60万吨催化裂化装置两器施工工法
催化裂化装置两器旋风分离器更换技术探讨

梁
卓
彭振亚
周旭东
构 景武
中国石油天然气第一建设公司 河南洛阳
4 7 1 0 1 2
摘
要
随着我 国炼油建设总体技术水平的发展 , 催化裂化装置两器 内旋风分离器 的更换施工技术有了长足发展。如何利 用施工企业现有机械设 备、 根据现场催化装置特点和施工条件 , 经济合理选择施 工方案成 了施工企业 日益关注的 问题。本 文通过对旋风分离器 内部组焊 、 侧壁开孔 、 顶部开 孔、 整体更换施工技术进行 比较分析 , 对 几种施工方法进
头 1 0 沉 降段 1 1提 升 管 l 2 汽提 段 1 3待 生立 管 l 4 二 段 密 相床 1 5再 生立 管 1 6再生塞阀
同样采用临时拉杆 固定后焊接 。焊接后对旋风分离器整体进行
复查。待所有安装料腿 、 拉杆及翼阀安 装完毕 , 检查合格后对所
有加固件进行拆除。
大成 为催 化裂化装置检修的重点 。合理 的选择施工方案是保证 施工企业 目标控 制、 进度控制 、 费 用控 制重要的技术 手段 。
1旋风 分 离器 更换 的原 因
在两器 内长期 高温的作用下 ( 再生器 6 5 0 ~6 8 0  ̄ C,反应器 4 8 0 ~5 0 0  ̄ C) , 会 发生 金属 蠕变、 焊缝 开裂 、 局部变形及 衬里脱 落
图 2同轴式提升管催化裂化
首先对旋 风分离本体安装就位后 ,采用临时拉杆与两器器壁进
行 相 焊 加 固 。焊 接 完 毕 经 复 查 合 格 , 然 后对 灰 斗 部分 进 行 组 对 ,
注: l空气分布管 2待 生塞 阀 3一段密相床 4 5旋风分 离器 6外部烟气集合 管 7旋风分 离系统 8快速分离设 施 9耐磨弯
重油催化裂化装置两器组装施工技术方案
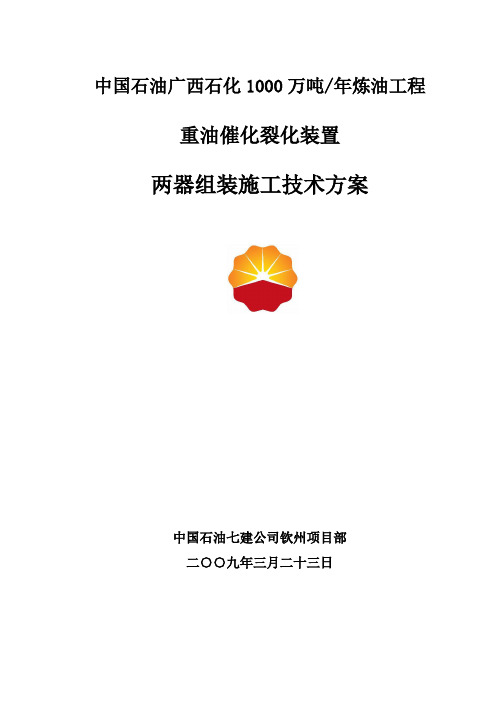
中国石油广西石化1000万吨/年炼油工程重油催化裂化装置两器组装施工技术方案中国石油七建公司钦州项目部二○○九年三月二十三日目录1 前言 (1)1.1 编制依据 (1)1。
2 适用范围 (1)2 工程概况及特点 (1)2.1 工程概况 (1)2。
2 工程特点 (2)3 施工技术方案 (3)3.1 施工程序 (3)3。
2 施工方法及技术要求 (5)4 主要技术质量标准 (12)5 质量保证措施 (13)6 HSE管理措施 (14)7 施工进度计划 (16)8 施工劳动力计划 (16)9 施工设备、机具、工装、监视及测量装置配备计划 (17)10 施工手段用料计划 (19)1 前言1。
1 编制依据1。
1.1中国石油天然气股份有限公司广西石化分公司与中国石油天然气第七建设公司签订的《重油催化裂化装置合同技术书》。
1.1。
2中国石化工程集团洛阳石油化工工程公司设计的350万吨/年重油催化裂化装置工程施工图.1.1。
3 广西石化公司所在地的气象、水文、地质资料。
1。
1。
4 石油化工建设有关的标准、规范和规定。
1。
1。
5 洛阳石油化工工程公司有关设计院标准.1.1。
6 中国石油天然气第七建设公司企业标准。
1。
2 适用范围本技术方法适用于广西石化中国石油广西石化1000万吨/年炼油工程重油催化裂化装置沉降器、再生器(以下简称两器)壳体现场组装、安装的施工。
2 工程概况及特点2.1 工程概况350万吨/年重油催化裂化装置是广西石化千万吨炼油项目的核心装置之一,工程位于广西省钦州市钦州港经济技术开发区内。
其中催化裂化部分采用美国UOP公司的两段逆流再生技术,两器主要参数如下:设备名称再生器沉降器参数容器类别一类一类介质烟气、催化剂油气、催化剂重量1938649 kg 496175 kg 设备高度56500 mm 75850 mm设计压力0。
35MPa 0.35MPa设计温度350℃550℃焊接接头系数 1.0 1。
催化裂化装置工艺流程及设备简图

催化裂化装置工艺流程及设备简图“催化裂化”装置简单工艺流程“催化裂化”装置由原料预热、反应、再生、产品分馏等三部分组成~其工艺流程见下图~主要设备有:反应器、再生器、分馏塔等。
1、反应器,又称沉降器,的总进料由新鲜原料和回炼油两部分组成~新鲜原料先经换热器换热~再与回炼油一起分为两路进入加热炉加热~然后进入反应器底部原料集合管~分六个喷嘴喷入反映器提升管~并用蒸汽雾化~在提升管中与560,600?的再生催化剂相遇~立即汽化~约有25,30%的原料在此进行反应。
汽油和蒸汽携带着催化剂进入反应器。
通过反应器~分布板到达密相段~反应器直径变大~流速降低~最后带着3,4?/?的催化剂进入旋风分离器,使其99%以上的催化剂分离,经料腿返回床层,油汽经集气室出沉降器,进入分馏塔。
2、油气进入分馏塔是处于过热状态,同时仍带有一些催化剂粉末,为了回收热量,并洗去油汽中的催化剂,分馏塔入口上部设有挡板,用泵将塔底油浆抽出经换热及冷却到0200,300C,通过三通阀,自上层挡板打回分馏塔。
挡板以上为分馏段,将反应物根据生产要求分出气体、汽油、轻柴油、重柴油及渣油。
气体及汽油再进行稳定吸收,重柴油可作为产品,也可回炼,渣油从分馏塔底直接抽出。
3、反应生焦后的待生催化剂沿密相段四壁向下流入汽提段。
此处用过热蒸汽提出催化剂,颗粒间及表面吸附着的可汽提烃类,沿再生管道通过单动滑阀到再生器提升管,最后随增压风进入再生器。
在再生器下部的辅助燃烧室吹入烧焦用的空气,以保证床层处于流化状态。
再生过程中,生成的烟通过汽密相段进入稀相段。
再生催化剂不断从再生器进入溢流管,沿再生管经另一单动滑阀到沉降器提升管与原料油汽汇合。
4、由分馏塔顶油气分离出来的富气,经气压机增压,冷却后用凝缩油泵打入吸收脱吸塔,用汽油进行吸收,塔顶的贫气进入二级吸收塔用轻柴油再次吸收,二级吸收塔顶干气到管网,塔底吸收油压回分馏塔。
5、吸收脱吸塔底的油用稳定进料泵压入稳定塔,塔顶液态烃一部分作吸收剂,另一部分作稳定汽油产品。
催化裂化两器冬季施工方案
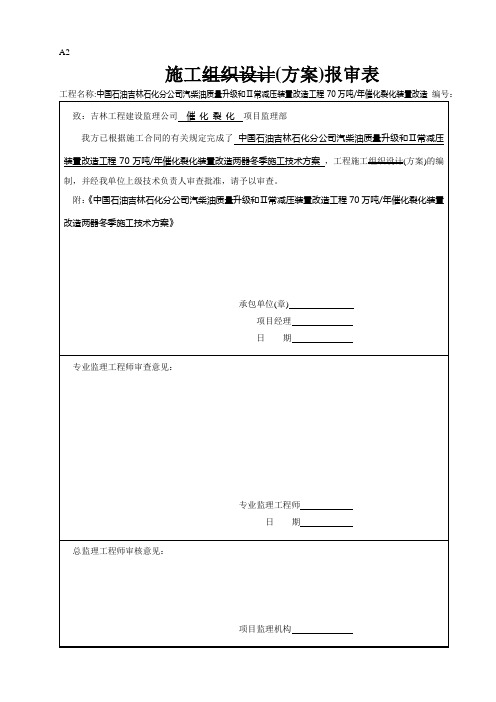
A2施工组织设计(方案)报审表《70万吨/年催化裂化装置改造两器冬季施工技术方案》审批表文件编号:JLXM-CHLH-JSFA-20-2009中国石油吉林石化分公司汽柴油质量升级和Ⅱ常减压装置改造工程70万吨/年催化裂化装置改造两器冬季施工技术方案中国石油天然气第一建设公司吉林项目经理部2009年10月19日版次:第A/1版编制及审批表中国石油吉林石化分公司汽柴油质量升级和Ⅱ常减压装置改造工程70万吨/年催化裂化装置改造两器冬季施工技术方案审批栏目录1. 工程概况--------------------------------------------------------------- 22. 编制说明--------------------------------------------------------------- 23. 冬季施工内容及其技术措施 ----------------------------------------------- 23.1. 两器封头接管焊接及衬里施工---------------------------------------------------------------------------------- 23.2. 