精馏节能技术
精馏塔精馏影响因素分析及节能技术的应用
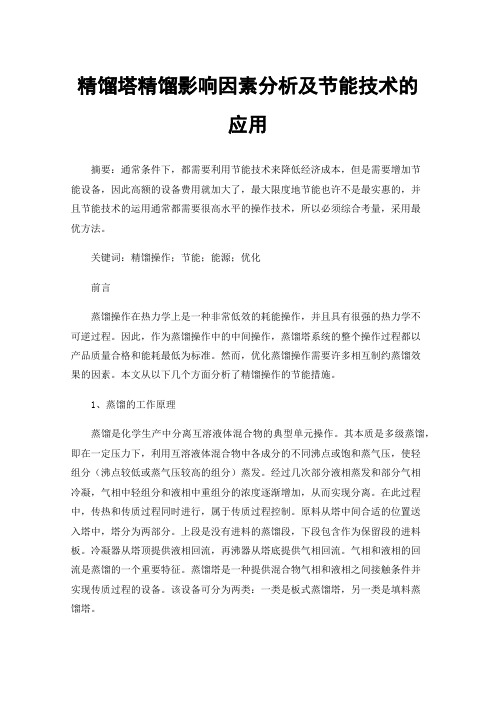
精馏塔精馏影响因素分析及节能技术的应用摘要:通常条件下,都需要利用节能技术来降低经济成本,但是需要增加节能设备,因此高额的设备费用就加大了,最大限度地节能也许不是最实惠的,并且节能技术的运用通常都需要很高水平的操作技术,所以必须综合考量,采用最优方法。
关键词:精馏操作;节能;能源;优化前言蒸馏操作在热力学上是一种非常低效的耗能操作,并且具有很强的热力学不可逆过程。
因此,作为蒸馏操作中的中间操作,蒸馏塔系统的整个操作过程都以产品质量合格和能耗最低为标准。
然而,优化蒸馏操作需要许多相互制约蒸馏效果的因素。
本文从以下几个方面分析了精馏操作的节能措施。
1、蒸馏的工作原理蒸馏是化学生产中分离互溶液体混合物的典型单元操作。
其本质是多级蒸馏,即在一定压力下,利用互溶液体混合物中各成分的不同沸点或饱和蒸气压,使轻组分(沸点较低或蒸气压较高的组分)蒸发。
经过几次部分液相蒸发和部分气相冷凝,气相中轻组分和液相中重组分的浓度逐渐增加,从而实现分离。
在此过程中,传热和传质过程同时进行,属于传质过程控制。
原料从塔中间合适的位置送入塔中,塔分为两部分。
上段是没有进料的蒸馏段,下段包含作为保留段的进料板。
冷凝器从塔顶提供液相回流,再沸器从塔底提供气相回流。
气相和液相的回流是蒸馏的一个重要特征。
蒸馏塔是一种提供混合物气相和液相之间接触条件并实现传质过程的设备。
该设备可分为两类:一类是板式蒸馏塔,另一类是填料蒸馏塔。
2、精馏塔影响的因素2.1、物料平衡精馏塔稳态操作的必须条件就是要保持精馏装置的物料平衡。
对于指定的原料液流量,只要分离度(馏出液中易挥发组分的摩尔分数)和釜残液中易挥发组分的摩尔分数是规定不变的,而馏出液流量和釜残液流量也能够确定了。
分离度和釜残液中易挥发组分的摩尔分数决定于气液平衡关系和理论板数,所以D和W或采出率 D F/ 与W F/ 只能根据分离度和釜残液中易挥发组分的摩尔分数确定,然而不能随意变化,否则进、出塔的两个组分的量会导致失衡,最终把塔内组成发生改变,波动不平的操作,这样一来整个工作工程的效率和效果不是特别理想。
浅析化工精馏高效节能技术开发及应用
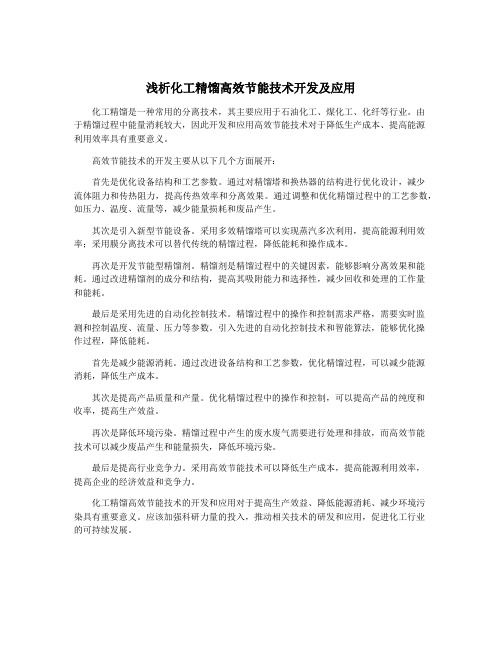
浅析化工精馏高效节能技术开发及应用化工精馏是一种常用的分离技术,其主要应用于石油化工、煤化工、化纤等行业。
由于精馏过程中能量消耗较大,因此开发和应用高效节能技术对于降低生产成本、提高能源利用效率具有重要意义。
高效节能技术的开发主要从以下几个方面展开:首先是优化设备结构和工艺参数。
通过对精馏塔和换热器的结构进行优化设计,减少流体阻力和传热阻力,提高传热效率和分离效果。
通过调整和优化精馏过程中的工艺参数,如压力、温度、流量等,减少能量损耗和废品产生。
其次是引入新型节能设备。
采用多效精馏塔可以实现蒸汽多次利用,提高能源利用效率;采用膜分离技术可以替代传统的精馏过程,降低能耗和操作成本。
再次是开发节能型精馏剂。
精馏剂是精馏过程中的关键因素,能够影响分离效果和能耗。
通过改进精馏剂的成分和结构,提高其吸附能力和选择性,减少回收和处理的工作量和能耗。
最后是采用先进的自动化控制技术。
精馏过程中的操作和控制需求严格,需要实时监测和控制温度、流量、压力等参数。
引入先进的自动化控制技术和智能算法,能够优化操作过程,降低能耗。
首先是减少能源消耗。
通过改进设备结构和工艺参数,优化精馏过程,可以减少能源消耗,降低生产成本。
其次是提高产品质量和产量。
优化精馏过程中的操作和控制,可以提高产品的纯度和收率,提高生产效益。
再次是降低环境污染。
精馏过程中产生的废水废气需要进行处理和排放,而高效节能技术可以减少废品产生和能量损失,降低环境污染。
最后是提高行业竞争力。
采用高效节能技术可以降低生产成本,提高能源利用效率,提高企业的经济效益和竞争力。
化工精馏高效节能技术的开发和应用对于提高生产效益、降低能源消耗、减少环境污染具有重要意义。
应该加强科研力量的投入,推动相关技术的研发和应用,促进化工行业的可持续发展。
精馏过程的节能降耗

精馏过程的节能降耗精馏过程在化工产业中是一项重要的分离技术,但是它也是能耗较高的过程。
为了降低能耗,节能降耗已经成为精馏技术的一个重要研究方向。
本文将介绍几种精馏过程的节能降耗技术。
首先,提高精馏塔的热效率是提高精馏过程的一个关键。
一种常见的做法是引入换热器网络来最大程度地利用出塔冷凝液和进塔蒸汽之间的热量传递。
这种方法可以降低所需的蒸汽量,从而降低了能耗。
此外,还可以使用多效精馏、热泵或采用废热回收技术进一步提高热效率。
其次,提高精馏过程的物质效率也是节能降耗的一个重要途径。
物质效率是指在精馏过程中使用的干燥剂或者吸附剂能够更有效地去除杂质,从而减少能耗。
通过改进精馏塔的操作条件,如温度、压力和液体流速等参数,可以提高物质效率。
同时,使用高效的精馏填料或者塔板也能够提高分离效果,减少杂质的含量。
此外,使用先进的辅助技术可以进一步降低精馏过程的能耗。
例如,在精馏过程中引入膜分离技术可以减少能源消耗。
膜分离技术是一种基于材料表面或孔隙的选择性渗透性原理分离混合物的方法。
与传统的溶剂萃取或者蒸馏技术相比,膜分离技术具有能耗低、操作简单、体积小等优点。
