转炉设备概述(
120转炉设备介绍
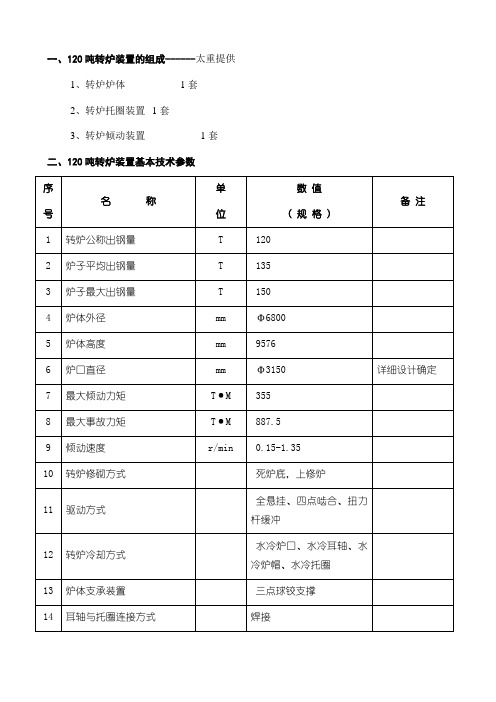
一、120吨转炉装置的组成------太重提供1、转炉炉体1套2、转炉托圈装置1套3、转炉倾动装置1套二、120吨转炉装置基本技术参数托圈耳轴轴向总长:13905 mm托圈断面宽度:850 mm托圈断面高度:2100 mm托圈内径:φ7250±8 mm转炉倾动角度:±360°水冷却系统:通过水气套八路进水,通过驱动侧旋转接头回水底吹配管:通过水气套八路进气三、120吨转炉成套设备技术说明1、转炉炉壳转炉炉壳为全焊接式固定炉底结构,采用16MnR、厚度75mm钢板焊接而成,炉体直径为Ø6800mm,炉壳高度为9196mm。
主要由炉口法兰、上下部圆锥段、圆柱炉身段以及锥柱间、锥球间均匀过渡用的圆环段和球形炉底等部分组成,炉口段和炉底段材料下料不准超过三块。
炉壳上部、中部、下部焊接后应进行消除应力退火;退火后,应保证尺寸和公差,圆柱度≤10mm,然后对这几个部件进行组装检查,最大错边量≤3mm。
炉口法兰用钢板拼焊而成。
上部圆锥段顶部焊接有加筋法兰,供固定炉口用。
上部圆锥段外表面有半割钢管及角钢焊接而成的冷却水循环通道。
在出钢口上部、下部焊有两圈法兰,上部法兰厚度为90mm,下部法兰厚度为140mm,材质为:16MnR,中间联以立筋,形成开放式箱形结构,用于安装炉体支承结构。
筋板及人孔材质为Q235。
炉壳分为四段八块运输,到安装现场后进行现场组焊,并进行超声波探伤检查,合格后采用加热方式进行退火处理以消除内应力。
水冷炉口分六块,材质为耐热球墨铸铁,采购厂家为宝钢铸造有限公司。
2、托圈、耳轴装配2.1托圈托圈的作用是托住炉体并在倾动装置的驱动下带动炉体旋转,是转炉设备的关键件。
托圈的主要尺寸为Ø8950 / Ø 7250×2100,托圈采用16MnR钢板焊接而成。
内弧板、外弧板厚度为60mm,上盖板、下盖板厚度为120mm。
转炉托圈为焊接箱形结构,其内通循环水冷却,两侧耳轴为空心结构,以容纳托圈冷却水、水冷炉口冷却水和炉壳上部圆锥段冷却水及转炉底吹供气管的通道。
卧式转炉简介
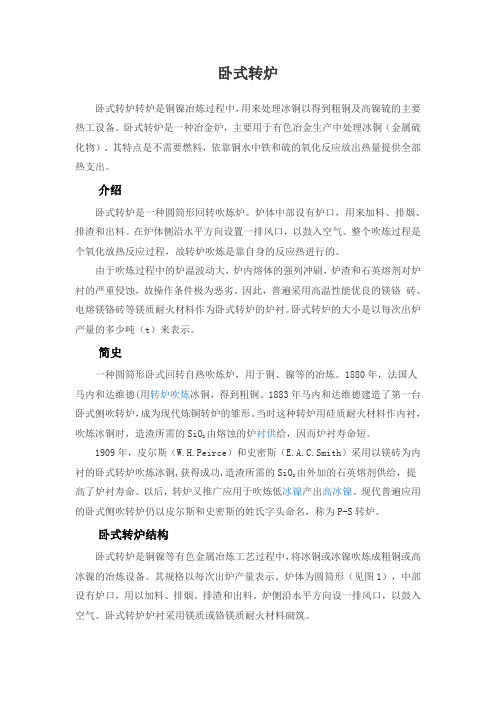
卧式转炉卧式转炉转炉是铜镍冶炼过程中,用来处理冰铜以得到粗铜及高镍锍的主要热工设备。
卧式转炉是一种冶金炉,主要用于有色冶金生产中处理冰铜(金属硫化物)。
其特点是不需要燃料,依靠铜水中铁和硫的氧化反应放出热量提供全部热支出。
介绍卧式转炉是一种圆筒形回转吹炼炉。
炉体中部设有炉口,用来加料、排烟、排渣和出料。
在炉体侧沿水平方向设置一排风口,以鼓入空气。
整个吹炼过程是个氧化放热反应过程,故转炉吹炼是靠自身的反应热进行的。
由于吹炼过程中的炉温波动大,炉内熔体的强列冲刷,炉渣和石英熔剂对炉衬的严重侵蚀,故操作条件极为恶劣。
因此,普遍采用高温性能优良的镁铬砖、电熔镁铬砖等镁质耐火材料作为卧式转炉的炉衬。
卧式转炉的大小是以每次出炉产量的多少吨(t)来表示。
简史一种圆筒形卧式回转自热吹炼炉,用于铜、镍等的冶炼。
1880年,法国人马内和达维德(用转炉吹炼冰铜,得到粗铜。
1883年马内和达维德建造了第一台卧式侧吹转炉,成为现代炼铜转炉的雏形。
当时这种转炉用硅质耐火材料作内衬,吹炼冰铜时,造渣所需的SiO由熔蚀的炉衬供给,因而炉衬寿命短。
21909年,皮尔斯(W.H.Peirce)和史密斯(E.A.C.Smith)采用以镁砖为内由外加的石英熔剂供给,提衬的卧式转炉吹炼冰铜,获得成功,造渣所需的SiO2高了炉衬寿命。
以后,转炉又推广应用于吹炼低冰镍产出高冰镍。
现代普遍应用的卧式侧吹转炉仍以皮尔斯和史密斯的姓氏字头命名,称为P-S转炉。
卧式转炉结构卧式转炉是铜镍等有色金属冶炼工艺过程中,将冰铜或冰镍吹炼成粗铜或高冰镍的冶炼设备。
其规格以每次出炉产量表示。
炉体为圆筒形(见图1),中部设有炉口,用以加料、排烟、排渣和出料。
炉侧沿水平方向设一排风口,以鼓入空气。
卧式转炉炉衬采用镁质或铬镁质耐火材料砌筑。
现代大型卧式转炉的壳内直径为4米左右,长9米左右。
外壳为4~5厘米厚的钢板,内衬为镁砖、镁铬砖或铬镁砖;炉体中部设有炉口,用以加料、排烟、排渣和出铜;有的转炉在炉体端壁设置加入石英熔剂的石英枪,但多数从炉口加石英;炉体一侧沿水平方向设置一排风眼,用以鼓入压缩空气。
转炉系统机械设备概述
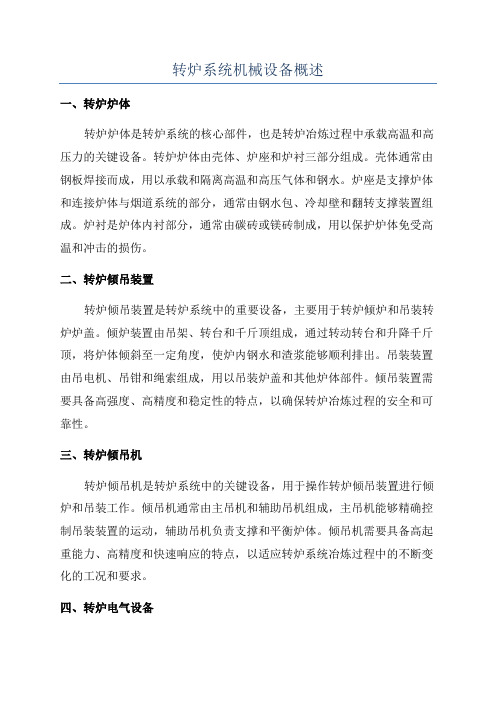
转炉系统机械设备概述一、转炉炉体转炉炉体是转炉系统的核心部件,也是转炉冶炼过程中承载高温和高压力的关键设备。
转炉炉体由壳体、炉座和炉衬三部分组成。
壳体通常由钢板焊接而成,用以承载和隔离高温和高压气体和钢水。
炉座是支撑炉体和连接炉体与烟道系统的部分,通常由钢水包、冷却壁和翻转支撑装置组成。
炉衬是炉体内衬部分,通常由碳砖或镁砖制成,用以保护炉体免受高温和冲击的损伤。
二、转炉倾吊装置转炉倾吊装置是转炉系统中的重要设备,主要用于转炉倾炉和吊装转炉炉盖。
倾炉装置由吊架、转台和千斤顶组成,通过转动转台和升降千斤顶,将炉体倾斜至一定角度,使炉内钢水和渣浆能够顺利排出。
吊装装置由吊电机、吊钳和绳索组成,用以吊装炉盖和其他炉体部件。
倾吊装置需要具备高强度、高精度和稳定性的特点,以确保转炉冶炼过程的安全和可靠性。
三、转炉倾吊机转炉倾吊机是转炉系统中的关键设备,用于操作转炉倾吊装置进行倾炉和吊装工作。
倾吊机通常由主吊机和辅助吊机组成,主吊机能够精确控制吊装装置的运动,辅助吊机负责支撑和平衡炉体。
倾吊机需要具备高起重能力、高精度和快速响应的特点,以适应转炉系统冶炼过程中的不断变化的工况和要求。
四、转炉电气设备转炉电气设备是转炉系统中的重要组成部分,主要包括电动机、变压器、控制系统和电缆等设备。
电动机用于驱动转炉系统中的各种机械设备,如倾吊机、风机和冷却设备,具备高起动力和可靠性的特点。
变压器用于将外部电源的电压和电流调整为适合转炉系统的工作要求,保证转炉系统正常运行。
控制系统用于监控和控制转炉系统的运行状态,包括转炉倾炉角度、温度、压力和气体流量等参数。
电缆用于传输电能和信号,连接转炉系统中的各种设备和控制系统。
