推行TPS的目的26页PPT
合集下载
TPS基础剖析

定标准作业组合表及改善后标准作业票并张贴在生产 现场,明确生产节拍,优化人员,实行标准作业。
2024/8/15
38
四、 平准化
• 平准化是多品种混流的一个流生产方式,是生产数量和产 品种类的均衡,即后工序只在必要时刻从前工序领取必要 数量的必要产品,是准时化生产的前提。
• 它要求后工序向前工序领取产品时,要均匀地领取各种产 品,实行混流生产,以防止在某一段时间内集中领取同一 种产品,以免造成前方工序的闲忙不均,以及由此引发的 生产混乱。
这些成绩的取得都得益于被世人称为“丰田黑匣子” 的202丰4/8/田15 生产方式——TPS(Toyota Production System) 7
• 日本和中国同处亚洲,两国的文化具有很大程度的相似性。 欧美学习TPS取得了巨大的成功,作为同样具有东方文化背 景的中国,可行度更高。
• TPS产生于日本战后经济基础薄弱之时,是一种在“供大于 求”的市场竞争环境下成功的先进管理模式,丰田人讲: TPS是赚钱的工业工程,穷人的工业工程。目前,我国企业 主要也正面临这方面的问题。一方面,汽车市场竞争激烈, 汽车价格在不断地下降;另一方面,钢铁等原材料又纷纷涨 价,汽车产业的整条供应链都面临着严峻的考验,在这一市 场条件下,学习和推行TPS更具有重要的现实意义。
JIT 在必要的时间生产必要 数量的必要产品
• 提前规划 • 持续性流程 • 拉动式制度 • 快速转换 • 整合物流作业
以人为本
挑战自我 参与决策. 共同目标 交叉训练.
减少浪费
现地现物 5W
解决问题. 注意浪费.
自働化 (现地品质管理)
使问题显现
• 出现问题马上自动停止 • 安东(视觉信号系统) • 人机分开 • 防错 • 现地品质管理 • 解决问题的真因
2024/8/15
38
四、 平准化
• 平准化是多品种混流的一个流生产方式,是生产数量和产 品种类的均衡,即后工序只在必要时刻从前工序领取必要 数量的必要产品,是准时化生产的前提。
• 它要求后工序向前工序领取产品时,要均匀地领取各种产 品,实行混流生产,以防止在某一段时间内集中领取同一 种产品,以免造成前方工序的闲忙不均,以及由此引发的 生产混乱。
这些成绩的取得都得益于被世人称为“丰田黑匣子” 的202丰4/8/田15 生产方式——TPS(Toyota Production System) 7
• 日本和中国同处亚洲,两国的文化具有很大程度的相似性。 欧美学习TPS取得了巨大的成功,作为同样具有东方文化背 景的中国,可行度更高。
• TPS产生于日本战后经济基础薄弱之时,是一种在“供大于 求”的市场竞争环境下成功的先进管理模式,丰田人讲: TPS是赚钱的工业工程,穷人的工业工程。目前,我国企业 主要也正面临这方面的问题。一方面,汽车市场竞争激烈, 汽车价格在不断地下降;另一方面,钢铁等原材料又纷纷涨 价,汽车产业的整条供应链都面临着严峻的考验,在这一市 场条件下,学习和推行TPS更具有重要的现实意义。
JIT 在必要的时间生产必要 数量的必要产品
• 提前规划 • 持续性流程 • 拉动式制度 • 快速转换 • 整合物流作业
以人为本
挑战自我 参与决策. 共同目标 交叉训练.
减少浪费
现地现物 5W
解决问题. 注意浪费.
