IPD16CN10NG中文资料
CN1610集群网络开关迁移指南说明书

Migrating to a two-node switched cluster with CN1610cluster switchesIf you have an existing two-node switchless cluster environment that uses cluster network switches,you can migrate to a two-node switched cluster environment using CN1610cluster network switches.The procedure you use depends on whether you have two dedicated cluster-network ports on each controller (as required on most systems)or a single cluster port on each controller(a supported option on N3150,N3220,and N3240storage systems).About this taskThere are two migration options available:v Migrating from a switchless cluster to a switched CN1610cluster environmentv Migrating from a switchless cluster(systems with a single cluster-network connection)Migrating from a switchless cluster to a switched CN1610cluster environmentIf you have an existing two-node switchless cluster environment,you can migrate to a two-node switched-cluster environment using CN1610cluster network switches.Before you beginTwo-node switchless configuration:v The two-node switchless configuration must be properly set up and functioning.v The nodes must be running Data ONTAP8.2or later.v All cluster ports must be in the up state.v All cluster LIFs must have be in the up state and on their home ports.CN1610cluster switch configuration:v The CN1610cluster switch infrastructure be redundant and fully functional on both switches.Refer to the IBM N series support website to ensure you have the latest RCF and FASTPATH versions on your switches.v Management network connectivity on both switches.v Console access to the cluster switches.v Necessary cabling for the node-to-switch and switch-to-switch connections has been completed.Twinax or fiber is supported for the CN1610switch.For more information on cabling,see Installation and Setup Instructions of your storage system and Clustered Data ONTAP Switch Setup and Configuration Guide.v Inter-Switch Link(ISL)cables are connected to ports13through16on both CN1610switches.v Initial customization of both CN1610switches has been completed.About this taskThis procedure migrates nodes in a two-node switchless environment into a two-node switched environment.The examples in this procedure use the following switch and node nomenclature:v cs1and cs2are the CN1610switches.v clus1and clus2are the cluster logical interfaces(LIFs).v The names of the Vservers are node1and node2.v The cluster::*>prompt indicates the name of the cluster.v The cluster ports used in this procedure as an example are e1a and e2a.Refer to the Installation and Setup Instructions of your storage system for the supported cluster ports.Procedure1.Disable all node-facing ports on both new cluster switches cs1and cs2.Do not disable the ISL ports.e the show port channel command to verify that the ISL and the physical ports on the ISLbetween the two CN1610cluster switches cs1and cs2are up.Results for the cs2switch:2e the show isdp neighbors command to display the list of neighboring devices.e the run*cdpd show-neighbors to ensure that each cluster port is connected to thecorresponding port on its partner cluster node.This example verifies that cluster ports e1a and e2a are connected to the same port on its cluster partner node:3e the network interface show-role cluster to ensure that all cluster LIFs are up ande the network interface modify command and set the auto revert parameter to false on clus1e the network interface migrate command on the console of each node to migrate clus1to port8.Shut down cluster port e1a on both nodes with the network port modify command.Verify the portstatus with the network port show command:49.Disconnect the cable from e1a on node1.Connect e1a on node1to port1on cs1,using theappropriate cabling supported by the CN1610switches.For more information on cabling,seeInstallation and Setup Instructions of your storage system and Clustered Data ONTAP Switch Setup and Configuration Guide.10.Disconnect the cable from cluster port e1a on node2.Connect e1a to port2on cs1,using theappropriate cabling supported by CN1610switches.11.12.13.14.Revert clus1(which was previously migrated)on both nodes back to e1a with the network interfacee the network interface show command to ensure that all cluster LIFs are up and operational anddisplay true in the Is Home column:516.17.On the console of each node,use the network interface migrate command to migrate clus2to porte the network port modify to shut down cluster port e2a on both e the network port19.Disconnect the cable from e2a on node1.Connect e2a on node1to port1on cs2using theappropriate cabling supported by CN1610switches.20.On node2,disconnect the cable from cluster port e2a.Connect e2a to port2on cs2,using theappropriate cabling supported by CN1610switches.21.622.23.24.On all nodes,revert clus1(which was previously migrated)back to e1a with the network interfacee the network interface show command to verify that all of the interfaces display true in the Ise the show isdp neighbors command to verify that both nodes have two connections to eachswitch.7e the run*cdpd show-neighbors command to ensure that each cluster port is connected correctlyto each cluster switch.This example verifies that cluster ports e1a and e2a are connected to the corresponding ports on28.29.e the network interface modify command and set the auto revert parameter to true on clus131.For more information,see Clustered Data ONTAP Switch Setup and Configuration Guide.Migrating to a two-node switched cluster(systems with a single cluster-network connection)If you have N3150,N3220,and N3240systems in an existing two-node switchless cluster in which each controller has a single,back-to-back10-GbE connection for cluster connectivity,you can use the switchless-cluster networking option and replace the direct back-to-back connectivity with switch connections.This is a non-disruptive procedure.Before you beginv Two cluster connections are required to migrate from a switchless configuration to a switched configuration.8v The cluster must be healthy and consist of two nodes connected with back-to-back connectivity.The nodes must be running Data ONTAP8.2or later.v The switchless cluster feature cannot be used with more than two nodes.v All cluster ports must be in the up state.About this taskThis procedure removes the direct cluster connectivity in a switchless environment and replaces each connection to the switch with a connection to the partner node.Procedure1.Check the cluster status of the nodes by entering the following command at the system console ofeither node:cluster show2.Check the status of the by entering the following command at the system console of either node:storage failover show3.Enter the following command at either node's prompt to change to the advanced privilege level:set-privilege advancedYou can respond y when prompted to continue into advanced mode.The advanced mode prompt appears(*>).4.Verify that the current state of the switchless cluster is true and then disable switchless-cluster mode:network options switchless-cluster modify-enabled false5.Enter the following command to return to the admin privilege level:set-privilege admin6.Take over the target node by entering the following command:storage failover takeover-ofnode target_node_nameIt does not matter which node is the target node.When it is taken over,the target nodeautomatically reboots and displays the Waiting for giveback...message.The active node is now serving data for the partner(target)node that has been taken over.7.It a node is impaired,wait at least two minutes after the takeover of the impaired node to ensurethat the takeover completed successfully.8.With the target node showing the Waiting for giveback...message,shut it down.The method youuse to shut down the node depends on whether remote management via a Service Processor(SP)is used.Is the SP configured?Then...Yes Log in to theimpaired node's SP and enter the followingcommand:system power off.9Is the SP configured?Then...No At the impaired node's prompt,press Ctrl-C andrespond Y to halt the node.9.On each controller,disconnect the cable that connects the10G cluster port to the switchless cluster.10.Connect the10-GbE cluster port to the switch on both controllers.Verify that the10-GbE clusterports connected on the switch are configured to be part of the same VLAN.If you plan onconnecting the cluster ports on each controller to different switches,verify that the ports on which the cluster ports are connected on each switch are configured for the same VLAN and that trunking is properly configured on both switches.11.Enter the following command to give back storage to the target node:storage failover giveback-ofnode node212.Enter the storage failover show-giveback command to monitor the progress of the givebackoperation.13.After the giveback operation is complete,enter the storage failover show command to confirm that14.Verify that the cluster port LIFs are operating correctly:15.Check the cluster status of the nodes by entering the following command at the system console ofeither node:cluster show16.Verify cluster connectivity with the cluster ping-cluster local command:a.Enter the following command at either node's prompt to change to the advanced privilege level:set-privilege advancedYou can respond y when prompted to continue into advanced mode.The advanced mode prompt appears(*>).b.Enter the following command to ping the cluster ports:cluster ping-cluster localThe command output should show connectivity between all cluster ports.c.Enter the following command to return to the admin privilege level:set-privilege admin10©Copyright IBM Corporation2013.US Government Users Restricted Rights–Use,duplication or disclosure restricted by GSA ADP Schedule Contract with IBM Corp.SC27-6298-00。
CIT-10中文手册new

端口进行连接,打开设备电源,此时系统会自动安装USB的驱动; z 安装后系统会产生一个名为CIT的目录(默认路径为C:\Program Files\CIT),目录中会
型号应用ae连接器eut连接器cdn801m1非屏蔽线主要4mmmc插孔4mmmc插孔cdn801m2非屏蔽线主要4mmmc插孔4mmmc插孔cdn801m3非屏蔽线主要4mmmc插孔4mmmc插孔cdn801m4非屏蔽线主要4mmmc插孔4mmmc插孔cdn801m5非屏蔽线主要4mmmc插孔4mmmc插孔cdn801m2m3非屏蔽线主要4mmmc插孔4mmmc插孔cdn801s1屏蔽线bncbnccdn801s2屏蔽线xlrfemalexlrmalecdn801s9屏蔽线subdcdn801s25屏蔽线subd25公subd25公cdn801af2非屏蔽非平衡线终端模块终端模块cdn801af4非屏蔽非平衡线终端模块终端模块cdn801af6非屏蔽非平衡线终端模块终端模块cit10cit1075用户手册19cdn801af8非屏蔽非平衡线终端模块终端模块cdn801t2非屏蔽平衡对线终端模块终端模块cdn801t4非屏蔽平衡对线终端模块终端模块cdn801t8非屏蔽平衡对线终端模块终端模块cdn801rj11非屏蔽数据线rj11接口rj11接口cdn801rj11s屏蔽数据线rj11接口rj11接口cdn801rj45非屏蔽数据线rj45接口rj45接口cdn801rj45s屏蔽数据线rj45接口rj45接口cdn801usbcusb设备usbausbbcdn801usbpusb设备usbbusba57技术参数rf功率表频率范围10khz400mhz测试电平30dbm40dbm精度典型值05db最大值10dbvswr输入接口bnc50欧姆rf信号发生器输出接口bnc50欧姆频率范围10khz400mhz频率分辨率hz输出电平63dbm输出电平分辨率01db输出电平精度典型值05db最大值10db精度频率ppmtcxo失真谐波30dbc
CN18J中文资料

NUMBER OF CYCLES AT 60Hz
FIG 4 . - TYPICAL JUNCTION CAPACITANCE JUNCTION CAPACITANCE, (pF)
2000 1000 500
FORWARD CURRENT, AMPERES
TJ = 25 °C
10
100 50
UPDATE : APRIL 23, 1998
元器件交易网
RATING AND CHARACTERISTIC CURVES ( CN18A - CN18M )
AVERAGE FORWARD OUTPUT CURRENT, AMPERES
FIG.1 - DERATING CURVE FOR OUTPUT RECTIFIED CURRENT PEAK FORWARD SURGE CURRENT, AMPERES
Typical Junction Capacitance (Note 1) Thermal Resistance, Junction to Case Junction Temperature Range Storage Temperature Range
Note : (1) Measured at 1.0 MHz and applied reverse Voltage of 4.0 V DC
CELL RECTIFIER DIODES
C18A
6.20
5.4
ANODE 1.43 CATHODE
0.51
0.38ቤተ መጻሕፍቲ ባይዱ
MECHANICAL DATA :
* Case : C18A * Terminals : Solderable per MIL-STD-202, Method 208 guaranteed * Polarity : Cathode to bigger size slug, For Anode to bigger size slug use "R" suffix. * Mounting position : Any * Weight : 0.29 gram Dimensions in millimeter
EN25QH16-104HIP中文资料(Eon Silicon)中文数据手册「EasyDatasheet - 矽搜」

3
VSS
4
8 VCC 7 HOLD# (DQ 3) 6 CLK 5 DI (DQ 0)
8 - 引脚SOP / PDIP
CS# 1 DO (DQ 1) 2 WP# (DQ 2) 3
VSS 4
8 VCC 7 HOLD# (DQ 3) 6 CLK 5 DI (DQ 0)
8 - 铅VDFN
芯片中文手册,看全文,戳
可锁定512字节OTP安全部门
支持串行闪存可发现 参数(小农发展方案)签名
阅读唯一ID号 最低100K耐久性周期
封装选项 - 8引脚SOP 150mil体宽 - 8引脚SOP 200mil体宽 - 8接触VDFN(5x6mm) - 8引脚PDIP - 24球TFBGA封装(6x8mm)
- 所有无铅封装符合RoHS标准
顶 视 图 ,球 朝 下
EN25QH16
24 - 球TFBGA
芯片中文手册,看全文,戳
图 2.框 图
EN25QH16
Note: 1. DQ 0 和DQ 1 用于双核和四核指令. 2. DQ 0 ~ DQ 3 用于四路说明.
