天然气脱硫相关环保工艺
天然气脱硫脱碳工艺综述

天然气脱硫脱碳工艺综述天然气脱硫脱碳工艺是一项关于天然气净化和提纯的技术,其主要目的是去除天然气中的硫化氢和二氧化碳等有害物质,以保证天然气的质量和环保要求。
天然气脱硫脱碳工艺主要分为化学吸收法、物理吸收法、膜分离法、化学反应法等多种类型,每种工艺均有其特点和适用范围。
化学吸收法是将天然气通过一种特定的溶液中,使其中的有害物质和溶剂发生化学反应,从而达到脱除有害物质的目的。
其中比较常见的方法是利用醇胺和胺类化合物作为吸收剂,如乙醇胺(MEA)、二甲醇胺(MDEA)等。
这种方法具有脱硫效率高、操作简单等优点,但是溶剂回收、能耗较高等问题也亟待解决。
物理吸收法则是通过溶剂的物理性质,如溶解度、表面张力等,将有害物质从天然气中去除。
常见的物理吸收法工艺有富勒烯吸附、极限凝聚法等。
这种方法操作简单、溶剂损耗少等优点,但是对溶剂选择和有害物质选择要求较高,同时对溶剂回收和循环技术也有一定要求。
膜分离法是将天然气通过一种特定的膜,利用渗透和选择性通透的原理,将有害物质从天然气中去除。
薄膜材料常见的有聚酰胺薄膜、聚氟乙烯薄膜等。
这种方法节能环保、操作简单等优点,但是需要对膜材料的选择和膜工艺的控制有一定的技术要求。
化学反应法则是利用特定的催化剂或化学反应条件,促使有害物质在天然气中发生化学反应,从而实现脱硫脱碳的目的。
常见的化学反应法工艺有氧化脱硫法、还原脱硫法等。
这种方法对催化剂和反应条件有一定的要求,但是脱硫效率高、反应速率快等优点。
天然气脱硫脱碳工艺在净化天然气、提高环境保护和资源利用效率方面具有重要意义。
随着清洁能源和低碳经济的提倡,天然气脱硫脱碳技术也将迎来更广泛的应用和发展。
天然气脱硫工艺

项目六 知识拓展
以上反应均是放热反应,反应式(3 -6-1)、式(3-6-2)在燃烧炉中进行, 不同的工艺对温度控制的要求有所不同,在1 100℃~1 600℃内,通过 严格控制空气量的条件下将硫化氢燃烧成二氧化硫,并生成部分产品硫, 同时为克劳斯催化反应提供H2S:SO2为2:1的混合气体。
上一页 下一页 返回
项目六 知识拓展
出废热锅炉的过程气进入一级克劳斯反应器在氧化铝催化剂作用下发生 反应式(3一6一3)。将硫组分转化为单质硫,反应器出u温度约320℃。 而后在一级硫冷凝器用锅炉给水降温到175 ℃ ,热量用来产生低压饱和 蒸汽,分离出部分冷凝的单质硫,再经过热器用中压蒸汽再加热到满足 二级克劳斯反应器入口的温度205℃,在二级克劳斯反应器中进一步转 化剩余的硫组分。反应之后的过程气约0. 14 MPa , 223℃,在二级硫冷 凝器中再次用锅炉给水降温到130℃,余热产生0. 4 MPa的低压饱和蒸 汽,低压饱和蒸汽用空冷器冷凝后返回二级硫冷凝器循环使用。在此温 度下硫的饱和蒸汽压小于0. 1 kPa,基本可以将单质硫全部冷凝。
过程气由硫黄分离器分离出液态单质硫后送焚烧炉处理后排放。
上一页 下一页 返回
图3 -6-1硫回收流程框图
返回
Байду номын сангаас
图3 -6 -2氧克劳斯硫回收工艺流程
返回
谢谢观赏
项目六 知识拓展
一、天然气脱硫工艺选择原则
通常情况下,规模较大的天然气脱硫装置应首先考虑采用胺法的可能性。 ①在原料气碳硫比较高时(CO2/H2S大于6),为获得适于克劳斯装置加工
的酸气而需要选择性脱除H2S时,以及其他可以选择脱除H2S的工况, 应采用MDEA选吸工艺;在脱除H2S同时亦需脱除相当数量CO2时,可采 用MDEA和其他醇胺(如DEA)组合的混合胺法;天然气压力较低,净化气 H2S指标要求严格且需要同时脱除CO2时,可采用MEA法、DEA法或混 合胺法;在高寒或沙漠缺水地区,可选用DEA法。 ②原料天然气需脱除有机硫时通常应采用矾胺法。
天然气脱硫脱碳工艺综述
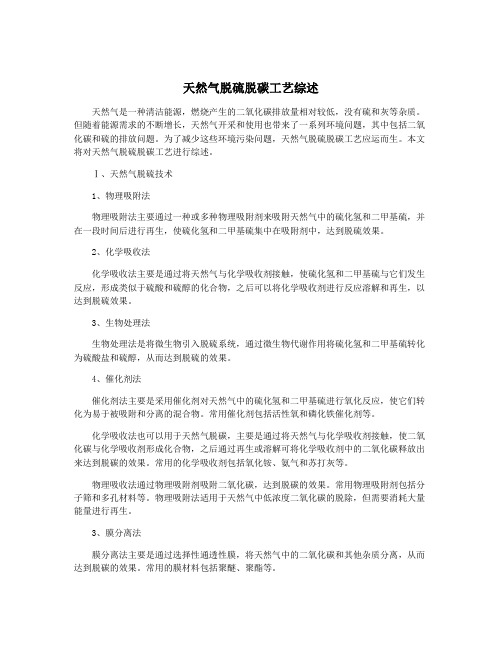
天然气脱硫脱碳工艺综述天然气是一种清洁能源,燃烧产生的二氧化碳排放量相对较低,没有硫和灰等杂质。
但随着能源需求的不断增长,天然气开采和使用也带来了一系列环境问题,其中包括二氧化碳和硫的排放问题。
为了减少这些环境污染问题,天然气脱硫脱碳工艺应运而生。
本文将对天然气脱硫脱碳工艺进行综述。
Ⅰ、天然气脱硫技术1、物理吸附法物理吸附法主要通过一种或多种物理吸附剂来吸附天然气中的硫化氢和二甲基硫,并在一段时间后进行再生,使硫化氢和二甲基硫集中在吸附剂中,达到脱硫效果。
2、化学吸收法化学吸收法主要是通过将天然气与化学吸收剂接触,使硫化氢和二甲基硫与它们发生反应,形成类似于硫酸和硫醇的化合物,之后可以将化学吸收剂进行反应溶解和再生,以达到脱硫效果。
3、生物处理法生物处理法是将微生物引入脱硫系统,通过微生物代谢作用将硫化氢和二甲基硫转化为硫酸盐和硫醇,从而达到脱硫的效果。
4、催化剂法催化剂法主要是采用催化剂对天然气中的硫化氢和二甲基硫进行氧化反应,使它们转化为易于被吸附和分离的混合物。
常用催化剂包括活性氧和磷化铁催化剂等。
化学吸收法也可以用于天然气脱碳,主要是通过将天然气与化学吸收剂接触,使二氧化碳与化学吸收剂形成化合物,之后通过再生或溶解可将化学吸收剂中的二氧化碳释放出来达到脱碳的效果。
常用的化学吸收剂包括氧化铵、氨气和苏打灰等。
物理吸收法通过物理吸附剂吸附二氧化碳,达到脱碳的效果。
常用物理吸附剂包括分子筛和多孔材料等。
物理吸附法适用于天然气中低浓度二氧化碳的脱除,但需要消耗大量能量进行再生。
3、膜分离法膜分离法主要是通过选择性通透性膜,将天然气中的二氧化碳和其他杂质分离,从而达到脱碳的效果。
常用的膜材料包括聚醚、聚酯等。
Ⅲ、综合技术天然气脱硫脱碳技术综合运用可以达到更好的脱除效果,例如物理吸附法和化学吸收法的组合,可以在低浓度下达到更高效的脱除效果;催化剂法和化学吸收法的组合,可以达到更低的能耗和更好的经济效益。
