钢中非金属夹杂物及其金相鉴别
ASTM E45 钢中非金属夹杂物的评定方法

ASTM E45钢中夹杂物含量的评定方法1 范围1.1 本标准的试验方法为测定锻钢中非金属夹杂物含量的方法。
宏观试验法包括微蚀、断口、台阶和磁粉法。
显微试验法通常包括 5种检测。
根据夹杂物形状而不是化学特点,显微法将夹杂物划分为不同类型。
这里主要讨论了金相照相技术,它允许形状类似的夹杂物之间略有不同。
这些方法在主要用来评定夹杂物的同时,某些方法也可以评估诸如碳化物、氮化物、碳氮化物、硼化物和金属间化合物的组成。
除了钢以外,其它合金在有些情况下也可以应用这些方法。
根据这些方法在钢中的应用情况,将分别给予介绍。
1.2 本标准适用于人工评定夹杂物含量。
其他 ASTM标准介绍了用 JK评级图的自动法( ASTME1122 )和图像分析法( ASTM E1245 )。
1.3 按照钢的类型和性能要求,可以采用宏观法或显微法,也可以将二者结合起来,以得到最佳结果。
1.4 这些试验方法仅仅为推荐方法,对任何级别的钢而言,这些方法都不能作为合格与否的判据。
1.5 本标准未注明与安全相关的事项,如果有的话,也只涉及本标准的使用。
标准使用者应建立适当的安全和健康操作规程,并且在使用标准前应确定其适用性。
2 参考文献2.1 ASTM 标准:A 295 高碳耐磨轴承钢技术条件A 485 强淬透性耐磨轴承钢技术条件A 534 耐磨轴承用渗碳钢技术条件A 535 特种性能的滚珠和滚柱轴承钢技术条件A 756 耐磨轴承用不锈钢技术条件A 866 耐磨轴承用中碳钢技术条件D 96 用离心法分离原油中水和沉淀物的试验方法E 3 制备金相试样指南E 7 金相显微镜术语E 381 钢棒,钢坯,钢锭和锻件的宏观试验法E 709 磁粉检测指南E 768 自动测定钢中夹杂物的试样的制备和评定操作规程E 1122 用自动图像分析法获得 JK夹杂物等级的操作规程E 1245 用自动图像分析法确定金属中夹杂物或第二相含量的操作规程2.2 SAE 标准:J421 ,磁粉法测定钢的清洁度等级J422 ,钢中夹杂物评定的推荐操作规程2.3 航空材料技术条件2300 ,高级飞行性能钢的清洁度:磁粉检测程序2301 ,飞行性能钢的清洁度:磁粉检测程序2303 ,飞行性能钢的清洁度:耐腐蚀马氏体钢磁粉检测程序2304 ,特种飞行性能钢的清洁度:磁粉检测程序2.4 ISO 标准:ISO 3763 ,锻钢——非金属夹杂物的宏观评定法ISO 4967 ,钢——使用标准图谱的非金属夹杂物显微评定方法2.5 ASTM 附加标准:钢中夹杂物评级图Ⅰ -r和评级图Ⅱ低碳钢的 4张显微照片3 术语3.1 定义:3.1.1 本标准中用到的定义,见 ASTM E7 。
钢中夹杂物知识.
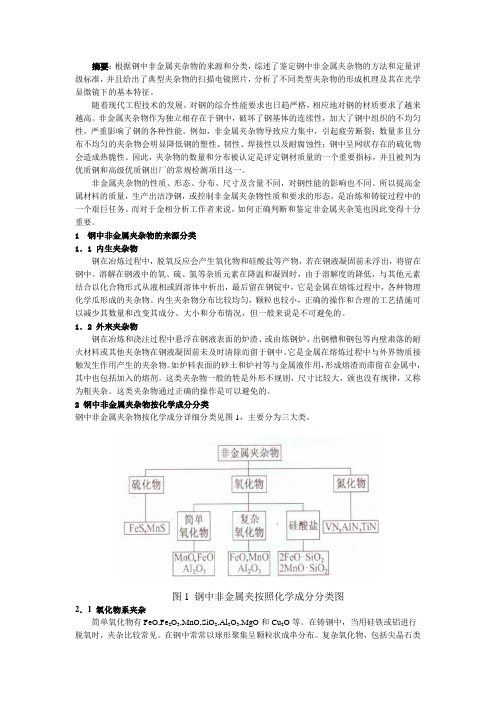
摘要:根据钢中非金属夹杂物的来源和分类,综述了鉴定钢中非金属夹杂物的方法和定量评级标准,并且给出了典型夹杂物的扫描电镜照片,分析了不同类型夹杂物的形成机理及其在光学显微镜下的基本特征。
随着现代工程技术的发展,对钢的综合性能要求也日趋严格,相应地对钢的材质要求了越来越高。
非金属夹杂物作为独立相存在于钢中,破坏了钢基体的连续性,加大了钢中组织的不均匀性,严重影响了钢的各种性能。
例如,非金属夹杂物导致应力集中,引起疲劳断裂;数量多且分布不均匀的夹杂物会明显降低钢的塑性、韧性、焊接性以及耐腐蚀性;钢中呈网状存在的硫化物会造成热脆性。
因此,夹杂物的数量和分布被认定是评定钢材质量的一个重要指标,并且被列为优质钢和高级优质钢出厂的常规检测项目这一。
非金属夹杂物的性质、形态、分布、尺寸及含量不同,对钢性能的影响也不同。
所以提高金属材料的质量,生产出洁净钢,或控制非金属夹杂物性质和要求的形态,是冶炼和铸锭过程中的一个艰巨任务。
而对于金相分析工作者来说,如何正确判断和鉴定非金属夹杂笺也因此变得十分重要。
1 钢中非金属夹杂物的来源分类1.1 内生夹杂物钢在冶炼过程中,脱氧反应会产生氧化物和硅酸盐等产物,若在钢液凝固前未浮出,将留在钢中。
溶解在钢液中的氧、硫、氮等杂质元素在降温和凝固时,由于溶解度的降低,与其他元素结合以化合物形式从液相或固溶体中析出,最后留在钢锭中,它是金属在熔炼过程中,各种物理化学瓜形成的夹杂物。
内生夹杂物分布比较均匀,颗粒也较小,正确的操作和合理的工艺措施可以减少其数量和改变其成分、大小和分布情况,但一般来说是不可避免的。
1.2 外来夹杂物钢在冶炼和浇注过程中悬浮在钢液表面的炉渣、或由炼钢炉、出钢槽和钢包等内壁肃落的耐火材料或其他夹杂物在钢液凝固前未及时清除而留于钢中。
它是金属在熔炼过程中与外界物质接触发生作用产生的夹杂物。
如炉料表面的砂土和炉衬等与金属液作用,形成熔渣而滞留在金属中,其中也包括加入的熔剂。
钢中非金属夹杂实验报告

