H14innsi
TURCK 非锥形感应器 NI3-EG08K-Y1-H1341 说明书

N I 3-E G 08K -Y 1-H 1341 | 11/29/2022 05-07 | t e c h n i c a l c h a n g e s r e s e r v e dNI3-EG08K-Y1-H1341Inductive SensorTechnical dataNI3-EG08K-Y1-H134******** Rated switching distance 3 mmNon-flush Secured operating distance ≤ (0.81 × Sn) mmSt37 = 1; Al = 0.3; stainless steel = 0.7; Ms = 0.4≤ 2 % of full scale ≤ ±10 %1…10 %2-wire, NAMUR 5 kHz Nom. 8.2 VDC Non-actuated current consumption ≥ 2.1 mA Actuated current consumption ≤ 1.2 mAKEMA 02 ATEX 1090X )/inductance (L i )150 nF/150 µHÉ II 1 G Ex ia IIC T6 Ga/II 1 D Ex ia IIIC T135 °C Da(max. U i = 20 V, I i = 60 mA, PThreaded barrel, M8 × 139 mmFeatures■Threaded barrel, M8 x 1■Stainless steel, 1.4427 SO ■DC 2-wire, nom. 8.2 VDC■Output acc. to DIN EN 60947-5-6 (NAMUR)■M12 x 1 male connector■ATEX category II 1 G, Ex zone 0■ATEX category II 1 D, Ex zone 20■SIL2 (Low Demand Mode) acc. to IEC 61508,PL c acc. to ISO 13849-1 at HFT0■SIL3 (All Demand Mode) acc. to IEC 61508,PL e acc. to ISO 13849-1 with redundant configuration HFT1Wiring diagramFunctional principleInductive sensors detect metal objectscontactless and wear-free. For this, they use a high-frequency electromagnetic AC field that interacts with the target. Inductive sensors generate this field via an RLC circuit with a ferrite coil.Technical dataMounting instructionsMounting instructions/Description222/92/11|1431H-1Y-K8GE-3INN I 3-E G 08K -Y 1-H 1341 | 11/29/2022 05-07 | t e c h n i c a l c h a n g e s r e s e r v e d AccessoriesBST-08B6947210Mounting clamp for threaded barrel sensors, with dead-stop; material:PA6QM-086945100Quick-mount bracket with dead-stop, chrome-plated brass, male thread M12 x 1. Note: The switchingdistance of proximity switches may be reduced through the use of quick-mount brackets.MW-086945008Mounting bracket for threaded barrelsensors; material: Stainless steel A21.4301 (AISI 304)BSS-086901322Mounting clamp for smooth and threaded barrel sensors; material:PolypropyleneMBS8069479Mounting clamp for smooth barrel sensors; mounting block material:Anodized aluminumWiring accessoriesDimension drawingTypeID RKC4.221T-2/TEB6628420Connection cable, female M12, straight,2-pin, cable length: 2 m, sheathmaterial: PVC, black; cULus approval;other cable lengths and qualities available, see WKC4.221T-2/TEB 6628427Connection cable, M12 femaleconnector, angled, 2-pin, cable length:2 m, jacket material: PVC, black; cULus approval; other cable lengths andqualities available, see N I 3-E G 08K -Y 1-H 1341 | 11/29/2022 05-07 | t e c h n i c a l c h a n g e s r e s e r v e dInstructions for useIntended useThis device fulfills Directive 2014/34/EC and is suited for use in areas exposed to explosion hazards according to EN 60079-0:2018 and EN 60079-11:2012.Further it is suited for use in safety-related systems, including SIL2 as per IEC61508.In order to ensure correct operation to the intended purpose it is required to observe the national regulations and directives.For use in explosion hazardous areas conform to classificationII 1 G and II 1 D (Group II, Category 1 G, electrical equipment for gaseous atmospheres and category 1 D, electrical equipment for dust atmospheres).Marking (see device or technical data sheet)É II 1 G and Ex ia IIC T6 Ga and É II 1 D Ex ia IIIC T135 °C Da acc. to EN 60079-0, -11Local admissible ambient temperature -25…+70 °CInstallation/CommissioningThese devices may only be installed, connected and operated by trained and qualified staff. Qualified staff must have knowledge of protection classes, directives and regulations concerning electrical equipment designed for use in explosion hazardous areas.Please verify that the classification and the marking on the device comply with the actual application conditions.This device is only suited for connection to approved Exi circuits according to EN 60079-0 and EN 60079-11. Please observe the maximum admissible electrical values.After connection to other circuits the sensor may no longer beused in Exi installations. When interconnected to (associated) electrical equipment, it is required to perform the "Proof of intrinsic safety" (EN60079-14).Attention! When used in safety systems, all content of the security manual must be observed.Installation and mounting instructionsAvoid static charging of cables and plastic devices. Please only clean the device with a damp cloth. Do not install the device in a dust flow and avoid build-up of dust deposits on the device.If the devices and the cable could be subject to mechanical damage, they must be protected accordingly. They must also be shielded against strong electro-magnetic fields.The pin configuration and the electrical specifications can be taken from the device marking or the technicaldata sheet.In order to avoid contamination of the device, please remove possible blanking plugs of the cable glands or connectors only shortly before inserting the cable or opening the cable socket.Service/MaintenanceRepairs are not possible. The approval expires if the device is repaired or modified by a person other than the manufacturer. The most important data from the approval are listed.。
Pepperl+Fuchs NJ5-18GK-SN 漏Magnetic感应传感器说明书

17-01-24 15:36D a t e o f i s s u e : 2017-01-24250929_e n g .x m lInstructionManual electrical apparatus for hazardous areas Device category 1Gfor use in hazardous areas with gas, vapour and mist EC-T ype Examination CertificateCE marking ATEX marking ¬ II 1G Ex ia IIC T6…T1 G aThe Ex-related marking can also be printed on the enclosed label.Standards EN 60079-0:2012+A11:2013 EN 60079-11:2012 Ignition protection "Intrinsic safety"Use is restricted to the following stated conditions Appropriate typeNJ 5-18GK-SN...Effective internal inductivity C i ≤ 120 nF ; a cable length of 10 m is considered.Effective internal inductance L i≤ 200 µH ; a cable length of 10 m is considered.G eneralThe apparatus has to be operated according to the appropriate data in the data sheet and in this instruction manual. The EU-type examination certificate has to beobserved. The special conditions must be adhered to! The ATEX directive and there-fore the EU-type-examination certificates generally apply only to the use of electrical apparatus under atmospheric conditions.The device has been checked for suitability for use at ambient temperatures of > 60 °C by the named certification authority. The surface temperature of the device remains within the required limits.For the use of apparatus outside of atmospheric conditions, a reduction of the per-missible minimum ignition energies may need to be considered.Ambient temperatureDetails of the correlation between the type of circuit connected, the maximum per-missible ambient temperature, the temperature class, and the effective internal reac-tance values can be found on the EC-type examination certificate. Note: Use the temperature table for category 1 The 20 % reduction in accordance with EN 1127-1 has already been applied to the temperature table for category 1.Installation, commissioningLaws and/or regulations and standards governing the use or intended usage goal must be observed. The intrinsic safety is only assured in connection with an appro-priate related apparatus and according to the proof of intrinsic safety. The associated apparatus must satisfy the requirements of category ia. Because of the risk of igni-tion, which can occur due to faults and/or transient currents in the equipotential bonding system, galvanic isolation is preferable in the supply and signal circuits. Associated apparatus without electrical isolation can only be used if the correspond-ing requirements of IEC 60079-14 are satisfied. If the Ex-related marking is printed only on the supplied label, then this must be attached in the immediate vicinity of the sensor. The sticking surface for the label must be clean and free from grease. The attached label must be legible and indelible, including in the event of possible chem-ical corrosion.Maintenance No changes can be made to apparatus, which are operated in hazardous areas.Repairs to these apparatus are not possible.Special conditionsProtection from mechanical dangerWhen using the device in a temperature range of -60 °C to -20 °C, protect the sensor against the effects of impact by installing an additional enclosure. The information regarding the minimum ambient temperature for the sensor as provided in the datasheet must also be observed.Electrostatic chargeWhen used in group IIC non-permissible electrostatic charges should be avoided on the plastic housing parts. Avoid electrostatic charges that can cause electrostatic dis-charge when installing or operating the device. Information on electrostatic hazards can be found in the technical specification IEC/TS 60079-32-1.Degree of protection required when installing connecting componentsThe connecting parts of the sensor must be set up in such a way that degree of pro-tection IP20, in accordance with lEC 60529, is achieved as a minimum.R e l e a s e d a t e : 2017-01-24 15:36D a t e o f i s s u e : 2017-01-24250929_e n g .x m lInstructionManual electrical apparatus for hazardous areas Device category 2Gfor use in hazardous areas with gas, vapour and mist EC-T ype Examination CertificateCE marking ATEX marking ¬ II 1G Ex ia IIC T6…T1 G aThe Ex-related marking can also be printed on the enclosed label.Standards EN 60079-0:2012+A11:2013 EN 60079-11:2012 Ignition protection "Intrinsic safety"Use is restricted to the following stated conditions Appropriate typeNJ 5-18GK-SN...Effective internal inductivity C i≤ 120 nF ; a cable length of 10 m is considered.Effective internal inductance L i ≤ 200 µH ; a cable length of 10 m is considered.G eneralThe apparatus has to be operated according to the appropriate data in the data sheet and in this instruction manual. The EU-type examination certificate has to beobserved. The special conditions must be adhered to! The ATEX directive and there-fore the EU-type-examination certificates generally apply only to the use of electrical apparatus under atmospheric conditions.The device has been checked for suitability for use at ambient temperatures of > 60 °C by the named certification authority. The surface temperature of the device remains within the required limits.For the use of apparatus outside of atmospheric conditions, a reduction of the per-missible minimum ignition energies may need to be considered.Maximum permissible ambient temperature T amb Details of the correlation between the type of circuit connected, the maximum per-missible ambient temperature, the temperature class, and the effective internal reac-tance values can be found on the EC-type examination certificate.Installation, commissioningLaws and/or regulations and standards governing the use or intended usage goal must be observed. The intrinsic safety is only assured in connection with an appro-priate related apparatus and according to the proof of intrinsic safety. If the Ex-related marking is printed only on the supplied label, then this must be attached in the imme-diate vicinity of the sensor. The sticking surface for the label must be clean and free from grease. The attached label must be legible and indelible, including in the event of possible chemical corrosion.Maintenance No changes can be made to apparatus, which are operated in hazardous areas.Repairs to these apparatus are not possible.Special conditionsProtection from mechanical dangerWhen using the device in a temperature range of -60 °C to -20 °C, protect the sensor against the effects of impact by installing an additional enclosure. The information regarding the minimum ambient temperature for the sensor as provided in the datasheet must also be observed.Degree of protection required when installing connecting componentsThe connecting parts of the sensor must be set up in such a way that degree of pro-tection IP20, in accordance with lEC 60529, is achieved as a minimum.17-01-24 15:36D a t e o f i s s u e : 2017-01-24250929_e n g .x m lInstructionManual electrical apparatus for hazardous areasDevice category 3G (nA) for use in hazardous areas with gas, vapour and mistX CE marking ATEX marking ¬ II 3G Ex nA IIC T6 GcThe Ex-related marking can also be printed on the enclosed label.Standards EN 60079-0:2012+A11:2013, EN 60079-15:2010 Ignition protection category "n"Use is restricted to the following stated conditionsG eneralThe apparatus has to be operated according to the appropriate data in the data sheet and in this instruction manual. The data stated in the data sheet are restricted by this operating instruction! The special conditions must be observed!Installation, commissioningLaws and/or regulations and standards governing the use or intended usage goal must be observed. If the Ex-related marking is printed only on the supplied label, then this must be attached in the immediate vicinity of the sensor. The sticking surface for the label must be clean and free from grease. The attached label must be legible and indel-ible, including in the event of possible chemical corrosion.MaintenanceNo changes can be made to apparatus, which are operated in hazardous areas.Repairs to these apparatus are not possible.Special conditionsMinimum series resistance R V A minimum series resistance R V is to be provided between the power supply voltage and the proximity switch in accordance with the following list. This can also be assured by using a switch amplifier.Maximum operating voltage U BmaxThe maximum permissible operating voltage UB max is restricted to the values in the following list. T olerances are not permissible.Maximum permissible ambient temperature T Umax Values can be obtained from the following list, depending on the max. operating voltage Ub max and the minimum series resistance Rv. at U Bmax =9 V , R V =562 Ω58 °C (136.4 °F) using an amplifier in accordance with EN 60947-5-6 58 °C (136.4 °F)Protection from mechanical danger The sensor must not be exposed to ANY FORM of mechanical danger.Protection from UV lightThe sensor and the connection cable must be protected from damaging UV-radiation. This can be achieved when the sensor is used in internal areas.Protection of the connection cable The connection cable must be prevented from being subjected to tension and torsional loading.Protection against transients Ensure transient protection is provided and that the maximum value of the transient pro-tection (140% of 85 V) is not exceeded.Material selection accessoriesWhen selecting accessories, ensure that the material allows the temperature of the enclosure to rise to up to 70 °C.R e l e a s e d a t e : 2017-01-24 15:36D a t e o f i s s u e : 2017-01-24250929_e n g .x m lInstructionManual electrical apparatus for hazardous areas Device category 3G (ic) for use in hazardous areas with gas, vapour and mistXCE marking ATEX marking ¬ II 3G Ex ic IIC T6…T1 GcThe Ex-related marking can also be printed on the enclosed label.StandardsEN 60079-0:2012+A11:2013 EN 60079-11:2012 Ignition protection category "ic"Use is restricted to the following stated conditions Effective internal