天然气脱硫工艺流程
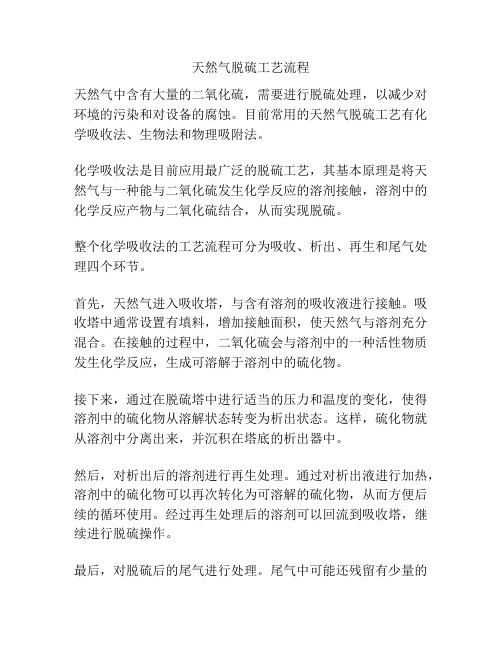
天然气脱硫工艺流程
天然气中含有大量的二氧化硫,需要进行脱硫处理,以减少对环境的污染和对设备的腐蚀。
目前常用的天然气脱硫工艺有化学吸收法、生物法和物理吸附法。
化学吸收法是目前应用最广泛的脱硫工艺,其基本原理是将天然气与一种能与二氧化硫发生化学反应的溶剂接触,溶剂中的化学反应产物与二氧化硫结合,从而实现脱硫。
整个化学吸收法的工艺流程可分为吸收、析出、再生和尾气处理四个环节。
首先,天然气进入吸收塔,与含有溶剂的吸收液进行接触。
吸收塔中通常设置有填料,增加接触面积,使天然气与溶剂充分混合。
在接触的过程中,二氧化硫会与溶剂中的一种活性物质发生化学反应,生成可溶解于溶剂中的硫化物。
接下来,通过在脱硫塔中进行适当的压力和温度的变化,使得溶剂中的硫化物从溶解状态转变为析出状态。
这样,硫化物就从溶剂中分离出来,并沉积在塔底的析出器中。
然后,对析出后的溶剂进行再生处理。
通过对析出液进行加热,溶剂中的硫化物可以再次转化为可溶解的硫化物,从而方便后续的循环使用。
经过再生处理后的溶剂可以回流到吸收塔,继续进行脱硫操作。
最后,对脱硫后的尾气进行处理。
尾气中可能还残留有少量的
二氧化硫,需要进一步处理以达到排放标准。
常用的尾气处理方法有吸收法、膜分离法和催化氧化法等。
总的来说,天然气的脱硫工艺流程是一个多环节、连续进行的过程。
通过吸收、析出、再生和尾气处理等步骤,可以有效地将天然气中的二氧化硫去除,达到环保和能源利用的双重目标。
不断的技术创新和工艺优化,将进一步提高天然气脱硫工艺的效率和经济性。
天然气脱硫脱碳工艺综述

天然气脱硫脱碳工艺综述天然气是一种清洁能源,是石油和煤炭的重要替代品。
天然气中含有硫化氢、二氧化碳等有害气体,其主要成分为甲烷。
在天然气的开采、运输和利用过程中,硫化氢和二氧化碳的含量需要得到有效的去除,以提高天然气的纯度和使用价值。
天然气的脱硫脱碳工艺十分重要。
在天然气脱硫脱碳工艺中,主要有化学吸收法、物理吸附法、膜分离法、生物法等多种技术。
下面将综述天然气脱硫脱碳的工艺方法,并对其优缺点进行评述。
一、化学吸收法化学吸收法是常用的天然气脱硫脱碳技术之一。
该方法是利用化学吸收剂(例如醇胺类化合物)与天然气中的硫化氢、二氧化碳进行化学反应,使其被吸收,从而实现天然气的脱硫脱碳。
化学吸收法具有处理效率高、操作稳定、投资和运行成本较低的特点,因此在天然气脱硫脱碳中得到广泛应用。
化学吸收法也存在一些不足之处。
由于化学吸收剂需要不断地更新和再生,因此会产生大量的废液和二次污染。
化学吸收法在高温高压条件下反应效率较低,处理大规模天然气的难度较大。
化学吸收法在实际应用中需要结合其他技术进行改进和完善。
二、物理吸附法物理吸附法是利用固体吸附剂(例如活性炭、分子筛等)对天然气中的硫化氢、二氧化碳进行吸附,从而实现天然气的脱硫脱碳。
物理吸附法具有操作简便、废物无二次污染等优点,因此在小规模天然气处理中得到广泛应用。
物理吸附法也存在一些限制。
吸附剂的再生和更新成本较高,需要消耗大量能源。
物理吸附法对天然气的含水量、温度等条件较为敏感,难以适应复杂的工业生产环境。
在大规模天然气处理中,物理吸附法的应用受到一定的限制。
膜分离法也存在一些问题。
膜分离法的选择性和透过率受到多种因素的影响,需要对膜材料和操作条件进行精细控制。
膜分离法的初投资较大,需要长周期才能回收成本。
在实际应用中需要综合考虑其技术和经济性能。
四、生物法生物法是一种新兴的天然气脱硫脱碳技术。
该方法是利用特定微生物对天然气中的硫化氢、二氧化碳进行生物降解,从而实现天然气的脱硫脱碳。
浅析天然气脱硫主要方法

浅析天然气脱硫主要方法天然气是一种重要的清洁能源,但是在天然气的生产和加工过程中,常常存在着硫化氢和二硫化碳等有害气体。
这些有害气体不仅污染了环境,还会对人们的健康和安全造成威胁。
脱除天然气中的硫化氢和二硫化碳是至关重要的。
目前,天然气脱硫主要采用化学法、物理法和生物法等方法。
下面将对这些方法进行浅析。
一、化学法1. 碱液脱硫法碱液脱硫法是一种较为常见的天然气脱硫方法。
其原理是利用强碱液与含硫天然气发生化学反应,将其中的硫化氢等有害气体转化为不溶于水的硫化物,从而实现脱硫的目的。
碱液脱硫法的优点是脱硫效率高,能够满足天然气中硫化氢含量的要求,但其缺点是造成了化学废水的排放,需要进行后续的处理和处理成本较高。
2. 氧化法氧化法是通过将含硫气体与氧气或氧化剂进行反应,将其中的硫化氢转化为硫酸氢盐或硫。
这种脱硫方法具有脱硫效率高、操作简单等优点,但也存在着氧化剂的选择、温度、压力等条件要求较高的缺点。
二、物理法1. 吸附法吸附法是一种常用的天然气脱硫方法。
其原理是利用吸附剂对天然气中的硫化氢和二硫化碳等有害气体进行吸附,从而实现脱硫的目的。
吸附法的优点是脱硫效果好,吸附剂可循环使用,但其缺点是对吸附剂的选择和再生过程等要求较高。
膜分离法是利用特定的膜对天然气中的硫化氢和二硫化碳进行分离,在膜上形成硫化氢和二硫化碳浓度梯度,从而实现脱硫的目的。
膜分离法的优点是脱硫效果好、操作简单,但其成本较高,对膜的选型和维护等要求较高。
三、生物法生物法是利用特定的微生物对天然气中的硫化氢和二硫化碳进行生物转化,从而实现脱硫的目的。
生物法的优点是环保、节能,但需要对微生物的培养和管理等进行一定的投入,同时在一些极端环境条件下生物法的脱硫效果可能会受到影响。
四、综合方法综合方法是指利用化学法、物理法和生物法等多种脱硫方法进行组合应用,从而达到更好的脱硫效果。
综合方法的优点是各种方法互补,能够提高脱硫效率,但同时也增加了设备投资和运行维护成本。
天然气脱硫技术

天然气脱硫技术引言随着全球能源结构的调整和清洁能源的兴起,天然气作为一种高效、环保的能源资源,正日益受到人们的和重视。
