驾驶室悬置机构总成设计规范
悬置系统设计及悬置部件专业资料
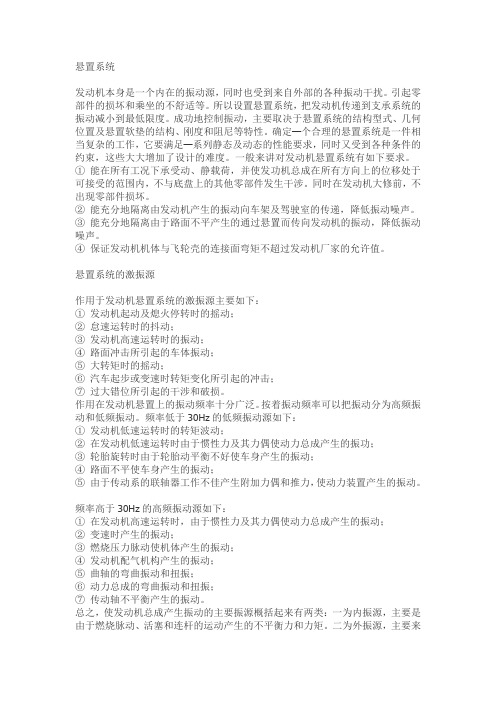
悬置系统发动机本身是一个内在的振动源,同时也受到来自外部的各种振动干扰。
引起零部件的损坏和乘坐的不舒适等。
所以设置悬置系统,把发动机传递到支承系统的振动减小到最低限度。
成功地控制振动,主要取决于悬置系统的结构型式、几何位置及悬置软垫的结构、刚度和阻尼等特性。
确定—个合理的悬置系统是一件相当复杂的工作,它要满足—系列静态及动态的性能要求,同时又受到各种条件的约束,这些大大增加了设计的难度。
一般来讲对发动机悬置系统有如下要求。
①能在所有工况下承受动、静载荷,并使发功机总成在所有方向上的位移处于可接受的范围内,不与底盘上的其他零部件发生干涉。
同时在发动机大修前,不出现零部件损坏。
②能充分地隔离由发动机产生的振动向车架及驾驶室的传递,降低振动噪声。
③能充分地隔离由于路面不平产生的通过悬置而传向发动机的振动,降低振动噪声。
④保证发动机机体与飞轮壳的连接面弯矩不超过发动机厂家的允许值。
悬置系统的激振源作用于发动机悬置系统的激振源主要如下:①发动机起动及熄火停转时的摇动;②怠速运转时的抖动;③发动机高速运转时的振动;④路面冲击所引起的车体振动;⑤大转矩时的摇动;⑥汽车起步或变速时转矩变化所引起的冲击;⑦过大错位所引起的干涉和破损。
作用在发动机悬置上的振动频率十分广泛。
按着振动频率可以把振动分为高频振动和低频振动。
频率低于30Hz的低频振动源如下:①发动机低速运转时的转矩波动;②在发动机低速运转时由于惯性力及其力偶使动力总成产生的振功;③轮胎旋转时由于轮胎动平衡不好使车身产生的振动;④路面不平使车身产生的振动;⑤由于传动系的联轴器工作不佳产生附加力偶和推力,使动力装置产生的振动。
频率高于30Hz的高频振动源如下:①在发动机高速运转时,由于惯性力及其力偶使动力总成产生的振动;②变速时产生的振动;③燃烧压力脉动使机体产生的振动;④发动机配气机构产生的振动;⑤曲轴的弯曲振动和扭振;⑥动力总成的弯曲振动和扭振;⑦传动轴不平衡产生的振动。
《驾驶室悬置》课件

轻量化
为了提高车辆燃油经济性和环保 性能,未来驾驶室悬置将更加注
重轻量化设计。
集成化
未来驾驶室悬置将更加集成化, 与车辆其他系统实现更好的协同 工作,提高整体性能和稳定性。
感谢您的观看
THANKS
动。
减震器通常安装在橡胶衬套上 ,用于吸收和缓冲来自车架的
振动和冲击。
支撑杆则起到支撑驾驶室的作 用,确保驾驶室的稳定性和刚
性。
悬置系统的重要性
良好的驾驶室悬置系统能够提高驾驶员的舒适性和车辆的平稳性,从而提高驾驶安 全性。
驾驶室悬置系统能够有效地隔离和吸收来自路面的振动和噪音,减少驾驶员的疲劳 感。
整减振效果。
优点
减振性能优异,能够根据不同路况 和驾驶需求进行实时调节。
缺点
结构复杂,成本高,需要高性能的 控制系统和传感器。
各种悬置的特点比较
比较结果
被动悬置成本低,可靠性高,但减振性能有限;半主动悬置减振性能较好,可 调节,但结构复杂、成本较高;主动悬置减振性能优异,可实时调节,但结构 复杂、成本高。
试验设备
振动台、噪声测试仪、数据采集 与分析系统等。
试验条件