实验报告姓名:班级:冶金1401班学号: 20142019实验名称:钢中非金属夹杂物观察与分析实验实验日期: 2017.11.7实验:钢中非金属夹杂物观察与分析实验一、实验目的1.掌握钢的磨制方法。
2.了解球磨机的使用方法。
3.了解金相显微镜的原理及使用。
4.对钢中的非金属夹杂物进行分析。
二、实验原理。
A钢中夹杂物的分类分类方法很多,但常见的有以下四种:1.按来源分类,可分为两类:(1)外来夹杂物:耐火材料、熔渣或两者的反应产物混入钢中并残留在钢中的颗粒夹杂称为外来夹杂。
包括从炉衬或包衬、或从汤道砖、中包绝热板、保护渣进入钢水中的夹杂物(有人还将钢水二次氧化生成的夹杂物包括在内)。
这类夹杂颗粒较大,易于上浮,但在钢中,它们的出现带着偶然性且不规则。
(2)内生夹杂物:在冶炼、浇注和凝固过程中,钢液、固体钢内进行着各种化学反应,对于在冶炼过程中所形成的化合物、脱氧时产生的脱氧产物、或在钢水凝固过程产生的化合物,当这些化合物来不及从钢水中彻底排出而残存在钢中者,叫做内在的非金属夹杂物。
内生夹杂物形成的时间可分为四个阶段:①一次夹杂(原生夹杂):钢液脱氧反应时生成的脱氧产物;②二次夹杂:在出钢和浇注过程中温度下降平衡移动时生成的夹杂物;③三次夹杂(再生夹杂):凝固过程中生成的夹杂;④四次夹杂:固态相变时因溶解度变化生成的夹杂。
一般说来外来夹杂物颗粒较大,在钢中比较集中,而内生夹杂物则与此相反。
从组成来看,内生夹杂物可以是简单组成,也可以是复杂组成;可以是单相的,也可以是多相的。
在铸坯凝固以及随后的冷却过程中,夹杂物不仅与钢基体保持平衡,而且夹杂物本身也不断发生改变,例如析出新的化合物以趋于稳定状态。
在轧制或热处理时,每次加热都为夹杂物和钢基体之间趋向平衡提供了条件,在室温下所观察到的夹杂物,实际上是经过了一系列复杂变化的结果。
2.按化学成分分类,一般分三类。
(1)氧化物:如FeO, Si02 , Al2O3等,有时它们各自独立存在,有时形成尖晶石(如MnO.Al203)或固溶体 (如FeO 和MnO)。
钢中非金属夹杂物的检测

钢中非金属夹杂物的检测一.概述非金属夹杂物是钢中不可避免的杂质,它的存在使金属基体的均匀连续性受到破坏。
非金属夹杂在钢中的形态、含量和分布情况都不同程度地影响着各种性能,诸如常规力学性能、疲劳性能、加工性能等。
因此,非金属夹杂物的测定与评定引起人们的普遍重视。
夹杂物的含量和分布状况等往往被认为是评定钢的冶金质量的一个重要指标,并被列为优质钢和高级钢的常规项目之一。
钢中非金属夹杂物按其来源和大小,大体可分为两大类:1.显微夹杂物或称内在夹杂物,这类夹杂物是钢冶炼和凝固过程中,由于一系列物理和化学反应所生成。
例如,在冶炼过程中,由于加入脱氧剂而形成氧化物和硅酸盐等。
这些夹杂物来不及完全上浮进入钢渣,而残留在钢液中,即为内在夹杂。
如:Al、Fe-si等脱氧剂可以形成下列夹杂:3FeO+2Al 3Fe+ Al2O32FeO+ Si SiO2+2FenFeO+mSiO2 nFeO·mSiO2nAl2O3+mSiO2 nAl2O3·mSiO2另外,钢在凝固冷却过程中,S、N等元素,由于溶解度的降低而生成硫化物、氮化物等也将残留在钢中。
2.宏观夹杂物或称外来夹杂物,这类夹杂物是在钢的冶炼或浇铸过程中,由于耐火材料等外来物混入造成。
其特点是大而无固定形状。
就对钢而言,宏观夹杂物的危害更大。
夹杂物的检验方法也有宏观检验法和显微检验法两种。
非金属夹杂物的显微检验法是指借助于金相显微镜在规定的实验条件下,检验金相试样中非金属夹杂物的方法。
该法的主要优点是可以确定夹杂物的类型、分布、数量和大小,可以发现极细小的夹杂物。
但是,由于受试样尺寸及取样位置、数量的限制。
所以显微检验法的评定结果在很大程度上存在偶然性。
往往会过分夸大细小夹杂物的重要性而将那些试样以外或检验面以外的较大夹杂物遗漏,所以,显微检验法总是与宏观检验法相辅相成、互相补充的。
如果非金属夹杂物的宏观检验对优质钢来说是必不可少的检验项目之一,那么显微检验法则是特殊用途钢(如轴承钢、重要用途的合金结构钢等)广泛采用的检验方法。
钢中非金属夹杂物观察和评级

