分选机PLC介绍
2.3分拣站PLC控制

四、传送和分拣的工作原理
本站的功能是完成从装配站送来的装配好的工件进行分拣。当输送站送来工件放到传送带上并为入料口漫射式光电传感器检测到时,将信号传输给PLC,通过PLC的程序启动变频器,电机运转驱动传送带工作,把工件带进分拣区,如果进入分拣区工件为白色,则检测白色物料的光纤传感器动作,作为1号槽
行分拣,使不同颜色的工件从不同的料槽分流的功能。当输送站送来工件放到传送带上并为入料口光电传感器检测到时,即启动变频器,工件开始送入分拣区进行分拣。
如图6-1所示分拣单元实物的全貌。
三、传送和分拣机构
传送和分拣机构如图6-3所示。传送已经加工、装配好的工件,在光纤传感器检测到并进行分拣。它主要由传送带、物料槽、推料(分拣)气缸、漫射式光电传感器、光纤传感器、磁感应接近式传感器组成。
项目二:2.3分拣站PLC控制
一、分拣单元的主要结构组成
主要结构组成为:传送和分拣机构,传动机构,变频器模块,电磁阀组,接线端口,PLC模块,底板等。它主要由传送带、物料槽、推料(分拣)气缸、漫射式光电传感器、旋转编码器、金属传感器、光纤传感器、磁感应接近式传感器组成。
二、分拣单元功能
分拣单元是335A中的最末Байду номын сангаас元,完成对上一单元送来的已加工、装配的工件进
连接了②④⑤三个端子。
图6-15 VF100的主电路接线
图6-16 VF100的控制电路接线
图6-17 VF100变频器操作面板示意图
1.熟悉分拣单元的功能及结构组成。
2.能够根据控制要求了解气动控制回路原理。
基于PLC的物料分拣系统设计
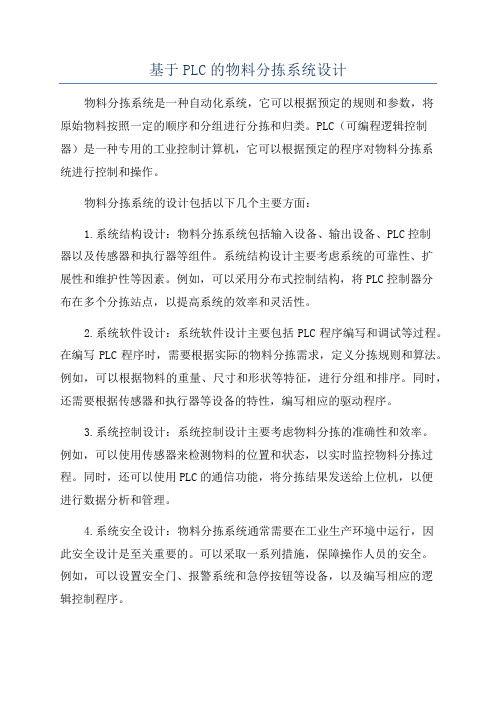
基于PLC的物料分拣系统设计物料分拣系统是一种自动化系统,它可以根据预定的规则和参数,将原始物料按照一定的顺序和分组进行分拣和归类。
PLC(可编程逻辑控制器)是一种专用的工业控制计算机,它可以根据预定的程序对物料分拣系统进行控制和操作。
物料分拣系统的设计包括以下几个主要方面:1.系统结构设计:物料分拣系统包括输入设备、输出设备、PLC控制器以及传感器和执行器等组件。
系统结构设计主要考虑系统的可靠性、扩展性和维护性等因素。
例如,可以采用分布式控制结构,将PLC控制器分布在多个分拣站点,以提高系统的效率和灵活性。
2.系统软件设计:系统软件设计主要包括PLC程序编写和调试等过程。
在编写PLC程序时,需要根据实际的物料分拣需求,定义分拣规则和算法。
例如,可以根据物料的重量、尺寸和形状等特征,进行分组和排序。
同时,还需要根据传感器和执行器等设备的特性,编写相应的驱动程序。
3.系统控制设计:系统控制设计主要考虑物料分拣的准确性和效率。
例如,可以使用传感器来检测物料的位置和状态,以实时监控物料分拣过程。
同时,还可以使用PLC的通信功能,将分拣结果发送给上位机,以便进行数据分析和管理。
4.系统安全设计:物料分拣系统通常需要在工业生产环境中运行,因此安全设计是至关重要的。
可以采取一系列措施,保障操作人员的安全。
例如,可以设置安全门、报警系统和急停按钮等设备,以及编写相应的逻辑控制程序。
在物料分拣系统的实际应用中,还需要考虑一些其他因素,如设备的选型和配置、系统的维护和保养等。
此外,还可以将物料分拣系统与其他自动化设备相结合,实现各个环节的无人化和智能化。
总之,基于PLC的物料分拣系统设计是一项复杂的工作,需要综合考虑多个方面的因素。
合理的系统结构设计、可靠的系统软件设计、高效的系统控制设计和安全的系统安全设计是保证系统正常运行和提高系统效率的关键。
通过合理配置和运用PLC技术,物料分拣系统可以在工业生产中发挥重要作用,提高生产效率和品质水平,降低生产成本和劳动强度。
基于某PLC的自动控制分拣系统的设计

基于某PLC的自动控制分拣系统的设计自动控制分拣系统是现代物流仓储行业非常重要的一环,它能够提高分拣的效率和准确性,降低分拣过程中的人为错误率,减少人力成本。
本文将基于PLC来设计一个自动控制分拣系统。
该系统的主要功能是将不同种类的货物根据事先设定的规则自动进行分拣,并将其送到相应的目的地或存储区域。
系统包括输入设备、PLC、执行机构和输出设备四个主要部分。
1.输入设备:将待分拣的货物信息输入到系统中。
例如,可以使用条形码扫描设备将货物的条形码信息输入到PLC。
2.PLC:作为系统的核心控制设备,负责接收输入的货物信息,并根据事先设定的规则进行分拣指令的生成。
PLC还可以接收其他传感器中的信息,如输送机上的检测装置,以确保分拣过程的准确性。
3.执行机构:根据PLC生成的指令,将货物送到相应的目的地。
执行机构可以是机械臂、输送带或滑道等。
这些设备需要与PLC进行通信,接收和执行PLC的指令。
4.输出设备:该设备用于输出分拣结果。
例如,可以使用LED显示屏或打印机来显示或打印分拣结果,以供操作员查看。
在设计该自动控制分拣系统时,首先需要进行需求分析和系统功能分析,确定具体的分拣规则和分拣目的地。
然后,根据这些规则和目的地,编写PLC的程序,实现分拣系统的自动控制。
在编写PLC程序时,需要考虑到各种情况,例如货物种类的多样性、货物尺寸的不同、运输速度的变化等。
接下来,需要选择适合的执行机构。
根据不同的需求,可以选择机械臂、输送带或滑道等设备。
这些设备需要与PLC进行连锁操作,以确保分拣的准确性和效率。
最后,在实际应用中,需要对系统进行测试和调试。
这包括验证系统是否能够按照设计的规则进行分拣,以及是否能够正常运行。
在测试和调试过程中,可能会遇到一些问题,例如分拣错误、传感器故障等,需要及时解决和修复。
总之,基于PLC的自动控制分拣系统的设计需要从需求分析、PLC编程、执行机构选择和测试调试等多个方面考虑。
PLC控制大小球分拣传送机

PLC控制大小球分拣传送机1. 引言本文档介绍了如何使用PLC(可编程逻辑控制器)控制大小球分拣传送机。
传送机是工厂自动化生产线中常见的设备,它可以将待分拣的物体按照不同的尺寸分拣到不同的位置。
本文档详细描述了PLC控制大小球分拣传送机的硬件结构、PLC 程序设计以及运行原理。
2. 硬件结构大小球分拣传送机的硬件结构主要包括以下几个部分: - 传送带:用于将物体从起点传送到分拣区域。
- 传感器:用于检测物体的尺寸。
- 分拣装置:根据检测到的尺寸,将物体分拣到不同的位置。
- PLC:负责控制传送带、传感器和分拣装置的运行。
3. PLC程序设计PLC程序设计是控制大小球分拣传送机的关键。
下面是一个简单的PLC程序的框图示例:START|- 检测传感器状态|- 如果感知到小球|- 传送带升起|- 推动小球到小球分拣位置|- 如果感知到大球|- 传送带升起|- 推动大球到大球分拣位置|- 传送带下降END在PLC程序中,首先会检测传感器的状态。