inductivity C i≤ 120 nF ; a cable length of 10 m is considered.Effective internal inductance L i≤ 200 µH ; A cable length of 10 m is considered.G eneralThe apparatus has to be operated according to the appropriate data in the data sheet and in this instruction manual. The data stated in the data sheet are restricted by this operating instruction! The special conditions must be observed! The ATEX Directive applies only to the use of apparatus under atmospheric conditions.If you use the device outside atmospheric conditions, consider that the permissible safety parameters should be reduced.Installation, commissioningLaws and/or regulations and standards governing the use or intended usage goal must be observed. The sensor must only be operated with energy-limited circuits, which satisfy the requirements of IEC 60079-11. The explosion group complies with the connected, supplying, power limiting circuit. If the Ex-relevant identification is printed exclusively on the adhesive label provided, this label must be affixed in the immediate vicinity of the sensor! The background surface to which the adhesivelabel is to be applied must be clean and free from grease! The applied label must be dura-ble and remain legible, with due consideration of the possibility of chemical corro-sion!Maintenance No changes can be made to apparatus, which are operated in hazardous areas.Repairs to these apparatus are not possible.Special conditionsfor Pi=34 mW, Ii=25 mA, T6 70 °C (158 °F) for Pi=34 mW, Ii=25 mA, T5 85 °C (185 °F) for Pi=34 mW, Ii=25 mA, T4-T1 100 °C (212 °F) for Pi=64 mW, Ii=25 mA, T6 69 °C (156.2 °F) for Pi=64 mW, Ii=25 mA, T5 84 °C (183.2 °F) for Pi=64 mW, Ii=25 mA, T4-T1 100 °C (212 °F) for Pi=169 mW, Ii=52 mA, T6 51 °C (123.8 °F) for Pi=169 mW, Ii=52 mA, T5 66 °C (150.8 °F) for Pi=169 mW, Ii=52 mA, T4-T1 80 °C (176 °F) for Pi=242 mW, Ii=76 mA, T6 39 °C (102.2 °F) for Pi=242 mW, Ii=76 mA, T5 54 °C (129.2 °F) for Pi=242 mW, Ii=76 mA, T4-T1 61 °C (141.8 °F)Protection from mechanical danger The sensor must not be mechanically damaged.When used in the temperature range below -20 °C the sensor should be protected from knocks by the provision of an additional housing.Connection partsThe connection parts are to be installed, such that a minimum protection class of IP20 is achieved, in accordance with IEC 60529.17-01-24 15:36D a t e o f i s s u e : 2017-01-24250929_e n g .x m lInstructionManual electrical apparatus for hazardous areas Device category 1Dfor use in hazardous areas with combustible dust EC-T ype Examination CertificateCE marking ATEX marking ¬ II 1D Ex ia IIIC T135°C DaThe Ex-related marking can also be printed on the enclosed label.Standards EN 60079-0:2012+A11:2013 EN 60079-11:2012Ignition protection "Intrinsic safety" Use is restricted to the following stated condi-tionsAppropriate typeNJ 5-18GK-SN...Effective internal inductivity C i ≤ 120 nF ; a cable length of 10 m is considered.Effective internal inductance L i≤ 200 µHA cable length of 10 m is considered.G eneralThe apparatus has to be operated according to the appropriate data in the data sheet and in this instruction manual. The EU-type examination certificate has to beobserved. The ATEX directive and therefore the EU-type-examination certificates generally apply only to the use of electrical apparatus under atmospheric conditions.The device has been checked for suitability for use at ambient temperatures of > 60 °C by the named certification authority. The surface temperature of the device remains within the required limits.For the use of apparatus outside of atmospheric conditions, a reduction of the per-missible minimum ignition energies may need to be considered.Permissible ambient temperature rangeDetails of the correlation between the type of circuit connected, the maximum per-missible ambient temperature, the surface temperature, and the effective internal reactance values can be found on the EC-type-examination certificate. The maxi-mum permissible ambient temperature of the data sheet must be noted, in addition, the lower of the two values must be maintained.Installation, commissioningLaws and/or regulations and standards governing the use or intended usage goal must be observed. The intrinsic safety is only assured in connection with an appro-priate related apparatus and according to the proof of intrinsic safety. If the Ex-related marking is printed only on the supplied label, then this must be attached in the imme-diate vicinity of the sensor. The sticking surface for the label must be clean and free from grease. The attached label must be legible and indelible, including in the event of possible chemical corrosion.Maintenance No changes can be made to apparatus, which are operated in hazardous areas.Repairs to these apparatus are not possible.Special conditionsProtection from mechanical dangerWhen using the device in a temperature range of -60 °C to -20 °C, protect the sensor against the effects of impact by installing an additional enclosure. The information regarding the minimum ambient temperature for the sensor as provided in the datasheet must also be observed.Electrostatic chargeAvoid electrostatic charges that can cause electrostatic discharge when installing or operating the device. Information on electrostatic hazards can be found in the techni-cal specification IEC/TS 60079-32-1. Do not attach the nameplate provided in areas where electrostatic charge can build up.Degree of protection required when installing connecting componentsThe connecting parts of the sensor must be set up in such a way that degree of pro-tection IP20, in accordance with lEC 60529, is achieved as a minimum.R e l e a s e d a t e : 2017-01-24 15:36D a t e o f i s s u e : 2017-01-24250929_e n g .x m lInstructionManual electrical apparatus for hazardous areas Device category 3D for use in hazardous areas with combustible dust CertificateCE marking ATEX marking ¬ II 3D Ex tc IIIC T80°C DcThe Ex-related marking can also be printed on the enclosed label.Standards EN 60079-0:2012+A11:2013, EN 60079-31:2014Protection by enclosure "tc" Some of the information in this instruction manual is more specific than the information provided in the datasheet.G eneralThe corresponding datasheets, declarations of conformity, EC-type examination certifi-cates, certifications, and control drawings, where applicable (see datasheets), form an integral part of this document. These documents can be found at . The maximum surface temperature of the device was determined without a layer of dust on the apparatus. Some of the information in this instruction manual is more specific than the information provided in the datasheet.Installation, commissioningLaws and/or regulations and standards governing the use or intended usage goal must be observed. The adhesive label provided must be affixed in the immediate vicinity of the sensor! The surface to which the label is applied must be clean, flat and free from grease! The affixed adhesive label must be readable and durable, taking account of the possibility of chemical corrosion!MaintenanceNo changes can be made to apparatus, which are operated in hazardous areas.Repairs to these apparatus are not possible.Special conditionsMinimum series resistance R V A minimum series resistance RV is to be provided between the power supply voltage and the proximity switch in accordance with the following list. This can also be assured by using a switch amplifier.Maximum operating voltage U BmaxThe maximum permissible operating voltage UBmax must be restricted to the values given in the following list. T olerances are not permitted.Maximum permissible ambient temperature T Umax Values can be obtained from the following list, depending on the max. operating voltage Ub max and the minimum series resistance Rv. at U Bmax =9 V, R V =562 Ω58 °C (136.4 °F) using an amplifier in accordance with EN 60947-5-6 331 KProtection from mechanical danger The sensor must not be exposed to ANY FORM of mechanical danger.Protection from UV lightThe sensor and the connection cable must be protected from damaging UV-radiation. This can be achieved when the sensor is used in internal areas.Protection of the connection cable The connection cable must be prevented from being subjected to tension and torsional loading.Electrostatic chargeAvoid electrostatic charges that can cause electrostatic discharge when installing or operating the device. Information on electrostatic hazards can be found in the technical specification IEC/TS 60079-32-1. Do not attach the nameplate provided in areas where electrostatic charge can build up.。
梅特勒称重使用说明书

使用说明书
本手册版权归梅特勒-托利多(常州)称重设备系统有限公司所有,未经许可不得翻 印、修改或引用! METTLER TOLEDO 为梅特勒-托利多公司的注册商标!
警告
1、请专业人员调试、检测和维修系统。 2、请保持本设备良好接地。
注意
1、严禁带电插拔。 2、请先切断电源,再进行电气设备连接,检修。
第 3 章 操作...................................................................................................................................18 3.1 显示屏..............................................................................................................................18 3.2 按键..................................................................................................................................19 3.3 菜单..................................................................................................................................20 3.3.1 快捷操作菜单与设置菜单...................................................................................20 3.3.2 菜单模式...............................................................................................................20 3.4 应用..................................................................................................................................21 3.4.1 目标值...................................................................................................................21 3.4.2 比较器...................................................................................................................21
Pepperl+Fuchs 温度多输入设备(区域1安装)说明书
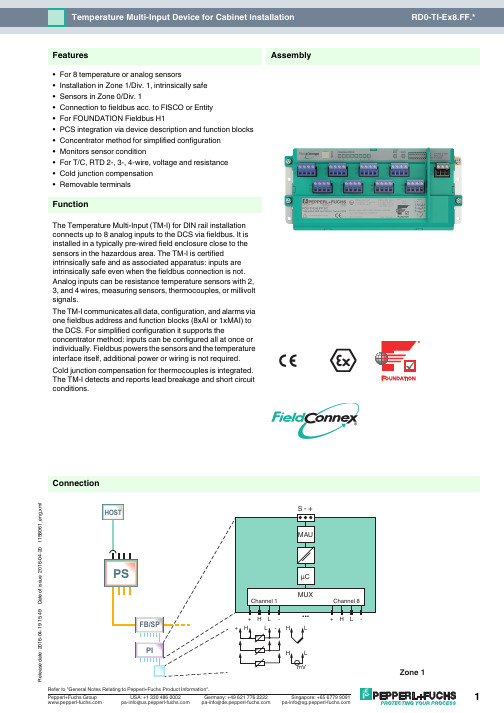
16-04-19 15:49D a t e o f i s s u e 2016-04-20t 158061_e n g .x m lConnectionAssembly•For 8 temperature or analog sensors•Installation in Zone 1/Div. 1, intrinsically safe •Sensors in Zone 0/Div. 1•Connection to fieldbus acc. to FISCO or Entity •For FOUNDATION Fieldbus H1•PCS integration via device description and function blocks •Concentrator method for simplified configuration •Monitors sensor condition•For T/C, RTD 2-, 3-, 4-wire, voltage and resistance •Cold junction compensation •Removable terminalsFunctionThe Temperature Multi-Input (TM-I) for DIN rail installation connects up to 8 analog inputs to the DCS via fieldbus. It is installed in a typically pre-wired field enclosure close to the sensors in the hazardous area. The TM-I is certifiedintrinsically safe and as associated apparatus: inputs are intrinsically safe even when the fieldbus connection is not. Analog inputs can be resistance temperature sensors with 2, 3, and 4 wires, measuring sensors, thermocouples, or millivolt signals.The TM-I communicates all data, configuration, and alarms via one fieldbus address and function blocks (8xAI or 1xMAI) to the DCS. For simplified configuration it supports theconcentrator method: inputs can be configured all at once or individually. Fieldbus powers the sensors and the temperature interface itself, additional power or wiring is not required.Cold junction compensation for thermocouples is integrated. The TM-I detects and reports lead breakage and short circuit conditions.Features®16-04-19 15:49D a t e o f i s s u e 2016-04-20t 158061_e n g .x mlGeneral specifications Design / Mounting Cabinet installationFieldbus interface Fieldbus type FOUNDATION FieldbusPhysical layer profile profile type 511 (FISCO), profile type 111 (Entity)ITK version 4.51Implementationresource block1x RSfunction block8x AI, 1x MAItransducer block8x sensor TB, 1x concentrator TB Execution time AI, MAI 40 ms max.Macro cycle typical for one device 8xAI or 1xMAI ≤ 500 ms Firmware updatevia separate plug connection FDE (Fault Disconnect Equipment) 6.7 mA Polarity not polarity sensitiveRated voltage U N 9 ... 32 V Rated currentI N≤ 23 mAIndicators/operating means LED PWR green: on, bus voltage existentLED COM ERR red: continuous lightning: hardware error; 2 Hz flashing: no bus activities or bus fault; off: no error LED CHANNEL ERROR red: 2 Hz flashing: lead breakage, overrange; off: no error InputNumber 8Sensor types see table 1Grounding grounding of thermoelements possibleError detection lead breakage, wiring error, hardware device error Common mode voltage Input to Input 600 V peakTransfer characteristics DeviationCold junction compensation ± 0.5 °C (32.9 °F)Resolution/accuracysee table 2Influence of ambient temperature see table 3LinearizationT/C input 0.1°C RTD input 0.03°C Internal measurement cycle for all sensor types ≤ 1 sElectrical isolation Fieldbus/inputs safe galvanic isolation acc. to EN 60079-11, voltage peak value 375 V Directive conformity Electromagnetic compatibilityDirective 2014/30/EU EN 61326-1:2013Standard conformity Electrical isolationEN 60079-11Electromagnetic compatibility NE 21:2011Degree of protection IEC 60529Fieldbus standard IEC 61158-2Shock resistance EN 60068-2-27Vibration resistance EN 60068-2-6Ambient conditions Ambient temperature-40 ... 70 °C (-40 ... 158 °F) hazardous area-40 ... 85 °C (-40 ... 185 °F) safe area Storage temperature -40 ... 85 °C (-40 ... 185 °F)Relative humidity ≤ 95 % non-condensing Shock resistance 15 g , 11 ms Vibration resistance 5 g , 10 ... 150 HzCorrosion resistance acc. to ISA-S71.04-1985, severity level G3Mechanical specifications Connection type plug-in terminals , spring terminal and screw terminal Core cross-sectionBus up to 2.5 mm 2Inputs up to 2.5 mm 2Housing material Polycarbonate Degree of protection IP20Mass 360 gMountingmounting on DIN rail in cabinet16-04-19 15:49D a t e o f i s s u e 2016-04-20t 158061_e n g .x mlsee manualGroup, category, type of protection, temperature class ¬ II 2 (1) G Ex ia [ia Ga] IIC T4 Gb , ¬ II (1) G [Ex ia Ga] IIC , ¬ II (1) D [Ex ia Da] IIIC , ¬ II 3 G Ex ic IIC T4 GcBus FISCO see EC-Type Examination Certificate Inputssee EC-Type Examination Certificate Statement of conformityPTB 03 ATEX 2238 X Group, category, type of protection, temperature class ¬ II 3 G Ex nA IIC T4 Gc Electrical isolationBus see Statement of Conformity Inputsee EC-Type Examination Certificate Directive conformityDirective 2014/34/EU EN 60079-0:2012 , EN 60079-11:2012 , EN 60079-15:2010International approvals IECEx approval IECEx PTB 05.0001 , IECEx PTB 05.0002XApproved forEx ia [ia Ga] IIC T4 Gb , [Ex ia Ga] IIC , [Ex ia Da] IIIC , Ex ic IIC T4 Gc , Ex nA IIC T4 Gc Certificates and approvals Marine approval DNV A-14038General information Supplementary informationEC-Type Examination Certificate, Statement of Conformity, Declaration of Conformity, Attestation of Conformity and instructions have to be observed where applicable. For information see .Type code/order designationType Code DescriptionRD0-TI-Ex8.FF .ST Fieldbus temperature interface with 8 inputs with screw terminals without field housing for mounting on DIN rail in cabinet RD0-TI-Ex8.FF .SCFieldbus temperature interface with 8 inputs with spring terminals without field housing for mounting on DIN rail in cabinetDimensionsInstallation note16-04-19 15:49D a t e o f i s s u e 2016-04-20t 158061_e n g .x mlAdditional informationTable 1: Sensor typesThermocoupleType Standard Range (°C)Range (°F)B EN 60584-1300 ... 