金属工艺复习全解
金属工艺学复习资料

金属工艺学复习资料第一章1.使用性能:材料在使用过程中所表现的性能(力学性能,物理性能,化学性能)2.工艺性能:材料在加工过程中表现的性能(铸造,锻压,焊接,热处理,材料性能)3.拉伸过程的4个阶段:I.弹性形变II.屈服III.均匀塑性变形阶段IV.颈缩4.δs:屈服强度δ0.2:条件屈服强度δb:抗拉强度A k:冲击韧性HB:布氏硬度HR:洛氏硬度HV:维式硬度Ψ:收缩率δ:伸长率5.韧脆转变温度:在某一温度范围内冲击韧性值急剧下降的现象。
6.疲劳极限:材料经过无数次应力循环而不发生疲劳断裂的最高应力。
用δ-1表示。
第二章1.常见纯金属的晶格类型:体心立方晶格:晶格常数a,原子数2,常见金属α-Fe,δ-Fe。
面心立方晶格:晶格常数a,原子数4,常见金属γ-Fe,Cu,Ag。
密排六方晶格:晶格常数:底面边长a和高c存在c/a=1.633,常见金属Mg,Zn,Be。
2.结晶:物质由液态转化为晶态的过程。
3.过冷度:理论结晶温度和实际结晶温度之差,过冷度大小与冷速有关。
冷速越大,过冷度越大,过冷是结晶的必要条件。
4.结晶的过程:晶核的形成----晶核长大,长成树枝晶。
5.晶粒大小对金属机械性能的影响:常温下,晶粒越细小,晶界面积越大,金属机械性能越好。
强度,硬度高,塑性韧性高。
6.细化晶粒的过程:控制过冷度----变质处理----振动搅拌----热处理7.同素异形体的转变:金属在固态下,随着温度的改变其晶体结构发生变化的现象。
912℃1394℃例:α-Fe------------γ-Fe-------------δ-Fe(体心)(面心)(体心)7.重结晶(二次结晶):同素异构的转变。
8.合金:由两种或两种材料以上(其中一种是金属)组成的具有金属特性的材料。
9.相:金属或结晶中凡是化学成分和晶体结构相同,并与其他部分有界面分开的均匀组成部分。
10.固溶强化:由于溶质原子融入溶剂晶格产生晶格畸变而造成材料硬度和强度升高,塑性和韧性没有明显降低。
金属工艺学复习资料

《金属工艺学》复习资料一、填空题1.机械设计时常用抗拉强度(σb)和屈服强度(σs或σ0.2)两种强度指标。
2.若退火亚共析钢试样中先共析铁素体占41.6%,珠光体58。
4%,则此钢的含碳量为约0。
46%。
3.屈强比是屈服强度与抗拉强度之比。
4。
一般工程结构用金属是多晶体,在各个方向上的性能相同,这就是实际金属的各向同性现象。
5.实际金属存在点缺陷、线缺陷和面缺陷三种缺陷。
实际晶体的强度比理想晶体的强度低(高,低)得多。
6。
根据组成合金的各组元之间的相互作用不同,合金的结构可分为两大类:固溶体和金属化合物。
固溶体的晶格结构同溶剂,其强度硬度比纯金属的高。
7。
共析钢加热至Ac1时将发生珠光体向奥氏体的转变,其形成过程包括四个阶段。
8。
把两个45钢的退火态小试样分别加热到Ac1~Ac3之间和Ac3以上温度水冷淬火,所得到的组织前者为马氏体+铁素体+残余奥氏体,后者为马氏体+残余奥氏体。
二、判断改错题( ×)1。
随奥氏体中碳含量的增高,马氏体转变后,其中片状马氏体减少,板条状马氏体增多。
(×)2.回火屈氏体、回火索氏体和过冷奥氏体分解时形成的屈氏体、索氏体,只是形成过程不同,但组织形态和性能则是相同的。
(×)3。
退火工件常用HRC标出其硬度,淬火工件常用HBS标出其硬度。
(√)4.马氏体是碳在α-Fe中所形成的过饱和固溶体;当发生奥氏体向马氏体的转变时,体积发生膨胀。
(×)5.表面淬火既能改变工件表面的化学成分,也能改善其心部组织与性能。
( √ )6。
化学热处理既能改变工件表面的化学成分,也能改善其心部组织与性能。
(√ )7.高碳钢淬火时,将获得高硬度的马氏体,但由于奥氏体向马氏体转变的终止温度在0℃以下,故钢淬火后的组织中保留有少量的残余奥氏体.(×)8。
为了消除加工硬化便于进一步加工,常对冷加工后的金属进行完全退火。
(× )9。
片状珠光体的机械性能主要决定于珠光体的含碳量。
金属工艺复习资料

锻造1、金属塑性变形的实质金属塑性变形的实质是晶体内部产生滑移的结果。
单晶体内的滑移变形。
在切向应力作用下,晶体的一部分与另一部分沿着一定的晶面产生相对滑移,从而造成晶体的塑性变形。
当外力继续作用或增大时,晶体还将在另外的滑移面上发生滑移,使变形继续进行,因而得到一定的变形量。
2、内部组织的变化①晶粒沿最大变形的方向伸长:(形成纤维组织)②晶粒破碎,位错密度增加,产生加工硬化③产生内应力3、加工硬化的概念及其原因在塑性变形过程中,随着金属内部组织的变化,金属的力学性能也将产生明显的变化,即随着变形程度的增加,金属的强度、硬度增加,而塑性、韧性下降,这一现象即为加工硬化或形变强化。
关于加工硬化的原因,目前普遍认为与位错的交互作用有关。
随着塑性变形的进行,位错密度不断增加,因此位错在运动时的相互交割加剧,产生固定割阶、位错缠结等障碍,使位错运动的阻力增大,引起变形抗力的增加,因此就提高了金属的强度。
4、可锻性好差的判断金属的可锻性是衡量材料在经受压力加工时获得优质制品难易程度的工艺性能。
可锻性常用金属的塑性和变形抗力来综合衡量。