通过将膜分离技术与精馏过程相结合,可以实现更高效的分离效果。
最后,优化精馏过程的操作策略也是节能降耗的一个重要途径。
通过优化参数设定和控制策略,可以使精馏过程更加稳定和高效。
例如,采用先进的控制算法,如模型预测控制或者模糊控制算法,可以实现对精馏过程的快速响应和精确控制,从而降低了能耗和运行成本。
总的来说,精馏过程的节能降耗是一个涉及多个方面的工程问题。
通过提高热效率、物质效率,使用先进的辅助技术和优化操作策略,可以有效地降低精馏过程的能耗。
这些节能降耗技术不仅可以减少环境污染,还可以提高精馏过程的经济效益。
因此,精馏过程的节能降耗在工业应用中具有重要的意义。
精馏节能技术

热泵精馏工艺分析化工行业就是能耗大户,其中精馏又就是能耗极高的单元操作,而传统的精馏方式热力学效率很低,能量浪费很大。
如何降低精馏塔的能耗,充分利用低温热源,已成为人们普遍关注的问题。
对此人们提出了许多节能措施,通过大量的理论分析、实验研究以及工业应用表明其中节能效果比较显著的就是热泵精馏技术。
热泵精馏就是把精馏塔塔顶蒸汽加压升温,使其用作塔底再沸器的热源,回收塔顶蒸汽的冷凝潜热。
热泵精馏在下述场合应用,有望取得良好效果:(1)塔顶与塔底温差较小,因为压缩机的功耗主要取决于温差,温差越大,压缩机的功耗越大。
据国外文献报导,只要塔顶与塔底温差小于36℃,就可以获得较好的经济效果。
(2)沸点相近组分的分离,按常规方法,蒸馏塔需要较多的塔盘及较大的回流比,才能得到合格的产品,而且加热用的蒸汽或冷却用的循环水都比较多。
若采用热泵技术一般可取得较明显的经济效益。
(3)工厂蒸汽供应不足或价格偏高,有必要减少蒸汽用量或取消再沸器时。
(4)冷却水不足或者冷却水温偏高、价格偏贵,需要采用制冷技术或其她方法解决冷却问题时。
(5)一般蒸馏塔塔顶温度在38~138℃之间,如果用热泵流程对缩短投资回收期有利就可以采用,但就是如果有较便宜的低压蒸汽与冷却介质来源,用热泵流程就不一定有利。
(6)蒸馏塔底再沸器温度在300℃以上,采用热泵流程往往就是不合适的。
以上只就是对一般情况而言,对于某个具体工艺过程,还要进行全面的经济技术评定之后才能确定。
根据热泵所消耗的外界能量不同,热泵精馏可分为蒸汽加压方式与吸收式两种类型1、蒸汽加压方式蒸汽加压方式热泵精馏有两种:蒸汽压缩机方式与蒸汽喷射式。
1、1蒸汽压缩机方式蒸汽压缩机方式又可分为间接式、塔顶气体直接压缩式、分割式与塔釜液体闪蒸再沸式流程。
1、1、1间接式当塔顶气体具有腐蚀性或塔顶气体为热敏性产品或塔顶产品不宜压缩时,可以采用间接式热泵精馏,见图1。
图1 间接式热泵精馏流程图它主要由精馏塔、压缩机、蒸发器、冷凝器及节流阀等组成。
精馏过程节能技术综述
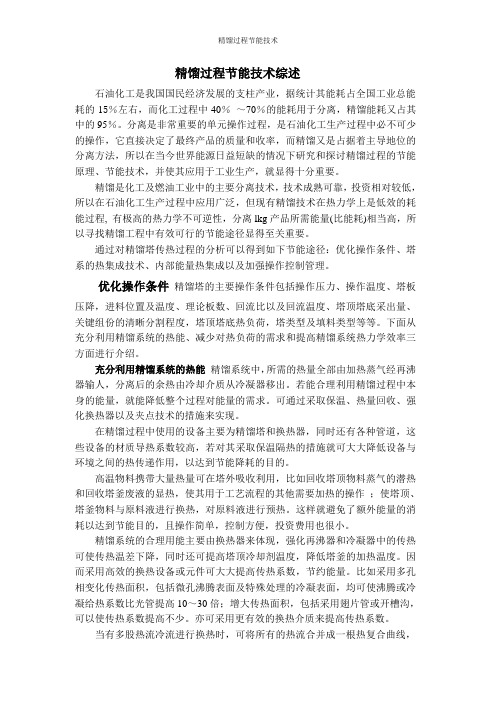
精馏过程节能技术综述石油化工是我国国民经济发展的支柱产业,据统计其能耗占全国工业总能耗的15%左右,而化工过程中40%~70%的能耗用于分离,精馏能耗又占其中的95%。
分离是非常重要的单元操作过程,是石油化工生产过程中必不可少的操作,它直接决定了最终产品的质量和收率,而精馏又是占据着主导地位的分离方法,所以在当今世界能源日益短缺的情况下研究和探讨精馏过程的节能原理、节能技术,并使其应用于工业生产,就显得十分重要。
精馏是化工及燃油工业中的主要分离技术,技术成熟可靠,投资相对较低,所以在石油化工生产过程中应用广泛,但现有精馏技术在热力学上是低效的耗能过程, 有极高的热力学不可逆性,分离lkg产品所需能量(比能耗)相当高,所以寻找精馏工程中有效可行的节能途径显得至关重要。
通过对精馏塔传热过程的分析可以得到如下节能途径:优化操作条件、塔系的热集成技术、内部能量热集成以及加强操作控制管理。
优化操作条件精馏塔的主要操作条件包括操作压力、操作温度、塔板压降,进料位置及温度、理论板数、回流比以及回流温度、塔顶塔底采出量、关键组份的清晰分割程度,塔顶塔底热负荷,塔类型及填料类型等等。
下面从充分利用精馏系统的热能、减少对热负荷的需求和提高精馏系统热力学效率三方面进行介绍。
充分利用精馏系统的热能精馏系统中,所需的热量全部由加热蒸气经再沸器输人,分离后的余热由冷却介质从冷凝器移出。
若能合理利用精馏过程中本身的能量,就能降低整个过程对能量的需求。
可通过采取保温、热量回收、强化换热器以及夹点技术的措施来实现。
在精馏过程中使用的设备主要为精馏塔和换热器,同时还有各种管道,这些设备的材质导热系数较高,若对其采取保温隔热的措施就可大大降低设备与环境之间的热传递作用,以达到节能降耗的目的。
高温物料携带大量热量可在塔外吸收利用,比如回收塔顶物料蒸气的潜热和回收塔釜废液的显热,使其用于工艺流程的其他需要加热的操作;使塔顶、塔釜物料与原料液进行换热,对原料液进行预热。
精馏节能技术
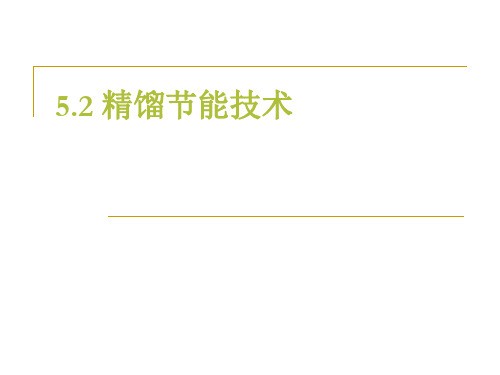
(3) 中间冷凝器和中间再沸器
如能在塔中部设置中间冷凝器,就可以采用较高温度 如能在塔中部设置中间冷凝器, 的冷却剂。 的冷却剂。 如在塔中部设置中间再沸器,对于高温塔, 如在塔中部设置中间再沸器,对于高温塔,可应用较 低温位的加热剂。 低温位的加热剂。 对于精馏,使操作线向平衡线靠拢,提高塔内分离过 对于精馏,使操作线向平衡线靠拢, 程的可逆程度。 程的可逆程度。 在生产过程中必须要由适当温位的加热剂或( 在生产过程中必须要由适当温位的加热剂或(和)冷 却剂与其相配,并需有足够大的热负荷值得利用, 却剂与其相配,并需有足够大的热负荷值得利用,再 加上塔顶和塔底的温度差要相当大, 加上塔顶和塔底的温度差要相当大,如此才会取得经 济效益。 济效益。