钢中的非金属夹杂1. 试验目的非金属夹杂物破坏金属基体的连续性,其形态、数量、尺寸和分布影响钢的塑性、韧性、焊接性能、疲劳性能和耐蚀性等,因此,夹杂物的数量和分布被认为是评定钢材质量的一个重要指标。
2. 相关标准标准GBT 10516 2005,该标准代替GBT 10516 1989,于2005年5月13日发布,2005年10月1日实施。
夹杂物试样不经腐蚀,在明场下放大100倍,80mm 直径的视场下进行观察,选取夹杂物污染最严重的视场,与其钢种的相应标准评级图对比评定。
夹杂物分类:硫化物类,标准图谱命名为A 类。
属于塑性夹杂,较宽范围形态比(长度/宽度)的单个灰色夹杂物,一般端部呈圆角,经锻、轧后沿加工方向变形,呈纺锤形或线段形,例如FeS 、MnS 。
氧化铝类:标准图谱命名为B 类。
属于脆性夹杂,形态比(一般<3),为黑色或带蓝色的颗粒,沿轧制方向排成一行(至少有3个颗粒)。
硅酸盐类:标准图谱命名为C 类。
是具有高延展性,较宽范围形态比(一般≥3)的单个呈黑色或深灰色的夹杂物,一般端部呈锐角。
例如2MnO ·SiO 2球状氧化物类:标准图谱命名为D 类。
不变形,带角或圆形的,形态比较小(一般<3),黑色或带蓝色,表现为无规则分布的颗粒。
例如SiO 2单颗粒球状类:标准图谱命名为DS 类。
为圆形或近似圆形,直径≥13μm 的单颗粒夹杂物。
非传统类型夹杂物的评定也可以通过其形状与上述五类夹杂物进行比较,并注明其化学特征。
沉淀相类如碳化物、氮化物、硼化物的评定,也可以根据它们的形态与上述五类夹杂物进行比较,并按上述方法表示其化学特征。
钢中的非金属夹杂物测定夹杂物类别A B C D DS 总长度 总长度 总长度 数量 直径 评级图级别iμmμm μm 个 μm 0.5 37 17 18 1 13 1 127 77 76 4 19 1.5 261 184 176 9 27 2 436 343 320 16 38 2.5 649 555 510 25 53 898 822 746 36 76 3(<1181)(<1147)(<1029)(<49)(<107)注:D 类夹杂物的最大尺寸定义为直径类别细系粗系最小宽度最大宽度最小宽度最大宽度μm μm μm μmA 2 4>4 12B 2 9 >9 15C 2 5 >5 12D 3 8 >8 13注:D类夹杂物的最大尺寸定义为直径3. 试样制备3.1 试样尺寸夹杂物形态很大程度上取决于钢材压缩变形程度,只有在变形度相似的试样坯制备的截面上才能进行结果的比较。
钢中非金属夹杂物的金相检验

钢中非金属夹杂物的金相检验碳素钢和合金钢中非金属夹杂物主要有硫化物、氧化物、硅酸盐、氮化物等。
非金属夹杂物往往是工件失效的主要原因。
钢中非金属夹杂物的金相检验主要包括夹杂物类型的定性和定量评级。
夹杂物的检验评定可按照GB/T 10561-1989《钢中非金属夹杂物显微评定方法》执行。
为什么要检验钢中的非金属夹杂物?因为非金属夹杂物破坏了金属基体的连续性、均匀性,易引起应力集中,造成机械性能下降,导致材料的早期破坏,其影响程度主要取决于夹杂物的形状、大小、分布和聚集状态。
钢中夹杂物的检验一般在出厂前钢厂或者收货单位验收时检验。
钢中非金属夹杂物的来源1、内在的:包括①铁矿石②钢厂在冶炼时,用Si、Al脱氧造成。
3FeO + 2Al →3Fe + Al2O32FeO + Si →2Fe + SiO22、外来的:浇铸过程卷入的耐火材料等。
对试样的要求1、取样时沿轧制方向,磨制纵向截面观察夹杂物大小、形状、数量,横向截面观察夹杂物从边缘到中心的分布。
试样表面无划痕、无锈蚀点、无扰乱层。
2、淬火以提高试样的硬度,保留夹杂物的外形3、试样表面不浸蚀。
非金属夹杂物的分类1、氧化物:FeO、MnO、Cr2O3、Al2O3;2、硫化物:FeS、Mn S及其共晶体3、硅酸盐:2FeO·SiO2、2MnO·SiO2;4、氮化物:TiN、VN;非金属夹杂物的鉴别方法1、明场:检验夹杂物的数量、大小、形状、分布、抛光性和色彩。
不透明夹杂物呈浅灰色或其他颜色,透明的夹杂物颜色较暗。
2、暗场:检验夹杂物的透明度、色彩。
透明夹杂物发亮,不透明夹杂物呈暗黑色、有时有亮边。
3、偏光:检验夹杂物的各向同性和各向异性,色彩、黑十字现象。
具体形貌主要有硫化铁(FeS)和硫化锰(MnS),以及它们的共晶体等2、氧化物常见氧化物有氧化亚铁(FeO)、氧化亚锰(MnO)、氧化铬(Cr2O3)、氧化铝(Al2O3)等。
二氧化硅(SiO2)也是常见的氧化物。
钢中非金属夹杂物及其检测法

