Paint_Troubleshooting_Guide
Java Troubleshooting Guide for HP-UX

trouble-shootingguide故障排除指南
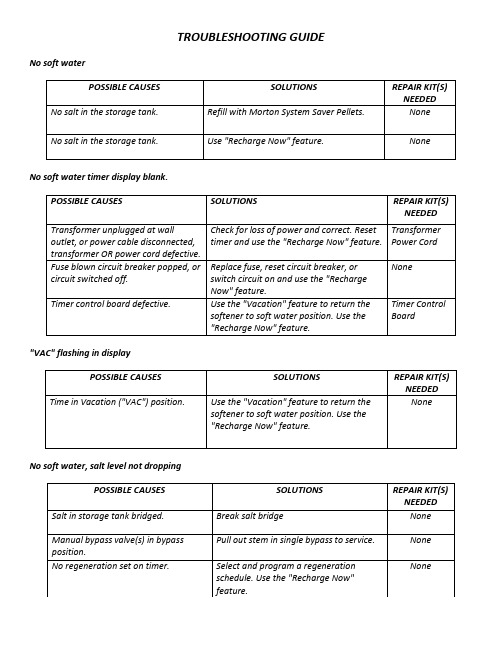
TROUBLESHOOTING GUIDE No soft waterNo soft water timer display blank."VAC" flashing in displayNo soft water, salt level not droppingNo soft water∙Salt storage tank full of water∙Water running to drain while unit in soft water cycle.Water is hard sometimesResin in household plumbing, resin tank leaking.Salt storage tank leakingMotor stalled or clicking.Error code E1, E2, E3 or E4 appears.Below is given annual work summary, do not need friends can download after editor deleted Welcome to visit againXXXX annual work summaryDear every leader, colleagues:Look back end of XXXX, XXXX years of work, have the joy of success in your work, have a collaboration with colleagues, working hard, also have disappointed when encountered difficulties and setbacks. Imperceptible in tense and orderly to be over a year, a year, under the loving care and guidance of the leadership of the company, under the support and help of colleagues, through their own efforts, various aspects have made certain progress, better to complete the job. For better work, sum up experience and lessons, will now work a brief summary.To continuously strengthen learning, improve their comprehensive quality. With good comprehensive quality is the precondition of completes the labor of duty and conditions. A year always put learning in the important position, trying to improve their comprehensive quality. Continuous learning professional skills, learn from surrounding colleagues with rich work experience, equip themselves with knowledge, the expanded aspect of knowledge, efforts to improve their comprehensive quality.The second Do best, strictly perform their responsibilities. Set up the company, to maximize the customer to the satisfaction of the company's products, do a good job in technical services and product promotion to the company. And collected on the properties of the products of the company, in order to make improvement in time, make the products better meet the using demand of the scene.Three to learn to be good at communication, coordinating assistance. On‐site technical service personnel should not only have strong professional technology, should also have good communication ability, a lot of a product due to improper operation to appear problem, but often not customers reflect the quality of no, so this time we need to find out the crux, and customer communication, standardized operation, to avoid customer's mistrust of the products and even the damage of the company's image. Some experiences in the past work, mentality is very important in the work, work to have passion, keep the smile of sunshine, can close the distance between people, easy to communicate with the customer. Do better in the daily work to communicate with customers and achieve customer satisfaction, excellent technical service every time, on behalf of the customer on our products much a understanding and trust.Fourth, we need to continue to learn professional knowledge, do practical grasp skilled operation. Over the past year, through continuous learning and fumble, studied the gas generation, collection and methods, gradually familiar with and master the company introduced the working principle, operation method of gas machine. With the help of the department leaders and colleagues, familiar with and master the launch of the division principle, debugging method of the control system, and to wuhan Chen Guchong garbage power plant of gas machine control system transformation, learn to debug, accumulated some experience. All in all, over the past year, did some work, have also made some achievements, but the results can only represent the past, there are some problems to work, can't meet the higher requirements. In the future work, I must develop the oneself advantage, lack of correct, foster strengths and circumvent weaknesses, for greater achievements. Looking forward to XXXX years of work, I'll be more efforts, constant progress in their jobs, make greater achievements. Every year I have progress, the growth of believe will get greater returns, I will my biggest contribution to the development of the company, believe in yourself do better next year!I wish you all work study progress in the year to come.Procedure for removing error code from faceplate:∙Unplug transformer∙Correct defect∙Plug in transformer.∙Wait for 6 minutes.The error code will return if the defect was not corrected. Press and hold the VAC/RCHG button for 3 seconds as an alternative way to clear an error code.Error code E5 appearsProcedure for removing error code from faceplate:∙Unplug transformer∙Correct defect∙Plug in transformer.∙Wait for 6 minutes.The error code will return if the defect was not corrected. Press and hold the VAC/RCHG button for 3 seconds as an alternative way to clear an error code.Brine tank full of water, No soft water or Not using salt.Solution: Disassemble and clean the nozzle and venturi:Clean all parts using a soft tooth brush, mild soap and warm water. Use resin bed cleaner if parts are iron coated. Rinse with clean fresh water. Do not use any sharp or hard objects to clean bottom of item #6. Remove parts 1-7, 9 and 10. Set parts aside and clean. Reinstall cap (#1) and o-ring (#2).Lift the brine valve assembly (#13) from the brinewell. Remove the plastic clip (#12) and pull the asembly apart. Use the SELECT or TOUCH HOLD button to enter the unit into a manual regeneration and advance the valve to the fill position.As the valve advances into FILL, there will be a flow of water from the tubing. Use this to wash down the brine valve assembly of any excess salt. Also wash down the brine well of excess salt. Move the bypass valve into BYPASS to shut off the flow of water to the valve. Use the toothbrush to thoroughly clean the nozzle and venturi (#6), flow plugs (#5 and #9) and screens (#4, #10 and #11). Carefully clean the flow plug center hole with a small wire.Reassemble all parts in the nozzle venturi. BE SURE #& is installed correctly, numbers up on the flow plugs (#5 and #9). Advance the valve into the BRINE position. Place the bypass valve into service and check for suction on the tubing that connects to the brine valve assembly. If not, recheck the assembly of the nozzle venturi. If suction is now working, reinstall the brine valve assembly and finish the regeneration.VALVE NOT WORKING∙Water running to drain∙Brine tank overflowing∙Motor stalled∙Water leaking from valveSolution: Before you start to service a valve, make sure it is in the service position. Place bypass valve in bypass to shut off water. Loosen 3 of 5 hex screws at top back of valve. This will relieve pressure in the softener.If water is running to drain in service, if brine tank is overflowing, or the motor is not turning the valve (valve stuck):1.Remove the 5 hex screws from the top of the valve and carefully remove the cover. Replace theseal kit parts #9 through #12. Be sure wear strip (#9) is placed on top of rubber seal (#10).Inspect the rotor for wear, scratches or cracks, and replace if needed. Check all o-rings for wear,cuts, flat spots, proper positioning, etc., and replace as needed. Install the valve cover and 5screws. Turn the water on and check to see if failure is corrected.If water is leaking from the top of the valve, or between #3 and #14, replace o-rings 4, 5 and 8. Turn water on and check again for leaks.If the brine tank is overfilling, with little or no water flow from the valve drain hose during regeneration, check flow plug #1, drain elbow #2, and the valve drain hose for obstruction.。
凯镭思互调仪操作手册(中英文)
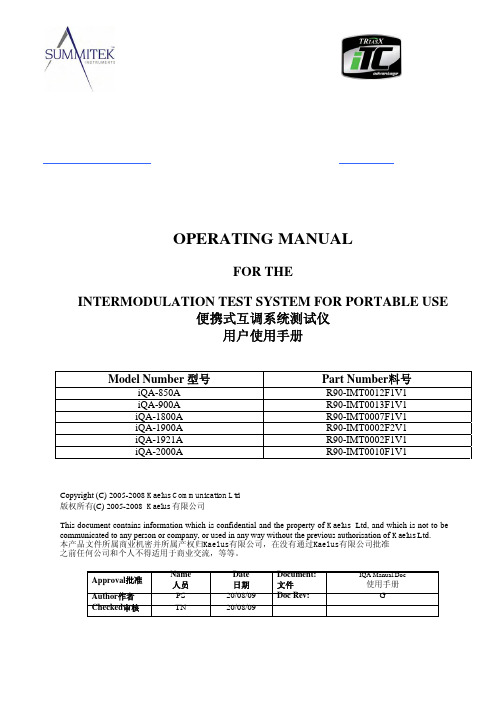
F
升级标题页添加Summitek/Triasx 商标和联系方式
22/06/09
(IR7317)
Updates. New state editor GUI. (IR7402)
G
升级,新版本的测试设置文件编辑器用户界面
(IR7402)
17/08/09
Authorisation 批准
PDS PDS PDS TN
B
removed.
17/04/08
升级1.3.2和1.3.5 删除USB窗口
Changes to section 1.5 by adding report number to the state
C
editor GUI.
16/05/08
升级1.5在测试设置文件编辑器中添加报告编号
Changes to AC specifications in section 1.2 and section
WA R N I N G- RF HAZARD 警告—射频危害
This equipment is designed for use in association with radio frequency (RF) radiating systems and is capable of producing up to 50W of RF power in the 800 to 2200 MHz region. Users are reminded that proper precautions must be taken to minimise exposure to these RF fields to the recommended limits. Please pay particular care to the following areas: 此设备设计用于无线电射频(RF)发射系统,能够在800至2200兆赫的射频区域内 产生高达50瓦的射频功率(RF)。用户应注意,必须采取适当的预防措施,尽量 减少暴露在射频区域里,保持在建议的范围内。请特别注意以下几个方面:
阿尔科尔热量传感器故障排查指南说明书

ALCOR EGT SYSTEMTROUBLESHOOTING GUIDEPlease Note: This troubleshooting guide does not include symptoms or solutions relating to malfunctioning engines, cylinders, or other mechanical components.NOTES1.The best way to troubleshoot ALCOR EGT probes is to check the loop resistance through the probeat room temperature. Use a good quality multi-meter fitted with alligator clips on the test leads.CAUTION: Voltage from a multi-meter can damage an EGT indicator. Care should be taken to be sure the probe has been disconnected from the system before checking for loop resistance.A grounded red/yellow or red/brown probe will normally show from 0.6 to 1.0 ohms resistance. To check millivolt output, remove probe from aircraft. Carefully heat the tip of the probe element with a propane torch until it just begins to glow dark cherry red. At this point, the probe should put out from 33 to 36 millivolts (1500︒F to 1650︒F) for red/yellow, or 61 to 67 millivolts (1500︒ to 1650︒F) for red/brown. CAUTION: Always wear gloves and have a fire extinguisher handy when using an open flame.2.To check continuity of an EGT extension lead, first inspect entire length of wire for chafing orbroken insulation. Inspect terminals for loose crimps or connections. With indicator and probe disconnected, check to be sure that there is no continuity from red to yellow or from red or yellow to thermocouple housing. Next, clip red to yellow at either end and check for continuity at opposite end through the entire lead.3.Modern EGT systems use a type K or chromel/alumel thermocouple. Older EGT systems usedchromel/constantan or type E thermocouple. Type K has a red/yellow color code. Type E has a red/brown color code. CAUTION: EGT systems with mixed color codes will not functionproperly. Call ALCOR, Inc. for details.4.Calibration on ALCOR, Inc. EGT or CHT indicators manufactured after 1980 are from the front.These indicators can usually be overhauled by ALCOR at a reasonable cost. NOTE: ALCOR does not authorize outside repair or overhaul of our indicators. Older indicators manufactured before 1980 have the calibration adjustment from the rear. They are not repairable due to unavailability of parts. Please call ALCOR for replacement information.5.To recalibrate ALCOR EGT indicators in flight, climb to 3,000 feet or higher and set up 65% poweraccording to your aircraft flight manual. Lean the mixture carefully until a slight RPM drop orengine roughness is observed, then re-enrichen slightly. Adjust the calibration potentiometer so that the indicator points to the asterisk or a point 100 degrees below the top of the scale. CAUTION: TIT indicators or EGT indicators with a true temperature read-out dial instead of plain hash marks cannot be calibrated in flight. Use an ALCOR ALCAL system tester or send indicator to ALCOR for calibration at no charge.6.To prevent indicator error due to induced EMF, the EGT or CHT extension lead wires must not bebundled up or routed with any high current bearing wires such as alternator, avionics, lighting or heaters.**Note: ALCOR does not authorize outside repair or overhaul of our indicators.**。
ProCu Troubleshooting Guide

IConn ProCu High Performance Wire Bonder98888-00CU-002-008.5Troubleshooting Guide8.5.1GeneralThis section contains a table of problems and solutions recommended. The prob-lems listed are component-related during bonder operation (e.g. EFO wand is damaged, etc.).8.5.2Troubleshooting Guide for ProCu Bonder HardwareWARNING: INJURY HAZARD. INCORRECT MAINTENANCE COULD CAUSEINJURY. DO NOT DO MAINTENANCE UNLESS YOU HAVE COM-PLETED THE APPROVED MAINTENANCE TRAINING COURSE. READ THE DATA IN THE SAFETY CHAPTER.Problem SolutionLow gas pressure (nitrogen or form-ing gas)1.The gas pressure on the ProCu pneumatic assem-bly must be set to 25 psi to 28 psi to make sure that sufficient gas is supplied to the ProCu flow-head assembly.•Do a check on the pressure gauge indication of the ProCu pneumatic assembly.•Adjust the knob on the pressure regulator if necessary.2.Do a check of the air filter element that is attached to the pressure regulator. Clean or replace if nec-essary. Refer to Section 8.4.6 for procedures.3.Do a check of pneumatic hoses connections. If necessary, replace the pneumatic hoses.Interference between the ProCu Flowhead assembly and the clamp up position1.Make sure that the clamp insert thickness is set to 165 mils. Refer to Section 8.3.2.for procedures.2.Do a check of the setup position of the ProCu flow-head assemby. Refer to Section 8.3.2. for proce-dures.3.Make sure that the EFO height offset is 30 mils. Refer to Section 8.3.4.4.Make sure that the EFO height is between 210 mils to 225 mils. If not, do the EFO height calibra-tion. Refer to Section 8.3.4 for procedures.Flowhead assembly cover is damaged1.Replace the ProCu complete flowhead assembly if the cover is damaged. Refer to 8.4.4 for proce-dures.EFO wand touches the capillary1.The EFO wand must not touch the capillary shaft. If necessary, use the X and Y adjustment screws to adjust the EFO wand position on the ProCu flowhead assembly. Refer to Section 8.3.2 for pro-cedure.2.Make sure that the EFO wand is not bent or dam-aged. Replace the EFO wand if necessary. Refer to Sectioin 8.4.2 for procedures.Maintenance ManualProCu Bonder EFO wand is damaged or bent1.EFO Wand must be replaced if it is bent or dam-aged. Refer to Sectioin 8.4.2 for procedures.2.Make sure that the EFO wand do not touch the capillary shaft.Incorrect flow rate operation on the flow monitor 1.The digital flow monitors must be set to show 0 l/min to 3 l/min.•Do a check of flow rate on the flowmeter moni-tor setup. If necessary, set the flow rate to0 l/min to 3 l/min. Refer to Section 8.3.3 Set Up Digital Flow Monitor , step B. for procedures.2.Do the gas supply check on the ProCu pneumatic assembly. Make sure that the gas pressure is set to 25 psi to 28 psi.3.Do a check of the flow sensor assembly. If neces-sary, replace the flow sensor assembly. Refer to Section 8.4.7 for procedures.No forming or nitrogen gas1.Do a check of the connection to factory supply. Make sure that the flow rate readings on the pres-sure gauge indication and flow monitors are cor-rect for process.2. Do a check of pneumatic hoses connections. If necessary, replace the pneumatic hoses.Flow sensor assembly defective1.Do a check of the flow sensor cable connections to the flow monitor.2.Do a check of pneumatic hoses connections. If necessary, replace the pneumatic hoses.3.Do a check of the flow sensor assembly. If neces-sary, replace the flow sensor assembly. Refer to Section 8.4.7 for procedures.Software system stops operation when the clamp insert is at the close position during copper wire bonding.1.Push the emergency off switch and the power stop switch.2.After 5 minutes, push the green button to set the machine to ON.Servo error/fault occurs when the clamp insert is at the close position during copper wire bonding.1.Push the power stop switch.2.After 5 minutes, push the green button to set the machine to ON.Problem SolutionIConn ProCu High Performance Wire Bonder98888-00CU-002-008.5.3Troubleshooting Guide for Dynamic Brake SystemWARNING: ELECTRICAL SHOCK HAZARD. DO NOT TOUCH LIVE DYNAMICBRAKE SYSTEM ELECTRICAL COMPONENTS AS THIS CAUSEELECTRIC SHOCK OR BURNS. MAKE SURE THAT THE BONDER IS PROPERLY SHUT DOWN BEFORE YOU DO THE SERVICING. PUSH [MOTOR STOP] BUTTON, THEN PUSH THE RED BUTTON TO SET THE MACHINE TO OFF. DISCONNECT THE BONDER FROM THE FACILITY POWER.Problem SolutionClamp Not Out of Home1.Do a check of the software version. Make sure that the sorftware version is 8-88-4-43A or later.2.Do a check of the cable connections. Refer to Sec-tion 8.1.3.3.Go to the console window on the GUI screen.a.Enter “sln_set_status(23,0,0,0)”.b.Enter “sln_set status(23,1,0,0)”.c.If necessary, start the machine again.Clamp drift to home position after emergency stop button is pushed.1.Do a check of the Bond Head position.2.Do a check of the settings for device parameters. Make sure that the bondplane offset and clamp force offset is set to 0. Refer to IConn ProCuOperation Manual, chapter 12 ProCu Specific Fea-tures for more data.Clamp jump to extended open posi-tion after emergency stop button is pushed.1.Do a check of the cable connections. Refer to Sec-tion 8.1.3.2.If necssary, replace the cable.3.If problem continues, speak to the Kulicke & Soffa technical support personnel.。
iN-Command Troubleshooting Guide

TROUBLESHOOTING GUIDEThis guide is made to ease troubleshooting the iN-Command system. It will cover the wiring code and where those wires are connected to the Body Control Module (BCM) and Display Commander (DC), system functions, and what to look for to discern where a problem could be.Display Commander (DC)Body Control Module (BCM)Table of contents.........................................Page 1Keystone wiring code..................................Page 2Body Control Module wiring diagram.........Page 3, 4BCM Pin Values...........................................Page 5 - 7Device Pairing Functionality Testing...........Page 8 - 12Troubleshooting..........................................Page 13Keystone 12 VDC Wire StandardHydraulic Wiring Guide for the BCM BCM Pins 1-31 are on the Left side, ascending from Top to Bottom BCM Pins 32-49 are on the Bottom and ascend from Left to Right BCM Pins 50-80 on the Right side, ascending from Bottom to TopElectric Wiring Guide for the BCM BCM Pins 1-31 are on the Left side, ascending from Top to Bottom BCM Pins 32-49 are on the Bottom and ascend from Left to Right BCM Pins 50-80 on the Right side, ascending from Bottom to TopBCM Pin ValuesiN-Command Pairing and Functionality TestThe BCM should be wired correctly, without loose connections, and connected to 12 VDC at pin 80.A RED LED will indicate that the BCM is receiving 12 VDC. A BLUE LED will indicate that Bluetooth communication is working. (Note: BLUE LED will not be lit until the DC is turned "on" & connected to the BCM)The 3 toggle switches on the BCM correspond to the 3 dials underneath them. (In the event where communication between the DC and BCM is non-functioning, these switches will enable "manual" functions of the selected devices) The Left switch and knob are used for Electric Slides 1-5. The Middle switch and knob are used for Front and Rear Electric Jacks (Hydraulic Jacks are manually controlled at the Hydraulic Pump. See the Hydraulic Pump Manual Override in the RV owner's manual), and the Right switch and knob are used for Awnings 1 and 2.The DC will be mounted in a "all access" area near the entrance. On the DC, hold down the Power button (the left button) for 5 seconds. After a moment, the Passcode Screen will appear. Enter your Passcode . If this is the first time the DC has been powered on, an End User License Agreement (EULA)screen will appear. Upon accepting the EULA, a Enter New Passcode screen will appear. Enter your new passcode twice.The DC will now Pair with the BCM and bring up the Home Screen If the Floor Plan has been loaded, All the devices should be listed with corresponding actitation buttonsStarting with the Lights, cycle ON/OFF, IN/OUT each device. All the functions should be smooth and instantaneous. Ensure all the Home Screen Main Buttons actuate/turn on the corresponding devices. When turning on the Water Pump, open the Kitchen Faucet and listen for the pump to turn on. The Water Pump is pressure controlled and will cycle based on demand. During this time the Water Pump button will stay highlighted. Cycle the Generator. When the Generator is being cycled for the first time (or if it has been a while since it has been used), it will need to be primed. Hold the Prime button down to 2 -5 seconds (it will never "over prime") then hold the Start button down until the generator starts.The Start Button should turn Red and display Stop. Hold the Stop Button to stop the Generator.If the DC is working correctly, a Handheld Device can now be added.On the Home Page, scroll down the list of actuations (swiping UP on the left side of the screen) to the Select the Bluetooth button.The Pairing Screen will appear:On the iOS Device, go to Settings and turn on Bluetooth. The iOS device will automatically begin broadcasting a signal and it will show up in the Unpaired Devices list. Select the device. On both the iOS device and the DC, a Pairing Request screen will appear. Accept the paring request. The BCM will now be listed in the iOS Device's Bluetooth menu (i.e.: JENSENDC05E1F7). Select the BCM on the iOS device, it will show "Connected" on the device's Bluetooth list, and the iOS device will show up in the DC's Paired Devices list. Now open the iN-Command App on the device. It will pair and show the Home screen.Display CommanderiOS (Apple) DeviceThe Android Devices pair a little differently:When the Pairing Screen is open on the DC, ensure that Bluetooth is functioning on the Android device, and open the iN-Command App. Select the Menu button the Android App and then the Bluetooth button. On the DC press Discover and on the Android device press Scan. The BCM (i.e.: JENSENDC05E1F7) will show in the Android's Unpaired list. Select the BCM. A Pairing Request will show on the DC and the Android device, accept both. The BCM will now appear in the Android's Paired List with yellow font (indicating that it is Actively paired with the BCM. There can be more than 1 BCM paired to a Android OR iOS device). Select the Home button, the DC Pairing screen will appear, then the App will show the Home screen.Android DeviceThe iOS and Android device Apps need to have the correct floorplan downloaded from the BCM to display the Trailer's functions. On either device (iOS or Android) go