(5) 热泵精馏
将温度较低的塔顶蒸汽经压缩后作为塔底再沸器的热源, 将温度较低的塔顶蒸汽经压缩后作为塔底再沸器的热源, 称为热泵精馏。 称为热泵精馏。 三种典型的热泵精馏流程:使用另外的工作流体, 三种典型的热泵精馏流程:使用另外的工作流体,塔顶 蒸汽再压缩,再沸器液体闪蒸。 蒸汽再压缩,再沸器液体闪蒸。 热泵精馏是消耗一定量的机械功来提高低温蒸汽的能位 而加以利用的。因此消耗单位机械能能回收的热量是一 而加以利用的。因此消耗单位机械能能回收的热量是一 消耗单位机械能能回收的热量 项重要经济指标,称为性能系数,常记为 项重要经济指标,称为性能系数,常记为C.O.P.。 。 显然, 显然,对于沸点差小的混合物分离的精馏塔应用热泵精 馏效果会更好。 馏效果会更好。5Fra bibliotek2 精馏节能技术
精馏节能技术

热泵精馏工艺分析化工行业是能耗大户,其中精馏又是能耗极高的单元操作,而传统的精馏方式热力学效率很低,能量浪费很大。
如何降低精馏塔的能耗,充分利用低温热源,已成为人们普遍关注的问题。
对此人们提出了许多节能措施,通过大量的理论分析、实验研究以及工业应用表明其中节能效果比较显著的是热泵精馏技术。
热泵精馏是把精馏塔塔顶蒸汽加压升温,使其用作塔底再沸器的热源,回收塔顶蒸汽的冷凝潜热。
热泵精馏在下述场合应用,有望取得良好效果:(1)塔顶和塔底温差较小,因为压缩机的功耗主要取决于温差,温差越大,压缩机的功耗越大。
据国外文献报导,只要塔顶和塔底温差小于36°C,就可以获得较好的经济效果。
(2)沸点相近组分的分离,按常规方法,蒸馏塔需要较多的塔盘及较大的回流比,才能得到合格的产品,而且加热用的蒸汽或冷却用的循环水都比较多。
若采用热泵技术一般可取得较明显的经济效益。
(3)工厂蒸汽供应不足或价格偏高,有必要减少蒸汽用量或取消再沸器时。
(4)冷却水不足或者冷却水温偏高、价格偏贵,需要采用制冷技术或其他方法解决冷却问题时。
(5)—般蒸馏塔塔顶温度在38〜138C之间,如果用热泵流程对缩短投资回收期有利就可以采用,但是如果有较便宜的低压蒸汽和冷却介质来源,用热泵流程就不一定有利。
(6)蒸馏塔底再沸器温度在300C以上,采用热泵流程往往是不合适的。
以上只是对一般情况而言,对于某个具体工艺过程,还要进行全面的经济技术评定之后才能确定。
根据热泵所消耗的外界能量不同,热泵精馏可分为蒸汽加压方式和吸收式两种类型1.蒸汽加压方式蒸汽加压方式热泵精馏有两种:蒸汽压缩机方式和蒸汽喷射式。
1.1蒸汽压缩机方式蒸汽压缩机方式又可分为间接式、塔顶气体直接压缩式、分割式和塔釜液体闪蒸再沸式流程。
1.1.1间接式当塔顶气体具有腐蚀性或塔顶气体为热敏性产品或塔顶产品不宜压缩时,可以采用间接式热泵精馏,见图1。
图1间接式热泵精馏流程图它主要由精馏塔、压缩机、蒸发器、冷凝器及节流阀等组成。
化工精馏技术的应用及节能研究

化工精馏技术的应用及节能研究摘要:化工行业应积极开展节能减排工作,优化改革化工生产过程,达到降耗节能的目的,同时减少对生态环境的污染与破坏。
化工行业的发展,为人们生产生活带来了便利,但也带来了环境污染和能源浪费问题。
因此,实现化工行业可持续发展,必须采取节能减排措施,优化化工生产过程,降低能耗和污染。
化工生产过程分离与反应两个过程,其中分离过程所造成的能源消耗量占据整体能源消耗量的75%。
这是化工生产中能源浪费的主要原因,因此,降低分离过程的能耗是化工行业节能减排的一个重要方向。
关键词:化工;精馏;节能技术;应用1化工精馏分析化工蒸馏技术是将不同性质的物料放入蒸馏塔装置中,通过塔板装置实现传质传热,在塔板中进行汽化分离。
传统的蒸馏技术虽然可以实现物料的分离,但是会造成大量的蒸汽损耗,导致能源浪费。
为了实现节能降耗,化工精馏技术应运而生。
化工精馏技术能够合理利用多余热量,实现能源的有效利用。
但是,化工精馏技术受到许多因素的影响,如回流比例、环境温度、塔内压力、物料量等,需要注重控制。
如果这些因素不能得到有效的控制,将会导致化工精馏技术的效率降低,甚至出现质量问题。
传统的化工精馏需要大量能源物质加热蒸馏塔底部结构,且存在热量损耗与能源浪费现象。
因此,需要创新研发高效应用化工精馏节能降耗技术。
这样不仅可以降低能源消耗,减少对环境的影响,还可以提高生产效率,降低生产成本,推动化工行业的可持续发展。
化工精馏技术是化工行业中的重要技术之一,它的应用能够实现物料的分离和能源的节约。
在未来的发展中,化工精馏技术需要不断创新,应用高效节能降耗技术,实现更加可持续的发展。
2化工精馏高效节能技术开发及应用的现实意义2.1有助于提高化工精馏过程的效率与质量化工精馏在许多工业领域中都扮演着重要的角色,它能够将混合物质分离出不同的组分,达到纯净度的要求。
然而,精馏蒸馏塔的多流程串联运行特点使得化工精馏过程中的能量损耗现象比较严重。
精馏节能减耗总结

精馏节能减耗总结引言在许多化学工艺中,精馏作为一种常见的分离技术,广泛应用于石油化工、化学制药、能源等行业。
