液压系统计算
液压计算常用公式

溢流阀的保养及故障排除减压阀的保养及故障排除流量控制阀的保养及故障排除方向控制阀的保养及故障排除的油封漏油B 机械操作的阀芯不能动作1、排油口有背压2、压下阀芯的凸块角度过大3、压力口及排油口的配管错误同上凸块的角度应在30°以上。
修正配管。
C 电磁阀的线圈烧坏1、线圈绝缘不良2、磁力线圈铁芯卡住3、电压过高或过低4、转换的压力在规定以上5、转换的流量在规定以上6、回油接口有背压更换电磁线圈。
更换电磁圈铁芯。
检查电压适切调整。
降下压力,检查压力计。
更换流量大小的控制阀低压用为1.0kgf/cm²,高压用为kgf/cm²回油口直接接回油箱,尤其是泄油(使用外部泄油)D 液控阀不会作动1、液控压力不足2、阀芯胶着,分解清理之,洗净3、灰尘进入,分解清理之,洗净液控压力为3.5kgf/cm²以上,在全开或中立回油阀须加装止回阀使形成液控压力。
分解清理之,洗净。
电磁阀的保养及故障排除故障原因处置A 动作不良1、因弹簧不良致滑轴无法恢复至原位置2、阀芯的动作不良及动作迟缓3、螺栓上紧过度或因温度上升至本体变形4、电气系统不良更换弹簧。
1、洗净控制阀内部除去油中的混入物。
2、检查过滤器,必要时洗涤过滤器或更换液压油。
3、检查滑轴的磨耗情形,必要时须更换。
松开螺栓上紧程度(对角交互上紧) 检查插入端子部的接触状态,确认电磁线圈的动作是否正常,如果线圈断线或烧损时须更换。
B 磁力线圈噪音及烧损1、负荷电压错误2、灰尘等不纯物质进入3、电磁线圈破损,烧损4、阀芯的异常磨耗检查电压,使用适当的电磁线圈。
除去不纯物。
更换更换C 内部漏油大外部漏油1、封环损伤2、螺栓松更换再上紧液压机器其他故障及排除共振、振动及噪音故障原因处置A 弹簧与弹簧共振二组以上控制阀的弹簧的共振(如溢流阀及溢流阀、溢流阀及顺序阀、溢流阀及止回阀)1、将弹簧的设定压力错开,10kgf/cm²或10%以上。
液压系统计算

注:油箱公称容量大于本系列10000L时,应按GB/T 321 油箱空气容量 10%~15%
流速 v(m/s) 高压胶管通径:6/8/10/13/16/19/22/25/32/38/45/51 钢管通径:3/4/5;6/8/10;12/15/20/25/32/40/50/65
管子承受的压力 安全系数S
说明:对于压力管,当压力高、流量大管路短时取大值 P=2.5~14MPa时,取v=3~4m/s,当p>14MPa时,取v
散热系数 K
W/(m2*℃) 15
环境温度 t2 ℃ 25
油箱散热面积 A=PL/(K*Δt)
m2 0.01
油液最高允许温度 t1 ℃ 40
油箱散热系数K(液压工程师手册) 油箱散热情况 整体式,通风差 单体式,通风较好 上置式,通风好 强制通风式
液压泵站油箱公称容量 系列(JB/T 7938— 2010) /L
2.5、4.0、6.3、10 16、25、40、63、100 160、250、315、400、500、630、800、1000 1250、1600、2000、2500、3150、4000、5000、6300、8000、
10000
吸油管
油箱散热量 PT kw 0
冷却介质温度 t1+t2 ℃ 30
PC=PL-PT kw 30
平均温度差 T=[(T1+T2)-(t1+t2)]/2
℃ 12.5
油的比热容 C
kJ/(kg*℃) 1.88
水的比热容 Cs
kJ/(kg*℃) 4.2
冷却器热交换量 PC=PL-PT kw 4.4
平均温度差 T=[(T1+T2)-(t1+t2)]/2
液压系统计算公式汇总

风冷计算 H=Qa*ρ k*Cp·Δ t(J/h) Qa——风扇风量(m3 / h) ρ k——空气密度(取ρ k=1.29kg/m3) Cp——空气比热容(取Cp=1008J/kg· K)
Δ t——散热温差(取Δ t=10K) 水冷计算 H=Qa*ρ k*Cp·Δ t(J/h) Qa——冷却水量(m3 / h) ρ k——水密度(取ρ k=1000kg/m3) Cp——水比热容(取Cp=4186.8J/kg· K) Δ t——进出水温差
油箱热平衡 油箱总体积V (L) 油箱传热系数 k 油比热( 1.7~2.1 KJ/(kg*K) 环境温度T0 (K) 设定油温 T (K) 油箱散热面积(m2) 系统温升(冷却时间) t(min) 系统热平衡温度(K) 风冷计算 风量(m3 / h) 散热温差t (K) 散热功率 (Kw) 水冷计算 冷却水量(m3 / h) 进出水温差t (K) 散热功率 (Kw) 温度换算 摄氏度 华氏度
2000 8 1.9 30 55 16 122.47 115.94
系统发热功率(Kw) 加热功率(Kw) 冷却功率(Kw) 油质量(kg) 油箱散热面积(m2)≈ 油箱冷却功率(Kw) 油箱壁厚(mm) 油箱重量(Kg)≈
11 0 0 1440 10.57 3.20 6.5 770.63
4000 10 14.45