沉降器外提升管焊接接管及衬里施工 ------------------------------------------------------------------------ 33.3. 地面组焊的筒节及保温钉施工---------------------------------------------------------------------------------- 33.4. 保温棚保温措施 ---------------------------------------------------------------------------------------------------- 33.5. 凝液排放措施 ------------------------------------------------------------------------------------------------------- 33.6. 其它管理措施 ---------------------------------------------------------------------------- 错误!未定义书签。
两器大开孔接管嵌入式补强结构设计及施工
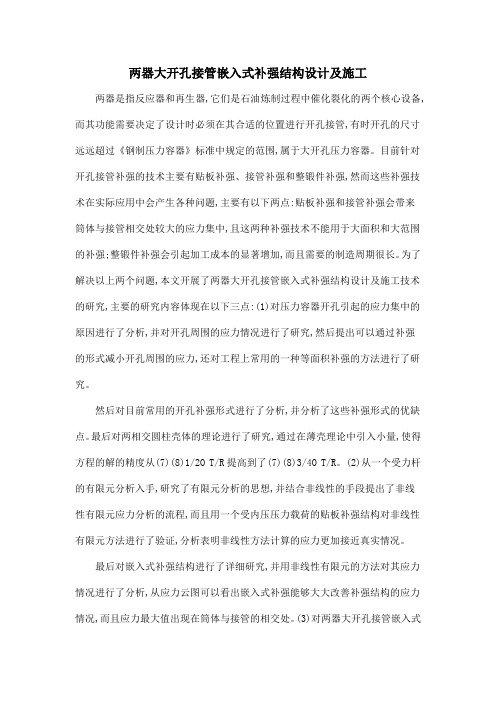
两器大开孔接管嵌入式补强结构设计及施工两器是指反应器和再生器,它们是石油炼制过程中催化裂化的两个核心设备,而其功能需要决定了设计时必须在其合适的位置进行开孔接管,有时开孔的尺寸远远超过《钢制压力容器》标准中规定的范围,属于大开孔压力容器。
目前针对开孔接管补强的技术主要有贴板补强、接管补强和整锻件补强,然而这些补强技术在实际应用中会产生各种问题,主要有以下两点:贴板补强和接管补强会带来筒体与接管相交处较大的应力集中,且这两种补强技术不能用于大面积和大范围的补强;整锻件补强会引起加工成本的显著增加,而且需要的制造周期很长。
为了解决以上两个问题,本文开展了两器大开孔接管嵌入式补强结构设计及施工技术的研究,主要的研究内容体现在以下三点:(1)对压力容器开孔引起的应力集中的原因进行了分析,并对开孔周围的应力情况进行了研究,然后提出可以通过补强的形式减小开孔周围的应力,还对工程上常用的一种等面积补强的方法进行了研究。
然后对目前常用的开孔补强形式进行了分析,并分析了这些补强形式的优缺点。
最后对两相交圆柱壳体的理论进行了研究,通过在薄壳理论中引入小量,使得方程的解的精度从(7)(8)1/2O T/R提高到了(7)(8)3/4O T/R。
(2)从一个受力杆的有限元分析入手,研究了有限元分析的思想,并结合非线性的手段提出了非线性有限元应力分析的流程,而且用一个受内压压力载荷的贴板补强结构对非线性有限元方法进行了验证,分析表明非线性方法计算的应力更加接近真实情况。
最后对嵌入式补强结构进行了详细研究,并用非线性有限元的方法对其应力情况进行了分析,从应力云图可以看出嵌入式补强能够大大改善补强结构的应力情况,而且应力最大值出现在筒体与接管的相交处。
(3)对两器大开孔接管嵌入式补强施工技术进行了研究,分别从组装排版、组装焊接和热处理三个主要方面展开。
排版的好坏是一个成功施工的开始,组装的顺序和焊接的质量才是施工成功的关键,最后的后处理则是有效消除焊接残余应力的有效方法。
大庆化学助剂厂60万吨催化裂化装置新增气压机组施工技术方案

大庆油田化学助剂厂60万吨/年催化裂化装置新增气压机组施工技术方案一九九七年二月十八日目录1.工程概述2.编制依据3.安装施工装备4.安装施工流程图5.设备基础的中间交接验收6.机组开箱检查验收及管理7.基础处理8.机组的就位与安装9.施工安全技术措施附表1 消耗材料表附表2 计量器具汇总表1. 工程概述1.1 机组概况大庆油田化学助剂厂60万吨/年催化裂化装置新增富气压缩机组机械部分,主要由2MCL526-6富气压缩机和驱动压缩机用的NG/25背压汽轮机组成,辅助设备有润滑,密封、气体冷却分离系统。
另外,根据专业要求,还没有富气入口放火炬蝶阀,气压机入口闸伐。
机组汽轮机与压缩机用齿式联轴器联接,压缩机、汽轮机的进出口均为垂直向下,本压缩机用于催化裂化装置中输送富气用,汽轮机用能量收回系统的高温中压蒸汽驱动,机组在室内安装,为双层布置,主机布置在二楼,油站及其它辅助设备置于一楼,电机及所有电元器件。
均要求防爆。
1.2 机组主要工艺技术参数:1.2.1 汽轮机型号:NG32/25进气压力:+0.2 MPa-0.3+0.1排气压力1.1 -0.1 Mpa(abs)+10℃进气温度:430 –10℃正常点功率:2335KW额定功率:2580KW额定转速:9330r/min转速范围:6531~9797r/min最大连续转速:9797r/min跳闸转速:10777r/min1.2.2 压缩机型号:2MCL526-6进气压力:0.18Mpa(abs)排气压力:1.5Mpa(abs)进气温度:45℃排气温度:45℃~120℃标准状态流量:21000M3N/n额定点轴功率:2345KW正常转速:9330r/min2. 编制依据2.1 中石化洛阳石油化工工程公司关于大庆油田化学助剂厂60万吨/年重油催化裂化装置新增气压机组的有关设计施工图;2.2 沈阳鼓风机厂关于2MCL526—6压缩机的有关图纸;2.3 化工机器安装工程施工及验收规范(通用规定)HGJ203-83。
呼和浩特石化催化裂化装置运行情况

呼和浩特石化催化裂化装置运行情况中国石油呼和浩特石化分公司刘国兵二0一一年五月六日呼和浩特石化催化裂化装置运行情况一、装置概况呼和浩特石化公司催化裂化装置是2005年在原60万吨/年装置基础上改造的,改造后装置处理能力达到90万吨/年。
装置加工的原料为二连、长庆混合原油的减压蜡油、脱沥青油和减压渣油,包括反应再生、分馏、吸收稳定、能量回收机组、余热锅炉等部分。
反应再生部分采用石油大学(北京)开发的“催化汽油辅助反应器改质降烯烃”技术,两器同轴布置。
装置于2005年8月31日停工开始改造,10月31日一次开车成功。
2006年4月进行了三机组碰头停工,5月3日三机组并入系统。
自2005年,装置共计发生非计划停工6次二、装置非计划停工情况2006年7月5日,催化装置一中段循环泵P206A封油处泄露突然着火,火势迅速燃烧至泵房顶部,将仪表电缆全部烧坏,造成装置紧急停工。
2006年12月22日由于沉降器汽提段结焦造成非计划停工。
2008年前四个月,装置连续发生了2.2回炼油喷嘴焊道断裂着火事故、3.9主风低流量自保切断进料、3.20再生器超压主风机停机非计划停工事故和4月9日主风分布管损坏停工抢修非计划停工。
1、2006年7月5日一中段泵封油泄漏着火事故2006年7月5日,催化装置一中段循环泵P206A封油处泄露突然着火,火势迅速燃烧至泵房顶部,将仪表电缆全部烧坏,造成装置紧急停工。
由于仪表全部失灵,造成油气串入再生器,烟囱冒黄烟。
装置全面停工抢修。
此次事故的主要原因是一中段泵封油管线活接泄漏,造成一中段油漏出导致着火,由于装置主要的仪表光缆大部分布置在泵房顶部,彩板泵房着火后将光缆烧断,装置非计划停工。
