机加工中刀具材料的应用及发展趋势
21世纪刀具材料的发展与应用

近年 来 , 为把我 国打造成 为制 造业 的强 国 , 展 大 发
为 W6 5 rV , MoC4 2 其碳 化物 分布 细小 均匀 , 韧性 和 高温
塑性 比 W1 C4 高 5 % , 弯 强 度 达 4 7 0 MP , 8 rV 0 抗 0 a 热 处理 硬度 和切 削性 能 与 W1 C4 8 rV基 本 相 同 , 本 低 , 成 目前 正在 取代 钨系 高速 钢 。常用 于制造 钻头 、 丝锥 、 铣 刀 、 刀 、 刀 、 轮 刀 具 等 刀 具 。但 耐 磨 性 略 逊 于 铰 拉 齿
A b t a t n t spa e ,t e e a iu to fto t rasi ic se sr c :I hi p r heg n r lst ai n o lmae i l sd s u s d,l ts e eo me t i d n p lc — o ae td v l p n ,k n sa d a p ia to ft o tra sa e i to u e Isp o pe to u u e d v lp e ti r d ce . inso o lma e il r n r d c d,t r s c ff t r e e o m n s p e it d K e wo d T o ;To lM ae il y r s: o l o tras;H ih— pe d S e l g s e te ;Ce e t d Ca b d m n e r i e; Ce a c r mi
CHU iu Kay
( c a i l n ier gD p r e t N r hn lc i P w rU i r t, adn 7 0 0 C N) Meh nc gnei e at n , o hC iaEetc o e nv s y B o ig0 0 , H aE n m t r ei 1
刀具材料论文

金属切削刀具的发展历史与现状前言刀具是机械制造中用于切削加工的工具,又称切削工具。
广义的切削工具既包括刀具,还包括磨具。
刀具技术的进步,体现在刀具材料、刀具结构、刀具几何形状和刀具系统四个方面,刀具材料新产品更是琳琅满目。
当代正在应用的刀具材料有高速钢、硬质合金、陶瓷、立方氮化硼和金刚石。
其中,高速钢和硬质合金是用得最多的两种刀具材料,分别约占刀具总量的30%~40%和50%~60%。
本文将介绍刀具的发展历程,发展现状,并对未来刀具的发展法相作出分析。
刀具的发展历史刀具的发展在人类进步的历史上占有重要的地位。
中国早在公元前28~前20世纪,就已出现黄铜锥和紫铜的锥、钻、刀等铜质刀具。
战国后期(公元前三世纪),由于掌握了渗碳技术,制成了铜质刀具。
当时的钻头和锯,与现代的扁钻和锯已有些相似之处。
然而,刀具的快速发展是在18世纪后期,伴随蒸汽机等机器的发展而来的。
1783年,法国的勒内首先制出铣刀。
1792年,英国的莫兹利制出丝锥和板牙。
有关麻花钻的发明最早的文献记载是在1822年,但直到1864年才作为商品生产。
那时的刀具是用整体高碳工具钢制造的,许用的切削速度约为5米/分。
1868年,英国的穆舍特制成含钨的合金工具钢。
1898年,美国的泰勒和.怀特发明高速钢。
1923年,德国的施勒特尔发明硬质合金。
在采用合金工具钢时,刀具的切削速度提高到约8米/分,采用高速钢时,又提高两倍以上,到采用硬质合金时,又比用高速钢提高两倍以上,切削加工出的工件表面质量和尺寸精度也大大提高。
由于高速钢和硬质合金的价格比较昂贵,刀具出现焊接和机械夹固式结构。
1949~1950年间,美国开始在车刀上采用可转位刀片,不久即应用在铣刀和其他刀具上。
1938年,德国德古萨公司取得关于陶瓷刀具的专利。
1972年,美国通用电气公司生产了聚晶人造金刚石和聚晶立方氮化硼刀片。
这些非金属刀具材料可使刀具以更高的速度切削。
1969年,瑞典山特维克钢厂取得用化学气相沉积法,生产碳化钛涂层硬质合金刀片的专利。
机加工中刀具使用和发展情况论文

机加工中刀具的使用和发展情况摘要:随着材料工业及精密机械工业的发展,精密切削、超精密切削和难切削材料使用的增多,超硬刀具材料的应用日益广泛。
本文通过分析超硬刀具材料的发展状况,对主要品种的应用进行探讨。
关键词:超硬刀具刀具材料金刚石一、超硬刀具材料发展概况超硬刀具材料是指天然金刚石及硬度、性能与之相近的人造金刚石和cbn(立方氮化硼)。
由于天然金刚石价格比较昂贵,所以生产上大多采用人造聚晶金刚石(pcd)、聚晶立方氮化硼(pcbn)以及它们的复合材料。
早在20世纪50年代,美国就利用人造金刚石微粉和cbn微粉在高温、高压、触媒和结合剂的作用下烧结成尺寸较大的聚晶块作为刀具材料。
之后,南非戴比尔斯(debeem)公司、前苏联和日本也相继研制成功。
20世纪70年代初又推出了金刚石或cbn和硬质合金的复合片,它们是在硬质合金基体上烧结或压制一层0.5mm~1mm 的pcd或pcbn而成,从而解决了超硬刀具材料抗弯强度低、镶焊困难等问题,使超硬刀具的应用进入实用阶段。
我国超硬刀具材料的研究与应用开始于上个世纪70年代,并于1970年在贵阳建造了我国第一座超硬材料及制品的专业生产厂第六砂轮厂,从1970—1990年整整20年中,超硬材料年产量从仅46万克拉增至3500万克拉。
上个世纪90年代前后,不少超硬材料生产专业厂从国外引进成套的超硬材料合成设备及技术,使产量得以迅速提高,至1997年,我国人造金刚石年产量就已达到5亿克拉左右,cbn年产量达800万克拉,跃居世界超硬材料生产大国之首。
金刚石具有极高的硬度和耐磨性,其显微硬度可达10000hv,是刀具材料中最硬的材料。