然而,天然气中含有的硫化物如硫化氢(H2S)和二硫化碳(CS2)等会对天然气开采和利用过程中的设备和管道造成严重的腐蚀和损害。
因此,为了提高天然气的品质和安全性,脱硫技术成为了天然气处理过程中的重要环节。
本文将详细介绍天然气脱硫的技术原理、工艺流程、优点及应用前景。
技术原理天然气脱硫技术主要基于化学吸收和物理吸收两种原理。
化学吸收法是利用酸性气体与碱性溶液反应的化学原理,将硫化物转化为可分离的硫化合物,如Na2S、CaS等。
物理吸收法则利用不同气体在特定溶剂中的溶解度差异,将硫化物从天然气中分离出来。
常用的物理吸收剂包括醇胺类、聚乙二醇类、毗啶类等。
工艺流程天然气脱硫的工艺流程主要分为以下几个步骤:1、预处理:去除天然气中的尘土、水分等杂质,保证进入脱硫装置的天然气品质。
2、吸收:将预处理后的天然气引入脱硫装置,与吸收剂发生反应,使硫化物被吸收剂吸收。
3、再生:将吸收剂从硫化物中分离出来,使其循环使用。
4、产品气处理:对脱硫后的天然气进行干燥、压缩等处理,以满足输配气要求。
具体案例中,化学吸收法的工艺流程如下:1、预处理:通过除尘、除水等措施,将天然气中的杂质分离出来。
2、吸收:在吸收塔中,用碱性溶液(如NaOH)与天然气中的酸性气体(如H2S)反应,生成可分离的盐类(如Na2S)。
3、再生:通过加热、减压等手段,使吸收剂从盐类中分离出来,循环使用。
4、产品气处理:对脱硫后的天然气进行干燥、压缩等处理,以满足输配气要求。
技术优点天然气脱硫技术具有以下优点:1、耗能低:相对于其他能源密集型处理方法,天然气脱硫技术的能耗较低。
2、效果好:采用化学吸收和物理吸收两种原理,可以有效地将天然气中的硫化物脱除,达到较高的净化效果。
3、操作简便:天然气脱硫装置的操作简单、稳定,可实现自动化控制。
天然气净化脱硫的工艺
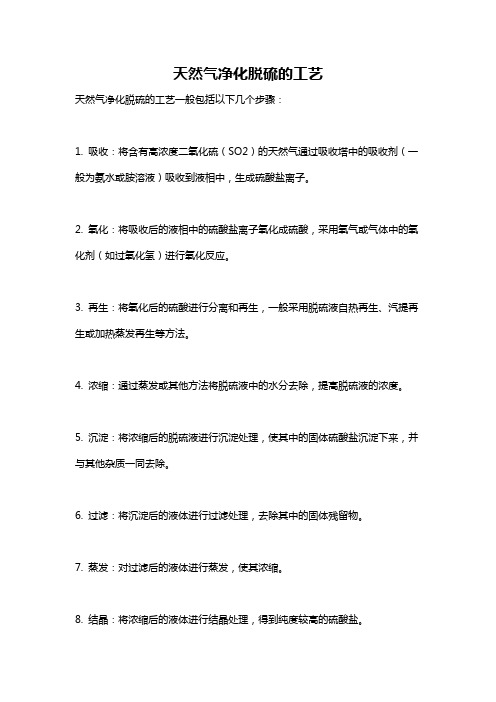
天然气净化脱硫的工艺
天然气净化脱硫的工艺一般包括以下几个步骤:
1. 吸收:将含有高浓度二氧化硫(SO2)的天然气通过吸收塔中的吸收剂(一般为氨水或胺溶液)吸收到液相中,生成硫酸盐离子。
2. 氧化:将吸收后的液相中的硫酸盐离子氧化成硫酸,采用氧气或气体中的氧化剂(如过氧化氢)进行氧化反应。
3. 再生:将氧化后的硫酸进行分离和再生,一般采用脱硫液自热再生、汽提再生或加热蒸发再生等方法。
4. 浓缩:通过蒸发或其他方法将脱硫液中的水分去除,提高脱硫液的浓度。
5. 沉淀:将浓缩后的脱硫液进行沉淀处理,使其中的固体硫酸盐沉淀下来,并与其他杂质一同去除。
6. 过滤:将沉淀后的液体进行过滤处理,去除其中的固体残留物。
7. 蒸发:对过滤后的液体进行蒸发,使其浓缩。
8. 结晶:将浓缩后的液体进行结晶处理,得到纯度较高的硫酸盐。
9. 干燥:对结晶后的硫酸盐进行干燥处理,使其达到所需的干燥程度。
以上就是一种常见的天然气净化脱硫工艺,不同的工艺会有所不同,具体可以根据需要来选择适合的工艺。
天然气脱硫工艺介绍
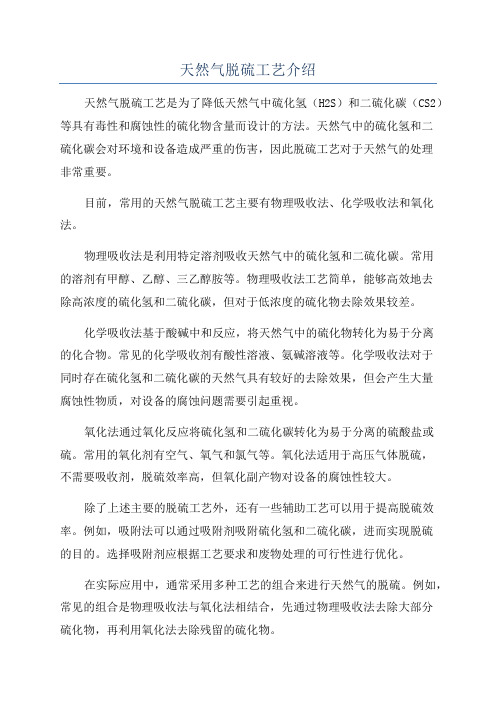
天然气脱硫工艺介绍天然气脱硫工艺是为了降低天然气中硫化氢(H2S)和二硫化碳(CS2)等具有毒性和腐蚀性的硫化物含量而设计的方法。
天然气中的硫化氢和二硫化碳会对环境和设备造成严重的伤害,因此脱硫工艺对于天然气的处理非常重要。
目前,常用的天然气脱硫工艺主要有物理吸收法、化学吸收法和氧化法。
物理吸收法是利用特定溶剂吸收天然气中的硫化氢和二硫化碳。
常用的溶剂有甲醇、乙醇、三乙醇胺等。
物理吸收法工艺简单,能够高效地去除高浓度的硫化氢和二硫化碳,但对于低浓度的硫化物去除效果较差。
化学吸收法基于酸碱中和反应,将天然气中的硫化物转化为易于分离的化合物。
常见的化学吸收剂有酸性溶液、氨碱溶液等。
化学吸收法对于同时存在硫化氢和二硫化碳的天然气具有较好的去除效果,但会产生大量腐蚀性物质,对设备的腐蚀问题需要引起重视。
氧化法通过氧化反应将硫化氢和二硫化碳转化为易于分离的硫酸盐或硫。
常用的氧化剂有空气、氧气和氯气等。
氧化法适用于高压气体脱硫,不需要吸收剂,脱硫效率高,但氧化副产物对设备的腐蚀性较大。
除了上述主要的脱硫工艺外,还有一些辅助工艺可以用于提高脱硫效率。
例如,吸附法可以通过吸附剂吸附硫化氢和二硫化碳,进而实现脱硫的目的。
选择吸附剂应根据工艺要求和废物处理的可行性进行优化。
在实际应用中,通常采用多种工艺的组合来进行天然气的脱硫。
例如,常见的组合是物理吸收法与氧化法相结合,先通过物理吸收法去除大部分硫化物,再利用氧化法去除残留的硫化物。
总之,天然气脱硫工艺是为了去除天然气中的硫化氢和二硫化碳而设计的方法。
各种脱硫工艺各有优缺点,根据天然气的特性和工艺要求选择合适的工艺和组合,以确保高效、安全地对天然气进行脱硫处理。
天然气脱硫工艺技术

天然气脱硫工艺技术介绍天然气中的硫化氢(H2S)是一种有毒有害气体,会对环境和人体健康造成严重影响。
因此,在天然气的处理过程中,需要采取脱硫工艺来减少H2S的含量。
本文将介绍几种常见的天然气脱硫工艺技术,包括化学吸收法、物理吸附法和生物脱硫法。
化学吸收法化学吸收法是一种常用的天然气脱硫工艺技术。
其主要原理是利用吸收剂与H2S发生化学反应,将H2S转化为可溶于吸收剂中的硫化物。
吸收剂可以选择胺类化合物,如甲醇胺(MEA)、二乙醇胺(DEA)等。
该工艺具有操作简单、效果稳定的优点,但存在吸收剂流失、生成废液处理问题。
物理吸附法物理吸附法是另一种常见的天然气脱硫工艺技术。
该工艺利用吸附剂的表面特性吸附H2S分子,达到脱硫的目的。
常用的吸附剂有活性炭和分子筛等。
物理吸附法操作简单,操作成本低,但吸附剂的再生和废气回收仍然是一个难题。
生物脱硫法生物脱硫法是一种新兴的天然气脱硫工艺技术。
