FMEA1
1-1 FMEA新版模板(AIAG-VDA R1)
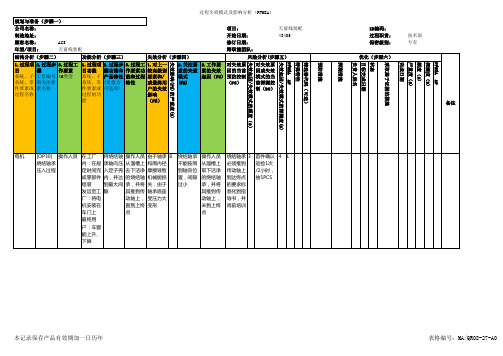
失效分析(步骤四)
风险分析(步骤五)
1.过程项 2.过程步 3.过程工
目
骤
作要素
系统,子 工位编号 4M类型
系统,零 和关注要
件要素或 素名称
过程名称
1.过程项 2.过程步 3.过程工 1.对上一
目功能 骤功能和 作要素功 较高级别
系统、子 产品特性 能和过程 要素和/
系统、零 (量值为 特性
或最终用
年型/项目:
天窗线装配
跨职能团队:
结构分析(步骤二)
功能分析(步骤三)
失效分析(步骤四)
风险分析(步骤五)
1.过程项 2.过程步 3.过程工
目
骤
作要素
系统,子 工位编号 4M类型
系统,零 和关注要
件要素或 素名称
过程名称
1.过程项 2.过程步 3.过程工 1.对上一
目功能 骤功能和 作要素功 较高级别
失效起因/失效模式的频度(O)
失效影响(FE)的严重度(S)
ID编码: 过程职责: 保密级别:
优化(步骤六)
技术部 专有
备注
本记录保存产品有效期加一日历年
表格编号:MA/QR08-27-A0
过程失效模式及影响分析(PFMEA)
规划与准备(步骤一)
公司名称:
项目:
天窗线装配
制造地址:
开始日期:
43405
影响
能
(FE)
2.关注要 3.工作要 对失效原
素的失效 素的失效 因的当前
模式
起因(FC) 预防控制
(FM)
(PC)
对失效原 因或失效 模式的当 前探测控 制(DC)
ID编码: 过程职责: 保密级别:
fmea全称是什么意思
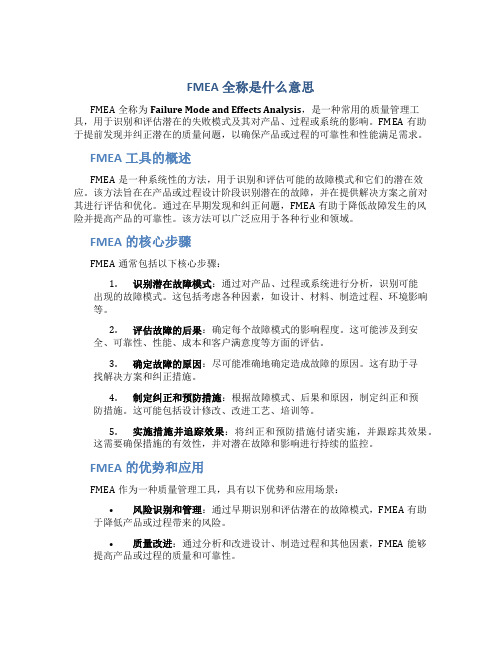
FMEA全称是什么意思FMEA全称为Failure Mode and Effects Analysis,是一种常用的质量管理工具,用于识别和评估潜在的失败模式及其对产品、过程或系统的影响。
FMEA有助于提前发现并纠正潜在的质量问题,以确保产品或过程的可靠性和性能满足需求。
FMEA工具的概述FMEA是一种系统性的方法,用于识别和评估可能的故障模式和它们的潜在效应。
该方法旨在在产品或过程设计阶段识别潜在的故障,并在提供解决方案之前对其进行评估和优化。
通过在早期发现和纠正问题,FMEA有助于降低故障发生的风险并提高产品的可靠性。
该方法可以广泛应用于各种行业和领域。
FMEA的核心步骤FMEA通常包括以下核心步骤:1.识别潜在故障模式:通过对产品、过程或系统进行分析,识别可能出现的故障模式。
这包括考虑各种因素,如设计、材料、制造过程、环境影响等。
2.评估故障的后果:确定每个故障模式的影响程度。
这可能涉及到安全、可靠性、性能、成本和客户满意度等方面的评估。
3.确定故障的原因:尽可能准确地确定造成故障的原因。
这有助于寻找解决方案和纠正措施。
4.制定纠正和预防措施:根据故障模式、后果和原因,制定纠正和预防措施。
这可能包括设计修改、改进工艺、培训等。
5.实施措施并追踪效果:将纠正和预防措施付诸实施,并跟踪其效果。
这需要确保措施的有效性,并对潜在故障和影响进行持续的监控。
FMEA的优势和应用FMEA作为一种质量管理工具,具有以下优势和应用场景:•风险识别和管理:通过早期识别和评估潜在的故障模式,FMEA有助于降低产品或过程带来的风险。
•质量改进:通过分析和改进设计、制造过程和其他因素,FMEA能够提高产品或过程的质量和可靠性。
•成本降低:通过减少故障和质量问题的发生,FMEA可以帮助避免额外的成本,并提高效率。
•客户满意度提升:通过识别和修正潜在的问题,FMEA有助于确保产品或过程满足客户的需求和期望。
FMEA可以应用于各种项目和领域,包括制造业、医疗保健、航空航天、汽车工业等。
03 新FMEA的评价准则-1版
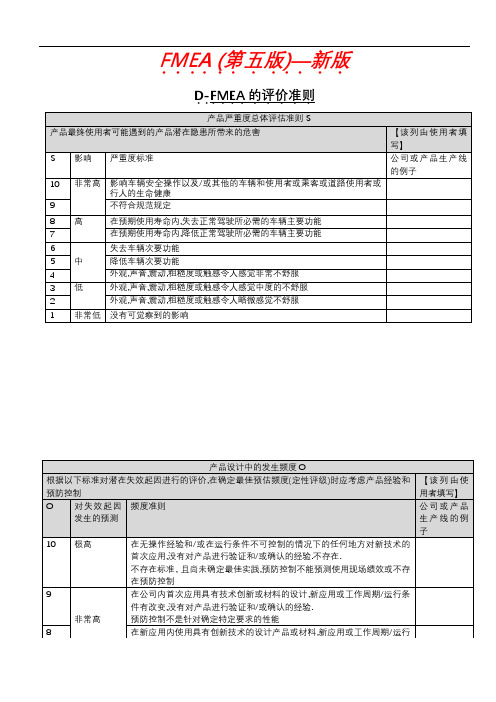
公司或产品系列示例
10
高
失效可能会导致从事生产或组装作业的工人面临严重的健康和、或安全风险
失效可能会导致从事生产或组装作业的工人面临严重的健康和、或安全风险
影响到车辆和、或其他车辆的操作安全性,驾驶员、乘客、交通参与者或行人的健康状况。
9
失效可能会导致厂内不符合法规
失效可能会导致厂内不符合法规
可以提出失效模式或失效起因的人工检验(视觉、触觉、听觉)方法,或使用人工检验(计数型或计量型)方式
7
以设备为基础的检验方式(采用光学、蜂鸣器等装置的自动化或半自动化方式),或使用可以提出失效模式或失效起因的检验设备,例如坐标测量机
6
中
测试或检验方法已经经过实践证明为有效和可靠(例如:工厂在测试或检验方法方面具备经验,有关类似过程或本程序的测量可重复性和再现性结果可以接受等)
预防控制不是针对确定特定要求的性能
8
在新应用内使用具有创新技术的设计产品或材料,新应用或工作周期/运行条件有改变,没有对产品进行验证和/或确认的经验.