同时它的摩擦系数小,与非铁金属无亲和力,切屑易流出,热导率高,切削时不易产生积屑瘤,加工表面质量好,能有效地加工非铁金属材料和非金属材料,如铜、铝等有色金属及其合金、陶瓷、末烧结的硬质合金、各种纤维和颗粒加强的复合材料、塑料、橡胶、石墨、玻璃和各种耐磨的木材(尤其是实心木和胶合板等复合材料)。
刀具材料及发展趋势

刀具材料及发展趋势[摘要] 本文重点阐述了高速钢、硬质合金、陶瓷刀具、超硬刀具材料等的切削性能和应用范围。
并对刀具材料的发展动向也作出了预测与展望。
[关键词] 刀具材料切削加工发展趋势0.引言切削加工是现代制造业应用最广泛的加工技术之一。
据统计,国外切削加工在整个制造加工中所占比例约为80%~85%,而在国内这一比例则高达90%。
刀具是切削加工中不可缺少的重要工具,无论是普通机床,还是先进的数控机床(nc)、加工中心(mc)和柔性制造系统(fmc),都必须依靠刀具才能完成切削加工。
刀具的发展对提高生产率和加工质量具有直接影响。
材料、结构和几何形状是决定刀具切削性能的三要素,其中刀具材料的性能起着关键性作用。
国际生产工程学会(cirp)在一项研究报告中指出:“由于刀具材料的改进,允许的切削速度每隔l0年几乎提高一倍”。
刀具材料已从20世纪初的高速钢、硬质合金发展到现在的高性能陶瓷、超硬材料等,耐热温度已由500~600℃提高到1200℃以上,允许切削速度已超过1000m/min,使切削加工生产率在不到100年时间内提高了100多倍。
因此可以说,刀具材料的发展历程实际上反映了切削加工技术的发展史。
我们应当重视刀具材料的选择和使用,关注新型刀具材料的研制和发展趋势。
1.刀具材料应具备的性能性能优良的刀具材料,是保证刀具高效工作的基本条件。
刀具切削部分在强烈摩擦、高压、高温下工作,应具备如下的基本要求:一是高硬度和高耐磨性;二是足够的强度与韧性;三是高耐热性、导热性和小的膨胀系数;四是良好的工艺性和经济性。
2.刀具材料的种类常用刀具材料有工具钢(包括碳素工具钢、合金工具钢)、高速钢、硬质合金、陶瓷、超硬刀具材料(金刚石、立方氮化硼)以及涂层刀具材料。
碳素工具钢和合金工具钢因其耐热性很差,仅用于手工工具。
陶瓷和超硬刀具材料则由于性质脆、工艺性差及价格昂贵等原因,目前尚在有限的范围内使用。
当今,用得最多的为高速钢和硬质合金,几乎各占一半。
中国刀具行业现状及趋势分析

中国刀具行业现状及趋势分析一、刀具行业产业链分析刀具是机械制造中用于切削加工的工具,又称切削工具。
金属切削刀具材料主要包括硬质合金、高速钢、陶瓷和超硬材料(包括人造金刚石、立方氮化硼等)。
硬质合金刀具是全球市场目前的主流刀具。
与高速钢相比,硬质合金具有较高的硬度、耐磨性和红硬性;与陶瓷和超硬材料相比,硬质合金具有较高的韧性。
因此,硬质合金刀具是全球市场目前采用的主流刀具。
2019年,硬质合金刀具在全球刀具市场中占比63%,国内市场占比53%。
二、刀具行业驱动因素2020年年初受疫情影响导致PMI指数出现大幅度下降,但自2020年第二季度以来,我国PMI保持在50%以上水平,制造业景气度回暖,提高机床开工率。
从工业增加值数据来看,2020年下半年以来,工业增加值同比依然保持较好的增长。
随着产业结构的调整升级,我国机床数控化率稳步增长,机床数控化率从2013年的28.83%稳定上升至2020年的43.27%。
数控机床一方面造就更多高端刀具的消费,另一方面也会推动刀具整体价格的上升。
三、刀具行业发展现状2016-2020年全球刀具市场规模保持稳步增长的状态,2020年全球切削刀具消费金额达370亿美元,同比增长3.06%。
我国切削刀具市场消费情况与我国制造业发展水平和结构调整息息相关。
2016-2018年,随着“十三五”规划落地,制造业的转型升级推动了我国刀具行业快速发展,切削刀具年消费规模快速增至421亿元,达到历史最高水平。
而2019年受中美贸易摩擦加剧、汽车等下游行业下行的影响,我国刀具消费额下降至393亿元。
2020年以来,我国刀具市场增速恢复至10%以上,金额达到446亿元,同比上升13.49%。
四、刀具行业竞争情况目前,国际刀具行业竞争格局大致分为三个梯队。
第一梯队是欧美刀具企业,主导高端定制化刀具市场;第二梯队是日韩刀具企业,非定制化刀具认可度高;而第三梯队才是我国国内刀具企业,在非定制化市场逐步追赶日韩。
CNC机床加工中的刀具材料选择与应用

CNC机床加工中的刀具材料选择与应用近年来,随着数控机床技术的不断发展,CNC机床在各行各业的应用日益广泛。
作为CNC机床中不可或缺的一部分,刀具的材料选择与应用对于工件加工质量、生产效率、刀具寿命等方面都起着至关重要的作用。
本文将围绕CNC机床加工中的刀具材料选择与应用进行探讨。
一、刀具材料的分类在CNC机床加工中,刀具材料主要可分为硬质合金、高速钢、陶瓷刀具、超硬材料等几大类。
1. 硬质合金硬质合金是一种由钨钴合金和硬质金属碳化物制成的刀具材料,具有高硬度、良好的耐磨性和抗冲击性能。
它是目前应用较广泛的刀具材料之一,适用于大多数金属材料的精密加工。
2. 高速钢高速钢是一种含有多种合金元素的刀具材料,具有良好的热硬性和切削性能。
它具有较高的耐磨性和高温强度,适用于高温切削加工,如铸铁、不锈钢等材料。
3. 陶瓷刀具陶瓷刀具是由陶瓷材料制成的刀具,具有高硬度、耐磨性和热稳定性。
它适用于高速切削和干切削加工,如高硬度合金、玻璃纤维增强塑料等难加工材料。
4. 超硬材料超硬材料是一种由金刚石或立方氮化硼制成的刀具材料,具有极高的硬度和热稳定性。
它适用于超硬材料的切削加工,如钛合金、高硬度合金等。
二、刀具材料的选择原则在CNC机床加工中,刀具材料的选择需要考虑以下几个方面的因素:1. 加工材料根据需要加工的材料特性选择刀具材料,例如加工铸铁时可选择高速钢刀具,加工钛合金时可选择超硬材料刀具等。
