MAX1818EUT18-TG16中文资料
Modutrol IV M6161、M6181、M6184、M6191、M6194电机说明书
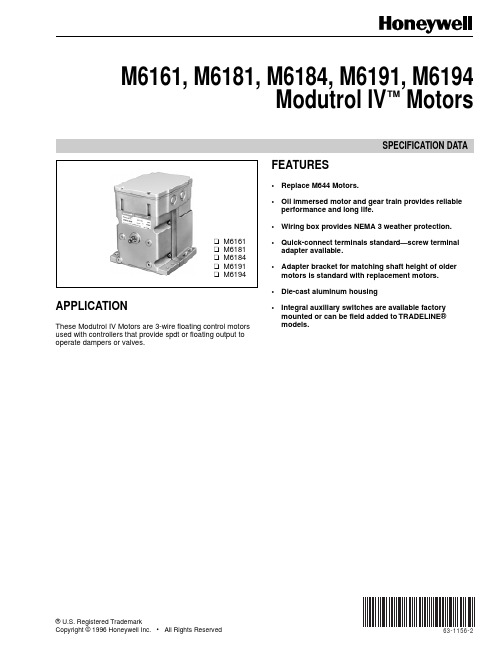
® U.S. Registered TrademarkCopyright © 1996 Honeywell Inc. • All Rights ReservedSPECIFICATION DATA63-1156-2M6161, M6181, M6184, M6191, M6194Modutrol IV ™ Motorsu M6161u M6181u M6184u M6191u M6194FEATURES•Replace M644 Motors.•Oil immersed motor and gear train provides reliable performance and long life.•Wiring box provides NEMA 3 weather protection.•Quick-connect terminals standard—screw terminal adapter available.•Adapter bracket for matching shaft height of older motors is standard with replacement motors.•Die-cast aluminum housing•Integral auxiliary switches are available factory mounted or can be field added to TRADELINE®models.APPLICATIONThese Modutrol IV Motors are 3-wire floating control motors used with controllers that provide spdt or floating output to operate dampers or valves.2M6161, M6181, M6184, M6191, M6194 Modutrol IV™ MOTORS63-1156—2SPECIFICATIONSTRADELINE ® ModelsTRADELINE models are selected and packaged to provide ease of stocking, ease of handling, and maximumreplacement value. TRADELINE model specifications are the same as those of standard models, unless otherwisespecified. M6184D1035 and M6194D1017 are TRADELINE models. TRADELINE models have auxiliary switch cams.Standard ModelsM6161A,B M6181A,D,F M6184A,B,D,F M6191A,B,D M6194A,B,D,E,FN N N NControl Type Suffix Letter 61is Series 60A:Fixed stroke(90° or 160°),Power Rating No auxiliary switches 6is low torque:B:Fixed stroke35 lb-in.(90° or 160°),8is high torque:1 auxiliary switch 150 lb-in. at standard D:Adjustable stroketiming (60 sec for 160°)(90° to 160°),9is extra high torque:No auxiliary switches 300 lb-in. at 2 or 4E:Adjustable strokeminute timing (90° to 160°),Output Drive2 auxiliary switches 4is dual-ended shaft,F:Adjustable strokenon-spring return (90° to 160°),1is single-ended shaft,2 auxiliary switchesnon-spring returnNOTE:Some motors are furnished to HVAC equipmentmanufacturers with no adapter bracket, a single-ended shaft and/or no wiring box.Dead Weight Load on Shaft:Power or Auxiliary End: 200 lb (90.8 kg) maximum.Maximum Combined Load: 300 lb (136 kg).Ambient Temperature Ratings:Maximum: 150°F (66°C) at 25% duty cycle.Minimum: Minus 40°F (-40°C).Crankshaft: 3/8 in. (9.5 mm) Square.M6184, M6194 have dual-ended shaft.M6161, M6181, M6191 have single-ended shaftController Type:Floating 3-wire (Series 60)—drive open, hold, drive closed.Stroke:Fixed stroke models available with 90° or 160° stroke. Other models available with stroke field adjustable from 90° to 160°.Start position of shaft changes with adjustment of stroke.(Midpoint of stroke remains fixed as stroke is adjusted.)Stroke is adjusted using cams located in wiring compartment.Dimensions:See Fig. 1.Underwriters Laboratories Inc. Listed:File No. E4436, Guide No. XAPX.Canadian Standards Association Certified:General Listing File No. LR1620, Guide No. 400-E.Timing and Torque:M6161, M6181, M6184, M6191, M6194 Modutrol IV™ MOTORS363-1156—2Accessories:ES650117 Explosion-proof Housing: Encloses motor for use in explosive atmospheres. Not for use with Q601,Q618, and Q455 Linkages. Order separately from Nelson Electric Co. Requires Honeywell 7617DM Coupling.Q607 External Auxiliary Switch: Controls auxiliary equipment as a function of motor position.Internal Auxiliary Switch Kits: Can be field-installed on TRADELINE models.220736A—One-switch Kit.220736B—Two-switch Kit.Q605 Damper Linkage: Connects motor to damper.Includes motor crank arm.Q618 Linkage: Connects Modutrol motor to water or steam valve.Q601 Bracket and Linkage Assembly: Connects Modutrol motor to water or steam valve.Q100A,B Linkage: Connects Modutrol motor to butterfly valve.Q68 Dual Control Potentiometer: Controls 1 through 9additional motors.Q181 Auxiliary Potentiometer: Controls 1 or 2 additional motors.221455A Infinitely Adjustable Crank Arm: Approximately 0.75 in. (19 mm) shorter than the 4074EL Y Crank Arm.Can rotate through downward position and clear base of motor without requiring use of adapter bracket.7617ADW Adjustable Crank Arm: Approximately 0.75 in.(19 mm) shorter than the 7616BR Crank Arm. Can rotate through downward position and clear base of motor without requiring use of adapter bracket.220741A Screw Terminal Adapter: Converts the standard quick-connect terminals to screw terminals.Transformers: Mounted internally, provide 24 Vac power to motor.198162JA—24 Vac; 50/60 Hz (for electrical isolation).198162EA—120 Vac; 50/60 Hz.198162GA—220 Vac; 50/60 Hz.198162AA—120/208/240 Vac; 50/60 Hz.BASE ENDFig. 1. Dimensions in in. (mm). Note: M6161, M6181, M6191 models do not have auxiliary shaft.All other dimensions are the same.463-1156—2Honeywell Europe S.A.3 Avenue du Bourget B-1140 Brussels BelgiumHoneywell Asia Pacific Inc.Room 3213-3225Sun Hung Kai Centre No. 30 Harbour Road Wanchai Hong KongHome and Building ControlHoneywell Limited-Honeywell Limitée 155 Gordon Baker Road North York, Ontario M2H 2C9Honeywell Latin American Division Miami Lakes Headquarters14505 Commerce Way Suite 500Miami Lakes FL 33016Helping You Control Your World63-1156—2 G.R. Rev. 5-96Home and Building Control Honeywell Inc.Honeywell Plaza P.O. Box 524Minneapolis MN 55408-0524Printed in U.S.A. on recycled papercontaining at least 10% post-consumer paper fibers By using this Honeywell literature, you agree that Honeywell will have no liability for any damages arising out of your use or modification to, the literature. You will defend and indemnify Honeywell, its affiliates and subsidiaries, from and against any liability, cost, or damages, including attorneys’ fees, arising out of, or resulting from, any modification to the literature by you.。
TA Instruments产品说明书
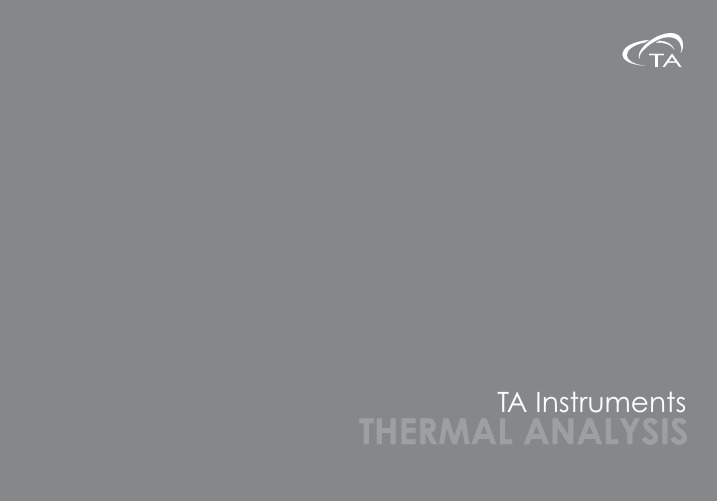
New Castle, DE USA Lindon, UT USA Crawley, United Kingdom Shanghai, China Beijing, ChinaTaipei, TaiwanTokyo, JapanSeoul, Korea Bangalore, IndiaParis, France Eschborn, Germany Brussels, BelgiumEtten-Leur, Netherlands Sollentuna, Sweden Milano, Italy Barcelona, Spain Melbourne, Australia Mexico City, MexicoDifferential Scanning Calorimetry (DSC) Q20004 Q206 DSC Technology8 Accessories10 Temperature Control Options14 Tzero®& MDSC® Technology18 Applications20Thermogravimetric Analysis (TGA) Q5000 IR32 Q50034 Q5036 Q5000 IR Technology38 Performance42 Q500 / Q50 Technology44 TGA Accessories & Options46 Applications52 TGA-HP58 Applications60Simultaneous DSC/TGAQ60064 SDT Technology66 Applications68Vapor Sorption AnalysisVTI-SA+72 VTI-SA+Technology74 Q5000 SA78 Q5000 SA Technology80 Applications86 Dynamic Mechanical Analysis (DMA) Q80092 Deformation Modes & Sample Size94 Subambient Operation95 Q800 Technology96 Modes of Deformation98 Accessories100 DMA Theory104 Modes of Operation105 Applications106Thermomechanical Analysis (TMA) Q400EM / Q400112 Q400 Technology114 Modes of Deformation116 TMA Theory / Modes of Operation118 Applications122CALORIMETRYDSC Q2000 SPECIFICATIONS TechnologiesTzero ®TechnologyAdvanced MDSC ®Available Direct Cp MeasurementIncluded Platinum™ Software IncludedHardware Features SVGA Touch Screen Included User Replaceable Tzero Cell Yes 50-Position Autosampler Available Autolid Included Dual Digital Mass Flow Controllers Included Full Range of Cooling Accessories (LNCS, RCS90, RCS40, FACS, QCA)Available Pressure DSC Available Photocalorimeter Available Performance Temperature Range Ambient to 725 ˚C With Cooling Accessories -180 to 725 ˚C Temperature Accuracy +/- 0.1 ˚C Temperature Precision +/- 0.01 ˚C Calorimetric Reproducibility (indium metal)+/- 0.05 %Calorimetric Precision (indium metal)+/- 0.05 %Dynamic Measurement Range>+/- 500 mW Baseline Curvature (Tzero; -50 to 300 ˚C)10 μW Baseline Reproducibility with Tzero+/- 10 μW Sensitivity 0.2 μW Indium Height / Width (mW/˚C)* 60The Q2000 is a research-grade DSC with superiorperformance in baseline flatness, precision,sensitivity, and resolution. Advanced Tzero ®technology and multiple exclusive hardware andsoftware features make the Q2000 powerful,flexible, and easy-to-use. Modulated DSC ®anda reliable 50-position autosampler are availableas options. An additional high-value feature isPlatinum™ software, which permits automaticscheduling of tests designed to keep the Q2000consistently in top operating condition. Availableaccessories, such as a new photocalorimeter,pressure DSC, and the widest array of coolingdevices, make the Q2000 a DSC well-equippedto satisfy the most demanding researcher.*Indium height/width ratio: 1.0 mg In heated at 10 ˚C/min in N 2atmosphere. (A larger number denotes better performance).DSC Q20 SPECIFICATIONSHardware FeaturesQ20AQ20Q20P Tzero ®Cell (fixed position)Included Included—User Replaceable Cell——Yes 50-Position Autosampler —Included—Autolid —Included—Dual Digital Mass Flow Controllers Included Included—Full Range of Cooling Accessories Available AvailableQCA Only (LNCS, RCS90, RCS40, FACS, QCA)Pressure DSC ——Yes Platinum Software —Included—MDSC Available Available —Performance Temperature Range Amb to 725 ˚C Amb to 725 ˚C Amb to 725 ˚C With Cooling Accessories -180 to 725 ˚C -180 to 725 ˚C -130 to 725 ˚C Temperature Accuracy +/- 0.1 ˚C +/- 0.1 ˚C +/- 0.1 ˚C Temperature Precision +/- 0.05 ˚C +/- 0.05 ˚C +/- 0.05 ˚C Calorimetric Reproducibility (indium metal)+/- 1 % +/- 1 %+/- 1 %Calorimetric Precision (indium metal)+/- 0.1 %+/- 0.1 %+/- 0.1 %Dynamic Measurement Range +/- 350 mW +/- 350 mW +/- 350 mW Digital Resolution>0.04μW >0.04μW >0.04μW Baseline Curvature (-50 to 300 ˚C)<0.15 mW <0.15 mW —Baseline Reproducibility< 0.04 mW <0.04 mW —Sensitivity1.0 μW 1.0 μW 1.0 μW Indium Height / Width (mW/˚C)* 8.08.0—*Indium height/width ratio: 1.0 mg In heated at 10 ˚C/min in N 2atmosphere. (A larger number denotes better performance).The Q20 (Q20, AQ20, Q20P) is a cost-effective,easy-to-use, general-purpose DSC module, with calorimetric performance superior to many competitive research-grade models. These are entry-level instruments not based on performance,but on available options. The Q20 is idealfor research, teaching, and quality controlapplications that require a rugged, reliable, basicDSC. The AQ20 is designed for unattendedanalysis of up to 50 samples in a sequentialmanner. The Q20 and AQ20 include dual digitalmass flow controllers and are available withMDSC ®. The Q20P is designed for studies ofpressure-sensitive materials or samples that mayvolatilize on heating.Cooling Rods Cooling Ring Furnace Tzero Thermocouple Constantan Sensor Chromel Area ThermocouplePhotocalorimeterThe Photocalorimeter Accessory (PCA), for the Q2000 DSC, permits characterizationof photocuring materials between -50 and 250 ˚C. UV/Visible light (250-650 nm) froma 200W high pressure mercury source is transmitted to the sample chamber via anextended range, dual-quartz light guide with neutral density or band pass filters. Tzero ®technology permits direct measurement of light intensity at both the sample and referencepositions. It also provides for simultaneous measurement of two samples.RCS40 ArrayRCS90TZERO ®DSC PERFORMANCE APPLICATIONSMDSC ®APPLICATIONSSTANDARD PANS/LIDS APPLICATIONSDSC pans & lids are available in aluminum, alodine-coated aluminum, gold, platinum, graphite, and stainless steel versions. They can be used under a variety of temperature and pressure conditions. Samples can be run in the standard DSC mode in open pans, crimped or hermetically sealed pans / lids or in pressure capsules. Samples in open pans can also be run at controlled pressures using the PDSC Cell. All aluminum standard pans have the same temperature and pressure rating. General details of the pans are shown here.TZERO ®PANS/LIDS APPLICATIONS© 2010 TA Instruments. All rights reserved.L90010.001。
LT1618中文资料
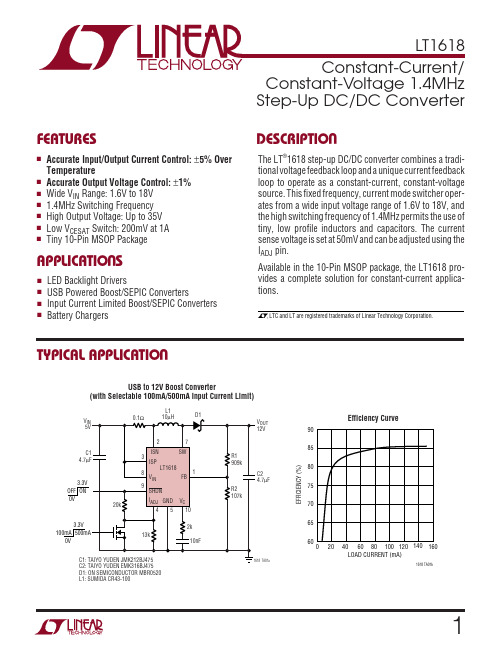
1618 TA01a
U
Efficiency Curve
60 80 100 120 140 160 40 LOAD CURRENT (mA)
1618 TA01b
U
1
元器件交易网
LT1618
ABSOLUTE
(Note 1)
AXI U RATI GS
U W U PACKAGE/ORDER I FOR ATIO
ELECTRICAL CHARACTERISTICS
temperature range are assured by design, characterization, and correlation with statistical process controls. Note 3: Bias currents flow into the ISP and ISN pins.
The q denotes specifications which apply over the full operating temperature range, otherwise specifications are at TA = 25°C. VIN = 1.6V, VSHDN = 1.6V, unless otherwise noted.
TYPICAL PERFOR A CE CHARACTERISTICS
Switch Saturation Voltage (VCE, SAT)
500
1.270
SATURATION VOLTAGE (mV)
400 TJ = 125°C 300 TJ = 25°C
FEEDBACK VOLTAGE (V)
VOLTAGE
PEAK CURRENT (A)
TK11818中文资料

TL: Tape Left
VIN
OSC
DK STARTUP CIRCUIT
OSCILLATOR
FEEDBACK CONTROL
REFERENCE VOLTAGE
VOUT T1
January 1999 TOKO, Inc.
