煤直接液化残渣热解气体析出规律研究_常松
煤直接液化残渣溶剂萃取组分的热解行为研究
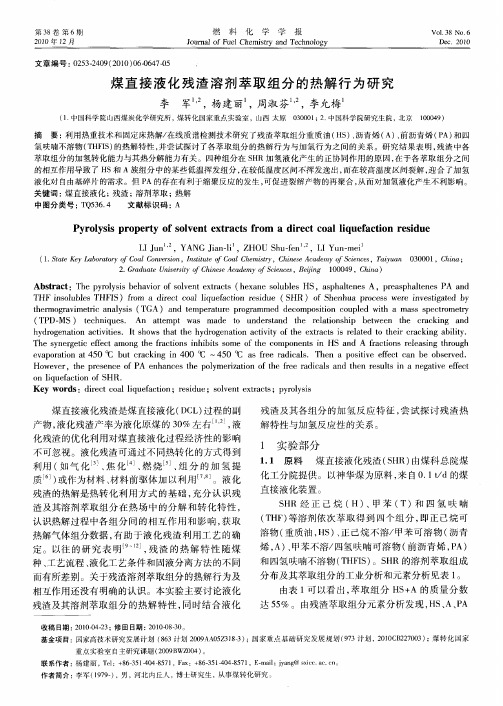
第3 8卷 第 6期
21 0 0年 1 2月
燃
料
化
学
学
报
Vo . 8 No 1 3 6 De . 2 1 c 00
J r a fFu lChe sr n c o o ou lo e n mity a d Te hn l gy
文 章 编 号 : 2320 (0 0 0 - 4 -5 0 5 —49 2 1 )60 70 6
煤 直 接 液 化 残 渣 溶 剂 萃 取 组 分 的 热 解 行 为 研 究
李 军 ,杨建丽 ,周淑芬 ,李允梅
(. 1 中国 科 学 院 山西 煤 炭 化 学研 究 所 , 转 化 国家 重 点 实 验室 பைடு நூலகம்山 西 太 原 煤 000 ; . 3 0 1 2 中国 科 学 院研 究 生 院 , 京 北 104 ) 0 09
中 图分 类 号 : Q 3 . T 5 64 文献标识码 : A
Py o y i o e t fs l e te t a t r m i e tc a i e a to e i e r l ss pr p r y o o v n x r c s f o a d r c o ll qu f c i n r sdu
煤直接液化残渣快速热解半焦特性的研究
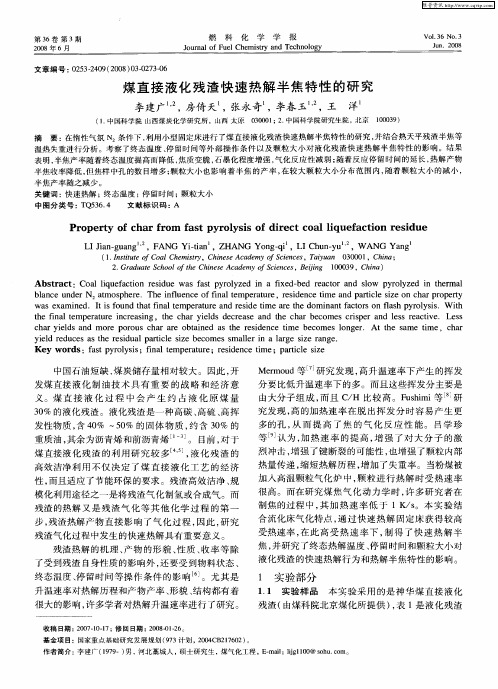
b a c n e ,a m o ph r . Th n u n e o n lt m p r t r l n e u d rN t s ee e i f e c ff a e l i e au e.r sd n e tme a d p ril ie o h rp o e t e i e c i n a tce sz n c a r p ry wa x mi e s e a n d. I sf un h tfn lt m p r tr n e i e t e a e t o i a tf c o son fa h p r yss ti o d t a a e i e au e a d r sd i r he d m n n a t r s y ol i .W ih m l t
c r e d n o e p r u h e o t i e s t e r sd n e tm e be o e on e . Att a e tm e. c a ha yil sa d m r o o s c a a b a n d a h e i e c i c m s 1 g r r r he s m i h r y ed r d c sa h e i u lp ril i e b c m e m alri a ge sz a g . il e u e st e r sd a atc e sz e o s s le n a 1 r ie r n e
煤直接液化残渣的性质及利用现状_谷小会
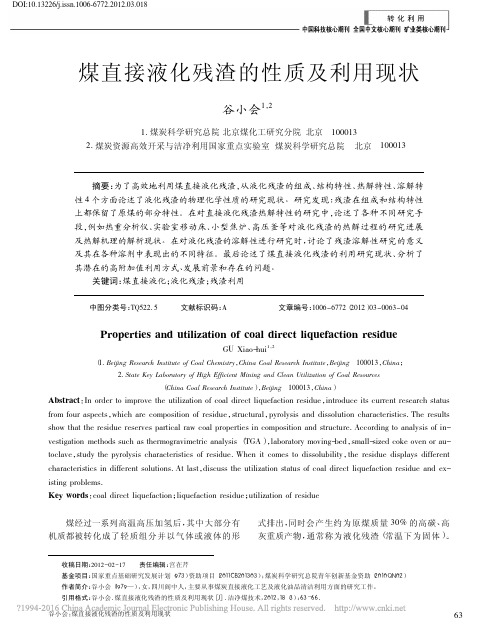
关键词:煤直接液化; 液化残渣; 残渣利用
中图分类号:TQ522. 5
文献标识码:A
文章编号:1006-6772( 2012) 03-0063-04
Properties and utilization of coal direct liquefaction residue
GU Xiao-hui1,2
尽管煤的性质、液化工艺条件对直接液化残渣 的组成和结构有很大影响,但是由于直接液化残渣 中的有机质通常被分为 3 个部分———残油、沥青烯 和前沥青烯,所以液化残渣都具有如下特点: ①残 油部分由分子量较低,分子结构相对简单的饱和或 部分饱和的脂肪烃和芳香烃组成,如烷烃、环烷烃、 氢化芳香烃等; ②沥青烯部分是以缩合芳香结构或 部分加氢饱和的氢化芳香结构为主体的复杂的芳
Abstract: In order to improve the utilization of coal direct liquefaction residue,introduce its current research status from four aspects,which are composition of residue,structural,pyrolysis and dissolution characteristics. The results show that the residue reserves partical raw coal properties in composition and structure. According to analysis of investigation methods such as thermogravimetric analysis ( TGA) ,laboratory moving-bed,small-sized coke oven or autoclave,study the pyrolysis characteristics of residue. When it comes to dissolubility,the residue displays different characteristics in different solutions. At last,discuss the utilization status of coal direct liquefaction residue and existing problems. Key words: coal direct liquefaction; liquefaction residue; utilization of residue
煤热解过程中气态产物分布的研究

煤热解过程中气态产物分布的研究煤热解是将煤分解为气态产物的一种工艺,是生产各种化工产品的重要原料。
煤热解过程中气态产物的分布具有重要的影响,因此研究煤热解过程中气态产物分布的规律是十分必要的。
煤热解过程中的气态产物主要有碳氢化合物、氮气、硫氧化物等。
其中,碳氢化合物是煤热解的主要产物,包括烷基烃、芳烃和芳香族化合物等。
氮气是煤热解过程中的副产物,主要来源于煤中的氮元素。
硫氧化物是煤热解过程中的污染物,主要来源于煤中的硫元素。
研究发现,煤热解过程中气态产物的分布与煤的种类、煤的质量分数和煤热解条件有关。
例如,在较低的温度和较低的氧浓度条件下,煤热解产生的气态产物中碳氢化合物的含量较高,而氮气和硫氧化物的含量较低。
而在较高的温度和较高的氧浓度条件下,煤热解产生的气态产物中碳氢化合物的含量较低,而氮气和硫氧化物的含量较高。
此外,煤的种类也会影响煤热解过程中气态产物的分布。
例如,较低热值的煤在煤热解过程中产生的碳氢化合物含量较高,而较高热值的煤在煤热解过程中产生的碳氢化合物含量较低。
此外,煤的质量分数也会影响煤热解过程中气态产物的分布。
例如,煤中灰分质量分数较高时,煤热解过程中产生的碳氢化合物含量较低,而氮气和硫氧化物的含量较高。
这是因为灰分中含有大量的氧元素,在煤热解过程中会与煤中的碳元素反应,从而降低煤热解产生的碳氢化合物含量,提高氮气和硫氧化物的含量。
综上所述,煤热解过程中气态产物的分布受煤的种类、煤的质量分数和煤热解条件的影响。