该工艺利用特定微生物对H2S 进行氧化还原反应,将其转化为硫。
生物脱硫法不需要额外添加化学药剂,具有低能耗、低废弃物产生的优势。
然而,生物脱硫法的工艺条件和微生物培养管理都比较复杂,还需要进一步的研究和发展。
工艺选择在选择合适的脱硫工艺技术时,需要考虑多个因素。
首先是天然气中H2S浓度的高低,高浓度时适合采用化学吸收法;其次是对产品纯度和成本的要求,物理吸附法相对较为经济;另外,生物脱硫法则适用于对能源消耗和废弃物产生有严格要求的情况。
结论天然气脱硫工艺技术在不断发展和改进中,化学吸收法、物理吸附法和生物脱硫法是目前常见的工艺选择。
不同的工艺技术适用于不同的天然气处理情况,需要根据实际情况进行选择。
随着技术的进步,未来可能出现更加高效和环保的脱硫工艺。
天然气脱硫工艺流程
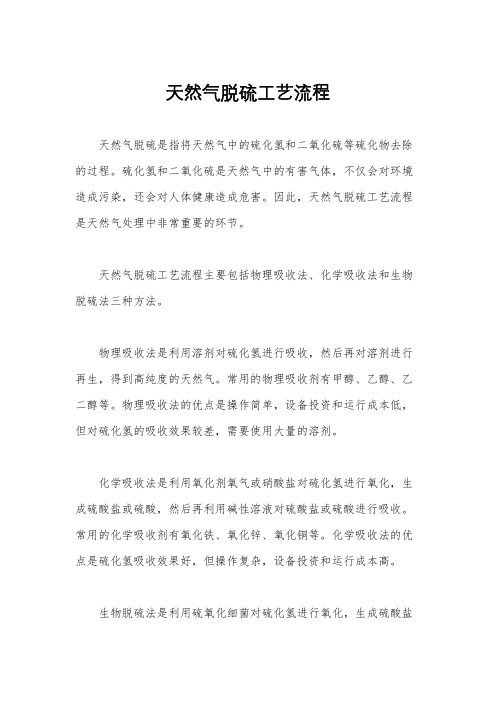
天然气脱硫工艺流程天然气脱硫是指将天然气中的硫化氢和二氧化硫等硫化物去除的过程。
硫化氢和二氧化硫是天然气中的有害气体,不仅会对环境造成污染,还会对人体健康造成危害。
因此,天然气脱硫工艺流程是天然气处理中非常重要的环节。
天然气脱硫工艺流程主要包括物理吸收法、化学吸收法和生物脱硫法三种方法。
物理吸收法是利用溶剂对硫化氢进行吸收,然后再对溶剂进行再生,得到高纯度的天然气。
常用的物理吸收剂有甲醇、乙醇、乙二醇等。
物理吸收法的优点是操作简单,设备投资和运行成本低,但对硫化氢的吸收效果较差,需要使用大量的溶剂。
化学吸收法是利用氧化剂氧气或硝酸盐对硫化氢进行氧化,生成硫酸盐或硫酸,然后再利用碱性溶液对硫酸盐或硫酸进行吸收。
常用的化学吸收剂有氧化铁、氧化锌、氧化铜等。
化学吸收法的优点是硫化氢吸收效果好,但操作复杂,设备投资和运行成本高。
生物脱硫法是利用硫氧化细菌对硫化氢进行氧化,生成硫酸盐或硫酸,然后再利用碱性溶液对硫酸盐或硫酸进行吸收。
生物脱硫法的优点是对硫化氢吸收效果好,操作简单,设备投资和运行成本低,但需要维护好生物脱硫系统的稳定性。
在天然气脱硫工艺流程中,选择合适的脱硫方法取决于天然气中硫化氢和二氧化硫的含量、脱硫效果要求、投资和运行成本等因素。
通常情况下,化学吸收法和生物脱硫法适用于高硫天然气的脱硫,而物理吸收法适用于低硫天然气的脱硫。
天然气脱硫工艺流程中,除了选择合适的脱硫方法外,还需要考虑脱硫设备的设计和运行参数的优化。
例如,脱硫设备的选型、操作温度和压力、溶剂或吸收剂的选择和再生方法等都会影响脱硫效果和成本。
总的来说,天然气脱硫工艺流程是一个复杂的系统工程,需要综合考虑技术、经济、环保等多方面因素。
只有选择合适的脱硫方法,并进行合理的设计和运行参数优化,才能保证天然气脱硫效果达标,同时降低投资和运行成本,实现经济效益和环保效益的双赢。
天然气脱硫工艺流程
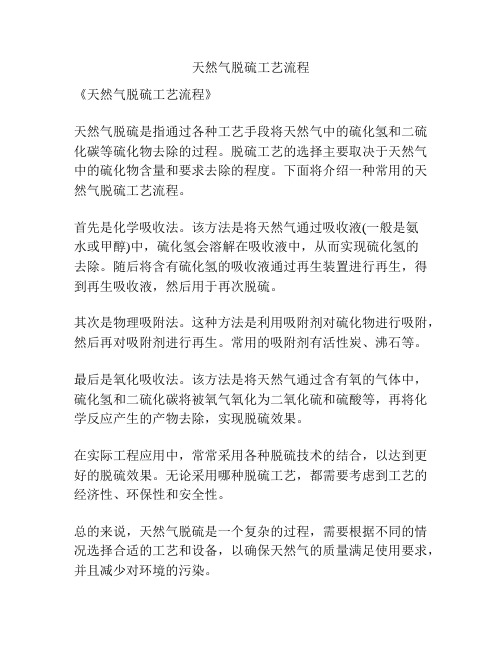
天然气脱硫工艺流程
《天然气脱硫工艺流程》
天然气脱硫是指通过各种工艺手段将天然气中的硫化氢和二硫化碳等硫化物去除的过程。
脱硫工艺的选择主要取决于天然气中的硫化物含量和要求去除的程度。
下面将介绍一种常用的天然气脱硫工艺流程。
首先是化学吸收法。
该方法是将天然气通过吸收液(一般是氨
水或甲醇)中,硫化氢会溶解在吸收液中,从而实现硫化氢的
去除。
随后将含有硫化氢的吸收液通过再生装置进行再生,得到再生吸收液,然后用于再次脱硫。
其次是物理吸附法。
这种方法是利用吸附剂对硫化物进行吸附,然后再对吸附剂进行再生。
常用的吸附剂有活性炭、沸石等。
最后是氧化吸收法。
该方法是将天然气通过含有氧的气体中,硫化氢和二硫化碳将被氧气氧化为二氧化硫和硫酸等,再将化学反应产生的产物去除,实现脱硫效果。
在实际工程应用中,常常采用各种脱硫技术的结合,以达到更好的脱硫效果。
无论采用哪种脱硫工艺,都需要考虑到工艺的经济性、环保性和安全性。
总的来说,天然气脱硫是一个复杂的过程,需要根据不同的情况选择合适的工艺和设备,以确保天然气的质量满足使用要求,并且减少对环境的污染。
天然气脱硫脱碳工艺综述
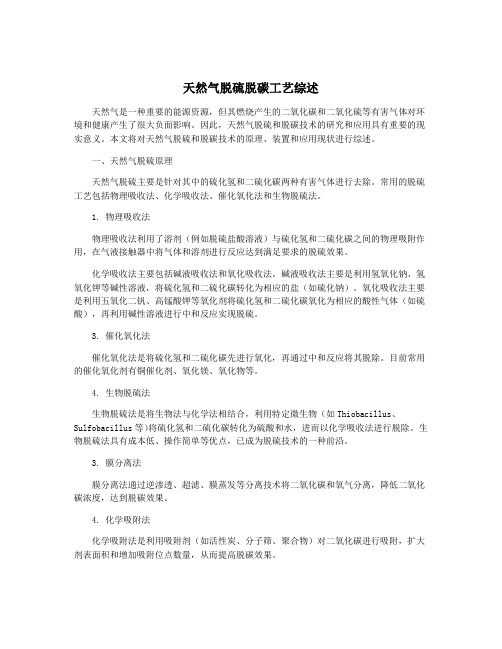
安保服务协议合同模板甲方(委托方):__________________________(以下简称甲方)乙方(服务方):__________________________(以下简称乙方)鉴于甲方为保障自身财产和人身安全需求,且为保障其周边环境良好秩序,特委托乙方提供安保服务,乙方愿意接受甲方的委托并提供相应的服务,双方经友好协商,达成如下协议:第一条服务内容1. 乙方提供的安保服务包括但不限于:a. 设立安保岗位,维护甲方财产和人员安全;b. 巡查管理区域,保障周边环境良好秩序;c. 协助应急事件处理,保障甲方利益;d. 提供安保建议,提升周边安全防范能力;e. 其他双方约定的安保服务。
第二条服务期限1. 本协议自双方签署之日起生效,服务期限为_______(具体时间);若服务期限届满,未经续约,本协议自动失效。
第三条服务费用1. 甲方应按照本协议约定,按时支付乙方服务费用,服务费用为________(具体金额)/________(服务周期),甲方应在每个月底支付上一个服务周期的服务费用。
2. 若服务期限中途解除协议,服务费用不予退还;若乙方原因造成解除协议,乙方应退还甲方未使用的服务费用。
第四条服务质量1. 乙方应按照本协议约定,提供优质的安保服务,确保服务内容的有效执行;2. 若因乙方原因导致服务不符合约定,甲方有权要求赔偿损失,并有权解除本协议。
第五条保密义务1. 双方应对本协议及相关事宜保密,不得擅自向第三方透露;2. 若因违反保密义务导致损失,违约方应承担赔偿责任。
第六条协议解除1. 若双方一方违约,经催告后未能纠正,另一方有权解除本协议,并要求违约方承担相应责任;2. 若因不可抗力等不可控因素导致服务无法继续,双方可协商解除本协议。
