真空压铸和普通压铸方法相比
铝合金压铸用高真空技术的开发与应用

铝合金压铸用高真空技术的开发与应用摘要:压力铸造的特点是高速高压。
在压铸过程中,金属液在进入型腔时难免进入空气,所以压铸件不适合利用热加工来提高力学性能。
高真空压铸工艺可以减少压铸件内气孔,提升压铸件力学性能。
本文介绍的新型高真空压铸用真空截止阀是在传统真空截止阀的一主动一从动两类活塞的结构基础上,通过液体金属冲击主动活塞提供动力,从动活塞封闭气路则由传动机构带动的动作原理。
用杠杆作为传动机构是其特点,它的优点在于可随时调节传动比,可随时开关活塞、既方便又可靠,改变了传统技术存在的设计灵活性差、不可靠的缺陷。
关键词:铝合金压铸技术;高真空技术一、真空压铸法及其工作原理真空压铸法是在型腔保持真空状态的情况下,把金属液填充到型腔的过程,因为卷入的气体少,铸件有较好的力学性能,且真空压铸保留了传统压铸法的优点。
高真空压铸工作原理是在传统压力制造技术的基础上加以对型腔内气体抽出的技术,即利用真空抽取设备将压铸模内压室和型腔内的空气抽出,使金属液体在真空的状态下充填型腔。
在压铸过程中利用真空压铸技术进行铸造,能提高铸件内部结构致密度,消除或明显减少压铸件表面气孔现象,可以有效提升压铸件表面质量,提高铸件的力学性能。
二、真空铝合金压铸法与普通压铸法区别真空铝合金压铸法与普通压铸法相比具有以下特点:(1)减少气孔现象的发生;(2)真空压铸的产品硬度高,微观结构精细;(3)真空铝合金压铸件有更高的力学性能。
三、真空铝合金压铸法的优缺点1、真空铝合金压铸主要以抽除型腔中的空气为主,通常有两种形式:(1)从型腔中直接抽取;(2)把模具放入真空箱中抽气。
利用真空铝合金压铸时,对模具排气道位置和排气道面积的合理设计非常关键。
型腔内抽出的气体量、抽气时长及填充时间影响着排气道的“临界面积”。
当排气道的面积比临界面积大时,铝合金压铸件的效果就好;反之,则不理想。
2、整体而言,真空压铸法具有以下优点:(1)真空压铸法能够让铸件内部的气孔减少或彻底清除,提高压铸件的力学性能和表面质量,改善整体性能;(2)真空压铸法可使型腔内的反压力减少,对合金的要求没有那么严格,甚至用小机器就可以压铸大型铸件;(3)真空压铸法使充填条件得以改变,对较薄的铸件也可压铸;(4)真空压铸法和普通压铸方法相比,生产效率几乎一样。
真空压铸与普通压铸的区别
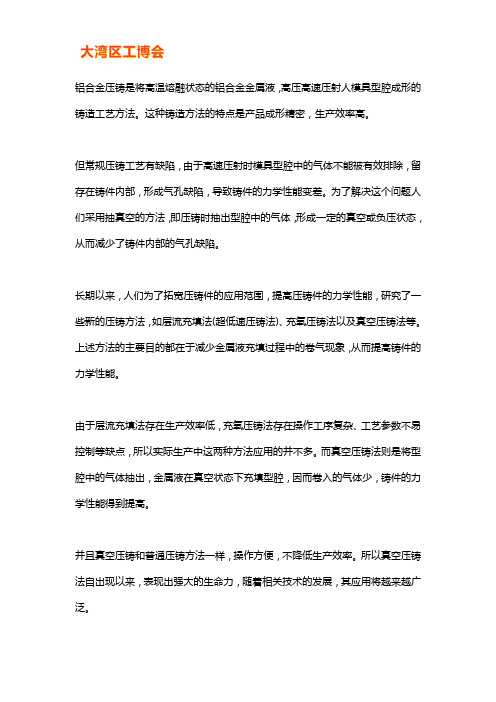
铝合金压铸是将高温熔融状态的铝合金金属液,高压高速压射人模具型腔成形的铸造工艺方法。
这种铸造方法的特点是产品成形精密,生产效率高。
但常规压铸工艺有缺陷,由于高速压射时模具型腔中的气体不能被有效排除,留存在铸件内部,形成气孔缺陷,导致铸件的力学性能变差。
为了解决这个问题人们采用抽真空的方法,即压铸时抽出型腔中的气体,形成一定的真空或负压状态,从而减少了铸件内部的气孔缺陷。
长期以来,人们为了拓宽压铸件的应用范围,提高压铸件的力学性能,研究了一些新的压铸方法,如层流充填法(超低速压铸法)、充氧压铸法以及真空压铸法等。
上述方法的主要目的都在于减少金属液充填过程中的卷气现象,从而提高铸件的力学性能。
由于层流充填法存在生产效率低,充氧压铸法存在操作工序复杂、工艺参数不易控制等缺点,所以实际生产中这两种方法应用的并不多。
而真空压铸法则是将型腔中的气体抽出,金属液在真空状态下充填型腔,因而卷入的气体少,铸件的力学性能得到提高。
并且真空压铸和普通压铸方法一样,操作方便,不降低生产效率。
所以真空压铸法自出现以来,表现出强大的生命力,随着相关技术的发展,其应用将越来越广泛。
高真空压铸技术

高真空压铸技术高真空压铸技术是一种在高度真空环境下进行的压铸工艺,通过减少气体和气体中的氧含量,从而避免合金在凝固时发生气孔、氧化和夹杂,提高了铸件的质量和性能。
高真空压铸技术已在航空航天、汽车、电子等领域广泛应用,得到了行业的认可和推崇。
1. 高真空压铸技术的原理高真空压铸技术是在真空中进行的压铸过程,其核心原理是通过减少氧气和气体对合金的影响,从而得到高质量的铸件。
在高真空环境下,避免了氧化反应和气体的夹杂,确保了合金的纯净度和均匀性。
这种工艺不仅可以有效地提高铸件的机械性能,还可以减少缺陷,提高生产效率。
2. 高真空压铸技术的应用高真空压铸技术已经在许多领域得到了广泛的应用,特别是在一些对铸件质量要求较高的行业中。
航空航天领域的发展需要具有高强度、高耐腐蚀性和高精度的铸件,而高真空压铸技术正是能够满足这些需求的重要工艺之一。
在汽车制造、电子产品、医疗器械等领域,高真空压铸技术也起着重要作用。
3. 高真空压铸技术的优势(1)提高铸件质量:通过减少气体和氧含量,避免了气孔、氧化和夹杂,大大提高了铸件的质量和性能。
(2)节约材料:高真空压铸技术可以减少废品率,降低原材料的浪费,提高了生产效率。
(3)节能减排:相比传统的压铸工艺,高真空压铸技术减少了氧化反应,减少了能源的消耗,符合环保要求。
4. 高真空压铸技术的发展趋势随着科技的不断进步,高真空压铸技术也在不断完善,未来可能会实现更高精度、更大规模的生产。
随着工业自动化程度的提高,高真空压铸技术也将更加智能化,能够更好地满足各行业对高质量铸件的需求。
高真空压铸技术是一种非常重要的先进工艺,对于提高铸件质量、降低成本、保护环境等方面都具有重要意义,值得在未来的工业生产中进一步推广和应用。
高真空压铸技术

高真空压铸技术
高真空压铸技术是一种先进的压铸成型技术,它利用高真空条件下的特殊环境,使金属液态在高压作用下快速充填模具型腔,并在一定压力作用下冷却凝固而得到铸件。
这种技术具有以下特点:
1. 高真空环境:高真空压铸技术利用高真空环境,可以减少金属液中的气体含量,避免气孔和裂纹等缺陷的产生,提高铸件的质量和可靠性。
2. 高压力充填:高真空压铸技术采用高压液体充填模具型腔,可以在短时间内将金属液快速压入模具型腔,缩短生产周期,提高生产效率。
