表面工程-热喷涂1
表面工程学五.喷涂

二、热喷涂技术的分类及其特点 1 热喷涂技术的分类 按热源分类,各喷涂方法的焰流温度和粒子速度不同。
热喷涂技术的特点 (1) 可在各种基材上制备各种涂层; (2) 基材温度低(30 ~ 200℃),热影响区浅,变形小;
(3) 涂层厚度范围宽(0.5
~
5mm) ;
(4) 操作灵活,可在不同尺寸和形状的工件上喷涂; (5) 加热效率低,喷涂材料利用率低, (6) 涂层与基体结合强度低。
热喷涂材料分类(金属类,表1-3)
金属类 分 类 品 种 纯金属 合 金 Sn、Pb、Zn、A1、Cu、Ni、W、Mo、Ti 等 (1)Ni 基合金:Ni-Cr、Ni-Cu;(2)Co 基合金:CoCrW (3)MCrAlY 合金:NiCrAlY,CoCrAlY、FeCrAlY (4)不锈钢;(5)铁合金;(6)铜合金;(7)铝合金 (8)巴氏合金;(9)Triballoy 合金 自熔性合金 (1)Ni 基自熔性合金:NiCrBSi、NiBSi (2)Co 基自熔性合金:CoCrWB、CoCrWBNi (3)Fe 基自熔性合金:FeNiCrBSi (4)Cu 基自熔性合金
热喷涂材料的要求
(1)热稳定性好,在高温焰流中不升华,不分解(复合粉末)。 (2) 有较宽的液相区,使熔滴在较长时间内保持液相。 (3)与基材有相近的热膨胀系数,以防止因膨胀系数相差过 大产生较大的热应力。 (4) 喷涂材料在熔融状态下应和基材有较好的浸润性,以保 证涂层与基材之间有良好的结合性能。
4) 压缩空气压力和流量:影响喷涂材料的雾化效果和熔粒的飞 行速度,对涂层的质量有很大的影响。 5) 喷涂距离应控制在100~200mm,喷涂角不应小于45°。
(3) 电弧喷涂的用途
1) 在钢铁构件上喷涂锌、铝涂层,对构件进行长效防护。 2) 在钢铁件上喷铝可防止高温氧化。
热喷涂加工

热喷涂加工热喷涂加工是一种广泛应用于工业生产领域的表面处理技术。
它通过将材料加热至熔点,然后高速喷射而形成的覆盖层,可以为工件提供耐磨、耐蚀、导热等特性,从而延长其使用寿命和提高性能。
本文将从热喷涂加工的原理、应用领域以及优势等方面进行探讨。
首先,我们来了解一下热喷涂加工的原理。
热喷涂加工主要通过喷涂设备将加热的材料喷射到待加工工件的表面上,形成一层覆盖层。
这个过程中,喷涂设备中的粉末或线材会被加热到熔点,然后通过高速气体流将其喷射到工件表面。
喷涂后,覆盖层会迅速冷却,形成致密的表面涂层。
热喷涂加工的应用领域非常广泛。
它可以用于加工金属、陶瓷、复合材料等多种材料。
在航空航天、汽车制造、电力工业、石油化工等行业中,热喷涂加工被广泛应用于各种工件的修复、保护和改性。
比如,在航空航天领域,热喷涂加工可以修复发动机叶片上的磨损、修补涡轮叶盘、提高涡轮增压器的性能等。
在汽车制造业中,热喷涂加工可以提高汽车部件的耐腐蚀性和耐磨性。
在电力工业中,热喷涂加工可以延长电站设备的使用寿命,提高其耐高温、耐磨等性能。
可以说,热喷涂加工在现代工业领域中起着至关重要的作用。
热喷涂加工相比其他表面处理技术具有一些独特的优势。
首先,热喷涂加工可以在低温条件下进行,避免了工件热影响区的形成。
这对于对热敏感的工件来说尤为重要。
其次,通过控制喷涂工艺参数,可以得到不同性能的涂层。
可以通过选择不同的材料、粒度和喷涂参数来调节涂层的硬度、粗糙度、粘附性等特性。
此外,热喷涂加工还可以应用于大尺寸工件的加工,具有较高的工艺灵活性和适用性。
在使用热喷涂加工技术时,需要注意一些问题。
首先,必须选择适合工件要求的喷涂材料。
材料的选择应根据工作环境、工件材料和使用要求来确定。
其次,需要合理控制喷涂参数,包括气体流速、加热功率等,以确保获得良好的涂层质量。
此外,对于较复杂的工件形状,还需要进行喷涂前的设计和模拟,以确保涂层的均匀性和一致性。
最后,还需要进行严格的质量控制和检测,以确保喷涂涂层的质量满足要求。
热喷涂技术及其应用讲解

4. 热喷涂工艺
热喷工艺过程如下:工件表面预处理 工件预热 喷涂 涂层后处理
1. 表面预处理
为了使涂层与基体材料很好地结合,基材表面必须清洁及粗糙. 净化处理的目的是除去工件表面的所有污垢, 方法有溶剂清洗法、蒸汽清 洗法、碱洗法及加热脱脂法等. 粗化处理的目的是增加涂层与基材间的接触面, 增大涂层与基材的机械咬 合力, 使净化处理过的表面更加活化,以提高涂层与基材的结合强度. 粗化处 理的方法有喷砂、机械加工法(如车螺纹、滚花)、电拉毛等。其中喷砂处 理是最常用的粗化处理方法,常用的喷砂介质有氧化铝、碳化硅和冷硬铸 铁等。多数工件表面的2.5-13 mRa就够了。 对于一些与基材粘结不好的涂层材料, 还应选择一种与基体材料粘结好 的材料喷涂一层过渡层,称为粘结底层,常用作粘结底层的材料有Mo、NiAl 、NiCr及铝青铜等.粘结底层的厚度一般为0.08-0.18m。
3. 硬度
由于热喷涂涂层在形成时的激冷和高速撞击,涂层晶粒细化以及晶格产生畸变使 涂层得到强化,因而热喷涂涂层的硬度比一般材料的硬度要高一些,其大小也会因 喷涂方法的不同而有所差异。
中海石油炼化有限责任公司
热喷涂涂层的性能
4. 结合强度
热喷涂涂层与基体的结合主要依靠与基体粗糙表面的机械咬合 (抛描效应)。基材表面的清洁程度、涂层材料的颗粒温度和颗粒 撞击基体的速度以及涂层中残余应力的大小均会影响涂层与基体的 结合强度,因而涂层的结合强度也与所采用的喷涂方法有关。
中海石油炼化有限责任公司
利用热源将涂层材料加热到熔融或者半熔融状态,借 助焰流及高速气体将涂层材料粒子喷射到基体表面, 获得沉积成具有某种特殊功能涂层。
中海石油炼化有限责任公司
表面涂敷技术

表面涂敷技术1.1热喷涂热喷涂是一种采用专用设备利用热源(可以是然烧热、电弧、等离子弧、激光等)将金属或非金属材料加热到熔化或半熔化状态,用高速气流将其吹成极微小颗粒(雾化)并喷射沉积到经过预处理的工件表面,形成覆盖层,以提高机件耐蚀、耐磨、耐热等性能的表面工程技术。
热喷涂技术最突出的特点:方法的多样性、制备涂层的广泛性、应用的经济性1.2热喷涂的一般原理喷涂材料在热源中的被加热过程和颗粒与基材表面的结合过程是热喷涂技术制备涂层的关键环节。