塑性越好,变形抗力越小,则金属的可锻性好。
反之则差。
金属的塑性用金属的断面收缩率ψ、伸长率δ等来表示。
变形抗力系指在压力加工过程中变形金属作用于施压工具表面单位面积上的压力。
变形抗力越小,则变形中所消耗的能量也越少。
金属的可锻性取决于金属的本质和加工条件。
5、锻造温度提高金属变形时的温度,是改善金属可锻性的有效措施。
金属在加热中,随温度的升高、金属原子的运动能力增强,很容易进行滑移,因而塑性提高,变形抗力降低,可锻性明显改善,更加适宜进行压力加工。
但温度过高,对钢而言,必将产生过热、过烧、脱碳和严重氧化等缺陷,甚至使锻件报废,所以应该严格控制锻造温度。
锻造温度范围系指始锻温度和终锻温度间的温度区间。
锻造温度范围的确定以合金状态图为依据。
碳钢的锻造温度范围,其始锻温度比AE线低200℃左右,终锻温度为800℃左右。
金属工艺复习资料

1影响液态合金充型的因素?(1)合金的流动性合金的流动性越好,充型能力愈强,愈便于浇铸出轮廓清晰薄而复杂的铸件。
(2)浇铸条件浇注温度浇注温度对合金充型能力有着决定性影响。
浇注温度愈高,合金的粘度下降,且因过热度高,合金在铸型中保持流动性时间长,故充型能力强反之充型能力差。
充型压力砂型铸造时,提高浇道高度使液态合金压力加大,充型能力可改善。
(3)铸件型填充条件铸型材料、铸型温度、铸型中的气体。
①铸型材料:导热性能越好,充型能力越差。
②铸型温度:铸型温度越高,充型能力越好。
③铸型中的气体:铸型排气能力越差,就越阻碍充型。
(4)铸件结构:铸件壁厚过薄,水平面过大,充型困难2缩孔、缩松产生的根本原因?形成过程?如何防止?缩孔产生的原因:纯金属共晶成分和凝固温度范围小的合金浇注后在行腔内是由表及里的逐层凝固。
在凝固过程中如得不到金属液的补充在铸件最后凝固的地发就回沉声缩孔。
形成过程:课本P42页倒数第一段缩松产生的原因:铸件最后凝注收缩未能得到补充,或者结晶温度范围宽的合金呈糊状凝固,凝固区域较宽,液固两相共存,树枝晶发达,枝晶骨架,将合金夜分割开得液体也难以得到补充收缩所致。
形成过程课本P43消除缩孔缩松的方法:原则顺序凝固铸件让远离冒口的地方先凝固,靠近的地方次凝固,最后才是冒口本身凝固实现以厚补薄将缩孔移到冒口中去。
方法:合理布置内浇道及确定浇铸工艺。
合理应用冒口、冷铁和补贴等工艺。
3手工造型的方法:整模造型分模造型活块造型三厢造型刮板造型和挖沙造型4铸造起模斜度与结构圆角的作用如何应用?起模斜度:为了在造型和制芯时便起模,以免损坏砂型和型芯,在模样芯的起模方向上留有一定的斜度。
因为直角在连接处的内侧较易产生缩孔缩松和应力集中,同时一些合金由于形成与铸件表面垂直的柱状晶使转角处的力学性能下降较易产生裂纹,所以应用结构圆角在减轻这些缺陷的产生。
5铸型分型面选取的原则:(1)应保证模样能顺利从铸型中取出(2)应尽量减少分型面的数量(3)应尽量使分型面是一个平直的面(4)应时铸件的全部或大部分置入同一砂箱(5)应尽量使型芯和活块的数量减少如何根据铸件的形状和生产批量选取分型面课本P68-P696铸造工艺图:在零件图上用各种工艺符号及参数表示处铸造工艺方案的图形其中包括:浇注位置铸型分型面型芯加工余量浇注系统起模斜度冒口和冷铁的尺寸和布置等(分析P73-P74课后题)7铸件内应力产生的根本原因内应力:热应力铸件在凝固和冷却过程中,由于铸件的壁厚不均匀,导致不同部位不均衡的收缩而引起的应力。
金属工艺学知识点总结资料讲解

金属工艺学知识点总结资料讲解1.金属材料的分类和特性:-金属材料的分类:金属材料分为黑色金属和有色金属两大类。
黑色金属包括铁、钢和铸铁等,有色金属包括铜、铝、镁、锌、铅等。
-金属材料的特性:金属材料具有导电性、导热性、延展性、可塑性、机械性能好等特点,适用于各种加工工艺。
2.金属加工方法:-切削加工:包括车削、铣削、钻削、刨削等,通过切削废料的去除改变工件形状和尺寸。
-成形加工:包括锻造、拉伸、锤压、挤压等,通过对金属材料的塑性变形改变工件形状。
-组合加工:包括焊接、铆接、螺纹连接等,通过将多个部件组合在一起形成复杂的工件。
-热处理加工:包括淬火、回火、退火等,通过控制材料的结构和性能来改变其力学性能和使用性能。
3.金属成形工艺:-钣金工艺:包括剪切、冲裁、弯曲等,用于制造薄板金属构件。
-铸造工艺:包括砂铸、压铸、精密铸造等,通过将熔融金属注入模具中,得到所需形状的铸件。
-高温成形工艺:包括真空热压、粉末冶金等,通过在高温条件下对金属进行成形,得到复杂形状的工件。
-冷镦工艺:通过在室温下使用特殊的冷镦机械设备,将金属材料进行快速塑性变形,得到各种螺纹、螺栓等小尺寸工件。
4.金属热处理工艺:-淬火:通过将加热至临界温度的金属材料迅速冷却,使其得到高硬度和高强度。
-回火:在淬火后,将金属加热至适当温度,然后冷却,以减轻淬火后的脆性和应力。
-退火:将金属材料加热至一定温度,保持一段时间后缓慢冷却,以改善其组织和性能。
-焊后热处理:焊接后的金属材料会产生应力和变形,通过热处理可以消除这些问题,提高焊接接头的强度和耐腐蚀性。
5.金属表面处理工艺:-镀层:通过在金属表面镀上一层金属或非金属涂层,增加其耐腐蚀性、装饰性和机械性能。