to the Settings screen and select the Reset button. The Reset Menu will appear. Select Floorplan. The functions will populate on the App's Menu screen. Press the Home button. Tanks and Generator functions will be listed (if a generator is in the floorplan). Press the Function List button. The Functions will be listed with an activation button next to them. The iOS or Android Device is now ready for use.The iN-Command system can only be paired to 7 devices 4 Android and 3 iOS)and only 4 of them can be active (3 Androids and 1 iOS). "Active" meaning they can activate functions and receive data. Apple programming dictates that only 1 iOS device can be actively paired. To use another iOS device that is paired to the iN-Command system, simply push the iOS App's Power button and shut the App down. This will disconnect the device from the BCM without having to go to the iOS device's Bluetooth list and disconnecting it. The new iOS device will need to have the BCM selected in it's Bluetooth settings before opening the App.3 Android devices are able to be used at one time. If a user wishes to use the 4th paired Android device, simply use the Power button on the device's App. The Android device will disconnect to allow the other device to be active.To verify that the Handheld device is connected to the DC, select the Interior Lights button. All the Interior Lights should cycle with each button press and the corresponding buttons on the handheld device and DC should cycle from OFF to ON and vice versa.Using the handheld device, cycle through all the functions previously tested on the DC. Ensure the DC display correlates with the handheld device's. While testing the handheld device, push buttons on the DC. Lights should function while using a Motor Function (slide, awning, etc.). Other Motor Functions should NOT be able to actuate while a Motor Function is in use. A System Busy message should appear.Using the DC, cycle through all the functions and ensure the corresponding buttons on the handheld device mirror the DC's as well.Disconnect Shore Power and start the Generator. Retest the DC and handheld device. If the RV/Trailer has a 12VDC battery installed, Turn off the generator and retest the DC and handheld device. Motor Functions will stop at 10.7 VDC. Lights will cease functioning at 10 VDC and the DC will shut down.When connecting multiple handheld devices, connection should be smooth, no other devices should be kicked off, actuation of systems on one device should correspond to the buttons on other devices, and only the non-motorized functions should be able to be actuated by any device while motorized functions are being actuated on one device.TroubleshootingTroubleshooting The iN-Command system is pretty painless. The BCM and DC simulate all the lights, gauges, and switches on the old control panels. The BCM Pin Vales portion of this guide will clear most issues. Basically, if the BCM does not have the desired voltage, or signal, input, it will not be able to function or read tanks. Also, if the BCM has the correct output voltage or signal , but nothing is functioning, the problem lies elsewhere.Any issues that are related to iN-Command that cannot be cleared using the above list will be tied to the BCM and DC hardware and software. Careful inspection of the BCM will need to be done (possibly blowing the BCM board with air to remove any dust and debris or conductive material). If the BCM looks clean and undamaged (no burnt or cracked components) with all the wires secure and not touching each other, troubleshooting the program is needed.Contact an ASA representative 1-877-845-8750。
大华6017793门禁控制器用户手册说明书
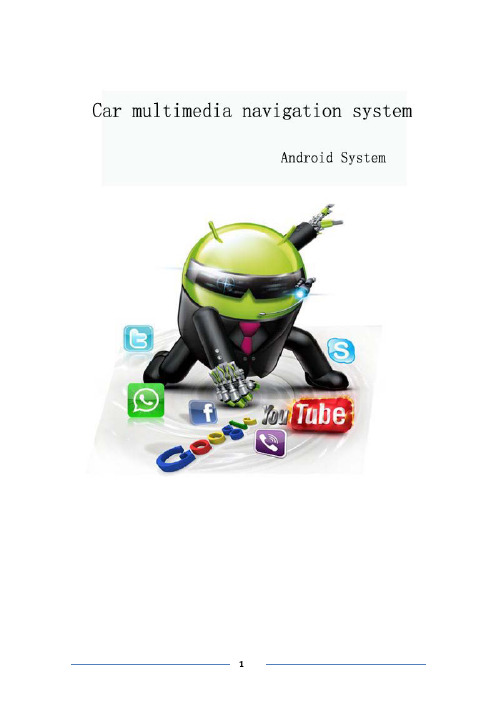
table of Contents1、matters needing attention (3)2、Basic operation (4)2.1、System reset (4)2.2、Start/off host (4)2.3、volume adjusting (4)2.4、Power Key (4)2.5、Backing camera (4)3、Main interface operation (5)4、Bluetooth (6)4.1、Bluetooth main interface (6)4.2、Bluetooth–dial (6)4.3、Outgoing state diagram (7)4.4、Call state diagram (7)4.5、Phone book and phone records (8)4.6、Bluetooth-Music (8)5、Vehicle setup (9)5.1、General settings (9)5.2、Factory settings (10)5.3、Touch learning (10)5.4、Sound settings (10)5.5、Navigation set (11)5.6、Square set (11)6、radio reception (12)7、Multimedia music (13)8、Multimedia video: (14)9、File management operation (14)10、Common troubleshooting wizard (15)1、matters needing attentionFor your safety,please try not to while driving to watch video and operate the machine.When you're driving the volume knob can clearly hear the sound of the outside world.Product change iterations,the system will be updated step by step.The contents of this manual are for reference only,please refer to the actual product.1.1First pay attention to traffic safety.1.2Please park your car in a safe place if you have difficulty in operating the system.1.3Do not allow children to operate the machine,in order to avoid damage to the adult or machine.1.4Please follow the traffic rules when using the satellite navigation system.1.5Please do not prohibit the use of electronic equipment or the use of open flame,such as:gas stations,wineries,strong electromagnetic interference areas,or may cause danger.1.6Do not self maintenance,maintenance,installation of the machine.In the power supply is switched on do not install or repair the machine,because of no electronic equipment or vehicle accessories installation training or lack of experienced personnel to install and repair the machine is very dangerous.1.7Don't put the machine storage or installed in direct sunlight.Don't make placed and other harmful substances into the environment,especially LCD screen.If installed,LCD screen just in air conditioning ventilation Road in the vicinity,please ensure cool or hot air not blowing directly on the machine,otherwise it might damage the machine,even the car or bodily harm.2、Basic operation2.1、System resetCaused by the improper operation of the crashes and other non normal phenomenon, please use the tip of the short by a panel reset hole,the machine can be restored to normal.(Note:due to the reset button panel on a small,please press this button),using the pen or similar pointed object point2.2、Start/off hostIn the ACC switch in the open position,according to the host panel"power"button to turn on the power,insert the CD into the trough dish,machine will automatically open, open access to read disk mode;when the phone is switched on,long press"power" button switch for host panel,or flameout pull bus key will shut closed the power of this machine.2.3、volume adjustingRotate the volume knob on the console panel(some models have the volume control keys on the panel"VOL+/VOL-"button),which can adjust the volume of the machine.2.4、Power KeyPress the Power key on the panel to mute the system,press again or adjust the volume to restore the sound.2.5、Backing cameraThe vehicle go into reverse,regardless of the machines in the boot or shutdown state, the display will immediately switch to reverse the camera screen.3、Main interface operationIn the main interface,a different function icon into the corresponding interface,the function of the detailed operating instructions.Please see the back.About touch sliding page can switch between multiple pages,as shown below:Click the icon to access the third-party application menu as follows,Long press the icon to drag to move the icon position4、Bluetooth4.1、Bluetooth main interfaceAs shown below:Search around the open Bluetooth device.Select the device that exists around the click on the link to wait for the match or match Will automatically link.Disconnect the connected device.Settings:mainly for the Bluetooth device function selection,automatic connection,auto answer,Bluetooth name modification and Bluetooth PIN code modification.4.2、Bluetooth–dialBluetooth connection is successful,the user can dial directly,through the touch screen number keys,as shown below:4.3、Outgoing state diagramAfter the Bluetooth connection is successful,you can enter the number by phonebook,dialing,and manually pressing the number keys on your keyboard use Dial outthe phoneThe voice of the other party's call is output from the machine(in-car speaker).Click this icon to switch the voice of the other party to the output of the paired mobile phone.The voice of the other party's call is output from the paired mobile phone.Click this icon to switch the voice of the other party to the output of the machine(in-car speaker).The microphone on the machine is turned on.During the call,the other party can hear the content of the user on the machine and the two parties talk normally.Click this icon to turn off the microphone on the machine.The microphone on the machine is off.During the call,the other party cannot hear the content of the user on the machine.Click this icon to turn on the microphone on the machine.Dial the call or hang up during the call to end the callIn the call interface,you can hide or display the dial pad4.4、Call state diagramBluetooth connection status,there will be incoming calls call interface as follows:Answer the call and enter the call state.4.5、Phone book and phone recordsBluetooth connection,can enter the phone book and phone records,as follows:number in the phone book.to dial the number to contact each other.Used to synchronize the phone book in this connected phoneHas been dialed out of the number recordList of numbers that have been answeredList of unanswered numbers4.6、Bluetooth-MusicBluetooth media media connection is successful,if the phone supports Bluetoothmusic player,the audio will be transmitted to the Bluetooth device,as shown below:You can control the phone through the three buttons to control the music on a song,pause playback and the next song function5、Vehicle setupSet the main settings,navigation settings,network settings,sound settings,time settings,brightness settings,language and input method, steering wheel settings,factory settings and on the car,as shown below:5.1、General settingsGeneral settings include brake warning,reverse volume switch,button tone,reverse mirror,default system volume,default call volume,home page style,as shown below:Brake Warning:Controls whether or not a traffic warning switch pops up when playing a video file.Reverse volume switch:control the volume when the reversing switch.Touch tone:Whether the control system has a tone switch when it touches.Reversing Mirror:Controls whether the camera is turned on.GPS mix:Switch function options,navigation work with music-video-Bluetooth music-mix outputGPS Mixing Ratio:Controls the mixing ratio of GPS.Default system volume:Controls the system volume size by default.Default call volume:Controls the default value of the Bluetooth call volume.5.2、Factory settingsFactory settings are mainly for production,installation,after-sales,maintenance,non-professionals,please do not use[Note]Non-professionals are not allowed to enter the factory settings.Improper settings may result in the product not working properly!!!5.3、Sound settingsSound settings are sound and balance two parts,as shown below:Sound effects:sound type settings,you can off,users,rock,pop,live,dance, classical and soft eight types to choose,according to their own preferences equal loudness,bass and treble to adjust.Balance:sound field balance mode settings,according to the different effects of the upper and lower left and right reverse adjustment.5.4、Navigation setSelect map application:press GPS key,will display the default navigation software5.5、Square setSteering wheel control button settings:enter the steering wheel learning interface,first press,And then long press the button on the steering wheel,select the appropriate key in the interface,when the settings are successful,the correspondinginterface button will be lit,after learning press Will save this learning content.6、radio receptionThe main radio interface,as shown below:[Note]The introduction is for reference only,please refer to the actual product.band,as:FM1、FM2、FM3、AM1、AM2Short press the button from the system will search the radio station step by step from high frequency to low frequency or from low frequency to high frequency until you find the radio frequency you want(FM band short press for FM1\FM2\FM3bandbetween the1-6units switch;long press to automatically scan the radio to the highfrequency;long press to the low-end scanning stationNote:If there is a tuner on some models of the front panel button,rotate it to the search frequency).The stronger the FM signal,the switch of the stereo,the radio broadcast effect is good,whereas in the remote area,the wireless signal is not stable,close the stereo switch to single channel,can improve the effect of the radio.When in a remote area,the radio signal is unstable,usually switching to the remote mode,the closer to the city center,the more powerful the FM broadcast signal, usually switching to the short range to improve the effect of the radio broadcast.Automatically browse stations and store up to six preset stations per band.The system can store up to30preset stations(18FM stations and12AM stations).(Click the browse button to browse the stations that have been memorized in the band(view a station every5seconds).After browsing to the appropriate station,click Browse and the selected station will play.Click on the button system will automatically search the radio from low to high frequency,during the search process,once again hit the button will stop the search,while the frequency of the screen will stop changing.Can enter the sound settings to switch the sound.7、Multimedia musicAfter inserting the USB flash drive,entering the music application will update all the audio files in the USB flash drive to the list,as shown below:Enter the song list,as shown below:You can select different paths to view music,and you can update the newly added audio files in the USB flash drive with the refresh button.Circle all the songs.Random play.Sound settings.previous track.Pause playback.next track.8、Multimedia video:After inserting the USB flash drive,the video will automatically detect the USB flash drive and enter the video playback screen.Music lists the video files in the USB drive.Enter the video playback page,as shown below:Function is similar to music,can be selected from U disk or local path(Note:This video player has a total of8interfaces,it supports MP4,AVI,RMVB,3GP,MKV,MOV, MPG,FLV and1080p HD video playback formatCan be displayed on the screen length and width to switch the ratio.9、File management operationEnter the file management interface,click Query the file to be found orclick Create a new folder,as shown below:Can be different from the path into the corresponding folder Long press the optional file on the file to copy,delete,cut and rename the details of the file,as shown below10、Common troubleshooting wizardIf you encounter the following problems in use,troubleshooting will help you quickly solve the problem,if the problem is still not resolved,it is recommended to contact our service department to help solve.phenomenon Reason HandleCan not boot The car key is not inserted intothe switch and the switch is notopenInsert the vehicle key and openthe door Power line insertion host Insert power cordTouch screen is not allowed Recalibrate the touch screen,press and hold the screen with fivefingers,and the system will automatically enter the calibrationscreen.The touch screen does notrespond The system is processing the transaction(road search,etc.),wait a moment,if it still can't be solved,please press the RST hole throughthe needle or the tip of the pen.Reversing without rear viewimageCamera not installed Install cameraCamera system is wrong Restart the machineThe system does not start,the rear view image appears after the reverse process,and thebutton is invalid.Pay attention to the principle ofdriving safety when designingproducts,and preset the rearview priorityYou must terminate the reverseaction before you can start thesystem by pressing the originalcar power button.Navigation cannot be located May be in the shielding area ofsome navigation signalsTry to drive the car out of a distance and observe whether the navigation resumes thesignal.If it is not restored,please restart or reset the machine.Cannot locate and navigate afterbootingNavigation map blind spots,some remote mountain areas orroads have not been built in thismapConfirm update mapFuzzy search can't find where togo First confirm that the entered Chinese character is correct,and then try to enter another name for the location.If it is not found,the location may not be in the map database.The navigation system gives the selected road"a far-reachingapproach"The navigation system will consider various factors in the road search.In addition to the distance,it will also consider the level of the road,the traffic regulations,the viaduct,the main line,etc.In short,it is convenient for the driver to reach the destination in the shortestpossible time.Blank on the map The machine has no network or no offline map data.It is alsopossible that the navigation scale is set too large or too small.Trychanging the scale to see if you can restore the map display.If it hasnot been resolved,it may be caused by the loss of positioning.Please re-select a marker point.FCC Radiation Exposure Statement:This equipment complies with FCC radiation exposure limits set forth for an uncontrolled environment. This equipment should be installed and operated with minimum distance 20cm between the radiator & your bodyFCC WarningThis device complies with Part 15 of the FCC Rules. Operation is subject to the following two conditions:(1) This device may not cause harmful interference, and (2) this device must accept any interference received, including interference that may cause undesired operation.NOTE 1: This equipment has been tested and found to comply with the limits for a Class B digital device, pursuant to part 15 of the FCC Rules. These limits are designed to provide reasonable protection against harmful interference in a residential installation. This equipment generates uses and can radiate radio frequency energy and, if not installed and used in accordance with the instructions, may cause harmful interference to radio communications. However, there is no guarantee that interference will not occur in a particular installation. If this equipment does cause harmful interference to radio or television reception, which can be determined by turning the equipment off and on, the user is encouraged to try to correct the interference by one or more of the following measures:- Reorient or relocate the receiving antenna.- Increase the separation between the equipment and receiver.-Connect the equipment into an outlet on a circuit different from that to which the receiver is connected.-Consult the dealer or an experienced radio/TV technician for help.NOTE 2: Any changes or modifications to this unit not expressly approved by the party responsible for compliance could void the user's authority to operate the equipment.。
小绿2067系列便携式手持地毯清洁机使用说明书
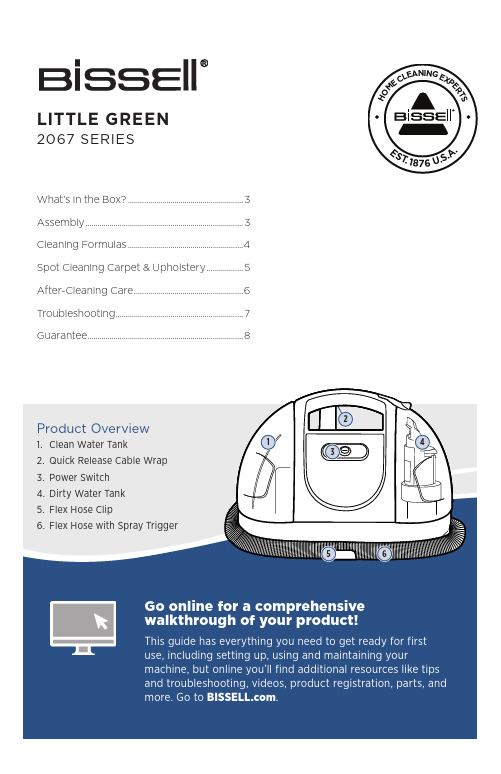