研究煤热解过程中气态产物分布的规律有助于优化煤热解工艺,提高煤热解的效率和产率,降低煤热解过程中的污染物排放。
在实际应用中,可以通过改变煤热解条件,如温度、氧浓度等,来调节煤热解过程中气态产物的分布。
例如,在生产甲醇的煤热解工艺中,可以通过提高温度和氧浓度来增加甲醇的产率。
而在生产焦炭的煤热解工艺中,则可以通过降低温度和氧浓度来增加焦炭的产率。
总的来说,研究煤热解过程中气态产物分布的规律是十分必要的,有助于优化煤热解工艺,提高煤热解的效率和产率,降低煤热解过程中的污染物排放。
煤直接液化残渣热解过程气体产物的析出
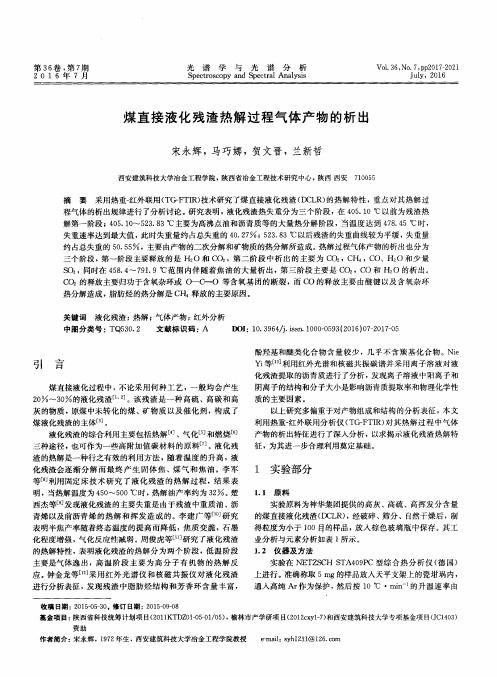
酚羟基和醚类化 合物 含量 较少 ,几 乎不含羰 基化 合物 。Nie Yi等_13]利用红外光谱 和核磁共 振碳谱并 采用离子溶 液对液 化残渣提取 的沥青质进行 了分析 ,发现离子溶 液中阳离子和 阴离子的结构和分子大小是影响沥青质提取率和物理化学性 质的主要 因素 。
以上研究多偏重于对产物组成和结构 的分析表征 ,本文 利用热重一红外联用分析仪 (TG-FTIR)对其热解 过程 中气体 产物的析 出特征进行了深入分析 ,以求揭示液化 残渣 热解特 征 ,为其进一步合理利用奠定基础 。
西安建筑科技大学冶金工程学 院,陕西省冶金工程技术研究 中心 ,陕西 西安 710055
摘 要 采用热重一红外联用 (TG-FTIR)技术研 究了煤直接液 化残渣 (DCLR)的热解 特性 ,重 点对其热解 过 程气体 的析 出规律进 行了分析讨论 。研究 表明 ,液化残渣热失 重分为三个 阶段 ,在 405.10℃ 以前 为残 渣热 解第一 阶段 ;405.10 ̄523.83℃主要为高沸点油和沥青质 等的大量热 分解 阶段 ,当温度 达到 478.45℃ 时, 失重速 率达 到最 大值 ,此时失重量约 占总失重 的 4O.27 ;523.83℃ 以后残渣 的失重曲线较为平 缓 ,失重量 约 占总失重 的 5O.55%,主要 由产物的二次分解和矿物质的热分解所造成 。热解过程气体产物 的析 出也 分为 三个 阶段 ,第一阶段主要释放 的是 Hz0 和 COz,第 二 阶段 中析 出的 主要 为 CO2,CH ,CO、HzO和少 量 S02,同时在 458.4~791.9℃范 围内伴随着 焦油 的大量析 出 ,第 三 阶段 主要是 CO2,CO 和 Hz0 的析 出。 CO2的释放 主要 归功于含氧杂环或 0一c===0 等含氧基 团的断裂 ,而 CO 的释放 主要 由醚键 以及 含氧杂环 热分解造成 ,脂肪烃 的热分解是 CH 释放的主要原 因。
煤直接液化残渣热解气体析出规律研究
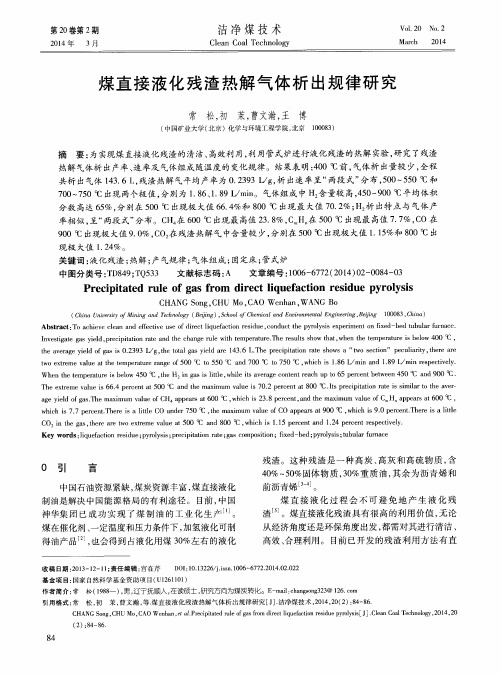
Pr e c i p i t a t e d r ul e o f g a s f r o m d i r e c t l i q ue f a c t i o n r e s i d ue p y r o l y s i s
CHANG S o n g, CHU Mo, CAO We n h a n, W ANG Bo
( C h i n a U n i v e r s i t y Mi n i n g a n d T e c h n o l o g y( B e i j i n g ) , S c h o o l o fC h e m i c a l a n d E n v i r o n m e n t a l E n g i n e e r i n g, B e i j i n g 1 0 0 0 8 3 , C h i n a )
7 0 0 ~ 7 5 0 o C出现 两个极值 , 分 别为 1 . 8 6 、 1 . 8 9 L / a r i n 。 气体 组成 中 H2 含 量较 高 , 4 5 0 — 9 0 0 o C平均 体积
分数 高达 6 5 %, 分 别在 5 0 0℃ 出现极 大值 6 6 . 4 %和 8 0 0℃ 出现 最 大值 7 0 . 2 %; H 2 析 出特 点 与 气体 产 率相似 , 呈“ 两段 式” 分布 。C H 在6 0 0 o C出现 最 高值 2 3 . 8 %, c H 在5 0 0 o C出现 最高值 7 . 7 %, C 0在 9 0 0 o C出现 极 大值 9 . 0 %, c 0 , 在残 渣热 解 气 中含量 较 少 , 分别在 5 0 0 o C出现极 大值 1 . 1 5 %和 8 0 0℃ 出
( 中国矿业大学( 北京 )化学与环境工程学院 , 北京 1 0 0 0 8 3 )
煤直接液化残渣的萃取和利用研究
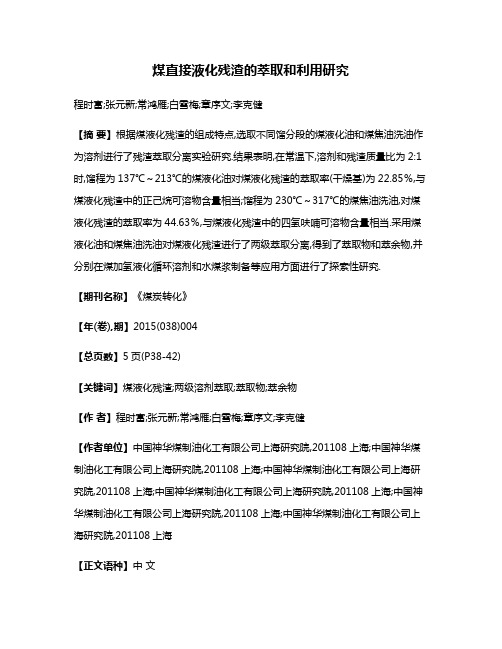
煤直接液化残渣的萃取和利用研究程时富;张元新;常鸿雁;白雪梅;章序文;李克健【摘要】根据煤液化残渣的组成特点,选取不同馏分段的煤液化油和煤焦油洗油作为溶剂进行了残渣萃取分离实验研究.结果表明,在常温下,溶剂和残渣质量比为2:1时,馏程为137℃~213℃的煤液化油对煤液化残渣的萃取率(干燥基)为22.85%,与煤液化残渣中的正己烷可溶物含量相当;馏程为230℃~317℃的煤焦油洗油,对煤液化残渣的萃取率为44.63%,与煤液化残渣中的四氢呋喃可溶物含量相当.采用煤液化油和煤焦油洗油对煤液化残渣进行了两级萃取分离,得到了萃取物和萃余物,并分别在煤加氢液化循环溶剂和水煤浆制备等应用方面进行了探索性研究.【期刊名称】《煤炭转化》【年(卷),期】2015(038)004【总页数】5页(P38-42)【关键词】煤液化残渣;两级溶剂萃取;萃取物;萃余物【作者】程时富;张元新;常鸿雁;白雪梅;章序文;李克健【作者单位】中国神华煤制油化工有限公司上海研究院,201108上海;中国神华煤制油化工有限公司上海研究院,201108上海;中国神华煤制油化工有限公司上海研究院,201108上海;中国神华煤制油化工有限公司上海研究院,201108上海;中国神华煤制油化工有限公司上海研究院,201108上海;中国神华煤制油化工有限公司上海研究院,201108上海【正文语种】中文【中图分类】TQ529.1;X784煤液化残渣是煤直接液化过程中的非目标产物,约占投煤量的30%[1],煤液化残渣的利用对液化过程的效率、整个液化厂的经济效益和环境保护等均有不可低估的影响.2011年以来,神华鄂尔多斯百万吨级煤直接液化示范工程实现商业化运转后,如何有效地开发利用年产约70万t的煤液化残渣,成为一个急需解决的课题.煤液化残渣主要是由重质液化油(正己烷可溶部分)、沥青类物质(正己烷不溶-四氢呋喃可溶部分)、未转化煤和无机质组成的.重质液化油约占20%(质量分数),主要由2环~4环的芳烃和部分氢化芳烃组成.[2]沥青类物质约占30%,主要由多环的缩合芳烃组成,具有芳香度高以及碳含量高的特点.[3]未转化煤是指残渣中不溶于四氢呋喃的有机质,约占残渣总量的30%,无机质主要是由煤中的矿物质和外加的催化剂组成,富集了灰分和硫分,约占残渣总量的20%.许多学者对煤液化残渣的热解性能[4-5]和转化利用[6-11]进行了大量的研究,主要集中在燃烧、气化和加氢转化上.但煤液化残渣气化或燃烧未充分利用残渣的重质液化油和沥青类物质的特性,加氢转化由于残渣中的高灰分,难于实现大规模应用.