从喷涂材料进入热源到形成涂层,喷涂过程一般经历四个阶段:1、喷涂材料被加热熔化2、熔化的喷涂材料被雾化粉末一般不存在熔粒被进一步破碎和雾化的过程,而是被气流或热源射流推向前喷射。
3、熔融或软化的微细颗粒的喷射飞行4、粒子在基材表面发生碰撞、变形、凝固和堆积1.3热喷涂技术的分类及特点目前还没有标准的热喷涂分类法,一般是根据所用热源的不同来分类,分为燃气法、气体放电法、电热法和激光热源法。
1.4热喷涂材料热喷涂材料按按分为线材、棒材、粉末和高分子材料做成的长柔性管中装有各种性能粉末的管材;按组成成分可分为:金属、合金、自熔性合金、复合材料、陶瓷和有机塑料等等。
下面我们重点介绍几种喷涂方法。
1、火焰喷涂①原理火焰喷涂历史最为悠久,它是利用气体燃烧放出的热实现热喷涂,目前被广泛采用的是氧乙炔火焰线材和粉末火焰喷涂。
一般说来,凡在2760℃以下温度区内不升华、能熔化的任何物质均可采用火焰喷涂获得涂层,但实际上熔点超过2500℃的材料很难用火焰进行喷涂。
②工艺火焰喷涂工艺流程为:工件表面准备——预热——喷涂打底层——喷涂工作层——喷后处理2、等离子喷涂①原理正常状态下原子呈中性,气体在常温下是不导电的,但当外界通过某种方式给予气体分子或原子以足够的能量时,就可使电子脱离原子而成为自由电子,而使原子或分子成为常电的正离子,也就是气体产生电离现象。
使气体产生电离的因素很多,如热电离、光电离等。
表面工程-热喷涂
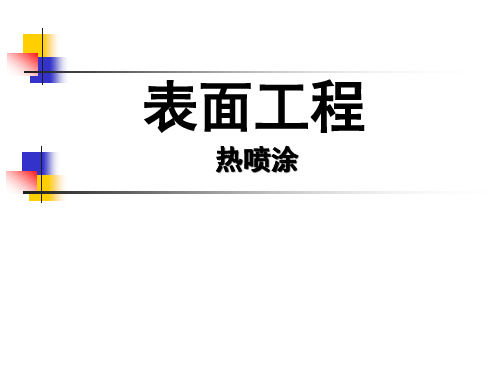
2、热喷涂的分类
(1)喷涂材料的形态: 丝材、粉末
(2)涂层的功能: 耐蚀、耐磨、隔热、抗氧化
(3)加热和结合方式: 喷涂、喷熔(喷涂+熔化,冶金结合)
(4)按照热源种类:
火焰类:包括火焰、爆炸、超音速喷涂 电弧类:电弧和等离子喷涂 电热类:电爆、感应和电容放电喷涂 高能束类:激光、电子束喷涂
机械法(喷砂、滚压、车削、车螺纹)、酸洗 预热基体
200~300℃
获得良好结合涂层要求:
①喷涂粒子尺寸合适,保持液态; ②飞行速度足够大; ③基体表面洁净并粗化; ④提高接触温度和高温停留时间; ⑤防止产生残余变形、开裂。
4.3 热喷涂方法
1、丝材火焰喷涂(Wire Flame Spray,最早,1910)
(2)扩散结合
➢ 变形和高温,足够能量原子间相互扩散→金属化 合物或固溶体
(3)物理结合
➢ 由范德华力或次价键形成的结合
(4)冶金结合
➢ 放热型喷涂材料或高温热源喷涂→达到熔点→焊合 微区冶金结合
➢ 重熔即喷焊时,主要是冶金结合
2.涂层间的结合
机械结合为主,扩散结合、物理结合、冶金 结合等也起一定作用。
2. 涂层的形成过程
由不断飞向基体表面的粒子撞击基体或涂层表面 堆积而成
即,粒子的碰撞→变形→冷凝收缩
➢冷速极高:106~108℃/s 金属 104~106℃/s 陶瓷
10-7~10-6s完成
➢ 两粒子撞击时间间隔0.1s左右
涂层材料的加热、加速、凝固是三个最 主要方面。
(1)希望涂层材料完全熔化,并保持到 撞击基体前;
3.热喷涂特点
①涂层材料取材范围广 金属、合金、陶瓷、塑料、尼龙、复合材料等。
热喷涂
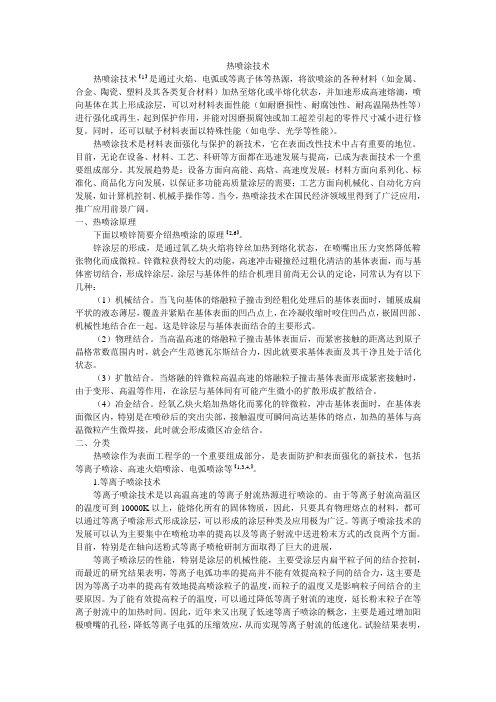
热喷涂技术热喷涂技术【1】是通过火焰、电弧或等离子体等热源,将欲喷涂的各种材料(如金属、合金、陶瓷、塑料及其各类复合材料)加热至熔化或半熔化状态,并加速形成高速熔滴,喷向基体在其上形成涂层,可以对材料表面性能(如耐磨损性、耐腐蚀性、耐高温隔热性等)进行强化或再生,起到保护作用,并能对因磨损腐蚀或加工超差引起的零件尺寸减小进行修复。
同时,还可以赋予材料表面以特殊性能(如电学、光学等性能)。
热喷涂技术是材料表面强化与保护的新技术,它在表面改性技术中占有重要的地位。
目前,无论在设备、材料、工艺、科研等方面都在迅速发展与提高,已成为表面技术一个重要组成部分。
其发展趋势是:设备方面向高能、高焓、高速度发展;材料方面向系列化、标准化、商品化方向发展,以保证多功能高质量涂层的需要;工艺方面向机械化、自动化方向发展,如计算机控制、机械手操作等。
当今,热喷涂技术在国民经济领域里得到了广泛应用,推广应用前景广阔。
一、热喷涂原理下面以喷锌简要介绍热喷涂的原理【2,6】。
锌涂层的形成,是通过氧乙炔火焰将锌丝加热到熔化状态,在喷嘴出压力突然降低鞥张物化而成微粒。
锌微粒获得较大的动能,高速冲击碰撞经过粗化清洁的基体表面,而与基体密切结合,形成锌涂层。
涂层与基体件的结合机理目前尚无公认的定论,同常认为有以下几种:(1)机械结合。
当飞向基体的熔融粒子撞击到经粗化处理后的基体表面时,铺展成扁平状的液态薄层,覆盖并紧贴在基体表面的凹凸点上,在冷凝收缩时咬住凹凸点,嵌固凹部、机械性地结合在一起。
这是锌涂层与基体表面结合的主要形式。
(2)物理结合。
当高温高速的熔融粒子撞击基体表面后,而紧密接触的距离达到原子晶格常数范围内时,就会产生范德瓦尔斯结合力,因此就要求基体表面及其干净且处于活化状态。
(3)扩散结合。
当熔融的锌微粒高温高速的熔融粒子撞击基体表面形成紧密接触时,由于变形、高温等作用,在涂层与基体间有可能产生微小的扩散形成扩散结合。
建筑外墙石材热喷涂施工工序
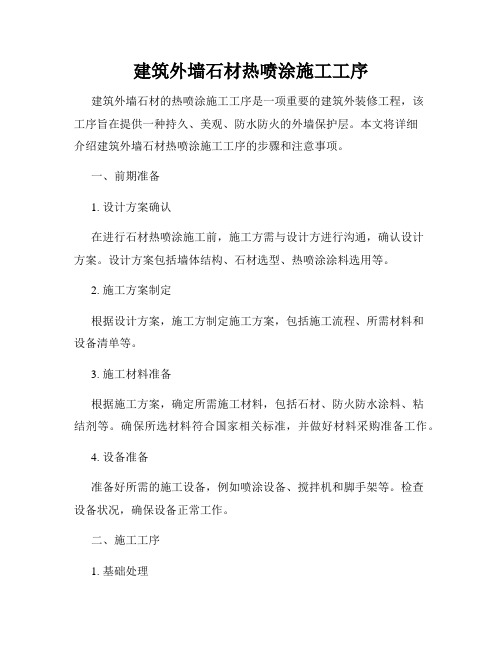
建筑外墙石材热喷涂施工工序建筑外墙石材的热喷涂施工工序是一项重要的建筑外装修工程,该工序旨在提供一种持久、美观、防水防火的外墙保护层。
本文将详细介绍建筑外墙石材热喷涂施工工序的步骤和注意事项。
一、前期准备1. 设计方案确认在进行石材热喷涂施工前,施工方需与设计方进行沟通,确认设计方案。
设计方案包括墙体结构、石材选型、热喷涂涂料选用等。
2. 施工方案制定根据设计方案,施工方制定施工方案,包括施工流程、所需材料和设备清单等。
3. 施工材料准备根据施工方案,确定所需施工材料,包括石材、防火防水涂料、粘结剂等。
确保所选材料符合国家相关标准,并做好材料采购准备工作。
4. 设备准备准备好所需的施工设备,例如喷涂设备、搅拌机和脚手架等。
