第三章 MEMS制造技术-1(半导体工艺)
半导体技术的生产工艺新一代制造技术的发展和应用
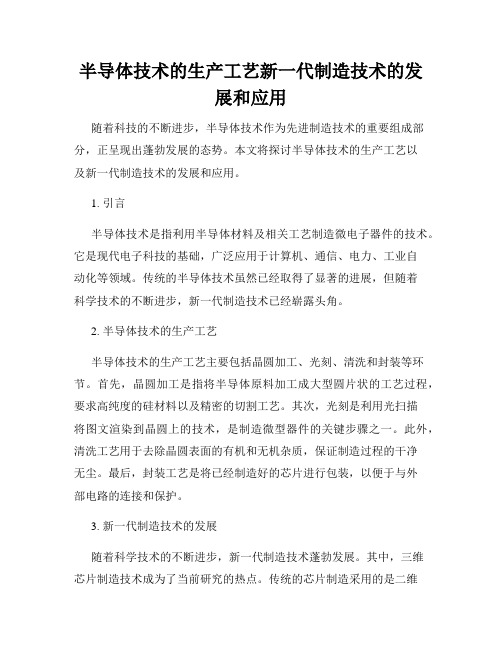
半导体技术的生产工艺新一代制造技术的发展和应用随着科技的不断进步,半导体技术作为先进制造技术的重要组成部分,正呈现出蓬勃发展的态势。
本文将探讨半导体技术的生产工艺以及新一代制造技术的发展和应用。
1. 引言半导体技术是指利用半导体材料及相关工艺制造微电子器件的技术。
它是现代电子科技的基础,广泛应用于计算机、通信、电力、工业自动化等领域。
传统的半导体技术虽然已经取得了显著的进展,但随着科学技术的不断进步,新一代制造技术已经崭露头角。
2. 半导体技术的生产工艺半导体技术的生产工艺主要包括晶圆加工、光刻、清洗和封装等环节。
首先,晶圆加工是指将半导体原料加工成大型圆片状的工艺过程,要求高纯度的硅材料以及精密的切割工艺。
其次,光刻是利用光扫描将图文渲染到晶圆上的技术,是制造微型器件的关键步骤之一。
此外,清洗工艺用于去除晶圆表面的有机和无机杂质,保证制造过程的干净无尘。
最后,封装工艺是将已经制造好的芯片进行包装,以便于与外部电路的连接和保护。
3. 新一代制造技术的发展随着科学技术的不断进步,新一代制造技术蓬勃发展。
其中,三维芯片制造技术成为了当前研究的热点。
传统的芯片制造采用的是二维平面结构,而三维芯片制造技术通过垂直堆叠多个晶圆,提高了芯片的集成度和性能。
这种技术不仅可以减小芯片的体积,还可以提高数据传输速度和功耗效率,对未来的电子产品发展具有重要意义。
此外,纳米技术也是新一代制造技术的重要方向。
纳米技术是指在纳米尺度上进行材料和器件的设计、制备和处理的技术。
通过纳米技术,可以制造出尺寸更小、性能更优的芯片和器件,极大地推动了半导体技术的发展。
例如,纳米结构的材料可以克服传统材料在导电、导热、光学等方面的限制,实现更高效的能量转化和传输。
4. 新一代制造技术的应用新一代制造技术不仅在计算机领域有着广泛的应用,还逐渐渗透到了其他行业。
例如,在医疗领域,新一代制造技术可以用于制造更小型、更精密的医疗器械和设备,提高手术的精确度和治疗的效果。
微机电系统(mems)工程技术 半导体制造工艺技术

微机电系统(mems)工程技术半导体制造工艺技术微机电系统(MEMS)是一种融合微电子技术、机械工艺和微纳米加工技术的新型技术,具有微小体积、高性能和低功耗等优点,被广泛应用于传感器、执行器、微机械系统等领域。
MEMS制造工艺技术作为其核心技术之一,在MEMS设备的设计、生产和测试过程中起着至关重要的作用。
一、MEMS制造工艺技术的基本原理MEMS制造工艺技术是利用微纳米加工技术对微电子元件进行加工,实现微小尺寸的器件。
其基本原理包括光刻、薄膜沉积、刻蚀、清洗和包装等步骤。
在制造过程中,需要考虑到器件的性能、成本和效率等因素,并采用不同的工艺流程进行处理。
二、MEMS制造工艺技术的工艺流程1.设计阶段:确定MEMS器件的功能和结构,并进行软件仿真和电路设计,制定完整的器件设计方案。
2.掩膜光刻:利用掩膜和紫外光曝光的技术,将器件的图形准确转移到光敏材料上,形成所需的图形。
3.薄膜沉积:采用物理气相沉积、化学气相沉积等技术,在衬底表面沉积一层或多层薄膜,用于制备MEMS器件的功能部件。
4.刻蚀工艺:采用干法或湿法刻蚀技术,将多余的材料去除,形成所需的器件结构。
5.清洗和检测:在制造过程中,需要对器件进行清洗和检测,确保器件的质量和性能。
6.包装封装:将制备好的器件封装在封装体中,保护器件免受外部环境的影响。
三、MEMS制造工艺技术的发展趋势1.纳米加工技术:随着纳米加工技术的发展,MEMS器件的尺寸将进一步减小,性能将得到显著提升。
2.多功能集成:未来的MEMS器件将具有多功能集成的特点,可以同时实现多种功能,提高器件的综合性能。
3.自组装技术:自组装技术的应用将使MEMS制造工艺更加灵活和高效,降低成本,提高生产效率。
4.高可靠性设计:随着MEMS器件在汽车、医疗等领域的广泛应用,高可靠性设计将成为MEMS制造工艺技术的重要发展方向。
四、结语MEMS制造工艺技术是一项复杂而重要的工艺技术,对MEMS器件的性能和质量起着决定性的作用。
mems工艺技术路线
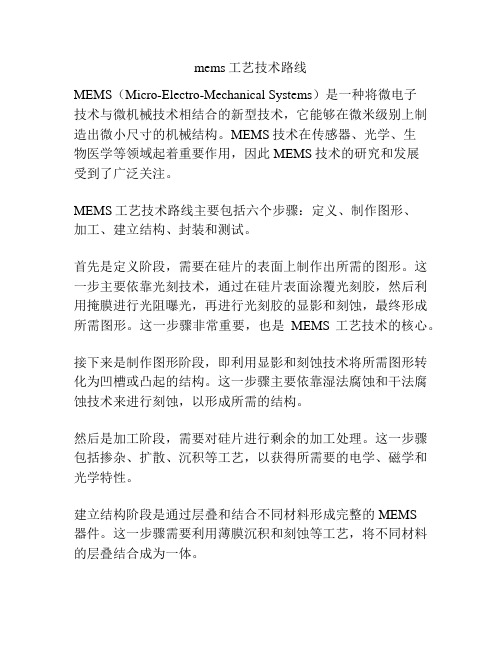
mems工艺技术路线MEMS(Micro-Electro-Mechanical Systems)是一种将微电子技术与微机械技术相结合的新型技术,它能够在微米级别上制造出微小尺寸的机械结构。
MEMS技术在传感器、光学、生物医学等领域起着重要作用,因此MEMS技术的研究和发展受到了广泛关注。
MEMS工艺技术路线主要包括六个步骤:定义、制作图形、加工、建立结构、封装和测试。
首先是定义阶段,需要在硅片的表面上制作出所需的图形。
这一步主要依靠光刻技术,通过在硅片表面涂覆光刻胶,然后利用掩膜进行光阻曝光,再进行光刻胶的显影和刻蚀,最终形成所需图形。
这一步骤非常重要,也是MEMS工艺技术的核心。
接下来是制作图形阶段,即利用显影和刻蚀技术将所需图形转化为凹槽或凸起的结构。
这一步骤主要依靠湿法腐蚀和干法腐蚀技术来进行刻蚀,以形成所需的结构。
然后是加工阶段,需要对硅片进行剩余的加工处理。
这一步骤包括掺杂、扩散、沉积等工艺,以获得所需要的电学、磁学和光学特性。
建立结构阶段是通过层叠和结合不同材料形成完整的MEMS器件。
这一步骤需要利用薄膜沉积和刻蚀等工艺,将不同材料的层叠结合成为一体。
