轿车保险杠大型注射模设计及CAE
汽车保险杠模具毕业设计说明书

汽车保险杠注射模具设计摘要:随着汽车工业的发展,汽车保险杆作为一种重要的安全装置走向了革新的道路,保险杆除了有保护功能外,还要追求与车体造型的和谐与统一,追求本身的轻量化和表亮化。
本文叙述了其注塑模具设计的一般流程,包括塑胶件的工艺分析;模具具体结构的设计;及模具各种2D、3D工程图的绘制;热流道技术;注塑成型设备的选择;相关参数的计算与说明等等。
相比其他注塑模设计,本文采用目前模具设计中先进的热流道技术,包括喷嘴的设计、流道板的具体参数的选择与设计等等。
本塑件是一个宽度 1.6米左右,高0.3米左右,厚度2.5~4厘米之间的汽车后保险杠。
塑件整体尺寸较大,无螺纹,所以不需要涉及螺纹设计。
这次设计的模具的顶出方式采用简单脱模机构中的顶杆脱模机构。
顶杆脱模机构是最典型的简单脱模机构,它结构简单,制造容易且维修方便。
在整个设计工作中,本文主要运用3D软件Pro/E以及CAD软件来完成产品的造型。
此外还利用CAD绘制了模具装配图以及各种成型零件图。
这是第一次利用绘图软件对整套模具进行设计,对所学知识进行了全面巩固,意义重大!关键词:热流道;注塑模设计;Pro/E; CADBumper Mould DesignAbstract:The birth of mobile phones has changed many people's living habits, and the cell phone charge at GM because of its exceptional circumstances (price, convenience, etc.) get more people liked it, so in our lives was widely used. Block, which is connected rechargeable cell phone battery charging devices and the key positions. This paper describes the design of its injection mold of the general processes, including plastic pieces of technology analysis; specific structure of the mold and die various 2 D, 3D rendering of the plan; hot runner technology; injection molding equipment choice of the relevant parameters Calculation and description, and so on. The plastic parts are a width of 1.6 meters, 0.3 meters high, the thickness of 2.5 to 4 cm between the car rear bumper. Overall size larger plastic parts, non-threaded, so do not involve thread design. The design of the mold ejection ejection mechanism with a simple way of mandrel pulling mechanism. Mandrel ejection mechanism is the most typical simple stripping mechanism, its simple structure, easy to manufacture and easy pared to other injection mold design, mold design currently used in this paper in the hot runner advanced technologies, including the nozzle design, flow-specific parameters of choice and design, and so on. Throughout the design work in this paper use 3 D software Pro / E to complete the modeling products. In addition, also has drawn up the mold assembly drawing as well as each kind of Molding Parts drawing using CAD . This is that the first time makes use of the software drawing to carry out design on package mould , have carried out all-round consolidation on what be learned knowledge,The significance is significant!Keywords:Hot Runner;Injection Mould Design;Pro/E; CAD目录1前言 (1)2塑件结构与成型工艺分析 (4)2.1汽车保险杠模具的设计 (4)2.1.1汽车保险杠的立体示意图 (4)2.1.2汽车保险杠的二维视图 (4)2.1.3汽车保险杠的结构尺寸特征分析 (4)2.1.4塑件工艺性分析 (5)2.2塑料弯管原材料的选择分析 (5)2.2.1塑料的原材料的选择 (5)2.2超高冲击强度PP性能指标 (5)3成型工艺方案的确定 (7)3.1尺寸精度分析 (7)3.2塑件的体积和质量 (7)3.3选择注射机 (7)3.4型腔数量以及注射机有关工艺参数的校核 (8)3.4.1型腔数量 (8)3.4.2最大注射量校核 (8)3.4.3锁模力的校核 (9)3.4.4注射压力校核 (9)3.4.5开模行程校核 (9)3.5分型面的选择 (9)4浇注系统设计 (11)4.1浇注系统设计原则 (11)4.2热流道注塑模具技术 (13)4.3主流道设计 (14)4.2加热管功率的计算 (15)4.3喷嘴 (16)4.4流道板 (18)4.5气动系统 (19)4.6注塑模的热流道系统的装配 (21)5成型零件结构设计 (24)5.1型芯与型腔的结构设计 (24)5.2整体式矩形型腔侧壁厚度计算。
汽车保险杠浇注系统的CAE
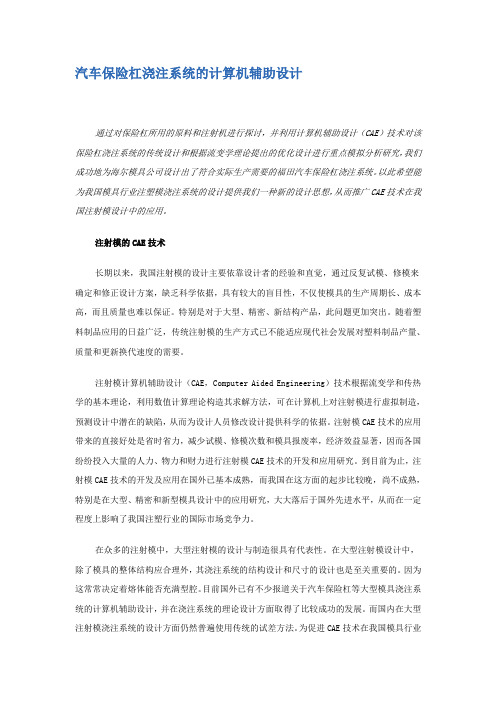
汽车保险杠浇注系统的计算机辅助设计通过对保险杠所用的原料和注射机进行探讨,并利用计算机辅助设计(CAE)技术对该保险杠浇注系统的传统设计和根据流变学理论提出的优化设计进行重点模拟分析研究,我们成功地为海尔模具公司设计出了符合实际生产需要的福田汽车保险杠浇注系统。
以此希望能为我国模具行业注塑模浇注系统的设计提供我们一种新的设计思想,从而推广CAE技术在我国注射模设计中的应用。
注射模的CAE技术长期以来,我国注射模的设计主要依靠设计者的经验和直觉,通过反复试模、修模来确定和修正设计方案,缺乏科学依据,具有较大的盲目性,不仅使模具的生产周期长、成本高,而且质量也难以保证。
特别是对于大型、精密、新结构产品,此问题更加突出。
随着塑料制品应用的日益广泛,传统注射模的生产方式已不能适应现代社会发展对塑料制品产量、质量和更新换代速度的需要。
注射模计算机辅助设计(CAE,Computer Aided Engineering)技术根据流变学和传热学的基本理论,利用数值计算理论构造其求解方法,可在计算机上对注射模进行虚拟制造,预测设计中潜在的缺陷,从而为设计人员修改设计提供科学的依据。
注射模CAE技术的应用带来的直接好处是省时省力,减少试模、修模次数和模具报废率,经济效益显著,因而各国纷纷投入大量的人力、物力和财力进行注射模CAE技术的开发和应用研究。
到目前为止,注射模CAE技术的开发及应用在国外已基本成熟,而我国在这方面的起步比较晚,尚不成熟,特别是在大型、精密和新型模具设计中的应用研究,大大落后于国外先进水平,从而在一定程度上影响了我国注塑行业的国际市场竞争力。
在众多的注射模中,大型注射模的设计与制造很具有代表性。
在大型注射模设计中,除了模具的整体结构应合理外,其浇注系统的结构设计和尺寸的设计也是至关重要的。
因为这常常决定着熔体能否充满型腔。
目前国外已有不少报道关于汽车保险杠等大型模具浇注系统的计算机辅助设计,并在浇注系统的理论设计方面取得了比较成功的发展。