极少存在现有标准和最佳实践,不能直接用于该设计产品,预防控制不能可靠地反映使用现场绩效.
7
高
根据相似技术和材料的新型设计,新应用或工作周期/运行条件有改变,没有对产品进行验证和/或确认的经验.
2
探测方法已经经过实践证明为有效或可靠(例如:工厂在探测方法、放错确认措施方面具备经验等)
以设备为基础的探测方法,其可以探测失效起因并避免出现失效模式(差异零件)
1
非常高
根据设计或加工过程而不会实际出现失效模式,或者探测方法经过实践验证总是能够探测到失效模式或失效起因
空白,由使用人填写
O
对失效起因发生的预防
FMEA参考手册解读1

九、PFMEA的说明和介绍9.1、PFMEA及其作用的简介制造过程的输出是产品,合格的产品是预期的输出。
通过PFMEA能识别过程变量,知道哪些因素影响产品质量。
过程特性就是影响产品质量的原因,过程特性不但要设计合理,而且还需要在后续的生产过程中进行管控,以确保过程特性符合管控要求。
比如工艺参数属于过程特性,有时即便工艺参数设计合理,但在生产过程中也可能需要对工艺参数进行监视,比如装配过程中的压装力的实时监控,比如电动扳手的扭力监控等,因为只有工艺参数满足设计时的要求,才能确保产品质量,所以制造过程的设计不但要确保过程特性设计的合理性,还要考虑制造过程后续的管控,以确保制造过程不生产不合格品,不流出不合格品,这才是制造过程设计的定位。
从制造过程设计角度考虑不流出不合格品,这也是制造过程设计的范围。
但产品设计就不同了,产品特性或设计特性设计合理了,就进行图纸发布,虽然量产后也需要对产品特性或产品质量进行管控或探测,但后续的产品质量管控或探测就不属于产品设计的范围了。
备注:和DFMEA相同的或类似的原则和内容,在第九章中就不再重复介绍。
PFMEA应当起一个催化剂的作用,通过PFMEA这个工具提供一个促进交流的平台,所以PFMEA的表格格式设计和内容应利于多方论证或跨职能交流,比如可以根据PFMEA中的失效影响,识别受影响的职能或人员参与到PFMEA的编制和评审过程中。
9.2、PFMEA的使用时机PFMEA应在可行性论证阶段或之前就启动,说明在可行性分析的时候就需要应用风险分析,如果是基于分析结果进行论证,就是在论证之前就应用风险分析。
对于过程FMEA应在工装和制造设备的开发、采购之前启动,也就是在决定买什么样的工装和设备之前就已经进行了FMEA分析,再细节一点,在工装设备的制造加工前也经过了FMEA分析。
如果型号或要求都确定了,采购订单都签了,再去分析有什么风险,FMEA的使用时机明显就滞后了。
从FMEA参考手册中也可知道,工装和设备也是需要进行FMEA分析的,至于是综合起来一起分析,还是基于一定条件分开分析,需要视实际情况而定。
FMEA(五版) (1)
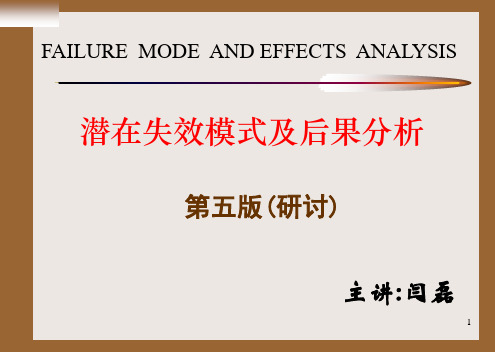
9
5、FMEA的类别
系统FMEA
根据产品范围分 子系统FMEA
根据使用对象分
IATF16949:2016 版权所有
部件FMEA
DFMEA PFMEA
汽车一般由发 动机、底盘、 车身和电气设 备等四个基本 部分组成
4
to assy area
将零部件送往装配区
item# 编号
1
KCC
pressure 压力
3 .结构分析
•PFMEA----依据过程流程图和工艺要求,重点清楚分析 ---过程及活动 •PFMEA应进行结构分解:
工序 + 工步 + 相关要素(有关的5M )
IATF16949:2016 版权所有 42
– 目的旨在:
A、评估产品或过程的潜在失效风险。 B、分析这些失效的原因和影响 C、记录预防和探测手段 D、建议采取措施以降低风险
3
2、FMEA发展历程
1950年,美国GRUMMAN飞机制造公司提出,飞机主操纵 系统的失效分析;
60年代初用于航天; 70年代用于三大汽车公司。 80年代被美国军方确认为军方规范(MIL-STD-1629A) 随着汽车的召回要求,现在在国内越来越重视.