封装是将MEMS器件封装到特定的封装中,保护器件并提供良好的电气和机械性能。
这一步骤主要包括背面研磨、切割、粘接等工艺。
最后是测试阶段,对制造好的MEMS器件进行各种测试。
这一步骤主要包括电学测试、机械测试、光学测试等,以确保器件的性能符合设计要求。
总的来说,MEMS工艺技术路线是一个复杂而精细的过程,需要运用各种微加工和微细结构制造技术。
这一技术路线的研究与发展为MEMS技术的进一步应用和推广提供了重要的支持。
同时,MEMS工艺技术路线也需要不断地进行改进和创新,以适应不断发展的科技需求。
MEMS的制造技术

具有的高选择性和物理腐蚀所具有的各向异性,目前 主要是将这两种方法组合起来使用。 4.2.2 (111)面自停止腐蚀技术 图4.16为(111)面自停止腐蚀工艺。其工艺流程为: 4.2.3 p-n结腐蚀自停止技术 p-n结腐蚀自停止是一种使用硅的各向异性腐蚀剂如氢 氧化钾的电化学腐蚀自停止技术,它利用了N型硅和P 型硅在各向异怀腐蚀液中的钝化电位不同这一现象。 图4.17给出了在氢氧化钾腐蚀液 (65℃,40%) 中 (100)晶向P型硅和N型硅样品的电流一电压特性。
图 4.23 X光过渡掩模板制造工艺流程图
(2) X光光刻胶
(3)同步辐射X光曝光 (4)光刻胶显影 4.3.3微电铸工艺 目前镍的微电铸工艺比较成熟,镍较稳定,且具有一定的硬度,可用于微复制模 具的制作。由于金是LIGA掩模板的阻挡层,所以,在LIGA技术中,金的微电铸技 术非常重要。有些传感器和执行器需要有磁性作为驱动力,所以,具有磁性的铁镍 合金的微电铸对LIGA技术也很重要。其他如银、铜等也是LIGA技术常用的金属材 料。
4.2.4电化学自停止腐蚀技术
图4.20是一种典型的电化学腐蚀自停止方法
图4.16 (111)面自停止腐蚀工艺
图4.17 P型和N型硅在KOH腐蚀液中的特性
图4.20 电化学腐蚀系统
图4.21 硅在5%HF中的电化学腐蚀I V
4.3 LIGA体微加工技术
四个工艺组成部分:LIGA掩模板制造工艺;X光 深层光刻工艺;微电铸工艺;微复制工艺。 4.3.1 LIGA掩膜板制造工艺
4.1.4.1 物理腐蚀技术 (1)离子腐蚀(Ion Etching ,IE)
图4.12平行板反应器的结构原理
(2)离子束腐蚀(Ion Beam Etching,IBE) 离子束腐蚀是一种利用惰性离子进行腐蚀的物理腐 蚀。在离子束腐蚀中,被腐蚀的衬底和产生离子的 等离子区在空间是分离的,如图4.13所示。
半导体工艺《半导体制造技术》答案
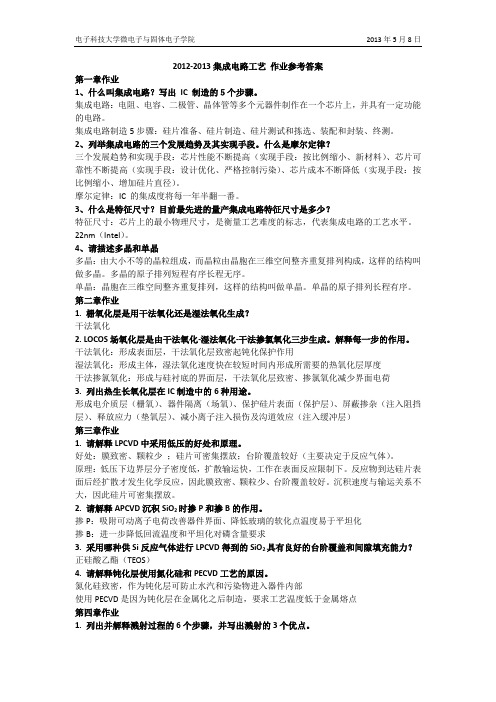
光刻 NMOS 管源漏区→NMOS 管源漏区磷注入
光刻 PMOS 管源漏区→PMOS 管源漏区硼注入
BPSG 沉积回流/增密
电子科技大学微电子与固体电子学院
2013 年 5 月 8 日
光刻接触孔BPSG 刻蚀
溅射 Si-Al-Cu→光刻金属互连刻蚀 Si-Al-Cu
该截面实际无压焊窗口,此图仅为示意,压焊窗口版图为一些亮区方块 SiO2 和 SiN 钝化层沉积→光刻压焊窗口→SiO2 和 SiN 刻蚀合金化退火 4. 什么是浅槽隔离 STI?(即简要描述浅槽隔离 STI) ,它取代了什么工艺? 浅槽隔离是在衬底上通过刻蚀槽、 氧化物填充及氧化物平坦化等步骤, 制作晶体管有源区之 间的隔离区的一种工艺。它取代了 LOCOS 隔离工艺。
N MAX 0.4 0.4 5 1015 cm2 9.7 1020 cm3 RP 207 A
exp t kT
x j RP RP 2 ln N MAX N B 582 A 207 A 2 ln 9.7 1020 cm 3 1016 cm 3 1574 A
电子科技大学微电子与固体电子学院
2013 年 5 月 8 日
步骤:等离子体形成、高能氩离子轰击金属靶材、金属原子溅射、金属原子输运、金属原子 沉积、尾气排出。 优点:台阶覆盖能力相对好、能沉积合金材料、能进行原位溅射刻蚀(反溅) 2. 列出集成电路金属互连对金属的 7 种要求。 电阻率低、电流密度高;粘附性好、接触电阻低;易于沉积、间隙填充好(大马士革) ;易 于刻蚀、易于平坦化(大马士革) ;抗温循性能好(延展性好) ;抗腐蚀性能好;抗应力性能 好。 3. 现代集成电路用铜互连取代铝互连的原因是什么?简要描述大马士革工艺的流程。 原因:铜电导率更低可以降低 RC 延迟;铜抗电迁移能力更好。 大马士革工艺流程:层间介质沉积和图形化、金属填隙、金属平坦化 CMP。 4. 列出硅化物的 3 个作用。 降低器件寄生电阻;降低接触电阻;作为金属与硅之间的粘合剂。 第五章作业 1. 请写出光刻的 8 个基本步骤 气相成底模、涂胶、软烘、对准和曝光、曝光后烘焙、显影、坚膜、显影后检查。 2. 请列出软烘的至少 2 个作用 去除溶剂从而: 改善胶的粘附性、 优化胶的光吸收特性和显影能力、 缓解涂胶时产生的应力、 防止曝光时挥发污染设备。 3. 已知接触孔版图图形为一些小方块,如果使用正胶,掩膜版应该是暗版还是亮版? 暗版。 接触孔处待刻蚀层材料应该去除, 因此不应被光刻胶覆盖, 因此该处光刻胶应曝光 (正胶) , 因此版图图形为透光部分,而其他部分为不透光部分,故为暗版。 4. 已知某台分步重复光刻机的紫外光源波长为 248nm、光学系统的数值孔径为 0.7、工艺 因子为 0.7,试计算该设备光刻的分辨率和焦深。 分辨率:R=kλ/NA=0.7*248nm/0.7=248nm 焦深:DOF=λ/2(NA)2=248nm/(2×0.72)=253nm 第六章作业 1. 