1800572 ... 3272E EN 60584-1-200 ... 1000-328 ... 1832J EN 60584-1-200 ... 1000-328 ... 1832K EN 60584-1-200 ... 1372-328 ... 2502N EN 60584-1-200 ... 1300-328 ... 2372R EN 60584-10 ... 1768-32 ... 3214S EN 60584-10 ... 1768-32 ... 3214T EN 60584-1-200 ... 400-328 ... 752W5Re/W26ReASTM 988-960 (2000)-32 (3632)Input voltageType Range (mV)Range 1-100 (150)RTDType Standard Range (°C)Range (°F)Pt50EN 60751 (ITS90)-200 ... 850-328 ... 1562Pt100EN 60751 (ITS90)-200 ... 850-328 ... 1562Pt100JIS C 1604-1989-200 ... 630-328 ... 1166Pt200EN 60751 (ITS90)-200 ... 850-328 ... 1562Pt500EN 60751 (ITS90)-200 ... 850-328 ... 1562Pt1000EN 60751 (ITS90)-200 ... 850-328 ... 1562Ni100DIN 43760-1987-60 ... 250-76 ... 482Ni120Minco standard -80 ... 320-112 ... 608Ni200DIN 43760-1987-60 ... 250-76 ... 482Cu10SAMA RC21-4-1966-70 (150)-94 (302)Resistance inputType Range (Ohm)Range 10 ... 650Range 20 ... 1300Range 30 ... 2600Range 40 (5200)Table 2: AccuracyThermocoupleType Range (°C)Range (°F)Accuracy (°C)(°F)B300 ... 600600 ... 12001200 ... 1800572 ... 11121112 ... 21922192 ... 3272± 3.32± 1.77± 1.08± 5.98± 3.19± 1.94E -200 ... -50-50 ... 1000-328 ... -58-58 ... 1832± 0.42± 0.31± 0.76± 0.56J -200 ... 00 ... 1000-328 ... 3232 ... 1832± 0.48± 0.31± 0.86± 0.56K -200 ... 00 ... 1372-328 ... 3232 ... 2502± 0.68± 0.43± 1.22± 0.77N -200 ... -100-100 ... 500500 ... 1300-328 ... -148-148 ... 932932 ... 2372± 1.03± 0.54± 0.39± 1.85± 0.97± 0.70R 0 ... 350350 ... 176832 ... 662662 ... 3214± 1.93± 1.16± 3.47± 2.09S0 ... 550550 ... 176832 ... 10221022 ... 3214± 1.92± 1.15± 3.46± 2.07T -200 ... -50-50 ... 400-328 ... -58-58 ... 752± 0.66± 0.35± 1.19± 0.63W5Re/W26Re0 ... 800800 (2000)-32 ... 14721472 ... 3632± 0.80± 1.05± 1.45± 1.89Input voltageType Accuracy (µV)Range 1± 20RTDAccuracyType (°C)(°F)Pt50± 0.77± 1.39Pt100± 0.33± 0.59Pt100 JIS ± 0.33± 0.59Pt200± 0.33± 0.59Pt500± 0.31± 0.56Pt1000± 0.31± 0.56Ni100± 0.18± 0.32Ni120± 0.18± 0.32Ni200± 0.18± 0.32Cu10± 2.99± 5.38Resistance inputType Accuracy (mOhm)Range 1± 115Range 2± 230Range 3± 460Range 4± 92016-04-19 15:49D a t e o f i s s u e 2016-04-20t 158061_e n g .x mlTable 3: Influence of ambient temperatureThermocoupleType Range (°C)Range (°F)Deviation (°C/K)B300 ... 600600 ... 12001200 ... 1800572 ... 11121112 ... 21922192 ... 3272± 0.0060± 0.0131± 0.0242E-200 ... -50-50 ... 200200 ... 1000-328 ... -58-58 ... 392392 ... 1832± 0.0070± 0.0036± 0.0203J-200 ... 00 ... 200200 ... 1000-328 ... 3232 ... 392392 ... 1832± 0.0072± 0.0039± 0.0243K-200 ... 00 ... 500500 ... 1372-328 ... 3232 ... 932932 ... 2502± 0.0077± 0.0097± 0.0323N-200 ... -100-100 ... 500500 ... 1300-328 ... -148-148 ... 932932 ... 2372± 0.0080± 0.0088± 0.0264R0 ... 350350 ... 800800 ... 176832 ... 662662 ... 14721472 ... 3214± 0.0057± 0.0129± 0.0338S0 ... 550550 ... 800800 ... 176832 ... 10221022 ... 14721472 ... 3214± 0.0094± 0.0135± 0.0355T-200 ... -50-50 ... 200200 ... 400-328 ... -58-58 ... 392392 ... 752± 0.0071± 0.0035± 0.0067W5Re/W26Re0 ... 800800 (2000)-32 ... 14721472 ... 3632± 0.0151± 0.0552Input voltageType Deviation (µV/K)Range 1± 2RTDType Deviation (°C/K)Pt50± 0.010Pt100± 0.010Pt100 JIS ± 0.010Pt200± 0.010Pt500± 0.010Pt1000± 0.010Ni100± 0.010Ni120± 0.010Ni200± 0.010Cu10± 0.010Resistance inputType Deviation (mOhm/K)Range 1± 6Range 2± 6Range 3± 13Range 4± 26。
sensirion shtix 数字温湿度传感器 技术手册说明书

技术手册SHT1x (SHT10, SHT11, SHT15)数字温湿度传感器∙ 完全标定 ∙ 数字信号输出 ∙ 低功耗∙ 卓越的长期稳定性∙ SMD 封装 – 适于回流焊接外形尺寸图1 SHT1x 传感器尺寸(1mm=0.039inch),“11”表示该传感器型号为SHT11。
外部接口:1:GND, 2: DATA, 3: SCK, 4: VDD传感器芯片此说明书适用于SHT1x-V4。
SHT1x-V4 是第四代硅传感芯片,除了湿度、温度敏感元件以外,还包括一个放大器,A/D 转换器,OTP 内存和数字接口。
第四代传感器在其顶部印有产品批次号,以字母及数字表示,如“A5Z”,见图1。
材质传感器的核心为CMOS芯片,外围材料顶层采用环氧LCP ,底层为FR4。
传感器符合ROHS 和WEEE 标准,因此不含Pb, Cd, Hg, Cr(6+), PBB, PBDE。
实验包如要进行直接的传感器测量,传感器性能检验或者温湿度实验(数据记录),客户可选用EK-H4,其中包含SHT71(与SHT1x 的芯片相同)传感器,4路传感器通道和与电脑配套的软、硬件。
更多其他传感器实验包信息请登录/humidity产品概述SHT1x (包括 SHT10, SHT11 和 SHT15) 属于Sensirion 温湿度传感器家族中的贴片封装系列。
传感器将传感元件和信号处理电路集成在一块微型电路板上,输出完全标定的数字信号。
传感器采用专利的CMOSens® 技术,确保产品具有极高的可靠性与卓越的长期稳定性。
传感器包括一个 电容性聚合体测湿敏感元件、一个用能隙材料制成的测温元件,并在同一芯片上,与14 位的A/D 转换器以及串行接口电路实现无缝连接。
因此,该产品具有品质卓越、响应迅速、抗干扰能力强、性价比高等优点。
每个传感器芯片都在极为精确的湿度腔室中进行标定,校准系数以程序形式储存在OTP 内存中,用于内部的信号校准。
InSwitch ISE 系列用户手册说明书

InSwitch工业以太网交换机ISE系列用户手册V3.5北京映翰通网络技术股份有限公司InSwitch ISE系列用户手册版权声明copyright © 2013 InHand Networks版权所有不得复制商标InHand及InHand Networks是映翰通网络公司的注册商标,本手册中的所有其他商标或注册商标归相应厂商所有。
免责声明任何未经允许擅自更改手册中的内容与映翰通无关。
本手册可能包含一些由于疏忽造成的技术或排版上的错误。
这样的错误将会被定期修正,并在再版中避免出现这类错误。
InHand保留修正此手册而不通知用户的权利。
如需查询手册的更新情况,请查询本公司网站或直接与本公司业务代表联系。
技术支持联络信息北京映翰通网络技术股份有限公司(总部)地址:北京市朝阳区望京科技园启明国际大厦11层西侧电话:(8610)6439 1099 / 8417 0010 转8005传真:(8610)8417 0089网址:技术支持:******************.cn上海办事处电话:************地址:上海市普陀区顺义路18号1103室广州办事处电话:************地址:广州市天河区棠东东路11号御富科贸园A2座C407室成都办事处电话:************地址:四川省成都市高新区府城大道西段339号,天府新谷6栋13层06~08室武汉办事处电话:************地址:湖北省武汉市洪山区珞瑜东路2号巴黎豪庭11栋2001室Put Internet in your hand!安全使用须知本产品在设计使用范围内安全、可靠,但需要避免人为对其造成损害或破坏。
仔细阅读本手册,并妥善保存以备将来参考。
在使用设备时,请注意以下事项:●不要将设备放置在接近水源或潮湿的地方。
●不要在电源电缆上放任何东西,应将其放在触不到的地方。
●为避免引起火灾,不要将电缆打结或包住。
●电源接头以及其它设备连接件应互相连接牢固,请经常检查。
EXFO 2000 系列以太网测试仪 中文说明书

S P E C S H E ETKEY FEATURES AND BENEFITSAccelerate Ethernet service activation with bidirectional EtherSAM (Y .156) and RFC 2544 test suites, multistream traffi c generation, Through mode and bit-error-rate (BER) testing Experience unprecedented confi guration simplicity with hybrid touchscreen/keypad navigation and data entry Increase technician autonomy and productivity with intelligent discovery of remote EXFO Ethernet testers, as well as in-service testing via dual-port Through mode Eliminate errors in data interpretation with revolutionary new GUI on 7-inch TFT screen, historical event logger, visual gauges and 3D-icon depictions of pass/fail outcomesSimplify reporting with integrated Wi-Fi and Bluetooth connectivity capabilitiesIntegrated applications to test VoIP services, and additional IP test utilities including VLAN scan and LAN discovery via EXpert VoIP and EXpert IP test toolsSupport for packet capture and analysis, wireless troubleshooting and TCP throughput testingExtend fi eld testing operations with compact, lightweight platform equipped with long-duration battery packFTB-860 NetBlazer Series Ethernet TestersPOWERFUL, FAST, INTUITIVE ETHERNET TESTINGeld technicians comprehensive, yet simple test suites to quickly and easily turn up, validate and troubleshoot Ethernet services, with full EtherSAM capabilities, from 10 Mbit/s to 10 Gbit/s.EXFO FTB-1 FTB-860G SpecsProvided by THE ULTRA-PORTABLE CHOICE FOR HIGH-SPEED ETHERNET TESTINGThe ongoing deployment of GigE and 10 GigE circuits across access and metro networks demands a testing solution that seamlessly adapts to either operating environment—without sacrificing portability, speed or cost—in order to guarantee the performance and quality of service (QoS) metrics of these services.Leveraging the powerful, intelligent FTB-1 handheld platform, the NetBlazer series streamlines processes and empowers field technicians to seamlessly transition between 10/100/1000/10000 interfaces to rapidly adapt to a variety of networking environments.Powerful and FastThe NetBlazer series is a portfolio of fully integrated 10 Mbit/s to 10 Gbit/s handheld Ethernet testers. Available in three hardware configurations, each FTB-860x offers the industry’s largest TFT screen with unprecedented configuration simplicity via hybrid touchscreen/keypad navigation. Platform connectivity is abundant via Wi-Fi, Bluetooth, Gigabit Ethernet or USB ports, making it accessible in any environment.FTB-860G: 10 M BIT /S TO 10 G BIT/SIf the need is for full Ethernet coverage from 10 Mbit/s up to 10 Gbit/s, › 10 Base-T to 10 gigabit testing› IPv6 testingFTB-860: GIGABIT ETHERNETIf the need is purely for Gigabit Ethernet coverage, then the FTB-860 is › 10 Base-T to 1 gigabit testing› IPv6 testingFTB-860GL: 10 M BIT/S TO 10 G BIT/S LOOPBACK ONLYCombined with the FTB-860G or FTB-860, the FTB-860GL is the most cost-effective solution for GigE and 10 GigE intelligent loopback testing; it supports bidirectional EtherSAM and RFC 2544 testing and offers five › 10 Base-T to 10 gigabit loopback› EtherSAM (bidirectional partner)*› RFC 2544 (bidirectional partner)› Intelligent autodiscovery› IPv6 testing› Ping/traceroute* Contact your EXFO representative to confirm availability.Setting a New GUI Standard: Unprecedented Simplicity in Configuration Setup and NavigationIntelligent Situational Configuration Setup›G uides technicians through complete, accurate testingprocesses(suggestion prompts, help guides, etc.)›R educes navigation by combining associated testingfunctions on a single screen›I ntelligent autodiscovery allows a single technician to performend-to-end testingDedicated Quick-Action Buttons›Remote discovery to fi nd all the other EXFO units›Laser on/off›T est reset to clear the results and statistics while running a test ›Report generation›Save or load test confi gurations›Quick error injectionAssorted Notifications›Clear indication of link status for single or dual ports›Negotiated speed display for single or dual ports›O ptical power status available at all times for single or dual ports›Pass/fail indication at all times for all testsStreamlined Navigation›R emote discovery button available at all times; no reason to leave your current location to scan for a remote unit›T esting status can be maximized to fi ll the entire screen by simply clicking on the alarm status button; whether the unit is in your hand or across the room, test results can be easily determined with a simple glance at the display screen›R FC 2544 configuration is maximized in a single page;no need to navigate through multiple screens to confiindividual subtests›R FC 2544 results and graphs are also maximized in a single page; no need to navigate through multiple screens to viewindividual RFC subtest results FO unitswhile running a testdual portsal portstimes for single mes; no reason toemote unite entire screen by ; whether the unit sults can be easily splay screenn a single page; eens to confi gure ximized in a single e screens to viewRAPID, ACCURATE TEST RESULTS AT YOUR FINGERTIPSKey FeaturesIntelligent Network Discovery ModeUsing any NetBlazer series test set, you can single-handedly scan the network and connect to any available EXFO datacom remote tester. Simply select the unit to be tested and choose whether you want traffic to be looped back via Smart Loopback or Dual Test Set for simultaneous bidirectional EtherSAM and RFC 2544 results. No more need for an additional technician at the far end to relay critical information—the NetBlazer products take care of it all.Smart Loopback FlexibilityThe Smart Loopback functionality has been enhanced to offer five distinct loopback modes. Whether you are looking to pinpoint loopback traffic from a UDP or TCP layer, or all the way down to a completely promiscuous mode (Transparent Loopback mode), NetBlazer has the flexibility to adjust for all unique loopback situations.Global Pass/Fail AnalysisThe NetBlazer series provides real-time pass/fail status via text or icons. Clicking on the pass/fail indicator maximizes this important status to full screen, providing instant, easily understood notification whether the unit is in the technician’s hands or across the room.Remembering the Last IP or MAC AddressesField technicians have enough things to worry about and don’t always have the luxury of time to enter the same IP or MAC address test after test. The NetBlazer series remembers the last 10 MAC, IPv4 and IPv6 addresses as well as J0/J1 traces for 10G WAN, even afterthe unit has been rebooted.Traffic GenerationUnparalleled analog visual gauges combined with user-defined thresholds show instantaneously whether or not the test traffic is in or out of expected ranges.Additionally, bandwidth and frame size can be modified on-the-fly without navigating away to a different page, giving technicians instantaneous reaction on the gauges. Traffic generation brings together over 10 critical stats in a very visual and organizedfashion, ensuring that technicians can quickly and easily interpret the outcome of the test.The analog gauges are lined with Green and Red layers to represent the expected thresholds.Real-time bandwidth and frame-size adjustment.Overall pass/fail assessment.Throughput, jitter and latency with visual pass/fail thresholds,analog gauges and digitalreadouts.Frame loss and out-of-sequence notification.Multistream ConfigurationConfiguring multiple streams with proper COS and QOS bits can be a complex task. NetBlazer makes it simpler, with all streams easily selectable and configurable from one location. With large icons located throughout the stream pages, configuration becomes as simple as a touch of a finger. Technicians can define one configuration profile and apply it to all the background streams simultaneously. From there, it is just a matter of making slight tweaks as needed rather than complete configuration profiles per stream.Through ModeThrough mode testing consists of passing traffic through either of the NetBlazer’s two 100/1000 Base-X ports or the two 10/100/1000 Base-T ports for in-service troubleshooting of live traffic between the carrier/service provider network and the customer network. Through mode allows technicians to access circuits under test without the need for a splitter.Supporting 10 Gigabit EthernetThe 10 G igabit Ethernet interface is available in both 10 G igE LAN and 10 G igE WAN modes via a single SFP+ transceiver. All Ethernet testing applications—from BER testing to the full EtherSAM suite—are available for both IPv4 and IPv6. Unique to the 10 GigE WAN interface is the ability to send and monitor SONET/SDH J0/J1 traces and the path signal label (C2). The WAN interface can also monitor SONET and SDH alarms and errors.E THER SAM: THE NEW STANDARD IN ETHERNET TESTINGUntil now, RFC 2544 has been the most widely used Ethernet testing methodology. However it was designed for network device testing in the lab, not for service testing in the field. ITU-T Y.156sam is the newly introduced draft standard for turning up and troubleshooting carrier Ethernet services. It has a number of advantages over RFC 2544, including validation of critical SLA criteria such as packet jitter and QoS measurements. This methodology is also significantly faster, therefore saving time and resources while optimizing QoS.EXFO’s EtherSAM test suite—based on the draft ITU-T Y.156sam Ethernet service activation methodology—provides comprehensive field testing for mobile backhaul and commercial services.Contrary to other methodologies, EtherSAM supports new multiservice offerings. It can simulate all types of services that will run on the network and simultaneously qualify all key SLA parameters for each of these services. Moreover, it validates the QoS mechanisms provisioned in the network to prioritize the different service types, resulting in better troubleshooting, more accurate validation and much faster deployment. EtherSAM is comprised of two phases, the network configuration test and the service test.Network Configuration TestThe network configuration test consists of sequentially testing each service. It validates that the service is properly provisioned and that all specific KPIs or SLA parameters are met.Service TestOnce the configuration of each individual service is validated, the service test simultaneously validates the quality of all the services over time.EtherSAM Bidirectional ResultsEXFO’s EtherSAM approach proves even more powerful as it executes the complete ITU-T Y.156sam test with bidirectional measurements. Key SLA parameters are measured independently in each test direction, thus providing 100 % first-time-rightservice activation—the highest level of confidence in service testing.EX PERT TEST TOOLSEXpert Test Tools is a series of platform-based software testing tools that enhance the value of the FTB-1 platform, providing additional testing capabilities without the need for additional modules or units.The EXpert VoIP Test Tools generates a voice-over-IP call directly from the test platform to validateperformance during service turn-up and troubleshooting.