通风条件 差 良好 风冷冷却 循环水冷却
系数k 8~9 15 23 110~174
24 2 55.82
204 200
ห้องสมุดไป่ตู้——〉华氏度 ——〉摄氏度
399.20 93.33
kA t H T T0 1 e C m k A
当t →∞ 时,系统热平衡公式
液压系统设计计算公式
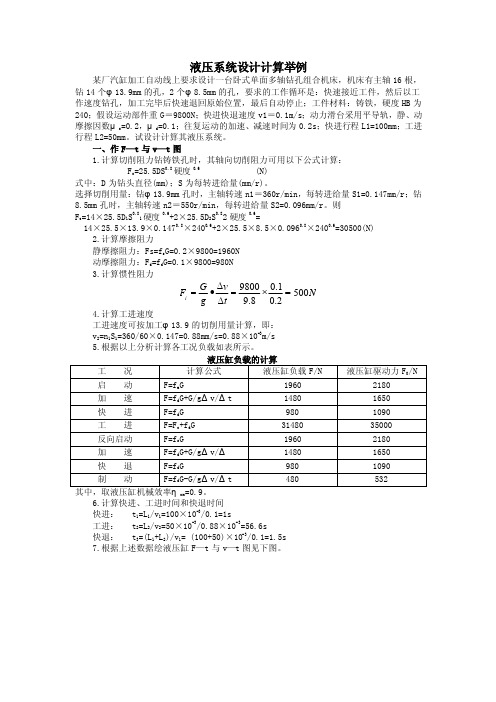
液压系统设计计算举例某厂汽缸加工自动线上要求设计一台卧式单面多轴钻孔组合机床,机床有主轴16根,钻14个φ13.9mm 的孔,2个φ8.5mm 的孔,要求的工作循环是:快速接近工件,然后以工 作速度钻孔,加工完毕后快速退回原始位置,最后自动停止;工件材料:铸铁,硬度HB 为240;假设运动部件重G =9800N ;快进快退速度v1=0.1m/s ;动力滑台采用平导轨,静、动摩擦因数μs =0.2,μd =0.1;往复运动的加速、减速时间为0.2s ;快进行程L1=100mm ;工进行程L2=50mm 。
试设计计算其液压系统。
一、作F —t 与v —t 图1.计算切削阻力钻铸铁孔时,其轴向切削阻力可用以下公式计算:F c =25.5DS 0.8硬度0.6(N)式中:D 为钻头直径(mm);S 为每转进给量(mm/r)。
选择切削用量:钻φ13.9mm 孔时,主轴转速n1=360r/min ,每转进给量S1=0.147mm/r ;钻8.5mm 孔时,主轴转速n2=550r/min ,每转进给量S2=0.096mm/r 。
则F c =14×25.5D 1S 0.81硬度0.6+2×25.5D 2S 0.82硬度0.6=14×25.5×13.9×0.1470.8×2400.6+2×25.5×8.5×0.0960.8×2400.6=30500(N) 2.计算摩擦阻力静摩擦阻力:Fs=f s G=0.2×9800=1960N 动摩擦阻力:F d =f d G=0.1×9800=980N 3.计算惯性阻力4.计算工进速度工进速度可按加工φ13.9的切削用量计算,即:v 2=n 1S 1=360/60×0.147=0.88mm/s=0.88×10-3m/s 5.根据以上分析计算各工况负载如表所示。
液压系统发热量的计算
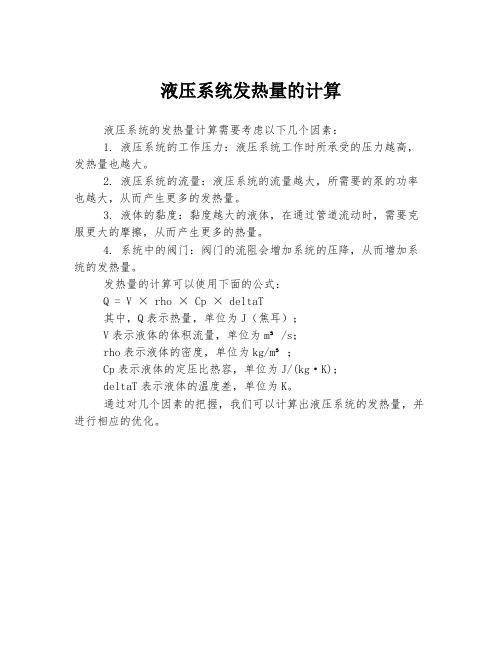
液压系统发热量的计算
液压系统的发热量计算需要考虑以下几个因素:
1. 液压系统的工作压力:液压系统工作时所承受的压力越高,发热量也越大。
2. 液压系统的流量:液压系统的流量越大,所需要的泵的功率也越大,从而产生更多的发热量。
3. 液体的黏度:黏度越大的液体,在通过管道流动时,需要克服更大的摩擦,从而产生更多的热量。
4. 系统中的阀门:阀门的流阻会增加系统的压降,从而增加系统的发热量。
发热量的计算可以使用下面的公式:
Q = V × rho × Cp × deltaT
其中,Q表示热量,单位为J(焦耳);
V表示液体的体积流量,单位为m³/s;
rho表示液体的密度,单位为kg/m³;
Cp表示液体的定压比热容,单位为J/(kg·K);
deltaT表示液体的温度差,单位为K。
通过对几个因素的把握,我们可以计算出液压系统的发热量,并进行相应的优化。
液压系统设计计算实例(共18张PPT)优秀
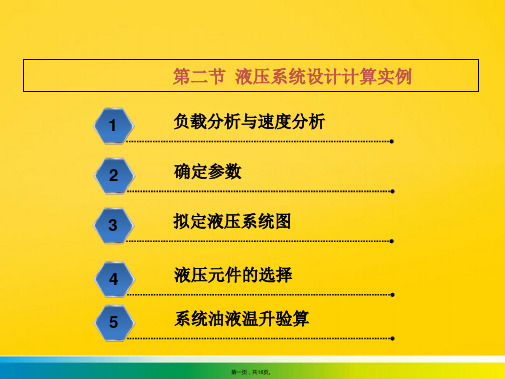
3)计算液压缸在工作循环各阶段的压力、流量和功率 值
差动时液压缸有杆腔压力大于无杆腔压力,取两腔间回路及阀的压 力损失为0.5MPa,则p2= p1+0.5MPa。计算结果见表9.5。
由教材中9-5表即可画出液压缸的工况图(略)。
第七页,共18页。
表9-5:液压缸工作循环各阶段压力、流量和功率值
工作循环 计算公式 量 输入功率
负载
P kW
快 启动加速
p1=F+A2(p2-p1) 3289
A1 -A2
q1=(A1 -A2)v1
p2= p1+0.5
进恒速
P= p1 q1
2178
回油背进油压力 输入流
p1MPa
q110-3 m3/s
-
0.88
0.50
0.44
p1= F+ A2p2
20mm/min~120mm/min按上述分析可绘制出负载循环图和速度循环图(略)
。
第三页,共18页。
第四页,共18页。
2.确定参数
1)初选液压缸的工作压力
由最大负载值查教材中表9-3,取液压缸工作压力为4MPa。
2)计算液压缸结构参数
为使液压缸快进与快退速度相等,选用单出杆活塞缸差动连接的方式实现快进
采用平(导轨4,)其换摩擦向系回数f=路0. :为了换向平稳,选用电液换向阀。为便于实现液压缸中位停止和
0大0流31量泵的输差入动功0率.连经接计算,为采70.用三位五通阀。
(5)压力控制回路:系统在工作状态时高压小流量泵的工作压力由溢 流阀调整,同时用外控顺序阀实现低压大流量泵卸荷。
第九页,共18页。
(3 据此选用Y112M—6—B5立式电动机,其额定功率为2.