检查设备状况,确保设备正常工作。
二、施工工序1. 基础处理清洁墙体表面,去除油污、尘土等杂物。
如发现墙体裂缝或缺陷,应及时修复。
2. 石材安装按照设计方案和客户要求,在基础处理后,安装石材。
使用适当的工具和材料,确保石材安装牢固平整。
3. 施工准备喷涂施工前,需将喷涂设备和喷嘴进行清洁,并检查是否运行正常。
准备好热喷涂涂料,加热至适当温度。
4. 热喷涂施工将已热化的喷涂涂料从喷涂设备中均匀地喷洒在石材表面。
要求施工人员掌握好喷涂距离和角度,确保喷涂均匀,防止出现漏喷或堆积现象。
5. 涂料固化热喷涂后,涂料需要进行一定时间的固化。
在固化过程中,应注意保持施工现场的干燥和通风,避免涂料受潮或受到其他不良环境因素的影响。
三、注意事项1. 安全措施施工人员应穿戴好相关的个人防护装备,如手套、口罩和安全帽等。
确保施工现场的安全,避免发生意外事故。
2. 质量控制施工过程中,应进行质量检查和验收。
检查石材表面是否存在开裂、渗漏等问题,确保施工质量符合相关要求。
3. 环境保护施工现场应做好环境保护工作,避免喷涂涂料污染周围环境。
未使用的涂料和废料应妥善处理,不可随意倾倒。
结语建筑外墙石材热喷涂施工工序的正确进行对于保证外墙质量至关重要。
热喷涂综述 一、热喷涂的定义 热喷涂技术,是采用某种高温热源,将欲涂

热喷涂综述一、热喷涂的定义热喷涂技术,是采用某种高温热源,将欲涂覆的涂层材料熔化或至少软化,并用气体使之雾化成微细液滴或高温颗粒,高速喷射到经过预处理的基体表面形成涂层的技术。
当热源的比能量足以使基体表面发生薄层熔化,与喷射的熔融颗粒形成完全致密的冶金结合涂层时,称为热喷焊,简称喷焊。
使用高温热源,如氧——可燃气体燃烧火焰、电弧、等离子电弧、激光束、爆炸能等,是热喷涂技术区别于其他喷涂方法和表面涂覆方法的主要特征。
不同热源的最高温度列于附表。
附表:不同热源的最高温度二、热喷涂技术的特点采用热喷涂技术,制备各种表面强化和表面防护涂层,具有许多独特的优点:(1)能够喷涂的材料范围特别广,包括各种金属及合金、陶瓷及金属陶瓷、塑料、非金属矿物等几乎所有固态工程材料。
因而能够制备耐磨、减摩、耐蚀、耐高温、抗氧化、绝缘、导电、催化、辐射、防辐射、抗干扰、超导、非晶态及生物功能等各种功能涂层;(2)能够在多种基体材料上形成涂层,包括金属基体、陶瓷基体、塑料基体、石膏、木材甚至纸板上都能喷涂,被喷涂的材料范围也十分广泛;(3)一般不受被喷涂工件尺寸和施工场所的限制,既可厂内施工,也可现场施工;(4)涂层沉积效率较高,特别适合沉积薄膜涂层。
涂层厚度可以控制,从几十微米到几毫米甚至可厚达 20mm;(5)除喷焊外,热喷涂施工对基体的热影响很小,基体受热温度不超过200℃,基体不会发生变形和性能变化;(6)在满足强度要求的前提下,制件基体可以采用普通材料代替贵重材料,仅涂层使用优质材料,使“好钢用在刀刃上”;(7)热喷涂施工艺灵活,方便,迅速,适应性强。
当然,热喷涂技术也有如下一些缺点:(1)除喷焊外,热喷涂涂层与基体的结合主要是物理机械结合,结合强度不大高,涂层耐冲击和重载性能较差;(2)喷涂涂层含有不同程度的孔隙,对于耐腐蚀、抗氧化、绝缘等应用,一般不如整体材料。
但可通过复合涂层系统设计等方法予以改进提高;(3)喷涂小件时,涂层材料的收得率低;(4)热喷涂手工操作时的劳动条件较差,有噪音、粉尘、热和弧光辐射问题,必须注意劳动保护措施。
热喷涂技术
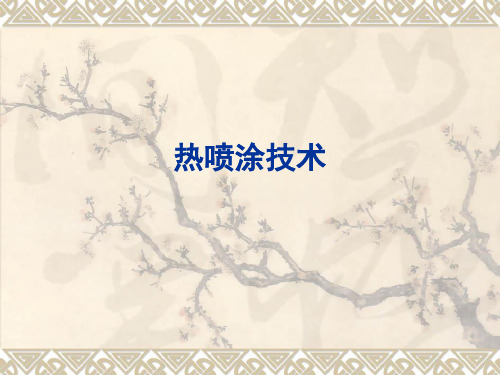
粉末火焰喷涂法:它与丝材火焰喷涂的不同之处是喷 涂材料不是丝材而是粉末。图3和图4分别为粉末火焰 喷涂装置和原理示意图。
图3 粉末火焰喷涂装置
图4 粉末火焰喷涂原理示意图
在火焰喷涂中通常使用乙炔和氧组合燃烧而提供热 量,也可以用甲基乙炔,丙二烯(MPS),丙烷,氢气 或天然气。火焰喷涂可喷涂金属,陶瓷,塑料等材 料,应用非常灵活,喷涂设备轻便简单,可移动, 价格低于其他喷涂设备,经济型好,是目前喷涂技 术中使用较广泛的一种方法。但是,火焰喷涂也存 在明显的不足。如喷出的颗粒速度较小,火焰温度 较低,涂层的粘结强度及涂层本身的综合强度都比较 低,且比其他方法得到的气孔率多
五 激光法 把高密度能量的激光束朝着接近于零件的基体 表面的方向直射,基体同时被一个辅助的激光加热 器加热,这时,细微的粉末以倾斜的角度被吹送到 激光束中。图9激光喷涂 熔化粘结到基体表面,形成了一层薄的表面涂 层,与基体之间形成良好的结合(喷涂环境可选择 大气气氛或惰性气体气氛,或真空下进行)。
⑤涂层表面粗糙度低。 ⑥喷涂距离可在较大范围内变动,而不影响 喷涂质量。 ⑦可得到比爆炸喷涂更厚的涂层,残余应力 也得到改善。 ⑧喷涂效率高,操作方便。 ⑨噪音大(大于120dB),需有隔音和防护 装置。
三 电弧类喷涂
1、电弧喷涂:
电弧喷涂:在两根焊丝状的金属材料之间产生 电弧,因电弧产生的热使金属焊丝逐渐熔化,熔化 部分被压缩空气气流喷向基体表面而形成涂层。电 弧喷涂按电弧电源可分为直流电弧喷涂和交流电弧 喷涂。直流:操作稳定,涂层组织致密,效率高。 交流:噪音大。电弧产生的温度与电弧气体介质、 电极材料种类及电流有关(如Fe料,电流280安,电 弧温度为6100K)。但一般来说,电弧喷涂比火焰喷 涂粉末粒子含热量更大一些,粒子飞行速度也较快, 因此,熔融粒子打到基体上时,形成局部微冶金结 合的可能性要大的多
热喷涂再制造技术(初稿)

热喷涂再制造技术1 概述1.热喷涂是一种材料表面强化和表面改性的新技术,是表面工程技术的重要组成部分,一直是我国重点推广的新技术项目.它是利用某种热源(如电弧、等离子喷涂或燃烧火焰等)将粉末状或丝状的金属或非金属材料加热到熔融或半熔融状态,然后借助焰留本身或压缩空气以一定速度喷射到预处理过的基体表面,沉积而形成具有各种功能的表面涂层的一种技术。
它可以使基体表面具有耐磨、耐蚀、耐高温氧化、电绝缘、隔热、防辐射、减磨、密封等性能。
原则上讲可在任何固体物质上喷涂。
可喷涂的材料有金属、合金、塑料、陶瓷、金属陶瓷以及它们的复合物等等。