›Supports a wide range of signaling protocols, including SIP, SCCP, H.248/Megaco and H.323 ›Supports MOS and R-factor quality metrics› Simplifies testing with configurable pass/fail thresholds and RTP metricsThe EXpert IP Test Tools integrates six commonly used datacom test tools into one platform-based application to ensure field technicians are prepared for a wide-range of testing needs. › Rapidly perform debugging sequences with VLAN scan and LAN discovery› Validate end-to-end ping and traceroute› Verify FTP performance and HTTP availabilityTEST TOOLS IPEXpert TEST TOOLS VoIPOPTICAL INTERFACESTwo ports: 100M and GigEAvailable wavelengths (nm)850, 1310 and 1550100 Base-FX100 Base-LX1000 Base-SX1000 Base-LX1000 Base-ZX1000 Base-BX10-D1000 Base-BX10-USFP+ OPTICAL INTERFACES (10G)10G Base-SR/SW10G Base-LR/LW 10G Base-ER/EW Wavelength (nm)85013101550Tx level (dBm)–5 to –1–8 to 0.5–4.7 to 4.0SPECIFICATIONSELECTRICAL INTERFACESTwo ports: 10/100 Base-T half/full duplex, 1000 Base-T full duplexGENERAL SPECIFICATIONSSize (H x W x D)130 mm x 36 mm x 252 mm (5 1/8 in x 1 7/16 in x 9 15/16 in)Weight (with battery) 0.58 kg (1.3 lb)TemperatureTESTINGEtherSAM (Y.156sam)Network configuration and service test as per ITU-T Y.156sam. Tests can be performed using remote loopback orADDITIONAL FEATURESOptical power measurement Supports optical power measurement at all times; displayed in dBm.UPGRADESFTB-8590SFP modules GigE/FC/2FC at 850 nm, MM, <500 mEXFO is certified ISO 9001 and attests to the quality of these products. This device complies with Part 15 of the FCC Rules. Operation is subject to the following two conditions: (1) this device may not cause harmful interference, and (2) this device must accept any interference received, including interference that may cause undesired operation. EXFO has made every effort to ensure that the information contained in this specification sheet is accurate. However, we accept no responsibility for any errors or omissions, and we reserve the right to modify design, characteristics and products at any time without obligation. Units of measurement in this document conform to SI standards and practices. In addition, all of EXFO’s manufactured products are compliant with the European Union’s WEEE directive. For more information, please visit /recycle. Contact EXFO for prices and availability or to obtain the phone number of your local EXFO distributor. For the most recent version of this spec sheet, please go to the EXFO website at /specs .In case of discrepancy, the Web version takes precedence over any printed literature.EXFO Corporate Headquarters > 400 Godin Avenue, Quebec City (Quebec) G1M 2K2 CANADA | Tel.: +1 418 683-0211 | Fax: +1 418 683-2170 |*************Toll-free: +1 800 663-3936 (USA and Canada) | EXFO America 3701 Plano Parkway, Suite 160Plano, TX 75075 USA Tel.: +1 800 663-3936 Fax: +1 972 836-0164 EXFO Asia 151 Chin Swee Road, #03-29 Manhattan House SINGAPORE 169876Tel.: +65 6333 8241 Fax: +65 6333 8242EXFO China 36 North, 3rd Ring Road East, Dongcheng District Beijing 100013 P. R. CHINATel.: + 86 10 5825 7755 Fax: +86 10 5825 7722Room 1207, Tower C, Global Trade Center EXFO Europe Omega Enterprise Park, Electron Way Chandlers Ford, Hampshire S053 4SE ENGLAND Tel.: +44 2380 246810 Fax: +44 2380 246801EXFO NetHawkElektroniikkatie 2 FI-90590 Oulu, FINLAND Tel.: +358 (0)403 010 300 Fax: +358 (0)8 564 5203EXFO Service Assurance270 Billerica RoadChelmsford, MA 01824 USATel.: +1 978 367-5600Fax: +1 978 367-5700FTB-860 NetBlazer Series Ethernet TestersORDERING INFORMATIONSPFTB860Series.1AN© 2010 EXFO Inc. All rights reserved.Printed in Canada 10/09FTB-860G-XX -XX -XXNotesa. Requires purchase of SFP.b. Requires purchase of SFP+.。
H11NM-R44II NVG兼容灯光系统安装说明说明书

(See continuation Sheet 3 of 3)
Limitations and Conditions:
Installation of NVG compatible interior lighting system does not include or imply approval for flight operations with NVGs. The operator must receive a determination from their civil aviation authority if an approval to operate with NVGs is required. Any subsequent deviation to the cockpit/cabin configuration specified in the type design of this STC may affect the compatibility of the NVIS and will require a re-evaluation for NVIS cockpit and NVG compatibility.
ATMLH412
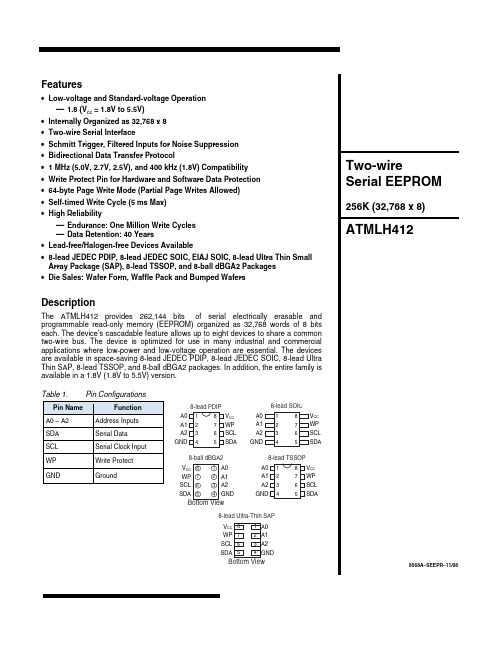
Table 1. Pin Configurations
Pin Name A0 – A2 SDA SCL
Function Address Inputs Serial Data Serial Clock Input
WP
Write Protect
GND
Ground
8-lead PDIP
A0 1 A1 2
8 VCC 7 WP
Absolute Maximum Ratings*
Operating Temperature...........................• 55°C to +125°C Storage Temperature ............................• 65°C to + 150°C Voltage on Any Pin with Respect to Ground................................ • 1.0 V +7.0V Maximum Operating Voltage.....................................6.25V DC Output Current ..................................................5.0 mA
CC
internally pulled down to GND. However, due to capacitive coupling that may appear during customer applications, Atmel recommends always connecting the WP pins to a known state. When using a pull-up resistor, Atmel recommends using 10kΩ or less.
AES 1235 品牌 BNS 产品名称 磁性安全传感器 型号 101170049说明书

DATASHEETDataOrdering dataNote (Delivery capacity)Phased-out product Product type description AES 1235101170049Article number (ordernumber)EAN (European Article4030661297118 Number)27-37-18-19eCl@ss number, version12.027-37-18-19eCl@ss number, version11.027-37-18-19eCl@ss number, version9.0EC001449ETIM number, version7.0EC001449ETIM number, version6.0Available until31.12.2023Approvals - StandardsCertificates BGcULusGeneral dataStandards BG-GS-ET-14BG-GS-ET-20EN IEC 62061EN ISO 13849-1EN IEC 60947-5-1EN IEC 60947-5-3EN IEC 60947-5-5EN IEC 60204-1EN IEC 60947-1Climatic stress EN 60068-2-3BG-GS-ET-14Enclosure material Glass-fibre reinforced thermoplastic, ventilated Gross weight240 gGeneral data - FeaturesStop-Category0Wire breakageYesdetectionCross-circuit detection YesFeedback circuit YesYesAutomatic resetfunctionReset afterYesdisconnection of supplyvoltageEarth connectionYesdetectionYesIntegral systemdiagnostics, statusNumber of LEDs12Number of normallyclosed (NC)1Number of normallyopen (NO)Number of undelayed2semi-conductor outputswith signaling functionNumber of safety2contactsNumber of signalling2outputsSafety classificationStandards EN ISO 13849-1EN IEC 61508Safety classification - Relay outputsdPerformance Level, uptoCategory3PFH value 1.00 x 10⁻⁷ /hNotice for max. 50,000 switching cycles/year and max. 80% contact load2Safety Integrity Level(SIL), suitable forapplications inMission time20 Year(s)Mechanical data20,000,000 OperationsMechanical life,minimumMounting Snaps onto standard DIN rail to EN 60715Mechanical data - Connection techniqueTerminal designations IEC/EN 60947-1Termination rigid or flexibleScrew terminals M20 x 1.5Cable section, minimum0.25 mm²2.5 mm²Cable section,maximumTightening torque of0.6 NmClipsMechanical data - DimensionsWidth22.5 mmHeight100 mmDepth121 mmAmbient conditionsDegree of protection ofIP40the enclosureDegree of protection ofIP54the mounting spaceDegree of protection ofIP20clips or terminalsAmbient temperature+0 ... +55 °CStorage and transport-25 °Ctemperature, minimumStorage and transport+70 °Ctemperature, maximumResistance to vibrations10...55 Hz, Amplitude 0.35 mm, ± 15 % Restistance to shock30 g / 11 msAmbient conditions - Insulation valuesRated impulse4 kVwithstand voltage UimpOvervoltage category IIIDegree of pollution2Electrical dataFrequency range50 Hz60 HzOperating voltage24 VAC -15 % / +10 %24 VDC -10 % / +20 %Ripple voltage10 %Thermal test current 6 ARated operating voltage24 VACRated operating voltage24 VDC20.4 VACRated AC voltage forcontrols, 50 Hz,minimum26.4 VACRated control voltage atAC 50 Hz, maximum20.4 VACRated AC voltage forcontrols, 60 Hz,minimum26.4 VACRated control voltage atAC 60 Hz, maximum20.4 VDCRated AC voltage forcontrols at DC minimumRated control voltage at28.8 VDCDC, maximum5 WElectrical powerconsumption0.1 ΩContact resistance,maximumin new stateNote (Contactresistance)Drop-out delay in case80 msof power failure,typically20 msDrop-out delay in caseof emergency, typically100 msPull-in delay atautomatic start,maximum, typically20 msPull-in delay at RESET,typicallyMaterial of the contacts,Ag-Ni 10 and 0.2 µm gold-plated electricalElectrical data - Safe relay outputsVoltage, Utilisation230 VACcategory AC-156 ACurrent, Utilisationcategory AC-15Voltage, Utilisation24 VDCcategory DC-136 ACurrent, Utilisationcategory DC-13Switching capacity,10 VDCminimum10 mASwitching capacity,minimum250 VACSwitching capacity,maximum8 ASwitching capacity,maximumElectrical data - Digital inputs10 … 30 VDCInput signal, HIGHSignal "1"0 … 2 VDCInput signal, LOW Signal"0"40 ΩConduction resistance,maximumElectrical data - Digital OutputVoltage, Utilisation24 VDCcategory DC-120.1 ACurrent, Utilisationcategory DC-12Electrical data - Relay outputs (auxiliary contacts) Switching capacity,24 VDCmaximumSwitching capacity,2 AmaximumElectrical data - Electromagnetic compatibility (EMC)EMC rating EMC-DirectiveIntegral system diagnosis (ISD)Note (ISD -Faults)The following faults are registered by the safety monitoring modules and indicated by ISD.Faults Failure of the safety relay to pull-in or drop-outFailure of door contacts to open or closeCross-wire or short-circuit monitoring of the switch connectionsInterruption of the switch connectionsFault on the input circuits or the relay control circuits of the safety monitoring moduleOther dataNote (applications)Safety sensorGuard systemNoteNote (General)Inductive loads (e.g. contactors, relays, etc.) are to be suppressed by means of asuitable circuit.Wiring exampleNote (Wiring diagram)The wiring diagram is shown with guard doors closed and in de-energised condition.To secure a guard door up to PL d and Category 3Monitoring 1 guard door(s), each with a magnetic safety sensor of the BNS rangeThe ISD tables (Intergral System Diagnostics) for analysis of the fault indications andtheir causes are shown in the appendix.Expansion of enable delay time: The enable delay time can be increased from 0.1 s to1 s by changing the position of a jumper link connection under the cover of the unit.The feedback circuit monitors the position of the contactors K3 and K4.Start push button: A start push button (NO) can optionally be connected into thefeedback circuit. With the guard door closed, the enabling paths are then not closeduntil the start push button has been operated.If only one external relay or contactor is used to switch the load, the system can beclassified in Control Category 3 to ISO 13849-1, if exclusion of the fault “Failure of theexternal contactor” can be substantiated and is documented, e.g. by using a reliabledown-rated contactor. A second contactor leads to an increase in the level of securityby redundant switching to switch the load off.If neither start button nor feedback circuit are connected, a jumper connection must bemounted between X1 and A1.Modification for 2 NC contacts: The safety monitoring module can be modified tomonitor two NC contacts by bridging the terminals A1 and X2. In this configuration, theshort-circuit detection becomes inoperative.Ordering codeProduct type description:AES 123(1)(1)56without start-up test6with start-up testDocumentsOperating instructions and Declaration of conformityAES 1235 / AES 1236(245.3 kB, 10.05.2019, Revision D)BG-test certificateAES and BNS - BG-GS-ET-14 - AES 1135 / AES 1136 / AES 1145 / AES 1146 / AES 1155 / AES 1156 / AES 1165 / AES 1166 / AES 1175 / AES 1176 / AES 1235 / AES 1236 / AES 1265 / AES 1266 / AES 1185(1.4 MB, 10.05.2019, Revision F)BG-test certificateAES - BG-GS-ET-20 - AES 1135 / AES 1136 / AES 1145 / AES 1146 / AES 1155 / AES 1156 / AES 1165 / AES 1166 / AES 1175 / AES 1176 / AES 1235 / AES 1236 / AES 1265 / AES 1266(738.9 kB, 10.05.2019, Revision D)UL CertificateAES / FWS / BNS / BN(415.3 kB, 01.08.2019)Wiring example (electr. wiring)AES 123x(19.6 kB, 10.05.2019)Wiring example (electr. wiring)AES 123x(19.7 kB, 10.05.2019)InfoAES 1135 / AES 1136 / AES 1165 / AES 1166 / AES 1185 / AES 1235 / AES 1236(34.3 kB, 30.06.2021)SISTEMA-VDMA library(659.5 kB, 23.03.2023)PicturesProduct picture (catalogue individual photo)ID: kaes1f09| 711.0 kB | .jpg | 265.642 x 529.167 mm - 753 x 1500 px - 72 dpi| 84.7 kB | .png | 74.083 x 147.461 mm - 210 x 418 px - 72 dpiWiring exampleID: maes1l11| 34.0 kB | .cdr || 143.8 kB | .jpg | 352.778 x 408.517 mm - 1000 x 1158 px - 72 dpiWiring exampleID: kaes1l41| 34.1 kB | .cdr || 139.5 kB | .jpg | 352.425 x 396.875 mm - 999 x 1125 px - 72 dpiK.A. Schmersal GmbH & Co. KG, Möddinghofe 30, 42279 WuppertalThe details and data referred to have been carefully checked. Images may diverge from original. Further technical data can be found in the manual. Technical amendments and errors possible.Generated on: 27/07/2023, 01:44。
WST3414高频点源负载同步挡罩MOSFET数据手册说明书

Gate Threshold Voltage VGS(th) Temperature Coefficient
IDSS
Drain-Source Leakage Current
IGSS gfs Rg Qg Qgs Qgd Td(on) Tr Td(off) Tf Ciss Coss Crss
Gate-Source Leakage Current Forward Transconductance Gate Resistance Total Gate Charge (4.5V) Gate-Source Charge Gate-Drain Charge Turn-On Delay Time Rise Time Turn-Off Delay Time Fall Time Input Capacitance Output Capacitance Reverse Transfer Capacitance
0.6
0.9
1.2
VSD , Source-to-Drain Voltage (V)
Fig.3 Forward Characteristics Of Reverse
1.8
1.4
1
0.6
0.2
-50
0
50
100
150
TJ ,Junction Temperature (℃ )
Fig.5 Normalized VGS(th) vs. TJ
The WST3414 meet the RoHS and Green Product requirement with full function reliability approved.