液压计算公式单位换算方法
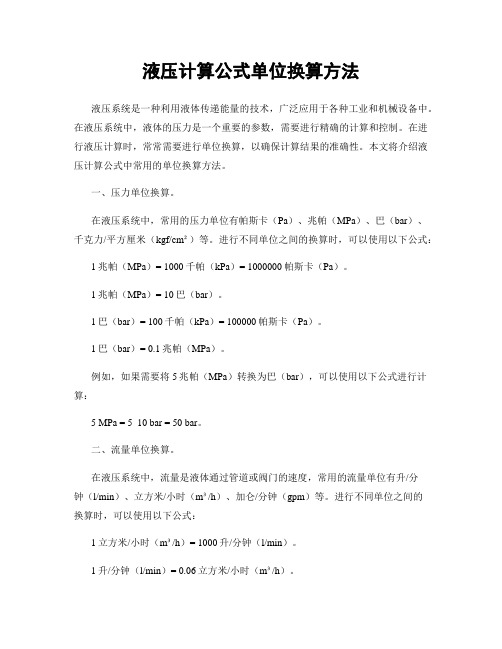
液压计算公式单位换算方法液压系统是一种利用液体传递能量的技术,广泛应用于各种工业和机械设备中。
在液压系统中,液体的压力是一个重要的参数,需要进行精确的计算和控制。
在进行液压计算时,常常需要进行单位换算,以确保计算结果的准确性。
本文将介绍液压计算公式中常用的单位换算方法。
一、压力单位换算。
在液压系统中,常用的压力单位有帕斯卡(Pa)、兆帕(MPa)、巴(bar)、千克力/平方厘米(kgf/cm²)等。
进行不同单位之间的换算时,可以使用以下公式:1兆帕(MPa)= 1000千帕(kPa)= 1000000帕斯卡(Pa)。
1兆帕(MPa)= 10巴(bar)。
1巴(bar)= 100千帕(kPa)= 100000帕斯卡(Pa)。
1巴(bar)= 0.1兆帕(MPa)。
例如,如果需要将5兆帕(MPa)转换为巴(bar),可以使用以下公式进行计算:5 MPa = 5 10 bar = 50 bar。
二、流量单位换算。
在液压系统中,流量是液体通过管道或阀门的速度,常用的流量单位有升/分钟(l/min)、立方米/小时(m³/h)、加仑/分钟(gpm)等。
进行不同单位之间的换算时,可以使用以下公式:1立方米/小时(m³/h)= 1000升/分钟(l/min)。
1升/分钟(l/min)= 0.06立方米/小时(m³/h)。
1加仑/分钟(gpm)= 3.785升/分钟(l/min)。
例如,如果需要将200升/分钟(l/min)转换为立方米/小时(m³/h),可以使用以下公式进行计算:200 l/min = 200 0.06 m³/h = 12 m³/h。
三、功率单位换算。
在液压系统中,功率是指单位时间内所做的功,常用的功率单位有千瓦(kW)、马力(hp)等。
进行不同单位之间的换算时,可以使用以下公式:1千瓦(kW)= 1.36马力(hp)。
1马力(hp)= 0.74千瓦(kW)。
液压系统设计计算
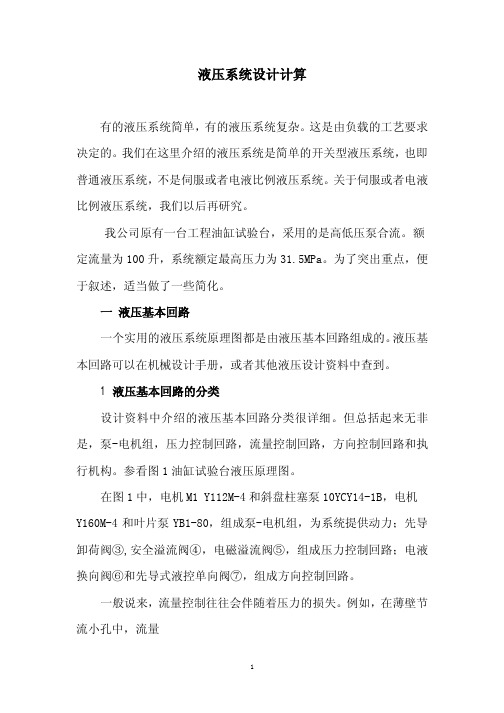
液压系统设计计算有的液压系统简单,有的液压系统复杂。
这是由负载的工艺要求决定的。
我们在这里介绍的液压系统是简单的开关型液压系统,也即普通液压系统,不是伺服或者电液比例液压系统。
关于伺服或者电液比例液压系统,我们以后再研究。
我公司原有一台工程油缸试验台,采用的是高低压泵合流。
额定流量为100升,系统额定最高压力为31.5MPa。
为了突出重点,便于叙述,适当做了一些简化。
一液压基本回路一个实用的液压系统原理图都是由液压基本回路组成的。
液压基本回路可以在机械设计手册,或者其他液压设计资料中查到。
1 液压基本回路的分类设计资料中介绍的液压基本回路分类很详细。
但总括起来无非是,泵-电机组,压力控制回路,流量控制回路,方向控制回路和执行机构。
参看图1油缸试验台液压原理图。
在图1中,电机M1 Y112M-4和斜盘柱塞泵10YCY14-1B,电机Y160M-4和叶片泵YB1-80,组成泵-电机组,为系统提供动力;先导卸荷阀③,安全溢流阀④,电磁溢流阀⑤,组成压力控制回路;电液换向阀⑥和先导式液控单向阀⑦,组成方向控制回路。
一般说来,流量控制往往会伴随着压力的损失。
例如,在薄壁节流小孔中,流量d Q C A = (1) 此公式的使用条件为0.5l d≤。
式中Q —经过薄壁小孔的流量,3/m s ;d C —薄壁小孔流量系数,对于紊流,0.600.61d C = ; 0A —孔口面积,2m ; ρ—流体的密度,3/kg m ; p ∆—压力差,12p p p ∆=−,Pa ;d —小孔的直径,m ; l —小孔的长度,m 。
这种压力能损失往往转化为热能,使液压系统升温。
在理论上,变量泵不会因为流量或压力的变量产生能量损失。
2 液压基本回路的联结液压基本回路,特别是液压元件,在液压原理图中的联结,要么是并联,要么是串联。
二 液压系统原理图1 液压系统原理图应该包括的的基本内容一个符合要求的液压原理图除了表示系统外,还应该包括两个基本内容:液压元件明细表和电磁铁动作顺序表。
液压油量计算
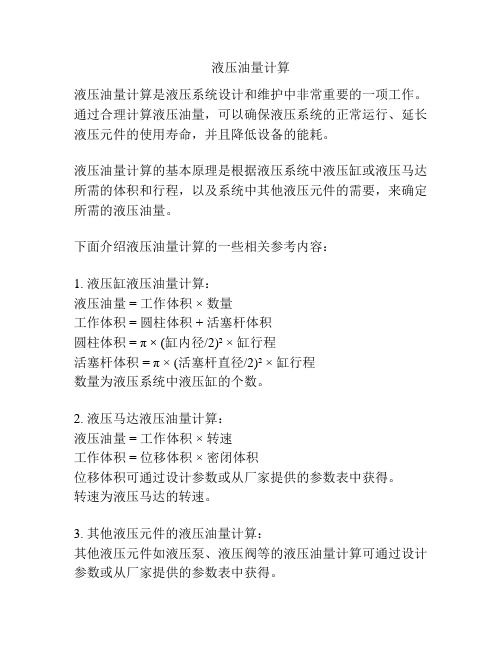