3. 快速冷却凝固:在高真空压铸技术中,金属液在高压作用下快速充填模具型腔,并在一定压力作用下冷却凝固。
这种快速冷却凝固的方式可以减少铸件中的缩孔、缩松等缺陷的产生。
4. 优化生产流程:高真空压铸技术可以优化生产流程,减少后处理工作量,降低生产成本。
同时,高真空压铸技术还可以实现自动化生产,提高生产效率。
5. 适用范围广:高真空压铸技术可以适用于各种不同材质的铸件,如铝合金、镁合金、铜合金等。
同时,高真空压铸技术还可以用于复杂形状的铸件的生产,如汽车发动机缸体、缸盖等。
需要注意的是,高真空压铸技术的实施需要具备相应的设备和工艺技术,并且对操作人员的技能要求较高。
同时,在生产过程中也需要进行严格的质量控制和管理,以确保产品的质量和可靠性。
总之,高真空压铸技术是一种先进的压铸成型技术,具有提高产品质量、优化生产流程、降低成本、适用范围广等优点。
随着科技的不断发展,高真空压铸技术将在未来得到更广泛的应用和发展。
助力高真空压铸和真空压铸技术介绍
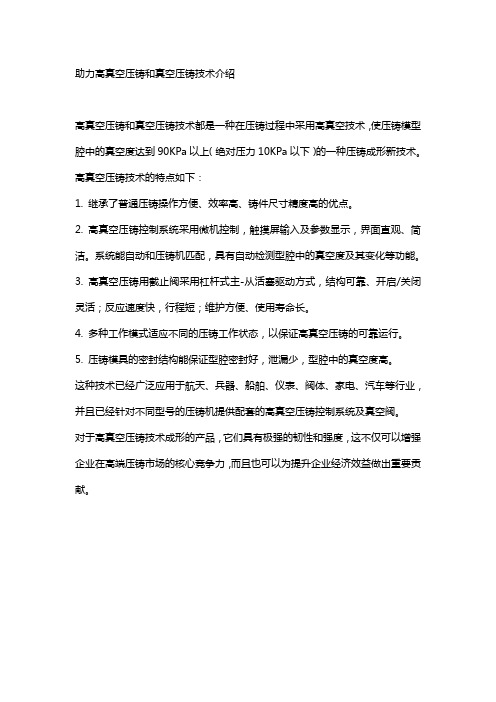
助力高真空压铸和真空压铸技术介绍
高真空压铸和真空压铸技术都是一种在压铸过程中采用高真空技术,使压铸模型腔中的真空度达到90KPa以上(绝对压力10KPa以下)的一种压铸成形新技术。
高真空压铸技术的特点如下:
1. 继承了普通压铸操作方便、效率高、铸件尺寸精度高的优点。
2. 高真空压铸控制系统采用微机控制,触摸屏输入及参数显示,界面直观、简洁。
系统能自动和压铸机匹配,具有自动检测型腔中的真空度及其变化等功能。
3. 高真空压铸用截止阀采用杠杆式主-从活塞驱动方式,结构可靠、开启/关闭灵活;反应速度快,行程短;维护方便、使用寿命长。
4. 多种工作模式适应不同的压铸工作状态,以保证高真空压铸的可靠运行。
5. 压铸模具的密封结构能保证型腔密封好,泄漏少,型腔中的真空度高。
这种技术已经广泛应用于航天、兵器、船舶、仪表、阀体、家电、汽车等行业,并且已经针对不同型号的压铸机提供配套的高真空压铸控制系统及真空阀。
对于高真空压铸技术成形的产品,它们具有极强的韧性和强度,这不仅可以增强企业在高端压铸市场的核心竞争力,而且也可以为提升企业经济效益做出重要贡献。
真空技术在改善压铸质量方面的应用

真空技术在改善压铸质量方面的应用[摘要]:在压铸生产过程中,压铸工艺的改进和优化对提高压铸件质量起到了极大的推动作用,本文简要阐述了在压铸技术创新和产品质量不断提高,其各方面的特点也越来越受到关注。
在压铸过程中,金属液体内会卷入气体。
真空压铸是可以减少铸件内气孔的有效工艺,提升铸件力学性能的有效方法。
关键词:真空压铸;压铸工艺;铝合金引言:随着压铸技术不断进步,追求高品质生产。
但因气孔的存在,也存在一些缺点,如何的避免这些缺点,是当今压铸行业不断探索的方向。
近年来,新能源汽车快速发展,汽车工业开始轻量化设计。
这为汽车行业提出了“减轻质量、节约能源、提高安全性”的新要求。
产品的质量是安全的保证,减少产品气孔是一条不懈探究的道路。
一、压铸工艺优点及其局限性优点:压铸的实质是在高压作用下,使液态或半固态金属以高速度填充进入压铸模具,并在压力作用下成型和冷却凝固而获得铸件的一种成形工艺。
由此可见,高压和高速是压铸工艺的两大特点。
因此,压铸件的主要特性有以下几点:1.在高压下成型,产品致密性、机械强度及表面硬度高,但产品的延伸率较低。
2.充型快,冷却时间短,生产效率高,批量生产时成本低。
3.产品表面粗糙可达到 Ra1.6-6.3。
4.可生产壁厚较薄的零件。
5.充型快,内部卷入气体多,气孔较多。
6.不可热处理。
热处理时内部气体会膨胀,导致产品出现鼓包或裂开等缺陷。
正是因为气孔问题的存在,不断推动着压铸工艺的改进,以满足人们对压铸件质量不断增高的要求,拓展压铸工艺的应用范围,真空压铸技术就是方法之一。
二、真空压铸:真空压铸技术是在传统铸造技术的基础上,对型腔抽真空的方法。
先采用真空抽取装置将压铸模内压室和型腔内的气体抽出,使金属熔液在相对真空的条件下充填型腔。
利用真空压铸技术抽出气体,能消除或显著减少铸件内的溶解气体,提高铸件内部组织致密度,从而达到提升铸件的表面质量和综合力学性能的目的。
为获得理想的铸件,必须减少喷射热金属与型腔内的空气和烟气接触;就是在压射开始至结束的全过程中尽可能地降低型腔内的空气和烟气的气体压力,将整个过程的气体含量减少到一个近于理想的状况。
铝合金真空压铸技术

铝合金真空压铸技术铝合金真空压铸技术是一种高效、精密的铝合金铸造工艺,通过在真空环境中进行压铸,可以有效避免铸件表面氧化、气孔等缺陷,提高铸件的质量和性能。
以下是关于铝合金真空压铸技术的详细介绍,包括其工艺流程、优势、应用领域等方面。
一、铝合金真空压铸技术概述铝合金真空压铸技术是一种在真空环境下进行的高压铸造工艺。
其主要步骤包括:模具封闭,抽真空,充填铝液,施加高压,保压定型,冷却固化,开模取件。
整个过程在真空条件下进行,以确保铸件表面无气孔、氧化等缺陷,同时通过高压实现铝液的充分充填,提高铸件的密度和机械性能。
二、铝合金真空压铸技术的工艺流程模具设计和制造:根据产品的形状和尺寸,设计并制造合适的压铸模具,确保模具具有足够的强度和耐磨性。
模具封闭:将设计好的模具封闭,形成一个密封的腔室,以准备进行真空铸造。
真空抽气:在模腔封闭后,通过真空泵将模腔内的空气抽出,创造真空环境。
真空状态有助于减少铝液中气体的溶解,防止气孔的生成。
铝液充填:在真空状态下,将预热至一定温度的铝液注入模腔,确保铝液在模腔中均匀充填。
施加高压:在铝液充填后,施加高压,使铝液充分充填模腔,提高铸件的密度和机械性能。
保压定型:在高压作用下,保持一段时间,使铝液定型成型。
冷却固化:在定型后,通过冷却系统将模腔内的铝液迅速冷却,固化成为铝合金铸件。
开模取件:冷却固化后,打开模具,取出成型的铝合金铸件,进行后续的处理和加工。