Page 1
元器件交易网
TK11816, TK11817, TK11818, TK11819
0.3
UNITS mA mA V V mA mA %
mV/° C mV/° C
TK11819 ELECTRICAL CHARACTERISTICS
Test Conditions: VIN = 5 V, TA = 25 °C (Notes 3 & 5), unless otherwise specified.
TYP 4.7 12.1 16.8 9.30 4.5 6.0 0.06 1.81 2.31
MAX 9.0 19.0 17.6 9.80
0.3
UNITS mA mA V V mA mA %
mV/° C mV/° C
Page 2
January 1999 TOKO, Inc.
元器件交易网
SYMBOL
PARAMETER
TEST CONDITIONS
MIN
IIN
Supply Current
VOUT
Output Voltage
IOUT
Output Current
Load Reg Load Regulation
VOUT = 16.8 V, IOUT = 0.1 mA
VOUT = 9.3 V, IOUT = 1.0 mA
TK11816 TK11817 TK11818 TK11819
MT8852B中文说明书
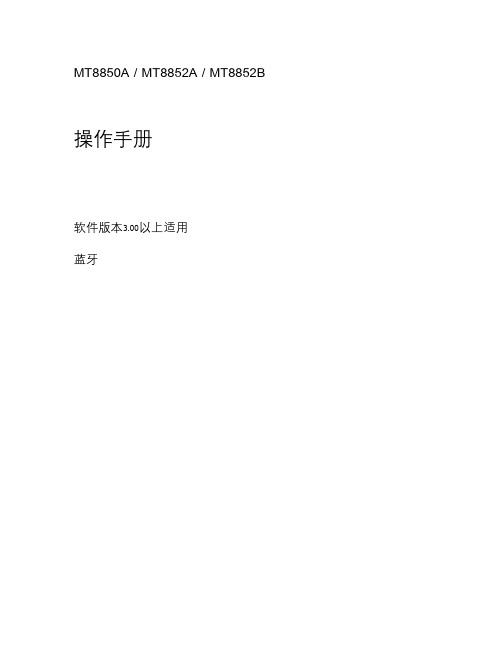
MT8850A / MT8852A / MT8852B 操作手册软件版本3.00以上适用蓝牙MT8850A / MT8852A /MT8852B蓝牙测试组操作手册供MT8850A、MT8852A、MT8852B 软件版本3.00及以上使用創作者: Anritsu Ltd,EMD,Stevenage,U.K.P/N: 13000-00109修訂: HCREATED August 2004COPYRIGHT 2004ANRITSU本手冊之重要通知使用者應了解本手冊為最初草稿版本,本手冊中某些章節的資訊在手冊付印時尚無法取得。
本手冊提供以下軟體版本之操作與功能細節:MT8850A: 3.00MT8852A: 3.00MT8552B: 4.00本手冊中所記載之某些功能於先前版本之軟體上可能無法提供。
產品保證Anritsu 公司的產品係為依據本保證書的內容,提供本產品其製作材質和作工品質缺陷,自產品出貨起1 年的產品保證。
Anritsu 提供的產品保證內容,係提供產品保證期間內,包括經證明產品瑕疵,其相關產品修護或更換服務。
產品用戶應先行支付運費,將有瑕疵的產品送回到Anritsu,以進行產品保證品質的修護服務。
本產品保證服務只限於原有的產品購買人,Anritsu 對於其後續用戶的使用產品瑕疵,不提供任何產品保證的擔保服務。
產品有限保證責任聲明上述的產品保證責任,不適用於Anritsu 的裝置接頭,係因為正常使用而損害者。
同樣地,本產品保證服務不適用於因為購買人不當的使用、未經授權的裝置修改或使用錯誤,或未依據產品的使用環境規範,而造成產品損害者。
本產品未再明文指示和暗示提供任何其他的品質保證責任,本產品修護保證服務,係僅限於本產品的原有購買人,所獨屬專有的權利。
註冊商標聲明藍芽註冊商標係由藍芽技術聯盟(SIG)所有,V Connector 與K Connector 係為Anritsu有限公司之註冊商標,Adobe Acrobat 與Acrobat Reader 係為Adobe 系統企業之商標。
ADM1818中文资料

REV.0Information furnished by Analog Devices is believed to be accurate and reliable. However, no responsibility is assumed by Analog Devices for its use, nor for any infringements of patents or other rights of third parties which may result from its use. No license is granted by implication or otherwise under any patent or patent rights of Analog Devices.aADM1810–ADM1813/ADM1815–ADM1818One Technology Way, P.O. Box 9106, Norwood, MA 02062-9106, U.S.A.Tel: 781/329-4700World Wide Web Site: Fax: 781/326-8703© Analog Devices, Inc., 1999Microprocessor Reset CircuitsFUNCTIONAL BLOCK DIAGRAMSV CCGNDV CCGNDV CCGNDV CCGNDFEATURESReliable Low Cost Voltage Monitor with Reset Output Supports Monitoring of Supplies Within 5%, 10%, 15%and 20% ToleranceActive High and Low Push-Pull Output Choices (ADM1810, ADM1812, ADM1815 and ADM1817)Open Drain Output Choices (ADM1811, ADM1813,ADM1816 and ADM1818)Can Be Used with a Manual Push-Button to Generate a Reset (ADM1813, ADM1818)Initialize Microprocessor Systems with Added Safety APPLICATIONSMicroprocessor Systems Computers ControllersIntelligent Instruments Automotive SystemsGENERAL DESCRIPTIONThe ADM181x range of voltage monitoring circuits can be used in any application where an electronic system needs to be reset when a voltage increases above or below a predetermined value.Because of the “reset delay time” incorporated into the ADM181x series, these devices can provide a safe startup for electronic systems. Before a system initializes, the power supply must stabi-lize. Using the ADM181x series ensures that there are typically 150 ms for the power supply to stabilize before the system is reset and safe system initialization begins.The ADM181x series of microprocessor reset circuits are avail-able in low cost, space-saving SOT-23 packages.ADM1810–ADM1813/ADM1815–ADM1818–SPECIFICATIONS(T A = –40؇C to +85؇C unless otherwise noted)Parameter Min Typ Max Units Test Conditions/NoteSUPPLYVoltage 1.2 5.5VCurrent3040µA(ADM1810/ADM1811/ADM1813)V CC < 5.5 V, RST Output Open3040µA(ADM1812) V CC < 5.5 V2835µA(ADM1815/ADM1816/ADM1817/ADM1818)V CC < 5.5 V, RST Output OpenOUTPUT CURRENT8mA@ 0.4 V, V CC≥ 2.7 V*350µA(ADM1810/ADM1812/ADM1815/ADM1817)@ 2.4 V, V CC≥ 2.7 VOUTPUT VOLTAGE V CC – 0.5V CC – 0.1V(ADM1810/ADM1812/ADM1815/ADM1817)@ 0 µA to 500 µAV CC TRIP-POINTADM1810-5, ADM1810-10, ADM1810-15/ADM1811/ADM1812/ADM1813-5 4.50 4.62 4.75V(5%)ADM1811/ADM1812/ADM1813-10 4.25 4.35 4.49V(10%)ADM1811/ADM1812/ADM1813-15 4.00 4.13 4.24V(15%)ADM1815/ADM1816/ADM1817/ADM1818-5 2.98 3.06 3.15V(5%)ADM1815/ADM1816/ADM1817/ADM1818-10 2.80 2.88 2.97V(10%)ADM1815/ADM1816/ADM1817/ADM1818-20 2.47 2.55 2.64V(20%)INTERNAL PULL-UP RESISTORADM1811/ADM1813/ADM1816/ADM1818 3.5 5.57.5kΩOUTPUT CAPACITANCE10pFRESET ACTIVE TIME100150300msV CC DETECT TO RSTFalling510µs(ADM1810/ADM1811/ADM1812/ADM1813)715µs(ADM1815/ADM1816/ADM1817/ADM1818) Rising100150300ms t R = 5 µsPUSH-BUTTON DETECT TO RST1µs(ADM1813/ADM1818)PUSH-BUTTON RESET100150300ms(ADM1818) 2.7 V ≤ V CC≤ 3.3 V100150300ms(ADM1813)NOTES*For ADM181x-20, V CC = V CCTP, sink current reduces to 8 mA.Specifications subject to change without notice.REV. 0–2–REV. 0ADM1810–ADM1813/ADM1815–ADM1818–3–ORDERING GUIDENOTESRL7 or REEL7 are in reels of 3000 parts. REEL are in reels of 10000 parts.All models in bold are ex-stock. Consult factory for availability.*Only Available in Reels.ABSOLUTE MAXIMUM RATINGS*V CC . . . . . . . . . . . . . . . . . . . . . . . . . . . . . . . +1.2 V to +5.5 V Input Current . . . . . . . . . . . . . . . . . . . . . . . . . . . . . . . . 40 µA Operating Temperature Range . . . . . . . . . . . –40°C to +85°C Power Dissipation, RT-3, SOT-23 . . . . . . . . . . . . . . 320 mW Derate by 4 mW/°C Above +70°CθJA Thermal Impedance . . . . . . . . . . . . . . . . . . . . . . 333°C/W Lead Temperature (Soldering, 10 sec) . . . . . . . . . . . +300°C Vapor Phase (60 sec) . . . . . . . . . . . . . . . . . . . . . . . +215°C Infrared (15 sec) . . . . . . . . . . . . . . . . . . . . . . . . . . . +220°C Storage Temperature Range . . . . . . . . . . . . –65°C to +150°C ESD Rating . . . . . . . . . . . . . . . . . . . . . . . . . . . . . . . . . . .3 kV*Typical values are measured at T A = +25°C unless otherwise noted.PIN CONFIGURATIONV CC Figure 2.Power-Up Timing DiagramREV. 0ADM1810–ADM1813/ADM1815–ADM1818–4–C 3459–8–3/99P R I N T E D I N U .S .A .ADM1813 AND ADM1818The ADM1813 and ADM1818 are low cost voltage monitoring devices with the inclusion of an optional push-button reset function.Figure 3.ADM1813/ADM1818 Typical ApplicationAn optional push-button reset switch can be connected be-tween RST and ground. Pressing this switch will pull the reset output low. If the push-button reset button pulls the RST output low for a period greater than 1 µs, then, when the reset button releases the RST line to float high, the RST line will stay low for a further 150 ms typical.Figure 4.Push-Button Reset Timing DiagramThe ADM1818 range has options which allow the user to monitor 3.3 V supplies with 10% and 20% tolerance options.While the ADM1813 range has options which allow the user to monitor 5 V supplies with 5%, 10% and a 15% tolerance options.ADM1810, ADM1812, ADM1815 AND ADM1817The ADM1812 is a 5 V low cost voltage monitor with an active high push-pull output. The ADM1812 supports 5%, 10% and15% tolerances. The ADM1810 is similar to the ADM1812,except that the ADM1810 has an active low push-pull output.The ADM1817 is 3.3 V voltage monitor with an active high push-pull output. The ADM1817 supports 5%, 10% and 20%tolerances. The ADM1815 is similar to the ADM1817, except that the ADM1815 has an active low push-pull output.The ADM1810/ADM1812/ADM1815/ADM1817 can be con-nected directly to most microprocessor-reset inputs without the need for external components.Figure 5.ADM1810/ADM1812/ADM1815/ADM1817Typical ApplicationOUTLINE DIMENSIONSDimensions shown in inches and (mm).3-Lead Plastic Surface Mount Package (SOT-23)(RT-3)ADM1811 AND ADM1816The ADM1811 is a low cost voltage monitor with an open drain output. The ADM1811 is designed to monitor 5 V supplies.The ADM1811 range comes in three different variants which allow the monitoring of a 5 V supply with a tolerance of 5%,10% and 15%. The ADM1816 is a 3.3 V version of the ADM1811and supports 5%, 10% and 20% tolerance options.Figure 6.ADM1811/ADM1816 Typical Application。
二极管封装大全
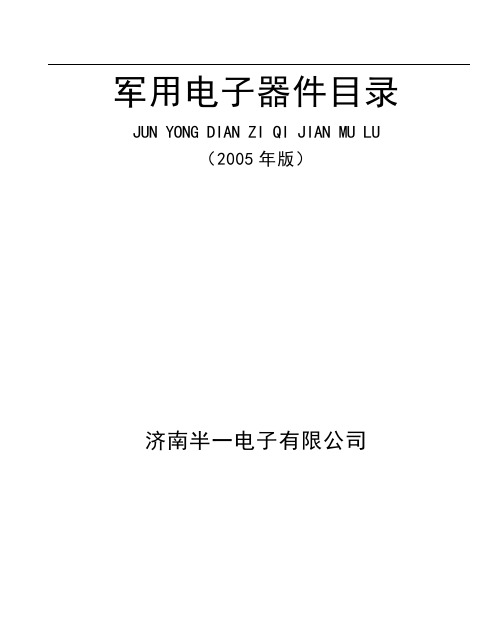
军用电子器件目录JUN YONG DIAN ZI QI JIAN MU LU(2005年版)济南半一电子有限公司目录半导体器件选用注意事项 (1)第一部分:二极管 (8)一. 开关二极管 (8)1. 锗金键开关二极管2AK1~20系列 (8)2. 锗金键检波二极管2AP1~31B系列 (9)3. 肖特基检波二极管SP1~31B系列(替代2AP1~31B) (10)4. 肖特基开关二极管SK1~20系列(替代2AK1~20) (11)5. 肖特基开关检波二极管2DKOlO、020、O3O型(替代2AK1~20、2AP1~31B)··126. 硅开关二极管2CK70~86、2CK49~56系列 (13)7. 硅开关二极管1N、1S、1SS、BAV系列 (16)8. 玻璃钝化封装大电流开关二极管RG0.5~5系列 (17)二. 整流二极管 (18)1. 玻封快速硅整流二极管2CZ50~57系列 (18)2. 玻璃钝化整流管1N、RL、6A系列 (19)3. 玻璃钝化高速整流管SF11G~66G系列 (20)4. 贴片玻璃钝化整流管S1~5系列 (21)5. 贴片高速整流管ES1~5系列 (22)6. 肖特基二极管SR0620~510、1N5817~5822系列 (23)7. 肖特基二极管SR735~4060系列 (24)8. 贴片肖特基二极管SS1~36、SS110系列 (25)三. 电压调整(稳压)二极管 (26)1. 硅稳压二极管2CW50~78系列 (26)2. 硅稳压二极管2CW100~121系列 (27)3. 硅稳压二极管ZW50~78系列 (28)4. 硅稳压二极管ZW100~121系列 (29)5. 硅稳压二极管2CW5221~5255(1N5221~5255)系列 (30)6. 硅稳压二极管2CW4728A~4754A(1N4728A~4754A)系列 (31)7. 硅稳压二极管1N746A~759A、1N957A~974A系列 (32)8. 硅稳压二极管1N4352B~4358B系列 (33)9. 硅稳压二极管HZ2~36系列 (34)10. 硅稳压二极管BZX55/C系列 (35)11. 硅稳压二极管BZX85/C系列 (36)四. 电压基准二极管 (37)1. 硅基准稳压二极管2DW14~18系列 (37)2. 硅平面温度补偿二极管2DW230~236系列 (38)五. 电流调整(稳流)二极管 (39)1. 稳流管2DH1~36系列 (39)六. 瞬变电压抑制二极管 (40)1. 单双向瞬变电压抑制二极管TVS500~534系列 (40)2. 单双向瞬变电压抑制二极管TVS1000~1034系列 (41)3. 单双向瞬变电压抑制二极管TVS1500~1534系列 (42)4. 单双向瞬变电压抑制二极管TVS5000~5034系列 (43)第二部分:晶体管 (44)一. 双极型晶体管 (44)1. 硅NPN型平面高频小功率三极管3DG110、3DG111、3DG130系列 (44)2. 硅NPN型外延平面高反压三极管3DG182系列 (45)3. 硅NPN型平面三极管3DK101、3DK106、3DK21系列 (46)4. 硅PNP型外延平面高频小功率三极管3CG111、3CG120、3CG130系列 (47)5. 硅PNP型外延平面高频小功率三极管3CK2、3CK120、3CK130系列 (48)6. 硅PNP型外延平面高频高反压小功率三极管3CG182、3CG184、2N2907系列 (49)7. 硅NPN低频大功率晶体管3DD1~8系列 (50)8. 硅NPN达林顿功率晶体管FH6~8系列 (53)二. 场效应晶体管 (54)1. N沟道MOS型场效应晶体管IRF120~823系列 (54)2. P沟道MOS型场效应晶体管IRF9130~9643系列 (56)3. N沟道结型场效应晶体管3DJ2、3DJ6/66、3DJ7/67/304、3DJ8/68系列 (57)三. 部分替代俄型号晶体管 (59)第三部分:半导体分立器件组件 (60)一. 说明 (60)二. 产品型号 (61)1. 200mA~2A玻璃钝化芯片整流桥DF、1W、RB、W系列 (61)2. 1~4A玻璃钝化芯片整流桥2W、GBP、GBL系列 (62)3. 4~15A玻璃钝化芯片整流桥GBU、GBP系列 (63)4. 15~35A玻璃钝化芯片整流桥GBPC系列 (64)5. 定制式三相整流桥 (65)6. 2Д906A型硅二极管矩阵 (65)7. 双向限幅器SXF0.25~5.8系列 (65)第四部分:电路及模块 (66)一. 集成稳压器 (66)1. 固定输出三端正稳压器CW7800系列 (66)2. 固定输出三端负稳压器CW7900系列 (66)3. 可调输出三端正稳压器CW117系列 (67)4. 可调输出三端负稳压器CW137系列 (67)5. 定制式5V以下电压基准DCW系列 (68)第五部分:外形图 (69)半导体器件选用注意事项半导体器件(以下简称器件)的质量问题,不仅有器件本身所固有的质量和可靠性问题,也有由于用户选择或使用不当造成的器件失效问题。
MAXIM MAX4561 MAX4568 MAX4569 数据手册

General DescriptionThe MAX4561/MAX4568/MAX4569 are low-voltage,ESD-protected analog switches. The normally open (NO) and normally closed (NC) inputs are protected against ±15kV electrostatic discharge (ESD) without latchup or damage, and the COM input is protected against 2.5kV ESD.These switches operate from a single +1.8V to +12V supply. The 70Ωat 5V (120Ωat 3V) on-resistance is matched between channels to 2Ωmax, and is flat (4Ωmax) over the specified signal range. The switches can handle Rail-to-Rail ® analog signals. Off-leakage current is only 0.5nA at +25°C and 5nA at +85°C. The digital input has +0.8V to +2.4V logic thresholds, ensuring TTL/CMOS-logic compatibility when using a single +5V supply. The MAX4561 is a single-pole/double-throw (SPDT) switch. The MAX4568 NO and MAX4569 NC are single-pole/single-throw (SPST) switches.The MAX4561 is available in a 6-pin SOT23 package,and the MAX4568/MAX4569 are available in 5-pin SOT23 packages.________________________ApplicationsHigh-ESD Environments Battery-Powered Systems Audio and Video Signal Routing Low-Voltage Data-Acquisition Systems Sample-and-Hold Circuits Communications CircuitsFeatureso ESD-Protected NO, NC±15kV—Human Body Model±15kV—IEC 1000-4-2, Air-Gap Discharge ±8kV—IEC 1000-4-2, Contact Discharge o Guaranteed On-Resistance70Ω+5V Supply120Ωwith Single +3V Supplyo On-Resistance Match Between Channels (2Ωmax)o Low On-Resistance Flatness: 4Ωmax o Guaranteed Low Leakage Currents0.5nA Off-Leakage (at T A = +25°C)0.5nA On-Leakage (at T A = +25°C)o Guaranteed Break-Before-Make at 5ns(MAX4561 only)o Rail-to-Rail Signal Handling Capabilityo TTL/CMOS-Logic Compatible with +5V Supplies o Industry Standard Pin-OutsMAX4561 Pin Compatible with MAX4544MAX4568/MAX4569 Pin Compatible with MAX4514/MAX4515MAX4561/MAX4568/MAX4569±15kV ESD-Protected, Low-Voltage,SPDT/SPST, CMOS Analog Switches________________________________________________________________Maxim Integrated Products 1Pin Configurations/Functional Diagrams/Truth Tables19-1714; Rev 0; 4/00For free samples and the latest literature, visit or phone 1-800-998-8800.For small orders, phone 1-800-835-8769.Ordering InformationRail-to-Rail is a registered trademark of Nippon Motorola, Ltd.查询MAX4561EUT-T供应商M A X 4561/M A X 4568/M A X 4569±15kV ESD-Protected, Low-Voltage,SPDT/SPST, CMOS Analog Switches 2_______________________________________________________________________________________ABSOLUTE MAXIMUM RATINGSELECTRICAL CHARACTERISTICS —Single +5V Supply(V+ = +4.5V to +5.5V, V IH = +2.4V, V IL = +0.8V, T A = T MIN to T MAX , unless otherwise specified. Typical values are at T A = +25°C.)Stresses beyond those listed under “Absolute Maximum Ratings” may cause permanent damage to the device. These are stress ratings only, and functional operation of the device at these or any other conditions beyond those indicated in the operational sections of the specifications is not implied. Exposure to absolute maximum rating conditions for extended periods may affect device reliability.V+ to GND................................................................-0.3 to +13V IN, COM, NO, NC to GND (Note 1)..............-0.3V to (V+ + 0.3V)Continuous Current (any terminal)....................................±10mA Peak Current(NO, NC, COM; pulsed at 1ms 10% duty cycle).........±30mA ESD Protection per Method IEC 1000-4-2 (NO, NC)Air-Gap Discharge........................................................±15kV Contact Discharge..........................................................±8kVESD Protection per Method 3015.7V+, GND, IN, COM.......................................................±2.5kV NO, NC..........................................................................±15kV Continuous Power Dissipation (T A = +70°C)SOT23 (derate 8.7mW/°C above +70°C)....................696mW Operating Temperature Range ...........................-40°C to +85°C Storage Temperature Range.............................-65°C to +150°C Lead Temperature (soldering, 10s).................................