IATF16949:2016 版权所有 33
IATF16949:2016 版权所有
35
第三章 PFMEA实战应用
P FM E A is fo cu s s e d o n th e P R O D U CT. N a m e ly , h o w th e P R OCE SS ca n ca u s e fla w s o r v a ria tio n in th e P R OD U CT.
SPC与FMEA[1]
![SPC与FMEA[1]](https://img.taocdn.com/s3/m/7ca4bd8b19e8b8f67c1cb987.png)
找出制程與品質特性VOE之關系, 以確定需做FMEA的重要制程
成員腦力激蕩完成PFMEA:
1.找出影響最大失效現象
2.魚骨圖分析失效原因
3.現行管制方式列出及RPN計算
4.對風險值(RPN)較大的給出建議措
施並實施.
SPC与FMEA[1]
1
一吉廠FMEA分析
Team Members
主題:6M09.00
人员疏忽
误判, 漏检
理線圈數 拔線角度
脚露铜 脚带钩 長短脚
锡比例,温度, 焊锡时间, 助焊剂比例, 接觸面距離
人员疏忽
印章错误, 印章断字, 印章反, 印章脱落
胶黄,胶 未干
测试架,仪器故障, 测试条件不符, 未较对样.
胶有气孔, 漏点胶, 点胶反, 點膠高蹺.
檢查
切腳
印章烘烤
烘烤
點膠
培训不足, 标准不明确
一吉廠SPC分析
制程能力分析、改善前数据收集及CPK 单位(MM)
SPC与FMEA[1]
一吉廠SPC分析 具体实施方案
SPC与FMEA[1]
一吉廠SPC分析
改善前制程能力分析、CA、CP、CPK
說明CSPPCK与<F1ME.A3[13] 需进行改善
一吉廠SPC分析
长短脚不良之改善对策拟定
SPC与FMEA[1]
测试条件不符;
测试条件
未较对样品;
人员疏忽; 合脚板孔徑; 厚度;
SPC与FMEA[1]
流程展开
一吉廠FMEA分析
SPC与FMEA[1]
一吉廠FMEA分析
根據風險RPN值 高,用魚骨圖的方法 找出處理對策
SPC与FMEA[1]
一吉廠FMEA分析
fmea的基本概念

fmea的基本概念
FMEA(Failure Mode and Effects Analysis),故障模式及影响分析,是一种系统化的风险管理工具,用于识别和评估系统、过程或产品可能出现的故障模式及其潜在影响。
FMEA的基本概念包括:
1. 故障模式(Failure Mode):指系统、过程或产品可能出现的故障或失效的方式或形式。
2. 影响(Effects):指故障模式对系统、过程或产品的潜在效果或影响。
这些影响可以是质量问题、安全风险、操作中断、生产延误等。
3. 原因(Causes):指导致故障模式发生的根本原因或相关因素,可以通过分析和识别原因来帮助预防或减少故障发生的可能性。
4. 控制措施(Control Measures):指针对特定故障模式的预防或控制措施,以减少或消除故障的概率和影响。
通过进行FMEA分析,可以帮助组织识别潜在的故障模式,评估其严重性和优先级,并采取相应的控制措施来降低风险和提高系统、过程或产品的性能和可靠
性。
FMEA介绍[1]
![FMEA介绍[1]](https://img.taocdn.com/s3/m/d046f13c3b3567ec102d8a69.png)
起因 机理
屈服 化学氧化
疲劳 电移
材料不稳定 蠕变
磨损
腐蚀
PPT文档演模板
FMEA介绍[1]
潜在失效的起因/机理分类
与制造装配无关的原因 与制造装配有关的原因
当制造与装配符合工程规范的情况下, 发生了失效。
由于所拟定采用的制造/装配设计在技 术上或操作者体力上的限制与难度, 以及容易产生误操作而引起的潜在失 效。也就是与产品设计中可制造性与 装配性有关的问题。
FMEA介绍
PPT文档演模板
2020/11/1
FMEA介绍[1]
什么是FMEA
在产品设计阶段和过程设计阶段,对构成产 品的子系统、零件,对构成过程的各个工序 逐一进行分析,找出所有潜在的失效模式, 并分析其可能的后果,从而预先采取必要的 措施,以提高产品的质量和可靠性的一种系 统化的活动
PPT文档演模板
✓ 应用失效树分析(FTA)找出复杂系统的失效原因与机
理;
✓ 充分发挥小组的经验,采用头脑风暴法,对可能的原因
进行归纳分析;
PPT文档演模板
FMEA介绍[1]
示例:五个为什么
失效模式:门锁扣不上。
为什么?因为:锁舌与锁座错位。 为什么?因为:车门下沉。 为什么?因为:门铰链变位。 为什么?因为:固定门铰链的框架变形。 为什么?因为:框架刚度不足。
使用地方性、行业性俚语。 • 常用的有两大类失效:Ⅰ类失效、Ⅱ类失效。
PPT文档演模板
FMEA介绍[1]
示例:失效模式的种类
Ⅰ类失效,指的是不能完成规定的功能,如:
突发型:断裂、开裂、碎裂、弯曲、塑性变形、失稳、短路、
断路、击穿、泄露、松脱等等。
渐变型:磨损、腐蚀、龟裂、老化、变色、热衰退、蠕变、
FMEA-1
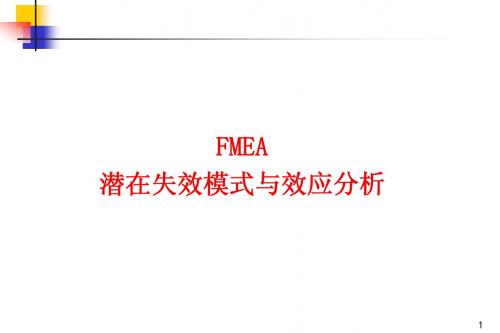
26
FMEA的开发:基本表格填写