温度、湿度、路面状况、车辆载 荷等。
试验方法与步骤
准备阶段
搭建试验台架,安装驾 驶室悬置和相关测试设
备。
测试阶段
按照预设条件进行振动 和噪声测试,记录相关
数据。
分析阶段
对采集的数据进行分析 ,评估驾驶室悬置的性
能。
优化阶段
根据测试和分析结果, 对驾驶室悬置的设计参
合理的驾驶室悬置设计能够确保驾驶室的稳定性和刚性,提高车辆的整体性能和耐 久性。
02
驾驶室悬置的类型与特点
基于ADAMS的驾驶室悬置优化设计

基于ADAMS的驾驶室悬置优化设计【摘要】本文针对驾驶室悬置优化设计问题展开了研究。
在介绍ADAMS 软件的基础上,分析了驾驶室悬置存在的问题,并提出了优化设计方法。
通过ADAMS软件进行仿真分析,深入探讨了驾驶室悬置优化的设计方案。
结合实际案例进行了详细分析和讨论,得出了相应的研究成果与结论。
总结了研究成果的重要性和可行性,并展望了未来的研究方向。
本研究对于提高驾驶室悬置性能,改善驾驶体验具有一定的理论和实践意义。
【关键词】ADAMS软件、驾驶室悬置、优化设计、案例分析、结果讨论、研究成果、未来展望、驾驶舱、振动、悬架系统、动力学模拟、载荷分析、优化算法、车辆工程、工程设计、模拟仿真。
1. 引言1.1 研究背景研究背景:随着汽车工业的快速发展,驾驶室的设计也变得越来越重要。
驾驶室的悬置设计不仅会影响驾驶员的舒适性和安全性,还会直接影响整车的性能和稳定性。
当前,很多汽车制造商在设计驾驶室悬置时主要依靠经验和试错方法,这种传统的设计方式存在着效率低、成本高、设计周期长等问题。
基于此,通过借助ADAMS软件这一强大的仿真工具,可以更加准确地评估驾驶室悬置设计的效果,实现设计过程的数字化、智能化。
ADAMS软件可以模拟不同路况下车辆的运动状态,有效分析驾驶室悬置系统的工作原理和性能表现,为驾驶室悬置优化设计提供科学依据。
针对驾驶室悬置设计存在的问题,开展基于ADAMS的驾驶室悬置优化设计研究具有重要的理论和实践意义。
通过该研究,可以提高驾驶室的舒适性和安全性,减少汽车制造过程中的资源浪费,推动汽车制造业的技术创新和发展。
1.2 研究目的本研究的目的是通过基于ADAMS的驾驶室悬置优化设计来提高车辆的舒适性和安全性,降低驾驶员的疲劳感和驾驶风险。
当前车辆驾驶室悬置结构存在一些问题,如在不同路况下产生的振动和冲击会影响驾驶员的驾驶体验和安全性。
通过优化设计驾驶室悬置结构,可以有效改善车辆的悬架性能,减少驾驶员的舒适性和安全性隐患。
悬置系统设计基本要素
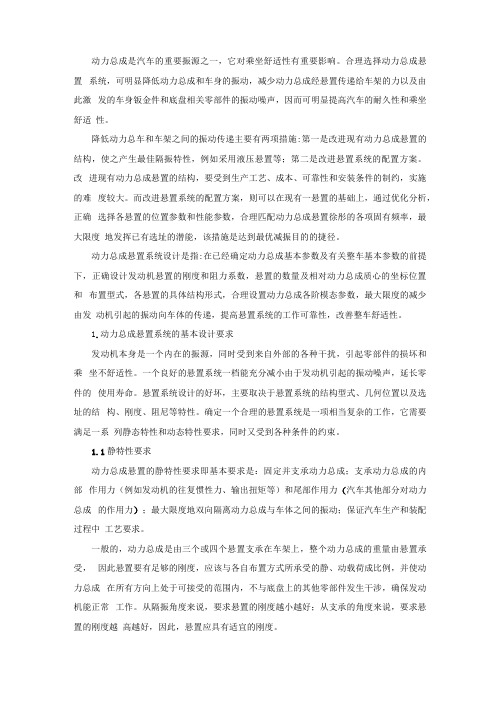
动力总成是汽车的重要振源之一,它对乘坐舒适性有重要影响。
合理选择动力总成悬置系统,可明显降低动力总成和车身的振动,减少动力总成经悬置传递给车架的力以及由此激发的车身钣金件和底盘相关零部件的振动噪声,因而可明显提高汽车的耐久性和乘坐舒适性。
降低动力总车和车架之间的振动传递主要有两项措施:第一是改进现有动力总成悬置的结构,使之产生最佳隔振特性,例如采用液压悬置等;第二是改进悬置系统的配置方案。
改进现有动力总成悬置的结构,要受到生产工艺、成本、可靠性和安装条件的制约,实施的难度较大。