三、铝合金真空压铸技术的优势减少氧化和气孔:在真空环境下进行铸造可以有效减少铸件表面的氧化,同时通过真空抽气减少气体的溶解,避免气孔的生成,提高铸件的表面质量。
提高密度和机械性能:高压充填和保压定型能够使铝液充分充填模腔,提高铝合金铸件的密度和机械性能。
精密铸造:铝合金真空压铸技术可以实现更精密的铸造,适用于复杂形状、高精度要求的铝合金零件生产。
高生产效率:由于真空压铸工艺的高压和高速度,可以实现较短的充填时间和较快的冷却速度,提高生产效率。
真空技术在压铸过程中的应用浅析-lcf
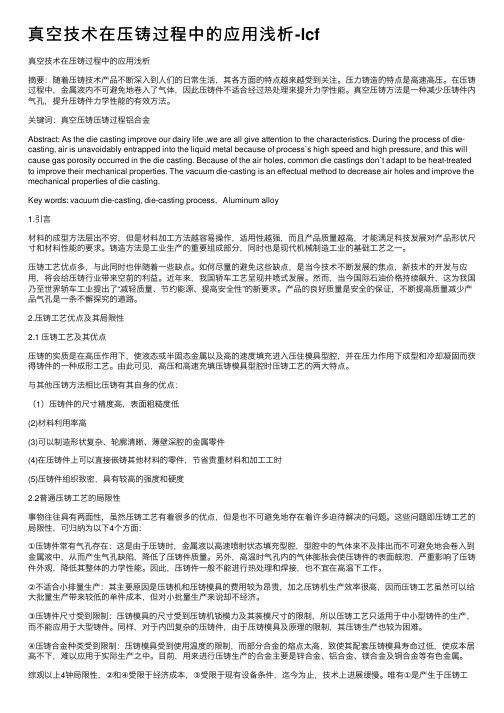
真空技术在压铸过程中的应⽤浅析-lcf真空技术在压铸过程中的应⽤浅析摘要:随着压铸技术产品不断深⼊到⼈们的⽇常⽣活,其各⽅⾯的特点越来越受到关注。
压⼒铸造的特点是⾼速⾼压。
在压铸过程中,⾦属液内不可避免地卷⼊了⽓体,因此压铸件不适合经过热处理来提升⼒学性能。
真空压铸⽅法是⼀种减少压铸件内⽓孔,提升压铸件⼒学性能的有效⽅法。
关键词:真空压铸压铸过程铝合⾦Abstract: As the die casting improve our dairy life ,we are all give attention to the characteristics. During the process of die-casting, air is unavoidably entrapped into the liquid metal because of process`s high speed and high pressure, and this will cause gas porosity occurred in the die casting. Because of the air holes, common die castings don`t adapt to be heat-treated to improve their mechanical properties. The vacuum die-casting is an effectual method to decrease air holes and improve the mechanical properties of die casting.Key words: vacuum die-casting, die-casting process,Aluminum alloy1.引⾔材料的成型⽅法层出不穷,但是材料加⼯⽅法越容易操作,适⽤性越强,⽽且产品质量越⾼,才能满⾜科技发展对产品形状尺⼨和材料性能的要求。
真空压铸
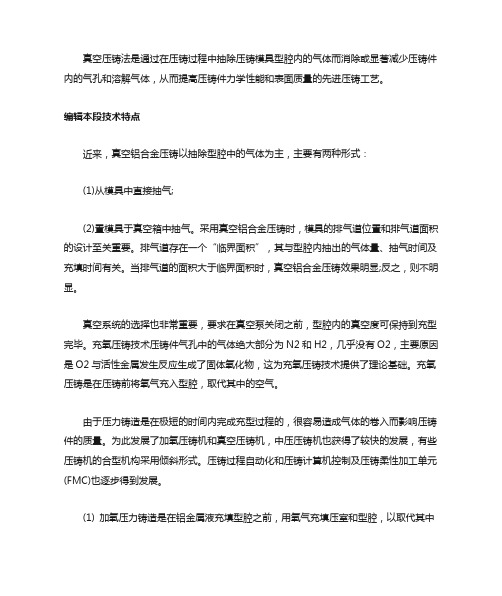
真空压铸法是通过在压铸过程中抽除压铸模具型腔内的气体而消除或显著减少压铸件内的气孔和溶解气体,从而提高压铸件力学性能和表面质量的先进压铸工艺。
编辑本段技术特点近来,真空铝合金压铸以抽除型腔中的气体为主,主要有两种形式:(1)从模具中直接抽气;(2)置模具于真空箱中抽气。
采用真空铝合金压铸时,模具的排气道位置和排气道面积的设计至关重要。
排气道存在一个“临界面积”,其与型腔内抽出的气体量、抽气时间及充填时间有关。
当排气道的面积大于临界面积时,真空铝合金压铸效果明显;反之,则不明显。
真空系统的选择也非常重要,要求在真空泵关闭之前,型腔内的真空度可保持到充型完毕。
充氧压铸技术压铸件气孔中的气体绝大部分为N2和H2,几乎没有O2,主要原因是O2与活性金属发生反应生成了固体氧化物,这为充氧压铸技术提供了理论基础。
充氧压铸是在压铸前将氧气充入型腔,取代其中的空气。
由于压力铸造是在极短的时间内完成充型过程的,很容易造成气体的卷入而影响压铸件的质量。
为此发展了加氧压铸机和真空压铸机,中压压铸机也获得了较快的发展,有些压铸机的合型机构采用倾斜形式。
压铸过程自动化和压铸计算机控制及压铸柔性加工单元(FMC)也逐步得到发展。
(1) 加氧压力铸造是在铝金属液充填型腔之前,用氧气充填压室和型腔,以取代其中的空气和其他气体。
其特点是:消除或减少了气孔,提高铸件的质量;结构简单,操作方便,投资少。
(2) 真空压力铸造是先将压铸型腔内空气抽除,然后再压入液体金属。
其特点是:可消除或减少压铸件内部的气孔,提高铸件的力学性能和表面质量;压铸时大大减少了型腔的反压力,可使用较低的比压和铸造性能较差的合金。
真空压铸法优点① 真空压铸法可消除或减少压铸件内部的气孔,提高压铸件的机械性能和表面质量,改善镀覆性能;② 真空压铸法大大减少型腔的反压力,可使用较低的比压及铸造性能较差的合金,有可能用小机器压铸较大的铸件;③ 真空压铸法改善了充填条件,可压铸较薄的铸件;④ 真空压铸法和普通压铸方法相比,生产效率几乎一样。
压铸生产中的新技术应用
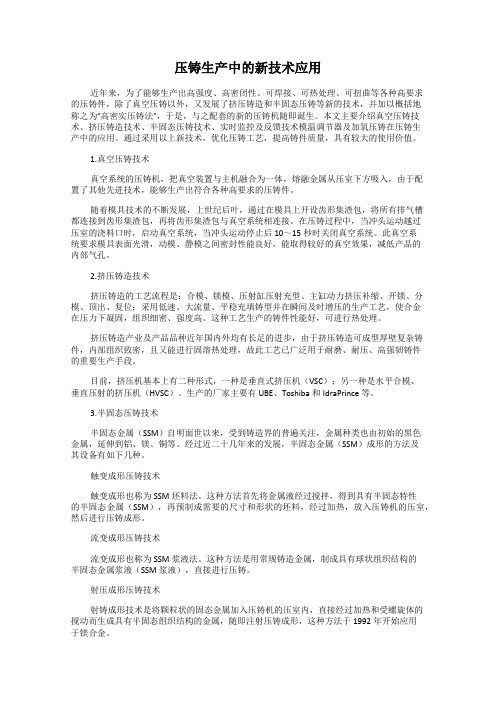
压铸生产中的新技术应用近年来,为了能够生产出高强度、高密闭性、可焊接、可热处理、可扭曲等各种高要求的压铸件,除了真空压铸以外,又发展了挤压铸造和半固态压铸等新的技术,并加以概括地称之为"高密实压铸法",于是,与之配套的新的压铸机随即诞生。
本文主要介绍真空压铸技术、挤压铸造技术、半固态压铸技术、实时监控及反馈技术模温调节器及加氧压铸在压铸生产中的应用。
通过采用以上新技术,优化压铸工艺,提高铸件质量,具有较大的使用价值。
1.真空压铸技术真空系统的压铸机,把真空装置与主机融合为一体,熔融金属从压室下方吸入,由于配置了其他先进技术,能够生产出符合各种高要求的压铸件。
随着模具技术的不断发展,上世纪后叶,通过在模具上开设齿形集渣包,将所有排气槽都连接到齿形集渣包,再将齿形集渣包与真空系统相连接。
在压铸过程中,当冲头运动越过压室的浇料口时,启动真空系统,当冲头运动停止后10~15秒时关闭真空系统。
此真空系统要求模具表面光滑,动模、静模之间密封性能良好,能取得较好的真空效果,减低产品的内部气孔。