芯片中文手册,看全文,戳
表 1.引 脚 名 称
该EN25QH16被设计为允许任何单
扇区/块
在同一时间或整片擦除操作.
该EN25QH16可以被配置为防护护存储器作为软件防护护模式一部分.该
设备可以维持一个最低100K编程/擦除周期每一个扇区
或块 .
芯片中文手册,看全文,戳
图一接线图
EN25QH16
CS#
1
DO (DQ 1)
2
WP# (DQ 2)
芯片中文手册,看全文,戳
EN25QH16
16兆 位 串 行 闪 存 与 4K字 节 统 一 部 门
MB85RC16PNF-G-JNE1;中文规格书,Datasheet资料

FUJITSU SEMICONDUCTORDATA SHEETCopyright©2011 FUJITSU SEMICONDUCTOR LIMITED All rights reserved 2011.6Memory FRAM16 K (2 K × 8) Bit I 2CMB85RC16■DESCRIPTIONThe MB85RC16 is an FRAM (F erroelectric Random Access Memory) chip in a configuration of 2,048 words × 8 bits, using the ferroelectric process and silicon gate CMOS process technologies for forming the nonvolatile memory cells.Unlike SRAM, the MB85RC16 is able to retain data without using a data backup battery.The memory cells used in the MB85RC16 have at least 1010 Read/Write operation endurance per bit, which is a significant improvement over the number of read and write operations supported by other nonvolatile memory products.The MB85RC16 can provide writing in one byte units because the long writing time is not required unlike Flash memory and E 2PROM. Therefore, the writing completion waiting sequence like a write busy state is not required.■FEATURES•Bit configuration : 2,048 words × 8 bits •Operating power supply voltage : 2.7 V to 3.6 V •Operating frequency : 1 MHz (Max) •T wo-wire serial interface : Fully controllable by two ports: serial clock (SCL) and serial data (SDA).•Operating temperature range : − 40 °C to + 85 °C •Data retention : 10 years ( + 75 °C) •Read/Write endurance : 1010 times •Package : Plastic / SOP , 8-pin (FPT -8P-M02)•Low power consumption : Operating current 0.1mA (Max: @1 MHz), Standby current 0.1 μA (Typ)DS501-00001-2v0-EMB85RC16■PIN FUNCTIONAL DESCRIPTIONSPinNumberPin Name Functional Description1 to 3NC Unconnected pins Leave it unconnected.4VSS Ground pin5SDA Serial Data I/O pinThis is an I/O pin of serial data for performing bidirectional communication of mem-ory address and writing or reading data. It is possible to connect some devices. It is an open drain output, so a pull-up resistance is required to be connected to the external circuit.6SCL Serial Clock pinThis is a clock input pin for input/output timing serial data. Data is sampled on the rising edge of the clock and output on the falling edge.7WP Write Protect pinWhen Write Protect pin is “H” level, writing operation is disabled. When Write Pro-tect pin is “L” level, the entire memory region can be overwritten. Reading operation is always enabled regardless of the Write Protect pin state. The write protect pin is internally pulled down to VSS pin, and that is recognized as “L” level (the state that writing is enabled) when the pin is the open state.8VDD Supply Voltage pinMB85RC16■I2C (Inter-Integrated Circuit)The MB85RC16 has the two-wire serial interface and the I2C bus, and operates as a slave device.The I2C bus defines communication roles of “master” and “slave” devices, with the master side holding the authority to initiate control. Furthermore, a I2C bus connection is possible where a single master device is connected to multiple slave devices in a party-line configuration.2MB85RC16■I2C COMMUNICATION PROTOCOLThe I2C bus provides communication by two wires only, therefore, the SDA input should change while SCL is the “L” level. However, when starting and stopping the communication sequence, SDA is allowed to change while SCL is the “H” level.•Start ConditionTo start read or write operations by the I2C bus, change the SDA input from the “H” level to the “L” level while the SCL input is in the “H” level.•Stop ConditionTo stop the I2C bus communication, change the SDA input from the “L” level to the “H” level while the SCL input is in the “H” level. In the reading operation, inputting the stop condition finishes reading and enters the standby state. In the writing operation, inputting the stop condition finishes inputting the rewrite data.Note : The FRAM device does not need the programming wait time (t WC) after issuing the Stop Condition during the write operation.MB85RC16■ACKNOWLEDGE (ACK)In the I2C bus, serial data including memory address or memory information is sent in units of 8 bits. The acknowledge signal indicates that every 8 bits of the data is successfully sent and received. The receiver side usually outputs the “L” level every time on the 9th SCL clock after every 8 bits are successfully trans-mitted. On the transmitter side, the bus is temporarily released on this 9th clock to allow the acknowledge signal to be received and checked. During this released period, the receiver side pulls the SDA line down to indicate that the communication works correctly.If the receiver side receives the stop condition before transmitting the acknowledge “L” level, the read operation ends and the I2C bus enters the standby state. If the acknowledge “L” level is not detected, and the Stop condition is not sent, the bus remains in the released state without doing anything.■MEMORY ADDRESS STRUCTUREThe MB85RC16 has the memory address buffer to store the 11-bit information for the memory address.As for byte write, page write and random read commands, the complete 11-bit memory address is configured by inputting the memory upper address (3 bits) and the memory lower address (8 bits), and saving to the memory address buffer and access to the memory is performed.As for a current address read command, the complete 11-bit memory address is configured by inputting the memory upper address (3 bits) and by the memory address lower 8-bit which has saved in the memory address buffer, and saving to the memory address buffer and access to the memory is performed.MB85RC16■DEVICE ADDRESS WORDF ollowing the start condition, the 8 bit device address word is input. Inputting the device address word decideswhether the master or the slave drives the data line. However, the clock is always driven by the master. The device address word (8bits) consists of a device T ype code (4bits), memory upper address code (3bits), anda Read/Write code (1bit).•Device Type Code (4bits)The upper 4 bits of the device address word are a device type code that identifies the device type, and are fixed at “1010” for the MB85RC16.•Memory Upper Address Code (3bits)Following the device type code, the 3 bits of the memory upper address code are input.The slave address selection is not performed by the external pin setting on this device. These 3 bits are not the setting bits for the slave address, but the upper 3-bit setting bits for the memory address.•Read/Write Code (1bit)The 8th bit of the device address word is the R/W (Read/Write) code. When the R/W code is “0” input, a write operation is enabled, and the R/W code is “1” input, a read operation is enabled for the MB85RC16. If the device code is not “1010”, the Read/Write operation is not performed and the standby state is chosen.MB85RC16■DATA STRUCTUREThe master inputs the device address word (8 bits) following the start condition, and then the slave outputs the Acknowledge “L” level on the ninth bit. After confirming the Acknowledge response, the sequential 8-bit memory lower address is input, to the byte write, page write and random read commands.As for the current address read command, inputting the memory lower address is not performed, and the address buffer lower 8-bit is used as the memory lower address.When inputting the memory lower address finishes, the slave outputs the Acknowledge “L” level on the ninth bit again.Afterwards, the input and the output data continue in 8-bit units, and then the Acknowledge “L” level is output for every 8-bit data.MB85RC16■FRAM ACKNOWLEDGE -- POLLING NOT REQUIREDThe MB85RC16 performs the high speed write operations, so any waiting time for an ACK* by the acknowl-edge polling does not occur.*: In E2PROM, the Acknowledge Polling is performed as a progress check whether rewriting is executed or not.It is normal to judge by the 9th bit of Acknowledge whether rewriting is performed or not after inputting the start condition and then the device address word (8 bits) during rewriting.