浅谈机械加工工艺中危险因素的控制
机械加工工业要注意如下职业病危害(三篇)

机械加工工业要注意如下职业病危害机械制造工业范围很广,包括运输工具、机床、农业机械、纺织机械、动力机械和精密仪器等各种机械的制造,一般有铸造、锻造、热处理、机加工及装配车间,工种混杂,但职业危害因素大致相同。
(1)生产性粉尘主要粉尘作业是铸造,在型砂配制、制型、落砂、清砂等过程,都可使粉尘飞扬,特别是用喷砂工艺修整铸件时,粉尘浓度很高,所用的石英危害较大。
在机械加工过程中,对金属零件的磨光与抛光过程可产生金属和矿物性粉尘,引起磨工尘肺。
电焊时焊药、焊条芯及被焊接的材料,在高温下蒸发产生大量的电焊粉尘和有害气体,长期吸入较高浓度的电焊粉尘可引起电焊工尘肺。
(2)高温、热辐射机械制造厂的高温和热辐射主要在铸造、锻造和热处理工种。
铸造车间的熔炉、干燥炉、熔化的金属、热铸件,锻造及热处理车间的加热炉和赤热的金属部件都产生强烈的热辐射,形成高温环境.严重时发生中暑。
(3)有害气体熔炼炉和加热炉均可产生一氧化碳和二氧化碳,加料口处的浓度往往高;用酚醛树脂等作粘结剂时产生甲醛和氨;黄铜熔炼时产生氧化锌烟,引起铸造热热处理时可产生有机溶剂蒸气,如苯、甲苯、甲醇等;电镀时可产生铬酸雾、镍酸雾、硫酸雾及氰化氰;电焊时可产生一氧化碳和氮氧化物;喷漆时可产生苯、甲苯二甲苯蒸气。
(4)噪声振动和紫外线机械制造过程中,使用砂型捣固机、风动工具、各种锻锤、砂轮磨光、铆钉等,均可产生强烈的噪声;电焊、气焊、亚弧焊及等离子焊接产生的紫外线,如防护不当可引起电光性眼炎。
(5)重体力劳动和外伤、烫伤在机械化程度较差的企业,浇铸、落砂、手工锻造时都是较繁重的体力劳动,即使使用气锤或水压机,由于需要变换工件的位置和方向,体力劳动强度很大,同时要在高温下作业,故易引起体温调节和心血管系统的改变。
铸造和锻造的外伤及烫伤率较高,多是由于铁水、钢水、铁屑、铁渣飞溅所致;机加工车间发生眼、手指外伤的较多。
另外金属切削的过程中使用的冷却液对工人的皮肤也有一定的影响。
浅谈机械设备危险因素辨识及预防

动中的金属接头 ; 运动和静止部位 的组合 , 如工作
台 与底 座 、 压 力 机 械 的 滑 块 与模 具 ; 处 于直 线 运 动
状态的刃部 , 如牛头刨床的刨刀、 带锯床的锯片等。
3 、 旋转 运动 的危 险 : 指人 体 或 穿戴 的 衣物 卷进
( 2 ) 灼烫与冻伤 : 如在热加工作业 中接触高温金
2 、 直 线运 动 的 危 险 : 人 与作 直线 运 动 的设 备 引
害, 应充分 了解其危 险有 害因素 , 以便采取有效 的
措 施 防止 事故 的发 生 。
一
、
机械 设 备 的危 险有 害因素 分析
起 的危险, 它分为接近式和经过式危险。具体包括 : ( 1 ) 接近式危险 , 当机械设备处于往复直线运动
浅谈机械设 备 危险 因素辨 识及预 防
福 斯特惠勒动力机械有 限公 司 陈锦胜
机械设备是现代制造 企业 中不可缺少 的生产 设备 。机械设备的使用在提高生产效率的同时也给
企业 的安 全生 产带 来较 大 的风 险 。机 械设 备种 类繁
( 1 ) 切 削 刀具 的刀 刃 。
( 2 ) 机械设备突出的较长部分 , 如设备表面的螺
述危 险 因素外 ,还会 产 生其他 类型 的危险 与有 害 因
素。具体包括 :
( 1 ) 电击 伤 : 包 括 机 械 电气 设 备 绝 缘 不 良 、 接 地 不 良或错 误 操作 等 原 因造 成 的触 电事 故 , 以及 机 械 加 工过 程产 生静 电所 导致 的爆炸 、 电击伤 等事 故 。
可塑性强 , 接受 新知识快 , 但 持久性 差 , 情绪 起伏 大, 所 以对他们必须强化培训 , 引导他们参加各种
机床加工危险源安全措施

机床加工危险源安全措施随着机械制造业的飞速发展,机床加工成为了制造业的重要环节。
但机床加工中存在一系列的危险源,如切削刀具、高温、高压等,所以必须加强机床加工危险源的安全措施,以确保生产作业的安全、稳定和高效。
下面就对机床加工危险源进行分析,并提出常见的安全措施。
危险源一:切削刀具切削刀具在机床加工中属于常见的危险源,它的运转速度非常高,在使用过程中,如果不小心碰到刀具,可能会导致身体受伤,所以必须采取严格的安全措施,减少切削刀具的危害。
安全措施:1. 避免工人操作时过度疲劳,操作人员需要在规定时间内轮班。
2. 在机床上进行操作前,必须仔细检查并确认是否将周围的其他工具清除,以确保操作区域干净、整洁,刀具不留有杂物。
3. 选择适合加工材料的切削刀具,必须根据工件的材质、大小、形状及加工工艺来选择。
4. 在操作机床加工时,必须佩戴个人防护设备,如安全帽、护目镜、手套等,以保护个人安全。
危险源二:高温机床在工作时温度非常高,需要用油来冷却,但这同时也是一个危险源,因为如果不加以注意,可能会导致油的泄漏或失火,从而引发严重的安全事故。
安全措施:1. 对机床的加油、更换油品、清洁机床进行规范管理。
2. 定期检查机床的油管、油泵等零配件,必须保证其正常工作。
3. 在机床加工时,必须保持机床周围的通风,以便热量排放得更加迅速,避免机床内的油温度过高。
4. 在机床的操作区域上加装防护罩,以避免机床的高温射向操作人员。
危险源三:高压机床在进行加工操作的过程中需要用到高压气体、水等,如果不采取足够的安全措施,可能会导致高压泄漏,从而引发严重的安全问题。
