零 件 尺寸 检 测 记 录 表
2-VDA6.3检查表P1-P7

过程规范
-设备、工具、检测检验设备适用性
-加工和检验设施的布局
-搬运、包装、仓储和标识
审核发现
评分
VDA6.3过程审核-2016版P部分
P2-P7 *
P1
运输&零 部件处置
过程要素
最低要求
示例 产品/过程开发
⁻顾客规范和标准
-安排,时间框架
对于可行性的程序,必须在跨部门范围 -法规,标准,法律,环境影响
内加以规范。
-产品责任要求
所有明确的产品和过程特殊要求(技术 -建筑,空间
、功能、质量、物流、软件…)必须针对 -CAM,CAQ
可行性分析进行检查。
-产品和过程创新
根据产品和过程 在可行性研究中,必须考虑物质和人力 -跨部门制造可行性分析(例如、销
3.2
*x
要求,是否对可 资源。
售、开发、采购、生产策划、生产
是否建立了事态 升级过程,并得 到有效的执行?
最低要求
通过这些活动,确保生产中仅使用经过 批准和具备质量能力的供方。 活动的水平取决于采购范围内供应品的 风险等级。 其中包括供方选择、发包标准、发包数 量以及发包目标日期。 确保顾客要求在供应链的传递。 这些活动还包括按协议由顾客要求的供 方(指定供方)。 也包括提供设备、机械、工具、检测和 测量系统以及服务的供方。 必须通过适当的文件记录,确保对供方 发包的追溯。 计划应包括:发包的日期、供方里程碑 和批准,与整体日程计划相协调,并监 控进度。 项目中的变更管理满足顾客特定要求。 针对变更(供方、内部或顾客发起的变 更)应进行评价,需要时,调整项目计 划。该评价必须含有对产品质量的风险 评估和截止期限。 应确保供方(关键供方)能够主动参与 到变更管理中。 应及时报告变更,并和顾客达成一致。 确保遵守规定的设计冻结步骤(设计定 型)。针对特殊情况,顾客和供方应协 商并记录。 所有变更必须记录,应规定顾客、内部 、供方的对口负责人员。 项目中的事态升级程序满足特定的顾客 要求。 项目中的偏差,一旦影响到总体的进 度,那么,就必须有一套事态升级模型 (风险管理)可供使用。应识别和评估 项目风险,并采取措施降低风险。 规定事态升级的标准,确定职责和权 限,在发生偏差的情况下,采取措施。 如果发现工艺技术、供方以及供方所在 国存在风险,那么,就应该在事态升级 管理中考虑这类情况。
公差表查询表
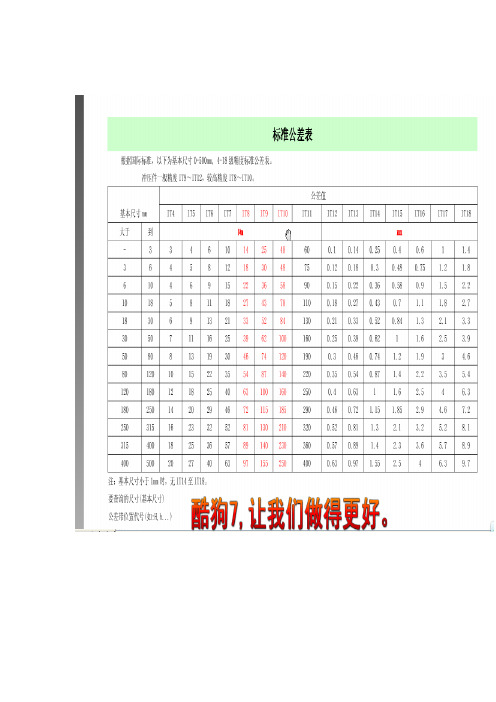
基本含义确定尺寸精确程度的等级称为公差等级,国标规定分为20个等级,从IT01、IT00、IT1、IT2~IT18, 数字越小,公差等级(加工精度)越高,尺寸允许的变动范围(公差数值)越小,加工难度越大。
具体可查询机械设计手册,不同的基本尺寸使用同一公差等级时,公差范围也不同。
公差等级的选择及应用公差等级的选择及应用公差等级应用范围及举例IT01 用于特别精密的尺寸传递基准,例如特别精密的标准量块IT0 用于特别精密的尺寸传递基准及宇航中特别重要的精密配合尺寸。
例如,特别精密的标准量块,个别特别重要的精密机械零件尺寸,校对检验IT6级轴用量规的校对量规IT1 用于精密的尺寸传递基准、高精密测量工具特别重要的极个别精密配合尺寸。
例如,高精密标准量规,校对检验IT7至IT9级轴用量规的校对量规,个别特别重要的精密机械零件尺寸IT2 用于高精密的测量工具,特别重要的精密配合尺寸。
例如检验IT6至IT7级工件用量规的尺寸制造公差,校对检验IT8至IT11级轴用量规的校对塞规,个别特别重要的精密机械零件尺寸IT3 用于精密测量工具,小尺寸零件的高精度的精密配合以及和C级滚动轴承配合的轴径与外壳孔径。
例如,检验IT8至IT11级工件用量规和校对检验IT9至IT13级轴用量规的校对量规,与特别精密的P4级滚动轴承内环孔(直径至100mm)相配的机床主轴,精密机械和高速机械的轴颈,与P4级向心球轴承外环相配合的壳体孔径,航空及航海工业中导航仪器上特殊精密的个别小尺寸零件的精度配合。
IT4 用于精密测量工具、高精度的精密配合和P4级、P5级滚动轴承配合的轴径和外壳孔径。
例如,检验IT9至IT12级工件用量规和校对IT12至IT14级轴用量规的校对量规,与P4级轴承孔(孔径>100mm)及与P5级轴承孔相配的机床主轴,精密机械和高速机械的轴颈,与P4级轴承相配的机床外壳孔,柴油机活塞销及活塞销座孔径,高精度(1级至4级)齿轮的基准孔或轴径,航空及航海工业中用仪器的特殊精密的孔径IT5 用于配合公差要求很小,形状公差要求很高的条例下,这类公差等级能使配合性质比较稳定,相当于旧国标中最高精度,用于机床、发动机和仪表中特别重要的配合尺寸,一般机械中应用较少。
