FMEA编号:
子系统页码:第页共页零部件:设计责任:编制人:
车型年/车辆类型:关键日期: FMEA日期(编制):(修订)
主要参加人:
潜在的失效模式及后果分析
(过程FMEA)
项目名称:工艺责任部门:FMEA编号:
页码:第页共页
编制人:
车型年/车辆类型:关键日期: FMEA日期(编制): (修订)主要参加人:
潜在的失效模式及后果分析(设计FMEA)
潜在的失效模式及后果分析(过程FMEA)
A—1设计FMEA检查清单
顾客或厂内零件号
修订日期
制定人:
A—7过程FMEA检查清单
顾客或厂内零件号
修订日期
制定人:。