而改进悬置系统的配置方案,则可以在现有一悬置的基础上,通过优化分析,正确选择各悬置的位置参数和性能参数,合理匹配动力总成悬置徐彤的各项固有频率,最大限度地发挥已有选址的潜能,该措施是达到最优减振目的的捷径。
动力总成悬置系统设计是指:在已经确定动力总成基本参数及有关整车基本参数的前提下,正确设计发动机悬置的刚度和阻力系数,悬置的数量及相对动力总成质心的坐标位置和布置型式,各悬置的具体结构形式,合理设置动力总成各阶模态参数,最大限度的减少由发动机引起的振动向车体的传递,提高悬置系统的工作可靠性,改善整车舒适性。
1.动力总成悬置系统的基本设计要求发动机本身是一个内在的振源,同时受到来自外部的各种干扰,引起零部件的损坏和乘坐不舒适性。
一个良好的悬置系统一档能充分减小由于发动机引起的振动噪声,延长零件的使用寿命。
悬置系统设计的好坏,主要取决于悬置系统的结构型式、几何位置以及选址的结构、刚度、阻尼等特性。
确定一个合理的悬置系统是一项相当复杂的工作,它需要满足一系列静态特性和动态特性要求,同时又受到各种条件的约束。
1.1静特性要求动力总成悬置的静特性要求即基本要求是:固定并支承动力总成;支承动力总成的内部作用力(例如发动机的往复惯性力、输出扭矩等)和尾部作用力(汽车其他部分对动力总成的作用力);最大限度地双向隔离动力总成与车体之间的振动;保证汽车生产和装配过程中工艺要求。
商用车驾驶室悬置隔振系统设计
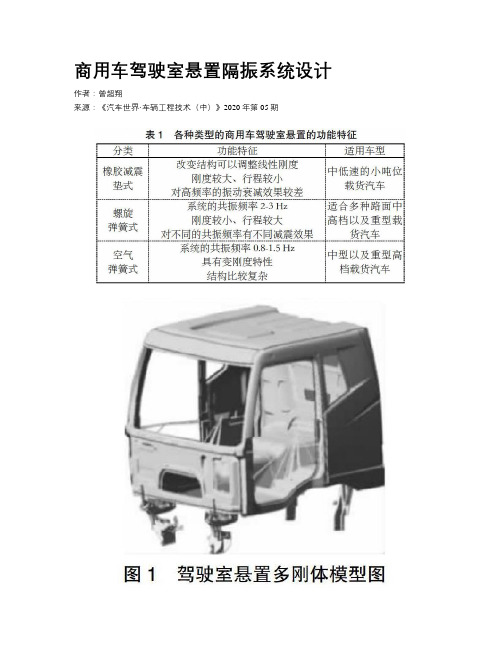
商用车驾驶室悬置隔振系统设计作者:曾超翔来源:《汽车世界·车辆工程技术(中)》2020年第05期摘要:随着社会的进步和发展,商用车在人们的生活中发挥着重要的作用,便利了人们的出行,而商用车的舒适度也成为人民关注的重点。
商用车驾驶室悬置装置将驾驶室与商用车的车架固定在一起,对驾驶室起到了支撑性的作用,商用车驾驶室悬置隔振系统的主要起到了保护驾驶室的平稳运行与衰减震动的功能,商用车驾驶室悬置隔振系统还可以改善驾驶室乘坐的舒适性,延长了驾驶室主体结构的使用寿命,也保障了商用车在驾驶时驾驶室中乘客的安全性。
因此,对商用车驾驶室悬置隔振系统设计进行研究具有深远的意义。
关键词:商用车;驾驶室悬置隔振系统;隔振设计时代不断进步,经济社会快速发展提升了人们的生活质量和水平,商用车的轿车化理念不断深入人心,人们对商用车舒适度的要求也更加严格,也使商用车驾驶室悬置隔振系统设计越来越复杂化。
本文从商用车驾驶室悬置隔振系统的国内外研究现状出发,对商用车驾驶室悬置隔振系统的结构进行研究,提出改善与优化商用车驾驶室悬置隔振系统检修方法的措施。
1 商用车驾驶室悬置隔振系统的国内外研究现状近年来,科技不断进步,设备与系统自动化进度不断加快,因此商用车驾驶室悬置隔振系统的精准度也在不断地提高,在外国,应用了高科技的控制方法与信息技术对商用车驾驶室悬置隔振系统进行设计,技术发展非常成熟,系统的重点在自动化、智能化的方向进行发展。
在国内,商用车驾驶室悬置隔振系统也有着不小的进步,在自动化和智能化方向仍有欠缺,但也有着不小的进步,但是在悬置系统刚度与阻尼的最佳匹配设计上还与国外有着一定的差距,为了解决商用车驾驶室悬置隔振系统现存的问题,提高了系统的可靠性、准确性,同时降低了成本,对商用车驾驶室悬置隔振系统进行更加优化的设计[1]。