机械工程制图零件图尺寸标注

h5 h5 h5
h5
h5 h5
h5 h5 h5 h5 h5
h6
F7 G7 H7 JS7 K7 M7 N7 P7 R7 S7 T7
U7
h6 h6 h6
h6 h6 h6
h6 h6 h6 h6 h6
h6
h7
E8 F8
H8 JS8 K8 M8 N8
h7 h7
h7
h7 h7 h7
h7
h8
D8 E8 F8
H8
h8 h8 h8
基本偏差 基本偏差一
般是指上、下 偏差中靠近零 线的那个偏差。 基本偏差共有 28个,它的代 号用拉丁字母 表示,大写为 孔,小写为轴。 当公差带在零 线上方时,基 本偏差为下偏 差;当公差带 在零线下方时, 基本偏差为上 偏差。
3.基本概念
公差带代号 公差带代号由基本偏差代号和表示标准公差
等级的数字组成,如H8,f7,…。
①表面质量
②极限与配合 ③形状和位置公差 ④材料及热处理
控制零件制 造质量的决 定性因素
一.表面质量
1.表面质量
表面质量是一种粗糙度。 表面粗糙度指零件的加工表面上具有的较小间距的峰谷所 形成的微观几何形状特性。
配合性质 抗腐蚀性
耐磨性
接触刚度
Y
密封性
抗疲劳强度 OX为基准线
X
o
L
2.表面粗糙度的评定参数
表面粗糙度的三个评定参数:
是指在取样长度L 内轮廓偏距绝对值
的算术平均值。
Ra:轮廓偏距绝对值的算术平均值
RZ:微观不平度十点高度 RY:轮廓最大高度
L
RaL 1 0 Y(X)dX
微观不平度十点高度Rz
在取样长度内,5个最大轮廓峰高Yp的平均值与5个最大 轮廓谷深Yv的平均值之和:
基于机器视觉的零部件尺寸检测技术
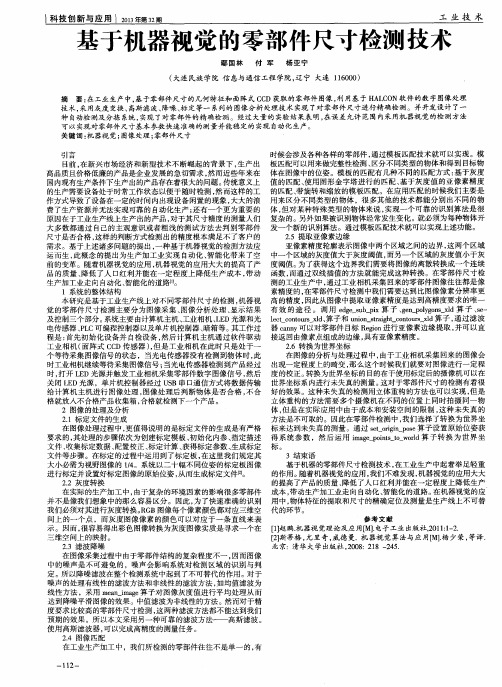
工 业 技 术
基 于机器视 觉 的零部 件尺寸检测 技术
鄢 国 林 付 军 杨 亚 宁
( 大连民族 学院 信 息与通信工程学院, 辽宁 大连 1 1 6 0 0 0 )
摘 要: 在 工业 生 产 中 , 基 于零 部 件尺 寸 的 几何 特征 和 面 阵 式 C C D获取 的零部 件 图像 , 利 用基 于 H A L C O N软 件 的数 字 图像 处理 技术, 采 用灰度 变换、 高斯滤波、 降噪、 标定等一 系列的图像分析处理技术 实现 了对零部件尺寸进行精确检测 。并开发设计 了一 种 自动 检 测及 分拣 系统 , 实现 了对 零部 件 的 精确 检 测 。 经过 大量 的 实验 结 果表 明 , 在误 差允 许 范 围 内采 用机 器视 觉 的检 测 方 法 可 以 实现 对零 部 件尺 寸基 本 参数 快 速 准确 的 测量 并 能稳 定 的 实现 自动 化 生产 。 关键 词 : 机 器视 觉 ; 图像 处 理 ; 零部 件 尺 寸 时候会 涉 及 各种 各 样 的零 部 件 , 通过 模 板 匹 配技 术 就 可 以实 现 。模 区分不同类型 的物体 和得到 目标物 目前 , 在新兴市场经济和新型技术不 断崛起 的背景下 , 生产出 板匹配可 以用来做完整性检测 、 基于灰度 高品质且价格低廉 的产品是企业发展的急切需求 , 然而近些年来在 体在图像 中的位姿 。模板的匹配有几种不同的匹配方式 : 使用 图形金字塔进行 的匹配 、 基于灰度值 的亚像素精度 国内现有生产条件下生产出的产品存在着很大的问题。 传统意义上 值 的匹配 、 带旋转和缩放的模板匹配 。在应用匹配 的时候我们主要是 的生产需要设备处于时常工作状态以便于随时检测 , 然而这样 的工 的匹配 、 作方式导致了设备在一定的时间内出现设备闲置 的现象 , 大大 的浪 用来区分不 同类型的物体 ,很多其他 的技术都能分别出不同的物 但 对某 种 特 殊 类 型 的 物体 来 说 , 实 现一 个 可 靠 的 识 别 算 法 是 很 费了生产资源并无法实现可靠的 自动化生产 ; 还有一个更为重要的 体 , 另 外 如果 被识 别 物体 经 常 发生 变化 。 就 必 须 为每 种 物体 开 原因在于工业生产线上生产出的产品 , 对于其尺寸精度 的测量人们 复 杂 的 。 大 多 数 都 通 过 自己 的主 观 意识 或 者 粗 浅 的 测试 方 法 去 判 别 零 部 件 发一个新的识别算法。通过模板匹配技术就可以实现上述功能。 2 . 5 提取 亚 像 素边 缘 尺寸是否合格 , 这样的判断方式检测出的精度根本满足不了客户的 需 求 。