安全措施:1. 机床的压力表必须经过标定校验,确保数据的准确性和可靠性。
2. 在机床的操作区域上加装防护罩,以避免高压气体、水等泄漏。
3. 在机床加工时,必须佩戴个人防护设备,如手套、护目镜等,以保护个人安全。
4. 定期检查机床管路、接头等零件的漏水情况,如发现问题,必须立即处理。
钳工危险有害因素辨识及控制措施

钳工危险有害因素辨识及控制措施钳工是一种涉及多种技能和工具的职业,包括机械加工、装配、维修等。
在进行钳工操作时,存在多种危险有害因素,对这些因素进行辨识并采取相应的控制措施是保证操作安全的关键。
本文将从机械伤害、工具和设备使用不当、噪音和振动以及环境污染四个方面进行详细探讨。
1.机械伤害机械伤害是钳工操作中最常见的危险有害因素之一。
在操作过程中,钳工常常需要接触各种机械工具,如机床、砂轮机、钻床等,如果不注意操作方法或使用不当,很容易造成机械伤害。
例如,机床的旋转部分可能会将手卷入其中,导致受伤;砂轮机高速旋转时,可能会产生飞溅的砂轮碎片,造成眼睛或身体受伤;钻床操作时,如果钻头固定不牢或操作不当,可能会产生严重的伤害。
控制措施:在使用机床时,必须佩戴防护手套和护目镜,并确保手部离旋转部分足够远;砂轮机使用前应检查砂轮是否平稳无裂纹,使用过程中要保持一定的倾斜角度,避免砂轮碎片飞溅;钻床操作时,应先检查钻头是否牢固,避免钻头突然脱落造成伤害。
钻小孔时,应采用挤压杆,避免用手直接推钻头。
2.工具和设备使用不当钳工在操作过程中需要使用各种工具和设备,如螺丝刀、榔头、锯、钳等。
如果使用不当或工具质量不好,很容易造成伤害。
例如,使用过长的螺丝刀可能会导致无法准确控制力量,造成手部受伤;使用劣质榔头可能会因其断裂而产生碎片飞溅;使用不合适的锯或钳可能会导致切割不准确或工具损坏等。
控制措施:选择合适的工具和设备,并确保其质量可靠;定期对工具和设备进行检查和维护,及时更换损坏的工具和设备;在使用工具和设备时,必须遵循操作规程和使用说明。
3.噪音和振动钳工在操作过程中常常会遇到噪音和振动问题。
长期处于高分贝噪音和振动环境中,会对听力、神经系统和身体健康产生负面影响。
例如,长期处于高噪音环境中可能会导致听力下降、心血管疾病、头疼头晕等问题;长期处于振动环境中可能会导致手颤、肌肉疲劳、手臂麻木等问题。
控制措施:在操作过程中佩戴防护耳塞或耳罩,减少噪音对听力的影响;尽量避免使用产生振动的工具和设备,如需使用时应采取相应的减振措施;在工作场所设置隔音设施和减振设备,降低噪音和振动对人体的影响。
机械企业(行业)常见危险源识别及控制措施

4、正确装卡刀具和工件,使之牢固。
5、摇把、板子、手柄等用后及时取下。
6、不在机床工作台表面浮放工具和工件。
7、平衡摆放工具,工件。
8、与起重机司机共同遵守起重作业安全规定。
9、穿戴好防护用品。
10、提高技术和操作水平。
11、严格按操作规程操作。
12、常检查接地线,检查照明线,使用安全电压。
4
镗床
1、滑块楔铁、刀杆顶丝销子松动,转动的偏心盘滑动、刃具飞出,镗杆有突出螺钉伤人。
2、工作台未开到机床中心位置,有关人员未站在安全位置,回转台转动工件时挤伤人。
3、螺栓、压板、垫铁、方箱等摆放位置不当,坠落伤人。
4、未穿防护鞋,脚的防护失效易被砸伤。
1、按规定使用防护罩。
2、认真检查已淘汰有缺陷的砂轮。
3、正确安装砂轮。
4、正确选择磨削量和行程速度。
5、及时检查设备,排除故障。
6、正确装卡工件。
7、不使用有缺陷的胎具、顶尖。
8、不在工作台表面浮放工具和工件。
9、要平衡地摆放工具,工件。
10、与起重机司机共同遵守起重作业安全规定。
11、经常检查接地线,检查照明线,使用安全电压。
11、操作不当,产生不安全隐患。
12、机床接地不好,照明灯线裸露,未采用安全电压,易造成触电伤害。
1、正确使防护用品,严禁戴手套操作和手拿棉纱操作。
2、不准在加工过程中测量工件、拆卸工件、擦轼机床及用手清理铁屑。
3、正确掌握进给量。
4、认真检查,及时淘汰有缺陷夹具,刀具。
5、正确装卡刀具和工件。
6、不在机床工作台表面浮放工具和工件。
机械企业(行业)常见危险源识别及控制措施
机械加工工艺中危险源辨识与危险因素控制

机械加工工艺中危险源辨识与危险因素控制作者:赵文光来源:《装饰装修天地》2015年第06期摘要:机械工业是国民经济的基础性产业,也是国民经济的装备产业,承担者为国民经济各部门、各行业提供技术装备和生产工具的任务。
因此它不仅是国家工业化的重要组成部分,也是国家工业化的物质和技术保障,机械工业的发展水平在很大程度上影响甚至决定着相关产业部门的技术进步和产业发展水平。
关键词:机械加工;危险源;危险因素;控制方法前言机械安全是制造业赖以生存和发展的基础,涉及到国民经济各个部门和人民的安全与健康。
为了有效地控制机械加工工艺的危险性,防止机械事故发生,减少人员伤亡和财产损失,文章介绍了机械加工工艺中危险源辨识方法,提出了机械加工工艺危险因素控制措施。
一、危险源的概念危险源是指系统中具有潜在能量和物质释放危险的,在一定触发因素作用下可能转化为事故的部位、区域、场所、空间、岗位、设备及其位置。
这里所指的触发因素是危险源转化为事故的外因,它包括压力、温度、安全措施、环境、工艺等等。
危险源的辨识评价和控制是企业安全管理的主要内容,它对于明确企业安全管理的重点,控制事故的发生,以寻求最低事故率、最少的人员伤亡和经济损失起着重要的作用,同时,也是建立《职业健康安全管理体系》的重要内容。