然而,传统的精馏过程存在能源消耗大的问题。
为了减少精馏过程中的能源消耗,提高能源利用率,许多节能减耗技术被引入并逐渐得到应用。
本文将对精馏节能减耗的相关技术进行总结,包括辅助加热装置、改进的精馏塔结构以及新型精馏塔填料等。
通过这些节能减耗技术的应用,精馏过程的能耗问题可以得到一定程度的改善,从而实现能源的可持续利用。
辅助加热装置传统的精馏过程中,常常需要大量的蒸汽或热能来提供塔底部的加热需求。
为了减少能源的消耗,引入一些辅助加热装置可以起到节能降耗的效果。
多效加热器多效加热器是一种高效的辅助加热装置,能够通过热传递的方式将高温废热回收利用。
其原理是在精馏塔的塔顶和塔底之间设置多级的加热器,利用顶部产生的低温蒸汽将底部的高温液体加热,从而实现能量的再利用。
热泵热泵是另一种常用的辅助加热装置,通过将低温的热能转移到高温区域,从而实现能量的传递和利用。
在精馏过程中,可以利用热泵将废热转化为可用的热能,供给精馏塔的加热需求。
这样不仅可以减少能源的消耗,还可以达到能源利用的最大化。
改进的精馏塔结构传统的精馏塔结构存在一些不利于能源节约的问题,如传质效率低、压力损失大等。
通过改进精馏塔的结构,可以减少能源的消耗,提高精馏效率。
塔板结构优化传统的精馏塔中,常见的结构是塔板结构,它的主要问题是传质效率低。
为了提高传质效率,可以引入一些新的塔板结构,如泡沫塔板、视窗塔板等。
这些新型塔板结构具有更大的表面积和更好的传质性能,能够有效地提高精馏效率,降低能源消耗。
塔内增加填料层除了改进塔板结构,也可以在精馏塔内部增加填料层,以增加界面面积,提高传质效果。
常见的填料包括金属填料、陶瓷填料、塑料填料等。
这些填料具有较大的表面积和较好的传质性能,能够增加相接触的机会,从而提高传质效率,减少能源消耗。
新型精馏塔填料塔填料作为精馏过程中的重要组成部分,对其传质效率和能源消耗有着直接的影响。
石油化工中的节能技术

石油化工中的节能技术段占庭教授博士生导师(清华大学)中国老教授协会能源与节能技术咨询中心目录一、精馏技术的节能二、精馏方法的改进与节能三、分离过程的改进与节能四、传质与传热设备的节能一、精馏技术的节能1. 多效蒸馏 多效蒸馏的原理与多效蒸发相同,即将前级塔塔顶蒸气直接作为后级塔塔釜的加热蒸气,这样可以充分利用不同品位的热能。
下图为典型的多效蒸馏流程。
进料分别引入若干塔进行并联操作,各塔操作压力不同,多效蒸馏的关键是选择适宜的各塔操作压力,使高压塔的塔顶蒸气在低压塔的再沸器中冷凝,同时作为低压塔的热源。
只有第一效需要外部加热,末效需要塔顶冷凝。
多效蒸馏受到第一效加热蒸气压力和末效冷却介质温度的限制,常见的是采用双效。
双效蒸馏回收DMF的双效蒸馏普通蒸馏蒸汽用量12100公斤/小时双效蒸馏蒸汽用量5400公斤/小时双效蒸馏可节约大量能量2.热泵精馏间接蒸汽压缩直接蒸汽压缩热泵精馏3. 热耦蒸馏热偶蒸馏用来分离沸点接近的多组元物,可以实现节能。
图为Stupin和Lockhart报道的热偶蒸馏流程分离A、B、C三元混合物。
物料进入第一个顶分馏塔,全部轻组分A和全部重组分C分别由塔底馏出,中间组分B则在塔顶和塔底都有。
将塔顶、塔底产品分别引入第二个分馏塔的合适位置。
这样第二个塔的上部分离A和B,下部分离C,中间产品B则由侧线采出。
由于第一个塔的塔顶冷凝和塔釜加热由两个塔气液直接传热获得,只有第二个塔有冷凝器和再沸器,故减少了能耗,节约了投资。
此概念可以用于分离超过三元的沸点接近物系。
对于N元混合物,采用一般连续蒸馏流程,要用N-1个塔才能把各组分分离,其中每个塔需要一个冷凝器和一个再沸器。
如果采用热偶蒸馏流程,只需要一个冷凝器和一个再沸器。
4.设置中间再沸器,中间冷凝器在普通精馏塔中,热量从温度最高的再沸器加入,从温度最低的塔顶冷凝器移出。
由式可看出,净功消耗大,热力学效率很低。
加热和冷却的费用也随釜温的升高和顶温的降低而升高。
精馏过程的节能优化综合ppt课件
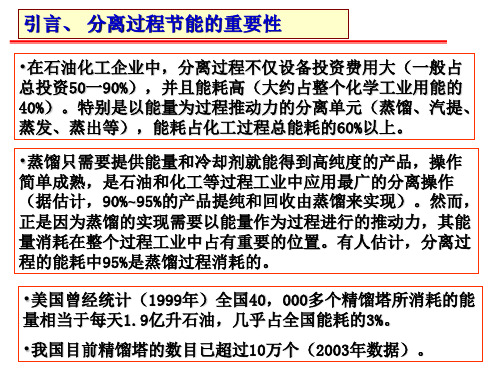
空气源空调(热泵)致热模式
室内(高 温热源)
冷空气 (5℃)
高压液体
冷凝器 (50℃)
热空气 (35℃)
高压蒸汽
节流阀
致冷剂(氟利昂)循环
压缩机
低压液体
低压蒸汽
室外(低 冷空气 温热源) (-5℃)
蒸发器 (-10℃)
冷空气 (-8℃)
空调的效率(COP)主要由什么确定?
问题:能否用其它热源?
空气源空调(热泵)致冷模式
通常所说的节能主要指降低能量消耗或操作费用。任何过程 节能是基于系统热力学分析提出的(热力学第一定律和第二 定律),节能不仅表现在数量上,更表现在品位上,同时要 明确节能和节钱的概念。
分离过程的优化包括分离方法的选择、流程结构的优化和操 作参数的优化等。优化的目标通常是系统的经济性,还包括 多个目标的优化(安全性、操作性、对环境的影响等)。优 化不仅可能节能,同时一定节钱。
3-1 热泵精馏
热泵精馏举例:分离丙烯—丙烷混合物
普通精馏系统:
常压沸点: 丙烯(-47.5℃ 丙烷(-42.1℃ )
(1)塔为什么带压操作? (2)塔为什么操作回流比很 高? (3)塔采用何种冷却介质和 加热介质? (4)要得到常压丙烯气体产 品,需要哪些步骤?
(5)要得到常压丙烷气体产品, 需要哪些步骤? (6)为什么可以考虑采用热泵 精馏?如何实现?