Troubleshooting (7)Guarantee (8)WARNINGTO REDUCE THE RISK OF FIRE, ELECTRIC SHOCK OR INJURY:»This appliance is not intended for use by persons (including children) with reduced physical, sensory or mental capabilities, or lack of experience and knowledge, unless they have been given supervision or instruction concerning use of the appliance by a person responsible for their safety.»Children should be supervised to ensure that they do not play with the appliance.»Unplug from electrical socket when not in use, before cleaning, maintaining,or servicing the appliance, and if your appliance has an accessory tool witha moving brush, before connecting or disconnecting the tool.»Do not immerse in water or liquid.»Keep hair, loose clothing, fingers, and all parts of body away from openings and moving parts of the appliance and its accessories.»Use only on carpet or upholstery moistened by the cleaning process.»Liquid must not be directed towards equipment containing electrical components.»Do not immerse. Use only on surfaces moistened by the cleaning process. Use only BISSELL® cleaning products intended for use with this machine.»Use only the type and amount of liquids specified under the operations section ofthis guide.»Always connect to a properly earthed electrical socket. Do not modify earthed plug.»Always install float before any wet pick-up operation.»Plastic film can be dangerous. To avoid danger of suffocation, keep away from children.»Use only as described in this user guide.»Use only manufacturer’s recommended attachments.»If appliance is not working as it should, has been dropped, damaged, left outdoors, or dropped into water; donot attempt to operate it and have it repaired at an authorised service center.»Do not put any object into openings.»Do not use with any opening blocked; keep free of dust, lint, hair, and anything that may reduce air flow.»Use extra care when cleaning on stairs.»Do not use to pick up flammable or combustible liquids, such as petroleum, or use in areas where they may be present.»Do not pick up toxic material (chlorine bleach, ammonia, drain cleaner, etc.).»Do not use appliance in an enclosed space filled with vapours given off by oil-based paint, paint thinner, some moth-proofing substances, flammable dust, or other explosive or toxic vapours.»Do not pick up hard or sharp objects such as glass, nails, screws, coins, etc.»Do not pick up anything that is burning or smoking, such as cigarettes, matches or hot ashes.»Do not use without filters in place.»Use indoors only.»If the supply cable is damaged, it must be replaced by the manufacturer, its service agent or similarly qualified person in order to avoid a hazard.»Do not run appliance over cable.»Do not leave appliance when plugged in.»Do not use with damaged cable or plug.»Do not pull or carry by cable, use cable as a handle, close door on cable, or pull cable around sharp edges or corners.»Keep cable away from heated surfaces.»To unplug, grasp the plug, not the cable.»Do not handle plug or appliance with wet hands.»Turn off all controls before unplugging.SAVE THESE INSTRUCTIONSORIGINAL INSTRUCTIONS. FOR OPERATION ON A 220-240 VOLT A.C. 50-60 HZ POWER SUPPLY ONLY.THIS MODEL IS FOR HOUSEHOLD USE ONLY.IMPORTANT INFORMATION»Keep appliance on a level surface.»To reduce the risk of a leaking condition, do not store machine where freezing may occur. Damage to internal components may result.2 3AssemblyNote: Always use genuine BISSELL® cleaning formulas for portable carpet and upholstery washers inyour machine.Spot & StainQuick andeffective spotcleaning.Pet Stain &OdourRemovestough petstains &odours.Stain PretreatLoosensset-in stains& odoursbefore carpetwashing.Pet StainPretreatLoosens toughpet stains& odoursbefore carpetwashing.Oxy BoostAdd toformula forpermanentstain removal. PretreatPretreat spots and stainsto improve cleaningperformance.FormulaKeep plenty of BISSELL cleaningformulas on hand so you can cleanwhenever it fits your schedule.BoostAdd to any formulato increase itseffectiveness.4 5IMPORTANT: Check the manufacturer’s tag before cleaning upholstery. If manufacturer’s tag is missing or not coded, check with your furniture dealer. Test a small, hidden area for colourfastness and examine when dry. If colour is aff ected do not use. Do not use on silk or velvet.6 7©2020 BISSELL Inc. All rights reserved. Part Number 1623999 07/20But wait, there’s more!Join us online for a complete guide to your new product, includingtroubleshooting, parts and more. Go to .VIDEOS INFO PARTSThis warranty gives you specific legal rights, in addition to rights you may have under the Australian Consumer Law . If you need additional instruction regarding this warranty or have questions regarding what it may cover, please contact your local BISSELL Consumer Care on the details set out below.It may be necessary to obtain some of yourpersonal information, such as a mailing address, to fulfill terms of this warranty. Any personal data will be handled pursuant to BISSELL’s Privacy Policy, which can be found at /privacy-policy.BISSELL® One Year WarrantySubject to the *conditions identified below, BISSELL will repair or replace (with new, refurbished, lightly used, or remanufactured components or products), at BISSELL’s option, free of charge from the date of purchase by the original purchaser, for one years any defective or malfunctioning part due to manufacturerdefect. This warranty applies to product used for personal purposes, and not commercial or rental service. This warranty does not apply to fans or routine maintenance or consumable components such as filters, belts, brush rolls, etc., damage or malfunction caused by negligence, abuse, neglect, unauthorized repair, or any other use not in accordance with the user guide. BISSELL recommends that the original packaging be kept for the duration of the warranty period in case such need arises within the warranty period that the item needs re-packing and transportation.*Conditions of WarrantySubject to whether such loss is reasonably foreseeable, BISSELL and its in-country distributors are not liable for incidental orconsequential damages of any nature associated with the use of this product.For Australian Consumers Only: Our goods come with guarantees that cannot be excluded under the Australian Consumer Law . You are entitled to a replacement or refund for a major failure and for compensation for any other reasonably foreseeable loss or damage. You are also entitled to have the goods repaired or replaced if the goods fail to be of acceptable quality and the failure does not amount to a major failure.This guarantee is in addition to other rights or remedies under law. Nothing in this guarantee excludes, limits or modifies any liability of BISSELL which is imposed by law, or limits or modifies any remedy available to the consumer which is granted by law. To make a claim under this guarantee contact BISSELL Australia PTY LTD (details below). Contact BISSELL prior to returning any goods. Where agreed, BISSELL will reimburse reasonable postage / handling costs (if any) for returning goods to BISSELL. To claim expenses incurred in making a claim under this guarantee please provide BISSELL with a copy of the receipt of the expenses by email or post.Consumer CareAustraliaTelephone: 1300 247 735Website: .au New ZealandTelephone: 0800 247 735 Website: 。
troubleshooting手册

troubleshooting手册一、简介《troubleshooting手册》是我们提供给客户的一本实用工具书,旨在帮助用户解决各种硬件、软件和网络方面的问题。
本手册涵盖了常见问题的解决方法,包括故障排查、系统优化、软件故障排除等,是一本全面的故障排除指南。
二、内容1.硬件故障排除a.电源问题:检查电源供应是否稳定,是否存在短路或断路现象。
b.内存问题:检查内存条是否安装正确,是否存在接触不良或损坏。
c.硬盘问题:检查硬盘是否正常工作,是否存在坏道或文件系统错误。
d.显卡问题:检查显卡驱动是否安装正确,是否存在驱动过时或冲突。
2.软件故障排除a.操作系统问题:检查操作系统是否存在病毒、木马或恶意软件,是否存在系统配置问题。
b.应用软件问题:检查应用软件是否存在版本过时或与操作系统不兼容的问题。
c.网络问题:检查网络连接是否稳定,是否存在DNS解析或路由问题。
d.驱动问题:检查驱动程序是否安装正确,是否存在过时或与硬件不兼容的问题。
3.网络故障排除a.路由器问题:检查路由器是否正常运行,是否存在配置错误或硬件故障。
b.线路问题:检查线路是否存在破损、老化或接触不良的问题。
c.设备问题:检查交换机、调制解调器等网络设备是否存在故障。
d.DNS问题:检查DNS设置是否正确,是否存在DNS服务器故障或网络连接问题。
4.系统优化a.系统垃圾清理:定期清理系统垃圾文件,释放磁盘空间。
b.注册表优化:根据需求优化注册表,提高系统性能。
c.更新与补丁:及时更新系统和软件补丁,确保系统安全性。
d.软件管理:使用软件管家或应用商店管理软件,确保软件安全且兼容。
三、常见问题及解决方法1.我的电脑无法启动,怎么办?首先检查电源是否正常,然后检查内存条、硬盘等硬件设备是否正常连接。
如果无法确定问题原因,请寻求专业人士帮助。
2.我安装的某个软件无法正常运行,怎么办?首先检查软件安装包是否完整,然后检查软件配置文件是否存在损坏。
西屋电动烤箱使用手册说明书

WARNING Read and understand this entire owner’s manual, including all safety information, before plugging in or using this product. Fail to do so could result in fire, electric shock, or serious personal injury.CAUTION Keep this owner’s manual for future reference. If you sell or give away this product,make sure this manual accompanies this product.NO VENTING REQUIRED120V AC; 60 Hz; 1500 WattsImportant Safety Information (3)Preparation (5)Product Dimension (6)Assembly (7)Battery Information (7)Operation (8)Control Panel (9)Remote Control (10)Care and Maintenance (11)Schematic Diagram (12)FAQ – Frequently Asked Questions (13)Troubleshooting Guide (14)Limited Warranty (15)Customer Service (15)WARNINGRead all instructions before using this heater!This heater is hot when in use. To avoid burns, DO NOT let bare skin touch hot surfaces. If provided,use handles when moving this burning heater.Keep combustible materials,such as furniture, pillows, bedding, papers, clothes, and curtains at least 3 feet (0.9m) from the front of the heater, and keep them away from the sides and rear.Extreme caution is necessary when any heater is used near children or invalids and whenever the heater is left operating and unattended.DO NOT operate any heater with a damaged cord or plug or after the heater malfunctions, has been dropped or damaged in any manner. Discard heater, or return to authorized service facility for examination and/or repair.DO NOT run power cord under carpeting. DO NOT cover power cord with throw rugs, runners, or similar coverings. DO NOT route power cord under furniture or appliances. Arrange power cord away from traffic area, and where it will not be tripped over.DO NOT insert or allow foreign objects to enter any ventilation or exhaust opening, as this may cause electric shock or fire, or damage the heater.To prevent a possible fire, DO NOT block air intakes or exhaust in any manner. This could cause a fire. DO NOT use on soft surfaces, like a bed, where openings may be blocked up.A heater has hot and arcing or sparking parts inside. DO NOT use it in areas where gasoline, paint, or flammable liquids are used or stored.Use this heater only as described in this manual. A ny other usage not recommended by the manufacturer may cause fire, electric shock, or injury to persons.ALWAYS plug heaters directly into a wall outlet/receptacle. NEVER use with an extension cord or relocatable power tap (outlet/power strip).Connect to properly grounded outlets ONLY.DO NOT place the heater near a bed because objects such as pillows or blankets can fall from the bed and be ignited by the heater.NEVER use this heater in bathrooms, laundry rooms, or any other location where the heater could fall into a bathtub or pool, become damp, or touch the water.AVOID FIRE! Regularly inspect all air vents to make sure they are free from dust, lint, or other blockage. Unplug the unit and clean with a vacuum ONLY. DO NOT rinse or get wet. NEVER permanently install in a recessed area of the wall. This may result in blocked air flow, overheating, or fire.WARNING: DO NOT DEPEND ON THE POWER SWITCH THE SOLE MEANS OF DISCONNECTING POWER WHEN SERVICING OR MOVING THE HEATER. ALWAYS UNPLUG THE POWER CORD.WARNING: REDUCE THE RISK OF FIRE OR ELECTRIC SHOCK---DO NOT USE THIS HEATER WITH ANY SOLID STATE SPEED CONTROL DEVICES.For residential use only! NOT for commercial use! Any commercial or public use of thisheater voids all warranties, and could cause injury.This product is not intended to be a primary heat source. It is for supplemental heat only. INDOOR use only!NEVER use this heater outdoors! Doing so may result in electric shock! Risk of electric shock! DO NOT OPEN! No user-serviceable parts inside!NEVER modify this heater. Doing so could result in personal injury or property damage. Modification of this fireplace completely voids all warranties.ALWAYS turn this heater off before unplugging it from the outlet.ALWAYS disconnect this unit from the power supply before performing any assembly or cleaning, or before relocating the electric fireplace.NEVER leave this heater unattended. ALWAYS unplug this heater when not in use.ALWAYS store this heater in a dry location. NEVER use the fireplace if it has become wet. ONLY use this heater on a 120V AC 15-Amp circuit. NEVER overload the circuit. If this heater trips the circuit breaker, unplug all other appliances on the same circuit before the next use. Avoid plugging other appliances into the same circuit as this heater.NEVER plug this heater into an outlet that is old, cracked, or has any loose wires or connections. Plugging this heater into a faulty outlet could result in electric arcing within the outlet that could cause the outlet to overheat or catch fire.ALWAYS check your heater cord and plug connections with each use!i) MAKE SURE the plug fits tight in the outlet! Faulty wall outlet connections or loose plugs cancause the outlet to overheat.ii) Heaters draw more current than small appliances. Overheating may occur even if it has not occurred with the use of other appliances.iii) During use check frequently to see if the plug outlet or faceplate is HOT!iv) If the outlet or faceplate is HOT, discontinue use immediately and have a qualified electrician inspect and/or replace the faulty outlets.This heater has a polarized plug (one blade is widerthan the other). As a safety feature to reduce the risk ofelectrical shock, this plug is intended to fit in a polarizedoutlet only one way. If the plug does not fit fully in theoutlet, reverse the plug. If it still does not fit, contact aqualified electrician. Do not attempt to defeat this safetyfeature.SAVE THESE INSTRUCTIONS!DO NOT use this Electric Fireplace if any part has been under water. Immediately call aqualified service technician to inspect and to replace any part of the electrical system ifnecessary. Keep plastic wrapping away from children.Unpacking the Electric Fireplace. Remove all parts and hardware from the carton and place them on a clean, soft, dry surface. Check the parts list to make sure nothing is missing. Dispose of packaging materials properly. Please recycle whenever possible. Keep the original packaging for future transport and/or storage.Owner’s Manual ×1 pcFireplace InsertFireplace MantelUnits:mmUnits:inchFireplace Insert SizeUnits:inchYour new electric fireplace may be installed virtually anywhere in your home. However, when choosing a location ensure that the general instructions are followed. For best results, install out of direct sunlight. Power supply service must be either completed or placed within the electric fireplace prior to finishing toWhen moving the insert into mantel, Do not let bottom of insert touch the mantel to avoid the scratch.BATTERY REPLACEMENTNOTE:The remote control not include the batteries.NOTE:Do not mix old and new batteries.Do not mix alkaine,standard(carbon zinc),or rechargeable(nicad,nimh,ect.)batteries.Read and understand this entire owner’s manual, including all safety information, beforeplugging in or using this product. Fail to do so could result in e lectric shock, fire, serious injury, or death.PowerMake sure the Power Switch, located on the control panel, is in the OFF position. Plug the power cord into a 110~120 Volt 15 Amp outlet (see IMPORTANT SAFETY INFORMATION on Pages 3 and 4). Make sure the outlet is in good condition and that the plug is not loose. NEVER exceed the maximum amperage for the circuit. DO NOT plug other appliances into the same circuit.Temperature Limiting ControlThis heater is equipped with a Temperature Limiting Control. Should the heater reach an unsafe temperature, the heater will automatically turn OFF. To reset:1. Unplug the power cord from the outlet.2. Turn the Power Switch on the CONTROL PANEL to OFF. Wait at least 5 minutes.3. Inspect the fireplace to make sure no vents are blocked, or clogged with dust or lint. If they are,use a vacuum to clean the vent areas.4. With the Power Switch in the OFF position, plug the power cord back into the outlet.5. If it switches off again, UNPLUG THE HEATER RIGHT AWAY!Have the outlets, wiring, andbreaker box inspected by a professional. Make necessary repairs before using the heater. Heater RatingMaximum heat output: 1500W (5000BTU); Maximum heating area: 400 square feet.OperationReview the IMPORTANT SAFETY INFORMATION on Pages 3 and 4before operating. NOTICE: When the heater is first turned on, a slight odor may be present. This is normal and should not occur again unless the heater is not used for a long period oftime.Open a door on the top right sidefor operation all functionsControl PanelLocated on the right and top side panel of the fireplace.Remote ControlNOTICE: Control panel Power Switch must be ON to use remote control.Aim the remote control at the remote receiver. Make sure you hear a beep each time you press the button! If not, the fireplace will not respond to the signal.Power ON/OFFNOTICE: Operation for all functions are same as the buttons on the fireplace.The TIMER button on the remote control can’t press 10s into the log speaker, also can’t press 10s into the TIMER,but you can press 10s on the fireplace Timer button,then press TIMER on the remote to get the log speaker,also you press the TIMER 10s on the fireplace,then press TIMER on the remote to operate the TIMER from 1hr,2hrs...9hrs,off.ALWAYSturn the heater OFF and unplug the power cord from the outlet before cleaning, performing maintenance, or moving this fireplace. Failure to do so could result in electric shock, fire, or personal injury . CleaningNEVER immerse in water or spray with water. Doing so could result in electric shock, fire, or personal injury.Metal:Buff using a soft cloth, slightly dampened with a citrus oil-based product.DO NOT use brass polish or household cleaners as these products will damage the metal trim.Glass:Use a good quality glass cleaner and dry thoroughly with a paper towel or lint-free cloth.NEVER use abrasive cleansers, liquid sprays, or any cleaner that could scratch the surface.Plastic:Wipe gently with a slightly damp cloth and a mild solution of dish soap and warm water.NEVER use abrasive cleansers, liquid sprays, or any cleaner that could scratch the surface.Vents:Use a vacuum or duster to remove dust and dirt from the heater and vent areas.Clean the exterior of the fireplace with a slightly damp cloth or duster.Maintenance Risk of electric shock ! DO NOT OPEN! No user-serviceable parts inside! ALWAYSturn the heater OFF and unplug the power cord from the outlet before cleaning, performing maintenance, or moving this fireplace. Failure to do so could result in electric shock, fire, or personal injury .Electrical and Moving Parts:The fan motors are lubricated at the factory and will not require lubrication.Electrical components are integrated in the fireplace and are not serviceable by the consumer.Storage:Store heater in a clean dry place when not in use.Replacement parts:Use only replacement parts supplied by the manufacturer. Use of any other parts, or modifying the fireplace in any way, will void all warranties.No internal parts are replaceable or serviceable.WARNING! No other servicing should be performed by the consumer. Do not attempt to service the unit by yourself.IN AC LED lightWhy does the fan blow before the heat comes on, and after the heater is turned off?Heat and cool gradually. The fan blows when the heater is first turned on, and the heat is still heating up. After the heater turns off, the fan will continue to blow air for 10 seconds. This allows the fireplace to cool slowly, and helps prevent overheating.What does the fireplace beep? Can I turn the beeping off?The beeps indicate that the signal from the control panel, or remote control, has been received by the fireplace. The beeping cannot be turned off.Why doesn’t the fireplace function change when remote control setting changes?The fireplace function will only change if there is a beep after pressing the button. If you do not hear a beep, try again. If you hear a beep, the fireplace function will change to match the remote control setting.Why does the remote control not work, or only work sometimes?Check to make sure the batteries are good. If necessary, change to new batteries. If the remote control is not aimed properly, if you are too far away, or if you are too far off to the side, the signal may not reach the fireplace. Get closer, aim at the upper top corner of the screen (where the red heat indicator light is located), and try again.How do I change from high heat to low heater?The heater is controlled by the heater button on the control panel, or the heater buttons on the remote control.Is the thermostat setting accurate?The temperature within a room can vary. Room size, fireplace location, air flow, sunlight, wall type (interior vs. exterior), insulation, etc. all affect temperature. The fireplace setting may not match your home thermostat exactly. This is normal. Try different thermostat setting on your fireplace until you find one that is right for you.N O I T U L O S M E L B O R P There is no power to the fireplace, or it does not turn on. 1. Make sure the power cord is plugged into a functioning and properly grounded 15 Amp 120V AC electrical outlet. 2. Make sure the Power Switch on the control panel is ON. 3. If the unit had been working, but then turned off by itself, the temperature limiting control may need to be reset. See p age 8 for instructions. 4. Check for damage to the power cord or plug. If damaged, DO NOT USE.The control panel functions do not work. 1. Make sure the Power Switch on the control panel is turned on.If it is OFF, the functions will not work. The FLAME button doesn’t work. 1. Make sure the Power Switch on the control panel is ON. 2. If the Power Switch is ON, and the functions do not work,The heater does not work. 1. Make sure the Power Switch on the control panel turned on. 2. Control Panel: Press the heater button on the control panel to override the thermostat at any time. 3. Remote control: Make sure the thermostat is not set too low. If the thermostat is set lower than room temperature, the heater will not turn on. The heater does not blow hot air when it turns on and off. This is normal. The fans blow cool air while the heater gradually heat up. The fans blow after the heater turn off to cool the heater and prevent overheating.The remote control does not work. 1. Make sure the battery is properly installed. 2. Make sure the Power Switch on the control panel is turned on. The remote control will not work unless the POWER SWITCH on the control panel is turned on. 3. Aim the remote control at the receiver. 4. Remove objects that may be in the way. Items between the remote control and the remote control receiver will block the signal. 5. Don’t press the remote control buttons too quickly. Give the unit time to respond to your commands.The thermostat does not work. 1. Make sure the heater is turned on. The thermostat will not work unless the heater is turned on. 2. Make sure the thermostat is not set too low. If the thermostat is set lower than room temperature, the heater will turn on.4. If none of these solutions work, please e-mail us .please e-mail u s.2. If the Power Switch is ON, and the functions do not work, please e-mail us .This warrants to the original purchaser that this product is free from defects in material and workmanship as of the date of purchase and that it will, under normal use and proper care, remain one year from the date of purchase. Missing or initially defective parts will be replaced free of charge during the period of this limited warranty. If parts are unavailable, comparable replacement of refund will be given. The original dated sales receipt is required for all warranty claims. This warranty does not cover damage which has occurred during transport from the point of purchase to the consumer’s home. This warranty does not cover glass, light bulbs, batteries, transportation, labor, or other issues not associated with the manufacture of the product.This product is for residential use only. Any and all commercial use of this product voids all warranties, and absolves the manufacturer from all liability.Read and understand all assembly and operating instructions, and all safety information and warnings, before use. The following will void this warranty: Damage caused by tampering,modifying, or altering the fireplace insert in any manner; Damage due to incorrect assembly, improper care, misuse, or abuse; Damage from being used with the wrong power source; Water damage; Damage caused from this insert being used outdoors; Damage caused by using for excessive periods of time; Damage caused by the insert being used in a commercial application; Damage from use as a primary heat source;Other misuse or abuse not specifically listed herein.This product is not intended to be used as a primary heat source. It is for supplemental heating purposes only.Power supply:120V-60HzPower consumption: 1500WProtection class: ILight bulb: LED。
Whirlpool 水冷器压缩器故障诊断指南说明书
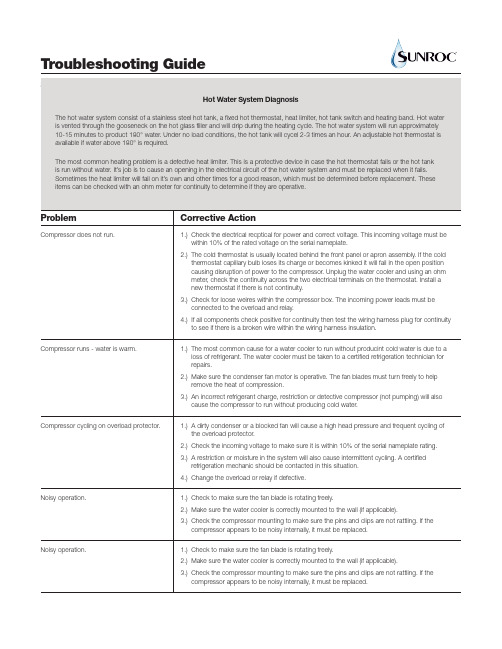
4.) If all components check positive for continuity then test the wiring harness plug for continuity to see if there is a broken wire within the wiring harness insulation.