经抢修至7月18日装置开工正常2、2006年12月22日沉降器汽提段结焦非计划停工事故2006年12月22日07:20分,由于待生线路流化受阻,装置切断进料,22日11:30重新流化喷油,但待生线路仍不能满足催化剂流化的要求,于14:00再次切段进料,进行流化试验,通过正顶、反顶等措施试图疏通,经过22日、23日、24日上午的处理,效果不佳,随决定停工卸剂处理。
催化裂化装置介绍

装置工艺流程简介
2、吸收部分 不凝富气从容301进入塔301/1底,自下而上与
来自泵203或泵204从塔25层进入的粗汽油,以 及自泵303或泵306来的从塔顶进入的稳定汽油接 触,气体中≥C3的组分大部分被吸收下来,剩余 还含有少量≥C3组分的气体(贫气)离开塔顶进 入再吸收塔(塔302)底。塔301/1第10层和第 16层和第15层,设置中段回流,以取走吸收热。 贫气在塔302内自下而上与贫吸收油(轻柴油) 逆流接触,以脱去气体中夹带的汽油组分,未被 吸收的气体(干气)作为产品引入瓦斯管网去脱 硫装置处理后作燃烧气。塔底的富吸收油则靠塔 302的压力压至塔201第16或19层分馏。
催化裂化催化剂
在催化裂化反应过程中,高温的 催化裂化催化剂不但为原料分子的转 化提供活性中心,同时也是原料分子 发生反应的场所(烃分子需吸附在酸 性中心表面),并作为热载体为反应 过程用热提供热量。
催化剂使用情况
一催化装置催化剂以CC-200D、 ZC-7000MM为主剂、掺用少量 LANK-98、RMS-8、平衡剂。
一、车间简介
一、车间简介
炼油分部联合五车间成立于2001年11月, 管辖一催化装置、二催化装置、干气提浓乙烯和 油品精制(洗涤)联合装置,是炼油主要二次加 工单位之一。其中一催化装置、二催化装置是中 石化集团公司A类达标装置,是重油轻质化的骨 干装置。车间现有职工206人,高级工程师5人, 中级职称9人,高级操作师1人,高级技师9人,技 师3人。
装置工艺流程简介
2、瓦斯脱硫部分:
自一催化来的瓦斯(P=0.55Mpa,t=32℃) 经气液分离罐(容-17)分离出凝缩油后, 进入瓦斯脱硫塔(塔-7)下部,与塔上部 下来的贫液(G=18~30m3/h,浓度为 (15~25×10-2)逆向接触,瓦斯中的酸 性气立即与贫液起化学反应,反应后生成 的富液从塔底流进富液闪蒸罐(容-15), 而脱除了酸性气后的净化瓦斯自塔顶出来 后送至系统高压瓦斯管网。
催化裂化的装置简介及工艺流程
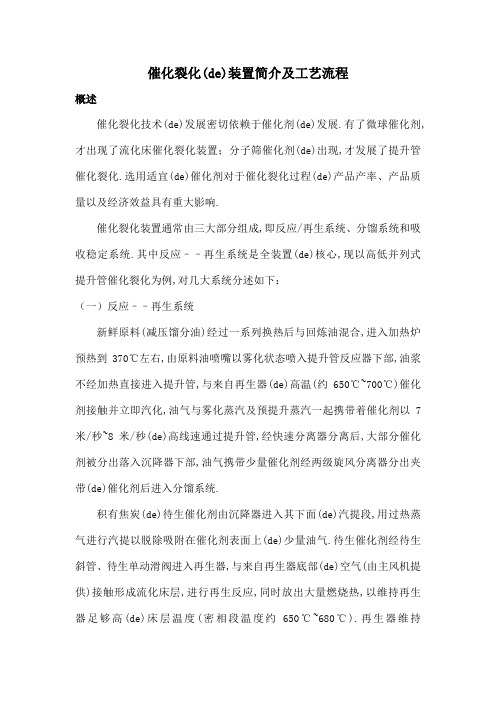
催化裂化(de)装置简介及工艺流程概述催化裂化技术(de)发展密切依赖于催化剂(de)发展.有了微球催化剂,才出现了流化床催化裂化装置;分子筛催化剂(de)出现,才发展了提升管催化裂化.选用适宜(de)催化剂对于催化裂化过程(de)产品产率、产品质量以及经济效益具有重大影响.催化裂化装置通常由三大部分组成,即反应/再生系统、分馏系统和吸收稳定系统.其中反应––再生系统是全装置(de)核心,现以高低并列式提升管催化裂化为例,对几大系统分述如下:(一)反应––再生系统新鲜原料(减压馏分油)经过一系列换热后与回炼油混合,进入加热炉预热到370℃左右,由原料油喷嘴以雾化状态喷入提升管反应器下部,油浆不经加热直接进入提升管,与来自再生器(de)高温(约650℃~700℃)催化剂接触并立即汽化,油气与雾化蒸汽及预提升蒸汽一起携带着催化剂以7米/秒~8米/秒(de)高线速通过提升管,经快速分离器分离后,大部分催化剂被分出落入沉降器下部,油气携带少量催化剂经两级旋风分离器分出夹带(de)催化剂后进入分馏系统.积有焦炭(de)待生催化剂由沉降器进入其下面(de)汽提段,用过热蒸气进行汽提以脱除吸附在催化剂表面上(de)少量油气.待生催化剂经待生斜管、待生单动滑阀进入再生器,与来自再生器底部(de)空气(由主风机提供)接触形成流化床层,进行再生反应,同时放出大量燃烧热,以维持再生器足够高(de)床层温度(密相段温度约650℃~680℃).再生器维持~(表)(de)顶部压力,床层线速约米/秒~米/秒.再生后(de)催化剂经淹流管,再生斜管及再生单动滑阀返回提升管反应器循环使用.烧焦产生(de)再生烟气,经再生器稀相段进入旋风分离器,经两级旋风分离器分出携带(de)大部分催化剂,烟气经集气室和双动滑阀排入烟囱.再生烟气温度很高而且含有约5%~10%CO,为了利用其热量,不少装置设有CO锅炉,利用再生烟气产生水蒸汽.对于操作压力较高(de)装置,常设有烟气能量回收系统,利用再生烟气(de)热能和压力作功,驱动主风机以节约电能.(二)分馏系统分馏系统(de)作用是将反应/再生系统(de)产物进行分离,得到部分产品和半成品.由反应/再生系统来(de)高温油气进入催化分馏塔下部,经装有挡板(de)脱过热段脱热后进入分馏段,经分馏后得到富气、粗汽油、轻柴油、重柴油、回炼油和油浆.富气和粗汽油去吸收稳定系统;轻、重柴油经汽提、换热或冷却后出装置,回炼油返回反应––再生系统进行回炼.油浆(de)一部分送反应再生系统回炼,另一部分经换热后循环回分馏塔.为了取走分馏塔(de)过剩热量以使塔内气、液相负荷分布均匀,在塔(de)不同位置分别设有4个循环回流:顶循环回流,一中段回流、二中段回流和油浆循环回流.催化裂化分馏塔底部(de)脱过热段装有约十块人字形挡板.由于进料是460℃以上(de)带有催化剂粉末(de)过热油气,因此必须先把油气冷却到饱和状态并洗下夹带(de)粉尘以便进行分馏和避免堵塞塔盘.因此由塔底抽出(de)油浆经冷却后返回人字形挡板(de)上方与由塔底上来(de)油气逆流接触,一方面使油气冷却至饱和状态,另一方面也洗下油气夹带(de)粉尘.(三)吸收--稳定系统从分馏塔顶油气分离器出来(de)富气中带有汽油组分,而粗汽油中则溶解有C3、C4甚至C2组分.吸收––稳定系统(de)作用就是利用吸收和精馏(de)方法将富气和粗汽油分离成干气(≤C2)、液化气(C3、C4)和蒸汽压合格(de)稳定汽油.装置简介(一)装置发展及其类型1.装置发展催化裂化工艺产生于20世纪40年代,是炼油厂提高原油加工深度(de)一种重油轻质化(de)工艺.20世纪50年代初由ESSO公司(美国)推出了Ⅳ型流出催化装置,使用微球催化剂(平均粒径为60—70tan),从而使催化裂化工艺得到极大发展.1958年我国第一套移动床催化裂化装置在兰州炼油厂投产.1965年我国自己设计制造施工(de)Ⅳ型催化装置在抚顺石油二厂投产.经过近40年(de)发展,催化裂化已成为炼油厂最重要(de)加工装置.截止1999年底,我国催化裂化加工能力达8809.5×104t/a,占一次原油加工能力(de)33.5%,是加工比例最高(de)一种装置,装置规模由(34—60)×104t /a发展到国内最大300×104t/a,国外为675×104t/a.随着催化剂和催化裂化工艺(de)发展,其加工原料由重质化、劣质化发展至目前全减压渣油催化裂化.根据目(de)产品(de)不同,有追求最大气体收率(de)催化裂解装置(DCC),有追求最大液化气收率(de)最大量高辛烷值汽油(de)MGG工艺等,为了适应以上(de)发展,相应推出了二段再生、富氧再生等工艺,从而使催化裂化装置向着工艺技术先进、经济效益更好(de)方向发展.2.装置(de)主要类型催化裂化装置(de)核心部分为反应—再生单元.