-涂装:通过在金属表面涂上油漆、涂料等防护层,保护金属不受氧化、腐蚀等损害。
-喷砂:通过在金属表面喷射高压喷砂颗粒,清除污物和氧化层,改善表面质量和光泽度。
-抛光:通过机械或化学方法对金属表面进行抛光,使其光洁度达到要求,提高外观质量。
《金属工艺学》复习资料

金属工艺学各章知识点第7章铸造成形二、基本内容1、铸造成形工艺基础1)合金的流动性和充型能力:流动性好的合金,充型能力强,易获得形状完整、尺寸准确、轮廓清晰、壁薄和形状复杂的铸件。
灰铸铁流动性最好,硅黄铜、铝硅合金次之,铸钢最差。
2)合金的收缩:液态收缩和凝固收缩是铸件产生缩孔和缩松的主要原因,固态收缩是铸件产生内应力、变形和裂纹的的主要原因。
1、铸造成形方法1)砂型铸造:各种手工造型方法的特点和应用,见书中表7-1。
铸件常见的缺陷的特征及产生原因,见书中表7-22)特种铸造:熔模铸造的工艺过程:制母模→压型→制蜡模→制壳→焙烧→浇注→清理。
熔模铸造的特点:铸件的尺寸精度及表面质量高,减少切削、节约材料,适于铸熔点高、难切削加工材料。
3、铸件结构工艺性1)砂型铸造对铸件结构设计的要求:减少和简化分型面;外形力求简单对称;有结构斜度;有利于节省型芯及型芯的定位、固定、排气和清理。
2)合金铸造性能对铸件结构设计的要求:铸件壁厚要合理、壁厚应均匀、有铸造圆角和过渡连接、尽量避免过大平面。
四、习题一、填空题1、合金的铸造性能主要是指()、()、()、()。
2、合金的收缩过程分为()、()、()三个阶段。
3、铸件产生缩孔和缩松的主要原因是()收缩和()收缩。
4、铸件产生内应力、变形和裂纹的主要原因是()收缩。
二、判断题1、机器造型不能进行三箱造型。
()2、铸造造型时,模样的尺寸和铸件的尺寸一样大。
()三、选择题1、下列铸造合金中,铸造性能最好的是(),铸造性能最差的是()。
A 铸钢B 铸铁C 铸铜2、下列铸件大批量生产时,采用什么方法铸造为宜?车床床身()、汽轮机叶片()、铸铁水管()。
A 砂型铸造B 熔模铸造C 离心铸造四、简答题1、砂型铸造工艺对铸件结构设计有哪些要求?2、合金铸造性能对铸件结构设计有哪些要求?3、下图中砂型铸造铸件结构工艺性不好,说明原因,画出正确图形。
第8章锻压成形二、基本内容1、锻压成形基础知识1)塑性变形对金属性能的影响:随着变形程度的增加,强度和硬度提高而塑性和韧性下降的现象称为冷变形强化。
金属工艺学复习资料(整理版)
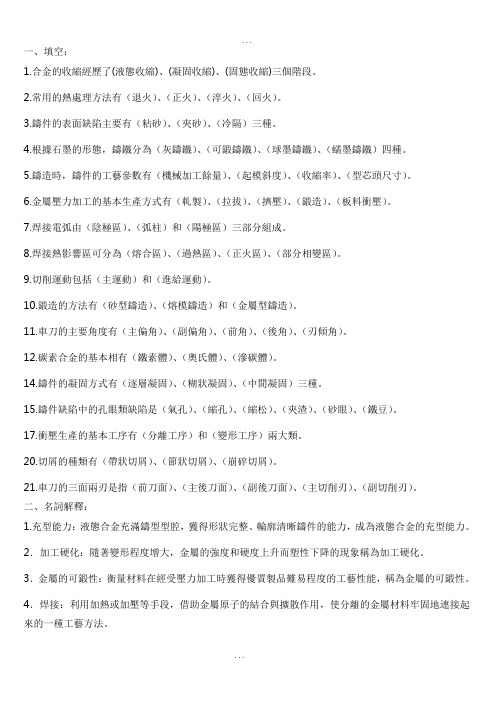
一、填空:1.合金的收縮經歷了(液態收縮)、(凝固收縮)、(固態收縮)三個階段。
2.常用的熱處理方法有(退火)、(正火)、(淬火)、(回火)。
3.鑄件的表面缺陷主要有(粘砂)、(夾砂)、(冷隔)三種。
4.根據石墨的形態,鑄鐵分為(灰鑄鐵)、(可鍛鑄鐵)、(球墨鑄鐵)、(蠕墨鑄鐵)四種。
5.鑄造時,鑄件的工藝參數有(機械加工餘量)、(起模斜度)、(收縮率)、(型芯頭尺寸)。
6.金屬壓力加工的基本生產方式有(軋製)、(拉拔)、(擠壓)、(鍛造)、(板料衝壓)。
7.焊接電弧由(陰極區)、(弧柱)和(陽極區)三部分組成。
8.焊接熱影響區可分為(熔合區)、(過熱區)、(正火區)、(部分相變區)。
9.切削運動包括(主運動)和(進給運動)。
10.鍛造的方法有(砂型鑄造)、(熔模鑄造)和(金屬型鑄造)。
11.車刀的主要角度有(主偏角)、(副偏角)、(前角)、(後角)、(刃傾角)。
12.碳素合金的基本相有(鐵素體)、(奧氏體)、(滲碳體)。
14.鑄件的凝固方式有(逐層凝固)、(糊狀凝固)、(中間凝固)三種。
15.鑄件缺陷中的孔眼類缺陷是(氣孔)、(縮孔)、(縮松)、(夾渣)、(砂眼)、(鐵豆)。
17.衝壓生產的基本工序有(分離工序)和(變形工序)兩大類。
20.切屑的種類有(帶狀切屑)、(節狀切屑)、(崩碎切屑)。
21.車刀的三面兩刃是指(前刀面)、(主後刀面)、(副後刀面)、(主切削刃)、(副切削刃)。
二、名詞解釋:1.充型能力:液態合金充滿鑄型型腔,獲得形狀完整、輪廓清晰鑄件的能力,成為液態合金的充型能力。
2.加工硬化:隨著變形程度增大,金屬的強度和硬度上升而塑性下降的現象稱為加工硬化。
3.金屬的可鍛性:衡量材料在經受壓力加工時獲得優質製品難易程度的工藝性能,稱為金屬的可鍛性。
4.焊接:利用加熱或加壓等手段,借助金屬原子的結合與擴散作用,使分離的金屬材料牢固地連接起來的一種工藝方法。
5.同素異晶轉變:隨著溫度的改變,固態金屬晶格也隨之改變的現象,稱為同素異晶轉變。
《金属工艺学》下册复习总汇讲解

下册切削加工P304.对刀具才来哦的性能有哪些要求⑴较高的硬度。
刀具材料的硬度必须高于工件材料的硬度,常温硬度一般在60HRC以上。
⑵足够的强度和韧度,以承受切削力、冲击、和振动。
⑶较好的耐磨性,以抵抗切削过程中的磨损,维持一定的切削时间。
⑷较高的耐热性,以便在高温下仍能保持较高硬度,又称为红硬性或热硬性。
⑸较好的工艺性,以便于制造各种刀具。
工艺性包括锻造、轧制、焊接、切削加工、磨削加工和热处理性能等。