所以,对企业危险源的识别、评价和控制是预防和控制工伤事故和职业危害的必要手段。
通过对系统的分析、界定出危险源,并评价其危险的性质、危害程度、存在状况、危险源能量与物质转化过程的规律、转化的条件、触发因素等,以便有效地控制能量和物质的转化、使危险源不至于转化为事故。
二、机械加工工艺中危险源辨识方法危险源辨识的方法很多,每一种方法都有其目的性和应用的范围。
下面介绍几种可用于建立体系的危险源辨识方法:1.现场观察通过对工作环境的现场观察,可发现存在的危险源。
从事现场观察的人员,要求具有安全技术知识和掌握了完善的职业健康安全法规、标准。
2.询问、交谈对于组织的某项工作具有经验的人,往往能指出其工作中的危害。
机床加工危险源辨识与控制措施:保障安全

机床加工危险源辨识与控制措施:保障安全机床加工危险源辨识和控制措施机床加工是一种广泛使用的制造过程,包括多种设备和工具,如钻床、铣床、磨床、锯床等。
在机床加工过程中,存在许多潜在的危险源,如果不加以控制,可能会导致事故发生。
本文将探讨机床加工危险源辨识和控制措施,主要包含以下方面内容:1.防护不当2.机床加工中,防护不当可能带来机械故障、漏电等危险。
为了降低风险,操作者必须使用正确的个人防护用品(如眼镜、面罩、耳塞等),并确保设备有良好的接地和漏电保护装置。
3.操作不当4.操作机床加工时,不当行为如带电作业、随意触摸带压部件等可能引发事故。
为避免危险,操作者应接受正规培训,熟练掌握操作规程,了解设备特性及应急处理方法。
5.工具和设备6.机床加工中常用的工具和设备,例如砂轮、钻床、铣床、磨床等,以及使用这些设备可能带来的危险。
使用砂轮时应注意佩戴防护眼镜,避免砂粒飞溅;使用钻床时应注意正确操作方法,避免工件、钻头破碎等;使用铣床和磨床时应按要求操作,避免机械伤害。
7.噪音和振动8.机床加工中可能产生噪音和振动,这些因素对人的生理影响较大,长时间暴露可能导致听力受损、手颤等。
为保障操作者健康,应佩戴耳塞、减震手套等防护用品,合理安排工作时间和休息时间。
9.高温环境10.机床加工中高温环境对人和设备的影响也较大。
为了降低风险,应合理安排工作场所的通风和降温设施,避免因高温导致设备故障和人员伤亡。
11.电源和机械故障12.机床加工中电源和机械故障可能带来的危险,以及如何避免这些危险。
操作者应定期检查电源线路和机械部件,避免老化和破损造成的危险。
同时应遵循“停电作业”等安全规定,确保操作者安全。
13.缺乏安全培训14.缺乏安全培训可能使得操作者对机床加工的危险源并不了解,从而在实际操作中容易发生事故。
因此,必须对操作者进行充分的安全培训,提高其安全意识,使其能够正确地处理各种危险情况。
15.不正确的维护和修理16.不正确的维护和修理可能给机床带来损害,甚至引发事故。
机械操作危险因素识别及控制措施
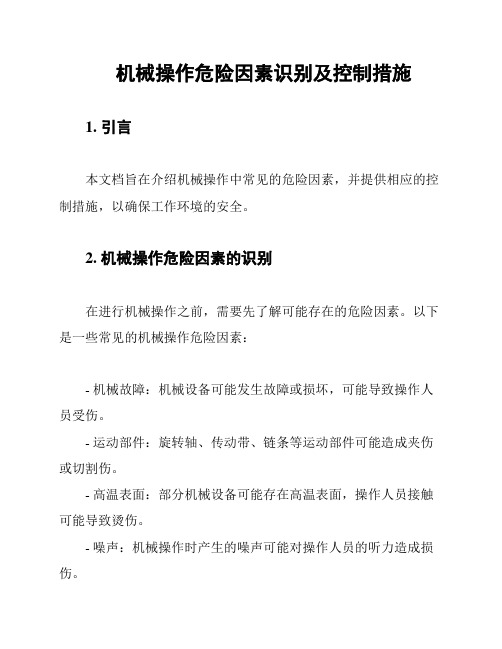
机械操作危险因素识别及控制措施1. 引言本文档旨在介绍机械操作中常见的危险因素,并提供相应的控制措施,以确保工作环境的安全。
2. 机械操作危险因素的识别在进行机械操作之前,需要先了解可能存在的危险因素。
以下是一些常见的机械操作危险因素:- 机械故障:机械设备可能发生故障或损坏,可能导致操作人员受伤。
- 运动部件:旋转轴、传动带、链条等运动部件可能造成夹伤或切割伤。
- 高温表面:部分机械设备可能存在高温表面,操作人员接触可能导致烫伤。
- 噪声:机械操作时产生的噪声可能对操作人员的听力造成损伤。
- 振动:某些机械设备的运行会产生振动,长期暴露可能对操作人员的健康产生不良影响。
3. 机械操作危险因素的控制措施为了减少机械操作中的危险风险,可以采取以下控制措施:- 定期维护:定期检查机械设备的状态,及时修复或更换存在问题的部件,以减少机械故障的风险。
- 使用防护装置:在机械设备上安装适当的防护装置,如安全挡板、护罩等,以防止操作人员接触到运动部件,减少夹伤和切割伤的风险。
- 提供个人防护装备:操作人员应佩戴适当的个人防护装备,如手套、耳塞等,以降低高温表面、噪声和振动对人体的伤害。
- 隔离噪声源:通过隔音设备或减少机械设备运行时间等方式,减少噪声对操作人员的影响。
- 提供培训和指导:为操作人员提供相关的培训和指导,使其了解机械操作的风险和安全措施,有效防范危险因素。
4. 总结机械操作危险因素的识别和控制是确保工作环境安全的重要步骤。
通过认真识别危险因素,并采取适当的控制措施,可以减少操作人员的伤害风险,并提高工作效率。
有关具体机械操作危险因素的识别和控制,请参考相关的安全规范和法律法规。
机械加工危险、危害因素与控制措施

仅供参考[整理] 安全管理文书机械加工危险、危害因素与控制措施日期:__________________单位:__________________第1 页共5 页机械加工危险、危害因素与控制措施(1)机械伤害。
由于设备旋转部位(齿轮、联轴节、工具、工件等)无防护装置或失效、人员操作不当等可能导致发生切伤、割伤、卷入等伤害;由于设备维护不良、工件装夹不牢固等操作失误,造成工件、工具或零部件飞出伤人:由于设备之间的距离或与墙、柱的距离过小,活动机件运动时造成人员挤伤;由于切削加工时长屑未断屑或短屑防护不当造成割伤或崩伤;冲剪压作业时由于防护装置失灵、手误人冲剪压区等造成伤手事故;机械设备上的尖角、锐边等可能引起划伤;检修过程中防护措施不到位,人员配合失误,未佩戴合适的防护用品等,可能导致碰伤、划伤、砸伤。