钢中非金属夹杂物及其检测法夹杂物的评级问题:不计较其组成成分和性能以及它们可能的来源等;只注意它们的数量、形状、大小和分布情况。
一般在明视场下放大100倍时检验即可。
现在采用的方法有:瑞典Jernkontoret(简称JK)夹杂物评级图。
美国试验及材料学会(ASTM)夹杂物评级标准亦采用JK评级图。
此外还有SAE(美国汽车工程师学会)夹杂物评级图等等。
中国冶金部YB25-59规定,夹杂物的评级有甲乙两种方法。
即:长度指数和与标准级别图对比评级法。
非金属夹杂的鉴定:(一)金相法:借助金相显微镜的明场、暗场及偏振光来观察夹杂物的形状、分布、色彩及各种特征,从而对夹杂物作出定性或半定性的结论。
但金相法不能获得夹杂物的晶体结构及精确成分的数据。
1.夹杂物的形状:鉴定夹杂物首先注意的是它们的形状,从它们的形状特点上,有时可以估计出它们属于那类夹杂物,这有利于考虑下一步应采取的鉴定方法。
如:玻璃质SiO2呈球形;TiN一般呈淡黄色的四方形。
在铸态时呈球形的夹杂物很多,但这些夹杂物有的具有一定的塑性,当钢在锻轧后,它们被压延拉长,如FeO 和2FeOSiO2共晶夹杂物,铸态时为球状,锻轧后被拉成长条状。
2.夹杂物分布:夹杂物的分布情况也有一定的特点,有的夹杂物成群,有的分散。
成群的夹杂物经锻轧后,即沿锻轧方向连续成串,Al2O3夹杂就属此类。
有的夹杂物,如FeS 及FeS-FeO共晶夹杂物等。
因其熔点低,所以钢凝固时,这类夹杂物多沿晶界分布。
3.夹杂物的色彩和透明度:观察夹杂物的色彩及透明度一般应在暗场或偏振光下进行。
可分为透明和不透明两大类。
透明的还可分为透明和半透明两种。
透明的夹杂物在暗场下显得十分明亮。
如果夹杂物是透明的并有色彩,则在暗场下将呈现它们的固有色彩。
各种夹杂物都有其固有的色彩和透明度,再结合其它特征来进行判断。
如某种夹杂物,它们的分布及外形呈有棱的细小颗粒并沿轧制方向连续成群,在明场下这些夹杂物多呈深灰略带紫色,而在暗场下则为透明发亮的黄色。
金相培训-GB10561钢中非金属夹杂物含量的测定

02
在定量金相技术中,需要了解 显微组织的形态、尺寸、分布 和相对含量等信息,以便对材 料的性能进行评估和预测。
03
定量金相技术的基础包括光学 显微镜、数字图像处理、计算 机辅助图像分析和统计方法等 。
图像分析系统在夹杂物测定中的应用
图像分析系统是一种基于计算机技术的数字图 像处理和分析系统,可以用于非金属夹杂物的 测定。
分类
根据其化学成分、形态、尺寸和分布 的不同,钢中非金属夹杂物可分为氧 化物、硫化物、硅酸盐等类型。
形成机制与影响因素
形成机制
钢中非金属夹杂物的形成主要与原料质量、熔炼气氛、温度场、化学成分等因素有关。 在炼钢过程中,钢液与炉渣、耐火材料、脱氧剂等发生化学反应,生成不同类型的非金
属夹杂物。
影响因素
钢的化学成分、熔炼温度、炉渣组成、脱氧方式等均对非金属夹杂物的形成产生影响。
对钢性能的影响
力学性能
非金属夹杂物在钢中充当应力集 中源,降低钢的抗拉强度、屈服 点和疲劳极限。
韧性
非金属夹杂物对钢的韧性具有不 利影响,可能导致钢材在低温或 冲击载荷下脆化。
加工性能
非金属夹杂物可能影响钢材的可 焊性和冷加工性能,如焊接时易 产生裂纹,降低冷弯性能等。
03
gb10561标准解读
标准背景与意义
钢中非金属夹杂物是影响钢材质量的 重要因素,gb10561标准是检测和 评定钢材中非金属夹杂物含量的重要 依据。
该标准的制定和实施,对于提高钢材 质量、保证工程安全、促进冶金工业 发展具有重要意义。
试验方法与步骤
01 试验前需准备样品,并进行研磨、抛光等 预处理。
为了减小误差,需要采取一系列措施,如制定科学的取样和制样方案、选 择合适的测量方法和仪器、加强操作人员的培训和技能提升等。
钢中非金属夹杂物检测技术