+300°CNote 1:Signals on NO, NC, COM, or IN exceeding V+ or GND are clamped by internal diodes. Limit forward current to maximumcurrent rating.MAX4561/MAX4568/MAX4569±15kV ESD-Protected, Low-Voltage,SPDT/SPST, CMOS Analog Switches_______________________________________________________________________________________3ELECTRICAL CHARACTERISTICS —Single +5V Supply (continued)050150100200250ON-RESISTANCEvs. V COM AND SUPPLY VOLTAGEV COM (V)R O N (Ω)4812302010405060021345ON-RESISTANCE vs. TEMPERATUREV COM (V)R D S (O N ) (Ω)40020010008006001600140012001800-4020-20406080100LEAKAGE CURRENT vs. TEMPERATURETEMPERATURE (°C)L E A K A G E C U R R E N T (p A )Typical Operating Characteristics(T A = +25°C, unless otherwise noted.)M A X 4561/M A X 4568/M A X 4569±15kV ESD-Protected, Low-Voltage,SPDT/SPST, CMOS Analog Switches 4_______________________________________________________________________________________ELECTRICAL CHARACTERISTICS —Single +3V Supply(V+ = +2.7V to +3.6V, V IH = +2.0V, V IL = +0.6V, T A = T MIN to T MAX , unless otherwise specified. Typical values are at T A = +25°C.)Note 3:Parameters are 100% tested at +25°C and guaranteed by correlation at the full rated temperature.Note 4:∆R ON = R ON(MAX)- R ON(MIN).Note 5:Flatness is defined as the difference between the maximum and the minimum value of on-resistance as measured over thespecified analog signal ranges.Note 6:Off-Isolation = 20log 10(V COM /V NO ), V COM = output, V NO = input to off switch.MAX4561/MAX4568/MAX4569±15kV ESD-Protected, Low-Voltage,SPDT/SPST, CMOS Analog Switches________________________________________________________________________________________50201040305060-402040-206080100SUPPLY CURRENTvs. TEMPERATURE AND SUPPLY VOLTAGETEMPERATURE (°C)S U P P L Y C U R R E N T (n A)40208060100120-40020-20406080TURN-ON/TURN-OFF TIME vs. TEMPERATURETEMPERATURE (°C)t O N /t O F F (n s )40208060100120021345TURN-ON/TURN-OFF TIME vs. V COMV COM (V)t O N /t O F F (n s )TURN-ON/TURN-OFF TIME vs. V COM02040608010012014016001.00.51.52.02.53.0V COM (V)t O N /t O F F (n s )010050200150300250350TURN-ON/TURN-OFF TIME vs. SUPPLY VOLTAGESUPPLY VOLTAGE (V)t O N /t O F F (n s )12345Typical Operating Characteristics (continued)(T A = +25°C, unless otherwise noted.)40208060120100140180160200-60-20-4020406080100SCR HOLDING CURRENT vs. TEMPERATURETEMPERATURE (°C)H O L D I N G C U R R E N T (m A )-40-25-30-35-20-15-10-5051021345MAX4561CHARGE INJECTION vs. V COMV COM (V)Q (p C)-1050-5101520021345MAX4568/MAX4569CHARGE INJECTION vs. V COMV COM (V)Q (p C )M A X 4561/M A X 4568/M A X 4569±15kV ESD-Protected, Low-Voltage,SPDT/SPST, CMOS Analog Switches 6_______________________________________________________________________________________Do not exceed the absolute maximum ratings because stresses beyond the listed ratings may cause perma-nent damage to the device.Proper power-supply sequencing is recommended for all CMOS devices. Always sequence V+ on first, fol-lowed by the logic inputs, NO/NC, or COM.High-Voltage SupplyThe MAX4561/MAX4568/MAX4569 are capable of +12V single-supply operation with some precautions.The absolute maximum rating for V+ is +13V (refer-enced to GND). When operating near this region,bypass V+ with a 0.1µF min capacitor to ground as close to the device as possible.Typical Operating Characteristics (continued)(T A = +25°C, unless otherwise noted.)10100010010,000100,000TOTAL HARMONIC DISTORTIONvs. FREQUENCYFREQUENCY (Hz)T H D (%)10.0010.010.10.010.11001000FREQUENCY RESPONSEFREQUENCY (MHz)L O S S (d B )20-100-80-60-40-200110MAX4561/MAX4568/MAX4569±15kV ESD-Protected, Low-Voltage,SPDT/SPST, CMOS Analog Switches_______________________________________________________________________________________7±15kV ESD ProtectionThe MAX4561/MAX4568/MAX4569 are ±15kV ESD-pro-tected at the NC/NO terminals in accordance with IEC1000-4-2. To accomplish this, bidirectional SCRs are included on-chip between these terminals. When the voltages at these terminals go Beyond-the-Rails ™,the corresponding SCR turns on in a few nanoseconds and bypasses the surge safely to ground. This method is superior to using diode clamps to the supplies because unless the supplies are very carefully decou-pled through low-ESR capacitors, the ESD current through the diode clamp could cause a significant spike in the supplies. This may damage or compromise the reliability of any other chip powered by those same supplies.There are diodes from NC/NO to the supplies in addi-tion to the SCRs. A resistance in series with each of these diodes limits the current into the supplies during an ESD strike. The diodes protect these terminals from overvoltages that are not a result of ESD strikes. These diodes also protect the device from improper power-supply sequencing.Once the SCR turns on because of an ESD strike, it remains on until the current through it falls below its “holding current.” The holding current is typically 110mA in the positive direction (current flowing into the NC/NO terminal) at room temperature (see SCR Holding Current vs.Temperature in the Typical Operating Characteristics ). Design the system so that any sources connected to NC/NO are current-limited to a value below the holding current to ensure the SCR turns off when the ESD event is finished and normal operation resumes. Also, remember that the holding current varies significantly with temperature. The worst case is at +85°C when the holding currents drop to 70mA. Since this is a typical number to guarantee turn-off of the SCRs under all conditions, the sources con-nected to these terminals should be current-limited to no more than half this value. When the SCR is latched,the voltage across it is approximately 3V. The supply voltages do not affect the holding current appreciably.The sources connected to the COM side of the switches need not be current limited since the switches turn off internally when the corresponding SCR(s) latch.Even though most of the ESD current flows to GND through the SCRs, a small portion of it goes into V+.Therefore, it is a good idea to bypass the V+ with 0.1µF capacitors directly to the ground plane.ESD protection can be tested in various ways. Inputs are characterized for protection to the following:•±15kV using the Human Body Model•±8kV using the Contact Discharge method speci-fied in IEC 1000-4-2 (formerly IEC 801-2)•±15kV using the Air-Gap Discharge method speci-fied in IEC 1000-4-2 (formerly IEC 801-2)ESD Test ConditionsContact Maxim Integrated Products for a reliability report that documents test setup, methodology, and results.Human Body ModelFigure 6 shows the Human Body Model, and Figure 7shows the waveform it generates when discharged into a low impedance. This model consists of a 100pF capacitor charged to the ESD voltage of interest, which can be dis-charged into the test device through a 1.5k Ωresistor.IEC 1000-4-2The IEC 1000-4-2 standard covers ESD testing and performance of finished equipment; it does not specifi-cally refer to integrated circuits. The MAX4561 enables the design of equipment that meets Level 4 (the highest level) of IEC 1000-4-2, without additional ESD protec-tion components.The major difference between tests done using the Human Body Model and IEC 1000-4-2 is higher peak cur-rent in IEC 1000-4-2. Because series resistance is lower in the IEC 1000-4-2 ESD test model (Figure 8), the ESD withstand voltage measured to this standard is generally lower than that measured using the Human Body Model.Figure 9 shows the current waveform for the ±8kV IEC 1000-4-2 Level 4 ESD Contact Discharge test.The Air-Gap test involves approaching the device with a charged probe. The Contact Discharge method connects the probe to the device before the probe is energized.Chip InformationPROCESS: CMOSBeyond-the-Rails is a trademark of Maxim Integrated Products.TRANSISTOR COUNT: 69(MAX4561)39(MAX4568/MAX4569)M A X 4561/M A X 4568/M A X 4569±15kV ESD-Protected, Low-Voltage,SPDT/SPST, CMOS Analog Switches 8_______________________________________________________________________________________Figure 1. Switching TimeFigure 2. Break-Before-Make IntervalFigure 3. Charge Injection Test Circuits/Timing DiagramsMAX4561/MAX4568/MAX4569±15kV ESD-Protected, Low-Voltage,SPDT/SPST, CMOS Analog Switches_______________________________________________________________________________________9Figure 4. Channel On/Off-CapacitanceFigure 5. Off-Isolation/On-ChannelFigure 6. Human Body ESD Test ModelFigure 7. Human Body Model Current WaveformFigure 8. IEC 1000-4-2 ESD Test Model Figure 9. IED 1000-4-2 ESD Generator Current WaveformTest Circuits/Timing Diagrams (continued)M A X 4561/M A X 4568/M A X 4569±15kV ESD-Protected, Low-Voltage,SPDT/SPST, CMOS Analog Switches 10______________________________________________________________________________________Package InformationMAX4561/MAX4568/MAX4569±15kV ESD-Protected, Low-Voltage,SPDT/SPST, CMOS Analog Switches______________________________________________________________________________________11Package Information (continued)M A X 4561/M A X 4568/M A X 4569±15kV ESD-Protected, Low-Voltage,SPDT/SPST, CMOS Analog SwitchesMaxim cannot assume responsibility for use of any circuitry other than circuitry entirely embodied in a Maxim product. No circuit patent licenses are implied. Maxim reserves the right to change the circuitry and specifications without notice at any time.12____________________Maxim Integrated Products, 120 San Gabriel Drive, Sunnyvale, CA 94086 408-737-7600©2000 Maxim Integrated Products Printed USAis a registered trademark of Maxim Integrated Products.NOTES。
18JM 18JM规格说明书

Rack-mounted DCS Signal Conditioners 18-RACKPOTENTIOMETER CONVERTERMODEL: 18JM–166–R• Linearization data (max. 16 points)Use Ordering Information Sheet (No. ESU-1669) to specifylinearization data when the I/O signals are non-linear.INPUT POTENTIOMETER1: Total resistance 100 Ω – 10 kΩOUTPUT 1Voltage6: 1 – 5 V DC (Load resistance 2000 Ω min.)OUTPUT 2Voltage6: 1 – 5 V DC (Load resistance 2000 Ω min.)POWER INPUTDC PowerR: 24 V DC(Operational voltage range 24 V ±10 %, ripple 10 %p-p max.)• PC configurator software (model: JXCON)Downloadable at M-System’s web site.A dedicated cable is required to connect the module to thePC. Please refer to the internet software download site orthe users manual for the PC configurator for applicablecable types.terminals on the front and connector on the rear; terminalcover providedConnectionInput: M3.5 screw terminals (torque 0.8 N·m)Output 1: ConnectorOutput 2: M3.5 screw terminals (torque 0.8 N·m)and connectorPower input: Supplied from connectorScrew terminal: Nickel-plated steelIsolation: Input to output 1 to output 2 to powerLinearization: 16 points max. within the range of -15.00 –+115.00 % input or output; represented as percentage offull-scaleAdjustments: Programming Unit (model: PU-2x);linearization data (Unused resistance of the potentiometer'stotal resistance can be programmed with the linearizationtable.), zero and span, simulating output, etc.(Refer to the users manual of JXCON for the adjustmentsconfigurable with JXCON.)Programming Unit [model: PU-2x] or PC configuratorsoftware [model: JXCON])Excitation: 0.25 V DCOperating temperature: -5 to +55°C (23 to 131°F)Operating humidity: 30 to 90 %RH (non-condensing)Mounting: Standard Rack 18BXx or 18KBXxWeight: 150 g (0.33 lb)with segment gain > 1Temp. coefficient: ±0.015 %/°C (±0.008 %/°F)Response time: ≤ 0.5 sec. (0 – 90 %)Line voltage effect: ±0.1 % over voltage rangeInsulation resistance: ≥ 100 MΩ with 500 V DCDielectric strength: 1500 V AC @ 1 minute(input to output 1 or output 2 or power)500 V AC @ 1 minute(output 1 to output 2 to power)1500 V AC @ 1 minute(input or output or power to ground)2–M3。
WM-1810X18颗单控洗墙灯说明书

WM-1810X18颗单控洗墙灯说明书广东万镁灯光科技有限公司电话:传真:1.图解部分:A.功能键B.加键C.减键D.确认键E.LED显示窗A B C D操作说明:按功能键A会循环出八种不同的功能效果,数码管前两位数字代表当前所处的功能(参照功能表)。
后两位数字代表该种功能所处的.地址码.或速度、的参数。
按B或C键即可修改其参数值。
按D键确认即可。
2.LED显示窗功能对照表,(所有的功能按选定后再按D键确认即可)序号显示功能说明1 A001 通道地址码,(001—512)B、C键加减地址码数值2 27ch/-9ch-82ch-72ch 通道选择(27通道、9通道、82通道、72通道)B、C键加减3 CC00 七彩跳变,(01—99)B、C键修改跳变速度4 Ed00 七彩渐变, 脉变,(01—99)B、C键修改渐变速度5 Er00 七彩跑动1,(01—99)B、C键修改脉变速度(设置I d,可实现多台灯流水)6 Po00 七彩跑动2,(01—99)B、C键修改脉变速度(设置I d,可实现多台灯流水)7 tr00 跑动变化,(00—8)B、C键修改跑动花样8 tU00 跑动变化,(00—99)B、C键修改跑动速度9 BE50 七彩声控跑动变化B、C键修改声控灵敏度10 R200 红色选色,(000—255)B、C键修改颜色值11 G200 绿色选色,(000—255)B、C键修改颜色值12 B200 兰色选色,(000—255)B、C键修改颜色值3.后台LED显示窗功能对照表,(在512模式下长按功能键进入,所有的功能按选定后再按D键确认即可)34445.功能特点:操作非常简单,人性化设计,调光无闪烁、抖动现象等。
可适应摄影,照相、电视台等对灯光要求严格的场合。
西门子 S7-1200 功能安全手册 - 设备手册说明书

SIMATICS7S7-1200 功能安全手册设备手册Siemens AGDigital IndustriesⓅ 10/2022 本公司保留更改的权利 Copyright © Siemens AG 2022. 保留所有权利法律资讯警告提示系统为了您的人身安全以及避免财产损失,必须注意本手册中的提示。
人身安全的提示用一个警告三角表示,仅与财产损失有关的提示不带警告三角。
警告提示根据危险等级由高到低如下表示。
危险表示如果不采取相应的小心措施,将会导致死亡或者严重的人身伤害。
警告表示如果不采取相应的小心措施,可能导致死亡或者严重的人身伤害。
小心表示如果不采取相应的小心措施,可能导致轻微的人身伤害。
注意表示如果不采取相应的小心措施,可能导致财产损失。
当出现多个危险等级的情况下,每次总是使用最高等级的警告提示。
如果在某个警告提示中带有警告可能导致人身伤害的警告三角,则可能在该警告提示中另外还附带有可能导致财产损失的警告。
合格的专业人员本文件所属的产品/系统只允许由符合各项工作要求的合格人员进行操作。
其操作必须遵照各自附带的文件说明,特别是其中的安全及警告提示。
由于具备相关培训及经验,合格人员可以察觉本产品/系统的风险,并避免可能的危险。
按规定使用 Siemens 产品请注意下列说明:警告Siemens 产品只允许用于目录和相关技术文件中规定的使用情况。
如果要使用其他公司的产品和组件,必须得到 Siemens 推荐和允许。
正确的运输、储存、组装、装配、安装、调试、操作和维护是产品安全、正常运行的前提。
必须保证允许的环境条件。
必须注意相关文件中的提示。
商标所有带有标记符号 ® 的都是 Siemens AG 的注册商标。
本印刷品中的其他符号可能是一些其他商标。
若第三方出于自身目的使用这些商标,将侵害其所有者的权利。
责任免除我们已对印刷品中所述内容与硬件和软件的一致性作过检查。
然而不排除存在偏差的可能性,因此我们不保证印刷品中所述内容与硬件和软件完全一致。
控制器TC1818a的操作手册(121202)

维持温度(设定模式)
一般情况下显示信息如下: MAINTAIN TEMP =104°F (维持温度=104°F) NEW VALUE=104°F (新设定值=104°F) 快速按动 UP 或 DOWN 箭头键将导致 NEW VALUE(新值)以 1 度增量逐渐变化。持续按键 将导致 NEW VALUE 以 10 度为增量变化。当设定值达到了最高或最低限定值,第二行将显示 信息 MAX(最高)或 MIN(最低)。这表明设定值已经达到了最大值或最小值或已经达到了报 警值。 MAINTAIN TEMP=104° (维持温度=104°F) NEW VALUE-50°F (新设定值=50°F)
模块尺寸:
4-1/2” × 19” × 7-1/2” (114mm × 482mm × 191mm)
操作电流报警 高值: 1.0A 到 30.0A 低值: 0.0A 到 30.0A
漏电电流报警/跳闸: 30mA 到 150Ma
自测频率:
可编程设定从 2 小时到 99 小时
典型 HEATCHEK 控制检测单元… TC 1818a 为模块式结构并可以组态成各种 HEATCHEK 控制检测单元。 信息 在赛盟样本 TEP0027 中有一些典型单元的举例说明。此外设计选型以及工程资料信息可以在 T-1008-E 中得到。
TC 1818a 控制模块 操作指南
本指南仅供赛盟 HeatChekTM 伴热监控装置用户使用。 本手册拥有版权并受版权保护。任何未经赛盟公司书面
许可而使用手册者都将被严格禁止。 © 赛盟 1999
HeatChek 及 TraceView 为赛盟制造公司商用标志。 Ryton 为菲利普 66 公司商用标志。 Kapton 为 E.I.杜邦公司商用标志。
TM1818

CLK-SDO tpLH
CLK-OUT
延迟时间
LE-OUT
(高电平到低电平) OE-OUT
CLK-SDO
电流输出上升沿时间
tpLH1 tpLH2 tpLH3 tpLH tor
电流输出下降沿时间
tof
十五、动态特性的测试电路
16 位恒流驱动 IC
VDS=1.0V VIH=Vdd
VIL=GND Rext=830Ω
二 、功能特点