2. 加工方式根据加工方式选择刀具材料,例如高速切削时可选择陶瓷刀具,干切削时可选择超硬材料刀具等。
3. 切削速度根据切削速度选择刀具材料,例如在高速切削时为了提高刀具寿命和加工效率,可选择高硬度、耐磨性好的刀具材料。
4. 切削力和切削温度根据切削力和切削温度选择刀具材料,例如降低切削力和切削温度可选择具有较好热稳定性的刀具材料。
三、刀具材料的应用案例以下是几种常见刀具材料在CNC机床加工中的应用案例:1. 硬质合金硬质合金刀具主要适用于钢材加工,如机械零件的车削、镗削等,可以提供较高的加工质量和寿命。
机械加工刀具发展现状与对策

机械加工刀具发展现状与对策浙江大学城市学院张润晨摘要:众所周知,机械加工离不开机床。
在目前的科技水平,机床又离不开刀具,刀具虽小,作用巨大。
随着科技的进步和生产的发展,机械产品金额机械制造技术的内涵正在不断地发生变化。
这对刀具的要求也越来越精密。
关键词:刀具;精密;涂层;发展我国的刀具制造业已有较长的历史,并已发展到相当大的规模,不仅有数量较多的专业刀具厂,而且还有大量的机械制造厂工具车间也生产刀具。
我国现在的生产总值和制造业规模,仅次于美国、日本,最近又超过了德国。
但是技术方面我们还差的很远,我们是要向德国学习的,不仅仅是学习他们的技术,最重要的是学习德国人严谨的思维和精神。
由于技术和材料的原因,我国年消耗刀具近20亿美元,其中很多都是浪费了的。
据估计,切削加工约占机械制造工作量的30%~40%,全世界每年约有1亿吨钢料通过刀具切削而成为切屑,全世界每年切削加工耗资约2500 亿美元。
与世界先进水平相比,目前我国的切削加工技术水平还是比较低,所以要努力研究和开发高速切削、硬切削、干切削、精密切削、虚拟切削等先进切削加工技术,还有新刀具的研发,这些对于提高我国机械制造技术水平和机电产品性能、质量及市场竞争力,推动先进制造技术的发展都具有重要意义。
目前我们学习的刀具主要有:车刀、刨刀、孔加工刀具、铣刀、拉刀、螺纹刀具、数控刀具、成形齿轮刀具、齿轮滚刀、加工蜗轮用刀具、插齿刀及梳齿到、剃齿刀、直齿锥齿轮加工刀具、曲线锥齿齿轮加工刀具、非渐开线齿轮刀具。
现在的数控加工主要有数控铣床和数控车床。
数控铣床的刀具种类有立铣刀、球铣刀、环形铣刀、机夹可转位铣刀。
数控车床一般都有自动回转刀架,,而且都采用6到12工位转塔式刀架。
数控车床的刀具一般分为三类,尖形车刀、圆弧车刀和成形车刀。
在世界切削刀具的近代发展中,上世纪70年代在西方广泛应用的硬质合金刀具方面发生了刀具结构与工艺的两次“革命”,一次起源于美国,将焊接刀片变革为机夹可转位刀片;另一次起源于欧洲,诞生了刀具涂层工艺。
PCBNPCD刀具的应用及发展趋势
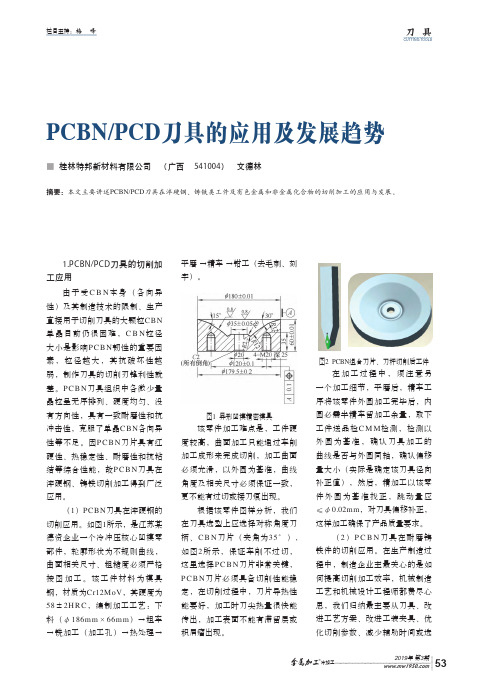
2019年 第3期冷加工53CUTTING TOOLS刀 具PCBN/PCD 刀具的应用及发展趋势■桂林特邦新材料有限公司 (广西 541004) 文德林摘要:本文主要讲述PCBN/PCD 刀具在淬硬钢、铸铁类工件及有色金属和非金属化合物的切削加工的应用与发展。
1.PCBN/PCD 刀具的切削加工应用由于受C B N 本身(各向异性)及其制造技术的限制、生产直接用于切削刀具的大颗粒CBN 单晶目前仍很困难,C B N 粒径大小是影响P C B N 韧性的重要因素,粒径越大,其抗破坏性越弱,制作刀具的切削刃锋利性就差。
P C B N 刀具组织中各微少量晶粒呈无序排列、硬度均匀、没有方向性,具有一致耐磨性和抗冲击性,克服了单晶CBN 各向异性等不足。
因P C B N 刀片具有红硬性、热稳定性、耐磨性和抗粘结等综合性能,故P C B N 刀具在淬硬钢、铸铁切削加工得到广泛应用。
(1)PCBN 刀具在淬硬钢的切削应用。
如图1所示,是江苏某德资企业一个冷冲压核心凹模零部件,轮廓形状为不规则曲线,曲面相关尺寸、粗糙度必须严格按图加工。
该工件材料为模具钢,材质为Cr12MoV ,其硬度为58±2H R C ,编制加工工艺:下料(φ186m m ×66m m )→粗车→铣加工(加工孔)→热处理→平磨 →精车 →钳工(去毛刺、刻字)。
图1 异形凹模精密模具该零件加工难点是,工件硬度较高,曲面加工只能通过车削加工成形来完成切削,加工曲面必须光滑,以外圆为基准,曲线角度及相关尺寸必须保证一致,更不能有过切或接刀痕出现。
根据该零件图样分析,我们在刀具选型上应选择对称角度刀柄、C B N 刀片(夹角为35°),如图2所示,保证车削不过切,这里选择P C B N 刀片非常关键,P C B N 刀片必须具备切削性能稳定,在切削过程中,刀片导热性能要好,加工时刀尖热量很快能传出,加工表面不能有滞留层或积屑瘤出现。
刀具材料在机械加工中的应用研究
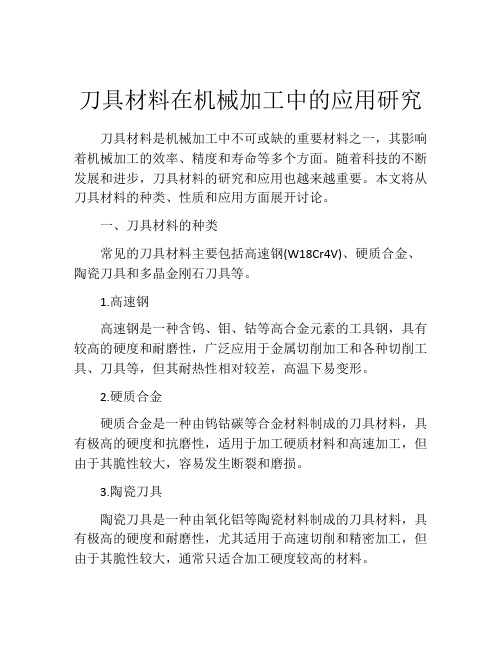
刀具材料在机械加工中的应用研究刀具材料是机械加工中不可或缺的重要材料之一,其影响着机械加工的效率、精度和寿命等多个方面。
随着科技的不断发展和进步,刀具材料的研究和应用也越来越重要。
本文将从刀具材料的种类、性质和应用方面展开讨论。
一、刀具材料的种类常见的刀具材料主要包括高速钢(W18Cr4V)、硬质合金、陶瓷刀具和多晶金刚石刀具等。
1.高速钢高速钢是一种含钨、钼、钴等高合金元素的工具钢,具有较高的硬度和耐磨性,广泛应用于金属切削加工和各种切削工具、刀具等,但其耐热性相对较差,高温下易变形。
2.硬质合金硬质合金是一种由钨钴碳等合金材料制成的刀具材料,具有极高的硬度和抗磨性,适用于加工硬质材料和高速加工,但由于其脆性较大,容易发生断裂和磨损。
3.陶瓷刀具陶瓷刀具是一种由氧化铝等陶瓷材料制成的刀具材料,具有极高的硬度和耐磨性,尤其适用于高速切削和精密加工,但由于其脆性较大,通常只适合加工硬度较高的材料。