■WRITE PROTECT (WP)The entire memory array can be write protected by setting the WP pin to the “H” level. When the WP pin is set to the “L” level, the entire memory array will be rewritten. Reading is allowed regardless of the WP pin's “H” level or “L” level.Do not change the WP signal level during the communication period from the start condition to the stop condition.Note : The WP pin is pulled down internally to VSS pin, therefore if the WP pin is open, the pin status is detected as the “L” level (write enabled).MB85RC16■COMMAND•Byte WriteIf the device address word (R/W “0” input) is sent after the start condition, an ACK responds from the slave.After this ACK, write memory addresses and write data are sent in the same way, and the write ends by•Page WriteIf data is continuously sent after the following address when the same command (expect stop condition) as Byte Write was sent, a page write is performed. The memory address rolls over to first memory address (000H)at the end of the address. Therefore, if more than 2 Kbytes are sent, the data is overwritten in orderMB85RC16•Current Address ReadIf the last write or read operation finishes correctly up to the end of stop condition, the memory address that was accessed last remains in the memory address buffer (the length is 11 bits).When sending this command without turning the power off, it is possible to read from the memory address n+1 which adds 1 to the total 11-bit memory address n, which consists of the memory upper address 3-bit from the device address word input and the lower 8-bit of the memory address buffer. If the memory address n is the last address, it is possible to read with rolling over to the head of the memory address (000H). The current address (address that the memory address buffer indicates) is undefined immediately after turning•Random ReadThe one byte of data from the memory address as saved in the memory address buffer can be read out synchronously to SCL by specifying the address in the same way as for a write, and then issuing another start condition and sending the Device Address Word (R/W “1” input).Setting values for the first and the second memory upper address codes should be the same.The final NACK (SDA is the “H” level) is issued by the receiver that receives the data. In this case, this bit is分销商库存信息: FUJITSUMB85RC16PNF-G-JNE1。
CNP10高效率LED驱动控制芯片说明书
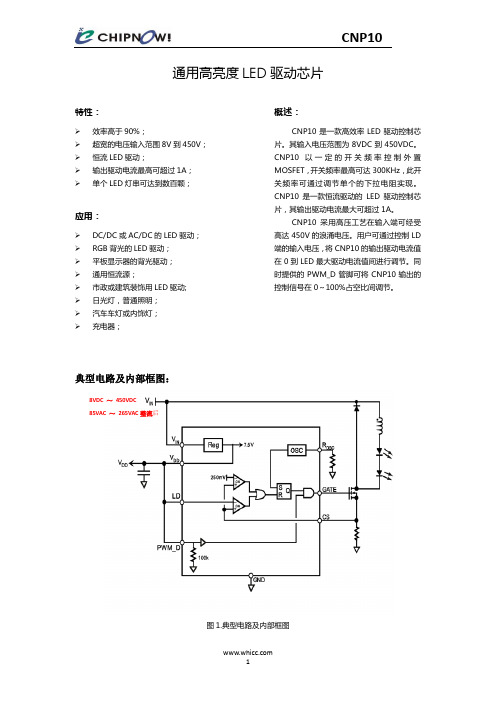
通用高亮度LED 驱动芯片特性:效率高于90%;超宽的电压输入范围8V 到450V ; 恒流LED 驱动;输出驱动电流最高可超过1A ;单个LED 灯串可达到数百颗;应用:DC/DC 或AC/DC 的LED 驱动; RGB 背光的LED 驱动; 平板显示器的背光驱动; 通用恒流源;市政或建筑装饰用LED 驱动; 日光灯,普通照明; 汽车车灯或内饰灯; 充电器;概述:CNP10是一款高效率LED 驱动控制芯片。
其输入电压范围为8VDC 到450VDC 。
CNP10以一定的开关频率控制外置MOSFET ,开关频率最高可达300KHz ,此开关频率可通过调节单个的下拉电阻实现。
CNP10是一款恒流驱动的LED 驱动控制芯片,其输出驱动电流最大可超过1A 。
CNP10采用高压工艺在输入端可经受高达450V 的浪涌电压。
用户可通过控制LD 端的输入电压,将CNP10的输出驱动电流值在0到LED 最大驱动电流值间进行调节。
同时提供的PWM_D 管脚可将CNP10输出的控制信号在0~100%占空比间调节。
典型电路及内部框图:图1.典型电路及内部框图8VDC ~ 450VDC85VAC ~ 265VAC 整流后应用说明:图2.典型应用电路● 电阻R1的选择.R1的连接方式分为两种: 1. R1直接接地,决定CNP10工作在固定频率(Fosc )模式.2.R1跨接于Rosc 与Gate 间,决定CNP10工作在固定关断时间(Toff )模式. 本应用中CNP10工作在固定频率(Fosc )模式,在大电压输入的情况下(220V 交流整流后输入),CNP10的工作频率越大要求电感L0的值越小,但是在电容上的动态功耗将会增加。
一般选取工作频率范围从20KHz-150KHz 。
在交流220V 整流后输入时,一般取Fosc 为50KHZ,电阻R1的大小为470K Ω.R1大小与CNP10的工作频率的相关关系可有以下计算公式得到:1R (k ) + 22T (us) =25osc Ω1F =T osc oscMOS 管关断时间t OFF 的计算公式为:t 1OOFF OSC IN VT V ⎛⎫=-⨯ ⎪⎝⎭● 电感L0的选择.电感的取值大小决定于负载的纹波电流的峰-峰值,一般取纹波电流为负载电流O I 最大值的30%,电感L0的大小可计算为:0t L =0.3O OFFOV I ∙∙在选择电感大小的同时,电感电流的选择也值得关注,如果选得过小则电感在工作时会发热,一般选取电感额定电流应为:()115%O I +。
UPD168116A资料

The information in this document is subject to change without notice. Before using this document, please confirm that this is the latest version.Not all products and/or types are available in every country. Please check with an NEC Electronics sales representative for availability and additional information.DATA SHEETDocument No. S16967EJ1V0DS00 (1st edition)Date Published December 2003 NS CP(K) Printed in Japan2003DESCRIPTIONThe µ PD168116A is a 7-channel H-bridge driver with a micro step function supporting pulse input that consists of a CMOS control circuit and a MOS output stage. It can reduce the current consumption and the voltage loss at the output stage compared with a conventional driver using bipolar transistors, thanks to employment of a MOS process. The µ PD168116A can drive a stepping motor by inputting pulses, so that the number of signal lines necessary for controlling the motor can be decreased.The package is a 56-pin WQFN that helps reduce the mounting area and height.The µ PD168116A can be used to drive two stepping motors, or two DC motors and one coil.FEATURES• Seven H-bridge circuits employing power MOSFET • Low-voltage driving V DD = 2.7 to 3.6 V V M = 2.7 to 5.5 V• Output on-state resistance: 1.0 Ω TYP., 1.5 Ω MAX. (sum of top and bottom stage, ch1 to ch4, and ch7)1.5 Ω TYP.,2.0 Ω MAX. (sum of top and bottom stage, ch5 and ch6)• PWM output (ch1 to ch6) , linear output (ch7) • Output current <ch1 to ch6>DC current: 0.4 A/ch (when each channel is used independently) Peak current: 0.7 A/ch (when each channel is used independently) <ch7>DC current: 0.5 A/ch (when used independently) Peak current: 0.7 A/ch (when used independently) • Input logic frequency: 100 kHz supported • Undervoltage lockout circuitShuts down the internal circuit at V DD = 1.7 V TYP. • Overheat protection circuitOperates at 150°C or more and shuts down internal circuitry. • 56-pin WQFN (□8 mm, 0.5 mm pitch)ORDERING INFORMATIONPart NumberPackageµ PD168116AK9-9B4-A56-pin plastic WQFN (8 x 8)Data Sheet S16967EJ1V0DS21. PIN CONFIGURATIONPackage: 56-pin plastic WQFN (8 x 8)C L K 2/I N 3BC W 2/I N 4AO U T 6BO U T 6AP G N D 56O U T 5AV M 56O U T 5BM O D E 4/I N 4BM O D E 3M O D E 2M O D E 1I N 6BI N 6AFIL 1FB 4FB 3FB 2FB 1OUT 1B V M12OUT 1A PGND 12OUT 2B V M12OUT 2A IN 5A IN 5BIN 7A FIL 7R 7FB 7OUT 7AV M7OUT 7BV DD LGND COSC OE 1CLK 1CW 1OE 2/IN 3AI N 7B S E L 7M O B 2M O B 1O U T 3BV M 34O U T 3AP G N D 34O U T 4BV M 34O U T 4AR E S E T BF I L 3F I L 22. PIN FUNCTIONS(1/2) Pin No. Pin Name Function1 CLK2/IN3B H-bridge 3, H-bridge 4 CLK input pin/H-bridge 3 input pin B2 CW2/IN4A H-bridge 3, H-bridge 4 driving direction input pin/H-bridge 4 input pin A3 OUT6B H-bridge 6 output pin B4 OUT6A H-bridge 6 output pin A5 PGND56H-bridge 5, H-bridge6 GND pin6 OUT5A H-bridge 5 output pin A7 V M56H-bridge 5, H-bridge 6 power supply pin8 OUT5B H-bridge 5 output pin B9 MODE4/IN4B Mode selection pin 4/H-bridge 4 input pin B10 MODE3Mode selection pin 311 MODE2Mode selection pin 212 MODE1Mode selection pin 113 IN6B H-bridge 6 input pin B14 IN6A H-bridge 6 input pin A15 IN5B H-bridge 5 input pin B16 IN5A H-bridge 5 input pin A17 OUT2A H-bridge 2 output pin A18 V M12H-bridge 1, H-bridge 2 power supply pin19 OUT2B H-bridge 2 output pin B20 PGND12H-bridge 1, H-bridge 2 GND pin21 OUT1A H-bridge 1 output pin A22 V M12H-bridge 1, H-bridge 2 power supply pin23 OUT1B H-bridge 1 output pin B24 FB1Current detection resistor connection pin 125 FB2Current detection resistor connection pin 226 FB3Current detection resistor connection pin 327 FB4Current detection resistor connection pin 428 FIL1Filter capacitor connection pin 129 FIL2Filter capacitor connection pin 230 FIL3ch3 reference voltage output pin (Leave this pin open.)31 RESETB Reset pin (low active)32 OUT4A H-bridge 4 output pin A33 V M34H-bridge 3, H-bridge 4 power supply pin34 OUT4B H-bridge 4 output pin B35 PGND34H-bridge 3, H-bridge 4 GND pin36 OUT3A H-bridge 3 output pin A37 V M34H-bridge 3, H-bridge 4 power supply pin38 OUT3B H-bridge 3 output pin BData Sheet S16967EJ1V0DS3Data Sheet S16967EJ1V0DS4(2/2)Pin No.Pin NameFunction39 MOB 1 MOB signal output pin 1 (open drain output) 40 MOB 2 MOB signal output pin 2 (open drain output) 41 SEL 7 ch7 excitation mode selection pin 42 IN 7B H-bridge 7 input pin B 43 IN 7A H-bridge 7 input pin A44 FIL 7 Amplifier operation stabilizing filter connection pin 45 R 7 Amplifier operation stabilizing resistor connection pin 46 FB 7 Current detection resistor connection pin 7 47 OUT 7A H-bridge 7 output pin A 48 V M7 H-bridge 7 power supply pin 49 OUT 7B H-bridge 7 output pin B 50 V DD Logic block power supply pin 51 LGND Logic block GND pin52COSCChopping frequency setting capacitor connection pin 53 OE 1 H-bridge 1, H-bridge 2 output enable pin 54 CLK 1 H-bridge 1, H-bridge 2 CLK input pin55 CW 1 H-bridge 1, H-bridge 2 driving direction input pin56 OE 2/IN 3AH-bridge 3, H-bridge 4 output enable pin/H-bridge 3 input pin AData Sheet S16967EJ1V0DS53. BLOCK DIAGRAMOUT 3A V M34OUT 3B PGND 34OUT 4A OUT 4BV DD OUT 2BV M12OUT 2A OUT 1B SEL 7OUT 1A PGND 12OE 2/OUT 6B V M7OUT 6A OUT 7BOUT 7A OUT 5BV M56OUT 5A PGND 56CLK 1CW 1COSCV M12V M34CLK 2/CW 2/MODE 4/RESETB FB 1FIL 1FIL 2FB 2MODE 3OE 1MOB 1IN 7B IN 7A IN 6A IN 6B IN 5A IN 5B FIL 3FB 3FB 4FB 7FIL 7R 7Data Sheet S16967EJ1V0DS64. STANDARD CONNECTION EXAMPLECautions 1. Be sure to connect all of the pins which have more than one.2. The constants shown in the above diagram are provided as examples only. Perform design based on thorough evaluation with the actual machine, and change the underlined constants as necessary.3. A pull-down resistor (50 to 200 k Ω) is connected to the MODE 1, MODE 2, MODE 3, SEL 7, OE 1, CLK 1, CW 1, OE 2/IN 3A , CLK 2/IN 3B , CW 2/IN 4A , MODE 4/IN 4B , IN 5A , IN 5B , IN 6A , IN 6B , IN 7A , and IN 7B pins. Fix these input pins to GND when they are not used.5. SYSTEM APPLICATION DIAGRAMCaution The constants shown in the above diagram are provided as examples only. Perform design