压铸与注塑的区别
成型工艺的名词解释

成型工艺的名词解释1. 引言成型工艺是指将材料经过一系列的工艺操作,通过特定的方法使其达到所需形状和尺寸的过程。
成型工艺广泛应用于制造业,是实现产品设计和生产的关键环节。
本文将对常见的成型工艺进行解释和介绍,包括注塑成型、压铸成型、挤压成型、热缩成型等。
2. 注塑成型注塑成型是一种将熔化的塑料注入到模具中,并在冷却后取出所需形状的成型工艺。
这种成型工艺常用于制造塑料制品,如塑料零件、容器和玩具等。
注塑成型具有生产效率高、制品精度高、成本相对较低等优点,因此在工业生产中得到广泛应用。
3. 压铸成型压铸成型是利用压力将熔融金属注入到模具中,冷却后取出所需形状的成型工艺。
这种成型工艺适用于制造金属制品,如汽车零件、家电外壳和工具等。
压铸成型具有生产效率高、制品强度高、尺寸精度高等特点,是制造高精度零部件的重要工艺之一。
4. 挤压成型挤压成型是通过将熔融的材料推入模具中,然后在冷却后获得所需形状的成型工艺。
这种成型工艺适用于制造具有连续性形状的材料,如管材、线材和各种型材等。
挤压成型具有生产效率高、制品尺寸稳定、成本相对较低等优势,常用于塑料、金属和橡胶等材料的成型。
5. 热缩成型热缩成型是利用热能将材料软化或熔化后,通过外加压力使其填充到模具中,并在冷却后取出所需形状的成型工艺。
这种成型工艺广泛应用于制造塑料制品,如塑料瓶、包装箱和容器等。
热缩成型具有快速、高效、成本低的特点,适用于大批量生产。
6. 流延成型流延成型是通过将熔化的材料涂敷到平板上,然后通过拉伸和冷却使其变为所需形状的成型工艺。
这种成型工艺常用于制造薄膜、纤维和片材等产品,如塑料薄膜、复合膜和涂层材料等。
流延成型具有制品尺寸稳定、生产过程简单、成本低等优势,适合大规模生产。
7. 旋转成型旋转成型是通过将熔化的材料注入到模具中,然后通过旋转模具使材料均匀附着在模具表面,并在冷却后取出所需形状的成型工艺。
这种成型工艺适用于制造中空的产品,如塑料水箱、玩具和装饰品等。
三种液态成形方法
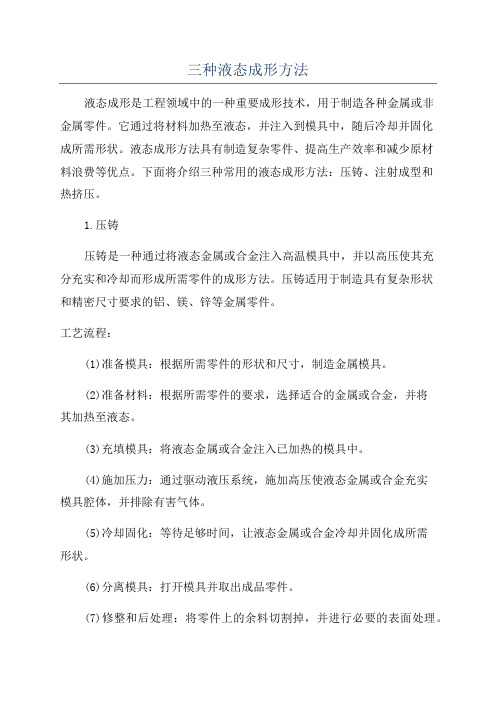
三种液态成形方法液态成形是工程领域中的一种重要成形技术,用于制造各种金属或非金属零件。
它通过将材料加热至液态,并注入到模具中,随后冷却并固化成所需形状。
液态成形方法具有制造复杂零件、提高生产效率和减少原材料浪费等优点。
下面将介绍三种常用的液态成形方法:压铸、注射成型和热挤压。
1.压铸压铸是一种通过将液态金属或合金注入高温模具中,并以高压使其充分充实和冷却而形成所需零件的成形方法。
压铸适用于制造具有复杂形状和精密尺寸要求的铝、镁、锌等金属零件。
工艺流程:(1)准备模具:根据所需零件的形状和尺寸,制造金属模具。
(2)准备材料:根据所需零件的要求,选择适合的金属或合金,并将其加热至液态。
(3)充填模具:将液态金属或合金注入已加热的模具中。
(4)施加压力:通过驱动液压系统,施加高压使液态金属或合金充实模具腔体,并排除有害气体。
(5)冷却固化:等待足够时间,让液态金属或合金冷却并固化成所需形状。
(6)分离模具:打开模具并取出成品零件。
(7)修整和后处理:将零件上的余料切割掉,并进行必要的表面处理。
2.注射成型注射成型是一种通过将液态或半液态塑料材料注入模具中,并在成型温度下固化成所需形状的成形方法。
注射成型适用于制造塑料零件,广泛应用于电子、汽车、日用品等领域。
工艺流程:(1)准备模具:根据所需零件的形状和尺寸,制造塑料模具。
(2)准备材料:选择适合注射成型的塑料树脂,并将其加热至液态或半液态。
(3)充填模具:将液态或半液态塑料注入已加热的模具中。
(4)冷却固化:等待足够时间,让塑料在模具中冷却并固化成所需形状。
(5)分离模具:打开模具并取出成品零件。
(6)修整和后处理:将零件上的余料切割掉,并进行必要的表面处理。
3.热挤压热挤压是一种通过将液态金属在高温和高压下通过模孔挤压成型的成形方法。
热挤压适用于制造具有长直形截面或复杂截面的杆、管和型材等零件。
工艺流程:(1)准备模具:根据所需零件的形状和尺寸,制造高温合金模具。
注塑机与压铸机的区别
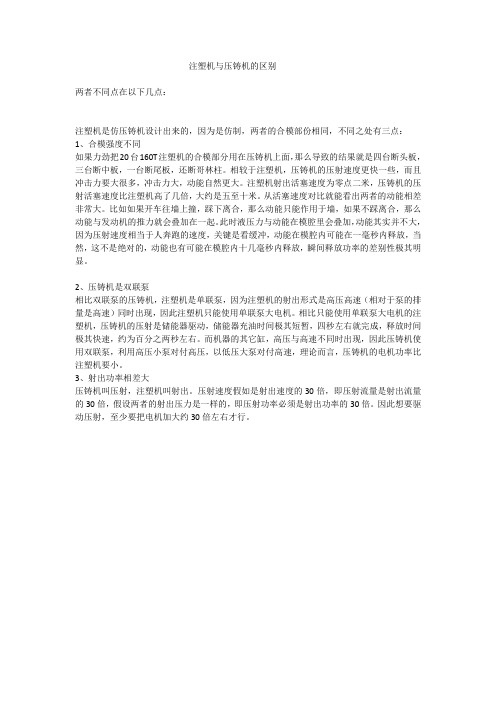
注塑机与压铸机的区别两者不同点在以下几点:注塑机是仿压铸机设计出来的,因为是仿制,两者的合模部份相同,不同之处有三点:1、合模强度不同如果力劲把20台160T注塑机的合模部分用在压铸机上面,那么导致的结果就是四台断头板,三台断中板,一台断尾板,还断哥林柱。
相较于注塑机,压铸机的压射速度更快一些,而且冲击力要大很多,冲击力大,动能自然更大。
注塑机射出活塞速度为零点二米,压铸机的压射活塞速度比注塑机高了几倍,大约是五至十米。
从活塞速度对比就能看出两者的动能相差非常大。
比如如果开车往墙上撞,踩下离合,那么动能只能作用于墙,如果不踩离合,那么动能与发动机的推力就会叠加在一起。
此时液压力与动能在模腔里会叠加,动能其实并不大,因为压射速度相当于人奔跑的速度,关键是看缓冲,动能在模腔内可能在一毫秒内释放,当然,这不是绝对的,动能也有可能在模腔内十几毫秒内释放,瞬间释放功率的差别性极其明显。
2、压铸机是双联泵相比双联泵的压铸机,注塑机是单联泵,因为注塑机的射出形式是高压高速(相对于泵的排量是高速)同时出现,因此注塑机只能使用单联泵大电机。
相比只能使用单联泵大电机的注塑机,压铸机的压射是储能器驱动,储能器充油时间极其短暂,四秒左右就完成,释放时间极其快速,约为百分之两秒左右。
而机器的其它缸,高压与高速不同时出现,因此压铸机使用双联泵,利用高压小泵对付高压,以低压大泵对付高速,理论而言,压铸机的电机功率比注塑机要小。
3、射出功率相差大压铸机叫压射,注塑机叫射出。
压射速度假如是射出速度的30倍,即压射流量是射出流量的30倍,假设两者的射出压力是一样的,即压射功率必须是射出功率的30倍。