自働化 (现地品质管理)
使问题显现
• 出现问题马上自动停止 • 安东(视觉信号系统) • 人机分开 • 防错 • 现地品质管理 • 解决问题的真因
TPS现场管理介绍

对策:
4.加工上的浪费
原因:
•工程顺序检讨不足 •作业内容与工艺检讨不足 •模夹治具不良 •标准化不彻底 •材料未检讨
•工程设计适正化 •作业内容的修正
•治具改善及自动化
•标准作业的贯彻 •VA/VE的推进 •设计FMEA的确实推进
注意:
•了解同行的技术发展 •公司各部门对于改善的共同 参与及持续不断的改善
生产率提升30%
空间节省50% 不良率降低70% 交货周期缩短了80%
TOYOTA Production System
TOYOTA Production System
TOYOTA Production System
丰田生产方式书籍
TOYOTA Production System
NO.2
TPS背景
TOYOTA Production System
2.等待的浪费
双手均未抓到及摸到东西的时间
材料、作业、搬运、检查之所有等待,以及宽放和监视作业
表现形式:
•自动机器操作中,人员的“闲视”等待 •作业充实度不够的等待 •设备故障、材料不良的等待 •生产安排不当的人员等待 •上下工程间未衍接好造成的工程间的等待
TOYOTA Production System
2007汽车企业排名
排名 企业 通用汽车 丰田汽车 营业额$
2073.49亿 2047.464亿
利润额$
-19.78亿 140.558亿
百分比
-0.954% 6.865% 2.1288% -7.877%
1 2 3
4
戴姆勒克莱斯勒 1901.914 亿 40.488亿
原因:
•人员过剩 •设备稼动过剩 •生产浪费大 •业务订单预测有误 •生产计划与统计错误
TPS的根本理念PPT课件
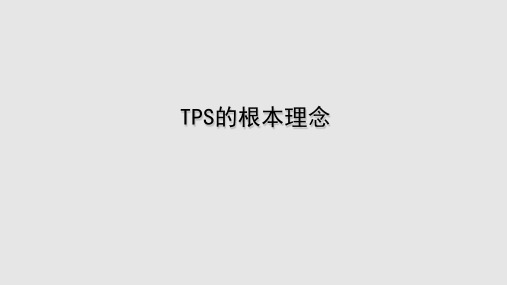
改善就是要把常识非常识化。
B)“过多库存 ”的浪费发生的理由?
<无管理的明证>
原
① 要对应机器故障、不良、缺勤、变更等“异常”(放心费)
因
② 负荷量(工序能力)不均,作业者技能差异・速度差异
系
③ 错误提高稼动率(开工率),「表面」效率提高
管理能力弱
问 题 隐
④ 停生产线是“罪恶”的思维认识。
⑤ 缺乏“必要人工”的考虑
库存是「隐性损失」
库存是腐蚀企业管理体质的病毒。
过多(滞留)库存(包括管理不在的库存)为什么不可取
* L/T
限制C/F,提升管理质量
多
库存解剖
(对原因行动,结果必然改变)
能力 & 领导能力
余 的 费
A)“ 过多库存”的“浪费”产生新的浪费(附带浪费多余的成本)。
① 购入原材料・部件提前占用资金
库存金额之外
·安排的人 ·生产的人 ·出货的人 ·销售的人
<材料费> ·材料费
<管理间接费····经费> ·搬运费 ·货车费用 ·销售费用
·叉车 ·吊车
·机械 ·电力
·油料 ·货车
·电话 ·IT机器
JIT 顾客
费 用 回 收 ( 销 售 额 )
不能售出时,变为库存,计为资产。
生产过程是成本中心
1、如何加快从成本发生到费用回收的循环,是【C/F(创出率)增大】的重 要关键(改善的目的不在于费用节约而在于C/F增加)。
低
成本上升 的要因
管理(工 时)的难 用眼看到的 浪费 (岩石) 库存
生
( 生 产 方 式 系 统 机 能 不
物设
生品备