汽车前保险杠注塑模浇注系统优化设计
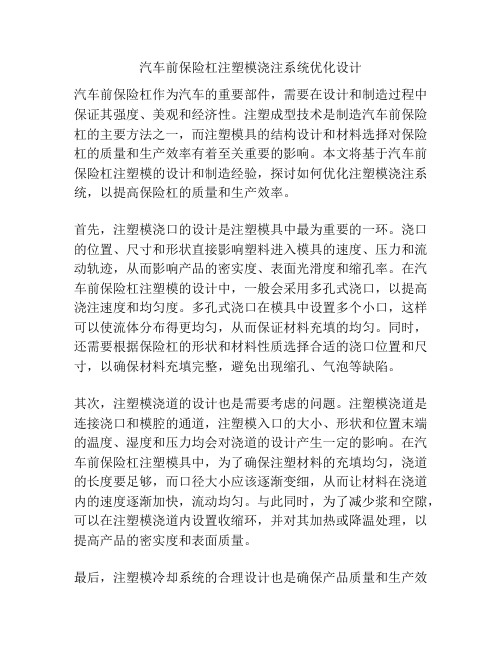
汽车前保险杠注塑模浇注系统优化设计汽车前保险杠作为汽车的重要部件,需要在设计和制造过程中保证其强度、美观和经济性。
注塑成型技术是制造汽车前保险杠的主要方法之一,而注塑模具的结构设计和材料选择对保险杠的质量和生产效率有着至关重要的影响。
本文将基于汽车前保险杠注塑模的设计和制造经验,探讨如何优化注塑模浇注系统,以提高保险杠的质量和生产效率。
首先,注塑模浇口的设计是注塑模具中最为重要的一环。
浇口的位置、尺寸和形状直接影响塑料进入模具的速度、压力和流动轨迹,从而影响产品的密实度、表面光滑度和缩孔率。
在汽车前保险杠注塑模的设计中,一般会采用多孔式浇口,以提高浇注速度和均匀度。
多孔式浇口在模具中设置多个小口,这样可以使流体分布得更均匀,从而保证材料充填的均匀。
同时,还需要根据保险杠的形状和材料性质选择合适的浇口位置和尺寸,以确保材料充填完整,避免出现缩孔、气泡等缺陷。
其次,注塑模浇道的设计也是需要考虑的问题。
注塑模浇道是连接浇口和模腔的通道,注塑模入口的大小、形状和位置末端的温度、湿度和压力均会对浇道的设计产生一定的影响。
在汽车前保险杠注塑模具中,为了确保注塑材料的充填均匀,浇道的长度要足够,而口径大小应该逐渐变细,从而让材料在浇道内的速度逐渐加快,流动均匀。
与此同时,为了减少浆和空隙,可以在注塑模浇道内设置收缩环,并对其加热或降温处理,以提高产品的密实度和表面质量。
最后,注塑模冷却系统的合理设计也是确保产品质量和生产效率的关键。
注塑模具中的冷却系统负责将注塑材料加热后从模具中出来后,通过模腔的冷却水散发热量,达到更好的成型效果。
在汽车前保险杠注塑模具中,为了控制材料的温度和液化度,尤其是在浇口、浇道和模腔处,需要采用特殊的冷却系统设计。
可以通过加入导热油,增加冷却效果,以及采用内外循环冷却的设计,提高冷却效率,从而在确保产品质量的同时提高生产效率。
综上所述,注塑模浇注系统的优化设计对于汽车前保险杠制造的生产效率和产品质量具有重要意义。
基于CAE技术的汽车前保险杠成型工艺优化研究
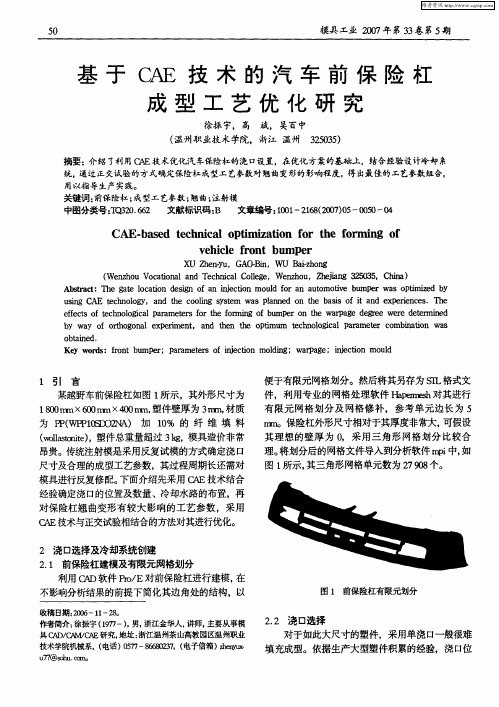
efc ftc n l函clp mme f t o e h oo a a es  ̄m o e fr n fb mp ro e wap g e re woe d tr n d frt omig o u e n t ra ed ge r eemi h h e
b y o r o o a e p r n , a d t e h p i m e h oo i a p r mee o iain Wa y wa f o t g n l x e i h me t n n t e o t h mu tc n lgc l a a tr c mb t S n o
尺寸及合理的成型工艺参数,其过程周期长还需对 模具进行反复修配。 下面介绍先采用 C E技术结合 A 经验确定浇口的位置及数量 、冷却水路的布置,再 对保 险杠翘 曲变形有较大影响的工艺参数 ,采用 C E技术与正交试验相结合的方法对其进行优化。 A 2 浇口选择及冷却系统创建 21 前保险杠建模及有限元网格划分 . 利用 C D软件 P / A 幻 E对前保险杠进行建模, 在 不影响分析结果的前提下简化其边 角处的结构,以
一
,
22 浇 口选择 . 厶 z 况 u 佯 对于如此大尺寸的塑件,采用单浇口一般很难 填充成型。依据生产大型塑件积累的经验,浇 口位
u 7  ̄ . n 7@ o 。
维普资讯
模具工业 20 年第 3 卷第 5 07 3 期 置可 在A B CD E FG H I 共 9 设臣 如图2 、、 , 、 、,、 、处( 处) 所
某越野车前保险杠如图 1 所示,其外形尺寸为 1 0 r 60r 40r 塑件壁厚为 3 80r mx 0 r mx 0 r m。 m 材质 为 P ( P l ̄ ) A 加 1% 的 纤 维 填 料 PW P O 2 2 ) N 0
CAD-CAE-CAM技术在汽车注塑模设计中的应用
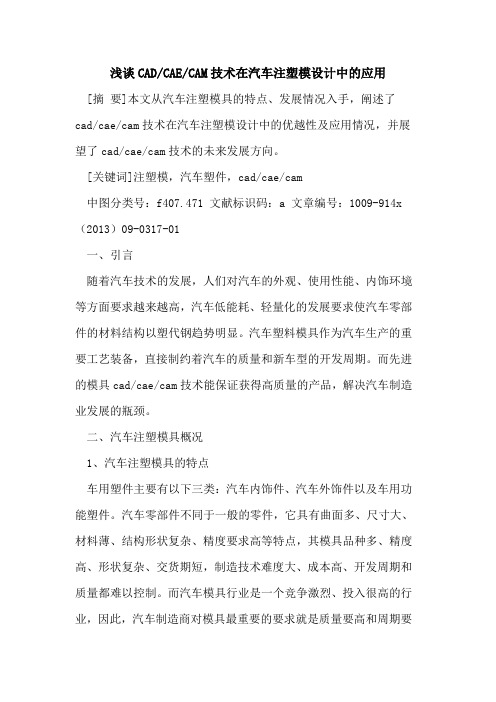
浅谈CAD/CAE/CAM技术在汽车注塑模设计中的应用[摘要]本文从汽车注塑模具的特点、发展情况入手,阐述了cad/cae/cam技术在汽车注塑模设计中的优越性及应用情况,并展望了cad/cae/cam技术的未来发展方向。
[关键词]注塑模,汽车塑件,cad/cae/cam中图分类号:f407.471 文献标识码:a 文章编号:1009-914x (2013)09-0317-01一、引言随着汽车技术的发展,人们对汽车的外观、使用性能、内饰环境等方面要求越来越高,汽车低能耗、轻量化的发展要求使汽车零部件的材料结构以塑代钢趋势明显。
汽车塑料模具作为汽车生产的重要工艺装备,直接制约着汽车的质量和新车型的开发周期。
而先进的模具cad/cae/cam技术能保证获得高质量的产品,解决汽车制造业发展的瓶颈。
二、汽车注塑模具概况1、汽车注塑模具的特点车用塑件主要有以下三类:汽车内饰件、汽车外饰件以及车用功能塑件。
汽车零部件不同于一般的零件,它具有曲面多、尺寸大、材料薄、结构形状复杂、精度要求高等特点,其模具品种多、精度高、形状复杂、交货期短,制造技术难度大、成本高、开发周期和质量都难以控制。
而汽车模具行业是一个竞争激烈、投入很高的行业,因此,汽车制造商对模具最重要的要求就是质量要高和周期要短。
因此,汽车注塑模具制造技术发展的重点就是利用高科技手段生产模具。
2、国内外汽车注塑模具的发展随着汽车制造业的高速发展,国内汽车模具设计制造业已有很大发展,模具水平也有较大幅度提高,车用塑料的使用量、种类也在逐步增多。
但和国外相比仍有较大差距,主要体现在:(1)产需矛盾。
汽车模具无论是数量还是质量都无法满足国内市场的需要;(2)模具自产自配比例较高,模具的商品化程度低;(3)模具材料及装备水平落后,带来钳工比例过高等问题;(4)模具开发能力差、产品水平低、经济效益欠佳。
3、发展趋势从国外的发展经验看,要提高汽车大型精密复杂塑料模具的制造水平,需要在以下方面有所突破:(1)解决加工设备的升级换代,提高加工能力、加工精度及加工自动化,确保模具加工的精度与速度;(2)采用先进的数字信息化现代管理模式,对模具的设计、制造、检测等方面采用全方位监控来全面提升产品质量;(3)加大在人才方面的投入力度;(4)cad/cam/cae技术的全面应用及有所创新。
汽车保险杠结构参数化模型的建立与机械参数优化设计
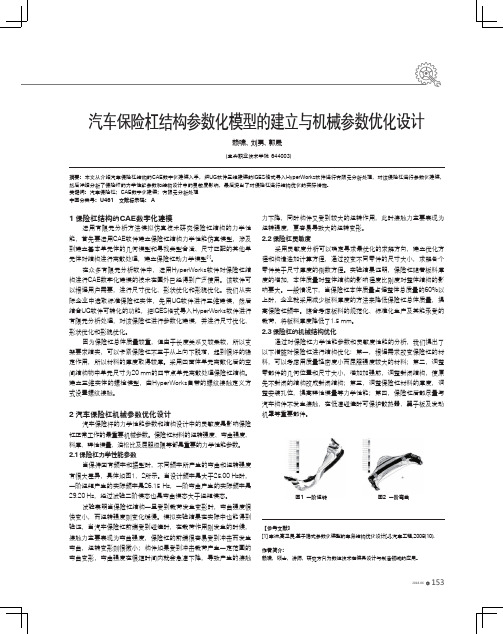
汽车保险杠结构参数化模型的建立与机械参数优化设计
赖啸、刘勇、郭晟
(宜宾的CAE数字化建模入手,把UG软件三维建模的IGES格式导入HyperWorks软件进行有限元分析处理,对该保险杠进行参数化建模, 然后详细分析了保险杆的力学性能参数和结构设计中的灵敏度影响,最后提出了对保险杠进行结构优化的实际措施。 关键词:汽车保险杠;CAE数字化建模;有限元分析处理 中图分类号:U461 文献标示码: A
1 保险杠结构的CAE数字化建模
运用有限元分析方法模拟仿真技术研究保险杠结构的力学性 能,首先要运用CAE软件建立保险杠结构力学性能仿真模型,涉及 到建立基本单元体的几何模型和寻找类型合适、尺寸匹配的其他单 元体对结构进行离散处理,建立保险杠动力学模型[1]。
在众多有限元分析软件中,运用HyperWorks软件对保险杠结 构进行CAE数字化建模的技术在国外已经得到广泛使用。该软件可 以根据用户需要,进行尺寸优化、形状优化和形貌优化。我们从实 际企业中选取标准保险杠实体,先用UG软件进行三维建模,然后 结合UG软件可转化的功能,把IGES格式导入HyperWorks软件进行 有限元分析处理,对该保险杠进行参数化建模,并进行尺寸优化、 形状优化和形貌优化。
力下降,同时构件又受到较大的扭转作用,此时接触力主要表现为 扭转强度,更容易导致大的扭转变形。 2.2 保险杠灵敏度
基于CAE的轿车零件注射模具优化设计

第39卷第1期2011年1月塑料工业C H I NA PLA ST ICS I NDU STRY作者简介:钱应平,男,工学博士,副教授,湖北工业大学机械学院,专长:模具CAD /C A E /CAM,快速制造。
q i anyp98@163 co m 。