热喷涂技术的应用主要包括:长效防腐、机械修复及先进制造技术、模具制作与修复、制造特殊的功能涂层等四个方面。
目前,热喷涂技术已广泛应用于几乎所有工业领域以及家庭用品(如不粘锅、红外线保健电热器等)。
2.热喷涂原理:热喷涂是指一系列过程,在这些过程中,细微而分散的金属或非金属的涂层材料,以一种熔化或半熔化状态,沉积到一种经过制备的基体表面,形成某种喷涂沉积层。
涂层材料可以是粉状、带状、丝状或棒状。
热喷涂枪由燃料气、电弧或等离子弧提供必需的热量,将热喷涂材料加热到塑态或熔融态,再经受压缩空气的加速,使受约束的颗粒束流冲击到基体表面上。
冲击到表面的颗粒,因受冲压而变形,形成叠层薄片,粘附在经过制备的基体表面,随之冷却并不断堆积,最终形成一种层状的涂层。
该涂层因涂层材料的不同可实现耐高温腐蚀、抗磨损、隔热、抗电磁波等功能,如下图所示。
3.定义:热喷涂是指采用氧—乙炔焰、电弧、等离子弧、爆炸波等提供不同热源的喷涂装置,产生高温高压焰流或超音速焰流,将要制成涂层的材料如各种金属、陶瓷、金属加陶瓷的复合材料、各种塑料粉末的固态喷涂材料,瞬间加热到塑态或熔融态,高速喷涂到经过预处理(清洁粗糙)的零部件表面形成涂层的一种表面加工方法。
我们把特殊的工作表面叫“涂层”,把制造涂层的工作方法叫“热喷涂”,它是采用各种热源进行喷涂和喷焊的总称。
热喷涂技术的原理及应用实验报告

热喷涂技术的原理及应用实验报告一、引言热喷涂技术是一种常用的表面涂覆技术,通过高速喷射热能将粉末或线状材料熔化,并在基材表面形成涂层。
本文将介绍热喷涂技术的原理以及在实验中的应用情况。
二、热喷涂技术的原理热喷涂技术基于热能喷射原理,通过将热能引入喷枪中,使喷口处的涂层材料达到熔化状态,然后以高速喷射到基材表面。
热喷涂技术主要包括燃烧喷涂和等离子喷涂两种方式。
2.1 燃烧喷涂原理燃烧喷涂是利用火焰的高温将涂层材料加热至熔化状态的技术。
其原理可以分为两个步骤:1.燃烧产生高温火焰:在喷涂枪中,燃烧剂和氧气混合燃烧产生高温火焰。
这种高温火焰可以使涂层材料达到熔化状态。
2.喷涂涂层:熔化状态的涂层材料通过高速喷射到基材表面,形成一层均匀的涂层。
涂层在快速冷却后变得致密,并具有良好的附着力。
2.2 等离子喷涂原理等离子喷涂是利用电弧放电将涂层材料加热至熔化状态的技术。
其原理可以分为三个步骤:1.弧电离气体:在喷涂枪中,高压电源产生电弧,将气体电离,形成等离子体。
等离子体产生的高温可以使涂层材料达到熔化状态。
2.喷涂涂层:熔化状态的涂层材料通过高速喷射到基材表面,形成一层均匀的涂层。
等离子体的高温状态有利于涂层材料的熔化和喷射。
3.冷却和固化:涂层在快速冷却后变得致密,并具有良好的附着力。
三、热喷涂技术的应用实验3.1 实验目的本实验旨在研究热喷涂技术在材料表面涂覆方面的应用情况,并对涂层性能进行评估。
3.2 实验材料和设备实验材料:使用钴基和铝基合金粉末作为涂层材料。
基材使用不锈钢板。
实验设备:燃烧喷涂设备和等离子喷涂设备。
3.3 实验步骤1.准备基材:将不锈钢板进行表面处理,保证其干净无杂质。
2.准备涂层材料:将钴基和铝基合金粉末进行筛选和混合。
3.燃烧喷涂实验:将喷涂枪调整到适当位置,控制喷涂距离和喷涂速度,进行燃烧喷涂实验。
4.等离子喷涂实验:将喷涂枪调整到适当位置,控制喷涂距离和喷涂速度,进行等离子喷涂实验。
热喷涂行业知识
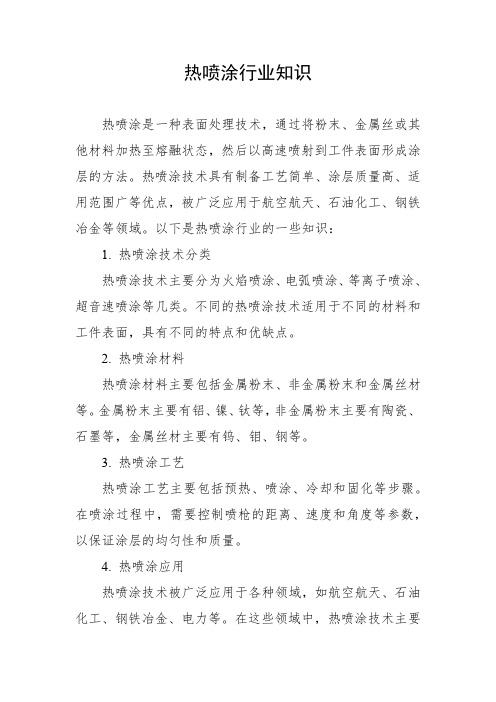
热喷涂行业知识
热喷涂是一种表面处理技术,通过将粉末、金属丝或其他材料加热至熔融状态,然后以高速喷射到工件表面形成涂层的方法。
热喷涂技术具有制备工艺简单、涂层质量高、适用范围广等优点,被广泛应用于航空航天、石油化工、钢铁冶金等领域。
以下是热喷涂行业的一些知识:
1. 热喷涂技术分类
热喷涂技术主要分为火焰喷涂、电弧喷涂、等离子喷涂、超音速喷涂等几类。
不同的热喷涂技术适用于不同的材料和工件表面,具有不同的特点和优缺点。
2. 热喷涂材料
热喷涂材料主要包括金属粉末、非金属粉末和金属丝材等。
金属粉末主要有铝、镍、钛等,非金属粉末主要有陶瓷、石墨等,金属丝材主要有钨、钼、钢等。
3. 热喷涂工艺
热喷涂工艺主要包括预热、喷涂、冷却和固化等步骤。
在喷涂过程中,需要控制喷枪的距离、速度和角度等参数,以保证涂层的均匀性和质量。
4. 热喷涂应用
热喷涂技术被广泛应用于各种领域,如航空航天、石油化工、钢铁冶金、电力等。
在这些领域中,热喷涂技术主要
用于强化金属表面性能、提高耐腐蚀性、耐磨损性和导电性等。
总之,热喷涂技术是一种表面处理技术,具有制备工艺简单、涂层质量高、适用范围广等优点,被广泛应用于航空航天、石油化工、钢铁冶金等领域。
热喷涂行业的发展前景广阔,未来将会有更多的创新和应用。
火焰喷涂

4
SQP-1型线材火焰喷枪外形图 1—混合头部分 2—送丝滚轮 3—导丝管 4— 阀杆旋钮 5—调速旋盘 6—机动部分 7—手柄
LEE MAN (SCETC)
表面工程与热喷涂
5
线材火焰喷涂的典型装置示意图
LEE MAN (SCETC)
表面工程与热喷涂
6
(二)粉末火焰喷涂法
线材火焰喷涂---以氧气、乙炔(丙烷)火焰为热源,将粉末材料熔 融后喷射在加工物表面形成涂层的热喷涂法,以自熔合金为材料的 粉末火焰喷涂法称为粉末喷涂。
LEE MAN (SCETC)
表面工程与热喷涂
12
4.喷后处理
喷后处理的目的: 密封火焰喷涂层的孔结构,防止腐蚀性介质渗入 涂层,从而对基体造成腐蚀,对在腐蚀条件下工作的 涂层和防腐涂层的性能产生不利影响。 喷后处理的方法:采用封孔剂封孔 常用的封孔剂有石蜡、酚醛树脂和环氧树脂等。密封石 蜡应使用有明显熔点的微结晶石蜡,而不是没有明显熔点 的普通石蜡。酚醛树脂封孔剂适用于密封金属及陶瓷涂层 的孔隙,这种封孔剂具有良好的耐热性,在200℃以下可连 续工作,且除强碱外,能耐大多数有机化学试剂的腐蚀。
LEE MAN (SCETC)
表面工程与热喷涂 水闸门喷涂锌的工艺:
表面预处理
采用粒径为0.5~2MM的硅砂对水闸门的喷涂表面进行喷砂 处理、去污、防锈,并且粗化水闸门表面。 喷涂时使用SQP-1型火焰喷枪,用锌丝喷涂材料。为保证涂层 质量及其与结构的结合强度,喷涂过程中,应严格控制氧和乙 炔的比例和压力,使火焰为中性焰或稍偏碳化焰。