当感知到小球时,传送带会升起,然后将小球推动到小球分拣位置。
当感知到大球时,传送带会升起,然后将大球推动到大球分拣位置。
最后,传送带会下降,准备接收下一个物体。
4. 运行原理当PLC接收到输入信号后,按照程序的逻辑顺序执行相应的输出操作。
在本例中,PLC会根据传感器的输出信号,控制传送带的升降和分拣装置的运动,以实现大小球的分拣。
传送带通过电机驱动,可以根据PLC的控制信号控制其升降。
传感器通过感知物体的尺寸来产生输出信号,然后将该信号传送给PLC。
分拣装置根据PLC的控制信号,将物体推送到相应的分拣位置。
5. 总结本文档介绍了使用PLC控制大小球分拣传送机的原理和方法。
通过合理的硬件结构设计和PLC程序编写,可以实现精确而高效的物体分拣。
基于PLC的自动分拣器设计
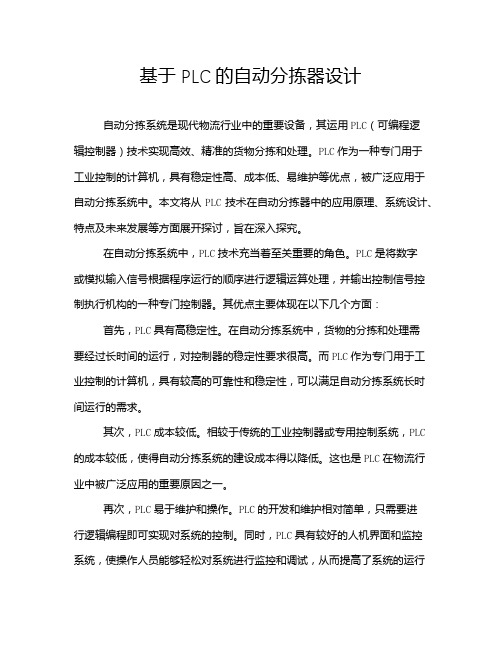
基于PLC的自动分拣器设计自动分拣系统是现代物流行业中的重要设备,其运用PLC(可编程逻辑控制器)技术实现高效、精准的货物分拣和处理。
PLC作为一种专门用于工业控制的计算机,具有稳定性高、成本低、易维护等优点,被广泛应用于自动分拣系统中。
本文将从PLC技术在自动分拣器中的应用原理、系统设计、特点及未来发展等方面展开探讨,旨在深入探究。
在自动分拣系统中,PLC技术充当着至关重要的角色。
PLC是将数字或模拟输入信号根据程序运行的顺序进行逻辑运算处理,并输出控制信号控制执行机构的一种专门控制器。
其优点主要体现在以下几个方面:首先,PLC具有高稳定性。
在自动分拣系统中,货物的分拣和处理需要经过长时间的运行,对控制器的稳定性要求很高。
而PLC作为专门用于工业控制的计算机,具有较高的可靠性和稳定性,可以满足自动分拣系统长时间运行的需求。
其次,PLC成本较低。
相较于传统的工业控制器或专用控制系统,PLC 的成本较低,使得自动分拣系统的建设成本得以降低。
这也是PLC在物流行业中被广泛应用的重要原因之一。
再次,PLC易于维护和操作。
PLC的开发和维护相对简单,只需要进行逻辑编程即可实现对系统的控制。
同时,PLC具有较好的人机界面和监控系统,使操作人员能够轻松对系统进行监控和调试,从而提高了系统的运行效率。
基于以上优点,PLC技术被广泛应用于自动分拣系统中。
其设计原理主要包括输入模块、处理器、输出模块和通信模块等组成。
输入模块用于接收传感器等设备提供的信号,处理器对输入信号进行逻辑处理,根据预先编写的程序输出控制信号,输出模块则将信号传输到执行机构控制其动作,通信模块用于与外部系统进行通信。
在自动分拣器设计中,PLC技术的运用可以实现货物的分拣、移动、堆垛等操作,提高了分拣效率和精度。
通过编写合适的逻辑程序和算法,PLC可以根据货物的属性、目的地等信息,智能地控制分拣器的运行,实现货物的快速准确分拣。
此外,基于PLC的自动分拣器还具有以下几个特点:首先,高效性。
物料分拣控制系统的设计(PLC)

目录中文摘要英文摘要1绪论1.1课题的背景和意义1.2材料分拣系统国内外研究现状1.3材料分拣系统特点1.4PLC简介及特点1.5本课题的设计内容2材料分拣系统工作原理和总体设计2.1工作原理2.2总体设计2.2.1结构设计2.2.2系统结构组成3PLC 控制系统的硬件设计3.1系统主回路设计3.2 PLC控制系统的设备组成3.3 CPU及数字量扩展模块选择4PLC控制系统的软件设计4.1PLC程序结构4.2PLC编程4.3PID控制的功能指令5结论致谢参考文献(附录)基于PLC的材料分拣系统摘要随着社会的不断进步,市场竞争的日趋激烈,各个生产企业都迫切地需要改进生产技术,提高生产效率,尤其在需要进行材料分拣的企业,以往一直采用人工分拣的方法,致使生产效率低,生产成本高,企业的竞争能力差,材料的自动分拣已成为企业的唯一选择。
本论文分析材料分拣系统的工作原理及系统的组成结构,采用稳定性较好的工控设备PLC对材料的运输、分拣进行实时控制。
最后对系统的软硬件设计进行详细的介绍。
本论文的材料分拣系统已在国内外许多实际的材料分拣系统中得到应用,并取得稳定可靠的运行效果和良好的节能效果。
经实践证明该系统能极大的节省劳力,具有明显的经济效益和社会效益。
关键词:材料分拣;自动生产线;物料传送;PLC;The material sorting system based on PLCAbstractWith the development of society, market competition become very fierce.Every enterprise tries its best to improve production technology for improving the productivity efficiency, especially in the enterprises which need the technology of material sorting .Many years ago ,we use hand to sort material. This method has low production efficiency,but high production costs. So automatic sorting has become the only choice of enterprises.This paper analyzes the working principle of material sorting system and introduce the structure of the system.This system has used PLC which has a good stability.I use PLC to control the transportation of material and sorting. In the end, the system hardware and software designing were introduced in detail. The material sorting system in this paper has been used in many factories at home and abroad.And it has a stable and reliable performance and good effect in energy saving. Using this control system can save the labor and get obvious economic benefits and social benefits.Keywords: material sorting; Automatic production line; PLC;1绪论1.1课题的背景和意义从二十世纪20年代开始,随着汽车、滚动轴承、小型电动机和缝纫机等工业发展,机械制造中开始出现自动线,最早出现的是组合机床自动线。