8.何谓积屑瘤?它是如何形成的?对切削加工有那些影响?在特定切削速度下,被切塑性金属材料,在刀刃附近前刀面上堆积形成金属层,叫积屑瘤。
是切屑与前刀面剧烈摩擦、粘贴吸附到前刀面上的。
积屑瘤可以增大刀具前角,降低切削力;可以保护前刀面减少刀具磨损。
但是,积屑瘤是不稳定的,易破碎、重复堆积,对加工尺寸精度、表面粗糙度有影响,适用于粗加工。
10. 切削热对切削加工有什么影响切削金属时,由于切屑剪切变形所作的功和刀具前面、后面摩擦所作的功都转变为热,这种热叫切削热。
使用切削液时,刀具、工件和切屑上的切削热主要由切削液带走;不用切削液时,切削热主要由切屑、工件和刀具带走或传出,其中切屑带走的热量最大,传向刀具的热量虽小,但前面和后面上的温度却影响着切削过程和刀具的磨损情况,所以了解切削温度的变化规律是十分必要的11.答:刃磨后的刀具自开始切削直到磨损量达到磨钝标准所经历的实际切削时间,称为刀具耐用度,以T表示。
粗加工时,多以切削时间(min)表示刀具耐用度。
精加工时,常以走刀次数或加工零件个数表示刀具的耐用度。
14. 切削液的主要作用是什么?切削加工中常用的切削液有哪几类?如何选用切削液主要作用有四个:润滑,冷却,清洁,防锈。
一般分为三大类:水溶性,全油性,全合成型,或者加上一个,半合成型。
选用方面根据:加工刀具,加工材料,厂房环境,操作员爱好。
(5)何为钻孔时的“引偏”?试举出几种减小引偏的措施。
答:是指加工时由于钻头弯曲而引起的孔径扩大、孔不圆或孔德轴线歪斜等。
金属工艺学复习笔记知识讲解
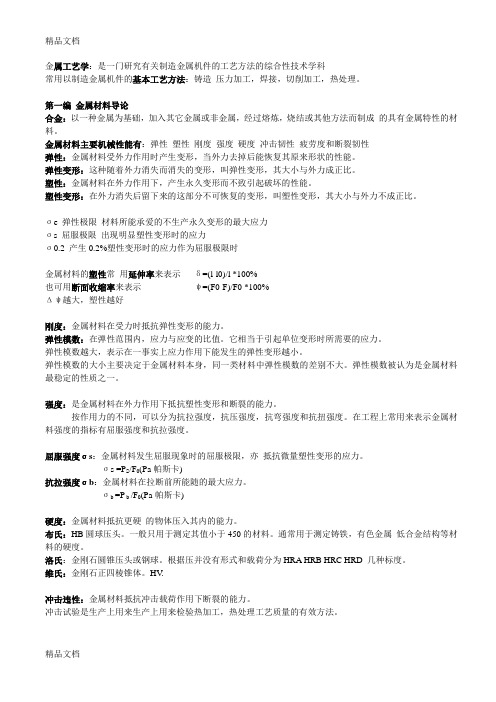
金属工艺学:是一门研究有关制造金属机件的工艺方法的综合性技术学科常用以制造金属机件的基本工艺方法:铸造压力加工,焊接,切削加工,热处理。
第一编金属材料导论合金:以一种金属为基础,加入其它金属或非金属,经过熔炼,烧结或其他方法而制成的具有金属特性的材料。
金属材料主要机械性能有:弹性塑性刚度强度硬度冲击韧性疲劳度和断裂韧性弹性:金属材料受外力作用时产生变形,当外力去掉后能恢复其原来形状的性能。
弹性变形:这种随着外力消失而消失的变形,叫弹性变形,其大小与外力成正比。
塑性:金属材料在外力作用下,产生永久变形而不致引起破坏的性能。
塑性变形:在外力消失后留下来的这部分不可恢复的变形,叫塑性变形,其大小与外力不成正比。
σe 弹性极限材料所能承爱的不生产永久变形的最大应力σs 屈服极限出现明显塑性变形时的应力σ0.2 产生0.2%塑性变形时的应力作为屈服极限时金属材料的塑性常用延伸率来表示δ=(l-l0)/l *100%也可用断面收缩率来表示ψ=(F0-F)/F0 *100%Δψ越大,塑性越好刚度:金属材料在受力时抵抗弹性变形的能力。
弹性模数:在弹性范围内,应力与应变的比值。
它相当于引起单位变形时所需要的应力。
弹性模数越大,表示在一事实上应力作用下能发生的弹性变形越小。
弹性模数的大小主要决定于金属材料本身,同一类材料中弹性模数的差别不大。
弹性模数被认为是金属材料最稳定的性质之一。
强度:是金属材料在外力作用下抵抗塑性变形和断裂的能力。
按作用力的不同,可以分为抗拉强度,抗压强度,抗弯强度和抗扭强度。
在工程上常用来表示金属材料强度的指标有屈服强度和抗拉强度。
屈服强度σs:金属材料发生屈服现象时的屈服极限,亦抵抗微量塑性变形的应力。
σs =P S/F0(Pa帕斯卡)抗拉强度σb:金属材料在拉断前所能随的最大应力。
σb =P b /F0(Pa帕斯卡)硬度:金属材料抵抗更硬的物体压入其内的能力。
布氏:HB圆球压头。
一般只用于测定其值小于450的材料。
金属工艺学复习资料
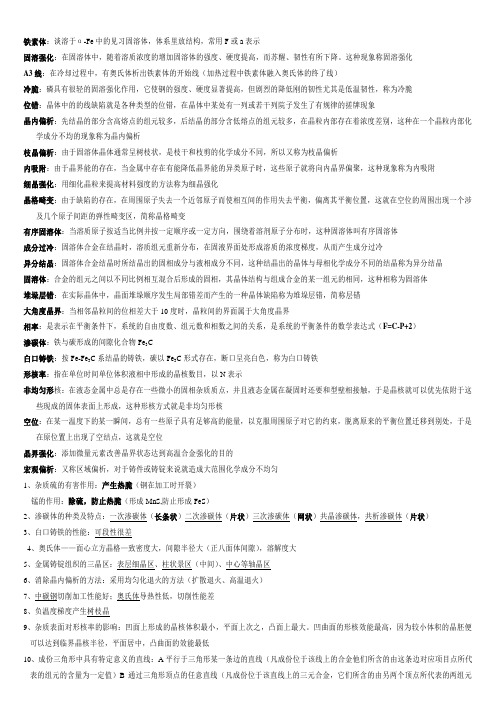
铁素体:谈溶于α-Fe中的见习固溶体,体系里放结构,常用F或a表示固溶强化:在固溶体中,随着溶质浓度的增加固溶体的强度、硬度提高,而苏醒、韧性有所下降。
这种现象称固溶强化A3线:在冷却过程中,有奥氏体析出铁素体的开始线(加热过程中铁素体融入奥氏体的终了线)冷脆:磷具有很轻的固溶强化作用,它使钢的强度、硬度显著提高,但剧烈的降低刚的韧性尤其是低温韧性,称为冷脆位错:晶体中的的线缺陷就是各种类型的位错,在晶体中某处有一列或若干列院子发生了有规律的搓牌现象晶内偏析:先结晶的部分含高熔点的组元较多,后结晶的部分含低熔点的组元较多,在晶粒内部存在着浓度差别,这种在一个晶粒内部化学成分不均的现象称为晶内偏析枝晶偏析:由于固溶体晶体通常呈树枝状,是枝干和枝剪的化学成分不同,所以又称为枝晶偏析内吸附:由于晶界能的存在,当金属中存在有能降低晶界能的异类原子时,这些原子就将向内晶界偏聚,这种现象称为内吸附细晶强化:用细化晶粒来提高材料强度的方法称为细晶强化晶格畸变:由于缺陷的存在,在周围原子失去一个近邻原子而使相互间的作用失去平衡,偏离其平衡位置,这就在空位的周围出现一个涉及几个原子间距的弹性畸变区,简称晶格畸变有序固溶体:当溶质原子按适当比例并按一定顺序或一定方向,围绕着溶剂原子分布时,这种固溶体叫有序固溶体成分过冷:固溶体合金在结晶时,溶质组元重新分布,在固液界面处形成溶质的浓度梯度,从而产生成分过冷异分结晶:固溶体合金结晶时所结晶出的固相成