第七条争议解决1. 双方因本协议引发的任何争议,应友好协商解决;协商不成,可提交仲裁机构解决。
第八条其他1. 本协议未尽事宜,双方可另行协商约定;2. 本协议一式两份,双方各执一份,具有同等法律效力。
天然气净化中的脱硫方法与节能措施
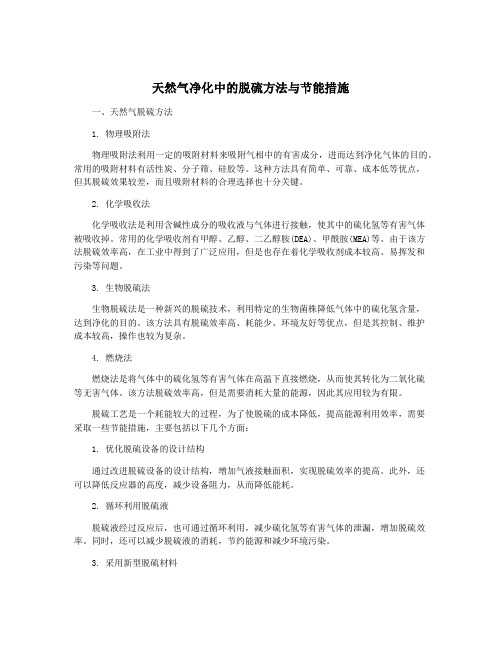
天然气净化中的脱硫方法与节能措施一、天然气脱硫方法1. 物理吸附法物理吸附法利用一定的吸附材料来吸附气相中的有害成分,进而达到净化气体的目的。
常用的吸附材料有活性炭、分子筛、硅胶等。
这种方法具有简单、可靠、成本低等优点,但其脱硫效果较差,而且吸附材料的合理选择也十分关键。
2. 化学吸收法化学吸收法是利用含碱性成分的吸收液与气体进行接触,使其中的硫化氢等有害气体被吸收掉。
常用的化学吸收剂有甲醇、乙醇、二乙醇胺(DEA)、甲酰胺(MEA)等。
由于该方法脱硫效率高,在工业中得到了广泛应用,但是也存在着化学吸收剂成本较高、易挥发和污染等问题。
3. 生物脱硫法生物脱硫法是一种新兴的脱硫技术,利用特定的生物菌株降低气体中的硫化氢含量,达到净化的目的。
该方法具有脱硫效率高、耗能少、环境友好等优点,但是其控制、维护成本较高,操作也较为复杂。
4. 燃烧法燃烧法是将气体中的硫化氢等有害气体在高温下直接燃烧,从而使其转化为二氧化硫等无害气体。
该方法脱硫效率高,但是需要消耗大量的能源,因此其应用较为有限。
脱硫工艺是一个耗能较大的过程,为了使脱硫的成本降低,提高能源利用效率,需要采取一些节能措施,主要包括以下几个方面:1. 优化脱硫设备的设计结构通过改进脱硫设备的设计结构,增加气液接触面积,实现脱硫效率的提高。
此外,还可以降低反应器的高度,减少设备阻力,从而降低能耗。
2. 循环利用脱硫液脱硫液经过反应后,也可通过循环利用,减少硫化氢等有害气体的泄漏,增加脱硫效率。
同时,还可以减少脱硫液的消耗,节约能源和减少环境污染。
3. 采用新型脱硫材料新型的脱硫材料具有吸附能力强、脱硫效率高等特点,可以降低脱硫设备的能耗。
此外,新型材料的生产成本也相对较低,因此在实际应用中具有广泛的市场前景。
4. 实施废气热回收废气热回收就是将排放的废气中含有的热量回收利用,用于加热脱硫液等,从而减少能源的浪费。
这将十分有利于天然气净化中能源利用的提高。
天然气干法脱硫技术

天然气干法脱硫技术1. 引言天然气作为一种清洁燃料,在能源领域扮演着重要的角色。
然而,天然气中的硫化氢和二氧化硫等有害气体会对环境和人体健康造成威胁。
因此,对天然气进行脱硫处理是必要的。
干法脱硫技术是一种成熟和高效的方法,本文将详细介绍天然气干法脱硫技术的原理、设备和工艺流程。
2. 原理干法脱硫技术是通过在一定的温度、压力和空气中使硫化氢和二氧化硫与添加剂发生化学反应,从而将其转化为易于处理的硫化物沉淀物。
干法脱硫技术的基本原理是利用添加剂对硫化氢和二氧化硫进行氧化反应,生成硫酸盐或硫酸,然后与添加剂中的氧化剂再次反应生成硫化物。
常用的氧化剂包括氢氧化钠、过硫酸钠等。
3. 设备天然气干法脱硫技术的设备主要包括脱硫反应器、氧化剂喷射装置、除尘设备和废气处理设备等。
3.1 脱硫反应器脱硫反应器是天然气干法脱硫的核心设备,其主要作用是提供反应的场所和条件。
脱硫反应器通常采用垂直筒形结构,内部充填着添加剂,如氢氧化钠颗粒。
天然气通过反应器时,与添加剂发生化学反应,脱硫效果显著。
3.2 氧化剂喷射装置氧化剂喷射装置用于向脱硫反应器中喷射氧化剂,提供氧气以促进脱硫反应。
常见的氧化剂喷射装置包括喷嘴和输送管道等。
3.3 除尘设备天然气中的颗粒物和灰尘会污染设备和环境,因此需要设置除尘设备,将颗粒物过滤掉。
常用的除尘设备包括布袋除尘器和电除尘器等。
3.4 废气处理设备天然气中的废气需要经过处理后才能排放。
常用的废气处理设备包括吸收塔、洗涤塔和催化转化器等,可以将废气中的硫化物进一步转化为无害物质,减少对环境的影响。
4. 工艺流程天然气干法脱硫技术的工艺流程主要包括:氧化剂喷射、脱硫反应、除尘和废气处理等步骤。
1.氧化剂喷射:将氧化剂喷射进入脱硫反应器中,提供氧气以促进反应。
2.脱硫反应:天然气通过脱硫反应器,与添加剂发生化学反应,生成硫酸盐或硫酸,然后与添加剂中的氧化剂再次反应生成硫化物。
3.除尘:将天然气中的颗粒物和灰尘通过除尘设备进行过滤,净化气体。
天然气脱硫脱碳工艺综述
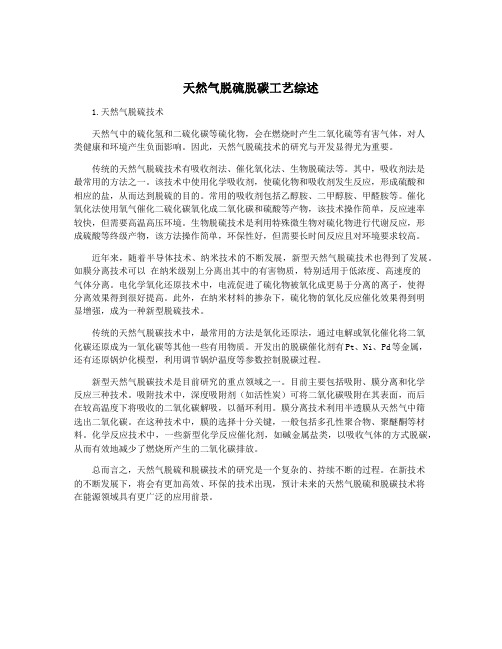
天然气脱硫脱碳工艺综述1.天然气脱硫技术天然气中的硫化氢和二硫化碳等硫化物,会在燃烧时产生二氧化硫等有害气体,对人类健康和环境产生负面影响。
因此,天然气脱硫技术的研究与开发显得尤为重要。
传统的天然气脱硫技术有吸收剂法、催化氧化法、生物脱硫法等。
其中,吸收剂法是最常用的方法之一。
该技术中使用化学吸收剂,使硫化物和吸收剂发生反应,形成硫酸和相应的盐,从而达到脱硫的目的。
常用的吸收剂包括乙醇胺、二甲醇胺、甲醛胺等。
催化氧化法使用氧气催化二硫化碳氧化成二氧化碳和硫酸等产物,该技术操作简单,反应速率较快,但需要高温高压环境。
生物脱硫技术是利用特殊微生物对硫化物进行代谢反应,形成硫酸等终级产物,该方法操作简单,环保性好,但需要长时间反应且对环境要求较高。
近年来,随着半导体技术、纳米技术的不断发展,新型天然气脱硫技术也得到了发展。
如膜分离技术可以在纳米级别上分离出其中的有害物质,特别适用于低浓度、高速度的气体分离。
电化学氧化还原技术中,电流促进了硫化物被氧化成更易于分离的离子,使得分离效果得到很好提高。
此外,在纳米材料的掺杂下,硫化物的氧化反应催化效果得到明显增强,成为一种新型脱硫技术。
传统的天然气脱碳技术中,最常用的方法是氧化还原法,通过电解或氧化催化将二氧化碳还原成为一氧化碳等其他一些有用物质。