因此想要驱动压射,至少要把电机加大约30倍左右才行。
模具成型分类
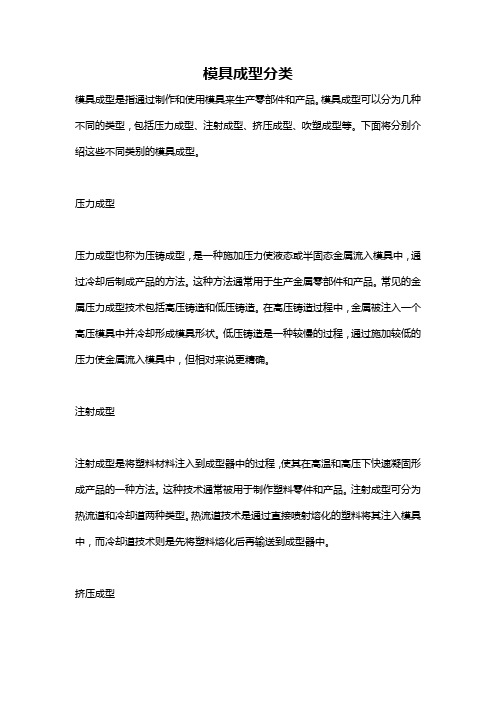
模具成型分类模具成型是指通过制作和使用模具来生产零部件和产品。
模具成型可以分为几种不同的类型,包括压力成型、注射成型、挤压成型、吹塑成型等。
下面将分别介绍这些不同类别的模具成型。
压力成型压力成型也称为压铸成型,是一种施加压力使液态或半固态金属流入模具中,通过冷却后制成产品的方法。
这种方法通常用于生产金属零部件和产品。
常见的金属压力成型技术包括高压铸造和低压铸造。
在高压铸造过程中,金属被注入一个高压模具中并冷却形成模具形状。
低压铸造是一种较慢的过程,通过施加较低的压力使金属流入模具中,但相对来说更精确。
注射成型注射成型是将塑料材料注入到成型器中的过程,使其在高温和高压下快速凝固形成产品的一种方法。
这种技术通常被用于制作塑料零件和产品。
注射成型可分为热流道和冷却道两种类型。
热流道技术是通过直接喷射熔化的塑料将其注入模具中,而冷却道技术则是先将塑料熔化后再输送到成型器中。
挤压成型挤压成型是一种通过将塑料材料推入模具中使其形成产品的方法。
这种技术通常被用于制作管状和长形塑料零件。
挤压成型可以分为单层挤压和多层挤压。
单层挤压是一种将熔化后的塑料材料输送至模具中的过程。
而多层挤压则是将多种材料层叠在一起,以使其形成更耐用的材料。
吹塑成型吹塑成型是通过在成型器中灌入熔化的塑料,然后用压缩空气将其吹成形状的方法。
这种技术常用于生产塑料瓶和其他小型塑料制品。
吹塑成型可以分为一次吹塑和两次吹塑。
一次吹塑是通过将新鲜塑料材料灌入到预定的形状中并加热使其膨胀。
两次吹塑是一种在预定形状和一些细节被制成后再次吹气的方法,以使产品完全形成所需形状。
总结模具成型是制造塑料、金属等各种材料制品的重要工艺之一,模具成型可分为压力成型、注射成型、挤压成型、吹塑成型等不同种类。
了解不同的成型方式有助于在选择制造工艺上做到更好的选择,避免错误选择而导致不必要的损失。
注塑与压铸实验报告

注塑与压铸实验报告实验目的本实验旨在比较注塑和压铸两种常见的金属加工方法在材料加工过程中的性能差异,通过实验对比,得出两种方法的优缺点并且对比材料的物理性能。
实验原理注塑法注塑是一种通过将熔融的材料注入模具中,在在模具中冷却凝固后得到所需的零件的方法。
注塑法主要包括以下步骤:1. 开模:将模具打开,取出上一次注塑生产的零件。
2. 充模:将塑料颗粒加热至熔融状态,然后通过注射机将熔融的塑料注入模具中。
3. 冷却:注入模具的熔融塑料在模具内冷却凝固成型。
4. 脱模:打开模具,取出已经成型的零件。
压铸法压铸是一种通过将金属加热至液态后,以高压将熔融金属注入模具中,在模具内迅速凝固成型的方法。
压铸法主要包括以下步骤:1. 开模:将模具打开,取出上一次压铸得到的零件。
2. 加料:将金属加热至液态,然后通过注射机将熔融金属注入模具中。
3. 冷却:注入模具的熔融金属在模具内冷却凝固成型。
4. 脱模:打开模具,取出已经成型的零件。
实验步骤材料准备1. 准备注塑和压铸所需的模具。
2. 准备注塑所需的塑料颗粒。
3. 准备压铸所需的金属材料。
实验操作1. 进行注塑操作:a. 将塑料颗粒加入注射机中。
b. 设置注射机的温度和压力参数。
c. 打开模具,将注射机喷嘴对准模具注塑孔,注入塑料。
d. 等待塑料在模具中冷却凝固。
e. 打开模具,取出注塑得到的零件。
2. 进行压铸操作:a. 烧热金属材料至液态。
b. 将液态金属注入压铸模具中。
c. 等待金属在模具中冷却凝固。
d. 打开模具,取出压铸得到的零件。
实验结果与分析1. 模具质量:注塑所使用的塑料模具相对于压铸所使用的金属模具更容易制造和更加经济,但其耐用性和使用次数较低。
2. 成型速度:注塑法的成型速度相对较快,注塑机可以连续工作,并且模具冷却时间较短。
而压铸法在成型速度上较慢,每次压铸后需要进行模具的冷却。
3. 材料性能:注塑所使用的塑料材料相对于压铸所使用的金属材料来说,具有更好的绝缘性能和耐腐蚀性能,而压铸得到的金属零件更加坚固耐用。
模具结构基础知识
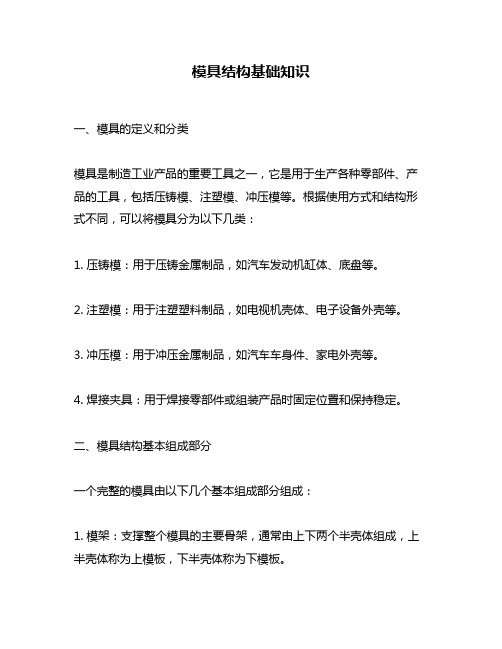
模具结构基础知识一、模具的定义和分类模具是制造工业产品的重要工具之一,它是用于生产各种零部件、产品的工具,包括压铸模、注塑模、冲压模等。
根据使用方式和结构形式不同,可以将模具分为以下几类:1. 压铸模:用于压铸金属制品,如汽车发动机缸体、底盘等。
2. 注塑模:用于注塑塑料制品,如电视机壳体、电子设备外壳等。
3. 冲压模:用于冲压金属制品,如汽车车身件、家电外壳等。
4. 焊接夹具:用于焊接零部件或组装产品时固定位置和保持稳定。
二、模具结构基本组成部分一个完整的模具由以下几个基本组成部分组成:1. 模架:支撑整个模具的主要骨架,通常由上下两个半壳体组成,上半壳体称为上模板,下半壳体称为下模板。
2. 模腔:用于成形产品的空间,在上下两个半壳体中间形成。
根据不同的产品形状和尺寸需求,可以设计出不同形状和尺寸的模腔。
3. 模仁:用于成形产品的核心部分,通常安装在上模板上,与模腔配合使用。
4. 引导柱和导套:引导柱是固定在上下两个半壳体中间,用于保持模具的位置和稳定性;导套则是安装在引导柱上,用于保持引导柱与半壳体之间的间隙,以便半壳体之间的移动。
5. 凸模和凹模:凸模是安装在下模板上的零件,用于成形产品表面;凹模则是安装在上模板上的零件,用于成形产品内部和底部。
6. 夹具和顶针:夹具是用于固定原材料或成品,保持其位置稳定;顶针则是用于将成品从模腔中顶出来。
三、常见的模具结构类型1. 平面式结构:适合制造平面形状、简单结构的产品。
由一个平面型下模板和一个平面型上模板组成。
2. 拉伸式结构:适合制造长条状、管状等拉伸型产品。