产 形
传 送
推行TPS的目的讲述

之四 美国式管理量化:使管理人员学会了习惯通过众多报表、众多数字中掌 控企业、发现问题。 丰田在内部管理中,更强调“眼见”的力量。 科学数据表明:在人类认 知世界的信息获取中,视觉比例高达87%。 因此,丰田致力于:将各种生产管理活动,都变得“可视”。 在外在表现上,丰田车间内的每一道工序、每一个规格、每一种状况, 都基于人性的特点,用“一望而知”的颜色、形状、位置和独具丰田特色的 “看板”来区别和显示。而其内在逻辑是:可视化,使得企业现场人员能够 迅速发现异常。 丰田会长张富士夫指出:“丰田生产方式是一种对异常情况进行管理的 方式。”因为他认为:“没有异常的现场根本就不存在。而没有异常的后面, 反而隐藏着重大的问题。” 持续对现场进行改善,是丰田TPS管理的着眼点。而完成可视化,是一 切改善的开始。
3
一、对TPS的深入认识
佐佐木元强调:如何看待TPS是学习TPS的关键。如果把TPS当
作知识来学,当作培训来做,那就是毫无意义的。TPS的实质,就
是去“行动”。没有行动的管理,根本就不是管理。只有行动中的 改善,才是真正的改善,否则都会反弹。不能用计划来修订计划, 一定要用行动。不要追求完美再行动,只要有六成把握就去做,在 做的过程中不断改善。“TPS在哪里?在我们大家的心里!一定要
6
之二
营销为王vs 成本制胜
几乎所有的知名营销理论和营销学家,都诞生自美国。甚至美国管理 思想认为:企业所有行为,都可以用营销的角度去看待。这种思想根深蒂 固地浸入了中国企业界,营销成了最受企业主管瞩目的一块。据调查,中 国企业家直接主抓的领域中,除了战略,最多的便是营销。 那么丰田呢?近几年丰田业绩持续上升,分析师们不断提及的一个重要 因素,便是其销售状况的持续提升。但如果你就此认为丰田的成功在于 营销,就大错特错了。事实上丰田的思维正相反:销售的改善,只是一 个自然而然的结果,其根源恰恰在于内部管理,高质量低成本的产品自 然会促进销售的上升。
TPS精益生产推行.ppt
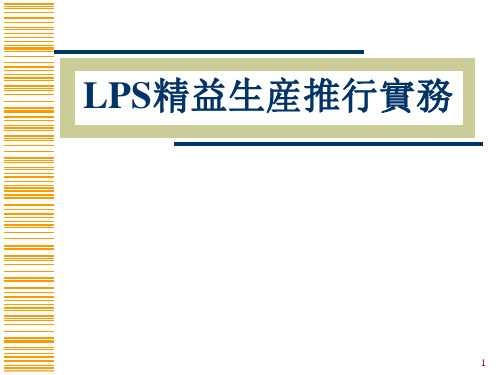
6
“Lean Production精實 生產”五大原則
Specify Value 確定價值 Identify the Value Stream 掌握"價值流程" Flow 朝流線生產方式邁進 Pull 建立"後拉式" Perfection 追求"盡善盡美"
7
“Lean Production精實 生產”的目的与效果
小步伐往上提升,形成大進步; • 要用自己的智慧、創意來改善; • 要運用新的生產思想觀念來改善。
改
改變
成为更
善
良善
22
改善的理解
對改善做法的強調:
1)改善不是專業工程師的工作,是 每個人運用正確的生產思想觀念,而 不是用傳統的思想來有能力的工作。
2)改善要以課題為導向,定期化、 制度化組成小集團完成改善目標。
2万元
450
平均每人生产台数 国内市场占有率 库存天数
平均每平方公尺附 加价值(USD)
59台 44% 10天
2500
41台 22% 20天
1100
144 200 50
LPS精益生産推行實務
1
目录
◆ 什么LPS ◆ LPS有哪些技法 ◆ 如何达成LPS ◆什么是改善 ◆改善新思维 ◆认识成本
◆浪费与无驮 ◆效率的認識 ◆改善基础 ◆改善基本技巧 ◆改善(IE)七手法 ◆改善不良之技巧
2
什么LPS?