(2)触电。
由于设备漏电,未采取必要的安全技术措施(如保护接零、漏电保护、安全电压、等电位联结等)或措施失效,操作人员的操作失误或违章等,可能导致人员触电。
(3)起重伤害。
由于起重设备质量缺陷、安全装置失灵、操作失误、管理缺陷等因素均可发生起重伤害事故。
(4)火灾。
机械设备使用的润滑油属于易燃物品,在有外界火源作用下可能引起火灾;由于电气设备故障、电线绝缘老化、电气设备检查维护不到位第 2 页共 5 页等还可能引起电气火灾。
(5)车辆伤害。
(6)噪声。
(7)振动。
(8)高处坠落。
2.金属切削机床的安全防护装置(1)防护罩(隔离外露的旋转部件)/防护网(防止人体通过)。
(2)防护挡板:隔离磨屑、切屑和冷却润滑液,避免其飞溅伤人。
(3)防护栏杆:防工作台往复运动时伤人。
(4)保险装置和控制装置。
超负荷保险装置:工作中发生超负荷情况时使机床停止运行。
行程限位装置:当工作台到达预定位置时,用档块或行程限位器压下行程开关,工作台就自动停止或返回。
顺序动作连锁装置:控制各运动按顺序进行,上一个动作未完成前,下一个动作不能进行。
机械加工危险点及其控制措施
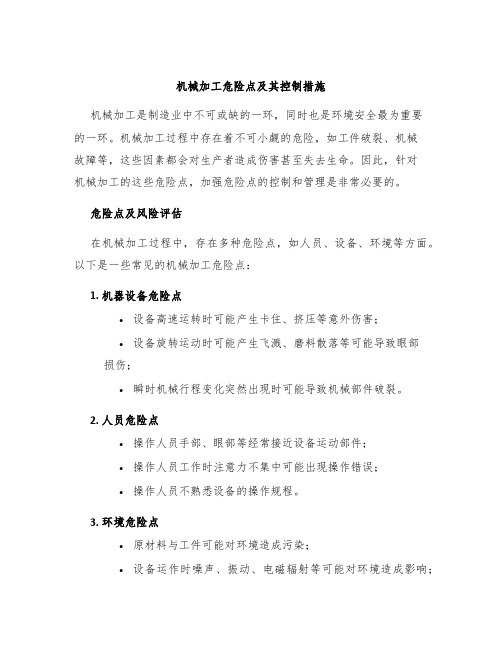
机械加工危险点及其控制措施机械加工是制造业中不可或缺的一环,同时也是环境安全最为重要的一环。
机械加工过程中存在着不可小觑的危险,如工件破裂、机械故障等,这些因素都会对生产者造成伤害甚至失去生命。
因此,针对机械加工的这些危险点,加强危险点的控制和管理是非常必要的。
危险点及风险评估在机械加工过程中,存在多种危险点,如人员、设备、环境等方面。
以下是一些常见的机械加工危险点:1. 机器设备危险点•设备高速运转时可能产生卡住、挤压等意外伤害;•设备旋转运动时可能产生飞溅、磨料散落等可能导致眼部损伤;•瞬时机械行程变化突然出现时可能导致机械部件破裂。
2. 人员危险点•操作人员手部、眼部等经常接近设备运动部件;•操作人员工作时注意力不集中可能出现操作错误;•操作人员不熟悉设备的操作规程。
3. 环境危险点•原材料与工件可能对环境造成污染;•设备运作时噪声、振动、电磁辐射等可能对环境造成影响;•机械加工过程中可能产生电火花,存在火灾隐患。
为了对这些危险进行准确评估,需要进行风险评估操作。
风险评估是对潜在危险进行评估,给出相应的风险等级,以便于后续做出相应的安全措施。
在机械加工中,风险评估通常包括以下几个步骤:•识别有可能发生的危险因素;•评估机械加工作业的特定危险成分和潜在风险;•确定每种危险的潜在危害和优先级;•制定及实施必要的控制措施;•监控并持续评估每种危险的持续时间和效果。
控制措施为了降低机械加工带来的风险,采取一系列控制措施是非常必要的。
以下是一些常见的机械加工控制措施:1. 设备安全措施•安装有效的保护装置以防止机械损伤;•检查设备的运行状况以确保其安全;•对机器设备实施定期保养和检查。
2. 人员安全措施•培训和审核操作人员的技能和知识;•鼓励自我保护行为;•提供全面的安全操作指南。
3. 设备环境措施•把设备、工作站、光源等离其他设备和人员远一些,以减少受环境影响;•确保适当的通风和气体排放。
4. 应急安全措施•制定和实施应急处理计划;•为人员提供应急处理培训以及应急装备。
常用机械的危险因素及控制方法

常用机械的危险因素及控制方法机械设备在生产和工作过程中发挥了重要的作用,但同时也会带来一定的危险因素。
在使用机械时,必须注意操作规程和安全方法,避免意外事故的发生。
本文主要介绍常用机械的危险因素及控制方法。
一、钳工机械危险因素1.机械部件旋转时,容易夹住危害操作人员。
2.大型的卷扬机可能会导致扭曲的绳索爆裂并再次捻断。
3.物品掉落从高处,导致金属毁坏而且人员会被压伤。
控制方法1.在起重机上安装护栏,避免人的接近。
2.对于较大的机械设备,应该使用保护罩或护栏。
3.当卷扬机操作时,应该始终保持绳子安全,动态调整绳索,以最小化发生滑动的概率。
二、电焊机危险因素1.电焊可以产生强大的热,可能会引发火灾或燃烧。
也会引起对眼睛和皮肤的危害。
2.电焊机在操作时会发出较强的电磁辐射,这可能会对周围的电子设备产生负面影响。
1.在现场设置消防器材,避免火灾的发生,并且使用专业防护面具等装备,防止热和光辐射造成的伤害。
2.在操作电焊机时,应该尽量避免长时间的暴露,必要时应采取防护措施。
3.对于那些无法承受电磁辐射,具体使用情况不明确的设备,应加以合理的隔离和保护。
三、切割机械危险因素1.当使用锯床或带锯床等旋转机械时,一定要注意避免手指或其他部位被绞住。
2.靠近起重机或其他危险机械时,可能会受到物件掉落的打击或埋入灰尘中。
控制方法1.在机械设备的周围设置护栏或保护装置,避免人的碰触和接近。
2.当使用锯床和类似切割机械时,应该减少手指和其他身体部位的接触,避免危险发生。
四、冲床机械危险因素1.换模和更换零件时,可能会受到机械碎片的伤害。
2.操作冲床机械接触生产过程物件时,发生滑动的情况。
该情景是产生的伤害性很大。
1.在生产设备中设置冲床设备的安全防护措施,如保护罩、护栏,避免人的接近。
2.在机械设备运转之前,必须检查一下设备是否完好,出现不良现象不要开机运行,及时进行修理。
五、起重机械危险因素1.指头、手掌或手臂会卡住机器中的绳索或元件而受伤。