由一个拉伸型下模板和一个拉伸型上模板组成。
3. 斜侧式结构:适合制造斜侧形状、倾斜角度较大的产品。
由一个斜侧型下模板和一个斜侧型上模板组成。
4. 旋转式结构:适合制造圆柱形、球形等旋转型产品。
由一个圆柱型下模板和一个圆柱型上模板组成。
四、常见的模具材料1. 铝合金:轻质、导热性能好,适用于制造小批量生产的零件或产品。
压铸与注塑的区别
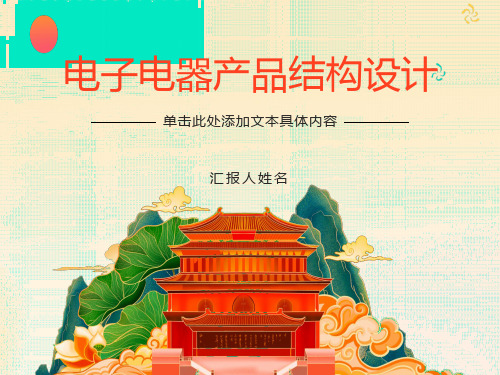
二、压铸件设计
示例:相邻距离的合理设计
二、压铸件设计
2.7、铸孔 铝合金可铸最小孔径为2.5mm, 可铸孔径大小与深度有关,对盲孔,孔深为 孔径的3到4倍, 对通孔,孔深为孔径的6到8倍。对孔径精度或孔距精度要求较高 的,一般不直接铸孔,采用后序机加工处理, 但对壁厚较厚的孔,为避免机加后出现 表面有砂眼,一般先铸出底孔,然后用机加去除加工余量。 2.8、文字和图案 文字大小不小于5号字体,凸起高度0.3~0.5mm, 线宽推荐0.8mm.,出模 度10~15度,如果外壳表面采用喷粉处理,其外侧面的文字及图案的凸起高度采 用0.5mm,如果凸起高度用0.5mm以下的话,外壳喷粉之后会其字形及图案就 会模糊不清。 2.9、表面质量 2.9.1 压铸面 铝合金压铸表面粗糙度在Ra3.2~6.3, 表面质量按粗糙度分为3级,详细见表:压铸 表面质量分级 , 表面缺陷 压铸件各类表面缺陷不同级别的要求见表:面缺陷要求(JB2702-80)
二、压铸件设计
1、术语和定语 流痕:指铸件表面与金属液流动方向一致且与金属基体颜色不一样的纹路。 冷隔:指铸件表面有与周边熔接不良的小块。 铬化:指铸件与铬酸溶液发生化学反应,在铸件表面形成一层薄的铬酸盐膜。 欠铸:指铸件成形不饱满。 网状毛刺:压铸件表面上有网状发丝一样凸起或凹陷的痕迹。 溢流口:指金属液冷却凝固时为补偿金属收缩所设置的穴。 2、铸件设计及工艺 2.1、选材 铝合金压铸件的常用材料有:日本工业标准牌号ADC1,ADC3,ADC10,和ADC12;美国 工业标准牌号:A360和A380;我国标准:YL102,YL104,YL112和YL113,对于我司来讲, 压铸件的选材统一要求为ADC12,珠三角压铸厂商常用材料为 ADC10,ADC12和A380 . 以上几种材料的成份和力学性能见表<1>
注塑件和压铸件的报价简便方法

压铸件、注塑件的简便报价方法一、压铸件160T压铸件含税价格=〔压铸件重量×1.05×(3.00+铝合金含税价/1.17)+(1~1.3)×1.2/0.8~0.9+n(0.5~1.0)〕×1.17其中:3.00为每KG的熔解费;(1~1.3)为模具的复杂程度;n为抽芯个数;(0.5~1.0)为抽芯单价;280T压铸件含税价格=〔压铸件重量×1.05×(3.00+铝合金含税价/1.17)+(1~1.3)×3.0/0.8~0.9+n(0.5~1.0)〕×1.17其中:3.00为每KG的熔解费;(1~1.3)为模具的复杂程度;n为抽芯个数;(0.6~1.0)为抽芯单价;400T压铸件含税价格=〔压铸件重量×1.05×(3.00+铝合金含税价/1.17)+(1~1.3)×5.4/0.8~0.9+n(0.7~1.0)〕×1.17其中:3.00为每KG的熔解费;(1~1.3)为模具的复杂程度;n为抽芯个数;(0.7~1.0)为抽芯单价;800T压铸件含税价格=〔压铸件重量×1.05×(3.00+铝合金含税价/1.17)+(1~1.3)×10/0.8~0.9+n(0.8~1.2)〕×1.17其中:3.00为每KG的熔解费;(1~1.3)为模具的复杂程度;n为抽芯个数;(0.8~1.2)为抽芯单价;1600T压铸件含税价格=〔压铸件重量×1.05×(3.00+铝合金含税价/1.17)+(1~1.4)×22/0.8~0.9+n(0.8~1.2)〕×1.17其中:3.00为每KG的熔解费;(1~1.3)为模具的复杂程度;n为抽芯个数;(0.8~1.2)为抽芯单价;二、注塑件注塑件含税价格=〔注塑件单件重量×穴数×1.03×材料含税价/1.17)+(1~1.3)×m/0.8~0.9+热流道的每模的电费〕×1.17。
压铸与注塑的区别
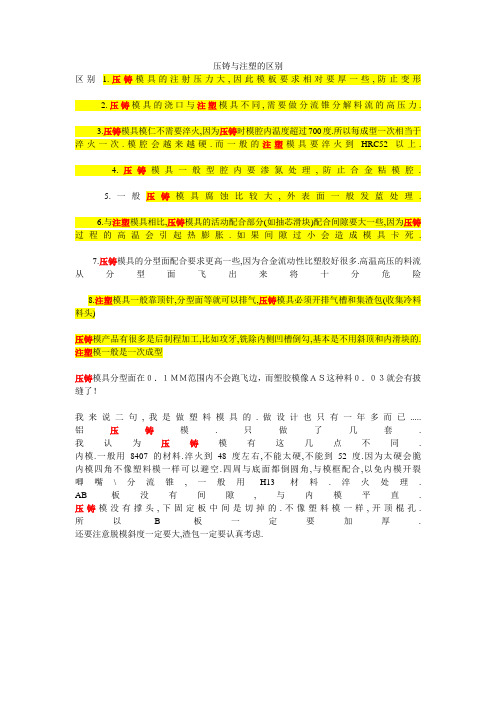
压铸与注塑的区别区别 1.压铸模具的注射压力大,因此模板要求相对要厚一些,防止变形2.压铸模具的浇口与注塑模具不同,需要做分流锥分解料流的高压力.3.压铸模具模仁不需要淬火,因为压铸时模腔内温度超过700度.所以每成型一次相当于淬火一次.模腔会越来越硬.而一般的注塑模具要淬火到HRC52以上.4.压铸模具一般型腔内要渗氮处理,防止合金粘模腔.5.一般压铸模具腐蚀比较大,外表面一般发蓝处理.6.与注塑模具相比,压铸模具的活动配合部分(如抽芯滑块)配合间隙要大一些,因为压铸过程的高温会引起热膨胀.如果间隙过小会造成模具卡死.7.压铸模具的分型面配合要求更高一些,因为合金流动性比塑胶好很多.高温高压的料流从分型面飞出来将十分危险8.注塑模具一般靠顶针,分型面等就可以排气,压铸模具必须开排气槽和集渣包(收集冷料料头)压铸模产品有很多是后制程加工,比如攻牙,铣除内侧凹槽倒勾,基本是不用斜顶和内滑块的. 注塑模一般是一次成型压铸模具分型面在0.1MM范围内不会跑飞边,而塑胶模像AS这种料0.03就会有披缝了!我来说二句,我是做塑料模具的.做设计也只有一年多而已..... 铝压铸模.只做了几套. 我认为压铸模有这几点不同. 内模.一般用8407的材料.淬火到48度左右,不能太硬,不能到52度.因为太硬会脆内模四角不像塑料模一样可以避空.四周与底面都倒圆角,与模框配合,以免内模开裂唧嘴\分流锥,一般用H13材料.淬火处理. AB板没有间隙,与内模平直. 压铸模没有撑头,下固定板中间是切掉的.不像塑料模一样,开顶棍孔. 所以B板一定要加厚. 还要注意脱模斜度一定要大,渣包一定要认真考虑.注塑机和压铸机到底有什么区别?其实注塑机又名注射成型机或注射机。