标准: 对产品影响的严重度 (对顾客的影响) 潜在失效模式影响了汽车的安全运行:或者包含不 符合政府法律法规的情形,失效发生时无预警。 不符合安全性 或者法规要求 潜在失效模式影响了汽车的安全运行:或者包含不 符合政府法律法规的情形,失效发生时无预警。 标准: 对过程影响的严重度 (对制造/装配的影响) 会使操作员身处危险(机械或装配),失效 发生时无预警。 会使操作员身处危险(机械或装配),失效 发生时有预警。
7
b.定 义 范 围
范围建立起FMEA分析的边界,它根据FMEA的类型(即:系统、子 系统或零部件)来界定,明确了应包括的和不应包括的内容。在 开始FMEA之前,必须清楚地明白需要评估的究竟是什么。在分析 过程中,明确范围之外不包括的,和范围内应包括的都同样重要。 过程起始之初,就需要建立一个范围,来确保一致的方向和关注 点。 下面内容可以帮助小组界定FMEA范围:
2
1、何谓FMEA
FMEA是一组系统化的活动,其目的是:
发现、评价产品/过程中潜在的失效及其后 果。 找到能够避免或减少这些潜在失效发生的措 施。 书面总结上述过程。
它是对设计(产品/过程)过程的完善,以 明确什么样的设计才能满足顾客要求。
3
1、何谓FMEA
FMEA 思考方法
哪些原因可能 分析 现行预计的产品/过程 分析 对顾客或下 可能产生的失效模式 工程的影响 造成这个失效模式
最终顾客:坐垫松动,有噪音。 制造和装配:由于受影响的部分 ,因而进行额外挑选和返工 最终顾客:由于螺钉断裂导致座 垫松动,有噪音。 制造和装配:由于受影响的部分 ,因而进行额外挑选和返工 最终顾客:由于螺钉逐渐松动导 致座垫松动,有噪音。制造和装 配:由于受影响的部分,因而进 行额外挑选和返工 25
FMEA表格讲解
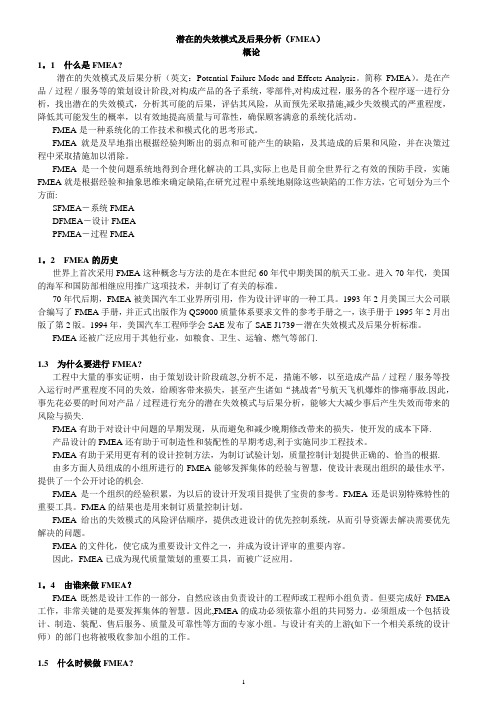
潜在的失效模式及后果分析(FMEA)概论1。
1 什么是FMEA?潜在的失效模式及后果分析(英文:Potential Failure Mode and Effects Analysis。
简称FMEA)。
是在产品/过程/服务等的策划设计阶段,对构成产品的各子系统,零部件,对构成过程,服务的各个程序逐一进行分析,找出潜在的失效模式,分析其可能的后果,评估其风险,从而预先采取措施,减少失效模式的严重程度,降低其可能发生的概率,以有效地提高质量与可靠性,确保顾客满意的系统化活动。
FMEA是一种系统化的工作技术和模式化的思考形式。
FMEA就是及早地指出根据经验判断出的弱点和可能产生的缺陷,及其造成的后果和风险,并在决策过程中采取措施加以消除。
FMEA是一个使问题系统地得到合理化解决的工具,实际上也是目前全世界行之有效的预防手段,实施FMEA就是根据经验和抽象思维来确定缺陷,在研究过程中系统地剔除这些缺陷的工作方法,它可划分为三个方面:SFMEA-系统FMEADFMEA-设计FMEAPFMEA-过程FMEA1。
2 FMEA的历史世界上首次采用FMEA这种概念与方法的是在本世纪60年代中期美国的航天工业。
进入70年代,美国的海军和国防部相继应用推广这项技术,并制订了有关的标准。
70年代后期,FMEA被美国汽车工业界所引用,作为设计评审的一种工具。
1993年2月美国三大公司联合编写了FMEA手册,并正式出版作为QS9000质量体系要求文件的参考手册之一,该手册于1995年2月出版了第2版。
1994年,美国汽车工程师学会SAE发布了SAE J1739-潜在失效模式及后果分析标准。
FMEA还被广泛应用于其他行业,如粮食、卫生、运输、燃气等部门.1.3 为什么要进行FMEA?工程中大量的事实证明,由于策划设计阶段疏忽,分析不足,措施不够,以至造成产品/过程/服务等投入运行时严重程度不同的失效,给顾客带来损失,甚至产生诸如“挑战者"号航天飞机爆炸的惨痛事故.因此,事先花必要的时间对产品/过程进行充分的潜在失效模式与后果分析,能够大大减少事后产生失效而带来的风险与损失.FMEA有助于对设计中问题的早期发现,从而避免和减少晚期修改带来的损失,使开发的成本下降.产品设计的FMEA还有助于可制造性和装配性的早期考虑,利于实施同步工程技术。
FMEA控制程序1

当失效模式按RPN值排出先后次序后,应首先针对高严重度和高RPN 值和小组指定的其它工程进展预防/纠正措施的工程评价。任何建议措施的意图都是要依以下顺序降低其风险级别:严重度,频度和探测度
当严重度是9或10时,公司必须对其予以特别注意,以确保现行的设计措施/控制或过程预防/纠正措施针对了这种风险,不管其RPN值是多大。在所有的已确定潜在失效模式的后果可能会给制造人员造成危害的情况下,都应考虑预防/给制造人员造成危害的情况下,都应考虑模式的产生,或者应对操作人员的适当防护予以规定;
2.风险系数值越高,那么代表风险越大,分析小组应优先改善风险系数大的过程;
3.风险系数值RPN≥80时,应采取整改措施,完成措施后,分析小组重新评价RPN值,直至符合要求为止。
分析小组
分析结果
改良措施
关键性评估指数越大的,其对应的失效模式应该在FMEA表中填写防止失效的措施,在下一次的设计验证与生产测试中加以鉴定,以重新评估指数是否降低
2.过程责任:填入部门和小组;
3.编制人:填入负责准备PFMEA工作的工程师的姓名、 及所在公司名称;
4.车型年/工程〔或产品型号〕:填入所分析的设计/过程将要应用和/或影响的车型年/工程〔如果的话〕,如果未知道的话那么填入进展PFMEA分析的产品规格/型号;
5.关键日期:填入初次PFMEA应完成的日期,该日期不应超过方案的投入生产的日期。对本公司初始的PFMEA日期不应超过顾客要求的生产件批准〔PPAP〕的提交日期;