溶剂萃取是一种有效地将煤液化残渣中的重质液化油、沥青类物质分离出来的方法[12-13],以往的研究大都采用成本较高的甲苯和四氢呋喃等纯化学试剂作为萃取溶剂.本课题组采用煤液化油作为溶剂对煤液化残渣萃取分离进行了系统的研究,并对沥青类物质的利用进行了基础性研究.[14-16]本实验在前期研发成果的基础上,根据神华煤液化残渣组成和特性,进行煤液化残渣的两级萃取分离实验研究,并对萃取物和萃余物的应用进行了探索性研究,为实现煤直接液化残渣萃取物的综合利用提供方向.煤液化残渣(CLR,简称残渣)取自神华鄂尔多斯百万吨级煤直接液化示范装置,软化点为198.8 ℃,实验前残渣经破碎并筛分,50 μm~150 μm的部分作为萃取原料.萃取溶剂为煤液化油(CLO,简称液化油)和煤焦油洗油(WO,简称洗油),液化油取自神华鄂尔多斯百万吨级煤直接液化示范装置,并经蒸馏分离得到的不同馏分段;洗油来自神华乌海焦油厂.两种溶剂油的基本组成及性质见表1(表1中IBP为初馏点,EP为终馏点).实验前,通过将其蒸馏切割成不同的馏分段作为萃取溶剂.残渣的萃取分离和综合利用流程[14]见图1.残渣经过一级萃取分离和溶剂回收后,得到一级萃取物和一级萃余物,一级萃取物经过适度加氢后作为煤液化的循环溶剂使用,一级萃余物再经过二级萃取分离和溶剂回收,得到二级萃取物和二级萃余物,二级萃取物可作为黏结剂或炭材料的原料,二级萃余物可进行气化或燃烧.残渣的萃取分离实验在带内置过滤器(精度1 μm~10 μm)的5 L搅拌釜装置上进行(见图2).残渣和溶剂按一定比例加入至搅拌釜反应器中,采用N2置换、密封,在一定的温度和时间下完成萃取,萃取混合物通过内置过滤器完成过滤,采用德国i-FISCHER DIST D2892MC-10L型自动实沸点蒸馏仪回收滤液中的萃取溶剂,得到萃取物;通过升温干燥回收滤饼中的溶剂,得到萃余物.根据不同溶剂对残渣的萃取率,选定两种合适的萃取溶剂进行残渣萃取,尽可能地将残渣中的重质油和沥青类物质分离开来,得到一级萃取物(1st extract)、二级萃取物(2nd extract)、一级萃余物(1st remain)和二级萃余物(2nd remain),并将一级萃取物和二级萃余物分别在煤液化循环溶剂和水煤浆制备中进行探索性应用研究. 残渣、萃取物和萃余物的工业分析执行GB/T 212-2008标准,元素分析执行GB/T 476-2001标准,软化点执行ASTM3461标准,采用溶剂抽提法,按照GB/T 2292-1997标准进行族组成分析,其中正己烷可溶部分(HS)为重质油,正己烷不溶-甲苯可溶部分为沥青烯(A),甲苯不溶-四氢呋喃可溶部分为前沥青烯(PA),四氢呋喃不溶部分(THFIS)为未转化煤和灰分.热重分析在SDTQ600热重分析仪上测定,氮气气氛,流量100 mL/min,以10 ℃/min的速率由室温升温至1 000 ℃.残渣一级萃取和二级萃取的萃取率wE1和wE2的计算公式如下:式中:m1为残渣原料的质量(干燥基);m2为一级萃余物的质量(干燥基,扣除其中的残留溶剂,并忽略萃取滤液中的不溶物);m3为二级萃余物的质量(干燥基,扣除其中的残留溶剂,并忽略萃取滤液中的不溶物).煤液化高压釜反应的煤转化率wL计算公式如下:式中:mC为原煤的质量(干燥无灰基);mUC为未反应煤的质量(干燥无灰基).采用洗油和不同馏分段的液化油作为溶剂,进行残渣的萃取分离实验,结果见表2. 由表2可以看出,在相同的萃取条件下,随着液化油馏分的升高,对残渣的萃取率也逐渐升高,馏程为137 ℃~213 ℃的液化油对残渣的萃取率为22.85%,与残渣中的正己烷可溶物含量相当(见表1),选定其作为残渣的一级萃取溶剂;而洗油对残渣的萃取率为44.62%,比相近馏分段230 ℃~316 ℃液化油的萃取率高,主要是因为洗油未经过加氢处理.[17]相对于煤液化油,洗油组分与残渣中的重质油和沥青质的组成更接近,对残渣的萃取率高,因此选定洗油作为残渣的二级萃取溶剂.根据不同溶剂对残渣萃取效果的差异,选取煤液化油(137 ℃~213 ℃馏分)和洗油作为溶剂对残渣进行两级萃取,结果见表3.由表3可以看出,在34 ℃,质量比为2∶1时,采用煤液化油(137 ℃~213 ℃馏分)对煤液化残渣进行了一级萃取,萃取率为23.97%;在180 ℃,质量比为2∶1时,采用洗油对一级萃余物进行了二次萃取,萃取率为26.61%.同时,得到了萃取物和萃余物的工业分析、元素分析和组分分析数据,并与残渣原料进行了比较(见表4).由表4可以看出:1) 经过液化油的一级萃取分离后,相对于残渣,一级萃余物中HS含量降低至1.67%,而THFIS含量升高至66.37%,表明残渣中的大部分HS被CLO选择性地萃取出来;2) 一级萃取物中的灰分(0.05%)、S含量(0.04%)相对于残渣大大降低,而一级萃余物中的灰分和S含量反而升高,表明残渣中的硫主要是以无机硫的形态存在,与灰分一起被分离出来;3) 二级萃余物中的HS,A和PA总和为7.13%,而THFIS为92.87%,表明洗油能将残渣中的大部分THFIS萃取出来,而少量的THFIS是由于未干燥的萃余物中残留洗油溶解的沥青类物质造成的;4) 比较一级萃取物与二级萃取物的元素分析,可以发现二级萃取物的n(C)∶n(H)比一级萃取物的高,表明二级萃取物中的分子芳环缩合程度比一级萃取物高;比较二者组分分析,可以发现二级萃取物的THFIS比一级萃取物的高,HS 比一级萃取物的低,说明二级萃取物中的组分比一级萃取物重.图3为煤液化残渣及萃取物和萃余物的热重曲线.由图3可以看出,950 ℃时,一级萃取物、二级萃取物、残渣、一级萃余物和二级萃余物的失重率分别为75.28%,55.77%,37.02%,25.11%和20.49%,与挥发分数据(见表4)基本一致.残渣、萃取物及萃余物在250 ℃~550 ℃都有失重,一级萃余物和二级萃余物失重率较小(lt;20%),是由其中的HS和A含量较低造成的;一级萃取物、二级萃取物和残渣的失重由250 ℃开始,主要是HS和A的失重造成的,一级萃余物和二级萃余物的失重由300 ℃开始,是由其中轻质组分A的失重造成的;一级萃余物和二级萃余物在550 ℃后基本不失重,而残渣、一级萃余物和二级萃余物在700 ℃~800 ℃还有一定的失重,是由残渣及其萃余物中的无机质受热分解造成的.在神华煤直接液化工艺[18]中,经减压蒸馏得到的煤液化粗油,经过适度加氢后,分离出其中gt;260 ℃的馏分作为煤液化循环供氢溶剂使用.而煤液化残渣的一级萃取物重质油含量为66.77%,可掺配至煤液化粗油中作为循环溶剂,一方面可以解决煤液化循环溶剂轻质化的问题;另一方面可以提高煤液化油的收率.将一级萃取物与煤液化油按照3.6∶96.4的质量比配制成加氢原料油,通过30 mL/h加氢微反装置进行加氢后,再分离出其gt;260 ℃的馏分作为煤液化循环溶剂,在500 mL高压釜中考察其对煤液化反应的影响.未掺加一级萃取物的煤液化油简称为CLO,掺加一级萃取物的煤液化油简称为CLOE,其加氢后的产物分别简称为CLOH和CLOEH.CLO,CLOE,CLOH和CLOEH的组成和性质见表5.由表5可以看出,掺加3.6%的一级萃取物后,原料油的密度由0.974 5 g/cm3增至0.984 8 g/cm3,黏度由4.59 mm2/s增至5.58 mm2/s,硫含量由111 μg/g 增至136 μg/g,氮含量由0.25%增至0.39%,n(H)∶n(C)由1.344 0降低至1.315 0,供氢指数(PDQI,指每克溶剂中的Hnβ毫克数)由14.99降至10.87,单环芳烃含量由44.0%降至42.1%,双环芳烃含量由24.2%降至23.6%;胶质(pectin)含量由8.4%升高至9.7%.