机械加工设备危险有害因素分类

机械加工设备危险有害因素分类机械加工设备是高效生产的关键设备,能够完成许多工业制造任务。
然而,与此同时,机械加工设备也带来了相应的危险和有害因素。
这些危险因素显著增加了机械加工设备的操作难度和工作强度,也增加了事故和疾病的风险。
本文将对机械加工设备的危险有害因素进行分类,并分析其可能的危害性。
一、机械加工设备的物理危险物理危险是指由于机械加工设备的构造、运行和使用方式而引起的危险。
这类危险主要包括以下几种:1.机械部件的旋转和运动:许多机械设备在操作时会产生旋转和运动,这将带来不小的危险。
例如,旋转的机械部件可能会使人受伤或造成严重的割伤和挤压,也可能会导致生产效率降低。
2.高温和高压:许多机械加工设备使用极高温度和压力。
在使用中,这些温度和压力可能会瞬间释放,危及人员安全。
例如,锅炉、压力罐和熔炉等设备会产生高温高压,如果操作不当就会引起爆炸事故。
3.机械设备的噪声:高噪声对人员的听力、身体健康和工作效率都会产生负面影响。
长期暴露在噪声环境中会引起听力下降、血压升高、心血管疾病和精神紊乱等疾病。
二、化学危害化学危害主要指机械加工设备使用的化学物质对人体健康的威胁。
机械加工设备在操作的过程中会产生不少有害物质,这些物质比如气体、液体或固体会在工作环境中释放出来,极易危害工人的健康甚至致命。
常见的化学危害物质有:1.重金属:许多工业生产中使用的重金属,如铬、铅、铜、锌等,都是有害物质。
这些重金属一旦被人体摄入过多,将导致健康损害或中毒。
2.有机化合物:许多机械加工设备使用的有机化合物,如涂料、溶剂、油漆等,也容易形成挥发性有机化合物,这些物质极易造成中毒。
3.卤素元素化合物:卤素元素化合物是化学物质的一种类型,如氯气、氢氟酸等,在工作环境中容易释放出来,对人体危害很大。
三、电气危险电气危险主要指与机械加工设备使用的电流有关的危险。
机械产品的电气危险包括电击、电焊火花、电短路等,即使使用低压电流的机械设备,也有可能对人员造成危险。
机械加工工艺中危险源辨识与危险因素控制
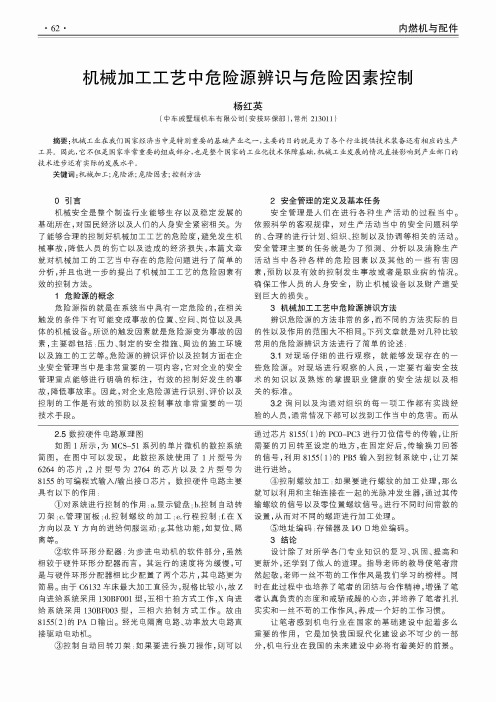
2 安全管理的定义及基本任务 安全管理是人们在进行各种生产活动的过程当中。 依 照 科 学 的 客 观 规 律 ,对 生 产 活 动 当 中 的 安 全 问 题 科 学 的 、合 理 的 进 行 计 划 、组 织 、控 制 以 及 协 调 等 相 关 的 活 动 。 安全管理主要的任务就是为了预测、分析以及消除生产 活动当中各种各样的危险因素以及其他的一些有害因 素 ,预防以及有效的控制发生事故或者是职业病的情况。 确 保 工 作 人 员 的 人 身 安 全 ,防 止 机 械 设 备 以 及 财 产 遭 受 到巨大的损失。 3 机械加工工艺中危险源辨识方法 辨 识 危 险 源 的 方 法 非 常 的 多 ,而不同的方法实际的目 的性以及作用的范围大不相同。下列文章就是对几种比较 常用的危险源辨识方法进行了简单的论述: 3 . 1 对 现 场 仔 细 的 进 行 观 察 ,就能够发现存在的一 些危险源。 对 现 场 进 行 观 察 的 人 员 ,一定要有着安全技 术的知识以及熟练的掌握职业健康的安全法规以及相 关的标准。 3.2询问以及沟通对组织的每一项工作都有实践经 验 的 人 员 ,通 常 情 况 下 都 可 以 找 到 工 作 当 中 的 危 害 。 而从
简易。由 于 C6 1 3 2 车床最大加工直径为,规格比较小,故 Z 时在此过程中也培养了笔者的团结与合作精神,增强了笔
向进给系统采用130BF0 0 1 型 ,五相十拍方式工作,X 向进 者认真负责的态度和戒骄戒躁的心态,并培养了笔者扎扎
给 系 统 采 用 130BF0 0 3 型 ,三 相 六 拍 制 方 式 工 作 。故由 实实和一丝不苟的工作作风,养成一个好的工作习惯。
⑤ 地址编码:存 储 器 及 1O □地处编码。
两^F。
机械加工工业要注意的职业病危害范文
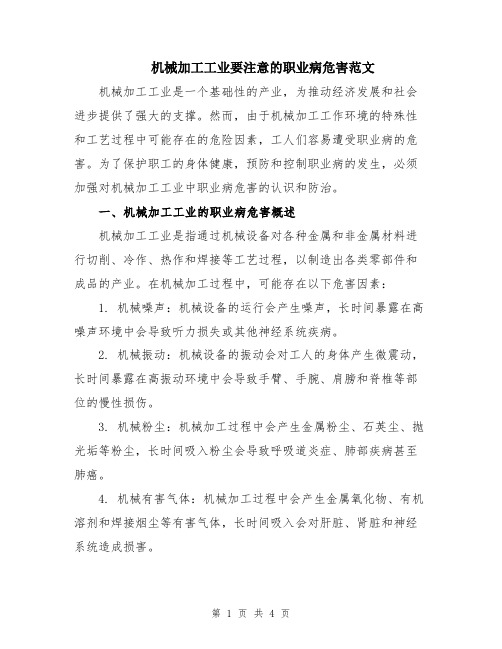
机械加工工业要注意的职业病危害范文机械加工工业是一个基础性的产业,为推动经济发展和社会进步提供了强大的支撑。
然而,由于机械加工工作环境的特殊性和工艺过程中可能存在的危险因素,工人们容易遭受职业病的危害。
为了保护职工的身体健康,预防和控制职业病的发生,必须加强对机械加工工业中职业病危害的认识和防治。
一、机械加工工业的职业病危害概述机械加工工业是指通过机械设备对各种金属和非金属材料进行切削、冷作、热作和焊接等工艺过程,以制造出各类零部件和成品的产业。
在机械加工过程中,可能存在以下危害因素:1. 机械噪声:机械设备的运行会产生噪声,长时间暴露在高噪声环境中会导致听力损失或其他神经系统疾病。
2. 机械振动:机械设备的振动会对工人的身体产生微震动,长时间暴露在高振动环境中会导致手臂、手腕、肩膀和脊椎等部位的慢性损伤。
3. 机械粉尘:机械加工过程中会产生金属粉尘、石英尘、抛光垢等粉尘,长时间吸入粉尘会导致呼吸道炎症、肺部疾病甚至肺癌。
4. 机械有害气体:机械加工过程中会产生金属氧化物、有机溶剂和焊接烟尘等有害气体,长时间吸入会对肝脏、肾脏和神经系统造成损害。
5. 机械辐射:机械加工过程中可能会产生紫外线、红外线和可见光等辐射,长时间接触辐射会导致皮肤炎症、眼睛疾病和恶性肿瘤。