2 商用车驾驶室悬置隔振系统设计2.1 系统参数分析对商用车驾驶室悬置隔振系统进行设计首先应该进行系统的参数分析,系统参数分析主要依靠各种类型的商用车驾驶室懸置的功能特征,具体特征见下表1。
汽车悬置系统设计标准有哪些

汽车悬置系统设计标准有哪些
汽车悬架系统设计标准包括以下几个方面:
1. 载重能力:设计标准要求悬架系统能够承受车辆整备质量及额定载荷,并确保悬架系统在运行过程中不会失效或损坏。
2. 舒适性:悬架系统应具备良好的减震能力,能够有效地减少车辆在行驶过程中的颠簸感,提供乘坐舒适性。
3. 稳定性:悬架系统设计要求在车辆急转弯、行驶过程中具有良好的稳定性,能够保持车辆的姿态,并避免侧倾或失控。
4. 控制性:悬架系统设计要求能够使车辆具备良好的操控性能,能够快速、准确地响应驾驶员的操作,提供良好的操控感。
5. 可靠性:悬架系统设计要求能够在各种复杂的路况下正常工作,并保持长时间的稳定性和可靠性。
6. 安全性:悬架系统设计要求能够确保车辆在紧急制动或避让情况下稳定,避免侧滑、打滑或翻车等危险情况。
7. 经济性:悬架系统设计要求要考虑成本和效益,尽可能减少材料和零部件的使用,提高整体系统的寿命,降低维护和保养成本。
8. 环保性:悬架系统设计要求考虑所使用的材料和技术对环境的影响,尽可能减少对自然资源的消耗和环境污染。
总之,汽车悬架系统设计标准旨在提高汽车悬架系统的性能、可靠性、安全性和经济性,为车辆提供良好的行驶稳定性和乘坐舒适性。
同时,还要考虑环境因素,减少对自然资源的消耗和环境的污染。
这些标准是汽车制造行业必须遵守的基本规范,确保汽车悬架系统的质量和性能达到国际标准。
发动机悬置的结构、作用、设计要求

目录发动机悬置的结构、作用、设计要求 (2)1.1 悬置的作用 (2)1.2 悬置的设计要求 (2)1.3 悬置的设计结构 (2)1.4 悬置的布置 (5)1.5 悬置系统设计程序 (9)1.1 悬置系统安装要求 (10)发动机悬置的结构、作用、设计要求1.1 悬置的作用悬置元件既是弹性元件又是减振装置,其特性直接关系到发动机振动向车体的传递,并影响整车的振动与噪声。
1.2 悬置的设计要求1.2.1 能在所有工况下承受动、静载荷,并使发功机总成在所有方向上的位移处于可接受的范围内,不与底盘上的其他零部件发生干涉。
同时在发动机大修前,不出现零部件损坏。
1.2.2 能充分地隔离由发动机产生的振动向车架及驾驶室的传递,降低振动噪声。
1.2.3 能充分地隔离由于路面不平产生的通过悬置而传向发动机的振动,降低振动噪声。
1.2.4 保证发动机机体与飞轮壳的连接面弯矩不超过发动机厂家的允许值。
1.3 悬置的设计结构1.3.1 发动机悬置软垫的设计-金属板件和橡胶组成1.3.1.1 悬置软垫的负荷通常前悬置位于发功饥机体前端或机体前部两侧,与后悬置相比、远离动力总成的质心,因此动力总成的垂直静负荷主要由后悬置承担,而前悬置主要承受扭转负荷。
对后悬置来说.距离动力总成的主惯性轴较近,承受较小的扭转负荷及振幅。
同时,由于它处于发动机动力输出端,受传动系不平衡力的严重干扰和外部轴向推力的冲击,当发动机输出最大转矩时.支承点出现的最大反作用力也应由后悬挂来承担。