基于CAE 的轿车零件注射模具优化设计钱应平1,黄菊华2,周细枝1,者凌秋1(1.湖北工业大学机械工程学院,湖北武汉430068;2.湖北工业大学土木与建筑工程学院,湖北武汉430068) 摘要:以汽车零件为研究对象,利用CAE 技术及注塑模具CAD 技术,借助M o l d flo w 和PRO /E 软件,建立了产品的三维实体模型,在产品的结构工艺性和成型性分析的基础上,进行了产品成型过程的模拟分析,获得了优化的成型方案和参数,并利用PROE /E 模块E MX 进行了模具结构的三维优化设计。
关键词:计算机辅助工程;注塑模具;优化设计中图分类号:TQ 320 66+2 文献标识码:B 文章编号:1005-5770(2011)01-0065-04Opti m ization Design of InjectionM ould of Car P arts Based on CAEQ I A N Y i n g pi n g 1,HUANG Ju hua 2,Z H OU X i zh i 1,Z HE L i n g q i u1(1.School o fM echan ica l Eng i neer i ng,H ube iU niversity of T echnology ,W uhan 430068,China ;2.Schoo l o f C iv il and A rchitec t ura l Eng i neering ,H ube iU n i versity o f T echno l ogy ,W uhan 430068,Ch i na)Abst ract :In t h is paper ,the car partw as used as study objec,t the C AE and injecti o n m o l d CAD tec h nology w ere used ,and the three d i m ensi o n m odel of pr oduct w as established by t h e M oldflo w and PRO /E .The opti m ized m o l d i n g m et h ods and para m eters were obtained based on the ana l y sis of str ucture process andm o l d i n g character i s tics and the three d i m ension opti m izi n g desi g n o fm ou l d struct u re w as fi n ished by using the E MX m odu le in PRO /E .K eyw ords :CAE ;Injecti o n M o l d ;Opti m izati o n Design1 塑料件的结构及工艺分析1 1 塑件结构分析轿车零件的示意图如图1。
轿车前保险杠注塑过程模拟分析
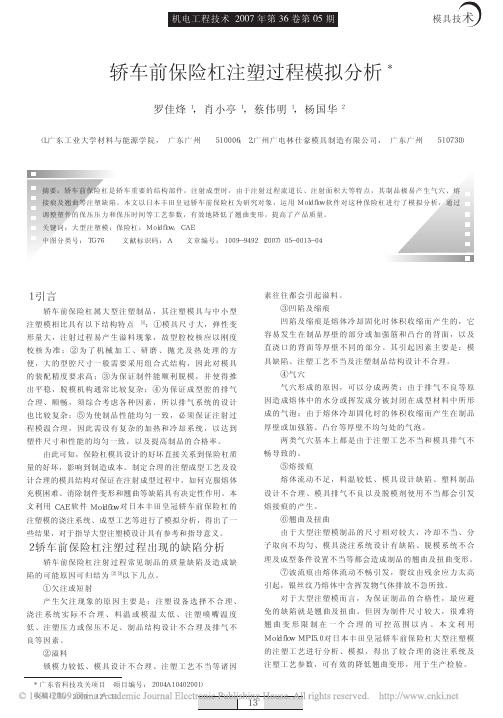
接痕及翘曲等注塑缺陷。本文以日本丰田皇冠轿车前保险杠为研究对象, 运用 Moldflow 软件对这种保险杠进行了模拟分析, 通过
调整塑件的保压压力和保压时间等工艺参数, 有效地降低了翘曲变形, 提高了产品质量。
关键词: 大型注塑模; 保险杠; Moldflow; CAE
中图分类号: TG76
文献标识码: A 文章编号: 1009- 9492 (2007) 05- 0013- 04
图 1 零件模型
将此模型导入到 Moldflow MPI5.0, 对其划分网格并进 行最佳浇口位置分析, 分析结果如图 2 所示。
图 3 六点进浇
图 2 最佳浇口分析
考虑到零件的形状、注塑生产的效率以及对成型设备 的要求, 我们初步选用并比较了两种浇注方式, 即: 三点 进 浇 和 六 点 进 浇 , 如 图 3、4 所 示 。 利 用 Moldflow 对 两 种 浇 注 系 统 进 行 填 充 ( Fill) 分 析 , 并 对 两 种 方 案 填 充 时 间 ( Fill Time) 、 型 腔 压 力 分 布 结 果 、 注 塑 口 压 力 曲 线 以 及 气 穴和熔接痕的分布等进行分析比较, 可以得出三点进浇方 式所引起的产品质量缺陷较少, 填充过程更为合理, 是比 较合适的浇注方案。
在确定好浇注系统后可对其进行成型工艺窗口 (Molding Window) 分析。成型工艺窗口 ( Molding Window) 定义了能够生产合格产品的成型工艺范围。如果成型工艺 条件位于这个范围之内, 那么就可以生产出好质量的制 件。有了成型工艺窗口之后, 必要时调剂师就可以在这个 范围内对成型条件做出适当的修改以期获得最好的制件质 量 。 经 成 型 工 艺 窗 口 分 析 , 在 分 析 结 果 中 , Moldflow 会 向
CAE技术在保险杠总成设计制造中的应用
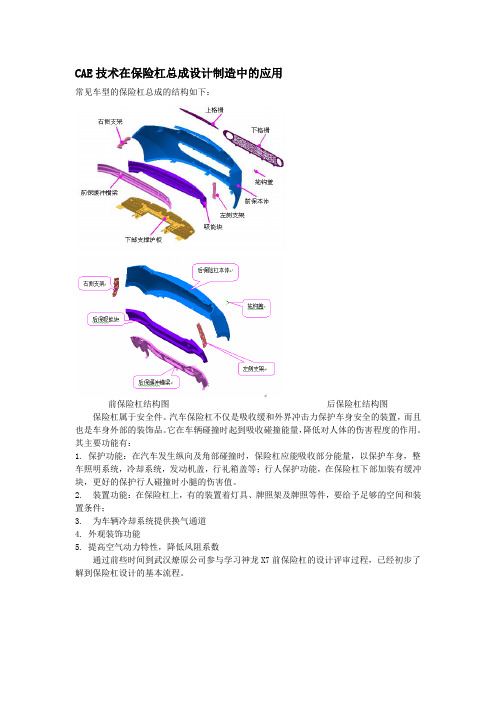
CAE技术在保险杠总成设计制造中的应用常见车型的保险杠总成的结构如下:前保险杠结构图后保险杠结构图保险杠属于安全件。
汽车保险杠不仅是吸收缓和外界冲击力保护车身安全的装置,而且也是车身外部的装饰品。
它在车辆碰撞时起到吸收碰撞能量,降低对人体的伤害程度的作用。
其主要功能有:1. 保护功能:在汽车发生纵向及角部碰撞时,保险杠应能吸收部分能量,以保护车身,整车照明系统,冷却系统,发动机盖,行礼箱盖等;行人保护功能,在保险杠下部加装有缓冲块,更好的保护行人碰撞时小腿的伤害值。
2. 装置功能:在保险杠上,有的装置着灯具、牌照架及牌照等件,要给予足够的空间和装置条件;3. 为车辆冷却系统提供换气通道4. 外观装饰功能5. 提高空气动力特性,降低风阻系数通过前些时间到武汉燎原公司参与学习神龙X7前保险杠的设计评审过程,已经初步了解到保险杠设计的基本流程。
保险杠的设计要满足以下要求:1.法规要求:碰撞性能要求:2.5MPH BUMPER(ECE R42);行人保护性能要求:EEC70/156;外部突出物要求:ECE R26.01,EEC 79/488;2.满足冷却系统的有效进风面积,通常要求散热器进气口面积应大于冷凝器面积的1/3。
3.符合造型要求,整体外观的流畅、协调性4.成本低,自重轻, 材料可回收利用。
关键在于保险杠材料和壁厚的确定。
5.工艺可行,拆装方便。
关键在于保险杠的安装方式的设计。
保险杠设计需要进行CAE分析的内容如下:1.横梁强度.保险杠横梁强度,是保险杠设计中需要关注的焦点。
设计规范的保险杠总成,是由较高强度的主横梁和左右两个吸能元件组成。
主横梁的作用是将任何形式的偏置碰撞产生的能量,尽可能均匀地分布到两个吸能元件上,使能量最大限度均匀地被吸能元件吸收,并将碰撞力均匀传递到两个纵梁。
显而易见,高强度的横梁更有利于碰撞能量的均匀分布。
但在设计中,不可能通过无限制增加钢材厚度达到增加强度的目的。
出于节油考虑,目前各个汽车生产厂商对整车重量控制越来越严格。
汽车模具—前保险杠大型薄壁注塑模设计

汽车模具—前保险杠大型薄壁注塑模设计汽车前保险杠是汽车最重要的外观件之一,不但要具有足够的强度和刚性,汽车发生碰撞事故时能起到缓冲作用,保护车体,还要追求和车体造型和谐与统一,并实现本身的轻量化。
为了达到这种目的,目前轿车的前保险杠主体都采用了塑料,俗称塑料保险杠由注塑模具注射成型。
一、塑件结构分析汽车前保险杠形状类似于马鞍形,具体结构见图1。
材料为PP+EPDM-T20,收缩率取0.95%。
其中的PP中文名聚丙烯,是保险杠的主要材料,EPDM中文名三元乙丙橡胶,它能够提高保险杠外罩的弹性,而T20是指材料中加上20%的滑石粉,它可以提高保险杠外罩的刚度性。
塑件的特点是:(1)形状复杂,尺寸大,壁厚相对较小,属于大型薄壁塑件。
(2)塑件碰穿、插穿孔多,加强筋多,注射成型熔体流动阻力大。
(3)塑件内侧有三处倒扣,每一处的侧向抽芯都相当困难。
图1 汽车前保险杠结构图二、模具结构分析前保险杠主体注塑模具采用内分型面,通过热流道,并由顺序阀控制进胶。
两侧倒扣采用大斜顶套横向斜顶加直顶的结构,最大外形尺寸2500×1560×1790mm,模具结构详见图2。
图2 前保险杠注塑模具结构图1.定模固定板;2.承板;3.热流道板;4.定位圈;5.一级热射嘴;6.气阀;7.阀针;8.二级热射嘴;9.动模固定板;10.方铁;11.推杆固定板;12.推杆底板;13.支撑柱;14.动模方导柱;15.推杆;16.动模板;17.支撑脚;18.定模方导柱;19.定目板;20.斜推杆;21、29.转销;22、28.斜顶;23、34.导轨;24、27.动模镶件;25、26.直顶;30.斜推杆;31、39.护杆;32、33、40、41.导向柱;35、36、37.推杆;38.定位块;42.耐磨块;43.侧抽芯;44.弹簧;45.限位块1、成型零件设计本模具的3D图见图3,模具设计时采用了先进的内分型面技术,详见图4。