基 于上 述 诸 多 问题 的提 出 , 一 种 基 于机 器 视觉 的检 测 方法 应 亚像素精度轮廓表示 图像 中两个 区域之间的边界 , 这两个 区域 而另 一 个 区域 的灰 度 值小 于灰 运而生 , 此概念 的提出为生产加工业实现 自动化 、 智 能化带来 了空 中一个 区域 的灰度 值 大 于灰 度 阈 值 , 为了获得这个边界我们需要将图像的离散转换成一个连续 前的变革 。随着机器视觉的应用 , 机器视觉 的应用大大 的提高了产 度阈值 。 品的质量 、 降低 了人 口红利并能在一定程度上 降低生产成本 , 带动 函数 , 而通过双线插值的方法就能完成这种转换 。在零部件尺寸检 测 的工 业 生产 中 , 通 过工 业 相机 采 集 回来 的零 部件 图像 往 往都 是 像 生 产 加工 业 走 向 自动化 、 智 能化 的道路 【 1 】 。 1系 统 的整 体结 构 素精度 的, 在零部件尺寸检测中我们需要达到 比图像像素分辨率更 因此从 图像 中提取亚像素精度是达到高精度要求的唯一 本研 究是 基 于 工业 生 产线 上 对 不 同零 部 件 尺 寸 的检 测 , 机 器视 高 的精度 , 觉 的零 部 件 尺 寸检 测 主 要 分 为 图像 采 集 、 图像 分 析 处 理 、 显 示 结 果 有 效 的途 径 。调 用 e d g e _ s u b _ p i x算 子 、 g e n _ p o l y g o n s _ x l d算 子 、 s e — e c t co nt our s x 及 控 制 三个 部 分 。 系 统主 要 由计 算机 主 机 、 工业 相 机 、 L E D光 源 和光 l l d 、 算子和 u n i o n _ s t r a i g h t _ c o n t o u r s _ x l d 算子, 通过滤波 a n n y 可 以对 零 部件 目标 R e g i o n进行 亚 像 素边 缘 提 取 , 并 可 以直 电传感器 、 P L C可编程控制器以及单片机控制器 、 暗箱等 。 其工作过 器 c 程是 : 首先初始化设备并 自检设备 , 然后计算机主机通过软件驱动 接返回由像素点组成的边缘 , 具有亚像素精度 。 工业相机 ( 面阵式 C C D传 感 器 ) , 但 是 工 业 相 机 在 此 时 只 是处 于一 2 . 6 转换 为世 界 坐标 个等待采集图像信号的状态 ,当光 电传感器没有检测到物体 时, 此 在图像的分析与处理过程 中, 由于工业相机采集回来 的图像会 那 么 这个 时 候 我们 就 要 对 图像 进 行 一 定程 时工业相机继续等待采集图像信号 ; 当光 电传感器检测到产品经过 出现 一定 程 度上 的 畸变 , 转 换 为世 界 坐标 的 目的在 于使 用标 定 后 的摄 像机 可 以 在 时, 打开 L E D光源并触发工业相机采集零部件数字图像 信号 , 然后 度 的校 正 。 关闭L E D光源,单片机控制器经过 U S B串口通信方式将数据传输 世界坐标系 内进行未失真的测量。 这对于零部件尺寸的检测有着很 但是 给计算机 主机进行图像处理 , 图像处理后判断物体是否合格 , 不合 好 的效果 。这种未失真的检测用立体重构 的方法 也可 以实现, 格就放入不合格产 品收集箱 , 合格就检测下一个产品。 立 体 重 构 的方 法需 要 多 个 摄像 机在 不 同的 位 置 上 同 时拍 摄 同一 物 2 图像 的 处理 及分 析 体, 但是在实 际应用中由于成本和安装空 间的限制 , 这种未失 真的 2 . 1标 定文 件 的 生成 方法是不可取的。因此在零部件检测 中, 我们选择 了转换 为世界坐 在图像处理过程 中, 更值得说明的是标定文件 的生成是有严格 标来达到未失真的测量。通过 s e t o r i g i n p o s e 算子设置原始位姿获 m a g e — p o i n t s _ t o _ w o r l d算 子 转 换 为 世 界 坐 要求 的, 其处理 的步骤依次为创建标定模板 、 初始化内参 、 指定描述 得 系 统 参 数 ,然 后 运 用 i 文件、 收集 标定 数 据 、 配 置校 正 、 标 定 计算 、 获得 标 定参 数 、 生成 标 定 标 。 文件 等 步 骤 。在标 定 的 过程 中运 用 到 了标定 板 , 在这 里 我 们规 定 其 3结 束 语 大 小必 需 为视 野 图像 的 1 / 4 。