为什么现代集成电路工艺多采用干法刻蚀? 干法刻蚀各向异性,可以实现图形精确转移。 2. 待刻蚀层厚度为 5000A,待刻蚀层与掩膜层选择比为 5:1,待刻蚀层与刻蚀终止层选择比 为 10:1,过刻蚀时间为 20%,请问需要掩膜层的最小厚度是多少?刻蚀终止层的刻蚀深度 是多少? 掩膜层厚度:5000A/(5:1)*(1+20%)=1200A 刻蚀终止层的刻蚀深度:5000A/(10:1)*20%=100A 3. 描述反应离子刻蚀的机理。 反应离子刻蚀属于物理和化学混合刻蚀。 ①进入真空反应室的刻蚀气体在射频电场的作用下分解电离形成等离子体, 等离子体由高能 电子、反应正离子、自由基、反应原子或原子团组成。 ②反应室被设计成射频电场垂直于被刻蚀样片表面且射频电源电极 (称为阴极) 的面积小于 接地电极(称为阳极)的面积时,在系统的电源电极上产生一个较大的自偏置电场。 ③等离子体中的反应正离子在自偏置电场中加速得到能量轰击样片表面, 这种离子轰击不仅 对样片表面有一定的溅射作用形成物理刻蚀, 而且提高了表面层自由基和反应原子或原子团 的化学活性,加速与样片的化学反应。 ④由于离子轰击的方向性,遭受离子轰击的底面比未遭受离子轰击的侧面的刻蚀要快得多,
微机电系统(mems)工艺基础与应用

微机电系统(mems)工艺基础与应用
微机电系统(MEMS)是指将微型机械元件、微电子元件、微光学元件、微流体元件及其它微加工技术相集成而成的系统。
它既是微电子技术、光学技术、力学技术、材料科学技术的综合,又是精密制造技术、微加工技术与传感器技术的相结合。
本文将对MEMS的工艺基础及其应用进行探讨。
一、MEMS的工艺基础 1.硅微加工技术 MEMS的制造材料主要是硅微电子材料及其它材料,硅微加工技术是MEMS 的核心技术。
硅微加工技术的主要工艺流程包括光刻、蚀刻、金属沉积、制膜、扩散、离子注入等。
2.压力传感器的制造工艺 MEMS的压力传感器主要采用压阻效应制作。
它的基本原理是利用极细硅悬臂梁作为传感器,在外界压力下悬臂梁弯曲,悬臂梁两端的电阻发生变化,进而反映出压力。
二、MEMS的应用 1.生物医学及生物传感技术应用MEMS技术制造的微型传感器,可以在细胞水平上检测微小的信号变化,诊断疾病、研究生物学行为。
2.汽车及工业应用汽车领域是MEMS技术的主要应用领域之一。
MEMS技术应用于汽车系统中,可以制造出精密的安全气囊、一个小孔的喷油嘴、传感器等元件。
3.消费市场在消费市场上,MEMS技术的应用范围同样广泛。
借助MEMS技术,可以生产出更小、更趋近于无形的产品,如MEMS振动器、MEMS加速计、MEMS麦克风。
总之,MEMS技术的应用范围和前景十分广阔,它在不断地为各个领域带来更多革命性的变革和新的想象空间。
同时,要想在MEMS领域取得更为显著的进展,需要更多的前沿科技、人才、资金等方面的支持和加速发展。
MEMS工艺(3半导体工艺)

掺杂的主要形式:注入和扩散
退火:也叫热处理,集成电路工艺中所有的在氮气等不
活泼气氛中进行的热处理过程都可以称为退火。
目的:激活杂质
消除损伤 结构释放后消除残余应力
退火方式:
炉退火 快速退火
1.扩散工艺
•定义:在一定温度下杂质原子具有一 定能量,能够克服阻力进入半导体并 在其中做缓慢的迁移运动。 •形式:替代式扩散和间隙式扩散
• 2.漏电电流大:表面沾污引起的表面漏电;氧化层的 缺陷破坏了氧化层在杂质扩散时的掩蔽作用和氧化层在 电路中的绝缘作用而导电;硅片的缺陷引起杂质扩散时 产生管道击穿。
• 3.薄层电阻偏差
• 4.器件特性异常:击穿电压异常;hFE异常;稳压二
极管稳压值异常。
。
工艺控制
• 污染控制:颗粒、有机物、薄膜、金属离子 • 污染来源:操作者,清洗过程,高温处理,工具 •• 参量控制:温度,时间,气体流量(影响最大?) • 1.温度控制:源温、硅片温度、升温降温、测温 •2.时间: 进舟出舟自动化, 试片 • 3.气体流量:流量稳定,可重复性,假片
离子注入
• 特点:横向效应小,但结深浅;杂质量可控;晶格缺陷多 • 基本原理:杂质原子经高能粒子轰击离子化后经电场加速轰击硅片表面,形成注入层 • 装置:离子源、聚焦、分析器、加速管、扫描、偏转、靶室、真空系统
离子注入系统的原理示意图
离子注入的步骤
注入的离子在基底中的分布
• 根据Ruska(1987),注入离子的浓度N(X)可遵循下面方程式
分类
• 普通热退火 • 硼的退火特性 • 磷的退火特性 • 扩散效应 • 快速退火
•方式:
•热退火:管式炉,保护气氛,900C, 20~30min,用于再扩散
MEMS工艺体硅微加工工艺

MEMS工艺体硅微加工工艺1. 简介MEMS(Micro-Electro-Mechanical Systems),即微电子机械系统,是一种集成了电子、机械和光学等技术的微型设备。
MEMS工艺体硅微加工工艺是MEMS制造中最常用的一种工艺。
本文将介绍MEMS工艺体硅微加工的基本原理、工序以及常见的应用领域。
2. 工艺原理MEMS工艺体硅微加工工艺以单晶硅片作为主要材料,通过一系列的加工工序,制造出具有复杂结构和微尺寸的器件。
其工艺原理主要包括以下几个方面:2.1 单晶硅片制备单晶硅片是MEMS工艺体硅微加工的基础材料。
通过化学气相沉积(CVD)或磁控溅射等方法,在硅熔体中生长出单晶硅片。
然后,通过切割和抛光等工艺,将单晶硅片制备成规定尺寸和厚度的硅衬底。
2.2 光刻工艺光刻工艺是MEMS工艺体硅微加工中的重要步骤。
首先,将光刻胶覆盖在硅片表面。