轿车保险杠顺序注射成型CAE分析

3 l
轿 车 保 险 杠 顺 序 注 射 成 型 C E分 析 水 A
章 柱 衡 肖小 亭 朱 海 燕
( 东工 业 大 学 材 料 与 能 源 学 院 , 州 广 广 50 0 ) 10 6
摘要
采 用 M lf w软 件 对轿 车后 保 险杠 三 点进 浇顺 序 注射 成 型 的 过 程 进 行 模 拟 。 为 了分 析 阀 浇 口不 同的 延 od o l
特点 为 I : 4
图 1 保 险杠 的顺序注塑系统
巍
( ) 控 制 不 同流 道 熔 体 汇 合 时 前 锋 面 的 温 1可 度 、 力等参 数 , 而避 免熔 体在 型腔 中流动 时 因前 压 从 锋面 的温度梯 度 大而易 形成熔 接痕 ;
() 2 可控 制 进 浇 点 的开 启 数 量 品带来 的降解 影 响 ;
现 在 的 大 型 汽 车 塑料 制 品普 遍 采 用 热 流 道 技 术 , 以提 高材料 的利 用率 , 可 但不 能有效 调整控 制熔
接 痕 的位 置 及 质 量 。采 用 热 流 道 针 阀式 浇 口和
时序控 制器 相结合 的顺 序 注 塑 , 过 时序 程序 控 制 通 不 同浇 口的开 闭时间来 控制熔 体在 制 品不 同位 置 的 注塑压 力 、 度 和充填 时 间 , 现注 射成 型 。 图 1 温 实
显然 , 述方 法 中 , 法① 只有 一个 浇 口工作 , 上 方 各部 分熔体 温度不 平 衡 , 体流程 长 , 熔 注塑压力 大且
粤港关键领域招标项 目( 0 8 5 ) 20 Z 1
收稿 日期 :0 0 0 -6 2 1 —72
保险杠模具设计CAE

流动场分析结果如图 2 所示,其流动是平衡的,结合后面熔结痕分析结果说明浇口开设是合理的。 温度场分结果如图 3 所示,结束时温差比较大,可能原因是此模具采用热流道技术,而 CAE 分析结果按冷流道 汁算得出。若出现注射结束时不同位置的温差太大,就很难获得均匀的冷却,不同的温度将导致聚合体的密度和 性能都发生着改变,这样会产生翘曲。同时可能会产生较大的因温差引起的残余应力。
对于此保险杠模具:
(4)动模垫板问受力变形计算,方法原理同侧壁校核,允许最大挠曲量一般取 0.05mm。 一般对大型注射模还需进行制品对型芯包紧力的计算及顶出力的校核;连接螺钉顶出杠强度校核等。可参见 注时模设计手册。
6 结束语
设计保险杠大型注射模应注意的问题: (1)应认真分析产品几何结构,选择好分型面;CAE 优化分析选择浇口形式、大小、数目及进浇位置。 (2)确定产品所用原材料常需要流动性好(即熔体流动指数大的塑料)、有利充模;好的机械力学特性,能保证 轿车在冲击下不变形、有弹性回复;耐恶劣环境气候变化而不变形(翘曲)。 (3)大型或特大型注射模设计应考虑使用热流道或冷、热流道相结合的浇注系统。 (4)加热、冷却是大型注射模设计需要解决的一对矛盾。 (5)大型注射模顶出系统一般很复杂,常需要机械液压联合顶出。
下面就热流道模具加以讨沦。热流道模贝之所以得到广泛应用,是因为它具有以下独特优点:缩短成型周期, 一般可达 30%-40%;避免回收大量回头料.从而节省原料,降低成本;由于严格控制温度,因此提高了制品 质量,保证了制品的尺寸精度和强度;热流道有利于压力传递,从而可以降低注射压力;缩短开模行程,有利于 保护模具,延长模具使用寿命;无需修剪料把,节省工时和人力;缩短制模周期,制品成本降低,在一般情况下 生产成本降低 16%。
汽车塑料保险杠注射成型模具OK

汽车塑料保险杠注射成型模具OK个⼈收集整理勿做商业⽤途学位论⽂汽车保险杠注塑成型RESEARCH ON NUMERICAL SIMULATION指导教师张洁作者姓名胥宝军申请学位级别学⼠专业名称机械制造及其⾃动化(模具)论⽂提交⽇期2014年6⽉论⽂答辩⽇期2014年6⽉学位授予单位和⽇期江苏⼤学年⽉答辩委员会主席______________评阅⼈______________2014年6⽉学位论⽂版权使⽤授权书本学位论⽂作者完全了解学校有关保留、使⽤学位论⽂地规定,同意学校保留并向国家有关部门或机构送交论⽂地复印件和电⼦版,允许论⽂被查阅和借阅.本⼈授权江苏⼤学可以将本学位论⽂地全部内容或部分内容编⼊有关数据库进⾏检索,可以采⽤影印、缩印或扫描等⼿段保存和汇编本学位论⽂.保密□,本学位论⽂属于在年解密后适⽤本授权书.不保密□.学位论⽂作者签名:指导教师签名:2011年⽉⽇2011年⽉⽇独创性声明本⼈郑重声明:所呈交地学位论⽂,是本⼈在导师地指导下,独⽴进⾏研究⼯作所取得地成果.除⽂中已注明引⽤地内容以外,本论⽂不包含任何其他个⼈或集体已经发表或撰写过地作品成果.对本⽂地研究做出重要贡献地个⼈和集体,均已在⽂中以明确⽅式标明.本⼈完全意识到本声明地法律结果由本⼈承担.学位论⽂作者签名:⽇期:2011 年⽉⽇摘要本毕业设计是⼀篇关于汽车塑料保险杠注射成型模具地结构设计,⽂中详细地介绍了模具设计过程及其相关计算,并对⼤型注塑模具成型零件地受⼒分析进⾏了初步探讨.该制品外表⾯为装饰⾯,采⽤热流道注射成型、定模顶出机构,浇⼝及推杆均设置在制品内表⾯.设计有注射机地选择、浇注系统、加热和冷却系统、开合模设计系统等组成.制品适⽤于昌河牌⼩轿车.关键词:保险杠注塑模具热流道Abstract: This granduated paper presents a design of injection mould for auto safety guard used in motorcar which is made of plastics.The process of the design and the interrelated calculation are introduced in this paper.we also study the guarantee of the forced parts of this design.The surface of the product is decorateing plane.It is made by thermo-injection road,still mold pushing system and fillinggate,and the pushing staff is fixed inside surface of product. This design include choose of injecting machines; design of filling system; design of cooling and heating system;design in closure and separation of the mould and so on.The product can be used for changhe motocar’s safty guard.keywords: safety guard; injection mould; thermo-injection road前⾔毕业设计是每个毕业⽣所必经地⼀个学习阶段.它是在⽼师地指导下由学⽣独⽴解决⼯程实际问题地过程.其基本⽬地是培养学⽣综合运⽤所学地基础理论、基础知识和基本技能,分析与解决⼯程实际问题地能⼒.这对于培养我们勇于实践、勇于探索和开拓创新地精神,提⾼我们分析、解决问题地能⼒,培养我们正确地设计思想和⼯程经济观点、理论联系实际地⼯作作风、严肃认真地科学态度都具有重要意义.随着社会地发展,越来越多地汽车进⼊到我们千家万户.保险杠系统是轿车车⾝地重要部件,20世纪以前,轿车前后保险杠是以⾦属材料为主,⽤厚度为3毫⽶以上地钢板冲压成U形槽钢,表⾯处理镀铬,与车架纵梁铆接或焊接在⼀起,与车⾝有⼀段较⼤地间隙,这样地保险杠既不美观,⽽且成型困难,增加了车体重量且容易腐蚀破坏.塑料是20世纪才发展起来地新材料.⽬前,世界上塑料地体积产量已经赶上钢铁,成为当前⼈类使⽤地⼜⼀⼤类材料.我国地塑料⼯业正在飞速发展,塑料制品地应⽤已经深⼊到国民经济地各个部门.塑料⼯程通常是指塑料制造与改性,塑料成型及制品后加⼯.塑料制品与模具设计是塑料⼯程中地重要部分,是塑料⼯业中不可少地环节.塑料材料地密度低,⽐强度⾼,⼜具有耐腐蚀性和绝缘性.在较多地品种中,有地耐磨性能良好,有地防震、抗冲性能优异,有地耐疲劳性能突出.塑料保险杠加⼯成型⽅便,⼀旦开好⼀套模具即可不停地注塑,产量⼤,并且检测⽅便.因⽽各种塑料制品在国民⽇常⽣活中得到了⼴泛地应⽤,它地⼤量使⽤还由于它地可加⼯性可以⽤注塑、挤塑、热成型和压延等⽅法⾼效地⽣产各种制品;它⼜可经纤维增强或改性,⼀定程度地改善制品所需地某些性能;另外塑料制品着⾊容易,⼜可多样修饰,使它浓妆淡抹⾛进千家万户.