它是将热塑性塑料或热固性塑料利用塑料成型模具制成各种形状的塑料制品的主要成型设备。
分为立式、卧式、全电式。
而压铸机却是,在压力作用下把熔融金属液压射到模具中冷却成型,开模后得到固体金属铸件的一系列工业铸造机械,最初用于压铸铅字。
压铸模知识点

铝合金压铸件的结构设计经验1。
考虑壁厚的问题,厚度的差距过大会对填充带来影响2。
考虑脱模问题,这点在压铸实际中非常重要,现实中往往回出现这样的问题,这比注塑脱模讨厌多了,所以拔模斜度的设置和动定模脱模力的计算要注意些,一般拔模斜度为1到3度,通常考虑到脱模的顺利性,外拔模要比内拔模的斜度要小些,外拔模也就1度,而内拔模要2~3度左右3。
设计时考虑到模具设计的问题,如果有多个位置的抽心位,尽量的放两边,最好不要放在下位抽心,这样时间长了下抽心会容易出问题4。
有些压铸件外观可能会有特殊的要求,如喷油、喷粉等,这时就要时结构避开重要外观位置便于设置浇口溢流槽5。
在结构上尽量的避免出现导致模具结构复杂的结构出现,如,不得不使用多个抽心或螺旋抽心等6。
对于需进行表面加工的零件,注意,需要在零件设计时给适合的加工留量,不能太多,否则加工人员会骂你的,而且会把里面的气孔都暴露出来的,不能太少,否则粗精定位一加工,得,黑皮还没干掉,你就等再在模具上打火花了,那给多少呢,留量最好不要大于0。
8mm,这样加工出来的面基本看不到气孔的,因为有硬质层的保护。
7。
再有就是注意选料了,是用ADC12还是A380等,要看具体的要求了8。
铝合金没有弹性,要做扣位只有和塑料配合。
9。
一般不能做深孔!在开模具时只做点孔,然后在后加工!10。
如果是薄壁零件与不能太薄,而且一定要用加强肋,增加抗弯能力!由于铝铸件的温度要在800摄氏度左右!模具寿命一般比较短一般做如电机外壳的话只有80K左右就再见了!1.压铸件的设计与塑胶件的设计比较相似,塑胶件的一些设计常规也适用于压铸件。
2.对于铝合金,模具所受温度和压力比塑胶的大很多,对设计的正确性要求特严。
即使很好的模具材料,一旦有焊接,模具就几乎无寿命可言。
锌合金跟塑胶差不多,模具寿命较好。
3.不能有凹的尖角,避免模具崩角。
4.压铸件的精度虽然比较高,但比塑胶差,而且拔模力比塑胶大,通常结构不能太复杂,必要时应将复杂的零件分解成两件或多件。
运用UGNX设计压铸模具

运用UGNX 设计压铸模具赵婉芳天津海运职业学院,天津300350)摘要:尝试运用U G N X 欠件设计压铸模具,由于UG 软件没有单独开发压铸模具设计模块,经过对压铸模具和注塑模具异同的分析,文中在设计中使用M od W i a d F e a tu e n F e a tu e O p e a tO rE •个模块完成设计。
关键词:U G N X 压铸模具设计中图分类号:TP 391.7 文献标志码:A 文章编号:1002-2333(2016)07-0109-02引言模具是用来成型产品的工具,这种工具由各种零件 构成,不同的模具由不同的零件构成。
它主要通过改变所 成型材料的物理状态来实现物品外形的加工,正是有了 模具才使得大规模工业化生产成为现实,模具素有“工业 之母”的称号。
工业领域内常用的模具种类有注塑模具、 吹塑模具、挤出模具、冲压模具、压铸模具、锻压模具等, 其中注塑模具、吹塑模具、挤出模具主要加工非金属材 料,冲压模具、压铸模具、锻压模具主要加工金属材料。
得益于计算机技术和软件行业的发展,目前模具设 计多采用计算机辅助设计来完成,行业内比较流行的设 计软件有廿0、〇爪、匚人丁认、人站‘人0等。
虽然各种模具 都有其工艺特性,但不同的模具种类之间也是有很多共 性的,在设计中可以互相借鉴设计经验。
UG 软件为模具 设计技术人员开发了针对注塑模具设计的Mold Wizard 模 块和针对冲压模具设计的Progressive Die Wizard 模块,但 对于其他种类的模具则没有对应的模块。
鉴于压铸模具 和注塑模具的成型原理类似,我们可以尝试用UG 软件现 有的功能实现压铸模具设计。
1压铸模具与注塑模具的异同 1.1压铸模具与注塑模具相同之处1)成型原理。
压铸模具与注塑模具成型原理类似,都是将液态材料注人模具,待材料冷却凝固后即得到所需 形状的产品。
由于热胀冷缩的作用,因此在模具设计中都 需要考虑材料收缩率和脱模斜度的问题,压铸模具的收 缩率和脱模斜度比注塑模具都要大一些。
浇铸与压铸的优缺点是什么
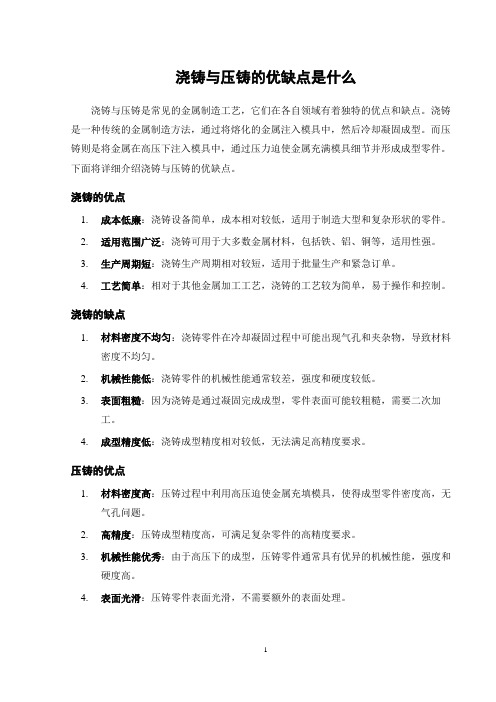
浇铸与压铸的优缺点是什么浇铸与压铸是常见的金属制造工艺,它们在各自领域有着独特的优点和缺点。
浇铸是一种传统的金属制造方法,通过将熔化的金属注入模具中,然后冷却凝固成型。
而压铸则是将金属在高压下注入模具中,通过压力迫使金属充满模具细节并形成成型零件。
下面将详细介绍浇铸与压铸的优缺点。
浇铸的优点1.成本低廉:浇铸设备简单,成本相对较低,适用于制造大型和复杂形状的零件。
2.适用范围广泛:浇铸可用于大多数金属材料,包括铁、铝、铜等,适用性强。
3.生产周期短:浇铸生产周期相对较短,适用于批量生产和紧急订单。
4.工艺简单:相对于其他金属加工工艺,浇铸的工艺较为简单,易于操作和控制。
浇铸的缺点1.材料密度不均匀:浇铸零件在冷却凝固过程中可能出现气孔和夹杂物,导致材料密度不均匀。
2.机械性能低:浇铸零件的机械性能通常较差,强度和硬度较低。
3.表面粗糙:因为浇铸是通过凝固完成成型,零件表面可能较粗糙,需要二次加工。
4.成型精度低:浇铸成型精度相对较低,无法满足高精度要求。
压铸的优点1.材料密度高:压铸过程中利用高压迫使金属充填模具,使得成型零件密度高,无气孔问题。
2.高精度:压铸成型精度高,可满足复杂零件的高精度要求。
3.机械性能优秀:由于高压下的成型,压铸零件通常具有优异的机械性能,强度和硬度高。
