PCD刀具的加工过程
什么是PCD
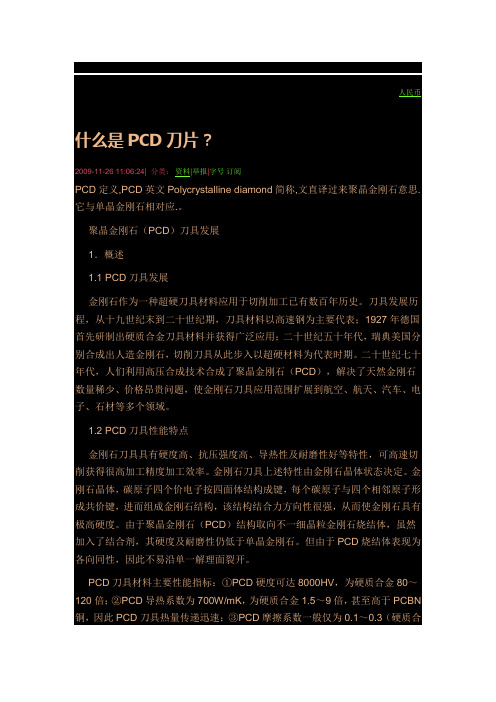
人民币什么是PCD刀片?2009-11-26 11:06:24| 分类:资料|举报|字号订阅PCD定义,PCD英文Polycrystalline diamond简称,文直译过来聚晶金刚石意思.它与单晶金刚石相对应.。
聚晶金刚石(PCD)刀具发展1.概述1.1 PCD刀具发展金刚石作为一种超硬刀具材料应用于切削加工已有数百年历史。
刀具发展历程,从十九世纪末到二十世纪期,刀具材料以高速钢为主要代表;1927年德国首先研制出硬质合金刀具材料并获得广泛应用;二十世纪五十年代,瑞典美国分别合成出人造金刚石,切削刀具从此步入以超硬材料为代表时期。
二十世纪七十年代,人们利用高压合成技术合成了聚晶金刚石(PCD),解决了天然金刚石数量稀少、价格昂贵问题,使金刚石刀具应用范围扩展到航空、航天、汽车、电子、石材等多个领域。
1.2 PCD刀具性能特点金刚石刀具具有硬度高、抗压强度高、导热性及耐磨性好等特性,可高速切削获得很高加工精度加工效率。
金刚石刀具上述特性由金刚石晶体状态决定。
金刚石晶体,碳原子四个价电子按四面体结构成键,每个碳原子与四个相邻原子形成共价键,进而组成金刚石结构,该结构结合力方向性很强,从而使金刚石具有极高硬度。
由于聚晶金刚石(PCD)结构取向不一细晶粒金刚石烧结体,虽然加入了结合剂,其硬度及耐磨性仍低于单晶金刚石。
但由于PCD烧结体表现为各向同性,因此不易沿单一解理面裂开。
PCD刀具材料主要性能指标:①PCD硬度可达8000HV,为硬质合金80~120倍;②PCD导热系数为700W/mK,为硬质合金1.5~9倍,甚至高于PCBN 铜,因此PCD刀具热量传递迅速;③PCD摩擦系数一般仅为0.1~0.3(硬质合金摩擦系数为0.4~1),因此PCD刀具可显著减小切削力;④PCD热膨胀系数仅为0.9×10 -6~1.18×10 -6,仅相当于硬质合金1/5,因此PCD刀具热变形小,加工精度高;⑤PCD刀具与有色金属非金属材料间亲力很小,加工过程切屑不易粘结刀尖上形成积屑瘤。
PCD球头刀的制作工艺
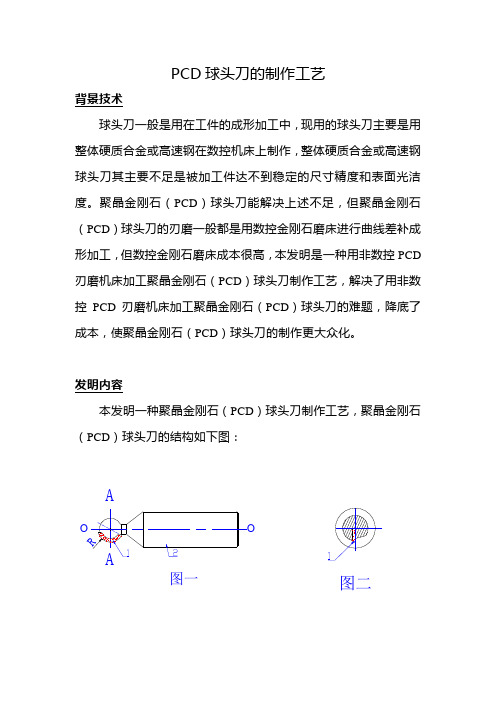
PCD 球头刀的制作工艺 背景技术球头刀一般是用在工件的成形加工中,现用的球头刀主要是用整体硬质合金或高速钢在数控机床上制作,整体硬质合金或高速钢球头刀其主要不足是被加工件达不到稳定的尺寸精度和表面光洁度。
聚晶金刚石(PCD )球头刀能解决上述不足,但聚晶金刚石(PCD )球头刀的刃磨一般都是用数控金刚石磨床进行曲线差补成形加工,但数控金刚石磨床成本很高,本发明是一种用非数控PCD 刃磨机床加工聚晶金刚石(PCD )球头刀制作工艺,解决了用非数控PCD 刃磨机床加工聚晶金刚石(PCD )球头刀的难题,降底了成本,使聚晶金刚石(PCD )球头刀的制作更大众化。
发明内容本发明一种聚晶金刚石(PCD )球头刀制作工艺,聚晶金刚石(PCD )球头刀的结构如下图:oA图一图二图一球头刀的正视图,图二是以A-A为剖面的侧面剖视图,它由带有圆弧R的PCD刀片1和金属刀杆2组成,PCD刀片1焊接或粘接在刀杆2球头上的刀槽内,前角0°,后角20°左右。
加工工件时,刀具绕刀杆2的回转中心O—O回转,在被加工件上形成一个半径为R的球形凹槽,最终产品的尺寸检测是用一半径为R标准球在涂有红丹的工件的凹槽内滚动,以接触面的百分比来判定合格否。
生产加工工艺方案聚晶金刚石(PCD)球头刀的刃磨一般都是用数控金刚石磨床进行曲线差补成形加工,在没有能刃磨球头PCD数控机床时,通过下工艺我们可以在非数控PCD刃磨机床上进行加工。
其工艺路线如下:10、切割PCD刀片120、磨PCD刀片1圆弧R控制尺寸精度和形状精度30、检验PCD刀片1尺寸R 下接第130工序40、刀杆2下料50、车刀杆2外形60、刀杆2淬火、回火70、电火花打刀杆2中心孔80、研磨刀杆2中心孔90、磨刀杆2外圆100、磨刀杆2球头110、线切割切刀杆2球头上刀槽120、磨刀杆2球头排屑倒角130、将PCD刀片1焊在刀杆2球头上刀槽内140、检验PCD刀片1中心偏量和轴向倾角150、检验PCD刀片1刃口在所有工序中,工序20、110、130、150对刀具精度的影响最大;其中,工序20磨PCD刀片1圆弧R控制尺寸精度是核心工艺技术,是关键工序。