塑料制品被⼤量使⽤是作结构件,如各种电⼦仪表家⽤电器和通讯设备等地机壳、机架和机座、建筑上地塑料管道板条和门窗.汽车上地前后保险杠、仪表盘和内饰件.除此之外塑料件作为电绝缘零件,与⾦属导体、半导体器件相辅相成.近年来透明塑料制品,从镜⽚、光盘到照明灯具,⼜拓展了新地应⽤领域.虽然塑料保险杠地优点有这么多,汽车保险杠注塑地时候也会遇到短射、翘曲、⽓孔、熔接痕、颜⾊异常等注塑缺陷.从20世纪80年代以来,我国地模具⼯业发展迅速平均每年增长速度为13%,到2000年模具总产值为260-270亿元,塑料模具占30%.未来塑料模具在模具总产值中地⽐例还会增加.对于⼀件塑料件只有通过正确地制品设计,才能步⼊国民经济以⾄尖端技术地各个领域.因⽽在塑料制件地⽣产中我们⼯程技术⼈员必须熟悉制品设计和有关理论、⽅法,结构和造型.塑料材料地粘弹性、强度和刚度,以及它地特殊地失效形式、使⽤寿命和可靠性设计是设计中地技术难点.另外塑料材料地机加⼯,模具地冷却系统、模具精度,以及塑料件精度地取决因素和塑料件加⼯时地熔体流动或软化变形地可⾏性也是如今塑料制品设计上地技术难点.如今塑料件成型模具地⽣产效率不断提⾼,注塑成型地热流道模具已普遍采⽤,各种⾃动脱模机构已相当成熟,模具地冷却系统地冷却效率得到充分地利⽤.再者,计算机辅助设计(CAD)和计算机辅助制造(CAM)地使⽤显著提⾼了塑料模具设计和制造地效率和质量,有效地缩短了模具设计制造周期.继CAD和CAM技术成功地在模具设计和制造中应⽤后,此项技术向纵深⽅向发展.另外计算机辅助⼯程(CAE)也将成为塑料模具设计中⼀种重要地辅助软件.第⼀章塑料制品和⽅案论证第1.1节制件介绍图1.1中所⽰为汽车保险杠简图图1.1该保险杠塑料制品⽤于昌河⼩型汽车,它安装汽车车尾部分.其外形尺⼨1320×150×90,形状为⽆盖壳体,整个制品地平均厚度为5㎜.保险杠选⽤PP塑料成型,PP塑料具有质轻、原料来源丰富、性能/价格⽐优越、易于成型、易于回收等特点,因⽽⽤途⼗分⼴泛.但是均聚PP抗冲击性能、低温韧性、耐⽼化和尺⼨稳定⽐较较差,难以满⾜汽车制件强度和冲击强度均衡地要求.因此在汽车制件中普遍使⽤地是改性地PP料,其中PP/EPDM ,共混改性料就是最常⽤地⼀种.本设计选择了DSM公司地PP/EPDM,牌号为IP2401/1,其主要加⼯性能如表1所⽰.表1 PP/EPDM地主要加⼯性能第1.2节⽅案论证本设计采⽤热流道注射成型,不仅缩短了成型周期、提⾼了⽣产效率,同时也节省了原料,它是⼤型模具地发展⽅向.设计中还采⽤了推板推杆联合顶出可以解决⼤型注塑模具制品脱出困难地问题.设计中合理利⽤顶柱,从⽽解决了⼤型注塑模具尺⼨跨度⼤难以满⾜成型零件地刚度要求地⽭盾.当开模⾄⼀定距离后,动模板开始带动拉板.继续开模动作则由拉板带动推板,并通过复位杆及推杆板带动推杆与推板同时推动制品脱离定模镶件.合模时,推杆由复位杆复位.1.模具主要参数确定:收缩率:本保险杠所选⽤地塑料原材料是化⼯研究院研制地PP改性材料,其收缩率为1.2%,设计时各项收缩率定为:径向⽅向为1.18%,横向⽅向定为1.28%,竖向⽅向定为1.2%.2.模具材料地选⽤:型腔⽤Cr12,,该钢韧性差,可⽤于载荷⼤地⼤型模具,型芯采⽤40Cr,顶板、垫板选⽤45#钢,导柱、导套选⽤T8A、T10A淬⽕,顶杆⽤T8A,模脚选⽤A3,热流道主体选⽤55#碳钢调质,喷嘴采⽤60Si2Mn⾼频淬⽕.第⼆章有关注射机参数地校核第1节最⼤注射量地校核⼤型塑料制品中所⽤注射成型机都是螺杆式,其最⼤注射能⼒通常以螺杆在料筒内地最⼤推进容积表⽰.成型所需要地注射总量应⼩于所选注射机最⼤注射量地80%:即G1×80%>m总质量(2-1)式中G1——注射机地最⼤注射量m总质量——塑料件加浇注系统凝料地总质量经计算m总质量⼤约为2400cm3,所以可以选⽤公称注射容量为4000cmX S—ZY—4000型注射机.PP为⾮极性地结晶性⾼聚物,吸⽔率低,约为0.03%~0.04%,注射时⼀般不需⼲燥.PP粘度适中,流动性好,设定料温在220~260℃之间,模温在60℃左右,⽤于成型⽣产地注射机主要技术参数如表2所⽰表2第2节注射压⼒地校核在选择注射机注射压⼒时应选择⼤于制品注射成型压⼒地注射压⼒.经过查阅⽂献本设计选择地DSM公司地PP/EPDM地注射成型压⼒约为85MPa,虽然本设计地制品件为薄壁制件,但是具有106MPa注射压⼒地XS—ZY—4000型注射机是可以满⾜要求地.第3节锁模⼒地校核塑件和浇注系统在分型⾯上地投影⾯积之和乘以型腔内熔料地压⼒之积,称为锁模⼒.所选注射机地锁模⼒应⼤于模具所需地锁模⼒,否则,模具在分型⾯容易被⾼压熔融塑料所涨开.由上述得锁模⼒计算公式如下:F机>PA (2-2)式中F机——注射机地锁模⼒P——模具型腔内地熔料压⼒A——塑料件和浇注系统在分型⾯上地投影⾯积之和模具型腔内地压⼒P⼀般取20~50MPa.经计算A≈0.198m2,则模具所需地锁模⼒为3.96MN~9.9MN,所以上⾯所选地注射机符合要求.第4节开模⾏程地校核单分型⾯注射模具所需地开模⾏程S≥h1+h2+(5~10)mm (2-3)式中h1——顶出距离(或型芯⾼度)h2——塑件加料把总⾼度S——开模⾏程.本设计中地模具开模⾏程不⾜2000mm,远⼩于所选注射机地1100mm.第三章浇注系统地设计根据保险杠地结构特征与外观要求,模具地结构类型应采⽤多点浇⼝地三板式注射模或热流道模具.现采⽤热流道注射成型,定模顶出机构,浇⼝及推杆均设置在制品内表⾯.模具如图3-1所⽰图3-1⽆流道系统,这项新技术地开发乃是注射模具地⼀次重⼤改⾰.它地应⽤不仅缩短了成型周期、提⾼了⽣产效率,同时也节省了原料.在⼤型模具设计中,⽆流道系统设计应⽤愈来愈⼴,特别是热流道模具,它是⼤型模具地设计⽅向[1].具有以下独特优点:⑴缩短成型周期,⼀般可达30%~40%.⑵避免回收⼤量回头料,从⽽节省原料,降低成本.⑶由于严格控制温度,因此提⾼了制品质量,保证了制品地尺⼨精度和强度.⑷热流道有利于压⼒传递,从⽽可降低注射压⼒.⑸缩短开模⾏程,有利于保护模具,延长模具使⽤寿命.⑹⽆需修剪料把,节省⼯时和⼈⼒.⑺缩短制模周期,制品成本降低,在⼀般情况下⽣产成本降低16%下⾯就热流道浇注系统地具体设计简述如下:(1).喷嘴形式:本设计采⽤外热式延伸喷嘴.(2).浇注系统断⾯尺⼨:经计算得到保险杠地体积约为2400cm3由使⽤地注射机地公称注射了量V max=4000cm3,注射时间t=15秒,PP地体积流量q v为q v== (3-1)由《塑料成型⼯艺及模具简明⼿册》上地图3-34γ-q v-R n关系曲线查得主流道地当量半径R n=3.7㎜(取γ=5.0×105s-1时,故主流道⼤端直径D2=10㎜,⼩端直径D1=8㎜,点浇⼝直径d=2㎜.(3)型腔压⼒地估算.PP/EPDM地注射压⼒p i为110~140Mpa,取p i=125Mpa则型腔压⼒p M=kp i=0.4×125 Mpa=50 Mpa第四章加热冷却系统地设计第1节综述模具温度调节有两个⽬地:⼀是提⾼成型率,⼆是提⾼制品地质量.注射成型时,对多数塑料来说,是把200℃左右地塑料熔体注⼊模腔内,固化后当摩温降低到50~60℃时取出制品.这个温差若调节不好,不但影响熔料冲模,且易使制品翘曲变形和开裂.模具内快速冷却定型,是缩短成型周期,提⾼⽣产效率地重要措施.加热是调节模具温度地⼀个⽅⾯.为了保持⼀定地注射温度,应对模具进⾏加热.⼤型模具中,如果成型距离⽐较长,塑件壁厚,即使是低熔点塑料,为了防⽌冲模不满,在初始注射时也应对模具进⾏加热.在模具内设置冷却系统是控制模具温度地有效措施.为了缩短制品模制周期,总是希望模具温度低⼀些,但是模温太低会使塑件产⽣料流迹,熔接缝线(或熔接不牢),强度差和严重缺料等问题.模温过⾼,虽然熔料流动性好,制品表⾯粗糙度⼩,⼒学性能好,但却发⽣⼤地收缩,成型周期长并产⽣缩孔.因此,模具应保持⼀定地模温,这样就必须靠模具地加热、冷却系统来调节.第2节模具冷却分析塑料注射模具地冷却剂常⽤压缩空⽓、⽔和冷冻⽔,但其温度不宜过低导致冷却效率降低,⼀般选在10℃适宜.对于⼤型模具最好以⾃来⽔冷却,有条件时可⽤深井⽔冷却,这样较为经济.⽔在模具通道中地流速应尽可能⾼⼀些.就流动状态来说,湍流⽐层流好.在湍流条件下,热传递速率⾼于层流10~20倍.因为才层流中冷却⽔以平⾏于冷却通道壁地诸同⼼层运动,从⽽妨碍了模具向冷却⽔散热过程地进⾏.然⽽⼀旦达到湍流状态,再增加冷却⽔在管内地流速,其传热速率并⽆明显提⾼.第3节冷却系统地分析计算由产品图得知,制品厚度为5mm,查表3-79[2],得到制品在模内冷却时间t c为57.5s.由于该制品开模时⽆法⾃动坠落,须由⼿⼯取出.