1.) The most common cause for a water cooler to run without producint cold water is due to a loss of refrigerant. The water cooler must be taken to a certified refrigeration technician for repairs.
Problem
Compressor does not run.
Compressor runs - water is warm. Compressor cycling on overload protector. Noisy operation. Noisy operation.
Corrective Action
2.) Make sure the condenser fan motor is operative. The fan blades must turn freely to help remove the heat of compression.
索尼 RX-D45 便携式 CD 立体声系统使用说明书
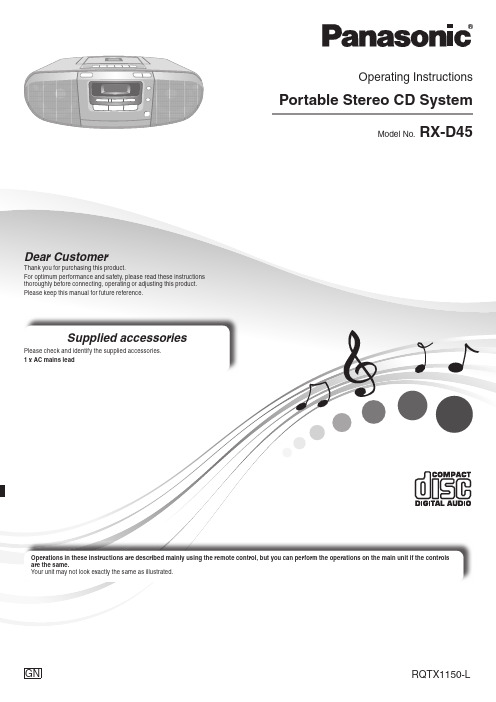
Supplied accessoriesPlease check and identify the supplied accessories.1 x AC mains leadOperations in these instructions are described mainly using the remote control, but you can perform the operations on the main unit if the controls are the same.Your unit may not look exactly the same as illustrated.2R Q T X 115Inside of productWARNING:TO REDUCE THE RISK OF FIRE, ELECTRIC SHOCK OR PRODUCT DAMAGE,• DO NOT EXPOSE THIS APPARATUS TO RAIN, MOISTURE, DRIPPING OR SPLASHING AND THAT NO OBJECTS FILLED WITH LIQUIDS, SUCH AS VASES, SHALL BE PLACED ON THE APPARATUS.• USE ONL Y THE RECOMMENDED ACCESSORIES.• D O NOT REMOVE THE COVER (OR BACK); THERE ARE NO USER SERVICEABLE PARTS INSIDE. REFER SERVICING TO QUALIFIED SERVICE PERSONNEL.CAUTION!• DO NOT INSTALL OR PLACE THIS UNIT IN A BOOKCASE, BUILT-IN CABINET OR IN ANOTHER CONFINED SPACE. ENSURE THE UNIT IS WELL VENTILATED. TO PREVENT RISK OF ELECTRIC SHOCK OR FIRE HAZARD DUE TO OVERHEATING, ENSURE THAT CURTAINS AND ANY OTHER MATERIALS DO NOT OBSTRUCT THE VENTILATION VENTS.• DO NOT OBSTRUCT THE UNIT’S VENTILATION OPENINGS WITH NEWSPAPERS, TABLECLOTHS, CURTAINS, AND SIMILAR ITEMS.• DO NOT PLACE SOURCES OF NAKED FLAMES, SUCH AS LIGHTED CANDLES, ON THE UNIT.• DISPOSE OF BATTERIES IN AN ENVIRONMENTALL Y FRIENDLY MANNER.The socket outlet shall be installed near the equipment and easily accessible.The mains plug of the power supply cord shall remain readily operable.To completely disconnect this apparatus from the AC Mains, disconnect the power supply cord plug from AC receptacle.This product may receive radio interference caused by mobile telephones during use. If such interference is apparent, please increase separation between the product and the mobile telephone.THIS UNIT IS INTENDED FOR USE IN MODERATE CLIMATES.–If you see this symbol–MaintenanceIf the surfaces are dirtyTo clean this unit, wipe with a soft, dry cloth.If the surfaces are extremely dirty, use a soft cloth dipped in a soap-and water solution or a weak detergent solution.• Never use alcohol, paint thinner or benzine to clean this unit.• Before using chemically treated cloth, read the instructions that came with the cloth carefully.Care of tape deck’s headsClean the heads regularly to ensure good quality playback and recording. Use a cleaning tape (not included).Q T X 1150• Avoid using or placing this unit near sources of heat. Do not leave it in an automobile exposed to direct sunlight for a long time with the doors and windows closed as this may deform the cabinet.• Avoid cuts, scratches, or poor connections in the AC mains lead, as they may result in possible fi re or electric shock hazard. Also, excessive bending, pulling or splicing of the lead should be avoided.• Do not unplug the AC mains lead by pulling on the lead. To do so may cause premature failure or shock hazard.• Do not operate this unit in a bathroom, as a potential shock hazard may result.• When not in use, disconnect the AC mains lead from the household mains socket.Maintenance ...................................................................2Safety precautions ........................................................3Use of batteries ..............................................................3Power sources ...............................................................3Overview of controls .....................................................4Discs ...............................................................................4Using the FM/AM radio ..................................................5Cassette tape – Play and record ..................................5Using the clock and timers ...........................................6Using sound effects ......................................................6Troubleshooting guide ..................................................6Specifi cations . (7)Connect the AC mains lead fi rmly to the unit and the household mains socket.✒Note• The included AC mains lead is for use with this unit only. Do not use it with other equipment.• The unit is in the standby condition when the AC power supply cord isconnected. The primary circuit is always “live” as long as the power cord is connected to an electrical outlet.• The unit cannot be powered by batteries if the AC mains lead is connected. Disconnect the AC mains lead from the unit to operate on battery power.• Use only alkaline batteries.When to change the batteriesWhen the battery indicator begins fl ashing, replace all 8 of the batteries. It is also a good idea to replace all the batteries before recording.✒NoteBefore any function starts, the battery indicator may fl ash although the batteries are not drained. The indicator will display its current status when the unit is powered from the household mains socket by using the AC mains lead.Memory back-upWhen the power supply is interrupted, the current time, timer settings and radio stations you have set are saved if you have inserted back-up batteries (not included).These batteries do not power the unit.When to change the batteries The batteries last about a year.Connect the unit to AC power before replacing the batteries.Before connecting or disconnecting the AC mains lead, press[8/x , STOP/EJECT] to stop the tape and press [TAPE/OFF] to turn the unit off. The back-up batteries ware out faster if the cord is disconnected with the power still on.✒NoteUse either alkaline or manganese batteries.• If this unit is not used for a long period of time or is used only from an AC power source, remove all the batteries to prevent potential damage due to possible battery leakage.• Do not mix old and new batteries.• Do not use different types of batteries at the same time.• Do not take apart or short circuit the batteries.• Do not attempt to recharge alkaline or manganese batteries.• Do not use batteries if the covering has been peeled off.• Do not heat or expose to fl ame.• Do not leave the battery(ies) in an automobile exposed to direct sunlight for a long period of time with doors and windows closed.• Mishandling of batteries can cause electrolyte leakage, which may cause a fi re.CAUTIONDanger of explosion if battery is incorrectly replaced. Replace only with the same or equivalent type recommended by the manufacturer. Dispose of used batteries according to the manufacturer’s instructions.4R Q T X 1150These speakers do not have magnetic shielding. Do not place them near televisions, personal computers or other devices easily infl uenced by magnetism.E Disc trayF Tuner (FM/AM) selection, auto preset selectionG Disc play or pauseH Stop disc playback, MONO selection for FM mode I Disc tray open or closeJ Play mode function, program function, tuning mode selectionK Track skip or search, check program content, preset channel selection, tuning function, time adjustment L Sound equalizer (EQ) selection M Display panel N Volume controlO Cassette play operations P Cassette deckHeadphone jack (PHONES)Plug type: Ø 3.5 mm stereo (not included)• Avoid listening for prolonged periods of time to prevent hearing damage.• Excessive sound pressure from earphones and headphones can cause hearing loss.1 Press [4/9, CD] and then [8] (stop).2 Press and hold [–PGM].“PGM” is displayed.3 Press [–/2] or [6/+] to select your desired track.4 Press [–PGM].Repeat steps 3 and 4 to program other tracks.Press [4/9, CD] to start play.✒Note• When you try to program more than 24 tracks, “FULL” appears.• You will not be able to add more tracks to the existing program. The existing program has to be cleared.• The program memory is cleared when you open the disc tray.Q T X 11501 Press [FM/AM] to select “FM” or “AM”.2 If “PGM” is displayed, press [TUNE MODE] to clear it.3 Press [–/2] or [6/+] to select the frequency of the required station.To tune automaticallyPress and hold [–/2] or [6/+] until the frequency starts changing rapidly. The unit begins auto tuning, stopping when it fi nds a station.• Auto tuning may not function when there is excessive interference.• To cancel auto tuning, press [–/2] or [6/+] once again.To improve receptionFM: Extend the whip antenna and adjust its direction.AM: Adjust the position of the unit.To improve FM sound qualityWhen “FM” is selectedPress [FM MODE] to display “MONO”.To cancelPress [FM MODE] again.• MONO is also cancelled if the frequency is changed.• Turn off “MONO” for normal listening.Up to 16 stations each can be set in the FM and AM bands.✒PreparationPress [FM/AM] to select “FM” or “AM”.Automatic presettingPress and hold [–AUTO PRESET] to start presetting.The tuner presets all the stations it can receive into the channels in ascending order. When fi nished, the last station memorised is tuned in.Manual presetting1 If “PGM” is displayed, press [TUNE MODE] to clear it.2 Press [–/2] or [6/+] to select the frequency of the required station.3 Press and hold [–PGM].“PGM” and the selected frequency blinks.4 Within 10 seconds or so Press [–PGM] followed by [–/2] or [6/+] to select the desiredchannel.5 Press [–PGM].The station occupying a channel is erased if another station is preset to that channel.6 Repeat steps 2 to 5 to preset more stations.Selecting a preset station1 Press [TUNE MODE].“PGM” is displayed.2 Press [–/2] or [6/+] to select thechannel.This system can also receive AM broadcasts allocated in 10 kHz steps.To change the step from 9 kHz to 10 kHz1 Press and hold [8] (stop).After a few seconds the display changes to a fl ashing display of the current minimum frequency.2 Continue to hold down [8] (stop).• When the minimum frequency changes, release the button. To return to the original step, repeat the above steps.• After the setting is changed, any previously preset frequency will be cleared.Use normal position tapes.High position and metal position tapes can be played, but the unit will not be able to identify the characteristics of these tapes.1 Press [TAPE/OFF].2 Open the cassette operation buttons’ lid.3 Press [8/x , STOP/EJECT] and insert the cassette.Insert with the side to be played facing up and the exposed tape facing towards you. Close the deck by hand.Press [4, PLAY] to start play.RecordingUse normal position tapes.High position and metal position tapes can be used, but the unit will not be able to record or erase them correctly.✒PreparationWind up the source tape so recording can begin immediately.1 Press [0, STOP/EJECT] and insert the cassette to be recorded.Insert with the side to be recorded facing up and the exposed tape facingtowards you.Select the source to be recorded.Press [V] to start recording.✒NoteChanges to volume and sound quality do not affect recording.Erasure preventionThe illustration shows how to remove the tabs to prevent recording. To record onthe tape again, cover as shown.To prevent recordingTo re-record✒Note• Tapes exceeding 100 minutes are thin and can break or get caught in the mechanism.• Tape slack can get caught up in the mechanism and should be wound up before the tape is played.• Endless tapes can get caught up in the deck’s moving parts if used incorrectly.6R Q T X 1150This is a 24-hour clock.1 Press [CLOCK/TIMER].Each time you press the button:# PLAY ON SLEEPCLOCKOriginal display2 Within 5 seconds or soPress [–/2] or [6/+] to set the time.Holding down the button will speed up the time selection.3 Press [CLOCK/TIMER] to fi nish setting the time.Displaying the clockPress [CLOCK/TIMER] to display the clock for few seconds.✒Note• Reset the clock regularly to maintain accuracy.• When the unit is in standby mode and it is powered by batteries, clock will not be displayed.You can set the timer to come on at a certain time to wake you up.✒Preparation• Turn the unit on and set the clock.• Prepare the music source you want to listen to; disc or radio source, and set the volume.1 Press [CLOCK/TIMER] repeatedly to select the play timer.2 Within 5 seconds or soPress [–/2] or [6/+] to set thestarting time.3 Press [CLOCK/TIMER] to confi rm.4 Repeat steps 2 and 3 to set the fi nishingtime.To activate the timer5 Press and hold [–# PLAY] to turn on the timer.# PLAYNo display (off)Press [TAPE/OFF] to turn off the unit.✒Note• The play timer will start at the preset time, with the volume increasing gradually to the preset level.• The timer comes on at the set time every day if the timer is on.• The unit must be in the standby mode for the timer to function.• If you turn the unit off and on again while a timer is functioning, the fi nish time setting will not be activated.Using the sleep timerThis function enables you to turn off the unit automatically after the set time except in tape mode.1 Press [CLOCK/TIMER] repeatedly to select “SLEEP”.2 Press [–/2] or [6/+] to select your desired time (in minutes).To cancelPress [CLOCK/TIMER] repeatedly to show the remaining time, and press [–/2] or [6/+] to select “OFF”.Changing the remaining timePress [CLOCK/TIMER] repeatedly to show the remaining time, and press [–/2] or [6/+] to select your desired time.✒Note• The play and sleep timer can be used together.• The sleep timer always has priority. Be sure not to overlap timer settings.Troubleshooting guideBefore requesting service, make the following checks. If you are in doubt about some of the check points, or if the solutions indicated in the chart do not solve the problem, consult your dealer for instructions.RadioQ T X 1150Output power2.5 W x 2 (RMS MAX / DC)PMPO output power60 WFrequency Modulation (FM) Frequency range87.50 MHz to 108.00 MHz (50 kHz step)Amplitude Modulation (AM) Frequency range 522 kHz to 1629 kHz (9 kHz step)520 kHz to 1630 kHz (10 kHz step)Headphone jack T erminalStereo, 3.5 mm jack (32 )Disc played (8 cm or 12 cm) CD-Audio (CD-DA), CD-R/W (CD-DA)Sampling frequency 44.1 kHz Decoding 16 bit linear Beam source Semiconductor laser {wavelength 795 nm (CD)}Frequency response 40 Hz to 20 kHz Number of channels 2 channel, stereo Wow and fl utter Less than possible measurement data Track system 4 track, 2 channel, stereo Monitor system Variable sound monitorRecording system AC bias 84 kHz Erase systemMulti Pole magnetOverall frequency response NORMAL50 Hz to 12 kHzSpeakers Impedance 8Full range2 x 8 cmPower supplyAC 230 V to 240 V , 50 Hz Battery 12 V (8 x LR14, C)Memory back-up 6 V (4 x R6/LR6, AA)Power consumption 13 W Battery life (use only alkaline batteries) Radio broadcast 10 hours Radio recording 10 hoursCD playback 7 hours CD recording 9 hours Tape playback 9 hours Dimensions (WxHxD) 408 mm x 148 mm x 271 mm Mass 3.2 k g without batteries (3.8 k g with batteries)Operating temperature range 0°C to +40°C Operating humidity range 35% to 80% (no condensation)Power consumption in standby mode:2 W (approximate)✒Note1. Specifi cations are subject to change without notice. Mass and dimensions are approximate.2. Total harmonic distortion is measured by the digital spectrum analyzer.Panasonic Corporation Web Site: En RQTX1150-LL0410LL0。
Selective Solder Troubleshooting Guide

PROBLEM: INSUFFICIENT HOLE FILLPOSSIBLE CAUSES:•Not enough f l ux•Distance from Fluxer to PCB is too high, Flux can not go up the hole•Pin to hole ratio is too small •Temperature on top side of board is too low •Solder temperature is too low •Distance from solder wave to PCB is too highPAGE 1165 Boro Line Road • King of Prussia , PA 19406 • USA • Phone: 610-337-3050 • Fax: 610-337-3054 • info@ddmnovastar .comPROBLEM: INSUFFICIENT SOLDERPOSSIBLE CAUSES:•Not enough f l ux •Solderability of component •Bad PCB pads •Solder time too short, reduce speed or increase dipping •Distance from solder wave to PCB is too high •Bad f lux solidsPROBLEM: BLOW HOLESPOSSIBLE CAUSES:•Board temperature is too low•Moisture in the PCBPAGE 2PROBLEM: EXCESSIVE SOLDERPOSSIBLE CAUSES:•Typically happens at the end of line soldering of connectors •Layout too tight to make a good peel off movement •Try to move over the connector or diagonally out of the connector •Let the wave switch off at the end of the connector •Board / Component solderability •Lead length is too long (1 to 1.5mm is perfect)•Solder temperature is too low •Speed is too fast, solder time is too shortPROBLEM: BRIDGINGPOSSIBLE CAUSES:•Typically happens at the end of line soldering of connectors•If bridging occurs in the middle or at the beginning of a connector,it is typically a heat or N2 purity problem•Layout is too tight to SMD component to make a good peel offmovement •Let the wave switch off at the end of the connector •Board / Component solderability •Lead leng t h is too long (1 to 1.5mm is perfect)•Solder temperature is too low •Speed is too fast, solder time is too shortPROBLEM: SOLDER BALLSPOSSIBLE CAUSES:•Occur more often in selective soldering than in wave soldering. Reason is typically due to the higher temperatures used in selective soldering•Solder mask type is the most important factor•Too much f l ux•N2 adjustment is too high•Preheat is too low165 Boro Line Road • King of Prussia , PA 19006 • USAPhone: 610-337-3050 • Fax: 610-337-3054 • www.ddmnovastar .com • info@ddmnovastar .comPAGE 3PROBLEM: POOR HOLE FILLINGPOSSIBLE CAUSES:Poor or incomplete hole f i ll is normally a f l uxing or heating issue. It is not commonly a printed board problem.As a guide, the topside temperature of the printed board should be 100° - 110°C just before wave contact. This is generally true for double sided and multilayer boards. Single sided boards should be processed at slightly lower temperatures as no solder penetration is needed.I n the above examples, the solder has not fully f i lled the plated thru-hole. This is either due to the preheat operation being set too low or poor f l ux application. In both cases, checking the processparameters should eliminate the problem.PROBLEM: SOLDER SHORTS ON PIN GRID ARRAYPOSSIBLE CAUSES:Solder shorts are a major problem in both selective and wave soldering, particularly as component pitches continue to decrease.In the example shown, shorts are seen on the Pin Grid Array device. Due to the close proximity and the number of pins, the solder separation is impeded from the base of the board. Shorting can occur due to poor f l uxing, incorrect heat or wave separation. Poor N2 quality can also cause shorts.All shorting can be decreased through good design rules with reduction in pad size and component lead length. A lead length from 1 - 1.5mm is perfect for selective soldering. Longer pinscan cause more shorts.165 Boro Line Road • King of Prussia , PA 19006 • USAPhone: 610-337-3050 • Fax: 610-337-3054 • www.ddmnovastar .com • info@ddmnovastar .com165 Boro Line Road • King of Prussia , PA 19006 • USAPhone: 610-337-3050 • Fax: 610-337-3054 • www.ddmnovastar .com • info@ddmnovastar .comPAGE 4PROBLEM: SOLDER SHORTS NEAR SMD COMPONENTSPOSSIBLE CAUSES:It is critical to selective solder a heavily populated board. Most can only be f lu xed by good design. Increasing the f l ux solids will improve the drainage on all joints.In the example shown, the pin length is correct at 1 - 1.5mm, but the surface pads could be reduced in size. With smaller pads, less solder is retained on the board to short between pins.If this is the only defect area on the boad , then a nice f i x is aglue dot placed between the two pins.PROBLEM: SUNKEN SOLDER JOINTSPOSSIBLE CAUSES:Sunken joints may be seen on the topside and base of the board.The most common cause for sunken joints is the hole to lead ratio. If the hole is large in comparison to the lead diameter, the solder literally drops in or out of the hole.Sunken solder joints can be caused by incorrect preheat or poor f l uxing when seen on the topside of the board.Sunken solder joints on the base of the board may be caused by outgassing. If the soldering process is functioning correctly, when the hole outgasses the solder tends to shrink back into the hole to f ill the void.。
NT114PH碳纤维牛顿望远镜使用说明书

NT114PHCARBON FIBER NEWTONIAN 114 MMW/ PAN HANDLE MOUNT INSTRUCTION MANUAL10+SUN HAZARD — Never look directly at the sun with this device.WARNING:CHOKING HAZARD — Small parts. WARNING:Contains button or coin cell battery. Hazardous if swallowed — see instructions.INCLUDEDX 1The lens contains lead that may be harmful. WARNING:Customer Service: Call 1-866-252-3811Instruction Manual and Downloadable Planisphere Visit:/pages/product-manualsHow To Set UpNote: We recommend assembling your telescope for the first time in the daylight or in a lit room so that you can familiarize yourself with assembly steps and all components.Telescope Terms To Know:Diagonal: A mirror that deflects the ray of light 90 degrees.With a horizontal telescope tube, this device deflects the light upwards so that you can comfortably observe by looking downwards into the eyepiece. The image in a diagonal mirror appears upright, but rotated around its vertical axis (mirror image).Focal length: Everything that magnifies an object via an optic lens has a certain focal length. The focal length is the length of the path the light travels from the surface of the lens to its focal point. The focal point is also referred to as the focus. In focus, the image is clear . In the case of a telescope, the focal length of the telescope tube and the eyepieces are used to determine magnification.Lens: The lens turns the light that falls on it around in such a way so that the light gives a clear image in the focal point after it has traveled a certain distance (focal length).568321724Parts Overview1. 114mm Objective Lens2. Pan-Tilt Alt-Azimuth Mount3. Tripod with Accessory Tray4. Focus Wheel5. 1.25” Eyepieces (9.7mm and 26mm)6. 2x Barlow Lens7. Red Dot Viewfinder8. Smartphone AdapterUsing your telescope:After you have aligned your viewfinder , you are ready to start observing! Put the 26 mm eyepiecewider field of view will make it easier to locate and track objects. Use the panhandle to move the scope up, down and side to side until your target comes into view in the eyepiece. It is important to remember that the rotation of the Earth means objects will move out of your eyepiece fairly quickly. Once you have found and focused on your desired target, you can track it as it journeys across the night sky using the panhandle.For a closer look at an object, you can insert the 9.7 mm eyepiece. The magnification will increase from 23x to 62x.For a more closer look at an object, you can insert the 2x Barlow lens. The magnification will increase to 46x for the 26 mm eyepiece and 124x for the 9.7 mm eyepiece.Cleaning:Your telescope is a precision optical device and keeping the optics free of dust and dirt is crucial for optimalperformance. To clean the lenses (objective and eyepiece) use only a photo-grade soft brush or a lint-free cloth, like a microfiber cloth. Do not press down too hard while cleaning, as this might scratch the lens. Ask your parents to help if your telescope is really dirty. f necessary, the cleaning cloth can be moistened with an optical glass cleaning fluid and the lens wiped clean using very little pressure. Do not use harsh detergents!Make sure your telescope is always protected against dust and dirt. After use, leave it in a warm room to dry off before storing.Eyepiece: An eyepiece is a system made for your eye and comprised of one or more lenses. In an eyepiece, the clear image that is generated in the focal point of a lens is captured and magnified still more.Magnification: The magnification corresponds to the difference between observation with the naked eye andobservation through a magnifying device like a telescope. If a telescope configuration has a magnification of 30x, then an object viewed through the telescope will appear 30 times larger than it would with the naked eye. To calculate the magnification of your telescope setup, divide the focal length of the telescope tube by the focal length of the eyepiece.Using/Aligning the Red Dot Viewfinder:The viewfinder is powered by a CR-1620 battery that is included. Before using the viewfinder for the first time, remember to remove the plastic insulator that is blocking the battery from connecting. Note: Please recycle batteries responsibly.For The Viewfinder To Be Effective, It Must Be Aligned.