经过加氢后,CLOH和CLOEH的密度、黏度、硫含量、氮含量和胶质含量都降低,而n(H)∶n(C)分别升高至1.489 0和1.469 1,PDQI分别升高至24.52和23.68.以加氢后gt;260 ℃的馏分作为溶剂,在500 mL高压釜中考察其对煤液化反应的影响,具体数据见表6.由表6可以看出,与未掺gt;260 ℃溶剂油相比,掺一级萃取物的加氢后gt;260 ℃溶剂油的煤液化反应,煤的转化率基本不变,氢耗由4.71%降低至4.43%,降幅为5.94%;液化油收率由54.75%降至53.63%,降幅为2.04%;沥青类物质收率由14.86%增至15.81%,增幅6.39%,这可能是由CLOEH的供氢性能较CLOH偏低造成的,但总体上看,残渣的一级萃取物作为循环溶剂,替代出煤液化油中的轻组分,增加煤液化工艺的整体油收率.将二级萃余物粉碎后,在添加剂加入量都为0.3%(干基/干粉,质量分数)下,单独或与神东煤一起配制水煤浆,考察其成浆性能.水煤浆的浓度按照GB/T 18856.2-2008测定,黏度按照GB/T 18856.4-2008测定,流动性和稳定性采用目测方法测定.流动性分三个等级:A,连续流动;B,间断流动;C,不流动.稳定性是将被测试样品密闭静置8 h后,插棒观测:A级,浆体保持其初始状态,无析出水和沉淀产生;B级,存在少量的析水或少许软沉淀产生;C级,有沉淀产生,密度分布不均,但经搅拌作用后可再生;D级,产生部分沉淀或全部硬沉淀.具体数据见第42页表7.由表7可以看出,单独采用二级萃余物配制水煤浆时,其质量分数可达76.49%,且稳定性和流动性都较好,而单独采用神东煤配制相同稳定性和流动性的水煤浆时,其质量分数只有60.29%.为防止增加后续气化炉或锅炉的脱硫、脱灰负担,采用神东煤与二级萃余物按照质量比4∶1配制水煤浆,其质量分数可达到64.46%,且稳定性和流动性均达到了采用煤配制的水煤浆的指标.1) 在室温下,溶剂与残渣质量比为2∶1时,馏程137 ℃~213 ℃煤液化油对残渣萃取率为22.85%,与残渣中的HS含量相当,洗油对残渣的萃取率为44.63%,与残渣的THFIS含量相当.2) 一级萃取物掺加至煤液化油中,通过加氢后,可作为煤液化循环溶剂使用.3) 采用二级萃余物配制的水煤浆,最高浓度达到76.49%,且稳定性和流动性都较好.【相关文献】[1] 舒歌平,史士东,李克健.煤炭液化技术[M].北京:煤炭工业出版社,2001:179-185.[2] 谷小会,周铭,史士东.神华煤直接液化残渣中重质油组分的分子结构[J].煤炭学报,2006,31(1):76-80.[3] 谷小会,史士东,周铭.神华煤直接液化残渣中沥青烯组分的分子结构研究[J].煤炭学报,2006,31(6):785-789.[4] 周俊虎,方磊,程军,等.神华煤直接液化残渣的热解性能研究[J].煤炭学报,2005,30(3):349-352.[5] 李军,杨建丽,刘振宇.煤直接液化残渣的热解特性研究[J].燃料化学学报,2010,38(4):1-6.[6] 崔洪,杨建丽,刘振宇,等.煤直接液化残渣的性质及气化制氢[J].煤炭转化,2001,24(1):15-20.[7] 方磊,周俊虎,周志军,等.煤液化残渣与褐煤混煤燃烧特性的实验研究[J].燃料化学学报,2004,34(2):245-248.[8] 颜丙峰,杜淑凤,张晓静.煤液化沥青脱除灰分的研究[J].煤炭转化,2013,36(2):33-35.[9] Li Jun,Yang Jianli,Liu Zhenyu.Hydro-treatment of a Direct Coal Liquefaction Residue and Its Components[J].Catal Today,2008,130(2/4):389-394.[10] 周颖,张艳,李振涛,等.以煤炭直接液化残渣为原料制备炭纳米管[J].煤炭转化,2007,30(3):41-44.[11] 王国龙,徐蓉,张德祥,等.煤液化残渣加氢性能[J].石油学报(石油加工),2009,25(5):747-751.[12] 刘朋飞,张永奇,房倚天,等.神华煤直接液化残渣超临界溶剂萃取研究[J].燃料化学学报,2012,40(7):776-781.[13] 刘朋飞,张永奇,房倚天.煤直接液化残渣及其萃取产物的热重分析[J].燃料化学学报,2012,40(6):655-659.[14] 吴秀章,张盛振,李克健,等.煤直接液化残渣的萃取方法及萃取物的应用:中国,101962560A[P].2011-02-02.[15] 吴秀章,朱晓苏,李克健,等.从煤直接液化残渣中提取重质油和中间相沥青类物质的方法及其应用:中国,101885976A[P].2010-11-17.[16] 盛英,李克健,李文博,等.煤直接液化残留物制备中间相沥青[J].煤炭学报,2009,34(8):1125-1128.[17] 肖瑞华.煤焦油化工学[M].北京:冶金工业出版社,2004:245-257.[18] 张德祥,刘瑞民,高晋生.煤炭直接加氢液化技术开发的几点思考[J].石油学报(石油加工),2011,27(3):329-335.。
煤化工工艺学第6章 煤的直接液化
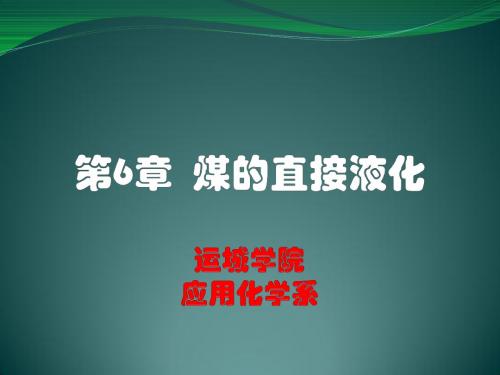
(2)煤的液化溶剂对煤的抽提溶解作用
根据溶剂种类、抽提温度和压力等条件的不同,主要有两类。 ①热解抽提溶解 用高沸点多环芳烃或焦油馏分(如蒽、菲、喹
啉等)作为溶剂,抽提温度在400℃左右,煤伴有热解反应并被抽 提溶解。烟煤抽提溶解率一般在60%以上,少数煤甚至可达90%。 ②加氢抽提溶解 采用供氢溶剂(如四氢萘、四氢喹啉、二氢蒽 和二氢菲)或非供氢溶剂在高氢压力下,在大于400℃的温度下发 生抽提溶解,同时发生激烈的热解和加氢反应。
掺混 掺混 酯交换工艺
煤炭直接液化是在高温高压下,借助于供氢、溶剂和催化剂,使 煤与氢反应,从而将煤中复杂的有机高分子结构直接转化为较低分子的 液体油。通过煤直接液化,不仅可以生产汽油、柴油、煤油、液化石油 气,还可以提取苯、甲苯、二甲苯混合物及生产乙烯、丙烯等重要烯烃 的原料。直接液化的优点是热效率较高、液体产品收率高;主要缺点是 煤浆加氢工艺条件相对苛刻,反应设备需能够承受高温、高压和氢的腐 蚀。图6-1是神华直接液化项目流程图。
根据相似相溶的原理,溶剂结构与煤分子近似的多环芳烃,
对煤热解的活性基团有较大的溶解能力。 溶剂溶解氢气的量与压力成正比,压力越高,溶解的氢气越 多。 在煤液化装臵的连续运转过程中,实际使用的溶剂是煤直接 液化产生的中质油和重质油的混合油,称作循环溶剂,其主 要组成是2~4环的芳烃和氢化芳烃。循环溶剂经过预先加氢, 提高了溶剂中氢化芳烃的含量,可以提高溶剂的供氢能力。 煤液化装臵开车时,没有循环溶剂,则需采用外来的其他油 品作为起始溶剂。起始溶剂可以选用高温煤焦油中的脱晶蒽 油;也可采用石油重油催化裂化装臵产出的澄清油或石油常 减压装臵的渣油;还可以选择热处理软化成液体的废塑料、 废橡胶、废油脂作为溶剂。
6.1.1.2 石油
煤直接液化性能的影响因素浅析