金刚石(PCD)铰刀的产品介绍及应用

量,是对金刚石铰刀寿命有很大的影响。 ⑥ 前导向部:前导部是考虑与加工前的孔,其中最小间隙为10--20米欧。
同时还需要注意冷却槽的设计 金刚石铰刀铰孔时,若热量和切屑来不及排出,刀体将发热膨胀,孔的加工质量会明显降低,严重时还会发生“咬死”刀现象。
内镀法
金刚石铰刀内镀的方法: 采用稳定材料制造一个与铰刀外形相反的
高精度内孔胎模,将金刚石磨粒电镀在胎模内表 面,加厚形成电镀层,再将镀层与刀杆粘结在一 起。
金刚石颗粒的顶端整齐,规则地排列在模具 的内表面上,等高性和均匀性较好;
无需修磨,微刃锋利;
所加工孔的尺寸精度和几何精度较高,表面 粗糙度较小,使用寿命较长。
2 PCD铰刀
PCD铰刀的定义及优势
PCD铰刀,一般根据直径大小,采用合金基体或者钢制基体。刃数为2刃或2刃以上。此类刀具主要用于加工公 差要求比较严格,光洁度要求比较高的孔,通孔盲孔均可加工。此类刀具加工的孔,光洁度最高可达Ra0.1以内。
PCD铰刀的优势
具有超高硬度和耐磨性; 具有超长刀具使用寿命; 切削性能稳定,加工效率高; 提高尺寸精度和工艺可靠性。
备注:一般直径15mm左右的可以做成可调式金刚石铰刀,但由于国内市场,可调式金刚石铰刀精度没有固定时金刚 石铰刀好,如果要求精度较高的情况下, 建议选择固定式金刚石铰刀
金刚石铰刀的组成结构及优势
金刚石铰刀的优势
镀层结合力,金刚石粘结牢度,金刚石颗粒分布均匀,外观质量高; 金刚石铰刀前后导向外圆度达到0.005mm,圆柱度为0.005mm/100mm,前导向外圆粗糙度Ra0.63微米, 后导向外圆粗糙度Ra0.16um,刀柄与前后导向部分的同轴度达到0.015mm; 被铰孔工件圆柱度小于0.003,粗糙度可达Ra0.4-0.2,精度高,效率高,使用寿命长; “量体裁衣”式服务,规范化流程,为客服创造的价值超越契约。
pcd工艺技术

pcd工艺技术PCD工艺技术(Polycrystalline Diamond)是一种综合利用钻石结晶技术制造的新材料。
它具有钻石硬度高、耐磨性好和热稳定性好等特点,被广泛应用于机械加工、矿山工具、石油勘探等领域。
PCD工艺技术的制造过程主要包括镀膜、压制和烧结三个步骤。
首先,在刀具表面镀上一层金属膜,以增加PCD与基体的结合力。
然后,将金属粉末与聚结剂混合均匀,填充在模具中,经过高温高压的条件下,金属粉末固化成坚硬的基体。
最后,将钻石晶粒均匀分布在基体中,再次进行高温高压的处理,使钻石晶粒与基体结合紧密,形成具有钻石硬度的PCD。
PCD工艺技术的优点主要体现在以下几个方面。
首先,PCD材料的硬度可达到钻石的六倍,因此具有极高的耐磨性。
在机械加工领域,使用PCD材料制造的刀具能够在高速切削和重负荷的工况下保持长时间的使用寿命。
其次,PCD材料具有极高的热稳定性,能够在高温和高速的加工环境下保持稳定的性能。
在石油勘探领域,使用PCD材料制造的特殊钻头能够快速、高效地穿透各种复杂的地层。
此外,PCD材料的导电性好,因此可以应用于电子器件的制造。
最后,PCD材料的结构稳定,不会轻易损坏,因此能够在恶劣的工作环境中长期使用。
然而,PCD工艺技术也存在一些挑战和局限性。
首先,PCD材料的制造工艺复杂,需要采用高温高压的处理,因此生产成本较高。
其次,由于钻石是一种贵重的材料,PCD材料的价格也相对较高,限制了其在一些领域的广泛应用。
此外,由于PCD材料的硬度高,加工和修复过程相对困难,也增加了维护和使用成本。
总之,PCD工艺技术是一种重要的先进材料制备技术。
它适用于各种领域,如机械加工、矿山工具和石油勘探等。
尽管制造工艺复杂,成本较高,但其优异的性能使其在特定领域有着广阔的应用前景。
未来,随着科技的不断发展,PCD工艺技术有望进一步完善,降低生产成本,提高材料性能,推动其在更多领域的应用。
加工石墨的刀具选择—PCD刀具

加工石墨的刀具选择—PCD刀具石墨是碳的一种同素异形体,尤其石墨的高磨蚀性、耐高温等性能,广泛应用于模具、坩埚、点击、电池、电刷等领域。
但由于石墨质坚而脆,所以采用车、铣等常规机械加工方法时,旺旺在加工表面会产生崩损现象。
因此车、铣加工石墨模/石墨电极等制品时,切削刀具需具备高的耐磨损性和抗冲击性。