系统 以二 十 幅不 同位 姿 的标 定板 图像 基 于机 器 的零 部件 尺寸 检测 技 术 , 在 工 业 生产 中起着 举 足 轻重 的作 用 。 随着 机 器 视觉 的应 用 , 我 们不 难 发 现 , 机 器 视觉 的应 用 大 大 进 行标 定 并设 置好 标 定 文件 目 。 2 . 2 灰 度转 换 的提高了产 品的质量 、 降低了人 口红利并能在一定程度上降低生产 在实际的生产加工中 , 由于复杂的环境 因素的影 响很多零部件 成 本 , 带 动 生产 加 工业 走 向 自动 化 、 智 能 化 的道 路 。 在机 器 视觉 的应 物体特征 的提取和尺寸的精确定位及测量是生产线上不可替 并不是像我们想象中的那么容易 区分。因此 , 为了快速准确的识别 用中, 我们必须对其进行灰度转换 。 R G B图像每个像素颜色都对应三维空 代 的环 节 。 参 考 文献 间上的一个点 ,而灰度图像像素 的颜色可以对应 于一条直线来表 示。因而 , 很容易得出彩色 图像转换为灰度 图像实质是寻求一个在 [ 1 】 赵鹏. 机 器视 觉理 论及 应 用[ M 】 . 电子 工业 出版 社 , 2 0 1 1 : 1 — 2 . 三 维空 间 上 的映 射 。 [ 2 】 斯蒂格 , 尤里奇 , 威德曼. 机器视觉算, a - -  ̄应 用[ MI . 杨少荣, 等译 2 - 3滤波降噪 北京: 清 华 大学 出版社 , 2 0 0 8 : 2 1 8— 2 4 5 . 在 图像采集过程 中由于零部件结构 的复杂程度不一 , 因而图像 中的 噪 声是 不可 避 免 的 ,噪声 会 影 响 系 统 对检 测 区域 的识 别 与判 定。 所以降噪滤波在整个检测系统 中起 到了不可替代的作用 。对于 噪 声 的处 理 有线 性 的滤 波 方法 和 非 线性 的滤 波方 法 , 如 均 值 滤 波为 线性方法 ,采用 m e a n _ i m a g e 算子对 图像灰度值进行平均处理从而 达到降噪平滑图像 的效果 。中值滤波为非线性的方法。然而对于精 度要求 比较高的零部件尺寸检测 , 这两种滤波方法都不能达到我们 预 期 的效 ��
主要零部件检验记录表
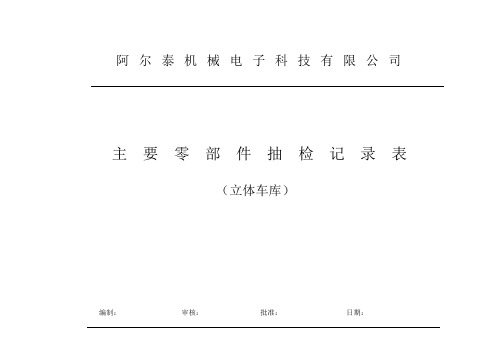
阿尔泰机械电子科技有限公司
主要零部件抽检记录表
(立体车库)
编制:审核:批准:日期:
主要零部件抽检记录
主要零部件抽检记录
主要零部件抽检记录
主要零部件抽检记录
主要零部件抽检记录
主要零部件抽检记录
主要零部件抽检记录
主要零部件抽检记录
主要零部件抽检记录
主要零部件抽检记录
主要零部件抽检记录
主要零部件抽检记录
主要零部件抽检记录
主要零部件抽检记录
主要零部件抽检记录
主要零部件抽检记录
主要零部件抽检记录
主要零部件抽检记录
主要零部件抽检记录
主要零部件抽检记录
主要零部件抽检记录
主要零部件抽检记录
主要零部件抽检记录
主要零部件抽检记录
主要零部件抽检记录
主要零部件抽检记录
主要零部件抽检记录
主要零部件抽检记录
主要零部件抽检记录
主要零部件抽检记录
主要零部件抽检记录
主要零部件抽检记录
主要零部件抽检记录
主要零部件抽检记录
主要零部件抽检记录
主要零部件抽检记录
主要零部件抽检记录
主要零部件抽检记录
主要零部件抽检记录
主要零部件抽检记录。
外购外协零部件检验记录卡
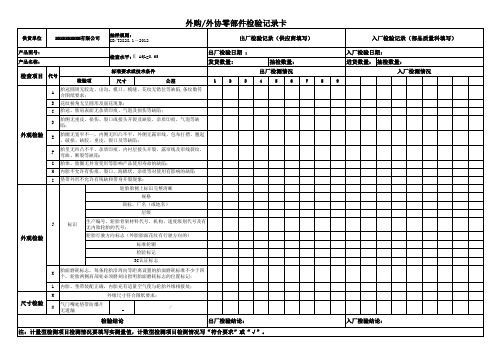
出厂检验结论:
入厂检验结论:
注:计量型检测项目检测情况要填写实测量值,计数型检测项目检测情况写“符合要求”或“√”。
பைடு நூலகம்
入厂检验记录(部品质量科填写) 入厂检验日期: 进货数量: 抽检数量: 入厂检测情况
检查项目 代号
A B C D
胎冠圆周无胶边、出沟,模口、模缝、花纹无错位等缺陷,条纹数符 合图纸要求; 花纹棱角无呈圆形及崩花现象; 胎冠、胎肩表面无杂质印痕、气泡及损伤等缺陷; 胎侧无重皮、损伤、裂口或接头开裂及缺胶、杂质印痕、气泡等缺 陷; 胎圈无宽窄不一,内侧无凹凸不平,外侧无露帘线、包布打摺、翘起 、破损、缺胶、重皮、裂口及等缺陷; 胎里无凹凸不平、杂质印痕、内衬层接头开裂、露帘线及帘线裂纹、 弯曲、断裂等缺陷; 胎体、胎圈无异常变形等影响产品使用寿命的缺陷; 内胎不允许有伤痕、裂口、海棉状、杂质等对使用有影响的缺陷 垫带外形不允许有残缺和带身开裂现象; 轮胎胎侧上标识完整清晰 规格 商标、厂名(或地名) 层级 生产编号、轮胎骨架材料代号、机构、速度级别代号及有 无内胎轮胎的代号; 轮胎行驶方向标志(外胎胎面花纹有行驶方向的) 标准轮辋 检验标记 3C认证标志