以上是机械加工工业常见的职业病危害,但并不是所有的厂商和工人都面临相同的危害。
具体的职业病危害取决于具体的工艺过程、机械设备、操作方式和环境条件等。
二、机械加工工业职业病防治的措施针对机械加工工业的职业病危害,制定和实施科学的职业病防治措施是非常重要的。
1. 工艺改进:通过改进工艺流程,选择合适的工艺装备和工具,降低机械加工过程中的噪声、振动和粉尘等危害因素。
例如,采用液切、激光切割等无尘切削技术,减少粉尘产生。
2. 安全防护:为工人提供科学的个人防护用品,如防护面具、防尘口罩、护目镜、防噪耳塞等,降低噪声、振动、粉尘和辐射等危害因素对工人的伤害。
机械制造业危害因素

“机械制造业为整个国民经济提供技术装备,是国家重要的支柱产业。
但机械制造过程中的铸造、锻造、热处理、机械加工和装配等工艺,均存在各种职业病危害因素,同时机械制造业涉及范围广泛,产业工人队伍庞大,因此机械制造业职业病危害因素对作业人员的健康影响日益突出。
那么,机械制造业职业病危害危害因素有哪些?又该该如何防治?危害因素机械制造业的主要生产工艺包括:铸造工艺、锻压工艺、热处理工艺、机械加工工艺(钻、铣、镗、车、刨、磨等)、金属表面处理工艺、焊接与气割工艺、涂装工艺和组装。
铸造工艺主要职业病危害因素包括粉尘、化学毒物、噪声、振动、高温与热辐射、高频电磁场和微波辐射等。
模样制造、铸件的落砂与清理过程中产生型砂尘,浇注过程中产生金属烟尘.用树脂做胶黏剂制芯时可接触酚、甲醛和氨;煤炉作业产生一氧化碳、二氧化碳、二氧化硫和氮氧化物等.在震实、压实等机械设备运行中产生噪声、振动。
砂型和砂芯烘干设备、合金熔炼设备、浇筑过程中产生高温与热辐射。
采用高频感应炉或微波炉加热时产生高频电磁场和微波辐射。
锻压工艺主要职业病危害因素包括生产性粉尘、化学毒物、噪声和振动、高温与热辐射.锻造炉、锻锤工序中加料、出炉、锻造过程可产生金属粉尘、煤尘和炉渣尘等.燃烧锻炉可产生一氧化碳、二氧化硫、二氧化碳、氮氧化物等有害气体;镁件时可产生氧化镁烟.冲床、剪床可产生高强度噪声,一般为脉冲式噪声.加热炉产生高温与强辐射热.热处理工艺主要职业病危害因素包括化学毒物、噪声、高温与热辐射、高频电磁场。
在渗碳、渗氮等过程中产生,如氮化过程产生氨气、氢化物、一氧化碳、氮氧化物.在机械设备运行时产生噪声。
各种加热炉和被加热的工件会产生高温与热辐射。
高频电炉运行时产生高频电磁场。
金属表面处理工艺主要职业病危害因素是化学毒物。
工艺过程中通常产生酸雾、碱(硫酸、盐酸、磷酸、氢氧化钠、二氧化氮、铬酸盐),有些工艺会使用氰化物、镍化合物、镉及其化合物、氧化锌、氯化物、苯、二甲苯、乙二醇等化学物质。
机械加工工艺中危险因素的控制

机械加工工艺中危险因素的控制我国机械加工的种类和形式非常多样,随着机械加工的复杂化、重型化,机械加工的工艺中存在着一定的危险因素,给机械加工的安全性带来了很大的挑战,危险因素给加工行业带来了很大的损失,影响行业加工效益的提升,文章结合作者自身的工作经验,分析机械加工工艺的种类和危险因素的控制,以便为相关的研究提供参考性的建议。
标签:机械加工;工艺;危险因素;种类引言机械加工行业是我国国民经济的支柱,承担着国民经济中的各种任务,为各行业的发展提供技术装备和生产的支持,是我国工业化发展的重要组成部分,机械行业的发展在很大程度上决定了产业的发展水平,是国家工业化的技术和物质的基础保障。
但是由于机械加工工艺存在着一定的危险,而据国际劳工组织的统计调查得出,全世界每年死于机械制造行业的人数大约有10万人,导致伤残的有150万人,这给机械加工行业带来了严重的影响,给员工和企业都带来了巨大的危害。
我国是机械加工大国,由于机械加工工艺中的危险所造成的损失不容乐观,后果严重。
作者结合已有的工作经验,从机械加工工艺的生产特点为出发点,分析其中存在的危险因素,并探讨其控制措施,以拓展相关研究。
1 机械加工工艺的分析机械加工中在获得原材料后,经过加工手段得到零件的半成品或成品,采用的机械加工工艺有焊接、锻压、铸造、切削等成型工艺,其本身种类多样,加工的形式复杂多变,以下做简要的分析论述:1.1 机械加工的工具设备种类多:机械加工的工艺非常多,因而要根据加工的需要采用不同的工具设备,如常见的切削加工,而切削加工中的机床有普通机床和数控机床,机床中使用的刀具、托架等形式非常广泛;如钳工操作中的工具有手锯、刮刀、锉刀、电钻、钻床等。
这些机械加工的工具设备在材料、型号、种类等方面都有极其细致的分别,适用于不同的场合。
1.2 机械加工的工种类型多:机械加工工艺的工种类型非常多,如车工、锻工、铣工、插工、钳工、磨工、钻工、冲压工、钣金工、下料工,还有一些特殊的工艺,如电火花加工、激光加工、电解加工、超声波加工和离子束加工等,由于加工种类的不同,在操作中存在的危险因素也不尽相同,但各工种中都存在一定的危险性,尤其是在传统的加工设备中,出现危险的情况几率较大。
浅谈机械加工工艺中危险因素的控制

浅谈机械加工工艺中危险因素的控制【摘要】近年来,随着我国经济的快速发展,工业发展进入重型化,我国工业生产,特别是机械加工企业的安全管理问题日益凸现,对于机械加工企业的安全管理的探讨已经迫在眉睫。
本文首先阐述了安全管理的定义及基本任务,针对机械加工企业主要存在的安全问题,分析了机械加工出现安全问题的原因,同时对如何加强对机械加工企业的安全管理提出了自己的看法。