3
LPS的含义
L 生产
9
LPS有哪些技法
10
第一技法:流線化生產
以建立“一貫化、一個流、同步化” 的產品別細胞式(Cell Production)的流線 生產線為目標; 透過流線生產,可以快速縮短生產交 期,減少在製品庫存,提高勞動生產力, 降低不良率,節省空間諸多好處; 可以說是“LPS”推行的切入點。
“Lean Production精實 生產”五大原則
Specify Value 確定價值 Identify the Value Stream 掌握"價值流程" Flow 朝流線生產方式邁進 Pull 建立"後拉式" Perfection 追求"盡善盡美"
7
“Lean Production精實 生產”的目的与效果
小步伐往上提升,形成大進步; • 要用自己的智慧、創意來改善; • 要運用新的生產思想觀念來改善。
改
改變
成为更
善
良善
22
改善的理解
對改善做法的強調:
1)改善不是專業工程師的工作,是 每個人運用正確的生產思想觀念,而 不是用傳統的思想來有能力的工作。
2)改善要以課題為導向,定期化、 制度化組成小集團完成改善目標。
2万元
450
平均每人生产台数 国内市场占有率 库存天数
平均每平方公尺附 加价值(USD)
59台 44% 10天
2500
41台 22% 20天
1100
144 200 50
LPS精益生産推行實務
1
目录
◆ 什么LPS ◆ LPS有哪些技法 ◆ 如何达成LPS ◆什么是改善 ◆改善新思维 ◆认识成本
◆浪费与无驮 ◆效率的認識 ◆改善基础 ◆改善基本技巧 ◆改善(IE)七手法 ◆改善不良之技巧
2
什么LPS?
3
LPS的含义
L 生产
9
LPS有哪些技法
10
第一技法:流線化生產
以建立“一貫化、一個流、同步化” 的產品別細胞式(Cell Production)的流線 生產線為目標; 透過流線生產,可以快速縮短生產交 期,減少在製品庫存,提高勞動生產力, 降低不良率,節省空間諸多好處; 可以說是“LPS”推行的切入點。
推行TPS的目的
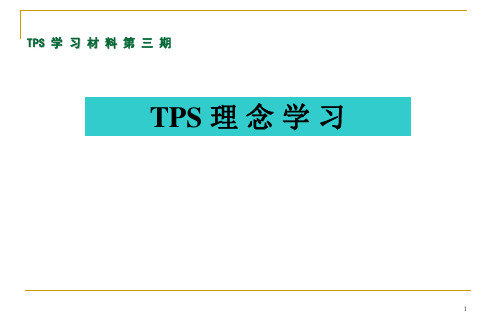
东京大学经济学部教授 藤本隆宏
出处:丰田强在何处? 日经BP社
企业的管理组织能力神经体系,达到了具有强大自律功能 的境界,员工意志被充分调动起来。
19
二、推行TPS的目的及意义
推行TPS是公司实现超越国内竞争对手的有效手段
1、好的发展环境 2、强有力的领导班子,带出好的团队敢于决策
3、成功抓住每一个机会
3
一、对TPS的深入认识
佐佐木元强调:如何看待TPS是学习TPS的关键。如果把TPS当
作知识来学,当作培训来做,那就是毫无意义的。TPS的实质,就
是去“行动”。没有行动的管理,根本就不是管理。只有行动中的 改善,才是真正的改善,否则都会反弹。不能用计划来修订计划, 一定要用行动。不要追求完美再行动,只要有六成把握就去做,在 做的过程中不断改善。“TPS在哪里?在我们大家的心里!一定要
等待时间显 在化
消除制造过剩 的浪费
第三层次的浪费过剩 库存的浪费
用能销售的速度制造 (丰田生产方式的中心课题) 好途径
第二层次的浪费(最大的浪费) 制造过剩的浪费(工作进展过度)
坏途径 多余的劳务费 多余的折旧费 多余的利息支出 13
第一层次的浪费(过剩的生产能力的存在) (1)过多的人员 (2)过剩的设备 (3)过剩的库存
22
c、关于计件工资:工人作业时间分为手动作业时间和机器作业时间, 作业改善的目的之一是用机器作业时间去覆盖手动作业时间。工人工资
的核算应该是以手动作业时间为准,而计件式工资无法区分手动作业时