总结起来,转炉系统机械设备包括转炉炉体、转炉倾吊装置、倾吊机和转炉电气设备等,它们都是转炉冶炼过程中不可或缺的关键设备。
这些设备需要具备高强度、高精度、稳定性和可靠性的特点,以确保转炉系统的安全和高效运行。
转炉 原理

转炉原理
转炉是一种用来炼钢的设备,其原理是利用高温将原料中的杂质和不纯物质去除,从而得到高纯度的钢材。
转炉的操作过程可以大致分为两个阶段:吹炼和出钢。
在吹炼阶段,首先将底吹氧气和喷吹煤气混合物以高速吹入转炉中。
煤气在高温下燃烧,产生的热量使转炉内部的温度升高。
吹入的氧气则与煤气中的一部分碳反应生成一氧化碳和二氧化碳,同时释放出大量的热量。
这些燃烧和反应过程会形成一个高温高碳的还原区,也称为“焦墨区”。
焦墨区内的高温和高碳环境有助于将原料中的杂质和不纯物质还原为气体或脆性的固体物质,从而实现了炉内的净化作用。
炉内的搅拌装置会将炉内的材料搅拌均匀,促进反应的进行。
吹炼过程中,转炉的操作工人会根据炉内的温度和氧气供应量等参数进行调节,以控制反应的速度和程度。
一般来说,吹炼时间为20-30分钟左右。
吹炼结束后,开始进行出钢操作。
操作工人会逐渐停止底吹和喷吹,采取顶吹的方式将氩气或氮气吹入炉内,以稳定温度,并形成一个保护层,防止钢液的再次氧化。
在出钢过程中,操作工人会打开底部的钢水口,将炉内的钢液流出,并通过连铸设备进行凝固和成型。
同时,还会对钢液进
行取样分析,以确保钢材的质量达到要求。
总的来说,转炉通过高温和高碳环境以及氧气的吹入,实现了对原料中的杂质和不纯物质的去除,从而得到高纯度的钢材。
这种炼钢方式具有高效、灵活和环保等特点,广泛应用于钢铁行业。
260吨转炉本体检修方案

目录1工程概况 (3)1.1转炉本体设备简介 (3)1.2 设备基本参数 (3)1.3 设备功能 (2)1.4 设备检修缺陷 (5)2施工内容 (6)2.1 施工组织、安全体系 (6)2.3施工工程量 (7)2.4 施工方案 (7)2.5施工前的准备工作 (15)2.6对施工单位的要求 (15)3 安全确认办理流程 (15)3.1安全确认流程 (15)3.2安全确认方式 (16)3.3安全确认内容 (16)3.4安全确认要求 (16)3.5填写要求 (17)3.6作业票填写流程 (18)4文明施工 (18)5安全事故预案 (18)5.1目的 (18)5.2组织机构及职责 (18)5.3 安全事故应急措施 (19)5.4注意事项 (19)1工程概况:1.1转炉本体设备简介转炉本体是由炉体、托圈、炉体下悬挂装置、驱动侧旋转接头、游动侧旋转接头、水冷炉口、水冷炉帽、滑板挡渣油缸及机构、底吹枪、驱动端轴承座、游动端轴承座、炉体挡渣板、托圈隔热防护板等设备组成。
在冶炼过程中主要用于承载钢水,并通过转炉倾动机构实现铁水、废钢的入炉以及钢水的出炉。
1.2 设备基本参数1.2.1 炉体主要参数1、公称出钢量:240 t ;平均出钢量:260 t2、炉壳外径:Φ8480mm ;炉壳内径:Φ8300 mm3、转炉全高:10975 mm ;内高:11200 mm4、炉壳内全高/炉壳内径 1.35 ;炉壳容积:495.5m35、砌砖后容积:256m3 ;V/t=0.985 m3/t (1.1)6、转炉炉口直径:Φ3600 (6块耐热球磨铸铁(QT40-17),内埋蛇形管冷却的散形段拼接而成)7、水冷炉口直径:Φ51008、出钢口角度:10°9、直径:Φ17010、熔池直径:Φ630011、转炉炉体冷却水(软化水):工作压力:0.5~0.9Mpa总流量:≥216 m3/h主动耳轴流量:≥3m3/h被动耳轴流量:≥3m3/h托圈流量:≥80 m3/h炉口流量:≥50 m3/h炉帽流量:≥80m3/h出水温度:<65 ℃12、炉壳重:233吨13、炉壳钢板:材料:Q345R炉口钢板厚:150mm 炉壳上部圆锥段板厚:80mm炉身圆柱段板厚:80mm 炉底部分板厚:80mm托圈与炉壳之间的间隙:250mm1.2.2 支撑装置主要参数1、托圈:箱形焊钢结构、水冷。
转炉机械设备讲义
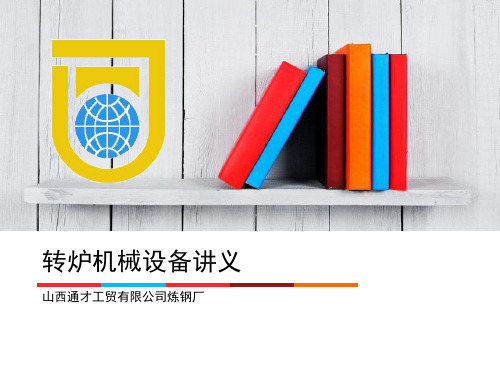
4.炉体支撑系统
(3)耳轴与托圈直接焊接。这种结构由于采用耳轴与托圈直接焊接, 因此,重量小、结构简单、机械加工量小。在大型转炉上用得较多。 为防止结构由于焊接的变形,制造时要特别注意保证两耳轴的平行度 和同心度。
图7-16 耳轴与托圈的焊接连接
4.炉体支撑系统
4.3炉体与托圈连接装置 ①支撑夹持器 法兰螺栓联接是早期出现的吊挂式联接装置,如图7—17a、b 所示。在炉壳上部周边焊接两个法兰,在两法兰之间加焊垂直 筋板加固,以增加炉体刚度。在下法兰上均布8~12个长圆形 螺栓孔,通过螺栓或销钉斜楔将法兰与托圈联接。在联接处垫 一块经过加工的长形垫板,以便使法兰与托圈之间留出通风间 隙。螺栓孔呈长圆形的目的是允许炉壳沿径向热膨胀并避免把 螺栓剪断。炉体倒置时,由螺栓(或圆锁)承受载荷。炉体处于 水平位置时,则由两耳轴下面的托架(见图7—8中的7)把载荷传 给固定在托圈上的定位块。而在与耳轴连接的托圈平面上有一 方块与大法兰方孔相配合,这样就能保证转炉倾动时,将炉体 重量传递到托圈上。
4.炉体支撑系统
(2)静配合连接。其耳轴具有过盈尺寸,装配时可将耳轴用液氮冷缩 或将轴孔加热膨胀,耳轴在常温下装入耳轴孔。为了防止耳轴与耳轴 座孔产生转动或轴向移动,在静配合的传动侧耳轴处拧入精制螺钉。 由于游动侧传递力矩很小,故可采用带小台肩的耳轴限制轴向移动。 这种连接结构比前一种简单,安装和制造较方便,但这种结构仍需在 托圈上焊耳轴座,故托圈重量仍较重。而且装配时,耳轴座加热或耳 轴冷却也较费事,故目前国内没广泛使用。
4.炉体支撑系统
炼钢生产有冶炼和浇铸两个基本环节。为了保证冶炼和浇
铸的正常运行,转炉车间主要包括原料系统(铁水、废钢和散 装料的存放和供应),加料、冶炼和浇铸系统。此外,还有炉
转炉一次除尘设备简介

转炉一次除尘设备简介转炉一次除尘设备是转炉炼钢不可缺少的工艺除尘环节,目前国内转炉一次除尘设备分为以下几种:一、两文三脱式两文三脱式分为两种型式:A 一级溢流文氏管+重力脱水器+二级R-D阀可调文氏管+90°弯头脱水器+丝网脱水器B一级溢流文氏管+重力脱水器+二级环缝(重砣)可调文氏管+90°弯头脱水器+丝网脱水器据以往工程经验来看,上述B型式较优于A型,A型除尘效果能达排放70mg/Nm3,目前已经逐步淘汰;B型除尘效果能达到排放50 mg/Nm3,能确保排放达标。