液压油量计算液压油量计算是液压系统设计和维护中非常重要的一项工作。
通过合理计算液压油量,可以确保液压系统的正常运行、延长液压元件的使用寿命,并且降低设备的能耗。
液压油量计算的基本原理是根据液压系统中液压缸或液压马达所需的体积和行程,以及系统中其他液压元件的需要,来确定所需的液压油量。
下面介绍液压油量计算的一些相关参考内容:1. 液压缸液压油量计算:液压油量 = 工作体积 ×数量工作体积 = 圆柱体积 + 活塞杆体积圆柱体积= π × (缸内径/2)² ×缸行程活塞杆体积= π × (活塞杆直径/2)² ×缸行程数量为液压系统中液压缸的个数。
2. 液压马达液压油量计算:液压油量 = 工作体积 ×转速工作体积 = 位移体积 ×密闭体积位移体积可通过设计参数或从厂家提供的参数表中获得。
转速为液压马达的转速。
3. 其他液压元件的液压油量计算:其他液压元件如液压泵、液压阀等的液压油量计算可通过设计参数或从厂家提供的参数表中获得。
4. 液压系统总油量计算:液压系统总油量 = 所有液压元件需求的液压油量之和通过以上计算方法得到各个液压元件需要的液压油量,将其累加得到液压系统的总油量。
在实际液压系统设计中,还需要考虑一些额外因素,例如润滑油的损耗和密封元件容纳的余量等。
这些因素可以根据具体的液压系统要求进行调整和计算。
总之,液压油量计算需要综合考虑液压系统中各个液压元件的需求,通过合理计算液压油量,可以确保液压系统的正常运行、延长液压元件的使用寿命,并且降低设备的能耗。
以上所提到的液压油量计算方法可以作为液压系统设计和维护的参考内容。
液压系统设计计算举例

液压系统设计计算举例液压系统设计计算举例XS-ZY-500注塑机液压系统设计计算⼆、XS-ZY-500注塑机成型设计技术参数公称注射量(L) 0.5螺杆直径(mm) 63螺杆⾏程(mm) 200最⼤注射压⼒(MPa) 110注射容量(理论值)(cm) 665预塑电机(KW) 7.5塑化容量(N/h) 450螺杆转速(r/min) 20—80 料筒加热功率(KW) 14注射座⾏程(mm) 280合模⼒(KN) 3500启模⼒(KN) 135顶出⼒(KN) 30最⼤注射⾯积(cm) 1000模板最⼤开距(mm) 950拉杆间距(mm) 540x440 模具最⼤厚度(mm) 450模具最⼩厚度(mm) 300注射总⼒(KN) 345注射座最⼤推⼒(KN) 73螺杆驱动功率PM(KW) 5KW各油缸运动数值如下:快速合模速度(m/s) 0.12慢速合模速度(m/s) 0.024 快速启模速度(m/s) 0.13慢速启模速度(m/s) 0.028 快速注射速度(m/s) 0.07注射座前移速度(m/s) 0.06注射座后退速度(m/s) 0.08顶出速度(m/s) 0.04三、⼯况分析xxxx塑料注射成型机械液压系统的特点是在整个动作循环过程中,系统负载和速度变化均较⼤,在进⾏⼯况分析时必须加以考虑:(⼀)合模油缸负载xxxx闭模动作的⼯况特点是:模具闭合过程中的负载是轻载,速度有慢—快—慢的变化;模具闭合后的负载为重载,速度为零。
1. 根据合模⼒确定合模缸推⼒:根据连杆受⼒分析可得出合模油缸推⼒为:式中:N1z——合模油缸为保证模具锁紧所需的推⼒,N.ssssss N合————模具锁紧所需的合模⼒,N.ssssss l1/l——有关长度⽐,⼀般取其值为0.7.为保证模具锁紧⼒(3500KN)所需的油缸推⼒为: N1z=223KN2. 空⾏程时油缸推⼒:aaaa空⾏程时油缸推⼒P1q只须克服摩擦⼒的要求,根据设计经验得:N1q=0.14N1z z, 故s N1q=31.22KN3. 启模时油缸的推⼒:ssss启模时油缸的推⼒需满⾜启模⼒和克服油缸摩擦⼒的要求。
液压系统设计计算举例

(9.20)
设计计算
步骤和内容
6
液压系统的发热功率
(3) 溢流阀的损失功率
k
Py
pYi qYi
式中
i 1
pYi ——各溢流阀的调整压力;
qYi ——各溢流阀的溢流量;
k——溢流阀数量。
(4) 节流功率损失
(9.21)
式中
k
Pj pji qji i 1
p ji ——各流量阀进出口压差;
q ji ——通过各流量阀的流量;
表9-5 液压缸在各工作阶段的负载值