2.挤压铸造技术挤压铸造的工艺流程是:合模、锁模、压射缸压射充型、主缸动力挤压补缩、开锁、分模、顶出、复位;采用低速、大流量、平稳充填铸型并在瞬间及时增压的生产工艺,使合金在压力下凝固,组织细密、强度高。
这种工艺生产的铸件性能好,可进行热处理。
挤压铸造产业及产品品种近年国内外均有长足的进步,由于挤压铸造可成型厚壁复杂铸件,内部组织致密,且又能进行固溶热处理,故此工艺已广泛用于耐磨、耐压、高强韧铸件的重要生产手段。
目前,挤压机基本上有二种形式,一种是垂直式挤压机(VSC);另一种是水平合模、垂直压射的挤压机(HVSC)。
生产的厂家主要有UBE、Toshiba和IdraPrince等。
3.半固态压铸技术半固态金属(SSM)自明面世以来,受到铸造界的普遍关注,金属种类也由初始的黑色金属,延伸到铝、镁、铜等。
《压铸工艺及模具设计》复习题1-答案
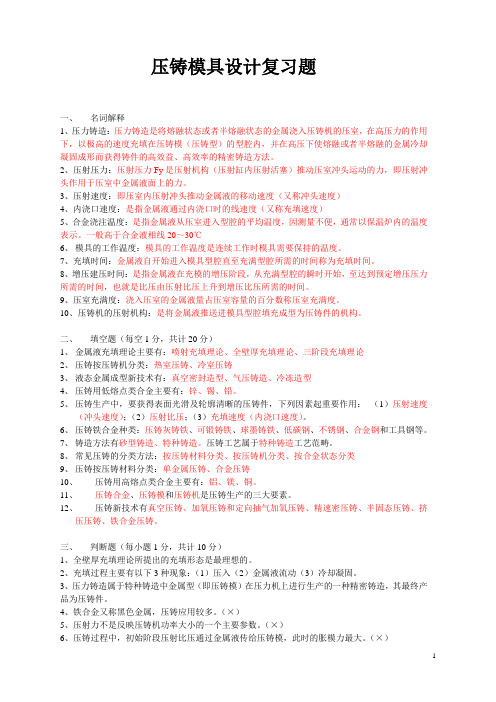
压铸模具设计复习题一、名词解释1、压力铸造:压力铸造是将熔融状态或者半熔融状态的金属浇入压铸机的压室,在高压力的作用下,以极高的速度充填在压铸模(压铸型)的型腔内,并在高压下使熔融或者半熔融的金属冷却凝固成形而获得铸件的高效益、高效率的精密铸造方法。
2、压射压力:压射压力Fy是压射机构(压射缸内压射活塞)推动压室冲头运动的力,即压射冲头作用于压室中金属液面上的力。
3、压射速度:即压室内压射冲头推动金属液的移动速度(又称冲头速度)4、内浇口速度:是指金属液通过内浇口时的线速度(又称充填速度)5、合金浇注温度:是指金属液从压室进入型腔的平均温度,因测量不便,通常以保温炉内的温度表示。
一般高于合金液相线20~30℃6、模具的工作温度:模具的工作温度是连续工作时模具需要保持的温度。
7、充填时间:金属液自开始进入模具型腔直至充满型腔所需的时间称为充填时间。
8、增压建压时间:是指金属液在充模的增压阶段,从充满型腔的瞬时开始,至达到预定增压压力所需的时间,也就是比压由压射比压上升到增压比压所需的时间。
9、压室充满度:浇入压室的金属液量占压室容量的百分数称压室充满度。
10、压铸机的压射机构:是将金属液推送进模具型腔填充成型为压铸件的机构。
二、填空题(每空1分,共计20分)1、金属液充填理论主要有:喷射充填理论、全壁厚充填理论、三阶段充填理论2、压铸按压铸机分类:热室压铸、冷室压铸3、液态金属成型新技术有:真空密封造型、气压铸造、冷冻造型4、压铸用低熔点类合金主要有:锌、锡、铅。
5、压铸生产中,要获得表面光滑及轮廓清晰的压铸件,下列因素起重要作用:(1)压射速度(冲头速度);(2)压射比压;(3)充填速度(内浇口速度)。
6、压铸铁合金种类:压铸灰铸铁、可锻铸铁、球墨铸铁、低碳钢、不锈钢、合金钢和工具钢等。
7、铸造方法有砂型铸造、特种铸造。
压铸工艺属于特种铸造工艺范畴。
8、常见压铸的分类方法:按压铸材料分类、按压铸机分类、按合金状态分类9、压铸按压铸材料分类:单金属压铸、合金压铸10、压铸用高熔点类合金主要有:铝、镁、铜。
《压铸工艺及模具设计》复习题答案
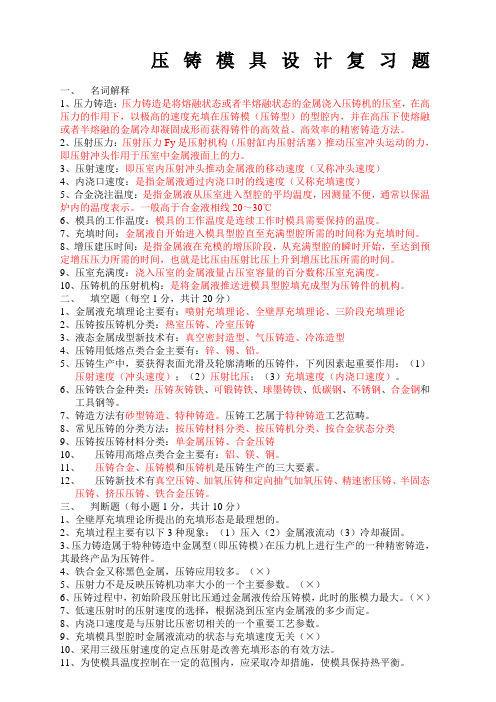
压铸模具设计复习题一、名词解释1、压力铸造:压力铸造是将熔融状态或者半熔融状态的金属浇入压铸机的压室,在高压力的作用下,以极高的速度充填在压铸模(压铸型)的型腔内,并在高压下使熔融或者半熔融的金属冷却凝固成形而获得铸件的高效益、高效率的精密铸造方法。
2、压射压力:压射压力Fy是压射机构(压射缸内压射活塞)推动压室冲头运动的力,即压射冲头作用于压室中金属液面上的力。
3、压射速度:即压室内压射冲头推动金属液的移动速度(又称冲头速度)4、内浇口速度:是指金属液通过内浇口时的线速度(又称充填速度)5、合金浇注温度:是指金属液从压室进入型腔的平均温度,因测量不便,通常以保温炉内的温度表示。
一般高于合金液相线20~30℃6、模具的工作温度:模具的工作温度是连续工作时模具需要保持的温度。
7、充填时间:金属液自开始进入模具型腔直至充满型腔所需的时间称为充填时间。
8、增压建压时间:是指金属液在充模的增压阶段,从充满型腔的瞬时开始,至达到预定增压压力所需的时间,也就是比压由压射比压上升到增压比压所需的时间。
9、压室充满度:浇入压室的金属液量占压室容量的百分数称压室充满度。
10、压铸机的压射机构:是将金属液推送进模具型腔填充成型为压铸件的机构。
二、填空题(每空1分,共计20分)1、金属液充填理论主要有:喷射充填理论、全壁厚充填理论、三阶段充填理论2、压铸按压铸机分类:热室压铸、冷室压铸3、液态金属成型新技术有:真空密封造型、气压铸造、冷冻造型4、压铸用低熔点类合金主要有:锌、锡、铅。
5、压铸生产中,要获得表面光滑及轮廓清晰的压铸件,下列因素起重要作用:(1)压射速度(冲头速度);(2)压射比压;(3)充填速度(内浇口速度)。
6、压铸铁合金种类:压铸灰铸铁、可锻铸铁、球墨铸铁、低碳钢、不锈钢、合金钢和工具钢等。
7、铸造方法有砂型铸造、特种铸造。
压铸工艺属于特种铸造工艺范畴。
8、常见压铸的分类方法:按压铸材料分类、按压铸机分类、按合金状态分类9、压铸按压铸材料分类:单金属压铸、合金压铸10、压铸用高熔点类合金主要有:铝、镁、铜。
金属材料短流程、近终形的生产工艺

金属材料短流程、近终形的生产工艺多个进程(如凝固与成形)的综合化,称短流程化,如喷射成形技术、半固态加工技术和持续铸轧技术等。
打破传统的材料成形与加工模式,缩短生产工艺流程,简化工艺环节,实现近终形、短流程的持续化生产,提高生产效率。
近终型、短流程的成形加工技术具有高效、节能等特点,在技术上突出的特点是缩短加工周期,尽可能减少变形量或后续加工环节,由金属熔体直接取得所需的制品或近似的制品,同时,这些制品还具有现有加工方式所生产制品的性能和组织,这可大大减少后续挤压、轧制和压铸等耗能大、投资大、用工多的加工进程。