¾ 16 个恒流源输出通道 ¾ 电流输出大小不因输出端负载电压变化而变化 ¾ 恒流电流范围值,3~45mA@VDD=5V;3~30mA@VDD=3.3V ¾ 极为精确的电流输出值,通道间最大误差:<±3%,芯片间最大误差:<±6% ¾ 通过调节外部电阻,可设定电流输出值 ¾ 高达 25MHz 时钟频率 ¾ 工作电压:3.3V~5V ¾ 封装形式:SSOP24
一、 特性描述
16 位恒流驱动 IC
TM1818
TM1818是LED显示面板设计的驱动IC,它内建的CMOS位移寄存器与锁存功
能,可以将串行的输入数据转换成平行输出数据格式。TM1818具有16个电流源,可以在 每个输出端口提供3~45mA恒定电流量以驱动LED;且当环境发生变化时,对其输出电流影响 很小。同时可以选用不同阻值(REXT)的外接电阻来调整TM1818各输出端口的电流大小, 因此,可精确地控制 LED的发光亮度。也可以在每个输出端口串接多个LED。
ns
135
ns
40
ns
180
ns
90
ns
十四、动态特性(VDD=3.3V)
特性 延迟时间
代表符
测量条件 最小值 一般值 最大值 单位
NCP1618A驱动的500W宽范围前端调节器评估板用户手册说明书

EVBUM2716/D 500 W, Wide-Mains,NCP1618A-driven Evaluation Board User's ManualIntroductionThe NCP1618A is an innovative multimode power factor controller [1]. The circuit naturally transitions from one operation mode (CCM,CrM or DCM) to another depending on the switching period duration so that the efficiency is optimized over the line/load range. In very light−load conditions, the circuit enters the soft−SKIP mode for minimized losses. Housed in a SO−9 package, the circuit further incorporates the features necessary for building robust and compact PFC stages, with few external components.The evaluation board is a 500 W wide−mains PFC stage.EVB ELECTRICAL SPECIFICATIONSDescriptionValue Units Input Voltage Range90−265V rms Line Frequency Range 45 to 66Hz Output Power500W Minimum Output Load Current 13mA Maximum Output Load Current1300mA Load Conditions For Efficiency Measurements (10%, 20%,..)10−100%Minimum Efficiency Over the Line/Load Range 94%Minimum PF Over The Line Range At Full Load95%Hold−Up Time (the output voltage remaining above 300 V)> 20ms Peak−To−Peak Low Frequency Output Ripple< 8%Note that the evaluation board does not need an external source to power the NCP1618A V CC . A charge pump is implemented on the board which typically provides V CC with a 23−V voltage.EVAL BOARD USER’S MANUALTHE BOARDFigure 1. The Wide−Mains, 500 W PFC StageAPPLICATION SCHEMATICPower SectionFigure 2. Power Section of the Application Schematic90−265 VrmsFigure 2 shows the power section of the application schematic. Charge pump (R 1, C 11, D Z1) provides the V CC voltage using an auxiliary winding of the PFC choke. Two ON Semiconductor FCPF165N65 MOSFETS (Q 1a and Q 1b ) are paralleled [2]. A Silicon Carbide Schottky diode (SiC) FFSPF0865A from ON Semiconductor is used as the boost diode [3]. An NTC is placed in series with the bulk capacitor C 4 to limit inrush currents when the PFC stage is plugged in. MOSFET Q 2 (FCA76N60 − 600 V , 36 m Ω,TO−3P MOSFET from ON Semiconductor [4]) is implemented to bypass the NTC when the bulk capacitor is charged. Practically, the drive voltage and a V CC charge pump output are applied to Q 2 gate so that Q 2 is on and the NTC bypassed as soon as the PFC stage is in operation. The evaluation board supports the use of a totem pole (Q 3, Q 4)to shorten the MOSFET transitions. However, if the pnp transistor (Q 4) is implemented to speed−up the turning off event, in this application, npn transistor Q 3 is not used (only its base−emitter junction is used as a diode for turning on current).Control SectionFigure 3. Control Section of the Application SchematicPin 5 of the NCP1618 is designed to monitor a signal from an auxiliary winding for detecting the core reset when this voltage drops to zero. This function ensures valley turn on in discontinuous and critical conduction modes (DCM and CrM). This pin can also be used to detect an over−voltage condition of the bulk voltage, hence offering a redundant OVP protection (OVP2). However, as detailed in [5] direct sensing of the bulk voltage for OVP2 may cause too much a power dissipation when an ultra−low standby consumption is targeted. That is why this board instead uses the auxiliary winding voltage to reconstruct a voltage representative of the bulk voltage. More specifically, charge pump R2, C10 and D5 of Figure 2 provides a signal representative of the drain−source voltage of the MOSFET (N*V DS), where N is the turns ratio (auxiliary winding number of turns / primary winding number of turns). This voltage biases the ZCD circuitry and as it is equal to (N*V BULK) during the demagnetization phase, it is sensed for OVP2. Components R5, C7 and D9 clamps reconstructed (N*V DS) signal to prevent that when the circuit starts or restarts operation after an interruption, an incorrect initial value of the C10 voltage causes OVP2 spurious tripping. See [5] for more details.Circuitry for Soft−SKIP TestingFigure 4. Circuitry for Soft−SKIP Mode TestingS1Manual switchThe NCP1618A is designed to enter the soft−SKIP mode at very light load. Soft−SKIP minimizes losses by forcing a very low frequency burst−mode of operation. First, the circuit charges the output voltage to 103% of its nominal voltage and at that moment, enters a deep idle mode where no DRV pulses are generated and all non−necessary circuitries are turned off so that the circuit consumption is reduced to a minimum (250 m A typically). The circuit wakes up and restarts a new active burst cycle when the output voltage has dropped to 98% of its nominal level. In other words, as illustrated by Figure 17a, the output voltage swings between 103% and 98% of its nominal value. The NCP1618A can be externally forced to enter the soft−SKIP mode by grounding the V M pin or applying negative pulses on the pfcOK pin (refer to [1] for more details). In the absence of a downstream converter, the circuit of Figure 4can be used to provide the soft−SKIP signal. A square−wave signal varying between about 0 and an upper voltage of 5 to 15 V should be applied to the SKIP_control2 input of the board. According to the position of manual switch S 1, either the V M or the pfcOK pin will be used for controlling the soft−SKIP mode.Important Remark:Proposed circuitry was designed to illustrate the NCP1618 operation. It should not be re−used in practical applications as is unless appropriate verifications are made to check that it can meet reliability and safety requirements and comply with relevant norms. In particular, the inrush management circuitry may not be re−used if risks exist that the NTC is not properly shorted when the PFC stage starts switching. If the NTC is not shorted, the V OUT voltage will be the sum of the bulk capacitor voltage plus the voltage produced by the inductor current across the NTC (V C4 + (R NTC * I L )) and in this case, too high a (R NTC * I L ) voltage can be destructive for the application. It must be also noted that the inrush management circuitry increases the current loop when the boost stage fuels the bulk capacitor,making the layout less optimal for very high−speed switching operation, particularly with high t RR boost diodes.TYPICAL WAVEFORMSFigure 5 shows the line current at 115 V rms and at below different load levels:•At full load, the NCP1618 operates in CCM.•At 50% of the load, the system operates in critical conduction mode•At 40% of the load, the 130 kHz frequency clamp starts to trip (Frequency−clamped critical conduction mode)leading to critical conduction mode operation at the top of the sinusoid and valley−2 operation near the line zero crossing as illustrated by Figure 6.•At 20% load, the NCP1618 frequency foldback makesthe PFC stage operate at nearly 30 kHz. Note that the circuit continues turning on at the valley and that the number of valleys depends on the line instantaneous voltage. For instance, the number of skipped valleys is high at the top of the sinusoid where the resonant period is short while turn on in the second valley is obtained at the line zero crossing where the resonant period is long. See Figure 7. However, the NCP1618always turns on at the valley as long as valleys are detectable.Figure 5. Line Current at 115 V rmsa)115 V rms, Full load (1.30 A)b)115 V rms, 50% load (0.65 A)c)115 V rms, 40% load (0.52 A)d)115 V rms, 20% load (0.26 A)V outI LINE (2 A/div)I LINE (5A/div)I LINE (2 A/div)I LINE (5A/div)V outV outV outFigure 6. Operation at 115 V rms, 40% Loada)Top of the sinusoid b)Near the line zero crossingI LINEV out V DSI LINEV outV DSFigure 7. Low Frequency Operation at 115 V rms, 20% Loada)Top of the sinusoid b)Near the line zero crossingI LINE V outV DSI LINEV outV DSCCM OperationThe transition point is measured by increasing /decreasing the load by 1 mA steps.Line rms voltageLoad current for exiting CCMLoad current for entering CCM90 V524 mA 610 mA 115 V 779 mA 893 mA 150 V 1034 mA 1205 mA 180 V 1133 mA 1460 mA 230 V 888 mA 1021 mA 265 V798 mA922 mABoard Performance•EfficiencyThe efficiency is measured on an automated bench at 90V rms, 115 V rms, 230 V rms and 265 V rms. After a 30−mn warm−up time at full load, the load is decreased from1.30 A down to 0.13 A by 0.13−A steps. The measure is made after 5 mn of operation at the operating point under test.Figure 8. Efficiency vs. LoadThe efficiency remains above 94% from 10% to 100% of the load at the 4 tested line levels (90 V rms, 115 V rms,230V rms and 265 V rms).•Power Factor and THDPower factor and THD are measured over the load range.Practically, the load current is swept starting from 1300 mA to 130 mA with 130 mA steps.Figure 9. PF and THD versus Loada)Power factor (PF)b)Total harmonic distortion (THD)On the 20% to 100% load range, the power factor remains higher than 0.9 and the THD well below 20% at the four tested line levels.Startup SequencesWhen the board is plugged in, the circuit first turns on the internal high−voltage start−up current source to charge up the VCC capacitor. When V CC reaches V CC (on ) (17 Vtypically), operation can begin and the PFC stage starts to deliver energy. When the bulk capacitor is charged to 98%of its nominal voltage, the pfcOK pin turns high to enable the downstream converter. As indicated in the data sheet, a 100m F V CC capacitor is typically charged from 0 to V CC (on )in about 215 ms. The total V CC capacitance of our board being 220 m F, we can hence expect the PFC stage to start about 470 ms after it is plugged in.Figure 10. Startup Sequence at Full Load, Low Linea)General view b)Magnified viewFigure 10 shows a start−up sequence done at full load (1.3A) and at the lowest line level (90 V), the V CC capacitor being discharged when the board is plugged in. As illustrated by Figure 10a, the total time necessary to have pfcOK high from PFC stage plug−in is nearly 590 ms (about 420 ms to raise V CC and 170 ms to charge the output capacitor). Magnified view of Figure 10b shows that it takes less than a line cycle to reach the full input current capability.Note that two rising slopes can be seen on the plot of Figure 10a during the V CC charge phase. This is because the NCP1618 startup current is limited to 1 mA (typically) until the V CC voltage exceeds about 0.8 V . This feature prevents the internal high−voltage current source from overheating if the V CC pin happens to be accidentally grounded. When this first sequence is completed, the NCP1618 sources the nominal charge current of 12 mA typically.Figure 11. Startup Sequence at No Load, Low Line (90 V rms)a)General view b)Magnified viewHowever, in normal operation, the PFC stage starts up with no load since the downstream converter is normally disabled until pfcOK gets high. Figure 11a shows that in this practical condition, the total start−up time is significantly less than 500 ms: the V CC still takes about 420 ms and the bulk capacitor is charged within 60 ms.TYPICAL BEHAVIOR AND WAVEFORMSAbrupt Line VariationsThe circuit detects the line range. Practically, the high−line mode is set when the HV pin voltage exceeds 236V (typically) and recovers the low−line mode when theHV pin voltage remains less than 222 V for more than 25 ms (typical values). More practically, these voltage levels corresponds to line rms values of 167 V and 157 V respectively.Figure 12. High−line DetectionFigure 13. 90 V rms to 265 V rmsLine Step at Full LoadThe line range detection circuit optimizes the operation for universal (wide input mains) applications. Practically, in “high−line”:•The regulation bandwidth is divided by 4•The power expression defining the threshold below which frequency foldback is engaged is changed (see data sheet [1]).Figure 13 shows a low− to high−line transition at full load (I out = 1.3 A). This abrupt line change causes a voltage increase well−contained by the over−voltage protection.Figure 14 details a high− to low−line transition at full load.The circuit moderately reacts to the abrupt line change during the 25 ms necessary for low−line detection. After this delay, the NCP1618 sharply reacts and effectively limits the output voltage decay. Practically, the output voltage remains above 320 V .Figure 14. 265 V rms to 90 V rms Line Drop at Full Loada)General view b)Magnified viewI LINEV outV inI LINEV outV in320 VLoad StepsIn essence, PFC stages are slow systems. Thus, the output voltage of PFC stages may exhibit excessive over− and under−shoots because of abrupt load or input voltage variations (e.g. at start−up). The NCP1618 incorporates a fast line / load compensation to avoid such large output voltage variations. Practically, the circuit monitors the output voltage and limits possible deviations with respect to the regulation nominal voltage (V out ,nom ). More specifically,the NCP1618:•Disables the drive to stop delivering power when the output voltage exceeds the over voltage protection level (105% of V out ,nom ) and until V out has decayed back to 103% of V out ,nom (typical values).•Drastically speeds−up the regulation loop (DynamicResponse Enhancer) when the output voltage goes below 95.5 % of V out ,nom .To illustrate these functions, every 500 ms, the load is abruptly changed from 0.13 A to 1.30 A (respectively 10%and 100% of the full load) and vice versa, with 2 A/m s edges.Figure 15 shows the resulting output voltage under the load changes at 115 V rms. We can see that the NCP1618 is able to maintain the output voltage above 350 V when the load is abruptly raised from 10% to 100% (Figure 15a) and below about 410 V when the load is suddenly 90% reduced (Figure 15b).Figure 15. 10% to 100% Load Steps at 115 V rmsa)Rising load step b)Falling load stepI LINEV outV M pin voltageI LINEV outV M pin voltageThe same test is made at 230 V rms. Again as illustrated by Figure 16, the output voltage remains within a narrow range (between about 360 and 411 V).Figure 16. 