本文就重点介绍一下车、铣加工石墨模具/石墨电极等制品的刀具材质选择,及其加工刀具的规格型号选择。
1、石墨制品的介绍(1)石墨制品之石墨模具的介绍模具作为工业生产中使用极为广泛的基础工艺装备,大到机身外壳,小到一个螺丝,都是根据成型模具,通过冲压、锻压、压铸、挤压、注塑等方式使坯料成为符合产品要求的零件。
模具的形状和加工质量、精度决定着产品的外形和质量。
近年来随着模具行业飞速发展,石墨以其良好的物理和化学性能逐渐成为模具制作的理想选择材料。
现如今许多产业部门,如机电、汽车、家电轻工、电器仪表、通讯、军械等行业的发展均依赖于模具工业的技术提高和发展。
(2)石墨制品之石墨电极的介绍石墨电极是指以石油焦、沥青焦为骨料,煤沥青为黏结剂,经过原料煅烧、破碎磨粉、配料、混捏、成型、焙烧、浸渍、石墨化和机械加工而制成的一种耐高温石墨质导电材料,称为人造石墨电极(简称石墨电极)。
石墨电极的优点是加工较容易,放电加工去除率高,石墨损耗小,因此,部分群基火花机客户放弃了铜电极而改用石墨电极。
目前石墨电极主要用于电弧炼钢炉,矿热电炉,电阻炉等行业,同时石墨电极的毛坯还用于加工成各种坩埚、模具、舟皿和发热体等异型石墨产品。
(3)石墨制品之石墨坩埚的介绍石墨坩埚,又称熔铜包、熔铜等,是指以石墨、粘土、硅石和腊石为原料烧制而成的一类坩埚。
石墨坩埚具有耐高温、导热性能强、热膨胀系数小、抗腐蚀性能好,化学稳定性强,使用寿命长等特点。
被广泛用于合金工具钢冶炼和有色金属(紫铜、黄铜、金、银、锌和铅)及其合金的冶炼。
(4)其他石墨制品介绍除了以上是那种零部件,石墨广泛用于耐火材料、导电材料、耐磨材料、润滑剂、耐高温密封材料、耐腐蚀材料、隔热材料、吸附材料、摩擦材料和防辐射等材料中,这些材料广泛应用于冶金、石油化工、机械工业、电子产业、核工业和国防等。
PCD刀具工序流程表

验收、打码、包装、入库(品检部)
→
出货(仓库)
→
新锯片 工序流程
新锯片 工序流程
→ → → 下订单
设计(绘图)
刀体下料(采购)
验收刀体(品检部)
→
入库、领刀体(品检部)
→
研磨刀体、加工焊刀位、领料、焊接(焊工部)
→
检测焊接(品检 部)
→
检测两侧跳动(品检部)
热处理、喷砂(焊工部)
→
→ → 研磨外圆(强力磨部)
验收、磨两侧(强力磨部) 验收、检测(品检部)
→ 包胶、喷砂、抛光、电镀(焊工部)
验收、打码、包装、入库(品检部)
→
出货(仓库)
→ →
新修边刀 工序流程
新修边刀 工序流程
→ → → 下订单
设计(绘图)
刀体下料(机பைடு நூலகம்部)
刀体车、铣、镗、刀体成型(机加部)
验收刀体(品检部)
→ → 割键槽(线切割)
验收、入库、领刀体(品质部)
→
→ → 处理焊刀位、领齿、焊接(焊工部)
检测焊接(品检部)
喷砂、磨平面、电镀(焊工部)
品质验收(品检部)
→ → 统一外径(强力磨部)
粗、精磨加工(火花机)
检测、打码、包胶、包装、入库(品检部)
→
出货(仓库)
→ → →
工序流程表
新V-CUT 工序流程
新V-CUT 工序流程
→ 下订单
设计(绘图)
→ 刀体下料(采购)
→
验收刀体(品检部)
→
入库、领刀体(品检部)
→ → → 研磨刀体(强力磨部)
验收刀体研磨(品检部)
→ → 加工焊刀位、领齿、焊接(焊工部)
PCD刀具磨削机理及刃磨工艺研究论文
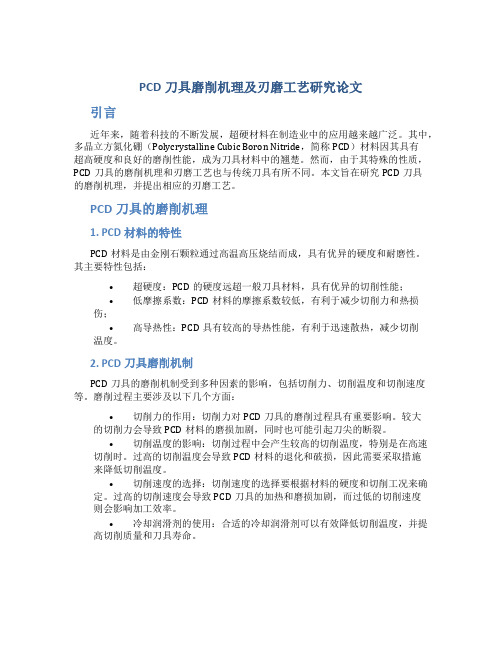
PCD刀具磨削机理及刃磨工艺研究论文引言近年来,随着科技的不断发展,超硬材料在制造业中的应用越来越广泛。
其中,多晶立方氮化硼(Polycrystalline Cubic Boron Nitride,简称PCD)材料因其具有超高硬度和良好的磨削性能,成为刀具材料中的翘楚。
然而,由于其特殊的性质,PCD刀具的磨削机理和刃磨工艺也与传统刀具有所不同。
本文旨在研究PCD刀具的磨削机理,并提出相应的刃磨工艺。
PCD刀具的磨削机理1. PCD材料的特性PCD材料是由金刚石颗粒通过高温高压烧结而成,具有优异的硬度和耐磨性。
其主要特性包括:•超硬度:PCD的硬度远超一般刀具材料,具有优异的切削性能;•低摩擦系数:PCD材料的摩擦系数较低,有利于减少切削力和热损伤;•高导热性:PCD具有较高的导热性能,有利于迅速散热,减少切削温度。
2. PCD刀具磨削机制PCD刀具的磨削机制受到多种因素的影响,包括切削力、切削温度和切削速度等。