●
沿铸坯厚度方向取试样,在金相显微镜F观察统计夹杂物分布如图2(b)所示。由图2(b)知,金相法得到与硫印 法相似的结果。 那么在铸坯厚度1/4左右夹杂物是由什么组成的呢?用金相法观察夹杂物,探针分析结果与浸入式水口内堵塞 物成分十分相似,见表4。由此可知,铸坯中大颗粒夹杂物是来源于浸入式水口堵塞物。这种以A1203为主的夹杂物 是造成冷轧薄板表面缺陷的主要原因。
●
试样大,电解时间长。为了捕捉更多的大型夹杂物,试样尺寸大(中50’60X 120’150mm),样重3’5kg,电 解时间15’20天。
・
使用物理方法分离碳化物。用淘洗法把碳化物淘洗掉,而夹杂物和铁的氧化物保留下来,用还原磁选把 夹杂物分离出来。
●
夹杂粒径分级和组成分析。 不足之处是不能完全保留云雾状的A1203夹杂。
・
●
●
下面把常用的几种方法简介如下:
3.1钢中非金属夹杂物评级法
有国家标准评级图,用于轧材或铸坯中夹杂物评级。评级图片是在100倍纵向抛光面上面积为0.5咖2视场。根 据夹杂物形态和分布,标准图谱分为A、B、C、D和Ds五大类。 A类(硫化物夹杂):延性好,长/宽比较大,夹杂物呈灰色; B类(氧化铝):不变形,带棱角,呈黑色粒状,沿轧制方向排列; C类(硅酸盐):延性好,长/宽比较大,夹杂物呈黑色或灰色; D类(球状氧化物):不变形,带棱角,长/宽比较小(<3),无规则分布,呈黑色或兰色。 Ds类(单颗粒球状):夹杂物呈圆形或近似圆形,直径大于13 ll 取样、制样和评级按规定标准(GB/T1056卜2005)执行。
・
(2)分析流程 大样电解主要用于分析钢9>50u nl大型氧化物夹杂。其分析流程主要包括电解、淘洗、还原和分离。分离出夹 杂物进行粒度分级、形貌照相和电子探针定量成分分析。大样电解分析流程如图5所示。 (3)大样电解设备 电解设备包括整流器(25V,20/I)、电解槽体、淘洗槽、还原磁选装置、体视显微镜、分级筛、称重天平和相机 等。 (4)大型夹杂物实例 下面介绍一下我们在某厂RH、中间包和连铸坯中大型夹杂物照片。图6为RH处理前后大颗粒夹杂物形貌相片。
非金属夹杂物

金相分析
表 主要元素及其参考含量 (wt%) 元素 Ca Si Mn Al O Na Mg K Fe 含量 22.43 15.49 0.91 4.12 47.27 6.45 1.12 0.14 2.07
元素
含量
表 O
主要元素及其参考含量 (wt%) Fe Mg Ca Si S Al
5.56 4.28 2.32 1.16 1.11
45.30 7.33
钢中非金属夹杂物的鉴定方法
夹杂物的鉴定分为宏观鉴定和微观鉴定。宏观鉴定的方法有探伤法、 低倍检验等,主要用于宏观性检验。本章主要介绍微观鉴定方法,有 金相分析、电子光学方法(电子探针、扫描电镜附能谱仪分析)等。 另外还可利用电解分离法分离出夹杂物,测定夹杂物的化学组成及含 量。 金相分析法 金相分析法是夹杂物一般定性及定量分析应用最为广泛的一种简便方 法,即利用金相显微镜进行比对或计算的方法测定钢中夹杂物的含量, 还能够鉴别夹杂物的类型、形状、大小和分布。在金相鉴别的基础上, 可为电子探针、能谱成分测定提供确切区域。 明场鉴定方法:在明场下,主要研究夹杂物的形状、大小、分布、数 量、表面色彩、反光能力、结构、磨光性和可塑性等,通常在放大 100~500倍下进行。 暗场鉴定方法:暗场下可研究夹杂物的透明度和固有色彩。 偏振光鉴定方法:在偏振光下主要判别夹杂物的各向异性效应和黑十 字等现象。
GB/T 10561-2005(ISO 4967:1998)检测方法
该标准把钢中非金属夹杂物分为A、B、C、D、DS等五大类,其中又 把A类~D类按夹杂物粗、细(宽度或直径)分为两类,分别评定,用 字母e表示粗系的夹杂物,每类夹杂物随含量(递增)级别从0.5级至3 级,级差为0.5级,共6个级别。 非常规类型夹杂物的评定也可通过将其形状与上述五类夹杂物进行比 较,并注明其化学特征,例如:球状硫化物可作为D类夹杂物评定, 但在实验报告中应加注一个下标(如Dsulf表示球状硫化物;Dcas表示 球状硫化钙;DRES表示球状稀土硫化物;DDup表示球状复相夹杂物, 如硫化钙包裹着氧化铝)。 沉淀相类如硼化物、碳化物、碳氮化合物或氮化物的评定,也可以根 据它们的形态与上述五类夹杂物进行比较,并按上述的方法表示它们 的化学特征。
钢中非金属夹杂物的金相鉴定