分与液相成分不同,这种结晶出的晶体与母相化学成分不同的结晶称为异分结晶固溶体:合金的组元之间以不同比例相互混合后形成的固相,其晶体结构与组成合金的某一组元的相同,这种相称为固溶体堆垛层错:在实际晶体中,晶面堆垛顺序发生局部错差而产生的一种晶体缺陷称为堆垛层错,简称层错大角度晶界:当相邻晶粒间的位相差大于10度时,晶粒间的界面属于大角度晶界相率:是表示在平衡条件下,系统的自由度数、组元数和相数之间的关系,是系统的平衡条件的数学表达式(F=C-P+2)渗碳体:铁与碳形成的间隙化合物Fe3C白口铸铁:按Fe-Fe3C系结晶的铸铁,碳以Fe3C形式存在,断口呈亮白色,称为白口铸铁形核率:指在单位时间单位体积液相中形成的晶核数目,以N表示非均匀形核:在液态金属中总是存在一些微小的固相杂质质点,并且液态金属在凝固时还要和型壁相接触,于是晶核就可以优先依附于这些现成的固体表面上形成,这种形核方式就是非均匀形核空位:在某一温度下的某一瞬间,总有一些原子具有足够高的能量,以克服周围原子对它的约束,脱离原来的平衡位置迁移到别处,于是在原位置上出现了空结点,这就是空位晶界强化:添加微量元素改善晶界状态达到高温合金强化的目的宏观偏析:又称区域偏析,对于铸件或铸锭来说就造成大范围化学成分不均匀1、杂质硫的有害作用:产生热脆(钢在加工时开裂)锰的作用:除硫,防止热脆(形成MnS,防止形成FeS)2、渗碳体的种类及特点:一次渗碳体(长条状)二次渗碳体(片状)三次渗碳体(网状)共晶渗碳体,共析渗碳体(片状)3、白口铸铁的性能:可段性很差4、奥氏体——面心立方晶格—致密度大,间隙半径大(正八面体间隙),溶解度大5、金属铸锭组织的三晶区:表层细晶区、柱状景区(中间)、中心等轴晶区6、消除晶内偏析的方法:采用均匀化退火的方法(扩散退火、高温退火)7、中碳钢切削加工性能好;奥氏体导热性低,切削性能差8、负温度梯度产生树枝晶9、杂质表面对形核率的影响:凹面上形成的晶核体积最小,平面上次之,凸面上最大。
金属工艺学复习资料
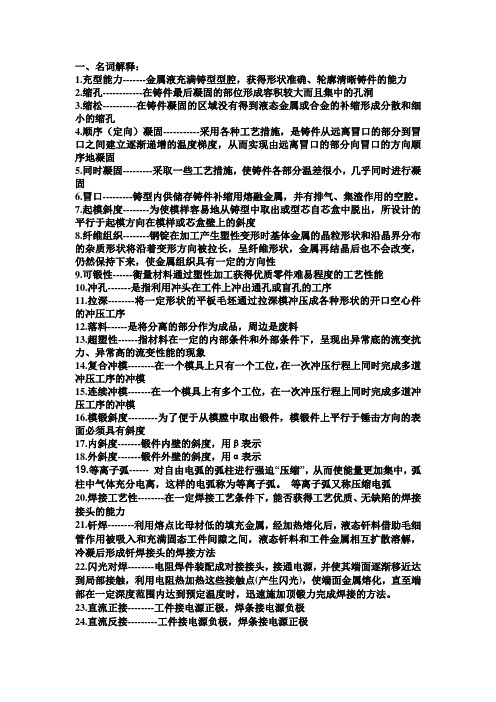
一、名词解释:1.充型能力-------金属液充满铸型型腔,获得形状准确、轮廓清晰铸件的能力2.缩孔------------在铸件最后凝固的部位形成容积较大而且集中的孔洞3.缩松----------在铸件凝固的区域没有得到液态金属或合金的补缩形成分散和细小的缩孔4.顺序(定向)凝固-----------采用各种工艺措施,是铸件从远离冒口的部分到冒口之间建立逐渐递增的温度梯度,从而实现由远离冒口的部分向冒口的方向顺序地凝固5.同时凝固---------采取一些工艺措施,使铸件各部分温差很小,几乎同时进行凝固6.冒口---------铸型内供储存铸件补缩用熔融金属,并有排气、集渣作用的空腔。
7.起模斜度--------为使模样容易地从铸型中取出或型芯自芯盒中脱出,所设计的平行于起模方向在模样或芯盒壁上的斜度8.纤维组织--------钢锭在加工产生塑性变形时基体金属的晶粒形状和沿晶界分布的杂质形状将沿着变形方向被拉长,呈纤维形状,金属再结晶后也不会改变,仍然保持下来,使金属组织具有一定的方向性9.可锻性------衡量材料通过塑性加工获得优质零件难易程度的工艺性能10.冲孔-------是指利用冲头在工件上冲出通孔或盲孔的工序11.拉深--------将一定形状的平板毛坯通过拉深模冲压成各种形状的开口空心件的冲压工序12.落料------是将分离的部分作为成品,周边是废料13.超塑性------指材料在一定的内部条件和外部条件下,呈现出异常底的流变抗力、异常高的流变性能的现象14.复合冲模--------在一个模具上只有一个工位,在一次冲压行程上同时完成多道冲压工序的冲模15.连续冲模-------在一个模具上有多个工位,在一次冲压行程上同时完成多道冲压工序的冲模16.模锻斜度---------为了便于从模膛中取出锻件,模锻件上平行于锤击方向的表面必须具有斜度17.内斜度-------锻件内壁的斜度,用β表示18.外斜度-------锻件外壁的斜度,用α表示19.等离子弧------对自由电弧的弧柱进行强迫“压缩”,从而使能量更加集中,弧柱中气体充分电离,这样的电弧称为等离子弧。
金属工艺学复习资料重要知识点详解
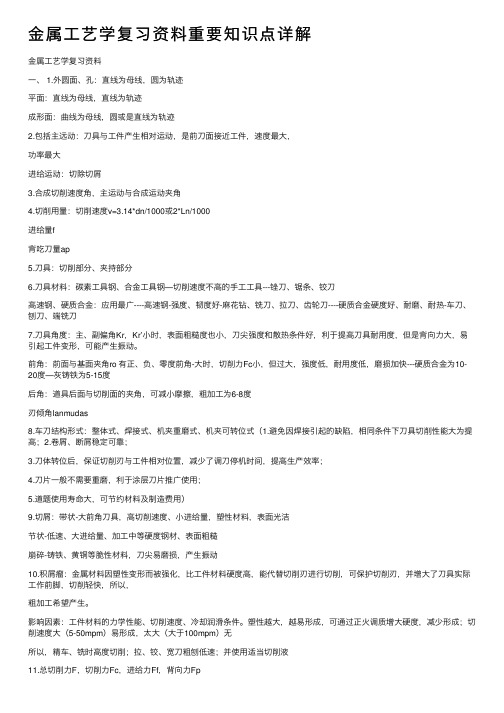
⾦属⼯艺学复习资料重要知识点详解⾦属⼯艺学复习资料⼀、 1.外圆⾯、孔:直线为母线,圆为轨迹平⾯:直线为母线,直线为轨迹成形⾯:曲线为母线,圆或是直线为轨迹2.包括主远动:⼑具与⼯件产⽣相对运动,是前⼑⾯接近⼯件,速度最⼤,功率最⼤进给运动:切除切屑3.合成切削速度⾓,主运动与合成运动夹⾓4.切削⽤量:切削速度v=3.14*dn/1000或2*Ln/1000进给量f背吃⼑量ap5.⼑具:切削部分、夹持部分6.⼑具材料:碳素⼯具钢、合⾦⼯具钢—切削速度不⾼的⼿⼯⼯具---锉⼑、锯条、铰⼑⾼速钢、硬质合⾦:应⽤最⼴----⾼速钢-强度、韧度好-⿇花钻、铣⼑、拉⼑、齿轮⼑----硬质合⾦硬度好、耐磨、耐热-车⼑、刨⼑、端铣⼑7.⼑具⾓度:主、副偏⾓Kr,Kr’⼩时,表⾯粗糙度也⼩,⼑尖强度和散热条件好,利于提⾼⼑具耐⽤度,但是背向⼒⼤,易引起⼯件变形,可能产⽣振动。