• Insert the 26 mm eyepiece into the diagonal and power on the viewfinder by sliding the switch on its right side to an “On” position.• Point the eyepiece at an easy to identify target like a telephone pole that is approximately 200 yards away. Center the object in the eyepiece. Lock the telescope into place by tightening the panhandle.• Without moving the telescope, position the red dot using the two adjustment screws so that it shares the same view as the one in your eyepiece. The front screw will move the viewfinder up and down, and the other will move it side to side. Your viewfinder is now aligned. Note: To preserve battery life, don’t forget to turn off the viewfinder after use.f=26 mmf=9.7 mmThe Moon f=26 mmf=9.7 mmTerrestrial Images Possible Objects for Observation:Terrestrial objectsTake note of the examples below, including Mount Rushmore and the golf course. Start with the 26 mm eyepiece and focus until the image is clear . After mastering the 26 mm eyepiece, switch to the 9.7 mm eyepiece and practice scanning and focusing until the image is clear . Choose several terrestrial objects to practicefocusing on, but never point your telescope at or near the sun, or you risk blindness.The MoonDiameter: 3,476 kmDistance: Approximately 384,401 kmThe Moon is the Earth’s only natural satellite, and it is the second brightest object in the sky (after the Sun). Although it is our closest neighbor , a lot of people have never really taken a good long like at the Moon. With your telescope, you should be able to see several interesting lunar features. These include lunar maria, which appear as vast plains, and some of the larger craters. The best views will be found along theterminator , which is the edge where the visible and cloaked portions of the Moon meet.Orion Nebula (M 42)M 42 in the Orion constellationRight ascension: 05:35 (Hours: Minutes) Declination: -5:22 (Degrees: Minutes)Distance from Earth: 1,500 light yearsLocated about 1,500 light years from Earth, the Orion Nebula (Messier 42,abbreviation: M 42) is the brightest diffuse nebula in the sky – visible with the naked eye, and a worthwhile object for telescopes of all types and sizes, from the smallest field glass to the largest earthbound observatories and the Hubble Space Telescope. When talking about Orion, we‘re actually referring to the main part of a much larger cloud of hydrogen gas and dust, which spreads out over half of the Orion constellation. The expanse of this enormous cloud stretches several hundred light years.Ring Nebula (M 57)M 57 in the Lyra constellationR ight ascension: 18:53 (Hours: Minutes) Declination: -33:02 (Degrees: Minutes)Distance from Earth: 2,400 light yearsThe famous Ring Nebula M 57 in the constellation of Lyra is often viewed as theprototype of a planetary nebula; it is one of the magnificent features of the Northern Hemisphere’s summer sky. Recent studies have shown that it is probably comprised of a ring (torus) of brightly shining material that surrounds the central star (only visible with larger telescopes), and not of a gas structure in the form of a sphere or an ellipsis. If you were to look at the Ring Nebula from the side, it would look like the Dumbbell Nebula (M27). When viewed from Earth, we are looking directly at the pole of the nebula.Dumbbell Nebula (M 27)M 27 in the Fox constellationRight ascension: 19:59.6 (Hours: Minutes) Declination: -+22:43 (Degrees: Minutes)Distance from Earth: 1,360 light yearsThe Dumbbell Nebula (M 27) in Fox was the first planetary nebula ever discovered. On July 12, 1764, Charles Messier discovered this new and fascinating class of objects. We see this nebula almost directly from its equatorial plane. If we could see the Dumbbell Nebula from one of its poles, we would see the shape of a ring, and we would seesomething very similar to what we know as the Ring Nebula (M 57). In reasonably good weather , we can see this object well even with low magnifications.f=26 mmf=9.7 mmOrion Nebula M 42f=26 mmf=9.7 mmRing Nebula in Lyra Constellation M 57f=26 mmf=9.7 mmDumbbell Nebula in Fox Constellation M 27Troubleshooting Guide:Using the Smartphone Adapter:SUPERVISION BY ADULTSRead and follow the instructions, safety rules and first aid informationThe Smartphone Adapter will allow you to connect almost any “smart” device to a 1.25” eyepiece.To use the adapter, place it directly onto the selected eyepiece and secure it by tightening the setscrew until snug.Be careful not to overtighten because this could damage the adapter and/or the eyepiece.The camera lens on your smart device will need to be centered over the eyepiece. This alignment is best done by opening the camera function and viewing the image while you center the device. Once you have positioned the device correctly, carefully press it onto the suction cup/non-skid surface of the adapter pad. Never allow the adapter pad to hold your device without you supporting the item as well.The point at which you secure the eyepiece/adapter combination into the diagonal depends largely on the dimensions of your device. For smaller devices like smart phones, it may be easier to secure it to the eyepiece/adapter combination before inserting the entire unit into the diagonal on the telescope. For larger devices, such as tablets, it may be easier to secure the eyepiece/adapter combination into the diagonal, and then align and attach your device.After positioning your device and capturing images, you can enhance and edit the photos using the imaging software of your choice. One option can be found at https:///.WARNING: Do not leave your device unsupported or unattended on the adapter pad.Though the surface of the adapter pad is designed with suction cups and is non-skid, the manufacturer cannot assure that the pad will support the weight of various devices or guarantee that it will adhere to all surfaces on various smart devices. The pad is not intended to secure, balance or support the device on its own, and the operator should not let the device rest solely on the adapter pad. Leaving the device unattended or allowing it to balance on its own without operator support may result in the device falling, unbalancing the entire instrument and possibly damaging the telescope or your smart device.CHEMICALSAny chemicals and liquids used in preparing, using, or cleaning should be kept out of reach of children. Do not drink any chemicals. Hands should be washed thoroughly under running water after use. In case of accidental contactwith the eyes or mouth rinse with water. Seek medical treatment for ailments arising from contact with the chemical substances and take the chemicals with you to the doctor.Keep packaging materials (plastic bags, rubber bands, etc.) away from children. There is a risk of SUFFOCATION. Dispose of packaging materials as legally required. Consult the local authority on the matter if necessary. DISPOSALDispose of the packaging materials properly, according to their type, such as paper or cardboard. Contact your local waste-disposal service or environmental authority for information on the proper disposal. Please take the current legal regulations into account when disposing of your device. You can get more information on the proper disposal from your local waste-disposal service or environmental authority.NotesNotesNotes©2018 National Geographic Partners LLC. All rights reserved. NATIONAL GEOGRAPHIC and Yellow Border Design are trademarks of the National Geographic Society, used under license.©2018 Explore Scientific, LLC.1010 S. 48th Street, Springdale AR 72762All rights reserved. | | 866.252.3811Made in ChinaCONFORMS TO THE SAFETY REQUIREMENTS OF ASTM F963。
Panasonic SC-HC25 操作说明书

Dear CustomerThank you for purchasing this system.For optimum performance and safety, readthese instructions fully before you connect,operate or adjust this system.Keep this manual for future reference.Your system and the illustrations can lookdifferently.Do the procedures with the remotecontrol. You can also use the buttonson the main unit if they are the same.SUPPLIED ACCESSORIESPlease check and identify the supplied accessories.1 x AC mains lead1 x FM indoor antenna1 x AM loop antennaCAUTION!THIS PRODUCT UTILIZES A LASER.USE OF CONTROLS OR ADJUSTMENTSOR PERFORMANCE OF PROCEDURESOTHER THAN THOSE SPECIFIED HEREINMAY RESULT IN HAZARDOUS RADIATIONEXPOSURE.DO NOT OPEN COVERS AND DO NOT REPAIRYOURSELF. REFER SERVICING TO QUALIFIEDPERSONNEL.THIS UNIT IS INTENDED FOR USE INMODERATE CLIMATES.The socket outlet shall be installed near theequipment and easily accessible.The mains plug of the power supply cord shallremain readily operable.To completely disconnect this apparatus from theAC Mains, disconnect the power supply cord plugfrom AC receptacle.This product may receive radio interferencecaused by mobile telephones during use. Ifsuch interference is apparent, please increaseseparation between the product and the mobiletelephone.Product identification marking is located on thebottom of unit.PlacementSet the system up on an even surface away fromdirect sunlight, high temperatures, high humidity,and excessive vibration. These conditions candamage the cabinet and other components, therebyshortening the service life of the system.Place it at least 15 cm away from wall surfaces toavoid distortion and unwanted acoustical effects.Do not place heavy items on the system.VoltageDo not use high voltage power sources. This canoverload the system and cause a fire.Do not use a DC power source. Check the sourcecarefully when setting the system up on a ship orother place where DC is used.AC mains lead protectionEnsure the AC mains lead is connected correctlyand not damaged. Poor connection and leaddamage can cause fire or electric shock. Do notpull, bend, or place heavy items on the lead.Grasp the plug firmly when unplugging the lead.Pulling the AC mains lead can cause electric shock.Do not handle the plug with wet hands. This cancause electric shock.SAFETY PRECAUTIONSWARNING:TO REDUCE THE RISK OF FIRE, ELECTRICSHOCK OR PRODUCT DAMAGE,• DO NOT EXPOSE THIS APPARATUSTO RAIN, MOISTURE, DRIPPING ORSPLASHING AND THAT NO OBJECTSFILLED WITH LIQUIDS, SUCH AS VASES,SHALL BE PLACED ON THE APPARATUS.• USE ONLY THE RECOMMENDEDACCESSORIES.• DO NOT REMOVE THE COVER (OR BACK);THERE ARE NO USER SERVICEABLEPARTS INSIDE. REFER SERVICING TOQUALIFIED SERVICE PERSONNEL.CAUTION!• DO NOT INSTALL OR PLACE THIS UNIT INA BOOKCASE, BUILT-IN CABINET OR INANOTHER CONFINED SPACE. ENSURETHE UNIT IS WELL VENTILATED. TOPREVENT RISK OF ELECTRIC SHOCK ORFIRE HAZARD DUE TO OVERHEATING,ENSURE THAT CURTAINS AND ANY OTHERMATERIALS DO NOT OBSTRUCT THEVENTILATION VENTS.• DO NOT OBSTRUCT THE UNIT’SVENTILATION OPENINGS WITHNEWSPAPERS, TABLECLOTHS, CURTAINS,AND SIMILAR ITEMS.• DO NOT PLACE SOURCES OF NAKEDFLAMES, SUCH AS LIGHTED CANDLES, ONTHE UNIT.• DISPOSE OF BATTERIES IN ANENVIRONMENTALLY FRIENDLY MANNER.Foreign matterDo not let metal objects fall inside the system. Thiscan cause electric shock or malfunction.Do not let liquids get into the system. This cancause electric shock or malfunction. If this occurs,immediately disconnect the system from the powersupply and contact your dealer.Do not spray insecticides onto or into the system.They contain flammable gases which can ignite ifsprayed into the system.ServiceDo not attempt to repair this system by yourself.If sound is interrupted, indicators fail to light,smoke appears, or any other problem that is notcovered in these instructions occurs, disconnectthe AC mains lead and contact your dealer or anauthorised service centre. Electric shock or damageto the system can occur if the system is repaired,disassembled or reconstructed by unqualifiedpersons.Extend operating life by disconnecting the systemfrom the power source if it is not to be used for along time.Bottom of productMAINTENANCETo clean this system, wipe with a soft, dry cloth.• Never use alcohol, paint thinner or benzine to clean this system.• Before using chemically treated cloth, read the instructions that came with the cloth carefully.MPEG Layer-3 audio coding technology licensed from Fraunhofer IIS and Thomson.XWVUFront view– If you see this symbol –11 TROUBLESHOOTING GUIDEBefore requesting service, make the following checks. If you are in doubt about some of the check points, or if the solutions indicated do not solve the problem, consult your dealer for instructions.■USBThe USB mass storage device or the contents in it cannot be read.• The format of the USB mass storage device or the contents in it is/are not compatible with the system.• USB mass storage devices with storage capacity of more than 32 GB cannot work in some conditions.Slow operation of the USB mass storage device.• Large content size or large memory USB mass storage device takes longer time to read.The elapsed time shown is different from the actual play time.• Transfer the data to another USB mass storage device or backup the data and reformat the USB mass storage device.■Main unit displays“NO PLAY”• Examine the content. You can only play supported format.• This system can read and play up to 255 albums or folders (audio and non-audio).“F76” or “F61”• There is a power supply problem.“ERROR”• An incorrect operation was done. Read the instructions and try again.“NOT MP3/ERROR”• An unsupported MP3 format. The system will skip that track and play the next one.“VBR–”• The system cannot show the remaining play time for variable bit rate (VBR) tracks.“NODEVICE”• The iPod or iPhone is not connected. Examine the connection.Memory reset (Initialisation)When the following situations occur, refer to the instructions below to reset the memory:• There is no response when buttons are pressed.• You want to clear and reset the memory contents.To reset the memory1 Disconnect the AC mains lead.(Wait 3 minutes before you continue with step 2.)2 While you press and hold [1] on the main unit, connect the AC mains lead again.“– – – – – – – –” shows on the display panel.3 Release [1].All the settings are set back to the factory preset.It is necessary to set the memory items again.■Common problemsNo operations can be done with the remote control.• Examine that the battery is installed correctly.Sound is distorted or no sound.• Increase the volume.• Switch off the system, determine and correct the cause, then switch the system on again. It can be caused by straining of the speakers through excessive volume or power, and when using the system in a hot environment.A “humming” sound can be heard during playback.• An AC mains lead or fluorescent light is near the cables. Keep other appliances and cords away from the cables of this system.■DiscsDisplay not shown correctly. Playback does not start.• You have not put in the disc correctly. Put it in correctly.• Disc is dirty. Clean the disc.• Replace the disc if it is scratched, warped, or non-standard.• There is condensation. Let the system dry for 1 to 2 hours.The total number of tracks shown is incorrect.The disc cannot be read.Distorted sound is heard.• You put in a disc that the system cannot play. Change to a playable disc.• You put in a disc that has not been finalised.■RadioA beat sound is heard.• Switch off the TV or move it away from the system.A low hum is heard during AM broadcasts.• Move the antenna away from other cables and cords.■iPod or iPhoneYou cannot switch on the iPod or iPhone.• Examine that the battery of the iPod or iPhone is not depleted.• Switch off the iPod or iPhone and the system before you connect the iPod or iPhone. Connect the iPod or iPhone and try again.No sound.• Switch off the iPod or iPhone and remove from the system. Connect the iPod or iPhone to the system and switch it on and play it again.Manual presetting30 FM and 15 AM stations can be preset.PreparationPress [RADIO, EXT-IN] to select “FM” or “AM”.1 Press [3] or [5] to tune in to thestation.2 Press [PROGRAM].3 Press the numeric buttons to select a presetnumber.Do steps 1 through 3 again to preset more stations.The new station replaces any station that occupies the same preset number.Selecting a preset stationPress the numeric buttons, [2] or [6] (main unit: [2/3] or [5/6]) to select the preset station.AM allocation setting (by main unit only)This system can also receive AM broadcasts allocated in 10 kHz steps.1 Press [RADIO, EXT-IN] to select “FM” or“AM”.2 Press and hold [RADIO, EXT-IN].After a few seconds, the display panel shows the current minimum radio frequency. Release the button when the minimum frequency changes.• To go back to the initial setting, do the above steps again.• After you change the setting, preset frequencies are erased.Manual tuning1 Press [RADIO, EXT-IN] to select “FM” or“AM”.2 Press [3] or [5] to select the frequencyof the required station.To tune automatically, press and hold the button until the frequency starts changing quickly.To improve the sound qualityWhen “FM” is selected1 Press [RADIO MENU] to select “FM MODE”.2 Press [Y , U ] to select “MONO” and thenpress [OK].To cancel, select “ST”.• “MONO” is also cancelled when you change the frequency.• Turn off “MONO” for normal listening.When “AM” is selected1 Press [RADIO MENU] to select “B.PROOF”.2 Press [Y , U ] to select “BP 1” or “BP 2” andthen press [OK].Automatic presetting30 FM and 15 AM stations can be preset.PreparationPress [RADIO, EXT-IN] to select “FM” or “AM”.1 Press [OK] to select “LOWEST” or“CURRENT” frequency.2 Press [RADIO MENU] to select “A.PRESET” and then press [OK].“START?” is shown.3 Press [OK] to start presetting.6 RADIO10 REMOTE CONTROL CODEWhen other Panasonic equipment responds to the remote control of this system, change the remote control code for this system.PreparationPress [RADIO, EXT-IN] to select “AUX”.To set the code to “REMOTE 2”1 Press and hold [RADIO, EXT-IN] on themain unit and [2] on the remote control until “REMOTE 2” is shown.2 Press and hold [OK] and [2] for a minimum of4 seconds.To set the code to “REMOTE 1”1 Press and hold [RADIO, EXT-IN] on themain unit and [1] on the remote control until “REMOTE 1” is shown.2 Press and hold [OK] and [1] for a minimum of4 seconds.。
1PPC控制器故障代码查询重要

Rexroth IndraControl VCP 20Industrial Hydraulics Electric Drivesand ControlsLinear Motion andAssembly Technologies PneumaticsServiceAutomationMobileHydraulicsRexroth VisualMotion 10 Multi-Axis Machine Control R911306327 Edition 01Troubleshooting GuideAbout this Documentation Rexroth VisualMotion 10 Troubleshooting Guide DOK-VISMOT-VM*-10VRS**-WA01-EN-PRexroth VisualMotion 10Multi-Axis Machine ControlTroubleshooting Guide DOK-VISMOT-VM*-10VRS**-WA01-EN-P Document Number, 120-2300-B323-01/ENPart of Box Set, 20-10V-EN (MN R911306370)This documentation describes …•the use of VisualMotion Toolkit for assitance in diagnostics •the proper steps for indentifing diagnostic faults • and the suggested remedies for clearing faults Description ReleaseDateNotes DOK-VISMOT-VM*-10VRS**-WA01-EN-P 08/2004Initial release© 2004 Bosch Rexroth AGCopying this document, giving it to others and the use or communicationof the contents thereof without express authority, are forbidden. Offendersare liable for the payment of damages. All rights are reserved in the eventof the grant of a patent or the registration of a utility model or design(DIN 34-1).The specified data is for product description purposes only and may notbe deemed to be guaranteed unless expressly confirmed in the contract.All rights are reserved with respect to the content of this documentationand the availability of the product.Bosch Rexroth AGBgm.-Dr.-Nebel-Str. 2 • D-97816 Lohr a. MainTel.: +49 (0)93 52/40-0 • Fax: +49 (0)93 52/40-48 85 • Telex: 68 94 21Bosch Rexroth Corporation • Electric Drives and Controls5150 Prairie Stone Parkway • Hoffman Estates, IL 60192 • USATel.: 847-645-3600 • Fax: 847-645-6201/Dept. ESG4 (DPJ)This document has been printed on chlorine-free bleached paper.Title Type of DocumentationDocument TypecodeInternal File Reference Purpose of Documentation Record of Revisions Copyright Validity Published byNoteRexroth VisualMotion 10 Troubleshooting Guide Table of Contents I Table of Contents1VisualMotion Tools for Diagnosing1-1 The Diagnostics Menu.............................................................................................................1-1System Diagnostics.................................................................................................................1-1Tasks Diagnostics...................................................................................................................1-3Drive Overview….....................................................................................................................1-42Monitoring and Diagnostics2-12.1System Diagnostics - Codes and Message...................................................................................2-1Parameters..............................................................................................................................2-2DriveTop..................................................................................................................................2-32.2Control Startup Messages.............................................................................................................2-4PPC Boot-Up Sequence..........................................................................................................2-4Control Firmware Sequence....................................................................................................2-42.3Status Messages (001-199)...........................................................................................................2-5001 Initializing System.............................................................................................................2-5002 Parameter Mode...............................................................................................................2-5003 Initializing Drives...............................................................................................................2-5004 System is Ready...............................................................................................................2-5005 Manual Mode....................................................................................................................2-5006 Automatic Mode: ABCD....................................................................................................2-5007 Program Running: ABCD.................................................................................................2-6008 Single-Stepping: ABCD....................................................................................................2-6009 Select Parameter Mode to Continue................................................................................2-6010 Breakpoint Reached: ABCD.............................................................................................2-6018 Please cycle power to continue........................................................................................2-6019 Executing User Initialization Task....................................................................................2-62.4Warning Messages (201-399).......................................................................................................2-7201 Invalid jog type or axis selected........................................................................................2-7202 Drive %d is not ready.......................................................................................................2-7203 Power Fail detected..........................................................................................................2-7204 Sercos ring was disconnected..........................................................................................2-8205 