4.多晶金刚石刀具多晶金刚石刀具是一种由多晶金刚石合成材料制成的刀具材料,具有极高的硬度和耐磨性,尤其适用于加工铸造铝合金和有色金属等难切削材料,但其价格较昂贵。
二、刀具材料的性质1.硬度刀具材料的硬度是判断其耐磨性和耐腐蚀性的重要指标,一般来说,硬度越高的刀具材料其耐磨性和耐腐蚀性也越强。
例如,硬质合金的硬度可达到1800HV以上,比钢材高出10倍以上。
2.耐磨性刀具材料的耐磨性是指其在长时间使用过程中的磨损程度,硬度高的刀具材料通常具有较强的耐磨性。
但同时,为了保证刀具材料的切削质量和加工效率,还需要考虑切削刃的磨损状态。
3.韧性刀具材料的韧性是指其在加工过程中的抗变形和抗断裂性能,因为刀具材料在加工过程中通常会受到较大的压力和冲击,所以必须具备较好的韧性,否则容易发生变形或者断裂。
4.耐热性刀具材料的耐热性通常是指其在高温下的机械性能和化学性能,如高温下的硬度下降、膨胀系数增大、氧化和腐蚀等。
选择适合的刀具材料,可以在保证加工精度的同时提高加工效率和降低成本。
2024年硬质合金刀具市场前景分析
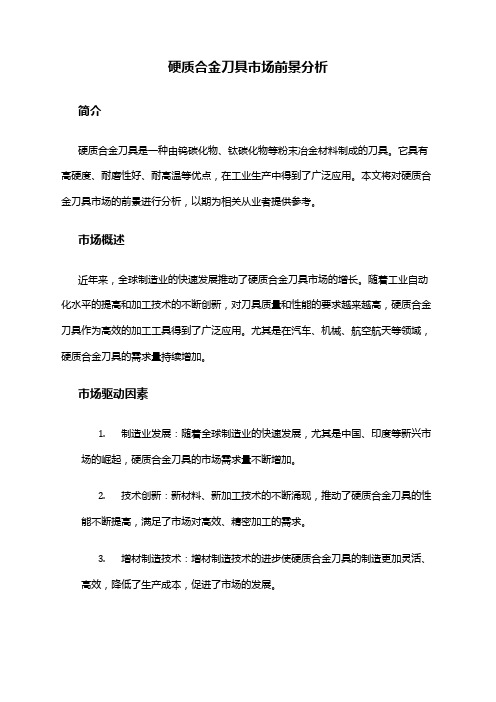
硬质合金刀具市场前景分析简介硬质合金刀具是一种由钨碳化物、钛碳化物等粉末冶金材料制成的刀具。
它具有高硬度、耐磨性好、耐高温等优点,在工业生产中得到了广泛应用。
本文将对硬质合金刀具市场的前景进行分析,以期为相关从业者提供参考。
市场概述近年来,全球制造业的快速发展推动了硬质合金刀具市场的增长。
随着工业自动化水平的提高和加工技术的不断创新,对刀具质量和性能的要求越来越高,硬质合金刀具作为高效的加工工具得到了广泛应用。
尤其是在汽车、机械、航空航天等领域,硬质合金刀具的需求量持续增加。
市场驱动因素1.制造业发展:随着全球制造业的快速发展,尤其是中国、印度等新兴市场的崛起,硬质合金刀具的市场需求量不断增加。
2.技术创新:新材料、新加工技术的不断涌现,推动了硬质合金刀具的性能不断提高,满足了市场对高效、精密加工的需求。
3.增材制造技术:增材制造技术的进步使硬质合金刀具的制造更加灵活、高效,降低了生产成本,促进了市场的发展。
市场挑战因素1.市场竞争激烈:随着市场需求的增加,硬质合金刀具市场竞争日益激烈,价格竞争压力加大。
2.环保限制:环保要求越来越高,对硬质合金刀具生产过程中产生的废水、废气等污染物的排放提出了更高要求,对企业的生产经营造成了一定限制。
市场前景展望未来,硬质合金刀具市场仍然充满机遇和挑战。
机遇: 1. 汽车行业需求增加:随着汽车市场的快速发展,汽车制造业对高精度、高质量加工的要求将进一步提高,硬质合金刀具将有更大的市场机会。
2.电子制造业需求增长:随着5G技术的普及和电子设备市场的快速发展,硬质合金刀具在电子制造业中的应用前景广阔。
3.新材料加工需求增加:新材料的不断涌现,例如复合材料、高温合金等,对加工工具的要求更高,硬质合金刀具有望在这些领域找到应用市场。
挑战:1. 技术创新压力:在市场竞争激烈的环境下,企业需要不断进行技术创新,提升刀具的性能和品质,以保持竞争力。
2.环保要求提高:随着环境保护意识的普及,对硬质合金刀具生产过程中的环境影响予以更高要求,企业需要加大研发投入,探索环保型生产工艺。
机械刀具知识点总结

机械刀具知识点总结一、概述机械刀具是机械加工时常用的切削工具,主要分为车刀、铣刀和钻刀。
它们在加工过程中起到了重要的作用,对加工精度和质量起着直接影响。
因此,了解机械刀具的知识是非常重要的。
二、机械刀具的分类1.车刀车刀是车床上用来切削工件的刀具,根据切削刀片排列的不同可以分为外圆刀具和内孔刀具。
外圆刀具又可分为外圆刀片和切断刀片两类。
内孔刀具分为内孔刀头和内孔刀架两类。
2.铣刀铣刀是铣床上用来切削金属材料的刀具,包括平刀、球头刀、锥形刀、T型槽刀等多种类型。
3.钻刀钻刀是用来钻孔的刀具,包括扁平钻、中心钻、排屑钻、扩孔钻、沉头钻和镗刀。
三、机械刀具的结构和性能1.刀片刀片是机械刀具的主要部件,它的材质和形状决定了刀具的耐磨性和切削性能。
刀片通常由高速钢、硬质合金、陶瓷和超硬材料制成。
2.刀柄刀柄是刀具的安装部件,通常由钢铁、铸铁和合金材料制成。
刀柄的质量直接影响刀具的稳定性和刚性。
3.刀具几何参数刀具的几何参数包括刀片的切削刃角、切削刃宽度、刀尖倒角、前角和刀刃后角等,这些参数决定了刀具的切削性能。
四、机械刀具的选择与使用1.选择刀具的原则刀具的选择应根据工件材料、加工类型、切削条件和加工精度要求进行选择。
一般情况下,应根据刀具的刃长、齿数、齿型、刃角和刀具结构等参数来确定。
2.刀具的安装和使用刀具的安装应保证刀具和机床的匹配性,并严格遵守刀具装夹规范,以保证刀具的刚性和稳定性。
在使用过程中,应及时调整刀具的位置、切削速度和进给速度,以确保切削质量和加工效率。
3.刀具的保养与维护刀具的保养应根据刀具的材质和使用情况,选择合适的保养方法和保养周期。
刀具的维护主要包括刀具的清洗、润滑、修磨和更换等。
五、机械刀具的加工技术1.车刀的刀具路径车刀的刀具路径是指车刀在工件上切削的轨迹,它的选择直接影响切削效果和工件的表面质量。
常用的车刀路径有直线刀路径、弧形刀路径和组合刀路径等。
2.铣刀的刀轴路径铣刀的刀轴路径是指铣刀在工件上切削的轨迹,它的选择与刀具的类型和切削方式有关。
数控刀具的现状与发展趋势
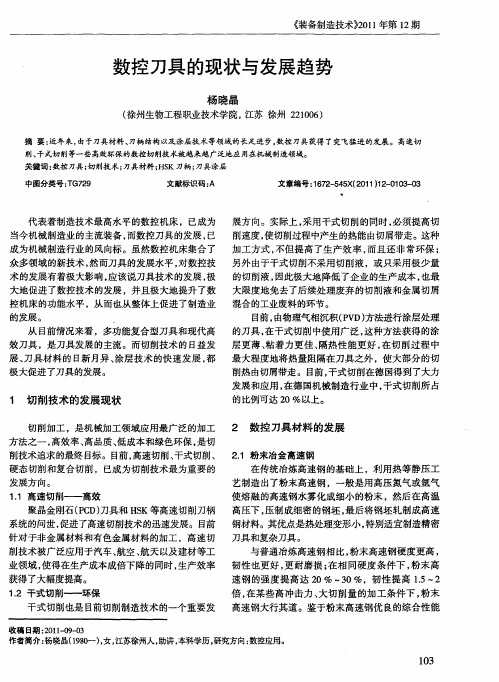
1 切削技术 的发展现状
切削加工 ,是机械加工领域应用最广泛的加工 2 数控 刀具材料 的发展
方法之一 , 高效率 、 品质、 高 低成本 和绿色环保 , 是切 削技术追求的最终 目 。目前 , 标 高速切削、 干式切削、 21粉末冶金高速钢 .