Features
z Advanced high cell density Trench technology z Super Low Gate Charge z Excellent Cdv/dt effect decline z Green Device Available
Flex System IB6131 InfiniBand Switch 产品指南说明书

Flex System IB6131 InfiniBand SwitchProduct Guide (withdrawn product)The Flex System IB6131 InfiniBand Switch is designed to offer the performance you need to support clustered databases, parallel processing, transactional services, and high-performance embedded I/O applications, helping to reduce task completion time and lower the cost per operation. The switch supports 40 Gbps QDR InfiniBand and can be upgraded to 56 Gbps FDR InfiniBand.The Flex System IB6131 InfiniBand Switch can be installed in the Flex System chassis, which provides a high bandwidth, low latency fabric for Enterprise Data Centers (EDC), high-performance computing (HPC), and embedded environments. When used in conjunction with IB6132 InfiniBand QDR and FDR dual-port mezzanine I/O cards, these switches will achieve significant performance improvements resulting in reduced completion time and lower cost per operation.Figure 1 shows the switch module.Figure 1. Flex System IB6131 InfiniBand SwitchDid you know?This switch is designed for low latency, high bandwidth, and computing efficiency for performance-driven server and storage clustering applications. The switch supports full bisectional bandwidth, and, when combined with the InfiniBand 56 Gbps FDR adapter, your organization can achieve efficient high-performance computing by providing maximum bandwidth and off-loading from the CPU protocol processing and data movement overhead, such as Remote Direct Memory Access (RDMA) andSend/Receive semantics, allowing more processor power for the application.Flex System, a new category of computing and the next generation of Smarter Computing, offers intelligent workload deployment and management for maximum business agility. This chassis delivers high-speed performance complete with integrated servers, storage, and networking for multiple chassis management in data center compute environments. Furthermore, its flexible design can meet the needs of varying workloads with independently scalable IT resource pools for higher utilization and lower cost per workload. While increased security and resiliency protect vital information and promote maximum uptime, the integrated, easy-to-use management system reduces setup time and complexity, providing a quicker path to a return on investment (ROI).Click here to check for updatesFigure 2. Location of the switch bays in the Flex System Enterprise ChassisFigure 3. Logical layout of the interconnects between I/O adapters and I/O modulesThe Flex System IB6131 InfiniBand Switch can be installed in bays 1, 2, 3, and 4 of the Enterprise Chassis.A supported InfiniBand adapter card must be installed in the corresponding slot of the compute node (slot A1 when modules are installed in bays 1 and 2 or slot A2 when switches are in bays 3 and 4).With compute nodes that have an integrated dual-port 10 GbE network interface controller (NIC), these switches can only be installed in bays 3 and 4, because integrated NIC's ports are routed to bays 1 and 2 with a specialized periscope connector, and the InfiniBand adapter card in slot A1 cannot be installed. However, when needed, the periscope connector can be replaced with an InfiniBand adapter card. In this case, the integrated NIC will be disabled, and the InfiniBand switches can be used in bays 1 and 2.The following table shows the connections between the adapters installed in the compute nodes other than x222 to the switch bays in the chassis.Table 3. Adapter to I/O bay correspondenceI/O adapter slot in the server Port on the adapter Corresponding I/O module bayin the chassisSlot 1Port 1Module bay 1Port 2Module bay 2 Slot 2Port 1Module bay 3Port 2Module bay 4Slot 3(full-wide compute nodes only)Port 1Module bay 1 Port 2Module bay 2Slot 4(full-wide compute nodes only)Port 1Module bay 3 Port 2Module bay 4The following table shows the connections between the adapters installed in the x222 compute nodes to the switch bays in the chassis.Table 4. x222 InfiniBand adapter to I/O bay correspondenceCompute node IB6132D 2-port FDR InfiniBand Corresponding I/O module bay in the chassis Upper compute node Upper Port 1Module bay 4Lower compute nodeLower Port 1Module bay 3The following table lists the InfiniBand I/O adapters that are supported by the IB6131 InfiniBand Switch.Table 5. Supported InfiniBand I/O adapter cardsDescriptionPart numberFeature code (x-config / e-config)Support for IB6131switch Flex System IB6132 2-port FDR InfiniBand Adapter 90Y3454A1QZ / None Yes Flex System IB6132 2-port QDR InfiniBand Adapter NoneNone / 1761Yes Flex System IB6132D 2-port FDR InfiniBand Adapter90Y3486A365 / A365YesThe adapters are installed in slots in each compute node. Figure 4 shows the locations of the slots in thex240 M5 Compute Node. The positions of the adapters in the other supported servers are similar.Figure 4. Location of the I/O adapter slots in the Flex System x240 M5 Compute NodeConnectors and LEDsFigure 5. Front panel of the Flex System IB6131 InfiniBand SwitchPopular configurationsFigure 6 shows the use of the Flex System IB6131 InfiniBand switches to route two InfiniBand FDR ports on the dual-port expansion card installed in slot 2 of the compute node. Each compute node has two InfiniBand ports, and two IB6131 switches are installed in bays 3 and 4 of the Enterprise Chassis. The connections between the adapter card and the modules are internal to the chassis. No cabling is needed.Figure 6. Using IB6131 InfiniBand Switch with dual-port InfiniBand FDR adapter cardsThe following table lists the solution components.Table 6. Components used when connecting the adapter to the InfiniBand switchesDescription QuantityPart number/machinetype1 to 149532-x4x Flex System x240 M5 with EN4172 2-port 10Gb EthernetAdapter90Y3454Flex System IB6132 2-port FDR InfiniBand Adapter 1 per server8721-A1x Flex System Enterprise Chassis195Y3309Flex System Fabric EN4093R 10Gb Scalable Switch290Y3450Flex System IB6131 InfiniBand Switch290Y3462Flex System IB6131 InfiniBand Switch (FDR Upgrade)290Y34703m FDR InfiniBand Cable Up to 18 per IB6131switchRelated publicationsTrademarksLenovo and the Lenovo logo are trademarks or registered trademarks of Lenovo in the United States, other countries, or both. A current list of Lenovo trademarks is available on the Web athttps:///us/en/legal/copytrade/.The following terms are trademarks of Lenovo in the United States, other countries, or both:Lenovo®Flex SystemLenovo ServicesSystem x®Other company, product, or service names may be trademarks or service marks of others.。
leviton-nsi微芯片控制器用户手册说明书

MC 7008MC 7016MC 7024MC 7008 / MC 7016 / MC 7024 MEMORY LIGHTING CONTROLLERSUSER GUIDESoftware Revision 1.00 and aboveDocument Revised: 8-30-02Copyright 1994, 2002Leviton Manufacturing Co., Inc.Table of Contents Introduction (3)Welcome (3)Specifications (3)Installation/Setup (3)Power Supply Requirements (3)Dimmer Equipment Connection (4)Overview (4)Front Panel (4)Rear Panel (5)Operation Guide (6)General (6)Operation Modes (6)Bump Buttons (7)Crossfaders (7)Chases (7)Master (7)Blackout (7)Programming Control Functions (8)General (8)Scene Masters (8)Flash Scenes (8)Chases (9)Optional DMX512 Installation (10)Instructions (10)Troubleshooting (11)INTRODUCTIONWelcomeThank you for your decision to purchase a Leviton-NSI product. The powerful Leviton-NSI Microplex design involves the electrical marriage of microprocessor technology and digitally controlled multiplexing. The result is a control package with the flexibility for a variety of applications.The Leviton-NSI MC 7000 Series Lighting Consoles feature an advanced microprocessor based design containing many benefits found in today’s personal computers. This technology provides for the option of adding programmable Memory Scene Masters and Chase effects to the simplicity of a familiar two-scene console.The Leviton-NSI Microplex technology found in all Leviton-NSI products allows components of your lighting system to be interconnected by way of standard 3-conductor microphone cables or audio snakes. Up to 128 individual control signals may be transmitted to dimmer packs through a single microphone cable and the returned phantom power eliminates the need for AC power cords on Leviton-NSI controllers. This makes the remote placement of the MC 7000 Series Lighting Console easy and convenient. Throughout this manual, specifications are listed for the MC 7008 followed by specifications for the MC 7016 in parenthesis () and MC 7024 in brackets [ ].The Leviton-NSI MC 7000 Series Lighting Console represents our continuing commitment of leading the industry in defining technological advances for stage lighting.SPECIFICATIONSControl Channels:8/16 (16/32) [24/48]Dimmers:16 (32) [48]Scene Masters (memory):8 (16) [24]Chases:2, 32 steps maximum eachMemory:Non-volatile EEPROM(approx. 10 year retention)Dimmer Outputs:Leviton-NSI MicroplexDMX512 (optional)Input Power:12-15 Volts DC, minimum 200mADimensions (HxWxD): 2 3/4” x 10 5/8” x 9”-(2 3/4” x 16 5/8” x 9”)[2 3/4” x 22 5/8” x 9”]Weight (approx.): 3.25 lbs. (5.0 lbs.) [6.75 lbs.]INSTALLATION/SETUPPower Supply RequirementsThe MC 7000 Series Lighting Console requires a source of 12-15 volts DC (at least 200 MA) to operate satisfactorily. When used with Leviton-NSI dimming equipment, power is provided through the Microplex microphone cord connection system when connected to the dimmers.If the console is equipped with the optional DMX512 output and used with DMX512 controlled dimmers or if the microphone cable length exceeds 100 feet, the external power supply jack can be used to apply power to the console. Use the power supply provided with the DMX512 option, or call your dealer for assistance in obtaining a proper supply. Make sure that the plug on any power supply not supplied through Leviton-NSI is configured so that the center connector is positive.Dimmer Equipment ConnectionConnecting the MC 7000 Series Lighting Console to Leviton-NSI dimming equipment is very simple.You need only connect a single 3 conductor audio cable (standard microphone cable equipped with a 3-pin XLR type connector) to either of the jacks marked MICROPLEX on the rear apron of the console. It doesn’t matter which jack is used, two jacks are provided for convenience. Connect the other end of the cable to the Leviton-NSI dimming equipment.If the console is equipped with the DMX512 option, connection to the dimming equipment is provided through the 5-pin XLR type connector located on the rear apron of the console. This connector adheres to the USITT standard on DMX512 and will support up to 32 (16) dimmer channels with one 3-wire cable. Since remote power is not provided on this connector, the power supply included with the DMX512option must be used.OVERVIEWFront Panel1. Channel Levels:These 8 (16) [24] LED’s show the current intensity of each of the console control channels. The LED’s are inactive whenever the console is in the single scene mode.2. Scene X:These 8 (16) [24] slide controls are used to control the intensities of channels 1 -8 (1 - 16) [1 - 32] . The overall intensity of the scene created is controlled with theX Crossfader.3. Scene Y:These 8 (16) [24] slide controls are used to control the intensities of channels 1 -8 (1 - 8) [1 - 24], channels 9 - 16 (17 - 32) [25 - 48], or scenes 1 - 8 (1 - 16) [1 - 24]depending upon the consoles current operating mode. The overall intensity ofthe scene created is controlled with the Y Crossfader.4. Bump Buttons:These 8 (16) [24] buttons are used to bring an individual or group of channels,depending upon console operating mode, to full intensity.5. Program Button:This button is used to program the Scene Masters, the 2 Chases, and the FlashScenes. Programming is active when the Program LED is lit.12345N / CN / C Common DMX Data -DMX Data +Female DMX512XLR Pin ConfigurationMPX Data 213+15 VDC Common Female MicroplexXRL Pin Configuration MPX Data123Common +15 vdcMale Microplex XRL Pin Configuration6. Mode Button:This button sequences the console through the 3 operating modes. The lit LED indicates the current mode.7. Tap Sync:Repeatedly tapping this button establishes the chase rate.8. Chase 1:This button toggles Chase 1 on and off, indicated by the LED.9. Chase 2:This button toggles Chase 2 on and off, indicated by the LED.10. X Crossfader:This slide control is used to proportionally vary the intensity of Scene X.11. Y Crossfader:This slide control is used to proportionally vary the intensity of Scene Y.12. Master:This slide control is used to proportionally vary the overall console intensities to stage except those from the Bump buttons.13. Blackout:This button is used to kill all output to stage except from the Bump buttons. Theconsole is in Blackout whenever the Blackout LED is lit.Rear Panel1. Microplex Outputs:These 2 outputs provide Leviton-NSI ’s microphone dimmer connection via a 3-pin XLR type connector. Either connector may be used (1-Male, 1-Female).2. DMX512:This optional output is used to provide dimmer control information to dimmersusing this protocol. Its 5 pin Female XLR connector conforms to the USITTstandard.3. AUX DC Power:This input jack allows a standard wall transformer rated at 15v DC (at least200 MA) to provide power to the MC 7000 Series Console.PUSH123Male Female Female 12345678123456781921031141251361471581600000001234136121110578,9OPERATION GUIDEGeneralThe MC 7000 Series Lighting Console consists of two manual scenes mastered by two split/dipless crossfaders, a set of bump buttons, two programmable chase effects, a master control and a blackout button. The console is designed to allow tailoring to your needs. Three modes of operation vary