前⾓:前⾯与基⾯夹⾓ro 有正、负、零度前⾓-⼤时,切削⼒Fc⼩,但过⼤,强度低,耐⽤度低,磨损加快---硬质合⾦为10-20度—灰铸铁为5-15度后⾓:道具后⾯与切削⾯的夹⾓,可减⼩摩擦,粗加⼯为6-8度刃倾⾓lanmudas8.车⼑结构形式:整体式、焊接式、机夹重磨式、机夹可转位式(1.避免因焊接引起的缺陷,相同条件下⼑具切削性能⼤为提⾼;2.卷屑、断屑稳定可靠;3.⼑体转位后,保证切削刃与⼯件相对位置,减少了调⼑停机时间,提⾼⽣产效率;4.⼑⽚⼀般不需要重磨,利于涂层⼑⽚推⼴使⽤;5.道题使⽤寿命⼤,可节约材料及制造费⽤)9.切屑:带状-⼤前⾓⼑具,⾼切削速度、⼩进给量,塑性材料,表⾯光洁节状-低速、⼤进给量、加⼯中等硬度钢材、表⾯粗糙崩碎-铸铁、黄铜等脆性材料,⼑尖易磨损,产⽣振动10.积屑瘤:⾦属材料因塑性变形⽽被强化,⽐⼯件材料硬度⾼,能代替切削刃进⾏切削,可保护切削刃,并增⼤了⼑具实际⼯作前脚,切削轻快,所以,粗加⼯希望产⽣。
金属工艺学复习资料(3篇)
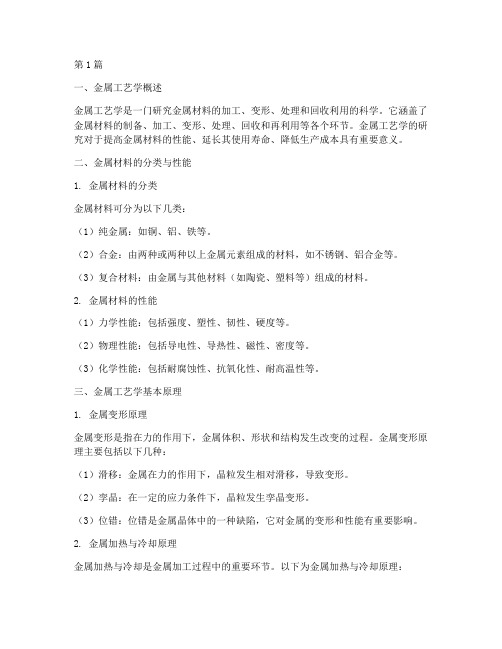
第1篇一、金属工艺学概述金属工艺学是一门研究金属材料的加工、变形、处理和回收利用的科学。
它涵盖了金属材料的制备、加工、变形、处理、回收和再利用等各个环节。
金属工艺学的研究对于提高金属材料的性能、延长其使用寿命、降低生产成本具有重要意义。
二、金属材料的分类与性能1. 金属材料的分类金属材料可分为以下几类:(1)纯金属:如铜、铝、铁等。
(2)合金:由两种或两种以上金属元素组成的材料,如不锈钢、铝合金等。
(3)复合材料:由金属与其他材料(如陶瓷、塑料等)组成的材料。
2. 金属材料的性能(1)力学性能:包括强度、塑性、韧性、硬度等。
(2)物理性能:包括导电性、导热性、磁性、密度等。
(3)化学性能:包括耐腐蚀性、抗氧化性、耐高温性等。
三、金属工艺学基本原理1. 金属变形原理金属变形是指在力的作用下,金属体积、形状和结构发生改变的过程。
金属变形原理主要包括以下几种:(1)滑移:金属在力的作用下,晶粒发生相对滑移,导致变形。
(2)孪晶:在一定的应力条件下,晶粒发生孪晶变形。
(3)位错:位错是金属晶体中的一种缺陷,它对金属的变形和性能有重要影响。
2. 金属加热与冷却原理金属加热与冷却是金属加工过程中的重要环节。
以下为金属加热与冷却原理:(1)加热:金属加热时,其温度逐渐升高,原子振动加剧,导致金属软化。
(2)冷却:金属冷却时,原子振动减弱,晶体结构逐渐稳定,金属硬化。
3. 金属热处理原理金属热处理是指在一定温度下对金属进行加热、保温和冷却,以改变其组织和性能的过程。
金属热处理原理主要包括以下几种:(1)退火:通过加热使金属组织发生变化,提高其塑性和韧性。
(2)正火:通过加热和冷却使金属组织发生变化,提高其硬度和耐磨性。
(3)淬火:通过快速冷却使金属组织发生变化,提高其硬度和耐磨性。
(4)回火:通过加热和冷却使金属组织发生变化,提高其韧性和稳定性。
四、金属工艺学主要加工方法1. 冲压加工冲压加工是指利用冲模对金属板材、带材、管材等进行压力加工的方法。
金属工艺学复习资料

金属工艺学复习资料
1. 金属材料的分类
金属材料可以分为两类:有色金属和黑色金属。
有色金属包括铝、铜、锡等,而黑色金属包括铁、钢、铸铁等。
不同的金属材料具有不同的物理和化学特性,因此在加工和应用过程中需要根据材料的特性进行相应的处理和选择。
2. 金属的加工方法
金属加工的方法主要有铸造、锻造、冷拔、热轧、冷轧、剪切、冲压等。
不同的加工方法适用于不同的金属材料和加工要求,可以使材料得到不同的形状和性质。
3. 金属结构和组织
金属的结构和组织主要包括原子结构、结晶结构、金属晶体、晶界、析出相等。
这些结构和组织的不同类型和形态对金属的强度、硬度、耐磨性、韧性等性质有着重要的影响。
4. 金属的热处理
金属的热处理包括退火、正火、淬火、回火等。
热处理能够改变金属材料的结构和组织,提高其机械性能,改善金属表面的性质以及消除加工应力等。
5. 金属的表面处理
金属的表面处理主要包括电镀、喷涂、镀层等。
这些方法可以保护金属表面不受腐蚀、磨损、氧化等环境因素的侵害,同时也可以改善金属的外观和使用寿命。
总之,金属工艺学是金属制造工业中非常重要的学科,掌握金属的材料特性、加工方法、结构组织和热处理等知识,对于提高金属制造品质的稳定性和性能的优化方案具有非常重要的意义。
- 1、下载文档前请自行甄别文档内容的完整性,平台不提供额外的编辑、内容补充、找答案等附加服务。
- 2、"仅部分预览"的文档,不可在线预览部分如存在完整性等问题,可反馈申请退款(可完整预览的文档不适用该条件!)。
- 3、如文档侵犯您的权益,请联系客服反馈,我们会尽快为您处理(人工客服工作时间:9:00-18:30)。
锻造1、金属塑性变形的实质金属塑性变形的实质是晶体内部产生滑移的结果。
单晶体内的滑移变形。
在切向应力作用下,晶体的一部分与另一部分沿着一定的晶面产生相对滑移,从而造成晶体的塑性变形。