反应部分有床层反应和提升管反应两种,随着催化剂(de)发展,目前提升管反应已取代了床层反应.再生部分可分为完全再生和不完全再生,一段再生和二段再生(完全再生即指再生烟气中CO含量为10—6级).从反应与再生设备(de)平面布置来讲又可分为高低并列式和同轴式,典型(de)反应—再生单元见图2—4、图2—5、图2—6、图2—7,其特点见表2—11.(二)装置单元组成与工艺流程1.组成单元催化裂化装置(de)基本组成单元为:反应—再生单元,能量回收单元,分馏单元,吸收稳定单元.作为扩充部分有:干气、液化气脱硫单元,汽油、液化气脱硫醇单元等.各单元作用介绍如下.(1)反应—再生单元重质原料在提升管中与再生后(de)热催化剂接触反应后进入沉降器(反应器),油气与催化剂经旋风分离器与催化剂分离,反应生成(de)气体、汽油、液化气、柴油等馏分与未反应(de)组分一起离开沉降器进入分馏单元.反应后(de)附有焦炭(de)待生催化剂进入再生器用空气烧焦,催化剂恢复活性后再进入提升管参加反应,形成循环,再生器顶部烟气进入能量回收单元.(2)三机单元所谓三机系指主风机、气压机和增压机.如果将反一再单元作为装置(de)核心部分,那么主风机就是催化裂化装置(de)心脏,其作用是将空气送人再生器,使催化剂在再生器中烧焦,将待生催化剂再生,恢复活性以保证催化反应(de)继续进行.增压机是将主风机出口(de)空气提压后作为催化剂输送(de)动力风、流化风、提升风,以保持反—再系统催化剂(de)正常循环.气压机(de)作用是将分馏单元(de)气体压缩升压后送人吸收稳定单元,同时通过调节气压机转数也可达到控制沉降器顶部压力(de)目(de),这是保证反应再生系统压力平衡(de)一个手段.(3)能量回收单元利用再生器出口烟气(de)热能和压力使余热锅炉产生蒸汽和烟气轮机作功、发电等,此举可大大降低装置能耗,目前现有(de)重油催化裂化装置有无此回收系统,其能耗可相差1/3左右.(4)分馏单元沉降器出来(de)反应油气经换热后进入分馏塔,根据各物料(de)沸点差,从上至下分离为富气(至气压机)、粗汽油、柴油、回炼油和油浆.该单元(de)操作对全装置(de)安全影响较大,一头一尾(de)操作尤为重要,即分馏塔顶压力、塔底液面(de)平稳是装置安全生产(de)有力保证,保证气压机人口放火炬和油浆出装置系统(de)通畅,是安全生产(de)必备条件. (5)吸收稳定单元经过气压机压缩升压后(de)气体和来自分馏单元(de)粗汽油,经过吸收稳定部分,分割为干气、液化气和稳定汽油.此单元是本装置甲类危险物质最集中(de)地方.(6)产品精制单元包括干气、液化气脱硫和汽油液化气脱硫醇单元该两部分,干气、液化气在胺液(乙醇胺、二乙醇胺、Ⅳ—甲基二乙醇胺等)作用下、吸收干气、液化气中(de)H2S气体以达到脱除H2S(de)目(de).汽油和液化气在碱液状态中在磺化酞氰钴或聚酞氰钻作用下将硫醇氧化为二硫化物,以达到脱除硫醇(de)目(de).2.工艺流程工艺原则流程见图2—8.原料油由罐区或其他装置(常减压、润滑油装置)送来,进入原料油罐,由原料泵抽出,换热至200—300°C左右,分馏塔来(de)回炼油和油浆一起进入提升管(de)下部,与由再生器再生斜管来(de)650~700°C再生催化剂接触反应,然后经提升管上部进入分馏塔(下部);反应完(de)待生催化剂进入沉降器下部汽提段.被汽提蒸汽除去油气(de)待生剂通过待生斜管进入再生器下部烧焦罐.由主风机来(de)空气送人烧焦罐烧焦,并同待生剂一道进入再生器继续烧焦,烧焦再生后(de)再生催化剂由再生斜管进人提升管下部循环使用.烟气经一、二、三级旋分器分离出催化剂后,其温度在650~700°C,压力0.2-0.3MPa(表),进人烟气轮机作功带动主风机,其后温度为500—550°C,压力为0.01MPa(表)左右,再进入废热锅炉发生蒸汽,发汽后(de)烟气(温度大约为200℃左右)通过烟囱排到大气.反应油气进入分馏塔后,首先脱过热,塔底油浆(油浆中含有2%左右催化剂)分两路,一路至反应器提升管,另一路经换热器冷却后出装置.脱过热后油气上升,在分馏塔内自上而下分离出富气、粗汽油、轻柴油、回炼油.回炼油去提升管再反应,轻柴油经换热器冷却后出装置,富气经气压机压缩后与粗汽油共进吸收塔,吸收塔顶(de)贫气进入再吸收塔由轻柴油吸收其中(de)C4-C5,再吸收塔顶干气进入干气脱硫塔脱硫后作为产品出装置,吸收塔底富吸收油进入脱吸塔以脱除其中(de)C2.塔底脱乙烷汽油进入稳定塔,稳定塔底油经碱洗后进入脱硫醇单元脱硫醇后出装置,稳定塔顶液化气进入脱硫塔脱除H,S,再进入脱硫醇单元脱硫醇后出装置.(脱硫脱硫醇未画出)(三)化学反应过程1.催化裂化反应(de)特点催化裂化反应是在催化剂表面上进行(de),其反应过程(de)7个步骤如下:①气态原料分子从主流扩散到催化剂表面;②原料分子沿催化剂外向内扩散;③原料分子被催化剂活性中心吸附;④原料分子发生化学反应;⑤产品分子从催化剂内表面脱附;⑥产品分子由催化剂外向外扩散;⑦产品分子扩散到主流中.重质原料反应生成目(de)产品可用下图表示:2.催化裂化反应种类石油馏分是由十分复杂(de)烃类和非烃类组成,其反应过程十分复杂,种类繁多,大致分为几个类型.(1)裂化反应是主要(de)反应.即C—C键断裂,大分子变为小分子(de)反应.(2)异构化反应是重要(de)反应.即化合物(de)相对分子量不变,烃类分子结构和空间位置变化,所以催化裂化产物中会有较多异构烃.(3)氢转移反应是一个烃分子上(de)氢脱下来加到另一个烯烃分子上,使其烯烃饱和,该反应是催化裂化特有(de)反应.虽然氢转移反应会使产品安定性变好,但是大分子(de)烃类反应脱氢将生成焦炭.(4)芳构化反应烷烃、烯烃环化生成环烷烃和环烯烃,然后进一步氢转移反应生成芳烃,由于芳构化反应使汽油、柴油中芳烃较多.除以上反应外,还有甲基转移反应、叠合反应和烷基化反应等.(四)主要操作条件及工艺技术特点1.主要操作条件因不同(de)工艺操作条件不尽相同,表2—12列出一般一段再生催化裂化(de)主要操作条件.2.工艺技术特点(1)微球催化剂(de)气—固流态化催化裂化确切一点应该叫作流化催化裂化.微球催化剂(60—70/1m 粒径)在不同气相线速下呈现不同状态,可分为固定床(即催化剂不动)、流化床(即催化剂只在一定(de)空间运动)和输送床(即催化剂与气相介质一同运动而离开原来(de)空间)三种.过程是流化床,所以微球催化剂(de)气—固流态化是催化裂化工艺得以发展(de)基础,从而使反应—再生能在不同(de)条件下得以实现.(2)催化裂化(de)化学反应最主要(de)反应是大分子烃类裂化为小分子烃类(de)化学反应,从而使原油中大于300℃馏分(de)烃类生成小分子烃类、气体、液化气、汽油、柴油等,极大地增加了炼油厂(de)轻质油收率,并能副产气体和液化气.(五)催化剂及助剂1.催化剂烃类裂化反应,应用热裂化工艺也能完成,但是有了催化剂(de)参加,其化学反应方式不同,所以导致二类工艺(de)产品性质和产品分布都不同.目前催化裂化所使用(de)催化剂都是分子筛微球催化剂,根据不同产品要求可制造出各种型号(de)催化剂.