这两种型式的除尘系统其电耗和水耗相当。
排放标准参见《炼钢工业大气污染物排放标准》GB28664-2012。
二、塔文式塔文式系统是由高效洗涤塔+重力脱水器+环缝文氏管+90°弯头脱水器+丝网脱水器组成,是目前较为常用的除尘方式,其优点主要在于电耗较低(与两文三脱式对比)。
高效洗涤塔较一级溢流文氏管除尘效果略差,但其阻损可低至500Pa(一级溢流文氏管设计阻损3000-5000Pa),能很大的缓解除尘风机的负荷,降低电耗。
对于系统的节水问题,严格来说,塔文式较两文三脱式节水并不明显,一些设计单位所述说的节水,仅是为了推广塔文除尘系统进行的误导而已。
究其原因在于两文三脱除尘系统在设计之初倡导的是用水多除尘效果更好,但实际上用水量可以降低。
另外,从热传递角度来看,定量的高温烟气降温至同样的温度,两种型式的除尘系统理论用水量是一样的。
塔文式除尘效果能达到排放50 mg/Nm3,能确保排放达标。
排放标准参见《炼钢工业大气污染物排放标准》GB28664-2012。
三、干法除尘式转炉煤气干法除尘是较为新型的除尘结构,其工艺流程为:转炉高温烟气在风机作用下经汽化冷却烟道冷却后的干烟气进入蒸发冷却器,由其对烟气进行灭火、降温、粗除尘,约计250度的烟气而后进入地面的静电除尘器进行精除尘,再经高温风机后进入煤气切换站:当不满足煤气回收条件时打到放散侧进行煤气放散点火;当满足煤气回收条件时打到回收侧,烟气经再一步降温后进入煤气柜区进行回收。
转炉设备概述
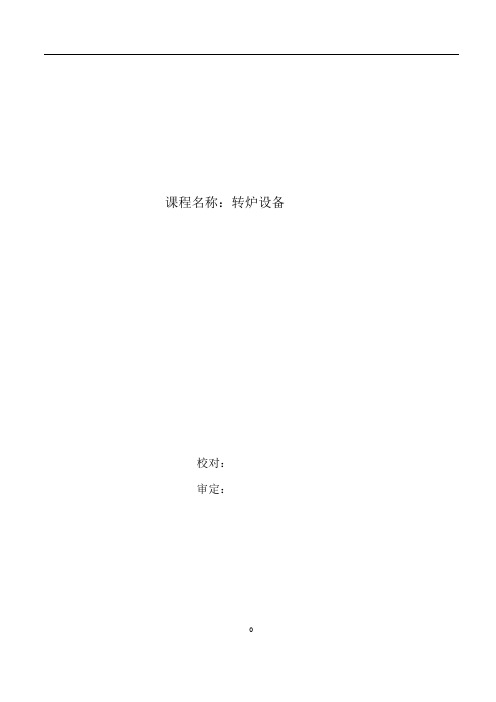
课程名称:转炉设备校对:审定:目录:前言2页第一章:培训目的第一节底子常识目标2页第二节能力目标2页第二章:转炉设备第一节转炉炼钢设备组成方框图- 4页第二节顶底复吹转炉炼钢设备特点 5页第三节转炉出产工艺流程图 6页第四节转炉设备的组成 5页第四章转炉设备安装、试车第一节制作单元预装 15-16页第二节现场设备安装 16-17页第三节空载荷试运转 17-18页第四节转炉试运转应满足的条件和技术要求 18页第五章转炉开新炉和冶炼第一节转炉开新炉需要具备的条件 18页第二节冶炼过程中的操作要求 18-19页第三节设备动行中故障的排除方法 19页第四节操作过程中紧急状态下的处置方法 20页第五节设备交接班规定 21页第六章转炉设备常见问题和解决方法 21--23页1前言按照分厂培训方案编写了这本教材,以便我们一起共同掌握转炉炼钢主要工艺设备和机械设备的相关常识和主要工艺操作技能、解决常见的故障处置方法,通过培训能够更进一步的提高使用和维护转炉炼钢设备的能力,并使我们的操作工人和点检员阐发和排除故障的能力有所提高。
同时,通过学习,进一步让点检人员了解如何更好的与一线员工的沟通。
2第一章培训目标第一节底子常识目标1了解氧气顶吹转炉设备组成和配套设备的构造。
1熟悉和掌握转炉设备布局、工艺参数、设备操作和维护。
第二节能力目标1了解转炉设备选型依据、设备布局特点等方面的能力。
1对转炉设备发生故障的问题点有准确判断能力。
1提高杜绝转炉设备故障、减少故障、处置故障的能力。
第二章转炉设备第一节转炉炼钢设备组成方框图3第二节顶底复吹转炉炼钢设备特点1、冶炼时间短,出产效率高,一般20—40分钟吹氧即可完成一炉钢水的冶炼。
而平炉那么需要5—6小时才能完成一炉钢的冶炼。
2、投资少、成本低、施工速度快。
一座顶底复吹转炉的投资只有平炉的70%摆布。
冶炼的品种也比平炉广。
3、顶底复吹可以有效的改变熔池的搅拌力,可以减少喷溅,提高收得率。
转炉的设备与工艺
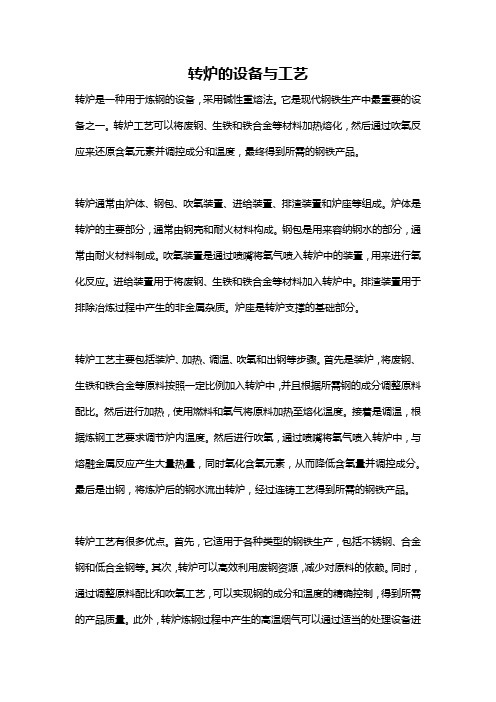
转炉的设备与工艺转炉是一种用于炼钢的设备,采用碱性重熔法。
它是现代钢铁生产中最重要的设备之一。
转炉工艺可以将废钢、生铁和铁合金等材料加热熔化,然后通过吹氧反应来还原含氧元素并调控成分和温度,最终得到所需的钢铁产品。
转炉通常由炉体、钢包、吹氧装置、进给装置、排渣装置和炉座等组成。
炉体是转炉的主要部分,通常由钢壳和耐火材料构成。
钢包是用来容纳钢水的部分,通常由耐火材料制成。
吹氧装置是通过喷嘴将氧气喷入转炉中的装置,用来进行氧化反应。
进给装置用于将废钢、生铁和铁合金等材料加入转炉中。
排渣装置用于排除冶炼过程中产生的非金属杂质。
炉座是转炉支撑的基础部分。
转炉工艺主要包括装炉、加热、调温、吹氧和出钢等步骤。
首先是装炉,将废钢、生铁和铁合金等原料按照一定比例加入转炉中,并且根据所需钢的成分调整原料配比。
然后进行加热,使用燃料和氧气将原料加热至熔化温度。
接着是调温,根据炼钢工艺要求调节炉内温度。
然后进行吹氧,通过喷嘴将氧气喷入转炉中,与熔融金属反应产生大量热量,同时氧化含氧元素,从而降低含氧量并调控成分。
最后是出钢,将炼炉后的钢水流出转炉,经过连铸工艺得到所需的钢铁产品。
转炉工艺有很多优点。
首先,它适用于各种类型的钢铁生产,包括不锈钢、合金钢和低合金钢等。
其次,转炉可以高效利用废钢资源,减少对原料的依赖。
同时,通过调整原料配比和吹氧工艺,可以实现钢的成分和温度的精确控制,得到所需的产品质量。
此外,转炉炼钢过程中产生的高温烟气可以通过适当的处理设备进行能量回收,实现能源的节约和环境保护。
然而,转炉工艺也存在一些问题。
首先,转炉冶炼周期长,通常需要数小时至数十小时,导致炼钢工艺的灵活性较差。
其次,转炉冶炼过程中产生的废气和废渣含有一定的有害物质,需要采取适当的措施进行处理和处置。
此外,由于转炉冶炼温度较高,设备寿命相对较短,需要定期进行维护和更换。
综上所述,转炉是一种重要的炼钢设备,通过碱性重熔工艺可以将废钢、生铁和铁合金等原料加热熔化,并通过吹氧反应调控成分和温度,最终得到所需的钢铁产品。
转炉炼钢主要工艺设备

艾默伊登
转炉炼钢主要工艺设备
杨暕
1、转炉设备
❖ 转炉 ❖ 装料行车 ❖ 出钢台车 ❖ 测温取样装置 ❖ 氧枪装置 ❖ 副枪装置 ❖ 氧气柜 ❖ 氮气柜
转炉炼钢车间设备组成