10% to 100% Load Steps at 230 V rmsa)Rising load step b)Falling load stepI LINEV outV M pin voltageI LINEV outV M pin voltageThe V M pin voltage is shown in Figure 15 and Figure 16as it is indicative of the operation mode. It is a constant dc voltage in FCCrM mode (2.50 V) and during an operation interruption caused by the over−voltage protection (3.75 V)while the V M pin voltage is a rectified sine−wave in CCM.Soft−SKIP ModeThe NCP1618 is designed to be externally forced to enter the soft−SKIP mode by grounding the V M pin or applying negative pulses on the pfcOK pin. When in soft−SKIP mode,the circuit charges the output voltage to 103% of its nominalvoltage and at that moment, enters a deep idle mode where no DRV pulses are generated and all non−necessary circuitries are turned off so that the circuit consumption is reduced to a minimum (250 m A typically). The circuit wakes up when the output voltage has decayed down to 98% of its nominal level and restarts a new active burst cycle. In other words, as illustrated by Figure 17a, the output voltage swings between 103% and 98% of its nominal value.Magnified view of Figure 17b shows the active part of the burst. It illustrates that for best efficiency, the PFC stage operates at low frequency with valley switching.Figure 17. Soft−Skip Operation (115 V, 1% Load)a)General view b)Magnified viewLine−Sag TestsTests can be made which consist of rapidly and repeatedly plug and unplug the power supply. If no specific function is implemented, a huge current can take place when the power supply is reconnected.The NCP1618 detects short drops/interruptions of the mains to prevent an excessive stress when the line recovers.Practically, such line−sag situations are detected when the input voltage remains below 100 V for 25 ms or more (typical values) and in such cases, CCM mode is disabled and a soft−stop sequence starts. Soft stop is the gradualdown−to−zero discharge of the control signal to smoothly stop operation.When the line recovers, the circuit resets the BUV timer.It is because a line−sag event is likely to cause a BUV (bulk under−voltage) detection. When a BUV fault is detected, no restart is normally possible until the BUV timer (500 ms typically) has elapsed. However, if the BUV protection trips during a line−sag sequence, operation resumes as soon as the line recovers. Also, the NCP1618 interrupts the soft−stop discharge, grounds the control signal and charges V CC to its startup level (V CC (on ) = 17 V) if below for a clean start−up [1].Figure 18. Line Short Drops to 50 V rmsa)20−ms line sag (115 V rms, full load)b)50−ms line sag (115 V rms, full load)I LINEV outV inV pfcOKI LINEV outV inV pfcOKFigure 18a shows the case of a very short line sag (20 ms)while the circuit is operating at 115 V rms, full load. It is too short to trip the line−sag protection. Figure 18b shows a longer line sag situation (50 ms). In this case, we can see that after 25 ms, soft−stop is engaged and that after 37.5 ms, the BUV protection trips as attested by the pfcOK grounding.Operation resumes as soon as the line is back without waiting for the BUV timer being elapsed.Hold−Up TimeHold−up time tests are made at 90 V , full load. In the Figure 19a case, the line is interrupted for 20 ms. In this situation, the output voltage drops to 310 V which is well above the bulk under−voltage level (V out ,BUV = 280 V). In turn, pfcOK remains high and keeps enabling the downstream converter which loads the PFC stage.In the Figure 19b case, the line interruption is extended to 50 ms (test still made at 90 V , full load). This test enables to confirm the BUV level (about 280 V) which is reached after about the first 24 ms of line absence. This is the moment when due to the bulk under−voltage tripping (BUV), the pfcOK pin is grounded to disable the downstream converter.The two plots of Figure 19 also show that when the output voltage decays, so does the pfcOK voltage (when it is not grounded). Actually, when in high state, the pfcOK voltage is proportional to the output voltage to provide the downstream converter not only with an enable/disable signal but also with a signal representative of the output voltage for feedforward.Figure 19. Mains Interruptionsa)20−ms line interruption (90 V, full load)b)50−ms line interruption (90 V, full load)I LINEV outV pfcOKV inI LINEV outV pfcOKV in24.5msBILL OF MATERIAL BILL OF MATERIALReference Qty Description Value Tolerance /Constraints Footprint Manufacturer Part number SubstitutionallowedPower SectionJ101AC Connector GSF1.1xxx.xxSCHURTER GSF1.1201.31NO1Fuse8 A /250 VSCHURTER34562611NO J1b1VBULK connector Multicomp24.243.1NO J1a1GND connector Multicomp24.243.2NOHS11Diodes Bridge(U1) Heatsink 4.5°C/W FischerElektronikSK481−50NOHS21Q1a, Q1b and D1Heatsink 2.8°C/W FischerElektronikSK481−100NO4HS1 and HS2Heatsink clip FischerElektronikTHFU1NOC1, C22X2 capacitor470 nF277V through−hole Wurth Elektronik890334025039CS NO C3a, C3b2Filtering capacitor680 nF450V through−hole Wurth Elektronik890283425008CS NO C41Electrolyticcapacitor330 m F450 V through−hole Wurth Elektronik861141486022NOC5, C62Y2 capacitors(note)1 nF275 V through−hole EPCOS B32021A3102NOC71Ceramic capacitor220 nF25V, 10%SMD, 1206various various YESC91High−voltagecapacitor 100 pF500 V through−hole Vishay D101K20Y5PL6.J5.NOC10, C112Capacitor10 nF25V, 10%SMD, 1206various various YESC121Capacitor 1 nF25V, 10%SMD, 1206various various YES C191ElectrolyticCapacitor220 m F35 V through−hole Wurth Elektronik860020273009YES U11Diodes Bridge GSIB158015A, 800V through−hole VISHAY GSIB1580NOCM11Common−ModeFilter2 mH 6 m W through−hole Wurth Elektronik7448031002NOD11Boost diode FFSPF0865A8A, 650V TO220F ON Semiconductor FFSPF0865A NO D2, D32Bypass diode1N54063A, 600 V Axial ON Semiconductor1N5406G NOD4, D5,D6, D7,D8, D96Switching diode D1N4148100 V SOD123Vishay1N4148W−V NODZ1124−V zener diode MMSZ24T124V, 0.5W SOD−123ON Semiconductor MMSZ24T1G NOL11Boost Inductor175 m H,14 APQ3230Wurth Elektronik750 317557NO L21DM Choke56 m H17 m W through−hole BOURNS2310−V−RC NOQ1a, Q1b2Power MOSFET FCFP165N65650V TO220F ON Semiconductor FCPF165N65S3L1NO Q21Power MOSFET FCA76N60600 V, 76 A TO−3PN ON Semiconductor FCA76N60N NOQ31NPN transistor MMBT489LT1G40 V / 1 A SOT−23ON Semiconductor MMBT489LT1G NOQ41PNP transistor MMBT589LT1G30V / 2A SOT−23ON Semiconductor MMBT589LT1G NONTC11Inrush CurrentLimiter 10 W @25°Cthrough−hole EPCOS B57237S0100M0NOR1, R2, R163SMD resistor,1206, 1/4W10 W10%, 1/4W SMD, 1206various various YESR31Through holeresistor0 W 1 W through−hole Vishay AC01R4, R52SMD resistor,1206, 1/4W100 k W10%, 1/4W SMD, 1206various various YESR8, R9, R153SMD resistor,1206, 1/4W2.2 W10%, 1/4W SMD, 1206various various YESBILL OF MATERIAL (continued)Reference Substitution allowedPart number Manufacturer Footprint Tolerance /Constraints Value Description Qty R10, R11,R12, R134SMD resistor,1206, 1/4W 27 k W 10%, 1/4W SMD, 1206various variousYES R141Current sense resistor 30 m W 1%, 3W through−holeVishayLVR03R0300FE12NO V11TVS Varistor275 V rmsWurth Elektronik820513011NOControl Section and Circuitry for Soft−SKIP Testing R18, R201SMD resistor,1206, 1/4W 0 k W 1%SMD, 1206various various YES R191SMD resistor,1206, 1/4W 5.6 k W 1%SMD, 1206various various YES R211SMD resistor,1206, 1/4W 560 k W 1%SMD, 1206various various YES R22, R232SMD resistor,1206, 1/4W 1800 k W 1%SMD, 1206various various YES R241SMD resistor,1206, 1/4W 27 k W 1%SMD, 1206various various YES R251SMD resistor,1206, 1/4W 56 k W 1%SMD, 1206Vishay various YES R26, R27,R283SMD resistor,1206, 1/4W 1 k W 1%SMD, 1206Vishay various YES R291SMD resistor,1206, 1/4W 6.8 k W 1%SMD, 1206Vishay various YES R30, R34,R353SMD resistor,1206, 1/4W 10 k W 1%SMD, 1206Vishay various YES R31, R332SMD resistor,1206, 1/4W 22 W 1%SMD, 1206Vishay various YES R321SMD resistor,1206, 1/4W 470 W 1%SMD, 1206Vishayvarious YES D10, D112StandardRecovery Diodes 1N40071000 V through−hole ON Semiconductor1N4007G NO D12, D13,D143Switching diode D1N4148100 V SOD123Vishay1N4148W−V NO DZ3110−V zener diode MMSZ10T110 V, 0.5 W SOD−123ON Semiconductor MMSZ10T1G NO DZ4127−V zener diode MMSZ27T127 V, 0.5 W SOD−123ON SemiconductorMMSZ27T1G NO C141Capacitor 2.2 nF 25 V, 10%SMD, 1206various various YES C15, C181Capacitor 10 nF 25 V, 10%SMD, 1206various various YES C161Capacitor 220 pF 25 V, 10%SMD, 1206various various YES C201Capacitor 22 nF 25 V, 10%SMD, 1206various various YES C221Capacitor 220 nF 25 V, 10%SMD, 1206various various YES C231Capacitor 22 pF 25 V, 10%SMD, 1206variousvarious YES Q61NPN transistor MMBT489LT1G 40 V / 1 ASOT−23ON SemiconductorMMBT489LT1G NO S11Manual Switch 1K2serie SW_sip3EOZ secme09−03290.01NO U21controller NCP1618SOIC9ON SemiconductorNCP1618NO J111Vcc socketWEIDMULLERPM5.08/2/90YESNOTE: All Components are Lead−FreeReferences[1] NCP1618 data sheet: https:///pub/Collateral/NCP1618−D.PDF[2] FCPF165N65 data sheet: https:///pub/Collateral/FCPF165N65S3L1−D.PDF [3] FFSPF0865 data sheet: https:///pub/Collateral/FFSPF0865A−D.PDF[4] FCA76N60 data sheet: https:///products/discretes−drivers/mosfets/fca76n60n [5] Joel Turchi, “NCP1618 tips and tricks”, application note AND90011/D,https:///pub/Collateral/AND90011−D.PDFANNEXThe board provides some flexibility and consists of few components which are shorted or not connected. For thesake of clarity, below schematic diagrams report them together with implemented ones.Figure 20. Power Section Schematic Diagram90−265 VrmsFigure 21. Control Section and Circuitry for Soft−SKIP TestingADDITIONAL INFORMATIONTECHNICAL PUBLICATIONS :Technical Library: /design/resources/technical−documentation onsemi Website: ONLINE SUPPORT : /supportFor additional information, please contact your local Sales Representative at /support/sales。
哈蒙德电子变压器1182系列产品说明说明书
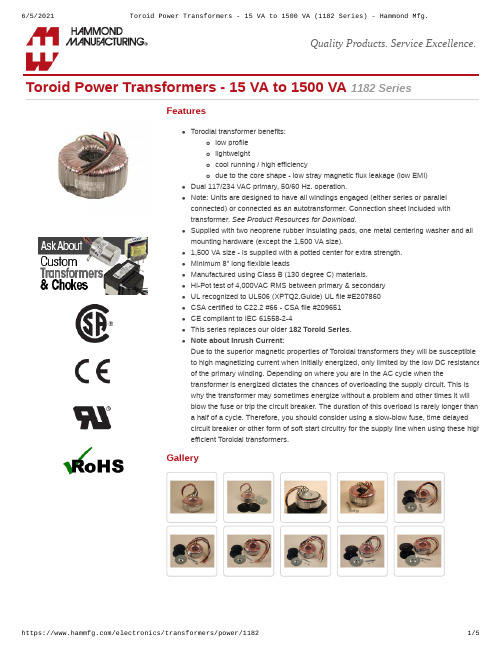
Quality Products. Service Excellence.Toroid Power Transformers - 15 VA to 1500 VA 1182 SeriesFeaturesTorodial transformer benefits:low profilelightweightcool running / high efficiencydue to the core shape - low stray magnetic flux leakage (low EMI)Dual 117/234 VAC primary, 50/60 Hz. operation.Note: Units are designed to have all windings engaged (either series or parallelconnected) or connected as an autotransformer. Connection sheet included withtransformer. See Product Resources for Download.Supplied with two neoprene rubber insulating pads, one metal centering washer and allmounting hardware (except the 1,500 VA size).1,500 VA size - is supplied with a potted center for extra strength.Minimum 8" long flexible leadsManufactured using Class B (130 degree C) materials.Hi-Pot test of 4,000VAC RMS between primary & secondaryUL recognized to UL506 (XPTQ2.Guide) UL file #E207860CSA certified to C22.2 #66 - CSA file #209651CE compliant to IEC 61558-2-4This series replaces our older 182 Toroid Series.Note about Inrush Current:Due to the superior magnetic properties of Toroidal transformers they will be susceptibleto high magnetizing current when initially energized, only limited by the low DC resistanceof the primary winding. Depending on where you are in the AC cycle when thetransformer is energized dictates the chances of overloading the supply circuit. This iswhy the transformer may sometimes energize without a problem and other times it willblow the fuse or trip the circuit breaker. The duration of this overload is rarely longer thana half of a cycle. Therefore, you should consider using a slow-blow fuse, time delayedcircuit breaker or other form of soft start circuitry for the supply line when using these highefficient Toroidal transformers.Gallery1182K615********************Dual12.41%Open A 1182L630************6V @ 5A Dual11.70%Open B 1182N650*********************Dual12.60%Open C 1182Q680**********************Dual9.70%Open D 1182H915**********************Dual11.42%Open A 1182K930*********************Dual12.80%Open B 1182M950*********************Dual13.20%Open C 1182N980*********************Dual10.50%Open D 1182Q9120**********************Dual9.00%Open E 1182K1230*********************Dual11.70%Open B 1182L1250**********************Dual12.60%Open C 1182M1280**********************Dual9.70%Open D 1182P1212024V C.T. @ 5A12V @ 10A Dual7.70%Open E 1182Q12160***********************Dual7.70%Open F 1182S12225***********************Dual7.20%Open G 1182T12300*************12V @ 25A Dual7.10%Open H 1182W121000**********************Dual 2.20%Open L-1 1182J153030V C.T. @ 1A15V @ 2A Dual12.30%Open B 1182K1550**********************Dual13.00%Open C 1182M1580**********************Dual10.20%Open D 1182N1512030V C.T. @ 4A15V @ 8A Dual8.50%Open E 1182P15160***********************Dual7.00%Open F 1182H15225************15V @ 15A Dual7.20%Open G 1182S1530030V C.T. @ 10A15V @ 20A Dual 5.00%Open H 1182F1815***********************Dual11.7%Open A 1182H1830**********************Dual12.20%Open B 1182J1850**********************Dual13.80%Open C 1182L1880**********************Dual10.50%Open D 1182M18120**********************Dual7.70%Open E 1182N18160**********************Dual7.70%Open F 1182G18225**********************Dual7.30%Open G 1182G2230**********************Dual12.60%Open B 1182J2250**********************Dual14.20%Open C 1182L2280**********************Dual10.40%Open D 1182M22120**********************Dual8.40%Open E1182N22160**********************Dual8.40%Open F 1182P22225***********************Dual 6.40%Open G 1182S24500************************Dual 5.10%Open I 1182T24625************************Dual 3.30%Open J 1182U24750************************Dual 3.60%Open L 1182V241000**********************Dual 2.20%Open L 1182K3080**********************Dual9.70%Open D 1182L3012060V C.T. @ 2A30V @ 4A Dual7.70%Open E 1182M30160**********************Dual7.70%Open F 1182F30225*********************Dual 6.30%Open G 1182P3030060V C.T. @ 5A30V @ 10A Dual 6.10%Open H 1182R30500***********************Dual 4.80%Open I 1182S30625************************Dual 4.10%Open J 1182T30750*************30V @ 25A Dual 3.10%Open K 1182T30P750*************30V @ 25A Dual 3.10%Potted K1182T601500120V C.T. @12.50A60V @ 25A Dual 2.91%Open M1182U301000**********************Dual 2.20%Open L 1182V40P1500**********************Dual 3.70%Potted MPart No.VAVAC Secondary (RMS)Dual or Single% Voltage Toroid Dim. Series Parallel Secondary Regulation Center Ref1182L60300*************60V @ 5A