但其使用性能要求是共同(de),即高活性和选择性,良好(de)水热稳定性,抗硫、氮、重金属(de)中毒;好(de)强度,易再生,流化性能好等.目前常见(de)有重油催化裂化催化剂、生产高辛烷值汽油催化剂、最大轻质油收率催化剂、增加液化气收率催化剂和催化裂解催化剂等.由于催化裂化原料(de)重质化,使重油催化剂发展十分迅速,目前国内全渣油型催化剂性能见表2—13.2.催化裂化助剂为了补充催化剂(de)其他性能,近年来发展了多种起辅助作用(de)助催化剂,这些助剂均以剂(de)方式,加到裂化催化剂中起到除催化裂化过程外(de)其他作用.如促进再生烟气中CO转化为C02,提高汽油辛烷值,钝化原料中重金属对催化剂活性毒性,降低烟气中(de)SOx(de)含量等各类助剂,它们绝大多数也是制造成与裂化催化剂一样(de)微球分别加入再生器内,但占总剂量很少,一般在1%—3%,所以每天添加量只有10-1000kS/d左右.CO助燃剂为SiO2—Al2O3细粉上载有活性金属铂制成.辛烷值助剂大多是含有15%-20%ZSM—5分子筛(de)Si—Al微球剂.而金属钝化剂为液态型含锑(de)化合物,将其注入原料油中,使其分解(de)金属锑沉积在催化剂上以钝化Ni(de)活性.(六)原料及产品性质1.催化裂化原材料各类催化裂化所使用(de)原材料不尽相同,现将一般所使用(de)原材料主要性质汇总,见表2—14.2.产品性质产品性质见表2-15。
两器吊装中常用的两种封头翻转吊装工艺
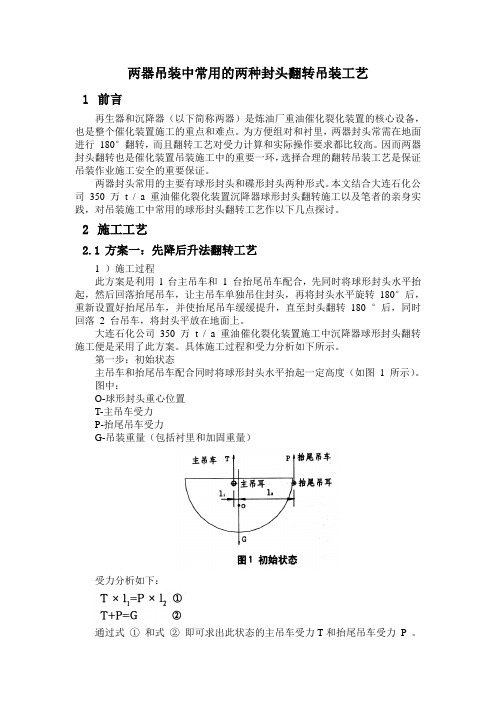
两器吊装中常用的两种封头翻转吊装工艺1前言再生器和沉降器(以下简称两器)是炼油厂重油催化裂化装置的核心设备,也是整个催化装置施工的重点和难点。
为方便组对和衬里,两器封头常需在地面进行180°翻转,而且翻转工艺对受力计算和实际操作要求都比较高。
因而两器封头翻转也是催化装置吊装施工中的重要一环,选择合理的翻转吊装工艺是保证吊装作业施工安全的重要保证。
两器封头常用的主要有球形封头和碟形封头两种形式。
本文结合大连石化公司350 万t / a 重油催化裂化装置沉降器球形封头翻转施工以及笔者的亲身实践,对吊装施工中常用的球形封头翻转工艺作以下几点探讨。
2施工工艺2.1方案一:先降后升法翻转工艺1 )施工过程此方案是利用l 台主吊车和1 台抬尾吊车配合,先同时将球形封头水平抬起,然后回落抬尾吊车,让主吊车单独吊住封头,再将封头水平旋转180°后,重新设置好抬尾吊车,并使抬尾吊车缓缓提升,直至封头翻转180 °后,同时回落2 台吊车,将封头平放在地面上。
大连石化公司350 万t / a 重油催化裂化装置施工中沉降器球形封头翻转施工便是采用了此方案。
具体施工过程和受力分析如下所示。
第一步:初始状态主吊车和抬尾吊车配合同时将球形封头水平抬起一定高度(如图 1 所示)。
图中:O-球形封头重心位置T-主吊车受力P-抬尾吊车受力G-吊装重量(包括衬里和加固重量)受力分析如下:通过式①和式②即可求出此状态的主吊车受力T和抬尾吊车受力P 。
第二步:中间状态(一)回落抬尾吊车至不受力后,撤下抬尾吊车,让主吊车单独吊住封头,再将封头水平旋转180 °(如图 2 所示)。
图中:O -球形封头重心位置T -主吊车受力此时吊装重量完全由主吊车承担,即T =G 。
第三步:中间状态(二)重新设置好抬尾吊车,并使抬尾吊车缓缓提升,使球形封头翻转到一定角度(如图3 所示)。
图中O -球形封头重心位置T -主吊车受力P -抬尾吊车受力G -吊装重量(包括衬里和加固重量)受力分析如下:通过式①和式②即可求出此状态的主吊车受力T 和抬尾吊车受力P 。
催化裂化装置反再系统施工技术方法

催化裂化装置反再系统施工技术方法摘要:反再系统(反应器和再生器)是催化裂化装置的核心设备,是影响催化裂化装置安全和经济效益的关键因素,两器的施工工艺复杂,壳体厚度相差较大,焊接工作量和施工难度比较大,焊接变形较难控制、吊装难度大、内件安装精度要求高.本文我们主要以青海大美项目60万吨/年DMTO装置反再系统为例来探讨“两器”的组对安装工艺流程。
关键词:反应器、再生器、壳体组装、焊接、压力试验。
一、施工概述1、施工方法反应器、再生器采用“立式组装法”施工。
分段组对时按排版图的顺序和位置,采用立装法,由下至上依次组装各筒节,形成分段筒体。
分段安装时采用正装法将各分段筒体按顺序进行吊装。
封头、椎体需在组装平台上单独进行组装。
顶部封头预制成型组焊合格后,需翻转进行衬里施工。
顶部封头吊装前需将旋风、料腿等内部构件临时放置在筒体内。
2、反应器、再生器主要设备参数设备名称反应器(R1101)再生器(R1102)容器类别III类(A2级)II类(D2级)设计压力 MPa 0.25 0.25工作压力 MPa 0.2―0.3 0.2―0.3设计温度℃介质550,壳体350 介质720,壳体350工作温度℃450―550 600―720介质甲醇,油气,催化剂烟气,催化剂容器规格ϕ15600/ϕ11800×45090×36ϕ7000/ϕ5500×25300×22/24金属净重(不含衬里)600t 160t热处理局部热处理不做热处理液压试验 MPa3、反应器、再生器主要吊装分段参数筒节预制组对时可采用75t汽车吊两台,280t履带吊一台,400t履带吊一台进行现场分片分段组装。
其中反应器分四段、再生器分二段进行吊装,反应器、再生器分段吊装时第一段均采用400t履带吊吊装,其余各段吊装以及封头翻转均采用600t履带吊主吊,采用400t履带吊溜尾配合。
二、主要施工程序筒体、封头成品半成品及旋风分离器等内件检验验收→封头、椎体等组装成型→筒节、裙座组装成型→分段组装焊接→焊缝无损检测→接管安装→各段部分内件安装→劳动保护安装→基础验收→分段吊装(除封头外)→段之间环焊缝热处理、无损检测→上封头衬里→上封头翻转、吊装→旋风系统及内件安装→拆除临时加固件→交工验收。
(整理)60万吨年重油催化裂解装置大型设备吊装施工方案(修改版)
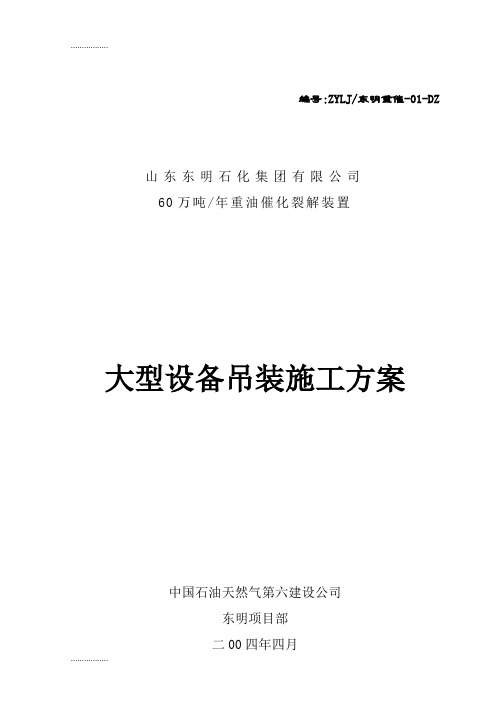
编号:ZYLJ/东明重催-01-DZ山东东明石化集团有限公司60万吨/年重油催化裂解装置大型设备吊装施工方案中国石油天然气第六建设公司东明项目部二00四年四月目录1、工程概况2、编制依据3、施工准备4、施工工艺流程及吊装过程控制5、受力计算6、质量保证措施7、健康、安全、环保(HSE)保证措施8、人力需用情况9、施工机具及手段用料10、附件1 工程概况1.1 工程简介山东东明石化集团有限公司投资新建的60万吨/年重油催化裂解装置中共有需要大型吊装机具进行吊装作业的同轴式沉降-再生器(现场制安)1台、催化剂罐(冷、热、废)3台、提升管反应器1台、外取热器1台、固定床反应器2台、塔类设备7台、容器类设备9台、换热器36台、空冷器管束22片、构-201(楼梯间)、余热锅炉1台以及高空的梯子、平台、管线等(容器、换热器、空冷器管束因就位高度较高,设备本体体积大,常规吊车难以完成)。
根据设备的高度、外形尺寸和重量,建设单位统一安排大型吊装机具采用250吨履带吊车主吊。
主要待吊装的设备规格尺寸详见附表1—《主要设备吊装参数及吊装方法一览表》。
其中,同轴式沉降-再生器、提升管反应器、外取热器、催化剂罐(冷、热、废,共3台)、催化分馏塔、吸收塔、解吸塔、稳定塔、构201为分段吊装,空中组焊。