氧气顶吹转炉总图
2、OG设备
❖ 文氏管 ❖ 脱水器 ❖ 引风机 ❖ 煤气柜
3、脱硫设备
❖ 混铁车 ❖ 脱硫装置 ❖ 排渣设备
❖ 混铁车一般容量为转炉的整数倍,我国最大260t、300t 。国外最理设备
❖ 铁粒回收装置
❖ ICS处理工艺:在钢渣车间设置高架泼渣盘,利用吊车将渣罐内液态钢
渣泼在渣盘内.渣层一般为30一120mm厚,然后喷以适量的水促使急冷破 裂。再将碎渣翻倒在渣车上,驱车至池边喷水降温,再将渣卸至水池内进一 步降温冷却。渣子粒度一般为5-100mm,最后用抓斗抓出装车,送至钢渣 处理车间,进行从大块破碎到小块,进入球磨机进行研磨,达到一定细度的, 用砂浆泵打入高频筛,筛分,筛下物进入磁选机磁选,不上磁的在进入重选, 摇床和螺旋溜槽比重进行分出,出来的品位可达到64%以上,钢厂三次回收 进入炼钢。
6、铁合金及副原料加料车
❖ 铁合金料仓 ❖ 副原料料仓 ❖ 称量设备 ❖ 皮带运输机
全胶带上料系统
7、RH 真空脱气设备
❖ 铁合金加料设备 ❖ 脱气槽 ❖ 真空设备 ❖ 钢水罐台车 ❖ 测温取样装置
RH 真空脱气设备示意图
8、铸锭设备
❖ 铸锭车 ❖ 钢锭模 ❖ 铸锭行车 ❖ 整脱模设备
连铸设备
倾翻机构、车体 ❖ 现代炼钢常用设备。
4、受铁设备
❖ 铁水罐 ❖ 铁水排渣机 ❖ 铁水罐台车 ❖ 测温取样装置
5、废钢装料设备
❖ 废钢槽 ❖ 电磁吊车 ❖ 用电磁吊车的主钩和副钩吊起废钢料槽,靠 主、 副钩的联合动作把废钢加入转炉。这种 方式的平台结构和设备都比较简单,废钢吊车 与兑铁水吊车可以共用,但一次只能吊起一槽 废钢,并且废钢吊车与兑铁水吊车之间的干扰 较大。 ❖ 废钢料槽:废钢料槽是钢板焊接的一端开口、 底部呈平面的长簸箕状槽。在料槽前部和后部 的两侧有两对吊挂轴,供吊车的主、副钩吊挂 料槽。
转炉的构造及主要尺寸

立志当早,存高远
转炉的构造及主要尺寸
转炉由炉体、燃油装置、炉口、转动装置、炉尾烟道、余热利用设备等主要部分组成。
一、炉体。
炉体为圆筒形,卧式,用锅炉钢板焊成,两端钢板与圆筒用螺钉联结固定,一端设重油燃烧孔,一端炉尾烟道与水平固定烟道相接。
二、重油燃烧系统。
采用100 号重油作燃料。
燃烧系统包括下述主要设备:齿轮油泵、流量计、压力式温度计、电加热器、减压阀、低压油嘴等。
三、炉口。
炉口在转炉中部,如图1 所示。
炉口有两个作用:炉料从炉口装入炉内:熔体(粗铋、冰铜、炉渣)从炉口放出。
四、转动装置。
用4.5 千瓦电动机经减速箱后,以6 分/转的转速转动炉体至任意位置。
五、炉尾烟道。
转炉炉头安装重油喷嘴,炉尾设烟道排送烟气,炉尾烟遭与水平固定烟道之间,用法兰盘螺钉密封联接,其联接部位示意图如图1 所示:
图1 铋转炉烟道接口示意图
1-固定部分;2-转动部分;3-接口部分
六、余热利用设备。
转炉炉尾烟气温度在1150℃左右,在水平固定烟遭中安装套管式换热器,如图2 所示。
铜转炉总结

铜转炉总结简介铜转炉是一种用于冶炼铜的设备,广泛应用于冶金工业。
它通过高温熔化原料,将其中的铜分离出来,用于后续加工。
本文将对铜转炉的工作原理、优缺点以及应用领域进行总结。
工作原理铜转炉的工作原理基于冶金学中的炼铜过程。
它通常由一个高炉筒和一个燃烧室组成。
1.加料:原料包括铜矿石和其他辅助材料,如焦炭。
它们被投入到高炉筒中。
2.燃烧:燃烧室中的燃料(通常是煤或天然气)被点燃,产生高温火焰。
3.炉料溶解:高温火焰使原料在高炉筒内熔化。
矿石中的铜以及其他金属被溶解并与其他成分分离。
4.分离:熔融的原料进入下部的渣池,铜和其他金属沉积到底部,而渣浮在上面。
通过调整流速和温度,分离程度可以控制。
5.出料:底部的铜被定期抽出,用于进一步加工。
优点铜转炉具有以下优点:1.高效:铜转炉具有高效的熔化和分离过程。
高温火焰可以快速溶解铜矿石,使得冶炼过程更加迅速。
2.可控性强:通过调整流速和温度等参数,可以准确控制分离程度。
这使得冶金工程师能够根据需要调整铜的纯度。
3.辅助材料利用率高:铜转炉可以利用多种辅助材料,如焦炭。
这些材料可以在高温条件下充分燃烧,提供能量,同时减少浪费。
4.适应性强:铜转炉适用于不同的铜矿石和炉料成分。
它可以应对不同原料的变化,适应不同矿石的含铜量和成分。
缺点铜转炉存在一些缺点:1.能耗较高:高温火焰需要大量能量供应,这意味着铜转炉需要大量的电力或燃料。
这增加了生产成本并产生环境影响。
2.渣产生:铜转炉过程中产生大量渣料。
处理和处理这些渣料需要额外的成本和资源。
3.对环境的影响:燃烧过程产生的废气和废水可能对环境造成污染。
处理这些废物需要额外的环保措施。
应用领域1.冶金工业:铜转炉广泛应用于冶金工业中的铜冶炼过程。
它是生产纯铜的重要设备。
2.金属加工:从铜转炉中提取的铜可以用于金属加工。
它可以被铸造成不同形状的铜制品,也可以用于制造电线、管道等。
3.电子行业:铜是电子器件的重要材料,铜转炉提供了大量高纯度铜供应,满足电子行业的需求。
转炉系统设备相关知识
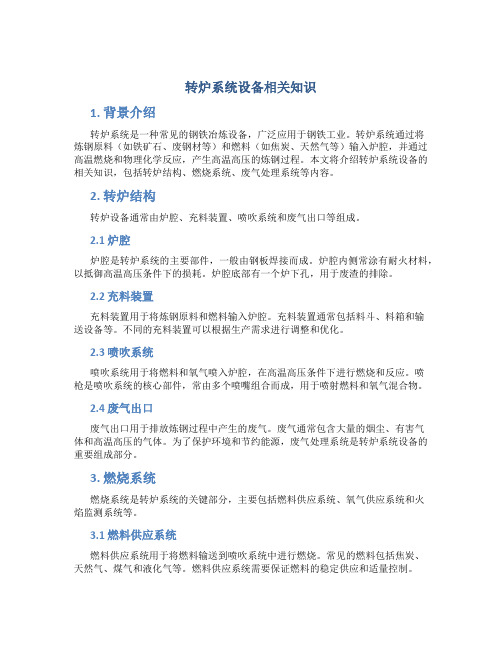
转炉系统设备相关知识1. 背景介绍转炉系统是一种常见的钢铁冶炼设备,广泛应用于钢铁工业。
转炉系统通过将炼钢原料(如铁矿石、废钢材等)和燃料(如焦炭、天然气等)输入炉腔,并通过高温燃烧和物理化学反应,产生高温高压的炼钢过程。
本文将介绍转炉系统设备的相关知识,包括转炉结构、燃烧系统、废气处理系统等内容。
2. 转炉结构转炉设备通常由炉腔、充料装置、喷吹系统和废气出口等组成。
2.1 炉腔炉腔是转炉系统的主要部件,一般由钢板焊接而成。
炉腔内侧常涂有耐火材料,以抵御高温高压条件下的损耗。
炉腔底部有一个炉下孔,用于废渣的排除。
2.2 充料装置充料装置用于将炼钢原料和燃料输入炉腔。
充料装置通常包括料斗、料箱和输送设备等。
不同的充料装置可以根据生产需求进行调整和优化。
2.3 喷吹系统喷吹系统用于将燃料和氧气喷入炉腔,在高温高压条件下进行燃烧和反应。
喷枪是喷吹系统的核心部件,常由多个喷嘴组合而成,用于喷射燃料和氧气混合物。
2.4 废气出口废气出口用于排放炼钢过程中产生的废气。
废气通常包含大量的烟尘、有害气体和高温高压的气体。