Dual 6.10%Open H 1182N60500***********************Dual 4.80%Open I 1182P60625************************Dual 4.10%Open J 1182Q60750***********************Dual 4.10%Open K 1182R601000**********************Dual 2.80%Open L 1182T60P1500**************60V @ 25A Dual 3.00%Potted M 1182L90225**********************Dual Open1182D11015**************************Dual11.9%Open A 1182E11030220V C.T. @ 136ma110V @ 272ma Dual13.10%Open B 1182G11050220V C.T. @ 227ma110V @ 454ma Dual14.10%Open C 1182H11080220V C.T. @ 364ma110V @ 728ma Dual10.50%Open D 1182J110120220V C.T. @ 545ma**********Dual8.40%Open E 1182K110160220V C.T. @ 727ma**********Dual8.00%Open F 1182L110225************************Dual 6.10%Open G 1182M110300************************Dual 6.10%Open H 1182P110500************************Dual 4.70%Open I 1182Q110625************************Dual 3.70%Open J 1182R110750************************Dual 3.10%Open K 1182S1101000**********************Dual 3.20%Open L 1182U110P1500***********************Dual 1.90%Potted M 1182E11730234V C.T. @ 128ma117V @ 256ma Dual12.40%Open B 1182G11750234V C.T. @ 214ma117V @ 428ma Dual13.40%Open C 1182H11780234V C.T. @ 342ma117V @ 684ma Dual10.00%Open D 1182J117120234V C.T. @ 513ma**********Dual8.00%Open E 1182K117160234V C.T. @ 684ma**********Dual7.60%Open F 1182L117225************************Dual 6.00%Open G 1182M117300************************Dual 5.80%Open H 1182N117500************************Dual 4.70%Open I 1182P117625************************Dual 3.80%Open J 1182Q117750************************Dual 3.60%Open K 1182R1171000***********************Dual 3.00%Open L 1182R117P1000***********************Dual 3.00%Potted L 1182T117P1500***********************Dual 2.10%Potted M 1182D24030-240V @ 125ma Single12.30%Open B 1182E24050-240V @ 208ma Single13.10%Open CPart No.VAVAC Secondary (RMS)Dual or Single% Voltage Toroid Dim. Series Parallel Secondary Regulation Center Ref1182F24080-240V @ 333ma Single9.90%Open D 1182G240120-*********Single7.90%Open E 1182H240160-240V @ 667ma Single7.70%Open F 1182J240225-**********Single 5.80%Open G 1182K240300-**********Single 5.80%Open H 1182L240500-**********Single 4.80%Open I 1182M240625-*********Single 3.70%Open J 1182N240750-**********Single 3.60%Open K 1182P2401000-**********Single 2.80%Open L 1182Q2401500-*********Single 2.30%Open M 1182Q240P1500-*********Single 2.30%Potted MMechanical & Schematic DataDimension VA OutsideHeight Inside Potted Included Mounting WeightReference Size Diameter Diameter Center Hardware(lbs.)(kg.) A15 2.65 1.20 1.25No10-24 x 1.75" bolt, with metal centering washer, nut, lockwasher & two (2) rubber insulating pads0.750.35 B30 3.00 1.25 1.50No10-24 x 1.75" bolt, with metal centering washer, nut, lockwasher & two (2) rubber insulating pads 1.10.5 C50 3.25 1.50 1.25No10-24 x 2.00" bolt, with metal centering washer, nut, lockwasher & two (2) rubber insulating pads 1.50.7 D80 3.50 1.50 1.60No10-24 x 2.00" bolt, with metal centering washer, nut, lockwasher & two (2) rubber insulating pads 2.11 E120 3.75 1.63 1.45No10-24 x 2.00" bolt, with metal centering washer, nut, lockwasher & two (2) rubber insulating pads3 1.3F160 4.25 1.75 1.70No 1/4-20 x 2.50" bolt, with metal centering washer, nut, lockwasher & two (2) rubber insulatingpads3.8 1.7G225 4.50 1.88 1.62No 1/4-20 x 2.50" bolt, with metal centering washer, nut, lockwasher & two (2) rubber insulatingpads4.7 2.1H300 4.88 1.88 1.85No 1/4-20 x 2.50" bolt, with metal centering washer, nut, lockwasher & two (2) rubber insulatingpads6 2.7I500 5.50 2.25 2.30No 1/4-20 x 3.00" bolt, with metal centering washer, nut, lockwasher & two (2) rubber insulatingpads9 4.1J625 5.88 2.38 2.45No 1/4-20 x 3.00" bolt, with metal centering washer, nut, lockwasher & two (2) rubber insulatingpads10.8 4.9K750 5.88 2.88 2.45No 3/8-16 x 3.50" bolt, with metal centering washer, nut, lockwasher & two (2) rubber insulatingpads12.9 5.8L1000 6.25 2.88 2.35No 3/8-16 x 3.50" bolt, with metal centering washer, nut, lockwasher & two (2) rubber insulatingpads16.37.4L-11000 6.85 3.402No 3/8-16 x 3.50" bolt, with metal centering washer, nut, lockwasher & two (2) rubber insulatingpads16.37.4M15007.25 3.25Potted Yes3/8-16 x 3.50" bolt, with nut, lockwasher & one (1) rubber bottom insulating pad23.210.5N15007.40 3.502No 3/8-16 x 3.50" bolt, with metal centering washer, nut, lockwasher & two (2) rubber insulatingpads24.7511.2Additional Hardware Kits:Part No.Additional Hardware Kit Metal WasherRubber Washer (included with transformers)DiameterSteelFor Use With Gauge Diameter Thickness1182KIT3030VA Models 10-24 x 1.75" bolt, with metal centering washer, nut, lockwasher & two (2)rubber insulating pads2.3718 2.500.061182KIT5050VA, 80VA & 120VA Models 10-24 x 2.00" bolt, with metal centering washer, nut, lockwasher & two (2)rubber insulating pads2.3718 2.500.061182KIT160160VA, 225VA & 300VA Models 1/4-20 x 2.50" bolt, with metal centering washer, nut, lockwasher & two (2)rubber insulating pads3.5616 3.750.061182KIT500500VA & 625VA Models 1/4-20 x 3.00" bolt, with metal centering washer, nut, lockwasher & two (2)rubber insulating pads4.3016 4.750.091182KIT750750VA & 1,000VA Models 3/8-16 x 3.50" bolt, with metal centering washer, nut, lockwasher & two (2)rubber insulating pads4.3016 4.750.091182KIT1500P1,500VA Models3/8-16 x 4.00" bolt, nut & lockwasher N/A N/AData subject to change without noticePart No.Additional Hardware Kit Metal WasherRubber Washer(included with transformers)Diameter SteelFor Use WithGauge Diameter Thickness 1182KIT1500Heavy Duty - Upgrade Kit1,500VA Models3/8-16 x 4.50" bolt, with metal centering washer, nut, lockwasher & two (2)rubber insulating pads4.30166.000.12© 2021. Hammond Manufacturing Ltd. All rights reserved.。
18号试验指测试标准

18号试验指测试标准
18号试验指是用于模拟儿童是否会触及电器设备中的危险部件的测试工具。
其测试标准主要包括以下几个方面:
1. 尺寸和形状:18号试验指的尺寸和形状需要符合相关标准,例如GB/T 16482图12等。
这些标准规定了试验指的长度、直径、倒圆角、节距等参数,以确保试验指能够代表儿童的手指尺寸和形状。
2. 材料和质地:18号试验指的材料和质地需要具有一定的硬度、韧性和耐
磨性,以确保在测试过程中不会因为材料的原因而影响测试结果。
3. 测试方法和程序:在测试过程中,需要按照规定的测试方法和程序进行操作。
例如,试验指需要按照规定的方向和角度插入设备的开口,测试过程中需要记录插入的深度和阻力等参数。
4. 结果判定:根据测试结果,判断电器设备是否符合标准要求。
一般来说,如果试验指能够顺利插入设备的开口,并且没有明显的阻力或异常现象,则认为设备符合标准要求;反之,则认为设备不符合标准要求。
需要注意的是,不同的国家和地区可能会有不同的测试标准和要求,因此在实际应用中需要根据具体的标准和要求进行测试和判断。
同时,由于试验指测试涉及到人身安全问题,因此测试人员需要经过专业培训并具备相应的资质和经验,以确保测试结果的准确性和可靠性。
MAX6018 精确、低电压、低掉电、微电压电压参考说明书

MAX6018AEUR16+ T MAX6018AEUR12+TMAX6018AEUR18+TMAX6018AEUR21+TMAX6018BEUR16+TGeneral DescriptionThe MAX6018 is a precision, low-voltage, low-dropout, micropower voltage reference in a SOT23 package. This three-terminal reference operates with an input voltage from (V OUT + 200mV) to 5.5V, and is available with output voltage options of 1.2V, 1.6V, 1.8V, and 2.048VThe MAX6018 voltage reference consumes less than 5μA (max) of supply current and can source and sink up to 1mA of load current. Unlike conventional shunt-mode (two-terminal) references that waste supply current and require an external resistor, devices in the MAX6018 family offer a supply current that is virtually independent of supply voltage (with only 0.1μA/V variation with supply voltage) and do not require an external resistor. The MAX6018 has initial accuracies of 0.2% (A grade) and 0.4% (B grade) and temperature drift of 50ppm/°C (max). The low-dropout voltage and the ultra-low, supply voltage-independent supply current make this device ideal for two-cell alkaline, end-of-life, battery-monitoring systems. The MAX6018 is available in a tiny 3-pin SOT23 package.Applications●Two-Cell, Battery-Operated Systems ●Battery-Operated Equipment ●Hand-Held Equipment ●Data-Acquisition Systems●Industrial and Process-Control SystemsBenefits and Features●Ultra-Low Supply Current: 5μA (max) ● 1.6V Output from 1.8V Input ●Ultra-Small, 3-Pin SOT23 Package ●Initial Accuracy: ±0.2% (max)●Low Temperature Drift: 50ppm/°C (max) ●200mV Dropout Voltage●Load Regulation (1mA Source): 700μV/mA (max) ●Line Regulation (V OUT + 200mV) to 5.5V: 250μV/V(max) ●Four Output Voltage Options: 1.2V, 1.6V,1.8V,2.048VPARTTEMP RANGE PIN-PACKAGE TOP MARK MAX6018AEUR12+T -40°C to +85°C 3 SOT23-3FZJH MAX6018BEUR12+T -40°C to +85°C 3 SOT23-3FZJI MAX6018AEUR16+T -40°C to +85°C 3 SOT23-3FZJJ MAX6018BEUR16+T -40°C to +85°C 3 SOT23-3FZJK MAX6018AEUR18+T -40°C to +85°C 3 SOT23-3FZJL MAX6018BEUR18+T -40°C to +85°C 3 SOT23-3FZJM MAX6018AEUR21+T -40°C to +85°C 3 SOT23-3FZJN MAX6018BEUR21+T-40°C to +85°C3 SOT23-3FZJOPARTOUTPUT VOLTAGE (V)INITIAL ACCURACY (%)MAX6018AEUR12 1.263±0.2MAX6018BEUR12 1.263±0.4MAX6018AEUR16 1.600±0.2MAX6018BEUR16 1.600±0.4MAX6018AEUR18 1.800±0.2MAX6018BEUR18 1.800±0.4MAX6018AEUR21 2.048±0.2MAX6018BEUR212.048±0.4MAX6018Precision, Micropower, 1.8V Supply, Low-Dropout, SOT23 Voltage ReferenceTypical Application CircuitPin ConfigurationOrdering InformationSelector Guide(Voltages Referenced to GND)V IN ...........................................................................-0.3V to +6V Output Short-Circuit Duration to GND or V IN............Continuous Continuous Power Dissipation (T A = +70°C)3-Pin SOT23 (derate 4.0mW/°C above +70°C) ..........320mW Operating Temperature Range ...........................-40°C to +85°C Junction Temperature ......................................................+150°C Storage Temperature Range ............................-65°C to +150°C Lead Temperature (soldering, 10s) .................................+300°C(V IN = 1.8V; C OUT = 47nF, I OUT = 0; T A = T MIN to T MAX, unless otherwise noted. Typical values are at T A = +25°C.) (Note 1) PARAMETER SYMBOL CONDITIONS MIN TYP MAX UNITS OUTPUTOutput Voltage V OUT MAX6018A_12 (0.2%) 1.2605 1.2630 1.2655V MAX6018B_12 (0.4%) 1.2580 1.2630 1.2681Output Voltage Temperature Drift TCV OUT(Note 2)1650ppm/°CLine Regulation ΔV OUT/ΔV IN1.8V ≤ V IN ≤ 5.5V50400µV/VLoad Regulation ΔV OUT/ΔI OUT0 ≤ I OUT ≤ 1mA90700µV/mA-100µA ≤ I OUT ≤ 029µV/µAShort-Circuit Current I SC Sourcing to GND3mA Sinking from V IN6Long-Term Stability ΔV OUT/Time1000hrs at T A = +25°C100ppmThermal Hysteresis(Note 4)130ppm DYNAMIC CHARACTERISTICSNoise Voltage e OUT 0.1Hz to 10Hz45µV p-p 10Hz to 10kHz100µV RMSRipple Rejection V IN = 1.8V ±100mV (f = 120Hz)85dB Turn-On Settling Time t R Settling to 0.1%; C OUT = 5nF200µs Capacitive-Load Stability Range C OUT(Note 2)471000nF INPUTSupply Voltage Range V IN Guaranteed by Line Regulation Test 1.8 5.5VQuiescent Supply Current I IN T A = +25°C35µA T A = T MIN to T MAX36Change in Quiescent Supply Current vs. Input Voltage ΔI IN/ΔV IN 1.8V ≤ V IN ≤ 5.5V0.10.5µA/VMAX6018Precision, Micropower, 1.8V Supply,Low-Dropout, SOT23 Voltage Reference Absolute Maximum RatingsStresses beyond those listed under “Absolute Maximum Ratings” may cause permanent damage to the device. These are stress ratings only, and functional operation of the device at these or any other conditions beyond those indicated in the operational sections of the specifications is not implied. Exposure to absolute maximum rating conditions for extended periods may affect device reliability.Electrical Characteristics (MAX6018_12–1.263V)(V IN = 1.8V; C OUT = 47nF, I OUT = 0; T A = T MIN to T MAX, unless otherwise noted. Typical values are at T A = +25°C.) (Note 1) PARAMETER SYMBOL CONDITIONS MIN TYP MAX UNITS OUTPUTOutput Voltage V OUT MAX6018A_16 (0.2%)T A = +25°C 1.5968 1.6000 1.6032V MAX6018B_16 (0.4%)T A = +25°C 1.5936 1.6000 1.6064Output Voltage Temperature Drift TCV OUT(Note 2)1650ppm/°CLine Regulation ΔV OUT/ΔV IN1.8V ≤ V IN ≤ 5.5V40250µV/VLoad Regulation ΔV OUT/ΔI OUT0 ≤ I OUT ≤ 1mA90700µV/mA-750µA ≤ I OUT ≤ 00.650µV/µADropout Voltage (Note 3)V IN - V OUT I OUT = 1mA100200mVShort-Circuit Current I SC Sourcing to GND6mA Sinking from V IN2Long-Term Stability ΔV OUT/Time1000hrs at T A = +25°C100ppmThermal Hysteresis(Note 4)130ppm DYNAMIC CHARACTERISTICSNoise Voltage e OUT 0.1Hz to 10Hz40µV p-p 10Hz to 10kHz150µV RMSRipple Rejection V IN = 1.8V ±100mV (f = 120Hz)85dB Turn-On Settling Time t R Settling to 0.1%; C OUT = 5nF200µs Capacitive-Load Stability Range C OUT(Note 2)0.11000nF INPUTSupply Voltage Range V IN Guaranteed by Line Regulation Test 1.8 5.5VQuiescent Supply Current I IN T A = +25°C35µA T A = T MIN to T MAX36Change in Quiescent Supply Current vs. Input Voltage ΔI IN/ΔV IN 1.8V ≤ V IN ≤ 5.5V0.10.5µA/VMAX6018Precision, Micropower, 1.8V Supply,Low-Dropout, SOT23 Voltage Reference Electrical Characteristics (MAX6018_16–1.600V)(V IN = 2.0V; C OUT = 47nF, I OUT = 0; T A = T MIN to T MAX, unless otherwise noted. Typical values are at T A = +25°C.) (Note 1) PARAMETER SYMBOL CONDITIONS MIN TYP MAX UNITS OUTPUTOutput Voltage V OUT MAX6018A_18 (0.2%)T A = +25°C 1.7964 1.8000 1.8036V MAX6018B_18 (0.4%)T A = +25°C 1.7928 1.8000 1.8072Output Voltage Temperature Drift TCV OUT(Note 2)1650ppm/°CLine Regulation ΔV OUT/ΔV IN2.0V ≤ V IN ≤ 5.5V40275µV/VLoad Regulation ΔV OUT/ΔI OUT0 ≤ I OUT ≤ 1mA90800µV/mA-1mA ≤ I OUT ≤ 00.450µV/µADropout Voltage (Note 3)V IN - V OUT I OUT = 1mA100200mVShort-Circuit Current I SC Sourcing to GND7.5mA Sinking from V IN3Long-Term Stability ΔV OUT/Time1000hrs at T A = +25°C100ppmThermal Hysteresis(Note 4)130ppm DYNAMIC CHARACTERISTICSNoise Voltage e OUT 0.1Hz to 10Hz45µV p-p 10Hz to 10kHz160µV RMSRipple Rejection V IN = 2.0V ±100mV (f = 120Hz)85dB Turn-On Settling Time t R Settling to 0.1%; C OUT = 5nF200µs Capacitive-Load Stability Range C OUT(Note 2)0.11000nF INPUTSupply Voltage Range V IN Guaranteed by Line Regulation Test 2.0 5.5VQuiescent Supply Current I IN T A = +25°C35µA T A = T MIN to T MAX36Change in Quiescent Supply Current vs. Input Voltage ΔI IN/ΔV IN2V ≤ V IN ≤ 5.5V0.10.5µA/VMAX6018Precision, Micropower, 1.8V Supply,Low-Dropout, SOT23 Voltage Reference Electrical Characteristics (MAX6018_18–1.800V)(V IN = 2.25V; C OUT = 47nF, I OUT = 0; T A = T MIN to T MAX , unless otherwise noted. Typical values are at T A = +25°C.) (Note 1)Note 1: Devices are 100% production tested at T A = +25°C and are guaranteed by design from T A = T MIN to T MAX .Note 2: Not production tested. Guaranteed by design.Note 3: Dropout voltage is the minimum input voltage at which V OUT changes ≤ 0.2% from V OUT at rated V IN and is guaranteed byLoad Regulation Test.Note 4: Thermal hysteresis is defined as the change in T A = +25°C output voltage before and after temperature cycling of the device(from T A = T MIN to T MAX ). Initial measurement at T A = +25°C is followed by temperature cycling the device to T A = +85°C then to T A = -40°C and another measurement at T A = +25°C is compared to the original measurement at T A = +25°C.PARAMETERSYMBOLCONDITIONSMINTYPMAXUNITSOUTPUT Output VoltageV OUT MAX6018A_21 (0.2%)T A = +25°C 2.0439 2.0480 2.0521V MAX6018B_21 (0.4%)T A = +25°C2.03982.0480 2.0562Output Voltage Temperature Drift TCV OUT (Note 2)1650ppm/°C Line Regulation ΔV OUT /ΔV IN 2.25V ≤ V IN ≤ 5.5V 45330µV/V Load Regulation ΔV OUT /ΔI OUT0 ≤ I OUT ≤ 1mA 901000µV/mA -1mA ≤ I OUT ≤ 00.350µV/µA Dropout Voltage (Note 3)V IN - V OUT I OUT = 1mA100200mV Short-Circuit Current I SC Sourcing to GND 10mA Sinking from V IN 4Long-Term Stability ΔV OUT /Time1000hrs at T A = +25°C 100ppm Thermal Hysteresis(Note 4)130ppmDYNAMIC CHARACTERISTICS Noise Voltage e OUT0.1Hz to 10Hz 50µV p-p 10Hz to 10kHz175µV RMS Ripple Rejection V IN = 2.25V ±100mV (f = 120Hz)85dB Turn-On Settling Timet R Settling to 0.1%; C OUT = 5nF 200µs Capacitive-Load Stability Range C OUT (Note 2)0.11000nFINPUTSupply Voltage Range V IN Guaranteed by Line Regulation Test 2.255.5V Quiescent Supply CurrentI INT A = +25°C 35µAT A = T MIN to T MAX36Change in Quiescent SupplyCurrent vs. Input VoltageΔI IN /ΔV IN 2.25V ≤ V IN ≤ 5.5V 0.10.5µA/VMAX6018Precision, Micropower, 1.8V Supply, Low-Dropout, SOT23 Voltage ReferenceElectrical Characteristics (MAX6018_21–2.048V)(T A = +25°C, unless otherwise noted.) 