磨削过程主要涉及以下几个方面:•切削力的作用:切削力对PCD刀具的磨削过程具有重要影响。
较大的切削力会导致PCD材料的磨损加剧,同时也可能引起刀尖的断裂。
•切削温度的影响:切削过程中会产生较高的切削温度,特别是在高速切削时。
过高的切削温度会导致PCD材料的退化和破损,因此需要采取措施来降低切削温度。
•切削速度的选择:切削速度的选择要根据材料的硬度和切削工况来确定。
过高的切削速度会导致PCD刀具的加热和磨损加剧,而过低的切削速度则会影响加工效率。
•冷却润滑剂的使用:合适的冷却润滑剂可以有效降低切削温度,并提高切削质量和刀具寿命。
PCD刀具的刃磨工艺研究1. PCD刀具的刃磨方法刃磨是PCD刀具加工过程中的重要环节。
常见的PCD刃磨方法包括:•电火花刃磨:利用电火花放电原理将切削刃磨成所需形状。
•摩擦刃磨:通过材料之间的摩擦磨去刃口,得到所需的切削刃。
•光束刃磨:利用高能光束将刃口融化并形成所需形状。
关于铝合金材料PCD刀具加工应用的研究

关于铝合金材料PCD刀具加工应用的研究作者:刘源来源:《科教导刊·电子版》2017年第12期摘要铝合金材料被广泛运用于汽车、飞机等装备制造领域,有利于减轻机械动力负荷,实现机械设备的轻型化、小型化发展。
在铝合金材料的运用过程中,PCD切割工具以其硬度高、热膨胀系数低、与铝合金亲合小的特点被广泛运用于铝合金的切削加工领域。
本文对PCD刀具加工应用方法进行了研究,探索了PCD刀具钝化处理的技术,以及钝化处理后对于切削铝合金材料的影响。
关键词 PCD刀具钝化处理铝合金材料目前,PCD(金刚石)刀具已经大规模的运用铝合金等有色金属的切削加工中。
为提高PCD刀具的使用寿命和加工质量,笔者在工作实践的基础上,结合现有的研究成果,进行了PCD刀具钝化和铝合金材料切削实验,对PCD刀具钝化技术和要求,有针对性地进行了优化。
1 PCD刀具的钝化技术的原理PCD刀具的钝化技术是对PCD刀具进行深加工,提高刀具运用水平的重要方法。
笔者在实践中发现,PCD刀具在切削加工铝合金的过程中,使用初期会表现出加工质量不高、磨损较快等问题。
随着使用时间的延长,其加工的质量越来越高。
其实现的原理主要是:PCD刀具在刃磨后会出现一些毛刺和微缺口,但是在车削铝合金材料长时间磨损中,刀具刃口出现钝化,毛刺和微缺口被去除,切削刃变得光滑,提高刀具的使用寿命和加工质量。
2 PCD刀具的钝化和铝合金材料车削实验本文进行的实验主要由两个部分组成:一是PCD刀具的钝化实验;一是钝化PCD刀具对铝合金材料的切削实验。
2.1关于的PCD刀具的钝化实验在实验中,笔者采用了小型可转位刀片刃口钝化机,通过刀具与钝化机磨刷之间的磨损运动,对PCD刀具进行刃口钝化观察。
为了观察不同的磨刷与PCD刀具钝化的关系,笔者在试验中分别选用含400目、800目、1000目、1200目金刚石磨料的磨料刷,转速800r/min,切削刃和磨料刷接触长度为2mm进行实验。
可与单晶金刚石刀具媲美的PCD刀具

车削加工也可以采用能帮助
3
为 了 获 得 更 长 的 刀具 寿 命 ,
同样 ,一些 新 的精 铣 技 术 可
刚 石 刀 具 的 切 削 刃 表 面 波 度 为 需要满足三个条件 : ① 刀具 的使 将 两 种 有效 的切 削技 术 融合 于 一
0 . 3 7 u m ,可 与单 晶 金 刚 石 刀具 用方式符合其设计 用途 ; ② 刀具 种 刀 轨之 中。这 种 刀 轨 能对 工件 的 表面 质 量 媲 美 。
镜 头 制造 商 C u s t o m C r a f t 公司
用这 种 C V D 金 刚 石 刀 具 在 与刀具寿命密切相 关 : ① 控制 刀 减 小 工作 量 和 刀具 磨 损 。其 他一
Op t o f o r m 车 床 上 加 工 镜 头 。 据 具的移动路径 ( 刀轨 ) ; ②确定 刀 些新 的动 态 铣 削技 术 也 有助 于 在 该 公 司 介 绍 ,在 需 要 重 磨 之 前 , 具切入 / 切 出工件 材料 的方式 。 清根加工 时提高刀具加工效 率。 C V D 金 刚 石 刀 具 加 工 的 镜 头 数 如 今 , 采 用 老式 算 法 驱 动 机 床 的 另 一 种 刀轨 采 用 高速 仿 形铣 沿 侧