Parameter transfer warning in Task %c...........................................................................2-8207 Axis %d position limit reached..........................................................................................2-8208 Lost Fieldbus Connection.................................................................................................2-9209 Fieldbus Mapping Timeout...............................................................................................2-9210 File System Defrag: %d completed................................................................................2-10211 Program- & Data memory cleared..................................................................................2-10212 Option Card PLS Warning, see ext. diag.......................................................................2-10213 Sercos cycle time changed.............................................................................................2-11214 PCI Bus Cyclic Mapping Timeout...................................................................................2-11 DOK-VISMOT-VM*-10VRS**-WA01-EN-PII Table of Contents Rexroth VisualMotion 10 Troubleshooting Guide215 RECO I/O Failure, see ext. diag.....................................................................................2-11216 Control PLS %d warning, see ext. diag..........................................................................2-12217 PCI Bus Communication, see ext. diag..........................................................................2-12218 PCI Bus Register Mapping Timeout...............................................................................2-13219 PCI Bus Lifecounter Timeout.........................................................................................2-13220 Excessive deviation in PMG%d, see ext. diag...............................................................2-13221 Excessive Master Position Slip Deviation......................................................................2-13222 ELS Config. Warning, see ext. diag...............................................................................2-14223 PCI Bus reset occurred, cyclic data are invalid..............................................................2-14225 System booted................................................................................................................2-14226 RS485 Serial Communication Error (port X1%d)...........................................................2-15227 Control Over-temperature Warning................................................................................2-15228 Control - SYSTEM WARNING.......................................................................................2-152.5Shutdown Messages (400 - 599).................................................................................................2-16400 EMERGENCY STOP......................................................................................................2-16401 Sercos Controller Error: %02d........................................................................................2-16402 Sercos Config. Error: see ext. diag................................................................................2-16403 System Error see ext. diag.............................................................................................2-17405 Phase %d: Drive did not respond...................................................................................2-17407 Drive %d Phase 3 Switch Error......................................................................................2-17409 Sercos Disconnect Error.................................................................................................2-18411 Drive %d Phase 4 Switch Error......................................................................................2-18412 No drives were found on ring..........................................................................................2-18414 Parameters were lost......................................................................................................2-19415 Drive %d was not found..................................................................................................2-19416 Invalid Instruction at %04x..............................................................................................2-19417 SYSTEM ERROR: pSOS #%04x...................................................................................2-19418 No program is active.......................................................................................................2-20419 Invalid Program File: code = %d....................................................................................2-20420 Drive %d Shutdown Error...............................................................................................2-20421 User Program Stack Overflow........................................................................................2-20422 Parameter transfer error in Task %c..............................................................................2-21423 Unimplemented Instruction.............................................................................................2-21425 Instruction error: see Task %c diag................................................................................2-21426 Drive %d is not ready.....................................................................................................2-22427 Calc: invalid table index %d............................................................................................2-22428 Calc: division by zero......................................................................................................2-22429 Calc: too many operands................................................................................................2-22430 Calc: invalid operator......................................................................................................2-23431 Calc error: see Task %c diag.........................................................................................2-23432 Calc: too many nested expressions...............................................................................2-23433 Setup instruction outside of a task.................................................................................2-23434 Axis %d configured more than once...............................................................................2-23435 Axis %d is not assigned to a task...................................................................................2-24436 General Compiler Error: %04x.......................................................................................2-24438 Invalid Axis Selected: %d...............................................................................................2-24DOK-VISMOT-VM*-10VRS**-WA01-EN-PRexroth VisualMotion 10 Troubleshooting Guide Table of Contents III439 Axis %d: Invalid Motion Type.........................................................................................2-24440 I/O Transfer Error: see task diag....................................................................................2-25450 Event %d: invalid event type..........................................................................................2-25451 Invalid event number ‘%d’..............................................................................................2-25452 More than %d event timers armed.................................................................................2-25453 Homing param. transfer error: %d..................................................................................2-25454 Axis %d homing not complete........................................................................................2-26459 Axis %d target position out of bounds............................................................................2-26460 Invalid program %d from binary inputs...........................................................................2-26463 Ratio command: invalid ratio..........................................................................................2-26464 Can't activate while program running.............................................................................2-27465 Drive %d config. error, see ext. diag..............................................................................2-27467 Invalid ELS Master Option..............................................................................................2-27468 ELS adjustment out of bounds.......................................................................................2-27470 Axis %d velocity > maximum..........................................................................................2-28474 Drive %d cyclic data size too large.................................................................................2-28477 Axis D: probe edge not configured.................................................................................2-28478 Calc: operand out of range.............................................................................................2-28483 Parameter Init. Error: see Task %c diag........................................................................2-29484 Control SYSTEM ERROR..............................................................................................2-29486 Sercos Device %d is not a drive.....................................................................................2-29487 CAM %d is invalid or not stored.....................................................................................2-29488 CAM Error: See Task %c diag........................................................................................2-30489 More than %d CAM axes selected.................................................................................2-30490 System Memory Allocation Error....................................................................................2-30492 Programs were lost, see ext. diag..................................................................................2-30496 Can't execute this instruction from an event..................................................................2-31497 Limit switch config. error, see ext. diag.........................................................................2-31498 Drive %d Shutdown Warning..........................................................................................2-32499 Axis number %d not supported in this version...............................................................2-32500 Axis %d is not referenced...............................................................................................2-32501 Drive %d comm. error, see ext. diag..............................................................................2-33502 ELS and cams not supported in this version..................................................................2-33504 Communication Timeout.................................................................................................2-33505 Axis %d is not configured...............................................................................................2-33508 User Watchdog Timeout.................................................................................................2-33509 Control System Timing Error (%d).................................................................................2-34515 PLC Communications Error............................................................................................2-34516 More than %d registration functions enabled.................................................................2-34519 Lost Fieldbus/PLC Connection.......................................................................................2-35520 Fieldbus Mapping Timeout.............................................................................................2-35521 Invalid Virtual Master ID: %d..........................................................................................2-36522 Invalid ELS Master ID: %d..............................................................................................2-36523 IFS status, facility = 0x%x..............................................................................................2-36524 Hardware Watchdog timeout..........................................................................................2-36525 I/O Configuration error, see ext. diag.............................................................................2-36 DOK-VISMOT-VM*-10VRS**-WA01-EN-PIV Table of Contents Rexroth VisualMotion 10 Troubleshooting Guide526 Sercos Multiplex Channel Config, see ext. diag.............................................................2-37527 Control Initialization Error, see ext. diag.........................................................................2-38528 System Event %d Occurred...........................................................................................2-38529 Invalid ELS Group ID: %d...............................................................................................2-38530 CAM %d is active, can't overwrite..................................................................................2-39531 Invalid variable for Fieldbus/PCI Bus Mapping...............................................................2-39532 Power fail brown out condition detected.........................................................................2-39533 Multiple instances of index CAM: %d found...................................................................2-39534 Hardware Version Not Supported..................................................................................2-40539 Invalid Parameter Number..............................................................................................2-40540 Option Card PLS error....................................................................................................2-40541 Link Ring Error, see ext. diag.........................................................................................2-41542 PLC Cyclic Mapping Timeout.........................................................................................2-42543 PCI Bus Runtime Error...................................................................................................2-42544 RECO I/O Failure, see ext. diag.....................................................................................2-42545 Invalid Coordinated Articulation Function ID: %d...........................................................2-43546 Multiple Instance of Coordinated Articulation Function with ID: %d...............................2-43547 Task %c Coordinated Articulation Error, see ext. diag...................................................2-43548 Invalid Kinematic Number: %d.......................................................................................2-43549 Fieldbus Initialization Error.............................................................................................2-43550 User Initialization Task Timeout.....................................................................................2-44551 Master Slip Config. Error, see ext. diag..........................................................................2-44552 Excessive Master Position Slip Deviation......................................................................2-44553 Invalid Parameter Detected, see C-0-2002....................................................................2-44554 Excessive Deviation in PMG%d, see ext. diag...............................................................2-45555 PCI Bus Register Mapping Timeout...............................................................................2-45556 PCI Bus Lifecounter Timeout.........................................................................................2-45557 PMG%d Maximum allowed deviation window is Zero....................................................2-45558 PMG%d Only 1 axis parameterized...............................................................................2-46559 PMG%d Number of offsets does not match number of Axis..........................................2-46560 PMG%d Max. allowed dev. window is larger than 25% of Modulo................................2-46561 PMG%d Offset is larger than Modulo.............................................................................2-46562 PMG%d Parameterized Axis is not in system................................................................2-46563 Invalid Task Specified, Must be A-D..............................................................................2-46564 PMG%d Invalid configuration, see ext. diag...................................................................2-46565 Axis %d: Configuration error, see ext. diag....................................................................2-47566 Filter sample rate and cutoff frequency mismatch.........................................................2-47567 ELS Config. Error, see ext. diag.....................................................................................2-47568 Axis %d: Assigned Task is Not Defined.........................................................................2-48570 ELS Max. Vel. Exceeded, see ext. diag.........................................................................2-48571 No Program Found.........................................................................................................2-49572 PCI Bus reset occurred, cyclic data is invalid.................................................................2-49573 CAM %d is being built....................................................................................................2-49575 ELS Master for ELS Group %d is invalid........................................................................2-49576 Event for input I%d is already armed, cannot arm again...............................................2-50577 Restored non volatile memory from compact flash........................................................2-50DOK-VISMOT-VM*-10VRS**-WA01-EN-PRexroth VisualMotion 10 Troubleshooting Guide Table of Contents V578 Virtual Master %d Exceeded Its Max. Vel., see ext. diag...............................................2-50579 Group %d Exceeded Its Jog Velocity, see ext. diag......................................................2-51580 pROBE Error Occurred in Task:0x%04X.......................................................................2-51581 Probe Function for Axis # is locked by the PLC.............................................................2-51582 Integrated PLC: PLC Stopped in Operation Mode.........................................................2-51583 Integrated PLC: Internal System Error...........................................................................2-51584 ELS System Master %d is invalid, see ext. diag............................................................2-51585 Drive %d separate deceleration not supported..............................................................2-52586 Master Encoder Card Error, see ext diag.......................................................................2-522.6Integrated PLC Status Messages................................................................................................2-536001 Integrated PLC: Running..............................................................................................2-536002 Integrated PLC: Stopped..............................................................................................2-536002 Integrated PLC: Stopped at Breakpoint........................................................................2-532.7Integrated PLC Error Codes........................................................................................................2-530016 Integrated PLC: Software Watchdog Error...................................................................2-530019 Integrated PLC: Program Checksum Error..................................................................2-530020 Integrated PLC: Fieldbus Master Error.........................................................................2-540021 Integrated PLC: I/O Update Error.................................................................................2-542000 Integrated PLC: Internal SIS System Error..................................................................2-542001 Integrated PLC: Internal Acyclic Access Error.............................................................2-542002 Integrated PLC: Internal Acyclic Memory Error............................................................2-542003 Integrated PLC: PLC Configuration Error.....................................................................2-552004 Integrated PLC: File Access Error................................................................................2-552005 Integrated PLC: Internal Fatal Task Error....................................................................2-556011 Integrated PLC: PLC Program Stopped in Operation Mode........................................2-556012 Integrated PLC: General Error.....................................................................................2-552.8Communication Error Codes and Messages...............................................................................2-56!01 Sercos Error Code # xxxx...............................................................................................2-56!02 Invalid Parameter Number..............................................................................................2-57!03 Data is Read Only...........................................................................................................2-57!04 Write Protected in this mode/phase...............................................................................2-57!05 Greater than maximum value.........................................................................................2-57!06 Less than minimum value...............................................................................................2-57!07 Data is Invalid.................................................................................................................2-57!08 Drive was not found........................................................................................................2-57!09 Drive not ready for communication.................................................................................2-57!10 Drive is not responding...................................................................................................2-57!11 Service channel is not open...........................................................................................2-57!12 Invalid Command Class..................................................................................................2-57!13 Checksum Error: xx (xx= checksum that control calculated).........................................2-58!14 Invalid Command Subclass............................................................................................2-58!15 Invalid Parameter Set.....................................................................................................2-58!16 List already in progress..................................................................................................2-58!17 Invalid Sequence Number..............................................................................................2-58!18 List has not started.........................................................................................................2-58!19 List is finished.................................................................................................................2-58 DOK-VISMOT-VM*-10VRS**-WA01-EN-P。
罗斯蒙特涡街流量计说明书
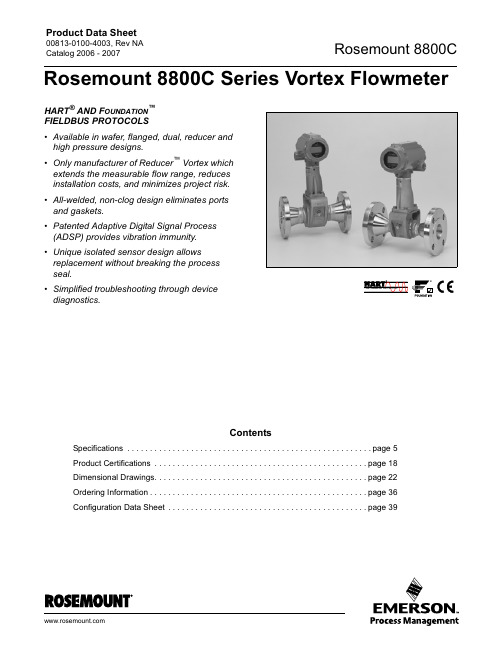
The transducer block calculates flow from sensor frequency. The calculation includes information about damping, shedding frequency, K-factor, service type, pipe ID, and diagnostics.