涂层均匀,厚度容易控制
涂层均匀,厚度容易控制,爆炸喷涂的涂层厚度一 般为0.025~0.3mm,涂层粗糙度可小于Ra1.60,经 磨削后可达Ra0.025。
热喷涂原理及介绍

热喷涂原理及介绍1.热喷涂原理及介绍热喷涂技术是表面工程领域的重要技术之一,它的原理是利用各种不同的热源,将预喷涂的各种材料如金属、合金、陶瓷、塑料及其各类复合材料加热至熔化或熔融状态,借助气流的高速雾化形成微粒雾流沉积在已预处理的工件表面形成堆积状,与基体紧密结合的涂层。
而将Ni-Cr-B-Si系列喷涂层进行重熔处理形成的具有冶金结合特征的涂层称为喷熔层或重熔层。
热喷涂技术可用来喷涂几乎所有的固体工程材料,如硬质合金、陶瓷、金属、石墨和尼龙等,形成耐磨、耐蚀、隔热、抗氧化、绝缘、导电、防辐射等具有各种特殊功能的涂层。
该技术还具有工艺灵活、施工方便、适应性强及经济效益好等优点,被广泛应用于宇航、机械、化工、冶金、地质、交通、建筑等工业部门,并获得了迅猛的发展。
从喷涂材料进入热源到形成涂层称喷涂过程,一般经历四个阶段既加热、雾化、飞行和沉积。
首先是喷涂材料被加热熔化或软化阶段。
当端部材料进入热源的高温区域,即被加热,形成熔滴,进而形成的熔滴,在外加压缩气流或热源自身射流的作用下,雾化成细微的熔粒。
第二阶段熔粒流飞行过程中,被加速。
当这些具有一定温度和速度的颗粒以一定的动能冲击基材表面,产生强烈的碰撞,在碰撞瞬间,颗粒的动能转化成热能传给基材,并沿凹凸不平的表面产生变形,变形的颗粒迅速冷凝并产生收缩,呈扁平状连续不断地沉积在基材表面,从而形成涂层。
众所周知,除少数贵金属外,金属材料会与周围介质发生化学反应和电化学反应而遭受腐蚀。
此外,金属表面受各种机械作用而引起的磨损也极为严重,大量的金属构件因腐蚀和磨损而失效,造成极大的浪费和损失。
据一些工业发达国家统计,每年钢材因腐蚀和磨损而造成的损失约占钢材总产量的10%,损失金额约占国民经济总产值的2-4%。
如果将因金属腐蚀和磨损而造成的停工、停产和相应引起的工伤、失火、爆炸事故等损失统计在内的话,其数值更加惊人。
因此,发展金属表面防护和强化技术,是各国普遍关心的重大课题。
表面工程知识总结(热喷涂)
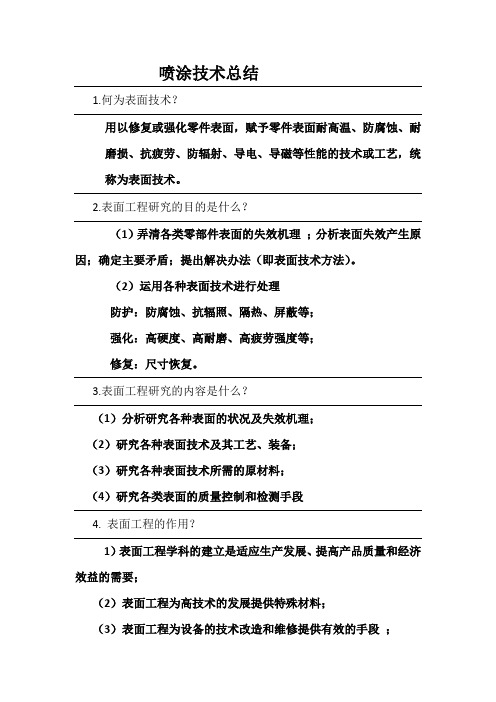
5.钢铁行业
锌浴轧辊 涂层性能: 防止粘附轧辊表面的锌渣 \降低锌的扩散 \提高耐磨 损性 \优化密封技术 特点 :提高了导辊的寿命 \改进了钢带的表面质量 炉底辊 涂层性能 :防止钢带因铁的氧化而被破坏 \抗氧化性和耐磨性温 度提高到 1100℃ 特点 :多层陶瓷层 \优化的密封技术
热喷涂材料的应用
10,上图喷涂工艺工程中,对气体的使用有什么样的要求,最高
的温度能够到达多少,喷涂材料有什么要求,喷涂对象为什么材料, 气体的速率能够达到多少,沉积速率?
a. 高温, 高能量密度 b. 高速 c. 稳定 d. 适用性广 100 ~ 700m/s
20000K;
105 ~ 106 W/cm2
被压缩的, 高Leabharlann 离子化, 稳定的电压和电流 几乎所有的材料
2.涡轮机中的应用
空气叶片:防腐蚀涂层 涂层能提高效率
刷涂 Al
电镀不受欢迎
完善的技术和
外部和内部的空气密封 : 间隙控制\ 大气等离子喷涂应用于耐磨 系统 \ 提高效率 \ 工业燃气轮机的新兴技术
3.汽轮机中的使用?
燃 烧 室 及 过 度 部分 : 热障涂 层 \ 大气 等离 子喷 涂 , 部分 采 用 CVD/PVD\具有抗氧化性的 Ni/Al 或 MCrAlY 粘结层 \具有隔热功能 的 YSZ 层 \抵抗热应力 \提高效率 支撑架 : 耐磨覆层 \ 大气等离子或 HVOF 喷涂碳化物涂层或 Stellite™(WC-4Cr-10Co) \叶片 \防氧化及硫化 \控制气氛等离子或 超音速火焰 MCrAlY \广泛的应用 \在粘接层中可能存在铝偏聚 \超 音速火焰喷涂大量小型零件相对经济 \控制气氛等离子喷涂能提供 更长的保护 \单独的粘接涂层也有应用 \延缓热疲劳 \热障系统 \控 制气氛等离子喷涂 MCrAlY 与等离子喷涂 YSZ 表面层 \普遍只用于第 一阶级叶片 密封涂层和叶尖涂层 :大气等离子喷涂: 陶瓷/氮化硼/聚酯, 其中 粘结层采用 MCrAlY \叶尖直接切入基体中 \如同有密封材料的系统 一样工作 \工业燃气轮机的新兴材料 进气口、排气口以及外壳 :防腐蚀 \溶胶涂镀方法 轴、轴承、混合接触点 :硬镀铬 \超音速或等离子喷涂氮化物或 硬质合金 \超音速火焰喷涂优势 \更高的结合强度 能 \厚度增加 \更好的表面光洁度 \ 更好的耐磨性
材料表面工程第五章 堆焊与热喷涂技术

5.1 一 概述
堆焊:是借用焊接的手段对金属材料表面进行厚膜改质。 对本来是用一般材料制成的零件,通过堆焊一层高合金, 可使其性能得到明显的改善或提高。堆焊也是修复的方法
堆焊是一种熔焊工艺 ,堆焊就其物理本质和冶金过程 而言,具有焊接的一般规律,原则上已有的熔焊方法都可 以用于堆焊。
• (4)为防止工件变形,对批量较大的工件,应采用 专用工卡具,以防止变形。也可以采用预制反变 形法。对于工况条件为低应力磨料磨损的工件, 在基体表面堆焊成网格状焊道,就可以获得很高 的抗磨损性能,这样即可以降低成本,又可以防 止变形过大。
氧-乙炔堆焊
氧-乙炔火焰温度较低(3050~3100℃),火焰加热面 积大,可获得较低的稀释率(1﹪~10﹪),堆焊层厚度 较小,可在1㎜左右。氧-乙炔火焰尤其适用于堆焊碳化钨 管状焊丝,这种合金要求在堆焊时WC颗粒不熔化,这样 才能最好地发挥WC的耐磨性。
线材火焰喷涂
棒材火焰喷涂
气体燃烧热源
粉末火焰喷涂 超音速火焰喷涂
粉末火焰喷焊
热 喷 涂 方 法 的
气体放电热源
电弧喷涂 等离子喷涂
大气等离子喷涂
真空等离子喷涂 保护气氛等离子喷涂 水稳等离子喷涂 超音速等离子喷涂
种
等离子喷焊
类
电热热源
电容放电喷焊 感应加热喷涂
爆炸热源 激光热源
燃气重复爆炸喷涂 线材电爆喷涂