2.0432.0452.0442.0472.0462.0492.0482.050-5025-255075100MAX6018_21OUTPUT VOLTAGE DRIFT vs. TEMPERATUREM A X 6018 t o c 02TEMPERATURE (°C)O U T P U T V O L T A G E (V )1.2601.2631.2621.2611.2641.2651.26604003001002005006007008009001000MAX6018_12LONG-TERM DRIFTM A X 6018 t o c 03TIME (HOURS)O U T P U T V O L T A G E (V )2.0452.0462.0472.0482.0492.05004005002003001006007008009001000MAX6018_21LONG-TERM DRIFTM A X 6018 t o c 04TIME (HOURS)O U T P U T V O L T A G E (V )0.050.150.100.200.251.5 2.5 3.02.0 3.5 4.0 4.5 5.0 5.5MAX6018_12LINE REGULATIONINPUT VOLTAGE (V)O U T P U T V O L T A G E C H A R G E (m V )0.050.150.100.200.250.30 2.53.02.03.54.04.55.05.5MAX6018_21LINE REGULATIONINPUT VOLTAGE (V)O U T P U T V O L T A G E C H A N G E (m V)020*********1201400.40.20.60.81.01.2MAX6018_21DROPOUT VOLTAGE vs. SOURCE CURRENTSOURCE CURRENT (mA)D R O P O U T V O L T A G E (m V )1.26101.26151.26251.26201.26301.2635-50-25255075100MAX6018_12OUTPUT VOLTAGE DRIFT vs. TEMPERATUREM A X 6018 t o c 01TEMPERATURE (°C)O U T P U T V O L T A G E (V )-0.20-0.10.20.10.40.30.50.70.60.8-1.0-0.6-0.4-0.2-0.800.20.40.80.6 1.0MAX6018_12LOAD REGULATIONLOAD CURRENT (mA)O U T P U T V O L T A G E C H A N G E (m V )-0.20-0.10.20.10.40.30.50.70.6-1.0-0.4-0.2-0.6-0.80.40.200.60.8 1.0MAX6018_21LOAD REGULATIONSOURCE CURRENT (mA)O U T P U T V O L T A G E C H A N G E (m V )MAX6018Precision, Micropower, 1.8V Supply, Low-Dropout, SOT23 Voltage ReferenceTypical Operating Characteristics(T A = +25°C, unless otherwise noted.)02010504030807060901100101k10k100kPOWER-SUPPLY REJECTION RATIOvs. FREQUENCYM A X 6018 t o c 10FREQUENCY (Hz)P S R R (d B )2.903.053.002.953.103.153.203.253.303.353.40132456SUPPLY CURRENT vs. INPUT VOLTAGEINPUT VOLTAGE (V)S U P P L Y C U R R E N T (µA )0.0110.1101001k 10k 100k0.0110.1101001k10kOUTPUT IMPEDANCE vs. FREQUENCYM A X 6018 t o c 12FREQUENCY (Hz)O U T P U T I M P E D A N C E (Ω)2.02.4 2.23.02.82.63.63.43.23.84.0-50-25255075100SUPPLY CURRENT vs. TEMPERATURETEMPERATURE (°C)S U P P L Y C U R R E N T (µA )20µV/divMAX6018_210.1Hz TO 10Hz OUTPUT NOISEM A X 6018 t o c 1410s/divMAX6018_12TURN-ON TRANSIENTV OUT 500mV/divV IN 1V/div100µs/divC OUT = 5nFV IN 1V/divV OUT 1V/div MAX6018_21TURN-ON TRANSIENT50µs/div C OUT = 5nFV IN 1V/divV OUT 1V/divMAX6018_21TURN-OFF TRANSIENT2ms/divC OUT = 5nFMAX6018_12LOAD-TRANSIENT RESPONSEMAX6018 toc18V OUT 500mV/divI OUT 500µA/div-300µA+1mA100µs/divC OUT = 150pF MAX6018Precision, Micropower, 1.8V Supply, Low-Dropout, SOT23 Voltage ReferenceTypical Operating Characteristics (continued)(T A = +25°C, unless otherwise noted.)Detailed DescriptionThe MAX6018 is a precision, low-voltage, low-dropout, micropower, bandgap voltage reference in a SOT23 package. This three-terminal reference operates with an input voltage from (V OUT + 200mV) to 5.5V, and is available with output voltage options of 1.2V, 1.6V, 1.8V, and 2.048V. These devices can source up to 1mA with <200mV of dropout voltage, making them attractive for use in low-voltage applications.Applications InformationOutput/Load CapacitanceThese devices require a minimum of 100pF load to maintain output stability.They remain stable for capacitive loads as high as 1μF. In applications where the load or the supply can experience step changes, a larger output capacitor reduces the amount of overshoot (or undershoot) and assists the circuit’s transient response. Otherwise, applications may not need more than 100pF.Supply CurrentThe 5μA maximum supply current varies only 0.1μA/V with the supply voltage.When the supply voltage is below the minimum-specified input voltage (as during turn-on), the devices can draw up to 20μA beyond the nominal supply current. The input voltage source must be capable of providing this current to ensure reliable turn-on.Turn-On TimeThese devices typically turn on and settle to within 0.1% of their final value in 200μs. The turn-on time can increase up to 1ms with the device operating at the minimum dropout voltage and the maximum load.PIN NAME FUNCTION1INSupply Voltage Input. Bypass with a 0.1µF capacitor to ground.2OUT Reference Voltage Output. Bypass with at least 100pF to ground. (See Output/Load Capacitance section).3GNDGroundI OUT 1mA/div+1mA-1mAV OUT 1V/divMAX6018_21LOAD-TRANSIENT RESPONSE100µs/divC OUT = 150pFMAX6018_12LINE-TRANSIENT RESPONSEV OUT 50mV/divV IN200mV/div100µs/divV IN200mV/divV OUT 50mV/divMAX6018_21LINE-TRANSIENT RESPONSE100µs/divC OUT = 550pFMAX6018Precision, Micropower, 1.8V Supply, Low-Dropout, SOT23 Voltage ReferencePin DescriptionTypical Operating Characteristics (continued)MAX6018Precision, Micropower, 1.8V Supply,Low-Dropout, SOT23 Voltage Reference Package InformationFor the latest package outline information and land patterns(footprints), go to /packages. Notethat a “+”, “#”, or “-” in the package code indicates RoHS statusonly. Package drawings may show a different suffix character, butthe drawing pertains to the package regardless of RoHS status.PACKAGE TYPE PACKAGECODE OUTLINE NO.LANDPATTERN NO.3 SOT23U3+121-005190-0179Chip Information TRANSISTOR COUNT: 87 PROCESS: BiCMOSMaxim Integrated cannot assume responsibility for use of any circuitry other than circuitry entirely embodied in a Maxim Integrated product. No circuit patent licenses are implied. Maxim Integrated reserves the right to change the circuitry and specifications without notice at any time. The parametric values (min and max limits) shown in the Electrical Characteristics table are guaranteed. Other parametric values quoted in this data sheet are provided for guidance.Maxim Integrated and the Maxim Integrated logo are trademarks of Maxim Integrated Products, Inc.MAX6018Precision, Micropower, 1.8V Supply, Low-Dropout, SOT23 Voltage Reference© 2015 Maxim Integrated Products, Inc. │ 10Revision HistoryREVISIONNUMBERREVISION DATE DESCRIPTION PAGES CHANGED 310/15Added lead-free options 1For pricing, delivery, and ordering information, please contact Maxim Direct at 1-888-629-4642, or visit Maxim Integrated’s website at .MAX6018BEUR18+ T MAX6018BEUR12+TMAX6018BEUR21+TMAX6018AEUR16+ T MAX6018AEUR12+TMAX6018AEUR18+TMAX6018AEUR21+TMAX6018BEUR16+T。
Belden 18 AWG 16x30 Tinned Copper 电线说明书

Yes
EU Directive 2002/95/EC (RoHS):
Yes
EU RoHS Compliance Date (mm/dd/yyyy):
07/01/2005
EU Directive 2002/96/EC (WEEE):
Yes
EU Directive 2003/11/EC (BFR):
Yes
CA Prop 65 (CJ for Wire & Cable):
Yes
MII Order #39 (China RoHS):
YesLeabharlann Flame Test UL Flame Test:
VW-1
CSA Flame Test:
FT1
Plenum/Non-Plenum
Plenum (Y/N):
No
Electrical Characteristics (Overall)
Color BROWN BROWN RED RED RED ORANGE ORANGE YELLOW YELLOW YELLOW GREEN, DARK GREEN, DARK GREEN, DARK VIOLET GRAY GRAY WHITE WHITE WHITE BLACK BLACK BLACK BLUE, DARK BLUE, DARK BLUE, DARK GREEN/YELLOW GREEN/YELLOW
Nom. Conductor DC Resistance: DCR @ 20°C (Ohm/1000 ft) 5.900
Max. Recommended Current:
Description
Current
Single conductor in free air @ 30C ambient 20 amps
LED18WT8F 48 XXX-G5D和LED18WT8F 48 XXXK-G6D系列LED灯具说

LED18WT8F/48/XXX-G5D series LED18WT8F/48/XXXK-G6D series Min. Dimension of Lighting Fixture : 1215 x 600 x 80 mm Max. 4 pcs LED tubes allowed, each tube spaced 15.5 cm apart.The tube can be extended utilizing with four in one ceiling or type IC recessed luminaires. The retrofit consists of installation manual(1 pcs), LED tube(1 pcs), relamping and cautionary label(1 pcs).Installation GuideFigure ARetrofit with One lampRetrofit Instruction ** During Retrofit, rewiring is a MUST, please always follow the installation instruc-tion below.1) Ensure power is off to luminaire by disconnecting the supply voltage 2) Remove all fluorescent lamps and starters, cut off all wires which are connected to ballast.3) Wire luminaire to the configuration shown on drawing figure A/B (Note: LED T8 tube will not work with shunted lamp holders.)4) Place warning label found in LED retrofit lamp package to ensure that the user understands that the system now uses LED tubes and replacement with fluorescent can cause damage 5) Insert LED retrofit lamp 6) Turn power back on and check for proper operationBEFORE YOU BEGIN Read these instructions completely and carefully.WARNING Risk of fire or electric shock. LED Retrofit installation must be done by a qualified electrician only and all safety instructions must be followed to avoid a risk of injury or property damage.WARNING Risk of Electric Shock. Disconnect power before installation of the product.LED T8 Tube Lights Figure BRetrofit with Two lamp and one ballastCAUTION-To avoid potential fire or shock hazard, do not use this retrofit lamp in luminaires em-ploying shunted bi-pin lampholders. Note: shunted lamp holders are found only in fluo-rescent luminaires with Instant-Start ballast, which can be indentified by the words “Instant Start” or “I.S” marked on the ballast.-A label needs to be placed onto the fixture in a location that is visible during retrofit that has the following caution. “*This luminaire has been modified and can no longer operate the originally intended lamp. *The LED retrofit has been installed and fixture has been modified so that it only works with EIKO product.”-NOT FOR USE WITH DIMMERSSafety Notes-Do not place lamps near combustible materials such as paper, alcohol, paint, etc., so as not to cause fire or electric shock-Under abnormal situations, please power off the lamp to repair and check, such as parts, light loose, cracking, smoking, and abnormal luminescence.-Do not expose to high humidity environment, since this lamp is only suitable for indoor -WARNING: To avoid potential fire or shock hazard, do not use this retrofit kit in lumi-naires employing shunted bi-pin lampholders. Note: Shunted lamp holders are found only in fluorescent luminaires with Instant-Start ballasts. Instant-start ballasts can be identified by the words “Instant Start” or “I.S.” marked on the ballast. This designation may be in the form of a statement pertaining to the ballast itself, or may be combined with the marking for the lamps with which the ballast is intended to be used, for example F40T12/IS. For more information, contact the LED luminaire retrofit kit manufacturer.-WARNING – Risk of fire or electric shock. LED Retrofit Kit installation requires knowl-edge of luminaires electrical systems. If not qualified, do not attempt installation. Con-tact a qualified electrician-WARNING – Risk of fire or electric shock. Install this kit only in the luminaires that have the construction features and dimensions shown in the photographs and/or drawings and where the input rating of the retrofit kit does not exceed the input rating of the lumi-naire.-Do not make or alter any open holes in an enclosure of wiring or electrical components during kit installation.-Installers should not disconnect existing wires from lampholder terminals to make new connections at lampholder terminals. Instead installers should cut existing lampholder leads away from the lampholder and make new electrical connections to lampholder lead wires by employing applicable connectors.-WARNING – To prevent wiring damage or abrasion, do not expose wiring to edges of sheet metal or other sharp objects.-WARNING – Risk of fire or electric shock. Luminaire wiring and electrical parts may be damaged when drilling for installation of LED retrofit kit. Check for enclosed wiring and components.-NOT FOR EMERGENCY LIGHTING。
- 1、下载文档前请自行甄别文档内容的完整性,平台不提供额外的编辑、内容补充、找答案等附加服务。
- 2、"仅部分预览"的文档,不可在线预览部分如存在完整性等问题,可反馈申请退款(可完整预览的文档不适用该条件!)。
- 3、如文档侵犯您的权益,请联系客服反馈,我们会尽快为您处理(人工客服工作时间:9:00-18:30)。