t i R o u g h刀 轨 的 高 效 铣 有 所 提 高 。 实验 室 测试 表 明 , 利 用 CAM 编 程 技 术 延 长 刀 图 采 用 Op
( 张)
S i mp l e T e c h n o l o g y公 司 用 于 加 具 寿 命
削 策 略
工精密光 学镜头 的新型 C V D金
量与单 晶金刚石刀具相 当 , 而 加 传 统 刀 轨 已被 采 用 先 进 算 法 的 壁切除工件材料。它支持 多次走
PCD刀具的刃口加工方法及技术

小, 可 降低加 工 表面粗 糙 度 。但 由 于聚 晶金 刚 石 与铁 族元 素有 很强 的亲和 力 , 因此不 适合 加工 黑 色金属 及
其合金。 P C D刀具在有色金属及其合金、 非 金 属 材 料 及 复合 材料 的切 削 中体 现 出优 良的切 削性 能 , 可用 于制 作 车刀 、 镗刀 、 铣 刀 和钻头 、 铰刀、 锪刀、 锯刀 、 镂刀、 剃
Ab s t r a c t : Th e P CD c u t t i n g t o o l i s a n e w t y p e o f t o o l d e v e l o p i n g s i n c e t h e 7 0 S ,i t s g o o d p e r f o r ma n c e s h a s p l a y e d a n i mp o r t a n t r o l e i n mo d e r n p r o c e s s i n g i n d u s t r y . Th i s p a p e r d e s c r i b e s t h e PC D c u t t i n g t o o l c o m mo n l y u s e d p a r t s p r o c e s s i n g me t h o d,i . e ..e l e c t r i c a l d i s c h a r g e ma c h i n i n g -d i a mo n d g r i n d i n g wh e e l p r o c e s s i n g a n d d i a mo n d g r i n d i n g p r o c e s s i n g - a n a l y z e s t h e p r o c e s s i n g p r i n c i p l e ,i n f l u e n c e f a c t o r s t p r o c e s s i n g c o n d i t i o n a n d a p p l i c a t i o n s i t u a t i o n e t c . . By c h o o s i n g t h e r e a s o n a b l e PC D c u t t i n g t o o l e d g e p r o c e s s i n g me t h o d t o
PCD聚晶金刚石刀具特性及其适合加工的材料简介

PCD 聚晶金刚石刀具特性及其适合加工的材料简介图1努氏硬度图2断裂韧性图3导热性制备工艺PCD是由大量随机定向的金刚石颗粒在极困难的条件下进行人工合成得到的。
它通过在高压高温下烧结精选的金刚石颗粒进行制备。
烧结过程在金刚石稳定区内被严格地控制,于是生产出一种极硬且耐磨的结构。
特性PCD是由大量随机定向的金刚石颗粒在极困难的条件下进行人工合成得到的。
它通过在高压高温下烧结精选的金刚石颗粒进行制备。
烧结过程在金刚石稳定区内被严格地控制,于是生产出一种极硬且耐磨的结构。
特性以聚晶形态组成的金刚石提供了一种强大的切削刀具,它提供极好的硬度及由此得到的耐磨性,并与聚晶结构所带来的极佳韧性相结合。
此外,金刚石拥有所有刀具材料中最高的导热性,使得热量迅速从切削刃传递出来。
除PCD与铁的高亲合力以外,PCD不会与工件材料粘结,在正确的切削参数下,积屑瘤是最小化的。
所有的SecomaxPCD刀具都拥有镜面抛光的前刀面,提供最低的摩擦系数和光滑的切削刃。
适合加工的工件材料铝合金铝合金已成为交通工业需求的致力于减轻重量的理想材料。
尽管铝合金的生产在能量消耗上具有更大的初始需求,但在长期运作中证明有更多的益处,这些合金的性能将超过其它与其竞争的材料。
纯铝的硬度低、耐腐蚀。
举例讲,添加铜或镁等合金元素将使该材料具有更高的强度。