工况 起动
负载组成 F= Ffs
负载值F/N 1962
推力 /N
F
2180 m
加速
F = Ffd + Fm 1564
1500
快进 工进 快退
F =Ffd F =Ffd + Ft F =Ffd
981 31449 981
1090 34943 1090
设计计算
设计实例
22
1 液压传动系统的设计计算步骤和内容
• 液压系统设计步骤如下: • (1) 明确液压系统的设计要求及工况分析; • (2) 主要参数的确定; • (3) 拟定液压系统原理图,进行系统方案论证; • (4) 设计、计算、选择液压元件; • (5) 对液压系统主要性能进行验算; • (6) 设计液压装置,编制液压系统技术文件。
设计计算
设计实例
19
负载分析
1. 工作负载
由切削原理可知,高速钢钻头钻铸铁孔时的轴向切削力Ft与钻头直径D(mm)、每转进给量s(mm/r) 和铸件硬度HB之间的经验计算式为
Ft 25.5Ds0.8 (HB)0.6 (9.27)
根据组合机床加工的特点,钻孔时的主轴转速n和每转进给量s
液压系统计算公式
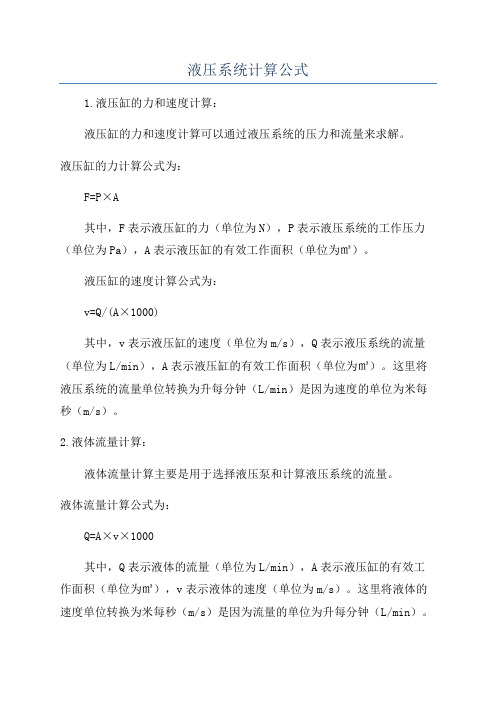
液压系统计算公式1.液压缸的力和速度计算:液压缸的力和速度计算可以通过液压系统的压力和流量来求解。
液压缸的力计算公式为:F=P×A其中,F表示液压缸的力(单位为N),P表示液压系统的工作压力(单位为Pa),A表示液压缸的有效工作面积(单位为㎡)。
液压缸的速度计算公式为:v=Q/(A×1000)其中,v表示液压缸的速度(单位为m/s),Q表示液压系统的流量(单位为L/min),A表示液压缸的有效工作面积(单位为㎡)。
这里将液压系统的流量单位转换为升每分钟(L/min)是因为速度的单位为米每秒(m/s)。
2.液体流量计算:液体流量计算主要是用于选择液压泵和计算液压系统的流量。
液体流量计算公式为:Q=A×v×1000其中,Q表示液体的流量(单位为L/min),A表示液压缸的有效工作面积(单位为㎡),v表示液体的速度(单位为m/s)。
这里将液体的速度单位转换为米每秒(m/s)是因为流量的单位为升每分钟(L/min)。
3.泵和马达的工作参数计算:液压系统中的泵和马达是系统的核心部件,其工作参数计算涉及到流量、压力、功率等方面。
泵的工作参数计算公式为:Pump Power (KW) = (Flow Rate (L/min) × Pressure (Bar)) ÷ 600其中,Pump Power表示泵的功率(单位为千瓦,KW),Flow Rate表示泵的流量(单位为L/min),Pressure表示泵的压力(单位为巴,Bar)。
马达的工作参数计算公式为:Motor Power (KW) = (Torque (Nm) × Speed (RPM)) ÷ 9550其中,Motor Power表示马达的功率(单位为千瓦,KW),Torque表示马达的扭矩(单位为牛顿米,Nm),Speed表示马达的转速(单位为转每分钟,RPM)。
4.液体管道的压力损失计算:液体管道的压力损失计算主要用于确定液体输送过程中的管道直径和管道长度。
液压系统设计及计算

45MPa)
兆帕 兆帕 兆帕 毫米
当P≤7MPa时,n=8;当P≤17.5MPa时,n=6;当P>17.5MPa时,n=4; Mpa 钢管451Mpa; Mpa 铜管210Mpa; σ p =σ b /n Mpa δ ≧P工da/(2σ p ) mm
***********特别说明1、本表上面保护工作表的制作方法为:点击顶排---审阅---允许用户编辑区域---新区域对话框中--引用单元格下的=号后点击---按back 退格键清除=号前的文字---ctrl键不松手的同时,光标选中其上可修改的蓝 色单元格---点击新区域对话框中的:确定---点新出的:允许用户编辑区域对话框中的:保护工作表按钮---保持电脑默 认的勾选的顶上1、2两格(选定锁定单元格---选定未锁定的单元格)---对话框中长空处:键入密码555等字样---新出确 认密码对话框中再次键入555等字样---点击:确定---OK。**********
液压系统设计计算
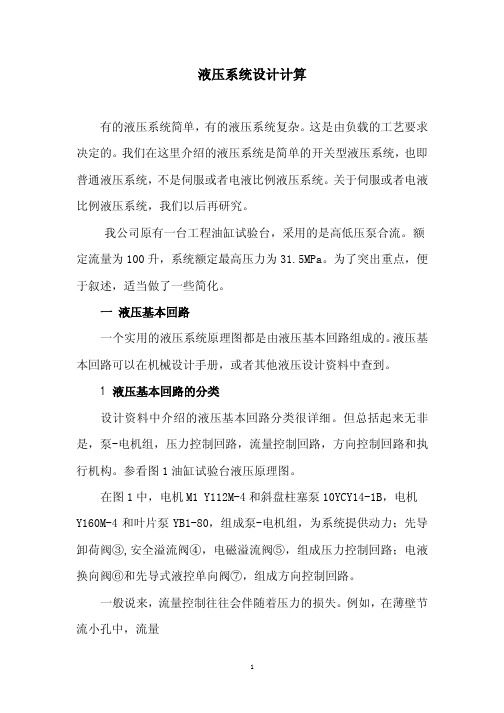