开发出的脱碳催化剂有Pt、Ni、Pd等金属,还有还原锅炉化模型,利用调节锅炉温度等参数控制脱碳过程。
新型天然气脱碳技术是目前研究的重点领域之一。
目前主要包括吸附、膜分离和化学反应三种技术。
吸附技术中,深度吸附剂(如活性炭)可将二氧化碳吸附在其表面,而后在较高温度下将吸收的二氧化碳解吸,以循环利用。
膜分离技术利用半透膜从天然气中筛选出二氧化碳。
在这种技术中,膜的选择十分关键,一般包括多孔性聚合物、聚醚酮等材料。
化学反应技术中,一些新型化学反应催化剂,如碱金属盐类,以吸收气体的方式脱碳,从而有效地减少了燃烧所产生的二氧化碳排放。
天然气净化中的脱硫方法与节能措施
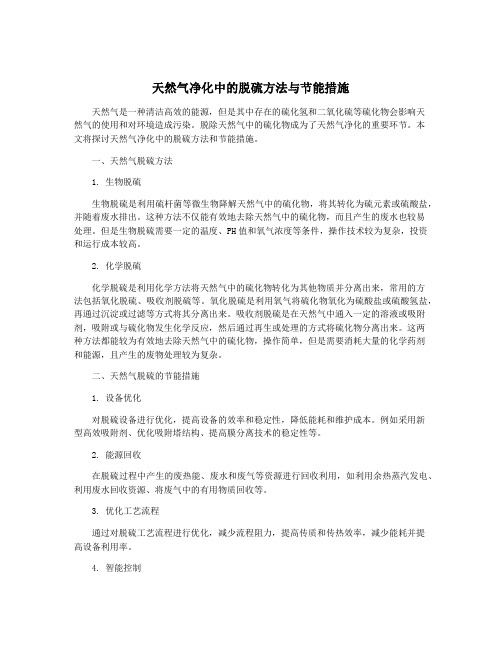
天然气净化中的脱硫方法与节能措施天然气是一种清洁高效的能源,但是其中存在的硫化氢和二氧化硫等硫化物会影响天然气的使用和对环境造成污染。
脱除天然气中的硫化物成为了天然气净化的重要环节。
本文将探讨天然气净化中的脱硫方法和节能措施。
一、天然气脱硫方法1. 生物脱硫生物脱硫是利用硫杆菌等微生物降解天然气中的硫化物,将其转化为硫元素或硫酸盐,并随着废水排出。
这种方法不仅能有效地去除天然气中的硫化物,而且产生的废水也较易处理。
但是生物脱硫需要一定的温度、PH值和氧气浓度等条件,操作技术较为复杂,投资和运行成本较高。
2. 化学脱硫化学脱硫是利用化学方法将天然气中的硫化物转化为其他物质并分离出来,常用的方法包括氧化脱硫、吸收剂脱硫等。
氧化脱硫是利用氧气将硫化物氧化为硫酸盐或硫酸氢盐,再通过沉淀或过滤等方式将其分离出来。
吸收剂脱硫是在天然气中通入一定的溶液或吸附剂,吸附或与硫化物发生化学反应,然后通过再生或处理的方式将硫化物分离出来。
这两种方法都能较为有效地去除天然气中的硫化物,操作简单,但是需要消耗大量的化学药剂和能源,且产生的废物处理较为复杂。
二、天然气脱硫的节能措施1. 设备优化对脱硫设备进行优化,提高设备的效率和稳定性,降低能耗和维护成本。
例如采用新型高效吸附剂、优化吸附塔结构、提高膜分离技术的稳定性等。
2. 能源回收在脱硫过程中产生的废热能、废水和废气等资源进行回收利用,如利用余热蒸汽发电、利用废水回收资源、将废气中的有用物质回收等。
3. 优化工艺流程通过对脱硫工艺流程进行优化,减少流程阻力,提高传质和传热效率,减少能耗并提高设备利用率。
4. 智能控制采用先进的自动化和智能控制技术,实现设备的智能化运行,减少人为操作和监管,提高设备的运行稳定性和效率。
5. 节能改造对现有的脱硫设备进行节能改造,采用新型高效节能设备、加装废热回收设备、优化设备运行参数等。
结语:天然气脱硫是天然气净化的关键环节,采用适当的脱硫方法和节能措施,不仅可以有效地去除天然气中的硫化物,降低环境污染,而且可以减少能源消耗,提高能源利用效率,实现可持续发展。
天然气脱硫工艺介绍

天然气脱硫工艺介绍( 1)工程中常用的天然气脱硫方法天然气脱硫的方法有很多种,习惯上把采用溶液或溶剂做脱硫剂的脱硫方法称为湿法脱硫,采用固体做脱硫剂的脱硫方法称为干法脱硫。
一般的湿法脱硫有化学溶剂法(如醇胺法)、物理溶剂法(如 Selexol 法、Flour 法)、化学 -物理溶剂法(如砜胺法)和直接转化法(如矾法、铁法)。
常见的干法脱硫有膜分离法、分子筛法、不可再生固定床吸附法和低温分离法等。
(2)天然气脱硫方法选用原则天然气组分、处理量、硫含量、厂站所处自然条件、产品质量要求、运行操作要求等都是天然气脱硫工艺的选择依据。
目前,根据国内外工业实践的经验,天然气脱硫脱碳工艺的选择原则可参考以下内容。
①原料气中含硫量高,处理量大,硫碳比高需要选择性吸收H2S 同时脱除相当量的 CO2,原料气压力低,净化气 H2S 要求严格等条件下,可选择醇胺法作为脱酸工艺。
②原料气中含有超量的有机硫化物需要脱除,宜选用砜胺法。
此外,H2S 分压高的原料气选用砜胺法时能耗远低于醇胺法。
③ H2S 含量较低的原料气中,潜硫量在0.2t/d~5t/d 时可考虑直接转化法,潜硫量低于 0.2t/d 的可选用非再生固体脱硫法如固体氧化铁法等。
实践中,往往在选择基本工艺方案之后,根据具体情况进行技术经济比较,最终确定天然气的脱硫脱碳方法。
图 1 和图 2 分别表示了原料气中酸气分压和出口气质量指标对脱硫方案选择的影响。
图 1 脱硫方案选择与酸气分压的关系图 2 脱硫方案选择与进、出口气质量指标的关系( 3)低含硫量天然气脱硫方案某项目天然气组分和参数如下:表 1 原料气组分表序号名称组分备注1N 20.001222CO20.01213H2S0.00014C10.7223634775C20.142121256C30.06867i-C40.01268n-C40.0239i-C50.0064310n-C50.0052311C60.0020512C70.0010813C8+0.00094527314H2O0.0021615合计 1.000表 2 原料气工艺参数表序号名称单位前期中期后期1操作压力psig125012501250 2操作温度℉96110110 3气源流量MMSCFD10 5.19.54气源密度 (操作条件 )lb/ft 36.95 6.588 6.7375出口气含硫量ppmv不大于 4由表可知,本工程的特点是含硫量低,处理量不大,出口气要求较严格。
天然气脱硫脱碳工艺综述
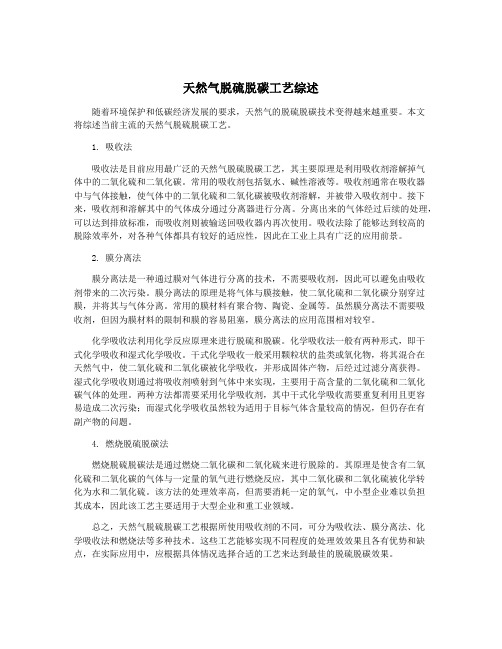
天然气脱硫脱碳工艺综述随着环境保护和低碳经济发展的要求,天然气的脱硫脱碳技术变得越来越重要。
本文将综述当前主流的天然气脱硫脱碳工艺。
1. 吸收法吸收法是目前应用最广泛的天然气脱硫脱碳工艺,其主要原理是利用吸收剂溶解掉气体中的二氧化硫和二氧化碳。
常用的吸收剂包括氨水、碱性溶液等。