• Replaceable Sensor - The sensor is isolated from the process and can be replaced without breaking the process seals. All line sizes use the same sensor design allowing a single spare to serve every meter.
• Alignment rings, provided with each wafer-style flowmeter, ensure that the meter body is properly centered with the adjacent piping.
• Both wafer and flanged style meter bodies are available in 316L stainless steel and Nickel Alloy materials of construction.
• Available as flanged meter for 1 through 12 inch stainless steel and nickel alloy C materials of construction.
MSI NB FAE Team True Color Troubleshooting Guide

[Troubleshooting] True Color Troubleshooting GuideOutline1. Basic Troubleshooting (2)1.1. Uninstall True Color (2)1.2. Clean install system graphic drivers (2)1.3. Install True Color (2)2. Common Q&A (3)2.1. Operation errors: (3)"Unable to load configuration file." (3)"The files native.bin and backup.bin do not exist: C:\ProgramData\Portrait Displays\Truecolor\native.bin" (3)"This system is not supported" (4)“Application only supports authentic MSI devices” (5)MSI True Color isn’t working properly (can’t open, no function) after Windows10 AU update. (8)How to fix the error message after installing True Color in Windows 7? (8)2.2. Other Problems: (9)What is “Desktop Partition” function? (9)There is always a Desktop Partition preview window showing up next to the window I'm dragging, how can I disable it? (10)“Disable Desktop Partition” setting doesn’t take effect (11)The color has no change when I switch between sRGB and AdobeRGB mode. . 12This guide only applies to True Color supported series.Please check the specification under the Overview page of your Notebook: https:///LaptopsIf it is True Color supported, you can find True Color feature introduction under your Notebook Overview page; if no such introduction exists, then the Notebook is none True Color series.1. Basic Troubleshooting1.1. Uninstall True ColorFor user who has common True Color error or fail to run True Color program, please uninstall old True Color program by Windows control panel.1.2. Clean install system graphic driversPlease unsintall old INTEL & NVIDIA graphic drivers and install the latest version on MSI Notebook Driver download page.[How To] Clean install Intel VGA driver[How To] Clean install NVIDIA VGA driver1.3. Install True ColorInst all the latest version from “Utility” download page of your MSI Notebook website. Please refer to the installation guide: MSI True Color Installation Guide*NOTE: Once the driver & True Color app re-installation complete, restart the system twice to load the color calibration file correctly.2. Common Q&AIf you are having the error message listed below when installing or running MSI True Color on authentic MSI notebooks, please follow the instructions in below content to solve the problem.2.1. Operation errors:Problem: "Unable to load configuration file."Solution:Please follow MSI True Color Installation Guide to uninstall True Color, delete hidden folder and reinstall.Problem: "The files native.bin and backup.bin do not exist:C:\ProgramData\Portrait Displays\Truecolor\native.bin"Solution:Please download and re-install the latest MSI True Color released on MSIwebsite to solve the problem.Problem: "This system is not supported"Solution:(1). Make sure that your notebook supports MSI True Color by checking theOverview page in the note book product page.(2). If you have external monitor connected, remove the external disaplyconnection and then run the installer once again.Problem: “Application only supports authentic MSI devices”Solution:The error message means the application detects the system manufacturer is not MSI or cannot detect the information properly.Please make sure it’s MSI brand notebook and confirm the on board BIOS is from MSI official website. Then follow below steps to re-configure the environment variables of your system:(1).R ight click on Start, and select "System"(2).S elect "Advanced System Settings"(3).S elect "Environment Variables..."(4).H ighlight "Path" Under the "System Variables" listing and click "Edit"(5).C lick new and add the following path:%SystemRoot%\System32\Wbem(6).C lick New again to add an additional path:%systemRoot%\System32(7).C lick OK to close the "Edit Environment Variable" window(8).C lick OK again to close the "Environment Variables" window.(9).N ow, you can try instlall MSI True Color again.***If above actions doesn’t help, you can also try to restore the system back to the factory settings by using the recovery media created by MSI BurnRecovery tool or the F3 recovery function to solve the program.For MSI preinstalled Windows:[Video Tutorial] How to Use Recovery Partition on Windows 8/8.1[Video Tutorial] How to restore Windows 10 system on MSI Notebooks For FreeDOS or empty system:How to Install Windows OS on Free DOS platformFreeDOS Install Windows Video GuideProblem: MSI True Color isn’t working properly (can’t open, no function) after Windows 10 AU update.Solution:It is compatibility problem with NVidia generic driver v.37x.xx (372.54 / 372.70) Please update MSI True Color v1.6.3.005 or later version. See also (FAQ-2391) Problem: How to fix the error message after installing True Color in Windows 7?Solution:Please update your IE (Internet Explorer) to IE 9.0 or later version.2.2. Other Problems:Question: What is “Desktop Partition” function?Answer:Problem: There is always a Desktop Partition preview window showing up next to the window I'm dragging, how can I disable it?Solution:Please open MSI True Color, click "Show Settings" to expand the menu and then select "Tools" tab. Cancel the check box of "Desktop Partition on" under "Desktop Partition" to disable the preview window.Problem: “Disable Desktop Partition” setting doesn’t take effect.When user right click on True Color icon from Windows system tray to enter setup menu, and click “Disable Desktp Partition”, “Desktop Partition” function doesn’t stop.Solution:Please enter advanced setting in True color control panel to disable the function.Problem: The color has no change when I switch between sRGB and AdobeRGB mode.Impact Series:MSI Notebook GT73VR 4K panel seriesSolution:Please follow the guide: MSI True Color Installation Guide to uninstall True Color and reinstall.。
三星250U USB 3G 4G 用户手册说明书

Troubleshooting GuideSprint 3G/4G USB 250U by Sierra WirelessIf you are unable to resolve your issue using the Troubleshooting steps below, please contact Sprint Customer Service at 1-866-639-9565for assistance.1.The Sprint SmartView TM software does not detect the USB 250U.Please be sure that you install the Sprint SmartView software from the CD in the box before inserting the 250U device.If you’ve installed the Sprint SmartView software onto your desktop and your computer is not detecting the USB 250U, here are several reasons why this behavior may occur: •If the device is plugged in at boot up sometimes the device is not recognized. You will need to:Validate that you are running Sprint SmartView version 2.40 (which comes with the USB 250U on the CD) or aboveRemove the device from your computerClose Sprint SmartView and re-start itRe-insert the device•The USB 250U is not fully inserted into the USB port on your PC.The USB 250U must be fully inserted into the USB port of your computer in order for the drivers to be installed and the Sprint SmartView software to recognize the USB 250U.If necessary, remove and reinsert the USB 250U into the USB port on the computer.If this does not resolve the problem, try using another USB port (if available).If the USB 250U is still not recognized, remove the USB 250U and reboot the computer. Once the computer is booted up, plug in the 250U USB again.Ensure the USB 250U is plugged directly into a computer— not a USB hub.•Another application is conflicting with the Sprint SmartView software.Ensure that applications such as ActiveSync, HotSync, WinFax and/or otherconnection managers and other WiMAX software are not running in the System Tray (that is, the icons located by the clock on the Windows taskbar) while using theSprint SmartView software.If the steps above do not resolve the issue, please contact Sprint Customer Service at1-866-639-9565 for assistance.2.I am having trouble activating my USB 250U.•Please ensure your device has been set-up on your Sprint account.•Make sure you are within the Sprint coverage area.•Remove the device, close all applications, reboot your computer and try activating again.If the steps above do not resolve the issue, please contact Sprint Customer Service at1-866-639-9565 for assistance.3.I receive an error when I try to connect to the Internet.Although there are a variety of error messages that you may encounter, most of them can be resolved by following the steps below.•There is not sufficient signal strength to connect.If low signal strength is displayed in the Sprint SmartView window, move to a location with better coverage. For a map of coverage in your area, using analternate Internet connection browse to the Sprint Coverage Tool at/coverage, enter your zip code and click Go.Try the external antenna (sold separately).•You encounter a problem with your data services.o Go to Sprint SmartView.o On the menu bar, select Tools, Settings, Hardware, Mobile devices/Modify.o Select Update profile.If the steps above do not resolve the issue, please contact Sprint Customer Service at1-866-639-9565 for assistance.4.I am able to connect, but not able to browse any web pages.Begin by clearing browser cookies, history, and cache typically found in your browser tools/Internet options. Below are some other potential resolutions:•The internet browser is incorrectly configured.Check the connection settings of your browser to ensure that no conflicting settings exist.For Internet Explorer, click Tools > Internet Options and select the Connections tab. Ensure that either Never dial a connection is selected, orthat the Sprint PCS connection is set as the default. Also ensure that no proxyinformation is specified by clicking the Settings button and ensuring that theUse a proxy server for this connection checkbox is not selected.For Mozilla Firefox, click Tools > Options and select the General tab. Click the Connection Settings button and ensure that Direct connection to theInternet is selected.For other browsers, consult the software manufacturer for assistance.•Random loss of IP address in fringe 4G network coverage.Sprint SmartView software may show the device is connected, but you are not able to browse, because there is no connection. This issue should only happen when you are located in fringe coverage of the Sprint 4G network. You will need to disconnect and reconnect to Sprint SmartView.•Users on Mac OS do not receive an indication from the User Interface that their connection has been lost when returning from sleep mode in fringe 4G coverage.You will need to disconnect and reconnect to Sprint SmartView.•The firewall or Internet security application is interfering with the browsing.Try to disable any applications that may be restricting your access to the Internet,such as Windows Firewall, Anti-Virus software. If the problem is resolved by thisaction, contact the software manufacturer for assistance configuring the software to allow for the desired connection.•While plugged into a LAN.Your LAN may be set to have a higher priority than your wireless connection. Please click on this link to determine the appropriate priority -/app/answers/detail/a_id/625•Disconnect all other Internet connections.While using the Sprint SmartView software, disconnect all other Internet connections (such as Wi-Fi or LAN connections) before you access the Sprint Mobile BroadbandNetwork.If the steps above do not resolve the issue, please contact Sprint Customer Service at1-866-639-9565 for assistance.5.With Windows 7 32-bit OS using a Dell Latitude e6400 and e6500, SprintSmartView software may hang in “initializing” or “no device found” state when resuming from hibernation/sleep mode in fringe 4G coverage areas.You will need to remove and re-insert the device. A reboot may also be required.If the steps above do not resolve the issue, please contact Sprint Customer Service at1-866-639-9565 for assistance.B port freezes after a suspend/resume on Windows® XP.Due to a known Windows XP issue with power management functionality, some users may experience USB ports that appear to freeze or stop working properly. The problem can be corrected by a simple Windows Registry change.Please go to /kb/817900 for instructions.If the steps above do not resolve the issue, please contact Sprint Customer Service at1-866-639-9565 for assistance.er experiencing degraded performance when using an external antenna.This could be caused when the user is not using the specific dual-connector antenna designed and certified for this device.If the steps above do not resolve the issue, please contact Sprint Customer Service at1-866-639-9565 for assistance.。
- 1、下载文档前请自行甄别文档内容的完整性,平台不提供额外的编辑、内容补充、找答案等附加服务。
- 2、"仅部分预览"的文档,不可在线预览部分如存在完整性等问题,可反馈申请退款(可完整预览的文档不适用该条件!)。
- 3、如文档侵犯您的权益,请联系客服反馈,我们会尽快为您处理(人工客服工作时间:9:00-18:30)。
T ROUBLESHOOTINGR EFINISHP ROBLEMSCause,Repair &PreventionPROBLEM INDEXPROBLEM ALTERNATE TERM1. Air Entrapment Craters2. Bleeding Discoloration3. Blistering Pimples,Bubbles,Bumps4. Blushing Milkiness5. Chalking Fading,Oxidation,Weathering6. Chemical Staining/Etching Acid Rain,Spotting,Discoloration7. Chipping Nicks,Stone Pecks,Chips,Bruises8. Color Mismatch Off Color,Off Shade9. Cracking Checking,Crazing,Splitting,Alligatoring,Crowsfeet10. Dust Contamination Dirt in Finish11. Edge Mapping Edge Ringing,Featheredge Lifting12. Fisheyes Silicon Contamination,Cratering13. Lifting Shriveling,Swelling,RaisingAlligatoring,Wrinkling14. Loss of Gloss Hazing Dulling,Dieback,Matting,Weathering15. Mottling Streaking,Tiger/Zebra Stripes,Floating,Flooding16. Orange Peel Poor Flow,Texture17. Peeling Delamination,Flaking18. Pinholing in Body Filler Bubbles,Air Pockets19. Rail Dust20. Runs/Sags Hangers,Curtains,Signatures21. Sanding Marks Streaked Finish,Sandscratches22. Sandscratches Swelling,Sinking,Shrinkage23. Seediness Gritty,Dirty,Grainy,Speckled24. Shrinkage Bulleyes,Ringing,Edge Mapping25. Soft Film Slow Dry26. Solvent Popping Boiling,Blowing,Gassing27. Staining/Plastic Bleed Through Discoloration28. Tape Tracking Tracks29. Transparency Poor Hiding,Poor Coverage,Translucent30. Water Spotting Water Marking31. Wrinkling Crinkling,Puckering,ShrivelingAIR ENTRAPMENT(Craters)Small crater like openings in or on the paint film.____________________________________________________________________________ CAUSE______________________________________________________ Trapped or buried air pockets in the wet paint film that rise to the surface and "burst" causing small craters. Lack of atomization is the cause of air entrapment and may be due to one or more of the following:(A) Spray gun travel too slow(B) Spray gun distance too close(C) Air pressure to low(D) Improper spray gun setupREPAIR__________________________________________(1) Sand with 1200 or finer grit sand paper,then compound and polish to restore gloss.(2)Or,sand smooth and refinish.PREVENTION__________________________________________(A)Maintain correct spray gun speed.(B) Maintain correct spray gun distance.(C) Use the recommended air pressure.(D) Use the correct air cap/nozzle/needle recommended for clear coats.Note:Some cases of air entrapment may have an appearance very similar to solvent pop or dust contamination. However,air entrapment normally occurs when the film is still wetand can be removed with compounding procedures. On the other hand,solvent pop willappear after the film is "skinned over" and when sanded will have pinholes. Dust cont-amination will appear while the film is drying but,still "tacky." These craters,underclose examination,will have a speck of dirt in the center of the crater.“Large”wet dropletsAir rises from film leaving a small craterBLEEDING(Discoloration)A Red or Yellow discoloration in the topcoat color.____________________________________________________________________________ CAUSE______________________________________________________ (A) Solvent in the new topcoat dissolves soluble dyes or pigments in the original finish,allowing them to seep into and discolor the new topcoat.REPAIR__________________________________________(1) Allow color to cure,isolate with two component undercoat(s) and refinish.(2) Or,remove original paint film and refinish.PREVENTION__________________________________________ ____ (A) Isolate suspected bleeding finish by applying a two component surfacer and/or sealer.Allow to cure following product recommendations,then apply desired topcoat.Solvent White PigmentRed PigmentNew FinishOld FinishPinkOld pigment dissolves into new finish.BLISTERING(Pimples,Bubbles,Bumps)Swelled areas appearing as pimples or bubbles in the topcoat film,often months after application. ____________________________________________________________________________ CAUSE_____________________________________________________(A) Moisture trapped beneath the paint film due to:1) Improper dry time after wet sanding;2) Contaminated air lines;3) Spraying in extreme high humidity conditions.(B) Using a poor grade and/or too fast evaporating thinner/reducer for spray conditions.(C) Trapped solvents from applying wet heavy coats with insufficient flash time between coats.(D) Improper dry time of undercoats before topcoating.(E) Painting over grease,oil or rust.REPAIR_________________________________________(1) Remove affected area and refinish.(2) Extreme cases must be stripped to bare substrate before refinishing. PREVENTION______________________________________________ (A) If wet sanding is preferred,allow sufficient time for moisture to evaporate. Avoid wetsanding lacquer type primer surfacer when possible. Drain moisture from compressor and air lines regularly. Allow additional flash time between coats and/or add retarder whenspraying in humid conditions,or spray at times of low humidity when possible.(B) Select proper thinner/reducer for spray conditions.(C) Apply materials according to product recommendations,allowing sufficient flash timebetween coats.(D) Allow undercoats to thoroughly dry/cure before topcoating.(E) Clean and prep substrate using recommended products and procedures.Moisture accumulates and expands,pushing up paint film.Trapped MoistureTopcoat UndercoatBLUSHING(Milkiness)A milky gray cloud appears on the surface of the paint film immediately or shortly after application.____________________________________________________________________________ CAUSE_____________________________________________________ (A) When spraying during humid conditions,air from the spray gun and solvent evaporationlowers the substrate temperature below the dew point,causing moisture in the air tocondense in or on the paint film. The condition is aggravated when too fast drying orunbalanced thinner/reducer is used.REPAIR_________________________________________ (1) Should blushing occur during application:(a) apply heat to the affected area,or (b) addretarder and apply additional coats.(2) If the finish has dried,minor blushing may be corrected by compounding or polishing,however,severe blushing will require sanding and refinishing.PREVENTION______________________________________________(A) Always use good quality solvent and thin/reduce material according to label directions.(B) Select proper thinner/reducer for spray condition.(C) Add the recommended amount of retarder when spraying in humid conditions.