上述推荐值,有的偏小。例如,现在高压管路中最大流速已接近 15 米/秒。 清华大学俞新陆老师主编的《液压机》介绍了国内外几家插装阀 生产厂家生产的插装阀的额定流量,如表 5。 表 5 插装阀的额定流量
推荐额定流量 L/min 设计制造单位 16 济南铸锻所 上海 704 所 德国 REXROTRH 德 国 Sauer 100 100 160 60 25 250 200 450 160 32 400 400 650 250 40 630 700 1100 400 通 径 mm 50 1000 1000 2000 630 2700 1000 4500 2500 7500 11000 3500 63 1600 80 2500 100 4000 125
Getriebe 日本不二越 中国(普通阀) (φ18) 63 300 (φ24) 100 600 (φ32) 200 (φ38) 250 1200 (φ50) 500 1700 (φ63) 800 2300 (φ80) 1250 3500
按公式(7) 可以计算出表 5 中各厂家产品阀口处的流速
v= 4Q 2Q = 10-4 2 1000 × 60π d 3π d 2
8
泵-机组的设计很重要,它是能源,Байду номын сангаас关泵的寿命,噪音水平。
图 6 泵-电机连接法兰
图 7 组合式泵-电机组 六 确定管径 一般说来,选取泵之后,管径也就确定了。这是因为,一般都是 根据泵的进出油口口径来确定管径的。 华南工学院杨宝光老师主编的《锻压机械液压传动》 ,推荐传动
9
系统中各种油路允许流速值如下: 高压管路 低压管路 排油管路 吸油管路 控制油路 充液油路 3~6 米/秒; ≤ 3 米/秒; ≤ 3 米/秒; 0.5~1 米/秒; 2~3 米/秒; 1~2 米/秒。
第八章 液压系统的设计计算

8液压系统的设计计算习题
1、设计一台卧式单面多轴钻孔组合机床液压系统,要求完成工件的定位与加紧,所需夹紧力不得超过3000N。
机床快进、快退的速度约为4.5m/min,工进速度可在20-100mm/min范围内无极调速,快进行程为150mm,工进行程为40mm,最大切削力为30000N,运动部件总重量为11000N,加速(减速)时间为0.1s,采用平导轨,静摩擦系数为0.2,动摩擦系数为0.1。
2、试设计卧式双面铣削组合机床的液压系统。
机床的加工对象为铸铁变速箱箱体,动作顺序为夹紧缸夹紧→工作台快速趋近工件→工作台进给→工作台快退→夹紧缸松开→原位停止。
工作台移动部件的总重力为4000N,加、减速时间为0.2s,采用平导轨,静、动摩擦因数μs=0.2,μd=0.1。
夹紧缸行程为30mm,夹紧力为800N,工作台快进行程为100mm,快进速度为3.5m/min,工进行程为200mm,工进速度为80~300mm/min,轴向工作负载为12000N,快退速度为6m/min。
要求工作台运动平稳,夹紧力可调并保压。
液压系统的设计与计算

下午2时22分
18
五、验算液压系统性能
液压系统初步确定后就需对系统的有关性能加以验算,以检测 系统的设计质量,并对液压系统进行完善和改进。根据液压系 统的不同,需要验算的项目也有所不同,但一般的液压系统都 要进行回路压力损失和发热温升的验算。
1. 系统压力损失的验算
p pl p pv
液压系统的压力损失包括沿程、局部损失和阀的局部损失。
液压与液力传动
第九章 液压系统的设计与计算
液压系统的设计与计算是液压机械总设计的一部分, 是对前面各章内容的综合运用。总设计过程为: (1)根据整机的用途、特点和性能,明确对液压系统的 设计任务。 (2)对工况进行分析,确定液压系统的主要参数; (3)拟定出合理的液压系统原理图; (4)计算和选择液压元件的规格 (5)演算液压系统的性能 (6)绘制工作图、编写技术文件。
要求验算液压缸尺寸 即
A qmin
vmin
• 在D和d确定之后,可求得液压缸所需流量为:
q1=vmaxA
下午2时22分
13
3 执行元件工况图
工况图是指液压执行元件结构参数确定之后,根 据主机工作循环,算出不同阶段中的实际工作压力、 流量和功率随时间变化图,如图所示。
工况图反映了液压系统在整个工作循环中,三个参 数的随时间变换情况。