基于plc的物流分拣系统
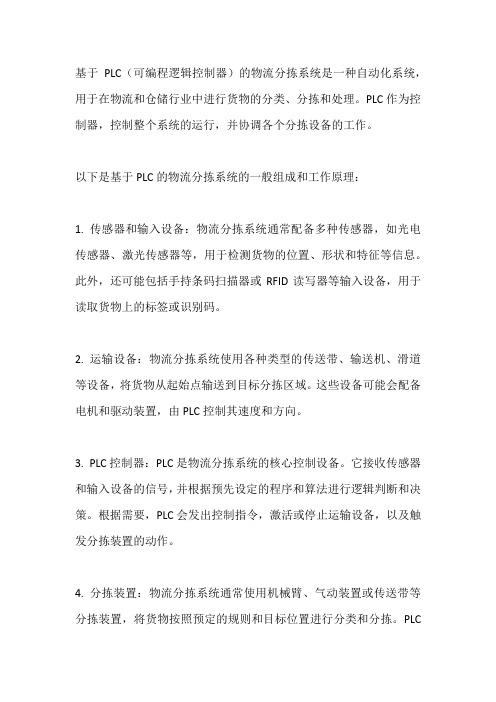
基于PLC(可编程逻辑控制器)的物流分拣系统是一种自动化系统,用于在物流和仓储行业中进行货物的分类、分拣和处理。
PLC作为控制器,控制整个系统的运行,并协调各个分拣设备的工作。
以下是基于PLC的物流分拣系统的一般组成和工作原理:1. 传感器和输入设备:物流分拣系统通常配备多种传感器,如光电传感器、激光传感器等,用于检测货物的位置、形状和特征等信息。
此外,还可能包括手持条码扫描器或RFID读写器等输入设备,用于读取货物上的标签或识别码。
2. 运输设备:物流分拣系统使用各种类型的传送带、输送机、滑道等设备,将货物从起始点输送到目标分拣区域。
这些设备可能会配备电机和驱动装置,由PLC控制其速度和方向。
3. PLC控制器:PLC是物流分拣系统的核心控制设备。
它接收传感器和输入设备的信号,并根据预先设定的程序和算法进行逻辑判断和决策。
根据需要,PLC会发出控制指令,激活或停止运输设备,以及触发分拣装置的动作。
4. 分拣装置:物流分拣系统通常使用机械臂、气动装置或传送带等分拣装置,将货物按照预定的规则和目标位置进行分类和分拣。
PLC控制器会根据输入的数据和算法,指导分拣装置的动作,将货物送至对应的出口或储存区域。
5. 人机界面:为了方便操作和监控物流分拣系统,通常会设置人机界面(HMI),提供可视化的界面和控制面板。
操作员可以通过HMI 进行参数设置、故障诊断和实时监控,确保系统的稳定运行。
基于PLC的物流分拣系统能够提高分拣效率、减少人工成本,并降低错误率。
通过合理设计和调试,结合适当的传感器和分拣装置,可以满足不同物流环境中的分拣需求。
然而,具体的物流分拣系统需要根据实际情况进行定制和优化,建议在实施前咨询专业的自动化设备供应商或工程师,以确保系统的可靠性和适应性。
PLC分拣系统
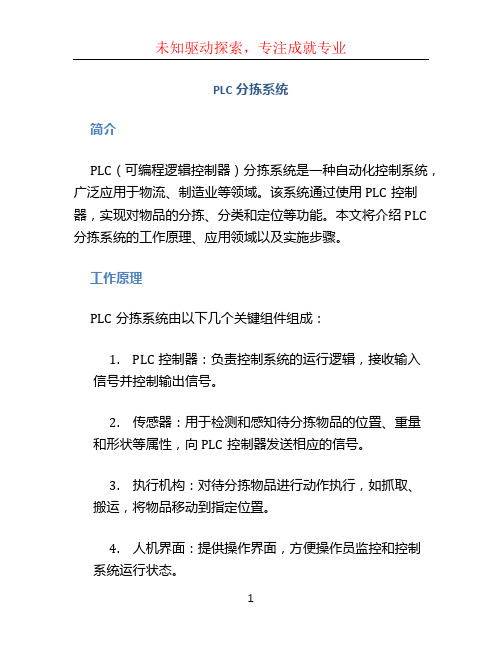
PLC分拣系统简介PLC(可编程逻辑控制器)分拣系统是一种自动化控制系统,广泛应用于物流、制造业等领域。
该系统通过使用PLC控制器,实现对物品的分拣、分类和定位等功能。
本文将介绍PLC 分拣系统的工作原理、应用领域以及实施步骤。
工作原理PLC分拣系统由以下几个关键组件组成:1.PLC控制器:负责控制系统的运行逻辑,接收输入信号并控制输出信号。
2.传感器:用于检测和感知待分拣物品的位置、重量和形状等属性,向PLC控制器发送相应的信号。
3.执行机构:对待分拣物品进行动作执行,如抓取、搬运,将物品移动到指定位置。
4.人机界面:提供操作界面,方便操作员监控和控制系统运行状态。
系统的工作流程如下:1.系统启动后,PLC控制器开始运行,并从传感器获取输入信号。
2.传感器检测到待分拣物品的属性后,将相关信号发送给PLC控制器。
3.PLC控制器根据接收到的信号,判断应当执行的操作,并控制执行机构进行相应的动作。
4.执行机构按照PLC控制器的指令,对待分拣物品进行抓取、搬运等动作。
5.分拣完成后,执行机构将物品移动到指定位置,并向PLC控制器发送信号确认完成。
6.PLC控制器更新系统状态,等待下一次分拣任务。
应用领域PLC分拣系统广泛应用于各个领域,尤其在物流和制造业的自动化生产线上得到了广泛应用。
以下是PLC分拣系统应用的几个典型领域:1.电子产品制造:PLC分拣系统可以对电子产品进行分类和检验,提高生产效率和质量。
2.物流分拣中心:PLC分拣系统可以帮助物流中心快速准确地进行货物分类、分拣,提高物流效率。
3.食品加工行业:PLC分拣系统可以对食品进行分拣和包装,降低人工损耗,提高食品安全和卫生。
4.仓储物料管理:PLC分拣系统可以对仓储物料进行分拣和管理,减少人工操作,提高仓储效率。
实施步骤实施PLC分拣系统通常需要以下几个步骤:1.需求分析:根据实际需求,明确分拣系统的功能和性能要求。
2.设计方案:根据需求分析结果,设计PLC控制器、传感器、执行机构等硬件设备,并进行系统整体架构设计。
分拣物品控制系统PLC设计
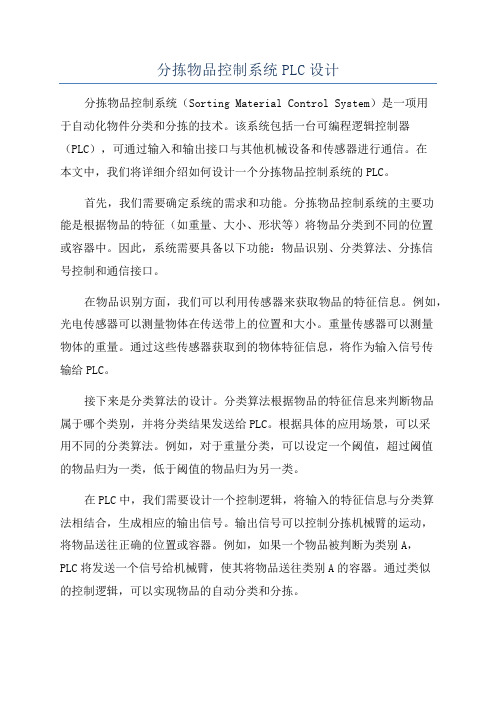
分拣物品控制系统PLC设计分拣物品控制系统(Sorting Material Control System)是一项用于自动化物件分类和分拣的技术。
该系统包括一台可编程逻辑控制器(PLC),可通过输入和输出接口与其他机械设备和传感器进行通信。
在本文中,我们将详细介绍如何设计一个分拣物品控制系统的PLC。
首先,我们需要确定系统的需求和功能。
分拣物品控制系统的主要功能是根据物品的特征(如重量、大小、形状等)将物品分类到不同的位置或容器中。
因此,系统需要具备以下功能:物品识别、分类算法、分拣信号控制和通信接口。
在物品识别方面,我们可以利用传感器来获取物品的特征信息。
例如,光电传感器可以测量物体在传送带上的位置和大小。
重量传感器可以测量物体的重量。
通过这些传感器获取到的物体特征信息,将作为输入信号传输给PLC。
接下来是分类算法的设计。
分类算法根据物品的特征信息来判断物品属于哪个类别,并将分类结果发送给PLC。
根据具体的应用场景,可以采用不同的分类算法。
例如,对于重量分类,可以设定一个阈值,超过阈值的物品归为一类,低于阈值的物品归为另一类。
在PLC中,我们需要设计一个控制逻辑,将输入的特征信息与分类算法相结合,生成相应的输出信号。
输出信号可以控制分拣机械臂的运动,将物品送往正确的位置或容器。
例如,如果一个物品被判断为类别A,PLC将发送一个信号给机械臂,使其将物品送往类别A的容器。
通过类似的控制逻辑,可以实现物品的自动分类和分拣。
为了实现系统的稳定运行和故障诊断,还需要设计相应的检测和保护机制。
例如,当传感器或机械臂出现故障时,PLC能够及时发现并采取相应的措施,如发送警报信号或切换到备用设备。
此外,我们还需要设计一个通信接口,使PLC能够与其他设备进行通信。
例如,PLC可以通过以太网接口与上位机通信,以获取系统的状态信息和控制指令。
通过与上位机的通信,PLC可以实现远程监控和控制,提高系统的灵活性和可维护性。
plc物料分拣系统毕业设计

plc物料分拣系统毕业设计PLC物料分拣系统是一种利用可编程逻辑控制器(PLC)技术对物料进行分拣的系统。