所以后悬置的垂直刚度较大,也起着限制动力总成前后位移的作用。
悬置系统同样还承受了汽车行驶在平平道路上的颠簸、冲击、汽车制动及转向时所产生的动负荷。
1.3.1.2 悬置软垫的机构形式在设计发动机悬置时。
必须充分的考虑悬置的使用日的,例如支承的质量和限制的位移等,选择合理的形状。
悬置的基本形式有三中,即压缩式、剪切式和倾斜式。
给出了这二种悬置的基本特性及用途。
通常采用倾斜式的悬置结构,利用这种悬置的弹性特性,支点设定可以获得较大的自由度。
动力总成悬置系统匹配设计规范

动力总成悬置系统匹配设计规范一、悬置系统主要作用 (1)二、元件的主要种类 (1)三、悬置系统的设计指标 (2)四、悬置系统设计参数的输入 (3)1、动力总成的惯性参数 (3)2、动力总成悬置系统的位置数据 (4)3、动力总成悬置系统的刚度数据 (4)4、变速器的各挡速比和主减速比 (5)5、发动机的其他参数 (5)6、动力总成悬置系统及周边的相关数模 (5)五、总成悬置系统的解耦设计及固有频率的合理配置 (5)1、解耦设计的原因 (5)2、固有频率的合理配置 (6)3、悬置系统解耦特性和固有频率的计算方法 (6)4、解耦和固有频率的合理配置的评价方法 (9)5、悬置系统解耦计算和固有频率配置的目的 (9)六、悬置系统的工况计算 (10)七、悬置支架设计 (12)八、置系统设计时应遵循的主要规范 (12)九、结语 (16)一、悬置系统主要作用发动机悬置是指专门设计制造的可以作为一个独立系统进行装备使用的安装在发动机与汽车底盘之间,以隔离(减少)发动机振动能量向周围环境的传播和影响为目的的隔振系统。
合理设计和使用发动机悬置,可以明显降低动力总成及车体的振动水平,减少系统传递给车体的激振力,以及由此激发的车身钣合金和底盘相关零件的振动和噪声,从而明显提高车辆的耐久性和乘坐舒适性。
悬置系统的主要作用如下:1、固定并支承汽车动力总成;悬置首先是一个支撑元件、它必须能支承发动机总成的重量,使其不至于产生过大的静态位移而影响正常工作。
从支承的角度考虑,要求悬置刚度越高越好;从隔振的角度考虑,要求悬置的刚度越低越好。
因此悬置要有合适的刚度。
2、限位作用发动机在受到各种干扰力(如制动、加速或其他动载荷)作用的情况下,悬置能有效的限制其最大位移,以避免发生与相邻件的碰撞与干涉,确保发动机能正常工作。
衰减作用于动力总成上的一切动态力和对车身造成的冲击。
3、隔振降噪作用承受和衰减动力总成内部因发动机不平衡旋转和平移质量产生的往复惯性力、力矩和不平衡扭矩;隔离发动机激励而引起的车架或车身的振动。
- 1、下载文档前请自行甄别文档内容的完整性,平台不提供额外的编辑、内容补充、找答案等附加服务。
- 2、"仅部分预览"的文档,不可在线预览部分如存在完整性等问题,可反馈申请退款(可完整预览的文档不适用该条件!)。
- 3、如文档侵犯您的权益,请联系客服反馈,我们会尽快为您处理(人工客服工作时间:9:00-18:30)。
M 扭=MG α扭=αG 式中 M 扭――扭杆的扭矩 MG――驾驶室的重力距 α扭――扭杆的扭转角度 αG――驾驶室的翻转角度
(3-1) (3-2)