For pricing, delivery, and ordering information, please contact Maxim Direct at 1-888-629-4642,or visit Maxim's website at .General DescriptionThe MAX1818 low-dropout linear regulator operates from a +2.5V to +5.5V supply and delivers a guaran-teed 500mA load current with low 120mV dropout. The high-accuracy (±1%) output voltage is preset at an internally trimmed voltage (see Selector Guide ) or can be adjusted from 1.25V to 5.0V with an external resis-tive divider.An internal PMOS pass transistor allows the low 125µA supply current to remain independent of load, making this device ideal for portable battery-operated equip-ment such as personal digital assistants (PDAs), cellu-lar phones, cordless phones, base stations, and notebook computers.Other features include an active-low open-drain reset output that indicates when the output is out of regula-tion, a 0.1µA shutdown, short-circuit protection, and thermal shutdown protection. The device is available in a miniature 800mW 6-pin SOT23 package.ApplicationsNotebook ComputersCellular and Cordless Telephones Personal Digital Assistants (PDAs)Palmtop Computers Base Stations USB Hubs Docking StationsFeatures♦Guaranteed 500mA Output Current ♦Low 120mV Dropout at 500mA♦±1% Output Voltage AccuracyPreset at 1.5V, 1.8V, 2.0V, 2.5V, 3.3V, 5V Adjustable from 1.25V to 5.0V ♦Power OK Output♦Low 125µA Ground Current ♦0.1µA Shutdown Current ♦Thermal Overload Protection ♦Output Current Limit♦Tiny 800mW 6-Pin SOT23 PackageMAX1818500mA Low-DropoutLinear Regulator in SOT23________________________________________________________________Maxim Integrated Products 119-1860; Rev 2; 6/08Ordering Information*Insert the desired two-digit suffix (see Selector Guide) into the blanks to complete the part number.Typical Operating CircuitPin ConfigurationNote :The MAX1818 requires a special solder temperature profile described in the Absolute Maximum Ratings section.T = Tape and reel.#Denotes an RoHS-compliant package.Selector Guide appears at end of data sheet.M A X 1818500mA Low-DropoutLinear Regulator in SOT23ABSOLUTE MAXIMUM RATINGSELECTRICAL CHARACTERISTICSStresses beyond those listed under “Absolute Maximum Ratings” may cause permanent damage to the device. These are stress ratings only, and functional operation of the device at these or any other conditions beyond those indicated in the operational sections of the specifications is not implied. Exposure to absolute maximum rating conditions for extended periods may affect device reliability.IN,SHDN ,POK, SET to GND...................................-0.3V to +6V OUT to GND ................................................-0.3V to (V IN + 0.3V)Output Short-Circuit Duration...............................................1min Continuous Power Dissipation (T A = +70°C) (Note 1)6-Pin SOT23 (derate 10mW/°C above +70°C)..............800mWOperating Temperature Range ...........................-40°C to +85°C Junction Temperature......................................................+150°C Storage Temperature Range.............................-65°C to +150°C Lead Temperature (soldering, 10s) (Note 2)...................+300°CNote 1:Thermal properties are specified with product mounted on PC board with one square-inch of copper area and still air. Withminimal copper, the SOT23 package dissipates 712mW at +70°C. With a quarter square inch of copper, it will dissipate 790mW at +70°C. Copper should be equally shared between the IN, OUT, and GND pins.Note 2:This device is constructed using a unique set of packaging techniques that imposes a limit on the thermal profile to whichthe device can be exposed during board-level solder attach and rework. The limit permits only the use of the solder profiles recommended in the industry standard specification, IPC JEDEC-J-STD-020A, paragraph 7.6, Table 3 for the IR/VPR and convection reflow. Preheating is required. Hand or wave soldering is not allowed.MAX1818500mA Low-DropoutLinear Regulator in SOT23_______________________________________________________________________________________3ELECTRICAL CHARACTERISTICS (continued)Note 4:The Dropout Voltage is defined as V IN - V OUT , when V OUT is 100mV below the value of V OUT measured for V IN = V OUT(NOM)+ 500mV. Since the minimum input voltage is 2.5V, this specification is only meaningful when V OUT(NOM)> 2.5V. For V OUT(NOM)between 2.5V and 3.5V, use the following equations: Typical Dropout = -93mV/V ✕V OUT(NOM)+ 445mV;Guaranteed Maximum Dropout = -137mV/V ✕V OUT(NOM)+7004mV. For V OUT(NOM)> 3.5V, Typical Dropout = 120mV;Maximum Dropout = 220mV.Typical Operating Characteristics(V IN = (V OUT + 500mV) or +2.5V, whichever is greater; SHDN = IN, C IN = 1µF, C OUT = 3.3µF, T A = +25°C, unless otherwise noted.)5025125100751501752252002500 1.0 1.50.5 2.0 2.5 3.0 3.5 4.0 4.5 5.0 5.5GROUND PIN CURRENT vs. INPUT VOLTAGEINPUT VOLTAGE (V)G R O U N D P I N C U R R E N T (μA )4070558513014511510016000.20.30.40.50.10.60.70.80.9 1.0LOAD CURRENT (A)G R O U N D P I N C U R R E N T (μA )GROUND PIN CURRENT vs. LOAD CURRENT110130120150140160170-4010-15356085TEMPERATURE (°C)G R O U N D P I N C U R R E N T (μA )GROUND PIN CURRENT vs. TEMPERATUREM A X 1818500mA Low-DropoutLinear Regulator in SOT234_______________________________________________________________________________________Typical Operating Characteristics (continued)(V IN = (V OUT + 500mV) or +2.5V, whichever is greater; SHDN = IN, C IN = 1µF, C OUT = 3.3µF, T A = +25°C, unless otherwise noted.)060301209015018000.20.10.30.40.5LOAD CURRENT (A)D R O P O U T V O L T A GE (m V )DROPOUT VOLTAGE vs. LOAD CURRENT-3.0-2.0-2.5-1.5-1.0-0.500.51.01.52.02.53.0LOAD CURRENT (A)O U T P U T V O L T A G E A C C U R A C Y (%)0.20.30.40.10.50.60.70.90.8 1.0OUTPUT VOLTAGE ACCURACYvs. LOAD CURRENT-3.0-2.0-2.5-1.5-1.0-0.500.51.01.52.02.53.0-40-1510356085TEMPERATURE (°C)O U T P U T V O L T A G E A C C U R A C Y (%)OUTPUT VOLTAGE ACCURACYvs. TEMPERATUREPOWER-SUPPLY REJECTION RATIOvs. FREQUENCY8002010P S R R (d B )40305060700.010.11101001000FREQUENCY (kHz)LINE TRANSIENTMAX1818 toc08V INV OUT2.5V 10m V /d i v3.5V 100μs/div500m V /d i vLOAD-TRANSIENT RESPONSEMAX1818 toc09I OUTV OUT500mA 100mA20m V /d i v40μs/divV IN = 3.3V V OUT = 2.5V LOAD-TRANSIENT RESPONSENEAR DROPOUTMAX1818 toc10V O U T 100m V /d i v200m A 0I O U T10μs/div V IN = V OUT + 100mV V OUT = 3.3VPOWER-ON RESETMAX1818 toc11V INV POKV OUT2V/div10ms/divMAX1818500mA Low-DropoutLinear Regulator in SOT23_______________________________________________________________________________________5SHUTDOWN WAVEFORMMAX1818 toc12POK SHUTDOWN VOLTAGEV OUT02V/div200μs/div1.001.011.021.031.041.051.061.071.081.091.101.112.53.03.54.04.55.05.5SHORT-CIRCUIT CURRENT LIMITvs. SUPPLY VOLTAGESUPPLY VOLTAGE (V)S H O R T -C I R C U I T C U R R E N T L I M I T (A )The MAX1818 is a low-dropout, low-quiescent-current linear regulator designed primarily for battery-powered applications. The device supplies loads up to 500mA and is available with preset output voltages. As illustrat-ed in Figure 1, the MAX1818 consists of a 1.25V refer-ence, error amplifier, P-channel pass transistor, and internal feedback voltage-divider.The 1.25V reference is connected to the error amplifier,which compares this reference with the feedback volt-age and amplifies the difference. If the feedback volt-age is lower than the reference voltage, thevoltage. If the feedback voltage is too high, the pass-transistor gate is pulled up, allowing less current to pass to the output.The output voltage is fed back through either an inter-nal resistive divider connected to OUT or an external resistor network connected to SE T. The Dual Mode comparator examines V SET and selects the feedback path. If V SET is below 50mV, the internal feedback path is used and the output is regulated to the factory-preset voltage.Pin DescriptionTypical Operating Characteristics (continued)(V IN = (V OUT + 500mV) or +2.5V, whichever is greater; SHDN = IN, C IN = 1µF, C OUT = 3.3µF, T A = +25°C, unless otherwise noted.)M A X 1818500mA Low-DropoutLinear Regulator in SOT236_______________________________________________________________________________________Additional blocks include an output current limiter, ther-mal sensor, and shutdown logic.Internal P-Channel Pass TransistorThe MAX1818 features a 0.25ΩP-channel MOSFE T pass transistor. Unlike similar designs using PNP pass transistors, P-channel MOSFETs require no base drive,which reduces quiescent current. PNP-based regula-tors also waste considerable current in dropout when the pass transistor saturates, and use high base-drive currents under large loads. The MAX1818 does not suf-fer from these problems and consumes only 125µA of quiescent current under heavy loads as well as in dropout.Output Voltage SelectionThe MAX1818’s Dual Mode operation allows operation in either a preset voltage mode or an adjustable mode.Connect SE T to GND to select the preset output volt-age. The two-digit part number suffix identifies the out-put voltage (see Selector Guide). For example, the MAX1818EUT33 has a preset 3.3V output voltage.The output voltage may also be adjusted by connecting a voltage-divider from OUT to SE T to GND (Figure 2).Select R2 in the 25k Ωto 100k Ωrange. Calculate R1with the following equation:R1 = R2 [(V OUT / V SET ) – 1]where V SET = 1.25V, and V OUT may range from 1.25V to 5.0V.ShutdownPull SHDN low to enter shutdown. During shutdown, the output is disconnected from the input and supply cur-rent drops to 0.1µA. When in shutdown, POK pulls low and OUT is high impedance. The capacitance and load at OUT determine the rate at which V OUT decays.SHDN can be pulled as high as 6V, regardless of the input and output voltage.Figure 1. Functional DiagramPOK OutputThe power OK (POK) output pulls low when OUT is less than 93% of the nominal regulation voltage. Once OUT exceeds 93% of the nominal voltage, POK goes high impedance. POK is an open-drain N-channel output. To obtain a voltage output, connect a pullup resistor from POK to OUT. A 100k Ωresistor works well for most appli-cations. POK can be used as a power-okay (POK) signal to a microcontroller (µC), or drive an external LED to indi-cate power failure. When the MAX1818 is shut down,POK is held low independent of the output voltage. If unused, leave POK grounded or unconnected.Current LimitThe MAX1818 monitors and controls the pass transis-tor’s gate voltage, limiting the output current to 0.8A (typ). This current limit doubles when the output voltage is within 4% of the nominal value to improve perfor-mance with large load transients.Thermal Overload ProtectionThermal overload protection limits total power dissipa-tion in the MAX1818. When the junction temperature exceeds T J = +170°C, a thermal sensor turns off the pass transistor, allowing the IC to cool. The thermal sensor turns the pass transistor on again after the junc-tion temperature cools by 20°C, resulting in a pulsed output during continuous thermal overload conditions.Thermal overload protection protects the MAX1818 in the event of fault conditions. For continuous operation,do not exceed the absolute maximum junction-temper-ature rating of T J = +150°C.Operating Region and Power DissipationThe MAX1818’s maximum power dissipation depends on the thermal resistance of the IC package and circuit board, the temperature difference between the die junction and ambient air, and the rate of air flow. The power dissipated in the device is P = I OUT ×(V IN -V OUT ). The maximum allowed power dissipation is 800mW at T A = +70°C or:P MAX = (T J(MAX)- T A ) / ( θJC + θCA )where T J - T A is the temperature difference between the MAX1818 die junction and the surrounding air, θJC is the thermal resistance of the junction to the case,and θCA is the thermal resistance from the case through the PC board, copper traces, and other materi-als to the surrounding air. For best heatsinking, the copper area should be equally shared between the IN,OUT, and GND pins.The MAX1818 delivers up to 0.5A RMS and operates with input voltages up to +5.5V, but not simultaneously.High output currents can only be sustained when input-output differential voltages are low, as shown in Figure 3.MAX1818500mA Low-DropoutLinear Regulator in SOT23_______________________________________________________________________________________7Figure 2. Adjustable Output Using External Feedback ResistorsApplications InformationCapacitor Selection andRegulator StabilityCapacitors are required at the MAX1818’s input and output for stable operation over the full temperature range and with load currents up to 500mA. Connect a 1µF capacitor between IN and ground and a 3.3µF low-E SR capacitor between OUT and ground. For output voltages less than 2V, use a 4.7µF low-E SR output capacitor. The input capacitor (C IN ) lowers the source impedance of the input supply. Reduce noise and improve load-transient response, stability, and power-supply rejection by using larger output capacitors, such as 10µF.The output capacitor’s (C OUT ) equivalent series resis-tance (ESR) affects stability and output noise. Use out-put capacitors with an E SR of 0.1Ωor less to ensure stability and optimum transient response. Surface-mount ceramic capacitors have very low E SR and are commonly available in values up to 10µF. Connect C IN and C OUT as close to the MAX1818 as possible to mini-mize the impact of PC board trace inductance.Noise, PSRR, and Transient ResponseThe MAX1818 is designed to operate with low dropout voltages and low quiescent currents in battery-powered systems while still maintaining good noise, transient response, and AC rejection. See the T ypical Operating Characteristics for a plot of power-supply rejection ratio (PSRR) versus frequency. When operating from noisy sources, improved supply-noise rejection and transient response can be achieved by increasing the values of the input and output bypass capacitors and through passive filtering techniques.The MAX1818 load-transient response (see T ypical Operating Characteristics ) shows two components of the output response: a DC shift from the output imped-ance due to the load current change, and the transient response. A typical transient response for a step change in the load current from 100mA to 500mA is 8mV. Increasing the output capacitor’s value and decreasing the ESR attenuates the overshoot.Input-Output (Dropout) VoltageA regulator’s minimum input-to-output voltage differen-tial (dropout voltage) determines the lowest usable sup-ply voltage. In battery-powered systems, this determines the useful end-of-life battery voltage.Because the MAX1818 uses a P-channel MOSFET pass transistor, its dropout voltage is a function of drain-to-source on-resistance (R DS(ON)) multiplied by the load current (see Typical Operating Characteristics ).V DROPOUT = V IN - V OUT = R DS(ON)× I OUTThe MAX1818 ground current remains below 150µA in dropout.M A X 18188_______________________________________________________________________________________500mA Low-DropoutLinear Regulator in SOT23Selector GuideChip InformationTRANSISTOR COUNT: 845Package InformationFor the latest package outline information and land patterns, go to /packages .MAX1818500mA Low-DropoutLinear Regulator in SOT23Maxim cannot assume responsibility for use of any circuitry other than circuitry entirely embodied in a Maxim product. No circuit patent licenses are implied. Maxim reserves the right to change the circuitry and specifications without notice at any time.Maxim Integrated Products, 120 San Gabriel Drive, Sunnyvale, CA 94086 408-737-7600 _____________________9©2008 Maxim Integrated Productsis a registered trademark of Maxim Integrated Products, Inc.。