该系统通过传感器和执行器来感知和控制物料的运动,并根据预设的分拣规则将物料分拣到相应的位置。
本文将介绍PLC物料分拣系统的原理和设计要点,并讨论相关的参考内容。
首先,PLC物料分拣系统的原理可以分为以下几个步骤:感知物料、分析物料、控制物料运动、执行分拣操作。
感知物料:系统通过使用传感器来感知物料的到达。
常用的传感器包括光电传感器、激光传感器和颜色传感器等。
这些传感器可以感知物料的位置、颜色、形状等特征。
分析物料:一旦物料被感知到,PLC将收集传感器的数据,并根据预设的分拣规则对物料进行分析。
通常,分析物料可以包括识别物料类型、重量、尺寸等。
控制物料运动:当物料被分析后,PLC将根据分析结果控制物料的运动。
这可以通过控制传送带、滑槽、电磁阀等执行器来实现。
PLC可以使用逐步执行的模式来控制物料的准确位置和速度。
执行分拣操作:最后,根据分析的结果和控制命令,执行器将根据指令将物料分拣到正确的位置。
这通常是通过控制气动装置、电磁铁或机械臂等来实现的。
对于PLC物料分拣系统的设计要点,主要包括以下几个方面:1. 传感器选择和布置:正确选择和布置传感器非常重要,以确保能够准确感知物料的位置、状态和特征。
需要根据物料的特性和分拣要求,选择合适的传感器,并根据实际情况布置传感器的位置和方向。
2. 分析规则和算法:设计分析规则和算法来识别物料类型、重量、尺寸等是设计过程中的关键环节。
这涉及到利用PLC编程语言(如Ladder Diagram、Structured Text等)进行逻辑控制和判断。
需要根据不同物料的特征和分拣要求,灵活运用逻辑控制来实现分拣操作。
3. 控制信号和执行器选择:设计控制信号和选择合适的执行器也是非常重要的。
根据分拣系统的要求,选择适当的控制信号(如开关量、模拟量)和执行器(如电机、气动装置)来实现物料的运动控制和分拣操作。
基于PLC的厨余垃圾分选自动控制系统

异常处理
2、电源故障:如系统电源出现故障,PLC将无法正常工作。应对措施为设置 UPS设备,确保在电源故障时PLC仍能正常工作一段时间。
异常处理
3、网络故障:如PLC与其他设备之间的通信出现故障,系统将无法实现远程 控制。应对措施为设置通信备份线路,当主线路故障时,自动切换到备份线路。
异常处理
系统测试
系统测试
为了验证基于PLC的厨余垃圾分选自动控制系统的性能,我们进行了以下测试: 1、测试方法:采用模拟厨余垃圾进行系统测试,将不同成分的垃圾放入系统 中,观察分选效果。
系统测试
2、测试结果:通过测试,系统能够准确识别不同类型的垃圾,按照预设的分 选逻辑将垃圾分为可回收物、有机物和不可利用物等不同类别。
5、通信模块:用于实现PLC与其 他设备的数据交换。
各部分通过相应的连接方式组成 完整的控制系统。
程序编写
程序编写
PLC的编程语言包括指令式编程和结构化编程等。在自动洗衣机控制系统的程 序编写中,一般采用结构化编程方法,将程序分为不同的功能块,便于调试和维 护。以下是编程时需注意的技巧:
1、合理使用PLC的输入输出模块, 确保信号的正确传递。
引言
引言
可编程逻辑控制器(PLC)作为一种可靠的自动化控制设备,已在众多行业得 到广泛应用。其中,自动洗衣机控制系统中PLC的应用具有重要地位。本次演示 将详细介绍基于PLC的自动洗衣机控制系统的设计、程序编写、控制方式及异常 处理等方面,旨在提高洗衣机的自动化水平和使用体验。
关键词:PLC、自动洗衣机、控 制系统
二、国外厨余垃圾处理技术
二、国外厨余垃圾处理技术
1、堆肥法:堆肥法是将厨余垃圾转化为有机肥料的一种处理方法。通过堆肥 处理,厨余垃圾中的有机物质可以转化为肥料,用于农业和园艺业。在欧洲和北 美,堆肥法已经成为一种主流的厨余垃圾处理方式。
分拣机(PLC+交流电机+电气元件)毕业设计

河南工业职业技术学院毕业设计标题:自动分拣站(PLC+交流电机+气动元件)控制系统系别:电气工程系专业:电气自动化专业学号:0401090219姓名:张少杰指导教师:屈保忠2011年12月1日摘要分拣控制系统在社会各行各业如:物流配送中心、邮局、采矿、港口、码头、仓库等行业得到广泛运用,分拣系统能够大大提高企事业单位该环节的生产效率。
本文在对熟悉了自动及分拣系统的原理的基础上,根据一定的分拣要求,对材料分拣进行了以三菱PLC为控制核心,MCGS组态软件为监控软件,设计出材料分拣控制系统的控制系统和监控系统。
该材料分拣系统以PLC为主控制器,结合气动装置、传感器技术、组态监控等技术,可以进行现场控制产品的自动分拣。
系统具有自动化程度高、运行稳定、分拣精度高、易控制的特点,对不同的分拣对象,稍加修改本系统即可实现要求。
对本系统完成其设计之后,进行了整体调试。
在硬件部分,调试其各部分安装的位置及角度,使其材料物块的运行与传感器安装的角度适合。
将硬件各部分的动作幅度进行调试之后,进行了软硬件综合调试,实现材料分拣系统中上料、传送与分拣的全过程。
关键词:材料分拣传感器气动装置 PLC MCGS组态软件前言自动分拣是指货物进入分拣系统到指定的分配位置为止,都是按照人们的指令靠自动装置来完成的。
这种装置是由接受分拣指示信息的控制装置、计算机网络、搬运装置、分支装置(负责把到达分拣位置的货物按运到别处的装置)、缓冲站(在分拣位置临时存放货物的装置)等构成。
除了使用终端的键盘、鼠标或者其它方式向控制装置输入分拣指示信息的作业外,由于全部采用自动控制作业,因此它的分拣能力、分拣数量同人为分拣相比都比较大,效率也得到了进一步突破。
自动分拣系统的规模和能力已有很大的发展,目前大型分拣系统大多能分拣几十到几百个种类的物品,分拣能力达到每小时万件以上。
国外分拣系统规模都很大,主要包括进给台、信号盘、分拣机、分拣信息识别系统、设备控制系统和计算机管理系统等几大部分,还要配备外围的各种运输和装卸机械,组成一个庞大而复杂的系统。
基于plc的快递分拣系统的设计的控制功能
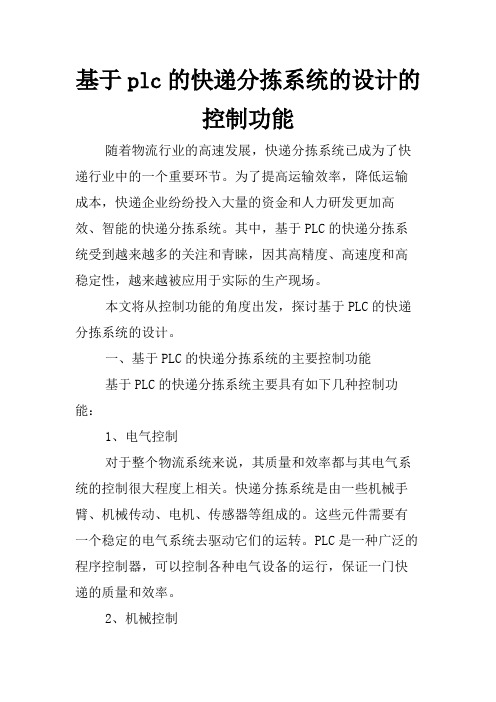
基于plc的快递分拣系统的设计的控制功能随着物流行业的高速发展,快递分拣系统已成为了快递行业中的一个重要环节。
为了提高运输效率,降低运输成本,快递企业纷纷投入大量的资金和人力研发更加高效、智能的快递分拣系统。
其中,基于PLC的快递分拣系统受到越来越多的关注和青睐,因其高精度、高速度和高稳定性,越来越被应用于实际的生产现场。
本文将从控制功能的角度出发,探讨基于PLC的快递分拣系统的设计。
一、基于PLC的快递分拣系统的主要控制功能基于PLC的快递分拣系统主要具有如下几种控制功能:1、电气控制对于整个物流系统来说,其质量和效率都与其电气系统的控制很大程度上相关。
快递分拣系统是由一些机械手臂、机械传动、电机、传感器等组成的。
这些元件需要有一个稳定的电气系统去驱动它们的运转。