与色彩、夹杂物的各向同性与各向异性。
球墨铸铁中,石墨球具有多晶 结构,内部有年轮状的特点,即 石墨球内部有一个核心,从核心 向外,碳原子形成年轮状堆积。 偏光照明下,石墨球的组织有明 显的各向异性效应。
球墨铸铁 石墨的多晶体特征 偏振光
球墨铸铁 石墨
氧化硅 玻璃质球状 明场 100X 黑色中心部分有亮点 呈“同心圆”特征
氧化硅 玻璃质球状 偏振光 100X 呈“黑十字”特征
硫化物 塑性夹杂物 100X
硅酸盐 100X
氮化物 100X
2、暗场照明 暗场照明时通过目镜观察的现场基
本上是黑暗的,仅在磨痕、坑洞、夹杂 物等表面不平处,因光线漫反射有部分 可以进入物镜成象,所以可以看到一些 明亮的象映衬在黑暗的视场内。在暗场 下因为没有金属表面反射光的混淆和遮 盖,我们可以辨别夹杂物的透明度以及 透明夹杂物的固有色彩。
3、偏振光照明
从物理学知道,自然光是在垂直于传播方向的平面
内各个方向的振动都相等的光,而偏振光则是仅在垂直 于传播方向的平面一个方向振动的光或以不等振幅在各 个方向振动的光。 欲得到偏振光,必须使自然光起偏。为此需要特殊的附 件。显微镜的偏光附件共有二件,一件插在入射光线 中,称为起偏镜,它的作用是使光源发出的光线变成偏 振光;一件放在目镜前的观察光程内,称检偏振镜,用 来检查偏振光,当偏振光发出的偏振光轴与检偏镜的光 轴平行时,透过检偏镜的光最强,当两个光轴垂直正交 时,由起偏镜产生的偏振光不过检偏镜而产生消光现 象,改变两偏振镜的交角,就会使视场中光线发生明暗 的变化。
实验五 钢中非金属夹杂 物的金相鉴定
一、实验目的
1、掌握钢中非金属夹杂物的金相检验方法; 2、学习使用显微镜的暗场,偏振光照明方 法; 3、熟悉常见夹杂物的金相特征。
钢中非金属夹杂物观察和评级

钢中的非金属夹杂1. 试验目的非金属夹杂物破坏金属基体的连续性,其形态、数量、尺寸和分布影响钢的塑性、韧性、焊接性能、疲劳性能和耐蚀性等,因此,夹杂物的数量和分布被认为是评定钢材质量的一个重要指标。
2. 相关标准标准GBT 10516 2005,该标准代替GBT 10516 1989,于2005年5月13日发布,2005年10月1日实施。
夹杂物试样不经腐蚀,在明场下放大100倍,80mm 直径的视场下进行观察,选取夹杂物污染最严重的视场,与其钢种的相应标准评级图对比评定。
夹杂物分类:硫化物类,标准图谱命名为A 类。
属于塑性夹杂,较宽范围形态比(长度/宽度)的单个灰色夹杂物,一般端部呈圆角,经锻、轧后沿加工方向变形,呈纺锤形或线段形,例如FeS 、MnS 。
氧化铝类:标准图谱命名为B 类。
属于脆性夹杂,形态比(一般<3),为黑色或带蓝色的颗粒,沿轧制方向排成一行(至少有3个颗粒)。
硅酸盐类:标准图谱命名为C 类。
是具有高延展性,较宽范围形态比(一般≥3)的单个呈黑色或深灰色的夹杂物,一般端部呈锐角。
例如2MnO ·SiO 2球状氧化物类:标准图谱命名为D 类。
不变形,带角或圆形的,形态比较小(一般<3),黑色或带蓝色,表现为无规则分布的颗粒。
例如SiO 2单颗粒球状类:标准图谱命名为DS 类。
为圆形或近似圆形,直径≥13μm 的单颗粒夹杂物。
非传统类型夹杂物的评定也可以通过其形状与上述五类夹杂物进行比较,并注明其化学特征。
沉淀相类如碳化物、氮化物、硼化物的评定,也可以根据它们的形态与上述五类夹杂物进行比较,并按上述方法表示其化学特征。
钢中的非金属夹杂物测定夹杂物类别A B C D DS 总长度 总长度 总长度 数量 直径 评级图级别iμmμm μm 个 μm 0.5 37 17 18 1 13 1 127 77 76 4 19 1.5 261 184 176 9 27 2 436 343 320 16 38 2.5 649 555 510 25 53 898 822 746 36 76 3(<1181)(<1147)(<1029)(<49)(<107)注:D 类夹杂物的最大尺寸定义为直径类别细系粗系最小宽度最大宽度最小宽度最大宽度μm μm μm μmA 2 4>4 12B 2 9 >9 15C 2 5 >5 12D 3 8 >8 13注:D类夹杂物的最大尺寸定义为直径3. 试样制备3.1 试样尺寸夹杂物形态很大程度上取决于钢材压缩变形程度,只有在变形度相似的试样坯制备的截面上才能进行结果的比较。
国外钢中非金属夹杂物检验标准解析