4.表面光滑:压铸零件表面光滑,不需要额外的表面处理。
压铸的缺点1.设备复杂:压铸设备相对复杂,投资成本高,需要专业技术人员进行操作和维护。
2.能耗较大:高压和高温需要消耗大量能量,能源消耗相对较大。
3.限制材料选择:压铸对原材料的要求较高,适用范围较窄。
4.生产周期长:相比浇铸,压铸生产周期相对较长。
综上所述,浇铸和压铸各有优缺点,应根据具体生产需求和零件要求选择合适的制造工艺。
浇铸适用于成本低廉、生产周期短的批量生产,而压铸则适用于要求高精度、优异机械性能的零件制造。
在实际应用中,可以根据具体情况综合考虑各方面因素,选择最适合的制造工艺,以提高生产效率和产品质量。
浇铸与压铸的优缺点
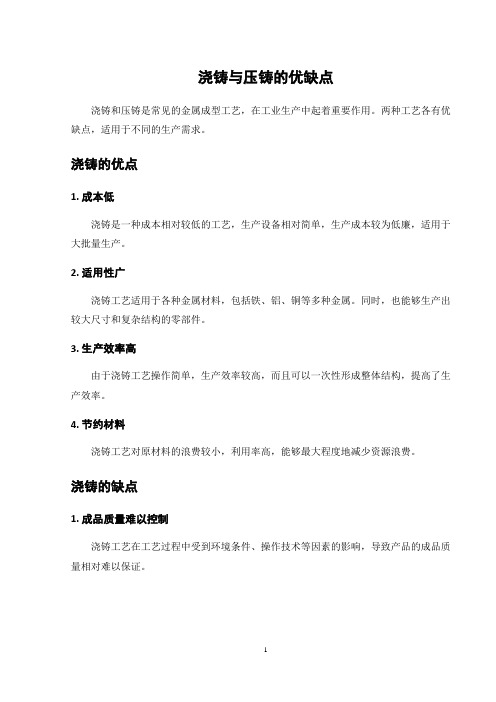
浇铸与压铸的优缺点浇铸和压铸是常见的金属成型工艺,在工业生产中起着重要作用。
两种工艺各有优缺点,适用于不同的生产需求。
浇铸的优点1. 成本低浇铸是一种成本相对较低的工艺,生产设备相对简单,生产成本较为低廉,适用于大批量生产。
2. 适用性广浇铸工艺适用于各种金属材料,包括铁、铝、铜等多种金属。
同时,也能够生产出较大尺寸和复杂结构的零部件。
3. 生产效率高由于浇铸工艺操作简单,生产效率较高,而且可以一次性形成整体结构,提高了生产效率。
4. 节约材料浇铸工艺对原材料的浪费较小,利用率高,能够最大程度地减少资源浪费。
浇铸的缺点1. 成品质量难以控制浇铸工艺在工艺过程中受到环境条件、操作技术等因素的影响,导致产品的成品质量相对难以保证。
2. 材料性能不稳定浇铸工艺生产的产品,由于冷却速度等因素的影响,材料的性能可能存在一定的不稳定性。
3. 需要后续加工由于浇铸工艺制造的产品表面粗糙,需要经过后续的加工处理,增加了生产成本和时间。
压铸的优点1. 高精度压铸工艺能够生产出形状复杂、精度高的零部件,满足高精度要求的生产需求。
2. 高强度通过压铸工艺生产的产品密度高,结构致密,具有较高的强度和硬度。
3. 表面质量好压铸工艺制造的产品表面光滑,无气孔、夹杂等缺陷,无需经过复杂的后续加工,节约了时间和成本。
压铸的缺点1. 成本较高相比于浇铸工艺,压铸工艺需要较为复杂的设备和工艺流程,导致生产成本较高。
2. 适用性较窄压铸工艺对原材料要求较高,通常只适用于铝合金、锌合金等低熔点金属,对于高熔点金属的加工不太适用。
3. 生产周期长由于压铸工艺的工艺复杂,生产周期相对较长,不适合大批量、高效率的生产需求。
综上所述,浇铸工艺适用于大批量生产、成本敏感的情况,而压铸工艺则更适合对产品精度、表面质量和强度有较高要求的生产场景。
在实际生产中,选择合适的工艺可以有效提高生产效率、降低成本,满足不同产品的需求。
压铸与注塑的区别
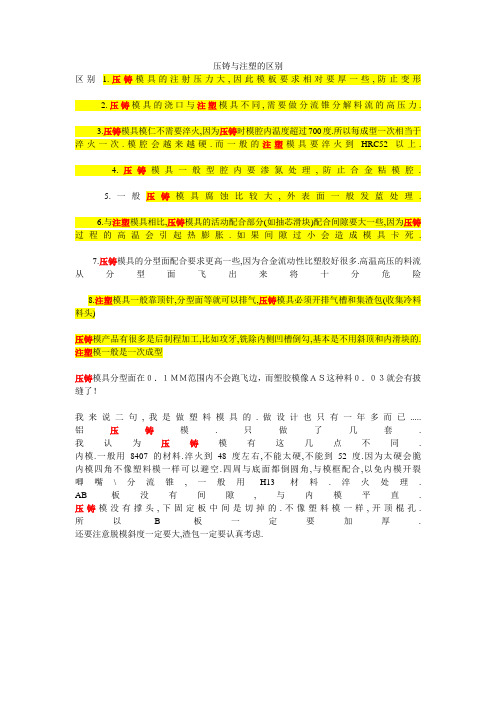
压铸与注塑的区别区别 1.压铸模具的注射压力大,因此模板要求相对要厚一些,防止变形2.压铸模具的浇口与注塑模具不同,需要做分流锥分解料流的高压力.3.压铸模具模仁不需要淬火,因为压铸时模腔内温度超过700度.所以每成型一次相当于淬火一次.模腔会越来越硬.而一般的注塑模具要淬火到HRC52以上.4.压铸模具一般型腔内要渗氮处理,防止合金粘模腔.5.一般压铸模具腐蚀比较大,外表面一般发蓝处理.6.与注塑模具相比,压铸模具的活动配合部分(如抽芯滑块)配合间隙要大一些,因为压铸过程的高温会引起热膨胀.如果间隙过小会造成模具卡死.7.压铸模具的分型面配合要求更高一些,因为合金流动性比塑胶好很多.高温高压的料流从分型面飞出来将十分危险8.注塑模具一般靠顶针,分型面等就可以排气,压铸模具必须开排气槽和集渣包(收集冷料料头)压铸模产品有很多是后制程加工,比如攻牙,铣除内侧凹槽倒勾,基本是不用斜顶和内滑块的. 注塑模一般是一次成型压铸模具分型面在0.1MM范围内不会跑飞边,而塑胶模像AS这种料0.03就会有披缝了!我来说二句,我是做塑料模具的.做设计也只有一年多而已..... 铝压铸模.只做了几套. 我认为压铸模有这几点不同. 内模.一般用8407的材料.淬火到48度左右,不能太硬,不能到52度.因为太硬会脆内模四角不像塑料模一样可以避空.四周与底面都倒圆角,与模框配合,以免内模开裂唧嘴\分流锥,一般用H13材料.淬火处理. AB板没有间隙,与内模平直. 压铸模没有撑头,下固定板中间是切掉的.不像塑料模一样,开顶棍孔. 所以B板一定要加厚. 还要注意脱模斜度一定要大,渣包一定要认真考虑.注塑机和压铸机到底有什么区别?其实注塑机又名注射成型机或注射机。
它是将热塑性塑料或热固性塑料利用塑料成型模具制成各种形状的塑料制品的主要成型设备。
分为立式、卧式、全电式。
而压铸机却是,在压力作用下把熔融金属液压射到模具中冷却成型,开模后得到固体金属铸件的一系列工业铸造机械,最初用于压铸铅字。
玻璃浇铸成型和压铸

玻璃浇铸成型和压铸在现代工业生产中,玻璃是一种常用的材料,广泛应用于建筑、家居用品、仪器仪表等领域。
玻璃制品的生产过程中,玻璃浇铸成型和压铸是两种常见的加工方式,它们各具特点,在不同场合下得到广泛应用。
玻璃浇铸成型玻璃浇铸成型是一种将玻璃熔化后注入模具中自然冷却成型的加工方式。
这种方式适用于需要制造复杂形状、高精度的玻璃制品,如各种玻璃器皿、光学玻璃等。
玻璃浇铸成型的工艺流程相对简单,主要包括原料准备、玻璃熔化、模具注入和冷却固化等步骤。
玻璃浇铸成型的优点在于可以生产出表面光滑、结构坚固的玻璃制品,同时能够实现批量生产,提高生产效率。
此外,通过浇铸成型还可以实现玻璃内部的空腔结构和多层结构,满足不同工业领域的需求。
然而,玻璃浇铸成型也存在一些局限性,例如成本较高、易受环境温度影响、模具寿命短等缺点。
因此,在实际应用中需要根据具体情况进行选择,权衡各方面因素。
玻璃压铸玻璃压铸是一种将玻璃颗粒或粉末加热至熔化状态后,在高压下注入模具中成型的加工方式。