这时驾驶室在翻转过程中,扭杆在驾驶室上的力的作用点与驾驶室之间无 相对滑动。这也是我们在设计单扭杆方案时常常采用的中心布置方式。 2、扭杆中心位于翻转中心之前,即扭杆中心和驾驶室重心在翻转中心的两侧。 这时有: M 扭>MG α扭>αG (3-3) (3-4)
211
因此,连接地板梁与翻转轴的翻转支架必须有足够的刚度和强度。在设计中往往 采用 5~10mm 厚的钢板冲压而成,或采用铸钢件。实际在设计时由于我们生产的 驾驶室自重不是太大,而翻转支架的钢材用的较好(通常用 16MnREL 或 Q345) , 采用 4mm 的厚度即可。翻转支架与驾驶室的连接要可靠,大多数在纵梁和横梁的 交接处连接。 在某些汽车中, 也有应用一厚壁钢管焊在纵梁前部经过加强的部位, 既可做前横梁又做翻转轴。 1.2 要从运动状态和间隙方面考虑 在驾驶室翻起的全过程中,驾驶室上的任何部分都不能与固定在车架上的 任何不翻转部分产生运动干涉。由于现在的货车对外型美观要求得越来越高,不 允许外观上有较大的间隙,而在以前的翻转车身,为了保证翻转,车身和安装在 车架上得保险杠往往留有很大的间隙。但通过对前围适当的造型,合理适当的翻 转中心位置可以使驾驶室在锁止时能保证和保险杠间隙较小又能保证驾驶室翻 转时的运动间隙。 1.3 接近性要好 为保证车辆在维修时便于方便的拆装驾驶室,以及对翻转系统的维护保养, 翻转点应当易于接近。 1.4 要求翻转轻便,运动自如 翻转中心越是靠近驾驶室的重心,翻转驾驶室时所需的翻转力矩越小。但 翻转重心越靠近驾驶室,前围部分的运动范围就越大,要求的空间就越大,车身 和保险杠的间隙也同时增大。所以翻转中心的布置要综合考虑。 2、驾驶室翻转角度的确定 从翻转中心到驾驶室重心的连线与水平面之间的夹角称之为驾驶室的重心 角。驾驶室翻转到最大角度时以重心过翻转中心的垂线为好。这时扭杆与驾驶室 脱离接触,限位器受力不大,而放下时只需轻轻拉动驾驶室,不用使很大的劲。 设计时保证翻转角度与驾驶室重心角互为余角即可。对于我们现生产的车型,一 般定义的翻转角度为 40°。 三、扭杆位置的确定 扭杆中心相对于翻转中心的位置可有以下几种情况。 1、扭杆中心与翻转中心重合 为了保证驾驶室能翻起来,应满足下式:
213
2
1
O
图 3-1(O 为翻转中心) 四、扭杆的计算 在考虑到扭杆支架(又称前悬置支架)的强度及扭杆的尺寸等因素之后, 我们希望扭杆中心与翻转中心尽量靠近。 1、 翻转驾驶室所需要的扭矩 下面仅以扭杆位于驾驶室翻转中心之前为例来说明。 在驾驶室翻转前、后的情况下,驾驶室的重心、翻转中心、扭杆中心之间 的几何关系如图 3-2 所示 图中 G――驾驶室的重量,kg g――重力加速度,m/s2 a――驾驶室翻转前重心位置 a1――驾驶室翻转后重心位置 o――驾驶室翻转中心
第三节
扭杆翻转系统结构设计
一、驾驶室重量、重心位置的确定
210