动摩擦因数0.1, 液压执行元件为液压元件。
设计液压缸的面积和确定液压系统控制图
下午2时22分
21
一、负载分析
(1)切削力:
Fe 22.5DS0.8(HB)0.6
式中,Fe为钻削力,N; D为钻头直径,mm;S为每 转进给量,mm; HB为工件硬度。
对于直径为13.9mm的孔,转速n1=360r/min, S1=0.147mm/r; 对于直径为8.5mm的孔,转速n2= 550r/min, S2=0.096mm/r; 带入上式,可得:
液压计算公式
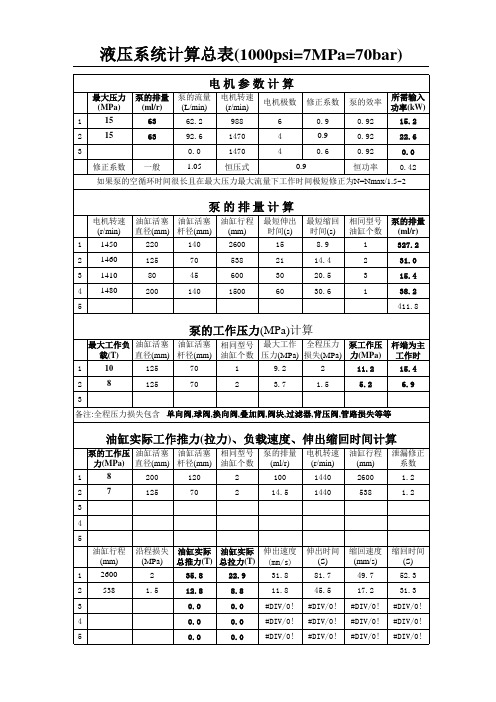
油缸实际工作推力(拉力)、负载速度、伸出缩回时间计算
泵的工作 油缸活塞 油缸活塞 压力(MPa) 直径(mm) 杆径(mm) 1 2 3 4 5 油缸行程 (mm) 1 2 3 4 5 2600 538 沿程损失 油缸实际 油缸实际 伸出速度 (MPa) 总推力(T) 总拉力(T) (mm/s) 2 1.5 35.8 12.8 0.0 0.0 0.0 22.9 8.8 0.0 0.0 0.0 31.8 11.8 #DIV/0! #DIV/0! #DIV/0! 伸出时间 (S) 81.7 45.5 #DIV/0! #DIV/0! #DIV/0! 缩回速度 (mm/s) 49.7 17.2 #DIV/0! #DIV/0! #DIV/0! 缩回时间 (S) 52.3 31.3 #DIV/0! #DIV/0! #DIV/0! 8 7 200 125 120 70 相同型号 油缸个数 2 2 泵的排量 (ml/r) 100 14.5 电机转速 (r/min) 1440 1440 油缸行程 (mm) 2600 538 泄漏修正 系数 1.2 1.2
泵理论流 油缸快出 最小工作 最大工作 充气压力 量(L/min) 时间(s) 压力(Mpa) 压力(MPa) P0(Mpa) 320 20 15 1 7.6 10 12.7 16.7 6.1 8.0
Pmax≤3Pmin,对压力要求稳定时,Pmax=Pmin/(0.6~0.85);Pmin ≥系统最低工作压力+沿程损失; Pmax≤Pp.充气压力P0: 0.48Pmax≤P0≤0.9Pmin,一般取P0=(0.8~0.85)Pmin 冲击载荷或坐热膨胀补充时,P0=Pmin;做吸收脉动降低噪声时,P0=0.3*(Pmin+Pmax) 修正系数:整体压力越低或Pmax/Pmin 越大,修正系数越小,一般取1.2~1.7
液压常用计算公式
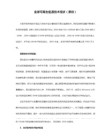
q:泵或马达的幾何排量(cc/rev) n = Q / q ×1000
Q:流量 (l / min)
泵或馬達扭矩(N.m)
T = q × p / 20π
液壓所需功率 (kw)
液压常用计算公式
项 目
公 式
符 号 意 义
液壓缸面積(cm2)
A =πD2/4
D:液壓缸有效活塞直徑 (cm)
液壓缸速度 (m/min)
V = Q / A
Q:流量 (l / min)
液壓缸需要的流量(l/min)
d:管的內徑(cm)
--------------------------------------------------------------------------------
非标液压、机电、试验、工控设备开发研制。
液压缸无杆腔面积A=3.14*40*40/10000000 (平方米)=0.005024(平方米)
Q=V×A/10=A×S/10t
V:速度 (m/min)
S:液壓缸行程 (m)
t:時間(min)
液壓缸出力(kgf)
F = p × A
F = (p × A)-(p×A)
(有背壓存在時)
p:壓力(kgf /cm2)
泵或馬達流量(l/min)
泵的理论流量Q=排量*转速=32*1430/1000000 (立方米/分)=0.04576(立方米/分)
液压缸运动速度约为V=0.95*Q/A=0.104 m/min
所用时间约为T=缸的行程/速度=L/V=0.8/0.104=8 (秒)
上面的计算是在系统正常工作状态时计算的,如果溢流阀的安全压力调得较低,负载过大,液压缸的速度就没有上面计算的大,时间T就会增大.