然后,使用掩膜板,通过紫外光照射,使光刻胶发生化学反应,形成图案。
接着,将硅片浸泡在显影液中,去除未曝光的光刻胶。
最后,通过加热或暴露于紫外光下,固化已经显影的光刻胶。
2.3 甜蜜刻蚀甜蜜刻蚀是MEMS工艺体硅微加工中的关键步骤。
将制备好的硅片放置在刻蚀室中,通过控制刻蚀气体的流量、温度和压力等参数,使硅片表面发生化学刻蚀。
根据刻蚀深度和刻蚀特性的要求,可以选择不同的刻蚀方法,如湿法刻蚀、干法刻蚀等。
2.4 互连与封装互连与封装是MEMS工艺体硅微加工的最后环节。
通过金属薄膜沉积、光刻和腐蚀等工艺,将金属导线、引线等结构制作在硅片上,并与芯片上的电极进行连接。
同时,为了保护MEMS器件免受机械损伤和环境腐蚀,常常需要对其进行封装,通常采用薄膜封装或微结构封装等方法。
3. 工序流程MEMS工艺体硅微加工的工序流程会因具体的器件设计和制造要求而有所差异。
下面是一个典型的MEMS工艺体硅微加工的工序流程:1.单晶硅制备:通过CVD或磁控溅射等方法,制备出单晶硅片。
(完整版)MEMS的主要工艺类型与流程

MEMS的主要工艺类型与流程(LIGA技术简介)目录〇、引言一、什么是MEMS技术1、MEMS的定义2、MEMS研究的历史3、MEMS技术的研究现状二、MEMS技术的主要工艺与流程1、体加工工艺2、硅表面微机械加工技术3、结合技术4、逐次加工三、LIGA技术、准LIGA技术、SLIGA技术1、LIGA技术是微细加工的一种新方法,它的典型工艺流程如上图所示。
2、与传统微细加工方法比,用LIGA技术进行超微细加工有如下特点:3、LIGA技术的应用与发展4、准LIGA技术5、多层光刻胶工艺在准LIGA工艺中的应用6、SLIGA技术四、MEMS技术的最新应用介绍五、参考文献六、课程心得〇、引言《微机电原理及制造工艺I》是一门自学课程,我们在王跃宗老师的指导下,以李德胜老师的书为主要参考,结合互联网和图书馆的资料,实践了自主学习一门课的过程。
本文是对一学期来所学内容的总结和报告。
由于我在课程中主讲LIGA技术一节,所以在报告中该部分内容将单列一章,以作详述。
一、什么是MEMS技术1、MEMS的概念MEMS即Micro-Electro-Mechanical System,它是以微电子、微机械及材料科学为基础,研究、设计、制造、具有特定功能的微型装置,包括微结构器件、微传感器、微执行器和微系统等。
一般认为,微电子机械系统通常指的是特征尺度大于1μm小于1nm,结合了电子和机械部件并用IC集成工艺加工的装置。
微机电系统是多种学科交叉融合具有战略意义的前沿高技术,是未来的主导产业之一。
MEMS技术自八十年代末开始受到世界各国的广泛重视,主要技术途径有三种,一是以美国为代表的以集成电路加工技术为基础的硅基微加工技术;二是以德国为代表发展起来的利用X射线深度光刻、微电铸、微铸塑的LIGA( Lithograph galvanfomung und abformug)技术,;三是以日本为代表发展的精密加工技术,如微细电火花EDM、超声波加工。
第三章-MEMS制造技术-1(半导体工艺)
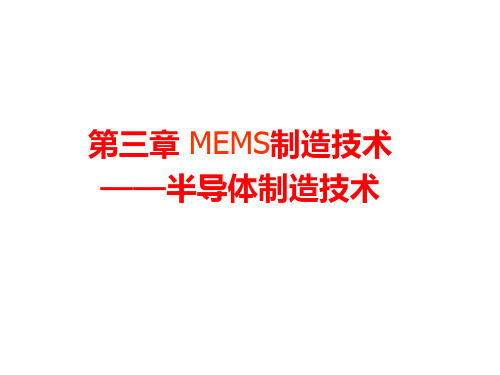
扩散的适用数学模型是Fick定律
N(x)
F D
x
式中:
F 为掺入量
D 为扩散率
N 每单位体积中掺入浓度
扩散方式
➢液态源扩散:利用保护气体携带杂质蒸汽进
入反应室,在高温下分解并与硅表面发生反
应,产生杂质原子,杂质原子向硅内部扩散
。
➢固态源扩散:固态源在高温下汽化、活化后
与硅表面反应,杂质分子进入硅表面并向内
蒸发、溅射等);厚度范围广,由几百埃至数
毫米。且能大量生产;
(4)淀积膜结构完整、致密,与衬底粘附性好。
常压化学气相淀积
特点:用于SiO2的淀积
➢◆ PWS-5000:
➢SiH4+O2=SiO2 +H2O
➢φ100mm:10片,φ125mm:8片
➢Time:15min
➢Temp:380~450℃±6℃
550~900℃ Si3N4 :30—80 高,晶片容量大 高淀积速率
多晶硅:30—80
掺杂或非掺杂氧
化物、氮化物、
晶体硅、钨
CVD
工艺
压强/温度
通常的淀积速
率10-10米/分
APCVD 100—10kPa SiO2:700
350~400℃
PECVD 0.2—5汞柱 Si3N4: 300—
300~400℃ 350
b)氧化层的形成
c)氧化层的生长
由颜色来确定氧化层厚度
氧化炉
2、化学气相淀积技术
➢ CVD:Chemical Vapor Deposition
➢ 定义:使用加热、等离子体和紫外线等各种能源,
使气态物质经化学反应(热解或化学合成),形成
固态物质淀积在衬底上。相对的蒸发和性好、台阶覆盖性
MEMS器件的制作方法及MEMS器件与流程

MEMS器件的制作方法及MEMS器件与流程什么是MEMS器件MEMS(Micro-Electro-Mechanical Systems)中文译作“微电子机械系统”,它是一种极小型、低功耗、高度集成的微机电器件,采用微电子加工工艺制作而成。
MEMS器件不仅具有微小体积和低功耗的特点,还具有高度的可靠性、可生产性和成本优势,广泛应用于惯性传感器、气体传感器、生物传感器、微泵、微阀、无线射频器等领域。
MEMS器件制作方法MEMS器件制作一般分为五个阶段:晶圆制备、表面处理、光刻、腐蚀和封装。
下面将对每个阶段进行详细阐述。
晶圆制备MEMS器件的制作通常采用硅晶圆为基板,晶圆制备是整个制作过程的第一步。
晶圆制备包括以下步骤:1.刺激掺杂(Doping):添加不同种类的杂原子到硅单晶中,控制晶体内部的电学性质,形成P型或N型材料。