引言、 分离过程节能的重要性
•在石油化工企业中,分离过程不仅设备投资费用大(一般占 总投资50一90%),并且能耗高(大约占整个化学工业用能的 40%)。特别是以能量为过程推动力的分离单元(蒸馏、汽提、 蒸发、蒸出等),能耗占化工过程总能耗的60%以上。
•蒸馏只需要提供能量和冷却剂就能得到高纯度的产品,操作 简单成熟,是石油和化工等过程工业中应用最广的分离操作 (据估计,90%~95%的产品提纯和回收由蒸馏来实现)。然而, 正是因为蒸馏的实现需要以能量作为过程进行的推动力,其能 量消耗在整个过程工业中占有重要的位置。有人估计,分离过 程的能耗中95%是蒸馏过程消耗的。
化工精馏高效节能技术及应用

化工精馏高效节能技术及应用摘要:化工精馏高效节能技术是现代化工生产中必不可少的生产技术,它的广泛应用不仅可以为化工企业增加经济效益,还可以响应国家可持续发展的政策。
本文以化工精馏高效节能技术的具体手法为切入点,对其技术开发的应用提出合理化建议,以期为我国的化工产业进入提质增效的绿色生产阶段提供参考。
关键词:化工生产;精馏;高效节能技术;应用引言:化工精馏技术是化工生产中应用最为广泛的一种技术,主要是利用精馏釜,将不同物质进行分化,进而实现了各类物质的分离。
在具体的化工精馏过程中,精馏釜会产生大量的热量,受到热能量的作用和影响,不同性质的物质均会产生一定的导热性,进而使得物料在气化分离的基础上,对其物料实行进一步的分离[1]。
1.节能高效精馏技术的开发模式1.1分级换热节能技术传统精馏技术热量传导集中在底部,冷却媒介集中在顶部。
物料在精馏釜停留时间较长,温度上升迟缓,热损比率大。
利用分级换热节能技术,需要在精馏釜的中部安装多个换热器。
在这种新的结构下,一旦精馏釜中出现了温度差异,就可以利用中部安装的加热器进行加热减少精馏釜底部的加热时间,降低能源消耗。
1.2多组分精馏技术利用温度较高的轻组分为温度较低的重组交换回收热量,这项技术在操作中往往能以加压塔塔顶组分作为热源向常组分进行热量交换,实现热量的高效、多次、分级利用,降低损耗的同时加大能量利用效率[2]。
1.3塔系热集成技术由于化工精馏均是在精馏釜内进行的,以至于在具体的精馏过程中,难以形成一个温度较高的大环境。
在这种情况下,由于周围环境中的温度比较低,精馏釜中的热量就会被周围的大气所吸收,进而导致精馏热量出现了严重的浪费。
在此条件下,可充分利用塔系热集成技术的优势,将多个化工精馏釜进行密集分布,进而使精馏釜产生集群效应,降低精馏过程中热量浪费。
在具体操作塔系热集成技术时,必须要对材料的物理性质有一个较好的把握,将物理特性相近的物质分离放在精馏釜的上部和下部。
精馏过程的节能降耗

炼油、石化生产过程中大量存在的分离、换热和反应工序,节能潜力巨大。
能源是社会发展和进步的重要物质基础。
我国的能源储量以及一次能源的开发和消费量居世界前列,而能源的总利用率则远低于欧美和日本。
化学工业是个耗能大户,能耗量约占全国能源总消费的9%-10%,占工业用能的13%-15%,因此,化工节能对缓解我国能源的供需矛盾影响很大。
在当前世界性的能源危机面前,化学工业必须首先关注节能降耗和节能新技术的研究应用。
本文就我国化学工业中最普通也是能耗较多的分离过程这一领域中的一些节能现状作一粗略介绍。
一精馏过程的节能降耗精馏技术是化工领域中最为成熟,应用最为广泛且必不可少的单元操作,同时也是工业过程中能耗和设备投资高的设备,在炼油、石化等行业中,其能耗占全过程总能耗的一半以上。
因此对精馏过程节能技术的研究具有极其重要的意义。
国内外已开发并应用了一些节能型耦合精馏塔,如反应精馏塔(Reactive Distillation Column)、热耦合精馏塔(Petlyuk Column)、隔板精馏塔(Dividi Wall Column,简称DWC)等。
精馏过程的节能主要有以下几种基本方式:提高塔的分离效率,降低能耗和提高产品回收率;采用多效精馏技术;采用热泵技术等。
1.1板式塔1.1.1高效导向筛板高效导向筛板具有生产能力大、塔板效率高、塔压降低、结构简单、造价低廉、维修方便的特点,目前已广泛应用于化学工业、石油化工、精细化工、轻工化工、医药工业、香料工业、原子能工业等。
1.1.2板填复合塔板板填复合塔板充分利用板式塔中塔板间距的空隙,设置高效填料,以降低雾沫夹带,提高气体在塔内的流速和塔的生产能力。
同时气液在高效填料表面再次传质,进一步提高了塔板效率。
由于负荷下限未变而上限大幅度提高,因此塔的操作弹性也大为提高。
板填复合塔板已在石化、化工中的甲苯、氯乙烯等多种物系中得到成功应用。
1.1.3复杂精馏塔传统的精馏塔及其精馏序列已不适应当前过程集成、设备集成的发展趋势。
精馏过程节能技术
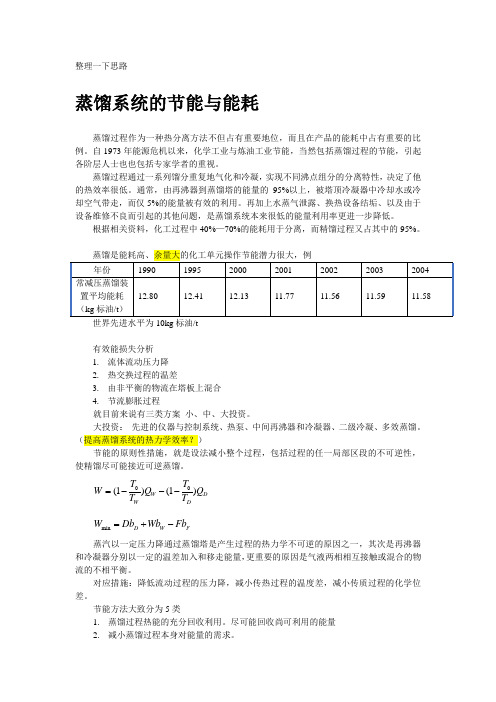
整理一下思路蒸馏系统的节能与能耗蒸馏过程作为一种热分离方法不但占有重要地位,而且在产品的能耗中占有重要的比例。
自1973年能源危机以来,化学工业与炼油工业节能,当然包括蒸馏过程的节能,引起各阶层人士也也包括专家学者的重视。
蒸馏过程通过一系列馏分重复地气化和冷凝,实现不同沸点组分的分离特性,决定了他的热效率很低。
通常,由再沸器到蒸馏塔的能量的95%以上,被塔顶冷凝器中冷却水或冷却空气带走,而仅5%的能量被有效的利用。
再加上水蒸气泄露、换热设备结垢、以及由于设备维修不良而引起的其他问题,是蒸馏系统本来很低的能量利用率更进一步降低。
根据相关资料,化工过程中40%—70%的能耗用于分离,而精馏过程又占其中的95%。
蒸馏是能耗高、余量大的化工单元操作节能潜力很大,例年份 1990 19952000 2001 2002 2003 2004 常减压蒸馏装置平均能耗(kg 标油/t )12.80 12.41 12.13 11.77 11.56 11.59 11.58 世界先进水平为10kg 标油/t有效能损失分析1. 流体流动压力降2. 热交换过程的温差3. 由非平衡的物流在塔板上混合4. 节流膨胀过程就目前来说有三类方案 小、中、大投资。
大投资: 先进的仪器与控制系统、热泵、中间再沸器和冷凝器、二级冷凝、多效蒸馏。
(提高蒸馏系统的热力学效率?)节能的原则性措施,就是设法减小整个过程,包括过程的任一局部区段的不可逆性,使精馏尽可能接近可逆蒸馏。