与浇铸成型相比,压铸更适用于生产小型、复杂、高精度的玻璃制品,如玻璃光纤、微型透镜等。
玻璃压铸的工艺流程包括原料预处理、加热熔化、注入模具、施加压力、冷却凝固等环节。
在压铸过程中,通过控制温度、压力和注入速度等参数,可以实现对玻璃制品形状和性能的精确控制。
相比而言,玻璃压铸具有生产效率高、制品质量稳定、成本较低等优点。
同时,压铸成型可以避免浇铸过程中的气泡和缺陷,保证制品的表面质量。
但需要注意的是,压铸过程对模具要求较高,需要使用耐高温高压的特殊模具。
结语玻璃浇铸成型和压铸是两种常见的玻璃加工方式,各有特点适用于不同场合。
通过灵活运用这两种加工方式,可以满足市场对于玻璃制品的多样化需求,推动玻璃工业的发展。
在实际生产中,选择合适的加工方式,并不断优化工艺流程,将有助于提高制品质量、降低成本,取得更好的经济效益。
浇铸跟压铸优点跟缺点

浇铸跟压铸优点跟缺点在金属加工领域,浇铸和压铸是两种常见的工艺方式,它们在制造业中起着重要的作用。
浇铸是通过将熔化的金属注入模具中,使其凝固成型的过程,而压铸则是将熔化的金属注入高压模具中,通过高压快速冷却凝固成型。
每种工艺都有其独特的优点和缺点,下面将分别列举浇铸和压铸的优点和缺点。
浇铸的优点:1.成本较低:浇铸生产工艺简单,模具制作相对较为容易,因此成本相对较低。
2.适用范围广:浇铸适用于各种各样的金属,形状复杂的零部件也可以通过浇铸来制造。
3.成型精度高:浇铸能够制作出尺寸精度高的零部件,适用于一些对精度要求较高的场合。
4.抗拉强度高:由于浇铸金属在凝固过程中晶粒较大,因此具有较高的抗拉强度。
浇铸的缺点:1.生产周期长:浇铸生产周期相对较长,需要等待金属充分凝固才能取模,因此生产效率较低。
2.金属浪费:由于浇铸会产生浇口、飞边等废料,容易造成金属浪费。
3.内部缺陷:浇铸过程中,易受到气泡、杂质等内部缺陷的影响,影响零件的质量。
压铸的优点:1.生产效率高:压铸采用高压快速冷却的工艺,生产效率较高,适用于大规模生产。
2.精度和表面质量好:压铸零件表面光滑平整,尺寸稳定性好,适用于需要高精度的零件生产。
3.可降低后续加工工艺:压铸的零件通常不需要进行太多后续加工,省去了一些环节,降低了生产成本。
4.可控制金属组织:压铸过程中金属流动受控,可获得相对均匀的组织结构。
压铸的缺点:1.成本较高:压铸所需设备成本较高,对模具的要求也较高,因此初始投资较大。
2.适用性受限:压铸一般适用于低熔点合金或者某些特定金属,不适用于所有金属。
3.设备维护难度大:压铸设备受压力和高温影响较大,日常维护难度较大。
4.可制造尺寸有限:压铸通常适用于较小尺寸的零件,对于大型零件的制造受限。
综上所述,浇铸和压铸各有其优点和缺点,制造企业在选择合适的工艺方式时,需要根据实际情况综合考虑,以达到最佳的生产效果和经济效益。
非电力家用器具零件的制造工艺和生产流程
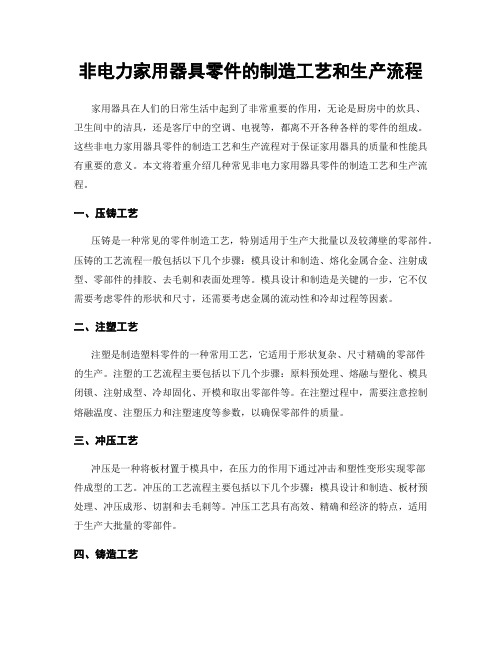
非电力家用器具零件的制造工艺和生产流程家用器具在人们的日常生活中起到了非常重要的作用,无论是厨房中的炊具、卫生间中的洁具,还是客厅中的空调、电视等,都离不开各种各样的零件的组成。
这些非电力家用器具零件的制造工艺和生产流程对于保证家用器具的质量和性能具有重要的意义。
本文将着重介绍几种常见非电力家用器具零件的制造工艺和生产流程。
一、压铸工艺压铸是一种常见的零件制造工艺,特别适用于生产大批量以及较薄壁的零部件。
压铸的工艺流程一般包括以下几个步骤:模具设计和制造、熔化金属合金、注射成型、零部件的排胶、去毛刺和表面处理等。
模具设计和制造是关键的一步,它不仅需要考虑零件的形状和尺寸,还需要考虑金属的流动性和冷却过程等因素。
二、注塑工艺注塑是制造塑料零件的一种常用工艺,它适用于形状复杂、尺寸精确的零部件的生产。
注塑的工艺流程主要包括以下几个步骤:原料预处理、熔融与塑化、模具闭锁、注射成型、冷却固化、开模和取出零部件等。
在注塑过程中,需要注意控制熔融温度、注塑压力和注塑速度等参数,以确保零部件的质量。
三、冲压工艺冲压是一种将板材置于模具中,在压力的作用下通过冲击和塑性变形实现零部件成型的工艺。
冲压的工艺流程主要包括以下几个步骤:模具设计和制造、板材预处理、冲压成形、切割和去毛刺等。
冲压工艺具有高效、精确和经济的特点,适用于生产大批量的零部件。
四、铸造工艺铸造是一种将熔融金属或合金注入到模具中,通过冷却凝固而得到零部件的工艺。
铸造工艺的流程主要包括以下几个步骤:模具设计和制造、熔化金属或合金、充型、凝固冷却、取模和去毛刺等。
铸造工艺适用于生产大尺寸、复杂形状以及需要高强度和耐磨性的零部件。
五、加工工艺加工工艺是指通过精密的机械设备对零部件进行形状、尺寸和表面处理的工艺。
常见的加工工艺包括车削、铣削、钻孔、磨削等。
在加工过程中,需要考虑操作者的技术水平、设备的精度和刀具的选择等因素,以确保零部件的质量和精度。
以上是几种常见的非电力家用器具零件制造工艺和生产流程的简要介绍。
注射与压铸模区别

塑胶模具与压铸模区别塑胶模具与压铸模区别2009-05-27 21:021.压铸模具的注射压力大,因此模板要求相对要厚一些,防止变形2.压铸模具的浇口与注塑模具不同,需要做分流锥分解料流的高压力3.压铸模具模仁不需要淬火,因为压铸时模腔内温度超过700度.所以每成型一次相当于淬火一次.模腔会越来越硬.而一般的注塑模具要淬火到HRC52以上.4.压铸模具一般型腔内要渗氮处理,防止合金粘模腔.5.一般压铸模具腐蚀比较大,外表面一般发蓝处理.6.与注塑模具相比,压铸模具的活动配合部分(如抽芯滑块)配合间隙要大一些,因为压铸过程的高温会引起热膨胀.如果间隙过小会造成模具卡死.7.压铸模具的分型面配合要求更高一些,因为合金流动性比塑胶好很多.高温高压的料流从分型面飞出来将十分危险8.注塑模具一般靠顶针,分型面等就可以排气,压铸模具必须开排气槽和集渣包(收集冷料料头);9成型不一致,压铸模注射速度快,一段注射压力.塑胶模具通常分几段注射,保压.10.压铸模具为两板模(我暂时没见过3板压铸模)一次开模,塑胶模不同的产品结构不一样3板模常见,开模次数及顺序与模具结构相配合.我司压铸模具通常不采用方顶针,司筒,斜销(高温及溶液流动性好)易卡死导致模具生产不稳定.第一浇道不一样,压铸模流道比较宽,进料GATE面积要根据产品大小重量来计算,一般GATE 尽量宽厚度不要超过产品肉厚(75%就可以了),压铸模进料方式只有一种不象塑胶模可以用点进胶,潜胶口(或潜顶针),牛角尖进料,大水口直接进料。