PLC是一种广泛的程序控制器,可以控制各种电气设备的运行,保证一门快递的质量和效率。
2、机械控制机械控制是指PLC通过控制机械元件运动的顺序、方式、位置与速度等来实现系统的控制。
PLC可以进行图形操作界面的设计与设置操作,可以预测机械运动的轨迹,精确控制机械手臂实现分拣功能。
3、数据处理在整个物流系统中,需要持续监控物流信息,有效的记录和传输各种数据的同时,执行相应的控制功能。
基于PLC的快递分拣系统可以实现物流数据的精确定位,记录每一个快递的物流信息,同时,对于快递分拣的任务也能更加精确高效的操作。
二、快递分拣机工作原理基于PLC的快递分拣系统的工作原理如下:1. 快递进入检测和称重系统快递包裹通过运输设备进入快递分拣机的第一个环节,经过一个电子称重模块后,包裹的重量数据被实时记录并上传到计算机控制系统,该系统可根据这些信息直接在运输带线路上对快递进行分拣。
2. 建立快递数据信息库快递分拣机将检测到的快递信息记录到数据库中,将快递的相应信息与其重量数据进行匹配,然后将其寄到快递分拣系统中,保证数据的精准管理。
3. 数据库中进行分拣操作基于PLC的快递分拣系统可以在对快递重量数据分析后,分配相应的 sorting 号码区域,同时分配相应的机械臂的动作轨迹和位置。
分拣机plc课程设计

分拣机plc课程设计一、课程目标知识目标:1. 理解PLC(可编程逻辑控制器)的基本原理和工作流程;2. 掌握分拣机的基本结构及其功能;3. 学会使用PLC编程软件进行程序设计,实现分拣机的自动控制功能;4. 了解传感器在分拣机中的应用,及其与PLC的连接方式。
技能目标:1. 能够运用PLC编程软件进行基本的逻辑编程;2. 能够根据实际需求,设计并调试分拣机PLC控制系统;3. 学会分析并解决分拣机PLC控制系统中的故障;4. 培养学生的团队协作和沟通能力,提高实际操作中的问题解决能力。
情感态度价值观目标:1. 培养学生对自动化技术及其应用的兴趣,提高学习积极性;2. 增强学生的环保意识,认识到自动化技术在节能降耗方面的优势;3. 树立正确的价值观,认识到技术发展对国家和社会的重要性;4. 培养学生的创新精神和实践能力,激发学生积极参与技术改造和创新。
本课程针对高年级学生,结合学科特点,注重理论与实践相结合,旨在提高学生对PLC及分拣机控制技术的理解和应用能力。
课程目标具体、可衡量,以便学生和教师能够清晰地了解课程的预期成果,并为后续的教学设计和评估提供依据。
二、教学内容1. PLC基本原理:介绍PLC的发展历程、基本组成、工作原理及其在工业自动化中的应用。
教材章节:第一章PLC概述。
2. 分拣机结构与功能:分析分拣机的机械结构、传感器选型及其在自动化生产线中的作用。
教材章节:第三章自动化设备结构与功能。
3. PLC编程软件应用:学习PLC编程软件的使用方法,进行基本逻辑编程和仿真。
教材章节:第五章PLC编程软件的使用。
4. 分拣机PLC控制系统设计:结合实际需求,设计分拣机PLC控制系统,实现自动控制功能。
教材章节:第七章PLC控制系统设计与应用。
5. 传感器与PLC连接:介绍传感器与PLC的连接方式,学习传感器信号的输入与输出。
教材章节:第四章传感器与PLC的连接。
6. 系统调试与故障排除:学习分拣机PLC控制系统的调试方法,分析并解决可能出现的故障。
毕业设计(论文)-分拣机器人PLC控制系统设计
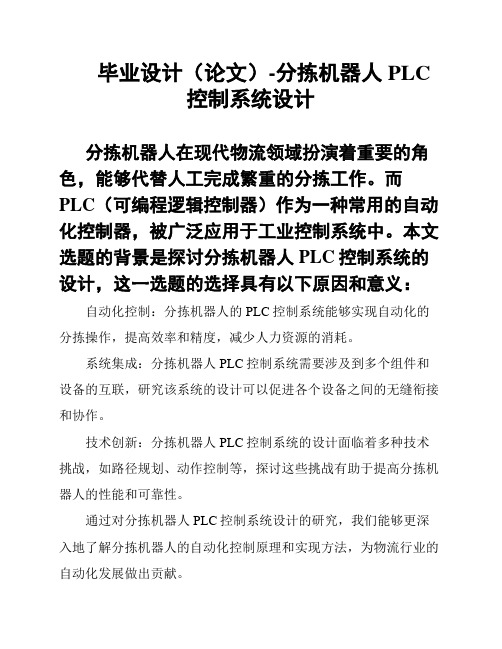
毕业设计(论文)-分拣机器人PLC控制系统设计分拣机器人在现代物流领域扮演着重要的角色,能够代替人工完成繁重的分拣工作。
而PLC(可编程逻辑控制器)作为一种常用的自动化控制器,被广泛应用于工业控制系统中。
本文选题的背景是探讨分拣机器人PLC控制系统的设计,这一选题的选择具有以下原因和意义:自动化控制:分拣机器人的PLC控制系统能够实现自动化的分拣操作,提高效率和精度,减少人力资源的消耗。
系统集成:分拣机器人PLC控制系统需要涉及到多个组件和设备的互联,研究该系统的设计可以促进各个设备之间的无缝衔接和协作。
技术创新:分拣机器人PLC控制系统的设计面临着多种技术挑战,如路径规划、动作控制等,探讨这些挑战有助于提高分拣机器人的性能和可靠性。
通过对分拣机器人PLC控制系统设计的研究,我们能够更深入地了解分拣机器人的自动化控制原理和实现方法,为物流行业的自动化发展做出贡献。
二、研究目的与意义明确研究的目的和意义,说明分拣机器人PLC控制系统设计在实际应用中的重要性和潜在的价值。
分拣机器人在现代工业生产中扮演着重要角色,能够实现自动化的物料分拣任务。
PLC控制系统是分拣机器人工作的核心,它负责对机器人的动作和运动进行精确控制。
因此,对于分拣机器人PLC控制系统设计的研究具有一定的重要性和意义。
首先,通过研究分拣机器人PLC控制系统设计,可以提高分拣效率和准确性。
传统的手工分拣方式存在速度慢、错误率高的问题。
而通过合理设计PLC控制系统,可以实现对分拣机器人的精确控制,提高分拣速度和准确性,从而提高工业生产的效率。
其次,分拣机器人PLC控制系统设计的研究可推动工业自动化水平的提升。
随着工业智能化的发展,越来越多的企业开始引入分拣机器人来完成物料分拣工作。
而PLC控制系统作为分拣机器人的核心控制部件,其稳定性和可靠性直接影响着分拣机器人的工作效果。
因此,深入研究分拣机器人PLC控制系统的设计,可以提升工业自动化水平,推动工业智能化的进一步发展。
材料自动分拣系统的PLC设计

材料自动分拣系统的PLC设计PLC(可编程逻辑控制器)是材料自动分拣系统中的核心控制单元。
它通常由中央处理器、输入/输出模块、通信模块和电源模块等组成。
PLC的设计要求具备以下功能:1.输入/输出处理:PLC需要能够处理外部传感器和执行机构的输入和输出。
因此,设计需要确保PLC具备足够的数字输入点和数字输出点,并且还应该考虑模拟输入和输出的数量。
2.灵活可扩展性:材料自动分拣系统的规模和要求有可能会发生变化,因此PLC设计应该具备灵活可扩展性。
这意味着PLC应该有足够的扩展槽,能够容纳多个输入/输出模块和通信模块。
3.高性能计算能力:PLC需要具备较高的计算能力,以便能够高效处理系统中传输的大量数据。
此外,它还需要快速的响应时间来满足实时性要求,确保系统可以准确地识别和分类物料。
4.高可靠性和稳定性:材料自动分拣系统需要长时间运行,因此PLC设计应该具备高可靠性和稳定性。
这要求PLC电源模块提供稳定的电源供应,同时需要考虑过电流和过电压保护电路来防止设备损坏。
5.通信能力:PLC需要与其他设备进行通信,例如与计算机、上位机或其它控制设备的通信。
因此,PLC设计需要支持多种通信协议,如以太网、串行通信等,以实现与其他设备的数据交换和控制。