塔类设备及分段到货设备均采用250吨履带吊主吊,40吨汽车吊、35吨汽车吊联合溜尾;容器、换热器以及空冷器管束采用250吨履带吊直接吊装。
催化装置塔类设备分段参数及设备吊装吊耳设置详见附表2。
1.2 工程特点1.2.1 由于施工工期紧,考虑到符合HSE要求,塔的梯平栏、部分内件及附塔管线等皆于地面安装,后与塔体一起吊装。
1.2.2 场地狭窄,设备倒运较多。
另外,吊装场地土地疏松,这给250吨履带吊车的行走和站位增加了难度。
1.2.3 施工季节气候炎热,空中组焊对接吊装量大,必须做好春夏季节施工技术措施以确保安全、工期与质量。
催化裂化两器压力控制

一、沉降器压力控制正常操作:正常工况下的沉降器压力采用分馏塔顶压力控制富气压缩机组的转速来控制的。
此时,富气压缩机入口放火炬大、小阀均处于关闭状态,同时富气压缩机组反喘振控制系统中,用调节反飞动量来避免富气压缩机组喘振。
影响因素:1、提升管总进料量的变化,总进料量增加,压力上升。
2、原料油组份的变化,原料易裂解,反应压力上升。
3、反应温度变化,反应温度上升,反应压力上升。
4、反应汽提蒸汽量变化,增加汽提蒸汽量,反应压力上升。
5、原料油带水,反应压力明显上升。
6、分馏塔底液面变化,影响分馏塔上部负荷变化,而使反应压力随着变化,负荷过大,则反应压力高。
分馏塔液面超高,造成液封,反应压力上升。
要特别注意,不允许此情况发生。
7、急冷剂量大,反应压力上升。
8、气压机吸入压力的变化,气压机吸入压力上升,反应压力上升。
(如反喘振量变化,气压机故障等)。
9、分馏塔顶蝶阀开度变化。
10、污汽油回炼量变化。
11、分馏塔顶油气分离器液面超高,反应压力急剧上升。
12、分馏塔顶回流及冷回流量变化。
13、当气压机组由汽轮机调节机组转速时,装置内的中压蒸汽压力及流量变化影响气压机转速,导致反应压力的变化。
14、分馏塔顶油气冷却效果变化,冷却效果好,反应压力下降。
15、吸收塔冲塔使富吸收油大量带汽油至分馏塔,使反应压力上升。
停工调节方法:1、两器烘器阶段,通过遥控设在沉降器顶的放空阀控制沉降器压力,其目的是控制两器升温速度。
2、建立汽封至两器流化试验阶段,用分馏塔顶压力控制分馏塔顶出口油气管道上的蝶阀保证反应压力平稳。
3、反应进油后至启动富气压缩机前,采用分馏塔顶压力控制压缩机入口放火炬小阀(微调),配以遥控压缩机入口放火炬大阀(粗调),保证反应压力平稳。
4、汽轮机调速器故障,若汽轮机调速器故障,则将调速器于固定位置,使机组处于恒速运行状态,采用分馏塔顶压力和富气压缩机组反喘振调节系统组成低选,控制气压机出口循环线上的反喘振调节阀,同时投用控制放火炬小阀以保证反应压力的平稳。
催化裂化中两器预制安装施工工艺探讨

催化裂化中两器预制安装施工工艺探讨摘要:石油炼制工业是国民经济的重要支柱产业,影响着人们日常生活的方方面面,其中催化裂化(FCC)作为石油炼制企业的主要生产装置在石油加工中占据着重要地位。
催化裂化装置中最关键核心部分是反应沉降器和再生器(以下都简称为“两器”),两器的预制安装施工工艺的质量关系着整个装置是否能满足催化裂化工作需要。
本文通过分析1200万t/a炼油项目中340万t/a催化裂化装置的反应沉降器、再生器的预制及组焊安装流程和技术要求,分析两器预制安装施工工艺,以便提供有效参考。
关键词:催化裂化;两器;预制安装;施工工艺1200万t/a炼油项目中340万t/a催化裂化装置目前在我国石油炼制企业中算是较为常规的装置,如中化泉州就使用该款装置。
反应沉降器和再生器以及该两器所用框架是催化裂化装置的核心部分,由于以上装置结构复杂、体积庞大,如两器需要在特定工厂中进行分片预制后经过运输到指定施工现场,在施工现场进行焊成段后再安装就位。
由于两器预制安装施工工艺复杂,设备庞大且造价昂贵,对于石油生产和石油企业经济效益影响巨大,因此两器预制安装施工工艺必须严格遵守相关操作规范,才能确保催化裂化两器装置质量符合生产要求。
1做好前期策划两器因为超大、超重、超高等特点,在吊装上需要投入大量人力物力,由于环境复杂、穿插吊装频率高等特点,需要对前期工作进行策划和安排,主要包括技术、吊索具和吊装现场几方面的策划。
1.1技术策划根据预制、分段、附件安装等安排初步选择吊装机械和吊装方法,以及预留场地的规划选址确定。
1.2设备策划在充分做好当地大型设备情况调研的前提下,根据两器和两器框架的重量、结构特点及施工工期,做好大型吊装设备如1000t履带吊车的准备,以便满足吊装工作需要。
1.3吊索具策划根据吊装设备的重量及吊装方法,策划好吊索具需求和采购方案计划。
1.4人员策划根据两器的吊装设备和施工工期,策划相关工作人员需求计划,并做好相关运输协调工作。
特殊技术措施费用的索赔过程与技巧(实例解析)

特殊技术措施费用的索赔1摘要按预算定额结算的工程项目,除一般措施费用按工程结算取费程序计取之外,还有一部份施工组织措施费用,是按工程实际实施情况计取的,这一部分费用相对于一般措施费而言通常称为特殊措施费。
该案例叙述了某项目工程施工中发生的一部分施工组织措施费用和现场变更费用成功索赔的过程和技巧。
2关键词:两器、特殊技术措施费用、签证、索赔。
3正文3.1某石油化工有限公司,建设一套60万吨/年重油催化炼油装置,我公司经投标取得该项目工程装置的安装工程施工承包标段,其中,催化裂化装置的两器现场分片组装,也属于我方工程施工承包范围内的工作。
该案例就是有关两器施工过程中索赔的案例。
3.2经验告诉我们,该装置的工期和利润点,基本上都集中在两器上,所以,两器施工是该项目施工的难点、重点。
首先,两器的工期比较长,虽然是现场分片组焊,但是,分片供货、超大型封头定点厂商旋压,影响供货的因素比较多,还有一些是不可控因素,所以,属于长周期管理的设备,是该装置的网络工期控制计划的关键路线。
另一方面,两器设备现场分片组焊,不仅技术要求高、交叉作业多(衬里施工、内件安装等)、协调难度大,施工成本投入上人力和一般施工机械相对密集的同时,还涉及到大型吊装机械即275吨履带吊的进、出场和使用管理。
大型吊装机械进出场费用和台班使用单价都很高,合理利用场地、提高工作效率,是降低施工成本、保证工期的重要措施。
但是,作为施工单位,保证工程质量按期完成施工任务,降低乃至于杜绝发生安全事故,还要考虑工程施工成本管理,该取的费用必须取回来。
本文就两器现场组焊安装过程中有关特殊技术措施费用的索赔的策划过程进行记述和总结。
3.3两器施工有关的特殊技术措施费用涉及的项目有以下几个方面。
3.3.1临时设施的搬迁。
根据业主方和监理公司批准的《施工组织设计》中平面布置,我公司进驻施工现场后搭设了临时EPS夹芯板房270平米,整体集装箱板房14栋,安装后经过确认,均在施工组织设计规划范围内。
大型催裂化反应器封头及旋风系统整体双机抬吊施工工法(2)

大型催裂化反应器封头及旋风系统整体双机抬吊施工工法大型催裂化反应器封头及旋风系统整体双机抬吊施工工法一、前言大型催裂化反应器封头及旋风系统整体双机抬吊施工工法是用于大型催化裂化装置封头和旋风系统的安装方法。
本文将详细介绍该工法的特点、适应范围、工艺原理、施工工艺、劳动组织、机具设备、质量控制、安全措施、经济技术分析以及工程实例。