巿场上有很多种铝合金,最著名的莫过于分别用于汽车与航空航天行业的2000及6000系列。
锻造和铸造铝合金之间有明显的分界线,各有几种不同的材质等级,而且有各式各样的硬化处理性能。
对于硅(Si)含量低到中等的硅合金来说,PCD在铣削应用与粗加工中提供了最好的耐磨性,见下表。
所遭遇到的最常见的问题应该是积屑瘤。
即使是很高的切削速度,加工低硅铝合金时也会发生这种情况。
切削刃的几何角度和质量必须要被小心地应用。
采用这样的参数,当与工件的接触时间越久,产生的热量上升,其直接的影响就是刀具寿命的缩短。
对于加工高硅铝合金,PCD的耐磨性被完全地利用。
PCD刀具应用综述
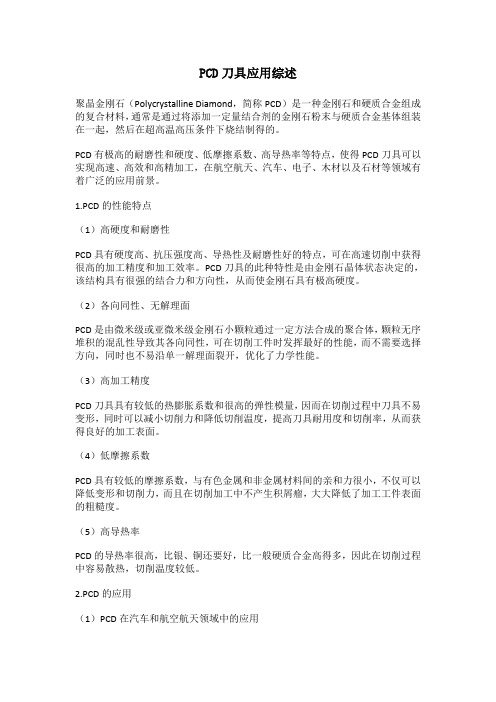
PCD刀具应用综述聚晶金刚石(Polycrystalline Diamond,简称PCD)是一种金刚石和硬质合金组成的复合材料,通常是通过将添加一定量结合剂的金刚石粉末与硬质合金基体组装在一起,然后在超高温高压条件下烧结制得的。
PCD有极高的耐磨性和硬度、低摩擦系数、高导热率等特点,使得PCD刀具可以实现高速、高效和高精加工,在航空航天、汽车、电子、木材以及石材等领域有着广泛的应用前景。
1.PCD的性能特点(1)高硬度和耐磨性PCD具有硬度高、抗压强度高、导热性及耐磨性好的特点,可在高速切削中获得很高的加工精度和加工效率。
PCD刀具的此种特性是由金刚石晶体状态决定的,该结构具有很强的结合力和方向性,从而使金刚石具有极高硬度。
(2)各向同性、无解理面PCD是由微米级或亚微米级金刚石小颗粒通过一定方法合成的聚合体,颗粒无序堆积的混乱性导致其各向同性,可在切削工件时发挥最好的性能,而不需要选择方向,同时也不易沿单一解理面裂开,优化了力学性能。
(3)高加工精度PCD刀具具有较低的热膨胀系数和很高的弹性模量,因而在切削过程中刀具不易变形,同时可以减小切削力和降低切削温度,提高刀具耐用度和切削率,从而获得良好的加工表面。
(4)低摩擦系数PCD具有较低的摩擦系数,与有色金属和非金属材料间的亲和力很小,不仅可以降低变形和切削力,而且在切削加工中不产生积屑瘤,大大降低了加工工件表面的粗糙度。
(5)高导热率PCD的导热率很高,比银、铜还要好,比一般硬质合金高得多,因此在切削过程中容易散热,切削温度较低。
2.PCD的应用(1)PCD在汽车和航空航天领域中的应用PCD刀具在汽车领域主要用于加工发动机活塞的裙部、销孔、汽缸体、变速箱等。
由于这些部件材料含硅量较高(10%以上),对刀具的使用寿命要求高,而PCD 刀具耐用度是硬质合金刀具的1-50倍,可保证零部件尺寸的稳定性,并可大大提高切削速度、加工效率和工件的表面质量。
聚晶金刚石(PCD)刀具

PCD的定义,PCD是英文Polycrystalline diamond的简称,中文直译过来是聚晶金刚石的意思.它与单晶金刚石相对应.摘自:中国机械资讯网聚晶金刚石(PCD)刀具发展1.概述1.1 PCD刀具的发展金刚石作为一种超硬刀具材料应用于切削加工已有数百年历史。
在刀具发展历程中,从十九世纪末到二十世纪中期,刀具材料以高速钢为主要代表;1927年德国首先研制出硬质合金刀具材料并获得广泛应用;二十世纪五十年代,瑞典和美国分别合成出人造金刚石,切削刀具从此步入以超硬材料为代表的时期。
二十世纪七十年代,人们利用高压合成技术合成了聚晶金刚石(PCD),解决了天然金刚石数量稀少、价格昂贵的问题,使金刚石刀具的应用范围扩展到航空、航天、汽车、电子、石材等多个领域。
1.2 PCD刀具的性能特点金刚石刀具具有硬度高、抗压强度高、导热性及耐磨性好等特性,可在高速切削中获得很高的加工精度和加工效率。
金刚石刀具的上述特性是由金刚石晶体状态决定的。
在金刚石晶体中,碳原子的四个价电子按四面体结构成键,每个碳原子与四个相邻原子形成共价键,进而组成金刚石结构,该结构的结合力和方向性很强,从而使金刚石具有极高硬度。
由于聚晶金刚石(PCD)的结构是取向不一的细晶粒金刚石烧结体,虽然加入了结合剂,其硬度及耐磨性仍低于单晶金刚石。
但由于PCD烧结体表现为各向同性,因此不易沿单一解理面裂开。