the function of the Bump buttons from individual Channel Bumps to Flash Scenes, and Scene Y from channels 1 - 8 (1 - 16) [1 - 24], to channels 9 –16 (17 - 32) [25 - 48], or to Memory Scene Masters. In addition, two Chase Effects allow automated sequencing of lights at varying rates.To give the user channel intensity feedback, channel intensity LED’s are provided above each of the Scene X slide controls. These LED’s show relative intensities from all console functions and are not affected by the Master control or the Blackout button, except single-scene mode.Operation ModesThe MC 7000 Series Lighting Console has three operating modes: the 2 x 8 (2 x 16) [2 x 24] mode, the 8 x 8 (16 x 16) [24 x 24] mode, and the 1 x 16 (1 x 32) [1 x 48] mode. These modes are selected with the Mode button. The lit LED indicates the current mode. In standard 2 x 8 (2 x 16) [2 x 24] mode, Scene Y controls the intensity of channels 1 - 8 (1 - 16) [1 - 24] along with Scene X giving the console two-scene capability between the scenes. In 8 x 8 (16 x 16) [24 x 24] mode, Scene Y becomes a bank of Scene Masters, which can be programmed by the user. Each Scene Master has level control of all channels and operates in a ‘‘pile on’’ fashion giving greatest level precedence. In the 1 x 16 (1 x 32) [1 x 48] mode, Scene Y becomes channels 9 - 16 (17 - 32) [25 - 48], joining with Scene X to give the console twice the control channels on one scene. Also in this mode, the bump buttons no longer control individual channels, but control Flash Scenes, which can be programmed by the user. Each scene can have any combination of channels so that they can be flashed to maximum intensity at any time. Programming either of the Chases while in this mode extends each step to 16 (32) [24] channels.Table 1 — MC 7008 Mode ChartMODE SCENE X SCENE Y BUMPS CHASES CHANNEL LEDS 2 x 8 Mode Channels 1 - 8Channels 1- 8Channels 1- 832 Steps x 8 Chan.Channels 1 - 8 8 x 8 Mode Channels 1 - 8Mem Scenes 1 - 8Channels 1 - 832 Steps x 8 Chan.Channels 1 - 8 1 x 16 Mode Channels 1 - 8Channels 9 - 16Prog for Ch 1 - 1632 Steps x 16 Chan.No FunctionTable 2 — MC 7016 Mode ChartMODE SCENE X SCENE Y BUMPS CHASES CHANNEL LEDS 2 x 16 Mode Channels 1 - 16Channels 1- 16Channels 1- 1632 Steps x 16 Chan.Channels 1 - 16 16 x 16 Mode Channels 1 - 16Mem Scenes 1 - 16Channels 1 - 1632 Steps x 16 Chan.Channels 1 - 16 1 x 32 Mode Channels 1 - 16Channels 17 - 32Prog for Ch 1 - 3232 Steps x 32 Chan.No FunctionTable 3 — MC 7024 Mode ChartMODE SCENE X SCENE Y BUMPS CHASES CHANNEL LEDS 2 x 24 Mode Channels 1 - 24Channels 1- 24Channels 1- 2432 Steps x 24 Chan.Channels 1 - 24 24 x 24 Mode Channels 1 - 24Mem Scenes 1 - 24Channels 1 - 2432 Steps x 24 Chan.Channels 1 - 24 1 x 48 Mode Channels 1 - 24Channels 25 - 48Prog for Ch 1 - 4832 Steps x 48 Chan.No FunctionBump ButtonsAlong the bottom edge of the console are 8 (16) [24] momentary push buttons. These buttons are used to bump each individual channel to full intensity regardless of the Blackout button or the setting of the Master control. When in the 1 x 16 (1 x 32) [1 x 48] mode, each button no longer controls only one channel, but can be programmed to control any combination of channels. This makes each button a Flash Scene. The console is shipped from the factory so that Bump button 1 is programmed for only channel 1, Bump button 2 for channel 2 and so on. This gives the impression that there is no functionality change from mode to mode on the bump buttons.The Bump buttons are also used in programming Flash Scenes and Scene Masters.CrossfadersThe two Manual Crossfaders are always tied to Scene X and Scene Y. These fade controls allow crossfading between Scene X and Scene Y with the X Crossfader controlling Scene X and the Y Crossfader controlling Scene Y. The X Crossfader is at its maximum in the fully up position, while the Y Crossfader is at its maximum in the fully down position. This configuration allows easy dipless crossfading providing both crossfaders are moved together. If the crossfaders are not kept in the same position, split crossfading effects can be accomplished.ChasesTwo Chase effects are provided on the MC 7000 Series Lighting Console. Each can be activated at any time by simply pressing its associated button. A Chase is active whenever the LED above its Chase button is lit. Each Chase has a maximum of 32 steps and each step can have any combination of channels. When programming in the 2 x 8 (2 x 16) [2 x 24] and the 8 x 8 (16 x 16) [24 x 24] modes each step has 8 (16) [24] channels of control, when in the 1 x 16 (1 x 32) [1 x 48] mode each step has 16 (32) [48] channels of control.Once a Chase is programmed, it will remain with the same number of channels it was programmed in, regardless of mode during playback. This can add expanded channel capabilities to the other two modes. For example, a 7016 chase could be programmed in the 1 x 32 mode to control only channels 17 - 32 for special effects, and then the console could be run in the 16 x 16 mode to make memory scenes available, and the Bump buttons could be used to create area and special lighting on channels 1 - 16.The Chase Rate is set by repeatedly tapping the Tap Sync button at the rate desired. The Chases will continue to run at the rate of the last two taps until another set of taps is seen. This allows easy synchronization with music or other timed events.MasterThe Master slide control provides proportional level control over all console functions to stage with the exception of the Bump buttons. For example, whenever the Master slide control is at minimum all stage outputs will be at zero except for any resulting from a Bump button, if the Master is at 50% all stage outputs will be at only 50% of their current console settings except for any resulting from a Bump button and if the Master is at full all stage outputs will follow the console settings.BlackoutThe Blackout button is used to disable all outputs to stage with the exception of those resulting from a Bump button. This provides for quick dousing of stage levels or for creating solo effects when used in conjunction with the Bump buttons. Blackout is active whenever the Blackout LED is lit.PROGRAMMING CONTROL FUNCTIONSGeneralThe functions that can be programmed on the MC 7000 Series Lighting Console are the two Chases, the Scene Masters in the 8 x 8 (16 x 16) [24 x 24] mode and the Flash Scenes in the 1 x 16 (1 x 32) [1 x 48] mode. To initiate programming, first tap the Program button. This will light the Program LED indicating that the program mode is active. Then tap the function button to be programmed. All programming is stored in non-volatile memory, which retains information for at least 10 years, even when power is removed.Scene MastersWhen in the 8 x 8 (16 x 16) [24 x 24] mode, the Scene Masters can be programmed for later recall. First create the desired scene on Scene X. Neither the level of the Master or the X Crossfader or the state of the Blackout function have any effect on the programmed levels from Scene X. Once the scene is satisfactory, enter the program mode by tapping the Program button. Then tap the Bump button under the Scene Y slide control that is to be used as the Scene Master. The Scene Master is now programmed and the Program mode is automatically released. Once programmed, the Scene Master is ready for immediate use. To playback the scene, use the Y fader associated with the bump button used to program that scene master.Flash ScenesSince there are only 8 (16) [24] Bump buttons, channels 9 - 16 (17 - 32) [25 - 48] cannot be accessed for bumping in the 1 x 16 (1 x 32) [1 x 48] mode. For this reason the Bump buttons can be programmed as Flash Scenes to access the upper channels whenever in this mode. Flash Scenes consist of any combination of fully on or fully off channels. Flash Scenes are programmed with both Scene X and Scene Y slide controls. Simply raise those sliders that are desired on to maximum and those desired off to minimum. Next, tap the program button to turn on the Program function. Finally, tap the Bump button to be programmed. Once programmed, the Flash Scene is ready for immediate use.ChasesEach of the two Chase functions can be programmed to include any channel in any step up to a maximum of 32 steps per Chase. To initiate Chase programming, first tap the Program button so that the Program LED is lit. Then tap the Chase button of the Chase to be programmed and the LED under the chase button should start flashing. The console is now ready to program the first step of the chase. Use the Scene X slide controls to indicate which channels should be on or off by either raising them to full or lowering them to minimum. Once set, tap the Program button again to store the step. The console is now ready to program the second step of the chase. Continue programming steps, up to 32, until the chase is complete. Tapping the Blackout button exits the chase programming. Programming will be automatically exited if more than 32 steps are attempted.If the console is in the 1 x 16 (1 x 32) [1 x 48] mode, Scene Y can be used to include the channels controlled by these sliders in the Chase program. Follow the same procedure explained above, but include the Scene Y channels into each step programmed.If the Chase is active when programming is initiated, the Chase will halt during programming and resume with the new programming when completed. If the Chase was not active, it will not be running when programming is complete.OPTIONAL DMX512 INSTALLATIONInstructionsFollowing are the instructions for field installation of the DMX512 option (OPT-07512-01).1. Remove screws from bottomof console and removebottom cover.2. Remove 2 screws and removeDMX512 option cover plate.3. Insert DMX512 connector intoopening and install hardwareprovided.4. Connect cable from DMX512connector to 5-pin connectionas shown.5. Install 3695 IC into 8-pinsocket as shown, be sure toobserve the location of thenotch or dimple. Be sure legsgo in straight and not bent.6. Replace bottom cover of unit.Note: DMX512 will activateautomatically. Microplex andDMX512 are transmittedconcurrently and both may be used at the same time.TROUBLESHOOTINGSymptom Check ListChannel Level LED’s do not respond. 1. Check to see if the 1 x 16 (1 x 32) [1 x 48] modeis selected. Since all channels cannot be viewed,the LED’s are disabled in this mode.Chase functions do not work. 1. Make sure a rate has been established with theTap Sync button. The rate is indicated by theflashing LED located directly above the Tap Syncbutton.Lights on stage do not operate even 1. Check that the Master slide control is not set at though Channel Level LED’s do. its minimum position and the Blackout LED is not ON. Scene X or Scene Y slide controls have 1. Make sure that the X or Y Crossfader is not in its no effect on channel levels. minimum position.Stage lights are ON, but will not respond 1. Make sure the dimmer packs are programmedor respond erratically. correctly. Dimmer packs programmed for channelshigher that 32 (16) will not respond to the controller.2. Check for a bad control cable by replacing it.3. The dimmer pack may be defective.4. If the microphone cable is in excess of 100 feet,heavier gauge (18 ga.) cable or an additionalpower supply located at the console may benecessary because of power loses over the lengthof the cable.Erratic operation when a particular 1. Defective fader.fade is up.Channel comes ON when adjacent 1. Defective fader.fader is up.Page 11PK-93130-00-01-1A LIMITED TWO YEAR WARRANTY AND EXCLUSIONSLeviton warrants to the original consumer purchaser and not for the benefit of anyone else that this product at the time of its sale by Leviton is free of defects in materials and workmanship under normal and proper use for two years from the purchase date. Leviton ’s only obligation is to correct such defects by repair or replacement, at its option, if within such two year period the product is returned prepaid, with proof of purchase date, and a description of the problem to Leviton Manufacturing Co.,Inc., Att: Service Department, 20497 SW Teton Ave., Tualatin, Oregon 97062. All products returned to Leviton-NSI must have factory authorization for return prior to shipping. The purchaser is responsible for completing and mailing to Leviton, within 15 days of purchase, the warranty registration card enclosed with each product.This warranty excludes and there is disclaimed liability for labor for removal of this product or reinstallation. This warranty is void if this product is installed improperly or in an improper environment, overloaded, misused, opened, abused, or altered in any manner, or is not used under normal operating conditions or not in accordance with any labels or instructions. There are no other or implied warranties of any kind,including merchantability and fitness for a particular purpose, but if any implied warranty is required by the applicable jurisdiction, the duration of any such implied warranty, including merchantability and fitness for a particular purpose, is limited to two years. Leviton is not liable for incidental, indirect, special, or consequential damages, including without limitation, damage to, or loss of use of, any equipment,lost sales or profits or delay or failure to perform this warranty obligation. The remedies provided herein are the exclusive remedies under this warranty, whether based on contract, tort or otherwise.For Technical Assistance Call:1-800-864-2502。
Meggitt SA IPC704信号条件器说明说明书
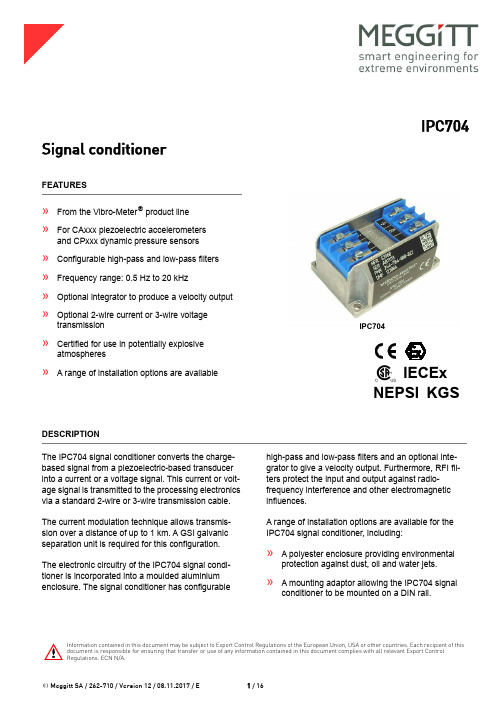