间和机器作业时间,改善之后体现的只能是工时的降低,导致的后果是 现场的强烈抵抗和改善的成果不能摆在经营者的面前。 计件工资制是在用计划束缚个人潜能的发挥,是无法持续调动员 工持续改进的激情的。而且,计件工资的本质就是鼓励多生产,就必 然导致库存。这些都与TPS思想相悖 。
出处:丰田强在何处? 日经BP社
企业的管理组织能力神经体系,达到了具有强大自律功能 的境界,员工意志被充分调动起来。
19
二、推行TPS的目的及意义
推行TPS是公司实现超越国内竞争对手的有效手段
1、好的发展环境 2、强有力的领导班子,带出好的团队敢于决策
3、成功抓住每一个机会
3
一、对TPS的深入认识
佐佐木元强调:如何看待TPS是学习TPS的关键。如果把TPS当
作知识来学,当作培训来做,那就是毫无意义的。TPS的实质,就
是去“行动”。没有行动的管理,根本就不是管理。只有行动中的 改善,才是真正的改善,否则都会反弹。不能用计划来修订计划, 一定要用行动。不要追求完美再行动,只要有六成把握就去做,在 做的过程中不断改善。“TPS在哪里?在我们大家的心里!一定要
等待时间显 在化
消除制造过剩 的浪费
第三层次的浪费过剩 库存的浪费
用能销售的速度制造 (丰田生产方式的中心课题) 好途径
第二层次的浪费(最大的浪费) 制造过剩的浪费(工作进展过度)
坏途径 多余的劳务费 多余的折旧费 多余的利息支出 13
第一层次的浪费(过剩的生产能力的存在) (1)过多的人员 (2)过剩的设备 (3)过剩的库存
22
c、关于计件工资:工人作业时间分为手动作业时间和机器作业时间, 作业改善的目的之一是用机器作业时间去覆盖手动作业时间。工人工资
的核算应该是以手动作业时间为准,而计件式工资无法区分手动作业时
间和机器作业时间,改善之后体现的只能是工时的降低,导致的后果是 现场的强烈抵抗和改善的成果不能摆在经营者的面前。 计件工资制是在用计划束缚个人潜能的发挥,是无法持续调动员 工持续改进的激情的。而且,计件工资的本质就是鼓励多生产,就必 然导致库存。这些都与TPS思想相悖 。
TPS教育资料.ppt

商业的原点
• 购买的材料带有附加价值 • 从客户处缴纳 • 然后资金快速回收
2
原先TOYOTA并没有钱, 只能买必要的东西
现场一直大批量生产 就形成大量库存
只生产卖出去的东西
(受到超级市场的启发)
丰田喜一郎的构想
这就是JUST-IN-TIME考虑 的原则 这是支持TPS的两大支柱 之一
为了追赶美国的汽车行业,
③改善的方法日趋发展
7
3ー(1)公司内所有潜在的浪费
浪费作业
(没有附加价值)
净作業
(产生附加价值)
C
A
附带作业
(没有附加价值但必要的作业) 上下活儿、搬运等
现场作业
B
我们的工作就是 要做到100%接近
净作业。
TPS的7个浪费 ①生产过剩浪费
②手持浪费 ③加工浪费 ④动作浪费 ⑤搬运浪费 ⑥库存浪费 ⑦不合格品
接受订单LT
设计LT
生产准备LT
筹备LT
标准化后就 不需要了
没有能力的话就有库存 (库存=生产能力弱)
缩短交货期 (生产LT<要求LT)
完全接订单生产化加工LTຫໍສະໝຸດ 安装LT 检验LT 出货LT
接受订单LT筹备LT 加工LT 安装、检验、出货LT 总交货期(生产交货期)
必要库存
诱发二次 浪费!
最大的浪费!
①材料的耗费 ②劳务费的耗费 ③经费的耗费 ④放置地点和搬运的浪费
8
3ー(2)排除浪费就有要使其可见化
容易发现浪费的现场应该是
库存水平低了, 就能逐渐发现问题处
・ 减少库存 也是使其可见化的方法(手段)
・库存多了就掩饰了浪费.