例如,半固态成形、持续铸轧和持续铸挤等是将凝固与成形两个进程合而为一,实行精准控制,形成以节能、降耗、高效和优质为主要特征的新技术和新工艺。
1半固态成型金属材料的半固态成型是在半液半固的两相状态下进行的,所以与全液体成型或全固体成型相较,具有许多长处。
首先,在凝固进程中有固液两相,同时存在的合金系都可进行半固态成型。
半固态材料浆的粘度比熔融金属的粘度高得多,因此成型时可形成层流,也能更均匀地填充模型。
金属浆的成型温度较低,与常规铸造工艺相较:可节约35%左右的能源;可以延长模型寿命;凝固时间较短;可缩短生产周期;由于有固体存在和温度较低,零件在模内的收缩较小。
用金属浆生产的零件内的宏观气孔与显微疏松比常规铸件中的少得多。
半固态材料填充模型时,材料前端呈层流充满型腔,比熔融金属的流动平稳得多,不会卷入气体。
半固态成型零件的尺寸可与成品零件的相等或几乎相等,极大地减少了机械加工量与切削量,既节约了材料,又可以生产形状复杂的零件或难于加工的薄壁零件。
半固态模锻件与压铸件表面平整滑腻,内部组织致密,晶粒细小,力学性能高。
2近终形轧制技术(1)热连轧技术热连轧技术是将均热后的坯锭同时在几个机架中产生塑形变形的持续轧制进程。
与单机架轧制相较较,热连轧技术具有工艺流程短,生产率高,产品质量高和生产本钱低等长处。
高真空压铸技术及其应用优势

1 模 2 杆 3 空 箱 4 空 管 5 封 圈 6真空 阀 . 定 . 顶 . 真 . 真 . 密 . 7 空罐 、 . 真 泵 8 头 9 调 温 压 射 室 1. . 冲 . 可 O动模 事实上 , 高真 空压 铸 技 术并 不 仅 是 模 具 密 封 的技 术 , 还 涉 及 它 金 属 熔 液 处 理 、 具 结 构设 计 、 注 工 艺 及 脱 模 剂 等 各 个 方 面 的 技 模 浇
铸机价格昂贵 , 本很 高。相对 而言 , F 成 M T法 由 于 使 用 的 是 普 通 压 铸 机 , 备 门槛 低 , 设 因而 普 及 率 较 高 , 用 前 景 好 。 还 有 一 种 日 应 本 雅 马 哈 公 司 开 发 的 V cu G l B x , 图 2 au m o e o 法 见 v 。因 考 虑 到 顶 杆 无 抽 芯 处 的 密 封 较 困 难 , 所 采 取 的结 构 是 将 整 个 模 具 装 在 一 个 它
示 , 面直观 、 洁 。 界 简
( ) 统 能 自动 和 压 铸 机 匹 配 , 有 自动 检 测 型 腔 中 的 真 空 度 3系 具
及其变化 ; 自动检 测 真 空 管 路 的 堵 塞 状 态 ; 自动 清 洗 管 路 ; 自动 报 警等功能 。 () 真空 压铸 用 截止 阀采 用 杠 杆式 主 一从 活 塞 驱 动 方 式 , 4高 结构 可靠 、 开启/ 闭灵活 ; 关 反应 速 度快 , 行程 短 ; 护方 便 、 用 寿命 长 。 维 使 () 5 多种 工作 模 式 适 应 不 同 的 压 铸 工 作 状 态 ( 模 具 调 试 、 如 压
技 术 , 造 出 的 模 具 能 保 证 模 具 型 腔 的 高 真 空度 , 生 产 高 质 量 的 压 铸 制 使
各种铸造工艺的区别

1.铸造还可按金属液的浇注工艺分为重力铸造和压力铸造。
重力铸造是指金属液在地球重力作用下注入铸型的工艺,也称浇铸。
广义的重力铸造包括砂型浇铸、金属型浇铸、熔模铸造,泥模铸造等;窄义的重力铸造专指金属型浇铸。
压力铸造是指金属液在其他外力(不含重力)作用下注入铸型的工艺。
广义的压力铸造包括压铸机的压力铸造和真空铸造、低压铸造、离心铸造等;窄义的压力铸造专指压铸机的金属型压力铸造,简称压铸。
这几种铸造工艺是目前有色金属铸造中最常用的、也是相对价格最低的。
2.砂型铸造是一种以砂作为主要造型材料,制作铸型的传统铸造工艺。
砂型一般采用重力铸造,有金属型既可采用重力铸造,也但是,金属型铸造也有一些不足之处:因为耐热合金钢和在它上面做出中空型腔的加工都比较昂贵,所以金属型的模具费用不菲,不过总体和压铸模具费用比起来则便宜多了。
对小批量生产而言,分摊到每件产品上的模具费用明显过高,一般不易接受。
又因为金属型的模具受模具材料尺寸和型腔加工设备、铸造设备能力的限制,所以对特别大的铸件也显得无能为力。
因而在小批量及大件生产中,很少使用金属型铸造。
此外,金属型模具虽然采用了耐热合金钢,但耐热能力仍有限,一般多用于铝合金、锌合金、镁合金的铸造,在铜合金铸造中已较少应用,而用于黑色金属铸造就更少了。
旭东精密铸件厂的金属型模具全部是自行设计、自行制造,因而能更及时地为客户提供价廉、适用的优质模具。
4.压铸是在压铸机上进行的金属型压力铸造,是目前生产效率最高的铸造工艺。
压铸机分为热室压铸机和冷室压铸机两类。
热室压铸机自动化程度高,材料损耗少,生产效率比冷室压铸机更高,但受机件耐热能力的制约,目前还只能用于锌合金、镁合金等低熔点材料的铸件生产。
当今广泛使用的铝合金压铸件,由于熔点较高,只能在冷室压铸机上生产。
压铸的主要特点是金属液在高压、高速下充填型腔,并在高压下成形、凝固,压铸件的不足之处是:所以,我们只能称“水纹”要,它是毫无办法的。
真空压铸全解

真空压铸
以上工艺存在的问题
排气槽 需要一定的理论和经验才能较正确的开设,也只能进行辅助排气,还未 从根本上根 除气体。 超低速压铸 虽能有效减少气体进入铸件内部,但已失去压铸的高效性
多段压射机台 此技术能够排除一定气体,但是只是排除压室和流道内的气体,对于 型腔内还是于 事无补。
真空压铸
其他改进工艺
为了比较彻底的排除型腔内气体,压铸前辈开发了真空 压铸和充氧压铸。 目前,真空压铸推广是比较成功的,也 是实际应用的比较多的。
真空压铸
什么是真空压铸
通过在压铸过程中抽除压铸模具型腔内的气体,而消除或减少压铸件内的气孔, 从 而提高压铸件力学性能和表面质量的先进压铸工艺。
真空压铸
真空压铸
什么情况下考虑真空压铸技术?