外观检验
E F G H I
J
标识
外观检验
K L M
胎面磨耗标志,每条轮胎沿周向等距离设置的胎面磨耗标准不少于四 个,轮胎两侧肩部处必须磨刻出指明胎面磨耗标志的位置标记; 内胎、垫带装配正确,内胎充有适量空气使与轮胎外缘相接处; 外缘尺寸符合图纸要求; 气门嘴处垫带防爆片 无遗漏 /
尺寸检验
N
检验结论
外购/外协零部件检验记录卡
供货单位 产品图号: 产品名称: 检查水平:Ⅱ AQL=0.65 标准要求或技术条件 检验项 尺寸 公差
零件尺寸检测记录表-20210602
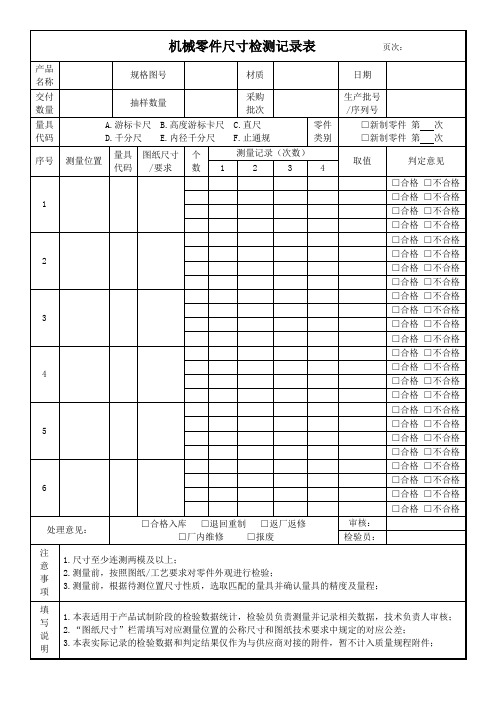
□合格 □不合格
□合格 □不合格
□合格 □不合格
□合格 □不合格
处理意见:
□合格入库□退回重制□返厂返修
□厂内维修□报废
审核:
检验员:
注
意
事
项
1.尺寸至少连测两模及以上;
2.测量前,按照图纸/工艺要求对零件外观进行检验;
3.测量前,根据待测位置尺寸性质,选取匹配的量具并确认量具的精度及量程;
填
写
说
□合格 □不合格
□合格 □不合格
□合格 □不合格
2
□合格 □不合格
□合格 □不合格
□合格 □不合格
□合格 □不合格
3
□合格 □不合格
□合格 □不合格
□合格 □不合格
□合格 □不合格
4
□合格 □不合格
□合格 □不合格
□合格 □不合格
□合格 □不ห้องสมุดไป่ตู้格
5
□合格 □不合格
□合格 □不合格
□合格 □不合格
□合格 □不合格
明
1.本表适用于产品试制阶段的检验数据统计,检验员负责测量并记录相关数据,技术负责人审核;
2.“图纸尺寸”栏需填写对应测量位置的公称尺寸和图纸技术要求中规定的对应公差;
3.本表实际记录的检验数据和判定结果仅作为与供应商对接的附件,暂不计入质量规程附件;
机械零件尺寸检测记录表页次:
产品名称
规格图号
材质
日期
交付
数量
抽样数量
采购
批次
生产批号/序列号
量具
代码
A.游标卡尺 B.高度游标卡尺 C.直尺
D.千分尺 E.内径千分尺 F.止通规
零件类别
测量仪器校验记录表

用游标卡尺去测量锻铸件毛坯或精度要求很高的尺寸,都是不合理的。 前者容易损坏量具,后者测量精度达不到要求,因为量具都有一定的示值误差。 游标读数值 示值总误差
0.02 ±0.02 0.05 ±0.05 0.10 ±0.10
游标卡尺的示值误差,就是游标卡尺本身的制造精度,不论你使用得怎样正确,卡尺本身就可能产生这 些 例误如差,。用游标读数值为0.02mm的0~125mm的游标卡尺(示值误差为±0.02mm),测量 50mm的轴时,若游 标卡尺上的读数为50.00mm,实际直径可能是 50.02mm,也可能是 49.98mm。这不是游标尺的使用方法上 有什么问题,而是它本身制造精度所允许产生的误差。 四 游标卡尺的使用方法 量具使用得是否合理,不但影响量具本身的精度,且直接影响零件尺寸的测量精度,甚至发生质量事 故,对国家造成不必要的损失。所以,我们必须重视量具的正确使用,对测量技术精益求精,务使获得 正确的测量结果,确保产品质量。 使用游标卡尺测量零件尺寸时,必须注意下列几点: 1 测量前应把卡尺揩干净,检查卡尺的两个测量面和测量刃口是否平直无损,把两个量爪紧密贴合时,应 无明显的间隙,同时游标和主尺的零位刻线要相互对准。这个过程称为校对游标卡尺的零位。 2 移动尺框时,活动要自如,不应有过松或过紧,更不能有晃动现象。用固定螺钉固定尺框时,卡尺的读 数不应有所改变。在移动尺框时,不要忘记松开固定螺钉,亦不宜过松以免掉了。 3 当测量零件的外尺寸时:卡尺两测量面的联线应垂直于被测量表面,不能歪斜。 测量沟槽时,应当用量爪的平面测量刃进行测量,尽量避免用端部测量刃和刀口形量爪去测量外尺寸。 而 4 当对测于量圆零弧件形的沟内槽尺尺寸寸时,:则要应使当量用爪刃分口开形的量距爪离进小行于测所量测,内不尺应寸当,用进平入面零形件测内量孔刃后进,行再测慢量慢。张开并轻轻接 触零件内表面,用固定螺钉固定尺框后,轻轻取出卡尺来读数。取出量爪时,用力要均匀,并使卡尺沿 着孔的中心线方向滑出,不可歪斜,免使量爪扭伤;变形和受到不必要的磨损,同时会使尺框走动,影 响 5 用测下量量精爪度的。外测量面测量内尺寸时,在读取测量结果时,一定要把量爪的厚度加上去。即游标卡尺上的 读数,加上量爪的厚度,才是被测零件的内尺寸。 6 用游标卡尺测量零件时,不允许过分地施加压力,所用压力应使两个量爪刚好接触零件表面。