【关键词】机械加工;工艺;事故;危险性机械工业是国民经济的基础性产业,也是国民经济的装备产业,承担着为国民经济各部门、各行业提供技术装备和生产工具的任务。
因此它不仅是国家工业化的重要组成部分,也是国家工业化的物质和技术保障,机械工业的发展水平在很大程度上影响甚至决定着相关产业部门的技术进步和产业发展水平。
根据国际劳工组织统计,机械制造业中全世界每年因工死亡人数约10万人,丧失工作能力的约150万人,可见,机械行业安全生产事故发生次数之频繁,后果之严重。
1.机械加工的生产特点在机械零件的制造过程中,利用去除多余材料获得所需零件或半成品的加工方法称为机械加工,而采用铸造、锻压、焊接等获得所需零件或毛坯的加工方法称为成型工艺。
机械加工业本身具有的特点有:(1)工种类别多:机械加工的工种包括锻工、车工、镗工、铣工、刨工、插工、磨工、钳工、钻工、木工、冲压工、下料工、铆工、钣金工等,各工种有各自的操作特点和操作危险性,不同类型和规模的企业涉及的操作工种也各不相同。
随着技术水平的提高,机械加工业还出现了一些新型的加工方法,包括特种加工、电火花加工、电解加工、激光加工、离子束加工和超声加工等,大大扩展了加工工艺类别。
(2)设备和工具类型多:机械加工过程中,由于加工工艺不同,使用的设备和工具也不同,如锻工操作中需要用到装料叉、装出炉夹钳、胎模操作机、锻造操作机等;钳工操作需要的工具和设备有锉刀、刮刀、手锯、凿子、手锤、手电钻、钻床等。
此外,根据使用要求这些工具和设备还分成不同的型号和类型,增加了其使用数量。
机械加工企业危险因素分析
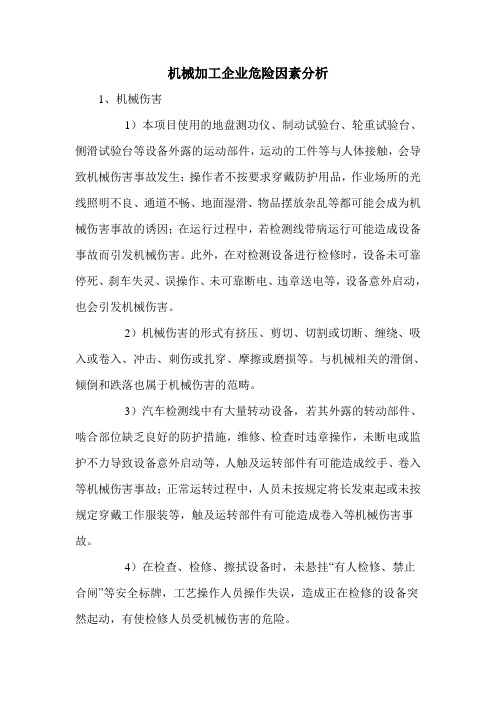
机械加工企业危险因素分析1、机械伤害1)本项目使用的地盘测功仪、制动试验台、轮重试验台、侧滑试验台等设备外露的运动部件,运动的工件等与人体接触,会导致机械伤害事故发生;操作者不按要求穿戴防护用品,作业场所的光线照明不良、通道不畅、地面湿滑、物品摆放杂乱等都可能会成为机械伤害事故的诱因;在运行过程中,若检测线带病运行可能造成设备事故而引发机械伤害。
此外,在对检测设备进行检修时,设备未可靠停死、刹车失灵、误操作、未可靠断电、违章送电等,设备意外启动,也会引发机械伤害。
2)机械伤害的形式有挤压、剪切、切割或切断、缠绕、吸入或卷入、冲击、刺伤或扎穿、摩擦或磨损等。
与机械相关的滑倒、倾倒和跌落也属于机械伤害的范畴。
3)汽车检测线中有大量转动设备,若其外露的转动部件、啮合部位缺乏良好的防护措施,维修、检查时违章操作,未断电或监护不力导致设备意外启动等,人触及运转部件有可能造成绞手、卷入等机械伤害事故;正常运转过程中,人员未按规定将长发束起或未按规定穿戴工作服装等,触及运转部件有可能造成卷入等机械伤害事故。
4)在检查、检修、擦拭设备时,未悬挂“有人检修、禁止合闸”等安全标牌,工艺操作人员操作失误,造成正在检修的设备突然起动,有使检修人员受机械伤害的危险。
2、电气系统危害1)汽车检测线用电量大,主要用电事故的原因有:线路短路;负荷超载引起火灾;由于设备自身故障导致过热而引起火灾;设备避雷、接地不良引起雷电火灾等。
另外,误操作,以及主要电气设备(变压器、避雷器、电缆等)没有定期检查、试验、维护而使绝缘老化也易引发火灾、爆炸事故。
2)变配电室没有挡鼠板,没有防小动物网,变配电室电缆出入口没有堵塞,有可能致使小动物窜入,从而引发短路、跳闸等故障,造成突然停电事故,有引起生产装置发生火灾爆炸的危险;变压器过载或线路短路、变压器油泄漏、设备自身故障导致过热等可引起火灾;变压器避雷、接地不良可引起雷电火灾;变压器故障可造成停电导致生产失控,可能发生火灾、爆炸、泄漏中毒事故。
- 1、下载文档前请自行甄别文档内容的完整性,平台不提供额外的编辑、内容补充、找答案等附加服务。
- 2、"仅部分预览"的文档,不可在线预览部分如存在完整性等问题,可反馈申请退款(可完整预览的文档不适用该条件!)。
- 3、如文档侵犯您的权益,请联系客服反馈,我们会尽快为您处理(人工客服工作时间:9:00-18:30)。
浅谈机械加工工艺中危险因素的控制
【摘要】近年来,随着我国经济的快速发展,工业发展进入重型化,我国工业生产,特别是机械加工企业的安全管理问题日益凸现,对于机械加工企业的安全管理的探讨已经迫在眉睫。
本文首先阐述了安全管理的定义及基本任务,针对机械加工企业主要存在的安全问题,分析了机械加工出现安全问题的原因,同时对如何加强对机械加工企业的安全管理提出了自己的看法。
【关键词】机械加工;工艺;事故;危险性
机械工业是国民经济的基础性产业,也是国民经济的装备产业,承担着为国民经济各部门、各行业提供技术装备和生产工具的任务。
因此它不仅是国家工业化的重要组成部分,也是国家工业化的物质和技术保障,机械工业的发展水平在很大程度上影响甚至决定着相关产业部门的技术进步和产业发展水平。
根据国际劳工组织统计,机械制造业中全世界每年因工死亡人数约10万人,丧失工作能力的约150万人,可见,机械行业安全生产事故发生次数之频繁,后果之严重。
1.机械加工的生产特点
在机械零件的制造过程中,利用去除多余材料获得所需零件或半成品的加工方法称为机械加工,而采用铸造、锻压、焊接等获得所需零件或毛坯的加工方法称为成型工艺。
机械加工业本身具有的特点有:
(1)工种类别多:机械加工的工种包括锻工、车工、镗工、铣工、刨工、插工、磨工、钳工、钻工、木工、冲压工、下料工、铆工、钣金工等,各工种有各自的操作特点和操作危险性,不同类型和规模的企业涉及的操作工种也各不相同。