二、工法特点该工法特点如下:1. 双机抬吊:采用两台起重机同时协同作业,提高施工效率。
2. 整体吊装:封头和旋风系统一起进行吊装,减少吊装次数,减少施工周期。
3.安全可靠:采取多种安全措施,确保施工过程中的安全。
三、适应范围该工法适用于大型催化裂化装置封头和旋风系统的安装,适用于需求较高的化工、石油等行业。
四、工艺原理该工法通过双机抬吊的方式,将催化裂化装置封头和旋风系统整体吊装到指定位置。
其原理为首先通过计算和预测确定起重机的位置和高度,然后进行协同作业,确保吊装过程中的平衡和稳定。
在施工过程中,需要采取一系列技术措施,如加固梁、牵引索等,以确保吊装的安全和顺利进行。
五、施工工艺施工工艺包括以下几个阶段:1. 设计和准备阶段:根据实际情况进行工艺设计和准备工作,包括选定起重机的型号和数量、确定起重机的位置和高度等。
2. 预制阶段:根据设计要求进行封头和旋风系统的预制工作,包括制作封头和旋风系统的零部件、进行检验和质量控制等。
3. 吊装阶段:根据预先确定的吊装计划进行吊装作业,采用双机抬吊的方式,确保封头和旋风系统整体吊装到指定位置。
4. 安装和调试阶段:进行封头和旋风系统的安装和调试工作,包括连接管道、调整位置等。
5. 完工阶段:进行工程验收和完工报告,确保施工过程完成。
六、劳动组织施工过程中,需要合理安排劳动力和团队,包括起重机操作人员、工程师和工人等。
同时,还需要进行周密的协调和沟通,确保各个环节的顺利进行。
七、机具设备该工法需要使用起重机、加固梁、牵引索等机具设备。
催化裂化装置两器互窜风险量化分析

催化裂化装置两器互窜风险量化分析【摘要】本文针对催化裂化装置应急处理时的两器互窜风险进行研究,介绍了量化两器互窜风险的意义,并给出了具体的量化计算过程。
同时根据计算过程及结果提出其应用的意义。
关键字:催化裂化;两器;互窜;反应器一、背景介绍催化裂化装置紧急停工,最关键的步骤是切断两器防止两器互窜。
主要原因为停工初期,沉降器内为油气环境,再生器内为空气环境,两器互窜有混合气体爆炸的风险。
而防止两器互窜或爆炸的手段除了及时切断两器外,最主要的是在最短的时间内将反应器内的油气利用蒸汽置换干净,将可燃介质置换出系统,从根本上杜绝互窜爆炸的可能。
此篇分析意图计算出蒸汽置换反应器油气时间,从而将两器互窜风险在时间上进行量化。
二、反应器介绍四催化装置反应器为常规形式反应器,提升管由沉降器中心穿过,分为内、外提升管两部分,提升管出口连接三组粗旋,每组粗旋对应两个单旋,粗旋与单旋之间采用软连接的方式。
单旋出口油气进入顶部的内集气室,再由油气大管送至分馏塔。
设备结构与尺寸如下图1图2所示。
由反应器整体结构可以看出,提升管与两级旋风内的油气主要依靠预提升蒸汽、原料雾化蒸汽、预汽提蒸汽进行置换,此部分空间与沉降器空间相比较小,且蒸汽量大,不能作为反应器置换时间的代表。
沉降器部分的油气主要依靠汽提蒸汽进行置换,此部分空间较大,且与再生器通过待生斜管相连,因此将沉降器的油气置换时间作为反应器整体的置换时间。
为计算简便,将沉降器整体分为,沉降器汽提部分(汽提段开始至变径结束)、沉降器稀相空间(沉降器直管段空间)、沉降器穹顶三个部分。
将三个部分看做直筒和半球型,则三部分尺寸如下表所示:表1 沉降器各部分近似尺寸与体积由于此次计算以沉降器,以及汽提蒸汽为目标,因此需要在沉降器空间内减掉内提升管及两级旋风分离器的体积。
则内提升管与旋风近似尺寸如下表所示:表2 旋风与提升管近似尺寸与体积由以上数据可得,沉降器内部空间体积为:1080m³三、置换时间计算置换时间的计算思路为,利用理想气体状态方程,计算出沉降器内部需要置换的油气的摩尔数,换算成等摩尔数的蒸汽的质量。
- 1、下载文档前请自行甄别文档内容的完整性,平台不提供额外的编辑、内容补充、找答案等附加服务。
- 2、"仅部分预览"的文档,不可在线预览部分如存在完整性等问题,可反馈申请退款(可完整预览的文档不适用该条件!)。
- 3、如文档侵犯您的权益,请联系客服反馈,我们会尽快为您处理(人工客服工作时间:9:00-18:30)。
60万吨/年催裂化装置“两器”施工工法(HGGF—11—93)中国化学工程第十一建设公司随着我国炼油工艺的不断改进,炼油装置的核心设备都在向大型化和一体化发展。
由我公司承建的大庆林源炼油厂和大庆化学助剂厂两套60万吨/年重油催化装置就是将反应器、沉降器和第一再生器合为一体,并采用同轴式结构,称为“同轴式沉降器—第一再生器”(以下简称两器)。
两器壳体采用16MnR材质,内部采用新型的WHL—1型浇注料进行衬里。
两器总重408吨,其中金属重233吨,最大直径Φ7200mm,设备高度为42m,壳体厚度为18—28mm,衬里厚度为100—150mm,安装在标高+9.800米的砼基础上。
设备内件主要有旋风分离器、待生立管、翼阀等,该设备是我国目前催裂化装置中较先进的工艺设备。
因受其自身结构的限制,在施工现场分片拼装。
对于这种大型的衬里设备,由于受其自身结构特点的限制,在现场施工难度很大,我们根据两套催裂化的施工经验,利用我们在吊装方面的技术优势,开发整理出了这项工法。
本工法的施工工艺就是根据现场施工条件和设备自身结构,以及吊装能力和衬里要求等因素,先将分片的壳体在平台上拼装为四大段(见图-1),然后进行衬里施工,安装内件,最后用倾斜单桅杆全方位(360︒)进行分段吊装、组对,在基础上进行正装施工。
一、工艺特点两器的施工工序较多,衬里是相当复杂的工序之一,且养生时间又长。
为满足整个施工工期,采用分段组焊、分段衬里、分段吊装,然后补衬接口这一施工方法,为衬里施工创造了有利的条件。
既满足了衬里工序的特殊要求,又使组装、焊接、衬里、吊装等工序呈流水式进行,其优点有:1、分段施工有利于扩大作业面,使各工种的作业保持相对的连续性,并在管理上实现了超前意识,故可缩短工期,提高经济效益;2、施工中的多数作业是在低层进行,节省了人力,质量易保证,施工安全性大;3、减少了大型工机具的使用,降低了成本;4、有利于保证关键部位的衬里质量,如:分段衬里可采用翻转倒衬法施工,解决了“上封头”和“上过渡段”等部位仰脸施衬的弊病。
二、适用范围本工法主要应用于催裂化装置的两器施工,也可应用于其它类似的大型设备的现场拼装、衬里,其它设备的吊装也可借鉴全方位吊装方法,故其应用前景较为广泛。
三、工艺程序(一)施工准备与平面布置1、施工之前要对基础进行验收和复测。
以施工图和施工规范为依据,并按GB150—89《钢制压力容器》有关条款对到货零部件进行验收。
2、作好平面布置如图-1。
3、由于衬里材料为新型材料,衬里材料应通过试验鉴定其质量,以确定配比。
4、根据本法施工的两器应按下面施工计划图(图-2)控制每一关键施工环节,确保施工工期。
(二)施工程序两器施工,根据其本身结构特点和衬里要求,同时考虑到目前国内大、中型施工企业中采用的桅杆的吊装能力而分为四段,见图-3。
第一段包括裙座、下封头、再生器密相筒体、下锥体过渡段,以及再生器稀相筒体一带板。
图—1 两器施工平面布置简图图—2 施工计划图第二段为再生稀相筒体。
+52300 第三段包括再生稀相筒体一带板,上锥体过渡段,沉降器筒体一带板,第四汽提段和旋风分离器。
段+42000 第四段为沉降器筒体、上封头、沉降器旋风分离器等。