如果测量 压力过大,不但会使量爪弯曲或磨损,且量爪在压力作用下产生弹性变形,使测量得的尺寸不准确(外尺 寸小于实际尺寸,内尺寸大于实际尺寸)。 在游标卡尺上读数时,应把卡尺水平的拿着,朝着亮光的方向,使人的视线尽可能和卡尺的刻线表面垂 直,以免由于视线的歪斜造成读数误差。 7 为了获得正确的测量结果,可以多测量几次。 即在零件的同一截面上的不同方向进行测量。对于较长零件,则应当在全长的各个部位进行测量,务使 获得一个比较正确的测量结果。 为了便于记忆,更好的掌握游标卡尺的使用方法,把上述提到的几个主要问题, 整理成顺口溜: 量爪贴合无间隙,主尺游标两对零。 尺框活动能自如,不松不紧不摇晃。 测力松紧细调整,不当卡规用力卡。 量轴防歪斜,量孔防偏歪, 测量内尺寸,爪厚勿忘加。 面对光亮处,读数垂直看。
模具FMEA(金型)
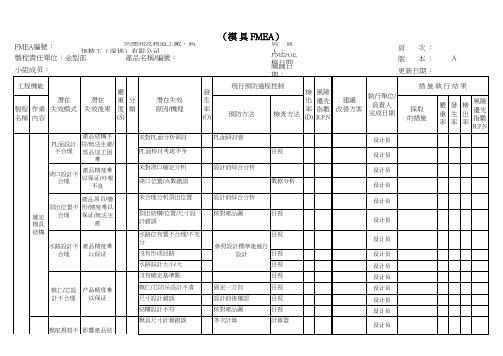
負 責 人:頁 次 : FMEA 定稿日期 2010-6-24版 本 :關鍵日期:更新日期:小組成员:A(模 具 FMEA)供應商及制造工廠:高畑精工(深圳)有限公司製程責任單位:金型部 產品名稱/編號:FMEA編號:負 責 人:頁 次 : FMEA 定稿日期 2010-6-24版 本 :關鍵日期:更新日期:小組成员:A(模 具 FMEA)供應商及制造工廠:高畑精工(深圳)有限公司製程責任單位:金型部 產品名稱/編號:FMEA編號:負 責 人:頁 次 : FMEA 定稿日期 2010-6-24版 本 :關鍵日期:更新日期:小組成员:A供應商及制造工廠:高畑精工(深圳)有限公司製程責任單位:金型部 產品名稱/編號:FMEA編號:圖設計負 責 人:頁 次 : FMEA 定稿日期 2010-6-24版 本 :關鍵日期:更新日期:小組成员:A供應商及制造工廠:高畑精工(深圳)有限公司製程責任單位:金型部 產品名稱/編號:FMEA編號:負 責 人:頁 次 : FMEA 定稿日期 2010-6-24版 本 :關鍵日期:更新日期:小組成员:A(模 具 FMEA)供應商及制造工廠:高畑精工(深圳)有限公司製程責任單位:金型部 產品名稱/編號:FMEA編號:負 責 人:頁 次 : FMEA 定稿日期 2010-6-24版 本 :關鍵日期:更新日期:小組成员:A(模 具 FMEA)供應商及制造工廠:高畑精工(深圳)有限公司製程責任單位:金型部 產品名稱/編號:FMEA編號:件检查負 責 人:頁 次 : FMEA 定稿日期 2010-6-24版 本 :關鍵日期:更新日期:小組成员:A(模 具 FMEA)供應商及制造工廠:高畑精工(深圳)有限公司製程責任單位:金型部 產品名稱/編號:FMEA編號:具制造負 責 人:頁 次 : FMEA 定稿日期 2010-6-24版 本 :關鍵日期:更新日期:小組成员:A(模 具 FMEA)供應商及制造工廠:高畑精工(深圳)有限公司製程責任單位:金型部 產品名稱/編號:FMEA編號:。
OTS文件目录参考

SP
PE填写的存在问题一览表发SP整改,由SP填写整改承诺表
注:1、SP:供应商PE:产品工程师S QE:供应商质量工程师QE:质量工程师
BUYER:采购员N/A:表式自定
2、空白记录表式由技术中心设计,由PE提供给供应商(一般在项目启动会上提交)
3、红色字体可根据开发过程情况需要进行删减;其它表式必须要。
按产品图纸或零件的全尺寸测量计划要求确认数据的真实性(若需要可由QE检验零件尺寸)
《零件材料检验报告》
SP
按产品图纸或零件材料代用单要求进行审核(若需要可由QE检验零件材料)
《零件性能(台架)试验报告》
SP
按产品认证试验大纲要求进行审核(若需要可由QE检验零件性能)
《供应商样件/工装样件(PROTOTYPE /OTS)保证书》
确认零件的试验大纲
《尺寸测量计划》
SP
确认零件的尺寸测量计划(启动会后前三周提交)
《产品认证试验大纲》
SP
确认零件的试验大纲(启动会后前三周提交)
《材料代用申请单》
SP
确认零件的材料代用单(启动会后前三周提交)
《分供方清单》
SP
PE
供应商填写所有分供方名单(启动会后前三周提交)
《零件尺寸检验报告》
SP
SP
由PE签署确认产品是否可以用在试验车上(不合格者,填写《整改计划》)
《产品设计与开发控制计划》
SP
供应商做产品设计与开发控制计划(启动会后前三周提交)
《产品设计开发计划》
SP
供应商做产品设计开发计划(启动会后前三周提交)
《模具开发计划》