吸收剂通常在吸收器中与气体接触,使气体中的二氧化硫和二氧化碳被吸收剂溶解,并被带入吸收剂中。
接下来,吸收剂和溶解其中的气体成分通过分离器进行分离。
分离出来的气体经过后续的处理,可以达到排放标准,而吸收剂则被输送回吸收器内再次使用。
吸收法除了能够达到较高的脱除效率外,对各种气体都具有较好的适应性,因此在工业上具有广泛的应用前景。
2. 膜分离法膜分离法是一种通过膜对气体进行分离的技术,不需要吸收剂,因此可以避免由吸收剂带来的二次污染。
膜分离法的原理是将气体与膜接触,使二氧化硫和二氧化碳分别穿过膜,并将其与气体分离。
常用的膜材料有聚合物、陶瓷、金属等。
虽然膜分离法不需要吸收剂,但因为膜材料的限制和膜的容易阻塞,膜分离法的应用范围相对较窄。
化学吸收法利用化学反应原理来进行脱硫和脱碳。
化学吸收法一般有两种形式,即干式化学吸收和湿式化学吸收。
干式化学吸收一般采用颗粒状的盐类或氧化物,将其混合在天然气中,使二氧化硫和二氧化碳被化学吸收,并形成固体产物,后经过过滤分离获得。
湿式化学吸收则通过将吸收剂喷射到气体中来实现,主要用于高含量的二氧化硫和二氧化碳气体的处理。
两种方法都需要采用化学吸收剂,其中干式化学吸收需要重复利用且更容易造成二次污染;而湿式化学吸收虽然较为适用于目标气体含量较高的情况,但仍存在有副产物的问题。
4. 燃烧脱硫脱碳法燃烧脱硫脱碳法是通过燃烧二氧化碳和二氧化硫来进行脱除的。
其原理是使含有二氧化硫和二氧化碳的气体与一定量的氧气进行燃烧反应,其中二氧化碳和二氧化硫被化学转化为水和二氧化硫。
该方法的处理效率高,但需要消耗一定的氧气,中小型企业难以负担其成本,因此该工艺主要适用于大型企业和重工业领域。
浅析天然气脱硫主要方法

浅析天然气脱硫主要方法天然气是一种重要的清洁能源,但在其生产和利用过程中会产生一定的硫化氢和二氧化硫等有害气体。
这些有害气体不仅对环境造成污染,而且对人体健康也会造成危害。
对天然气中的硫化氢和二氧化硫进行脱除是十分必要的工作。
目前,主要的天然气脱硫方法包括物理吸附法、化学吸收法和生物脱硫法等。
本文将对这些主要的脱硫方法进行一次浅析。
一、物理吸附法物理吸附法主要是通过适当的吸附剂将天然气中的硫化氢和二氧化硫吸附下来,从而实现脱硫的目的。
目前广泛应用的吸附剂有活性炭、分子筛和硅胶等。
物理吸附法的工作原理比较简单,操作成本低,但是由于对硫化氢和二氧化硫的吸附能力有限,所以需要定期更换或再生吸附剂,增加了运行成本。
物理吸附法只能对低浓度的硫化氢和二氧化硫进行有效脱除,对于高浓度的有害气体效果不佳。
二、化学吸收法化学吸收法是利用具有一定亲和力的化学溶剂,将天然气中的硫化氢和二氧化硫溶解到溶剂中,再通过吸收溶剂再生的方式实现脱硫。
目前应用较多的化学吸收剂有胺类和碱液等。
化学吸收法脱硫效率高,能够对高浓度的硫化氢和二氧化硫进行有效脱除,但操作成本较高,而且对溶剂的再生和回收过程存在一定的技术难度。
三、生物脱硫法生物脱硫法是利用一些特定的微生物或者酶类来将天然气中的硫化氢和二氧化硫进行生物降解,从而实现脱硫的目的。
生物脱硫法是一种环保、经济的脱硫方法,具有设备简单、能耗低、无二次污染等优点。
但是生物脱硫法需要较为长时间的培养和生物反应过程,对操作人员的技术要求较高。
以上所述为天然气脱硫的主要方法,不同的方法各有优劣,具体应用还需根据天然气脱硫的实际情况来选择。
未来,随着环保技术的发展和进步,相信会有更多更先进的脱硫方法应用于天然气脱硫领域,为清洁能源的生产和利用提供更为可靠的技术支撑。
- 1、下载文档前请自行甄别文档内容的完整性,平台不提供额外的编辑、内容补充、找答案等附加服务。
- 2、"仅部分预览"的文档,不可在线预览部分如存在完整性等问题,可反馈申请退款(可完整预览的文档不适用该条件!)。
- 3、如文档侵犯您的权益,请联系客服反馈,我们会尽快为您处理(人工客服工作时间:9:00-18:30)。
脱硫后的酸气主要成分是硫化氢(H2S)和二氧化碳(CO2)的混合气体,其组成为(体积分数,%):H2S32~36;CO260~65;CH4~1.5。
酸气中的CO2和H2S是极好的化工原料。
以前,高硫含量的酸气,用克劳斯法生产硫磺,产品单一,经济效益较低,制硫尾气中仍含少量H2S,不能排放,需经焚烧后高烟囱排入大气。
这样既浪费宝贵的化工原料又造成大气污染。
为了更加合理有效地利用资源、减少废气污染、提高酸气治理的经济效益,通过查阅相关资料,我们找到了一种综合利用方案—酸气制备碳酸锶(SrCO3)、硫氢化钠(NaHS)、硫磺(S)、硫代硫酸钠(Na2S2O3・5H2O)。
酸气通过碳还原硫酸锶的SrS溶液,生成SrCO3;碳化尾气用Na2S溶液吸收,生成NaHS;NaHS尾气采用克劳斯法制备硫磺;制硫尾气与H2S燃烧气体部分混合后,用纯碱液吸收,添加硫磺合成硫代硫酸钠。
废气排放符合国家标准。
上述产品除硫磺建有生产装置外,其余品种的生产工艺均采用本厂的酸气,产品质量符合标准,排放废气基本无有毒有害气体H2S和SO2。
产品市场销售畅通,经济效益和社会效益好。
现将SrCO3、NaHS、Na2S2O3・5H2O生产情况分别叙述如下。
1 碳酸锶
规模3000t/a,产品质量标准GB10660—89。
1.1 技术方案
碳还原法制SrCO3。
1.1.1 反应原理
SrSO4+2C←→SrS+2CO2↑
CO2+SrS+H2O←→SrCO3+H2S↑
1.1.2 工艺流程及简述
天青石矿体统返回水酸气
↓↓↓
↓↓↓
弃渣碳化尾气制
↓ SrCO3
酸气制碳酸锶工艺流程
天青石、焦炭分别粉碎至规定细度,按比例混合,投入回转窑内经高温还原为SrS熟料,用水浸取,过滤洗涤,SrS溶液通入酸气,生成SrCO3,过滤洗涤,干燥获SrCO3产品。
碳化尾气制NaHS,滤渣经第二次浸取后弃之;滤液、洗水合并返回一次浸取。
1.2生产工艺
1.2.1 主要原料与设备