当外力继续作用或增大时,晶体还将在另外的滑移面上发生滑移,使变形继续进行,因而得到一定的变形量。
2、内部组织的变化①晶粒沿最大变形的方向伸长:(形成纤维组织)②晶粒破碎,位错密度增加,产生加工硬化③产生内应力3、加工硬化的概念及其原因在塑性变形过程中,随着金属内部组织的变化,金属的力学性能也将产生明显的变化,即随着变形程度的增加,金属的强度、硬度增加,而塑性、韧性下降,这一现象即为加工硬化或形变强化。
关于加工硬化的原因,目前普遍认为与位错的交互作用有关。
随着塑性变形的进行,位错密度不断增加,因此位错在运动时的相互交割加剧,产生固定割阶、位错缠结等障碍,使位错运动的阻力增大,引起变形抗力的增加,因此就提高了金属的强度。
4、可锻性好差的判断金属的可锻性是衡量材料在经受压力加工时获得优质制品难易程度的工艺性能。
可锻性常用金属的塑性和变形抗力来综合衡量。
塑性越好,变形抗力越小,则金属的可锻性好。
反之则差。
金属的塑性用金属的断面收缩率ψ、伸长率δ等来表示。
变形抗力系指在压力加工过程中变形金属作用于施压工具表面单位面积上的压力。
变形抗力越小,则变形中所消耗的能量也越少。
金属的可锻性取决于金属的本质和加工条件。
5、锻造温度提高金属变形时的温度,是改善金属可锻性的有效措施。
金属在加热中,随温度的升高、金属原子的运动能力增强,很容易进行滑移,因而塑性提高,变形抗力降低,可锻性明显改善,更加适宜进行压力加工。
但温度过高,对钢而言,必将产生过热、过烧、脱碳和严重氧化等缺陷,甚至使锻件报废,所以应该严格控制锻造温度。
锻造温度范围系指始锻温度和终锻温度间的温度区间。
锻造温度范围的确定以合金状态图为依据。
碳钢的锻造温度范围,其始锻温度比AE线低200℃左右,终锻温度为800℃左右。
终锻温度过低,金属的可锻性急剧变差,使加工难于进行,若强行锻造,将导致锻件破裂报废。
6、应力状态压应力的数目越多,则金属的塑性越好;拉应力的数目越多,则金属的塑性越差。
同号应力状态下引起的变形抗力大于异号应力状态下的变形抗力。
拉应力使金属原子间距增大,尤其当金属的内部存在气孔、微裂纹等缺陷时,在拉应力作用下,缺陷处易产生应力集中,使裂纹扩展,甚至达到破坏报废的程度。
压应力使金属内部原子间距离减小,不易使缺陷扩展,故金属的塑性会增高。
但压应力使金属内部摩擦阻力增大,变形抗力亦随之增大。
综上所述,金属的可锻性既取决于金属的本质,又取决于变形条件。
在压力加工过程中,应力求创造最有利的变形条件,充分发挥金属的塑性,降低变形抗力,使功耗最少,变形进行得充分,达到加工目的。
7、自由锻和模锻的区别见书185页第三节模锻第二段和第三段8、拔长和冲孔的工序拔长:圆形截面坯料拔长时,先锻成方形截面,在拔长到边长直径接近锻件直径时,锻成八角形截面,最后倒棱滚打成圆形截面,这样拔长效率高,且能避免引起中心裂纹。
冲孔:冲孔用冲子在坯料上冲出通孔或不通孔的锻造工序。
实心冲子双面冲孔,在镦粗平整的坯料表面上先预冲一凹坑,放稍许煤粉,再继续冲至约3/4深度时,借助于煤粉燃烧的膨胀气体取出冲子,翻转坯料,从反面将孔冲透。
9、圆环和圆筒的过程工序10、预锻和终锻的区别预锻模膛的圆角、斜度较大,没有飞边槽。
终锻模膛的圆角、斜度较小,有飞边槽。
11、胎膜锻和其他两个的区别胎膜不是固定在自由锻锤上,使用时放上去,不用时取下来。
与自由成型相比,胎模成型具有较高的生产率,锻件质量好,节省金属材料,降低锻件成本。
与模锻相比,节约了设备投资,简化了模具制造。
但锻件质量比模锻低,劳动强度大,安全性差,模具寿命短,生产率低。
12、分模面合理与否及其原因(书187也有图,图12-7)(1) 应保证模锻件能从模膛中取出来。
轮形件,把分模面选定在a-a面时,已成形的模锻件就无法取出。
一般情况,分模面应选在模锻件的最大截面处。
(2) 按选定的分模面制成锻模后,应使上下两模沿分模面的模膛轮廓一致,以便在安装锻模和生产中容易发现错模现象,及时而方便地调整锻模位置。
c-c面被选定为分模面,就不符合此原则。
(3) 分模面应选在能使模膛深度最浅的位置上。
这样有利于金属充满模膛,便于取件,并有利于锻模制造。
b-b面,就不适合作分模面。
(4) 选定的分模面应使零件上所加的敷料最少。
b-b面被选作分模面时,零件中间的孔不能锻出来,孔部金属都是敷料,既浪费金属,又增加了切削加工的工作量。
所以该面不宜作分模面。
错动。
按上述原则综合分析,d-d面是最合理的分模面。
13、加强筋(a)(b)铸件时选择B合理,可以防止缩孔缩松,加强筋可以提高强度锻件时选择A合理,加强筋一般锻不出14、冲孔连皮冲孔连皮:对于具有通孔的锻件,由于不可能靠上、下模的突起部分把金属完全挤压到旁边去,故终锻后在孔内留有一薄层金属。
因此,把冲孔连皮和飞边冲掉后,才能得到具有通孔的模锻件。
15、复杂的模锻件对形状复杂的模锻件,使坯料形状基本接近模锻件形状,使金属能合理分布和很好地充满模锻模膛,就必须预先在制坯模镗内制坯,因而设制坯模膛铸造1、缩孔缩松形成原因、形成的机理、影响因素形成原因:液态收缩和凝固收缩是铸件产生缩孔和缩松的基本原因。
而固相收缩对应力、变形与裂纹影响较大。