随着技术水平的提高,机械加工业还出现了一些新型的加工方法,包括特种加工、电火花加工、电解加工、激光加工、离子束加工和超声加工等,大大扩展了加工工艺类别。
(2)设备和工具类型多:机械加工过程中,由于加工工艺不同,使用的设备和工具也不同,如锻工操作中需要用到装料叉、装出炉夹钳、胎模操作机、锻造操作机等;钳工操作需要的工具和设备有锉刀、刮刀、手锯、凿子、手锤、手电钻、钻床等。
此外,根据使用要求这些工具和设备还分成不同的型号和类型,增加了其使用数量。
(3)加工对象繁多:加工对象有坯料和工件,其形状各异:包括块状、柱状、板状、棒状、锥状、不规则状等;材质不同:有钢、铸铁、各种合金、塑料、木材等。
此外,机械加工采用各种类型的工艺装置,工艺方法也多种多样,生产工序复杂多变,许多操作需要多人配合才能完成,因此产生的事故也是多种多样的。
2.安全管理的定义及基本任务
安全管理是人类在各种生产活动中,按照安全科学所揭示的客观规律,对生产活动中的安全问题进行计划、组织、指挥、控制和协调等一系列活动的总称。
安全管理的基本任务是预测、分析和消除生产活动中的各种危险因素和有害因素,预防和控制事故和职业病的发生,保障职工的人身安全及身心健康,避免设备和财产遭受损失,创造优良的工作环境,从而推动生产活动的顺利进行,为提高生产活动的经济效益和社会效益服务。
3.机械加工工艺危险因素分析和控制
我国《企业职工伤亡事故分类》(GB 6441-1986)综合考虑起因物和诱导性原因、致害物和伤害方式,将伤害事故分为20类,其中,与机械方面相关的伤害事故统称为机械伤害事故,但没有把机械伤害按不同的伤害方式进行分类。
就目前关于机械行业的事故统计资料来看,也大都没有将机械伤害种类细分,导致防治不利,事故频发。
针对这种情况,本文在进行事故统计的过程中,在考虑其他事故类型的同时,将机械伤害事故按不同伤害形式细化,从绞伤、碾压、夹挤、摩擦等方面单独进行分析,以便有针对性地提出防范措施。
为了研究机械加工工艺的危险性,对收集到的机械加工行业的生产事故进行统计分析表明,在1050起事故中,造成死亡42人,重伤997人,轻伤20人,分别占伤亡情况的4%,94%,2%,为了便于分析研究,将收集的事故按加工工艺分类,各加工工艺事故所占事故总数比重见。
3.1车工、镗工操作
针对车工、镗工的操作特点,在生产过程中应着力加强一下三个方面的管理:(1)旋转部位的防护,包括:①工件、夹具的防护,如卡盘、拨盘、花盘等;②光杆、丝杆的防护;③皮带轮与挂轮的防护。
(2)切屑的防护措施,针对带状切屑,可以采用断屑槽或断屑器使其折断或变成节状,减小对人身的伤害,对于崩碎的切屑可采用防护板或防护罩挡住碎屑的飞溅。
另外,要及时对操作地点堆积的切屑要用安全工具(毛刷、钢钩等)进行清理。
(3)加强生产管理,尤其对不佩戴防护用具、不安全装束、注意力不集中、违规操作等现象严加管制,及时检修更换设备,防止因设备“带病”作业和设备老旧引发事故。
3.2铣工操作
由车工事故统计结果不难看出,铣工常易发生的事故时铣床的旋转部位的伤害,其中由铣刀造成的切割伤害所占比重最大,为72.8%,其次是旋转部位的绞伤和切屑伤害,分别为13.6%和10.7%。
发生铣工操作事故的原因归纳起来主要有:缺乏必要的安全技术知识而导致操作失误,所占比例为37.9%,缺少必要的防护装置,所占比例为31.1%,此外,还存在着生产管理缺陷、夹具安装不当或结构不合理,刀具选用不当等原因。
为保证铣工操作安全顺利进行,生产单位应经常进行安全教育和技能培训,提升员工的专业素质水平,设置或改进铣刀刀罩、防屑挡板等防护装置,对铣床外露的旋转部分,如卧式铣床主轴后端紧固刀杆的拉紧螺杆头部、挂轮架上转动着的齿轮等加以重点防护,确保刀具和夹具安装正确牢固,对于设计制造不合理或质量有缺陷的工具严格把关,不能用于生产过程当中。
3.3磨工操作
根据上述分析原因及磨工操作的特点,生产单位应当遵循正确的验收及保管原则,选择合理粒度和硬度的砂轮进行加工,磨削前必须仔细检查工件的装夹是否正确,制定并严格遵守磨工操作规程,干磨和修整砂轮时戴手套和防护眼镜,为各种磨床砂轮安装合理的防护罩,磨床配备吸尘装置,创造良好的工作环境。
4.结论
(1)机械加工工种类别多,加工工艺复杂,生产事故频发,事故等级多为一般事故,通常一起事故导致一人伤亡,多则两三人。
(2)机械加工事故虽然死亡人数不多,但是伤害后果严重,一旦发生事故多是丧失劳动能力的重伤事故。
(3)在统计的资料中,冲压工操作最易发生事故,占所有操作工种事故的30%,其次是钻工钳工和车工钳工,分别占17%和14%。
因此,要加强这些危险性高的工艺的生产管理,对容易引发事故的机械部位进行改进或防护,定期对设备进行检修和维护,加强员工的安全培训。
(4)机械加工过程中操作方法不当和缺乏必要的防护措施分别占事故原因的26%和14%,是引起事故的主要原因,因此,在生产过程中应严格按照操作规程操作,加强重点部位的防护,杜绝违章指挥、冒险操作现象的发生。
[科] 【参考文献】
[1]黄土宝.发电企业安全管理探讨[J].现代商贸工业,2009,(09).
[2]李鑫,李新予,王伟.论施工安全管理[J].科技信息,2009,(07).
[3]李瑞锋.浅谈施工安全管理[J].今日科苑,2009,(04).
[4]张东明,李慧谦.浅谈隧道施工的安全管理[J].山西建筑,2009,(01).。