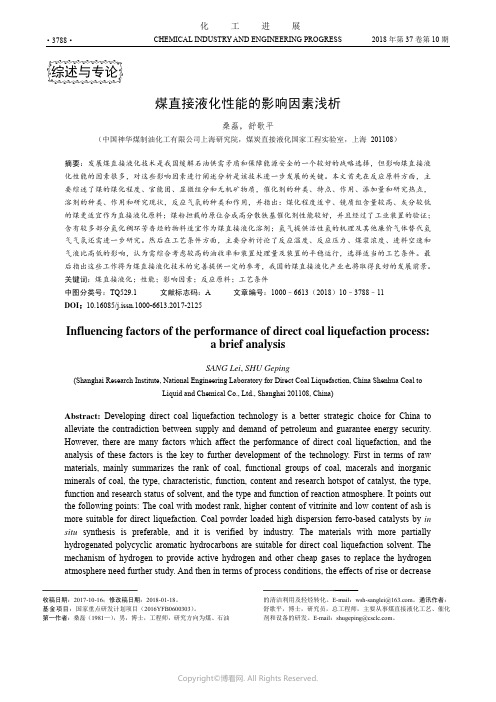
CHEMICAL INDUSTRY AND ENGINEERING PROGRESS 2018年第37卷第10期·3788·化 工 进展煤直接液化性能的影响因素浅析桑磊,舒歌平(中国神华煤制油化工有限公司上海研究院,煤炭直接液化国家工程实验室,上海 201108)摘要:发展煤直接液化技术是我国缓解石油供需矛盾和保障能源安全的一个较好的战略选择,但影响煤直接液化性能的因素很多,对这些影响因素进行阐述分析是该技术进一步发展的关键。
本文首先在反应原料方面,主要综述了煤的煤化程度、官能团、显微组分和无机矿物质,催化剂的种类、特点、作用、添加量和研究热点,溶剂的种类、作用和研究现状,反应气氛的种类和作用,并指出:煤化程度适中、镜质组含量较高、灰分较低的煤更适宜作为直接液化原料;煤粉担载的原位合成高分散铁基催化剂性能较好,并且经过了工业装置的验证;含有较多部分氢化稠环芳香烃的物料适宜作为煤直接液化溶剂;氢气提供活性氢的机理及其他廉价气体替代氢气气氛还需进一步研究。
然后在工艺条件方面,主要分析讨论了反应温度、反应压力、煤浆浓度、进料空速和气液比高低的影响,认为需综合考虑较高的油收率和装置处理量及装置的平稳运行,选择适当的工艺条件。
最后指出这些工作将为煤直接液化技术的完善提供一定的参考,我国的煤直接液化产业也将取得良好的发展前景。
关键词:煤直接液化;性能;影响因素;反应原料;工艺条件中图分类号:TQ529.1 文献标志码:A 文章编号:1000–6613(2018)10–3788–11 DOI :10.16085/j.issn.1000-6613.2017-2125Influencing factors of the performance of direct coal liquefaction process:a brief analysisSANG Lei , SHU Geping(Shanghai Research Institute, National Engineering Laboratory for Direct Coal Liquefaction, China Shenhua Coal toLiquid and Chemical Co., Ltd., Shanghai 201108, China)Abstract: Developing direct coal liquefaction technology is a better strategic choice for China to alleviate the contradiction between supply and demand of petroleum and guarantee energy security. However, there are many factors which affect the performance of direct coal liquefaction, and the analysis of these factors is the key to further development of the technology. First in terms of raw materials, mainly summarizes the rank of coal, functional groups of coal, macerals and inorganic minerals of coal, the type, characteristic, function, content and research hotspot of catalyst, the type, function and research status of solvent, and the type and function of reaction atmosphere. It points out the following points: The coal with modest rank, higher content of vitrinite and low content of ash is more suitable for direct liquefaction. Coal powder loaded high dispersion ferro-based catalysts by in situ synthesis is preferable, and it is verified by industry. The materials with more partially hydrogenated polycyclic aromatic hydrocarbons are suitable for direct coal liquefaction solvent. The mechanism of hydrogen to provide active hydrogen and other cheap gases to replace the hydrogen atmosphere need further study. And then in terms of process conditions, the effects of rise or decrease的清洁利用及轻烃转化。
《2024年神华煤直接液化残渣中无机物成分分析》范文

《神华煤直接液化残渣中无机物成分分析》篇一摘要:本研究通过对神华煤直接液化过程中产生的残渣进行详细的无机物成分分析,探究其化学组成与分布情况,旨在为煤炭的深度开发与综合利用提供科学依据。
通过对残渣进行一系列化学分析实验,包括X射线衍射、红外光谱、元素分析和热重分析等手段,得到了无机物的具体成分及其含量分布,为后续的煤炭液化工艺优化和资源回收利用提供了理论支持。
一、引言随着煤炭的深度开发与利用,煤直接液化技术作为一种重要的煤炭转化方式,得到了广泛的研究与应用。
在煤直接液化过程中,产生的残渣是一种重要的产物,其中含有大量的无机物成分。
对这些无机物成分进行深入分析,有助于了解煤的化学组成与结构,同时也能为煤炭的综合利用提供重要依据。
二、实验材料与方法本实验选用的样品为神华煤直接液化后的残渣。
实验过程中,首先对残渣进行破碎、研磨处理,使其达到实验所需的粒度要求。
然后采用X射线衍射、红外光谱、元素分析和热重分析等手段对残渣中的无机物成分进行检测与分析。
三、实验结果与分析1. X射线衍射分析:通过对残渣进行X射线衍射分析,我们发现其中含有多种无机矿物成分,如石英、长石、粘土矿物等。
这些矿物的存在形式和含量可以通过衍射图谱的峰值和强度来反映。
2. 红外光谱分析:红外光谱分析结果表明,残渣中的无机物具有特定的红外吸收峰,这些吸收峰与无机物的化学键类型和结构密切相关。
通过对比标准谱图,可以确定残渣中无机物的具体类型和结构。
3. 元素分析:元素分析结果显示,神华煤直接液化残渣中无机物的主要元素包括Si、Al、Fe、Ca等。
这些元素在残渣中的含量分布因煤种和液化条件的不同而有所差异。
4. 热重分析:热重分析结果表明,残渣中的无机物在加热过程中具有不同的热稳定性和分解行为。
这有助于了解残渣的热处理过程和无机物的转化情况。