机理:缩孔:纯金属、共晶成分合金和结晶温度范围窄的合金,在一般铸造条件下按由表及里逐层凝固的方式凝固。
由于金属或合金在冷却过程中发生的液态收缩和凝固收缩大于固态收缩,从而在铸件最后凝固部位形成尺寸较大的集中缩孔。
缩松:结晶温度范围较宽的合金,一般按照体积凝固的方式凝固,凝固区内的小晶体很容易发展成为发达的树枝晶。
当固相达到一定数量形成晶体骨架时,尚未凝固的液态金属便被分割成一个个互不相通的小熔池。
在随后的冷却过程中,小熔池内的液体将发生液态收缩和凝固收缩,已凝固的金属则发生固态收缩。
由于熔池金属的液态收缩和凝固收缩之和大于其固态收缩,两者之差引起的细小孔洞又得不到外部液体的补充,便在相应部位形成了分散性的细小缩孔,即缩松。
影响因素:金属的性质(收缩系数α大)铸型的冷却能力(蓄热系数b小)浇注温度与浇注速度(高,快)铸件尺寸(大)补缩能力(弱)预防措施:1)顺序凝固铸件各部位由远及近,朝着帽口方向顺序凝固。
用于凝固收缩大、结晶间隔窄的金属。
2)同时凝固凝固时产生热裂纹、变形倾向小。
用于凝固收缩小、对气密性要求不高的铸件。
3)使用冒口、补贴和冷铁2、铸件的残余应力(1)厚壁筋板内拉伸应力,薄壁筋板内压缩应(2)中心近轴线部位受拉,外部近圆周部位受压3、热裂纹、冷裂纹的产生以及预防措施(1)热裂纹产生:金属凝固结晶末期,在固相线附近发生的晶间开裂现象,称为凝固裂纹或结晶裂纹。
(其形成与凝固末期晶间存在的液膜有关,断口具有沿晶间液膜分离的特征。
裂纹无金属光泽,有明显的氧化色彩。
)预防措施:1)尽量选择凝固温度范围小、热裂倾向小的合金2)提高铸型和型芯的退让性,以减小机械应力3)合理设计浇道冒口4)对于铸钢件和铸铁件,严格控制硫的含量,防止热脆性(2)冷裂纹产生:冷裂纹是指金属经焊接或铸造成形后冷却到较低温度时产生的裂纹。
(这类裂纹是中碳钢、高碳钢、低合金高强钢、工具钢、钛合金及铸铁等材料成形加工时或使用过程中极易出现的一类工艺缺陷,对结构的安全使用破坏极大。
铸造冷裂纹是铸件凝固后冷却到弹性状态时,因局部铸造应力大于材料强度极限而引起的开裂。
这类裂纹总是发生在冷却过程中承受较高拉应力的部位,特别是应力集中部位。
壁厚不均匀、形状复杂的大型铸件容易产生冷裂纹。
)预防措施:凡是能减小铸造内应力或减低合金的脆性的因素均能防止热裂4、浇注系统浇口杯作用:用来承接来自浇包的金属液,防止金属液飞溅和溢出,减轻液流对型腔的冲击;分离渣滓和气泡,增加充型压力头直浇道的作用:引导金属进入横浇道,提供足够的压力头直浇道窝:缓冲金属液对直浇道底部的冲击作用,缩短直-横拐弯处的高度温流区,改善内浇道的流量分布,浮出金属液的气泡横浇道:向内浇道分配洁净的金属液,储留最初浇入的气体和渣污的低温金属液并阻留渣滓内浇道:控制充型速度和方向,分配金属,调节铸件各部位的温度和凝固顺序5、浇注位置的确定1.)铸件的重要工作面或主要加工面朝下或位于侧面2、)铸件的大平面朝下或倾斜浇注3.)铸件的薄壁朝下、侧立或倾斜。
4.)铸件的厚大部分应放在顶部或在分型面的侧面5.)浇注位置应有利于砂芯的定位和稳固支撑,保证排气通畅及下芯和检验方便。
尽量少用或不用砂芯,若确需使用砂芯时,应尽量避免用吊砂、吊芯或悬臂式砂芯。
6.)在大批量生产中,应使铸件的毛刺、飞翅易于清理。
7.)要避免厚实铸件冒口下面的主要工作面产生偏析。
6、看图合理与否见书166-168页焊接1、 焊接接头组成与组织受热循环的影响,焊缝附近的母材组织和性能发生变化的变化区域称为焊接热影响区。
熔焊焊缝和母材的交界线叫熔合线,熔合线两侧有一个很窄的焊缝与热影响区的过渡区,叫熔合区。
因此焊接接头由焊缝、熔合区和热影响区组成。
具体见书2032、 三种焊接方法(钎焊、压焊、熔焊)的焊接方法、工艺特点3、 焊接性能估算钢材可焊性的方法:碳当量法C 当量<0.4%时,钢材塑性良好,淬硬倾向不明显,可焊性良好。
C 当量=0.4%~0.6%时,钢材塑性下降,淬硬倾向明显,可焊性较差。
C 当量>0.6%时,钢材塑性较低,淬硬倾向很强,可焊性不好。
4、 热裂纹、冷裂纹的产生原因及其预防热裂纹:热裂纹可发生在焊缝区或热影响区。
热裂纹的微观特征是沿晶界开裂,所以又称晶间裂纹。
因热裂纹在高温下形成,所以有氧化色彩热裂纹产生的原因:● 晶间存在液态薄膜。
● 接头中存在拉应力热裂纹的防止:限制钢材和焊条、焊剂的低熔点杂质,如硫和磷含量。
Fe 和FeS 易形成低熔点共晶,其熔点为988℃,很容易产生热裂纹。
缩小结晶温度范围,改善焊缝组织,细化焊缝晶粒,提高塑性减少偏析。
减少焊接应力的工艺措施,如采用小线能量,焊前预热,合理的焊缝布置等。
冷裂纹的形态和特征焊缝区和热影响区都可能产生冷裂纹。
冷裂纹的特征是无分支,通常为穿晶型。
冷裂纹无氧化色彩。
最常见的冷裂纹是延迟裂纹,即在焊后延迟一段时间才发生的裂纹。
延迟裂纹的产生原因:焊接接头(焊缝和热影响区及熔合区)的淬火倾向严重,产生淬火组织,导致接头性能脆化。
焊接接头含氢量较高,并聚集在焊接缺陷处形成大量氢分子,造成非常大的局部压力,使接头脆化。
存在较大的拉应力。
因氢的扩散需要时间,所以冷裂纹在焊后需延迟一段时间才出现。
由于是氢所诱发的,也叫氢致裂纹。