based on thorough evaluation with the actual machine.Data Sheet S16967EJ1V0DS7Data Sheet S16967EJ1V0DS86. FUNCTION OPERATION TABLE6.1 Power Save FunctionThis IC can be placed in the power-save mode by making MODE 1, MODE 2, MODE 3, and MODE 4 high level.This function allows holding of the excitation position when the stepping motor mode is selected and the operation tobe started from where the excitation position is held when the power-save mode is cleared. In the power-save mode,the current consumption is reduced to 20 µA TYP. because the internal circuits other than UVLO are stopped. In the power-save mode, only input of the RESETB pin is acknowledged, and the other input signals are ignored. The operation modes of ch1 to ch4 can be set by a combination of MODE 1 to MODE 4. For the combination of the MODE pins, refer to Table 6−1. MODE Pin Truth Table .Table 6−1. Mode Pin Truth TableMODE 1 MODE 2 MODE 3 MODE 4 Operation Mode(/IN 4B ) ch1, ch2ch3, ch4L L L IN 4B input2-phase excitationGeneral-purpose driving L L L LLH1-2 phase excitationGeneral-purpose driving L L HL HL Micro step General-purpose driving L H LL HHL 2-phase excitation 2-phase excitation L H H H 1-2 phase excitation 1-2 phase excitation HLLL2-phase excitation (current limiting)2-phase excitation (current limiting)H L L H1-2 phase excitation (current limiting)1-2 phase excitation(current limiting)H L H L 2-phase excitation Micro step HLHH1-2 phase excitationMicro stepHHL L Micro step 2-phase excitation H H L H Micro step 1-2 phase excitation HHHLMicro stepMicro stepH HHHPower save modeRemark H: High level, L: Low levelData Sheet S16967EJ1V0DS96.2 ch1, ch2 (Dedicated to Stepping Motor)Remark x: High level or low level, Hi-Z: High impedance6.3 ch3, ch4 (Selecting Stepping Motor, DC Motor and Coil Driving)<General-purpose drive mode>RESETB IN 3A /IN 4A IN 3B /IN 4B OUT 3A /OUT 4A OUT 3B /OUT 4B Operation ModeL L Z Z Stop L L H NoteReverseH H LH NoteL ForwardH H H H HBrake LxxReset mode (output Hi-Z)Note When the µ PD168116A is used for constant-current driving (when a sense resistor is connected to the FBpin) , PWM chopping driving is performed.Remark Z: Output high impedanceData Sheet S16967EJ1V0DS106.4 ch5, ch6RESETB IN 5A /IN 6A IN 5B /IN 6B OUT 5A /OUT 6A OUT 5B /OUT 6B Operation ModeHL L Z Z Stop H LLReverse H HL L Forward HH Brake LxxReset mode (output Hi-Z)MGND ForwardMGNDReverseGND StopGNDBrake6.5 ch7RESETB SEL7 IN7A IN7B OUT7A OUT7B H-bridge Output StateQ1Q2Q3Q4HHL L Z Z OFF OFF OFF OFFH H LHLHOFFON ONOFF(linear) (linear)H H H L L ONOFFOFFON(linear) (linear)H H H L ON ONOFFOFFH L Weak excitation operation when SEL7 = H (Function is equivalent.)L x x x Z Z OFF OFF OFF OFF6.6 SEL7 PinThe current that flows into ch7 can be changed by setting the SEL7 pin.SEL7 OperationMode L Weak excitation mode (Current 2/3 of the normal setting flows.)H Normal operation mode7. COMMAND INPUT TIMING CHARTFigure 7−1. In The Micro Step ModeRESETBCLKCWOEPulse out(internal)ChoppingpulseMOBTable 7−1. Relationship between Revolution Angle, Phase Current, and Vector Amount (64 micro steps)Step Revolution Phase A - Phase Current Phase B - Phase Current VectorAngle Amount MIN. TYP. MAX. MIN. TYP. MAX. TYP.θ 0 0 − 100 −−0 3.8 100 θ 1 5.625 94.5 100 104.5 2.5 9.8 17.0 100.48 θ 2 11.250 93.2 98.1 103.0 12.4 19.5 26.5 100 θ 3 16.875 90.7 95.7 100.7 22.1 29.0 36.1 100.02 θ 4 22.500 87.4 92.4 97.4 31.3 38.3 45.3 100.02 θ 5 28.125 83.2 88.2 93.4 40.1 47.1 54.1 99.99 θ 6 33.750 78.1 83.1 88.1 48.6 55.6 62.6 99.98 θ 7 39.375 72.3 77.3 82.3 58.4 63.4 68.4 99.97 θ 8 45 65.7 70.7 75.7 65.7 70.7 75.7 99.98 θ 9 50.625 58.4 63.4 68.4 72.3 77.3 82.3 99.97 θ 10 56.250 48.6 55.6 62.6 78.1 83.1 88.1 99.98 θ 11 61.875 40.1 47.1 54.1 83.2 88.2 93.2 99.99 θ 12 67.500 31.3 38.3 45.3 87.4 92.4 97.4 100.02 θ 13 73.125 22.1 29.0 36.1 90.7 95.7 100.7 100.02 θ 14 78.750 12.4 19.5 26.5 93.2 98.1 103.0 100 θ 15 84.375 2.5 9.8 17.0 94.5 100 104.5 100.48 θ 16 90 −0 3.8 −100 −100Caution θ 0 shows the excitation start position after release of reset. Each value is an ideal value and is not a guarantee value.8. FUNCTIONAL DEPLOYMENT8.1 Reset FunctionAn initialization operation is performed and all the internal data is cleared when RESETB = L. The output remains in the Hi-Z state.When RESETB = H, signals can be input. Be sure to perform a reset operation after turning on power supply.When RESETB = L, the internal circuitry is stopped whenever possible, so that the self current consumption can be reduced. When the external input signal is stopped, the current consumption can be lowered to 1 µA MAX.Immediately after release of reset, excitation is started from the position where the current of ch1 is 100% and the current of ch2 is 0%, in the micro step drive mode and 1-2 phase excitation drive mode. In the 2-phase excitation drive mode, excitation is started from the position where the currents of ch1 and ch2 are 100%.8.2 2-phase Excitation Drive Mode and 1-2 Phase Excitation Drive ModeIn the 2-phase excitation drive mode, current of ±100% is allowed to flow into ch1 and ch2 simultaneously. In the 1-2 phase excitation drive mode, the motor can be driven at a higher torque by allowing a current to flow so that the synthesized torque of ch1 and ch2 is the same as the torque at phase 1 position. The 2-phase excitation, 1-2 phase excitation, and micro step driving modes are selected by the MODE1 to MODE4 pins.Note that 100% (= saturation drive mode) and a mode in which the current set by the sense resistor is used can be selected by the MODE pin. Current control is performed by chopping drive.8.3 Micro Step Drive Mode of Stepping MotorThe current flowing into the H-bridge is constant by using a vector value so that one period can be stopped in 1/64 steps. This function is provided to realize high-accuracy positioning control of a stepping motor.To realize this micro step driving, the following functions are internally realized by the driver.• Detection of current flowing into each channel by sense resistor as voltage value• Synthesizing half the dummy sine waveform generated by the internal D/A with PWM oscillation waveform for chopping operation• Driver stage performing PWM drive based on result of comparing detected voltage and synthesizedwaveformBecause the internal dummy sine wave consists of 64 steps per period, it can be used to drive a stepping motor using 64 divisions. The micro step drive mode, 2-phase excitation drive mode, and 1-2 phase excitation drive mode can be selected by using external pins.Figure 8−1. Concept of Micro Step Drive Operation8.4 Output Enable (OE) PinThe OE1 (OE2) pin can be used to forcibly stop pulse output of ch1 and ch2 (or ch3 and ch4) .When OE1 (OE2) = L, the output is forcibly made to go into Hi-Z. Because the internal information is held, however, the motor position information is recorded unless reset is performed.To drive a motor, make sure that OE1 (OE2) = H.8.5 MOB OutputIn the micro step drive mode, L is output from the MOB1 (MOB2) pin when the current of ch1 (ch3) or ch2 (ch4) is ±100%.In the 2-phase excitation or 1-2 phase excitation drive mode, L is output when the current of ch1 and ch2 is +100%. By monitoring the MOB output, the excitation position of the stepping motor can be checked. When OE1 (OE2) = L, MOB1 (MOB2) = Hi-Z.8.6 Current Detection Resistor Connection (FB) Pin(1) ch1 to ch4The current detection resistor is connected when current driving is necessary. It is used for micro step driving and solenoid driving.The current that flows into the output is {500 mV (reference voltage) /FB pin resistance x 1000}.Example) Where FB = 4.7 kΩOutput current = 500 (mV) /4.7 (kΩ) x 1000≅ 106 (mA)This means constant current driving of about 106 mA.When current driving is not performed, connect the FB pin to GND.