四、讨论与结论通过对神华煤直接液化残渣的无机物成分进行分析,我们得出了以下结论:1. 残渣中含有多种无机矿物成分,包括石英、长石、粘土矿物等。
TGFTIR法研究低变质煤共热解过程气体的析出规律
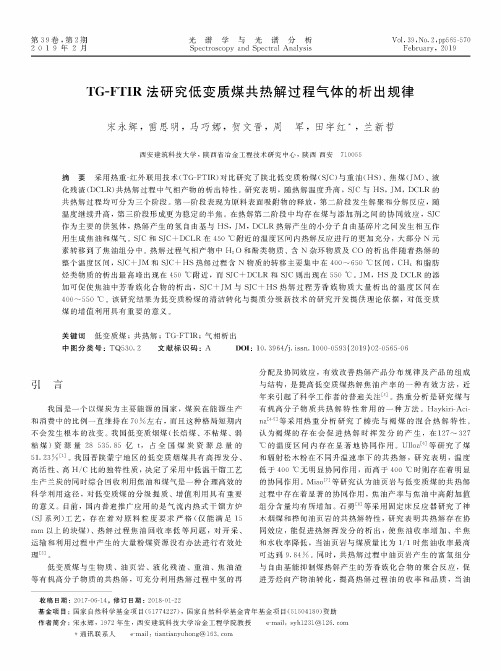
第39卷,第2期 2 0 19年2月光谱学与光谱分析Spectroscopy and Spectral AnalysisV o l. 39,N o. 2,pp565-570F e b ru a ry,2019T G-F T IR法研究低变质煤共热解过程气体的析出规律宋永辉,雷思明,马巧娜,贺文晋,周军,田宇红兰新哲西安建筑科技大学,陕西省冶金工程技术研究中心,陕西西安710055摘要采用热重-红外联用技术(T G-F T I R)对比研究了陕北低变质粉煤(SJC)与重油(H S)、焦煤(JM)、液 化残渣(DCLR)共热解过程中气相产物的析出特性。
研究表明,随热解温度升高,SJC与H S,JM,D C L R的共热解过程均可分为三个阶段。
第一阶段表现为原料表面吸附物的释放,第二阶段发生解聚和分解反应,随 温度继续升高,第三阶段形成更为稳定的半焦。
在热解第二阶段中均存在煤与添加剂之间的协同效应,SJC 作为主要的供氢体,热解产生的氢自由基与H S,JM,D C L R热解产生的小分子自由基碎片之间发生相互作用生成焦油和煤气。
SJC和S J C+D C L R在850+附近的温度区间内热解反应进行的更加充分,大部分N元 素转移到了焦油组分中。
热解过程气相产物中H2O和酚类物质、含N杂环物质及C O的析出伴随着热解的 整个温度区间,S J C+J M和S J C+H S热解过程含N物质的转移主要集中在400〜650 +区间,CH4和脂肪 烃类物质的析出最高峰出现在450 +附近,而S J C+D C L R和SJC则出现在550 +。
JM,H S及D C L R的添 加可促使焦油中芳香族化合物的析出,S J C+J M与S J C+H S热解过程芳香族物质大量析出的温度区间在400〜550 +。
该研究结果为低变质粉煤的清洁转化与提质分级新技术的研究开发提供理论依据,对低变质 煤的增值利用具有重要的意义。
一种煤直接液化的煤液化残渣的排放系统、故障维修方法及其应用[
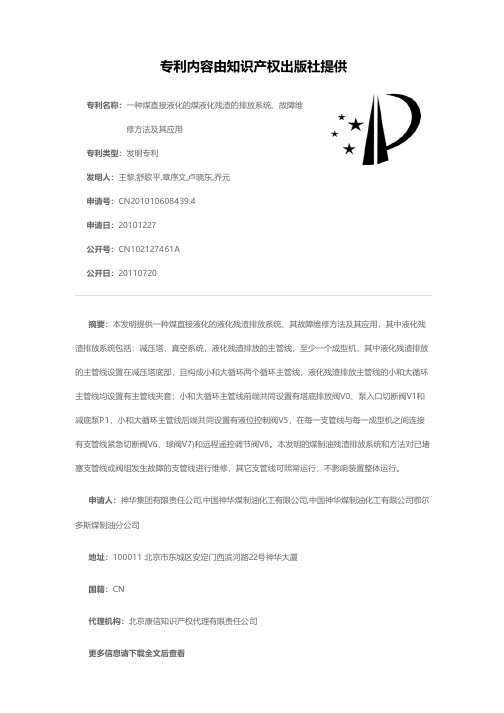
专利名称:一种煤直接液化的煤液化残渣的排放系统、故障维修方法及其应用
专利类型:发明专利
发明人:王黎,舒歌平,章序文,卢晓东,乔元
申请号:CN201010608439.4
申请日:20101227
公开号:CN102127461A
公开日:
20110720
专利内容由知识产权出版社提供
摘要:本发明提供一种煤直接液化的液化残渣排放系统、其故障维修方法及其应用,其中液化残渣排放系统包括:减压塔,真空系统,液化残渣排放的主管线,至少一个成型机,其中液化残渣排放的主管线设置在减压塔底部,且构成小和大循环两个循环主管线,液化残渣排放主管线的小和大循环主管线均设置有主管线夹套;小和大循环主管线前端共同设置有塔底排放阀V0、泵入口切断阀V1和减底泵P1,小和大循环主管线后端共同设置有液位控制阀V5,在每一支管线与每一成型机之间连接有支管线紧急切断阀V6、球阀V7)和远程遥控调节阀V8。
本发明的煤制油残渣排放系统和方法对已堵塞支管线或阀组发生故障的支管线进行维修,其它支管线可照常运行,不影响装置整体运行。
申请人:神华集团有限责任公司,中国神华煤制油化工有限公司,中国神华煤制油化工有限公司鄂尔多斯煤制油分公司
地址:100011 北京市东城区安定门西滨河路22号神华大厦
国籍:CN
代理机构:北京康信知识产权代理有限责任公司
更多信息请下载全文后查看。
《2024年神华煤直接液化残渣中无机物成分分析》范文

《神华煤直接液化残渣中无机物成分分析》篇一一、引言随着能源需求的持续增长,煤炭作为主要能源之一,其高效利用和清洁转化成为研究热点。
神华煤作为一种优质的煤炭资源,其直接液化技术得到了广泛的应用。
然而,在煤直接液化过程中,会产生大量的残渣。
这些残渣中不仅含有有机物,还富含无机物成分。
对这些无机物成分进行深入分析,有助于更好地了解残渣的组成和性质,进而为残渣的综合利用提供理论依据。
本文以神华煤直接液化残渣为研究对象,对其中的无机物成分进行详细分析。
二、实验材料与方法1. 实验材料本实验所使用的神华煤直接液化残渣取自某煤炭液化工厂。
在实验前,对残渣进行了预处理,以去除其中的杂质。
2. 实验方法(1)X射线衍射(XRD)分析:采用XRD技术对残渣中的无机物进行物相分析,确定其晶体结构。
(2)化学浸取法:通过化学浸取法将残渣中的无机物与有机物分离,然后对浸取液进行成分分析。
(3)扫描电镜(SEM)分析:利用SEM技术观察残渣的微观形貌,进一步了解无机物的分布和形态。
三、结果与讨论1. XRD分析结果通过XRD分析,我们发现神华煤直接液化残渣中的无机物主要为硅酸盐、硫酸盐、氧化物等。
其中,硅酸盐的衍射峰较为明显,表明其在残渣中含量较高。
此外,还观察到了一些其他矿物质的衍射峰,如钙、镁、铁等元素的化合物。
2. 化学浸取法分析结果通过化学浸取法,我们成功地将残渣中的无机物与有机物分离。
对浸取液进行成分分析,发现其中含有大量的钙、镁、铁、铝等元素。
这些元素主要以离子形式存在,如钙离子、镁离子、铁离子等。
此外,还检测到少量的硫、磷等元素。
3. SEM分析结果通过SEM分析,我们观察到神华煤直接液化残渣的微观形貌呈现出不规则的颗粒状结构。
在这些颗粒表面,可以清晰地看到一些无机物的分布和形态。
这些无机物主要以硅酸盐、氧化物等形式存在,与XRD和化学浸取法的分析结果相一致。
四、结论通过对神华煤直接液化残渣中无机物成分的分析,我们得出以下结论:1. 残渣中的无机物主要以硅酸盐、硫酸盐、氧化物等形式存在。
《煤热解、气化过程中含氮化合物的生成与释放研究》

《煤热解、气化过程中含氮化合物的生成与释放研究》篇一一、引言煤作为全球主要的能源之一,其利用过程中产生的环境问题日益受到关注。
在煤的热解和气化过程中,含氮化合物(如NH3、HCN等)的生成与释放行为,对于了解煤的转化过程及其环境影响具有关键作用。
本文将对煤热解和气化过程中含氮化合物的生成与释放进行研究,为进一步优化煤的清洁利用提供理论依据。
二、文献综述在煤的转化过程中,含氮化合物的生成与释放一直是研究的热点。
早期的研究主要关注于煤热解过程中氮的迁移和转化,随着气化技术的发展,气化过程中含氮化合物的生成与释放也逐渐成为研究重点。
研究表明,煤中氮的形态和含量对含氮化合物的生成与释放具有重要影响。
此外,反应条件如温度、压力、气氛等也会影响含氮化合物的生成与释放。
三、研究内容(一)实验材料与方法本实验选用不同类型和不同氮含量的煤样进行热解和气化实验。
实验设备包括管式炉、气相色谱仪等。
实验过程中,通过改变反应条件,如温度、压力、气氛等,研究煤样在热解和气化过程中的氮迁移和转化规律。
(二)实验结果与分析1. 煤热解过程中含氮化合物的生成与释放在煤热解过程中,随着温度的升高,氮的迁移和转化逐渐加剧。
实验结果表明,NH3是热解过程中主要的含氮化合物,其生成量随温度的升高而增加。
此外,HCN、N2等含氮化合物也有所生成。
煤中氮的形态和含量对含氮化合物的生成与释放具有重要影响。
2. 煤气化过程中含氮化合物的生成与释放在煤气化过程中,气氛对含氮化合物的生成与释放具有重要影响。