驾驶室的重量和重心位置是扭杆和翻转中心设计的依据,它们准确与否将 直接关系到驾驶室翻转时的轻便性。 如果将驾驶室的重量估计的过重或重心位置 偏低、偏后,则设计处的扭杆扭矩必然过大,致使驾驶室向前翻转的速度过快, 回位困难,甚至不能回位。反之,如果将驾驶室的重量估计的过轻或重心位置偏 高,在翻转驾驶室时将会感到沉重,甚至翻不起来。因此,在设计时对驾驶室的 重量和重心位置必须认真对待。 在新车设计中,驾驶室的重量和重心位置可以采用以下方法确定。 1、根据样车的驾驶室来定 如果有参考样车,应首先把样车驾驶室的重量和重心位置测出,并估计新 设计的驾驶室与样车驾驶室的差别,定出其重量及重心的位置。样车驾驶室的重 量和重心位置的测定可参照 JZQS04-04-02《EQ1040G/T 驾驶室重量及重心测定》 中的方法。 2、估计 根据所设计的新车驾驶室外廓尺寸、结构、材料、内部设施及其布置等, 与已知重量、重心位置的一种或几种驾驶室对照比较,可以估计出新车驾驶室的 重量和重心位置。这种方法以经验为基础,不易估计得很准确。 3、计算 根据驾驶室得每块板的尺寸、形状、料厚等分别计算出它们的重量和重心 位置,同时计算出驾驶室内各种设施的重量和重心位置,然后再详细计算车总的 重量和重心位置。这种方法非常复杂,也不易计算得很准确。 利用以上各种方法得到驾驶室得大致重量和重心位置,然后计算出扭杆得 尺寸,用以布置设计,待驾驶室制造出来以后,再实测出其重量和重心位置,最 后进行精确计算,修改扭杆设计。 特别说明: 通常在设计时认为驾驶室的重心位置在左右对称的中心面内 (即 Y0 平面内) ,下文中所以关于扭杆计算的角度也是认为在 Y0 平面内。 二、翻转中心位置及驾驶室翻转角的确定 1、确定翻转中心的原则 1.1 应有足够的刚度和强度。 翻转中心也是驾驶室的悬置点。当驾驶室被翻起来时,它的整个重量全由 两个支承点来承担。 汽车运行中的各种力、 力矩和振动等也由此点传递给驾驶室。
208
在驾驶室悬置设计工作中,应注意以下事项。 1.1 应使悬置几个的垂直方向较软,以便于缓冲和减小车架变形对驾驶室的影 响;而在纵向及横向方向应较硬,以防止驾驶室传动。 1.2 当采用四点式悬置时,应注意调整各点高度,使之同时接触。若不能同时接 触时,应利用垫片调整,切不可采用加力的办法使之接触,防止驾驶室产生装配 应力, 使橡胶垫额外加重负担。 在驾驶室悬置机构中, 弹性元件的刚度可以不同, 当应使前两点的刚度相同,后两点的刚度也相同。 1.3 驾驶室悬置机构中的橡胶弹簧元件,应选择强度高、耐久性好、防振性也很 好的橡胶材料。 2、全浮式悬置 一般形式驾驶室悬置,不论是三点式还是四点式,都存在着一些难以克服 的缺点。近几年来,随着对汽车乘坐舒适性要求的提高,驾驶室的悬置也不断得 到改进和完善,出现了所谓全浮式悬置。在这种悬置结构中采用与汽车悬挂结构 相似得钢板弹簧或螺旋弹簧作为弹性元件,设计时考虑与悬挂匹配,并配置筒式 减振器。因此,它不但具有良好得缓冲性能,而且还具有良好得减振性,大大提 高了汽车得乘坐舒适性。 在全浮式悬置结构中,其弹簧得变形量要比橡胶软件大许多倍。采用这种 悬置得汽车,在车架受扭变形时,弹簧的变形可以抵消车架变形量的大部分,从 而改善驾驶室的受力状况,对驾驶室起到保护作用。然而,由于全浮式悬置比一 般悬置结构的重量重,成本高,安装空间大,因此并未得到广泛应用,尤其在中 小吨位的载货汽车上,更难以实现。
第七篇 车身系统设计规范
第一章 驾驶室悬置机构总成设计规范
第一节 不翻转驾驶室悬置