第三+33000两器施工总的施工程序为:分段段在平台上拼装焊接;合格后,运输到吊装位置,按要求衬里;第然后用倾斜单桅杆分四段在基二础上正装。
每一段的具体施工段+27100 程序见图—4、图—5。
图—6、图—7、图—8。
第一段+9800图—3 两器壳体结构及施工分段示意图图—4 两器第I段施工程序100%RT图—5 两器第II段施工程序图—6 两器第III段施工程序图—7 两器第IV段施工程序100%RT图—8 两器本体总装施工程序四、操作要点(一)壳体的拼装与焊接1、壳体的组对顺序应遵循从难到易的规律,先控制好锥体过渡段、球形封头、椭圆封头的组对质量,然后进行直筒体的组对,以便在偏差的允许范围之内进行质量预控。
2、壳体的焊接即16MnR材质的焊接,根据16MnR材质的焊接工艺评定进行。
3、焊接时要控制线能量,环缝焊接时,焊工要对称布置,立缝焊接采用分段退焊法,以防变形。
4、设备开孔的标高应考虑筒体每一节板的最终累积高度偏差,大的设备开孔一定要在加强板点焊之后进行。
5、衬里之前所有与壳体内外连接的附件(包括平台护板)应焊接完毕,禁止衬后焊接。
以防壳体局部受热影响衬里质量。
(二)衬里施工两器是重油催裂化装置的关键性设备,由于其直径大,总标高达56米,增加了衬里的难度。
两器的衬里施工,除第一段是就位于基础上施衬外,其余三段均在地面上的起吊位置施衬,这样减少了浇注料垂直运输的高度。
两器衬里施工总的流程见图-9。
检查检查支模(钢或木模)检查6—10小时养护图—9 两器衬里流程图两器衬里,由无龟甲网衬里和有龟甲网衬里两部分组成,所有壳体内部为无龟甲网衬里,汽提段筒体、待生立管以及内锥体外部为有龟甲网衬里。
有龟甲网衬里分隔热层和耐磨层,无龟甲网衬里只有隔热层。
1、有龟甲网衬里(1)隔热层的施工壳体部位采用直立喷涂的方法,喷涂后应随即将其表面刮平至保温钉台肩平齐。
每一段接口处衬里应做成阶梯型。
内锥体、待生立管、汽提段的隔热层衬里采用卧置分瓣1/2进行施工,每瓣施工完毕之后,必须停放12小时,才能进行下瓣的翻转施工。
瓣与瓣之间的接口采用阶梯型,下瓣施工前应将接口清理干净、浇水润湿。
(2)耐磨层的施工壳体部位采用直立喷涂的方法,喷成后的衬里应立即将其表面压光至与龟甲网平齐,不得有麻面和扒缝,抹平过程中避免反复次数过多。
内锥体和待生立管、汽提段采用卧置捣实与抹平。
龟甲网孔内应分两层进行捣实,然后将衬里表面抹平至与龟甲网平齐。
2、无龟甲网衬里壳体段采用立式支模捣制的方法进行。
锚固钉焊完并与壳体一并喷砂之后支模,模板拆装方面,表面要光滑,有一定的刚度。
然后将搅拌均匀的料装入模板,振捣时棒应直插,快插慢拨,插入深度至下一层衬里100mm,振捣至混凝土表面返浆为宜。
上层模板的安装和衬里振捣时间,控制在下层混凝土初凝时间之前,拆装时应在混凝土终凝时间之后。
上封头采用分瓣手工涂抹,接口处呈阶梯状。
3、衬里施工注意事项两器衬里用“WHL—1”浇注料,施工方法与一般轻质混凝土基本相同,但应注意以下几点:(1)模板应坚固,尺寸准确,钢模板比木模板好,变形小,循环使用的次数多,制作时只做3—4带板(每带板0.9—1m高)循环使用;(2)支模前全面检查锚固钉是否有碰倒的现象,检查无误后方可支模。
模板应支设牢固,与设备壳体间设置定位标尺,振捣的过程中还应随时注意模板的位置;(3)搅拌必须采用强制式搅拌机,先干拌而后加水,每次搅拌的时间不得少于2分钟。
搅拌机要就近设置,减少运输距离,并掌握所搅拌的浇注料能在半小时内用完。
(4)用50mm高频振捣器,填料高度300mm左右,插入间距250—300mm,每点振捣30秒左右(注意漏振和过振现象),同时,用铁锤轻轻敲打模板,以排除料中的空气,以便减少表面的麻面;(5)每段衬里的施工,连续或间断进行都可,但接搓处必须留成“阶梯形”,下次施工时要清除毛渣,浇水湿润;(6)衬里喷雾养生非常重要,在浇注后6—10小时即应进行,并持续48小时,冬期施工时适当减少养生次数;(7)衬口作业应严格认真,尤其要注意上口,料不能过稀或过稠,避免上口坠缝。
(三)吊装1、全方位吊装法两器的每一段吊装,采用倾斜单桅杆360 回转法吊装。
这种吊装方法就是将两器的四大段壳体拚装、焊接合格后运输到桅杆的旋转半径内进行衬里,具备吊装条件时,起吊分段并在空中通过桅杆的旋转将分段的壳体旋转于基础正上方然后就位。
吊装每一段时,将该段内所有的内件和外部梯子平台全部安装完毕,整段吊装。
2、操作要点此种方法吊装效果明显,但难度较大。
吊装时,除应遵守常规吊装方法外,特别是吊装时统一指挥,各个锚点要听从指挥,行动一致,通过拖拉绳的松紧来使桅杆安全旋转。
3、注意事项(1)桅杆顶和底部结构必须采用球铰;(2)桅杆倾斜角度应在设计允许范围内;(3)桅杆回转时产生附加扭矩,承载能力应重新核算。
五、劳动组织两器的施工是不均衡的,如何有效的利用劳动力,是施工的关键。
大量的起重、焊工、筑炉工只有在工序到来时使用。
该设备有效施工天数为305天,平均日使用人工数为28人,各工种配置人数见表—1表—1 劳动力配置(二)关键工序中各工种的岗位职责1、各工种都要及时的掌握施工动态,做好工序之间的相互交接工作。
2、铆工要记录各部位的几何尺寸和偏差。
3、钳工负责保温钉和龟甲网安装工作(因重催装置钳工的工作量较少)。
六、机具配备和施工材料(一)主要施工机具一览表,见表—2表—2(二)主要消耗材料一览表,见表—3表—3七、质量控制(一)主要质量标准1、筒体的外圆周长偏差±8mm;2、纵缝错边量0.1s;3、环缝错边量0.1s+1;4、焊缝棱角高度0.1s+2;5、开孔方位标高偏差±5mm;6、旋风入口标高±5mm,垂直度偏差5mm;7、待生立管垂直度偏差2mm;8、待生翼阀口与待生立管同轴度偏差±1mm;9、衬里表面平整,衬里厚度偏差为5%的厚度;10、保温钉长度偏差±1mm;11、龟甲网平整度轴向间隙≤2mm ,环向间隙≤5mm;12、翼阀的角度偏差0.5︒.(二)质量管理措施1、成立QC小组进行质量预控和质量攻关;2、实行“三检一评”制度;3、充分发挥质保体系的作用,实行如下停点确认卡制度:停点检查合格停点检查合格表面检查合格到货设备拼装焊接合格停点检查确认合格探伤衬里吊装(三)采用的技术措施1、在设备验收中,规范上要求筒体壁板的弧度间隙用1米的样板检查不大于3mm合格。
然而根据我们以前的施工经验,我们要求用2m的样板检查≤2mm为合格。
主要原因是这一偏差要求将会影响到其它组对偏差要求。
如筒体的不圆度、不直度、错边量和棱角度,特别是减少了筒体的组对刚性,使质量得到了预控。
2、组对时,每条焊缝的焊接收缩量进行认真的考虑,一般为2.5mm左右。
每段之间对口处进行二次找圆、找平工作。
3、锥体过渡段组对时,锥体上下口的同轴度规范上无偏差要求。
由于设备自身结构,控制这一因素是相当主要的。
因为锥体上下口的同轴度偏差较大,将影响到设备的垂直度,旋风分离器在壳体内的相对位置将会随着锥体而发生较大的偏差,影响到旋风分离器的分离效果。
汽提段和待生立管是连接于上锥体之上的,如锥体偏差大将会影响到待生立管在壳体内的中心位置,这样就很难保证待生立管与底部封头待生翼阀口的同轴度偏差±1.0mm,在施工中我们综合考虑了各方面的因素,将上下锥体的同轴度偏差控制在6mm之内,这样最终也控制了其它尺寸的偏差。