SP
供应商做模具开发计划(启动会后前三周提交)
全尺寸检测报告
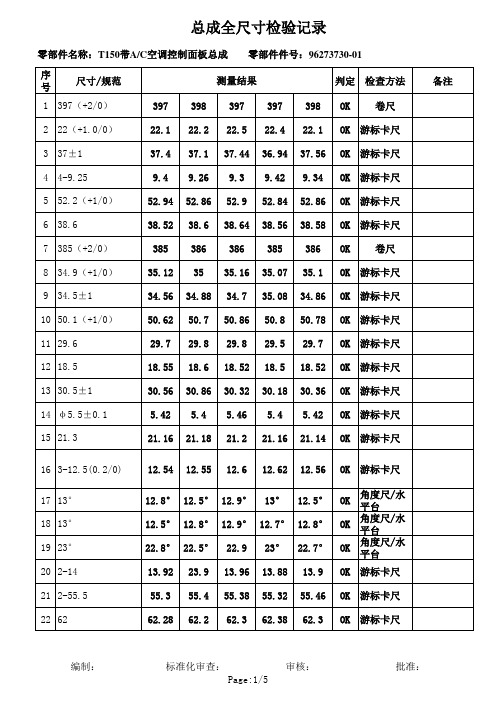
38.52 38.6 38.64 38.56 38.58 OK 游标卡尺 385 386 386 385 386 OK 卷尺
35.12 35 35.16 35.07 35.1 OK 游标卡尺
9 34.5±1 10 50.1(+1/0)
34.56 34.88 34.7 35.08 34.86 OK 游标卡尺 50.62 50.7 50.86 50.8 50.78 OK 游标卡尺
审核:
Page:4/5
批准:
总成全尺寸检验记录
零部件名称:T150带A/C空调控制面板总成 零部件件号:96273730-01
96 R3
OK
OK
OK
OK
OK OK R规
97 2° 98 5° 99 5.4
1.8° 1.9° 2.1° 2.2° 2.1° OK 角度尺 4.9° 4.8° 5° 4.8° 5.1° OK 角度尺 5.27 5.28 5.26 5.28 5.26 OK 游标卡尺
83 12.2 84 10 85 φ7(0/-0.2)
12.1 12.16 12.14 12.12 12.1 OK 游标卡尺 9.92 9.94 9.94 9.92 9.96 OK 游标卡尺 6.86 6.88 6.88 6.84 6.84 OK 游标卡尺
86 2.7 87 29.2
2.72 2.74 2.74 2.72 2.74 OK 游标卡尺 29.38 29.4 29.36 29.4 29.38 OK 游标卡尺
4.97
5
5.02 5.1 5.08 OK 游标卡尺
19.62 19.6 19.58 19.62 19.58 OK 游标卡尺
69 6 70 15 71 14.4
零部件测绘(定稿)PPT3

4.孔间距的测量
孔间距可以用卡钳(或游标卡尺)结合直尺测出。
D=D0=K+d
● 18
孔中心距测量
先测出A1和d, 则A = A1 + d
52
孔中心距测量
标准棒
53
● 19
5.深度及壁厚尺寸的测量
壁厚尺寸可以用直尺测量,如图中底壁厚度X= A-B, 或用卡钳和直尺测量,如图中侧壁厚度Y= C- D
• 对某些零件的相对位 置、装配间隙等装配尺 寸应先测量
• 拆卸后要将各零件编 号、扎上标签,避免散 失、错乱
拆卸调压螺钉、螺母、 弹簧、钢球等
19
● 34
二、画装配示意图
装配示意图是在部件拆卸过程中所画的记录图样, 其作用是避免由于零件拆卸后可能产生错乱而给重 新装配时带来困难,它是通过目测,徒手用简单的 线条示意性地画出部件的图样,主要表达部件的结 构、装配关系、工作原理、传动路线等。 注意事项:
拆卸并画装配示意图 零件分类、列出零、部件及标准件明细表 零件测绘,画零件草图 画装配䓍图及装配图 画零件工作图 写实习报告、装订图册
天数
0.5
0.5 0.5 2 3.5 2 1 10
第二部分 了解和分析测绘对象
一、用途
齿轮泵是各种机械润滑和液压系统的输油装置。用 于液压系统的泵站,将油箱中的油液输送到机器有关运 动部件需要润滑的部位。主要用于低压或噪声水平限制 不严的场合。
• 确定主视图、视图数量和表达方法。
2.徒手画零件图:
• 徒手目测画零件视图 • 保持零件各部分的比例关系,尽量按1:1画; • 要求线型分明,图面整洁,表达清楚、简练; • 先画图框和标题栏; • 画视图时要注意在视图之间留出标注尺寸的位置; • 选定的表达方案画全各个视图和剖视等
外购(外协)件检-验记录表

年月日
检验记录
不合格问题描述记录
序号 检验项目
1 2 3 4 5 6 7 8 9 10 11 12 13 14 15
第
一
1 外观质量
联
外
2 安装尺寸
检
科
/Leabharlann 3 附件检查第4
标识
二
5 出厂检验报告
检查结果: 处理意见:
□合格 □入库
□A 类不合格 □退货
□B 类不合格 □返工
返工 处理 结果
□合格入库 □不合格退货
RC03-ZL-06-01-01 车型 供应商名称 来货数量
外购(外协)件检验记录表
零部件图号 3C 产 品 检查数量
Y□
N□
零部件名称 产品批次号 AQL Ac/Re
年月日
序
检验项目
号
检验记录 1 2 3 4 5 6 7 8 9 10 11 12 13 14 15
不合格问题描述记录
第
1
外观质量
一
联
管
科
联
检验员签字:
注:1、能用数据表示的必须用数据表示;不能用数据表示的,可用“√”表示合格,用“×”表示不合格的同时必须在不合格问题描述栏中进行问题描述;无检 物