实验结果表明,在氧气气氛下,NH3和NOx是主要的含氮化合物;而在无氧或还原性气氛下,HCN等含氮化合物成为主要产物。
此外,气化温度和压力也会影响含氮化合物的生成与释放。
四、讨论煤热解和气化过程中含氮化合物的生成与释放受到多种因素的影响。
从热力学角度来看,高温有利于氮的迁移和转化;从动力学角度来看,煤中氮的形态和含量、反应气氛等也会影响含氮化合物的生成与释放。
颗粒粒径对油页岩热解产油率的影响_畅志兵

图 1 不同粒级样品制备过程示意图 Figure 1 Schematic diagram of sample preparation procedure
1. 2 热解实验 热解实验在铝甑炉中进行,在甑盖上增设进气
管,反应装置示意图见图 2。实验前用氮气置换装 置 内 空 气,此 部 分 气 体 不 收 集,实 验 过 程 中 以
E-mail: cm@ cumtb. edu. cn。
664
燃料化学学报
Байду номын сангаас
第 43 卷
0. 6 mm粒级组分。此外,在相似的粒径范围内,某 “细粉样品”,比较各组分和对应细粉样品的热解特
些研究又得出了油产率随粒径减小先增大后减小的 结论[7,8]。事实 上,文 献 在 解 释 这 些 变 化 规 律 时 都
Abstract: The influence of particle size on oil yield from pyrolysis of Huadian oil shale w as investigated. The raw material w as crushed and sieved to 6 fractions w ith different particle size: < 0. 074,0. 074 ~ 0. 125,0. 125 ~ 0. 25,0. 25 ~ 0. 5,0. 5 ~ 1 and 1 ~ 3 mm. Then,the fraction of 0. 25 ~ 0. 5,0. 5 ~ 1 and 1 ~ 3 mm w ere ground to obtain the corresponding pow der samples. A standard method and thermogravimetric analysis w ere applied to measure and characterize the oil yield and organic matter content in different samples. The results show that both the oil yield ( from 11. 92% to 6. 14% ) and organic matter content decrease gradually w ith decrease in particle size,and a significantly linear relationship is observed betw een oil yield and organic matter content. The oil yield for pow der sample of 0. 25 ~ 0. 5,0. 5 ~ 1,and 1 ~ 3 mm decreases,w hile gas yield increases,but the variation is slight and below 1% . Both preferential distribution of organic matter and secondary reaction of shale oil determine the oil yield of fractions w ith different particle sizes. Furthermore,the selective enrichment of organic matter is the predominant factor. Ke y words: oil shale; particle size; pyrolysis; organic matter preferential distribution; secondary reaction
- 1、下载文档前请自行甄别文档内容的完整性,平台不提供额外的编辑、内容补充、找答案等附加服务。
- 2、"仅部分预览"的文档,不可在线预览部分如存在完整性等问题,可反馈申请退款(可完整预览的文档不适用该条件!)。
- 3、如文档侵犯您的权益,请联系客服反馈,我们会尽快为您处理(人工客服工作时间:9:00-18:30)。
液化残渣工业分析和元素分析。
表 1 液化残渣工业分析和元素分析
工业分析 /%
Mad
Ad
Vd
FCdaf
18. 48
33. 88
47. 64
ω( Cdaf ) 89. 19
ω( Hdaf ) 4. 83
元素分析 /% ω( Ndaf ) 1. 07
85
2014 年第 2 期
洁净煤技术
第 20 卷
图 4 液化残渣热解气组成随温度变化
由图 4b) 可知,450 ℃ 前,H2 体积分数不高,450 ℃ 时,H2 体积分数突增至 65. 9% ,此时 H2 主要来自 氢化芳香结构的缩聚脱氢反应[11]; 500 ℃ 出现极大 值 66. 4% ,500 ~ 600 ℃ ,H2 体积分数随温度的升高 而减少,600 ℃ 出现极低值 57. 1% ; 600 ~ 800 ℃ ,H2 体积分数随温度的升高而增加,800 ℃ 出现最大值 为 70. 2% ,此时 H2 来源于芳香结构的进一步缩聚反 应。H2 的析出特点与气体产率相似,呈“两段式”分 布。残渣热解气中含有较多 H2 ,说明液化残渣中含 有较丰富的芳香族结构。
Abstract: To achieve clean and effective use of direct liquefaction residue,conduct the pyrolysis experiment on fixed - bed tubular furnace. Investigate gas yield,precipitation rate and the change rule with temperature. The results show that,when the temperature is below 400 ℃ ,the average yield of gas is 0. 2393 L / g,the total gas yield are 143. 6 L. The precipitation rate shows a " two section" peculiarity, there are two extreme value at the temperature range of 500 ℃ to 550 ℃ and 700 ℃ to 750 ℃ ,which is 1. 86 L / min and 1. 89 L / min respectively. When the temperature is below 450 ℃ ,the H2 in gas is little,while its average content reach up to 65 percent between 450 ℃ and 900 ℃ . The extreme value is 66. 