• (1)焊前清除工件表面上的油、锈。 • (2)将工件放平防止铁水流出。 • (3)用碳化焰将工件表面加热至半熔化温度,即呈现"出
汗"状态,此时添入堆焊材料进行堆焊。注意堆焊时不要 使母材完全熔化形成熔池。 • (4)堆焊时,焊丝和熔化区应处于还原焰的保护中,不得将 火焰急速移开,以防止堆焊金属氧化。 • (5)单层堆焊一般在2~3㎜厚,厚度不够时可用多层堆焊, 必要时可用火焰重熔堆焊层,以消除堆焊缺陷。
热喷涂过程记录范文
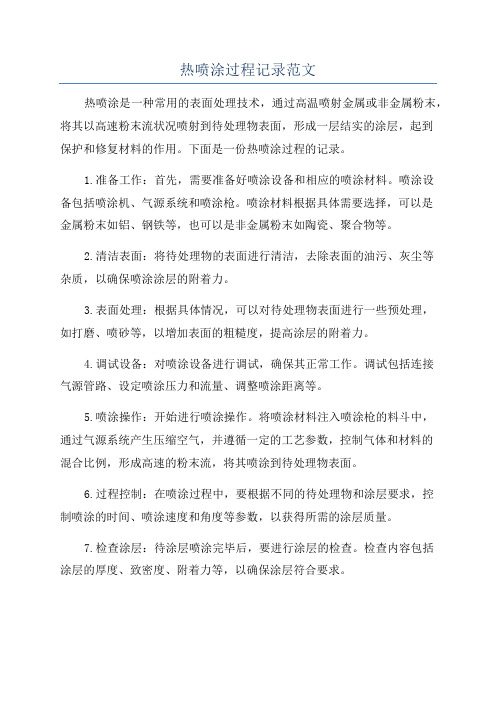
热喷涂过程记录范文热喷涂是一种常用的表面处理技术,通过高温喷射金属或非金属粉末,将其以高速粉末流状况喷射到待处理物表面,形成一层结实的涂层,起到保护和修复材料的作用。
下面是一份热喷涂过程的记录。
1.准备工作:首先,需要准备好喷涂设备和相应的喷涂材料。
喷涂设备包括喷涂机、气源系统和喷涂枪。
喷涂材料根据具体需要选择,可以是金属粉末如铝、钢铁等,也可以是非金属粉末如陶瓷、聚合物等。
2.清洁表面:将待处理物的表面进行清洁,去除表面的油污、灰尘等杂质,以确保喷涂涂层的附着力。
3.表面处理:根据具体情况,可以对待处理物表面进行一些预处理,如打磨、喷砂等,以增加表面的粗糙度,提高涂层的附着力。
4.调试设备:对喷涂设备进行调试,确保其正常工作。
调试包括连接气源管路、设定喷涂压力和流量、调整喷涂距离等。
5.喷涂操作:开始进行喷涂操作。
将喷涂材料注入喷涂枪的料斗中,通过气源系统产生压缩空气,并遵循一定的工艺参数,控制气体和材料的混合比例,形成高速的粉末流,将其喷涂到待处理物表面。
6.过程控制:在喷涂过程中,要根据不同的待处理物和涂层要求,控制喷涂的时间、喷涂速度和角度等参数,以获得所需的涂层质量。
7.检查涂层:待涂层喷涂完毕后,要进行涂层的检查。
检查内容包括涂层的厚度、致密度、附着力等,以确保涂层符合要求。
8.后续处理:根据需要,可以对涂层进行后续处理。
例如,对涂层进行热处理,以提高涂层的硬度和耐磨性。
或者进行表面处理,如研磨、抛光等,以改善涂层的光洁度。
9.记录与分析:记录喷涂过程中的关键参数,如喷涂材料、喷涂压力、喷涂速度等。
同时,对涂层的质量进行分析和评估,以总结经验,改进工艺。
热喷涂是一项技术含量较高的工艺,需要操作人员具备一定的专业知识和技能。
通过对喷涂过程的记录和分析,可以不断改进和优化喷涂工艺,提高涂层的品质和性能,满足不同工程要求。
热喷涂技术

热喷涂技术热喷涂技术在国家标准GB/T18719—2002《热喷涂术语、分类》中定义:热喷涂技术是利用热源将喷涂材料加热至溶化或半溶化状态,并以一定的速度喷射沉积到经过预处理的基体表面形成涂层的方法。
热喷涂技术在普通材料的表面上,制造一个特殊的工作表面,使其达到:防腐、耐磨、减摩、抗高温、抗氧化、隔热、绝缘、导电、防微波辐射等一系多种功能,使其达到节约材料,节约能源的目的,我们把特殊的工作表面叫涂层,把制造涂层的工作方法叫热喷涂。
热喷涂技术是表面过程技术的重要组成部分之一,约占表面工程技术的三分之一。
热喷涂技术具有的优点:1、设备轻便,可现场施工。
2、工艺灵活、操作程序少。
可快捷修复,减少加工时间。
3、适应性强,一般不受工件尺寸大小及场地所限。
4、涂层厚度可以控制。
5、除喷焊外,对基材加热温度较低,工件变形小,金相组织及性能变化也较小。
6、适用各种基体材料的零部件、几乎可在所有的固体材料表面上制备各种防护性涂层和功能性涂层。
热喷涂技术的特点从热喷涂技术的原理及工艺过程分析,热喷涂技术具有以下一些特点. 1. 由于热源的温度范围很宽,因而可喷涂的涂层材料几乎包括所有固态工程材料,如金属,合金,陶瓷,金属陶瓷,塑料以及由它们组成的复合物等. 因而能赋予基体以各种功能(如耐磨,耐蚀,耐高温,抗氧化,绝缘,隔热,生物相容,红外吸收等)的表面. 2. 喷涂过程中基体表面受热的程度较小而且可以控制,因此可以在各种材料上进行喷涂(如金属,陶瓷,玻璃,布疋,纸张,塑料等),并且对基材的组织和性能几乎没有影响,工件变形也小. 3.设备简单,操作灵活, 既可对大型构件进行大面积喷涂,也可在指定的局部进行喷涂;既可在工厂室内进行喷涂也可在室外现场进行施工. 4.喷涂操作的程序较少,施工时间较短,效率高,比较经济. 随着热喷涂应用要求的提高和领域的扩大, 特别是喷涂技术本身的进步, 如喷涂设备的日益高能和精良,涂层材料品种的逐渐增多,性能逐渐提高, 热喷涂技术近十年来获得了飞速的发展, 不但应用领域大为扩展, 而且该技术已由早期的制备一般的防护涂层发展到制备各种功能涂层;由单个工件的维修发展到大批的产品制造;由单一的涂层制备发展到包括产品失效分析,表面预处理, 涂层材料和设备的研制,选择, 涂层系统设计和涂层后加工在内的喷涂系统工程;成为材料表面科学领域中一个十分活跃的学科.并且在现代工业中逐渐形成象铸,锻,焊和热处理那样的独立的材料加工技术.成为工业部门节约贵重材料,节约能源,提高产品质量,延长产品使用寿命,降低成本,提高工效的重要的工艺手段, 在国民经济的各个领域内得到越来越广泛的应用.编辑本段热喷涂工艺技术近年发展趋势与特点热喷涂技术目前在国内已经得到了比较广泛的推广应用,近年来发展的趋势和特点是:(1)大面积长效防护技术得到了广泛应用对于长期暴露在户外大气的钢铁结构件,采用喷涂铝、锌及其合金涂层,代替传统的刷油漆方法,实行阴极保护进行长效大气防腐,近年来得到了迅速发展。
表面工程技术

表面工程技术一、热喷涂热喷涂技术是采用气体、液体燃料或电弧、等离子弧、激光等作热源,使金属、合金、金属陶瓷、氧化物、碳化物、塑料以及它们的复合材料等喷涂材料加热到熔融或半熔融状态,通过高速气流使其雾化,然后喷射、沉积到经过预处理的工件表面,从而形成附着牢固的表面层的加工方法。
1.热喷涂具有以下特点:1)取材范围广,几乎所有的工程材料都可以作为喷涂材料。
2)几乎所有固体材料都可以作为基体进行喷涂。
3)工艺灵活, 施工范围小到10mm的内孔,大到铁塔、桥梁。
4)喷涂层厚度可调范围大,从几十微米到几毫米,而且表面光滑,加工量少。