真空压铸
真空冷室压铸系统
真空压铸
真空热室压铸系统
真空压铸
型腔内部的压力
真空压铸
型腔内部的压力
真空压铸
影响压铸模内空气压力的相关因素:
•模具开闭的紧密程度。 •模具表面的清洁和干燥程度。 •压铸工艺中的冲头速度。 •冲头在压室中的紧密程度。 •真空罐与模腔容积的比率。 •真空通道长度和截面尺寸(流动阻力)。 •真空阀大小。 •真空设备的型号和其性能。 •铸件连带的真空注口和通道。
真空压铸
压铸成形工艺环节与抽真空时间
真空压铸示意图
真空压铸
真空压铸的三种技术
1、德国Vacural 法 将熔化炉通过升液管和压射室直接相连,抽真空时先将金属液吸入到 压室内,接着 继续抽真空至预定真空度后再压射成型。
特点: 真空效果不错 需专用压铸机 投资成本较高 应用不是很广泛
真空压铸
真空压铸的三种技术 2、MFT(Minimum Fill Time)法 MFT(Minimum Fill Time)法是完全在普通压铸机上进行,所以运用较 为广泛, 在慢压射开始时(冲头越过浇料口),真空系统开始抽真空,充型完成前, 抽真空 系统停止抽真空。
压铸工艺参数对真空压铸成品率的影响研究

链 条 盖 产 品 技 术 要求 :
(1) 产品投影面积 : 8 c 。产 品质量 :.k ; 75m, 21 g ( 外观 质量 的确认标 准 : 品的表面 不允许有 裂纹 、 2) 产 冷
隔、 毛刺 、 烧伤、 扣伤 ( 擦伤 ) 等压铸缺 陷。 其余按 压铸 件的标准 ; ( 内部质 量的确认 标准 : 3) 螺纹孔气孔 大小不允许 2 X 牙
密度 、 解决涂料脱皮 、 电镀起 泡及盲孔缺料等工艺难题 。 但是 ,真空压铸在我 国的应用水平 目前还处于推广初期 阶 段, 对真空压铸理论与实践均缺乏 系统深入的研究 , 真空压铸时
压铸在该 产品生产商优势 ;然后系统改变 真空压铸工艺参数 , 研 究个股也参数对压铸工艺 品质 和生产 效率 的影 响。
经计算 机虚拟现 实和工艺优化后 , 确定 了图 2的链 条盖 的
真空压铸工艺模 具。 实验思路 : 采用真 空压铸和 普通压 铸对 比试 验 , 考察真空
(1) 汽车 、 摩托 车零部件 , 油压件 , 航天航空等领域有气密性及 强度要 求的铸件 ; 2) ( 装潢 和装饰 、 日常生活 等对产 品外 观质 量要求 苛刻 的领域 ; 3) ( 结构复 杂 、 安装尺寸要 求精确 或使用 性能要求高 的产品 , : 如 电脑配件、 冷却器 、 通讯等 。 对于上述有特殊性能和高工艺 品质要求 的零部件 , 在压铸 生产 中引入真空 , 消除表面气孔 、 可 提高表面质量 , 改善铸件致
( . 东鸿 图科技 股 份有 限公 司 , 东 高 要 5 6 8 . 大 学 , 1广 广 2 l ;2重庆 0 重庆 4 0 3 ) 0 0 0
助力高真空压铸和真空压铸技术介绍
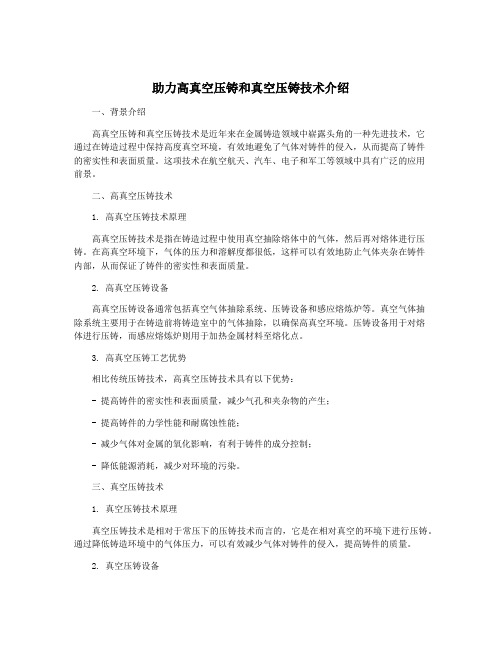
助力高真空压铸和真空压铸技术介绍一、背景介绍高真空压铸和真空压铸技术是近年来在金属铸造领域中崭露头角的一种先进技术,它通过在铸造过程中保持高度真空环境,有效地避免了气体对铸件的侵入,从而提高了铸件的密实性和表面质量。
这项技术在航空航天、汽车、电子和军工等领域中具有广泛的应用前景。
二、高真空压铸技术1. 高真空压铸技术原理高真空压铸技术是指在铸造过程中使用真空抽除熔体中的气体,然后再对熔体进行压铸。
在高真空环境下,气体的压力和溶解度都很低,这样可以有效地防止气体夹杂在铸件内部,从而保证了铸件的密实性和表面质量。
2. 高真空压铸设备高真空压铸设备通常包括真空气体抽除系统、压铸设备和感应熔炼炉等。
真空气体抽除系统主要用于在铸造前将铸造室中的气体抽除,以确保高真空环境。
压铸设备用于对熔体进行压铸,而感应熔炼炉则用于加热金属材料至熔化点。
3. 高真空压铸工艺优势相比传统压铸技术,高真空压铸技术具有以下优势:- 提高铸件的密实性和表面质量,减少气孔和夹杂物的产生;- 提高铸件的力学性能和耐腐蚀性能;- 减少气体对金属的氧化影响,有利于铸件的成分控制;- 降低能源消耗,减少对环境的污染。
三、真空压铸技术1. 真空压铸技术原理真空压铸技术是相对于常压下的压铸技术而言的,它是在相对真空的环境下进行压铸。
通过降低铸造环境中的气体压力,可以有效减少气体对铸件的侵入,提高铸件的质量。
2. 真空压铸设备真空压铸设备主要包括真空系统、压铸机床和感应熔炼炉等。
其中真空系统用于维持设备工作环境中的相对真空度,压铸机床则用于对金属熔体进行压铸,感应熔炼炉则用于提供金属材料的熔化热源。
3. 真空压铸工艺优势真空压铸技术相对于常压下的压铸技术,具有以下优势:- 减少气孔、夹杂和表面缺陷的产生,提高了铸件的质量和性能;- 在熔化和注射过程中,金属氧化的程度较低,有利于提高合金的成分控制;- 降低了金属液体的熔化温度,减少了合金的成分消耗,降低了生产成本。
真空压铸和普通压铸方法相比
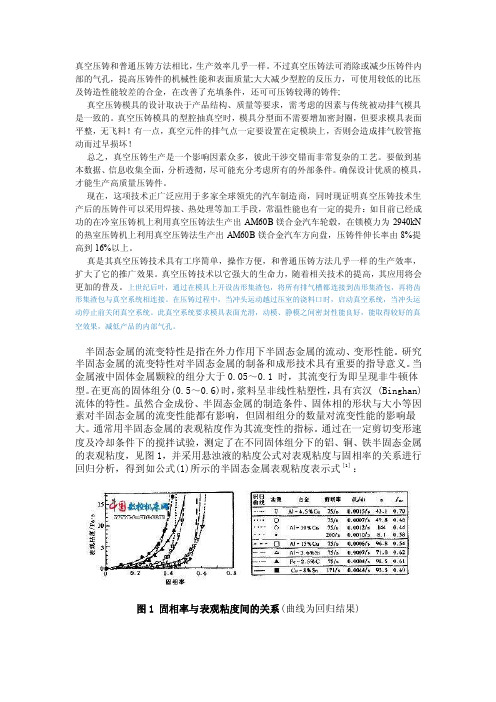
真空压铸和普通压铸方法相比,生产效率几乎一样。
不过真空压铸法可消除或减少压铸件内部的气孔,提高压铸件的机械性能和表面质量;大大减少型腔的反压力,可使用较低的比压及铸造性能较差的合金,在改善了充填条件,还可可压铸较薄的铸件;真空压铸模具的设计取决于产品结构、质量等要求,需考虑的因素与传统被动排气模具是一致的。
真空压铸模具的型腔抽真空时,模具分型面不需要增加密封圈,但要求模具表面平整,无飞料!有一点,真空元件的排气点一定要设置在定模块上,否则会造成排气胶管拖动而过早损坏!总之,真空压铸生产是一个影响因素众多,彼此干涉交错而非常复杂的工艺。
要做到基本数据、信息收集全面,分析透彻,尽可能充分考虑所有的外部条件。
确保设计优质的模具,才能生产高质量压铸件。