硬态切削和复合切削 ,已成为切削技术最为重要 的 在传统冶炼高速钢的基础上 ,利用热等静压工 发展方向。 艺制造出了粉末高速钢 ,一般是用高压氮气或氩气 11高速切削——高效 . 使熔融的高速钢水雾化成细小的粉末 ,然后 在高温 聚晶金刚石( C 刀具和 H K等高速切削刀柄 高压下 , P D) S 压制成细密 的钢坯 , 最后将钢坯轧制成高速 系统的问世 , 促进 了高速切削技术 的迅速发展。目前 钢材料。其优点是热处理变形小 , 特别适宜制造精密 针对于非金属材料和有色金属材料 的加工 ,高速切 刀具 和复杂刀具 。 削技术被广泛应用于汽车、 航空 、 航天 以及 建材等工 与普通冶炼高速钢相 比 , 粉末高速钢硬度更 高 , 业领域 , 使得在生产成本成倍下降 的同时 , 生产效率 韧性也更好 , 耐磨损 ; 更 在相 同硬度条件下 , 粉末高
削、 干式切 削等一些高效环保 的数控切 削技 术被越 来越 广泛地应 用在机械制造领域 。
关键 词 : 数控刀具 ; 削技术 ; 切 刀具材料 ; K刀柄 ; HS 刀具涂层
中图分类号 :G7 9 T 2
文献标识码 : A
文章编号 :6 2 5 5 2 1 )2 0 0 — 3 1 7 - 4 X( 0 1 - 1 3 0 1
《 装备制造技术) O 1 ) l 年第 1 期 2 2
数控 刀具 的现 状与发展趋 势
杨 晓晶
( 徐州生物工程职业技术学院, 江苏 徐州 2 10 ) 20 6
切削刀具的发展现状与趋势及对策
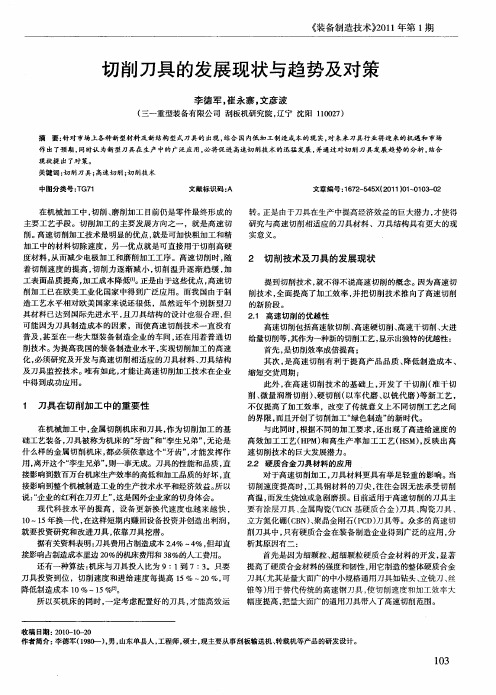
现代科 技水平 的提高 ,设 备更新换 代速度也越 来越 快 , 1 0~1 5年换 一代 , 在这样短期 内赚 回设备投资并创造 出利润 ,
就要投资研究和改进刀具 , 依靠刀具挖潜。 据有关资料表 明: 刀具费用占制造成本 2 % ~ % , . 4 4 但却直 接 影 响 占制造 成本 里 边 2 % 的机床 费 用 和 3 % ̄A3 费用 。 0 8 2 还有一种算法 : 机床与刀具投入 比为 9: 到 7: 。只要 1 3
削技术 。 为提高我 国的装备制造业水平 , 实现切削加工 的高速 化, 必须研究及开发与高速切削相适应 的刀具材料 、 刀具结 构
及 刀具监控技术 。 唯有如此 , 才能让高速切削加工技术 在企业
中得 到 成 功 应 用 。
1 刀具在 切 削加 工 中的重 要性
在机械加工 中, 金属切削机床和刀具 , 为切削加工 的基 作
刀具投资到位 ,切 削速度 和进 给速 度每提高 1 2 5% O%, 可
降低制造成本 1 ~1 0% 5%田 。
础工艺装备 , 刀具被称为机床 的“ 牙齿 ” 孪生兄 弟” 无论是 和“ , 什么样的金属切削机床 , 都必须依 靠这个“ 牙齿 ” 才能发挥作 ,
用, 离开这个“ 孪生兄弟 ”则一事无成 。刀具的性能和品质 , , 直
高效加工 工艺 ( P 和高生产率 加工工 艺 ( s , H M) H M) 反映 出高 速切削技术 的巨大发展潜力 。
高速切削包括高速软切削、 高速硬 切削 、 高速干切削、 大进 给量切削等 , 其作为一种新的切削工艺 , 显示出独特的优越性: 首先 , 是切削效率成倍提高 ; 其次 , 高速切削有利 于提高产 品 品质 、 是 降低 制造成本 、 缩短交货周期 ; 此外 , 高速 切削技术 的基础上 , 发了干切 削( 在 开 准干切 削、 微量 润滑切削 )硬切削 ( 、 以车代磨 、 以铣代磨 ) 等新工艺 , 不仅提高 了加工效率 ,改变 了传统意 义上 不同切削工艺之间 的界限 , 而且开创 了切削加工“ 绿色制造” 的新 时代 。 与此同时 , 根据不 同的加 工要求 , 出现了高进给速度的 还
中国刀具与切削加工技术的发展现状与趋势
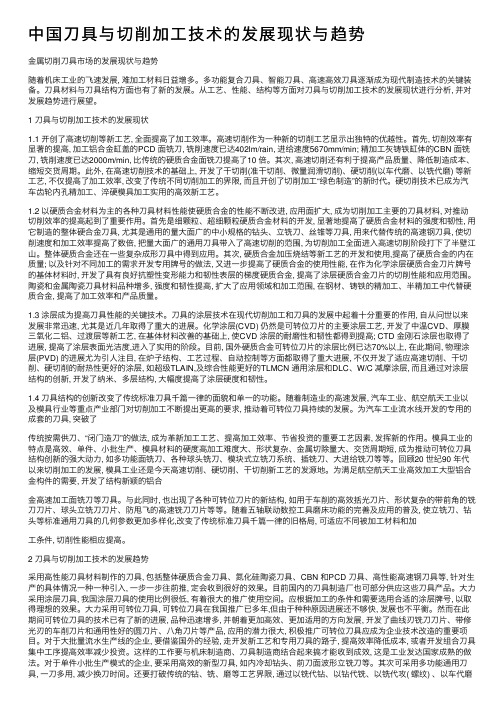
中国⼑具与切削加⼯技术的发展现状与趋势⾦属切削⼑具市场的发展现状与趋势随着机床⼯业的飞速发展, 难加⼯材料⽇益增多。
多功能复合⼑具、智能⼑具、⾼速⾼效⼑具逐渐成为现代制造技术的关键装备。
⼑具材料与⼑具结构⽅⾯也有了新的发展。
从⼯艺、性能、结构等⽅⾯对⼑具与切削加⼯技术的发展现状进⾏分析, 并对发展趋势进⾏展望。
1 ⼑具与切削加⼯技术的发展现状1.1 开创了⾼速切削等新⼯艺, 全⾯提⾼了加⼯效率。
⾼速切削作为⼀种新的切削⼯艺显⽰出独特的优越性。
⾸先, 切削效率有显著的提⾼, 加⼯铝合⾦缸盖的PCD ⾯铣⼑, 铣削速度已达402lm/rain, 进给速度5670mm/min; 精加⼯灰铸铁缸体的CBN ⾯铣⼑, 铣削速度已达2000m/min, ⽐传统的硬质合⾦⾯铣⼑提⾼了10 倍。
其次, ⾼速切削还有利于提⾼产品质量、降低制造成本、缩短交货周期。
此外, 在⾼速切削技术的基础上, 开发了⼲切削(准⼲切削、微量润滑切削)、硬切削(以车代磨、以铣代磨) 等新⼯艺, 不仅提⾼了加⼯效率, 改变了传统不同切削加⼯的界限, ⽽且开创了切削加⼯“绿⾊制造”的新时代。
硬切削技术已成为汽车齿轮内孔精加⼯、淬硬模具加⼯实⽤的⾼效新⼯艺。
1.2 以硬质合⾦材料为主的各种⼑具材料性能使硬质合⾦的性能不断改进, 应⽤⾯扩⼤, 成为切削加⼯主要的⼑具材料, 对推动切削效率的提⾼起到了重要作⽤。
⾸先是细颗粒、超细颗粒硬质合⾦材料的开发, 显著地提⾼了硬质合⾦材料的强度和韧性, ⽤它制造的整体硬合⾦⼑具, 尤其是通⽤的量⼤⾯⼴的中⼩规格的钻头、⽴铣⼑、丝锥等⼑具, ⽤来代替传统的⾼速钢⼑具, 使切削速度和加⼯效率提⾼了数倍, 把量⼤⾯⼴的通⽤⼑具带⼊了⾼速切削的范围, 为切削加⼯全⾯进⼊⾼速切削阶段打下了半壁江⼭。
整体硬质合⾦还在⼀些复杂成形⼑具中得到应⽤。
其次, 硬质合⾦加压烧结等新⼯艺的开发和使⽤,提⾼了硬质合⾦的内在质量; 以及针对不同加⼯的需求开发专⽤牌号的做法, ⼜进⼀步提⾼了硬质合⾦的使⽤性能, 在作为化学涂层硬质合⾦⼑⽚牌号的基体材料时, 开发了具有良好抗塑性变形能⼒和韧性表层的梯度硬质合⾦, 提⾼了涂层硬质合⾦⼑⽚的切削性能和应⽤范围。
先进刀具使用现状及发展方向