5)工件受热程度可以控制,热喷涂时工件受热程度可控制在30~200℃之间,保证不改变基体的金相组织,工件不会发生畸变。
6)比电镀生产率高。
7)可赋予普通材料以特殊的表面性能,可使材料满足耐磨、耐蚀、抗高温氧化、隔热等性能要求,达到节约贵重材料,提高产品质量,满足多种工程和尖端技术的需求。
2.热喷涂工艺原理喷涂层是由无数变形粒子互相交错呈波浪式堆叠在一起的层状组织结构。
3.热喷涂材料热喷涂材料的材质可分为金属及其合金、陶瓷、金属化合物、某些有机塑料、玻璃、复合材料等。
4.几种不同热源的热喷涂方法1)火焰喷涂火焰喷涂的基本原理是通过乙炔、氧气喷嘴出口处产生的火焰,将线材(棒材)或粉末材料加热熔化,借助压缩空气使其雾化成微细颗粒,喷向经预先处理的粗糙工件表面使之形成涂层。
2)电弧喷涂电弧喷涂的基本原理是将两根被喷涂的金属丝作自耗性电极,连续送进的两根金属丝分别与直流的正负极相连接。
在金属丝端部短接的瞬间,由于高电流密度,使两根金属丝间产生电弧,将两根金属丝端部同时熔化,在电源作用下,维持电弧稳定燃烧;在电弧发射点的背后由喷嘴喷射出的高速压缩空气使熔化的金属脱离金属丝并雾化成微粒,在高速气流作用下喷射到基材表面而形成涂层。
3)等离子喷涂等离子喷涂法是利用等离子焰的热能将引入的喷涂粉末加热到熔融或半熔融状态,并在高速等离子焰的作用下,高速撞击工件表面,并沉积在经过粗糙处理的工件表面形成很薄的涂层。
- 1、下载文档前请自行甄别文档内容的完整性,平台不提供额外的编辑、内容补充、找答案等附加服务。
- 2、"仅部分预览"的文档,不可在线预览部分如存在完整性等问题,可反馈申请退款(可完整预览的文档不适用该条件!)。
- 3、如文档侵犯您的权益,请联系客服反馈,我们会尽快为您处理(人工客服工作时间:9:00-18:30)。
3Fe3O4+8Al → 9Fe+4Al2O3 3/2O2+CaWO4+CaC2+2Al→ WC+2CaO+Al2O3+CO2
③ The first reaction starts at about 1070K while the second one takes place in the temperature range 2720–3270 K. After cooling, the crystal mass contains 65wt% WC. Leaching with acids leaves pure WC with less than 0.2wt% Fe.
➢The high-temperature treatment that occurs at sintering or fusion of chromium oxide may lead to reduction to suboxides or to metallic chromium:
Cr3+ → Cr2+ → Cr0 ➢The metallic chromium should be washed away with acids.
1.1 Atomization(雾化)
1.2 SINTERING OR FUSION (烧结或熔炼)
✓Oxides, carbides and cermets powders can be manufactured by sintering or fusion. The resulting powder particles are ‘blocky’ and irregular, which renders their flowability to be relatively poor. ✓To improve this parameter, they can be submitted to spheroidization in flame or in plasma.
1.3 SPRAY DRYING (AGGLOMERATION)(喷雾干燥法)
Principle of Spray Drying
➢The spray-drying process consists of introducing a slurry containing finely dispersed precursors to be agglomerated, organic binder and water. ➢The pump (2) feeds the slurry into a centrifugal atomizer (1a) or a nozzle atomizer (1b). ➢The atomized slurry is dried in the stream of cleaned (3) and heated (4) gas (mostly air) and the moisture contained in the droplets evaporates during flight in the chamber (6). ➢The gas is cleaned out in the cyclone (9) and recycled again to the heater(10).The solid particles are collected in the powder collector (8).
Advantages: ➢the molten particles are single-sized. ➢the lamellae (扁平粒子)are homogeneous than powders. Disadvantages: ➢deposition techniques of AS(电弧喷涂) or FS (火焰喷涂)-wire produce porous (多孔的) coatings. which reduce this advantage.
(1) Chromium Oxide (氧化铬)
1. The raw material for the production of Cr2O3 powder is a fine green pigment obtained chemically from the chromic iron ore. The pigment contains submicron particles. The pigment can be fused in an arc furnace for 10–20 h.