功能和目的
潜在失效模式
潜在失效后果
关键特性
严重度
潜在失效机理
发生度
现行控制方法
现行监测方法
探测度
风险顺序数
建议措施
FMEA评价准则(1)

表1 FMEA严重度评价标准
表2 FMEA发生频度评价准则
表3 FMEA探测度评价准则
说明:
1、FMEA作为预先的风险评估工具,通常应用于:
新设计、新技术或新过程;现有设计或过程的修改;现有设计或过程在新环境/场所应用。
2、FMEA应由技术部组织多功能(或跨功能)小组来开发,并负责所有的建议措施得到实施或充分阐述。
3、在项目描述时,FMEA的语言应尽可能规范且简要。
4、FMEA作为动态文件,应一直反应最新的水准,其维护时机:
在产品或过程设计更改和更新时,以及市场或生产问题发生时,小组应对FMEA进行评审。
此外,FMEA的更新还包括周期性评审,即每年定期评审2次。
5、当RPN值大于80时,小组应考虑采取相应的措施,以最大程度降低综合风险和失效模式发生的可能性。
(完整版)FMEA经典案例(1)
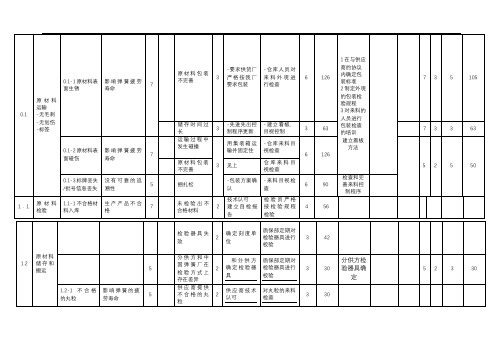
54
无
12
包装
包装混乱
用户不满意
7
工人失误
准确包装
3
42
13
入库
1运输中散落、磕碰伤
2锈蚀
使用寿命降低
7
运输不当
雨淋
2
堆放整齐合理
放置环境防雨;雨天运输盖防雨塑料布
3
42
5-6表面轧伤
弹簧疲劳断裂
6
1.设备故障
2.人为因素
4
-设备预防性维修
-弹簧上料位置正确
1.在强压工位目视检查100%
4
96
弹簧位置防错图
6
压缩
-尺寸定型
6-1压缩长度不符合规范
1.弹簧长度偏差
2.弹簧表面轧伤
6
HIC
1.设备故障
2.工艺参数设置误差
4
-首件认可
-光电开关控制保证
-设备预防性维修
光电开关控制100%
6
1测负荷高度有偏差
3
-测力机由质保部定期作校验
1每班测力前对负荷高度由检验员校对。
2
36
无
弹簧表面磕碰,涂层剥落,易锈蚀.
弹簧生锈
弹簧使用寿命降低
弹簧早期断裂
7
7
7
2测力机有故障
3
-测力机由质保部定期作校验
2
36
无
1塑纸破或未包装好使弹簧表面外露
3
用完好的塑纸将每只弹簧包装并堆放整齐
2
42
无
2堆放高,运输中掉落
2
供应商技术认可
对粉末进行来料检查
3
30
1.2-4原材料表面生锈
影响弹簧疲劳寿命
FMEA课程1
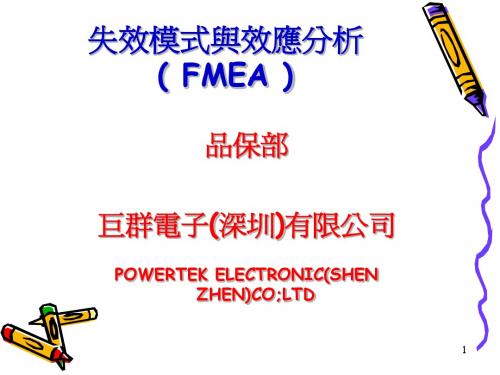
工程設計 工程計劃圖
設備設計 設備設計圖 對製品品質的影響 層面來做設備重要 部位的改善 配合製品的設計機能 、性能進行設備設計 改善
圖面
從Feasibility層面 的工程改善
設計的機能、性能在 量產工程上能否達成 (人、設備、方法)的 檢討
目
檢討系統、製品 機能的潛在缺陷
標
用 途 與 格 式
系統FMEA
12
定位故障模式權重與評價
消除故障模式
FMEA實施流程
任務確認 決定 分析層級 機能 方塊圖
DFMEA
流程步驟 風險分析表
PFMEA
列舉 故障模式 B.S 故障事例
經驗累積 提出 對策案 製作 FMEA表 列舉 故障原因
詴驗報告 不良報告 顧客抱怨
選定對象
選定 故障模式
13
FMEA展開時機
1. 依照FMEA定義,它是一種方法,消除或減少已知或潛在問題, 以強化顧客滿意至最大極限。因此,為了要達成此目的,展開FMEA 的時機必頇愈早愈好!縱使相關數據/資訊仍然未知時。 FMEA的口號為:(就你所有,儘全力而為) 經由品質機能展開(QFD)已知某些資料時,就應立刻展開FMEA。 當設計新的系統,新的設計,新產品,新製程,新的服務時。 當現有系統,設計,產品,製程,或服務等不管是何種理由,將要變 更時。 當既有的系統,設計,產品,製程,或服務的條件有新的應用時。
計畫/定義 研發守案
生產階段/ 回饋矯正
24
先期產品品質規劃(APQP)階段區分
I II 計劃及定義 產品設計及開發 2.1 DFMEA 1.1 顧客心聲 1.7 設計目標 1.1.1 市場研究 III IV V 製程設計及開發 產品及製程查證 回饋評估及矯正 3.1 包裝標準 4.1 試驗生產 5.1 減少變異 4.2 量測系統分析 5.2 顧客滿意 評估 4.3 PPK 研究 5.3 交貨及服務 4.4 PPAP
fmea 评分标准
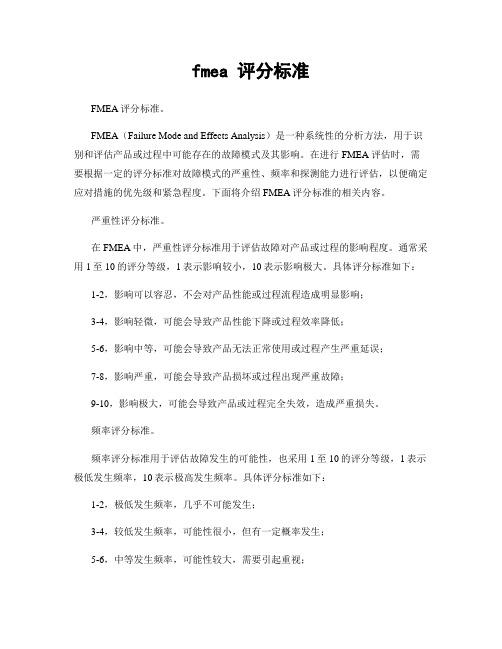
fmea 评分标准FMEA评分标准。
FMEA(Failure Mode and Effects Analysis)是一种系统性的分析方法,用于识别和评估产品或过程中可能存在的故障模式及其影响。
在进行FMEA评估时,需要根据一定的评分标准对故障模式的严重性、频率和探测能力进行评估,以便确定应对措施的优先级和紧急程度。
下面将介绍FMEA评分标准的相关内容。
严重性评分标准。
在FMEA中,严重性评分标准用于评估故障对产品或过程的影响程度。
通常采用1至10的评分等级,1表示影响较小,10表示影响极大。
具体评分标准如下:1-2,影响可以容忍,不会对产品性能或过程流程造成明显影响;3-4,影响轻微,可能会导致产品性能下降或过程效率降低;5-6,影响中等,可能会导致产品无法正常使用或过程产生严重延误;7-8,影响严重,可能会导致产品损坏或过程出现严重故障;9-10,影响极大,可能会导致产品或过程完全失效,造成严重损失。