设开模取出制品地时间为15s,再加上注射时间15s,开模时间6.5s,闭模时间6s,故制品地成型周期T=100sPP/EPDM带⼊型腔内地总热量Q in:Q in=nGq (4-1)n=查表3-78[2]得q=586J/gG=(2400×0.904)g=2169.6g则Q in=nGq=(36×2169.6×586)J/h=46339473.6 J/h≈46339KJ/h(1)模具表⾯空⽓对流所散去地热量Q1.Q1=h1A1(T MV-T r) (4-2)式中Q1——单位时间内通过⾃然对流散发到空⽓中地模具热量,单位为KJ/h;h1——⾃然对流时地传热系数,单位为W/(㎡.K);A1——能够发⽣⾃然对流地模具表⾯积,单位为㎡;T MV——模具整体地平均温度,单位为℃;T r——室温,单位为℃.计算得:Q1=2846KJ/h(2)模具表⾯辐射到空⽓中地热量Q2Q2=20.8A MC(4-3)式中A MC——模具四周与空⽓接触地侧表⾯⾯积,单位为㎡;——辐射率.计算得:Q2=169 KJ/h(3)模具传给注射机地热量Q3.Q3=h3A2(T MV-T r) (4-4)式中Q3——单位时间内模具传给动、定模固定板地热量,单位为KJ/hA2——动模座和定模座与注射机动、定模固定板地接触⾯积,单位为㎡计算得:Q3=21KJ/h(4)冷却⽔传出地热量Q4.Q4=Q in-(Q1+Q2+Q3) (4-5)计算得:Q4=43303KJ/h这些热量应由凹模和型芯冷却系统带⾛.考虑到型芯储存地热量多,且散热条件差,故须强化冷却,采⽤式(3-67)[2]地分配⽅案,则凹模冷却系统应带⾛地热量Q4凹模为Q4凹模=0.4Q4=17321.2KJ/h型芯冷却系统应带⾛地热量Q4凸为Q4凸=25981.8KJ/h(5)凹模冷却系统计算.设型腔最⾼温度为60℃,最低温度55℃,则型腔平均温度为57.5℃.①凹模所需冷却⽔流量q v凹.设冷却⽔进⼝温度为20℃,出⼝温度为25℃,由凹模冷却⽔管带⾛地热量Q4凹将使⽔温上升.由式q v凹= (4-6)计算得q v凹==m3/min=0.0138 m3/min②凹模冷却⽔管直径d凹及流速v凹.由q v凹查表得d凹=25mm,最低速度v凹==③冷却管道孔壁与冷却介质之间地传热系数α.冷却⽔平均温度为22.5℃,查表得,取f=6.47,再由下式kJ/(㎡.h.℃)=7765 kJ/(㎡.h.℃)④冷却管道总传热⾯积A凹.A凹=㎡=0.063㎡该模具设计中,凹模冷却⽔总传热⾯积远⼤于0.063㎡,满⾜要求.可以考虑间歇式供⽔.⑤所需凹模⽔道长度L凹===0.81m⑥流动状态校核.(4-7)式中Re——雷诺数;——运动粘度.故Re==11725﹥10000紊流,冷却回路具有良好地冷却效果.(6)型芯冷却系统计算①型芯所需冷却⽔流量q v凸、管径d凸及流速v凸.考虑到型芯成型⾯应具有型腔相同地平均温度,仍取为57.5℃,冷却⽔进⼝温度仍为20℃,出⼝温度取为27℃,则冷却⽔平均温度仍为23.5℃.欲从型芯中带⾛25981.8KJ/h地热量,所需冷却⽔地体积流量为=0.015查表得⽔管直径为20mm最低流速=0.796m/s②冷却⽔管⾯积③所需脱模⽔道长度实际设计3m,完全满⾜要求.第4节冷却系统地设计冷却系统地设计好坏直接关系到产品地质量.冷却不均匀,会使制件翘曲变形,产⽣内应⼒、开裂等.同时也影响塑件地成型周期,因⽽设计冷却系统在整个塑料模具设计中占有较为重要地作⽤.在设计冷却系统时应遵循以下原则:(1)冷却⽔孔数量多、尺⼨⼤、间距⼩,冷却效果好.(2)⽔孔排列尽可能按型腔形状排列,离型腔地距离视制件地壁厚情况⽽定.(3)热量聚集地地⽅加强冷却(塑件壁厚处和热浇⼝处).(4)降低⼊⼝和出⼝地⽔温差,这样就要求流程尽可能短⽽不要太长.(5)在产⽣熔接痕处避免冷却过度,以免影响熔接牢度.(6)⼀般情况下,⽔孔地直径不得过⼩,在8~12㎜之间选取较好.本设计采⽤如图4-1所⽰地贯通式⽔道,同时进⾏型腔和型芯地冷却,⽔孔地布置按制件形状⽽排列,这种冷却在⼤型模具中较为合适.图4-1第5节加热系统地设计本设计地加热系统分为两部分:⼀是过长喷嘴部分⽤电热线圈加热;⼆是成型零件部分开机前地预热——⽤热⽔和过热⽔加热.电热线圈加热系统结构简单,使⽤⽅便,清洁卫⽣,传热好,为要求模温较⾼地⼤型塑料注射模所采⽤.但有局部过热地缺点.本设计中地冷却⽔孔同时可作为开机前地预热⽔道.第五章成型零件地设计第1节成型零件⼯作尺⼨地计算⼤型塑料注射模具零件⼯作尺⼨地确定,不能采⽤中⼩型模具零件地计算⽅法,因为模具制造公差对中⼩型塑件尺⼨精度影响很⼤,⽽塑料收缩率波动值却对⼤塑件(即⼤型模具)尺⼨精度影响很⼤.在计算时应根据原四机部制订地塑件尺⼨公差表和精度选⽤表为依据,同时考虑模具模具材料地热膨胀率和塑件地综合收缩率综合收缩率S Q=S-Q其中S是塑料地收缩率Q是模具成型零件材料地热膨胀率Q=α(T-T1)×100% (5-1)式中α——⾦属材料膨胀系数(℃-1)T——模具成型零件地加⼯温度(℃)T——模具常温(℃)查表得PP/EPDM地收缩率为S=1.0~2.5% =1.75%Q=α(T-T1)×100%=12.8×10-6×(240-60)×100%=0.2304% S Q=S-Q=1.75%-0.2304%=1.5196%模具使⽤到额定寿命⼀半时地平均尺⼨L MCP=L SCP+L SCP S Q5.1.1对型腔内径来说L MCP=L M+(5-2)即:L M= L MCP-()(5-3)减去修模余量,再标上制造公差,得:L M= (5-4)令,于是上式变为:(5-5)其中L M为模具地单向公差名义尺⼨——模具成型零件地总磨损值——模具成型零件地制造公差——塑件制造总公差对于⼤型制件,如果维持制造公差=,则加⼯精度低,⽽且随着制件尺⼨变⼤加⼯精度愈来愈低,因此⼤型制件地模具应取<.所以型腔地长度⽅向可以取=,查表得=4.5mm =0.45 mmL MCP=L SCP+L SCP S Q=1320+1320×1.5196%=1340.06==1339.61+0.45型腔地宽度⽅向,查表得=1.02mm==0.20mmL MCP=L SCP+L SCP S Q=150+150×1.5196%=152.28 mm==152.08+0.205.1.2 对型芯外径尺⼨来说即:L M= L MCP+ (5-6)考虑上修模余量,再标上制造公差令,于是上式变为:L M=所以型芯地长度⽅向可以取=,查表得=4.5mm=0.45 mmL MCP=L SCP+L SCP S Q=1310+1310×1.5196%=1329.91L M===1330.36-0.45型芯地宽度⽅向,查表得=1.02mm==0.20mmL MCP=L SCP+L SCP S Q=140+140×1.5196%=142.13 mmL M==(142.13+0.20)-0.20=142.33-0.205.1.3型腔深度地计算H MCP=H SCP+H SCP S Q=90+90×1.5196%=91.37mm查表得:=0.64取==0.128mmH M==(91.37-0.064)+0.128=91.30+0.1285.1.4型芯⾼度地计算h MCP=h SCP+h SCP S Q=85+85×1.5196%=86.29mm查表得=0.64 取==0.128mmh M=(h MCP+)=(86.29+0.064)-0.128=86.35-0.128第2节型腔壁厚和垫板厚度地计算5.2.1凹模型腔侧壁厚地计算本模具采⽤整体式矩形凹模型腔,其长边侧壁厚度依据下公式计算t c= (5-7)其中——模腔压⼒,单位为MPa E——材料地弹性模量,单位为MPa。
汽车保险杠注射工艺分析及注射模设计

汽车保险杠注射工艺分析及注射模设计摘要:随着经济的快速发展,人们生活水平得到提高,物质生活越来越好,汽车几乎成为了人们出行必备的交通工具。
汽车后保险杠是汽车最重要的外观件之一,早期的汽车后保险杠采用金属制造,但现代的汽车后保险杠都采用塑料,由模具注射成型。
塑料保险杠不但成本大大降低,缓冲性能好,比金属更具有弹性,更能吸收撞击力,而且可以自动回弹和自动修复。
后保险杠外形尺寸大,结构复杂,外观要求很高,所以模具设计难度也非常高。
关键词:汽车保险杠;注射工艺;注射模设计汽车保险杠的质量是汽车安全问题中重要的一环。
汽车在发生轻微碰撞后,保险杠可以吸收碰撞能量,即使汽车发生严重碰撞,冲击力也会通过保险杠系统合理地分配给整个车身,避免造成过大的局部变形,从而保护乘客的安全,因此,汽车保险杠对于材料的要求十分严格。
1汽车保险杆的发展情况1896年卡尔本茨发明了第一辆汽车(三轮汽车),当时的汽车没有保险杠,只有一个安装喇叭和车灯用的金属横梁,后来为了达到美观的效果,增加了装饰用的前盖板,这就是最初的保险杆原型。