库存水平
仅减少库存不是目的
• 购买的材料带有附加价值 • 从客户处缴纳 • 然后资金快速回收
2
原先TOYOTA并没有钱, 只能买必要的东西
现场一直大批量生产 就形成大量库存
只生产卖出去的东西
(受到超级市场的启发)
丰田喜一郎的构想
这就是JUST-IN-TIME考虑 的原则 这是支持TPS的两大支柱 之一
为了追赶美国的汽车行业,
③改善的方法日趋发展
7
3ー(1)公司内所有潜在的浪费
浪费作业
(没有附加价值)
净作業
(产生附加价值)
C
A
附带作业
(没有附加价值但必要的作业) 上下活儿、搬运等
现场作业
B
我们的工作就是 要做到100%接近
净作业。
TPS的7个浪费 ①生产过剩浪费
②手持浪费 ③加工浪费 ④动作浪费 ⑤搬运浪费 ⑥库存浪费 ⑦不合格品
接受订单LT
设计LT
生产准备LT
筹备LT
标准化后就 不需要了
没有能力的话就有库存 (库存=生产能力弱)
缩短交货期 (生产LT<要求LT)
完全接订单生产化加工LTຫໍສະໝຸດ 安装LT 检验LT 出货LT
接受订单LT筹备LT 加工LT 安装、检验、出货LT 总交货期(生产交货期)
必要库存
诱发二次 浪费!
最大的浪费!
①材料的耗费 ②劳务费的耗费 ③经费的耗费 ④放置地点和搬运的浪费
8
3ー(2)排除浪费就有要使其可见化
容易发现浪费的现场应该是
库存水平低了, 就能逐渐发现问题处
・ 减少库存 也是使其可见化的方法(手段)
・库存多了就掩饰了浪费.
库存水平
仅减少库存不是目的
工厂管理-工厂TPS推进成果会(ppt29页)
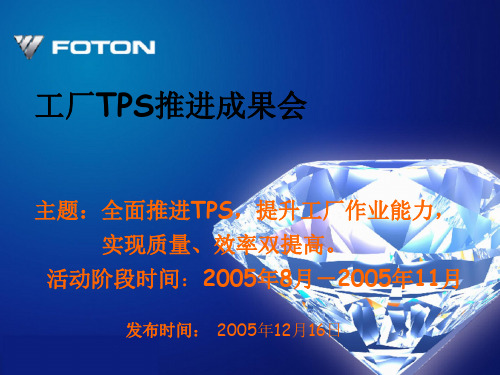
总体目标
1.时代工厂推进与公司试点事业部保持同步。 2.从05年8月份,由过去单纯的生产作业改善,
向系统工作流程再造扩展,将现场作业改善 融入业务流程改造的管理框架之内。 3.培养一支推进骨干队伍,全面推进工厂工作。
具体目标
• 成熟产品 一年内(2005年8月~2006年 8月)生产制造周期缩短15%。
• 以推进(六个流)改造为手段,缩短生产制造过程 周期时间。
• 以TPS为手段,新产品准备为载体,实现新产品 开发一步到位。
(二)TPS推进主要业务
TPS推进主要业务
(三)工厂成立推进领导小组和推进工作小组 TPS推进组织机构图
系统推进 开展合理化建议、QC小组活动,营造
T
改善组
推进氛围,激活员工参与管理热情。
2. 将问题点填入《问题点对策管理表》 进行立项。
3. 排。
• 推进背景 • 推进工作策划 • 推进工作目标 • 推进工作切入点 • 目前的成果 • 推进实践中的启发 • 下步的推进重点
TPS推进
成果录像
• 推进背景 • 推进工作策划 • 推进工作目标 • 推进工作切入点 • 目前的成果 • 推进实践中的启发 • 下步的推进重点
1.产品结构调整产品转型;生产中、高端汽车。 2.从原点分析和审视,时代工厂在管理方面存
在较大的差距。 3.质量现状比起竞争对手,还存在不小的差距。
推进TPS是解决问题的最有效途径, 需要自上而下的全面推进。
推进工作要求 :
• 本厂推进进度与试点事业部 同步
• 跟进咨询专家在欧曼试点工 厂的指导和培训
推进着眼点之四:工艺管理改善