为了保护环境和节约能源,废气处理系统是转炉系统设备的重要组成部分。
3. 燃烧系统燃烧系统是转炉系统的关键部分,主要包括燃料供应系统、氧气供应系统和火焰监测系统等。
3.1 燃料供应系统燃料供应系统用于将燃料输送到喷吹系统中进行燃烧。
常见的燃料包括焦炭、天然气、煤气和液化气等。
燃料供应系统需要保证燃料的稳定供应和适量控制。
3.2 氧气供应系统氧气供应系统是转炉系统的重要组成部分,用于向喷吹系统中提供所需的氧气。
氧气供应系统需要保证氧气的稳定供应和压力控制,以确保燃烧过程的正常进行。
3.3 火焰监测系统火焰监测系统用于监测和控制炉腔内的火焰状态。
通过监测火焰温度、颜色和形态等参数,可以判断燃烧过程的稳定性和效果,并及时进行调整和优化。
4. 废气处理系统废气处理系统是转炉系统设备的重要组成部分,主要用于处理和净化炼钢过程中产生的废气。
转炉系统机械设备概述
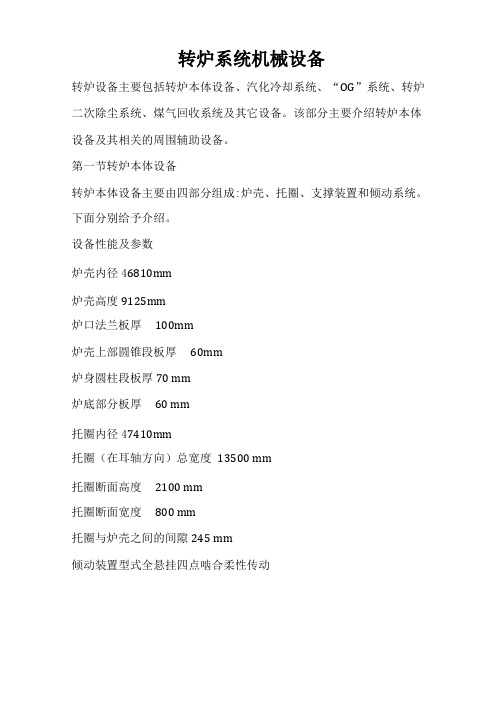
转炉系统机械设备转炉设备主要包括转炉本体设备、汽化冷却系统、“OG”系统、转炉二次除尘系统、煤气回收系统及其它设备。
该部分主要介绍转炉本体设备及其相关的周围辅助设备。
第一节转炉本体设备转炉本体设备主要由四部分组成:炉壳、托圈、支撑装置和倾动系统。
下面分别给予介绍。
设备性能及参数炉壳内径46810mm炉壳高度9125mm炉口法兰板厚100mm炉壳上部圆锥段板厚60mm炉身圆柱段板厚70 mm炉底部分板厚60 mm托圈内径47410mm托圈(在耳轴方向)总宽度13500 mm托圈断面高度2100 mm托圈断面宽度800 mm托圈与炉壳之间的间隙245 mm倾动装置型式全悬挂四点啮合柔性传动倾动装置总速比73.48X7.118=523,031倾动电机总功率(4台交流变频电机)132X4=528 kW设备重量约500t 一、炉壳炉壳主要由炉口、上下部圆锥段、圆柱炉身段及锥柱间、锥球间均匀过渡用的园环段和球形炉底等部分组成。
炉口由4块(2#、3#转炉炉口为6块)内埋蛇形管冷却的耐热球墨铸铁扇形段拼装而成,易于更换。
上部圆锥段的顶部焊有加筋法兰,供固定炉口扇形段用。
上部圆锥段外表面半割管(2#、3#转炉为角钢)焊接成冷却水循环通道。
在出钢口上下焊有两圈法兰,中间联有立筋,用于安装炉体支撑装置。
二、托圈托圈为焊接箱形结构,其内部通循环水冷却。
耳轴为空心,以容纳供托圈冷却水、炉口冷却水、炉帽冷却水及转炉底吹供气管道。
设备重量约为222.7吨。
托圈的前后共有12个通气孔,托圈同炉壳的间隙为225mm。
托圈耳轴同大齿轮的联接靠切向键,配合为间隙配合,①950e7。
托圈焊接部分材质为16乂的耳轴材质为20MnMoNb。
两侧的轴承座分别称作驱动端轴承座和非驱动端轴承座,驱动端轴承座为固定式,非驱动端为铰支结构,以缓解托圈热胀冷缩及在重力作用下的变形。
轴承的型号为240/1060 CAF/W33 (SKF)。
轴承的润滑为稀油润滑(2#、3#转炉为干油润滑)。
转炉工作原理

转炉工作原理
转炉是一种用于钢铁冶炼的设备,其工作原理主要包括以下几个步骤。
首先,转炉会预热并预处理废钢。
废钢通常包括废旧钢材、废钢屑等。
这些废钢会被切碎并清理,然后送入转炉。
预热的目的是提高废钢的温度,以加快冶炼过程。
接下来,废钢被加入到转炉中,并加入适量的石灰石和焦炭。
石灰石的作用是与废钢中的杂质反应,形成熔渣,将杂质分离出去。
而焦炭则为提供还原剂,帮助将铁氧化物还原为金属铁。
在高温下,转炉内部的氧气被吹入,氧气与废钢中的碳反应,产生大量的热量。
这样的高温环境下,废钢中的铁和其他成分开始熔化并混合在一起。
熔融的废钢逐渐转变为炉渣和钢水。
炉渣是由废钢中的氧化物、碱金属和杂质等组成,可通过与废钢的比重差异,从钢水中分离出来。
而钢水则是由熔化的废钢中的金属铁和其他合金元素组成,钢水会流出转炉底部的铁口。
最后,钢水被收集并送往连铸机进行连铸成型。
连铸机会将钢水注入到多个铸模中,使其快速冷却并形成连铸坯。
这些连铸坯可进一步加工成不同形状和尺寸的钢材。
总的来说,转炉的工作原理是通过在高温、高氧气环境下,利用石灰石和焦炭的反应产生的热量和还原剂的作用,使废钢熔
化,并将其中的杂质分离出去,最终得到熔融的钢水,再通过连铸工艺将其加工成为实际应用的钢材。
转炉(zhuanlu)基本知识
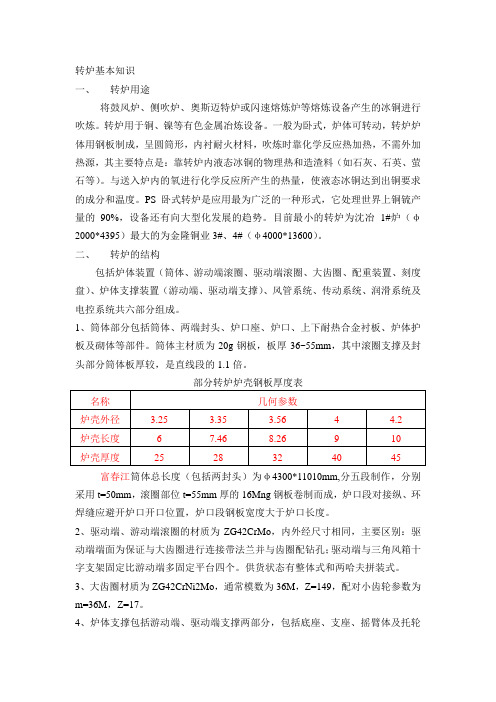
转炉基本知识一、转炉用途将鼓风炉、侧吹炉、奥斯迈特炉或闪速熔炼炉等熔炼设备产生的冰铜进行吹炼。
转炉用于铜、镍等有色金属冶炼设备。
一般为卧式,炉体可转动,转炉炉体用钢板制成,呈圆筒形,内衬耐火材料,吹炼时靠化学反应热加热,不需外加热源,其主要特点是:靠转炉内液态冰铜的物理热和造渣料(如石灰、石英、萤石等)。
与送入炉内的氧进行化学反应所产生的热量,使液态冰铜达到出铜要求的成分和温度。
PS卧式转炉是应用最为广泛的一种形式,它处理世界上铜锍产量的90%,设备还有向大型化发展的趋势。
目前最小的转炉为沈冶1#炉(φ2000*4395)最大的为金隆铜业3#、4#(φ4000*13600)。
二、转炉的结构包括炉体装置(筒体、游动端滚圈、驱动端滚圈、大齿圈、配重装置、刻度盘)、炉体支撑装置(游动端、驱动端支撑)、风管系统、传动系统、润滑系统及电控系统共六部分组成。
1、筒体部分包括筒体、两端封头、炉口座、炉口、上下耐热合金衬板、炉体护板及砌体等部件。
筒体主材质为20g钢板,板厚36~55mm,其中滚圈支撑及封头部分筒体板厚较,是直线段的1.1倍。
部分转炉炉壳钢板厚度表富春江筒体总长度(包括两封头)为φ4300*11010mm,分五段制作,分别采用t=50mm,滚圈部位t=55mm厚的16Mng钢板卷制而成,炉口段对接纵、环焊缝应避开炉口开口位置,炉口段钢板宽度大于炉口长度。
2、驱动端、游动端滚圈的材质为ZG42CrMo,内外经尺寸相同,主要区别:驱动端端面为保证与大齿圈进行连接带法兰并与齿圈配钻孔;驱动端与三角风箱十字支架固定比游动端多固定平台四个。
供货状态有整体式和两哈夫拼装式。
3、大齿圈材质为ZG42CrNi2Mo,通常模数为36M,Z=149,配对小齿轮参数为m=36M,Z=17。