6.用户界面:为了方便操作和维护,PLC设计还应该具备友好的用户界面。
这包括易于使用的编程软件、调试界面和监控界面,以便用户能够轻松地进行配置、监控和故障排除。
在PLC设计过程中,还需要考虑其他因素,如系统的安全性、抗电磁干扰能力等。
此外,为了确保PLC的可靠性和稳定性,还需要进行适当的故障检测和纠正措施。
总之,材料自动分拣系统的PLC设计需要满足输入/输出处理、灵活可扩展性、高性能计算能力、高可靠性和稳定性、通信能力和用户界面等要求。
通过合理的设计和选型,可以实现系统的高效运行和稳定性。
垃圾自动分拣机构PLC控制

垃圾自动分拣机构PLC控制第1章前言最初的分拣系统是完全基于人力的作业系统。
通过人工搜索、搬运来完成货物的提取。
这种分拣系统的作业效率低下,无法满足现代化物流配送对速度和准确性的高要求。
随着科学技术的飞速发展,分拣系统中开始运用各种各样的自动化机械设备。
计算机控制技术和信息技术成为信息传递和处理的重要手段。
机械化、自动化、智能化成为现代分拣系统的主要特点与发展趋势。
自动分拣系统是二战后在美国、日本以及欧洲广泛采用的一种分拣系统。
一般由控制装置、分类装置、输送装置及分拣道口四部分组成,它们通过计算机网络联结在一起,配合人工控制及相应的人工处理环节构成一个完整的分拣系统。
随着计算机技术的飞速发展,可编程控制器应运而生。
并且功能也越来越强大。
在应用上,PLC有着其他设备无以比拟的优越性,它可靠性高,抗干扰能力高;适用性强,应用灵活;编程方便,易于使用;功能强大,扩展能力强;控制系统设计、安装、调试方便;维修方便,维修工作量少;体积小,质量轻,易于实现机电一体化。
对本系统完成其设计之后,进行了整体调试。
在硬件部分,调试其各部分安装的位置及角度,使其材料物块的运行与传感器安装的角度适合。
将硬件各部分的动作幅度进行调试之后,进行了软硬件综合调试,实现材料分拣系统中上料、传送与分拣的全过程。
第2章垃圾分拣自动分拣的设计背景2.1分检系统的基本介绍自动分拣系统(Automatic sorting system)是先进配送中心所必需的设施条件之一。
它具有很高的分拣效率,通常每小时可分拣商品6000-12000箱,可以说,自动分拣机是提高物流配送效率的一项关健因素。
它是二次大战后在美国、日本的物流中心中广泛采用的一种自动分拣系统,该系统目前已经成为发达国家大中型物流中心不可缺少的一部分。
自动分拣机是自动分拣系统的一个主要设备。
它本身需要建设短则40-50米,长则150-200米的机械传输线,还有配套的机电一体化控制系统、计算机网络及通信系统等,这一系统不仅占地面积大(动辄20000平方米以上),而且还要建3-4层楼高的立体仓库和各种自动化的搬运设施(如叉车)与之相匹配,这项巨额的先期投入通常需要花10-20年才能收回。
分选机PLC介绍
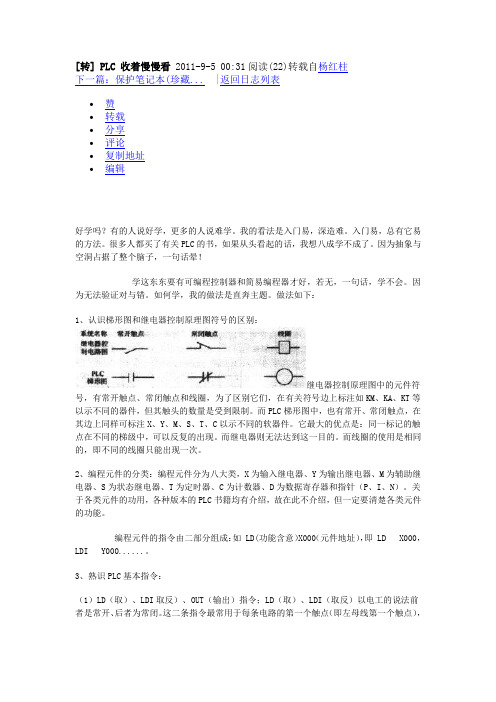
[转] PLC 收着慢慢看2011-9-5 00:31阅读(22)转载自杨红柱下一篇:保护笔记本(珍藏... |返回日志列表∙赞∙转载∙分享∙评论∙复制地址∙编辑好学吗?有的人说好学,更多的人说难学。
我的看法是入门易,深造难。
入门易,总有它易的方法。
很多人都买了有关PLC的书,如果从头看起的话,我想八成学不成了。
因为抽象与空洞占据了整个脑子,一句话晕!学这东东要有可编程控制器和简易编程器才好,若无,一句话,学不会。
因为无法验证对与错。
如何学,我的做法是直奔主题。
做法如下:1、认识梯形图和继电器控制原理图符号的区别:继电器控制原理图中的元件符号,有常开触点、常闭触点和线圈,为了区别它们,在有关符号边上标注如KM、KA、KT等以示不同的器件,但其触头的数量是受到限制。
而PLC梯形图中,也有常开、常闭触点,在其边上同样可标注X、Y、M、S、T、C以示不同的软器件。
它最大的优点是:同一标记的触点在不同的梯级中,可以反复的出现。
而继电器则无法达到这一目的。
而线圈的使用是相同的,即不同的线圈只能出现一次。
2、编程元件的分类:编程元件分为八大类,X为输入继电器、Y为输出继电器、M为辅助继电器、S为状态继电器、T为定时器、C为计数器、D为数据寄存器和指针(P、I、N)。
关于各类元件的功用,各种版本的PLC书籍均有介绍,故在此不介绍,但一定要清楚各类元件的功能。
编程元件的指令由二部分组成:如 LD(功能含意)X000(元件地址),即 LD X000,LDI Y000......。
3、熟识PLC基本指令:(1)LD(取)、LDI取反)、OUT(输出)指令;LD(取)、LDI(取反)以电工的说法前者是常开、后者为常闭。
这二条指令最常用于每条电路的第一个触点(即左母线第一个触点),当然它也可能在电路块与其它并联中的第一个触点中出现。
这是一张梯形图(不会运行)。
左边的纵线称为左母线,右母线可以不表示。
该图有三个梯级;第1梯级;左边第一个触点为常开,上标为X000,X表示为输入继电器,其后的000数据,可以这样认为它使用的是输入继电器中的编号为第000的触点(下同)。
邮件分拣机的PLC控制

课程设计任务书机械工程学院系班学生课程设计课题:邮件分拣机的PLC控制一、课程设计工作日自 2010 年 6 月 15 日至 2010 年 6 月 25 日二、同组学生:三、课程设计任务要求(包括课题来源、类型、目的和意义、基本要求、完成时间、主要参考资料等):1、邮件分拣机简介邮件分拣机是邮政系统用于对寄往各地的邮件进行快速分拣的设备,它主要由邮件编码识别传感器、邮件传送带拖动电动机、与拖动电动机同轴的旋转脉冲发生器、邮件分拣装置和邮件收信箱组成。
它通过传感器识别各地不同的邮政编码,用传送带将邮件传送到各个邮件收集箱位置分拣。
传送带由电动机拖动,不同地方的邮件在传送带上传送的距离由与电动机同轴连接的旋转编码器发出的脉冲数决定,传送到位后,由邮件分拣装置将邮件分拣到邮件收集箱。
由于用旋转编码器脉冲进行传送距离的定位,所以能保证邮件精确运送到位。
2、邮件分拣机的控制要求邮件分拣机实训模块的控制要求如下:1)机器由按钮作起动与停止控制,起动后,绿灯发光;各元件应处于复位位置,此时可用拨码开关设定不同地方的邮政编码。
2)用按钮S1发出的信号来确定邮件编码已被检测,按下S1后(表示邮件已检测),传送带电动机运转,旋转脉冲发生器(BV)发出高速脉冲,此时绿灯熄灭,红灯发光,表示正在传送邮件,暂定检测。
3)用BV发出的高速脉冲数量来确定邮件传送的距离,高速脉冲数量应按不同的邮政编码设定,以保证将邮件传送到指定的分拣位置。
邮件送到定位置后,该位置的分拣装置指示灯发光。
4)设邮件分拣时间为2S,完成分拣后红灯熄灭,绿灯发光,机器等待邮件检测。