频率评分标准。
频率评分标准用于评估故障发生的可能性,也采用1至10的评分等级,1表示极低发生频率,10表示极高发生频率。
具体评分标准如下:1-2,极低发生频率,几乎不可能发生;3-4,较低发生频率,可能性很小,但有一定概率发生;5-6,中等发生频率,可能性较大,需要引起重视;7-8,较高发生频率,经常会发生,需要立即采取措施;9-10,极高发生频率,几乎肯定会发生,需要立即采取紧急措施。
探测能力评分标准。
探测能力评分标准用于评估故障是否容易被检测到,也采用1至10的评分等级,1表示容易被检测到,10表示难以被检测到。
具体评分标准如下:1-2,容易被检测到,几乎可以立即发现;3-4,较容易被检测到,需要一定的检测手段才能发现;5-6,中等被检测到,需要较为复杂的检测手段才能发现;7-8,较难被检测到,需要专业的检测设备才能发现;9-10,难以被检测到,几乎不可能在事前发现,需要采取其他预防措施。
综合评分和优先级。
FMEA评级标准

FMEA评级相关标准
一、严重度数标准
分值严重程度
1 失效对产品的性能无任何影响,使用者几乎不知道该失效
2-3 失效并不明显,使用者只会轻微的受到影响
4-6 部分使用者对失效表示不满,产品对使用者有负面影响
7-8 部分使用者对失效感到很烦恼,失去了部分产品功能
9 尚未涉及到安全和违法的失效,当产生系统性的失效
10 涉及到人身安全和/或与政府的法规违背的失效
二、频度数标准
分值失效的可能性可能失效比率
1 几乎不可能失效<1PPM
2 极少发生1PPM<X<50PPM
3 50PPM<X<250PPM
4 偶尔发生250PPM<X<0.1%
5 0.1%<X<0.25%
6 0.25%<X<1.25%
7 经常重复发生 1.25%<X<2.50%
8 2.50%<X<5.00%
9 几乎不可避免 5.00%<X<12.50%
10 无具体参考点 12.50%<X<?
三、可探测度数标准
分值探测的可能性
1 失效可在制造交付前被发现
2-3 失效极有可能在最终发运前被发现,能在发运后在大批量生产前被发现4-6 可能在最终发运前被发现,能在最终交付前发现
7-8 该控制可能无法探测设计失效问题,当可在现场使用前被探测
9-10 除非在现场失效,其他环节无法探测其失效
四、RPN
RPN=频度数×严重度数×可探测度数。
FMEA分析法讲解

评估故障模式对生产过程的影响
故障频率评估
分析历史故障数据,确定各种故障模式发生 的频率。
故障严重程度评估
评估故障模式对生产质量、成本、交货期等 方面的影响程度。
故障可检测性评估
评估在现有技术条件下,故障模式被及时检 测出的可能性。
制定预防措施以降低故障率
设备维护与保养
建立完善的设备维护与保养制度,确保设备 处于良好状态。
FMEA应用领域
制造业
服务业
FMEA在制造业中广泛应用于产品设计、过 程设计、设备维护等方面,以确保产品质 量和生产过程的稳定性。
FMEA也可应用于服务业,如金融、医疗、 教育等,用于识别服务过程中的潜在失效 模式,提高服务质量。
软件开发
风险管理
在软件开发领域,FMEA可用于识别软件系 统中的潜在故障模式,提高软件的可靠性 和稳定性。
05 FMEA在生产过程中的应用
CHAPTER
识别生产过程中的潜在故障模式
分析历史故障数据
收集并整理过去生产过程中出现的故障记录,通过统 计分析识别出常见的故障模式。
工艺流程审查
对生产流程进行详细审查,找出可能导致故障的环节 和因素。
设备与工具检查
检查生产过程中使用的设备和工具,识别其可能存在 的故障模式。
03
根据风险等级,对故障模式进行排序,优先处理高 风险故障模式。
优化产品设计以降低风险
01
针对识别出的故障模式和评估 结果,提出相应的优化措施, 如改进设计、采用更可靠的元 器件、增加冗余设计等。
02
对优化措施进行实施,并对实 施效果进行验证和评估,确保 措施的有效性。
03
通过对产品设计的持续改进和 优化,不断降低故障模式的风 险等级,提高产品的可靠性和 安全性。
FMEA评定标准
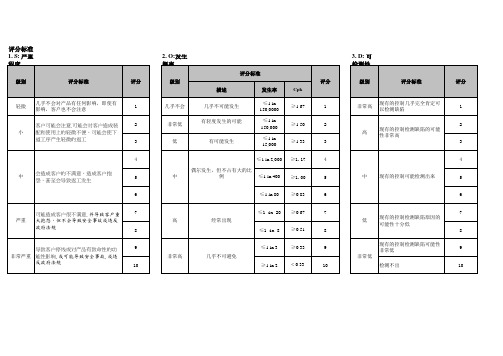
评分
1 2 3 4 5 6 7 8 9 10
3. D: 可检测性
小
≥1.17 ≥1.00 ≥0.83 ≥0.67
严重
可能造成客户很不满意,并导致客户重 大抱怨,但不会导致安全事故或违反 政府法规
导致客户停线或对产品有致命性的功能 非常严重 性影响,或可能导致安全事故,或违反 政府法规
备注: 严重程度S*发生概率 可检测性D 备注 风险指数 (RPN) =严重程度 发生概率 可检测性 严重程度 发生概率O*可检测性 severity*occur probability*display