© Meggitt SA / 262-710 / Version 12 / 08.11.2017 / E 1 / 16Information contained in this document may be subject to Export Control Regulations of the European Union, USA or other countries. Each recipient of this document is responsible for ensuring that transfer or use of any information contained in this document complies with all relevant Export ControlRegulations. ECN N/A.IPC704Signal conditionerFEATURES»From the Vibro-Meter ® product line »For CAxxx piezoelectric accelerometers and CPxxx dynamic pressure sensors »Configurable high-pass and low-pass filters »Frequency range: 0.5 Hz to 20 kHz»Optional integrator to produce a velocity output »Optional 2-wire current or 3-wire voltage transmission»Certified for use in potentially explosive atmospheres»A range of installation options are availableIPC704IECEx NEPSI KGSDESCRIPTIONThe IPC704 signal conditioner converts the charge-based signal from a piezoelectric-based transducer into a current or a voltage signal. This current or volt-age signal is transmitted to the processing electronics via a standard 2-wire or 3-wire transmission cable. The current modulation technique allows transmis-sion over a distance of up to 1 km. A GSI galvanic separation unit is required for this configuration.The electronic circuitry of the IPC704 signal condi-tioner is incorporated into a moulded aluminium enclosure. The signal conditioner has configurablehigh-pass and low-pass filters and an optional inte-grator to give a velocity output. Furthermore, RFI fil-ters protect the input and output against radio-frequency interference and other electromagnetic influences.A range of installation options are available for the IPC704 signal conditioner, including:» A polyester enclosure providing environmental protection against dust, oil and water jets.»A mounting adaptor allowing the IPC704 signal conditioner to be mounted on a DIN rail.Signal conditioner IPC7042 / 16© Meggitt SA / 262-710 / Version 12 / 08.11.2017 / EDESCRIPTION (continued)Two versions of the IPC704 signal conditioner are available:»An IPC704 for sensors using standard piezoelectric materials, for example, CAxxx,CP10x and CP2xx(ordering number 244-704-000-042-... ).»An IPC704 for sensors using GaPO4 piezoelectric material, for example, CP50x (ordering number 244-704-000-511-... ).BLOCK DIAGRAM(electrically c onductive)COM O/P +24VSPECIFICATIONSEnvironmental characteristics(Specifications according to IEC 60068-2 recommendations)GeneralTemperature•Operation:−30 to +85 °C•Storage:−40 to +85 °CHumidity:Max. 95 % non-condensing.Note: For operation in a humid environment, ordering option A3 (pottedversion) should be considered.Protection rating(according to IEC 60529):IP40Vibration(according to IEC 60068-2-26):2 g peak between 10 and 500 HzShock acceleration(according to IEC 60068-2-27):15 g peak (half sine, 11 ms duration)Industrial housing (ordering option G1)Protection rating(according to IEC 60529):IP66Impact resistance:> 4mJ/mm2 (DIN 53453)Chemical resistance:Good resistance to seawater, acids, alkaline solutions, gasoline and oils Flammability:UL94V-0 self-extinguishing© Meggitt SA / 262-710 / Version 12 / 08.11.2017 / E3 / 16Signal conditionerIPC704Explosive atmospheresAvailable in Ex approved versions for use in hazardous locationsType of protection Ex i: intrinsic safety (ordering option A2)EuropeEC type examination certificate LCIE 02 ATEX 6085 XII 2G (Zones 1, 2)Ex ib IIC T6 … T4 GbNorth AmericaC CSAUS certificate C CSA US 1243981Class I, Division 1, Groups A, B, C, DEx ia (T6 to T4)International IECEx certificate of conformity IECEx LCI 06.0009XEx ib IIC T6 … T4 GbChina NEPSI certificate of conformity*GYJ12.1450XEx ib IIC T6 to T4 GbKoreaKGS certificate of conformity 12-GA4BO-0396XEx ib IIC T6 to T4Type of protection Ex nA: non-sparking (ordering option A3)EuropeVoluntary type examination certificate LCIE 09 ATEX 1027 XII 3G (Zone 2)Ex nA IIC T6 … T5 GcNorth AmericaC CSA US certificate C CSA US 1243981Class I, Division 2, Groups A, B, C, D Ex nA IIC T6 to T5 Gc Class I, Zone 2AEx nA IIC T6 to T5 GcInternationalIECEx certificate of conformity IECEx LCIE 13.0053XEx nA IIC T6 … T5 Gc* N ot engraved on the product marking.For specific parameters of the mode of protection concerned and special conditions for safe use, refer to the certificates that are available from Meggitt SA on demand.When using protection mode ‘nA’ (non-sparking apparatus), the user shall ensure that the signalconditioner is installed in an enclosure that ensures a protection rating of at least IP54 (or equivalent).For the most recent information on the Ex certifications that are applicable to this product, refer to the Ex product register (PL-1511) document that is available from Meggitt SA.Industrial housing (ordering option G1)Available in Ex approved versions for use in hazardous locations•Environment:II 2 G (Zones 1, 2) Ex e II < 109Ω (DIN 53482)•Surface resistivity for Ex version:Stuffing glandsAvailable in Ex approved versions for use in hazardous locations•Environment:II 2 G/D (Zones 1, 2) Ex e II For specific parameters of the mode of protection concerned and special conditions for safe use,refer to the certificates that are available from Meggitt SA on demand.For the most recent information on the Ex certifications that are applicable to this product, refer to the Ex product register (PL-1511) document that is available from Meggitt SA.SPECIFICATIONS (continued)Signal conditioner IPC7044 / 16© Meggitt SA / 262-710 / Version 12 / 08.11.2017 / EPower supply to IPC704Voltage :18 to 30 V DC Current:25 mA (max.)Transfer characteristics (ordering option B)IPC704 for sensors using standard piezoelectric materials (244-704-000-042-... )•Transfer without integrator:0.1 to 10 mV/pC or 0.1 to 10 µA/pC •Transfer with integrator:981 to 98 100 mV/(pC.s) or 981 to 98 100 µA/(pC.s)IPC704 for sensors using GaPO 4 piezoelectric material (244-704-000-511-... )•Transfer:0.1 to 50 mV/pC or 0.1 to 50 µA/pC Linearity error:≤ 0.2 %Temperature stability :100 ppm / °C typicalPhase:180° between the input signal and the acceleration output.180° between the input signal and the pressure output. 90° between the acceleration and velocity outputs.See the graph below.Input characteristics (ordering option C)Compatible sensors:Any piezoelectric-based transducer – symmetrical or non-symmetrical, case grounded or insulated Dynamic range:100 000 pC peak Input sensitivity•Accelerometers:See IPC704 for accelerometers (acceleration output) using standard piezoelectric materials on page 6 andIPC704 for accelerometers (velocity output) using standard piezoelectric materials on page 6•Dynamic pressure transducers:See IPC704 for pressure sensors using standard piezoelectric materials on page 7 andIPC704 for pressure sensors using GaPO4 piezoelectric material on page 8Charge amplifier:Symmetrical RFI filter:Symmetrical LC network Resistance:≥ 50 k Ω (sensor and cable)Capacitance:≤ 10 nF (sensor and cable)SPECIFICATIONS(continued)Input signalAcceleration and pressureVelocity At© Meggitt SA / 262-710 / Version 12 / 08.11.2017 / E 5 / 16Signal conditionerIPC704Output characteristics (ordering option D)RFI filter:Symmetrical LC network 2-wire current transmission•Dynamic signal:Max. ± 5 mA peak •Standing current :12 mA ± 0.5 mA•Electrical connection:+24 V = “+”, COM = “−”•Output sensitivity:See Ordering information on page 12•Max. dynamic range:5 mA peak / o utput sensitivity 3-wire voltage transmission•Dynamic signal :Max. ± 5 V peak •Standing voltage :7.5 V ± 0.2 V•Output sensitivity:See Ordering information on page 12•Output impedance:750 Ω (3-wire configuration)•Max. dynamic range :5 V peak / o utput sensitivityThe 3-wire voltage output without galvanic separation unit should only be used with piezoelectric-basedtransducers which are insensitive to frame voltage.Dynamic pressure transducers should always be used with a GSI galvanic separation unit .Filter characteristics (ordering options E and F)High-pass filter•Cutoff frequencies (at −3 dB):0.5, 1, 2, 5 or 10 Hz (all ± 20 %)•Slope:24 dB/octave (4th order)When selecting a high-pass filter, be careful to select an appropriate frequency for the charge amplifier. See the charge amplifier frequencies versus transfer unit graphs on the following pages.Low-pass filter•Cutoff frequencies (at −1 dB):200, 500, 1 000, 2 000, 5 000, 10 000 or 20 000 Hz (all ± 10 %)•Slope:12 dB/octave (2nd order)SPECIFICATIONS(continued)Signal conditioner IPC7046 / 16© Meggitt SA / 262-710 / Version 12 / 08.11.2017 / ECharge amplifier frequencies versus transfer unitIPC704 for accelerometers (acceleration output) using standard piezoelectric materialsIPC704 for accelerometers (velocity output) using standard piezoelectric materialsSPECIFICATIONS (continued)Output sensitivity (mV/ g or µA / g )T r a n s d u c e r s e n s i t i v i t y (p C / g )1001NotesFor operation in different regions of the chart, the cutoff frequency of the IPC704’s charge amplifier dictates the required high-pass filter settings. (See the HP FILTER (E) option in ordering information.)Region 1: Cutoff frequency is 0.5 Hz → HP filter ≥0.5 Hz.Region 2: Cutoff frequency is 1 Hz → HP filter ≥1Hz.Region 3: Cutoff frequency is 2 Hz → HP filter ≥2Hz.Region 4: Cutoff frequency is 3 Hz → HP filter ≥5Hz.200100502010521502010Ordering number 244-704-000-042-... with ordering options B01 and B02T r a n s d u c e r s e n s i t i v i t y (p C / g )1001502010Output sensitivity (mV/ m m/s or µA / m m/s)1005020105210.5Output sensitivity (mV/ i ps or µA / i ps)2540127050825412750.825.412.7Ordering number 244-704-000-042-... with ordering options B03, B04, B05 and B06NotesFor operation in different regions of the chart, the cutoff frequency of the IPC704’s charge amplifier dictates the required high-pass filter settings. (See the HP FILTER (E) option in ordering information.)Region 1: Cutoff frequency is 0.5 Hz → HP filter ≥0.5 Hz.Region 2: Cutoff frequency is 1 Hz → HP filter ≥1Hz.Region 3: Cutoff frequency is 2 Hz → HP filter ≥2Hz.Region 4: Cutoff frequency is 3 Hz → HP filter ≥5Hz.© Meggitt SA / 262-710 / Version 12 / 08.11.2017 / E 7 / 16Signal conditionerIPC704IPC704 for pressure sensors using standard piezoelectric materialsSPECIFICATIONS (continued)Output sensitivity (mV/ m bar or µA / m bar)T r a n s d u c e r s e n s i t i v i t y (p C /b a r )95010750250190Output sensitivity (mV/ p si or µA / p si)25T r a n s d u c e r s e n s i t i v i t y (p C / p s i )NotesFor operation in different regions of the chart, the cutoff frequency of the IPC704’s charge amplifier dictates the required high-pass filter settings. (See the HP FILTER (E) option in ordering information.)Region 1: Cutoff frequency is 0.5 Hz → HP filter ≥0.5 Hz.Region 2: Cutoff frequency is 1 Hz → HP filter ≥1Hz.Region 3: Cutoff frequency is 2 Hz → HP filter ≥2Hz.Region 4: Cutoff frequency is 3 Hz → HP filter ≥5Hz.Ordering number 244-704-000-042-... with ordering options B07, B08, B09 and B10Signal conditioner IPC7048 / 16© Meggitt SA / 262-710 / Version 12 / 08.11.2017 / EIPC704 for pressure sensors using GaPO 4 piezoelectric materialSPECIFICATIONS (continued)Output sensitivity (mV/ m bar or µA / m bar)T r a n s d u c e r s e n s i t i v i t y (p C / p s i )T r a n s d u c e r s e n s i t i v i t y (p C / b a r )Output sensitivity (mV/ p si or µA / p si)NotesFor operation in different regions of the chart, the cutoff frequency of the IPC704’s charge amplifier dictates the required high-pass filter settings. (See the HP FILTER (E) option in ordering information.)Region 1: Cutoff frequency is 0.5 Hz → HP filter ≥0.5 Hz.Region 2: Cutoff frequency is 1 Hz → HP filter ≥1Hz.Ordering number 244-704-000-511-... with ordering options B07, B08, B09 and B10Signal conditionerIPC704Physical characteristicsSignal conditioner without industrial housing (ordering option G0)•Enclosure:Injection moulded aluminium, anodized•Mounting:Two or four M4 screws•Weight:Standard version: 170 gEx version: 250 g (the signal conditioner is moulded into silicon)•Dimensions:See Mechanical drawings on page 10•Electrical connection (input):Three screw terminals – wire section 2.5 mm2 (max.)