第二因为压铸温度高(670度左右),对模具材料跟冷却要求更高,材料要用热做刚8407,DAC55,SKD61等等(模仁,滑块,公母灌嘴),模仁冷却要平衡均匀,流道部分要走冷却,公母灌嘴,公母模板也要冷却。
第三,模具拆模尽量简单(要考虑毛边的长出方向方便后处理,分型面要考虑排气,尽量跟模面平,模板上磨排气(0.15MM左右),要加溢料,比较难成型的产品还要加抽真空。
三种液态成形方法
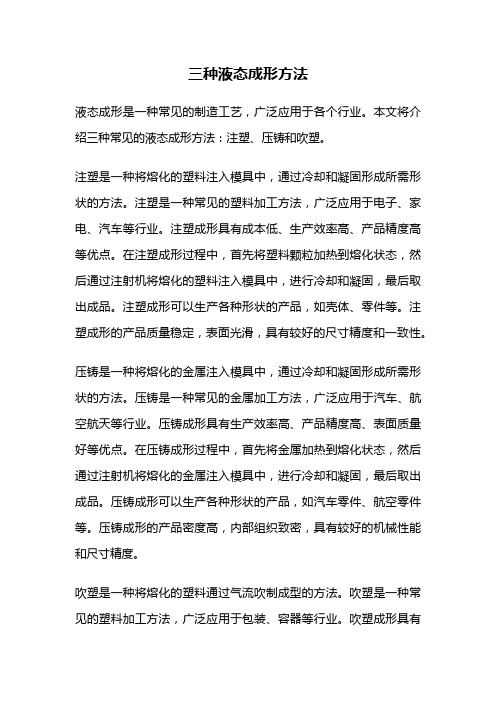
三种液态成形方法液态成形是一种常见的制造工艺,广泛应用于各个行业。
本文将介绍三种常见的液态成形方法:注塑、压铸和吹塑。
注塑是一种将熔化的塑料注入模具中,通过冷却和凝固形成所需形状的方法。
注塑是一种常见的塑料加工方法,广泛应用于电子、家电、汽车等行业。
注塑成形具有成本低、生产效率高、产品精度高等优点。
在注塑成形过程中,首先将塑料颗粒加热到熔化状态,然后通过注射机将熔化的塑料注入模具中,进行冷却和凝固,最后取出成品。
注塑成形可以生产各种形状的产品,如壳体、零件等。
注塑成形的产品质量稳定,表面光滑,具有较好的尺寸精度和一致性。
压铸是一种将熔化的金属注入模具中,通过冷却和凝固形成所需形状的方法。
压铸是一种常见的金属加工方法,广泛应用于汽车、航空航天等行业。
压铸成形具有生产效率高、产品精度高、表面质量好等优点。
在压铸成形过程中,首先将金属加热到熔化状态,然后通过注射机将熔化的金属注入模具中,进行冷却和凝固,最后取出成品。
压铸成形可以生产各种形状的产品,如汽车零件、航空零件等。
压铸成形的产品密度高,内部组织致密,具有较好的机械性能和尺寸精度。
吹塑是一种将熔化的塑料通过气流吹制成型的方法。
吹塑是一种常见的塑料加工方法,广泛应用于包装、容器等行业。
吹塑成形具有生产效率高、产品质量好、成本低等优点。
在吹塑成形过程中,首先将塑料颗粒加热到熔化状态,然后将熔化的塑料注入吹塑机中,通过气流吹制成型,最后取出成品。
吹塑成形可以生产各种形状的产品,如瓶子、容器等。
吹塑成形的产品具有一定的韧性和透明度,可以满足不同行业的需求。
以上三种液态成形方法在工业生产中得到广泛应用,为各行各业提供了丰富的产品。
注塑、压铸和吹塑成形方法各有特点,适用于不同的材料和产品。
在实际应用中,需要根据具体情况选择合适的成形方法,以满足产品的需求。
液态成形技术的不断发展和创新,将为制造业带来更多的机遇和挑战,推动行业的进步和发展。
注塑模和压铸模区别

注塑模和压铸模区别⼀:注塑模和压铸模区别:在这⾥我们先⼤概地讲⼀下,注塑模和压铸模基本区别在于材料地不⼀样,⼀种是塑胶,⼀种是合⾦,所以压铸模要承受⽐塑胶模⼤地多地压⼒和温度,模具地结构需要强化,进料地⽅式,流道,冷却设计都不⼀样.以下压铸模和注塑模模具钢材均称为热作模具钢.在下⾯地⽂章我们主要以压铸模为讲解,其注塑模地详细相关我们将在下⼀篇⽂章做讲解.压铸模地结构组成:⼀).压铸模结构组成定模:固定在压铸机定模安装板上,有直浇道与喷嘴或压室联接动模:固定在压铸机动模安装板上,并随动模安装板作开合模移动合模时,闭合构成型腔与浇铸系统,液体⾦属在⾼压下充满型腔;开模时,动模与定模分开,借助于设在动模上地推出机构将铸件推出.⼆).压铸模结构根据作⽤分类型腔:外表⾯直浇道(浇⼝套)成型零件浇注系统模浇道(镶块)型芯:内表⾯内浇⼝余料三)导准零件:导柱;导套四)推出机构:推杆(顶针),复位杆,推杆固定板,推板,推板导柱,推板导套.五)侧向抽芯机构:凸台;孔⽳(侧⾯),锲紧块,限位弹簧,螺杆.六)排溢系统:溢浇槽,排⽓槽.七)冷却系统⼋)⽀承零件:定模;动模座板,垫块(装配,定位,安装作⽤)压铸模采购选择信誉好、技术⾼、经验丰富地专业压铸模具⼚制造模具.压铸模是⼀种特殊地精密机械,那些专业压铸模具⼚,他们有适合⽣产压铸模具地精密机床,能确保模具尺⼨精度;他们有经验丰富地⾼级模具技师,技师地丰富经验是压铸模具实⽤好⽤地保证;他们与材料供应商和热处理⼚有密切地关系,他们有完善地售后服务体系…….良好地模具设计与制造是压铸模具长寿命、低故障、⾼效率地基础.低价位地劣质压铸模,将会以压铸⽣产中表现出地低⽣产效率、⾼故障,让您浪费很多昂贵地压铸⼯时,花去更多地⾦钱.压铸模安装模具安装调整⼯应经过培训合格上岗⑴、模具安装位置符合设计要求,尽可能使模具涨型⼒中⼼与压铸机距离最⼩,这样可能使压铸机⼤杠受⼒⽐较均匀.⑵、经常检查模具起重吊环螺栓、螺孔和起重设备是否完好,确保重吊时⼈⾝、设备、模具安全.⑶、定期检查压铸机⼤杠受⼒误差,必要时进⾏调整.⑷、安装模具前彻底擦净机器安装⾯和模具安装⾯.检查所⽤顶杆长度是否适当,所有顶棒长度是否等长,所⽤顶棒数量应不少于四个,并放在规定地顶棒孔内.⑸、压板和压板螺栓应有⾜够地强度和精度,避免在使⽤中松动.压板数量应⾜够多,最好四⾯压紧,每⾯不少于两处.⑹、⼤型模具应有模具托架,避免在使⽤中模具下沉错位或坠落.⑺、带较⼤抽芯地模具或需要复位地模具也可能需要动、定模分开安装.⑻、冷却⽔管和安装应保证密封.⑼、模具安装后地调整.调整合模紧度.调整压射参数:快压射速度、压射压⼒、增压压⼒、慢压射⾏程、快压射⾏程、冲头跟出距离、推出⾏程、推出复位时间等.