先进刀具使用现状及发展方向(总13页)--本页仅作为文档封面,使用时请直接删除即可----内页可以根据需求调整合适字体及大小--先进刀具使用现状和未来发展方向先进刀具的使用与先进制造技术水平有着密切的联系。
从20 世纪80年代在世界制造业发展及制造技术进步的带动下,切削技术和刀具逐渐进入了高速、高效、创新工艺的发展新阶段,切削加工效率成倍提高,为制造业发展作出了重要贡献。
至今,应用创新的切削工艺和先进刀具,提高加工效率和加工质量,降低制造成本,从而提高企业的竞争实力,已成为工业发达国家机械加工企业的共识,也引起我国机械加工企业的关注。
因此,注重应用先进刀具,提高切削刀具的应用水平,不断进行技术革新,在机械金属切削行业具有重要的现实意义。
必要性分析目前,杭州发电设备厂已成为中国建设中小型发电机组重要企业。
然而,我厂的切削加工水平与世界先进切削技术相比,仍有较大差距。
造成切削技术落后的原因,除了技术上的差距以外,还有长期以来形成的忽视切削技术和刀具的落后观念。
这种低性价比的刀具应用法实质上是牺牲了加工效率、提高了工人劳动强度,但从年度统计上又未能降低零件制造成本。
据切削加工的经济分析指出:由于刀具成本在零件成本中所占的比例仅为3%~5%,如果把刀的购买价格降低30%,企业也只能节省1%的零件制造成本,但用量相比大幅增加,总刀具前,在精加工汽发细长轴类零件时,因轴本身直径较大、且长度长,用普通刀具车削往往不能一次走刀完成,要调换多次刀,尺寸精度差,加工质量难以保证;在购进性能优异的夹固式刀具后,切削性能大大改善,从而提高生产效率、降低成本[1]。
因此,在企业快速发展的新形势下,要生产出数量多、规格多的产品,切削加工中合理应用刀具也是提高生产效率、保质保量生产的重要环节。
采用新的刀具材料,尽可能有针对性地采用新的刀具材料牌号,以更好地适应工件材料和切削条件。
被加工材料覆盖着很广的范围,包括钢铁材料、有色金属、耐热合金及合成材料等。
机加工中刀具材料的应用及发展趋势

和合理使用 , 关注新型刀具材料的研制和发展趋势 。 l刀具 材料 应具 备的 性能 性能优 良的刀具材料 , 是保证刀具高效工作的 基本条件。刀具切削部分在强烈摩擦 、 高压 、 高温下 工 作 , 具备 如下 的基本 要 求 : 应 一是 高 硬度 和高 耐磨
性; 二是 足够 的强 度 与 冲 击 韧性 ; 是 高 耐 热 性 、 三 导
Ap lc to n v l pi g Te d nc fCu tn p ia i n a d De eo n n e y o ti g To l SM a e ili u s fM a h ni g o ’ t ra n Co r eo c i n
Ga i o Hu
本的加工方法 , 在其过程中, 刀具直接完成切削余量
和形 成 已加工表 面 的任 务 , 刀 具 材 料 又是 决 定 刀 而 具 切削性 能 的根本 因素 , 对 加 工 效 率 、 工 质量 、 它 加 加 工成本 以及 刀具 耐用 度 的影响极 大 。就拿 切 削速 度来 说 , 在最初 使用 碳素 工具 钢作 为 刀具材料 时 , 切 削速度 只有每分 钟 1 左 右 ;9世 纪 末 2 纪 初 0米 1 0世 出现 了高 速钢刀 具 材 料 , 削 速 度 提 高 到每 分 钟 几 切 十米 ;0年 代 出 现 了硬 质 合 金 , 削 速 度 提 高 到 每 3 切 分 钟 10 0 0 -5 0米 ;0世 纪 中 叶 以 后 又 出 现 了复 合 2 陶瓷 、 刚石 、B 金 C N超 硬刀 具 材料 等 , 速 钢 和硬 质 高
c iig I as n lsst ef n t n wh c h aeil fc tig t l h udb t n h r sn i ain h nn .t l a aye h u ci ih t em tra o u t o o l ewih a d t ep ee t t t o o n s su o o e eo me ta d a pia inwihal id f u tn lSmae i 1Atls , rn su h e eo igtn fd v lp n n p l t t lk n so tigt ’ tr a . at i b ig p t ed v lpn e — c o c o c t d n yo u tn o lSmae i l n t ef tr . e c fc tig t ’ trc h u u e ai Ke rs ma hnn ;t em aeia f u t g t l ywo d : c iig h trc l ti o ;mae ia’ u cin d v lpn e d n y o c n tr lSf n t ; e eo ig tn e c c o
刀具材料的应用和发展

业 ,有着 5 0多年使 用 刀具材 料 的历史 。 自 16 年 起 , 98
根据 原冶金部 、原一机部 ( 机械部 )联 合通知 ,上海 工
刀具在 50 70 / i以上条件下高速切削 。 0 ~ 0m mn
刀具材料 的发展对人类进步 有着重要 的影 响,在过 去的 2 世纪 里 ,由于材料性 能 的不 断改 进 ,使 刀具 的 0 切削效率提高 了 10倍左右。 5
更正 :第 7 期易孚迪感应设备 ( 上海 )有限公 司封 面广告说明 文字中 ,“ 滚球丝杠 应为 。 滚珠丝杠 特此 更正 。 ,
囝 趔堕 旦 堡 复
缸板 热工 l 加
维普资讯
删
…
t
圈
上时,硬度仍 可保 持 6 H C以上。按照 主要 合金 元素 2R 配 比可以分为通用高速钢 、 低合金 高速钢和 高性 能高速
粉。人造金 刚石 P D的研究始 于 14 年 ,15 C 90 94年美 国
正式宣告人造金刚石研制成功 。这些材 料发 展很 快 ,以 后又相继研制 、生产 了聚 晶人造金 刚石 和聚 晶立方 氮化
硼PB C N刀片 。我 国在 2 世 纪 6 0 0年代 ,研制成 功单晶
C N、P B B C N和 P D 目前我 国人造 金刚石 年产量 已居 C。
展数控 、超硬等高效 、精密切削 刀具 ,以满足客户 的加
二、用于刀具材料的工具钢
1 碳素工具钢和合金工具钢 .