2.清洗:将晶圆放入超纯水中清洗去除表面的污垢和残留物。
3.割晶:将大块硅单晶切割成薄片,保证晶格方向一致。
4.粗磨和细磨:对硅晶圆进行处理,使其表面平整。
5.氧化:在硅晶圆表面形成一层二氧化硅氧化膜,保护晶圆表面免受污染或损伤。
表面处理表面处理是指对硅晶圆表面进行化学或物理处理,以准备结构的定义。
常见的表面处理方式有以下几种:1.清洗:利用超纯水和有机溶液等清除表面的杂质,保持晶圆表面洁净。
2.烘烤:用于去除化学处理后的残垢和溶剂,一般在烘炉或烘箱中进行。
3.清除二氧化硅膜:通过化学腐蚀或刻蚀的方式去除晶圆上的二氧化硅膜。
光刻光刻是MEMS器件制作工艺中比较关键的一个步骤。
在这个步骤中,芯片表面被覆盖了一层称为光刻胶的物质。
光刻胶的化学性质使得其对紫外线具有不同的反应,晶圆上光学显微镜上方的掩膜被置于紫外线光源下方,向光刻胶中投射图形化学图案。
投射光的图形化学图案将使得光刻胶局部性质发生变化,然后进一步处理。
1.选择合适的掩膜2.涂覆光刻胶并旋转均匀3.热压辊使得光刻胶均匀压贴到硅晶上4.紫外线曝光5.开发6.检验腐蚀MEMS制造中的腐蚀是利用腐蚀性的化学液体来沿着在晶圆上部署的光刻图形剥去目标材料的步骤。
MEMS工艺1
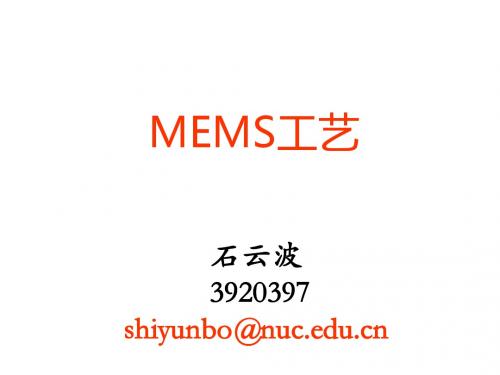
PACKAGE SEAL
FINAL TEST
采用特殊的检测和划 片工艺保护释放出来的机 械结构
封装时暴露部分零件
机、电系统 全面测试
集成电路:
Integrated Circuit,缩写IC
通过一系列特定的加工工艺,将晶体管、 二极管等有源器件和电阻、电容等无源 器件,按照一定的电路互连,“集成” 在一块半导体单晶片(如硅或砷化镓) 上,封装在一个外壳内,执行特定电路 或系统功能
MEMS工艺的基本概念
MEMS工艺的国内外情况及发展趋势
MEMS的国内外概况
MEMS发展历史回顾
1947年:发明晶体管--技术基础
压力传感器:
54年:Si、Ge压阻效应 66年:机械研磨做硅腔 70年:各向同性腐蚀硅腔 76年:KOH 腐蚀,MEMS加工 手段 80年代:集成式压力传感器 目前:新机理压力传感器
MEMS工艺
硅工艺
体硅工艺 表面工艺 两者结合
非硅工艺
LIGA工艺 DEM工艺 其他工艺:超精密加工、 非切削加工、特种加工 技术
MEMS与集成电路工艺的不同
集成电路与MEMS器件特点比较: 集成电路:薄膜工艺; 制作各种晶体管、电阻电容等 重视电参数的准确性和一致性 MEMS:工艺多样化 制作梁、隔膜、凹槽、孔、密封洞、锥、针尖、 弹簧及所构成的复杂机械结构 更重视材料的机械特性,特别是应力特性
(2) 微加速度计 微加速度计是微型惯性测量组合的关 键基础元件 汽车安全气囊系统:体积小、成本低、 集成化等特点
美国AD公司的ADXL 美国摩托罗拉公司批量生产汽车用 MMAS40G电容式微加速度计 美国EG&G IC
(3)微喷 基于MOEMS技术的微喷已成为MOEMS领 域的一种典型器件,它的应用涉及科学仪 器、工业控制以及生物医疗等多个领域, 目前主要的应用方向有喷墨打印、芯片冷 却、气流控制以及微推进系统,应用于药 物雾化供给的微喷研究也正在兴起。 喷墨打印机的喷墨打印头,年产值数亿美 元
《半导体制造技术》课程教学大纲
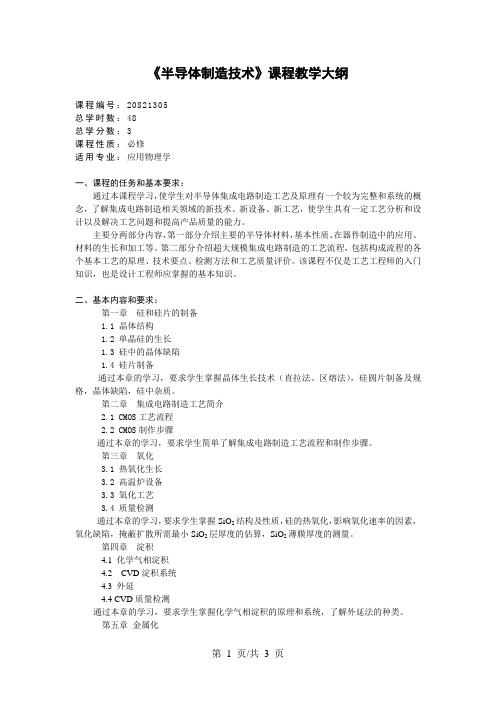
《半导体制造技术》课程教学大纲课程编号:20821305总学时数:48总学分数:3课程性质:必修适用专业:应用物理学一、课程的任务和基本要求:通过本课程学习,使学生对半导体集成电路制造工艺及原理有一个较为完整和系统的概念,了解集成电路制造相关领域的新技术、新设备、新工艺,使学生具有一定工艺分析和设计以及解决工艺问题和提高产品质量的能力。
主要分两部分内容,第一部分介绍主要的半导体材料,基本性质、在器件制造中的应用、材料的生长和加工等。
第二部分介绍超大规模集成电路制造的工艺流程,包括构成流程的各个基本工艺的原理、技术要点、检测方法和工艺质量评价。
该课程不仅是工艺工程师的入门知识,也是设计工程师应掌握的基本知识。
二、基本内容和要求:第一章硅和硅片的制备1.1 晶体结构1.2 单晶硅的生长1.3 硅中的晶体缺陷1.4 硅片制备通过本章的学习,要求学生掌握晶体生长技术(直拉法、区熔法),硅圆片制备及规格,晶体缺陷,硅中杂质。
第二章集成电路制造工艺简介2.1 CMOS工艺流程2.2 CMOS制作步骤通过本章的学习,要求学生简单了解集成电路制造工艺流程和制作步骤。
第三章氧化3.1 热氧化生长3.2 高温炉设备3.3 氧化工艺3.4 质量检测通过本章的学习,要求学生掌握SiO2结构及性质,硅的热氧化,影响氧化速率的因素,氧化缺陷,掩蔽扩散所需最小SiO2层厚度的估算,SiO2薄膜厚度的测量。
第四章淀积4.1 化学气相淀积4.2 CVD淀积系统4.3 外延4.4 CVD质量检测通过本章的学习,要求学生掌握化学气相淀积的原理和系统,了解外延法的种类。
第五章金属化5.1 金属淀积系统5.2 金属化方案通过本章的学习,要求学生掌握金属化的原理和系统。
第六章光刻6.1 光刻工艺简介6.2 旋转涂胶6.3 前烘6.4 对准和曝光6.5 显影和坚膜通过本章的学习,要求学生掌握光刻工艺流程,光刻缺陷控制及检测,光刻技术分类(光学光刻,非光学光刻),了解最新的光刻工艺技术动态。
MEMS的主要工艺类型与流程