国外钢中非金属夹杂物检验标准解析ISO非金属夹杂物检验标准(1)ISO 4967:2013ISO 4967:2013《钢非金属夹杂物含量的测定标准评级图显微检验法》,替代ISO 4967:1998,但其内容仅有极少变化,其检验方法及评级图均未改变。
该标准的1988版已被GB/T 10561-2005等同采用。
(2)ISO 9341-1996ISO 9341-1996《光学和光学仪器接触镜固定接触镜中夹杂物和表面缺陷不完备性的测定》,介绍了使用固定接触镜检测夹杂物和表面缺陷的方法和步骤,已于2006年废止,并由ISO 18369.3:2006 《光学和光学仪器接触镜第3部分:测试方法》替代。
美国非金属夹杂物检验标准(1)ASTM B796-2014ASTM B796-2014《粉末锻造件非金属夹杂物含量测试方法》,替代 ASTM B796-2007,适用于粉末锻造件中非金属夹杂物级别金相法测定,要求试样核心区域100%无孔隙检出。
如有空隙存在,则残余的孔隙很难与氧化物夹杂区分。
(2)ASTM E45-2013ASTM E45-2013《测定钢材夹杂物含量的试验方法》,是应用相当广泛的非金属夹杂物检验标准,其中的检验方法包括4种宏观检验方法和5种微观检验方法(手动和图像分析),用来描述钢中夹杂物的含量和检验结果的报告方法,其中5种微观检验方法包括:A法(最差视场法)、B法(长度法)、C法(氧化物和硅酸盐法)、D法(低夹杂物含量法)和E法(SAM评级法);ASTM E45建立了一系列描述典型夹杂物特征(尺寸,类型和数量)的标准参考图谱(JK图谱和SAE图谱),其中SAE图谱见SAE手册上推荐的J422操作规程;A 法(最恶劣视场),D法(低夹杂物含量)和E法(SAM评级)的图谱是以JK图谱为基础开发的,而C法(氧化物和硅酸盐法)使用SAE 图谱。
(3)ASTM E1122-1996ASTM E1122-1996《应用自动图象分析测定JK夹杂物级别的标准试验方法》,已于2006年作废,相关内容融合到新修订的ASTM E45-2013中的A法和D法中。
钢中非金属夹杂物的金相鉴定实验

钢中非金属夹杂物的金相鉴定实验主讲教师:张明远一、实验目的�1.初步掌握金相显微镜的正确操作。
� 2 .初步掌握钢中非金属夹杂物的定性鉴定。
二、金相法的优缺点�1 优点�操作简便,迅速,直观。
不仅能确定夹杂物的类型,是氧化物、硫化物、硅酸盐还是复杂的固溶体,而且能直观的看到夹杂物的大小、形状、分布等等,夹杂物是球形还是有规则的外形,是弥散分布还是成群分布,是塑性夹杂还是脆性夹杂。
这将给改善工艺操作提供重要依据。
�2 缺点�只能定性的鉴定那些已知特性的夹杂物,就是表上列出的夹杂物。
因此,当遇到新的物质或复杂的固溶体时,还要配合其他的方法综合运用。
而且鉴定的准确度和熟练程度有关,即主要靠经验;不能确定夹杂物准确的化学组成,只能根据经验估计。
二、金相法的优缺点�要想确定夹杂物准确的化学组成,还需要用电子探针,打出夹杂物的成分分布:用电子:衍射或X射线衍射确定夹杂物的结构等。
�鉴定钢中非金属夹杂物的方法很多,各有优缺点。
例如:电子显微镜、X射线衍射、电解一化学�分析法等等。
若要对夹杂物进行准确和全面的鉴定往往需要综合使用这些方法。
�目前,常用的方法为:先用金相显微镜确定夹杂物有哪些类型,然后再测出不同规格夹杂物的数量,再用大样电解的方法将夹杂物分离出来,最后用电镜确定夹杂物的化学组成及成分分布。
三、钢中非金属夹杂物的来源�1 外来夹杂物。
�1) 冶炼、出钢及浇注过程中被卷入的耐火材料或炉渣等。
�2) 与原材料同时进入炉中的杂物。
�外来夹杂物一般较粗大:是可以减少和避免的。
�2 内生夹杂物。
� 1) 冶炼过程中加的脱氧剂及合金添加剂和钢中元素化学反应的产物,一部分在钢液凝�固前没有浮出而残留在钢中。
� 2) 在出钢和浇注过程中,钢水和大气接触,钢水中容易氧化和氮化的元素被氧化·氮�化的产物。
� 3) 从出钢到浇注过程中,·随钢水温度下降,造成氧、硫、氮等元素及其化台物的溶解度降低,因而产生或析出的类夹杂物。
钢中非金属夹杂物分析