00(1)(1)W D W DT T W Q Q T T =--- min D W F W Db Wb Fb =+-蒸汽以一定压力降通过蒸馏塔是产生过程的热力学不可逆的原因之一,其次是再沸器和冷凝器分别以一定的温差加入和移走能量,更重要的原因是气液两相相互接触或混合的物流的不相平衡。
对应措施:降低流动过程的压力降,减小传热过程的温度差,减小传质过程的化学位差。
节能方法大致分为5类1. 蒸馏过程热能的充分回收利用。
甲醇精馏技术应用和节能减排

甲醇精馏技术应用和节能减排【摘要】本文主要介绍了甲醇精馏技术在工业生产中的应用和节能减排的重要性。
首先阐述了甲醇精馏技术的原理,以及在生产过程中提高甲醇纯度和质量方面的优势。
然后探讨了甲醇精馏技术对节能减排的作用,以及在环保领域的应用。
结合实际案例,说明了甲醇精馏技术在减少能源消耗和减少污染物排放方面的重要性。
最后展望了甲醇精馏技术的应用前景,并指出未来发展趋势是更加注重节能减排,提高产业化水平,推动甲醇产业向绿色环保方向发展。
通过本文的介绍,读者可以更深入地了解甲醇精馏技术的重要性和影响,促进该技术在工业生产中的广泛应用。
【关键词】关键词:甲醇精馏技术、节能减排、甲醇纯度、工业生产、环保、应用前景、发展趋势、原理分析、质量提高、重要性、环保领域。
1. 引言1.1 甲醇精馏技术应用和节能减排的重要性通过甲醇精馏技术的应用,可以实现甲醇生产过程中的能源回收和再利用,进而实现节能减排的目的。
甲醇精馏技术在环保领域的应用也可以有效降低甲醇生产过程中的排放物质,减少对环境的不良影响。
加强甲醇精馏技术的研究和应用对于推动清洁能源发展、促进工业结构优化和提高能源利用效率具有重要意义。
甲醇精馏技术的应用和节能减排对于实现可持续发展目标、保护环境和促进经济社会可持续发展具有重要意义。
在未来的发展中,应不断加强甲醇精馏技术的研究和推广,促进甲醇产业的健康发展,为实现可持续发展目标贡献力量。
1.2 甲醇精馏技术概述甲醇精馏技术是指利用甲醇的物理性质,在适当的工艺条件下,通过蒸馏来实现对甲醇的提纯和分离的技术。
甲醇精馏技术主要包括多级蒸馏、回流蒸馏、萃取蒸馏等方式,通过这些技术可以有效地提高甲醇的纯度和质量。
甲醇精馏技术在工业生产中得到了广泛的应用,不仅可以用于生产高纯度的甲醇作为化工原料,还可以用于生产燃料乙醇和甲醇汽油等清洁能源产品。
甲醇精馏技术在节能减排和环保领域也有着重要的作用,可以减少生产过程中的能耗和排放,促进工业生产的可持续发展。
精馏的节能技术

精馏过程的节能技术摘要:精馏是化工、石化、医药等过程的重要单元操作,本文主要讨论精馏过程的节能。
从精馏过程热能的充分利用;提高蒸馏系统的分离效率,提高产品回收率来实现降低能耗;减少蒸馏过程对能量的需要和加强管理等几个方面,详细论述了精馏过程的节能技术。
关键词:精馏;节能1、前言在工业生产中,石油化学工业的能耗所占比例最大,而石油化学工业中能耗最大者为分离操作,其中又以精馏的能耗居首位。
精馏过程是一个复杂的传质传热过程,表现为:过程变量多,被控变量多,可操纵的变量也多;过程动态和机理复杂”.首先,随着石油化工的迅速发展,精馏操作的应用越来越广,分离物料的组分不断增多,分离的产品纯度要求亦不断提高,但人们同时又不希望消耗过多的能量,这就对精馏过程的控制提出了要求。
其次,作为化工生产中应用最广的分离过程,精馏也是耗能较大的一种化工单元操作.在实际生产中,为了保证产品合格,精馏装置操作往往偏于保守,操作方法以及操作参数设置往往欠合理。
另外,由于精馏过程消耗的能量绝大部分并非用于组分分离,而是被冷却水或分离组分带走.因此,精馏过程的节能潜力很大,合理利用精馏过程本身的热能,就能降低整个过程对能量的需求,减少能量的浪费,使节能收效也极为明显.据统计,在美国精馏过程的能耗占全国能耗的3%,如果从中节约10%,每年可节省5亿美元。
我国的炼油厂消耗的原油占其炼油量的8%~10%,其中很大一部分消耗于精馏过程.因此,在当今能源紧缺的情况下,对精馏过程的节能研究就显得十分重要.例如,美国巴特尔斯公司在波多黎各某芳烃装置的8个精馏塔上进行节能优化操作,每年可节约310万美元。
蒸馏过程的节能基本上可从以下几个方面着手:(1)精馏过程热能的充分利用;(2)提高蒸馏系统的分离效率,提高产品回收率来实现降低能耗;(3)减少蒸馏过程对能量的需要;(4)加强管理。
2、蒸馏过程热能的充分利用2。
1加强保温保冷以改进热的利用在精馏过程中使用的主要设备为精馏塔和换热器,另外还有各种管道,这些设备多为金属制成,对热的传导较为容易,加之环境温度的影响,若对其采取保温保冷的措施,可以大大降低设备与环境之间的热传递作用,从而达到节约热能的目的.强化再沸器和冷凝器中的传热可使传热温差下降,由于传热温差减小还可使塔顶冷却剂温度提高,塔釜的加热温度下降。
科技成果——自回热精馏节能新技术
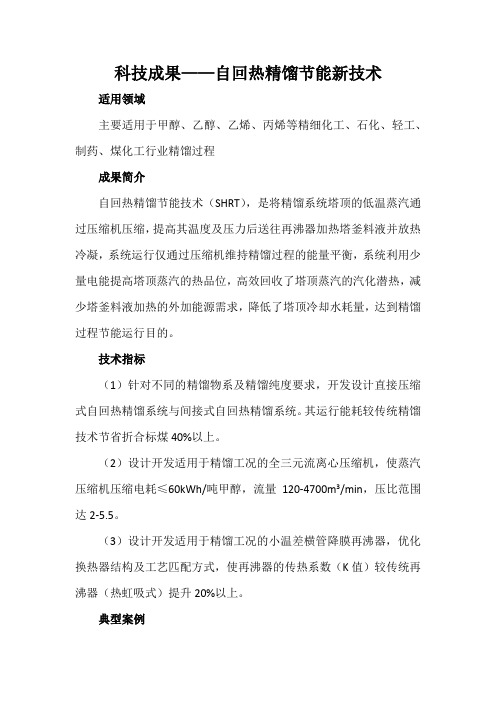
科技成果——自回热精馏节能新技术适用领域
主要适用于甲醇、乙醇、乙烯、丙烯等精细化工、石化、轻工、制药、煤化工行业精馏过程
成果简介
自回热精馏节能技术(SHRT),是将精馏系统塔顶的低温蒸汽通过压缩机压缩,提高其温度及压力后送往再沸器加热塔釜料液并放热冷凝,系统运行仅通过压缩机维持精馏过程的能量平衡,系统利用少量电能提高塔顶蒸汽的热品位,高效回收了塔顶蒸汽的汽化潜热,减少塔釜料液加热的外加能源需求,降低了塔顶冷却水耗量,达到精馏过程节能运行目的。
技术指标
(1)针对不同的精馏物系及精馏纯度要求,开发设计直接压缩式自回热精馏系统与间接式自回热精馏系统。
其运行能耗较传统精馏技术节省折合标煤40%以上。
(2)设计开发适用于精馏工况的全三元流离心压缩机,使蒸汽压缩机压缩电耗≤60kWh/吨甲醇,流量120-4700m3/min,压比范围达2-5.5。
(3)设计开发适用于精馏工况的小温差横管降膜再沸器,优化换热器结构及工艺匹配方式,使再沸器的传热系数(K值)较传统再沸器(热虹吸式)提升20%以上。
典型案例
应用单位:江苏泰利达新材料有限公司
7.3m3/h乙醇自回热精馏节能改造项目,采用直接压缩式SHRT 技术,系统采用高效双螺杆压缩机及横管降膜式再沸器,物料经预热后进入精馏塔,塔顶蒸汽进入压缩机,压缩后的塔顶蒸汽进入再沸器对塔底物料进行加热,塔顶蒸汽冷凝液与物料换热后排出。
本项目已稳定运行近1年时间,总投资约350万元,系统改造后的能源消耗为蒸汽0.95t/h,耗电218kW,循环水量5m3/h。
年节能收益约216万元。
自回热精馏节能技术使用计划方案