在工具钢材料中 ,碳 素工具钢性 能相 对较差 ,一 般 在 10 以下使 用 , W 5% =0 6 % 一13 %,含 碳 量 越 .5 .5
工要求 , 从而在 刀具材料 的使 用和 热处理 工艺 等方 面 ,
2022年行业报告我国刀具行业市场发展情况及趋势分析

我国刀具行业市场发展情况及趋势分析要实现国内刀具企业的又好又快进展,需打破现有的研发思路,从客户的角度动身,与客户一起成长,从实际需求中开发出自己的产品,而不是仅仅替代国外的刀具。
我们不仅需要有制造刀具的力量,还需要有将刀具应用到实际生产过程中的力量,这样才能真正有扎实的理论和实践基础,才能拥有自己的学问产权。
刀具制作过程中需要模具进行成型工艺,对我国的模具产业大有裨益。
我国五金刀具的高速进展,与强大的市场需求密不行分。
2022年我国国产刀具的生产总量达到了350亿元,出口刀具85亿元,同比增长21.4.按此增速计算,估计2022年刀具消费规模将达到485亿以上。
在消费的刺激下,我国的刀具生产规模正在不断扩大。
在刀具市场的推动下,我国的刀具模具的市场需求必定会得到提升,将会促进国内刀具模具产业更好进展。
刀具行业涵括了基体材质设计、涂层组织结构设计、刀具外观结构设计、专用数字化技术开发等学问领域,任一学科理论、技术的更新换代都会随之带动整个刀具行业技术系统性变化调整。
同样在生产线上,与以上技术关联的任一环节程序的微小缺失或浮动势必影响刀具产品性能指标的稳定性。
就刀具基体材料而言,成分在国内各家公司对应的牌号基本相同,硬度、密度、矫顽磁力等常规性能报告也基本全都,然而实际使用性能的反馈良莠不齐。
要打破这种“形似神不似”的尴尬,亟待对刀具研发进行系统性夯实积累,对各环节相关性探究连接,层层相符、环环相扣,从而指导实际生产,确保产品的稳定性,找到“神形兼备”的关键。
配套服务力量缺失国产刀具无法尽施其“神”高速、高效切削在航空零部件加工中,高速切削正在被大量应用,主要有以下几个缘由:(2)飞机零件的结构简单、精度高,零件的薄壁、细筋结构刚度差,要尽量削减加工中的径向切削力和热变形,只有采纳高速切削加工才能满意这些要求。
(3)难加工材料,如镍基高温合金、钛合金、高强度结构钢被现代航空产品大量采纳,这些材料强度大、硬度高,耐冲击、加工中简单硬化,切削温度高、刀具磨损严峻,属于难加工材料。
机械制造工具

机械制造工具在现代机械制造行业中,机械制造工具是不可或缺的一部分。
机械制造工具的开发和使用对于提高生产效率、提升产品质量具有重要作用。
本文将探讨机械制造工具的分类、应用以及未来发展趋势。
一、机械制造工具的分类机械制造工具按照其功能和用途的不同,可以分为以下几类:1. 切削工具:包括刀具、钻头、锯片等,用于将材料进行切削加工;2. 量具:用于测量和检验零件尺寸和形状的工具,如千分尺、游标卡尺等;3. 夹具与模具:用于固定工件、定位工件或者实现工件的成形等,如夹具、模具等;4. 磨削工具:包括砂轮、磨料带等,用于对工件进行研磨和抛光加工;5. 组合工具:由多个独立的工具组合而成,如刀柄、刀片组合成的可更换刀具等。
二、机械制造工具的应用机械制造工具在各个行业和领域都有广泛的应用。
以下几个方面是机械制造工具应用的典型案例:1. 刀具在车床、铣床等加工设备上的使用,可用于对金属材料进行切削,实现复杂零件的加工;2. 夹具与模具在注塑、冲压等成型设备中的应用,可以使产品成形更加精确,并提高生产效率;3. 量具的使用对于保证产品质量至关重要,通过精确测量和检验,可以避免产品质量缺陷;4. 磨削工具在表面处理、精密加工等环节中的应用,能够提供更高的表面光洁度和尺寸精度。
三、机械制造工具的发展趋势随着科技的进步和制造业的发展,机械制造工具也在不断创新和提升。
以下几个方面是机械制造工具的发展趋势:1. 材料和涂层技术的进步:新材料和涂层的应用可以提高工具的硬度、耐磨性和寿命,提高工具的加工能力和稳定性;2. 数控技术的应用:数控技术的普及与应用,使得机械制造工具的加工精度、效率和自动化水平得到了大幅提升;3. 人工智能技术的融合:机械制造工具的发展趋势是向智能化、自动化方向发展,通过机器学习和人工智能技术,实现工具的智能监测和优化;4. 环保和节能:机械制造工具的研发和使用也越来越注重环保和节能,开发更加环保的切削液和涂层,减少资源的浪费和能源的消耗。
- 1、下载文档前请自行甄别文档内容的完整性,平台不提供额外的编辑、内容补充、找答案等附加服务。
- 2、"仅部分预览"的文档,不可在线预览部分如存在完整性等问题,可反馈申请退款(可完整预览的文档不适用该条件!)。
- 3、如文档侵犯您的权益,请联系客服反馈,我们会尽快为您处理(人工客服工作时间:9:00-18:30)。
机加工中刀具材料的应用及发展趋势金属切削加工是现代机械制造工业中一种最基本的加工方法,在其过程中,刀具直接完成切削余量和形成已加工表面的任务,而刀具材料又是决定刀具切削性能的根本因素,它对加工效率、加工质量、加工成本以及刀具耐用度的影响极大。
就拿切削速度来说,在最初使用碳素工具钢作为刀具材料时,切削速度只有每分钟10米左右;19世纪末20世纪初出现了高速钢刀具材料,切削速度提高到每分钟几十米;30年代出现了硬质合金,切削速度提高到每分钟100~500米;20世纪中叶以后又出现了复合陶瓷、金刚石、CBN超硬刀具材料等,高速钢和硬质合金则发展了许多新品种。
迄今,已使切削速度提高到每分钟一千米以上。
历史事实表明,在切削加工的发展过程中,刀具材料始终是最积极的因素。
同时,被加工材料的发展也大大地推动了刀具材料的发展。
因此,我们应当重视刀具材料的正确选择和合理使用,关注新型刀具材料的研制和发展趋势。
1刀具材料应具备的性能性能优良的刀具材料,是保证刀具高效工作的基本条件。
刀具切削部分在强烈摩擦、高压、高温下工作,应具备如下的基本要求:一是高硬度和高耐磨性;二是足够的强度与冲击韧性;三是高耐热性、导热性和小的膨胀系数;四是良好的工艺性和经济性。
2常用刀具材料常用刀具材料有工具钢(包括碳素工具钢、合金工具钢、高速钢)、硬质合金、超硬刀具材料和陶瓷。
碳素工具钢和合金工具钢因其耐热性很差,仅用于手工工具。
陶瓷和超硬刀具材料则由于性质脆、工艺性差及价格昂贵等原因,目前尚在有限的范围内使用。
当今,用得最多的为高速钢和硬质合金, 几乎各占一半。
2.1高速钢高速钢是一种加入了较多的钨、铬、钒、钼等合金元素的高合金工具钢,有良好的综合性能。
其强度和韧性是现有刀具材料中最高的。
高速钢的制造工艺简单,容易刃磨成锋利的切削刃,锻造、热处理变形小,目前在复杂的刀具,如麻花钻、丝锥、拉刀、齿轮刀具和成形刀具制造中,仍占有主要地位。
2.2硬质合金硬质合金是高强度难溶的金属化合物(主要是WC、TiC等,又称高温碳化物)微米级的粉末,用钴或镍等金属作粘结剂烧结而成的粉末冶金制品。
其中高温碳化物的含量超过高速钢,绝大多数车刀、端铣刀和部分立铣刀、钻孔绞刀等均已采用其制造,切削速度可达到100~200m/min以上,是最主要的刀具材料之一。
但因其工艺性较差,用于复杂刀具尚受到很大限制。
3新型刀具材料3.1涂层刀具涂层刀具材料是近20年出现的一种新型刀具材料。