metals, e.g. Mo; oxides and oxide alloys, e.g. Cr2O3+TiO2 orZnO+Al2O3; nitrides and mixtures of nitrides with oxides(氮化物或氮化物复合氧化 物), e.g. Si3N4+Al2O3+Y2O3; Cermets(金属陶瓷), e.g. TiC+Ni or WC+Co.
3. Fusion occurs above the melting point of the material (Tm= 2710K for Cr2O3). Sintering takes place at a temperature which is usually about 0.7 ×Tm. A typical, commercially available fused and crushed chromium oxide powder is shown in Figure 50 μm.
(2)Cermet of Tungsten Carbide with Cobalt (钴包碳化物)
Tungsten carbide can be prepared by carburizing tungsten in the following way: ① A solid-state reaction (T = 1673–1973K) between fin3 SPRAY DRYING (AGGLOMERATION)(喷雾干燥法)
The spray-drying technique allows many kinds of materials to be agglomerated. Spray drying has beenapplied to manufacture powders of:
WIRE • metals, Al or Zn; • alloys, Ni+5 wt%Al or Ni+18wt% Cr+6 wt%Al ;
• composites that are cored wires, which contain a metallic sheath (Co or FeCr) and a filler made of a Phaorwd mdeatresriaalresuuchseads WmCainorlyCirn3Cth2ermalspraying.
and thermogravimetric analysis (TGA).(差热分析,热 重分析)
1. Materials Used for Spraying
The following types of powders are currently used in thermal spraying:
➢ metals, e.g. molybdenum or nickel; ➢ alloys, e.g. a self-fluxing alloy of Ni + 1.6wt% Cr + 3.5wt%B+3.5wt% Si+4.5wt% Fe+1wt% C; ➢oxide ceramics, e.g. Al2O3; ➢ oxide alloys, e.g. ZrO2+8wt% Y2O3; ➢ cermet clads, e.g. graphite + 20wt% Ni; ➢cermet agglomerates, e.g. WC+12wt% Co; ➢ carbides, e.g. Cr2C3; ➢ composite4 clads, e.g. AlSi+47 wt% polyimide and 6wt% organic binder.
④ Carbon-resistance melting of tungsten-bearing materials (powders, wires, etc.) in a graphite crucible(石墨坩埚) to form cast tungsten carbide WC–W2C containing about 3.9wt% carbon.
2. Thereafter, a block of chromium oxide is broken after removing an outer shell. Finally, jaw crushers and double-roll mills crush the remaining block into smaller particles.
1. Materials Used for Spraying
1. Materials Used for Spraying
1.1 Atomization(雾化)
Atomization(雾化) is applied mainly to the manufacture of metal and alloy powders. A typical process consists of melting the metal in an inductive heater (1, 2), the melt (3) is then poured into the previously heated funnel (4) having a calibrated outlet (5) and drops down as a liquid jet (6) onto the nozzle (7). Inside the nozzle is introduced, under high pressure, the atomizing medium which is usually a gas or water (8). The metal solidifies during the ‘free-fall’ forming small powder particles (9).