MEMS的主要工艺类型与流程(LIGA技术简介)目录〇、引言一、什么是MEMS技术1、MEMS的定义2、MEMS研究的历史3、MEMS技术的研究现状二、MEMS技术的主要工艺与流程1、体加工工艺2、硅表面微机械加工技术3、结合技术4、逐次加工三、LIGA技术、准LIGA技术、SLIGA技术1、LIGA技术是微细加工的一种新方法,它的典型工艺流程如上图所示。
2、与传统微细加工方法比,用LIGA技术进行超微细加工有如下特点:3、LIGA技术的应用与发展4、准LIGA技术5、多层光刻胶工艺在准LIGA工艺中的应用6、SLIGA技术四、MEMS技术的最新应用介绍五、参考文献六、课程心得〇、引言《微机电原理及制造工艺I》是一门自学课程,我们在王跃宗老师的指导下,以李德胜老师的书为主要参考,结合互联网和图书馆的资料,实践了自主学习一门课的过程。
本文是对一学期来所学内容的总结和报告。
由于我在课程中主讲LIGA技术一节,所以在报告中该部分内容将单列一章,以作详述。
一、什么是MEMS技术1、MEMS的概念MEMS即Micro-Electro-Mechanical System,它是以微电子、微机械及材料科学为基础,研究、设计、制造、具有特定功能的微型装置,包括微结构器件、微传感器、微执行器和微系统等。
一般认为,微电子机械系统通常指的是特征尺度大于1μm小于1nm,结合了电子和机械部件并用IC集成工艺加工的装置。
微机电系统是多种学科交叉融合具有战略意义的前沿高技术,是未来的主导产业之一。
MEMS技术自八十年代末开始受到世界各国的广泛重视,主要技术途径有三种,一是以美国为代表的以集成电路加工技术为基础的硅基微加工技术;二是以德国为代表发展起来的利用X射线深度光刻、微电铸、微铸塑的LIGA(Lithograph galvanfomung und abformug)技术,;三是以日本为代表发展的精密加工技术,如微细电火花EDM、超声波加工。
mems微镜制造工艺
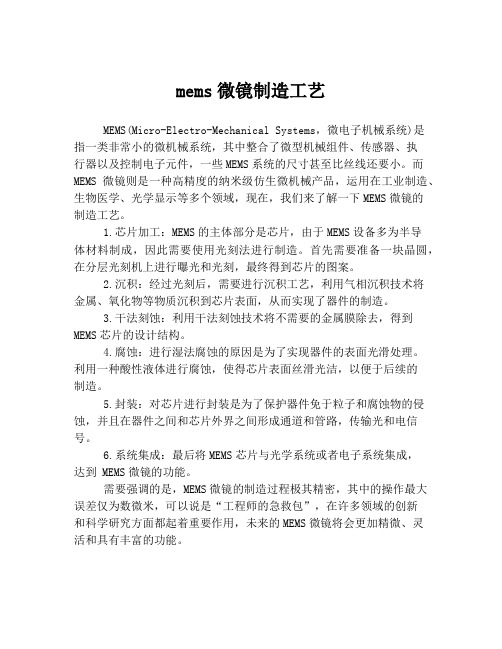
mems微镜制造工艺
MEMS(Micro-Electro-Mechanical Systems,微电子机械系统)是
指一类非常小的微机械系统,其中整合了微型机械组件、传感器、执
行器以及控制电子元件,一些MEMS系统的尺寸甚至比丝线还要小。
而MEMS微镜则是一种高精度的纳米级仿生微机械产品,运用在工业制造、生物医学、光学显示等多个领域,现在,我们来了解一下MEMS微镜的
制造工艺。
1.芯片加工:MEMS的主体部分是芯片,由于MEMS设备多为半导
体材料制成,因此需要使用光刻法进行制造。
首先需要准备一块晶圆,在分层光刻机上进行曝光和光刻,最终得到芯片的图案。
2.沉积:经过光刻后,需要进行沉积工艺,利用气相沉积技术将
金属、氧化物等物质沉积到芯片表面,从而实现了器件的制造。
3.干法刻蚀:利用干法刻蚀技术将不需要的金属膜除去,得到MEMS芯片的设计结构。
4.腐蚀:进行湿法腐蚀的原因是为了实现器件的表面光滑处理。
利用一种酸性液体进行腐蚀,使得芯片表面丝滑光洁,以便于后续的
制造。
5.封装:对芯片进行封装是为了保护器件免于粒子和腐蚀物的侵蚀,并且在器件之间和芯片外界之间形成通道和管路,传输光和电信号。
6.系统集成:最后将MEMS芯片与光学系统或者电子系统集成,
达到 MEMS微镜的功能。
需要强调的是,MEMS微镜的制造过程极其精密,其中的操作最大误差仅为数微米,可以说是“工程师的急救包”,在许多领域的创新
和科学研究方面都起着重要作用,未来的MEMS微镜将会更加精微、灵
活和具有丰富的功能。
MEMS制造技术
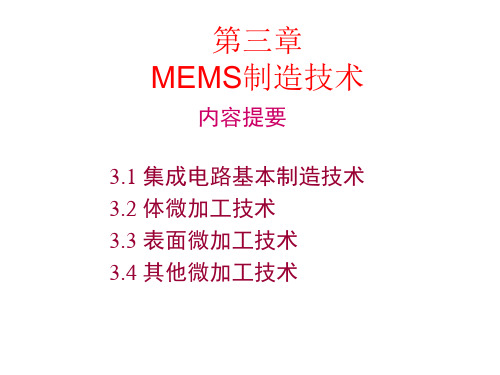
化学腐蚀技术 化学腐蚀高选择性+物理腐蚀所具有的各向异性
(1)等离子体腐蚀(Plasma Etcing, PE) (2)反应离子腐蚀(Reactive Ion Etching,,RIE) (3)反应离子束腐蚀
总结
CH3COOH=CH3COO-+H+
湿法刻蚀
各向同性湿法刻蚀
– 二倍刻蚀速率 – 与刻蚀剂成分比例有关 – 与晶向有关
湿法刻蚀
各向同性湿法刻蚀
– 保护层 (Passivation layer)
• SiN 和Au基本不刻蚀 • 热生长SiO2 刻蚀速度 30-80 nm/min, 慢100x • Al 刻蚀极快 • 正胶可以短时使用
硅各向同性腐蚀最常用的腐蚀液为HF-HNO3加水或 者乙酸系统(通常称为HNA系统) ,其刻蚀机理:
硝酸硅发生氧化反应生成二氧化硅,然后由HF将 二氧化硅溶解 Si+HNO3+HF=H2SiF6+HNO2+H2O+H2
水和乙酸(CH3COOH)通常作为稀释剂,在HNO3 溶液中,HNO3几乎全部电离,因此H+浓度较高,而 CH3COOH是弱酸,电离度较小,它的电离反应为
表面微加工 (Surface micromachining)
• 集成电路技术 • 牺牲层技术 (Sacrificial layer )
键合 (Bonding) LIGA 软光刻技术(Soft Lithography)
典型MEMS制造方法
2 MEMS光刻
深槽光刻 厚胶光刻 双面光刻
深槽光刻
• 版图设计时进行部分补偿
厚胶光刻
• 厚胶应用
– 集成电路光刻胶层厚度1 μm – MEMS中光刻胶层厚度1 μm -1mm
半导体微系统制造技术

半导体微系统制造技术随着科技的不断发展,半导体微系统已经成为现代电子设备中不可或缺的一部分。
它们广泛应用于通信、计算、传感器、医疗和能源等领域,为人们的生活带来了诸多便利。
而在半导体微系统的制造过程中,半导体微系统制造技术的发展起到了至关重要的作用。