评分标准 1. S: 严重程度 2. O: 几乎不会对产品有任何影响,即使有影 响,客户也不会注意 客户可能会注意,可能会对客户造成装 配和使用上的轻微不便。可能会使下道 工序产生轻微的返工 1 2 3 4 中 会造成客户的不满意,造成客户抱怨, 甚至会导致返工发生 5 6 7 高 8 9 非常高 10 几乎不可避免 ≥1 in 2 < 0.33 10 经常出现 ≤1 in 8 ≤1 in 3 ≥0.51 ≥0.33 8 9 非常低 检测不出 现有的控制检测缺陷可能性 非常低 中 偶尔发生,但不占有大的比 例 几乎不会 非常低 低 几乎不可能发生 有轻度发生的可能 发生率 ≤1 in 150,0000 ≤1 in 150,000 ≤1 in 15,000 ≤1 in 2,000 ≤1 in 400 ≤1 in 80 ≤1 in 20 Cpk ≥1.67 ≥1.50 ≥1.33 1 2 高 有可能发生 3 4 5 6 7 低 现有的控制检测缺陷原因的 可能性十分低 中 现有的控制可能检测出来 现有的控制检测缺陷的可能 性非常高 非常高 现有的控制几乎完全肯定可 以检测缺陷 评分 级别 评分标准
- 1、下载文档前请自行甄别文档内容的完整性,平台不提供额外的编辑、内容补充、找答案等附加服务。
- 2、"仅部分预览"的文档,不可在线预览部分如存在完整性等问题,可反馈申请退款(可完整预览的文档不适用该条件!)。
- 3、如文档侵犯您的权益,请联系客服反馈,我们会尽快为您处理(人工客服工作时间:9:00-18:30)。
ϕ
2001-12-22
Jess Consultant
21
制造和裝配過程 潛在的失效模式及後果分析 (PFMEA)
FMEA表格之應用
20) 責任(對建議措施)
ϕ
填寫負責建議措施的組織和個人, 以及預計完成 的日期 簡單記載具體實施一項措施的執行情況 估計并記錄糾正後的嚴重度、頻度和不易採測度 及計算糾正後的RPN值
2001-12-22
Jess Consultant
20
制造和裝配過程 潛在的失效模式及後果分析 (PFMEA)
FMEA表格之應用
19) 建議措施
ϕ
ϕ
應對RPN值排出先後次序, 并對最關鍵的過程項 目首先採取糾正措施 失效起因不详时,建議採用的措施應通過統計實 驗設計(DOE)Design of Experiment 來確定
依靠集體協作, 綜合各方面專業人才的智慧 FMEA能夠減少或消除因產品/過程的修改而帶 來時間和金錢的損失 消除潛在的隱患,能夠避免許多不必要的事件 發生
2001-12-22 Jess Consultant 5
制造和裝配過程 潛在的失效模式及後果分析 (PFMEA)
簡介
由“主管/工程師/工程小組”採用的一種分析 技術 充分地考慮到已知的潛在失效模式及後果之起 因/形成 在任何制造計劃過程中, 必須與正常經歷的思 維過程一致
2001-12-22
Jess Consultant
6
制造和裝配過程 潛在的失效模式及後果分析 (PFMEA)
目的
確定與產品相關的過程潛在失效模式 評價失效對顧客的潛在影響 確定潛在制造或裝配過程失效的起因, 減少失 效發生或找出失效條件的過程控制變量 編制潛在失效模式分級表, 建立糾正措施的優 先體系 將制造或裝配過程的結果編制成文件
ϕ ϕ
2001-12-22
Jess Consultant
15
制造和裝配過程 潛在的失效模式及後果分析 (PFMEA)
FMEA表格之應用
14)潛在失效起因/机理
ϕ ϕ ϕ
指失效是怎樣發生的 列出每個可以想到的失效起因 典型失效起因包括:
ϕ ϕ ϕ ϕ ϕ
焊接不正確 - 電流、時間、壓力不正確 測量不精確 熱處理不正確 - 時間、溫度有誤 潤滑不當或無潤滑 零件漏裝或錯裝
QS9000五大工具培训 QS9000五大工具培训 Failure Mode and Effect Analysis 失效模式及效果分析
2001-12-22 Jess Consultant 1
潛在的失效模式及後果分析 (FMEA)
概述
FMEA是一組系統化的活動, 其目的是:
ε ε ε
發現、評價產品/過程中潛在的失效及其後果; 找到能夠避免或減少這些潛在失效發生的措施; 書面總結上述過程
10
制造和裝配過程 潛在的失效模式及後果分析 (PFMEA)
FMEA表格之應用
4) 編制者
ϕ
填入負責準備FMEA工作的工程師的姓名、電話及 所在公司名稱 填入將使用和/或正被分析過程影響的預期年型 及車型 填入初次FMEA預定完成的日期, 該日期不應超過 計劃開始生產的日期
Jess Consultant 11
2001-12-22
Jess Consultant
4
潛在的失效模式及後果分析 (FMEA)
FMEA的實施
FMEA是一個“事前的行為”, 而不是“事後的 行 為 ” (To be a “before-the-event” action, not an
“after-the-fact” exercise)
Jess Consultant 17
16) 現行過程控制
ϕ ϕ
2001-12-22
制造和裝配過程 潛在的失效模式及後果分析 (PFMEA)
FMEA表格之應用
ϕ
對過程/工序進行評價, 可考慮以下三種過程控制 方法/特點:
1
2 3
阻止失效起因/机理或失效模式/後果的發生, 或减少其 發生率 查明起因并找到糾正措施 查明失效模式
2001-12-22
Jess Consultant
2
發展簡史
六十年代中期,FMEA技術首次應用在航天工業上
1950年美国格鲁曼(GRUMMAN)飞机公司首先提出, 应用于飞机主操作系统的失效分析 1957年,波音(BOEYING)与马丁公司列出正式的 FMEA程序 60年代初,美国航空太空总署将FMEA成功应用于航太 计划,同时美国军方开始使用FMEA 技术 1974年,军方颁布MIL-STD-1629,1980年改版为 MIL-STD-1629A
ε ε
過程/零件怎麼不能滿足規范? 顧客會提出什麼異議?