(2) ch7Connect the current detection circuit between the source of the driver low side and GND. Because the circuit is configured to detect current directly, connect a detection resistor of low resistance (1 Ω maximum) . The current that flows into the output is {200 mV (reference voltage) /FB 7 pin resistance} (when SEL 7 = H) .Example) Where FB 7 = 0.5 ΩOutput current = 200 (mV) /0.5 (Ω)= 400 (mA)This means constant current driving of 400 mA.Because only ch7 employs the linear drive mode and directly detects the output current, the current accuracy is determined only by the external resistor and the offset of the current control amplifier.8.7 Undervoltage Lockout (UVLO) CircuitThis function is to forcibly stop the operation of the IC to prevent malfunctioning if V DD drops. When UVLO operates, the IC is in the reset status.If V DD drops abruptly in the order of several µs, this function may not operate.8.8 Overheat Protection (TSD) CircuitThis function is to forcibly stop the operation of the IC to protect it from destruction due to overheating if the chip temperature of the IC rises.The overheat protection circuit operates when the chip temperature rises to 150°C or more. When overheat is detected, all the circuits are stopped. When RESETB = L or when UVLO is detected, the overheat protection circuit does not operate.8.9 Power Up SequenceThis IC has a circuit that prevents current from flowing into the V M pin when V DD = 0 V. Therefore, the current that flows into the V M pin is cut off when V DD = 0 V.Because the V DD pin voltage and V M pin voltage are monitored, a current of 3 µA MAX. flows into the V M pin when V DD is applied.9. OPERATION DESCRIPTION9.1 Output Current SettingThe peak value of the output current (100% of the current of ch1 (ch3) or ch2 (ch4) ) is determined by resistor R FB connected to FB 1 (FB 3) or FB 2 (FB 4) . This IC has reference power supply V REF (500 mV TYP.) for current comparison, and performs driving with the current obtained from R FB and V REF as the peak output current. Peak output current: I MAX (A) ≅ V REF (V) ÷ R FB (Ω) x 10009.2 Pulse OutputThe motor is driven by inputting a pulse to the CLK 1 (CLK 2) pin. The operation advances by one pulse at the rising edge of the CLK 1 (CLK 2) signal.9.3 Motor Revolution Direction SettingCLK 1 (CLK 2) is used to specify the motor revolution direction.In the CW mode, the current of ch2 (ch4) is output, 90° degrees in phase behind the current of ch1 (ch3) . In the CCW mode, the current of ch2 (ch4) is output, 90° degrees in phase ahead of the current of ch1 (ch3) .9.4 Selecting 2-phase Excitation/Micro Step Drive ModeThe 2-phase excitation, 1-2 phase excitation, or micro step drive mode can be selected by using the MODE 1 to MODE 4 pins.Refer to Table 6−1. Mode Pin Truth Table for details.Immediately after release of reset, the IC is initialized. In the 1-2 phase excitation and micro step drive mode, excitation is started from the position where the output current of ch1 (ch3) is 100% and output current of ch2 (ch4) is 0%. In the 2-phase excitation drive mode, excitation is started from the position where the currents of both ch1 (ch3) and ch2 (ch4) are +100%.When the mode is changed from the micro step driving to the 2-phase excitation (or 1-2 phase excitation) , the position of micro step is held until CLK is input. Pulse output is started by the first CLK input, the position is skipped to the 2-phase position of the next quadrant (or to the closest 1-2 phase position at the rotation direction destination) , and driving is started.Figure 9−1. Concept of Change Operation, Micro Step Driving ↔ 2-phase Excitation (1-2 Phase Excitation) .Microstep stop 2-phase excitation stop position10. NOTE ON CORRECT USE10.1 Transmitting DataData input when RESETB = L is ignored.10.2 Pin Processing of Unused CircuitThe input/output pins of an unused circuit must be processed as specified below.A V M power supply pin is provided for each output circuit. The current consumption of the internal circuit can be reduced by dropping the V M power of the unused circuit to GND. However, if there are multiple power supply pins, be sure to connect all of them to the same potential.<ch1, ch2>Lower OE1, CLK1, and CW1.Open FIL1, FIL2, OUT1A, OUT1B, OUT2A, and OUT2B.Connect FB1 and FB2 to GND.<ch3, ch4>Set the general-purpose drive mode.Lower OE2/IN3A, CLK2/IN3B, CW2/IN4A, and MODE4/IN4B.Open FIL3, OUT3A, OUT3B, OUT4A, and OUT4B.Connect FB3 and FB4 to GND.<ch5, ch6>Lower IN5A (IN6A) and IN5B (IN6B) .Open OUT5A (OUT6A) and OUT5B (OUT6B) .<ch7>Lower SEL7, IN7A, and IN7B.Open OUT7A and OUT7B.Connect FIL7, FB7, and R7 to GND.11. STEPPING MOTOR DRIVING WAVEFORMFigure 11−1. 2-phase Excitation Output ModeFigure 11−2. 1-2 Phase Excitation Output Mode−−−−Remarks 1. Solid line: Output duty 100% drive, Dotted line: Current control drive (The current is in accordance withthe current setting.)2. The horizontal axis of the above charts indicates the number of steps. The above charts show an example in the CW (forward) mode.The current flowing into phases A and B is positive in the direction from OUT pin A to OUT pin B, and negative in the direction from OUT pin B to OUT pin A.Figure 11−3. Micro Step Drive Mode−99.599.5−95.795.710098.192.4−92.4−98.1−100−88.288.2−83.183.1−77.377.3−70.770.7−63.463.4−55.655.6−47.147.1−38.338.3−29.029.0−19.519.5−9.89.80−99.599.5−95.795.710098.192.4−92.4−98.1−100−88.288.2−83.183.1−77.377.3−70.770.7−63.463.4−55.655.6−47.147.1−38.338.3−29.029.0−19.519.5−9.89.80ch2 currentch1 currentRESET position510152025303540455055606505101520253035404550556065Remark The horizontal axis of the above charts indicates the number of steps. The above charts show an examplein the CW (forward) mode.The current flowing into phases A and B is positive in the direction from OUT pin A to OUT pin B, and negative in the direction from OUT pin B to OUT pin A.Data Sheet S16967EJ1V0DS2112. ELECTRICAL SPECIFICATIONSAbsolute Maximum Ratings (T A = 25°C, glass epoxy board of 100 mm x 100 mm x 1 mm with copper foil areaof 15%)Parameter SymbolConditionRating Unit Power supply voltage V DD Control block −0.5 to +6.0 VV M Motor block −0.5 to +6.0 V Input voltage V IN−0.5 to V DD +0.5V Output pin voltageV OUT Motor block 6.2VDC output current (ch1 to 6ch) I D(DC) DC (during output independent operation) ±0.4 A/ch DC output current (ch7) I D(DC) DC (during output independent operation) ±0.5 A/ch Instantaneous output current I D(pulse) PW < 10 ms, Duty Cycle ≤ 20% ±0.7 A/ch(during output independent operation)Power consumption P T 1.0 W Peak junction temperature T ch(MAX) 150 °C Storage temperatureT stg−55 to +150°CRemark The overheat protection circuit operates at T ch > 150°C. When overheat is detected, all the circuits arestopped. The overheat protection circuit does not operate at reset or on detection of ULVO.Caution Product quality may suffer if the absolute maximum rating is exceeded even momentarily for anyparameter. That is, the absolute maximum ratings are rated values at which the product is on the verge of suffering physical damage, and therefore the product must be used under conditions that ensure that the absolute maximum ratings are not exceeded.Recommended Operating Conditions (T A = 25°C, glass epoxy board of 100 mm x 100 mm x 1 mm with copperfoil area of 15%)Parameter SymbolConditionMIN. TYP. MAX. Unit Power supply voltage V DD Control block 2.73.6 VV M Motor block 2.7 5.5 V Input voltageV IN 0V DD VDC output current (ch1 to 6ch) I D(DC) DC (during output independent operation) −0.3 +0.3 A/ch DC output current (ch7) I D(DC) DC (during output independent operation) −0.4 +0.4 A/ch Instantaneous output current I D(pulse) PW < 10 ms, Duty Cycle ≤ 20% −0.6 +0.6 A/ch(during output independent operation) Capacitor capacitanceCOSC330 pF MOB pin output sink current I MOB Open-drain output5mALogic input frequency f IN100 k HzOperating temperature rangeT A−10 75 °CData Sheet S16967EJ1V0DS22Electrical Characteristics (Unless otherwise specified, T A = 25°C, V DD = 3.0 V, V M = 3.0 V)Parameter Symbol ConditionMIN. TYP. MAX. Unit V DD pin current in standby mode I DD(STB) RESETB pin: Low level 1.0 µAV DD pin current in during operation I DD(ACT) RESETB pin: High level5.0mAHigh-level input currentI IH V IN = V DD 60 µA Low-level input current I ILV IN = 0 V−1.0 µA Input pulldown resistance R IND50200 k Ω High-level input voltage V IH 2.7 V ≤ V DD ≤ 3.6 V 0.7 x V DDV Low-level input voltage V IL 2.7 V ≤ V DD ≤ 3.6 V 0.3 x V DD VCOSC oscillation frequency f OSC COSC = 330 pF100kHzH-bridge on-state resistanceR onI M = 0.3 A, sum of upper and lower stages (ch1 to ch4, and ch7)1.0 1.5 ΩR on56 I M = 0.3 A, sum of upper and lower stages (ch5 and ch6)1.52.0 ΩOutput leakage current Note1I M(off) Per V M pin, All control pin: low level 1.0 µALow-voltage detection voltage V DDS1.72.5 V Internal reference voltage Note2V REF ch1 to ch4 450 500 550 mVV REF7 ch7180200220 mVCurrent detection ratioNote2I M = 0.1 A, with sense resistor of 2 k Ω, ch1 to ch4950 1050 1150Output turn-on time t on R L = 20 Ω 0.02 0.35 1.0 µsOutput turn-off timet off0.02 0.35 1.0 µsNotes 1. This IC has a circuit that prevents current from flowing into the V M pin when V DD = 0 V.2. The motor current accuracy varies depending on the motor actually used. With this IC, the total of the reference voltage EVRMAX error and the current sense circuit error is within ±10%.Data Sheet S16967EJ1V0DS2313. PACKAGE DRAWINGITEM DIMENSIONS D E f HD HE t7.757.750.640.23±0.050.20±0.030.14−0.200.500.40±0.100.050.080.100.6250.6250.170.14−0.160.208.008.000.20P56K9-50-9B40.03+0.02–0.025(UNIT:mm)A2b b1c c1c2e Lp x y y1ZD ZEA10.67+0.08–0.04A56-PIN PLASTIC WQFN (8x8)INTERCONNECTION, BUT FOR MANUFACTURING PROCESS OF THE PACKAGE, THEREFOR DO NOT INTEND TO