半导体微系统制造技术是指将微电子器件与微机械系统相结合,通过制造工艺将它们集成到同一个芯片上的过程。
这项技术的关键在于精确的制造工艺和材料选择,以及高度的集成度和可靠性要求。
半导体微系统的制造过程通常从硅基底开始。
硅材料是制造半导体微系统的常用材料,因为它具有良好的电学特性和机械强度。
制造过程中,首先需要将硅片进行清洗和抛光,以确保表面的光滑度和纯净度。
然后,利用光刻技术将设计的图案转移到硅片上,形成微电子器件的结构。
制造微机械系统的关键在于微加工技术。
微加工技术是一种将微米级结构制造到硅片上的技术,常用的方法包括湿法腐蚀、干法腐蚀、离子刻蚀等。
这些方法可以实现对硅片的加工,形成微机械系统的各种结构,如微阀、微泵、微传感器等。
半导体微系统制造技术还需要进行封装和测试。
封装是将制造好的芯片封装到外部包装中,以保护芯片免受外界环境的影响。
测试是对芯片进行功能性能和可靠性的测试,以确保芯片的质量和性能符合设计要求。
半导体微系统制造技术的发展带来了许多创新和应用。
例如,微电子器件的小型化和集成度的提高,使得电子设备更加轻薄和便携。
微机械系统的发展使得传感器和执行器的性能得到了大幅提升,广泛应用于汽车、医疗、工业等领域。
然而,半导体微系统制造技术也面临着一些挑战和难题。
首先,制造过程中需要高度准确的控制和监测,以确保微米级结构的制造精度和一致性。
其次,材料选择和制造工艺的优化需要大量的研究和实验。
同时,成本和可扩展性也是制约半导体微系统制造技术发展的因素之一。
总结起来,半导体微系统制造技术是一项关键的技术,对现代电子设备的发展和应用具有重要意义。
通过精确的制造工艺和材料选择,半导体微系统制造技术可以实现微电子器件和微机械系统的高度集成,为人们的生活带来更多的便利和创新。
- 1、下载文档前请自行甄别文档内容的完整性,平台不提供额外的编辑、内容补充、找答案等附加服务。
- 2、"仅部分预览"的文档,不可在线预览部分如存在完整性等问题,可反馈申请退款(可完整预览的文档不适用该条件!)。
- 3、如文档侵犯您的权益,请联系客服反馈,我们会尽快为您处理(人工客服工作时间:9:00-18:30)。
扩散工艺主要参数
结深:当用与衬底导电类型相反的杂质 进行扩散时,在硅片内扩散杂质浓度与 衬底原有杂质浓度相等的地方就形成了 pn结,结距扩散表面的距离叫结深。 薄层电阻Rs(方块电阻)
表面浓度:扩散层表面的杂质浓度。
较低的衬底温度 快、好的附着性
易受化学 污染
在金属上和钝 化物的低温绝 缘体
3.外延沉积
概念:
在单晶体基底生长同样单晶体材料的薄膜
特点:
生长的外延层能与衬底保持相同的晶向
外延速率可控制更加精确
利用外延层可以有效控制准三维结构深度
微电子工业中有几种技术可用于外延沉积
第三章 MEMS制造技术 ——半导体制造技术
主要内容
掺杂技术、退火技术 表面薄膜制造技术 光刻技术 金属化技术 刻蚀技术 净化与清洗 接触与互连 键合、装配和封装
集成电路制造过程
一、 掺杂与退火
掺杂定义:就是用人为的方法,将所需的杂
质(如磷、硼等),以一定的方式掺入到半 导体基片规定的区域内,并达到规定的数量 和符合要求的分布,以达到改变材料电学性 质、制作PN结、集成电路的电阻器、互联线
的目的。
掺杂的主要形式:注入和扩散
退火:也叫热处理,集成电路工艺中所有的在氮气等不
活泼气氛中进行的热处理过程都可以称为退火。
目的:激活杂质
消除损伤
结构释放后消除残余应力
退火方式:
炉退火 快速退火
1.扩散工艺 定义:在一定温度下杂质原子具有一 定能量,能够克服阻力进入半导体并 在其中做缓慢的迁移运动。
O2
干氧氧化:Si+O2 SiO2
干氧典型速度:1200oC,50min,180nm
H2O
湿氧氧化:Si+H2O SiO2 H2
二氧化硅膜的五种用途: ������ ������ ������ ������ ������ 杂质扩散掩蔽膜a 器件表面保护或钝化膜b 电路隔离介质或绝缘介质c 电容介质材料d MOS管的绝缘栅材料e
ΔRP为分散度或者“离散度”
Q是离子束的剂量(原子数/cm2)
硅中常用掺杂剂的离子注入
离子 范围 Rp,nm 分散 Rp,nm
在30keV 能级 硼(B)
磷(P) 砷(As) 在100 keV 能级 硼(B) 307.0 69.0
106.5
42.0 23.3
39.0
19.5 9.0
磷(P) 砷(As)
液态源扩散
磷P
扩散源:POCl3,PCl3,PBr3等 扩散原理:三氯氧磷600C分解后与硅反应, 在硅片表面形成磷硅玻璃,磷原子继续向内 部扩散,形成扩散层。
扩散系统:O2和N2气源、纯化、扩散源、源冷 却系统、扩散炉 扩散工艺:预沉积,去PSG,再分布
固态源扩散 箱法B扩散
B2O3或BN源,石英密封箱
常用CVD
常压冷壁:(APCVD)
用于生长掺杂与不掺杂的二氧化硅
低压热壁:(LPCVD)
用于生长多晶硅与氮化硅
等离子体激活(PECVD)
可以降低反应所需温度,常用于生长氮化 硅,作最后钝化层使用
CVD中的化学反应
常用三种薄膜的化学反应:
二氧化硅
氮化硅
多晶硅
CVD工艺特点:
(1)CVD成膜温度远低于体材料的熔点或软点。 因此减轻了衬底片的热形变,减少了玷污,抑 制了缺陷生成; 设备简单,重复性好;
扩散与注入的特点
扩散
工艺温度: 横向扩散: 晶格损伤: 工艺自由度: 工艺成本: 高温 大 小 低 低
注入
常温
浓度和分布控制: 较精确
精确
小 大 高 高
二、表面薄膜技术