5)当从检测到不符合指定邮政编码的数值时,红灯闪烁,表示邮编有错,红灯闪烁5S熄灭。
3.设计任务1) 根据控制要求,进行邮件分拣机的PLC I/O分配与接线。
2) 根据控制要求,编制机床控制PLC应用程序,有条件可以利用模拟开关板调试程序,模拟运行。
3) 编写设计说明书,内容包括:①设计过程和有关说明。
自动分拣PLC
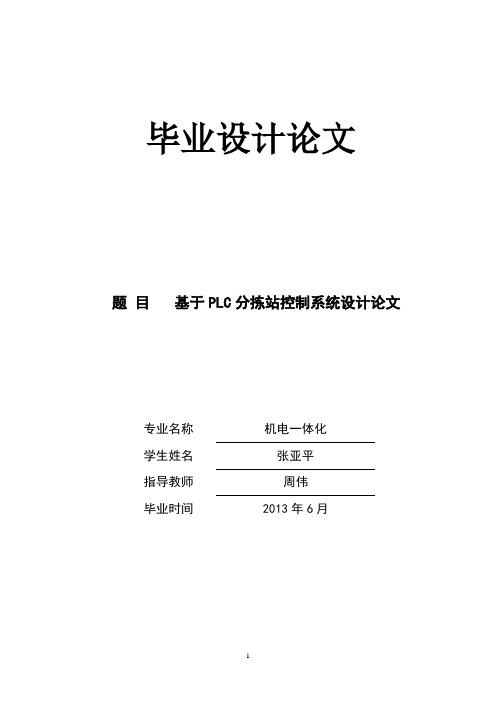
毕业设计论文题目基于PLC分拣站控制系统设计论文专业名称机电一体化学生姓名张亚平指导教师周伟毕业时间2013年6月毕业任务书一、题目自动分拣站(PLC+交流电机+气动元件)控制系统设计。
二、指导思想和目的要求以PLC为核心,为产品分拣自动生产线设计一个电气控制系统。
三、主要技术指标(1)正确选择PLC和交流电机。
(2)掌握电气控制元件的选择。
(3)掌握气动元件选择与运用。
(4)正确使用传感器、变频器。
(5)掌握变频器的选择方法。
四、设计要求实现对不同材质、不同颜色货物的自动输送、分拣。
五、主要参考书及参考资料常斗南。
可编程控制器原理、应用、实验[M]。
北京:机械工业出版社,1998,24-241 樊尚春。
传感器技术及应用[M]。
北京:北京航空航天大学出版社,2004.230-268 刘小春.电气控制与PLC计数[M].人民邮电出版社,2008,92-200吕景泉.自动化生产线安装与调试. 中国铁道出版社 , 2008, 116-205宋爽。
变频技术及应用。
高等教育出版社, 2008,1-210黄志昌黄鹏.液压与气动技术电子工业出版社2010,7李国厚.PLC原理与应用设计[M].北京化工工业出版社,2005白娟娟,郭军,PLC技术应用,北京理工大学出版社,2010张桂香,马全广,电气控制与PLC应用,化学工业出版社,2003学生张亚平指导教师___周伟___摘要本文讨论的材料分拣控制系统,完成了材料自动分拣系统的所有基本工作。
它使用了PLC、传感器、位置控制、电气传动和气动等技术,可以实现不同材料的自动分拣和归类功能,并可配置监控软件由上位计算机监控。
PLC控制是目前工业上最常用的自动化控制方法,由于其控制方便,能够承受恶劣的环境,因此,在工业上优于单片机的控制。
PLC将传统的继电器控制技术、计算机技术和通信技术融为一体,专门为工业控制而设计,具有功能强、通用灵活、可靠性高、环境适应性强、编程简单、使用方便以及体积小、重量轻、功耗低等一系列优点,因此在工业上的应用越来越广泛。
- 1、下载文档前请自行甄别文档内容的完整性,平台不提供额外的编辑、内容补充、找答案等附加服务。
- 2、"仅部分预览"的文档,不可在线预览部分如存在完整性等问题,可反馈申请退款(可完整预览的文档不适用该条件!)。
- 3、如文档侵犯您的权益,请联系客服反馈,我们会尽快为您处理(人工客服工作时间:9:00-18:30)。
[转] PLC 收着慢慢看2011-9-5 00:31阅读(22)转载自杨红柱下一篇:保护笔记本(珍藏... |返回日志列表∙赞∙转载∙分享∙评论∙复制地址∙编辑好学吗?有的人说好学,更多的人说难学。
我的看法是入门易,深造难。
入门易,总有它易的方法。
很多人都买了有关PLC的书,如果从头看起的话,我想八成学不成了。
因为抽象与空洞占据了整个脑子,一句话晕!学这东东要有可编程控制器和简易编程器才好,若无,一句话,学不会。
因为无法验证对与错。
如何学,我的做法是直奔主题。
做法如下:1、认识梯形图和继电器控制原理图符号的区别:继电器控制原理图中的元件符号,有常开触点、常闭触点和线圈,为了区别它们,在有关符号边上标注如KM、KA、KT等以示不同的器件,但其触头的数量是受到限制。
而PLC梯形图中,也有常开、常闭触点,在其边上同样可标注X、Y、M、S、T、C以示不同的软器件。
它最大的优点是:同一标记的触点在不同的梯级中,可以反复的出现。
而继电器则无法达到这一目的。
而线圈的使用是相同的,即不同的线圈只能出现一次。
2、编程元件的分类:编程元件分为八大类,X为输入继电器、Y为输出继电器、M为辅助继电器、S为状态继电器、T为定时器、C为计数器、D为数据寄存器和指针(P、I、N)。
关于各类元件的功用,各种版本的PLC书籍均有介绍,故在此不介绍,但一定要清楚各类元件的功能。
编程元件的指令由二部分组成:如 LD(功能含意)X000(元件地址),即 LD X000,LDI Y000......。
3、熟识PLC基本指令:(1)LD(取)、LDI取反)、OUT(输出)指令;LD(取)、LDI(取反)以电工的说法前者是常开、后者为常闭。
这二条指令最常用于每条电路的第一个触点(即左母线第一个触点),当然它也可能在电路块与其它并联中的第一个触点中出现。
这是一张梯形图(不会运行)。
左边的纵线称为左母线,右母线可以不表示。
该图有三个梯级;第1梯级;左边第一个触点为常开,上标为X000,X表示为输入继电器,其后的000数据,可以这样认为它使用的是输入继电器中的编号为第000的触点(下同)。
其指令的正确表示应为(如右图程序所示):0、LD X000 (前头的0 即为从第0步开始,指令输入时无须理会,它会自动按顺序显示出)。
第2梯级;左边的第一个触点为常闭触点,上标为T0,T表示定时器(有时间长短不同,应注意),0则表示定时器中的编号为0的触点。
其指令的正确表示应为:2、LDI T0(如程序所示)。
第3梯级;左边第一个触点为常闭,上标为M0, M为辅助继电器(该继电器有多种,注意类别),其指令的正确表示应为:4、LDI M0(如程序所示)。
本梯级的第2行第一个触点为常开,上标为Y000,Y表示输出继电器,由于该触点与后面Y001触点呈串联关系,形成了所谓的电路"块",故而其触点的指令应为 5、LD Y000。
总之LD与LDI指令从上面可以看出,它们均是左母线每一梯级第一触点所使用的指令。
而梯级中的支路(即第3梯级的第2行)有二个或二个以上触点呈串联关系,其第一触点同样按LD或LDI指令。
可使用LD、LDI指令的元件有:输入继电器X、输出继电器Y、辅助继电器M、定时器T、计数器C、状态继电器S。
OUT为线圈驱动指令,该指令不能出现在左母线第一位。
驱动线圈与驱动线圈不能串联,但可并联。
同一驱动线圈只能出现一次,并安排在每一梯级的最后一位。
如上图中的1、OUT Y000,3、OUT Y001,Y为输出继电器,其线圈一旦接获输出信号,可以这样认为,线圈将驱动其相应的触点而接通外部负载(外部负载多为接触器、中间继电器等)。
而上图8、OUT T0 K40 为定时器驱动线圈指令,其中的K为常数40为设定值(类似电工对时间继电器的整定)。
可使用OUT指令元件有:输出继电器Y、辅助继电器M、定时器T、计数器C、状态继电器S。