SOLDER THESE 4 TERMINALS, SOLDERABLITY OF THE 4 TERMINALS ARE NOT GUARANTEED.Data Sheet S16967EJ1V0DS2414. RECOMMENDED SOLDERING CONDITIONSThe µ PD168116A should be soldered and mounted under the following recommended conditions.For soldering methods and conditions other than those recommended below, contact an NEC Electronics sales representative.For technical information, see the following website.Semiconductor Device Mount Manual (/pkg/en/mount/index.html)Type of Surface Mount Deviceµ PD168116AK9-9B4-A: 56-pin plastic WQFN (8 x 8)Process Conditions SymbolInfrared reflowPackage peak temperature: 260°C, Time: 60 seconds MAX. (at 220°C or higher) , Count: Three times or less, Exposure limit: 3 daysNote(after that, prebake at 125°C for10 hours) , Flux: Rosin flux with low chlorine (0.2 Wt% or below) recommended. <Precaution>Products other than in heat-resistant trays (such as those packaged in a magazine, taping, or non-thermal-resistant tray) cannot be baked in their package.IR60-103-3Note After opening the dry pack, store it a 25°C or less and 65% RH or less for the allowable storage period.Caution Do not use different soldering methods together (except for partial heating) .Data Sheet S16967EJ1V0DS25Reference DocumentsNEC Semiconductor Device Reliability/Quality Control System (C10983E) Quality Grades On NEC Semiconductor Devices (C11531E)The information in this document is current as of December, 2003. The information is subject to change without notice. For actual design-in, refer to the latest publications of NEC Electronics data sheets or data books, etc., for the most up-to-date specifications of NEC Electronics products. Not all products and/or types are available in every country. Please check with an NEC Electronics sales representative for availability and additional information.No part of this document may be copied or reproduced in any form or by any means without the prior written consent of NEC Electronics. NEC Electronics assumes no responsibility for any errors that may appear in this document.NEC Electronics does not assume any liability for infringement of patents, copyrights or other intellectual property rights of third parties by or arising from the use of NEC Electronics products listed in this document or any other liability arising from the use of such products. No license, express, implied or otherwise, is granted under any patents, copyrights or other intellectual property rights of NEC Electronics or others.Descriptions of circuits, software and other related information in this document are provided for illustrative purposes in semiconductor product operation and application examples. The incorporation of these circuits, software and information in the design of a customer's equipment shall be done under the full responsibility of the customer. NEC Electronics assumes no responsibility for any losses incurred by customers or third parties arising from the use of these circuits, software and information.While NEC Electronics endeavors to enhance the quality, reliability and safety of NEC Electronics products, customers agree and acknowledge that the possibility of defects thereof cannot be eliminated entirely. To minimize risks of damage to property or injury (including death) to persons arising from defects in NEC Electronics products, customers must incorporate sufficient safety measures in their design, such as redundancy, fire-containment and anti-failure features.NEC Electronics products are classified into the following three quality grades: "Standard", "Special" and "Specific".The "Specific" quality grade applies only to NEC Electronics products developed based on a customer-designated "quality assurance program" for a specific application. The recommended applications of an NEC Electronics product depend on its quality grade, as indicated below. Customers must check the quality grade of each NEC Electronics product before using it in a particular application."Standard":Computers, office equipment, communications equipment, test and measurement equipment, audioand visual equipment, home electronic appliances, machine tools, personal electronic equipment and industrial robots."Special":Transportation equipment (automobiles, trains, ships, etc.), traffic control systems, anti-disastersystems, anti-crime systems, safety equipment and medical equipment (not specifically designed for life support)."Specific":Aircraft, aerospace equipment, submersible repeaters, nuclear reactor control systems, lifesupport systems and medical equipment for life support, etc.The quality grade of NEC Electronics products is "Standard" unless otherwise expressly specified in NEC Electronics data sheets or data books, etc. If customers wish to use NEC Electronics products in applications not intended by NEC Electronics, they must contact an NEC Electronics sales representative in advance to determine NEC Electronics' willingness to support a given application.(Note)(1)"NEC Electronics" as used in this statement means NEC Electronics Corporation and also includes itsmajority-owned subsidiaries.(2)"NEC Electronics products" means any product developed or manufactured by or for NEC Electronics (asdefined above).••••••M8E 02. 11-1。
中兴通讯视讯产品手册 2021说明书

PRODUC T INTRODUC TION 中兴通讯视讯产品手册2021专业品质行业专家,品质体验S pecialty H.265 沉浸式 5G+4K安全稳定有效保障,方有作为S tability 电信级 十二重备份 三重加密智能易用从UI 到AIS mart智能运维 自助式 AI+融合互联深度融合,广泛互联S yncretic全场景终端 多网融合 高兼容性平台接入应用媒体服务器融合网关行政会议部门协作项目讨论远程招聘移动接入视频处理芯片ZX296719拥有全自研DCS1000中兴通讯提供全系列多形态视频通讯终端产品,包括会议室型群组终端系列、视频会议个人终端系列、一体式终端、幻真系列终端等,为多种视讯应用场景提供定制化的视频会议产品。
扫码获得更多资讯07XT802 / XT702 先锋型5G+4K超高清视频会议终端 5G移动视讯 · 4K超高清体验 · 大型会场首选全球首款5G+4K超高清视讯终端,能够同时支持两路高达4K30的视频流,给用户提供极致的超高清晰视频体验;具有4KXT602 新锐型4K超高清视频会议终端双路4K30超高清体验 · 性价比最优 · 中型会场首选XT602是4K超高清视频会议终端,采用先进的H.265编解码技术,实现双路4K30的超高性能,同时分体式的设计可4KXT501 灵动型4K超高清视频会议终端融合协作 · 一体化设计 · 中型会场首选XT501 4K一体化超高清视频会议终端,采用全球领先的H.265视频编解码技术,提供4K超高清视频体验,一体化设计极大简化部署操作,提升会议体验,降低协同成本。
ET301/ET312 精巧型智能超高清视频会议终端VT100 移动视讯软终端能力开放 · 随时随地沟通 · 移动办公首选轻松安装在个人电脑和移动手机上,提供便捷的视频会议功能,享受随时随地的面对面远程沟通及在线协作体验。
MCP41010数据手册中文版

概述
MCP41XXX 和 MCP42XXX 器件是具有 256 个抽头的数 字电位器,有 10 kΩ、 50 kΩ 和 100 kΩ 3 种电阻选择。 MCP41XXX 是单通道器件, 有 8 引脚 PDIP 和 SOIC 两 种封装形式。 MCP42XXX 是双通道器件,有 14 引脚 PDIP、 SOIC 或 TSSOP 三种封装形式。 MCP41XXX/ 42XXX 的抽头位置在工业级 SPI 接口控制下线性变化。 此器件的静态工作电流 < 1 µA。 软件关断功能可将 “A” 端与电阻阵列断开,同时将抽头连接到“B”端。此外, 双通道 MCP42XXX 还有一个 SHDN 引脚,可通过硬件 实现上述相同功能。在关断模式期间,能更改抽头控制 寄存器的内容,电位器在退出关断模式后将使用新值。 在上电时抽头复位到半量程 (80h) 。通过 RS (复位) 引脚执行硬件复位并将抽头返回半量程。 MCP42XXX SPI 接口包括 SI 和 SO 引脚,允许使用菊花链连接多个 器件。 MCP42XXX 上通道与通道的电阻匹配变化小于 1%。这些器件使用 2.7 - 5.5V 单电源供电,并可在扩展 级和工业级温度范围下工作。
ppm/°C 编码 80h
, RS 和 SHDN 引脚的工作方式请参见图 2-12 数字输入 / 输出 (CS、 SCK、 SI 和 SO)
VAB = VDD,抽头上无连接。 变阻器位置非线性度 R-INL 是指抽头在最大电阻和最小电阻范围内测量的实际位置偏离理想位置的程度。 R-DNL 测量连续抽头位置 间的步长相对理想值的变化。对于 10 kΩ 的电位器, VDD = 3V 时 IW = 50 µA, VDD = 5V 时 IW = 400 µA。测试电路请参见图 2-26。 在器件配置为分压器或电位器模式时,在 VW 上测量 INL 和 DNL。 VA = VDD 且 VB = 0V。 DNL 规范极限值 ±1 LSB (最大值)是在规 定的单调操作条件下的值。测试电路请参见图 2-25。 电阻端子 A、 B 和 W 相互间无极性限制。满量程误差和零刻度误差使用图 2-25 进行测量。 在 VW 引脚上测得,此时该引脚附近的另一个 VW 引脚上的电压满幅摆动。 供电电流与流经电位器的电流无关。
GN16中文资料

.045 ±.005 .386 – .393* (9.804 – 9.982) 28 27 26 25 24 23 22 21 20 19 18 17 1615 .033 (0.838) REF
.254 MIN
.150 – .165 .229 – .244 (5.817 – 6.198) .150 – .157** (3.810 – 3.988)
.229 – .244 (5.817 – 6.198) .254 MIN .150 – .165
.150 – .157** (3.810 – 3.988)
1 .0165 ± .0015 RECOMMENDED SOLDER PAD LAYOUT .015 ± .004 × 45° (0.38 ± 0.10) .0075 – .0098 (0.19 – 0.25) .016 – .050 (0.406 – 1.270) NOTE: 1. CONTROLLING DIMENSION: INCHES INCHES 2. DIMENSIONS ARE IN (MILLIMETERS) 3. DRAWING NOT TO SCALE *DIMENSION DOES NOT INCLUDE MOLD FLASH. MOLD FLASH SHALL NOT EXCEED 0.006" (0.152mm) PER SIDE **DIMENSION DOES NOT INCLUDE INTERLEAD FLASH. INTERLEAD FLASH SHALL NOT EXCEED 0.010" (0.254mm) PER SIDE 0° – 8° TYP .0532 – .0688 (1.35 – 1.75) .0250 BSC
SinOne SCT80S16B 10V CS 8 通道触控按键专用 IC 说明书

SCT80S16B SinOne10V CS 8通道触控按键专用IC 目录目录 (1)1 总体描述 (3)2 主要功能和优势 (3)2.1 功能 (3)2.2 优势 (3)3 管脚定义 (3)3.1 管脚配置 (3)3.2 管脚定义 (4)4 电气性能 (4)4.1 推荐工作条件 (4)4.2 直流电气特性 (4)5 封装信息 (5)6 应用设计指南 (6)6.1 未使用通道处理 (6)6.2 邻键距离 (6)6.3 通讯输出选择 (6)6.3.1 通讯输出选择OUTS (6)6.3.2 灵敏度设置和键值读取格式 (6)7 注意事项 (9)7.1 典型应用电路 (9)7.2 电路Check List (9)7.3 电源要求 (9)7.4 PCB布局 (9)7.5 PCB布线 (10)7.6 PCB参考图 (10)Page 1 of 11 V 1.17.7 触控面板材料选择 (10)8 规格更改记录 (11)1 总体描述SCT80S16B 是一颗有8个触控通道,带UART/IIC 通讯接口的触控专用IC ,用户可通过UART/IIC 通讯来设置灵敏度。
此IC 具有工业级规格,拥有4KV EFT 和6KV 接触ESD 能力,可顺利通过3V 动态和10V 静态CS 测试,是用户高性能触控按键方案的首选。
非常适合应用于大小家电、安防、工控等应用场合。
2 主要功能和优势2.1 功能● 工作电压:3.3V ~ 5.5V ● 工作温度:-40 ~ 85℃● 触控按键通道:8通道,最多支持两个按键同时被按下 ● 触控按键输出通讯协议:UART/IIC 输出 ● 灵敏度调节:UART/IIC 通讯调节● 上电2s 内可通过UART/IIC 通讯来设置触控通道灵敏度等级 ● 覆盖物厚度:0 ~ 10mm● 有效触摸反应时间:小于100ms ● 允许按键长按时间为10S ●封装:SOP162.2 优势● 发明专利,业界独创; ● 完美触控按键操作体验; ● 用户根据需要设置灵敏度;●超强抗干扰能力,4KV EFT 、6KV ESD 、10V CS 。
FPGA可编程逻辑器件芯片10M16SAU16917G中文规格书

×10
100
—
100
100
—
100
100
—
100
Mbps
continued...