在IC及MEMS加工技术中,有时候需要在 由不同材料构成的大面积的薄膜层中构造 功能完善的结构。
功能:结构层、牺牲层、钝化保护、刻蚀掩蔽、 键合连接、电气连接、光学传输等 方式:氧化(Oxidation)、淀积(Deposition)、外延 (Epitaxy)、电镀(Electroplating)
C-V性能检测
在硅基上产生二氧化硅最经济的方法就 是热氧化。此工艺中的化学反应如下:
二氧化硅的热氧化设备
a)氧化初始阶段
b)氧化层的形成
c)氧化层的生长
由颜色来确定氧化层厚度
氧化炉
2、化学气相淀积技术
CVD:Chemical Vapor Deposition
定义:使用加热、等离子体和紫外线等各种能源, 使气态物质经化学反应(热解或化学合成),形 成固态物质淀积在衬底上。相对的蒸发和溅射为 物理气相淀积。
薄膜定义:
“薄”——厚度很薄,一般尺度在亚微米到十 微米左右
决定了其制备工艺控制精度 决定了其制造工艺的方法 决定了其必须附着于支撑
“膜”——在很大面积(整个表面)上连续分 布,除非有意加工,不存在断裂不连续区域。 “多孔薄膜”,有孔,但仍然连续
薄膜的制备——氧化
定义:硅与氧化剂反应生成二氧化硅。 原理:氧化剂被表面吸附,向膜中扩散,在二氧化 硅和硅的接触界面反应生成新的二氧化硅,接触界 面向深层逐步推进。
基本原理:杂质原子经高能粒子轰击离子化 后经电场加速轰击硅片表面,形成注入层 装臵:离子源、聚焦、分析器、加速管、扫 描、偏转、靶室、真空系统
离子注入系统的原理示意图
离子注入的步骤
注入的离子在基底中的分布
根据Ruska(1987),注入离子的浓度N(X) 可遵循下面方程式
RP 为注入的范围,um
Si3N4: SiH2Cl2 +NH3������
PSG: SiH4 +PH3 +O2 ������
三种主要CVD工序的总结和比较
CVD 工艺 压强/温度 通常的淀积速 率10-10米/分 优点 简单、高速、 低温 缺点
覆盖度较差 微粒污染
应用
掺杂或非掺杂 氧化物
掺杂或非掺杂氧 化物、氮化物、 晶体硅、钨
(2)薄膜的成分精确可控、配比范围大; (3)淀积速率一般高于PVD(物理气相淀积,如 蒸发、溅射等);厚度范围广,由几百埃至数 毫米。且能大量生产; (4)淀积膜结构完整、致密,与衬底粘附性好。
常压化学气相淀积
特点:用于SiO2的淀积
◆ PWS-5000: SiH4+O2=SiO2 +H2O φ100mm:10片,φ125mm:8片 Time:15min Temp:380~450℃±6℃ 厚度均匀:< ±5%
• 掺杂深度由注入杂质离子的能量和质量决定
• 掺杂浓度由注入杂质掺杂的均匀性好 温度低:小于600℃
可以精确控制杂质分布
可以注入各种各样的元素
横向扩展比扩散要小得多
可以对化合物半导体进行掺杂
离子注入
特点:横向效应小,但结深浅;杂质量可控; 晶格缺陷多
光刻胶粘附性好,但氧化速度慢。
湿氧:速度快,但二氧化硅疏松,与光刻胶粘 附性不好,易脱落。 实际工作中,往往用干氧、湿氧、干氧的方法, 速度快粘附性好。
水汽氧化速度更快,但是质量差,一般不用。
常压氧化技术
设备:
氧化源、加热器、氧化炉、热电偶
氧化效果分析
厚度检测:比色法、干涉法
针孔检测:腐蚀法、电化学法
二氧化硅膜的性质(2)
3. 二氧化硅膜的绝缘性质 热击穿、电击穿、混合击穿:
a.最小击穿电场(非本征)--针孔、裂缝、杂质。
b.最大击穿电场(本征)--厚度、导热、界面态电荷等;
氧化层越薄、击穿电场越低。
介电常数3~~4(3.9)
常压氧化技术
种类:水汽氧化、干氧氧化、湿氧氧化 干氧:二氧化硅膜干燥致密,掩蔽能力强,与
扩散的适用数学模型是Fick定律
式中:
F 为掺入量 D 为扩散率 N 每单位体积中掺入浓度
扩散方式
液态源扩散:利用保护气体携带杂质蒸汽进 入反应室,在高温下分解并与硅表面发生反 应,产生杂质原子,杂质原子向硅内部扩散。
固态源扩散:固态源在高温下汽化、活化后 与硅表面反应,杂质分子进入硅表面并向内 部扩散。
液态源扩散
硼B
扩散源:硼酸三甲酯,硼酸三丙酯等
扩散原理:硼酸三甲酯500C分解后与硅反 应,在硅片表面形成硼硅玻璃,硼原子继 续向内部扩散,形成扩散层。
扩散系统:N2气源、纯化、扩散源、 扩散炉 扩散工艺:预沉积,去BSG,再分布 工艺条件对扩散结果的影响
气体流量、杂质源、温度
APCVD 100—10kPa SiO2:700 350~400℃
LPCVD 1—8汞柱℃ SiO2:50—180 纯度高和均匀性 温度高 550~900℃ Si3N4 :30—80 高,晶片容量大 高淀积速率 多晶硅:30—80
PECVD 0.2—5汞柱 Si3N4: 300— 300~400℃ 350
形式:替代式扩散和间隙式扩散
恒定表面浓度扩散和再分布扩散
替位式扩散:杂质离子占据硅原子的位:
Ⅲ、Ⅴ族元素 一般要在很高的温度(950~1280℃)下进行 磷、硼、砷等在二氧化硅层中的扩散系数均 远小于在硅中的扩散系数,可以利用氧化层 作为杂质扩散的掩蔽层
间隙式扩散:杂质离子位于晶格间隙:
工艺控制
污染控制:颗粒、有机物、薄膜、金属离子 污染来源:操作者,清洗过程,高温处理,工具
参量控制:温度,时间,气体流量(影响最大?)
1.温度控制:源温、硅片温度、升温降温、测温 2.时间: 进舟出舟自动化, 试片 3.气体流量:流量稳定,可重复性
2.离子注入
• 定义:将掺杂剂通过离子注入机的离化、加 速和质量分析,成为一束由所需杂质离子组 成的高能离子流而投射入晶片(俗称靶)内 部,并通过逐点扫描完成整块晶片的注入