•Electrical connection (output):Three screw terminals – wire section 2.5 mm2 (max.)Signal conditioner with industrial housing (ordering option G1)•Enclosure:Polyester reinforced with glass fibre•Cover seal:Silicone gasket•Mounting:M6 x 30 mm Allen screws•Dimensions:See Mechanical drawings on page 10Input/output stuffing glands (ordering options H and I)•Type:See Ordering information on page 12•Material:Nickel-plated brass with Viton® sealSignal conditioner with MA130 mounting adaptor (ordering option G2)Universal DIN rail holder type:TSH 35DIN rail type(according to EN 50022 / IEC 60715):TH 35-7.5 or TH 35-15SPECIFICATIONS (continued)© Meggitt SA / 262-710 / Version 12 / 08.11.2017 / E9 / 16Signal conditioner IPC70410 / 16© Meggitt SA / 262-710 / Version 12 / 08.11.2017 / EMECHANICAL DRAWINGSSignal conditionerIPC704MECHANICAL DRAWINGS (continued)Signal conditioner IPC704ORDERING INFORMATIONIPC704 signal conditioner for sensors using standard piezoelectric materials Ordering number: 244 - 704 - 000 - 042ENVIRONMENT (A)Standard 1Explosive Ex i 2Explosive Ex nA3TRANSFER UNIT (B)INPUT OUTPUT pC/g µA/g 01pC/g mV/g 02pC/g µA /m m/s 03pC/g mV/ m m/s 04pC/g µA /i n/s 05pC/g mV/ i n/s 06pC/bar µA/mbar 07pC/bar mV/mbar 08pC/psi µA/psi 09pC/psimV/psi10OUTPUT CABLE FITTING (I)No cable fitting (no hole)0M16 x 1.5 with plug1Cable gland M16 x 1.5 for cable Ø4 - Ø7 mm 3Cable gland M16 x 1.5 for cable Ø7 - Ø11 mm 4Adaptor M16 x 1.5 / PG9 with plug 8Adaptor M16 x 1.5 / M20 x 1.5 with plug10B A D E F G H IC INPUT SENSITIVITY (C)Sensor sensitivityOUTPUT SENSITIVITY (D)Value per mechanical unitLP FILTER (F)Value in HzHP FILTER (E)Value in HzINPUT CABLE FITTING (H)No cable fitting (no hole)0M16 x 1.5 with plug1Cable gland M16 x 1.5 for cable Ø4 - Ø7 mm 3Cable gland M16 x 1.5 for cable Ø7 - Ø11 mm 4Adaptor M16 x 1.5 / PG9 with plug 8Adaptor M16 x 1.5 / M20 x 1.5 with plug10INSTALLATION (G)Signal conditioner only0Signal conditioner with industrial housing 1Signal conditioner assembled on MA130 mounting adaptor2Low-pass filter200 Hz 500 Hz 1 000 Hz 2 000 Hz 5 000 Hz 10 000 Hz 20 000 HzHigh-pass filter0.5 Hz 1 Hz 2 Hz 5 Hz 10 Hz(2)(2)(1)Notes1. With options A3 and G0 / G 2, the user shall ensure that the signal conditioner is installed in an enclosure that ensures a protection rating of at least IP54 (or equivalent).2. With option H0, only option I0 is available.Signal conditionerIPC704IPC704 signal conditioner for sensors using GaPO 4 piezoelectric material ORDERING INFORMATION (continued)Ordering number: 244 - 704 - 000 - 511ENVIRONMENT (A)Standard 1Explosive Ex i 2Explosive Ex nA3TRANSFER UNIT (B)INPUT OUTPUT pC/bar µA/mbar 07pC/bar mV/mbar 08pC/psi µA/psi 09pC/psimV/psi10OUTPUT CABLE FITTING (I)No cable fitting (no hole)0M16 x 1.5 with plug1Cable gland M16 x 1.5 for cable Ø4 - Ø7 mm 3Cable gland M16 x 1.5 for cable Ø7 - Ø11 mm 4Adaptor M16 x 1.5 / PG9 with plug 8Adaptor M16 x 1.5 / M20 x 1.5 with plug10B A D E F G H IC INPUT SENSITIVITY (C)Sensor sensitivityOUTPUT SENSITIVITY (D)Value per mechanical unitLP FILTER (F)Value in HzHP FILTER (E)Value in HzINPUT CABLE FITTING (H)No cable fitting (no hole)0M16 x 1.5 with plug1Cable gland M16 x 1.5 for cable Ø4 - Ø7 mm 3Cable gland M16 x 1.5 for cable Ø7 - Ø11 mm 4Adaptor M16 x 1.5 / PG9 with plug 8Adaptor M16 x 1.5 / M20 x 1.5 with plug10INSTALLATION (G)Signal conditioner only0Signal conditioner with industrial housing 1Signal conditioner assembled on MA130 mounting adaptor2Low-pass filter200 Hz 500 Hz 1 000 Hz 2 000 Hz 5 000 Hz 10 000 Hz 20 000 HzHigh-pass filter0.5 Hz 1 Hz 2 Hz 5 Hz 10 Hz(2)(2)(1)Notes1. With options A3 and G0 / G 2, the user shall ensure that the signal conditioner is installed in an enclosure that ensures a protection rating of at least IP54 (or equivalent).2. With option H0, only option I0 is available.Signal conditioner IPC704MOUNTING ACCESSORIESABA160 industrial housingNotes1. Suitable for potentially explosive atmospheres only when used with Ex i certified products from Meggitt Sensing Systems’ Vibro-Meter p roduct line. A ll machining on the industrial housing must comply with the operational manual of the housing manufacturer.2. With option B00, only option C00 is available.Ordering number: 830 - 160 - 000 - 111ENVIRONMENT (A)Standard polyester 1Explosive Ex i2CABLE FITTING INPUT (B)No cable fitting (no hole)00M16 x 1.5 with plug01Cable gland M16 x 1.5 for cable Ø4 - Ø7 mm 03Cable gland M16 x 1.5 for cable Ø7 - Ø11 mm 04Adaptor M16 x 1.5 / PG9 with plug 08Adaptor M16 x 1.5 / M20 x 1.5 with plug (cable Ø12 mm max.)10CABLE FITTING OUTPUT (C)No cable fitting (no hole)00M16 x 1.5 with plug01Cable gland M16 x 1.5 for cable Ø4 - Ø7 mm 03Cable gland M16 x 1.5 for cable Ø7 - Ø11 mm 04Adaptor M16 x 1.5 / PG9 with plug 08Adaptor M16 x 1.5 / M20 x 1.5 with plug (cable Ø12 mm max.)10A B1C1(2)(2)(1)Signal conditionerIPC704MA130 mounting adaptorOrdering number: 809-130-000-011Base plate for IPC704 signal conditionerThis aluminium base plate can be used when an old IPC620 unit is replaced by an IPC704 signal conditioner. The housing of the IPC620 can be reused and the IPC704 mounted on it.Ordering number: 244-620-002S034MOUNTING ACCESSORIES (continued)Note: All dimensions in mm unless otherwise stated.R 49123054~ R 2~ R 24.53970139Ø5, 5H 114.527454.5130148Note: All dimensions in mm unless otherwise stated.Signal conditionerIPC704Headquartered in the UK, Meggitt PLC is a global engineering group specializing in extreme environment components and smart sub-systems for aerospace, defence and energy markets.Meggitt Sensing Systems is the operating division of Meggitt specializing in sensing and monitoring systems, which has operated through its antecedents since 1927 under the names of ECET, Endevco, Ferroperm Piezoceramics, Lodge Ignition, Sensorex and Vibro-Meter. Today, these operations are integrated under one strategic business unit called Meggitt Sensing Systems, headquartered in Switzerland and providing complete systems, using these renowned brands, from a single supply base.The Meggitt Sensing Systems facility in Fribourg, Switzerland was formerly known as Vibro-Meter SA, but is now Meggitt SA. This site produces a wide range of vibration and dynamic pressure sensors capable of operation in extreme environments, leading-edge microwave sensors, electronics monitoring systems and innovative software for aerospace and land-based turbo-machinery.All statements, technical information, drawings, performance rates and descriptions in this document, whilst stated in good faith, are issued for the sole purpose of giving an approximate indication of the products described in them, and are not binding on Meggitt SA (Meggitt Sensing Systems) unless expressly agreed in writing. Before acquiring this product, you must evaluate it and determine if it is suitable for your intended application. You should also check our website at /energy for any updates to data sheets, Ex certificates, product drawings, user manuals, service bulletins and/or other instructions affecting the product. Unless otherwise expressly agreed in writing with Meggitt SA, you assume all risks and liability associated with use of the product. Any recommendations and advice given without charge, whilst given in good faith, are not binding on Meggitt SA.Meggitt SA (Meggitt Sensing Systems) takes no responsibility for any statements related to the product which are not contained in a current Meggitt Sensing Systems publication, nor for any statements contained in extracts, summaries, translations or any other documents not authored and produced by Meggitt SA. Meggitt SA reserves the right to alter any part of this publication without prior notice.In this publication, a dot (.) is used as the decimal separator and thousands are separated by thin spaces. Example: 12 345.678 90.Sales offices Your local agent Head officeMeggitt Sensing Systems has offices in more than 30 countries. For a complete list, please visit our website.Meggitt SARoute de Moncor 4PO Box 16161701 FribourgSwitzerlandTel: +41 26 407 11 11Fax: +41 26 407 13 01*****************.com /energyISO 9001FS 584089。
E+H四线制变送器CM14

优势 • 一体式结构设计,采用盘装型外壳 ( 外形尺寸: 48 x 96 mm) • 操作简便 • Memosens 技术 - 使用预标定传感器 - 高安全性,自动电缆断裂检测 • 两个限位触点 • 温度作为第二电流输出
TI494C/28/zh/01.11
Liquiline CM14
功能与系统设计
10
Endress+Hauser
Liquiline CM14
附件
测量电缆 Memosens 数字电缆 CYK10 • 适用于 Memosens 数字式传感器 • 订购信息请参考 《技术资料》 TI376C pH 玻璃电极 Orbisint CPS11D • Memosens pH 数字式电极,用于过程测量 • 抗污型 PTFE 隔膜 • 订购信息请参考 《技术资料》 TI028C Orbipore CPS91D • Memosens pH 数字式电极 • 带开放式腔室,用于重度污染介质的测量 • 订购信息请参考 《技术资料》 TI375C Orbipac CPF81D • 一体式 pH 电极,浸入式安装在过程水和污水中测量 • 订购信息请参考 《技术资料》 TI191C ORP 电极 Orbisint CPS12D • Memosens ORP 数字式电极 • 抗污型 PTFE 隔膜 • 订购信息请参考 《技术资料》 TI367C Orbipore CPS92D • Memosens ORP 数字式电极 • 带开放式腔室,用于重度污染介质的测量 • 订购信息请参考 《技术资料》 TI435C Orbipac CPF82D • 一体式 ORP 电极,浸入式安装在过程水和污水中测量 • 订购信息请参考 《技术资料》 TI191C 电导式电导率传感器 Condumax W CLS15D • 用于纯水和超纯水测量,可在防爆 (Ex) 场合中使用 • 订购信息请参考 《技术资料》 TI109C Condumax H CLS16D • 卫生型传感器,用于纯水和超纯水测量,可在防爆 (Ex) 场合中使用 • EHEDG 测试和 3A 认证 • 订购信息请参考 《技术资料》 TI227C Condumax W CLS21D • 双电极传感器,带整体电缆和接头连接 • 订购信息请参考 《技术资料》 TI085C 电感式电导率传感器 Indumax CLS50D • 高稳定性电感式电导率传感器,可在标准场合、防爆 (Ex) 场合和高温应用场合中使用 • Memosens 数字式传感器 • 订购信息请参考 《技术资料》 TI182C 溶解氧传感器 Oxymax COS51D • 覆膜法 Memosens 数字式溶解氧传感器 • 订购信息请参考 《技术资料》 TI413C Oxymax H COS22D • Memosens 溶解氧传感器,可消毒 • 订购信息请参考 《技术资料》 TI446C
nextivityinc CEL-FI GO G41 快速入门指南说明书
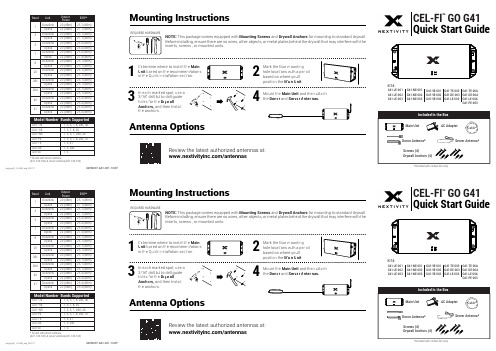
KIT#:KIT#:CEL-FI ™GO G41Quick Start GuideMounting InstructionsDetermine where to install the Main Mark the four mounting31In each marked spot, use a 3/16” drill bit to drill guide holes for the Drywall Anchors,the anchors.24NOTE: This package comes equipped with Mounting Screws and Drywall Anchors for mounting to standard drywall. Before installing, ensure there are no wires, other objects, or metal plates behind the drywall that may interfere with the inserts, screws , or mounted units.Antenna Optionsqsg-go-g41_1-3-5-28L_eng_23-0717Review the latest authorized antennas at: /antennasG41-JE-001G41-JE-002G41-JE-003G41-NE-001G41-NE-002G41-NE-003420N007-G41-001-10-RF*Included with certain kits only.(A21-100-100) & server antenna(A51-100-100)G41-9E-001G41-9E-002G41-9E-003G41-TE-003G41-DE-003G41-LE-003G41-TE-00A G41-DE-00A G41-LE-00AG41-PE-003CEL-FI ™ GO G41Quick Start GuideMounting InstructionsUnit based on the recommendations in the Quick Installation section.hole locations with a pencilposition the 3124REQUIRED HARDWARENOTE: This package comes equipped with Mounting Screws and Drywall Anchors for mounting to standard drywall. Before installing, ensure there are no wires, other objects, or metal plates behind the drywall that may interfere with theinserts, screws , or mounted units.Antenna Optionsqsg-go-g41_1-3-5-28L_eng_23-0717Mount the Main Unit and then attach the Donor and Server Antennas.Review the latest authorized antennas at: /antennasG41-JE-001G41-JE-002G41-JE-003G41-NE-001G41-NE-002G41-NE-003420N007-G41-001-10-RF(A21-100-100) & server antenna(A51-100-100)G41-9E-001G41-9E-002G41-9E-003G41-TE-003G41-DE-003G41-LE-003G41-TE-00A G41-DE-00A G41-LE-00AG41-PE-003IMPORTANT: Your CEL-FI GO G41 is electronic equipment. The CEL-FI GO G41 must be kept indoors and in a dry, cool, well ventilated area.Attach the Donor Antenna and Server Antenna to the Main Unit . Make sure to mount the Server Antenna horizontally.Use your phone to find where coverage is needed. This is where the Server Antenna should be installed on a wall.Place the main unit your ISP modem LAN port or external LTE modem to manage via web interface Wave Portal.Select Sever Antenna LocationQuick InstallationFor best results, separate the Donor and Server Antenna(s) as much as possible. Antenna separation (isolation) can be achieved with either physical distance or walls and floors between the antennas.Make sure any cables, splitters, and antennas used in the system are properly matched. (CEL-FI GO G41 is rated for 50 Ω)Recommended:• > 20 dB port-to-port isolation for any splitter Downlink power should be:• > 0 dBm to use a two-way splitter • > 3 dBm to use a four-way splitterAdvanced InstallationCopyright © 2023 by Nextivity, Inc., U.S. Patents pending. All rights reserved. The Nextivity and CEL-FI logos are registered trademarks of Nextivity, Inc. All other trademarks or registered trademarks listed belong to their respective owners. Designed by Nextivity, Inc. in California.1Ideally it should be placed with at least one wall between the donor and server antennas. If the patch antenna cable is too short, it may be extended.Select Main Unit Location2Server PortDonor PortThe Donor Antenna should be separated/isolated as far away as possible from the Server Antenna , with greater separation providing best performance.Splitting Server Antenna Plug in the Main Unit to power with the included AC adapter. The LED on the front will blink during set up and turn green when the device is ready. After powering on the device, connect the Power Cable Clamp .Donor AntennaDonor AntennaIMPORTANT: Your CEL-FI GO G41 is electronic equipment. The CEL-FI GO G41 must be kept indoors and in a dry, cool, well ventilated area.Attach the Donor Antenna and Server Antenna to the Main Unit . Make sure to mount the Server Antenna horizontally.your ISP modem LAN port or external LTE modem to manage via web interface Wave Portal.Quick InstallationFor best results, separate the Donor and Server Antenna(s) as much as possible. Antenna separation (isolation) can be achieved with either physical distance or walls and floors between the antennas.Make sure any cables, splitters, and antennas used in the system are properly matched. (CEL-FI GO G41 is rated for 50 Ω)Recommended:• > 20 dB port-to-port isolation for any splitter Downlink power should be:• > 0 dBm to use a two-way splitter • > 3 dBm to use a four-way splitterAdvanced InstallationCopyright © 2023 by Nextivity, Inc., U.S. Patents pending. All rights reserved. The Nextivity and CEL-FI logos are registered trademarks of Nextivity, Inc. All other trademarks or registered trademarks listed belong to their respective owners. Designed by Nextivity, Inc. in California.Ideally it should be placed with at least one wall between the donor and server antennas. If the patch antenna cable is too short, it may be extended.Server PortDonor PortThe Donor Antenna should be separated/isolated as far away as possible from the Server Antenna , with greater separation providing best performance.Splitting Server Antenna Plug in the Main Unit to power with the included AC adapter. The LED on the front will blink during set up and turn green when the device is ready. After powering on the device, connect the Power Cable Clamp .Donor AntennaDonor AntennaScan to Download: The WAVE App is available for smart-phones and tablets.Scan to Download: The WAVE App is available for smart-phones and tablets.。
莱斯阿电子设备有限公司-莱斯阿MHT410在线单氯DGA和湿度监测器说明书

environmental conditions, and as such, they could not proceed with the monitoring program.
“We asked Vaisala to demonstrate the quality of their online monitoring solution in practice by installing an MHT410 transmitter in our 60 MVA transformer at SEWA substation” Shankar Narayanan, Engineer, Testing & Commissioning at SEWA, explained. “The MHT410 was easy to install, and demonstrated true reliability in tough conditions. We are extremely pleased with the results after this live trial period and plan to expand the utilization of MHT410 in our substations.”
CUSTOMER CASE
The Vaisala MHT410 Proves Itself to SEWA in the Arabian Desert and Wins an Award in the Process
Sharjah Electricity and Water Authority is looking to move towards a condition-based system of maintenance for their transformer fleet. Issues with harsh local conditions have been an issue.