Send Feedback
13.4
–13.4
SSTL-15 Class I
—
VREF – 0.1 VREF + 0.1
—
SSTL-15 Class II
—
VREF – 0.1 VREF + 0.1
—
SSTL-135 HSTL-18 Class I
—
VREF –
VREF +
—
0.09
0.09
—
VREF – 0.1 VREF + 0.1
ms
Send Feedback
Symbol tPLL_PSERR
Parameter Accuracy of PLL phase shift
Condition —
Min —
Intel® MAX® 10 FPGA Device Datasheet M10-DATASHEET | 2020.06.30
Typ —
Condition —
— FINPFD ≥ 100 MHz FINPFD < 100 MHz
— –6 speed grade –7 speed grade –8 speed grade Duty cycle set to 50%
—
After switchover, reconfiguring any non-post-scale counters or
0.18
—
VREF –
VREF +
—
VTT – 0.57 VTT + 0.57
16位数智能温度控制器 E5CN 产品说明书

Digital Temperature ControllersE5CNCompact and Intelligent TemperatureControllersVarious temperature inputs: thermocouple, plati-num resistance thermometer, non-contact temper -ature sensor, and analog inputs.Auto-tuning and self-tuning available. Auto-tuning is possible even while self-tuning is being executed.Heating or heating/cooling control is available.Event input allows multiple SP selection and run/stop function.Water-resistant construction (NEMA4X: equivalent to IP66).Conforms to UL, CSA, and IEC safety standards aswell as CE marking.48(W) x 48(H) x 78(D) mm2.The heating and cooling function is available for models with two alarm points.3.Specify the power supply specifications when ordering.The E5CN provides communications or event input functionality when mounted with one of the following Option Units.NameModelFunctionCommunications Unit E53-CNH03 (For relay and voltage output)RS-485 communication and heater burnout alarmCo u ca o s U E53-CN03 (For current output)RS-485 communicationEvent Input Unit E53-CNHB (For relay and voltage output)Event input and heater burnout alarme u U E53-CNB (For current output)Event inputNote:The heater burnout alarm is available by mounting the E53-CNH03 or E53-CNHB Option Unit on the E5CN.Model E54-CT1E54-CT3Hole diameter5.8 dia.12.0 dia.Model E53-COV10Note:The Terminal Cover comes with the E5CN and does not have to be purchased separately .Platinum Resistance Thermometer Input/Thermocouple InputApplicable standards by input type are as follows:K, J, T, E, N, R, S, B: JIS C1602-1995L: Fe-CuNi, DIN 43710-1985U: Cu-CuNi, DIN 43710-1985JPt100: JIS C1604-1989, JIS C1606-1989Pt100: JIS C1604-1997, IEC751Shaded ranges indicate default settings.RatingsSupply voltage100 to 240 V AC, 50/60 Hz24 V AC, 50/60 Hz/24 VDCOperating voltage range85% to 110% of rated supply voltagePower consumption7 V A 4 V A/3 WSensor input Thermocouple: K, J, T, E, L, U, N, R, S, BPlatinum resistance thermometer:Pt100, JPt100Non-contact temperature sensor:10 to 70_C, 60 to 120_C, 115 to 165_C, 160 to 260_CV oltage input: 0 to 50 mVControl outputControl output Relay output SPST-NO, 250 V AC, 3 A (resistive load), electrical life: 100,000 operationsV oltage output12 VDC (PNP), max. load current: 21 mA, with short-circuit protection circuitCurrent output 4 to 20 mA DC, load: 600 Ω max., resolution: approx. 2,600Alarm output SPST-NO, 250 V AC, 1 A (resistive load), electrical life: 100,000 operationsControl method2-PID or ON/OFF controlSetting method Digital setting using front panel keysIndication method7-segment digital display and single-lighting indicatorCharacter height: PV: 9.9 mm; SV: 6.4 mmOther functions According to Controller modelAmbient temperature–10 to 55_C (with no condensation or icing)Ambient humidity25% to 85%Storage temperature–25 to 65_C (with no condensation or icing)CharacteristicsIndication accuracy Thermocouple:(±0.5% of indicated value or ±1_C, whichever greater) ±1 digit max. (see note )Platinum resistance thermometer:(±0.5% of indicated value or ±1_C, whichever greater) ±1 digit max.Analog input: ±0.5% FS±1 digit max.CT input: ±5% FS±1 digit max.Hysteresis0.1 to 999.9 EU (in units of 0.1 EU)Proportional band (P)0.1 to 999.9 EU (in units of 0.1 EU)Integral time (I)0 to 3999 s (in units of 1 s)Derivative time (D)0 to 3999 s (in units of 1 s)Control period 1 to 99 s (in units of 1 s)Manual reset value0.0% to 100.0% (in units of 0.1%)Alarm setting range-1999 to 9999 (decimal point position depends on input type)Sampling period500 msInsulation resistance20 MΩ min. (at 500 VDC)Dielectric strength2000 V AC, 50 or 60 Hz for 1min (between dif ferent charging terminals)V ibration resistance10 to 55 Hz, 10 m/s2 for 2 hours each in X, Y and Z directionsShock resistance300 m/s2, 3 times each in 3 axes, 6 directions (relay: 100 m/s2)Weight Approx. 150 g Mounting bracket: Approx. 10 gProtective structure Front panel: NEMA4X for indoor use (equivalent to IP66), rear case: IP20, terminals: IP00Memory protection EEPROM (non-volatile memory) (number of writes: 100,000)EMC Emission Enclosure:EN55011 Group 1 class AEmission AC Mains:EN55011 Group 1 class AImmunity ESD:EN61000-4-2: 4 kV contact discharge (level 2)8 kV air discharge (level 3)Immunity RF-interference:ENV50140:10 V/m (amplitude modulated,80 MHz to 1 GHz) (level 3)10 V/m (pulse modulated, 900 MHz)Immunity Conducted Disturbance:ENV50141:10 V (0.15 to 80 MHz) (level 3)Immunity Burst:EN61000-4-4: 2 kV power-line (level 3)2 kV I/O signal-line (level 4) Approved standards UL3121-1, CSA22.2 No. 14, E.B.1402CConforms to EN50081-2, EN50082-2, EN61010-1 (IEC61010-1)Conforms to VDE0106/part 100 (Finger Protection), when the terminal cover is mounted.Note:The indication of K thermocouples in the -200 to 1300°C range, and T and N thermocouples at a temperature of -100°C or less, and U and L thermocouples at any temperature is ±2°C±1 digit maximum. The indication of B thermocouples at a temperature of 400°C or less is unrestricted.The indication of R and S thermocouples at a temperature of 200°C or less is ±3°C±1 digit maximum.Note:The baud rate, data bit length, stop bit length, or vertical parity can be individually set using the communications setting level.Dielectricstrength 1,000 V AC (1 min)V ibration resistance 50 Hz 98 m/s 2WeightE54-CT1: Approx. 11.5 g E54-CT3: Approx. 50 g Accessories (E54-CT3 only)Armature (2)Plug (2)Max. heater currentSingle-phase AC: 50 A (see note 1)Input current readout accuracy ±5%FS ±1 digit max.Heater burnout alarm setting range 0.0 to 50.0 A (0.1 A units) (see note 2)Min. detection ON time 190 ms (see note 3)Note:1.When heater burnout is detected on a 3-phase heater , use the K2CU-F jj A-j GS (with gate input terminal).2.When the set value is “00 A,” the heater burnout alarm will always be OFF . When the set value is “50.0 A,” the heater burnout alarm will always be ON.3.When the control output ON time is less than 190 ms, heater burnout detection and heater current measurement will not be carried out.Level keyOperation indicatorsTemperature unitMode key Down keyNo.1 displayNo.2 displayUp key•Recommended panel thickness is 1 to 5 mm.•Group mounting is not possible in the vertical direction.(Maintain the specified mounting space between Controllers when they are group mounted.)•To mount the E5CN so that it is waterproof, apply the waterproof packing to the E5CN.•When two or more E5CNs are mounted, make sure that the surrounding temperature does not exceed the allowable operating temperature specified in the specifications.(48 number of units -2.5)60 min.60 min.