Jess Consultant 13
2001-12-22
制造和裝配過程 潛在的失效模式及後果分析 (PFMEA)
FMEA表格之應用
ϕ
典型的失效模式可能是下列情況:
ϕ
彎曲、毛刺、轉運損壞、斷裂、變形、安裝調試不當、 接地、開路、短路、工具磨損等
2001-12-22 Jess Consultant 8
制造和裝配過程 潛在的失效模式及後果分析 (PFMEA)
PFMEA的開發
應從整個過程中的流程圖/風險評定(附錄C) 流程圖應確定與每個過程有關的產品/過程特 性參數 用于FMEA準備工作中的流程/風險評定圖的覆 制件應伴隨FMEA過程
2001-12-22
Jess Consultant
9
制造和裝配過程 潛在的失效模式及後果分析 (PFMEA)
FMEA表格之應用
1) FMEA編號
ϕ
填入FMEA文件的編號, 以便查詢 填入所分析的系統、子系統或零件的過程名稱和 編號 填入責任部門、小組或供方的名稱
2) 項目
ϕ
3) 過程責任
ϕ
2001-12-22
Jess Consultant
2001-12-22
制造和裝配過程 潛在的失效模式及後果分析 (PFMEA)
FMEA表格之應用
12)嚴重度 (Severity)
ϕ ϕ ϕ
指潛在失效模式對顧客影響的嚴重程度的評價指標 嚴重度只適用于失效的後果 嚴重度評估分為“1 - 10”級13)分級 (Classification) 小组对评定准则和分级规则应意见一致。 對過程控制的零部件、子系統或系統的特殊特性進行分級 (如: 關鍵、主要、重要及重點等)
Jess Consultant 22
21) 採取的措施
ϕ
22) 糾正後的RPN
ϕ
2001-12-22
介绍完毕
谢 谢 各 位!
2001-12-22 Jess Consulta2-22
制造和裝配過程 潛在的失效模式及後果分析 (PFMEA)
FMEA表格之應用
15)頻度 (Occurrence)
ϕ ϕ
ϕ
指具體的失效起因發生的頻率 頻度的分級數注重其含義而不是數值, 以“1 10”級來估計頻度的大小 小组对评定准则和分级规则应意见一致。 能阻止失效模式發生的現行過程控制方法的描述 可以是防錯夾具之類的過程控制方法, 或者統計 過程控制 (SPC),或工程控制。
5) 年型/車型
ϕ
6) 關鍵日期
ϕ
2001-12-22
制造和裝配過程 潛在的失效模式及後果分析 (PFMEA)
FMEA表格之應用
7) FMEA日期
ϕ
填入編制FMEA原始稿的日期及最新修訂的日期 列出有權確定和/或執行任務的責任部門和個人 姓名 簡單描述被分析的過程或工序(如: 蝕板、沉銅、 鍍金等等)
2001-12-22 Jess Consultant 7
制造和裝配過程 潛在的失效模式及後果分析 (PFMEA)
集體的努力 (Team Effort)
負責過程的工程師應直接地、主動地聯繫所有 相關部門的代表 部門不限於: 設計、裝配、制造、材料、質量、 服務、供方以及負責下一道裝配的部門 充分地交換意見, 提高整個集體工作水平 應在生產工裝準備、過程可行性分析階段之前 開始,考慮从單個零件到完成品的所有制造工 序
2001-12-22
Jess Consultant
3
發展簡史
1985年,IEC(国际电工技术委员会)出版IEC812 70年代,美国汽车工业开始导入FMEA 80年代,逐步发展成内部的FMEA 手册,并形成DFMEA 和PFMEA两部分 1993年,FORD、GM、CHRYSLER三大公司在ASQC、 AIAG的赞助下,整合各公司要求,完成统一的FMEA参考 手册 1995年修订为第二版,并成为SAE正式技术文件SAE J1739
Jess Consultant 12
8) 核心小組
ϕ
9) 過程功能/要求
ϕ
2001-12-22
制造和裝配過程 潛在的失效模式及後果分析 (PFMEA)
FMEA表格之應用
10)潛在失效模式
ϕ
ϕ
ϕ
指過程可能發生的不滿足過程要求和/或設計意 圖, 對某具體工序不符合要求的描述 在FMEA準備中, 應假定提供的零件/材料是合格 的 假設失效可能發生, 工程師/小組成員應提出下 列問題:
ϕ
以上三种控制方法的优先运用顺序是:(1)-〉 (2)-〉(3)
2001-12-22
Jess Consultant
18
制造和裝配過程 潛在的失效模式及後果分析 (PFMEA)
FMEA表格之應用
17) 不易探測度 (Detection)
ϕ
ϕ ϕ
指零件離開制造工序或裝配工位之前, 第二種現 行過程控制方法找出失效起因/過程缺陷的可能 性之評價指標; 或用第三種過程控制方法找出後 工序發生失效模式的可能性之評價指標 評價指標分為“1 - 10”級 不要擅自推斷, 因頻度低, 不易探測度數也低。 一定要評價過程控制方法去找出不易發生的失效 模式的能力或阻止它們進一步蔓延