测 项 目 的 用 “ — ” 表示; 如 有 不 在 检 测 项 目内的 检 验 内 容 在 空 格 内进行 填 写 并 做 好 检 查 记录。 2.上 述 检 测 项 目 必 须根 据 外 购 件 检 验 规 范如实 检 测 、 填 写 。
外
2
尺寸测量
检
科
/
第
3 标识和包装
●产品 3C 合格证是否符合要求 Y□ N□
平行检验记录表新版

设计桩顶标高(M)
实际桩顶标高(M)
桩端连接情况
备 注
监理单位平行检验结论
监理工程师
日期: 年 月 日
建筑物垂直度、标高、全高平行检验记录
工程名称
监理单位
测量项目
层次、部位
允许偏差
平行检验实测偏差(mm)
备注
标
高
层高:
±10mm
全高
±30mm
垂
直
度
层高:
≤5m,8mm。
>5m,
10mm。
一般项目
钢筋应平直、无损伤,表面不得有裂纹、油污、颗粒或片状老锈
监理单位平行检验结论
监理工程师
日期: 年 月 日
混凝土回弹法检测平行检验记录
工程名称:监理单位:
回弹部位:
编号
回弹值ቤተ መጻሕፍቲ ባይዱi
碳化深度
dm
测区推定值
构件
测区
1
2
3
4
5
6
7
8
9
10
11
12
13
14
15
16
N
监理单位平行检验结论
监理工程师
日期: 年 月 日
室内标高、轴线、楼板厚度平行检验记录
工程名称:监理单位:
检测部位
施工单位
测量项目
层次或部位
设计值
允许偏差
平行检验实测偏差
室
内
标
高
±10
(mm)
轴
线
墙、柱、梁:8,剪力墙:5
(mm)
楼
板
厚
度
-5~+8
(mm)
监理单位平行检验结论
零部件检测作业指导书
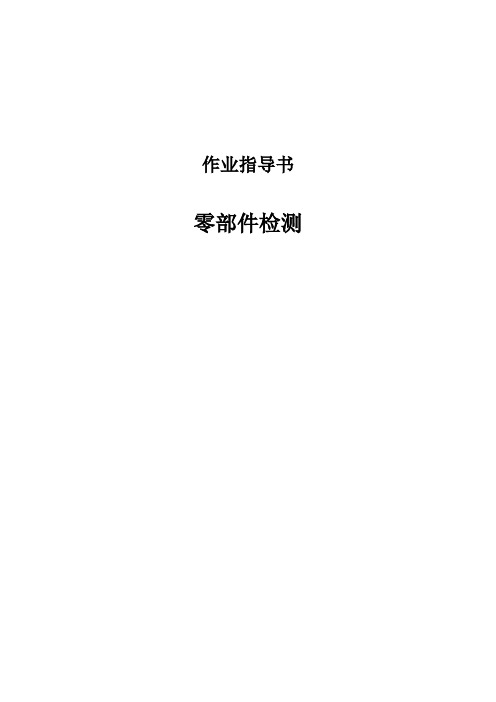
4.1.2.1 用扫描枪扫描主阀条形码,检查核对读取的编号与实物一致,确保
条形码信息正确录入 HMIS 检修系统中。
4.1.2.2 主阀配件检修限度需符合表 1 规定。
表 1 零件检修限度表
序号
名称
检测项目
原型 (mm)
限度 (mm)
检测器具
滑阀厚度不小于
17±0.15
16
1
滑阀
游标卡尺
缓解槽深度不小于
图5
4.3.2.2 用通针疏通触杆Φ1.5mm 孔及Φ4mm 孔,疏通时,采用小于各孔径的 通针疏通,通针硬度小于零部件硬度,如图 6。
图6
4.3.3 KZW 系列调整阀配件检查 4.3.3.1 各零部件状态良好,不得有损伤,裂纹。 4.3.3.2 各零部件连接部位或铆接部位状态良好,不松动。 4.3.4 KZW 系列调整阀配件测量 4.3.4.1 测量显示活塞Φ8 mm 柱面,柱面直径小于Φ17.6mm 时更换,划伤时 可用细砂纸或油石打磨修理,各柱塞及铜套表面须光滑,如图 7。
0.5mm 刀口尺
1mm
游标卡尺或 样板
4.3.7 T-1 系列调整阀配件检查
4.3.7.1 各零部件状态良好,不得有损伤,裂纹。各零件表面不得有目视可 见的污垢、沙尘、水分、纤维物和其它污物。 4.3.7.2 各零部件连接部位或铆接部位状态良好,不松动。
各零部件检测不合格者严禁使用。 4.4 检查阀体双头螺柱 对主阀、半自动缓解阀、紧急阀要双头螺栓逐一检查,双头螺柱松动时,须 分解检查,重新组装时,装入阀体端螺纹须均匀涂抹螺纹锁固剂,并严格执 行先紧固双头螺柱再组装压紧阀盖螺母的组装顺序,不得在双头螺柱上先装 上阀盖螺母再向阀体上组装双头螺柱。 4.5 检修记录填写 4.5.1 将 120/120-1 阀检测结果录入 HMIS 系统,在《型货车空气控制阀主阀 检修记录》(ZG-03),《120/120-1 型货车空气控制阀紧急阀检修记录》(ZG05)的 “零部件检查”填写相应的检测数据(检测数据精确到小数点后 2 位),并在“检测”栏录入工作者名,检查录入无误。 4.5.2 将 KZW 系列传感配件的检测结果填入《KZW 系列传感阀检修记录》(ZG16)“检测结果”栏,并在“检测”栏加盖工作者名章。 4.5.3 将 KZW 系列调整阀配件检测结果填入《KZW 系列调整阀检修记录》(ZG18)“检测结果”栏,并在“检测”栏加盖工作者名章。 4.5.4 将 WG-1A/C 型传感阀配件检测结果填入《WG-1A/C 型传感阀检修记录》 (ZG-20)“检测结果”栏,并在“检测”栏加盖工作者名章。 5. 设备故障处置 工作者在设备点检和操作过程中,要注意观察设备状态,发现异常,立即停 机检查处理,属于自修范围的故障由工作者处理。超出自检自修范围的故