酸气、天青石矿、焦炭;回转窑、SrS浸取槽、过滤机、碳化塔、回转干燥器、溶液贮槽等。
1.2.2 主要工艺条件
还原:矿粉细度150~180m;矿∶煤=1∶0.6~1;温度1100~1200℃;物料停留时间1~1.5h。
浸取:固∶液=1∶5~7;温度80~95℃;时间4.5~5h(两次浸取)。
碳化:酸气空塔速度0.05~0.06m/s;酸气压力0.1~0.2MPa;碳化温度60~70℃;碳化终点pH值~7。
干燥:温度350~400℃;时间1~1.5h;产品包装温度40℃。
1.2.3 结果
SrCO3生产工艺稳定、可行,产品质量达到国家标准。
锶总回收率大于70%,CO2利用率60%,酸气中H2S提高至60%~65%。
废渣主要成分是未分解的天青石矿、SiO2、少许煤粉,基本无废水、废气排放。
原材料及动力消耗定额见表2。
表2 原材料动力消耗表
名称天青石
矿/t 焦炭
/t
酸气
/m3
水
/t
蒸汽
/t
天然气
/m3
电
kW·h
规格% SrSO4
≥78
C
≥85
CO2
≥35
——CH4
≥95
—
消耗定
额/t
2.2 1.2 600 12 4 300 450
2 硫氢化钠
规模3000t/a;副产SrCO3650t/a。
硫氢化钠企业标准为:NaHS≥70%,Na2S<3.0%。
2.1 技术方案
2.1.1 反应原理
主反应:
Na2S+H2O←→NaOH+NaHS
NaOH+H2S—→NaHS+H2O
Na2S+H2S—→2NaHS
副反应:
NaOH+CO2—→Na2CO3+H2O
Na2CO3+CO2+H2O—→NaHCO3
NaHS+CO2+H2—→ONaHCO3+H2S
NaHS与NaHCO3的分离可用SrS清液与溶液中NaHCO3生成SrCO3沉淀,其反应式如下:
NaHCO3+SrS—→SrCO3↓+NaHS
2.1.2 工艺流程(见图2)及简述
Na2S溶液 SrS清液
↓↓
↓↓
尾气制S NaHS
图2 硫氢化纳生产工艺流程
碳化尾气通入Na2S溶液吸收塔,流出溶液中加入SrS溶液,析出SrCO3,过滤洗涤,滤液蒸发浓缩得NaHS产品。
洗出液循环配制Na2S溶液沉淀SrCO3送至碳酸锶车间干燥得产品。
2.2 生产工艺
2.2.1 主要原料与设备
碳化尾气、Na2S溶液、SrS清液;H2S吸收塔、NaHCO3转化槽、过滤机、NaHS蒸发浓缩器、溶液贮槽。
2.2.2主要工艺条件
气体流量100~107m3/h;
压力0.03~0.05MPa;
空塔速度≤0.3m/s。
Na2S溶液浓度20%~22%;
喷淋密度13~15m3/m2・h。
NaHS浓缩终止温度175℃左右。
2.2.3 结果
硫氢化钠生产工艺稳定、可行,产品质量达到企业标准。
副产品SrCO3同样达到国家标准。
H2S吸收率60%~65%,Na2S利用率98%。
本产品基本无“三废”排放。
原材料及动力消耗定额见表3。
表3 原材料动力消耗综合表
名称规格/% 单t消耗定额
硫化钠/t Na2S≥60 0.85
碳化尾气/m3 H2S≥65 2580
无然气/m3 CH4≥95 37
电/kW・h 106
3 硫代硫酸钠
规模3000t/a,Na2S2O3・5H2O
产品质量标准:HG1—210—79。
3.1 技术方案硫磺纯碱法。
3.1.1反应原理
2H2S+3O2—→2SO2+2H2O
SO2+Na2CO3—→Na2SO3+CO2
Na2SO3+S—→Na2S2O3
3.1.2工艺流程及简述
H2S燃烧气按比例与制S第二转换出气相混合后,通入Na2CO3溶液吸收塔,在流出的Na2SO3溶液中添加S,加热蒸煮合成Na2S2O3,过滤,滤液蒸发浓缩,保温脱硝,冷却结晶,过滤洗涤,得Na2S2O3・5H2O产品。
母液返回蒸发浓缩。
吸收塔排出废气直接放空。
生产工艺流程见图3。
废气硫磺
燃烧炉气↘↑↓
制S
↑↓
Na2CO3溶液
Na2S2O3·5H2O┙
图3 硫代硫酸钠生产工艺流程
3.2 生产工艺
3.2.1 主要原料与设备
混合气体,碳酸钠,硫磺;气体混合器,吸收塔,反应釜,二效真空蒸发器,结晶槽,过滤机,贮槽。
3.2.2 主要工艺条件
混合气SO2≥6%,少许H2S;
温度150~200℃;
压力:0.05MPa;
空塔速度:0.7m/s。
Na2CO3溶液浓度16%~20%;
喷淋密度8m3/m2・h;
喷淋量4m3/h;
吸收溶液浓度Na2S2O320%~22%。
加S合成温度100~108℃。
第二效蒸发完成溶液浓度Na2S2O357%;脱硝温度≥85℃。
结晶温度47~50℃。
3.2.3 结果
Na2S2O3・5H2O生产工艺稳定、可行,产品质量符合HG1—210—79。
SO2吸收率大于98%,合成率98%,S利用率98%,Na2CO3利用率95%。
排放废气基本无有毒气体H2S和有害气体SO2,符合国家废气排放标准。
生产过程基本无废渣、废水排放。
原材料及动力消耗定额见表4。
表4 原材料动力消耗综合表
名称规格单t消耗定额
混合气体/m3 SO2≥6% 226
碳酸钠/t Na2CO3≥98% 0.49
硫磺/t S≥99% 0.145
电/kW・h 275
蒸汽/t 0.5MPa 3
结论
酸气制备SrCO3、NaHS、S、Na2S2O3・5H2O产品总体工艺流程研究设计合理,试验生产稳定、可行。
SrCO3、NaHS、Na2S2O3・5H2O、S产品质量分别达到国家、行业和企业标准。
生产过程中基本无有毒有害气体排出,废气主要成分为N2、CO2和水蒸气;生产过程中绝大部分水在系统中循环使用,有少许设备、地面清洗水排出,基本无有害成分;SrCO3车间有固体废渣排出,主要成分为未分解的矿石、SiO2和少许煤粉,达到“三废”治理之目的。
!新增SrCO3、NaHS和Na2S2O3・5H2O产品成本较低,市场较好,经济效益和社会效益好。