现在,这项技术正广泛应用于多家全球领先的汽车制造商,同时现证明真空压铸技术生产后的压铸件可以采用焊接、热处理等加工手段,常温性能也有一定的提升:如目前已经成功的在冷室压铸机上利用真空压铸法生产出AM60B镁合金汽车轮毂,在锁模力为2940kN 的热室压铸机上利用真空压铸法生产出AM60B镁合金汽车方向盘,压铸件伸长率由8%提高到16%以上。
真是其真空压铸技术具有工序简单,操作方便,和普通压铸方法几乎一样的生产效率,扩大了它的推广效果。
真空压铸技术以它强大的生命力,随着相关技术的提高,其应用将会更加的普及。
上世纪后叶,通过在模具上开设齿形集渣包,将所有排气槽都连接到齿形集渣包,再将齿形集渣包与真空系统相连接。
在压铸过程中,当冲头运动越过压室的浇料口时,启动真空系统,当冲头运动停止前关闭真空系统。
此真空系统要求模具表面光滑,动模、静模之间密封性能良好,能取得较好的真空效果,减低产品的内部气孔。
半固态金属的流变特性是指在外力作用下半固态金属的流动、变形性能。
研究半固态金属的流变特性对半固态金属的制备和成形技术具有重要的指导意义。
当金属液中固体金属颗粒的组分大于0.05~0.1 时,其流变行为即呈现非牛顿体型。
- 1、下载文档前请自行甄别文档内容的完整性,平台不提供额外的编辑、内容补充、找答案等附加服务。
- 2、"仅部分预览"的文档,不可在线预览部分如存在完整性等问题,可反馈申请退款(可完整预览的文档不适用该条件!)。
- 3、如文档侵犯您的权益,请联系客服反馈,我们会尽快为您处理(人工客服工作时间:9:00-18:30)。
真空压铸和普通压铸方法相比,生产效率几乎一样。
不过真空压铸法可消除或减少压铸件内部的气孔,提高压铸件的机械性能和表面质量;大大减少型腔的反压力,可使用较低的比压及铸造性能较差的合金,在改善了充填条件,还可可压铸较薄的铸件;真空压铸模具的设计取决于产品结构、质量等要求,需考虑的因素与传统被动排气模具是一致的。
真空压铸模具的型腔抽真空时,模具分型面不需要增加密封圈,但要求模具表面平整,无飞料!有一点,真空元件的排气点一定要设置在定模块上,否则会造成排气胶管拖动而过早损坏!总之,真空压铸生产是一个影响因素众多,彼此干涉交错而非常复杂的工艺。
要做到基本数据、信息收集全面,分析透彻,尽可能充分考虑所有的外部条件。
确保设计优质的模具,才能生产高质量压铸件。
现在,这项技术正广泛应用于多家全球领先的汽车制造商,同时现证明真空压铸技术生产后的压铸件可以采用焊接、热处理等加工手段,常温性能也有一定的提升:如目前已经成功的在冷室压铸机上利用真空压铸法生产出AM60B镁合金汽车轮毂,在锁模力为2940kN 的热室压铸机上利用真空压铸法生产出AM60B镁合金汽车方向盘,压铸件伸长率由8%提高到16%以上。
真是其真空压铸技术具有工序简单,操作方便,和普通压铸方法几乎一样的生产效率,扩大了它的推广效果。
真空压铸技术以它强大的生命力,随着相关技术的提高,其应用将会更加的普及。
上世纪后叶,通过在模具上开设齿形集渣包,将所有排气槽都连接到齿形集渣包,再将齿形集渣包与真空系统相连接。
在压铸过程中,当冲头运动越过压室的浇料口时,启动真空系统,当冲头运动停止前关闭真空系统。
此真空系统要求模具表面光滑,动模、静模之间密封性能良好,能取得较好的真空效果,减低产品的内部气孔。
半固态金属的流变特性是指在外力作用下半固态金属的流动、变形性能。
研究半固态金属的流变特性对半固态金属的制备和成形技术具有重要的指导意义。
当金属液中固体金属颗粒的组分大于0.05~0.1 时,其流变行为即呈现非牛顿体型。
在更高的固体组分(0.5~0.6)时,浆料呈非线性粘塑性,具有宾汉 (Binghan)流体的特性。
虽然合金成份、半固态金属的制造条件、固体相的形状与大小等因素对半固态金属的流变性能都有影响,但固相组分的数量对流变性能的影响最大。
通常用半固态金属的表观粘度作为其流变性的指标。
通过在一定剪切变形速度及冷却条件下的搅拌试验,测定了在不同固体组分下的铝、铜、铁半固态金属的表观粘度,见图1,并采用悬浊液的粘度公式对表观粘度与固相率的关系进行回归分析,得到如公式(1)所示的半固态金属表观粘度表示式[1]:图1 固相率与表观粘度间的关系(曲线为回归结果)(1)式中:ηa —半固态金属表观粘度,Pa.s,ηLa—金属液表观粘度(Pa.s),ρm—合金密度(kg.m-3),C—凝固速度,s-1,—剪切变形速度,s-1,fs—固相率。
由于半固态金属浆料中的固相率主要由半固态金属的温度来决定,因此在实际应用中温度的控制非常重要。
使半固态金属发生变形时的剪切应变率对表观粘度也有很大影响。
用高温旋转粘度计对稳定状态的半固态A356铝合金的表观粘度进行了测定,结果如图2所示。
该表观稳定态粘度可以用公式(2)的形式来表示[2]:图2 A356铝合金浆料稳态表观粘度与剪切率的关系(2)式中:η—表观粘度,—剪切率,C—稠度,m—为指数,其数值为-1.2至-1.3。
上述情况都是在搅拌试验进行几十分钟,粘度不再变化,达到稳定状态时得出的结果。
对于连续冷却状态,则表观粘度较稳定态的稍高。
在实际成型加工中,半固态金属充填型腔的时间只持续几秒钟,在这一瞬间由于液体相的粘度,固体颗粒的数量、大小、形貌均在变化,情况变得十分复杂。
文献[3]通过对锡-15% 铅所作的试验后指出,在给定的结构下,半固态浆料的瞬时结构特性为随着剪切率的增加表观粘度有所增加。
nextpage将搅拌的半固态金属浆料凝固后再重新加热至半固态,由于半固态金属的触变性,当切变速率很小或等于零时,半固态金属的粘度很高,可以象固体一样夹持及搬运,而当其受到较高剪切应力,产生较大切变速率时,粘度迅速降低,变得与流体一样很容易成形。
和其它具有触变性能的材料一样,半固态金属浆料也具有滞后回线现象,如图3所示。
对于初晶为树枝状的半固态合金,当固相率达到0.3左右就无法流动,而初晶形状为近乎圆形的半固态合金,即使固相率超过0.5,也还有流动性,这说明凝固时晶粒形态对流变性有重大影响。
制造半固态金属浆料时,搅拌速度、冷却速度及固相组分对非树枝状结构的生成具有如图4所示的影响[4]。