4、炉体支撑包括游动端、驱动端支撑两部分,包括底座、支座、摇臂体及托轮装置等部件,其中驱动端支撑中含小齿轮装配,驱动端托轮有轮缘,游动端无。
2.1炉体设备部分
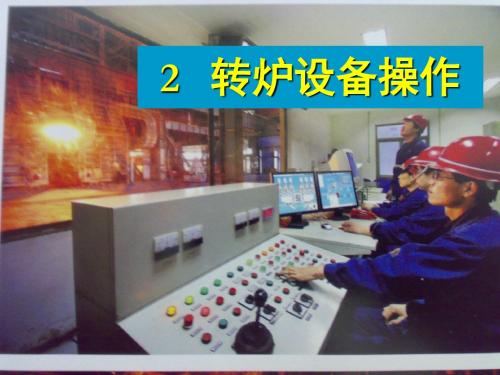
B 类型
(1)滑动轴承 优点: 滑动轴承便于制造、安装,所以小 型转炉上用的较多。 缺点:轴承无自动调心作用,托圈变形后 磨损很快。 (2)球面调心滑动轴承 球面调心滑动轴承是滑动轴承改进后的 结构,磨损有所减少。
(3)自动调心双列圆柱滚子轴承 自动调心双列圆柱滚子轴承,能补偿 耳轴由于托圈翘曲和制造安装不准确而引 起的不同心度和不平行度。该轴承结构如 图9-14所示 。
(2) 炉壳的组成:
锥形炉帽 圆柱形炉身 炉底
(3) 制作: 各部分用钢板成型后,再焊成整体。 三部分联接的转折处必须以不同曲率的圆 滑曲线来联接,以减少应力集中。
(4) 要求: 为了适应转炉高温作业频繁的特点, 要求转炉炉壳必须具有足够的强度和刚度, 在高温下不变形、在热应力作用下不破裂。 考虑到炉壳各部位受力的不均衡,炉帽、 炉身、炉底应选用不同厚度钢板,特别是 对大转炉来说更应如此。炉壳各部位钢板 的厚度可根据经验选定。
C 全悬挂式倾动机构
(1) 结构 全悬挂式倾动 机构,是把转炉传 动的二次减速器的 大齿轮悬挂在转炉 耳轴上,而电动机、 制动器、一级减速 器都装在悬挂大齿 轮的箱体上。
(2)特点 全悬挂式倾动机 构具有结构紧凑、重量 轻、占地面积小、运转 安全可靠、工作性能好 的特点。但由于增加了 啮合点,加工、调整和 对轴承质量的要求都较 高。这种倾动机构多为 大型转炉所采用。我国 上海宝钢的300 t、首钢 的210 t转炉均采用了全 悬挂式倾动机构。
① 接近水平位置时——慢速 ② 当转炉空炉、或从水平位置摇直、或刚 从垂直位置摇下时,均可用较高的倾动速 度,以减少辅助时间。 倾动速度范围如下: 小于30 t的转炉:可以不调速,倾动转速为 0.7r/min; 50~100 t转炉可采用两级转速,低速为 0.2r/min,高速为0.8r/min; 大于150t的转炉可无级调速,转速在0.15~ 1.5r/min。
转炉的介绍 冶炼设备
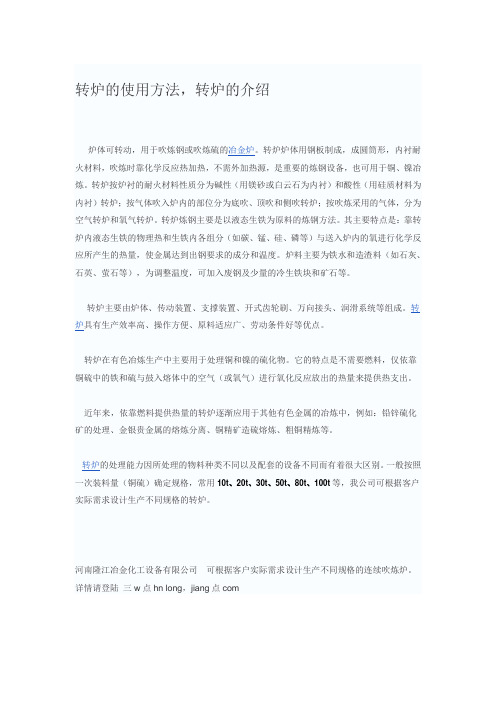
转炉的使用方法,转炉的介绍炉体可转动,用于吹炼钢或吹炼硫的冶金炉。
转炉炉体用钢板制成,成圆筒形,内衬耐火材料,吹炼时靠化学反应热加热,不需外加热源,是重要的炼钢设备,也可用于铜、镍冶炼。
转炉按炉衬的耐火材料性质分为碱性(用镁砂或白云石为内衬)和酸性(用硅质材料为内衬)转炉;按气体吹入炉内的部位分为底吹、顶吹和侧吹转炉;按吹炼采用的气体,分为空气转炉和氧气转炉。
转炉炼钢主要是以液态生铁为原料的炼钢方法。
其主要特点是:靠转炉内液态生铁的物理热和生铁内各组分(如碳、锰、硅、磷等)与送入炉内的氧进行化学反应所产生的热量,使金属达到出钢要求的成分和温度。
炉料主要为铁水和造渣料(如石灰、石英、萤石等),为调整温度,可加入废钢及少量的冷生铁块和矿石等。
转炉主要由炉体、传动装置、支撑装置、开式齿轮刷、万向接头、润滑系统等组成。
转炉具有生产效率高、操作方便、原料适应广、劳动条件好等优点。
转炉在有色冶炼生产中主要用于处理铜和镍的硫化物。
它的特点是不需要燃料,仅依靠铜硫中的铁和硫与鼓入熔体中的空气(或氧气)进行氧化反应放出的热量来提供热支出。
近年来,依靠燃料提供热量的转炉逐渐应用于其他有色金属的冶炼中,例如:铅锌硫化矿的处理、金银贵金属的熔炼分离、铜精矿造硫熔炼、粗铜精炼等。
转炉的处理能力因所处理的物料种类不同以及配套的设备不同而有着很大区别。
一般按照一次装料量(铜硫)确定规格,常用10t、20t、30t、50t、80t、100t等,我公司可根据客户实际需求设计生产不同规格的转炉。
河南隆江冶金化工设备有限公司可根据客户实际需求设计生产不同规格的连续吹炼炉。
详情请登陆三w点hn long,jiang点com。
转炉基本概念和设备学习
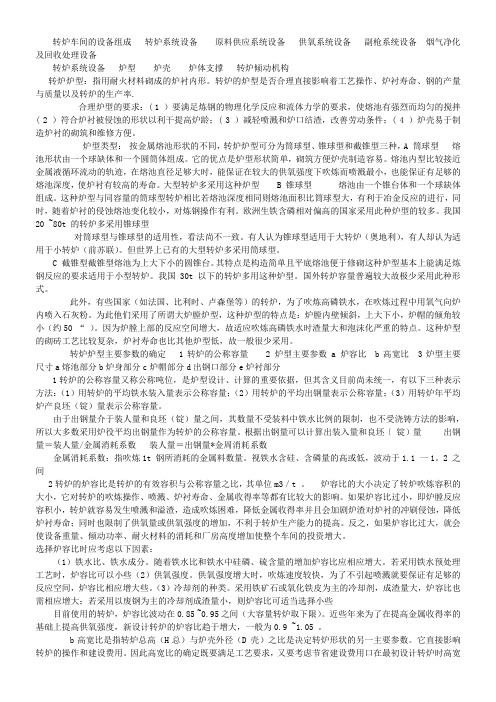
转炉车间的设备组成转炉系统设备原料供应系统设备供氧系统设备副枪系统设备烟气净化及回收处理设备转炉系统设备炉型炉壳炉体支撑转炉倾动机构转炉炉型:指用耐火材料砌成的炉衬内形。
转炉的炉型是否合理直接影响着工艺操作、炉衬寿命、钢的产量与质量以及转炉的生产率.合理炉型的要求:( 1 )要满足炼钢的物理化学反应和流体力学的要求,使熔池有强烈而均匀的搅拌( 2 )符合炉衬被侵蚀的形状以利干提高炉龄;( 3 )减轻喷溅和炉口结渣,改善劳动条件;( 4 )炉壳易于制造炉衬的砌筑和维修方便。
炉型类型:按金属熔池形状的不同,转炉炉型可分为筒球型、锥球型和截锥型三种,A 筒球型熔池形状由一个球缺体和一个圆筒体组成。
它的优点是炉型形状简单,砌筑方便炉壳制造容易。
熔池内型比较接近金属液循环流动的轨迹,在熔池直径足够大时,能保证在较大的供氧强度下吹炼而喷溅最小,也能保证有足够的熔池深度,使炉衬有较高的寿命。
大型转炉多采用这种炉型 B 锥球型熔池由一个锥台体和一个球缺体组成。
这种炉型与同容量的筒球型转炉相比若熔池深度相同则熔池面积比筒球型大,有利于冶金反应的进行,同时,随着炉衬的侵蚀熔池变化较小,对炼钢操作有利。
欧洲生铁含磷相对偏高的国家采用此种炉型的较多。
我国20 ~80t 的转炉多采用锥球型对筒球型与锥球型的适用性,看法尚不一致。
有人认为锥球型适用于大转炉(奥地利),有人却认为适用于小转炉(前苏联)。
但世界上已有的大型转炉多采用筒球型。
C 截锥型截锥型熔池为上大下小的圆锥台。
其特点是构造简单且平底熔池便于修砌这种炉型基本上能满足炼钢反应的要求适用于小型转炉。
我国30t 以下的转炉多用这种炉型。
国外转炉容量普遍较大故极少采用此种形式。
此外,有些国家(如法国、比利时、卢森堡等)的转炉,为了吹炼高磷铁水,在吹炼过程中用氧气向炉内喷入石灰粉。
为此他们采用了所谓大炉膛炉型,这种炉型的特点是:炉膛内壁倾斜,上大下小,炉帽的倾角较小(约50 “)。
转炉炼钢设备与工艺
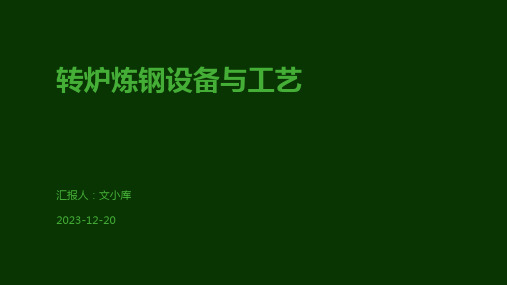