钢中非金属夹杂物分析发布时间:2022-09-02T01:28:12.493Z 来源:《科学与技术》2022年4月8期(下)作者:李洪芳[导读] 非金属夹杂物在钢中含量虽少,但对材料性能影响较大,是钢材理化检验中不可缺少的一项,李洪芳内蒙古包钢钢联股份有限公司化检验中心内蒙古包头市014010摘要:非金属夹杂物在钢中含量虽少,但对材料性能影响较大,是钢材理化检验中不可缺少的一项,但由于其数量少、分布无规律、来源无法控制、光学显微镜下特征复杂等特点,给非金属夹杂物检验工作带来了一些困难。
钢中非金属夹杂物的金相鉴定工作是一项十分复杂与专业的工作,对钢中非金属夹杂物的判定十分重要,也能够对钢的质量进行反映。
在金相显微镜下,对非金属夹杂物的形态与颜色等进行判断,并对透明度等各种性质进行分析。
关键词:钢;非金属;夹杂物如今,现代工业技术的发展,对钢的质量和综合性能要求越来越高。
影响钢材性能的因素是多方面的,往往涉及到炼钢、轧钢和热处理等多道工序,而钢中非金属夹杂物的存在是影响钢材性能的一个重要因素,有时甚至是决定性因素。
钢中非金属夹杂物的研究一直是炼钢连铸生产中的重要课题,夹杂物分析是评定钢材质量的一个重要指标,并且被列为优质钢出厂常规检验项目之一。
钢中存在非金属夹杂物是不可避免的,钢中夹杂物包括内生夹杂物、外来夹杂物两大类,对于金相分析人员来说,如何正确判断和鉴定非金属夹杂物的性质是十分重要。
一、非金属夹杂物分类非金属夹杂物的分类方法也有很多种,根据非金属夹杂物的产生机理,可将其分为内生夹杂物和外来夹杂物两种,也是非金属夹杂物最常见的分类方法。
外来夹杂物主要是由耐高温材料、各类残渣或二者残留物,生成的废物。
外来夹杂物的形成是随机的,它是偶然性因素,人为不可控的,并且外来夹杂物是非规则的。
内生夹杂物是在炼钢过程中,各种物质发生反应,生成含有O、S、N等元素的废物,这些废物不能及时排出去,因而形成了内生夹杂物。
非金属夹杂物判定

钢中非金属夹杂物等级和分类根据GB/T 10561-2005《钢中非金属夹杂物含量的测定标准评级图显微检验法》标准规定如下:
A类:硫化物类夹杂物,由于它具有高的延展性,一般以单个细长的灰色夹杂物为常见类型,两端呈圆角状态。
B类:氧化铝类夹杂物,大多数没有变形,带角的,形态比小(一般﹤3 um),呈不规则的椭圆状,在金相显微镜下为黑色或蓝色的颗粒,沿钢材轧制方向排成一排,一排至少有3个以上颗粒组成。
C类:硅酸盐类夹杂物,具有较高的延展性,有较宽范围的形态比(一般≥3 um),其颜色呈黑色或深灰色夹杂,形态细长,一般头部呈锐角。
D类:球状氧化物类夹杂物,不易变形,带角或圆形状,形态比小(一般﹤3 um),是黑色或蓝色的,无规则分布的颗粒,这类夹杂物的组成比较多样复杂,有单相夹杂物,也有多相夹杂物,在金相显微镜下可见分布比较弥散。
DS类:为单颗粒的圆形球状夹杂物,直径较大,一般≥13um。
钢中非金属夹杂物含量高,尺寸大是造成紧固件冷镦开裂的一个重要原因,尤其是非金属夹杂物中B类和D类夹杂物,距线材表面越近危害性越大,所以要求B类夹杂物距表面2mm之内应不大于15μm。
B类和D类夹杂物一般控制在2级以内,这也可减少热处理淬火开裂的可能性,预防性。
钢中夹杂物知识

摘要:根据钢中非金属夹杂物的来源和分类,综述了鉴定钢中非金属夹杂物的方法和定量评级标准,并且给出了典型夹杂物的扫描电镜照片,分析了不同类型夹杂物的形成机理及其在光学显微镜下的基本特征。
随着现代工程技术的发展,对钢的综合性能要求也日趋严格,相应地对钢的材质要求了越来越高。
非金属夹杂物作为独立相存在于钢中,破坏了钢基体的连续性,加大了钢中组织的不均匀性,严重影响了钢的各种性能。
例如,非金属夹杂物导致应力集中,引起疲劳断裂;数量多且分布不均匀的夹杂物会明显降低钢的塑性、韧性、焊接性以及耐腐蚀性;钢中呈网状存在的硫化物会造成热脆性。
因此,夹杂物的数量和分布被认定是评定钢材质量的一个重要指标,并且被列为优质钢和高级优质钢出厂的常规检测项目这一。
非金属夹杂物的性质、形态、分布、尺寸及含量不同,对钢性能的影响也不同。
所以提高金属材料的质量,生产出洁净钢,或控制非金属夹杂物性质和要求的形态,是冶炼和铸锭过程中的一个艰巨任务。
而对于金相分析工作者来说,如何正确判断和鉴定非金属夹杂笺也因此变得十分重要。
1 钢中非金属夹杂物的来源分类1.1 内生夹杂物钢在冶炼过程中,脱氧反应会产生氧化物和硅酸盐等产物,若在钢液凝固前未浮出,将留在钢中。
溶解在钢液中的氧、硫、氮等杂质元素在降温和凝固时,由于溶解度的降低,与其他元素结合以化合物形式从液相或固溶体中析出,最后留在钢锭中,它是金属在熔炼过程中,各种物理化学瓜形成的夹杂物。
内生夹杂物分布比较均匀,颗粒也较小,正确的操作和合理的工艺措施可以减少其数量和改变其成分、大小和分布情况,但一般来说是不可避免的。
1.2 外来夹杂物钢在冶炼和浇注过程中悬浮在钢液表面的炉渣、或由炼钢炉、出钢槽和钢包等内壁肃落的耐火材料或其他夹杂物在钢液凝固前未及时清除而留于钢中。
它是金属在熔炼过程中与外界物质接触发生作用产生的夹杂物。
如炉料表面的砂土和炉衬等与金属液作用,形成熔渣而滞留在金属中,其中也包括加入的熔剂。