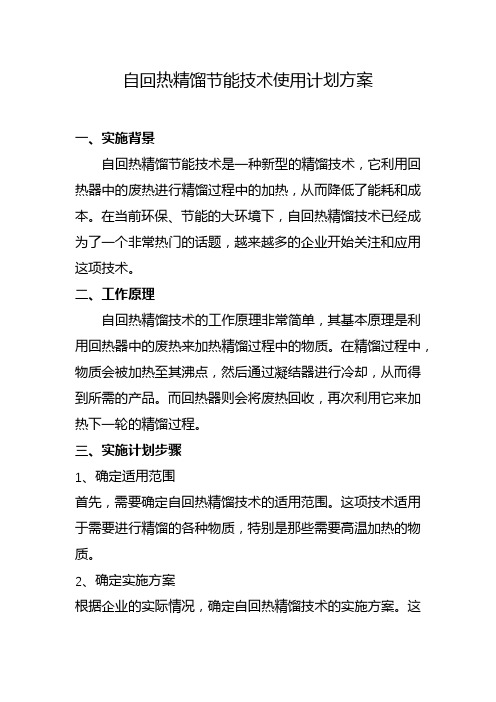
自回热精馏节能技术使用计划方案一、实施背景自回热精馏节能技术是一种新型的精馏技术,它利用回热器中的废热进行精馏过程中的加热,从而降低了能耗和成本。
在当前环保、节能的大环境下,自回热精馏技术已经成为了一个非常热门的话题,越来越多的企业开始关注和应用这项技术。
二、工作原理自回热精馏技术的工作原理非常简单,其基本原理是利用回热器中的废热来加热精馏过程中的物质。
在精馏过程中,物质会被加热至其沸点,然后通过凝结器进行冷却,从而得到所需的产品。
而回热器则会将废热回收,再次利用它来加热下一轮的精馏过程。
三、实施计划步骤1、确定适用范围首先,需要确定自回热精馏技术的适用范围。
这项技术适用于需要进行精馏的各种物质,特别是那些需要高温加热的物质。
2、确定实施方案根据企业的实际情况,确定自回热精馏技术的实施方案。
这包括确定使用的设备和工艺流程,以及需要进行的改造和调整。
3、进行设备改造根据实施方案,对设备进行改造。
这包括添加回热器、调整加热方式等。
4、进行试运行在设备改造完成后,进行试运行。
这可以帮助企业发现设备中存在的问题,并进行调整和改进。
5、正式应用在试运行结束后,正式应用自回热精馏技术。
在使用过程中,需要不断优化和改进,以达到更好的效果。
四、适用范围自回热精馏技术适用于各种需要进行精馏的物质,特别是那些需要高温加热的物质。
此外,该技术还适用于各种规模的企业,无论是大型企业还是中小型企业。
五、创新要点自回热精馏技术的创新点主要包括以下几个方面:1、利用回热器中的废热进行加热,降低了能耗和成本。
2、采用自动控制系统,可以对加热温度和流量进行精确控制,提高了生产效率和产品质量。
3、在设备改造过程中,可以采用先进的材料和工艺,提高了设备的稳定性和可靠性。
六、预期效果通过应用自回热精馏技术,企业可以获得以下效果:1、降低能耗和成本,提高生产效率。
2、减少废气和废水的排放,降低环境污染。
3、提高产品质量和市场竞争力。
七、达到收益应用自回热精馏技术可以带来以下收益:1、降低能耗和成本,提高经济效益。
- 1、下载文档前请自行甄别文档内容的完整性,平台不提供额外的编辑、内容补充、找答案等附加服务。
- 2、"仅部分预览"的文档,不可在线预览部分如存在完整性等问题,可反馈申请退款(可完整预览的文档不适用该条件!)。
- 3、如文档侵犯您的权益,请联系客服反馈,我们会尽快为您处理(人工客服工作时间:9:00-18:30)。
热泵精馏工艺分析化工行业是能耗大户,其中精馏又是能耗极高的单元操作,而传统的精馏方式热力学效率很低,能量浪费很大。
如何降低精馏塔的能耗,充分利用低温热源,已成为人们普遍关注的问题。
对此人们提出了许多节能措施,通过大量的理论分析、实验研究以及工业应用表明其中节能效果比较显著的是热泵精馏技术。
热泵精馏是把精馏塔塔顶蒸汽加压升温,使其用作塔底再沸器的热源,回收塔顶蒸汽的冷凝潜热。
热泵精馏在下述场合应用,有望取得良好效果:(1)塔顶和塔底温差较小,因为压缩机的功耗主要取决于温差,温差越大,压缩机的功耗越大。
据国外文献报导,只要塔顶和塔底温差小于36℃,就可以获得较好的经济效果。
(2)沸点相近组分的分离,按常规方法,蒸馏塔需要较多的塔盘及较大的回流比,才能得到合格的产品,而且加热用的蒸汽或冷却用的循环水都比较多。
若采用热泵技术一般可取得较明显的经济效益。
(3)工厂蒸汽供应不足或价格偏高,有必要减少蒸汽用量或取消再沸器时。
(4)冷却水不足或者冷却水温偏高、价格偏贵,需要采用制冷技术或其他方法解决冷却问题时。
(5)一般蒸馏塔塔顶温度在38~138℃之间,如果用热泵流程对缩短投资回收期有利就可以采用,但是如果有较便宜的低压蒸汽和冷却介质来源,用热泵流程就不一定有利。
(6)蒸馏塔底再沸器温度在300℃以上,采用热泵流程往往是不合适的。
以上只是对一般情况而言,对于某个具体工艺过程,还要进行全面的经济技术评定之后才能确定。
根据热泵所消耗的外界能量不同,热泵精馏可分为蒸汽加压方式和吸收式两种类型1.蒸汽加压方式蒸汽加压方式热泵精馏有两种:蒸汽压缩机方式和蒸汽喷射式。
1.1蒸汽压缩机方式蒸汽压缩机方式又可分为间接式、塔顶气体直接压缩式、分割式和塔釜液体闪蒸再沸式流程。
1.1.1间接式当塔顶气体具有腐蚀性或塔顶气体为热敏性产品或塔顶产品不宜压缩时,可以采用间接式热泵精馏,见图1。
图1 间接式热泵精馏流程图它主要由精馏塔、压缩机、蒸发器、冷凝器及节流阀等组成。
这种流程利用单独封闭循环的工质(冷剂)工作:冷剂与塔顶物料换热后吸收热量蒸发为气体,气体经压缩提高压力和温度后,送至塔釜加热釜液,而本身凝结成液体。
液体经节流减压后再去塔顶换热,完成一个循环。
于是塔顶低温处的热量,通过冷剂的媒介传递到塔釜高温处。
在此流程中,制冷循环中的冷剂冷凝器与塔釜再沸器合为一个设备。
在此设备中冷剂冷凝放热而釜液吸热蒸发。
间接式热泵精馏的特点是:(1)塔中要分离的产品与冷剂完全隔离;(2)可使用标准精馏系统,易于设计和控制;(3)与塔顶气体直接压缩式相比较,多一个热交换器(即蒸发器),压缩机需要克服较高的温差和压力差,因此其效率较低。
考虑到工质的化学稳定性,间接式热泵精馏应用的温度范围限制在130℃左右,而许多有机产品的精馏塔却在较高的温度下操作。
与普通制冷剂相比,水的化学和热稳定性好,泄漏时对人和臭氧层无负效应,价格便宜,而且具有极好的传热特性,在热交换中所需的换热面积较小,特别适合精馏塔底温度较高的精馏系统。
表1是以水为工质,用间接式热泵精馏分离乙苯-对二甲苯的节能结果。
虽然单独工质循环式热泵精馏比常规精馏的总投资费用大,但回收期短,一般在一年之内。
表1 不同热泵精馏流程处理乙苯-对二甲苯溶液的节能及经济效果1.1.2塔顶气体直接压缩式塔顶气体直接压缩式热泵精馏是以塔顶气体作为工质的热泵,其流程见图2,精馏塔顶气体经压缩机压缩升温后进入塔底再沸器,冷凝放热使釜液再沸,冷凝液经节流阀减压降温后,一部分作为产品出料,另一部分作为精馏塔顶的回流。
图2 塔顶气体直接压缩式热泵精馏流程图塔顶气体直接压缩式热泵精馏的特点是:(1)所需的载热介质是现成的;(2)因为只需要一个热交换器(即再沸器),压缩机的压缩比通常低于单独工质循环式的压缩比;(3)系统简单,稳定可靠。