PCD刀具材料的主要性能指标:①PCD的硬度可达8000HV,为硬质合金的80~120倍;②PCD的导热系数为700W/mK,为硬质合金的1.5~9倍,甚至高于PCBN和铜,因此PCD刀具热量传递迅速;③PCD的摩擦系数一般仅为0.1~0.3(硬质合金的摩擦系数为0.4~1),因此PCD刀具可显著减小切削力;④PCD的热膨胀系数仅为0.9×10 -6~1.18×10 -6,仅相当于硬质合金的1/5,因此PCD刀具热变形小,加工精度高;⑤PCD刀具与有色金属和非金属材料间的亲和力很小,在加工过程中切屑不易粘结在刀尖上形成积屑瘤。
PCD刀具

PCD的定义,PCD是英文Polycrystalline diamond的简称,中文直译过来是聚晶金刚石的意思.它与单晶金刚石相对应.摘自:中国机械资讯网聚晶金刚石(PCD)刀具发展1.概述1.1 PCD刀具的发展金刚石作为一种超硬刀具材料应用于切削加工已有数百年历史。
在刀具发展历程中,从十九世纪末到二十世纪中期,刀具材料以高速钢为主要代表;1927年德国首先研制出硬质合金刀具材料并获得广泛应用;二十世纪五十年代,瑞典和美国分别合成出人造金刚石,切削刀具从此步入以超硬材料为代表的时期。
二十世纪七十年代,人们利用高压合成技术合成了聚晶金刚石(PCD),解决了天然金刚石数量稀少、价格昂贵的问题,使金刚石刀具的应用范围扩展到航空、航天、汽车、电子、石材等多个领域。
1.2 PCD刀具的性能特点金刚石刀具具有硬度高、抗压强度高、导热性及耐磨性好等特性,可在高速切削中获得很高的加工精度和加工效率。
金刚石刀具的上述特性是由金刚石晶体状态决定的。
在金刚石晶体中,碳原子的四个价电子按四面体结构成键,每个碳原子与四个相邻原子形成共价键,进而组成金刚石结构,该结构的结合力和方向性很强,从而使金刚石具有极高硬度。
由于聚晶金刚石(PCD)的结构是取向不一的细晶粒金刚石烧结体,虽然加入了结合剂,其硬度及耐磨性仍低于单晶金刚石。
但由于PCD烧结体表现为各向同性,因此不易沿单一解理面裂开。
PCD刀具材料的主要性能指标:①PCD的硬度可达8000HV,为硬质合金的80~120倍;②PCD的导热系数为700W/mK,为硬质合金的1.5~9倍,甚至高于PCBN和铜,因此PCD刀具热量传递迅速;③PCD的摩擦系数一般仅为0.1~0.3(硬质合金的摩擦系数为0.4~1),因此PCD刀具可显著减小切削力;④PCD的热膨胀系数仅为0.9×10 -6~1.18×10 -6,仅相当于硬质合金的1/5,因此PCD刀具热变形小,加工精度高;⑤PCD刀具与有色金属和非金属材料间的亲和力很小,在加工过程中切屑不易粘结在刀尖上形成积屑瘤。
PCD﹑PCBN刀具材料及刀具涂层
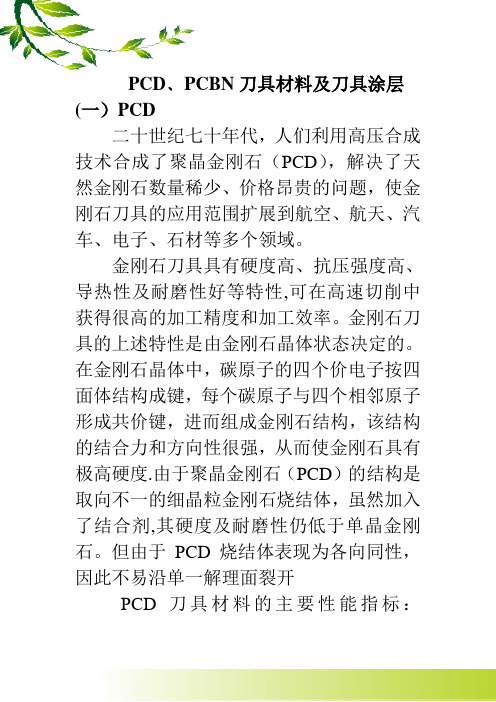
PCD﹑PCBN刀具材料及刀具涂层(一)PCD二十世纪七十年代,人们利用高压合成技术合成了聚晶金刚石(PCD),解决了天然金刚石数量稀少、价格昂贵的问题,使金刚石刀具的应用范围扩展到航空、航天、汽车、电子、石材等多个领域。
金刚石刀具具有硬度高、抗压强度高、导热性及耐磨性好等特性,可在高速切削中获得很高的加工精度和加工效率。
金刚石刀具的上述特性是由金刚石晶体状态决定的。
在金刚石晶体中,碳原子的四个价电子按四面体结构成键,每个碳原子与四个相邻原子形成共价键,进而组成金刚石结构,该结构的结合力和方向性很强,从而使金刚石具有极高硬度.由于聚晶金刚石(PCD)的结构是取向不一的细晶粒金刚石烧结体,虽然加入了结合剂,其硬度及耐磨性仍低于单晶金刚石。
但由于PCD烧结体表现为各向同性,因此不易沿单一解理面裂开PCD刀具材料的主要性能指标:①PCD的硬度可达8000HV,为硬质合金的80~120倍;②PCD的导热系数为700W/mK,为硬质合金的1.5~9倍,甚至高于PCBN和铜,因此PCD刀具热量传递迅速;③PCD的摩擦系数一般仅为0。
1~0。
3(硬质合金的摩擦系数为0。
4~1),因此PCD 刀具可显著减小切削力;④PCD的热膨胀系数仅为0。
9×10 —6~1。
18×10 -6,仅相当于硬质合金的1/5,因此PCD刀具热变形小,加工精度高;⑤PCD刀具与有色金属和非金属材料间的亲和力很小,在加工过程中切屑不易粘结在刀尖上形成积屑瘤. PCD刀具的应用:工业发达国家对PCD刀具的研究开展较早,其应用已比较成熟。
自1953年在瑞典首次合成人造金刚石以来,对PCD刀具切削性能的研究获得了大量成果,PCD刀具的应用范围及使用量迅速扩大.目前,国际上著名的人造金刚石复合片生产商主要有英国De Beers公司、美国GE公司、日本住友电工株式会社等。