转炉炼钢设备应用领域
钢铁工业
用于生产高质量钢材,满足汽车、建筑、机械制 造等领域的需求。
国防建设
用于生产特殊钢材,满足武器装备制造的需求。
其他领域
还可应用于航空航天、能源等领域。
02
转炉炼钢工艺流程
原料准备与配料
原料准备
准备铁水、废钢、合金等原料,确保 原料质量和成分符合要求。
配料计算
根据钢种和冶炼要求,计算出各种原 料的加入量,确保钢水成分和温度的 稳定。
1 2
设备检查
操作前应对转炉设备进行全面检查,确保设备处 于良好状态。
严格遵守操作规程
按照规定的操作步骤进行操作,避免违规操作。
3
定期维护保养
对设备进行定期维护保养,确保设备正常运行。
转炉炼钢工艺环保要求及措施
减少废气排放
采用低硫、低磷、低氮 等环保型炼钢原料,降 低废气排放。
废水处理
对产生的废水进行分类 处理,实现废水零排放 。
维修保养
根据设备的使用情况和维修计划,进 行维修和保养工作,确保设备的正常 运行。
定期检查
定期对设备进行检查,包括关键部位 的检查和测量,确保设备处于良好状 态。
转炉炼钢设备故障排除方法
故障诊断
对设备出现的故障进行诊断,确 定故障的原因和部位。
排除故障
根据故障诊断结果,采取相应的措 施排除故障,恢复设备的正常运行 。
根据钢种和冶炼要求,向钢水中加入合金元素(如铬、镍、钨等),调整钢水成 分,以满足产品要求。
浇注与凝固过程
浇注
将脱氧和合金化后的钢水浇注到钢锭模或连铸结晶器中,形 成钢锭或连铸坯。
凝固
通过控制冷却速度和温度,使钢锭或连铸坯在凝固过程中形 成合理的晶粒结构和机械性能。
- 1、下载文档前请自行甄别文档内容的完整性,平台不提供额外的编辑、内容补充、找答案等附加服务。
- 2、"仅部分预览"的文档,不可在线预览部分如存在完整性等问题,可反馈申请退款(可完整预览的文档不适用该条件!)。
- 3、如文档侵犯您的权益,请联系客服反馈,我们会尽快为您处理(人工客服工作时间:9:00-18:30)。
课程名称:转炉设备编制:校对:审定:目录:前言2页第一章:培训目的第一节基本知识目标2页第二节能力目标2页第二章:转炉设备第一节转炉炼钢设备组成方框图- 4页第二节顶底复吹转炉炼钢设备特点 5页第三节转炉生产工艺流程图 6页第四节转炉设备的组成5页第四章转炉设备安装、试车第一节制作单位预装15-16页第二节现场设备安装16-17页第三节空载荷试运转17-18页第四节转炉试运转应满足的条件和技术要求18页第五章转炉开新炉和冶炼第一节转炉开新炉需要具备的条件 18页第二节冶炼过程中的操作要求 18-19页第三节设备动行中故障的排除方法 19页第四节操作过程中紧急状态下的处理方法 20页第五节设备交接班规定 21页第六章转炉设备常见问题和解决办法 21--23页前言根据分厂培训计划编写了这本教材,以便我们一起共同掌握转炉炼钢主要工艺设备和机械设备的相关知识和主要工艺操作技能、解决常见的故障处理方法,通过培训能够更进一步的提高使用和维护转炉炼钢设备的能力,并使我们的操作工人和点检员分析和排除故障的能力有所提高。
同时,通过学习,进一步让点检人员了解如何更好的与一线员工的沟通。
第一章培训目标第一节基本知识目标1.1.1了解氧气顶吹转炉设备组成和配套设备的构造。
1.1.2熟悉和掌握转炉设备结构、工艺参数、设备操作和维护。
第二节能力目标1.2.1了解转炉设备选型依据、设备结构特点等方面的能力。
1.2.2对转炉设备发生故障的问题点有准确判断能力。
1.2.3提高杜绝转炉设备故障、减少故障、处理故障的能力。
第二章转炉设备第一节转炉炼钢设备组成方框图第二节顶底复吹转炉炼钢设备特点1、冶炼时间短,生产效率高,一般20—40分钟吹氧即可完成一炉钢水的冶炼。
而平炉则需要5—6小时才能完成一炉钢的冶炼。
2、投资少、成本低、施工速度快。
一座顶底复吹转炉的投资只有平炉的70%左右。
冶炼的品种也比平炉广。
3、顶底复吹可以有效的改变熔池的搅拌力,可以减少喷溅,提高收得率。
4、吹氧设备和除尘设备需要较高的厂房第三节转炉生产工艺流程图第四节转炉设备的组成3.2.1顶底复吹转炉炼钢是以转炉主体设备、供氧系统设备、铁水供应系统设备、散状料供应设备、废钢供应设备、铁合金供应设备、出渣出钢设备、烟气净化冷却回收系统设备、及修炉机械设备。
3.2.2转炉主体设备是由炉体、托圈、炉体支撑装置、倾动机构等组成。
1、炉帽:做成上小下大截圆锥形或球缺截圆锥形的目的是减少吹炼时的喷溅和热量损失,有利于炉气的排出;由于炉帽接近高温炉气,炉气温度可以达到1300—1400℃,并且直接受喷溅物烧损,为了防止炉帽和炉口变形,普遍采用水冷形式,但是存在缺点就是炉口容易被钢水烧坏,造成漏水,如果不注意就会引起爆炸,造成事故,因此需要非常注意水冷炉口的质量和维护及规范化操作。
2、水冷炉口:国内一般采用焊接和铸造两种结构1)焊接水箱式制作容易,冷却强度大,工作效率高,但是比埋管铸造式容易引起烧穿,且在制作时不注意就会造成水箱上部积气引起爆炸(必须将回水管路的出水接近水箱的顶部)。
2)埋管铸造式一般采用无缝钢管弯曲成蛇形埋铸于球墨铸铁或耐热铸铁中,这种结构安全性和寿命均比焊接水箱式炉口高,但是制作困难(也有采用分体埋管铸造式)3、炉身一般为圆柱形,40T以上转炉炉身钢板一般采用16Mn或16MnNb,并且在整体焊接结束后进行整体退火去除应力,炉身上出钢口设计为可拆卸链接形式(便于修栖、维护、更换方便、堵出钢口方便等)。
4、炉底有圆锥形和球形两种,球形炉底的制作困难砌筑复杂,但是壳体受载情况好,一般大型转炉(80T)以上采用。
也有采用大活炉底和小活炉底形式,使用吊架丁字型销钉和楔板链结,这种链结形式结构简单,拆卸方便,同时切记销钉和楔板不能采用碳素钢,最好使用低合金钢,避免楔板打弯或销钉顶部端口出现毛刺。
5、托圈托圈是转炉的重要承载和传动部件,它在工作中承受炉体、炉衬、钢水和自重,还承受频繁启动、制动所产生的冲击负荷,同时来自于炉体的热辐射而引起的托圈的径向、圆周、轴向所产生的热负荷。
托圈一般采用钢板焊接成箱型断面的环形结构,两侧焊接铸钢耳轴座,耳轴装在耳轴座内,耳轴材料一般采用合金钢,锻造毛坯后进行加工和退火。