- 1、下载文档前请自行甄别文档内容的完整性,平台不提供额外的编辑、内容补充、找答案等附加服务。
- 2、"仅部分预览"的文档,不可在线预览部分如存在完整性等问题,可反馈申请退款(可完整预览的文档不适用该条件!)。
- 3、如文档侵犯您的权益,请联系客服反馈,我们会尽快为您处理(人工客服工作时间:9:00-18:30)。
管子承受的压力 安全系数S
管内流速
管路内径 d mm 90
说明:对于压力管,当压力高、流量大管路短时取大值 P=2.5~14MPa时,取v=3~4m/s,当p>14MPa时,取v
油箱散热系数K(液压工程师手册) 散热系数 K W/(m2*℃) 15
油箱散热面积
A=PL/(K*Δ t)
m2
0.01
油箱散热情况 整体式,通风差 单体式,通风较好 上置式,通风好 强制通风式
吸油管 压油管 0.5~1.5 2~6 通径:6/8/10/13/16/19/22/25/32/38/45/51 :3/4/5;6/8/10;12/15/20/25/32/40/50/65/80/100
P<7MPA 8
P<17.5MPA 6
P>17.5MPA 4
对于压力管,当压力高、流量大管路短时取大值,反之取小值;当系统压力p<2.5MPa时,取v=2m/s,当 ~14MPa时,取v=3~4m/s,当p>14MPa时,取v≤5m/s;对于行走机械,当P>21MPa时,取v≤5~6m/s
散热系数K(液压工程师手册) 散热系数K 11~28 29~57 58~74 142~341
散热系数K(液压元件与系统)
散热系数K 8~10 14~20 20~25 110~175
种类
散热系数K
列管式 波纹板 风冷 机械制冷
350~580 230~815 116~175 冷却效果最好
润滑系统 25~30
吸油管路内径 d=4.61*(Q/0.8)^0.5
mm
102.9
管子内径 d mm 60 壁厚 Δ = P*d*S/(2*σ b-P*S) mm 6.04 流速 4Q/(π d^2) m/s 1.05
流速 v(m/s) 高压胶管通径:6/8/10/13/16/19/22/25/32/38/45/51 钢管通径:3/4/5;6/8/10;12/15/20/25/32/40/50/65
mm
46.1
20#钢抗拉强度 σb Mpa 410 液面高 C=V*10^6/(A*B) mm 0.47
65.2
承受压力 P Mpa 25
管道壁厚
安全系数 S 3
液面高度差计算
无杆腔体积 v L 0.50
油箱散热面积
允许温升 Δt ℃ 10
输出功率 P kw 10 总效率 η 0.87 系统损失功率 PL=P*0.15 kw 1.5 系统损失功率 PL=P*(1-η ) Kw 3.9
容积计算
经验系数 a 6 流量 Q L/min 400.00 宽 B mm 900 容积 V=Q*a L 2400.00 高 C mm 690
体积计算
长 A mm 1200
管路内径
系统流量 Q L/min 400.00 压力管路内径 d=4.61*(Q/4)^0.5
mm
回油管路内径 d=4.61*(Q/2)^0.5
冷却水量
油的流量 Q L/min 232 水的流量
Qs=C*ρ *Δ T/(Cs*ρ s*Δ t)
m3/h 8.41
风冷却器散热面积
系统发热量 PL=P*(1-η ) kw 4.4 液压油温度 T1+T2 ℃ 40
系统压力 经验系数a
注:油箱公称容量大于本系列10000L时,应按GB/T 321 体积 V=A*B*C/10^6 L 745.2 有效容积 V1=V*0.85 L 633.42 油箱空气容量 10%~15%
环境温度 t2
℃ 25
油液最高允许温度 t1
℃ 40
油箱散热系数K(液压元件与系统)
通风条件 差 良好 风扇却 循环水冷却
散热系数
散热面积
种类
k W/(m2*℃) 350 冷却介质进口温度 t1 ℃ 30 油进出口温度差 Δ T=T1-T2 ℃ 15 水进出口温度差 Δ t=t2-t1 ℃ 10 散热系数 k W/(m2*℃) 116 散热面积 A≈PC/(T*k) m2 3.79
PT kw 0 液压油出温度 T2 ℃ 40 油的密度 ρ kg/m3 900 水的密度 ρ s kg/m3 1000 油箱散热量 PT kw 0 冷却介质温度 t1PT kw 30 平均温度差 T=[(T1+T2)-(t1+t2)]/2 ℃ 12.5 油的比热容 C kJ/(kg*℃) 1.88 水的比热容 Cs kJ/(kg*℃) 4.2 冷却器热交换量 PC=PL-PT kw 4.4 平均温度差 T=[(T1+T2)-(t1+t2)]/2 ℃ 10
油箱自然通风最小有效容积
输出功率 P kw 30 散热系数 K W/(m2*℃) 8
油液温升 Δ t=t1-t2 ℃
15
油箱散热容积
V≈10^3*{[PL/(0.065*K*(t1-t2))]^3}^0.5
m3
353.55
水冷却器散热面积
系统发热量 油箱散热量 冷却器热交换量
PL=P*(1-η ) kw 30 液压油进口温度 T1 ℃ 55
A≈PC/(T*k) m2 6.86 冷却介质出口温度 t2 ℃ 40
水冷却式 风冷却式 制冷
行走机械 1~2
p≤2.5MPa 2~4
2.5MPa<p≤6.3MPa 5~7
p>6.3MPa 6~12
公称容量大于本系列10000L时,应按GB/T 321—2005《优先数和优先数系》中R10数系选择。 液压泵站油箱公称容量 系列(JB/T 7938— 2010) /L 2.5、4.0、6.3、10 16、25、40、63、100 160、250、315、400、500、630、800、1000 1250、1600、2000、2500、3150、4000、5000、6300、8000、 10000 回油管 1.5~2.5 短管及局部收缩处 ≤10