据报道,1995年一季度仅日本的PCD刀具产量即达10。
PCD刀具应用PPT课件
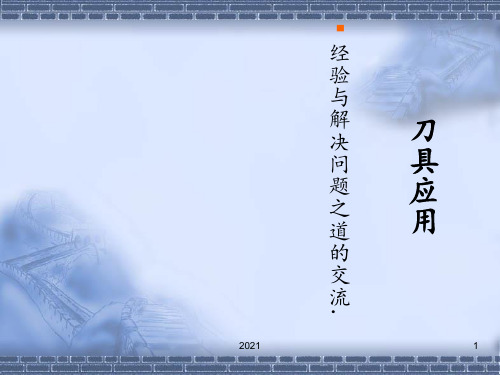
Hole diameter
/孔的直径
Hole diameter if tool is low end High toleranz
/上公差
1 1000 4000 8000 12000 16000 25000 50000 75000100000125000
holes
2021
43
改进程序
是什么让改进方法获得成功
2021
20
镗刀形式介绍
缩写注解
D = 刀具直径 RS = 圆刃带宽度 S = PCD层厚度 W = 直径后角
2021
21
镗刀形式介绍-样式 1
旋转方向
标准导引角
• 几乎60%的镗刀可以采用 • 需研磨 • 最好做成圆刃带 • 用于通孔 • 盲孔但是没有特别指明工件孔底形状的
进给方向
2021
22
7
8
9 10 11 12
▪ 步骤4: 将得到的数据做成表格如果有问题改换试验数 据重复以上步骤试验.
2021
13
问题解答
刀具直径和孔直径的比较
▪ 理想的孔直径是比刀具直 径大3 -4µm
▪ 如果孔直径超差则90%的 可能是刀具的圆跳动超差,
▪ 修正刀具到圆跳动符合要 求.
2021
14
问题解答
刀具直径和孔直径的比较
油泵壳体精加工
2+4刃设计 从第一段就开始用导条 钢质刀杆 第二段用刀尖圆角设计
2021
34
从切削刃直径到导条直径
▪ 在导条的做法上, Mapal和WWS是不同的.
▪ Mapal刀具装上导条目的是让导条直接撑住加工 表面,
▪ WWS的导条浮动在孔内, 在孔内引导和稳定道具.
PCD刀具激光加工技术及其装备研究进展

PCD刀具激光加工技术及其装备研究进展
郭靖雅;胡小月;王成勇;丁峰;唐梓敏
【期刊名称】《工具技术》
【年(卷),期】2024(58)4
【摘要】聚晶金刚石(PCD)刀具在硬脆材料的高精高效加工方面具有显著优势,但常规的PCD刀具制造技术存在加工效率低、局限性大等问题,激光加工是一种实现PCD刀具高效高质加工的有效技术。
本文总结了PCD材料激光加工去除机理,归纳了激光加工中波长、脉宽等工艺参数对PCD材料加工质量的影响规律,重点概述了激光加工技术在PCD刀具切削刃、表面纹理、烧蚀成型等方面的应用现状,介绍了国内激光加工装备的研发进展与现状。
【总页数】10页(P3-12)
【作者】郭靖雅;胡小月;王成勇;丁峰;唐梓敏
【作者单位】广东工业大学机电工程学院;高性能工具全国重点实验室
【正文语种】中文
【中图分类】TG711;TG665;TH162.1
【相关文献】
1.PCD刀具的刃口加工方法及技术
2.PCD刀具孔加工过程中的切屑控制方法
3.PCD刀具精密切削纯铜材料表面粗糙度及加工残余应力研究
4.PCD的磨削特点与PCD刀具的刃磨技术
5.激光工艺参数对PCD刀具材料去除量的影响
因版权原因,仅展示原文概要,查看原文内容请购买。
- 1、下载文档前请自行甄别文档内容的完整性,平台不提供额外的编辑、内容补充、找答案等附加服务。
- 2、"仅部分预览"的文档,不可在线预览部分如存在完整性等问题,可反馈申请退款(可完整预览的文档不适用该条件!)。
- 3、如文档侵犯您的权益,请联系客服反馈,我们会尽快为您处理(人工客服工作时间:9:00-18:30)。
苏州固瑞合金制品有限公司
苏州固瑞合金制品有限公司PCD刀具的加工过程
PCD刀具作为最常用的切割工具,再制造工艺上也是相当严格的,那么它的加工过程是怎么样的呢?这里由小编慢慢道来。
PCD刀具加工过程主要包括两个阶段:①PCD复合片的制造:PCD 复合片是由天然或人工合成的金刚石粉末与结合剂(其中含钴、镍等金属)按一定比例在高温(1000~2000℃)、高压(5~10万个大气压)下烧结而成。
在烧结过程中,由于结合剂的加入,使金刚石晶体间形成以TiC、SiC、Fe、Co、Ni等为主要成分的结合桥,金刚石晶体以共价键形式镶嵌于结合桥的骨架中。
通常将复合片制成固定直径和厚度的圆盘,还需对烧结成的复合片进行研磨抛光及其它相应的物理、化学处理。
②PCD刀片的加工:PCD刀片的加工主要包括复合片的切割、刀片的焊接、刀片刃磨等步骤。