6、耳轴与托圈的链结一般采用三种链接方式:1)法兰螺栓链结(采用过度配合装入托圈的铸造耳轴座中,用螺栓和圆销链结,防止耳轴转动和轴向移动,这种结构制作困难);2)静配合链接(耳轴具有过盈尺寸,装配式使用液氮将耳轴冷却插入耳轴座或把耳轴座加热装入耳轴,自然冷却,但是加热耳轴座会造成托圈局部变形,同时为了防止耳轴转动和轴向移动,在配合面拧入精致螺栓);3)耳轴与托圈直接焊接(这种结构节省了较重的耳轴座和连接件,重量轻、结构简单、加工量小,但是需要大型加工设备,耳轴与托圈进行整体同轴加工,以保证耳轴的平行度和同心度)。
7、托圈通过结构形式可分为两种1)普通焊接筋板结构(为了加强托圈的刚度在托圈内设有垂直筋板,垂直筋板限制了托圈因外在原因引起的变形,在转炉旋转时交变应力有可能造成钢板疲劳破坏,会出现裂纹在垂直筋板上或附近的内腹板上,但是可以利用斜筋板代替垂直筋板,可以使耳轴附近托圈有较大的抗扭刚度)。
2)水冷托圈两类(水冷托圈又分为内冷式和外冷式两种,内冷式是在封闭断面内直接通入循环水进行托圈冷却;外冷式是在托圈上下盖板和内腹板表面设置冷却水管;不论哪一类水冷托圈都要考虑钢板韧性问题,所以在选择材料时必须考虑韧性、屈服强度和焊接性能)8、炉体与托圈的连接装置—自调螺栓链结装置(球铰支撑)在炉体上部焊接两个加强圈,炉体通过加强圈和三个带球面垫的自调螺栓与托圈链结在一起,成120度分布,其中两个在出钢侧与耳轴轴线成30度夹角,另一个在装料侧与耳轴轴线成90度夹角位置。
当炉体产生热张冷缩位移时,自调螺栓本身倾斜并靠其球面垫自动调位,使炉体中心位置保持不变;另外在耳轴位置还设有上下托架装置,在托加上的剪切块与焊接在托圈上的卡板配合,当转炉倾动到水平位置时,由剪切块把炉体的负荷传给托圈,这也属于三点支撑装置,可以适应炉体和托圈的不等量变形,载荷分布均匀,结构简单,维护量少,制作简单。
9、炉体挡渣板挡渣板有多块钢板胡成,钢板厚度为16毫M,分为上下两层,上层板焊于炉帽上,下层板焊于球铰装置联接安装环板上,在球铰联接装置安装位置处,挡渣板制成凸起护板以保护球铰联接装置,其它板的焊接以保护托圈为原则。
10、耳轴轴承耳轴轴承要承载炉体、铁水或钢水和托圈的全部重量、倾动机构重量,工作条件处于高温和多尘中,另外托圈在高温下还会产生耳轴方向的伸长和挠曲变形,所以要求耳轴轴承达到:有足够的强度,能承受静力和动力载荷、抗疲劳的耐久性、对中性好、安装更换方便、维修容易和经济性好等要求。
在耳轴轴承选型时要考虑:操作条件下的静负荷和不正常操作下的附加载荷(兑铁水和加废钢时铁包或废钢斗压在炉口上产生的负荷)、倾动转炉时的倾动机构传递倾动力矩产生的载荷、炉体倾动时的启停所产生的惯性力、清理炉口积渣引起的载荷。
1)主动端轴承座主动端轴承座是采用双列调向心滚子轴承,将其设计成固定结构,在靠转炉一侧设有挡渣,并固定在轴承座上;轴承端盖为双层密封,轴承座为剖分式结构,采用ZG270-500铸造而成;整个轴承座支架采用钢板焊接结构。
2)从动端轴承座从动端轴承座为铰链式轴承支座,耳轴轴承处和主动端轴承该处结构相同,轴承固定在轴承座上,轴承座通过两个铰链支承在基础上,两个铰链的销轴在同一轴线上,此轴线位于与耳轴轴线垂直的方向上,依靠支座的摆动来补偿耳轴轴线的位移。
11、转炉水冷系统转炉水冷系统包括炉口水冷,炉帽水冷、及托圈两耳轴水冷,炉口、炉帽和托圈的冷却水是由装在从动端耳轴上的六孔旋转接头进入耳轴,在由耳轴法兰处接管分别进入炉口、炉帽和托圈,在水流通过从动端耳轴时,也同时起到了冷却从动耳轴的作用,从动端耳轴有六个孔,作为炉口、炉帽、托圈水路的进回水通道(供水压力要求达到≥0.4Mpa);12、转炉倾动机构1)转炉倾动机构应该满足转炉工艺要求,能使转炉360度正反旋转,并且能够准确的停止在任意角度位置,用以满足兑铁水、装料、取样、测温、出钢、出渣、以及返回等工艺操作要求,同时还要于氧枪、烟罩提升、等操作要求进行连锁,以免产生误操作。
2)转炉倾动机构的机构操作要求灵活,转炉操作一般应具备两种以上倾动速度转炉在出钢、出渣、测温取样时,要求平稳缓慢的倾动,以避免钢渣猛烈冲击而发生炉液严重喷溅和溢出,当转炉大幅度倾转时则采用较快的速度,来节约辅助时间,缩短冶炼周期。
3)倾动机构必须安全可靠,由于转炉工作对象是高温液体金属,在生产过程中,必须避免传动机构任何环节发生故障,,即使在倾动机构的某一个环节发生故障,也要求传动系统具有自备能力,能继续工作,直到本炉冶炼结束。
4)倾动机构能够适应载荷的变化和结构的变形,当托圈产生挠曲变形而引起耳轴轴线偏斜时,仍能够保持各传动齿轮副的正常啮合,同时还要使机构具有减缓动载荷和冲击载荷的性能。
5)倾动机构最大的特点是大扭矩,转炉炉体自身重量大,和炉液一起,整个转炉的倾动部分重量达到百吨,甚至千吨,所以炉体旋转必须在转炉耳轴上施加几百甚至几千千牛×M的力矩,同时转炉在操作中需要进行频繁的摇动,所以倾动机构除承受静载荷外还要承受由于启动、制动引起的动载荷,还有一点就是传动机构中存在较大的啮合间隙,当进行炉口积渣等操作时使机构承受较大的动载冲击,可以达到静载荷的两倍以上。
另外倾动机构的速度特点是低转速,一般为0.1---1.5r/min,一般50T 以上转炉都有两种以上的倾动速度,慢速0.1---0.3r/min,快速0.7---1.5r/min,30T以下的转炉一般采用0.7—1.5r/min。
6)倾动机构的结构形式一般分为落地式、半悬挂式和全悬挂式。
6.1)落地式倾动机构主要是使用在30T以下的转炉上,最大的缺点是托圈发生挠曲变形时会因起耳轴轴线偏斜,大小齿轮的正常啮合会备破坏,导致齿轮磨损严重、齿断裂或其他事故。
优点是结构简单。
6.2)半悬挂式的大小齿轮通过悬挂减速机悬挂在耳轴上,所以耳轴轴线的偏斜不会影响大小齿轮的正常啮合。
缺点是有一部分安装在地上,站地面积比较大,笨重等。
6.3)全悬挂式结构紧凑,重量轻,站地面极小,运转安全可靠,工作性能好;啮合点一般2――4点,由于采用两套以上传动装置,所以一般1、2套损坏后仍然可以继续操作;因为全悬挂减速机都挂在耳轴上,即便是耳轴发生挠曲变形也不会造成齿轮副的正常啮合;全悬挂式和半悬挂式都要求加强减速机壳体的强度,并且要求有非常好的抗扭装置;缺点是由于啮合点的增加也增加了结构的复杂性,加工和调整要求精度比较高。