+1.00454545+0.6+0.60+0.60Panel CutoutsGroup mounting does not allow waterproofing.Mounted SeparatelyGroup MountedNote :The suffix “500” is added to the model number of each Controller provided with a E53-COV10 Terminal Cover.48 x 4844.8 x 44.8Terminal CoverE53-COV10Current Transformer (Sold Separately)E54-CT1E54-CT35.8 dia.Two, 3.5 dia.12 dia.Two, M3 (depth: 4)40 x 402.36 dia.The voltage output (control output) is not electrically insulated from the internal circuits. When using a grounding thermocou-ple, do not connect the control output terminals to the ground. If the control output terminals are connected to the ground, errors will occur in the measured temperature values as a result of leakage current.Standard insulation is applied to the power supply I/O sections. If reinforced insulation is required, connect the input and output terminals to a device without any exposed current-carrying parts or to a device with standard insulation suitable for the maximum operating voltage of the power supply I/O section.Control output 1Analog inputInput power supplyAlarm outputALM1/Heater burnoutALM2/Control output 2Two input power supplies are available: 100 to 240 VAC or 24 VDC.Voltage OutputRelay Output12 VDC 21 mACurrent outputEvent Input/Heater Burnout DetectionE53-CNHB Event Input/Heater Burnout Alarm UnitContact inputNon-contact inputHeater burnout detection inputEvent InputE53-CNB Event InputContact inputNon-contact inputDo not connect anything.Do not connect anything.Communications Specification/Heater Burnout SpecificationE53-CNH03 Communications/Heater Burnout Alarm UnitDo not connect anything.H o s t c o m p u t e rCommunications SpecificationE53-CN03 Communications UnitDo not connect anything.H o s t c o m p u t e rDo not connect anything.Do not connect anything.ALL DIMENSIONS SHOWN ARE IN MILLIMETERS.To convert millimeters into inches, multiply by 0.03937. T o convert grams into ounces, multiply by 0.03527.。
CMS1617 用户手册 LED 驱动控制专用电路 Rev. 1.20说明书

CMS1617用户手册LED驱动控制专用电路Rev. 1.20请注意以下有关CMS知识产权政策*中微半导体(深圳)股份有限公司(以下简称本公司)已申请了专利,享有绝对的合法权益。
与本公司MCU或其他产品有关的专利权并未被同意授权使用,任何经由不当手段侵害本公司专利权的公司、组织或个人,本公司将采取一切可能的法律行动,遏止侵权者不当的侵权行为,并追讨本公司因侵权行为所受的损失、或侵权者所得的不法利益。
*中微半导体(深圳)股份有限公司的名称和标识都是本公司的注册商标。
*本公司保留对规格书中产品在可靠性、功能和设计方面的改进作进一步说明的权利。
然而本公司对于规格内容的使用不负责任。
文中提到的应用其目的仅仅是用来做说明,本公司不保证和不表示这些应用没有更深入的修改就能适用,也不推荐它的产品使用在会由于故障或其它原因可能会对人身造成危害的地方。
本公司的产品不授权适用于救生、维生器件或系统中作为关键器件。
本公司拥有不事先通知而修改产品的权利,对于最新的信息,请参考官方网站目录1.产品概述 (3)1.1功能特性 (3)1.2特性说明 (3)1.3管脚分布 (4)2.指令说明 (5)3.显示寄存器地址 (7)4.显示 (8)4.1驱动共阴数码管 (8)5.键扫描和键扫数据寄存器 (9)6.按键 (10)6.1按键扫描 (10)6.2按键复用 (11)7.串行数据传输格式 (12)8.应用时串行数据的传输 (13)8.1地址增加模式 (13)8.2固定地址模式 (13)8.3读按键时序 (14)8.4采用地址自动加一和固定地址方式的程序设计流程图 (15)9.应用电路 (17)10.电气参数 (18)11.封装 (20)11.1SOP16 (20)12.版本修订说明 (21)1. 产品概述1.1 功能特性CMS1617是一种带键盘扫描接口的LED(发光二极管显示器)驱动控制专用IC,内部集成有MCU数字接口、数据锁存器、LED驱动、键盘扫描等电路。
CN5G资料

CELL RECTIFIER DIODES
C5A
4.82
3.94
Anode 1.25 Cathode
0.51
MECHANICAL DATA :
* Case : C5A * Terminals : Solderable per MIL-STD-202, Method 208 guaranteed * Polarity : Cathode to bigger size slug, For Anode to bigger size slug use "R" suffix. * Mounting position : Any * Weight : 0.22 gram Dimensions in millimeter
元器件交易网
CN5A - CN5M
PRV : 50 - 1000 Volts Io : 5.0 Amperes
FEATURES :
* * * * * * High current capability High surge current capability High reliability Low reverse current Low forward voltage drop Chip form
0.38
Rating at 25 °C ambient temperature unless otherwise specified. Single phase, half wave, 60 Hz, resistive or inductive load. For capacitive load, derate current by 20%.
10
100 50
1.0
Pulse Width = 300 µs 2% Duty Cycle TJ = 25 °C
- 1、下载文档前请自行甄别文档内容的完整性,平台不提供额外的编辑、内容补充、找答案等附加服务。
- 2、"仅部分预览"的文档,不可在线预览部分如存在完整性等问题,可反馈申请退款(可完整预览的文档不适用该条件!)。
- 3、如文档侵犯您的权益,请联系客服反馈,我们会尽快为您处理(人工客服工作时间:9:00-18:30)。
Opti MOS®
IPP16CN10N G PG-TO263-3PG-TO252-3PG-TO262-3PG-TO220-3
Parameter
Symbol Conditions
Unit
min.
typ.
max.
Thermal characteristics
Thermal resistance, junction - case R thJC -- 1.5K/W
R thJA
minimal footprint --626 cm2 cooling area 4)--40minimal footprint --756 cm2 cooling area 4)
--50
Electrical characteristics, at T j =25 °C, unless otherwise specified Static characteristics
Drain-source breakdown voltage V (BR)DSS V GS =0 V, I D =1 mA 100--V
Gate threshold voltage V GS(th)V DS =V GS , I D =61 µA 234Zero gate voltage drain current
I DSS
V DS =80 V, V GS =0 V, T j =25 °C
-0.1
1
µA V DS =80 V, V GS =0 V, T j =125 °C
-10100Gate-source leakage current I GSS V GS =20 V, V DS =0 V -1100nA Drain-source on-state resistance
R DS(on)
V GS =10 V, I D =53 A, (TO252)
-
12.2
16
m Ω
V GS =10 V, I D =53 A, (TO262)
-12.416.2
V GS =10 V, I D =53 A, (TO220, TO263)
-12.716.5Gate resistance R G - 1.2-ΩTransconductance
g fs
|V DS |>2|I D |R DS(on)max , I D =53 A
33
65
-S
Values 4)
Device on 40 mm x 40 mm x 1.5 mm epoxy PCB FR4 with 6 cm 2 (one layer, 70 µm thick) copper area for drain connection. PCB is vertical in still air.
Thermal resistance, junction - ambient (TO220, TO262, TO263)Thermal resistance, junction - ambient (TO252)
Parameter
Symbol Conditions
Unit
min.
typ.
max.
Dynamic characteristics Input capacitance C iss -24203220pF
Output capacitance
C oss -364484Reverse transfer capacitance C rss -2335Turn-on delay time t d(on)-1522ns
Rise time
t r -1421Turn-off delay time t d(off)-2741Fall time
t f
-
7
11
Gate Charge Characteristics 5)Gate to source charge Q gs -1318nC
Gate to drain charge Q gd -913Switching charge Q sw -1521Gate charge total Q g -3648Gate plateau voltage V plateau - 5.6-V Output charge Q oss
V DD =50 V, V GS =0 V -
38
51
nC
Reverse Diode
Diode continous forward current I S --53A
Diode pulse current I S,pulse --212Diode forward voltage V SD V GS =0 V, I F =53 A, T j =25 °C -1 1.2
V Reverse recovery time t rr -110ns
Reverse recovery charge
Q rr
-
215
-nC
5)
See figure 16 for gate charge parameter definition
V R =50 V, I F =I S , d i F /d t =100 A/µs
T C =25 °C
Values V GS =0 V, V DS =50 V, f =1 MHz
V DD =50 V, V GS =10 V, I D =26.5 A, R G =1.6 ΩV DD =50 V, I D =53 A, V GS =0 to 10 V
1 Power dissipation
5 Typ. output characteristics
9 Drain-source on-state resistance
13 Avalanche characteristics
PG-TO220-3: Outline
PG-TO-263 (D²-Pak)
PG-TO252-3: Outline
Published by
Infineon Technologies AG
81726 München, Germany
© Infineon Technologies AG 2006.
All Rights Reserved.
Attention please!
The information given in this data sheet shall in no event be regarded as a guarantee of conditions or characteristics (“Beschaffenheitsgarantie”). With respect to any examples or hints given herein, any typical values stated herein and/or any information regarding the application of the device, Infineon Technologies hereby disclaims any and all warranties and liabilities of any kind, including without limitation warranties of
non-infringement of intellectual property rights of any third party.
Information
For further information on technology, delivery terms and conditions and prices please contact your nearest Infineon Technologies Office ().
Warnings
Due to technical requirements components may contain dangerous substances. For information on the types in question please contact your nearest Infineon Technologies Office.
Infineon Technologies Components may only be used in life-support devices or systems with the express written approval of Infineon Technologies, if a failure of such components can reasonably be expected to cause the failure of that life-support device or system, or to affect the safety or effectiveness of that device or system. Life support devices or systems are intended to be implanted in the human body, or to support and/or maintain and sustain and/or protect human life. If they fail, it is reasonable to assume that the health of the user or other persons may be endangered.。