图3 半固态金属剪切应力与粘度的触变现象图4 非树枝晶结构生成机理示意图2 半固态金属的制备生产中常用机械或电磁搅拌的方法来制备金属浆料,用这两种方法可以得到固体组分的颗粒大小在50~100μm范围内的浆料。
图5为采用机械搅拌方式连续生产金属浆料的装置[5]。
对于铝、铜合金和铸铁,该法可实现固相率为0.5的浆料的连续生产。
机械搅拌也可采用剪切冷却辊方式[6]。
电磁搅拌法与机械搅拌相比,减少了搅拌器对浆料的污染,但在制备高固相率的浆料时,搅拌速度会急剧降低,表观粘度迅速增加,使浆料的排出发生困难。
图6为一种采用半固态金属制造铝基复合材料的电磁搅拌装置[7]。
该装置中的4对磁极以0~3000r/min的速度回转。
为了使浆料产生三维运动,磁铁与旋转中心轴之间有10°的偏转角,呈螺旋形放置。
采用该装置已制造出A356铝合金为基体,加入平均颗粒尺寸为29μm 的20vol%SiC颗粒的复合材料锭。
图5 机械搅拌式半固态金属制造装置图6 制造铝基复合材料用电磁搅拌装置nextpage 日本发明了一种制备触变成型用坯料的方法,在含Si量为4%~6%的铝合金中添加0.001%~0.01%的B及 0.005%~0.30%的Ti,合金液的过热度不超过液相线以上30℃,再以1.0℃/s以上的冷却速度在凝固区间冷却,可得到200μm以下细小等轴晶的铸坯[8]。
还可以采用应变诱发熔体活化等方法来制备半固态金属成形用的原材料。
3 半固态金属的成形与应用对于各种合金只要有固、液相同时存在的凝固区间,都可以进行半固态金属成形加工。
已经对铝、镁、锌、铜合金及钢、铸铁、镍基超耐热合金、复合材料进行过许多试验研究。
目前应用的合金还是直接取自现有的铸造或锻造合金系列,例如铝合金为3XXX系列铝硅铸造合金及2XXX、7XXX系列锻造合金。
应用得最多的为A356合金,其凝固区间约为60℃。
镁合金则主要为AZ91D。
至今专门应用于半固态成形的合金的研究工作还做得不多。
在美国和西欧铝、镁合金的半固态成形主要用于汽车零件的生产。
日本则对黑色金属的半固态成形作过较多的研究。
3.1 压铸目前生产中主要采用触变成型压铸铝合金铸件,如图7所示。
在西欧比较有代表性的公司是瑞士和德国的Alusisse/Alusingen,意大利的 Stampal及法国的Pechiney。
在德国Singer的Alusingen工厂装备了9800kN的压铸机及同时能加热12个坯料的加热工段,该生产线于1996年投产,主要生产汽车零件[9]。
由半固态金属压铸件上切取的试样的机械性能如表1所示[10]。
Stampal 公司除用该法大量生产汽车零件外,还生产航空和航天用构件,其典型产品为福特Zeta 发动机的燃油分配器。
美国宾夕法尼亚洲Johnstown的 Concurrent Technologies Corp.(CTC)起着国防部的金属加工制造技术国家中心(NCEMT)的作用。
该公司用触变压铸成形法生产的A356铝合金铸件的机械性能为σb=315MPa,σs=266MPa,δ=12%[9]。
正在进行的一项具有挑战性的新研究项目为生产用于LPD-17两栖攻击舰的钛液压操纵阀。
目前用半固态金属压铸法生产的最大构件质量达6.7kg,系牌号为“欧洲人”汽车的后部悬挂构件,并已于1995年投产。
用该法压铸的汽车构件还有主制动器缸体、齿轮齿条传动的操纵壳体、转向横拉杆头、喷油轨、托架等。
触变压铸成形也可在立式压铸机上进行,日本已在这方面取得了专利[11]。
图7 半固态金属压铸流程图表1 半固态金属压铸件上切取试样的机械性能日本レオツク(株)采用流变成形法对半固态AC4C合金(Al-7%Si-0.3%Mg)进行了连杆的压铸,此时将经机械搅拌的金属浆料放入耐火材料制造的容器中直接供给立式压铸机。
所得连杆的尺寸精度与密度均优于金属液压铸的[5]。
由于半固态金属压铸可以明显降低铸型温度,为黑色固态金属的压铸创造了有利条件。
试验表明,铸铁可以采用流变或触变铸造的方式进行压铸。
将铸铁在 1637K熔化后以500r/min的速度搅拌至1408K(低于液相线温度65K)制成半固态浆料,在2450kN的立式压铸机上可成功地压铸成100 ×150×6(mm)的板状件。
触变压铸成形时,将铸铁坯料放在卧式压铸机的压室部位,高频加热至固相率为0.2的半固态,压铸成壁厚为3mm的铸件,其机械性能如表2所示[12]。
日本还发明了有关的专利[13]。
除上述方法以外,还可将不同金属粉末混合压实后加热至半固态压铸零件[14]。
表2 铸铁压铸件的机械性能nextpage3.2 锻造半固态金属锻造与半固态金属触变压铸实质上并无明显差别,其主要不同之处在于半固态金属在锻造设备上加工成形。
锻造半固态金属可以在较低的压力下进行,如图8所示[6],这使得一些传统锻造无法成形的形状复杂构件可以用半固态金属锻造方法来生产。
在半固态金属锻造领域中占领先地位的是美国Alumax公司的子公司Alumax Engineered Metal Processes(AEMP)[9]。
位于田纳西州Jackson的工厂耗资7500万美元,利用该公司拥有的半固态金属锻造专利技术,每年能生产2.25万吨高质量的汽车零件。
该公司最近在阿肯色州的Bentonville又建造了一个生产汽车零件的工厂,该厂装备有二条完整的半固态金属锻件生产线。
其生产流程为将铝合金液冷却至半固态,用电磁搅拌装置搅拌后在水平连铸机上铸成坯料,其晶粒直径约为30μm。
切断的坯料感应加热至半固态(固相率约为0.5),在立式压力机上锻造。
锻造速度每秒几百mm到一千多mm,模压从几MPa到十多MPa,甚至更高。
材料的加热、运送、夹持和锻造均实现了自动化。
Alumax生产的第一个半固态锻件为福特汽车空调压缩机前、后外壳。
克莱斯勒公司214匹马力3.5L24气门V-6发动机上也首次使用Alumax的半固态锻造铝合金摇臂轴支座。
由于减少了机械加工,357铝合金半固态锻件支座的单价较球铁的还低13美分。