4 percent at 500 ℃ and the maximum value is 70. 2 percent at 800 ℃ . Its precipitation rate is similar to the average yield of gas. The maximum value of CH4 appears at 600 ℃ ,which is 23. 8 percent,and the maximum value of Cm Hn appears at 600 ℃ ,which is 7. 7 percent. There is a little CO under 750 ℃ ,the maximum value of CO appears at 900 ℃ ,which is 9. 0 percent. There is a little CO2 in the gas,there are two extreme value at 500 ℃ and 800 ℃ ,which is 1. 15 percent and 1. 24 percent respectively. Key words: liquefaction residue; pyrolysis; precipitation rate; gas composition; fixed - bed; pyrolysis; tubular furnace
84
常 松等: 煤直接液化残渣热解气体析出规律研究
2014 年第 2 期
接燃烧、干馏、气化等[6 - 7]。已有大量科研工作者对 液化残渣进行研究,主要考察了残渣自身性质、热解 成焦性及焦油性质,对残渣热解气体析出规律的研 究尚少。笔者通过固定床管式炉对残渣进行热解实 验,研究其气体析出规律。
1 实验条件
Precipitated rule of gas from direct liquefaction residue pyrolysis
CHANG Song,CHU Mo,CAO Wenhan,WANG Bo
( China University of Mining and Technology ( Beijing) ,School of Chemical and Environmental Engineering,Beijing 100083,China)
整个热解过程中,CO2 含量都不高,在 500、800 ℃ 出现两个极值,分别为 1. 15% 和 1. 24% ,500 ℃ 的 CO2 来源于残渣中残留的褐煤热解,而碳酸盐类 矿物质在 800 ℃ 开始分解[12 - 13],因此可认为 800 ℃ 内 CO2 释出速率略有回升,主要是由于残渣中碳酸 盐分解导致。CO 在 750 ℃ 前含量很少,最高值不超 过 0. 1% ,750 ℃ 后,CO 含量随温度升高而增加,900 ℃ 达到极大值 9. 0% 。一般认为,CO 和 CO2 来自煤结 构中各种含氧官能团的脱落[14],煤直接液化时,经历 了 450 ℃ 液化温度后,CO 和 CO2 已大量脱除[15]。因 此残渣热解气中,CO 和 CO2 含量都较少,750 ℃ 后 CO 含量增加可能是由于残渣中碳酸盐类矿物质开始分 解,产生了 CO2 ,同时又被 C 还原生成 CO。
图 3 各温度区间产气速率
由图 3 可知,残渣热解的气体析出呈“两段式” 分布。500 ~ 550 ℃ 和 700 ~ 750 ℃ 为两个产气高峰 区,其产气速率分别为 1. 86 和 1. 89 L / min。 2. 2 液化残渣热解气组成
液化残渣热解气组成随温度变化如图 4 所示。 由图 4a) 可知,液化残渣热解气中 CH4 和 Cm Hn 体积 分数随温度升高都呈先增加后减少的趋势。一般认 为,CH4 来自煤结构中脂肪—CH 侧链的断裂,温度 为 600 ℃ 时,CH4 体积分数最高为 23. 8% ; 而 Cm Hn 来自煤大分子结构的裂解过程[8 - 9],温度为 500 ℃ 时,CmHn体积分数最高为 7. 7% 。500 ~ 600 ℃ 时煤 结构裂解速率最大[10]。可见,残渣中仍有类似煤的 结构存在,且仍含有较丰富的脂肪—CH 侧链。
图 2 热解累计产气量随温度变化
图 1 固定床管式炉热解及色谱分析示意
1. 3 实验方法 煤气产率为单位质量残渣的产气量,即从开始
升温到实验结束得到的总产气量除以热解用残渣总 质量。析出速率为 400 ~ 900 ℃ 内,从 400 ℃ 开始, 每隔 50 ℃ 的热解温度区间内每分钟平均产气量。
采用 SP2100 - A 气相色谱仪对气体组成进行 分析。由 TCD 热导填充柱检测 CO、CO2 、H2 含量。 由 FID 氢火焰毛细柱检测 CH4 、Cm Hn ( C2 H2 、C2 H4 、 C2 H6 、C3 H8 、正 C4 H10 、异 C4 H10 ) 含量。从 400 ~ 900 ℃ ,每隔 50 ℃ 集取一个热解气样本进行色谱分析。
ω( Odaf ) 1. 86
ω( Sdaf ) 2. 95
H/C 0. 62
1. 2 实验装置 固定床管式炉实验装置如图 1 所示。实验采用
液化残渣粒度为 6 ~ 13 mm,进料量为 600 g,升温速 率为 5 ℃ / min,热解温度为 400 ~ 900 ℃ 。热解升温 前,通入 N2 排出管式炉内空气。
2 结果与讨论
2. 1 液化残渣热解气产率及析出速率 热解累计产气量随温度变化如图 2 所示,各温
度区间产气速率如图 3 所示。 由图 2 可知,400 ℃ 前,气体析出量较少,从开
始升温至 400 ℃ ,共析出气体 8. 8 L; 从 400 ~ 900 ℃ ,产气量为 134. 8 L; 全程共析出气体 143. 6 L,则 600 g 残渣热解的平均煤气产率为 0. 2393 L / g。
0引 言
中国石油资源紧缺,煤炭资源丰富,煤直接液化 制油是解决中国能源格局的有利途径。目前,中国 神华集 团 已 成 功 实 现 了 煤 制 油 的 工 业 化 生 产[1]。 煤在催化剂、一定温度和压力条件下,加氢液化可制 得油产品[2],也会得到占液化用煤 30% 左右的液化
残 渣。 这 种 残 渣 是 一 种 高 炭、高 灰 和 高 硫 物 质,含 40% ~ 50% 固体物质,30% 重质油,其余为沥青烯和 前沥青烯[3 - 4]。
煤直接液化过程会不可避免地产生液化残 渣[5]。煤直接液化残渣具有很高的利用价值,无论 从经济角度还是环保角度出发,都需对其进行清洁、 高效、合理利用。目前已开发的残渣利用方法有直
收稿日期: 2013 - 12 - 11; 责任编辑: 宫在芹 DOI: 10. 13226 / j. issn. 1006 - 6772. 2014. 02. 022 基金项目: 国家自然科学基金资助项目( U1261101) 作者简介: 常 松( 1988—) ,男,辽宁抚顺人,在读硕士,研究方向为煤炭转化。E - mail: changsong323@ 126. com 引用格式: 常 松,初 茉,曹文瀚,等. 煤直接液化残渣热解气体析出规律研究[J]. 洁净煤技术,2014,20( 2) : 84 - 86.