它是在一些韧性较好的硬质合金或高速钢刀具基体上,涂覆一层耐磨性高的难熔化金属化合物而获得的,是刀具材料发展中的一项重要突破。
涂层技术可提高刀具的耐磨性而不降低其韧性,较好的解决了刀具材料存在的强度和韧性之间的矛盾,是切削刀具发展的一次革命。
从上世纪70年代初首次在硬质合金基体上涂覆一层碳化钛(TiC)后,到1981年就把普通硬质合金刀具的切削速度从80m /min提高到300m/min。
在高速钢基体上刀具涂层多为TiN,常用物理气相沉积法(PVD法)涂覆,相当于一般硬质合金的硬度,耐用度可提高2~5倍,切削速度可提高20%~40%;在韧性较好的硬质合金基体上,涂层多为高耐磨、难熔化的金属化合物,一般采用化学气相沉积法(CVD法)涂覆,表面硬度可达2500~4200HV。
目前,各工业发达国家对涂层刀具的研究和推广使用发展非常迅速。
处于领先地位的瑞典,在车削上使用涂层硬质合金刀片已占到70%~80%,在铣削方面已达到50%以上。
但是涂层刀具不适宜加工高温合金、钛合金及非金属材料,也不适宜粗加工有夹砂、硬皮的锻铸件。
3.2稀土硬质合金稀土硬质合金是硬质合金材料的一个新品种。
它是在各种硬质合金刀具材料中,添加了少量的稀土元素。
稀土元素是指化学元素周期表中原子序数为57~71(从La到Lu),再加上21和39(Sc和Y)的元素,共17个元素。
将某些稀土元素,以一定方式,微量添加到传统的硬质合金牌号中,即可有效地提高它们的机械性能与切削性能。
添加稀土元素后硬质合金的组织比较致密;室温和高温硬度都有所改善;断裂韧性和抗弯强度显著提高,分别提高20%和10%以上;其耐磨性和使用寿命也均有不同程度的提高。
稀土硬质合金刀片在切削时表层有富钴现象,故能降低切屑、工件与刀具间的摩擦系数,从而可以降低切削力。
因此,它在机械加工中发挥着重要作用。
我国对稀土硬质合金的研究开发,领先于其他国家。
3.3超硬刀具材料超硬刀具材料是指天然金刚石及硬度、性能与之相近的人造金刚石和CBN(立方氮化硼)。
由于天然金刚石价格比较昂贵,所以生产上大多采用人造聚晶金刚石(PCD)、聚晶立方氮化硼(PCBN),以及它们的复合材料。
上世纪中叶,美国利用人造金刚石微粉和人造CBN微粉在高温、高压、触媒和结合剂的作用下烧结成尺寸较大的聚晶块作为刀具材料。
之后,南非戴比尔(D eBeers)公司、前苏联和日本也相继研制成功。
后来又推出了金刚石或CBN和硬质合金的复合片。
目前,又出现了人工合成大单晶金刚石,以及用CVD(化学气相沉积)法制出的金刚石薄膜涂层和金刚石厚膜等功能性材料,大大拓宽了超硬刀具材料的应用领域。
我国超硬刀具材料的研究与应用开始于上世纪70年代,现跃居世界上超硬材料生产大国之首。
金刚石的优点是具有极高的硬度和耐磨性,是刀具材料中最硬的材料。
同时它的摩擦系数小,与非铁金属无亲和力,切屑易流出,热导率高,切削时不易产生积屑瘤,加工表面质量好,能有效地加工非铁金属材料和非金属材料。
其缺点是韧性差,热稳定性低。
三种主要金刚石刀具材料—PCD、CVD厚膜和人工合成单晶金刚石各自的性能特点为:PCD焊接性、机械磨削性和断裂韧性最高,抗磨损性和刃口质量居中,抗腐蚀性最差;CVD厚膜抗腐蚀性最好,机械磨削性、刃口质量、断裂韧性和抗磨损性居中,可焊接性差;人工合成单晶金刚石刃口质量、抗磨损性和抗腐蚀性最好,焊接性、机械磨削性和断裂韧性最差。
各种不同形式的金刚石切削刀具能很好地相互补充,当然也存在一些相互交叉的应用领域,在这些领域需对刀具产品进行合理选择。
而立方氮化硼(CBN)是纯人工合成的材料,它的硬度仅次于金刚石,并且热稳定性高,较适合于高速切削黑色金属。
因此,超硬材料刀具不仅是加工高硬度材料的理想刀具,而且适用于高速精密和自动化加工,尤其是用超硬材料刀具进行以车代磨、以铣代磨,更具有高效、低耗、适应性强、缩短制造周期等优点,目前已在要求精度高、批量大的汽车零部件加工中得到广泛应用。
3.4新型陶瓷新型陶瓷刀具的出现,是人类首次通过运用陶瓷材料改革机械切削加工的一场技术革命的成果。
很早,德国与英国已经开始寻求采用陶瓷刀具取代传统的碳素工具钢刀具。
陶瓷材料因其高硬度与耐高温特性已成为新一代的刀具材料,但陶瓷也由于其人所共知的脆性受到局限。
工程技术界努力研制与推广陶瓷刀具的主要原因,一是可以大大提高生产效率;二是由于构成高速钢与硬质合金的主要成分钨资源在全球范围内的枯竭。
钨资源的稀缺与价格的攀升,在一定程度也上促进了陶瓷刀具的研制与推广,并取得了令人瞩目的成果。
就世界范围讲,德国陶瓷刀具已不仅用于普通机床,且已将其作为一种高效、稳定可靠的刀具用于数控机床加工及自动化生产线;日本陶瓷刀片在产品种类、产量及质量上均具国际先进水平;美国在氧化物-碳化物-氮化物陶瓷刀具研制开发方面一直占世界领先地位;中国陶瓷刀具开发应用也取得许多重大成果。
纯氧化铝陶瓷,其优点是在室温与高温时,硬度都高于硬质合金材料,且此时的抗压强度也都很好;缺点是在切削铁合金及钢件时,较易产生粘结磨损及缺口磨损。
它最适于高速切削硬而脆的金属材料,或用于大件机械零部件切削及用于高精度零件的切削加工;氧化铝-金属系陶瓷的材料密度、抗弯强度及硬度均有提高,但其抗蠕变强度低,抗氧性差;氧化铝-碳化物金属陶瓷,最适用于加工淬硬钢、合金钢、锰钢、冷硬铸铁、铸钢,镍基或镍铬合金等, 还可用于非金属材料如纤维玻璃、塑料夹层及陶瓷材料的切削加工,亦可采用切削液进行湿式切削;氧化铝-氮化物金属陶瓷具有更好的抗热震性能且更适用于间断切削,但其抗弯强度与硬度都比添加TiC的金属陶瓷低一些,对它的研究与深度开发仍在继续中;氮化硼陶瓷刀具在对硬度甚高的铸铁进行切削加工时,刀具的头端不会发生常见的受热龟裂与缺屑;利用纳米材料制作的新型金属陶瓷刀具材料有利于提高材料的强度、硬度和断裂韧性,这对开发和研制新型刀具材料具有重要的意义;复合金属陶瓷刀具材料具有更好的耐磨性、耐热性和优良的切削性能,适合于淬硬钢、合金耐磨铸铁、高强度钢等一系列超硬难加工材料的加工,也可以用来制作模具、喷嘴等耐磨、耐腐蚀的机械零部件。
4刀具材料的发展趋势纵观刀具材料发展的历史,结合我国的实际情况,新型刀具材料的发展趋势是:因我国稀土元素资源蕴藏丰富,价格也不贵,稀土硬质合金刀具材料极有应用前景;超硬刀具材料是一种先进的刀具材料,在生产中也有着广阔的发展空间;在超精密镜面切削的高技术应用领域,天然金刚石起到了重要作用。
人工合成大尺寸金刚石的成功为开辟新的应用领域(如木材加工业)提供了可能。
CVD金刚石薄膜和厚膜具有很高的机械强度和良好的热学性能,尽管至今生产还未形成规模,但因其性能优异,且已迅速发展,表明其将在刀具工业中发挥积极作用。
PCD则向大直径、细粒度、高抗冲击、高热稳定性方向发展。
随着更耐磨、更难加工的工件材料日益增多,各类金刚石刀具的应用也将持续增加。
可以预料,今后随着各种新型难切削材料应用的增多,必将促进超硬刀具材料进一步的发展与应用。
另外,陶瓷刀具材料的强度低、韧性差,曾一度制约了它的应用推广,但随着特种陶瓷材料研变与开发工作的不断深入,超微粉技术的发展和纳米复合材料的研究为其发展增添了新的活力,随着陶瓷技术的发展,陶瓷刀具材料的力学。