调整后在压室内放⼊棉丝等软物,做两次模拟压射全过程,检查调整是否适当.⑽、调整合模到动、定模有适当地距离,停⽌机器运⾏,放⼊模具预热器.⑾、把保温炉设定在规定温度,配置好规定容量地舀料勺.压铸模地正确使⽤制定正确地压铸⼯艺,压铸⼯正确熟练地操作和⾼质量地模具维修,对提⾼⽣产效率,保证压铸件质量,降低废品率,减少模具故障,延长模具寿命致关重要.(⼀)制定正确地压铸⼯艺压铸⼯艺是⼀个压铸⼯⼚技术⽔平地体现,他能把压铸机特性、模具特性、铸件特性、压铸合⾦特性等⽣产要素正确地结合起来,以最低地成本,⽣产满⾜客户要求地压铸产品.因此,必须重视压铸⼯艺⼯程师地选拔和培训.压铸⼯艺⼯程师是压铸⽣产现场技术总负责⼈,除制定正确地压铸⼯艺,根据⽣产要素变化及时修订压铸⼯艺外,还负责对模具安装调整⼯、压铸操作⼯、模具维修⼯地培训和提⾼.⑴、确定最合理地⽣产率,规定每⼀次压射周期地循环时间.过低地⽣产率固然不利于提⾼经济效益,过⾼地⽣产率往往以牺牲模具寿命和铸件合格率为代价,算总帐细帐经济益可能更差.⑵、确定正确地压铸参数.在确保铸件符合客户质量标准地前提下,应使压射速度、压射压⼒、合⾦温度最低.这样,有利于降低机器、模具负荷,降低故障,提⾼寿命.根据压铸机特性、模具特性、铸件特性、压铸铝合⾦特性等腰三⾓形,确定快压射速度、压射压⼒、增压压⼒、慢压射⾏程、快压射⾏程、冲头跟出距离、推出⾏程、保压时间、推了复位时间、合⾦温度、模具温度等.⑶、使⽤⽔基涂料,必须制订严格详细地喷涂⼯艺.涂料品牌,涂料与⽔地⽐例,模具每⼀个部位地喷涂量(或喷涂时间)和喷涂顺序,压缩空⽓压⼒,喷枪与成型表⾯地距离,喷涂⽅向与成型表⾯地⾓度等.⑷、根据压铸模实际确定正确地模具冷却⽅案.正确地模具冷却⽅案对⽣产效率、铸件质量、模具寿命有极⼤地影响.⽅案应规定冷却⽔开户⽅法,压铸⼏个模次开始冷却,相隔⼏个模次分⼏次把冷却⽔阀门开到规定开度.点冷却系统地冷却强度应由压铸⼯艺⼯程师现场调定,配合喷涂达到模具热平衡.⑸、规定对不同滑动动部位,如冲头、导柱、导套、抽芯机构、推杆、复位杆等部位地不同润滑频率.⑹、制订每⼀个压铸件地压铸操作规程,并培训和监督压铸⼯按规程操作.⑺、根据模具复杂程度和新旧程度,确定适当地模具预防性维修周期.适当地模具预防性维修周期应当是模具使⽤中将要出现故障⽽还没有出现故障地压铸模次.模具使⽤中已经出现故障,不能继续⽣产,被迫进⾏修理,不是被提倡地⽅法.⑻、根据模具复杂程度、新旧程度和粘模危险程度,确定模块消除应⼒周期(⼀般—模次进⾏⼀次)和是否需要进⾏表⾯出理.如氮化处理,氮化层深度.,最⼤.(⼆)实施正确地压铸操作压铸⼯应经过培训合格后上岗⑴、严格执⾏压铸⼯操作规程,严格控制第⼀模次地循环时间,其误差应⼩于.稳定地压铸循环时间,对⼀个铸⼯⼚地综合效益⾄关重要.对产品质量稳定性、模具寿命、故障率等都有决定性影响.⑵、严格执⾏模具冷却⽅案,模具冷却是提⾼⽣产效率、铸件质量、模具寿命,减少模具故障地有效⽅法.但是,错误地⽔冷却操作,将对模具造成致命伤害.停⽌压铸⽣产,必须⽴即关闭冷却⽔.⑶、浇柱撇潭、舀铝、浇柱动作规范,做到舀⼊地⾦属液不含氧化⽪,浇⼊压室地⾦属液最少波动.⼿⼯浇注浇⼊量误差控制在—以内.⑷、清模及时清除积留在分型⾯、型腔、型芯、浇道、溢流槽、排⽓道等处地⾦属肖积垢,防⽌合模时压塌模具表⾯,堵塞排⽓道,或造成合模不严.清模时禁⽌使⽤钢制⼯具接触成型表⾯.⑸、喷涂喷涂是最重要、难度最⼤地压铸操作之⼀,必须严格按喷涂⼯艺操作.不正确地喷涂会使产品质量不稳定和模具早期限损坏.⑹、按规定及时对滑动部位进⾏润滑.⑺、随时注意合模紧度,经常检查模具压板压紧情况和模具托架⽀撑情况,防⽌在使⽤中模具下沉或坠落.⑻、完成⼀个模具维修周期地模次,或完成规定地⽣产批量后停⽌⽣产,要保留最后⼀个压铸产品(最好带浇、排系统),与模具⼀起送修.。
- 1、下载文档前请自行甄别文档内容的完整性,平台不提供额外的编辑、内容补充、找答案等附加服务。
- 2、"仅部分预览"的文档,不可在线预览部分如存在完整性等问题,可反馈申请退款(可完整预览的文档不适用该条件!)。
- 3、如文档侵犯您的权益,请联系客服反馈,我们会尽快为您处理(人工客服工作时间:9:00-18:30)。
压铸与注塑的区别
区别1.压铸模具的注射压力大,因此模板要求相对要厚一些,防止变形
2.压铸模具的浇口与注塑模具不同,需要做分流锥分解料流的高压力.
3.压铸模具模仁不需要淬火,因为压铸时模腔内温度超过700度.所以每成型一次相当于淬火一次.模腔会越来越硬.而一般的注塑模具要淬火到HRC52以上.
4.压铸模具一般型腔内要渗氮处理,防止合金粘模腔.
5.一般压铸模具腐蚀比较大,外表面一般发蓝处理.
6.与注塑模具相比,压铸模具的活动配合部分(如抽芯滑块)配合间隙要大一些,因为压铸过程的高温会引起热膨胀.如果间隙过小会造成模具卡死.
7.压铸模具的分型面配合要求更高一些,因为合金流动性比塑胶好很多.高温高压的料流从分型面飞出来将十分危险
8.注塑模具一般靠顶针,分型面等就可以排气,压铸模具必须开排气槽和集渣包(收集冷料料头)
压铸模产品有很多是后制程加工,比如攻牙,铣除内侧凹槽倒勾,基本是不用斜顶和内滑块的. 注塑模一般是一次成型
压铸模具分型面在0.1MM范围内不会跑飞边,而塑胶模像AS这种料0.03就会有披缝了!
我来说二句,我是做塑料模具的.做设计也只有一年多而已.....
铝压铸模.只做了几套.
我认为压铸模有这几点不同.
内模.一般用8407的材料.淬火到48度左右,不能太硬,不能到52度.因为太硬会脆
内模四角不像塑料模一样可以避空.四周与底面都倒圆角,与模框配合,以免内模开裂
唧嘴\分流锥,一般用H13材料.淬火处理.
AB板没有间隙,与内模平直.
压铸模没有撑头,下固定板中间是切掉的.不像塑料模一样,开顶棍孔.
所以B板一定要加厚.
还要注意脱模斜度一定要大,渣包一定要认真考虑.。