(2)触点的串联指令AND(与)ANI(与非);前者为常开,后者为常闭。
二者均用于单个触点的串联。
二指令可重复出现,不受限制,。
如下图所示。
由第1梯级来看;X000、T0、Y001三触点成串联关系,即T0的常闭串接于X000的后端,而Y001的常闭则串接于T0常闭的后端。
由于都是常闭故用ANI指令。
现来看第2梯级;X000、M0、Y001,同样三触点也是串联关系,M0的常闭接点串接于X001的后端,而Y000的常开接点则串接于M0的后端。
故M0的指令用ANI,而Y000的指令则用AND(具体编程详上图),一句话只要是串联后面是常开的用AND,是常闭的则用ANI。
可使用AND、ANI指令元件有:输入继电器X、输出继电器Y、辅助继电器M、定时器T、计数器C、状态继电器S。
(3)触点并联指令OR(或)、ORI(或反);触点并联时,不管梯级中有几条支路,只要是单个触点与上一支路并联,是常开的用OR,是常闭的则用ORI。
如下图所示。
可以看出上图的X000、X001、M0三者处于并联关系。
由于X000下面二条支路均为单个触点,因X001是常开触点,故用OR指令。
而M0是常闭触点,则用ORI指令。
三接点并联后又与M1串联,串联后又与Y000并联,而Y000也是单个触点,所以仍采用OR指令。
可使用OR、ORI指令元件有:输入继电器X、输出继电器Y、辅助继电器M、定时器T、计数器C、状态继电器S。
(4)串联电路块的并联指令ORB(或);任一梯级中有多(或单支路)支路与上一级并联,只要是本支路中是二个以上的触点成串联关系(即所谓的:串联电路块),则应使用ORB指令。
如下图所示。
由上图可以看出,第一支路X003的常开触点与M1的常开触点成串联关系(在这样的情况下,形成了块的关系),它是与上一行的X000与M0串联后相并联,此时程序的编写,如步序号0、1、2、3、4所示。
4所出现的第一个ORB指的是与上一行并。
而第二支路,常闭Y001与M2同样是串联关系。
也是一个块结构,其串联后再与第一支路并。
故步序7再次出现ORB。
ORB指令并无梯形图与数据的显示。
可以这样认为;它是下一行形成电路块的情况下与上一行并联的一条垂直直线(如图中所示的二条粗线)。
(5)并联电路块与块之间的串联指令ANB;如左下图虚线框内所示的二电路块相串,各电路块先并好后再用ANB指令进行相串。
左图的梯形图可以用右图进行简化。
程序的编写如下图所示。
ANB指令并无梯形图与数据的显示。
可以这样认为;它是形成电路块与电路块之间的串联联接关系,是一条横直线。
(6)进栈指令MPS、读栈指令MRD、出栈指令MPP和程序结束指令END;MPS、MRD、MPP这是一组堆栈指令。
如下图使用的二种堆栈形式;在堆栈形式下MPS应与MPP成对出现使用。
如在第一堆栈形式下,则采用MPS、MPP指令。
若在MPS、MPP指令中间还有支路出现,则增加MRD指令,如下图的第二堆栈所示。
应知道MPS、MPP成对出现的次数应少于11次,而MRD的指令则可重复使用,但不得超过24次。
要知道这一组指令,同样并无梯形图与数据的显示。
可以这样认为;MPS是堆栈的起始点,它起到承上启下的联接点作用,而支路的MRD、MPP则与之依次联接而已。
而END指令则是结束指令,它在每一程序的结束的末端出现。
当然还有其它的指令,但只要熟织和应用以上的指令,我以为入个门应该没什么问题了,也够用了。
入了门后再去研究其它的指令就不是很难了。
故不再一一说明。
4、熟知简易编程器各键的功能:以下是FX-10P(手持式编程器)面板分布(当然少了晶液显示屏)及各键功能。
各键下方标注的中文与元件符号均为我所增加(目的是为了输入时易找到对象),其余均与原键盘相同(即实线框内英文与数码)。
(1)液晶显示器;在编程时可显示指令(即指令、元件符号、数据)。
在监控运行时,可显示元器件工作状态。
(2)键盘;由35个按键组成,有功能键、指令键、元件符号键和数据键,大多可切换。
各键作用如下:①功能键:RD/WR......读出/写入,若在左下角出现R为程序读出,若出现W则为写入,即程序输入时应出现W,否则无法输入程序。
按第一下如为R,再按一下则为W。
INS/DEL......插入/删除,若在程序输入过程中漏了一条程序,此时应按该键,显现I则可输入遗漏程序。
若发现多输了一条程序,同样按该键,显现D则可删除多余或错误的程序。
MNT/TEST......监视/测试,T为测试,M为监视,同样按该键,可相互切换。
在初学时要学会使用监视键M, 以监视程序的运行情况,以利找出问题,解决问题。
②菜单键:OTHER, 显示方式菜单。
③清除键:CLEAR,按此键,可清除当前输入的数据。
④帮助键:HELP,显示应用指令一览表,在监视方式时进行十进制数和十六进制数为转换。
⑤步序键:STEP,监视某步输入步序号。
⑥空格键:,/SP,输入指令时,用于指定元件号和常数。
⑦光标键:↑、↓,用这二键可移动液晶显示屏上光标,作行(上或下)滚动。
⑧执行键:GO,该键用于输入指令的确认、插入、删除的执行等。
⑨指令键/元件符号键/数字键(虚线框内):这些键均可自动切换,上部为指令键,下部为元件符号键或数字键。
一旦按了指令键,其它键即切换成元件符号或数字,可以进行选择输入。
其它Z/V、K/H、P/I均可同一键的情况下相互切换。
5、熟习编程器的操作按规定联接好PLC与简易编程器。
PLC通入电源,小型指示灯亮。
将PLC上的扭子开关拨向STOP(停止)位置。
操作要点:①清零:扭子开关拨向STOP(停止)位置,会出现英文,别管它。
直接按RD/WD(使显示屏左侧出现W即写的状态),此时先按NOP,再按MC/A中的A,接着按二次GO予以确认即可(即:W→NOP→A→GO→GO)。
②输入指令:如指令LD X000,按以下顺序输入LD→X→0→GO 即可,屏上自动显现LD X000。
其它指令类推。
对于ORB、ANB、MPS、MRD、MPP、END、NOP等指令,输入后只要按GO确认即可(ORB→GO)。
③定时器的输入:如指令OUT T0 K 40按如下顺序输入即可OUT→T→0→,/SP→K→40→GO(T0为100ms为单位,其整定值为:100×40=4000ms=4S)。
④删除指令:移动光标对准欲删除的指令,将INS/DEL键置于D,再予以GO确认即可。
即:移动光标对准欲删除指令→D→GO。
⑤插入指令:若欲在步序4、5之间插入新的步序,移动光标对准5,将INS/DEL键置于I,予以确认,再输入新的程序再次确认即可。
如欲插入AND Y001即:移动光标对准欲插入部位→I→GO→AND→Y→1→GO。
⑥GO键:每一步序输入完毕均应输入GO予以确认。
⑦结束指令:每一程序输入完毕在结束时应输入END指令,程序才可运行。