驾驶室安装在车架上,为了减少车架的振动及变形对驾驶室的影响,通常 是在驾驶室与车架之间加装弹性装置,即驾驶室的悬置系统。 一、悬置的数量 根据驾驶室悬置的数量不同,可以分为三点式和四点式悬置。 1、三点式悬置 三点式悬置机构为前面两点,后面一点。从理论上讲,三点可以决定一个 平面, 因此三点悬置式静定结构, 当车架产生扭转变形时, 对驾驶室的影响不大, 即驾驶室不会随着受扭而变形。但是,三点悬置的驾驶室,其横向稳定性较差, 随着车架的反复扭转而左右摇晃,驾驶室也因摇晃的惯性力而产生扭矩。由于驾 驶室是三点悬置, 只有前两点的支反力与左右摇晃的惯性力平衡, 因此应力较大。 2、四点式悬置 四点悬置结构为前面两点,后面两点。从理论上讲,它是超稳定问题。四 点悬置驾驶室的横向稳定性虽然较好,但当车架受扭而变形时,扭矩也传递给了 驾驶室,使之产生扭转变形,如果驾驶室的整体扭转刚度很大时,势必要在悬置 点和地板的悬置支架部分产生很大的应力。 二、悬置形式 悬置中的弹性元件起缓冲作用,根据它的不同,有一般悬置和全浮式悬置 之分。 1、一般悬置 到目前为止,大多数载货汽车的驾驶室都是采用由橡胶制成各种形式的垫 块充当弹性元件的一般悬置结构。 悬置部件要在反复变换的拉力和压力情况下工作,但橡胶最怕在这种交变 载荷工况下工作,交变载荷易使橡胶件产生破坏。因此,一般悬置中的橡胶中的 橡胶垫多数为上下两个或更多,每个垫块都只在单向压力下工作。
在驾驶室翻转过程中,扭杆臂与驾驶室支座之间有相对滑动。 3、扭杆中心位于翻转中心之后,即扭杆中心和驾驶室重心在翻转中心的同侧。 这时有: M 扭<MG α扭<αG (2-5) (2-6)
在驾驶室翻转过程中,扭杆臂与驾驶室支座之间也有相对滑动。 由上述分析可知,第一种情况时最好。但是由于驾驶室前面区域中布置了 各种机构,如各种管路、拉丝、电线束,翻转支架本身的结构尺寸,车身和车架 的间隙等诸多限制,往往布置起来较为困难。 在采用其它两种结构情况时(此时我们往往采用双扭杆结构) ,若将扭杆布 置在如图 3-1 所示的阴影区内,则扭杆臂与驾驶室支座之间的相对滑动量较小。
ad od
(3-8)
oa――翻转中心与驾驶室重心的连线,也是常量,oa=
od (3-9) cos α
MG 随翻转角度β变化如图 3-3 所示,为余弦曲线的一部分 在驾驶室翻转过程中,由于预先把扭杆 扭过一定角度, 因此在打开锁止机构后, 驾驶 室在扭杆扭矩的作用下, 可以自行翻转一定的 角度,然后处于平衡状态。锁止时,需要在驾 驶室上施加一定的拉力(选择拉力为 100~150N) ,在乘以扭杆中心到把手的距离, 即得到锁止时需要的附加力矩 M 附,则 MG+M 附=Mmax (3-10汽车中,发动机大都位于驾驶室后部的座椅之下,为改善发动机 的接近性,便于维修,往往采用可翻驾驶室。 翻转机构(含锁止机构)是翻转车型中连接车身和车架总成,是翻转车型的 悬置部件,同时也是驾驶室翻起时的运动部件。其主要功能有以下几点: 1、连接驾驶室和车架,有适当的弹性,对车架的振动变形起隔振、缓冲的 作用。 2、作为驾驶室翻起时的运动部件,由扭杆提供适当的翻转力矩。
β (β) α θ ψ
o1――扭杆中心 b――驾驶室翻转前,扭力臂 在驾驶室上的力作用点 b1――驾驶室翻转后,扭力臂 在驾驶室上的力作用点, 通常假设翻
δ
图 3-2
转后的作用点不变。 α――驾驶室重心角, (°)