(D) Apply heat after application to evaporate moisture.Moisture SolventAs thinner evaporates,moisture in theair condenses in the paint film.CHALKING(Fading,Oxidation,Weathering)A chalky white appearance on the surface of the paint film____________________________________________________________________________ CAUSE_____________________________________________________ (A) Pigment is no longer held and protected by resin,resulting in a powder-like surface and lackof gloss due to:(1) Natural weathering of the paint film;(2) Improper application of paint material;(3) Using generic thinner/reducer and/or hardener in the paint material;(4) Excessive use of mist/fog coats when applying single stage metallic finishes. REPAIR_________________________________________(1) Compound to remove oxidation and polish to restore gloss.(2) Or,sand to remove "weathered" paint film and refinish.PREVENTION______________________________________________(A) Weekly washing and occasional polishing or waxing will remove oxidation from the finish.(B) Thoroughly stir,shake or agitate all paint materials.(C) Use the recommended thinner/reducer,hardener,and measure accurately.(D) When spraying single stage metallic finishes,apply mist/fog coats panel bypanel while finish is still wet.Flake Clear Resin PigmentPigment and Flake protected by clear resin.When clear resin wears away,pigmentand flake are exposed to the environmentand deteriorate rapidly.CHEMICAL STAINING/ETCHING(Spotting,Acid Rain,Discoloration)Irregular shaped pitting,etching or discoloration on the paint film.____________________________________________________________________________CAUSE_____________________________________________________ A chemical change occurs when harmful environmental contaminants,such as acid rain,tree sap, bird droppings,road tar,etc. remain on the surface for an extended period of time.REPAIR_________________________________________(1) Wash the vehicle with soap and hot water,rinse and dry.(2) Solvent clean with appropriate surface cleaner.(3) Wash with baking soda solution and rinse thoroughly. (One tablespoon baking soda per onequart water.)(4) Compound damaged surface and polish to restore gloss.(5) If polishing does not remove the damage,wet sand with 1500-2000 grit sandpaper,thencompound and polish to restore gloss.*(6) If refinishing is necessary,sand to remove damaged area with appropriate grit sandpaper,wash with a baking soda solution,then refinish. In severe cases,the finish must be removed to bare metal.PREVENTION______________________________________________ (A) Remove harmful water soluble contaminants by regularly washing with detergent and clearwater.(B) Polish or wax periodically.(C) Avoid parking under trees or near factories that produce chemical fallout.(D) Refinish with an acrylic urethane basecoat/clearcoat system to provide the maximumprotection.* When sanding and buffing a basecoat/clearcoat finish,a minimum filmthickness of the clearcoat (2 mils) is required to maintain adequate ultraviolet protection.If correcting the damage will result in removing more than .5 mils,refinishing isrecommended.Acid rain dropletsChemical StainingDamage caused by acid rain.PaintPaintCHIPPING(Nicks,Stone Pecks,Chips,Bruises)Small areas of damage to the paint film leaving a nick,notch or void in the finish.____________________________________________________________________________ CAUSE_____________________________________________________ (A) Loss of adhesion of the paint film to the substrate caused by an impact from stones or otherhard objects.REPAIR_________________________________________ (1) Sand and featheredge damaged areas to remove chips,then refinish. PREVENTION______________________________________________(A) Use premium two component undercoat and topcoat system.(B) Use a flex agent in undercoat and/or topcoat system in areas that are prone to chipping.COLOR MISMATCH(Off Shade,Off Color)The original finish and repair exhibit a noticeable difference in color when viewed under the same lighting conditions.____________________________________________________________________________ CAUSE_____________________________________________________(A) Original finish has "drifted" from manufacturer's standard.(B) Old finish weathered and oxidized.(C) Color over or under reduced.(D) Improper spray procedures.(E) Color not properly stirred or shaken.(F) Improper spray gun set up.(G) Inaccurate mixing of the color formula.(H) "Panel" painting instead of blending.(I) Evaluating color under a light source other than "color corrected" lighting or natural light. (J) Adjusting a color before it has been sprayed,or adjusting a basecoat before applying clearcoat.REPAIR_________________________________________ (1) If color is close enough to blend:(1) prepare adjacent panel(s) for blending,then (2) blendcolor into adjacent panels.(2) If color must be tinted:(1) tint the color for a blendable match,(2) prepare adjacentpanel(s) for blending,then (3) respray the repair,blending into the adjacent panel(s). PREVENTION______________________________________________ (A) Check alternate color selector for variances. Choose the alternate that provides a blendablematch.(B) All color must be viewed under equal gloss; compound or polish the area to be matched.(C) Thin/reduce according to label direction.(D) Follow label directions for proper application of color coat.(E) Stir or shake materials thoroughly to be sure all pigments and metallics are in solution andsuspension.(F) Refer to product label or data sheet for spray gun,fluid nozzle,and air caprecommendations.(G) Recheck color code,formula number,formula weights before mixing colors.(H) Spray a test panel prior to application to determine if blending or tinting is necessary.(I) Always use natural daylight or color corrected lights to make color matching decisions. (J) All color must be sprayed out for an accurate evaluation. Basecoats must have clearcoat applied. Check color from all angles,face (90 degrees) and side tone (20-60 degrees).CRACKING(Checking,Crazing,Spitting,Alligatoring,Crowsfeet)Cracks or lines of various lengths and widths in the topcoat finish often resembling the cracking of dried mud.____________________________________________________________________________ CAUSE_____________________________________________________(A) Excessive film thickness of the undercoat and/or topcoat.(B) Refinishing over a previously crazed/cracked surface.(C) Insufficient flash time between coats and/or force drying undercoats using air from thespray gun.(D) Mixing incorrectly or using too much hardener.(E) Paint ingredients not thoroughly stirred or agitated.(F) Breakdown of finish due to prolonged exposure to sunlight,moisture,and extremetemperature changes.(G) Using generic reducers and/or hardeners.REPAIR_________________________________________ (1) Remove all cracked paint film and refinish..PREVENTION______________________________________________(A) Apply all materials following label direction.(B) Completely remove crazed/cracked finishes before refinishing.(C) Do not force dry undercoats by fanning with spray gun air.(D) Mix ingredients thoroughly using the recommended additives. Add each component inproper sequence following the recommended mixing ratio.(E) Stir or agitate materials thoroughly before use to ensure all ingredients are in solution.(F) Use premium two component undercoat and topcoat system to provide maximum gloss anddurability.(G) Use the recommended thinner/reducer and hardener,and then measure accurately.Topcoat Film ShrinkageUndercoatDUST CONTAMINATION(Dirt in finish)Foreign particles embedded in paint film.____________________________________________________________________________ CAUSE_____________________________________________________(A) Inadequate cleaning of the surface to be painted.(B) Dirty spraying environment.(C) Inadequate air filtration or unfiltered air entering the booth.(D) Dirty or unsuitable work clothes that contain dust,lint,or fibers.(E) Particles from deteriorated air supply lines.(F) Using a poor grade masking paper.(G) Dirty spray gun.(H) Removing the vehicle from the spray booth before the finish is "dust free".REPAIR_________________________________________(1) Sand with 1200 or finer grit sandpaper,then compound and polish to restore gloss.(2) Or,sand smooth and refinish.PREVENTION______________________________________________ (A) Thoroughly blow off around windows,doors,jambs,hood,trunk,moldings,enginecompartment,and wheel openings. Wipe the surface to be painted and the masking paperwith the tack rag.(B) Maintain a clean working area.(C) Install proper air filters. Never use residential-type furnace filters in the spray booth.Repair any leakage found in the spray booth due to poor fitting doors,gaskets,seams or filters.(D) Wear a lint free paint suit during the spray application.(E) Use quality masking materials. "Wicks" found on newspaper can break away and blowinto the wet paint.(F) Repair or replace defective air lines.(G) Properly clean and maintain spray equipment.(H) Vehicle should be kept in a clean environment until finish is "dust free"NOTE:Fine dust particles that fall on a tacky surface can be encapsulated by the finish, creating an appearance almost identical to solvent pop. This "solvent pop" appearanceusually occurs on vehicles that are removed from the booth in a tacky condition andplaced in another location to dry. Fine dust contamination can be removed by sandingand polishing. However,If the condition is solvent pop the finish will contain pinholesor small craters after sanding.Dust ParticlesNew FinishOld FinishDust particles adhere to a wet or tacky finish.Dust ParticlesClearcoatBasecoatDust particles become encapsulated by a wet or tackyclearcoat.EDGE MAPPING(Edge Ringing,Featheredge Lifting)Raised or lifted edges in the wet or dry paint film that outline sand throughs or featheredges.____________________________________________________________________________ CAUSE_____________________________________________________ (A) Solvent from the new topcoat penetrates a solvent sensitive substrate causing a lifting orwrinkling that outlines the featheredge.REPAIR_________________________________________(1) Sand smooth or remove the affected area. (Final sand with 400 or finer grit sandpaper.)(2) Isolate affected area with two component primer surfacer and refinish.(3) Or,apply water borne primer surfacer,sand smooth and refinish.(4) Or,apply acrylic lacquer primer surfacer thinned with non-penetrating thinner,sand smoothand refinish.PREVENTION______________________________________________ Check questionable finishes by rubbing a small inconspicuous area with a shop towel saturated with lacquer thinner. Finishes susceptible to lifting will soften,wrinkle or shrivel as lacquer thinner is applied. If any of these reactions occur,the following recommendations should be considered. (A) Use acrylic urethane primer surfacer,water borne primer surfacer,or an acrylic lacquerprimer surfacer thinned with non-penetrating thinner over sensitive substrates.(B) Use 400 or finer grit sandpaper when featheredging.(C) Avoid sanding through insoluble topcoat color or clear,exposing solvent sensitive orsoluble finishes.Insoluble Undercoat New FinishSolventEdge lifting caused by swelling of a soluble finishunderneath an insoluble undercoat.Soluble Old FinishInsoluble UndercoatNew FinishSolventSoluble Old FinishFISHEYES(Silicone Contamination,Cratering)Small circular,crater-like openings that appear during or shortly after the spray application.____________________________________________________________________________ CAUSE_____________________________________________________(A) Spraying over surfaces contaminated with oil,wax,silicone,grease,etc.(B) Use of thinner/reducer in place of a solvent cleaner.(C) Spraying over previously repaired areas containing "fisheye eliminator" additive.REPAIR_________________________________________(1) Remove wet paint film with solvent,clean and refinish.(2) Add the recommended fisheye eliminator and respray the affected area.(3) If fisheyes appear in a basecoat,allow the color to flash then spray a mist coat over affectedarea. Do not use fisheye eliminator in undercoats or basecoat color.(4) If the paint has dried,sand to a smooth finish below the fisheye cratering and refinish. PREVENTION______________________________________________ (A) Thoroughly clean the surface to be painted with detergent and hot water,followed by therecommended solvent cleaner. Wipe dry with clean rags.(B) Use fisheye eliminator that is specifically recommended for the topcoat.(C) Install an air filtering system that removes and prevents oil and moisture contamination.(D) Maintain air supply by draining,cleaning and changing filter(s) on a routine basis.Old FinishNew FinishFisheye CrateringSilicone OilLIFTING(Wrinkling,Raising,Alligatoring,Shriveling,Swelling)The existing paint film shrivels,wrinkles or swells during new finish application or drying.____________________________________________________________________________ CAUSE_____________________________________________________ (A) Solvents in a newly applied product attack the previous finish causing wrinkling,raising,orpuckering of the paint film due to:(1) Recoating enamels or urethanes that are not fully cured;(2) Exceeding maximum flash or recoat times during application;(3) Recoating a basecoat/clearcoat finish,where existing clearcoat has insufficient filmbuild.REPAIR_________________________________________ (1)Remove lifted areas and refinish.PREVENTION______________________________________________ Check questionable finishes by rubbing a small inconspicuous area with a shop towel saturated with lacquer thinner. Finishes susceptible to lifting will soften,swell or shrivel as lacquer thinner is applied. If any of these reactions occur,the following recommendations should be considered.(A) Do not exceed a product's maximum recoat time during or after application.(B) Allow enamels or urethanes to thoroughly cure before recoating or attempting a repair.(C) Avoid applying undercoats or topcoats excessively wet.(D) Avoid the use of lacquer products over an air dried enamel finish.(E) When insoluble material (enamel/urethane) has been applied over a soluble material(lacquer):(1) avoid sanding through and exposing areas of the soluble material. (2) apply two component primer surfacer and/or sealer as a barrier between the new and the oldfinish. When applying two component undercoats over soluble finishes,the complete panel must be coated.(F) Use water borne undercoats to repair extremely sensitive finishes.Old FinishNew FinishSolventOld FinishNew FinishSolvent penetration causes lifting ofimproperly cured finishes.LOSS OF GLOSS(Hazing,Dulling,Dieback,Matting,Weathering)A dulling of the gloss as the film dries or ages.CAUSE_____________________________________________________(A) Topcoat applied in heavy,wet coats.(B) Inadequate flash time between coats.(C) Insufficient film thickness of topcoat color or clearcoat.(D) Insufficient drying/curling of undercoats before applying topcoats.(E) Using a poor grade and/or too fast evaporating thinner/reducer for spray conditions.(F) Improper cleaning of the substrate.(G) Insufficient air movement during and after application.(H) Spraying over a deteriorated or solvent sensitive substrate finish without proper priming orsealing procedures.(I) Natural weathering of the finish.REPAIR_________________________________________(1) Allow finish to cure thoroughly,compound or polish to restore gloss.(2) Or,sand and refinish.PREVENTION______________________________________________ (A) Apply the topcoat according to product label directions using the recommended gun set-upand air pressure.(B) Allow all coatings sufficient flash between coats.(C) Apply sufficient number of coats to achieve recommended proper film thickness.Check with film thickness gauge if possible.(D) Allow undercoats to thoroughly dry/cure before topcoating.(E) Select recommended thinner/reducer based on temperature,humidity,air movement,andsize of repair.(F) Clean substrate thoroughly before and after sanding.(G) For air dry situations:(1) allow exhaust fan to run 40 minutes or longer after spraying;(2) open booth doors after finish is dust free; and (3) maintain a shop temperature of 60degrees fahrenheit or above,especially when drying overnight.(H) For maximum holdout,use a premium two component undercoat system.(I) Properly wash and care for the finish on a regular basis.(J) Using premium topcoat color or clearcoat system will provide maximum gloss and durability.MOTTLING(Streaking,Tiger/Zebra Stripes,Floating,Flooding)A streaked spotty,or striped appearance in a metallic color.____________________________________________________________________________ CAUSE_____________________________________________________(A) An uneven distribution of metallic flake caused by:(1) Using a spray gun that gives an unbalanced spray pattern;(2) Improper application technique such as tilting the spray gun during application,causing the spray pattern to become heavy at the top or bottom.(3) Holding the gun too close to the surface (flooding);(4) Uneven spray pattern overlap;(5) Omitting/Improper use of mist coats.(B) Too much thinner/reducer. Color over thinned/reduced.(C) Applying clearcoat to a basecoat that has not thoroughly flashed/dried.(D) Improper application of basecoat (e.g. failure to apply or an improper use of a low pressuremist coat,wet basecoat application).REPAIR_________________________________________ (1) To uniform single stage metallic finishes,apply a higher pressure mist coat,panel by panel,while previous coat is still wet.(2) Or,allow basecoat color to flash,then apply a low pressure mist coat.(3) Finishes that have dried must be sanded and refinished. Caution:Large areas of basecoatmust have clearcoat applied before sanding. However,small nibs or lint may be removedfrom basecoat by wet sanding,concentrating only on the defect. Apply additional basecoat to the sanded area before clearcoating.PREVENTION______________________________________________ (A) Use recommended spray gun,including fluid tip and air cap for the material being sprayed.Always adjust the gun for best atomization and balanced spray pattern before paintapplication.(B) Use the correct ratio of thinner/reducer.(C) Allow basecoat proper flash/dry time before clearcoating.(D) Follow basecoat application procedures.Unbalancedspray patternNew FinishUneven distribution of metallic flake causesstreaks and mottling.ORANGE PEEL( Poor Flow,Texture)Paint film having an uneven texture that resembles the skin of an orange.____________________________________________________________________________ CAUSE_____________________________________________________(A) Under reduction and/or air pressure too low.(B) Thinner/reducer evaporates too fast for spray conditions.(C) Excessive film thickness or piling on of heavy wet coats.(D) Improper spray gun set-up.(E) Improper painting technique.REPAIR_________________________________________(1) Compound or polish to reduce surface texture.(2) Or,sand smooth with 1200 or finer grit sandpaper,compound and polish to restore gloss.(3) Or,sand smooth and refinish.PREVENTION______________________________________________(A) Use proper reduction ratio and spray at recommended air pressure.(B) Select recommended thinner/reducer based on temperature,humidity,air movement,and sizeof repair.(C) Avoid heavy coats and excessive film thickness.(D) Use recommended spray gun,fluid tip and air cap for the material being sprayed. Alwaysadjust the gun for best atomization and balanced spray pattern before paint application. (E) During paint application,hold the gun perpendicular and parallel to the surface. Adjustspeed of pass,pattern overlap,and distance from the panel to achieve the desired appearance.。