塔顶气体直接压缩式热泵精馏适合应用在塔顶和塔底温度接近,或被分离物质因沸点接近难以分离,必须采用较大回流比的情况下,因此需要消耗大量加热蒸汽(即高负荷的再沸器),或在低压运行必须采用冷冻剂进行冷凝。
为了使用冷却水或空气作冷凝介质,必须在较高塔压下分离某些易挥发物质的场合。
塔顶气体直接压缩式热泵精馏应用十分广泛,如丙烯-丙烷的分离采用该流程,其热力学效率可以从3.6%提高到8.1%,节能和经济效益非常显著。
某厂采用热泵精馏的结果见表2,由此可见,当选用热泵精馏时,能源费用急剧下降。
此时,冷却水温度已不再是决定因素,精馏塔可在更低的压力下操作,既简化了分离过程,又降低了设备成本。
表2 不同精馏形式下丙烯-丙烷分离的节能和经济效果比较1.1.3分割式热泵分割式热泵精馏组成及其流程如图3所示。
图3 分割式热泵精馏流程图分割式热泵精馏流程分为上、下两塔,上塔类似于直接式热泵精馏,只不过多了一个进料口;下塔则类似于常规精馏的提馏段即蒸出塔,进料来自上塔的釜液,蒸汽则进入上塔塔底。
分割式热泵精馏的节能效果明显,投资费用适中,控制简单。
分割式热泵精馏的特点是可通过控制分割点浓度(即下塔进料浓度)来调节上塔的温差,从而选择合适的压缩机。
在实际设计时,分割点浓度的优化是很必要的。
分割式热泵精馏适用于分离体系物的相图存在恒浓区和恒稀区的大温差精馏,如乙醇水溶液、异丙醇水溶液等。
表3是某工厂采用常规精馏、塔顶直接式热泵精馏和分割式热泵精馏工艺处理异丙醇水溶液的结果。
表3 不同精馏形式下异丙醇溶液分离的节能和经济效果比较从表3可以看出,分割式可选择单级压缩机,其耗电量大大降低;而塔顶直接式就必须选择昂贵的多级压缩机。
其耗电量几乎是分割式的2倍。
1.1.4闪蒸再沸闪蒸再沸是热泵的一种变型,它以釜液为工质,其流程如图4所示。
与塔顶气体直接压缩式相似,它也比间接式少一个换热器,适用场合也基本相同。
不过,闪蒸再沸在塔压高时有利,而塔顶气体直接压缩式在塔压低时更有利。
图4 闪蒸再沸式热泵精馏流程图1.2蒸汽喷射式图5是采用蒸汽喷射泵方式的蒸汽汽提减压精馏工艺流程。
在该流程中,塔顶蒸汽是稍含低沸点组成的水蒸气,其一部分用蒸汽喷射泵加压升温,随驱动蒸汽一起进入塔底作为加热蒸汽。
图5 蒸汽喷射式热泵精馏流程图在传统方式中,如果进料预热需蒸汽量10,再沸器需蒸汽量30,则共需蒸汽量40。
而在采用蒸汽喷射式热泵的精馏中,用于进料预热的蒸汽量不变,但由于向蒸汽喷射泵供给驱动蒸汽15就可得到用于再沸器加热的蒸汽30,故蒸汽消耗量是25,可节省37.5%的蒸汽量,所以节能效果十分显著。
采用蒸汽喷射泵方式的热泵精馏具有如下优点:(1)新增设备只有蒸汽喷射泵,设备费用低;(2)蒸汽喷射泵没有转动部件,容易维修,而且维修费用低。
蒸汽喷射式热泵精馏如果在大压缩比或高真空度条件下操作,蒸汽喷射泵的驱动蒸汽量增大,再循环效果显著下降。
因此,这种方式的热泵精馏适合应用在:(1)精馏塔塔底和塔顶的压差不大;(2)减压精馏的真空度比较低的情况下。
2吸收式吸收式热泵由吸收器、再生器、冷却器和再沸器等设备组成,常用溴化锂水溶液或氯化钙水溶液为工质。
由再生器送来的浓溴化锂溶液在吸收器中遇到从再沸器送来的蒸汽,发生了强烈的吸收作用,不但升温而且放出热量<Q吸>,该热量即可用于精馏塔蒸发器,实际上热泵的吸收器即为精馏塔的蒸发器。
浓溴化锂溶液吸收了蒸汽之后,浓度变稀,即送再生器蒸浓。
再生器所耗用的热能<Q生>是热泵的原动力。
从再生器中蒸发出来的水蒸气,在冷却器中冷却、冷凝,而后送入精馏塔冷凝器,在此冷凝器中,塔顶馏出物被冷凝,而水又重新蒸发进入吸收器。
由此可见,精馏塔的冷凝器也是热泵的再沸器,详见图6。
图6 吸收式热泵精馏流程图吸收式热泵按照机内循环方向的不同可分为:冷凝器压力大于蒸发器压力的第一类吸收式热泵(Ⅰ型)和蒸发器压力高于冷凝器压力的第二类吸收式热泵(Ⅱ型)。
第一类吸收式热泵需要高温热源驱动,但不需要外界冷却水,热量能得到充分利用,主要应用于产生热水;第二类吸收式热泵可利用低品位热能直接驱动,以低温热源与冷却水之间的温差为推动力,可产生低压蒸汽。
表4 吸收式热泵的特点由表4可看出:I型吸收式热泵与Ⅱ型吸收式热泵虽是吸收式热泵的两大分支,二者原理相似,但由于驱动能量及供热量温度的差异,使二者应用条件有所不同。
一般在余热源温度较低(30~60℃),用热温度也较低(60~100℃)时,可用I型热泵,其COP 值可达1.7左右,即消耗1kW驱动能,可以获得1.7kW的可用热。
而在余热源温度较高(60~100℃)需要的供热温度也较高(100~150℃)时,可用Ⅱ型热泵,其COP值约为0.5,即每供给热泵1kW的低温余热,可以获得1.5kW温度较高的可用热,相当于不需要其它代价,就可以将低温余热的一半左右回收利用。
吸收式热泵与压缩式热泵相比,虽然供热系数COP较小,但避免了使用动力,在动力紧张的情况下,有压缩式热泵所不可替代的优点。
吸收式热泵的优点是:可以利用温度不高的热源作为动力,如工厂废汽、废热。
除功率不大的溶液泵外没有转动部件,设备维修方便,耗电量小,无噪音。
缺点是热效率低,需要较高的投资,使用寿命不长。
因此只有在产热量很大、而温度提升要求不高,并且可用废热直接驱动的情况下,吸收式热泵的工业应用才具有较大的吸引力。
以下是吸收式热泵的应用举例。
日本某化工厂用Ⅱ型热泵回收精馏塔有机蒸汽的余热8.5t/h。
80℃的有机余热蒸汽进入热泵的发生器和蒸发器,由吸收器将100℃的热水加热到125℃,经闪蒸获得1kg/cm2(表压)120℃的蒸汽4.25t/h,热泵一年运行以8000h计算,则可节约蒸汽34000t。
上海通用机械研究所为上海酒精厂研制Ⅱ型热泵回收蒸馏塔顶76℃酒精蒸汽23222kW功能量,产生0.5kg/cm2 (表压)的蒸汽1.8t/h。
据估算热泵每年收利15万元,装置费用的回收期约为1.5年。
上海交通大学为上海溶剂厂研制LiBr/H2O高温吸收式热泵,回收溶剂生产过程的7547kW103℃余热,产生1kg/cm2(表压)的蒸汽0.5t/h。
据估算的热泵每年收益约8万元,装置费用回收期约三年。
可见目前我国在能源价格偏低的情况下,采用Ⅱ型热泵节能,仍有一定的经济效益。
综上所述,热泵精馏确实是一种高效的节能技术,但需要注意的是,在选择精馏方案时除应考虑能源费用外,还应考虑其设备投资费用等因素对其经济合理性进行综合评价。
在实际设计中,可把前面介绍的几种典型流程加以改进,以拓展热泵精馏的应用范围,而且要进行优化设计,以便获得节能效果和经济效益最佳的热泵精馏方案。