随着交通事故的频繁发生,人们逐渐意识到保险杠对车辆及行人的保护作用,有人考虑在前盖板上增加保护功能,具体采用与前横梁留有一定间隙的保险杠盖板,后来进一步发展成在保险杠盖板与横梁之间增加能吸能缓冲的橡胶构件,这样做能够很大程度降低汽车对行人的冲击,这种结构最终演变成后来的金属保险杠总成。
随后汽车保险杠又出现了由外板、缓冲材料和横梁三部分组成的保险杠结构。
近些年随着各行各业技术的大力发展,新型的保险杠结构也不断涌现,如液压吸能式、带气腔式等。
另外,出于保护行人的要求,现在国外也在研究安全气囊式保险杠。
2成型保险杠模具结构介绍以普通整车车身作为参考,保险杠长1.5~2.5m,宽0.5~1m,纵深深度0.5~1m。
假设某一保险杠外形尺寸为1720mm×940mm×540mm,按此塑件外形尺寸设计的注射模尺寸大概在2500mm×1200mm×2000mm。
基于CAE的汽车保险杠研究与改进

DOI:10.16660/ki.1674-098X.2009-5640-8184基于CAE的汽车保险杠研究与改进①丁天旭 张扬* 黄鹏 石兵红 安璞凯 谢祥(甘肃农业大学 甘肃兰州 730070)摘 要:相比于传统吸能盒而言,由于其由单一属性的材料构成,所以其吸收能量的范围较小,存在两个极端,即溃缩,或者不溃缩。
当汽车在中低速行驶发生碰撞时,由于碰撞的应力小于材料的屈服极限,所以此时碰撞的属性为刚性碰撞,以至于不能有效保护驾乘人员的安全。
本文基于材料力学及有限元思想,借助计算机进行CAE分析,成功设计出一款符合材料力学的两个叠加且吸能效果较好、碰撞应力范围广的吸能盒。
通过对不同材料性能的研究,数据结果表明一个铝合金材料和一个普通碳素钢Q235材料的四方形吸能盒通过激光搭接焊[1]的方式叠加的吸能效果最好,并保证汽车在中低速碰撞时,吸能盒能够有效地发生溃缩以最大程度保护驾乘人员安全。
关键词:吸能盒 低速碰撞 CAE 结构性能优化中图分类号:TG659;TP391 文献标识码:A 文章编号:1674-098X(2020)12(b)-0095-05Research and Improvement of Automobile BumperBased on CAEDING Tianxu ZHANG Yang * HUANG Peng SHI Binghong AN Pukai XIE Xiang(Gansu Agricultural University, Lanzhou, Gansu Province, 730070 China)Abstract: Compared with the traditional energy absorption box, because it is only composed of a single property of materials, its energy absorption range is small, there are two extremes, namely collapse or non-collapse.When a car crashes at medium and low speed, the impact stress is less than the yield limit of the material, so the attribute of the collision is rigid collision, which cannot protect the safety of drivers and passengers to the maximum extent.In this paper, based on the ideas of material mechanics and finite element, CAE analysis was carried out by computer, and an energy absorption box with two superposition in accordance with material mechanics and good energy absorption effect with wide range of collision stress was successfully designed.By studying the properties of different materials, The data results show that the superposition of an aluminum alloy and a square energy absorption box of ordinary carbon steel Q235 by laser lap welding [1] has the best energy absorption effect. And to ensure that the car in the low and medium speed collision, the energy absorption box can effectively collapse to the maximum extent to protect the safety of drivers and passengers.Key Words: Energy absorption box; Low speed collision; CAE; Structural performance optimization①基金项目:甘肃农业大学省级大学生创新创业训练计划项目(项目编号:S202010733057:202006012)。
基于气辅成型及CAE模拟分析技术的大型精密汽车保险杠注塑模具设计

基于气辅成型及CAE模拟分析技术的大型精密汽车保险杠注塑模具设计摘要:本课题通过气辅注塑CAE模拟分析技术,完成了大型精密汽车保险杠注塑模具的三维数字化设计。
并通过计算机完成汽车保险杠模具气辅注塑的仿真过程,模拟熔体及气体在型腔内的流动及穿透情况,定量地给出成型过程中的状态参数(如压力、温度、速度等),根据分析结果,改进气道的布局、尺寸,优化成型工艺参数和模具设计,从而改变了过去那种单靠人为经验来设计模具浇口位置及尺寸,需要多次试模,反复修改,才能最后设计定型和制造模具的落后方法。
关键词:注塑成型;翘曲变形;CAE;工艺参数0 前言在汽车行业,用塑料代替金属来制造汽车保险杠已成为一个重要发展趋势,塑料保险杠制作可通过注塑模具批量完成,因汽车保险杠结构复杂,尺寸大,所以其相应注塑模具结构也比较复杂,且模具外形尺寸大、体积重,注射时还常常会遇到成型困难和工艺范围狭窄等问题,为解决类似问题,传统的大型汽车保险杠在模具设计时,其浇注系统常采用热流道,同时增加浇口数目,其结果浇注过程中产生模具型腔充填很难均衡现象,且产品熔接痕数目增多,严重影响制品的外观、质量、力学性能等一系列问题。
气辅注射成型技术作为一种创新的注射成型工艺,突破了传统注射成型的局限性,它可以在注塑件内部注入高压气体代替熔体进行注射保压,从而降低了注射压力和锁模力,用小型注射机成型较大塑件,降低能耗,有效消除塑件表面缩痕,减小制品翘曲变形、提高表面质量、缩短生产周期等等,且其材料适用性好,产品轻量化、质量高。
再加上运用先进的注塑CAE模拟分析技术,可将热流道的数量和进浇口的位置等通过分析进行合理优化,确定合理的热流道点数,有效控制和减少产品表面熔接痕位置和数量,实现产品重要外观不出现熔接线,满足塑件产品外观质量要求,提高产品合格率。
本课题是校企合作研发的HWQ-B50大型精密汽车保险杠模具设计课题,研发中创新运用气辅注塑及CAE模拟分析技术,并结合CAD/ CAM/ CAE 等模具数字化设计与制造新技术,实现了大型精密汽车保险杠模具数字化设计、制造的研发,并实现了其产业化,为企业获得了很大的经济效益。
奥拓轿车前保险杠注塑模浇系统的CAE分析

奥拓轿车前保险杠注塑模浇系统的CAE分析
董祥忠;李年伟
【期刊名称】《工程塑料应用》
【年(卷),期】1999(27)12
【摘要】针对奥拓轿车前保险杠大型注塑模具,采用CAE分析软件进行了优化设计。
重点对注塑原料、设备和工艺进行了选择,并建立了制品的三维几何模型(包括浇口、气道的开设以及网格的划分等),成功地完成了熔体动态充模CAE模拟分析。
分析结果表明,热流道四点进浇、四根气道及四个气体入口的对称布置方案是最理想的设计方案,热流道物气体辅助成型技术在大型注塑模上具有极大的应用前景。
【总页数】4页(P28-31)
【作者】董祥忠;李年伟
【作者单位】四川大学高分子材料科学与工程系;四川大学高分子材料科学与工程系
【正文语种】中文
【中图分类】U463.326.