工艺科职责比较集中,工艺脱离实际 容易出现设计错误。需要对现行工艺管 理模式进行改进,增加各生产部二级工 艺管理职责内容,以便推进标准化作业 改善。
精益生产-TPS培训PPT课件

5 如何开展持续推进改善活动
6 TPS看板管理 编制:
审核:
3月 下旬
5月初
2小时 2小时
6月-7月 3小时 批准:
现场管理者应具备的技能 如何培养多能工
公司内开展TPS自主研究会 根据三现原则,实施各种改善方法
后工序领取,后补充生产 看板管理生产方式的介绍
1
1
1 TPS培训
主题
(1)TPS的基本思路 (2)TPS的具体推进方法
精益生产,精益标杆学习,丰田学习
更多精益生产资料,精益生产知识库: /repository/
资料提供:广州策益咨询管理()
TPS培训计划
序
号
培训主题
1
TPS的基本思想 及推进方式
培训对象
负责人以上
2 如何实施有效的生产现场品质管理
⑤库存的浪费
生产时必要的最少的物件以外的物件 …指由生产·搬运结构导致的库存
⑥动作的浪费 不产生附加价值的动作 ⑦不良品·返修的浪费 成不了产品的生产浪13 费
精益生产,精益标杆学习,丰田学习 更多精益生产资料,精益生产知识库: /repository/ 资料提供:广州策益咨询管理()
12
精益生产,精益标杆学习,丰田学习
④加工的浪费 更多精益生产资料,精益生产知识库: /repository/ 资料提供:广州策益咨询管理()
12
和工序进度、加工物件的精度等毫无关系啊 的不必要的加工浪费啊啊啊啊啊啊啊啊啊啊
2
2
主题(1)
TPS的基本思路
3
精益生产,精益标杆学习,丰田学习
更多精益生产资料,精益生产知识库: /repository/ 资料提供:广州策益咨询管理()
生产力提升之tps的幻灯片PPT

5S之间相互关系
为了使用的方便性而 打扫现场,为了发
进行的三定活动
现问题并加以改善 的点检活动
整顿
清扫
到处都是浪 费源
5S方法
纳期迟延是平 常事
出不良是当 然的
整理
区别必要的,不必 要的扔掉无用的
清洁
实施目视化管理 使一眼就能看请状 态,发现问题
习惯化
用5S的思想来指导业务,发现问题 立即去改善它。
4 调查可用品的使用频度,决定日常用量
5 不急品和非用品处理(丢弃、出卖、)
推进手段 相关部门讨论制定 红牌作战推进
制作不用品/不急品登记管理报表
制定不用品/不急品处理流程及基准
5S---整顿
整顿
为了更容易地找到必要的东西,标 识保管场所与数量
必要性
① “查找”是时间浪费 ② 发生必要的 “动作”的浪费使
为什么需要5S?
5S不好的现场直接导致生产现场的浪费现场. 3定也无法推进.
请关注浪费
浪费 7 制作不良的浪费
材料不良, 加工 不良, 检查不良.
浪费 6 动作的浪费
不必要的动作。 无附加价值的 动作.
浪费 5 等待的浪费
材料或作业的 等待,或因有 剩余时间而等 待作业.
浪费 1 过赢生产的浪费
在不必要的时间 将不必要的产品 以不必要的数量 制作出来.
浪费 2 库存的浪费
在库是工厂的 精神安定剂, 药是不吃为 好的.
浪费 3 搬运的浪费
一会儿抬,一会儿放, 一会儿搬,之后 再把东西堆在其 上面.
浪费 4 作业本身的浪费
目前正在做的作业 的确是必要的吗?
5S必要性与效果
实现安全,无 灾害事业工厂
相关主题