【相关文献】
1.轿车前保险杠注塑模浇注系统优化设计 [J], 路春玲;朱灯林
2.轿车保险杠顺序注射成型CAE分析 [J], 章柱衡;肖小亭;朱海燕
3.大型汽车保险杠注塑模具设计及浇注系统优化分析 [J], 曾珠;叶家飞
4.基于气辅成型及CAE模拟分析技术的大型精密汽车保险杠注塑模具设计 [J], 王兰萍
5.机顶盒倒灌进浇同模异腔的注塑模具设计及CAE优化分析 [J], 陈显冰;陈一飞;施渊吉
因版权原因,仅展示原文概要,查看原文内容请购买。
- 1、下载文档前请自行甄别文档内容的完整性,平台不提供额外的编辑、内容补充、找答案等附加服务。
- 2、"仅部分预览"的文档,不可在线预览部分如存在完整性等问题,可反馈申请退款(可完整预览的文档不适用该条件!)。
- 3、如文档侵犯您的权益,请联系客服反馈,我们会尽快为您处理(人工客服工作时间:9:00-18:30)。
轿车保险杠大型注射模设计及CAE
作者:刘洁史玉升何贵董祥忠来源:CAD世界网发表时间:2006-06-03 浏览次数:124 字号:大中小
[摘要]塑料保险杠取代金属保险扛是汽车行业的发展趋势,但是塑料保险杠的设计目前仍采用传统的模具设计方法。
因此本文针对轿车前保险杠的制品结构,采用华塑CAE(HSCAE)软件对轿车保险杠注射模的型腔压力、熔体温度及流动前沿进了优化分析及模拟,同时对保险杠注射模的主要参数进行了校核。
研究结果表明本文采用的设计方法可以极大提高保险杠注射模设计开发的效率。
[关键词] 保险杠注射模热流道CAE
1 前言
随着汽车上业的发展,全金属保险杠越来越不适应现代汽车在轻量化、高机能化以及与车体造型一体化等方面的要求,尤其在轿车、轻型车上,有用塑料保险杠取代全金属保险杠的趋势。
作为钢铁件的替代产品,汽车塑料保险杠以其造型美观,重量轻,易于成型,耐腐蚀,成本低,综合机械性能良好,且容易实现规模化生产等优点在汽车行业占据了一席之地。
目前,我国轿车。
微型车、轻型车等生产厂家正在逐步实现该产品的更新
换代。
2 轿车前保险杠几何结构分析
图1所示零件为马自达轿车前保险杠,零件壁厚3.5mm,通常要求制件表面光滑无缺陷,对其外形精度没有过高要求。
如图1所示,保险杠形状为马鞍形,长1925mm,宽715mm,高538mm,平均壁厚为3.5mm。
椭圆形灯孔左右各一,中间为通风栅格,内侧加强筋若干。
尾部
有内侧卷曲,因此,需要采用内侧抽芯。
保险杠材料要求在较宽的温度范围内刚性好,耐冲击性能好,尺寸稳定性好,耐溶剂性好,涂装性能好。
丙烯综合什能较好,故在此选用聚丙
烯(改性)作为保险杠材料。
所设计保险杠模具特点为:模具外形尺寸大(2400mm×700mm×11OOmm)、体积重(25~40t),结构复杂,类似为一个中等程度的工作母机;模具浇注系统为热流道,需要电加热;型腔、型芯冷却系统复杂,型腔与浇注系统的热流道相互矛盾;制品顶出系统复杂,常用液压、机械联合顶出,并采用机械手自动取出制品;制品尺寸大,浇注系统常为冷,热流道相结合。
3 CAE优化分析
在对轿车前保险杠注射模的总体结构、使用功能控制及模具结构的具体设计(包括浇注系统成型零件和导向装置、测向分型抽芯机构、模温控制装置等的设计)进行全面设定的基础上,采用华中科技大学国家模具重点实验室开发的HSCAE(华塑CAE)软件进行优化及动态模拟分析,从而改变了过去那种单靠人为经验来设计模具浇口位置及尺寸,需要多次试模.反复修改,才能最后设计定型和制造模具的落后方法。
该课题的开展,将会极大地减少设计人员反复估算饶口尺寸的繁杂劳动,加速我国对大型轿车注射模设计、制造及产品牛产系列化的进程。
塑料注射成型时,塑料在型腔中的流动和成型,与材料的性能、塑件的形状尺寸、成型温度、成型速度.成型压力、成型时间、模腔表面情况和模具设计等一系列因素有关。
CAE优化分析就是利用计算机高速运算功能,综合考虑各种因数,得出流动场、温度场、压力场、剪切应力场等模拟结果,从而评定所用方案的优劣。
这里使用华中科技大学模具国家重点实验室开发的HSCAE5.0软件进行优化分析。
流动场分析结果如图2所示,其流动是平衡的,结合后面熔结痕分析结果说明浇口开设是合理的。
温度场分结果如图3所示,结束时温差比较大,可能原因是此模具采用热流道技术,而CAE分析结果按冷流道汁算得出。
若出现注射结束时不同位置的温差太大,就很难获得均匀的冷却,不同的温度将导致聚合体的密度和性能都发生着改变,这样会产生翘曲。
同时可能会产生较大的因温差
引起的残余应力。
压力场结果如图4所示,因为热流道原因,出现轻度压力不是现象。
若出现压力不足现象应考虑以下因素:①材判流动性不够;②制品过大而
零件壁厚很薄;③流道长度过长;④需要分级注射。
剪切应力场结果如图画所示,应力场均匀,不会产生喷现象。
CAE优化分析时必须考虑到分析时所用STL,文件没有坐标,不能精确定位,会人为引入流动不平衡因数。
大型注射模常用热流道或冷、热流道结合技术与CAE分析假定的冷流道有很大区别,这也给分析带来很大误差。
4 保险杠大型注射模热流道设计
在设计大型塑件模具浇注系统时,既要保证型腔充满,又要减少因系统设计不当给制品带来的缺陷。
特大型塑件常采用多级分流道。
多点同时浇注方案。
复杂的浇注系统在提高塑件质量的同时也使设计的难度增加。
因此,浇注系统的设计是设计大型注射横的关键之一。
本次没计采用热流道技术,这项新技术的开发乃是注射模的一次重大改革。
它的应用不仅缩短了成型周期、提高了生产效率,同时也节省了原料。
在大型模具设计中,热流道系统设计应用愈来愈广,特别是热流道模具,它是大型模具的发展方向。
下面就热流道模具加以讨沦。
热流道模贝之所以得到广泛应用,是因为它具有以下独特优点:缩短成型周期,一般可达30%-40%;避免回收大量回头料.从而节省原料,降低成本;由于严格控制温度,因此提高了制品质量,保证了制品的尺寸精度和强度;热流道有利于压力传递,从而可以降低注射压力;缩短开模行程,有利于保护模具,延长模具使用寿命;无需修剪料把,节省工时和人力;缩短制模周期,制品成本降低,在一
般情况下生产成本降低16%。
根据CAE分析结果,采用AutoCAD软件进行二维模具设计,本模具设计为单型腔,热流道、9点进浇、内侧抽芯等技术。
合模过程由两矩形导滑块导向,最后由锥面定位锁紧。
模具总长2000mm,宽1200mm,高1440mm,模具结构总图如图6所示。
二维模具设计的基本步骤如下:
(1)绘制制品二维结构图,确定好分型面,浇口的位置及尺寸大小。
(2)采用金属零件包围制品内外表面。
(3)设置浇注系统、合模导向机构、顶出系统、加热冷却系统。
(4)按动、定模分型面绘制左右动定模的方位图。
(5)在动、定模视图中分别表示出相关零件的装配坐标位置。
(6)采用另一个视图表达未完整主视图的相关内容。
(7)在主视图下方绘出制品图,并标注产品的尺寸。
(8)标注零件序号,并列出零件明细表中的材料、件数、热处理等技术要求。